锻件超声检测及常见缺陷特征
锻钢件的超声波探伤检查方法缺陷等级分类及判定标准

锻钢件的超声波探伤检查方法缺陷等级分类及判定标准1•目的规范公司锻钢件的超声波探伤检查方法,规范缺陷等级分类及判定标准2•内容2.1探伤装置使用脉冲反射式超声波探伤仪。
2.2探伤方法原则上采用单晶头垂直探伤法。
但是精密探伤及有特殊要求的部位,将同时采用其他探伤方法。
2.3探伤方向及探伤范围按下表实施探伤。
但是,认定有缺陷等异状时,必须从所有方向开始探伤。
探伤方向及扫查范围向:对半圆周进行全面探伤。
但小齿轮、螺纹轴、蜗轮、辊子等表层附近特别重要的锻钢件,要从整周开始进行全面探伤。
轴类锻钢件径向:外周全面探伤轴向:从两个方向进行全面探伤轴向:从两个方向开始进行全面探伤从长度方向,宽度方向,板厚方向三个方向开始进行全面探伤。
但齿条等表层附近特别重要的锻钢件,三个方向均需从两面开始全面探伤。
径向:对外周进行全面探伤轴向:从一个方向开始全面探伤。
但是,齿圈等表层附近特别重要的锻钢件要从两个方向起全面探伤。
径向:对外周进行全面探伤轴向:从一个方向开始全面探伤。
但是,齿轮、车轮等表层附近特别重要的锻钢件要从两个方向起全面探伤。
探伤表面的表面粗糙度要达至【Ra12.5以上较好精加工状态。
2.5测量范围的调整原则上,测定范围要调整至底面回波在显示屏时间轴上显现2次。
2.6探伤方式、使用频率和使用探头探伤方式,使用频率和使用探头见下表。
2.7探伤灵敏度的设定2.7.1底面回波方式的灵敏度设定⑴直径或壁厚在2mm以下的部位,将各不同直径或壁厚的致密部位上第1次底面回波高度(BG)调整至探伤仪显示器刻度板的80%。
然后,根据图4进行灵敏度的增幅,以此作为探伤起始灵敏度。
另外,对于超过检查部位的壁厚1/2以上的区域进行探伤时,需要进一步提高灵敏度12dB进行探伤。
关于小齿轮、螺纹轴、蜗轮、齿轮、齿条、车轮等表层附近特别重要的锻钢件,则用提高了12dB后的灵敏度进行全面或是从两面开始探伤。
⑵试验部位的壁厚超过2m时,使用探头专用的DGS曲线图。
超声波探伤常见缺陷波形特征

超声波探伤常见缺陷波形特征标准化管理部编码-[99968T-6889628-J68568-1689N]分析超声波探伤仪常见八大缺陷的波形特征疏松锻件中的疏松,在低灵敏度时伤波很低或无伤波,提高灵敏度后才呈现典型的疏松波形,中心疏松多出现心部,一般疏松出现始波与底波之间。
疏松对底波有一定影响但影响不大,随着灵敏度提高,底波次数有明显增加。
铸件中的疏松对声波有显着的吸收和散射作用,常使底波显着减少,甚至使底波消失,严重的疏松既无底波又无伤波,探头移动时会出现波峰很低的蠕动波形。
白点缺陷波为林状波,波峰清晰,尖锐有力,伤波出现位置与缺陷分布相对应,探头移动时伤波切换,变化不快,降低超声波探伤灵敏度时,伤波下降较底波慢。
白点对底波反射次数影响较大,底波1~2次甚至消失。
提高灵敏度时,底波次数无明显增加。
圆周各处探伤波形均相类似。
纵向探伤时,伤波不会延续到锻坯的端头。
内裂纹1、横向内裂纹轴类工件中的横向内裂纹直探头探伤,声速平行于裂纹时,探伤仪既无底波又无伤波,提高灵敏度后出现一系列小伤波,当探头从裂纹处移开,则底波多次反射恢复正常。
斜探头轴向移动探伤和直探头纵向贯穿入射,都出现典型的裂纹波形即波形反射强烈,波底较宽,波峰分枝,成束状。
斜探头移向裂纹时伤波向始波移动,反之,向远离始波方向移动。
2、中心锻造裂纹??伤波为心部的强脉冲,圆周方向移动探头时伤波幅度变化较大,时强时弱,底波次数很少或者底波消失。
3、纵向内裂纹??轴类锻件中的纵向内裂,直探头圆周探伤,声束平行于裂纹时,既无底波也无伤波,当探头转动90°时反射波最强,呈现裂纹波形,有时会出现裂纹的二次反射,一般无底波。
底波与伤波出现特殊的变化规律缩孔伤波反射强烈,波底宽大,成束状,在主伤波附近常伴有小伤波,对底波影响严重,常使底波消失,圆周各处伤波基本类似,缩孔常出现在冒口端或热节处。
缩孔残余伤波幅度强,出现在工件心部,沿轴向探伤时伤波具有连续性,由于缩孔锻造变形,圆周各处伤波幅度差别较大,缺陷使底波严重衰减,甚至消失。
超声波检测:第11部分 锻件超声检测
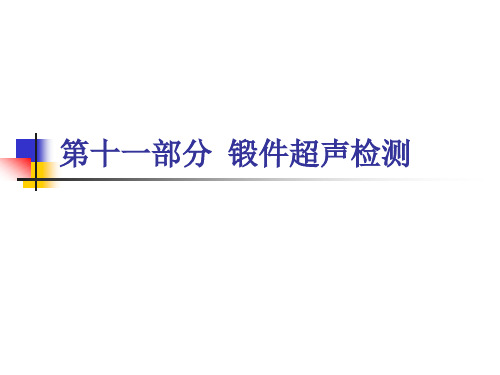
(d)
11.4 探头的选择
标准规定:
双晶直探头:工件检测距离<45mm,频率5MHz, 晶片面积≥150mm2
单晶直探头:频率2~5MHz,晶片尺寸φ14~ φ25mm。
斜探头:频率2.5MHz、K1,晶片直径Ф12~20mm。
11.5 检测灵敏度
扫查灵敏度:一般不得低于最大检测距离处的φ2平底孔
φ3平底孔(至少三个)。调节衰减器,作出双晶直探头
的距离—波幅曲线,并以此作为基准灵敏度。
11.5 检测灵敏度
试块序号
CSⅡ-1 CSⅡ-2 CSⅡ-3 CSⅡ-4
检测距离L
孔径 123456789
φ2 φ3
5 10 15 20 25 30 35 40 45
φ4 φ6
11.5 检测灵敏度
3.斜探头灵敏度调节 60° V形槽对比试块 详见标准P116 附录C
2.机加工后: 防止因表面不平,氧化皮较多影响检测
3.在冲孔、开槽和台阶加工前: 防止这些部位的干扰杂波影响检测。
11.3 锻件的检测方向
1.轴类锻件(拔长) 主要检测方向:直探头径向检测(a) 辅助检测方向:直探头轴向检测(b)
11.3 锻件的检测方向
2.饼类锻件(镦粗) 主要检测方向:直探头端面检测(a)
11.6 缺陷判别和测定
1.单个缺陷回波:记录当量直径≥φ4
2.密集缺陷回波:在50×50mm2范围内,饼形锻件
记录≥φ4当量直径的缺陷密集区,其他锻件记录 ≥φ3当量直径的缺陷密集区,且≥5个。
3.底波降低量 BG/BF≥8dB,且缺陷声程>N
BG:在靠近缺陷处的无缺陷完好区域内第一次底波幅度 BF缺陷区域内的第一次底波幅度
当量直径。
锻件超声波检测

33
底面回波 1.底波消失,缺陷很高或缺陷波出现多次反射, 大多为与探测面平行的大面积缺陷,如缩孔、夹 层、大裂纹等。 2.底波消失或很低,缺陷波很低或无缺陷,可能 是靠近探测面很近的大面积缺陷,或与探测面倾 斜的大缺陷。 3.出现密集的互相此起彼落的缺陷回波。底波明 显下降或消失为密集缺陷,如缺陷面积远大于声 束截面,当量非常小,底波降低不多,大多为金 属夹杂物。 如缺陷波密集,面积成片,缺陷波当量较大,底 波下降很快,大多为白点。
二、锻件探伤一般知识
1、探伤方法 轴类锻件 缺陷特点:与轴线平行 直探头径向探测为主, 直探头轴向探测和斜 探头周向、轴向探测为辅
5
6
饼形锻件
缺陷特点:与轴线垂直 直探头轴向探测为主,直探头径向探测为辅
7
筒类锻件
缺陷特点:缺陷沿圆周方向和轴线方向延伸 直探头径向探测为主,直探头轴向探测和斜探头周 向、轴向探测为辅(筒形) 直探头轴向探测为主,直探头径向探测和斜探头周 向探测为辅。
灵敏度补偿 表面耦合补偿 表面耦合损耗测定 材质衰减补偿 材料衰减系数测定
α=[20lg(Bm/Bn)-§]/2(m-n)T
曲率补偿 曲面试块测定
10
底波计算法
适用条件 T≥3N 、底面平行或底面为曲面工件 平行底面工件和实心圆柱体
20 lg
空心圆柱体
47
灵敏度校准试块
26
• 1)缺陷波在荧光屏上游动的范围相应于缺陷到轴 中心距离的2倍。 • 2)缺陷波最大值的位置无一定规律。如果缺陷表 面的反射条件各向同性,那末,最大缺陷波的位 置应出现在缺陷深度最小的位置。 • 3)当探头沿周向移动一周时,在工件表面的任何 位置上均可发现缺陷波。 • 注:d——缺陷到轴类工件中心的距离(毫米); • θ——探头的半扩散角; • R——轴类工件的半径(毫米)。
锻件超声波探伤缺陷类型识别
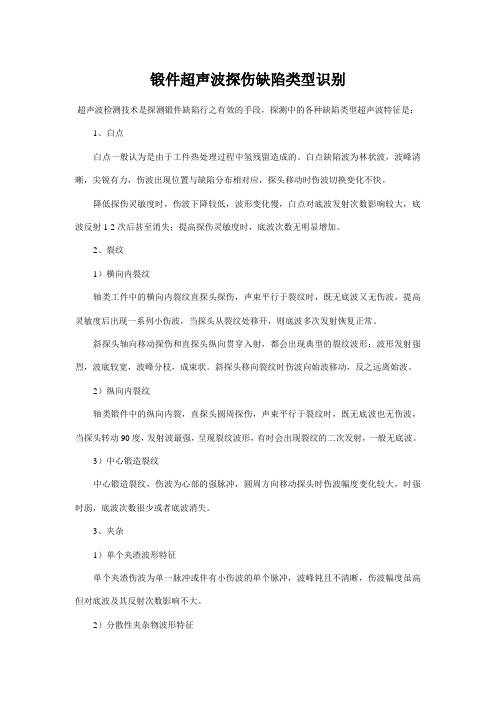
锻件超声波探伤缺陷类型识别
超声波检测技术是探测锻件缺陷行之有效的手段,探测中的各种缺陷类型超声波特征是:
1、白点
白点一般认为是由于工件热处理过程中氢残留造成的。
白点缺陷波为林状波,波峰清晰,尖锐有力,伤波出现位置与缺陷分布相对应,探头移动时伤波切换变化不快。
降低探伤灵敏度时,伤波下降较低,波形变化慢,白点对底波发射次数影响较大,底波反射1-2次后甚至消失;提高探伤灵敏度时,底波次数无明显增加。
2、裂纹
1)横向内裂纹
轴类工件中的横向内裂纹直探头探伤,声束平行于裂纹时,既无底波又无伤波,提高灵敏度后出现一系列小伤波,当探头从裂纹处移开,则底波多次发射恢复正常。
斜探头轴向移动探伤和直探头纵向贯穿入射,都会出现典型的裂纹波形:波形发射强烈,波底较宽,波峰分枝,成束状。
斜探头移向裂纹时伤波向始波移动,反之远离始波。
2)纵向内裂纹
轴类锻件中的纵向内裂,直探头圆周探伤,声束平行于裂纹时,既无底波也无伤波,当探头转动90度,发射波最强,呈现裂纹波形,有时会出现裂纹的二次发射,一般无底波。
3)中心锻造裂纹
中心锻造裂纹,伤波为心部的强脉冲,圆周方向移动探头时伤波幅度变化较大,时强时弱,底波次数很少或者底波消失。
3、夹杂
1)单个夹渣波形特征
单个夹渣伤波为单一脉冲或伴有小伤波的单个脉冲,波峰钝且不清晰,伤波幅度虽高但对底波及其反射次数影响不大。
2)分散性夹杂物波形特征
分散性夹杂物伤波为多个,有时呈现林状波,但波顶圆钝不清晰,波形分枝,伤波较高,但对底波及底波多次发射次数影响较小。
通过观察以上各类波形特征,可以对锻件各类缺陷的定性分析,为有效的缺陷评判提供依据。
齿轮锻件超声波探伤的分类
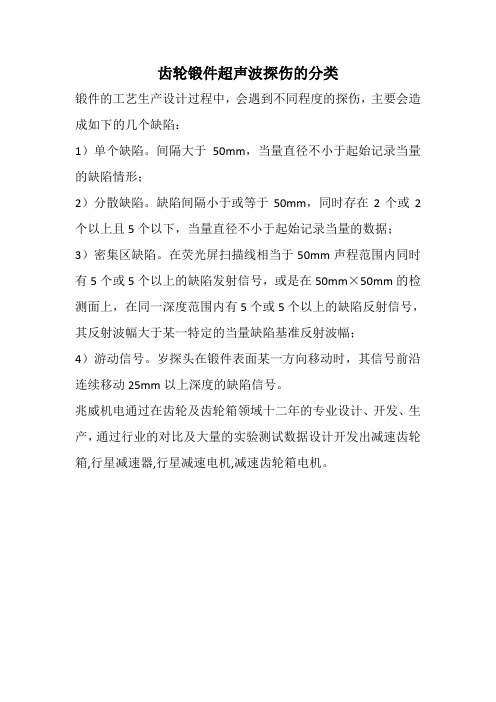
齿轮锻件超声波探伤的分类
锻件的工艺生产设计过程中,会遇到不同程度的探伤,主要会造成如下的几个缺陷:
1)单个缺陷。
间隔大于50mm,当量直径不小于起始记录当量的缺陷情形;
2)分散缺陷。
缺陷间隔小于或等于50mm,同时存在2个或2个以上且5个以下,当量直径不小于起始记录当量的数据;
3)密集区缺陷。
在荧光屏扫描线相当于50mm声程范围内同时有5个或5个以上的缺陷发射信号,或是在50mm×50mm的检测面上,在同一深度范围内有5个或5个以上的缺陷反射信号,其反射波幅大于某一特定的当量缺陷基准反射波幅;
4)游动信号。
岁探头在锻件表面某一方向移动时,其信号前沿连续移动25mm以上深度的缺陷信号。
兆威机电通过在齿轮及齿轮箱领域十二年的专业设计、开发、生产,通过行业的对比及大量的实验测试数据设计开发出减速齿轮箱,行星减速器,行星减速电机,减速齿轮箱电机。
超声波探伤缺陷类型及识别

超声波探伤常见缺陷及识别
(技术培训教材)
一.底波严重降低或消失
1.空洞类缺陷
如缩孔、疏松、内部裂纹、白点、内部撕裂等,该类缺陷大量吸收声波。
2.粗晶
呈密集草状波形态,比较容易识别。
因为晶界较宽,原子排列紊乱,空隙也多,所以吸收声波情况严重。
二.底波降低量不大
1.固体类缺陷
如密集或单个夹杂物、钢锭冒口或底部夹渣、折叠裹入、异金属、偏析、析出物、局部混晶等,这些缺陷经锻造压实后,致密度还是比较高,吸收底波较少。
2.应力集中缺陷
该类缺陷的波形很像密集夹杂物,通常发生在轴类锻件因弯曲稍大,没有加热而冷较直,由内部应力集中所致。
一经回火便可消除。
三. 探伤假象
最常见于筒类锻件、矩形锻件、黑皮探伤薄管板、轴类锻件靠近台阶附近等。
因表面粗糙或存在台阶、棱角、锤印、斜面等因素,使声波大量反射、折射,造成类似“海市蜃楼”现象。
最典型的探伤现象是:只在一个方向上发现缺陷,其它方向没有。
但对于黑皮探伤的薄管板和轴类锻件靠近台阶附近等,就需要经验和了解过程等知识来判断了。
能够准确识别和判断缺陷,说出其产生的原因及环节,是一个探伤师(包括技术人员)的最高境界!这需要广博的理论知识和丰富的实践经验。
钢制锻件超声探伤缺陷分析
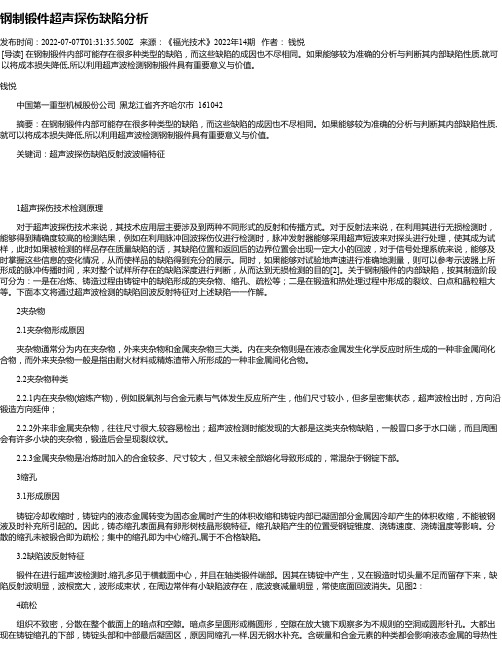
钢制锻件超声探伤缺陷分析发布时间:2022-07-07T01:31:35.500Z 来源:《福光技术》2022年14期作者:钱悦[导读] 在钢制锻件内部可能存在很多种类型的缺陷,而这些缺陷的成因也不尽相同。
如果能够较为准确的分析与判断其内部缺陷性质,就可以将成本损失降低,所以利用超声波检测钢制锻件具有重要意义与价值。
钱悦中国第一重型机械股份公司黑龙江省齐齐哈尔市 161042摘要:在钢制锻件内部可能存在很多种类型的缺陷,而这些缺陷的成因也不尽相同。
如果能够较为准确的分析与判断其内部缺陷性质,就可以将成本损失降低,所以利用超声波检测钢制锻件具有重要意义与价值。
关键词:超声波探伤缺陷反射波波幅特征1超声探伤技术检测原理对于超声波探伤技术来说,其技术应用层主要涉及到两种不同形式的反射和传播方式。
对于反射法来说,在利用其进行无损检测时,能够得到精确度较高的检测结果,例如在利用脉冲回波探伤仪进行检测时,脉冲发射器能够采用超声短波来对探头进行处理,使其成为试样,此时如果被检测的样品存在质量缺陷的话,其缺陷位置和返回后的边界位置会出现一定大小的回波,对于信号处理系统来说,能够及时掌握这些信息的变化情况,从而使样品的缺陷得到充分的展示。
同时,如果能够对试验地声速进行准确地测量,则可以参考示波器上所形成的脉冲传播时间,来对整个试样所存在的缺陷深度进行判断,从而达到无损检测的目的[2]。
关于钢制锻件的内部缺陷,按其制造阶段可分为:一是在冶炼、铸造过程由铸锭中的缺陷形成的夹杂物、缩孔、疏松等;二是在锻造和热处理过程中形成的裂纹、白点和晶粒粗大等。
下面本文将通过超声波检测的缺陷回波反射特征对上述缺陷一一作解。
2夹杂物2.1夹杂物形成原因夹杂物通常分为内在夹杂物,外来夹杂物和金属夹杂物三大类。
内在夹杂物则是在液态金属发生化学反应时所生成的一种非金属间化合物,而外来夹杂物一般是指由耐火材料或精炼渣带入所形成的一种非金属间化合物。
ut超声波锻件检测标准大全

标题:UT超声波锻件检测标准大全引言:UT超声波(Ultrasonic Testing)是一种常用的无损检测方法,适用于锻件等金属材料的检测。
一、UT超声波锻件检测的基本原理UT超声波锻件检测通过传输高频声波进入锻件内部,利用声波的反射和散射来检测缺陷和材料性质。
其基本原理包括声波的发射、传播、接收和信号处理等过程。
二、UT超声波锻件检测的设备及工艺要求1. 设备要求:a. UT超声波探头:选择合适的频率和类型的探头,以满足对不同锻件的检测需求。
b. UT仪器:确保仪器的稳定性、精度和可靠性。
c. 耦合剂:选择适当的耦合剂,确保声波能够有效地传递到锻件表面。
2. 工艺要求:a. 清洁表面:确保锻件表面干净,无杂质和涂层,以保证声波的传播质量。
b. 调节参数:根据锻件的材料和尺寸,合理调节超声波仪器的参数,如增益、频率等,以获得清晰的声波信号。
c. 扫描方式:选择适当的扫描方式,如直线扫描、扇形扫描等,以全面覆盖锻件的检测区域。
三、UT超声波锻件检测的缺陷类型和评定标准1. 缺陷类型:a. 线性缺陷:包括裂纹、夹杂、疏松等。
根据缺陷的位置、长度和宽度等特征进行分类。
b. 表面缺陷:如气孔、夹渣等。
根据缺陷的大小和密度进行评定。
2. 评定标准:a. 线性缺陷:按照标准规定的缺陷尺寸和数量限制进行评定,如长度、深度等。
b. 表面缺陷:按照标准规定的缺陷密度和尺寸进行评定,如单位面积内的缺陷数量。
四、UT超声波锻件检测的操作步骤1. 准备工作:根据锻件的材料和尺寸,选择合适的探头、仪器和耦合剂,并确保设备的正常运行。
2. 清洁表面:使用适当的清洁剂将锻件表面清洁干净,以确保声波的传播质量。
3. 设定参数:根据锻件的要求,调节超声波仪器的参数,如增益、频率等,以获得清晰的声波信号。
4. 扫描检测:按照事先确定的扫描方式,将探头移动在锻件表面,全面扫描检测区域。
5. 数据记录与分析:记录检测数据并进行分析,判断缺陷类型和评定标准是否符合要求。
超声检测应用
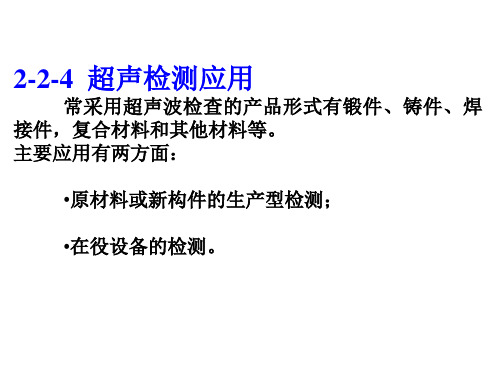
2
3次 波
4级:有4次背面回波,有4~5个小缺陷。 5级:有5次背面回波,有1 ~ 2个小缺陷。 6级:有6次或更多次底面回波,无缺陷。
始脉冲
1
2
3
4
5
6次 回波
(3)焊缝检测
常用的焊接接头型式有对接、角接、丁字按和 搭接4种,如图所示。
超声检测中最常遇到的是对接接头,其次是角 接接头和丁字接接头,搭接接头较少。
无垫板的单面焊底部有反射波时,若从焊 缝两侧测到的当量值相差悬殊,可能是错边引起 。焊角和咬边在探伤时,反射波容易与内部缺陷 混淆
(4) 管材检测
管材中常见的缺陷有裂纹、夹层、夹杂、折叠及翘皮等。 由 于管材在热轧或冷拔过程中沿轴线方向的压延伸长,其受力和变 形主要是在厚度方向上,造成缺陷方向大多数与管材轴线平行。 因此在管材探伤中,根据声束轴线与缺陷反射面垂直的原则,一 般采用垂直于管轴的空间斜入射的横波探伤法。 对于小口径管材为了解决耦合问题,一般采用水浸法。对于大 口径管,耦合和补偿问题较容易解决,可采用直接接触法。
测中仅用反射波高度和缺陷深度指示比较难以区分,还必须从 移动探头时得到的图形变化来补充。夹杂物一般位于锻件中心 部位或环状部位,其波型大多表现为数量很多、大小不一的密 集反射波。裂纹一般更规则、更分散,其大小比非金属夹杂物 均匀,而且与锻造方向有关。与夹杂物相比,裂纹反射波间的 基线明显地分开。裂纹区的反射波衰减显著,为了使差异更明 显,有时采用5MHz频率。
B 缩松 铸锭冷却收缩时形成不致密和小孔穴,单个尺寸很小,呈弥 散分布,当锻件锻压比不足时未能焊合,这种缺陷一般也在锻件 中心。 C 夹杂物 根据其来源和牲质可分为:内在非金属夹杂物、外来非金 属夹杂物和金属夹杂物。内在非金属夹杂物尺寸较小,常被钢液 漂浮、位于钢锭的最后凝固区域。外来非金属夹杂物尺寸较大, 位置不固定。 D 裂纹 裂纹种类甚多,形成的原因不一。
超声无损检测 第8章 锻件铸件超声检测

夹杂有内在夹杂、外来非金属夹杂和金属夹杂。内在夹杂主要集中于钢锭中心 及头部。
裂纹的形成原因很多,锻造裂纹和热处理裂纹等。奥氏体钢轴心晶间裂纹就是 铸造引起的裂纹。锻造和热处理不当,会在锻件表面或芯部形成裂纹。
例如:轴类锻件的锻造工艺主要以拔长为主,因而 大部分缺陷的取向与轴线平行。此类工件的探伤以纵波 直探头从径向探测效果最佳。考虑到缺陷会有其它的分 布及取向。因此轴类锻件探伤,还应辅以直探头轴向探 测和斜探头周向探测及轴向探测。
摸锻件的变形流线是与外表平行的,检测时要尽量 使声束与外表面垂直,采用水浸法比较容易实现。
周向探测时,缺陷定位计 算参见第六章第五节。
a
b 图6.5
8.1.3 探测条件的选择
1.探头的选择
主要使用纵波直探头,低碳钢或低合金钢的材料,晶粒比较细
小,因此可选用较高的探伤频率,常用2~5.0MZHz。晶片 尺寸直径为14~25mm。对于较小的锻件或为了检出近表面
的缺陷,考虑到盲区和近场区的影响,还可采用双晶直探头, 常用频率为5.0MZHz。为了探测与探测面成一定倾角的缺 陷,也可采用一定K值的探头进行探测,一般选择K1探头进 行检测。
锻件的探伤需对表面和外形加工具有光滑的表面, 满足入射面的要求,以提高灵敏度。
水浸法对工件表面的要求低与接触法。
1.轴类锻件的探伤 直探头径向和轴向探测:如图8.1所
示,直探头作径向探测时将探头置于轴的 外缘,沿外缘作全面扫查。以发现轴类锻 件中常见的纵向缺陷。直探头作轴向探测 时,探头置于轴的端头,并在轴端作全面 扫查,以检出与轴线相垂直的横向缺陷。 但当轴的长度太长或轴的多个直径不等的 轴段时,会有声束扫查不到的死区,因而 此方法有一定的局限性。
超声波探伤缺陷分析
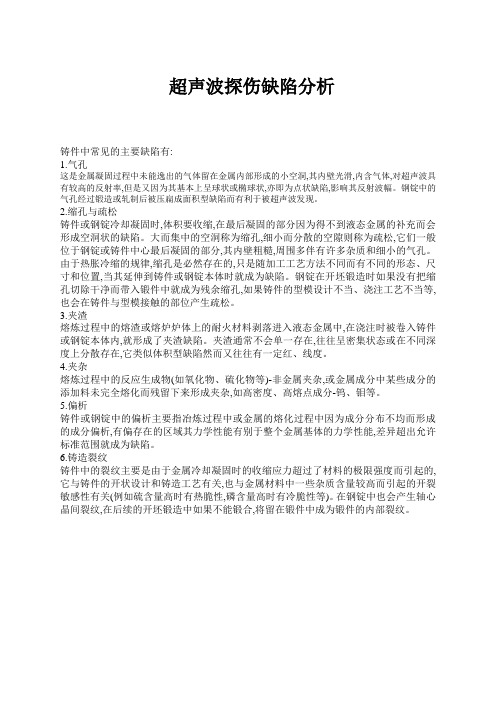
超声波探伤缺陷分析铸件中常见的主要缺陷有:1.气孔这是金属凝固过程中未能逸出的气体留在金属内部形成的小空洞,其内壁光滑,内含气体,对超声波具有较高的反射率,但是又因为其基本上呈球状或椭球状,亦即为点状缺陷,影响其反射波幅。
钢锭中的气孔经过锻造或轧制后被压扁成面积型缺陷而有利于被超声波发现。
2.缩孔与疏松铸件或钢锭冷却凝固时,体积要收缩,在最后凝固的部分因为得不到液态金属的补充而会形成空洞状的缺陷。
大而集中的空洞称为缩孔,细小而分散的空隙则称为疏松,它们一般位于钢锭或铸件中心最后凝固的部分,其内壁粗糙,周围多伴有许多杂质和细小的气孔。
由于热胀冷缩的规律,缩孔是必然存在的,只是随加工工艺方法不同而有不同的形态、尺寸和位置,当其延伸到铸件或钢锭本体时就成为缺陷。
钢锭在开坯锻造时如果没有把缩孔切除干净而带入锻件中就成为残余缩孔,如果铸件的型模设计不当、浇注工艺不当等,也会在铸件与型模接触的部位产生疏松。
3.夹渣熔炼过程中的熔渣或熔炉炉体上的耐火材料剥落进入液态金属中,在浇注时被卷入铸件或钢锭本体内,就形成了夹渣缺陷。
夹渣通常不会单一存在,往往呈密集状态或在不同深度上分散存在,它类似体积型缺陷然而又往往有一定红、线度。
4.夹杂熔炼过程中的反应生成物(如氧化物、硫化物等)-非金属夹杂,或金属成分中某些成分的添加料未完全熔化而残留下来形成夹杂,如高密度、高熔点成分-钨、钼等。
5.偏析铸件或钢锭中的偏析主要指冶炼过程中或金属的熔化过程中因为成分分布不均而形成的成分偏析,有偏存在的区域其力学性能有别于整个金属基体的力学性能,差异超出允许标准范围就成为缺陷。
6.铸造裂纹铸件中的裂纹主要是由于金属冷却凝固时的收缩应力超过了材料的极限强度而引起的,它与铸件的开状设计和铸造工艺有关,也与金属材料中一些杂质含量较高而引起的开裂敏感性有关(例如硫含量高时有热脆性,磷含量高时有冷脆性等)。
在钢锭中也会产生轴心晶间裂纹,在后续的开坯锻造中如果不能锻合,将留在锻件中成为锻件的内部裂纹。
钢锻件超声检测缺陷性质和波形分析
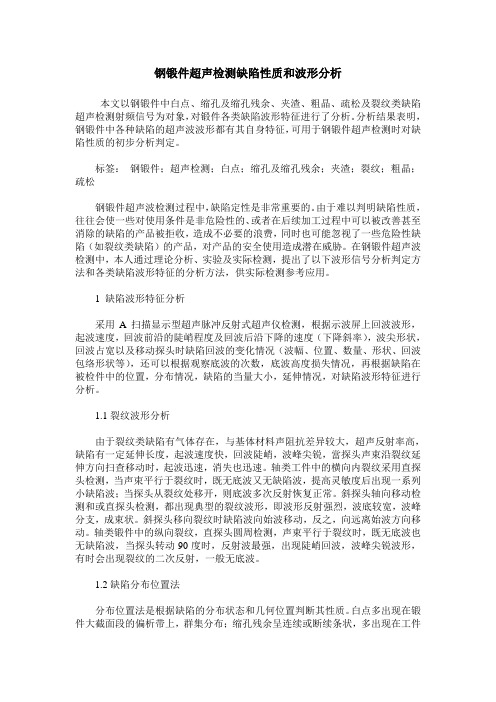
钢锻件超声检测缺陷性质和波形分析本文以钢锻件中白点、缩孔及缩孔残余、夹渣、粗晶、疏松及裂纹类缺陷超声检测射频信号为对象,对锻件各类缺陷波形特征进行了分析。
分析结果表明,钢锻件中各种缺陷的超声波波形都有其自身特征,可用于钢锻件超声检测时对缺陷性质的初步分析判定。
标签:钢锻件;超声检测;白点;缩孔及缩孔残余;夹渣;裂纹;粗晶;疏松钢锻件超声波检测过程中,缺陷定性是非常重要的。
由于难以判明缺陷性质,往往会使一些对使用条件是非危险性的、或者在后续加工过程中可以被改善甚至消除的缺陷的产品被拒收,造成不必要的浪费,同时也可能忽视了一些危险性缺陷(如裂纹类缺陷)的产品,对产品的安全使用造成潜在威胁。
在钢锻件超声波检测中,本人通过理论分析、实验及实际检测,提出了以下波形信号分析判定方法和各类缺陷波形特征的分析方法,供实际检测参考应用。
1 缺陷波形特征分析采用A扫描显示型超声脉冲反射式超声仪检测,根据示波屏上回波波形,起波速度,回波前沿的陡峭程度及回波后沿下降的速度(下降斜率),波尖形状,回波占宽以及移动探头时缺陷回波的变化情况(波幅、位置、数量、形状、回波包络形状等),还可以根据观察底波的次数,底波高度损失情况,再根据缺陷在被检件中的位置,分布情况,缺陷的当量大小,延伸情况,对缺陷波形特征进行分析。
1.1裂纹波形分析由于裂纹类缺陷有气体存在,与基体材料声阻抗差异较大,超声反射率高,缺陷有一定延伸长度,起波速度快,回波陡峭,波峰尖锐,當探头声束沿裂纹延伸方向扫查移动时,起波迅速,消失也迅速。
轴类工件中的横向内裂纹采用直探头检测,当声束平行于裂纹时,既无底波又无缺陷波,提高灵敏度后出现一系列小缺陷波;当探头从裂纹处移开,则底波多次反射恢复正常。
斜探头轴向移动检测和或直探头检测,都出现典型的裂纹波形,即波形反射强烈,波底较宽,波峰分支,成束状。
斜探头移向裂纹时缺陷波向始波移动,反之,向远离始波方向移动。
轴类锻件中的纵向裂纹,直探头圆周检测,声束平行于裂纹时,既无底波也无缺陷波,当探头转动90度时,反射波最强,出现陡峭回波,波峰尖锐波形,有时会出现裂纹的二次反射,一般无底波。
第6章锻、棒、铸件的超声检测
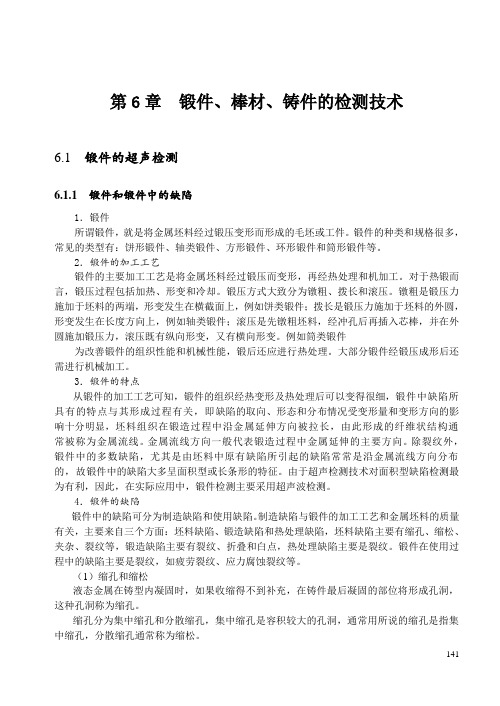
第6章锻件、棒材、铸件的检测技术6.1 锻件的超声检测6.1.1 锻件和锻件中的缺陷1.锻件所谓锻件,就是将金属坯料经过锻压变形而形成的毛坯或工件。
锻件的种类和规格很多,常见的类型有:饼形锻件、轴类锻件、方形锻件、环形锻件和筒形锻件等。
2.锻件的加工工艺锻件的主要加工工艺是将金属坯料经过锻压而变形,再经热处理和机加工。
对于热锻而言,锻压过程包括加热、形变和冷却。
锻压方式大致分为镦粗、拨长和滚压。
镦粗是锻压力施加于坯料的两端,形变发生在横截面上,例如饼类锻件;拨长是锻压力施加于坯料的外圆,形变发生在长度方向上,例如轴类锻件;滚压是先镦粗坯料,经冲孔后再插入芯棒,并在外圆施加锻压力,滚压既有纵向形变,又有横向形变。
例如筒类锻件为改善锻件的组织性能和机械性能,锻后还应进行热处理。
大部分锻件经锻压成形后还需进行机械加工。
3.锻件的特点从锻件的加工工艺可知,锻件的组织经热变形及热处理后可以变得很细,锻件中缺陷所具有的特点与其形成过程有关,即缺陷的取向、形态和分布情况受变形量和变形方向的影响十分明显,坯料组织在锻造过程中沿金属延伸方向被拉长,由此形成的纤维状结构通常被称为金属流线。
金属流线方向一般代表锻造过程中金属延伸的主要方向。
除裂纹外,锻件中的多数缺陷,尤其是由坯料中原有缺陷所引起的缺陷常常是沿金属流线方向分布的,故锻件中的缺陷大多呈面积型或长条形的特征。
由于超声检测技术对面积型缺陷检测最为有利,因此,在实际应用中,锻件检测主要采用超声波检测。
4.锻件的缺陷锻件中的缺陷可分为制造缺陷和使用缺陷。
制造缺陷与锻件的加工工艺和金属坯料的质量有关,主要来自三个方面:坯料缺陷、锻造缺陷和热处理缺陷,坯料缺陷主要有缩孔、缩松、夹杂、裂纹等,锻造缺陷主要有裂纹、折叠和白点,热处理缺陷主要是裂纹。
锻件在使用过程中的缺陷主要是裂纹,如疲劳裂纹、应力腐蚀裂纹等。
(1)缩孔和缩松液态金属在铸型内凝固时,如果收缩得不到补充,在铸件最后凝固的部位将形成孔洞,这种孔洞称为缩孔。
- 1、下载文档前请自行甄别文档内容的完整性,平台不提供额外的编辑、内容补充、找答案等附加服务。
- 2、"仅部分预览"的文档,不可在线预览部分如存在完整性等问题,可反馈申请退款(可完整预览的文档不适用该条件!)。
- 3、如文档侵犯您的权益,请联系客服反馈,我们会尽快为您处理(人工客服工作时间:9:00-18:30)。
②不可到达时,采用折射角为45。的斜 探头在轴的外圆面位置③处也能对缺陷B
取得较好的检测效果。
易漏掉的缺陷,缺陷B就是这种情况,由 于使用直探头在轴的外圆面上无法检测 到缺陷B,因此在对轴类锻件进行超声检 测时,必须辅以直探头从轴的端头,即 在位置②进行检测,在轴过长或者位置
万方数据
删攀婆二…。+
基于缺陷分布的特点,对于饼形锻件, 超声波检测时,主要采用端面赢探头垂 童入射的方式进行检验。
t垄燮…一…~
在要求较高时,辅以赢探头圆周方向检 测可以对锻件进行全匿的超声波检测。
●竺婴垡……~一
I
』抉陷
图1
万方数据
《丝塑型……j
一轴类锻件的超声检测 》轴类锻件由于金属流线方向与轴线方向
一致,多数缺陷方向是沿金属流线方向
》轴类锻件由于制造工艺的原因,也可能 存在上述方法难以发现其它类型的缺陷, 当锻件要求较赢时,可以辅以横波斜入
射的轴向、周向扫查、表面波扫查或小
矗塑!!塑鲨一…
・筒类或环形锻件超声检测 》筒类锻件由于工艺过程复杂,造成其内 部缺陷的取向复杂},选取的检测方案也 就更复杂些。
角度入射等多种方式进行检测。
t。堕
…~.
渊k塑皇..笙型箜萎砂
一扇于锻件内部缺陷具有方向性的特点, 在进行超声波检测时只有与声波方向垂 赢的缺陷才能最有效反射声波,并被探 头接收进而被发现。因此,在锻件探伤 时,选择尽可能多的超声波入射方向是 有效检出所有方向缺陷的基础。在实际 检测中虽然不能做到无限多的检测方向, 但是合理的超声波入射方向组合对于检 测尤为重要。
延伸,因此,缺陷多为沿轴线方向分布, 比如像图2中缺陷A即为沿轴线方向具有 延伸性的缺陷,此种缺陷最有效的检测 方法是使用直探。
■2
≯但在某燕情况下,在锻造的台阶处会产 生垂直于轴向的裂纹,这类缺陷是危害
性最大的缺陷,但是却是超声检测最容
‘型查鲨,,……………。
80
万方数据
矗堂里箜堕墨堑征
一白点 》白点是锻件在锻后冷却过程中产生的一
薯堂里箜堕墨墅每
≯自点的波形特征:白点是由于氢的存在 而产生的小裂纹。超声波波形反映了缺 陷的分布情况,缺陷波孤立、尖锐,一 般波形不高,典型分布为中。&,2/3直径的 环形分布,见图5,对底波的影响情况与 缺陷的大小和多少有关,多数情况底波
薯丝塑壁。………
一饼形锻件锻件超声检测 》由于饼形锻件的主变形方向在轴线方向, 因此钢锭中的缺陷在变形过程中形变方
向沿着金属流动方向,即平行于端藤。
缺陷的分布和特点也不尽相同,在超声 检测中,根据锻件的形状、加工方式以 及缺陷的分布和特点,设计和采用不同 的方法来发现缺陷,从而保证锻件质量 是超声检测的主要目的。
价锻件质量。
万方数据
_在当今众多的无损检测方法中,超声检 测是发现锻件内部缺陷的最有效的无损 检测方法。由于锻件内部缺陷的取向、 形态和分布受到锻件变形的影响,因此 缺陷多具有扁平状和方向性的特点,通 过适当的检测方法设计以及缺陷特征的 识别,能够有效发现锻件中的各类缺陷。
万方数据
t竺型查鲨.。……………。
-不同的锻件由于不同的加工方法,从而
叫k笙型查鲨。。。…………
纹,见图3。
删‘孝垡堕鲨……………。
》对于筒类锻件,由于缺陷方向的多样性, 为了全面检出所有缺陷,就需要多方向 的超声入射方向,随着超声检测仪器的 进步,相控阵超声检测仪器可以很容易 实现多方向超声入射,可以作为检测筒 类锻件的一个很好选择。
≯宜探头在外圆周径向检测,以检测与轴 平行的周向缺陷,以及直探头在端面做 轴向检测,以检测与轴线垂赢的横向缺 陷。另外,采用斜探头在外圆周面上作 周向和轴向检测,以发现内外麓上的裂
・疏松 >在锻件的中心部位,往往因锻比小而产 生疏松,表现为组织不致密。 ≯疏松的波形特征:其波形一般不高,呈 密集状分布于锻件的中心部位,并且伴 随着不同程度的底波降低,见图10。
矗堂墨箜堕冬特征
一锻件超声检测是保证锻件质量的重要检 测手段,根据不同锻件的不同特点,选 用适当的检测方法才能保证检测的有效 性。通过认识不同缺陷的特征,能够分 析和识别锻件内部缺陷的类型,正确评
万方数据
‘堂里箜堕墨塑征
-缩孔 ≯缩孔是钢锭在凝固过程中由于体积收缩 而在钢锭最后凝固区形成的管状或分散
的孔洞,具有较大的体积,并且位于横 截面的中心,孔洞的外缘呈枝权状,在 轴向有延伸长度。
圈3
卅‘.堂里箜堕墨婶征
≯缩孔的波形特征:缩孔是锻造时因切头
量不足而残留下来,波形一般不不强烈,
底部宽,呈包络状,但是,底波衰减强 烈,甚至完全消失,见图4。
损失较大。
种内部缺陷。白点多星放射状分布在从 中心到2/3R区,也有里同心圆状分布在 从中。&,至U2/3R区。
0堂里箜堕譬母征
●堂里箜堕墨姆鍪
_裂纹
≯裂纹种类多,产生的原因也不都一样, 典型表现有纵向裂纹和横向裂纹,裂纹 可能产生在铸锭阶段、锻造阶段以及后
续的热处理阶段。
万方数据
‘.堂墨竺堕墨梦征
锻件超声检测及常见缺陷特征
杜建彤(中信重工机械股份有限公司)
—-壁丝壑重撞测壁常见缺陷特征
杜建彤 中信重工机械股份有限公司
一锻件由于锻造方法的不同,产生的缺陷 也不完全相同,对于不同缺陷需要采用 有针对性的超声检测方法来有效检嫩。 了鳃锻件超声检测方法及典型缺陷特征, 对锻件超声检测及质量控制具有积极意 义。
>横向裂纹:横向裂纹为垂赢于轴向的裂
纹,典型的横向裂纹在使用直探头从轴 的端头检测时,表现出与纵向裂纹相似 的波形特征,即波形反射较强,可出现 缺陷的多次反射,见图8。但是,在轴的 端头不能接近时,只有使用横波斜探头 才能发现此类缺陷,缺陷波随着探头的
前后移动在显示屏上左右游动。
万方数据
‘.堂里竺堕墨鳖簪
_纵向裂纹的波形特征:纵向裂纹为沿轴
0堂里箜堕墨特征
向延伸的裂纹形态,一般采用纵波直探
头在外圆面上即可有效检测,波形反射 较强,有时出现类似底波反射的多次缺 陷波反射,见图6。纵向裂纹在反射最强
位置的垂直方向检测时,表现出不同的
波形特征,见图7。有时,甚至不能发现 缺陷。
‘.堂里箜燮征
图7在图6中纵向垂直方向的波形
一夹杂物
≯在炼钢过程中,少量炉渣、耐火材料及 冶炼中反应产物可能进入钢液,形成夹
杂物。
‘堂里箜堕墨梦年
0.堂里箜堕垄母征
≯夹杂物的波形特征:夹杂物大小不等, 因此波形特征不完全相同,但是,一般 比较容易被超声波发现,多数夹杂物呈
聚集状分布,波形高度变化较大,呈单
根或多根波形聚集状,见图9。
万方数据
‘堂里箜堕墨壁征