第三章先进制造工艺技术(激光加工)课件
先进制造工艺技术.pptx

23
25
熔模铸造的应用:
• 熔模铸造是一种实现少无切削加工的、先进的精密成形 工艺,它最适用于25kg以下的高熔点、难以切削加工的 合金铸件的成批、大量生产。
• 目前主要用于航天飞行器、飞机、汽轮机、泵、汽车、 拖拉机和机床上的小型精密铸件和复杂刀具的生产。
压力铸造
26
2、压力铸造
2.1概念
适用。
20
熔模铸造的缺点:
⑴ 工序复杂,生产周期长。 ⑵ 原材料价格高,铸件成本高。 ⑶ 铸件不能太大、太长,否则蜡模易变形,丧失原有精
度。
21
4-6 离心铸造
离心铸造是将金属液浇入高速旋转 (250~1500r/min)的铸型中,并在 离心力作用下充型和凝固的铸造方法。 其铸型可以是金属型,也可以是砂型。 既适合制造中空铸件,也能用来生产 成形铸件。
Process
3.1 先进成形技术
Advanced Forminging
Technology
9
特种铸造
特种铸造
10
4-3 压力铸造
压力铸造是在专用设备—压铸 机上进行的一种铸造。即在高速、 高压下将熔融的金属液压入金属 铸型,使它在压力下凝固获得铸 件的方法。
12
压铸工艺过程
13
压力铸造的特点及应用
——成形工艺 去除成形 受迫成形 堆积成形 生成成形
6
3.1.1 概述
◆先进制造工艺技术的内容
➢精密、超精密加工技术。它是指对工件表面材料进行去 除,使工件的尺寸、表面性能达到产品要求所采取的技 术措施。当前,纳米(nm)加工技术代表了制造技术的最 高精度水平。超精加工材料由金属扩大到非金属。根据 加工的尺寸精度和表面粗糙度,可大致分为三个不同的 档次,如表3-1所示。
先进制造技术教学课件PPT先进制造工艺技术.ppt
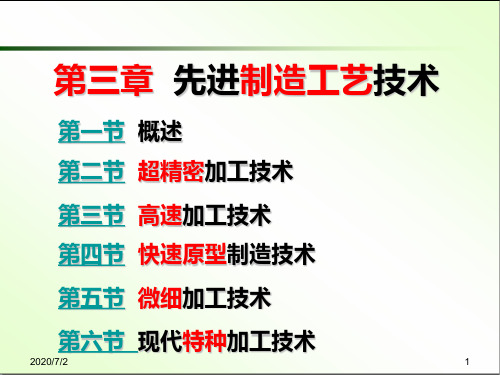
19子线分析
手段:优化加工方法;开发和研制新型刀具材料;研
制超精密机床;对加工精度进行监控。
2020/7/2
7
21世纪的超精密加工将向分子级、原子级精度推进
2020/7/2
8
(2)切削加工速度迅速提高
刀具材料发展。
2020/7/2
9
20世纪前,碳素钢,耐热温度低于200ºC,切削速度不超 过10m/min;
、电火花、激光切割;
• 堆积成形 将材料有序地合并 堆积成形,如快速原形制造、焊 接等。
2020/7/2
6
二、先进制造工艺的产生和发展
先进制造工艺是在传统的机械制造工艺基础上发展来的, 优化后的工艺和新型加工方法。是核心和基础。
(1)制造加工精度不断提高
18世纪,其加工精度为1mm; 19世纪末,0.05mm; 20世纪初,μm级过渡; 20世纪50年代末,实现了μm级的加工精度; 目前达到10nm的精度水平。
1900
2020/7/2
普通加工
加工设备 车床,铣床
精密车床 磨床
测量仪器 卡尺
百分尺 比较仪
精密加工
坐标镗床 坐标磨床
气动测微仪 光学比较仪
金刚石车床 光学磁尺
精密磨床
电子比较仪
超精密加工
超精密磨床 激光测长仪 精密研磨机 圆度仪轮廓仪
超高精密磨床 激光高精度 超精密研磨机 测长仪
1920 1940
代 码
名称
0
1
2
3
4
5
6
7 89
中类名称
0 铸造
砂型铸造 特种铸造
1 压力加工
锻造
轧制
冲压 挤压 旋压 拉拔
第三章 先进制造工艺技术

徐州工程学院教案徐州工程学院教案纸、金刚石刀具超精切削刀具材料:天然金刚石,人造单晶金刚石金刚石的晶体结构:规整的单晶金刚石晶体有八面体、十二面体和六面体,有三根4次对称轴,四根3次对称轴和六根2次对称轴。
图 3-5 砂带磨削示意图图3-6 几种砂带磨削方式砂带磨削特点:1)砂带与工件柔性接触,磨粒载荷小,且均匀,工件受力、热作用小,加工质量好( R a值可达 0.02μm)。
2)静电植砂,磨粒有方向性,尖端向上,摩擦生热小,磨屑不易堵塞砂轮,磨削性能好。
2. 产品设计中的应用——快速产品开发(RPD)第四节微细加工技术二、微细机械加工1、主要采用铣、钻和车三种形式,可加工平面、内腔、孔和外圆表面。
2、刀具:多用单晶金刚石车刀、铣刀(图3-20)。
铣刀的回转半径(可小到5μm)靠刀尖相对于回转轴线的偏移来得到。
当刀具回转时,刀具的切削刃形成一个圆锥形的切削面。
3、微细机械加工设备微小位移机构,微量移动应可小至几十个纳米。
图 3-11 FANUC型微型超精密加工机床三、微细电加工、线放电磨削法(WEDG)电极线沿着导丝器中的槽以5~10mm/min的低速滑动,可加工圆柱形(图3-12)。
如导丝器通过数字控制作相应的运动,还可加工出各种形图3-12 WEDG工作原理图3-14 电致伸缩微动工作台第五节现代特种加工技术图3-15 激光加工原理图、激光加工特点图 3-16 超声波加工原理图、超声波加工特点及应用适用于加工各种脆性金属材料和非金属材料,如玻璃、陶瓷、半导体、宝石、金刚石等。
可加工各种复杂形状的型孔、型腔、形面。
工具与工件不需作复杂的相对运动,机床结构简单。
被加工表面无残余应力,无破坏层,加工精度较高,尺寸精度可0.05mm 。
加工过程受力小,热影响小,可加工薄壁、薄片等易变形零件。
图3-17水射流加工装置示意图水射流切割加工的应用和发展水射流切割具有切口平整、无毛边、无火花、加工清洁等特点,已用于汽。
先进制造技术特种加工系列激光加工课件PPT
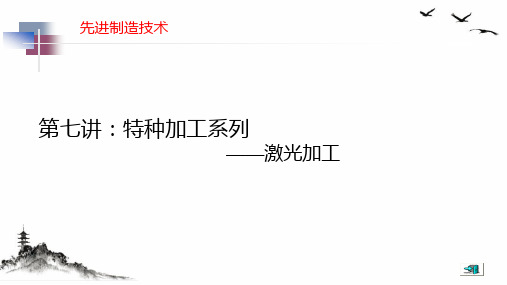
二.激光加工过程
激光加工阶段—工件材料的加热
2) 工件材料的加热 光能转换成热能的过程就是工件材料的加热。激光束在很薄
(0.01-0.1um)的金属表层内被吸收,使金属中自由电子的热运动能 增加,并在与晶格碰撞中的极短时间内(10(^-11)-10(^-10)s)将电子 的能量转化为晶格的热振动能,引起工件材料温度的升高,同时 按热传导规律向周围或内部传播,改变工件构料表面或内部各加 热点的温度。
Laser(Light Amplification by Stimulated Emission of Radiation )
一.激光加工(LBM)的原理和特点
1. 激光产生的原理
(1)光的物理概念及原子的发光过程 光是一种人类眼睛可以见的电磁波(可见光谱)。在科学上的定义,光有时候是指所有的电磁波谱
一.激光加工原理 3.激光加工的基本原理
固体激光器加工简图 1-全反射镜 2-激光工作物质 3-激励能源 4-部分反射镜 5-透镜 6-工件
一.激光加工原理
全反射镜
工作物质
光泵
电容
触发电路
高压充电源
部分反射镜
激光束
激光束
镀金反射镜 透镜 工件
二.激光加工过程
激光加工阶段
可以认为,激光加工是以激光为热源对工件材料进行热加工。其加工过程大体分为如下几个阶段:
5)能以简单的措施实现光束偏转,更适用于复杂零件焊接 光斑大小与聚焦透镜的焦距成正比。
二.激光加工过程
激光加工阶段—光能吸收及转化
1)光能的吸收及其能量转化 激光束加上是—个高速熔化、气化的过程,光能传至工件表
面时,工件材料吸收光能有—个开始瞬态过程:开始时,即使工 件表面很粗糙,反射光也都是较高的(尤其是金属材料);当工件 表面材料的温度逐渐上升,高温下表面被氧化或成熔融状态之后, 反射率便逐渐降低.吸收率迅速增加,激光的功率密度愈高,这 一过程作用时间就愈短。此间,光能转换为热能。
先进制造技术5激光加工.ppt

(3)掺钕钇铝石榴石(YAG)激光器 工作介质为 掺有1.5%左右钕的钇铝石榴石晶体,发射 λ=1.06μm的红外激光。
二、激光加工常用激光器
(二)气体激光器
一般采用电激励,效率高、寿命长、连续输出功率大, 广泛用于切割、焊接、热处理等加工。常用于材料加工 的气体激光器有二氧化碳激光器、氩离子激光器等:
一、激光打孔
3. 焦点位置
一、激光打孔
4. 光斑内的能量分布
一、激光打孔
5. 激光的照射次数
一、激光打孔
6. 工件材料
二、激光切割
原理
激光切割的原理和激光打孔原理基本相同。所不同的是, 工件与激光束要相对移动。
激光器
采用重复频率较高的脉冲激光器或连续输出的激光器。
但连续输出的激光束会因热传导而使切割效率降低,同 时热影响层也较深。因此,在精密机械加工中,一般都 采用高重复频率的脉冲激光器。
五、激光热处理
激光热处理与火焰淬火,感应淬火等成熟工艺相比具有以 下优点: (1)加热快、热影响小、工件变形小; (2)可以对形状复杂的零件或局部处理,如盲孔底等; (3)因加热点小,散热快,形成自淬火,不需冷却介 质。不仅节省能源,并且工作环境清洁。
缺点 硬化层浅,一般小于1mm,只是一种表面处理方法。
100至1000W
打孔、焊接
打孔、切割、 焊接、微调
脉冲 连续
几J
几十至几千 W
切割、焊接、 热处理、微调
光盘录刻存贮
二、激光加工常用激光器
(一)固体激光器
组成
二、激光加工常用激光器
二、激光加工常用激光器
先进制造技术激光加工技术ppt

激光加工技术在先进制造中的发展前景
01
精密制造与超精密制造
随着制造业的不断升级,精密制造与超精密制造已成为发展的重要趋
势。激光加工技术能够实现高精度、高质量的制造,如光学元件、半
导体芯片等精密器件的制造,具有广泛的应用前景。
02
柔性制造与个性化定制
随着消费者需求的多样化,柔性制造与个性化定制已成为制造业的重
技术要求高
激光加工技术的操作需要专业的技术人员,对技术人员的技能 要求较高。
加工材料有限
激光加工技术适用于金属、塑料等材料,对于一些特殊材料, 如玻璃、陶瓷等则较难实现加工。
如何克服激光加工技术的局限性
加强技术研发
通过加强技术研发,不断优化激光加工技术的设备及工 艺,降低成本,提高效率。
加强技术培训
激光加工技术的特点
高能量密度、高精度、低热影响区、加工速度快、可加工材 料范围广、加工质量好等。
激光加工技术的发展历程
第一阶段
第二阶段
20世纪60年代,激光器的诞生,标志着激 光加工技术的开始。
20世纪70年代,激光加工技术开始进入工 业应用,出现了激光切割、焊接、表面处理 等技术。
第三阶段
第四阶段
先进制造技术激光加工技术ppt
xx年xx月xx日
目录
• 激光加工技术概述 • 激光加工技术在先进制造中的应用 • 激光加工技术的工艺及设备 • 激光加工技术的优势及局限性 • 激光加工技术在先进制造中的发展趋势和前景 • 案例分析
01
激光加工技术概述
激光加工技术的定义与特点
激光加工技术的定义
激光加工技术是一种利用高能激光束照射在材料表面,实现 材料熔化、汽化、冲击等过程,从而对材料进行切割、焊接 、表面处理、打孔等加工的技术。
先进激光加工技术(上)ppt课件

20
交通领域中的应用
最新版整理ppt
21
(汽车制造)
最新版整理ppt
22
Audi A2 焊接
Laser welds
最新版整理ppt
23
汽车焊接件
最新版整理ppt
24
(航空领域)
1. 激光焊接
高强铝合金激光焊接已应用于空客A380,机身减重18%,成本下 降21.4%-24.3%
2. 激光分离
内容
1. 引言 2. 工业用激光器 3. 激光加工基本物理过程 4. 激光加工典型应用
在宏观制造领域中的应用 微细加工领域的应用 激光增材制造技术(3D打印技术)
最新版整理ppt
1
一、引 言
• 1960年世界上第一台激光器诞生,随后各种激光器层出不 穷,如气体、液体、固体、化学、准分子、半导体激光器 和光纤激光器等。
• 功率密度对靶材的影响:
103~104 W/cm2,加热
104~106 W/cm2,熔融
106~108 W/cm2,气化
靶
108~1010 W/cm2,等离子体
烧蚀蒸汽
激光束
激光加工:热加工,冷加工
最新版整理ppt
5
相互作用机理研究尚待深入
• 激光与材料的相互作用过程十分复杂:靶材的多 样化,作用激光参数的多样化,作用条件的多样 化。
( 1 R ) P s t od 0 [ c s ( T v T 0 ) ( L n L v )]
1. 激光功率密度越高,所需气化时间越短。
2. 气化时间比熔化时间高出一个数量级,主要原因是 沸点比熔点高很多,且气化潜热比熔融潜热大一个 数量级。
最新版整理ppt
15
举例:铝材料
先进制造技术基础 第3章 先进制造工艺技术.ppt

造
技
术
基
础
第3章 先进制造工艺技术
3.超精密加工技术的国内外发展现状
日本著名学者谷口纪男教授在所著《纳米技术的应
用和基础——超精密、超微细加工和能束加工》一书中,
从综合加工精度出发,将加工的发展分为普通加工、精
先 进
密加工、高精密加工和超精密加工四个阶段,并预计在 制
2000年加工精度可达到纳米级。超精密加工提出以后, 造
发展趋势;
先
掌握先进制造工艺技术中超高速加工技术、超精密加工 技术、特种加工技术、快速原型制造技术以及微细加工 技术的基本概念、关键支撑技术及发展应用 ;
进 制
造
通过实例分析了解这些先进技术手段在日常生活以及现 技
代机械产品中的实际应用。
术
通过本章的学习,使学生获得先进制造工艺技术的基本 基
础
第3章 先进制造工艺技术
先
进
制
造
技
术
基 7075铝合金零件(毛坯1818kg 零件14.5kg 2388*2235*82.6)
主轴18000r/min,进给2.4~2.7m/min 刀具直径18~20mm
础
第3章 先进制造工艺技术
(2)汽车、摩托车工业领域 (3)模具工具工业领域
※刀具 PCD CBN 金属陶瓷 ※可切削硬度60HRC或更高的材料
立柱与底座合为一个整体,使机床整体刚性得以提高;
二:使用高阻尼特性材料,如聚合物混凝土。
日本牧野高速机床的主轴油温与机床床身的温度 通过传感控制保持一致,协调了主轴与床身的热变形。
先
进
3.超高速切削机理
制
4.超高速切削工艺
造
※工艺特点
先进制造工艺技术..ppt课件
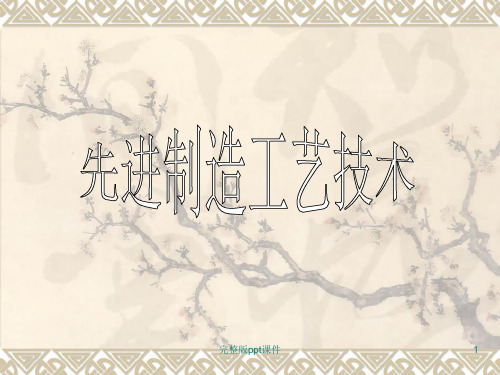
完整版ppt课件
30
刀具切削刃比较
立方氮化硼烧结体(CBN)
金刚石粉烧结体
单晶金刚石
完整版ppt课件
31
单晶金刚石刀具
Ø 金刚石的晶体结构和刃磨
立方体
八面体
十二面体
多晶金刚石研磨后的刀刃
完整版ppt课件
HRR2
f2 4
1/2
f2 8R
n 切削刃口的复映性 n 毛刺与加工变质层
Hcotcotf
完整版ppt课件
26
金刚石切削刀具
超精密切削刀具应具备的条件:
Ø 刀具刃口的锋利性好。刃口半径值极小,能实现超薄切削
厚度。
Ø 切削刃的粗糙度低。切削时刃形将复制在被加工表面上,
从而得到超光滑的镜面。
Ø 刀具与被切削材料的亲和性低。以得到极好的加工表面完
完整版ppt课件
12
2) 技术要求
❖ 超微量切削特征 ❖ 刀尖附近的极小局部区域能承受高温高压 ❖ 实现超薄切削 ❖ 刀刃平直 ❖ 工件材料的抗粘性好,化学亲和力好,摩擦
系数小
完整版ppt课件
13
3)加工机床
目前的超精密加工机床一般采用高精度空气静压轴承 支撑主轴系统;空气静压导轨支撑进给系统的结构模式。
完整版ppt课件
37
金刚石切削机床
要求高精度、高刚度、良好稳定性、抗振性及数控功能等
型号(生产厂家)
径向跳动(μm)
主轴
轴向跳动(μm) 径向刚度(N/μm) 轴向刚度(N/μm)
Z向(主轴)直线度
导轨
X向(刀架)直线度 X、Z向垂直度(")
先进制造工艺技术
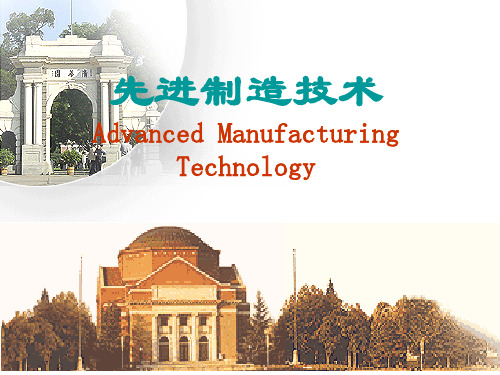
4
第一节 概 述
一、机械制造工艺的定义和内涵
机械制造工艺: 将各种原材料通过改变其形状、尺寸、性能或相 对位置,使之成为产品或半成品的方法和过程。
2020/6/24
5
粉末冶金
铸造 金 属 锻压 材 料 焊接
毛 坯
热 处 理
切 削 零 装机 加 件 配器
工
➢ 毛坯和零件成形——铸造、锻压、冲压、焊接 、压制、烧结、注塑、压
2020/6/24
16
第二节 精密洁净铸造工艺
本节要点
1.定义 2.近代化学硬化砂铸造工艺 3.高效金属型铸造工艺及设备 •压力铸造 •挤压铸造 •消失模铸造
2020/6/24
17
2020/6/24
18
2020/6/24
19
2020/6/24
20
精密、洁净、高效
2020/6/24
21
2020/6/24
2020/6/24
78
常用精密加工和超精密加工方法
分类
刀具切 切 削加工 削
加工方法 精密、超精密车削 精密、超精密铣削
精密、超精密镗削
加工刀具
精度 /μm
天然单晶金刚石刀具、人 造聚晶金刚石刀具、立方 氮化硼刀具、陶瓷刀具、 硬质合金刀具
1~0.1
微孔钻削
硬质合金钻头,高速钢钻 头
20~10
磨 削
磨料加
工
研
磨
精密、超精密砂轮 磨削 精密、超精密砂带 磨
精密、超精密研磨
油石研磨 磁性研磨 滚动研磨
砂
氧化铝、碳化硅、 轮
立方氮化硼、金刚
石等磨料
砂
带
5~0.5
铸铁、硬木、塑料等研具,
先进制造技术(PPT 78页)
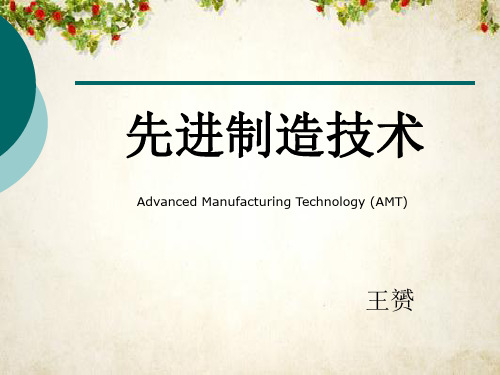
AMT特征
传统制造技术
仅驾驭生产过程 系统性 物质流和能量流
先进制造技术
能驾驭生产过程 物质流、信息流和能量流
仅指将原材料变为 贯穿从产品设计、加工制造到产品销售 广泛性 成品的加工工艺 的整个过程
集成性 动态性
学科专业单一、独 立,相互间界限分 明
尤里卡计划(EREKA):1988年用5亿美元资助16个欧洲
国家、600家公司的165个合作性高科技研究开发项目。
信息技术研究发展战略计划(ESPRIT):在13个成员
国向5500名研究人员提供了资助,明确设计原理、工厂自动化、 生产过程管理三大课题。
欧洲工业技术基础研究计划(BRITE):重点资助材
1.社会经济发展背景
(1)消费需求:主题化、个性化和多样化,产品寿命周期缩短。
(2)全球性产业结构调整:制造商之间既有激烈竞争,又有基 于实力的合作。
(3)快速响应市场:满足已有和潜在顾客需求,主动适应市场, 引导市场,是赢得竞争,获取最大利润的关键。
先进制造技术产生的背景
2.科学技术发展背景
(1)制造技术在向宏观(制造系统)和微观(超精密加工)两 个方向发展
5.系统性
随着微电子、信息技术的引入,先进制造技术能驾驭信息生成、 采集、传递、反馈、调整的信息流动过程。先进制造技术是可以 驾驭生产过程的物质流、能量流和信息流的系统工程。
6.动态性
不断地吸收各种高新技术成果,将其渗透到企业生产的所有领域 和产品寿命循环的全过程,实现优质、高效、低耗、清洁、灵活 的生产。
先进制造技术的体系结构及分类
先进制造技术的体系结构
激光加工技术PPT课件
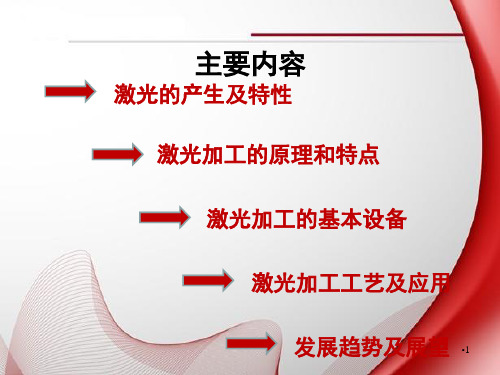
•38
•39
用激光照射一次,加工的深度大约是孔径的5倍, 但锥度较大。 如果用激光多次照射,其深度可以增加,锥度可 以较小,而孔径几乎不变。但是,孔的深度并不 是与照射次数成正比,而是加工到一定深度后, 由于孔内壁的反射、透射以及激光的散射,使孔 的前段能量密度不断减小,以致不能继续打下去。
•40
主要内容
激光的产生及特性 激光加工的原理和特点
激光加工的基本设备 激光加工工艺及应用 发展趋势及展望 •1
激光加工技术
自然界存在着自发辐射和受激辐射两种不同的发光 方式,前者发出的光是随处可见的普通光,后者发出的 光便是激光。 激光如果通过透镜将其聚焦成直径为几十微米到几微 米的极小光斑,使能获得极高的能量密(108——1010W /cm2)。当激光照射在工件表面时,光能被工件吸收并 迅速转化为热能,光斑区的温度可达10000℃以上,使 材料熔化甚至气化,这就是激光加工 。
激光可以切割金属,也可以切割非金属。 在激光切割过程中,由于激光对被切割材料不产 生机械冲击和压力,再加上激光切割切缝小,便 于自动控制,故在实际中常用来加工玻璃、陶瓷 、各种精密细小的零部件激光切割过程中,影响 激光切割参数的主要因素有激光功率、吹气压力 、材料厚度等。
•46
• 激光切割特性
• 1)能切割任何难加工的高熔点材料、耐高温和硬 脆材料
(4)非接触加工,工件不受机械切削力,无弹性变 形。
(5)激光束容易实现空间控制时间控制,可进行微 细的精密图形加工。
•16
• (6)不存在工具磨损问题。 • (7)在大气中无能量损失,设备简单,不需
要真空室。 • (8)可通过空气、惰性气体或者光学透明解
质,可对隔离室或真空室内工件进行加工 • (9)加工时不产生振动和机械噪声。 • (10)属于热加工,影响因素多。 • (11)产生金属气体,火星等飞溅物,操作人员
- 1、下载文档前请自行甄别文档内容的完整性,平台不提供额外的编辑、内容补充、找答案等附加服务。
- 2、"仅部分预览"的文档,不可在线预览部分如存在完整性等问题,可反馈申请退款(可完整预览的文档不适用该条件!)。
- 3、如文档侵犯您的权益,请联系客服反馈,我们会尽快为您处理(人工客服工作时间:9:00-18:30)。
要使光能够在腔内来回振荡形成激光.必须要求 光在谐振腔内单程得到的放大比单程的损耗要大、 这就是激光能够振荡的条件。
红宝石激光的示意图
固体激光器
激光器的工作方式
(1)连续激光 (2)脉冲激光 (3)巨脉冲激光 (4)超短脉冲激光
激光的特点
(1)良好的单色性 (2)良好的方向性 (3)高亮度 (4)极好的相干性
激光加工方法
打孔; 切割; 微调; 表面改性; 存储等。
激光加工机理
利用热效应加工。 影响加工有的参数:
激光的基本概念
电子围绕原子核旋转时,只能处于某些特 定的轨道上,即原子只能具有某些特定的 内能。原子的内能不能连续改变。一般把 原子中分裂成一挡一挡的能量称为原子的 能级,电子处于不同的核外轨道上.就对 应了不同能级。原子处于的最低能级称为 基态.即电子离核最近位置.而其余能级 称为激发态或高能态。
外来光子的带动是导致原子从高能级向低能级跃 迂的又一原因.称为受激辐射跃迁。
激光产生过程及特性
自发吸收 - 电子透过吸收光子从低能阶跃迁到高能阶 自发辐射 - 电子自发地透过释放光子从高能阶跃迁到较低能阶 受激辐射 - 光子射入物质诱发电子从高能阶跃迁到低能阶,并释放光子。 由受激辐射跃迁产生的光子跟外来的光子有着相同的特征:频率相同:相位相同,
离子束加工的应用范围
离 子 束 加 工
2.10.4 复合加工
2.10.4.1 电解磨削 2.10.4.2 超声电解复合抛光 2.10.4.3 超声电火花复合抛光
偏振方向相同;传播方向相同。而自发辐射的光子则没有这些特征。 在原子中还存在着受激吸收过程。同样.如果入射到原于上的光子频率满足=E2一
E1的条件,则处于低能级E1的原子有可能吸收这个光子的能量,被激发到较高能级 上去。这时,不但得不到两个光子,反而消失了一个光子.这就是受激吸收过程。
粒子数反转的状态
激光的起源
美国休斯实验室量子电子学部的负责人梅曼于 1960年7月,从红宝石激光器实验装置中射出一 束红光,这标志着世界上第一台激光器的诞生。 在这台红宝石激光器发明后约半年,美国IBM公 司的年轻的科学家索洛金和史蒂文森研制了世界 上第二台、第三台激光器:但是这两台激光器未 能获得实用,远不及1960年12月研制的世界上第 四台激光器,即由美国贝尔实验室贾范发明的, 目前还在广泛应用的氦氖激光器。
激光器的组成
(1)放大介质 放大介质(以下称为激光介质)是指在外界能量的
激励下,可以在其原子的某两个能级间满足粒子 数反转的物质。某种激光介质可以使某个或者某 些持定频率(由达到粒子数反转的两个能级决定) 的光得到放大.最终得到激光输出。
激光介质可以是气体、液体、固体和半导体。根 据激光介质的小同。可以把激光器分为气体激光 器、固体激光器、半导体激光器、化学激光器及 染料激光器等。
溅射去除(芯片的刻蚀); 溅射镀膜(原子、分子级附着加工,制作金属
化合物、合金和氧化薄膜等); 注入加工(材料成分、结构、性能变化,用于
半导体的掺杂、材料改性等); 离子束 暴光(灵敏度、分辨率高,可实现线宽
〈0.1µm的精密暴光)
离子束加工装置
加工装置由离子源、真空、控制、电源系 统等组成;
难加工材料) 加工性能好(无须在防护内进行,无须工具) 加工速度快,效率高; 价格昂贵。
激光加工的各种应用
激光打孔示意图
激光打孔时孔实例
在铝上刻槽
在钼上打直径 为100um的孔
在厚度为1.1mm 的铝上打直径为
200um的孔
激光打孔时孔实例
在陶瓷上打直径 为25um的孔阵列
在硅片上打直径 为6um的孔阵列
2.10.3.3 离子束加工(续)
碰撞模型:
一次溅射 二次溅射 回弹溅射 排斥离子 置换离子
一次碰撞中传递的能量E=4E0m0m/(m0+m)² (E0 :入射离子能量;m0 :被撞击粒子质 量;当m0和m相等时,E取极值。)
离子碰撞过程模型
2.10.3.3 离子束加工(续)
加工方法:
(2)泵浦源
泵浦源的作用就是使激光基态能级的原子 被激发到较高能级,在激光上能级和下能 级之间达到粒子数反转的条件:
不同的激光器类型采用不同的泵浦激励方 式。
固体激光器一般采用闪光灯或者半导体激 光进行泵浦。
(3)反射镜与谐振腔
要想获得单色性(接近单一频率)和方向性好的激 光.我们必须选则一定传播方向和频率的光信号, 使其只有最优的放大作,而抑制其他方向和频率的 光信号。可以在激光介质的两头加上两块相互平行 的反射镜,这对反射镜所形成的是激光谐振腔。
激光的基本概念
由于某种原因激发到高能级的原子在 该能级具有一定的寿命。这种寿命是 非常短的,一般为10-7s左右。原子 在各个能级的寿命有长有短,基态的 寿命最长;在原子中存在着亚稳态, 寿命相对较长为10-3S左右,称为亚 稳态能级,这是激光形成的重要条件。
激光பைடு நூலகம்基本概念
外力作用使原子由低能级过渡到高能级的过程叫 做激发。
离子源分为:
双等离子体(高密度); 离子簇射型(离子流,能量低,但稳定,用于
刻蚀); 高频等离子体(可获金属离子和气体离子,强
度低)。
离子束加工装置
离子束加工加工特点
精度和表面质量高(微观力效应,束径r<1µm, 精度可达nm);
加工材料广(脆性、半导体以高分子材料等); 加工方法丰富:去除、镀膜、注入; 控制性能好,易实现自动化; 应用广。
蓝色激光加工光盘
激光加工用于多层光学光盘
电子束加工
电子束加工的原理
电子束加工是在真空条件下,利 用聚焦后能量密度极高(106一 109w/cm2)的电子束,以极高的 速度冲击到工件表面极小面积上, 在极短的时间(几分之一微秒)内, 其能量的大部分转变为热能,使 被冲击部分的工件材料达到几千 摄氏度以上的高温,从而引起材 料的局部熔化和气化,被真空系 统抽走。 控制电子束能量密度的 大小和能量注入时间,就可以达 到不同的加工目的。
利用电子束热效应的加工
低功率密度、 中等功率密度、 高功率密度照射
(二)加工型孔及待殊表面
电子束不仅可以加工各种直的型 孔和型面,而且也可以加工弯孔 和曲面。
(三)电子束刻蚀
在微电子器件生产中,为了制造多层固体 组件,可利用电子束对陶瓷或半导体材料 刻出许多微细沟槽和孔来,如在硅片上刻 出宽2.5微米,深0.25微米的细槽,在混合 电路电阻的金属镀层上刻出40微米宽的线 条。还可在加工过程中对电阻值进行测量 校准,这些都可用计算机自动控制完成。
光波在腔内来回反射并跟原子发生作用,持续不断 地产生受激辐射,这个方向的光就越来越强,大量 的发光粒子相互关联地向着一个方向发光,这样我 们就获得了激光。
为了引出激光,一块反射镜对激光是全反射的。另 一块是部分透过的,激光在装有部分透过反射镜的 一端输出。
(4)振荡条件
客观上还存在着不利于激光振荡的一面,即放大 介质和谐振腔造成的光在腔内的损耗,如果损耗 的光子数大于放大的光子数。则显然激光就不可 能产生。
值得指出的是,我国在激光领域起步也较早。王 之江等人于1961年也研制成功了我国第一台激光 器“红宝石”激光器。
激光的基本概念
电子围绕原子核旋转的动能和原子核吸引 电子具有的位能构成了整个原子的能量, 即原子的内能。
在无外力作用下,原子的内能是不变的。 在外力的作用下,如果电子和原子核的距 离增大,则原子的内能增加;如果电子和 原于核的距离减小,则原子的内能也要相 应地减小。
电子束焊接可焊接很簿的工件,也可焊接几百毫米厚的工件。 电子束焊接还能完成一般焊接方法难以实现的异种金属焊接。
如铜和不锈钢的焊接,钢和硬质台金的焊接,铬、镍和钼的焊 接等。
2.10.3.3 离子束加工
原理:离子束力效应及其溅射现象。离子质 量》电子质量,加速时间长,但可以达到 10kev的量级。加工是通过弹性碰撞,轰击 加工表面具有强穿透力,表层不产生热量, 无机械应力和损伤。
(四)电子束焊接
由于电子束的能量密度高,焊接速度快,所以电子束焊接的焊 缝深而窄,焊件热影响区小,变形小。电子束焊接一般不用焊 条,焊接过程在真空中进行.因此焊缝化学成分纯净,焊接接 头的强度往往高于母材。
电子束焊接可以焊接难熔金属如钽、铌、钼等。也可焊接钛、 锆、铀等化学性能活泼的金属。对于普通碳钢、不锈钢、合金 钢、铜、铝等各种金屑也能用电子束焊接。
加工特点
束径小,能量密度高(束径r=100~0.1µm,长度可达束 径几十倍,适合深孔加工);
被加工对象广泛(热效应和化学效应加工); 加工速度快,效率高; 控制性能好,易于实现自动化(通过磁场或电场对电子
束的强度、束径、位置进行迅速、准确的控制,自动化 程度高。易于实现加工图形、圆孔、异形孔、盲孔、锥 孔、弯孔及狭缝等。) 由于电子束加工是在真空中进行,因而污染少,加工表 面不氧化,特别适用于加工易氧化的金属及合金材料, 以及纯度要求极高的半导体材料。 电子束加工需要一整套专用设备和真空系统,价格较 贵.生产应用有一定局限性。
激光的起源
1916年,38岁的爱因斯坦发表了一篇论文。 提出了一种受激吸收和发射的观点。所谓 受激吸收就是一个光子照射一个原子,原 子吸收光子后光子消失,原子中的电子从 较低能级跃迁到较高能级;受激发射则是 光子照射处于较高能级的原子,原子发射 出一个跟照射光子频率相同的光子,从而 得到两个光子。这一观点竞成为未来激光 领域的开山之斧。
电子束加工的应用
(一)高速打孔 电子束打孔已在生产中实际应用,目前