SMC的发展及其成型工艺研究
SMC材料与工艺简介(免费)
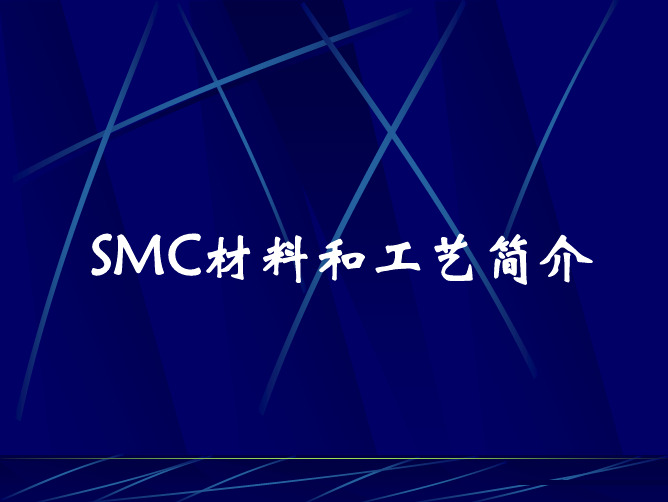
SMC简述
SMC的特点
轻质高强 -实现轻量化目标 -实现节能目标 -良好的抗冲吸能性
SMC简述
产品设计自由度大 -实现产品的流线型设 计 -通过后粘接技术实现 中空结构的成型 -减轻产品重量
SMC简述
材料流动性好,可实现复杂 结构的成型
-筋、台结构的一次成型 -预埋件的成型 -抽芯结构的实现
SMC简述
-产品开发周期一般为3~5个 月; -一次性投资较大; -适于2~5万件/年的需求量
SMC配方设计
SMC的配方一般可分为三种基本类型 标准(或基本)的SMC配方 特殊性能要求的SMC配方 根据制品应用要求配制的SMC配方
SMC配方设计
不同材料性能的配方特点 耐水煮型 阻燃型 A级表面型 高强型 低密度型等 据最终制品用途设计的SMC配方特点 轿车级A级表面用(外观件兼一定功能性) 发动机罩下零件(功能性) 公共交通车辆用低密度、阻燃SMC配方 电工用着色低收缩SMC配方
SMC的生产工艺及其过程质量控制
工艺流程简图
SMC的生产工艺及其过程质量控制
上糊区立面图
SMC的生产工艺及其过程质量控制
SMC片材的一般规格参数 幅宽0.45~1.5m 厚度1.3~6.4mm 玻纤含量20%~35% 纤维长度12~50mm 纤维取向任意 承载薄膜厚度0.05mm 单重范围2~6Kg,一般3~4Kg,控制精度 ±0.1Kg 树脂糊浸渍粘度10~50Pa ·s 树脂糊涂覆量3~12Kg/min 最佳模压粘度2×104 Pa·s
SMC的生产工艺及其过程质量控制
典型的SMC材料物理机械性能
序号 项 目 依维柯保险杠 福田重卡面罩 切诺基后门
1 2 3 4 5 6 7
8 9
SMC
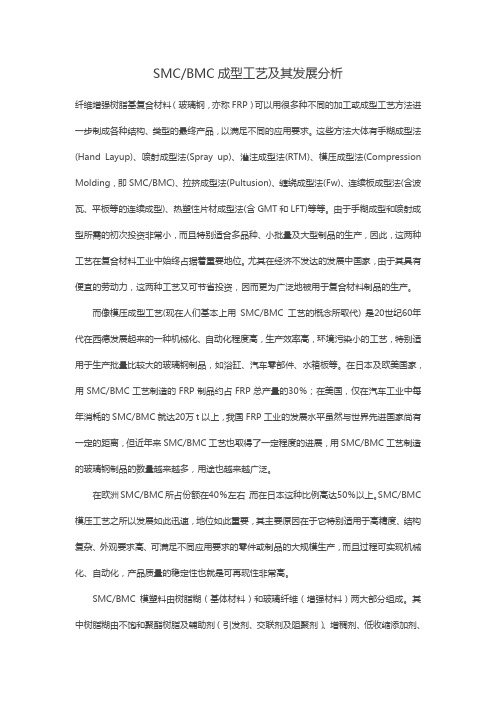
SMC/BMC成型工艺及其发展分析纤维增强树脂基复合材料(玻璃钢,亦称FRP)可以用很多种不同的加工或成型工艺方法进一步制成各种结构、类型的最终产品,以满足不同的应用要求。
这些方法大体有手糊成型法(Hand Layup)、喷射成型法(Spray up)、灌注成型法(RTM)、模压成型法(Compression Molding,即SMC/BMC)、拉挤成型法(Pultusion)、缠绕成型法(Fw)、连续板成型法(含波瓦、平板等的连续成型)、热塑性片材成型法(含GMT和LFT)等等。
由于手糊成型和喷射成型所需的初次投资非常小,而且特别适合多品种、小批量及大型制品的生产,因此,这两种工艺在复合材料工业中始终占据着重要地位。
尤其在经济不发达的发展中国家,由于其具有便宜的劳动力,这两种工艺又可节省投资,因而更为广泛地被用于复合材料制品的生产。
而像模压成型工艺(现在人们基本上用SMC/BMC工艺的概念所取代) 是20世纪60年代在西德发展起来的一种机械化、自动化程度高,生产效率高,环境污染小的工艺,特别适用于生产批量比较大的玻璃钢制品,如浴缸、汽车零部件、水箱板等。
在日本及欧美国家,用SMC/BMC工艺制造的FRP制品约占FRP总产量的30%;在美国,仅在汽车工业中每年消耗的SMC/BMC就达20万t以上,我国FRP工业的发展水平虽然与世界先进国家尚有一定的距离,但近年来SMC/BMC工艺也取得了一定程度的进展,用SMC/BMC工艺制造的玻璃钢制品的数量越来越多,用途也越来越广泛。
在欧洲SMC/BMC所占份额在40%左右,而在日本这种比例高达50%以上。
SMC/BMC 模压工艺之所以发展如此迅速,地位如此重要,其主要原因在于它特别适用于高精度、结构复杂、外观要求高、可满足不同应用要求的零件或制品的大规模生产,而且过程可实现机械化、自动化,产品质量的稳定性也就是可再现性非常高。
SMC/BMC模塑料由树脂糊(基体材料)和玻璃纤维(增强材料)两大部分组成。
smc生产工艺介绍
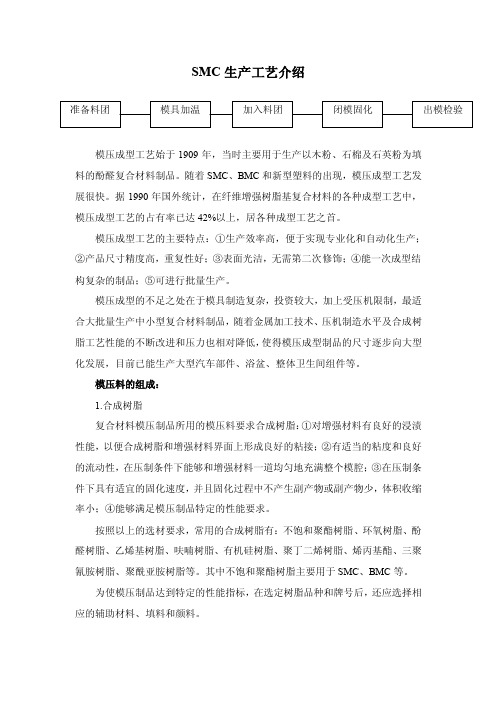
SMC生产工艺介绍模压成型工艺始于1909年,当时主要用于生产以木粉、石棉及石英粉为填料的酚醛复合材料制品。
随着SMC、BMC和新型塑料的出现,模压成型工艺发展很快。
据1990年国外统计,在纤维增强树脂基复合材料的各种成型工艺中,模压成型工艺的占有率已达42%以上,居各种成型工艺之首。
模压成型工艺的主要特点:①生产效率高,便于实现专业化和自动化生产;②产品尺寸精度高,重复性好;③表面光洁,无需第二次修饰;④能一次成型结构复杂的制品;⑤可进行批量生产。
模压成型的不足之处在于模具制造复杂,投资较大,加上受压机限制,最适合大批量生产中小型复合材料制品,随着金属加工技术、压机制造水平及合成树脂工艺性能的不断改进和压力也相对降低,使得模压成型制品的尺寸逐步向大型化发展,目前已能生产大型汽车部件、浴盆、整体卫生间组件等。
模压料的组成:1.合成树脂复合材料模压制品所用的模压料要求合成树脂:①对增强材料有良好的浸渍性能,以便合成树脂和增强材料界面上形成良好的粘接;②有适当的粘度和良好的流动性,在压制条件下能够和增强材料一道均匀地充满整个模腔;③在压制条件下具有适宜的固化速度,并且固化过程中不产生副产物或副产物少,体积收缩率小;④能够满足模压制品特定的性能要求。
按照以上的选材要求,常用的合成树脂有:不饱和聚酯树脂、环氧树脂、酚醛树脂、乙烯基树脂、呋喃树脂、有机硅树脂、聚丁二烯树脂、烯丙基酯、三聚氰胺树脂、聚酰亚胺树脂等。
其中不饱和聚酯树脂主要用于SMC、BMC等。
为使模压制品达到特定的性能指标,在选定树脂品种和牌号后,还应选择相应的辅助材料、填料和颜料。
2.增强材料模压料中常用的增强材料主要有玻璃纤维开刀丝、无捻粗纱、有捻粗纱、连续玻璃纤维束、玻璃纤维布、玻璃纤维毡等,也有少量特种制品选用石棉毡、石棉织物(布)和石棉纸以及高硅氧纤维、碳纤维、有机纤维和天然纤维等品种。
有时也采用两种或两种以上纤维混杂料作增强材料。
SMC成型工艺分析

-
材料学院彭进波
4.3.3 SMC的生产工艺
SMC生产工艺流程和生产机组详见 p92图4-18和图4-19,主要包括以下 工序: 1.树脂糊的制备及上糊操作 树脂糊的制备分为两种方法:批 混合法和连续计量混合法, 树脂糊的粘度要求及控制, 上糊操作的要求
200307
材料学院彭进波
4.3.3 SMC的生产工艺
SMC常用的Up树脂种类
1、低粘度;便于浸渍GF。 1、顺酐型Up树脂; 2、易同增稠剂反应;满足增稠的要求。 2、乙烯基树脂; 3、可降低收缩性; 3、丙烯酸环氧脂树 4、固化迅速,提高生产效率; 脂; 5、应具有较高的热强度和一定的韧性; 4、环氧化聚丁二烯 在制品脱模时,不易损坏或开裂。 树脂;
200307
材料Байду номын сангаас院彭进波
200307
材料学院彭进波
4.3.2 SMC的组分及其性能
SMC的组分及其性能
SMC
树脂糊 增强纤维
UP 树 脂
交 联 剂
引 发 剂
增 稠 剂
脱 模 剂
低收 缩添 加剂
无 机 填 料
200307
材料学院彭进波
4.3.2 SMC的组分及其性能
1.不饱和聚脂树脂(Up树脂)
SMC对Up树脂的基本要求
4.3.2 SMC的组分及其性能
6、低收缩添加剂
品种 PS PE Up树脂的固化收缩率,保 PVAc 降低 低收缩添加剂的作用 证制品的表光洁度及尺寸稳定 1. 热塑性聚合物的添加量通常控制在 5%左右(质 用量 1. 热塑性聚合物的热膨胀作用; 15 20 25 30 15 20 性。 25 30 15 20 25 30 量比)。过多将会对 Up体系起增塑作用,降低 % 低收缩机理 2. 热塑性聚合物的贮存作用; 树脂体系的强度;同时使放热峰值下降,固化 线收 3. 热塑性聚合物的溶解或溶胀作用。 时间延长。 0.25 0.23 0.14 0.103 0.217 0.187 0.160 0.146 0.219 0.216 0.143 0 .057 缩率 2. 低收缩添加剂的用量对制品线收缩率的影响。 常用热塑性聚合物低收缩添加剂的种类及特性 %
SMC模压成型工艺过程
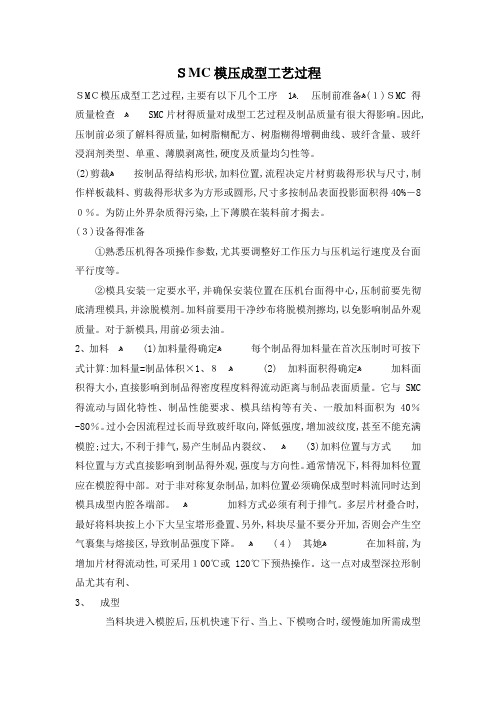
SMC模压成型工艺过程SMC模压成型工艺过程,主要有以下几个工序ﻫ1. 压制前准备ﻫ(1)SMC得质量检查ﻫSMC片材得质量对成型工艺过程及制品质量有很大得影响。
因此,压制前必须了解料得质量,如树脂糊配方、树脂糊得增稠曲线、玻纤含量、玻纤浸润剂类型、单重、薄膜剥离性,硬度及质量均匀性等。
(2)剪裁ﻫ按制品得结构形状,加料位置,流程决定片材剪裁得形状与尺寸,制作样板裁料、剪裁得形状多为方形或圆形,尺寸多按制品表面投影面积得40%-80%。
为防止外界杂质得污染,上下薄膜在装料前才揭去。
(3)设备得准备①熟悉压机得各项操作参数,尤其要调整好工作压力与压机运行速度及台面平行度等。
②模具安装一定要水平,并确保安装位置在压机台面得中心,压制前要先彻底清理模具,并涂脱模剂。
加料前要用干净纱布将脱模剂擦均,以免影响制品外观质量。
对于新模具,用前必须去油。
2、加料ﻫ(1)加料量得确定ﻫ每个制品得加料量在首次压制时可按下式计算:加料量=制品体积×1、8ﻫ(2) 加料面积得确定ﻫ加料面积得大小,直接影响到制品得密度程度料得流动距离与制品表面质量。
它与SMC 得流动与固化特性、制品性能要求、模具结构等有关、一般加料面积为40%-80%。
过小会因流程过长而导致玻纤取向,降低强度,增加波纹度,甚至不能充满模腔;过大,不利于排气,易产生制品内裂纹、ﻫ(3)加料位置与方式加料位置与方式直接影响到制品得外观,强度与方向性。
通常情况下,料得加料位置应在模腔得中部。
对于非对称复杂制品,加料位置必须确保成型时料流同时达到模具成型内腔各端部。
ﻫ加料方式必须有利于排气。
多层片材叠合时,最好将料块按上小下大呈宝塔形叠置、另外,料块尽量不要分开加,否则会产生空气裹集与熔接区,导致制品强度下降。
ﻫ(4) 其她ﻫ在加料前,为增加片材得流动性,可采用100℃或120℃下预热操作。
这一点对成型深拉形制品尤其有利、3、成型当料块进入模腔后,压机快速下行、当上、下模吻合时,缓慢施加所需成型压力,经过一定得固化制度后,制品成型结束。
SMC产品工艺流程

SMC产品工艺流程一.SMC的成型工艺流程压制前准备(模具升温、压机工艺参数设定)——SMC片材裁料——模具投料——保压——脱模——加工(去废边等)——成品。
⑴压制前准备(模具升温、压机工艺参数设定):通常模具温度一般来说是到130°~150°之间,成型压力为5~10兆帕,相当于每平方厘米施加50公斤到100公斤的压力,压力非常高。
⑵ SMC片材裁料:裁剪SMC片材,为模具投料做准备。
⑶模具投料:经过严格的重量计算,将SMC片材投入模具中,通常投料面积在50%-90%之间。
⑷保压:模具闭合后,保持高温高压,通常保持时间根据产品要求不同在2-10分钟之间。
⑸脱模:控制压机模具开启,将产品从模具中起出。
⑹加工:剪裁废边,打磨模具边缘与缝隙间的毛刺。
⑺得出半成品半成品按照一定规律进行码放,经质检合格的产品转运入库。
二.科逸SMC模压生产工艺参数三.提高SMC制品的条件与方法SMC配件的模压质量,取决于压机设备、模具、工艺参数以及作业人员素质等因素。
科逸SMC模压件质量的优异稳定,不仅仅来自于对制造工艺和生产管理手段的严格控制,更重要的主要是科逸在生产的各个方面都有良好的积累。
首先,在压机设备上,卫浴SMC部品对于压机要求十分严格。
模压时需要对产品施加的压力为50-100公斤/平方厘米。
所以面积越小的产品需要的压力就小,面积较大的部件,如防水盘、壁板、浴缸、顶板等才需要压力更大的压机。
所以卫浴企业拥有单台压机最大压力值越大,产品就可以做的越大。
反之,就无法提供完善的产品。
其次,SMC部件的模压工艺,决定了对生产过程中的各个方面都必须精确,包括对压机的水平定位,压机滑块上下移动速度,模具精度等等方面。
生产时模具内每一个区域的压力、温度,甚至是开闭模具瞬间的压力都要平均准确。
这就要求SMC 部件压机、模具精度都极高,远超其他行业,压机、模具的数量规模和精度是一个整体浴室企业保障产品质量、丰富产品门类的关键设备。
SMC模压成型工艺介绍

共聚物
PVAc
0.25
线
收
缩 率
0.20
0.16
低收缩剂的种类、用量与线收缩 率的关系
1
2 1-氯醋共聚物;2-聚苯乙烯; 3-聚乙烯
3
0.01
15 20 25 30 添加量(重量份)
.29.
SMC的组分及其性能
无机填料
属惰性物质 作用: 1、降低材料成本;
2、改善制品性能。 缺点: 随填料加入量增加,树脂糊粘度
若缩短贮存SMC的启用 0
期,可将其在45℃烘房内进行
0
1
23 45
时间(h)
稠化,若延长贮存期,应在较
低的温度(小于25℃)下存放。
树脂增稠与温度的关系
.20.
SMC的组分及其性能
(4)增稠机理
两个阶段 第一阶段
金属氧化物或氢氧化物与聚酯端基- COOH进行酸碱反应,生成碱式盐。
O
C OH + MO
使用时除去薄膜,按尺寸裁剪,然后进行模压成型。
.2.
SMC的特点与种类
SMC具有的特点:
1) 制品的重现性好, SMC的制造不易受操作者和外界条 件的影响 2) 加工制品操作处理方便,不粘手 3) 作业环境清洁,大大改善了劳卫环境 4) 片材质量均匀,适宜压制截面变化不大的大型薄壁制品 5) 树脂和玻璃纤维可以流动,可成型带肋条和凸部的制品 6) 成型的制品表面光洁度高 7) 生产效率高、成型周期短、成本低
细度: 粒径要求小于120μm(120目)。 88μm(170目,水泥细度) 60μm(200目)
颗粒太粗容易分离沉淀;太细、吸油率高,树脂用量大。
油吸附量: 填料被亚麻仁油润湿的质量百分比。
SMC片状模塑料的研究
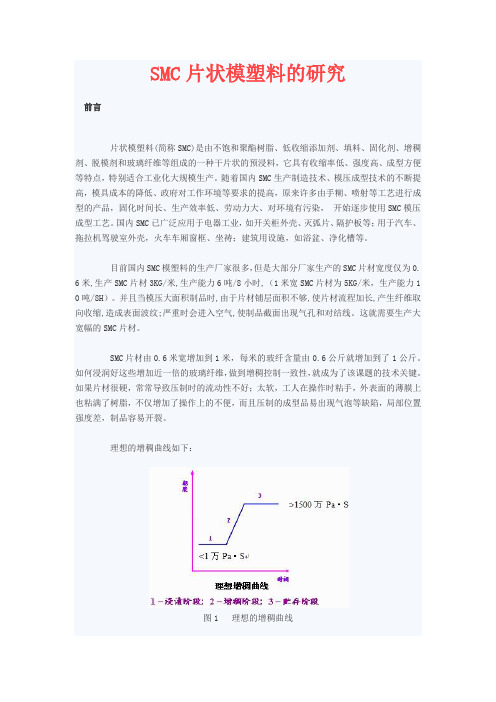
SMC片状模塑料的研究前言片状模塑料(简称SMC)是由不饱和聚酯树脂、低收缩添加剂、填料、固化剂、增稠剂、脱模剂和玻璃纤维等组成的一种干片状的预浸料,它具有收缩率低、强度高、成型方便等特点,特别适合工业化大规模生产。
随着国内SMC生产制造技术、模压成型技术的不断提高,模具成本的降低、政府对工作环境等要求的提高,原来许多由手糊、喷射等工艺进行成型的产品,固化时间长、生产效率低、劳动力大、对环境有污染,开始逐步使用SMC模压成型工艺。
国内SMC已广泛应用于电器工业,如开关柜外壳、灭弧片、隔护板等;用于汽车、拖拉机驾驶室外壳,火车车厢窗框、坐祷;建筑用设施,如浴盆、净化槽等。
目前国内SMC模塑料的生产厂家很多,但是大部分厂家生产的SMC片材宽度仅为0.6米,生产SMC片材3KG/米,生产能力6吨/8小时,(1米宽SMC片材为5KG/米,生产能力10吨/8H)。
并且当模压大面积制品时,由于片材铺层面积不够,使片材流程加长,产生纤维取向收缩,造成表面波纹;严重时会进入空气,使制品截面出现气孔和对结线。
这就需要生产大宽幅的SMC片材。
SMC片材由0.6米宽增加到1米,每米的玻纤含量由0.6公斤就增加到了1公斤。
如何浸润好这些增加近一倍的玻璃纤维,做到增稠控制一致性,就成为了该课题的技术关键。
如果片材很硬,常常导致压制时的流动性不好;太软,工人在操作时粘手,外表面的薄膜上也粘满了树脂,不仅增加了操作上的不便,而且压制的成型品易出现气泡等缺陷,局部位置强度差,制品容易开裂。
理想的增稠曲线如下:图1 理想的增稠曲线1) 初期浸渍阶段,树脂增稠要足够缓慢,保证玻纤良好的浸渍。
一般要求半小时内粘度不超过6万厘泊。
2) 增稠阶段速度要足够快,能够尽快进入模压操作。
即树脂糊粘度大于1500万厘泊。
3) 模压料达到模压粘度时,粘度保持平稳,有较长的贮存寿命。
做好增稠粘度的控制,可以带来以下优点:1) SMC片材表面不粘手,易于操作;2) SMC成型时,玻璃纤维能够流向成型品的所有部分,保证成型品各部分物理、化学性能的稳定;3) 使成型品具有好的外观。
片状模塑料(SMC)

片状模塑料(SMC)时间:2005-08-30关键词:片状塑料SMC来源:互联网一、 SMC简介片状模塑料(SMC),是一种干法制造不饱和聚酯玻璃钢制品的模塑料。
它在60年代初期首先出现在欧洲,在1965年左右美、日相继发展了这种工艺。
世界市场上的SMC大约在60年代末期即已初具生产规模,此后一直以每年20%~25%的增长速率快速增长,广泛应用于运输车辆、建筑、电子/电气等行业中。
SMC模压片材的组成如图1所示。
中间芯材是由经树脂糊充分浸渍的短切纤维(或毡)组成,上下两面用聚乙烯薄膜覆盖。
树脂糊里含有不饱和聚酯树脂、引发剂、化学增稠剂、低收缩添加剂、填料、脱模剂、着色剂等各种组分。
其生产与成型过程大致如下:短切原纱毡或玻纤粗纤铺放于预先均匀涂敷了树脂糊的PE 膜上,然后在其上覆盖另一层涂敷了树脂糊的PE膜,形成了一种"夹芯"结构。
它通过浸渍区时,树脂糊与玻纤(或毡)充分揉捏,然后收集成卷,进行必要的熟化处理。
所制成的片材达到不粘手后,即可按要求裁剪成一定尺寸,揭去两面的PE膜,按一定要求叠放于金属对模中加温加压成型。
二、 SMC应用领域:1、在汽车工业中的应用欧、美、日等发达国家已在汽车制造中大量采用SMC材料,涉及到轿车、客车、火车、拖拉机、摩托车,以及运动车、农用车等所有车种,主要应用部件包括以下几类:1)悬架零件前后保险杠,仪表板等。
2)车身及车身部件车身壳体、硬壳车顶、地板、车门、散热气护栅板、前端板、阻流板、行李舱盖板、遮阳罩、翼子板、发动机罩、大灯反光镜。
3)发动机盖下部件如空调器外壳、导风罩、进气管盖、风扇导片圈、加热器盖板、水箱部件、制动系统部件,以及电瓶托架,发动机隔音板等。
4)车内装饰部件门内饰板、车门把手、仪表盘、转向杆部件、镜子边框、座椅等。
5)其他如泵盖等电气部件,以及齿轮隔音板等驱动系统零件。
其中,尤以保险杠、车顶、前脸部件、发动机罩、发动机隔音板、前后翼子板等部件最重要,产量最大。
SMC模压成型工艺过程
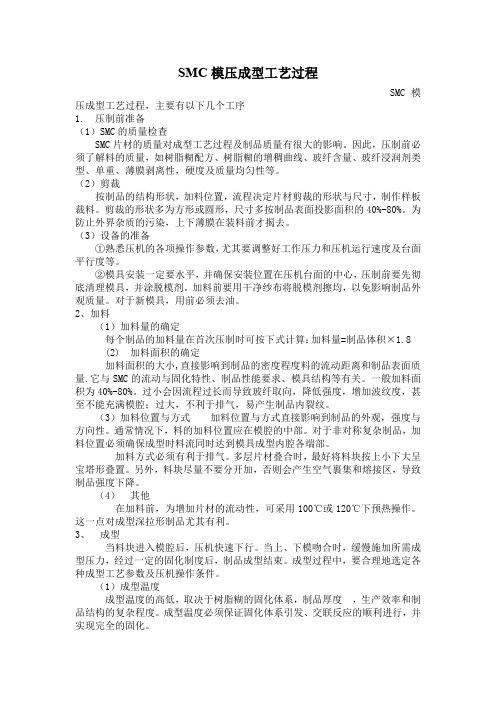
SMC模压成型工艺过程SMC模压成型工艺过程,主要有以下几个工序1. 压制前准备(1)SMC的质量检查SMC片材的质量对成型工艺过程及制品质量有很大的影响。
因此,压制前必须了解料的质量,如树脂糊配方、树脂糊的增稠曲线、玻纤含量、玻纤浸润剂类型、单重、薄膜剥离性,硬度及质量均匀性等。
(2)剪裁按制品的结构形状,加料位置,流程决定片材剪裁的形状与尺寸,制作样板裁料。
剪裁的形状多为方形或圆形,尺寸多按制品表面投影面积的40%-80%。
为防止外界杂质的污染,上下薄膜在装料前才揭去。
(3)设备的准备①熟悉压机的各项操作参数,尤其要调整好工作压力和压机运行速度及台面平行度等。
②模具安装一定要水平,并确保安装位置在压机台面的中心,压制前要先彻底清理模具,并涂脱模剂。
加料前要用干净纱布将脱模剂擦均,以免影响制品外观质量。
对于新模具,用前必须去油。
2、加料(1)加料量的确定每个制品的加料量在首次压制时可按下式计算:加料量=制品体积×1.8(2) 加料面积的确定加料面积的大小,直接影响到制品的密度程度料的流动距离和制品表面质量.它与SMC的流动与固化特性、制品性能要求、模具结构等有关。
一般加料面积为40%-80%。
过小会因流程过长而导致玻纤取向,降低强度,增加波纹度,甚至不能充满模腔;过大,不利于排气,易产生制品内裂纹。
(3)加料位置与方式加料位置与方式直接影响到制品的外观,强度与方向性。
通常情况下,料的加料位置应在模腔的中部。
对于非对称复杂制品,加料位置必须确保成型时料流同时达到模具成型内腔各端部。
加料方式必须有利于排气。
多层片材叠合时,最好将料块按上小下大呈宝塔形叠置。
另外,料块尽量不要分开加,否则会产生空气裹集和熔接区,导致制品强度下降。
(4)其他在加料前,为增加片材的流动性,可采用100℃或120℃下预热操作。
这一点对成型深拉形制品尤其有利。
3、成型当料块进入模腔后,压机快速下行。
当上、下模吻合时,缓慢施加所需成型压力,经过一定的固化制度后,制品成型结束。
复合材料成型工艺---SMC模压成型
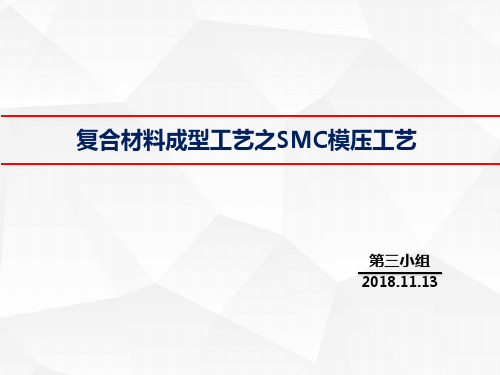
模压形状复杂、壁薄、 深度大的制品时,不宜 选用高模温,但经过预 热的塑料进行模压时, 由于内外层温度均匀, 流动性好,可选较高模 温。
模压时间主要与塑料的 固化速度有关,而固化 速度决定于塑料的种类 ,此外,模压时间与制 品的形状、厚度、模压 温度和压力以及是否预 热和预压有关
SMC模压工艺的优缺点
玻璃钢花盆
汽车装饰板
非球面透镜
模压材料工艺参数
流动性
在一定温度和压力下模压料充 满模腔的能力。不同的产品对模 塑料的流动性有不同的要求,形 状复杂和薄壁制品要求模塑料有 较大的流动性
固化速率
固化速率主要由热固性塑料的 交联反应性质决定,并受成型前 的预压、预热条件以及成型温度、 成型压力等多种因素的影响
优点
没有浇注系统,原料损失小
制品的收缩率小,且重复性较好
制品受纤维取向的影响较小,内应力 低,翘曲变形小,机械性能稳定
特别适用于成型不得翘曲的薄壁制品, 可生产壁厚小至0.6mm的制品
模压料流动距离短,模腔的磨损小且 模具的结构简单,制造成本低,维修 方便
模压成型适应性广,几乎每种塑料都 能适用,对于不适合采用注塑和挤出 成型的塑料,可采用模压成型
A段为装料室
由于具备装料室,该模具可适 用于压缩率较大的塑料。压制时, 当阳模伸入阴模,溢料只能从阳模 上开设的溢料槽中溢出。所以,物 料的外溢在这种模具中是受到一定 限制的。这种模具的特点是制造成 本高,压制时物料容易积留在支承 面上,从而导致型腔内的物料不能 得到足够的压力。
不溢出式压模
不溢式压缩模示意图 1.阳模 2.阴模 3.制品 4.推顶杆 5.定位下模板
模压成型工艺是将一定量预浸料放入到金属模具的对模模腔中,利用带热源的 压机产生一定的温度和压力,合模后在一定的温度和压力作用下使预浸料在模 腔内受热软化、受压流动、充满流动、充满模腔成型和固化,从而获得复合材 料制品的一种工艺方法
SMC模压成型工艺过程
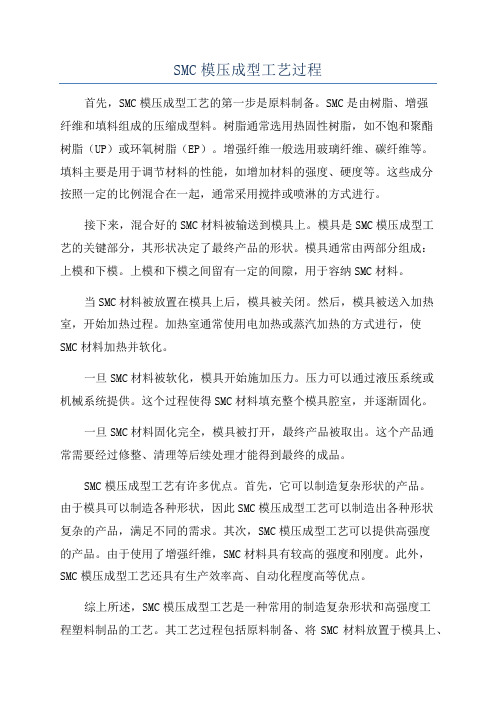
SMC模压成型工艺过程首先,SMC模压成型工艺的第一步是原料制备。
SMC是由树脂、增强纤维和填料组成的压缩成型料。
树脂通常选用热固性树脂,如不饱和聚酯树脂(UP)或环氧树脂(EP)。
增强纤维一般选用玻璃纤维、碳纤维等。
填料主要是用于调节材料的性能,如增加材料的强度、硬度等。
这些成分按照一定的比例混合在一起,通常采用搅拌或喷淋的方式进行。
接下来,混合好的SMC材料被输送到模具上。
模具是SMC模压成型工艺的关键部分,其形状决定了最终产品的形状。
模具通常由两部分组成:上模和下模。
上模和下模之间留有一定的间隙,用于容纳SMC材料。
当SMC材料被放置在模具上后,模具被关闭。
然后,模具被送入加热室,开始加热过程。
加热室通常使用电加热或蒸汽加热的方式进行,使SMC材料加热并软化。
一旦SMC材料被软化,模具开始施加压力。
压力可以通过液压系统或机械系统提供。
这个过程使得SMC材料填充整个模具腔室,并逐渐固化。
一旦SMC材料固化完全,模具被打开,最终产品被取出。
这个产品通常需要经过修整、清理等后续处理才能得到最终的成品。
SMC模压成型工艺有许多优点。
首先,它可以制造复杂形状的产品。
由于模具可以制造各种形状,因此SMC模压成型工艺可以制造出各种形状复杂的产品,满足不同的需求。
其次,SMC模压成型工艺可以提供高强度的产品。
由于使用了增强纤维,SMC材料具有较高的强度和刚度。
此外,SMC模压成型工艺还具有生产效率高、自动化程度高等优点。
综上所述,SMC模压成型工艺是一种常用的制造复杂形状和高强度工程塑料制品的工艺。
其工艺过程包括原料制备、将SMC材料放置于模具上、加热软化材料、施加压力固化材料,最终取出产品等步骤。
这一工艺具有许多优点,并且被广泛应用于各个领域。
SMC成型工艺分析报告

4.3.2 SMC的组分及其性能
SMC的组分及其性能
树脂糊
增强纤维
UP树脂
引发剂
交联剂
增稠剂
脱模剂
低收缩添加剂
无机填料
SMC
4.3.2 SMC的组分及其性能
1.不饱和聚脂树脂(Up树脂)
1、低粘度;便于浸渍GF。2、易同增稠剂反应;满足增稠的要求。3、可降低收缩性;4、固化迅速,提高生产效率;5、应具有较高的热强度和一定的韧性;在制品脱模时,不易损坏或开裂。
9、静夜四无邻,荒居旧业贫。。10、雨中黄叶树,灯下白头人。。11、以我独沈久,愧君相见频。。12、故人江海别,几度隔山川。。13、乍见翻疑梦,相悲各问年。。14、他乡生白发,旧国见青山。。15、比不了得就不比,得不到的就不要。。。16、行动出成果,工作出财富。。17、做前,能够环视四周;做时,你只能或者最好沿着以脚为起点的射线向前。。9、没有失败,只有暂时停止成功!。10、很多事情努力了未必有结果,但是不努力却什么改变也没有。。11、成功就是日复一日那一点点小小努力的积累。。12、世间成事,不求其绝对圆满,留一份不足,可得无限完美。。13、不知香积寺,数里入云峰。。14、意志坚强的人能把世界放在手中像泥块一样任意揉捏。15、楚塞三湘接,荆门九派通。。。16、少年十五二十时,步行夺得胡马骑。。17、空山新雨后,天气晚来秋。。9、杨柳散和风,青山澹吾虑。。10、阅读一切好书如同和过去最杰出的人谈话。11、越是没有本领的就越加自命不凡。12、越是无能的人,越喜欢挑剔别人的错儿。13、知人者智,自知者明。胜人者有力,自胜者强。14、意志坚强的人能把世界放在手中像泥块一样任意揉捏。15、最具挑战性的挑战莫过于提升自我。。16、业余生活要有意义,不要越轨。17、一个人即使已登上顶峰,也仍要自强不息。
SMC材料技术发展趋势及应用
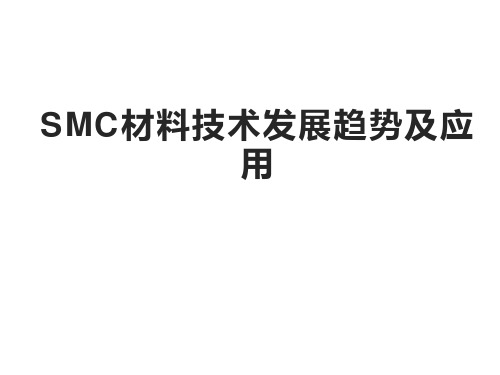
北京中材汽车复合材料有限公司
概要Contents
1 SMC工艺介绍
2 SMC技术发展趋势
3
SMC材料技术应用
工艺介绍
SMC=Sheet Molding Compound(片状模塑料)
图1.1
SMC机组照片
Page3
SMC模压成型
SMC模压成型图片
3、轻质高强
比强度和比模量是衡量材料承载能力的指标之一,SMC材料的比模量与钢材相当,但其比强度 可达到钢材的4倍。
4、抗疲劳性能好
SMC材料的拉伸强度略好于钢材,钢材及大多数金属材料的抗疲劳极限是其拉伸强度的40%-50%,
而SMC材料的抗疲劳极限普遍高于这一数值,最高的可达到70%-80%
Page5
Page19
3.2SMC在铁路车辆中的应用
1、 机车导流罩 2、 司机室 3、 外顶板 4、 上顶板和下层地板 5、 内墙板 6、 通过台 7、 卫生间 8、 外部门板 9、 设备保护外壳 10、 内板家具和 座椅
行李架
Page20
3.3SMC在电气中的应用
天线罩
电话亭
电线分配箱
Page21
3.4SMC在建筑领域的应用
2.2.2炭纤维SMC的特点 ➢ 高的强度 ➢ 高的刚度 ➢ 低密度 ➢ 良好的流动性及成型工艺性
2.2.3碳纤维SMC的应用
第一次批量应用碳纤维SMC的2003款Dodge Viper车
2.3模内涂层技术的发展及 应用
2.3.1模内涂层技术的发展
模内涂层(in-mold coating 即IMC)是在SMC模塑件固化 完成后,在脱模前向模内注入涂层材料并使其固化,以此填充表 面孔隙、针眼、凹痕、收缩痕,达到 A级表面。实现IMC的方法 有三种,下面简单介绍一下。
SMC的发展现状及成型工艺
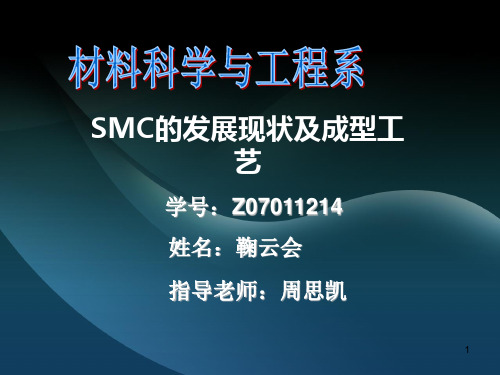
7
第二章 SMC的生产设备及工艺
• 2.1 片材的生产工艺:无捻粗纱经过切割器切割沉降,然后在成型机 中浸渍压实,通过压实后用收卷装置将其卷成卷,最后片状模塑料从
成型机卸下,经熟化成型后稳定存放;
• 2.2 制片机的类型大致有辊式和带式两种:辊式制片机靠卷绕张力对 辊筒产生的压力实现浸渍、脱泡;带式制片机则靠带槽滚筒对输送带
SMC的发展现状及成型工艺
学号:Z07011214 姓名:鞠云会 指导老师:周思凯
1
SMC的发展现状及成型工艺
• • • • • • 前言 第一章 SMC复合材料的基本组成 第二章 SMC的生产设备及工艺 第三章 SMC产品缺陷的改善措施 第四章 SMC的应用及回收 结论
2
简介
•
现代高科技的发展离不开复合材料,复合材料对现代 科学技术的发展,有着十分重要的作用。复合材料的研究 深度和应用广度,及其生产发展的速度和规模,已成为衡
量一个国家科学技术先进水平的重要标志之一。而片状模
塑料(SMC)是正是复合材料的皎皎者之一,本文分别介 绍了SMC的发展现状,组成原料,成型工艺,改善措施以 及应用和回收,希望通过此文大家能对SMC及其制品有一 个更深的了解。
3
SMC的发展史
• SMC在上世纪60年代开始出现,60年代末初具生产规模;
上的片材进行滚压来实现浸渍、脱泡;
• 2.3 模压成型工艺,包括压制前的准备,加料,成型,脱模,修整, 制品成型等;
8
第二章 SMC的生产设备及工艺
• 成型工艺参数对质量的影响:成型温度取决于树脂和固化剂类型,温
度太高或太低都会影响制品质量;成型压力,根据制品形状及SMC制
品特性选择合适压力及加压时机;保压时间即在成型压力和温度下的 保温保压时间,其作用是使制品消除内应力。 • 2.4模压成型设备:目前主要采用对模的压制成型法,成型设备主要 是压机和模具; • 2.5设备系统维修与维护。
SMC制造工艺
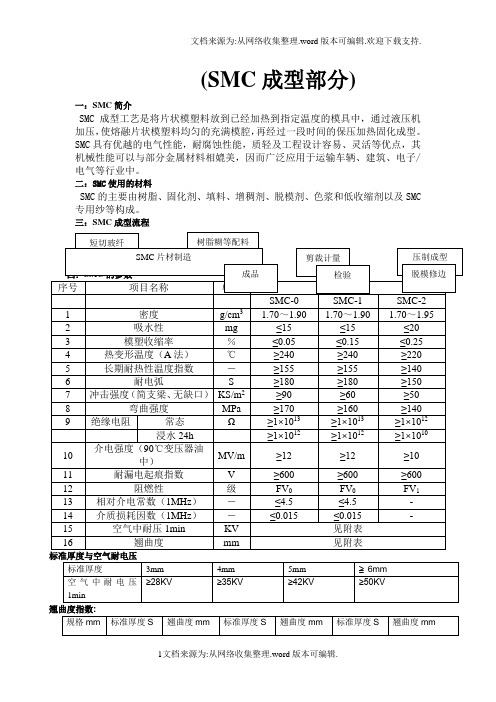
(SMC成型部分)
一:SMC简介
SMC成型工艺是将片状模塑料放到已经加热到指定温度的模具中,通过液压机加压,使熔融片状模塑料均匀的充满模腔,再经过一段时间的保压加热固化成型。
SMC具有优越的电气性能,耐腐蚀性能,质轻及工程设计容易、灵活等优点,其机械性能可以与部分金属材料相媲美,因而广泛应用于运输车辆、建筑、电子/电气等行业中。
二:SMC使用的材料
SMC的主要由树脂、固化剂、填料、增稠剂、脱模剂、色浆和低收缩剂以及SMC 专用纱等构成。
三:SMC成型流程
离型不良,脱模不良
裂痕(Crack)
光泽不良,光泽不均匀。
SMC成型工艺
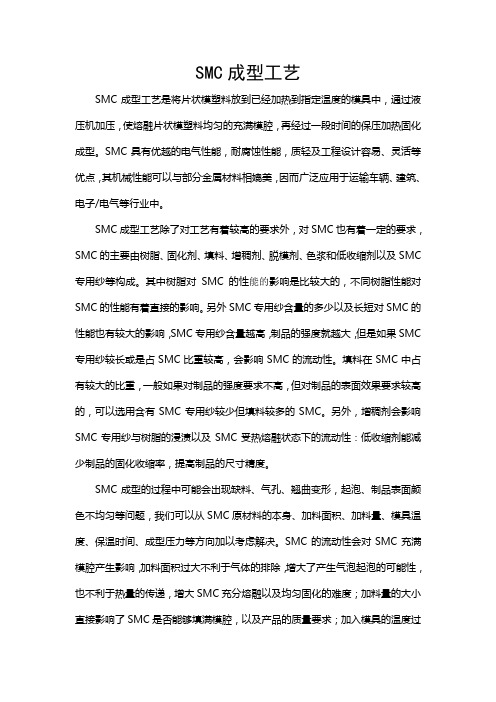
SMC成型工艺SMC成型工艺是将片状模塑料放到已经加热到指定温度的模具中,通过液压机加压,使熔融片状模塑料均匀的充满模腔,再经过一段时间的保压加热固化成型。
SMC具有优越的电气性能,耐腐蚀性能,质轻及工程设计容易、灵活等优点,其机械性能可以与部分金属材料相媲美,因而广泛应用于运输车辆、建筑、电子/电气等行业中。
SMC成型工艺除了对工艺有着较高的要求外,对SMC也有着一定的要求,SMC的主要由树脂、固化剂、填料、增稠剂、脱模剂、色浆和低收缩剂以及SMC 专用纱等构成。
其中树脂对SMC的性能的影响是比较大的,不同树脂性能对SMC的性能有着直接的影响。
另外SMC专用纱含量的多少以及长短对SMC的性能也有较大的影响,SMC专用纱含量越高,制品的强度就越大,但是如果SMC 专用纱较长或是占SMC比重较高,会影响SMC的流动性。
填料在SMC中占有较大的比重,一般如果对制品的强度要求不高,但对制品的表面效果要求较高的,可以选用含有SMC专用纱较少但填料较多的SMC。
另外,增稠剂会影响SMC专用纱与树脂的浸渍以及SMC受热熔融状态下的流动性:低收缩剂能减少制品的固化收缩率,提高制品的尺寸精度。
SMC成型的过程中可能会出现缺料、气孔、翘曲变形,起泡、制品表面颜色不均匀等问题,我们可以从SMC原材料的本身、加料面积、加料量、模具温度、保温时间、成型压力等方向加以考虑解决。
SMC的流动性会对SMC充满模腔产生影响,加料面积过大不利于气体的排除,增大了产生气泡起泡的可能性,也不利于热量的传递,增大SMC充分熔融以及均匀固化的难度;加料量的大小直接影响了SMC是否能够填满模腔,以及产品的质量要求;加入模具的温度过高,加压过快,会使SMC表面快速固化,不利于热量的传递,中间部位不能充分熔融,使SMC不能够充满模腔,并且由于表面固化太快,SMC中裹有的气体不易排出,那么容易在制品表面形成气孔和起泡;保温时间过短不利于制品的充分固化;成型压力过小,不利于增加制品的密实性以及降低制品的收缩率,从而可能会制品翘曲变形。
SMC的发展现状及成型工艺

S M C的发展现状及成型工艺(总64页)--本页仅作为文档封面,使用时请直接删除即可----内页可以根据需求调整合适字体及大小--SMC的发展现状及成型工艺摘要模压料的选取在一定程度上决定了片状模塑料(SMC)制品的质量,选择适当的原料能满足制品的特殊性能要求,而且成型工艺也是制造模压制件的重中之重。
本文首先介绍了SMC的原料组成,其中包括树脂,引发剂,低收缩添加剂,化学增稠剂,内脱模剂,着色剂以及增强材料,对于各组分的性能要求也作了简单介绍;其次分层论述了SMC的成型工艺,包括制片机组的类型和结构,SMC的生产工艺,SMC模压成型设备及工艺,而对于SMC制品存在的问题本文借鉴了几种国外改善措施,包括表面漆泡,溶剂吸入,密度大,污染环境及汽车零部件生产线的完善等等;最后对于SMC的工业应用及回收利用作了简单论述。
希望大家能通过此文对SMC复合材料有一个新的认识。
关键词:SMC,树脂,玻璃纤维,模压成型,汽车部件SMC Moulded Situation And The Development ProcessABSTRACTMolding material selection to a certain extent, determine the sheet molding compound (SMC) product quality, select the appropriate raw materials to meet the performance requirements of special products, and the molding process is the priority of mould article first describes the SMC feedstock composition, including resin, initiators, LPA, chemical thickeners, releasing agent, stains, and enhanced materials, for each component of performance requirements had also made a simple introduction; Secondly tiered discusses the SMC molding process, including the production unit of the type and structure of the production process of SMC, SMC molding equipment and technology, as for SMC problems this article draws on several foreign improvement measures, including the surface paint on the bubble, solvent inhalation, density, pollution of the environment and the improvement of the production line of automotive components, etc.; finally for industrial applications and recycling of SMC briefly discussed. I hope you can pass this article on the SMC composites have a new understanding.KEY WORDS: SMC , resin, glass fiber, moulding, auto parts目录前言 0第1章SMC复合材料的基本组成 (2)树脂 (2)引发剂 (4)填料 (5)低收缩添加剂 (6)化学增稠剂 (7)内脱模剂 (9)着色剂 (10)增强材料 (10)第2章 SMC的生产设备及工艺 (11)概述 (11)制片机组的类型和结构 (12)类型 (12)制片机组结构 (13)SMC的生产工艺 (13)SMC模压成型设备与工艺 (13)成型工艺对SMC 表面质量的影响 (14)SMC模压成型设备 (16)设备系统性维护与维修 (17)举例: (18)第3章 SMC产品缺陷的改善措施 (19)增韧型UP克服漆泡 (19)减少溶剂吸入 (20)改性树脂作低轮廓添加剂 (20)免喷涂 SMC (20)低密度 SMC (20)环境友好 SMC (21)成型监控仪器 (21)成型生产线的发展方向 (21)第4章 SMC的应用及回收 (22)在汽车工业中的应用 (22)SMC的回收 (23)SMC的回收方法 (23)SMC回收材料的再利用 (24)结论 (24)谢辞 (26)参考文献 (27)外文资料翻译 (29)前言SMC在上世纪60年代初开始出现,60年代末在世界市场上初具生产规模。
- 1、下载文档前请自行甄别文档内容的完整性,平台不提供额外的编辑、内容补充、找答案等附加服务。
- 2、"仅部分预览"的文档,不可在线预览部分如存在完整性等问题,可反馈申请退款(可完整预览的文档不适用该条件!)。
- 3、如文档侵犯您的权益,请联系客服反馈,我们会尽快为您处理(人工客服工作时间:9:00-18:30)。
SMC的发展及其成型工艺研究
发表时间:2019-08-08T16:07:02.517Z 来源:《知识-力量》2019年9月36期作者:陈厚锟郑小涛
[导读] 介绍了SMC片材的发展过程以及广泛的应用前景,吸引了大批高技术人才对热固性树脂固化工艺的研究,其中最主要的成型工艺有:手糊成型工艺,模压成型工艺,喷射成型工艺,缠绕成型工艺以及热压罐成型工艺;本文主要对模压成型工艺进行了研究,分别阐述了模压温度,模压时间和保温保压的时间在
(武汉工程大学机电工程学院,湖北 武汉 430200)
摘要:介绍了SMC片材的发展过程以及广泛的应用前景,吸引了大批高技术人才对热固性树脂固化工艺的研究,其中最主要的成型工艺有:手糊成型工艺,模压成型工艺,喷射成型工艺,缠绕成型工艺以及热压罐成型工艺;本文主要对模压成型工艺进行了研究,分别阐述了模压温度,模压时间和保温保压的时间在模压成型过程中的影响以及如何加以优化控制才能得到理想的成型制品。
关键词:SMC片材,模压工艺,模压温度,模压时间,保温保压时间
SMC是片状模塑料的简称,是由加有低收缩剂、填料、添加剂等组分的树脂混合料浸渍增加材料后加工而成的片状或板状热固性模塑材料。
通常采用在模具内热压的方法使之固化,很容易加工成FRP制品。
自60年代中期,西德拜耳公司在世界上率先推出不饱和聚酯基SMC,利用树脂中含有羧基与氧化镁反应,树脂会变成无粘附性的固体,且在热压条件下容易流动。
而用热塑性树脂降低不饱和聚醋树脂收缩性的技术恰好问世,利用这一技术,SMC成为生产率、强度特性、耐热性、表面性能优良的模压材料,迅速进入运输车辆、建筑、电子/电气各个应用领域,并以每年%20--%25的增长率快速增长。
目前世界SMC产量涨到全部玻璃钢总产量的%40--%50。
我国是在七十年代开始研究SMC树脂糊、SMC生产与模压工艺,1976年研制成功了第一条SMC机组。
SMC主要产品有水箱板、风扇、座椅、电器配件、防爆型灯罩、冷冻鱼盘、拖拉机顶棚,以及汽车的备轮仓等许多制品。
现在,在山东德州市及其周边的地区已形成了一些资产上千万的民营玻璃钢企业,对我国的SMC产业贡献巨大,已名副其实地成为中国FRP之乡。
2004年SMC产值达到2亿元左右。
但在新技术方面尚未取得很大进展,如汽车配件方面,还以小、散、结构简单为主。
国外的复合材料产业开始的比较早,发展的也比较快。
这里处于领先优势主要是日本和美国,玻璃钢复合材料的日新月异的发展,降低汽车产业的成本,提高了生产效率,反过来也促使玻璃钢被广泛的运用。
1.复合材料成型方法
由于复合材料的迅猛发展以及广阔的应用前景,使得复合材料的成型工艺也越来越趋于成熟,几种熟知的成型工艺方法包括:手糊成型工艺,模压成型工艺,喷射成型工艺,缠绕成型工艺以及热压罐成型工艺。
手糊(也叫裱糊、层贴)成型是以手工业为主成型复合材料制件的方法,其特点是操作简单,易会;生产成本低;能生产大型及复杂的制品;设计性能好且易改变,材料广;结构能制成夹层。
缺点是产品质量与工作人员的技术有关,成型周期长;喷射成型是通过喷枪将短切纤维和雾化树脂同时喷射到开模表面,经辊压、固化制取复合材料制件的方法;喷射成型一般将分装在两个罐中的混有引发剂的树脂和促进剂的树脂,由液压泵或压缩空气按比例输送从喷枪两侧(或在喷枪内混合)雾化喷出,同时将玻璃纤维无捻粗纱用切割机切断并由喷枪中心喷出,与树脂一起均匀沉积到模具上。
待沉积到一定厚度,用手辊滚压,使纤维浸透树脂、压实并除去气泡,再继续喷射,直至完成坯件制作,最后固化成型。
其特点是成本低;半机械操作,比手糊成型效率高;制品整体效果好;损耗低。
缺点是制品强度差;污染大;固化不均匀;有气泡;热压罐成型是借助成型袋与模具之间抽真空形成的负压或袋外施加压力,使复合材料坯料紧贴模具,从而固化成型的方法。
其特点是仅用一个模具就可以得到形状复杂,尺寸较大、质量较好的制件,也能制造夹层结构件,缺点是花费大、结构不简单;缠绕成型是将浸过树脂胶液的连续纤维或布带,按照一定规律缠绕到芯模上,然后固化脱模成为增强制品的工艺过程;其特点是生产效率高而成本低,产品准确度高且质量稳定,生产是自动化生产;缺点是投资大且技术要求严,适应性低,表面有凹陷的制品不能缠绕;模压成型是将裁好的片材放在一定温度的模具中,在一定的压力下成型的过程。
其特点是效率高;成品美观、尺寸准确重复性好;价格低、易用机械化和自动化;可一次成型;缺点是成本高;只适合中小型制品。
2.模压成型工艺
由上文介绍可知,模压成型的工艺是热固性树脂在一定的温度和压力下固化成型,所以模压制品是否能够很好的成型以及成型制品的质量在很大程度上受到模压温度,模压压力和保温保压时间的影响。
2.1模压温度
模压成型过程中预浸料的流动,充模,固化反应速度都与温度有着密切关系,而且温度在模压成型过程中起着十分重要的作用,它影响着树脂基体的交联程度和复合材料制品的最终性能。
温度使复合材料的粘度和流动性都发生了较大的变化,使聚合物松弛,即粘度降低,流动性增加;同样也会使复合材料发生交联反应,即粘度增加,流动性增加。
反应刚开始时,温度升高使预浸料逐渐熔融,粘度由大减小,随着反应的继续进行,复合材料发生交联反应,此时,粘度开始增加,流动性降低。
随着工装模具温度逐渐传至预浸料,预浸料的温度不断升高,交联反应的速度也会增大。
实践表明,升高模温可以加速固化温度,缩短固化时间,但过高温度会使预浸料由于固化速度太快使其流动性迅速降低而引起充模不满,特别是大型薄壁,形状复杂的复合材料制品,温度过高时,制品外层固化比内层固化快的多,致使内层挥发物难以排除,从而使制品物理和力学性能降低,还会使制品产生缺隙和变形。
当固化温度过低时,固化温度慢,会出现固化度低等现象。
结论1:模压温度根据成型制品的复杂程度和质量大小,不可设计的过高或者过低。
2.2模压压力
模压压力可以加速预浸料在模腔内的流动,增加密度,克服树脂基体缩聚反应时放出的低分子物产生的压力,避免出现肿胀,脱层等现象,同时模压压力也可使工装模具闭合,制品具有固定尺寸和防止冷却时发生变形等作用。
模压压力可用理论公式计算,模压压力的大小取决于预浸料的种类,制品形状及预浸料的状态。
假设预浸料的流动性越小,固化速度越快以及压缩率越大,则所需的模压压力也越大。
反之,所需的模压压力也就越小。
在模压制品成型过程中,温度和压力是相互关联的,提高模具温度,可增加预浸料的流动性。
如在模压开始到流动性最大这段时间降低成型压力也可以增加预浸料的流动性。
2.3模压时间
模压时间是固化过程所需要的时间,指预浸料放入工装模具中开始升温,加压至完全固化的这段时间。
模压时间与预浸料的类型,挥发物含量,制品形状,厚度,工装模具结构,模压温度,压力等因素有关。
模压时间的长短对制品性能影响甚大,模压时间太短,固化不完全,制品物理和力学性能低,表面粗糙度差,制品易出现变形,模压时间增加可降低制品收缩率和变形,但应注意模压时间过长,树脂交联过度,制品内应力会增加,因此应选择适当的模压时间。
3.结论
(1)市场上SMC片材的发展应用仍呈上升趋势,而我国生产高质量片材的能力与发达国家仍有很大的差距;
(2)各种成型工艺优缺点是并存的,选择适当的成型工艺更有利于得到理想的成型制品,实现经济效益的最大化;
(3)在不损害制品强度和性能指标的前提下,应适当提高模压温度和模压压力,过低会使交联反应难以充分进行,从而使制品强度不高,外观无光泽,适当的保温时间有利于制品成型且节约能耗。
参考文献
1]陈元芳,李小平,宫敬禹.SMC模压成型工艺参数对成型质量的影响[J].工程塑料应用,2009,37(04):39-41.
2]付恒,陈玉廷.SMC的现状与发展[J].纤维复合材料,2005(03):58-60.。