化工石油C4管道施工方案
管道吊装专项方案
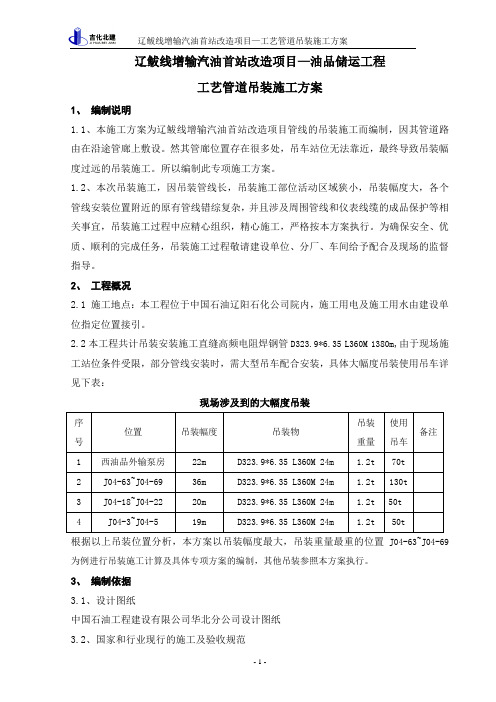
辽鲅线增输汽油首站改造项目—油品储运工程工艺管道吊装施工方案1、编制说明1.1、本施工方案为辽鲅线增输汽油首站改造项目管线的吊装施工而编制,因其管道路由在沿途管廊上敷设。
然其管廊位置存在很多处,吊车站位无法靠近,最终导致吊装幅度过远的吊装施工。
所以编制此专项施工方案。
1.2、本次吊装施工,因吊装管线长,吊装施工部位活动区域狭小,吊装幅度大,各个管线安装位置附近的原有管线错综复杂,并且涉及周围管线和仪表线缆的成品保护等相关事宜,吊装施工过程中应精心组织,精心施工,严格按本方案执行。
为确保安全、优质、顺利的完成任务,吊装施工过程敬请建设单位、分厂、车间给予配合及现场的监督指导。
2、工程概况2.1 施工地点:本工程位于中国石油辽阳石化公司院内,施工用电及施工用水由建设单位指定位置接引。
2.2本工程共计吊装安装施工直缝高频电阻焊钢管D323.9*6.35 L360M 1380m,由于现场施工站位条件受限,部分管线安装时,需大型吊车配合安装,具体大幅度吊装使用吊车详见下表:现场涉及到的大幅度吊装序号位置吊装幅度吊装物吊装重量使用吊车备注1 西油品外输泵房22m D323.9*6.35 L360M 24m 1.2t 70t2 J04-63~J04-69 36m D323.9*6.35 L360M 24m 1.2t 130t3 J04-18~J04-22 20m D323.9*6.35 L360M 24m 1.2t 50t4 J04-3~J04-5 19m D323.9*6.35 L360M 24m 1.2t 50t根据以上吊装位置分析,本方案以吊装幅度最大,吊装重量最重的位置J04-63~J04-69为例进行吊装施工计算及具体专项方案的编制,其他吊装参照本方案执行。
3、编制依据3.1、设计图纸中国石油工程建设有限公司华北分公司设计图纸3.2、国家和行业现行的施工及验收规范《现场设备工业管道焊接工程施工及验收规范》 GB50236—2011 《大型设备吊装工程施工工艺标准》 SH/T3515-2003 《石油化工工程起重施工规范》 SH/T 3536-2002 《石油化工施工安全技术规程》 SH/T 3505-1999 《工程建设安装工程起重施工规范》 HG20201-2000 《建筑机械使用安全技术规程》 JGJ33-2012 《施工现场临时用电安全技术规范》 JGJ46-2012 《建筑施工安全检查标准》 JGJ59-2011 《重要用途钢丝绳》 GB8918-2006 《吊装带标准》 JBT_8521.1-2007 《起重吊装常用数据手册》《汽车吊车性能表》4、吊装施工工序吊装安装位置脚手架搭设-管线进场检查→吊车站位→吊装物捆绑及试吊→正式起吊→吊装就位5、吊装前准备工作1、熟悉、审核图纸,勘察现场实际情况,与施工图纸仔细核对,发现差异时,及时调整思路。
管道安装施工方案模板

一、工程概况1. 工程名称:____________________2. 工程地点:____________________3. 工程规模:____________________4. 工程类型:____________________5. 施工周期:____________________二、编制依据1. 国家相关法规、标准及规范2. 设计图纸及技术文件3. 施工合同及工程要求4. 施工现场实际情况三、施工组织与管理1. 施工组织机构- 项目经理:____________________ - 技术负责人:____________________ - 质量负责人:____________________ - 安全负责人:____________________ - 施工班组:____________________ 2. 施工管理制度- 施工现场管理制度- 质量管理制度- 安全管理制度- 交工验收制度四、施工工艺及方法1. 管道材料及设备- 管道材质:____________________- 管道规格:____________________- 管道连接方式:____________________- 设备型号:____________________2. 施工工艺流程- 土建基础施工- 管道预制- 管道安装- 焊接施工- 管道压力试验- 管道吹扫与清洗- 管道防腐与保温- 交工验收3. 施工方法- 土建基础施工:根据设计图纸进行土方开挖、基础垫层、混凝土浇筑等。
- 管道预制:按照设计要求进行管道、管件、阀门等材料的切割、加工、焊接等。
- 管道安装:按照设计图纸及施工规范进行管道的定位、吊装、连接等。
- 焊接施工:采用合适的焊接方法进行管道焊接,确保焊接质量。
- 管道压力试验:按照设计要求进行管道压力试验,确保管道密封性。
- 管道吹扫与清洗:采用合适的吹扫与清洗方法,确保管道内部清洁。
- 管道防腐与保温:按照设计要求进行管道防腐与保温处理。
输油管道 施工方案

输油管道施工方案输油管道施工方案一、工程概况输油管道施工工作是在输油管道建设项目中最关键的一环,本方案将对输油管道施工的工程概况进行介绍。
1.1 项目背景输油管道建设项目是为了满足能源运输需求而进行的重点工程,本项目由甲方负责设计、施工和运营,包括管道敷设、设备安装、通气通油测试等工作。
1.2 工程范围本次项目涉及输油管道的敷设和各种设备的安装,管道总长度100公里,包括起点站、终点站和中间的输油站。
1.3 工程目标本项目的目标是确保输油管道能够安全、高效地运输油品,并保证工程质量和工期的完成。
二、施工组织2.1 组织结构本次施工所涉及的部门包括甲方施工负责人、施工班组、设备安装组、土建组等,各个部门之间密切配合,形成高效的施工组织。
2.2 人员配置施工方案中需要配备的人员包括:工程师、技术工人、机械操作工、安全员、质量员等,根据工程进度和实际需要进行合理调配。
三、施工流程3.1 前期准备前期准备工作主要包括施工人员培训、现场布置、设备采购、施工方案编制等,确保施工所需资源的准备就绪。
3.2 土建工程土建工程包括基础设施的建设和外围工程,确保输油管道的基础坚固、周围环境整洁。
3.3 管道敷设管道敷设包括开挖沟槽、管道铺设、焊接等工作,确保管道敷设的质量和准确度。
3.4 设备安装设备安装包括压力设备、阀门、泵站等的安装调试,确保设备能够正常运行。
3.5 通气通油测试在管道敷设和设备安装完成后,进行通气通油测试,测试管道的密封性和流量等性能指标。
3.6 竣工验收在所有工作完成后,进行竣工验收,确保工程满足设计和施工标准。
四、安全管理4.1 安全措施施工过程中,要加强对施工现场的管理,设置安全警示标志,引导施工人员佩戴个人防护装备,并定期举行安全教育培训。
4.2 环境保护在施工过程中,要加强对环境的保护,对施工现场产生的废弃物进行集中处理,确保环境的卫生和整洁。
五、质量控制5.1 质量目标施工方案中明确了质量目标,要求在施工过程中严格按照相关标准和规范进行施工,确保工程质量达到设计要求。
石油管道沟槽开挖专项施工方案

石油管道沟槽开挖专项施工方案1. 施工背景为确保石油管道的安全运行,需要对管道进行检修和维护。
本文档旨在提供石油管道沟槽开挖专项施工方案,确保施工过程安全、高效进行。
2. 施工目标- 安全开挖石油管道沟槽,确保管道表面不受损;- 确保施工过程不对管道运行造成影响;- 减少施工过程中的环境污染。
3. 施工步骤1. 施工前准备:- 确定施工区域;- 准备所需施工材料和设备;- 检查石油管道的运行情况,确保可以进行开挖施工。
2. 施工方案设计:- 根据石油管道的位置和深度,设计合适的开挖方案;- 考虑管道的承载能力,采取适当的支撑措施;- 确定安全施工的限制条件,如施工时间、安全距离等。
3. 施工过程:- 根据设计方案进行开挖,确保施工的准确性和稳定性;- 在施工过程中,密切关注管道的运行情况,如有异常及时停工检修;- 施工结束后,及时清理施工场地,确保环境卫生。
4. 施工验收:- 检查开挖工程的质量,确保符合相关安全要求;- 检查施工过程中是否有损坏管道的情况;- 提交相关施工报告和验收材料。
4. 安全措施- 按照相关安全法规和标准进行施工;- 在开挖过程中,设置明显的警示标志,防止他人误入施工区域;- 确保施工现场的通风良好,防止有害气体积聚;- 严格控制施工人员的工作时间,保证其在最佳状态下工作;- 在石油管道附近设置防护设施,以防止意外碰撞或其他损伤。
5. 管理与监督- 指定专人负责施工管理,并与相关部门保持沟通;- 按照施工计划和方案进行施工,及时调整计划以应对不可预见情况;- 定期进行施工过程的监督和检查,并记录相关数据;- 针对施工中的问题和难点,及时采取措施解决。
以上是石油管道沟槽开挖专项施工方案的基本内容,请相关人员根据实际情况进行具体操作,并遵守相关法规和标准,确保施工过程的安全性和顺利进行。
化工厂施工方案(3篇)
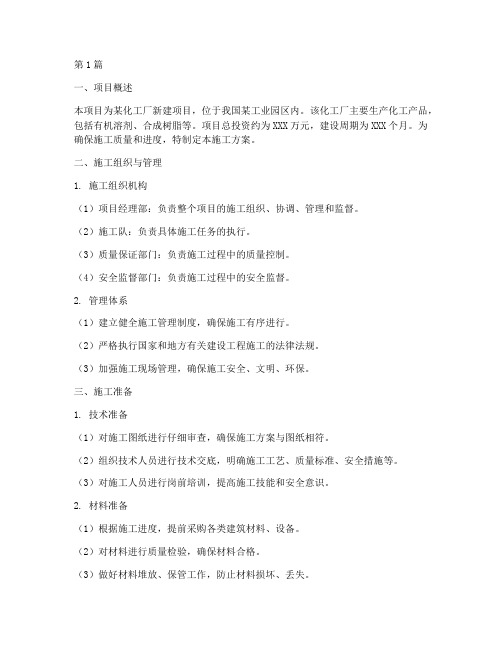
第1篇一、项目概述本项目为某化工厂新建项目,位于我国某工业园区内。
该化工厂主要生产化工产品,包括有机溶剂、合成树脂等。
项目总投资约为XXX万元,建设周期为XXX个月。
为确保施工质量和进度,特制定本施工方案。
二、施工组织与管理1. 施工组织机构(1)项目经理部:负责整个项目的施工组织、协调、管理和监督。
(2)施工队:负责具体施工任务的执行。
(3)质量保证部门:负责施工过程中的质量控制。
(4)安全监督部门:负责施工过程中的安全监督。
2. 管理体系(1)建立健全施工管理制度,确保施工有序进行。
(2)严格执行国家和地方有关建设工程施工的法律法规。
(3)加强施工现场管理,确保施工安全、文明、环保。
三、施工准备1. 技术准备(1)对施工图纸进行仔细审查,确保施工方案与图纸相符。
(2)组织技术人员进行技术交底,明确施工工艺、质量标准、安全措施等。
(3)对施工人员进行岗前培训,提高施工技能和安全意识。
2. 材料准备(1)根据施工进度,提前采购各类建筑材料、设备。
(2)对材料进行质量检验,确保材料合格。
(3)做好材料堆放、保管工作,防止材料损坏、丢失。
(1)根据施工需要,配置各类施工设备,如挖掘机、搅拌机、起重设备等。
(2)对设备进行检查、调试,确保设备运行正常。
(3)做好设备维护、保养工作,提高设备使用寿命。
四、施工方案1. 施工顺序(1)土方工程:先进行场地平整,再进行基础施工。
(2)主体工程:先进行结构施工,再进行装饰装修。
(3)设备安装:先进行管道安装,再进行设备安装。
2. 施工方法(1)土方工程:采用机械开挖、人工配合的方式进行。
(2)基础工程:采用钢筋混凝土基础,分步施工。
(3)主体工程:采用装配式钢筋混凝土结构,分片施工。
(4)设备安装:采用现场组装、吊装的方式进行。
3. 施工质量控制(1)严格执行施工规范和质量标准。
(2)加强施工过程中的质量检验,确保工程质量。
(3)对不合格工程进行返工、返修。
4. 施工安全措施(1)建立健全安全生产责任制,明确各级人员的安全职责。
SH∕T3517-2001石油化工钢制管道工程施工工艺标准
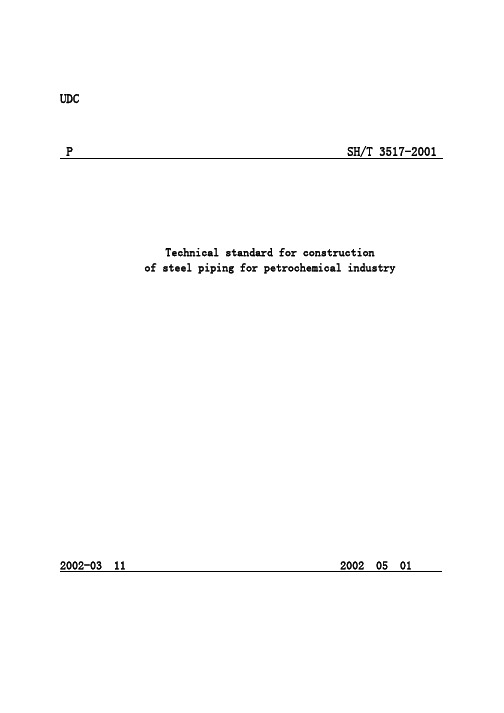
UDC中华人民共和国行业标准P SH/T 3517-2001 石油化工钢制管道工程施工工艺标准Technical standard for constructionof steel piping for petrochemical industry主编单位:中国石化集团第五建设公司主编部门:中国石化集团公司批准部门:中华人民共和国国家经济贸易委员会2002-03—11 发布 2002—05—01 实施中华人民共和国国家经济贸易委员会发布中华人民共和国国家经济贸易委员会二OO二年第12号关于发布《石油化工防火堤设计规范》等19项石油化工行业标准的公告中国石油化工集团公司:你公司报批的《石油化工防火堤设计规范》等19项石油化工行业标准草案,经国家经贸委批准,现予发布,自2002年5月1日起实施。
标准名称、编号为:强制性标准:编号标准编号标准名称1.SH 3125—200l 石油化工防火堤设计规范2.SH 3059—200l 石油化工管道设计器材选用通则(代替SH 3059—94、SH3059—1994)3.SH 3021—2001 石油化工仪表及管道隔离和吹洗设计规范(代替SHJ 21—90、SH 3021—1990)4.SH 3126—2001 石油化工仪表及管道伴热和隔热设计规范(代替SHJ 21-90、SH3021—1990)5.SH 3020—2001 石油化工仪表供气设计规范(代替SHJ 20-90、SH 3020—1990)6.SH 3501—200l 石油化工剧毒、可燃介质管道工程施工及验收规范(代替SH350l—1997)7.SH 3503—2001 石油化工工程建设交工技术文件规定(代替SH 3503—93、SH3503—1993)8.SH 3514—2001 石油化工设备安装工程质量检验评定标准(代替SHJ 514—90、SH 3514—1990)9.SH 3534—2001 石油化工筑炉工程施工及验收规范10.SH 3009—200l 石油化工企业燃料气系统和可燃性气体排放系统设计规范(代替SHJ 9—89、SH 3009—2000)推荐性标准:序号标准编号标准名称11.SH/T 3110-2001 石油化工设计能量消耗计算方法(代替SYJ 1029—82、SH/T3110—2000)12.SH/T 3123-2001 石油化工钢储罐地基充水预压监测规程13.SH/T 3124—2001 石油化工给水排水工艺流程设计图例14.SH/T 3517—2001 石油化工钢制管道工程施工工艺标准(代替SHJ 517—91、SH/T 3517—1991)15.SH/T 3516—200l 催化裂化装置轴流压缩机—烟气轮机机组施工技术规程(代替SHJ 516—90、SH/T 3516—1990)16.SH/T 3530—2001 石油化工立式圆筒形钢制储罐施工工艺标准(代替SH3530-93、SH/T 3530-1993)17.SH/T 3127—2001 石油化工管式炉铬钼钢焊接回弯头技术规范18.SH/T 3109—2001 炼油厂添加剂设施设计规范(代替SYJ 1025—82、SH/T3109—2000)19.SH/T 3096-2001 加工高硫原油重点装置主要设备设计选材导则(代替SH/T3096—1999)中华人民共和国国家经济贸易委员会二OO二年三月十一日前言本标准是根据中石化(1998)建标字l59号和中石化(98)建标便函字第124号文的要求,由中国石化集团第五建设公司对原《石油化工钢制管道工程施工工艺标准》SHJ 517-9l修订而成。
化工工艺设备安装与管道安装施工方案

化工工艺设备安装与管道安装施工方案一、背景介绍二、施工前准备1.准备施工图纸和相关材料清单,确保大部分材料和设备已经到货,并进行检查和验收。
2.制定施工计划和进度安排,确定每个阶段的工作量和时间节点。
3.租赁或购买必要的施工设备和工具,如吊车、起重机、焊接设备等。
4.设立施工现场的安全警戒线和指定安全通道,确保施工现场的安全。
5.组建施工队伍,明确每个成员的职责和工作内容。
三、设备安装1.设备验收:按照相关标准和规范对设备进行验收,确保设备的质量和符合要求。
2.设备安装位置确定:根据施工图纸确定设备的安装位置,并进行测量和标记。
3.地基处理:对设备安装位置的地基进行处理,如挖掘、平整、加固等。
4.设备搬运与安装:a.设备搬运:使用吊车或起重机将设备从运输车辆上吊离,然后平稳搬运到设备安装位置。
b.设备安装:根据设备的安装要求和施工图纸的引导进行安装,包括固定、连接管道等。
四、管道安装1.管道检查:检查管道的质量和完整性,确保管道无损伤、无堵塞等问题。
2.管道布局规划:根据设备的位置和管道连接要求进行管道布局规划,并在地面上进行标记。
3.管道铺设与连接:a.管道准备:根据管道要求进行砂磨、清洗和除锈等处理。
b.管道铺设:根据施工图纸和管道布局规划进行管道的铺设,确保管道的平直和安全。
c.管道连接:使用焊接、螺纹连接、法兰连接等方法进行管道的连接,确保连接的牢固和密封性。
五、施工安全1.施工现场设置警示标志和安全通道,确保人员和设备安全。
2.施工人员必须穿戴安全装备,如安全帽、防护眼镜、防护手套等。
3.施工人员必须经过相关安全培训,了解施工现场的危险和安全操作规程。
4.严禁在设备或管道上进行高空作业,如需进行高空作业,必须使用安全缆线和防护设备。
5.设备和管道安装完成后,进行验收和试运行,确保设备和管道的正常运行。
六、施工后工作1.清理施工现场,将无用材料和废弃物清理干净,并进行垃圾分类和处理。
2.对安装的设备和管道进行记录和标记,便于以后的维护和管理。
石油管道施工专项施工方案

石油管道施工专项施工方案1. 引言本施工方案旨在为石油管道施工提供详细的操作指导和安全保障,确保施工过程安全、高效进行。
本方案适用于石油管道施工的各个阶段,包括勘察、设计、施工和验收等环节。
2. 施工准备2.1 勘察与设计在施工前,进行详细的勘察和设计工作,包括地形地质调查、路径规划、管道设计等。
确保施工过程中的安全和可行性。
2.2 材料准备对所需的施工材料进行清单和检查,确保材料的质量和数量满足施工的需求。
2.3 人员培训对相关人员进行安全培训和操作指导,确保施工人员具备必要的技能和知识。
3. 施工过程3.1 安全措施在施工过程中,应严格遵守安全操作规程,采取必要的安全措施,包括佩戴个人防护装备、设置警示标识等,防范可能发生的安全事故。
3.2 施工方式根据具体的施工需求选择合适的施工方式,包括开挖、铺设、焊接等。
确保施工质量和效率。
3.3 环境保护在施工过程中,应注意环境保护,避免对周边生态环境造成污染和破坏。
4. 施工验收4.1 施工质量检查在施工完成后,进行详细的质量检查,包括管道连接、焊接质量等方面,确保施工质量符合相关标准。
4.2 环境影响评估对施工过程中可能对环境造成的影响进行评估和监测,确保环境受到的影响在可控范围内。
4.3 完工验收经过质量检查和环境影响评估合格后,进行完工验收,确保施工符合相关要求和合同规定。
5. 安全保障5.1 紧急应急措施制定应急预案,明确各种紧急情况下的处置措施,确保施工人员和设备的安全。
5.2 安全培训和教育定期组织安全培训和教育活动,提高施工人员的安全意识和应对能力。
5.3 安全监测建立健全的安全监测系统,定期进行安全检查和评估,发现并解决安全隐患。
6. 结论本施工方案全面细致地介绍了石油管道施工的各个环节和安全保障措施,能够有效指导施工,并确保施工过程的安全和质量。
(最全)石油化工管道施工方案
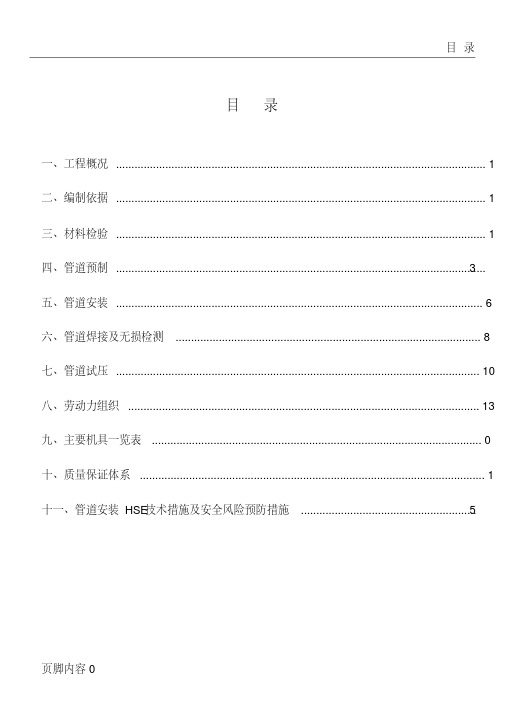
目录一、工程概况 (1)二、编制依据 (1)三、材料检验 (1)3四、管道预制 ........................................................................................................................五、管道安装 (6)六、管道焊接及无损检测 (8)七、管道试压 (10)八、劳动力组织 (13)九、主要机具一览表 0十、质量保证体系 (1)十一、管道安装HSE技术措施及安全风险预防措施 (5)一、工程概况南化公司-南京化工厂资源优化重组项目外管工程由南化设计院设计,南化建设公司南化工程目部承担施工。
本项目的工艺管道贯穿整个厂区管廊,管线比较长,总长度约3万多米,管道材质包括10#、20#、Q235B、Q235A镀锌管、304、C4、15CrMo、衬聚丙烯钢管、衬四聚四氟钢管等,其中20#管材中采用GB/T8163、GB3087、GB9948三种标准,最大管径为DN450,最小管径为DN50。
由于整个工程具有工作量较大,施工场地受到限制的因素比较多,施工难度大,安装质量要求高等特点,该工程施工质量的好坏,对整个厂区各装置运行的效果都很重要,也是衡量施工单位技术水平、取得信誉的关键所在。
因此,我们在施工中一定要严格执行国家、部有关标准,一丝不苟地把好质量关,加上精心组织、合理安排,才能保质保量,安全、准点地完成管道施工任务。
二、编制依据2.1《石油化工剧毒、可燃介质管道工程施工及验收规范》SH3501-20022.2《工业金属管道工程施工及验收规范》GB50235-972.3《现场设备、工业管道焊接工程施工及验收规范》GB50236-982.4《工业金属管道工程质量检验评定标准》GB50184-932.5《石油化工管道器材标准》SH3401-96~SH3410-962.6《建筑排水硬聚乙烯管道工程技术规程》CJJ/T29-982.7 南化集团设计院设计的图纸及设计技术交底三、材料检验1、所有管道组成件(管子、管件、阀门、法兰、补偿器、安全保护装置)及管道支撑件必须具有制造厂的质量证明书及出厂标志,其质量不得低于国家现行行业标准的规定,无质量证明文件的产品不得使用。
石油管道施工工艺流程

石油管道施工工艺流程
石油管道施工工艺流程主要包括以下步骤:
1. 施工准备:包括技术准备、物资准备和施工队伍准备。
这包括熟悉和审查图纸及设计文件,摸清工程内容、工程量和工作量,编制管道工程施工技术方案,组织焊接工艺试验与评定,准备施工机具及工装设施,以及组织施工队伍。
2. 现场制作与安装:包括基础验收、设备的安装和管道的安装。
基础验收要求检查基础质量合格证明书、测量记录,基础的外观不得有裂纹、蜂窝、空洞或露筋等缺陷。
设备的安装需要确认设备安装方向、位置、高度准确。
管道的安装需要确认阀门按要求进行水压试验合格后,方可安装在管道上,并要求管线安装做到横平(坡度)竖直、支点牢固。
3. 质量检测与验收:在施工完成后,需要进行质量检测和验收,确保管道施工符合设计要求和相关规范。
以上是石油管道施工工艺流程的大致步骤,具体实施时可能需要根据实际情况进行调整。
石油化工管道安装施工方案
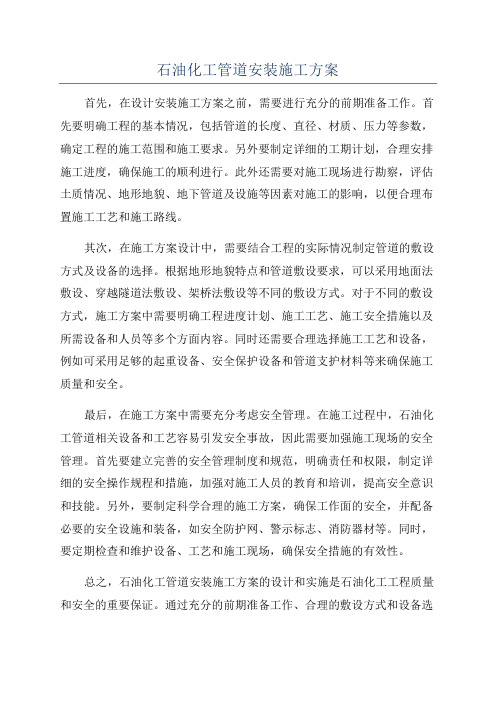
石油化工管道安装施工方案首先,在设计安装施工方案之前,需要进行充分的前期准备工作。
首先要明确工程的基本情况,包括管道的长度、直径、材质、压力等参数,确定工程的施工范围和施工要求。
另外要制定详细的工期计划,合理安排施工进度,确保施工的顺利进行。
此外还需要对施工现场进行勘察,评估土质情况、地形地貌、地下管道及设施等因素对施工的影响,以便合理布置施工工艺和施工路线。
其次,在施工方案设计中,需要结合工程的实际情况制定管道的敷设方式及设备的选择。
根据地形地貌特点和管道敷设要求,可以采用地面法敷设、穿越隧道法敷设、架桥法敷设等不同的敷设方式。
对于不同的敷设方式,施工方案中需要明确工程进度计划、施工工艺、施工安全措施以及所需设备和人员等多个方面内容。
同时还需要合理选择施工工艺和设备,例如可采用足够的起重设备、安全保护设备和管道支护材料等来确保施工质量和安全。
最后,在施工方案中需要充分考虑安全管理。
在施工过程中,石油化工管道相关设备和工艺容易引发安全事故,因此需要加强施工现场的安全管理。
首先要建立完善的安全管理制度和规范,明确责任和权限,制定详细的安全操作规程和措施,加强对施工人员的教育和培训,提高安全意识和技能。
另外,要制定科学合理的施工方案,确保工作面的安全,并配备必要的安全设施和装备,如安全防护网、警示标志、消防器材等。
同时,要定期检查和维护设备、工艺和施工现场,确保安全措施的有效性。
总之,石油化工管道安装施工方案的设计和实施是石油化工工程质量和安全的重要保证。
通过充分的前期准备工作、合理的敷设方式和设备选择、严格的质量控制和安全管理措施,可以确保石油化工管道安装施工的顺利进行,减少事故的发生,保证工程的质量和安全。
管道施工方案(上交)

管道施工方案(上交)
在工程建设中,管道施工方案的制定至关重要。
一个科学合理的施工方案,可
以有效降低工程施工难度,提高施工效率,保证工程质量和安全。
下面,我们将就管道施工方案的制定进行详细介绍。
一、施工前准备
1.方案制定
在启动管道施工前,首先需要编制施工方案。
施工方案应包括施工方法、工期
计划、安全防护措施等内容,确保施工过程有序进行。
2.现场准备
在施工开始前,需要做好现场准备工作,包括清理施工道路、搭设施工设施等,为施工进展提供便利条件。
二、施工过程
1.开挖工程
首先进行管道路线的开挖工程,确保开挖深度、宽度符合设计要求,及时清理
渣土,确保施工安全。
2.管道铺设
在完成开挖工程后,进行管道铺设工作。
根据设计要求,将管道逐段铺设并进
行连接,保证管道的密封性。
3.管道焊接
对于需要焊接的管道,进行焊接工作。
确保焊接质量,预防焊接缺陷,提高管
道的使用寿命。
三、施工后工作
1.试压验收
在管道施工完成后,进行试压验收工作。
通过试压验收,检测管道是否存在漏
气情况,保证管道质量。
2.保养维护
对于已完成的管道,进行保养维护工作。
定期检查管道是否有漏水、腐蚀等情况,及时进行修理和维护。
四、总结与展望
通过上述施工方案的实施,可以保证管道施工工程顺利进行,提高施工效率,确保工程质量和安全。
在未来的施工中,还需要进一步完善管道施工方案,适应不同环境和工程要求,提升施工水平。
以上就是关于管道施工方案的介绍,希望对相关工程人员有所帮助。
石油化工剧毒易燃可燃介质管道施工及验收规范
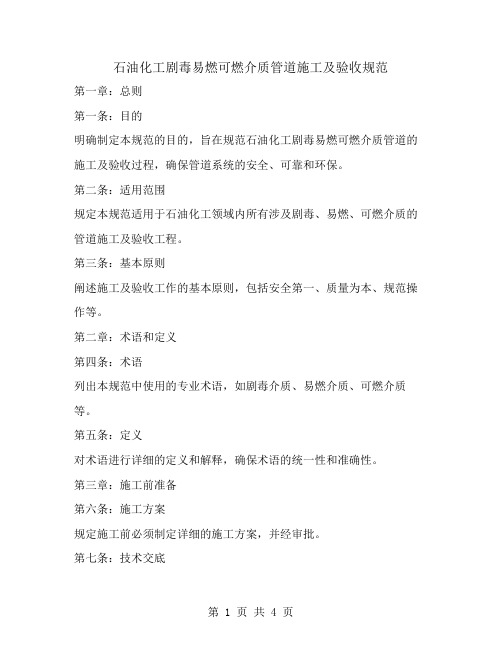
石油化工剧毒易燃可燃介质管道施工及验收规范第一章:总则第一条:目的明确制定本规范的目的,旨在规范石油化工剧毒易燃可燃介质管道的施工及验收过程,确保管道系统的安全、可靠和环保。
第二条:适用范围规定本规范适用于石油化工领域内所有涉及剧毒、易燃、可燃介质的管道施工及验收工程。
第三条:基本原则阐述施工及验收工作的基本原则,包括安全第一、质量为本、规范操作等。
第二章:术语和定义第四条:术语列出本规范中使用的专业术语,如剧毒介质、易燃介质、可燃介质等。
第五条:定义对术语进行详细的定义和解释,确保术语的统一性和准确性。
第三章:施工前准备第六条:施工方案规定施工前必须制定详细的施工方案,并经审批。
第七条:技术交底说明技术交底的要求,确保施工人员对施工方案的理解和掌握。
第八条:材料和设备规定施工所需材料和设备的选型、检验和验收标准。
第四章:施工过程控制第九条:施工工艺详细描述施工工艺流程,包括管道铺设、连接、焊接等。
第十条:安全防护阐述施工过程中的安全防护措施,如防火、防爆、防毒等。
第十一条:质量控制规定施工过程中的质量控制点和控制方法。
第五章:管道焊接与连接第十二条:焊接工艺详细说明管道焊接的工艺要求,包括焊接材料、焊接方法等。
第十三条:连接质量规定管道连接的质量标准和检查方法。
第十四条:无损检测阐述管道焊接接头的无损检测要求和标准。
第六章:管道试压与清洗第十五条:试压要求规定管道试压的压力、时间、方法和安全措施。
第十六条:清洗与吹扫说明管道清洗和吹扫的要求,确保管道内部清洁。
第七章:管道防腐与保温第十七条:防腐施工详细描述管道防腐层的施工工艺和质量要求。
第十八条:保温施工规定管道保温材料的选择和保温施工的技术要求。
第八章:施工验收第十九条:验收标准列出管道施工验收的标准和要求。
第二十条:验收程序规定施工验收的程序,包括自检、互检、专检等。
第二十一条:验收记录说明验收记录的内容和格式,确保验收过程的可追溯性。
第九章:安全管理第二十二条:安全管理制度建立施工过程中的安全管理制度。
管道工程施工技术方案范本

管道工程施工技术方案范本1. 引言管道工程是指为了运输液体、气体和固体颗粒等物质而在地下或地面铺设的管道系统。
管道工程的施工技术方案是施工单位在施工过程中根据设计要求和实际情况制定的具体施工措施和方法。
本文就某管道工程的施工技术方案进行分析和总结,以期为类似工程的施工提供参考。
2. 工程概况某管道工程是指一条长距离输送原油或天然气的管道,全长1000公里,跨越多个省市。
管道主要由钢管组成,直径为DN800,设计压力为10MPa。
管道设计温度为-40℃至70℃。
管道线路经过山区、平原和板块,地质条件复杂。
3. 技术方案(1)前期准备工作在进行管道施工前,首先要进行前期准备工作,包括:1)地质勘察:对管道线路的地质条件进行勘察,着重关注特殊地质条件(如山区、河流和特殊土质)对管道的影响。
2)设计方案确认:要确认管道的设计方案,包括管道线路、材料和安装等技术指标。
3)施工组织设计:确定施工组织架构、施工队伍配备和施工计划。
(2)施工准备在进行管道施工前,要进行施工准备工作,包括:1)人员培训:对施工人员进行安全操作培训,包括管道安装、焊接和防腐等技能培训。
2)设备调试:检查施工所需的设备和机械设备,保证设备工作正常。
3)材料采购:采购符合设计要求的管道材料,包括钢管、管道配件、焊接材料和防腐涂料等。
4)施工图纸制作:根据设计方案,制定细化的施工图纸和工艺流程图。
(3)施工工艺管道工程施工工艺主要包括以下几个方面:1)开挖和铺设:根据设计要求和现场情况进行开挖和铺设,保证管道线路的直线和平整。
2)焊接:使用符合要求的焊接工艺对钢管进行接头焊接,保证焊缝质量。
3)防腐处理:对接头和管道表面进行防腐处理,采用喷涂或涂刷方式进行防腐处理。
4)安装管道配件:按照设计要求对管道进行支架安装、阀门安装和测量仪表安装等。
5)试压和清洗:施工完成后进行管道试压和清洗,检测管道的质量和密封性。
(4)安全防护在进行管道工程施工过程中,要严格执行安全防护措施,包括:1)人员安全:施工人员要佩戴符合要求的安全防护装备,包括安全帽、安全鞋、防护眼镜和手套等。
石化单位给排水管道安装施工方案(超详细)

石化单位给排水管道安装施工方案(超详细)一、施工准备1.1 方案目的石化单位的给排水管道安装施工方案的目的是确保管道系统能够有效运行,达到预期的排水效果,保证设施的安全和持续性运转。
1.2 项目范围本方案适用于石化单位给排水管道系统的安装施工,包括管道材料的选择、施工工艺、设备布置等方面。
1.3 施工前准备在开始施工前,需要进行现场勘查,确认管道布置方案,准备所需的材料、设备和工具,并建立施工组织、安全防护、质量控制等管理措施。
二、管道材料选择与准备2.1 管道材料根据给排水管道的使用环境和介质,选择合适的管道材料,如不锈钢、聚氯乙烯(PVC)、聚乙烯(PE)等,确保其耐腐蚀、耐高温等性能。
2.2 材料准备在施工前,对所选管道材料进行检查,确保材料质量符合要求,同时储备足够的备用材料,以应对可能的损耗与替换需求。
三、施工工艺及步骤3.1 准备工作1.清理施工现场,确保施工区域整洁。
2.检查设备完好,准备施工所需的工具和材料。
3.2 安装管道1.按照设计要求,进行管道的布置和连接。
2.确保管道铺设平整、连接处牢固,并且管道的坡度和弯角符合规范要求。
3.3 安装附件1.安装管道的支架、阀门、法兰等附件,确保连接牢固、紧密。
2.安装管道的检修口、清洗口等配件,以方便后期管道的维护和管理。
3.4 检查与试压1.完成管道安装后,进行全面的检查,确保每一处连接都符合要求。
2.进行管道的试压测试,检查管道系统的密封性和稳定性。
四、质量与安全控制4.1 质量控制1.每个施工节点均需进行质量检查,确保施工符合设计要求。
2.强化施工过程记录,持续跟踪管道安装的各项参数,确保质量可控。
4.2 安全防护1.严格遵守安全操作规程,保证施工人员的人身安全。
2.安排专人负责安全监督,确保施工过程中不发生事故。
五、施工后处理5.1 清理与验收1.施工完成后,对施工现场进行清理,恢复原貌。
2.进行管道系统的验收工作,验证安装质量和功能性。
C4装置吹扫、气密、置换方案

C4装置吹扫、气密、置换方案第一章装置简介 (1)第二章项目组织机构 (1)2.1 项目部组织机构 (1)2.2项目部分项职责 (1)2.2.1项目经理职责: (1)2.2.2 技术负责人职责: (1)2.2.3 物资供应负责人职责: (1)2.2.4 HSE负责人职责: (2)第三章吹扫 (2)3.1 装置吹扫目的 (2)3.2 装置吹扫的注意事项 (2)3.3 装置吹扫具备的条件和准备工作 (3)3.4 吹扫方法 (3)3.5 吹扫准备 (4)第四章公用工程吹扫、冲洗 (4)4.1 低压氮气管线吹扫 (4)4.2 中压氮气管线吹扫 (6)4.3 净化风管线吹扫 (6)4.4 非净化风管线吹扫 (7)4.5 脱盐水管线冲洗 (7)4.6 新鲜水管线冲洗 (7)4.7 生活水管线冲洗 (8)4.8循环水管线冲洗 (8)4.8.1 循环水总管引循环水 (8)4.8.2 冷凝器H-102循环水管线冲洗 (8)4.8.3 冷凝器H-105循环水管线冲洗 (9)4.8.4 冷凝器H-106循环水管线冲洗 (9)4.8.5 冷凝器H-201循环水管线冲洗 (9)4.8.6 冷凝器H-204循环水管线冲洗 (9)4.8.7 冷凝器H-206循环水管线冲洗 (10)4.8.8 冷凝器H-208循环水管线冲洗 (10)4.8.9 冷凝器H-209循环水管线冲洗 (10)4.8.10 冷凝器H-211循环水管线冲洗 (10)4.8.11 冷凝器H-213循环水管线冲洗 (10)4.8.11 冷凝器H-214循环水管线冲洗 (11)4.8.12冷凝器H-302循环水管线冲洗 (11)4.8.13 冷凝器H-305循环水管线冲洗 (11)4.8.14 冷凝器H-306循环水管线冲洗 (11)4.8.15 冷凝器H-307循环水管线冲洗 (11)4.8.16 V-405冷却器循环水管线冲洗 (12)4.8.17 各取样器冷却水管线冲洗 (12)4.9低压蒸汽及凝结水管线吹扫 (13)4.9.1低压蒸汽总线 (13)4.9.2 加热器H-101支线 (13)4.9.3 再沸器H-205支线 (14)4.9.4 再沸器H-210支线 (14)4.10 低低压蒸汽及凝结水管线吹扫 (14)4.10.1低低压蒸汽总线 (14)4.10.2 加热器H-101支线 (14)4.10.3 再沸器H-104支线 (15)4.10.4再沸器H-212支线 (15)4.10.5 再沸器H-301支线 (15)4.10.6 再沸器H-304支线 (15)4.10.7 V-402加热盘管支线 (15)4.10.8各蒸汽吹扫线支线 (16)4.10.9各公用工程站支线 (16)4.10.10 消防管线支线 (16)第五章 MTBE装置贯通吹扫方案 (17)5.1贯通吹扫的目的 (17)5.2吹扫的方法及要求 (17)5.3吹扫贯通注意事项 (18)5.4主要设备蒸汽吹扫试压压力 (19)5.5非净化风吹扫流程 (19)5.5.1 加氢单元吹扫方案 (19)5.5.1.1 V-101吹扫方案 (19)5.5.1.2 R-101A吹扫方案 (20)5.5.1.3 R-101B吹扫方案 (21)5.5.1.4 T-101吹扫方案 (22)5.5.2醚化单元吹扫方案 (22)5.5.2.1 V-202吹扫方案 (22)5.5.2.2 R-101A/B吹扫方案 (23)5.5.2.3 T-201A/B吹扫方案 (24)5.5.2.4 T-204吹扫方案 (25)5.5.3 水洗单元吹扫方案 (26)5.5.3.1 T-202吹扫方案 (26)5.5.3.2 T-203吹扫方案 (26)5.5.4 丁烯-1精制单元吹扫方案 (27)5.5.4.1 V-301吹扫方案 (27)5.5.4.2 T-301吹扫方案 (28)5.5.4.3 T-302吹扫方案 (28)5.6 V-401吹扫方案 (29)5.7 V-402吹扫方案 (30)第六章气密 (30)6.1气密的目的 (30)6.2气密试验原则 (30)6.3气密的条件和准备工作 (30)6.4气密检查方法 (31)6.5 装置气密方案 (32)6.5.1 V-101氮气气密 (32)6.5.2 R-101A氮气气密 (32)6.5.3 R-101B氮气气密 (32)6.5.4 T-101氮气气密 (33)6.5.5 V-202氮气气密 (33)6.5.6 R--201A/B氮气气密 (34)6.5.7 T-201A/B氮气气密 (34)6.5.8 T-202氮气气密 (35)6.5.9 T-203氮气气密 (35)6.5.10 T-204氮气气密 (36)6.5.11 火炬管线氮气气密 (36)6.5.12 V-301氮气气密 (36)6.5.13 T-301氮气气密 (37)6.5.14 T-302氮气气密 (37)6.5.15蒸汽管线试漏 (38)6.5.16蒸汽凝液管线试漏 (38)6.5.17循环水管线试漏 (38)6.5.18脱盐水管线试漏 (38)6.5.19新鲜水管线试漏 (39)6.5.20氮气管线试漏 (39)第七章置换 (39)7.1 氮气置换的目的 (39)7.2 装置氮气置换原则 (39)7.3 氮气置换的条件和准备工作 (40)7.4 氮气置换步骤 (40)7.5 装置置换方案 (41)7.5.1 氢气总管氮气置换 (41)7.5.2 V101氮气置换 (41)7.5.3 R-101A氮气置换 (41)7.5.4 R-101B氮气置换 (42)7.5.5 T-101氮气置换 (42)7.5.6 V202氮气置换 (42)7.5.7 R-201A/B氮气置换 (43)7.5.8 T-201A/B氮气置换 (43)7.5.9 T-202氮气置换 (43)7.5.10 T-203氮气置换 (44)7.5.11 T-204氮气置换 (44)7.5.12 V-301氮气置换 (44)7.5.13 T301氮气置换 (45)7.5.14 T-302氮气置换 (45)7.5.15 V-402氮气置换 (45)7.5.16 V-401氮气置换 (46)第八章 HSE管理 (46)8.1 安全措施 (46)8.1.1技术安全措施 (46)8.1.2、置换安全措施 (47)8.2环境保护措施 (47)第一章装置简介MTBE/丁烯-1装置(简称C4装置)以分离装置脱丁烷塔塔顶来的混合碳四为原料,由PSA变压吸附制氢、1,3丁二烯加氢、醚化、水洗和回收、丁烯-1精制、五个单元组成,生产出高纯度的MTBE,同时精制出高纯度的丁烯-1。
5.1.12.催化裂化工艺管道施工方案

5.1.12.催化裂化工艺管道施工方案中化w工程第三建o公司5.1.12催化裂化工艺管道安装施工方案1.总结惠州炼油项目c4催化裂化/气体分馏/mtbe/烷基化四套装置中共有管道79521米,主要材质有:20#、q235b、l245、1cr5mo、alloy20(引进)、0cr18ni9、0cr18ni10ti、0cr17ni12mo2等。
主要工程量见下表:一一一一一一一一一一一一一一一一一一一一一一一一一一一一一一一一一一一一一一一一一一一一一一一一一一一一一一一一一一一一一一一一一一一一一一一一一一一一一一一一一一一一一一一一一一一一一一一一一一一一一一一一一一一一一一一一一一一一一一一一一一一一一一一一一一一一一一一一一一一一一一一一一一一一一一一一一一一一一一一一一一一一一一一一一一一一一一一一一一一一一一一一一一一一一一一一一一一一一一一一一一一一一一一一一一一一一一一一一一一一一一一一一一一一一一一一一一一一一一一一一一一一一一一一一一一一一一一一一一一一一一一一一一一一一一一一一一一一一一一一一一一一一一一一一一一一一一一一一一一一一一一一一一一一一一一一一一一一一一一一一一一一一一一一一一一一一一一一一一一一一一一一一一一一一一一一一一一一一一一一一一一一一一一一一一一一一一一一一一一一一一一一一一一一一一一一一一一一一一一一一一一一一一一一一一一一一一一一一一一一一一一一一一一一一一一一一一一一一一一一一一一一一一一一一一一一一一一一一一一一一一一一一一一一一一一一一一一一一一一一一一一一一一一一一一一一一一一一一一一一一一一一一一一一一一一一一一一一一一一一一一一一一一一一一一一一一一一一一一一一一一一一一一一一一一一一一一一一一一一一一一一一一一一一一一一一一一一一一一一一一一一一一一一一一一一一一一1-1-1-1-1-1-1-1-1-1-1-1-1-235b(galv)L245材料数量(m)5195536795.85985882.51876.833582370.3313.5760636958389743416194143382174.818.4 634.8备注:施工组织设计工艺管道等四套机组施工方案惠州炼油项目as C4催化裂化417中化w工程第三建设o公司序号23四1名称合金钢管不锈钢管mtbe装置(105)碳钢管合计规格dn600~dn20dn150~dn40dn500~dn15dn50dn300材质alldy200cr17ni12mo220#q235b(galv)l245数量(m)74066.550034887813579521备注引进直缝焊管催化裂化是炼油工程的核心,工艺流程复杂,温度、压力等参数较高,生产介质大多为易燃、易爆、有毒介质。
石油化工厂施工方案

石油化工厂施工方案一、概述本文旨在提供一份石油化工厂的施工方案,以确保项目顺利进行,高效完成。
该方案将涵盖施工流程、安全措施、质量管理和沟通协调等方面。
二、施工流程1. 前期准备在施工前期,需要进行详细的项目规划和调研,包括土地评估、环境影响评估和相关政府审批等工作。
同时,确定施工队伍和设备供应商,并进行合同签订。
2. 地基基础施工在地基基础施工阶段,需要进行土地平整、挖掘和填筑工程,确保土壤承载力满足要求。
此外,还需进行地基基础监测和检测,确保施工质量。
3. 主体结构施工主体结构施工是石油化工厂的核心部分,包括设备安装、管道铺设和厂房建设等工作。
施工过程中需严格按照设计图纸和相关规范要求进行操作,确保质量和安全。
4. 完工调试在主体结构施工完成后,需进行各项设备的调试工作,包括安全系统、供气系统和电力系统等。
同时,还需进行压力测试和性能验证,确保设备正常运行。
三、安全措施1. 安全培训在施工过程中,所有参与方需接受相关安全培训,熟悉施工现场的安全规范和操作流程。
同时,还需制定应急预案,以应对突发事故和事件。
2. 安全监测设置全方位的安全监测系统,包括视频监控、温度检测和气体监测等装置。
及时发现隐患和风险,保障施工过程的安全。
3. 安全防护为施工人员提供必要的安全防护设备,如安全帽、安全鞋和防护服等,以确保其个人安全。
四、质量管理1. 施工标准严格按照国家相关标准和行业规范进行施工,遵循工艺流程和质量要求。
对施工过程进行全程监控和抽样检测,确保产品和工程质量。
2. 质量检测建立科学合理的质量检测体系,包括原材料检测、工序检测和成品检测等环节。
将不合格品及时处理或替换,确保产品质量符合要求。
3. 质量验收在施工完成后,组织相关专业人员进行质量验收。
对建筑工程和设备进行全面检查和测试,确保施工达到设计要求和安全标准。
五、沟通协调1. 内部沟通建立良好的内部沟通机制,及时共享项目进展、问题和疑虑,确保各部门之间的协作和配合顺畅,提高工作效率。
输油管道施工方案
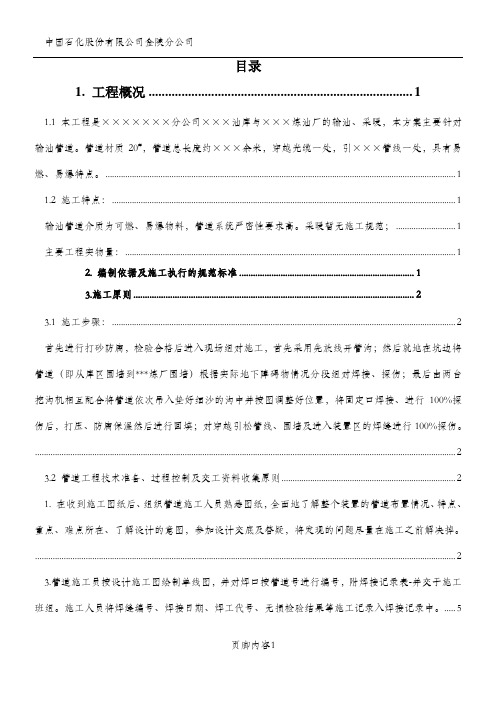
目录1. 工程概况 (1)1.1 本工程是×××××××分公司×××油库与×××炼油厂的输油、采暖,本方案主要针对输油管道。
管道材质20#,管道总长度约×××余米,穿越光缆一处,引×××管线一处,具有易燃、易爆特点。
(1)1.2 施工特点: (1)输油管道介质为可燃、易爆物料,管道系统严密性要求高。
采暖暂无施工规范; (1)主要工程实物量: (1)2. 编制依据及施工执行的规范标准 (1)3.施工原则 (2)3.1 施工步骤: (2)首先进行打砂防腐,检验合格后进入现场组对施工,首先采用先放线开管沟;然后就地在坑边将管道(即从库区围墙到***炼厂围墙)根据实际地下障碍物情况分段组对焊接、探伤;最后由两台挖沟机相互配合将管道依次吊入垫好细沙的沟中并按图调整好位置,将固定口焊接、进行100%探伤后,打压、防腐保温然后进行回填;对穿越引松管线、围墙及进入装置区的焊缝进行100%探伤。
(2)3.2 管道工程技术准备、过程控制及交工资料收集原则 (2)1. 在收到施工图纸后、组织管道施工人员熟悉图纸,全面地了解整个装置的管道布置情况、特点、重点、难点所在、了解设计的意图,参加设计交底及答疑,将发现的问题尽量在施工之前解决掉。
(2)3.管道施工员按设计施工图绘制单线图,并对焊口按管道号进行编号,附焊接记录表-并交于施工班组。
施工人员将焊缝编号、焊接日期、焊工代号、无损检验结果等施工记录入焊接记录中。
(5)4. 对于管道施工中形成的施工记录(如隐蔽工程记录、管道试压记录、管道的预拉伸记录等)应及时办理各方的签字确认。
格式采用SH3503-J201/J202/J115/J117; (5)3.3 现场预制、安装施工原则 (5)3.3.1.管道的焊接采用手工氩弧焊打底,手工电弧焊盖面。
管道施工工程方案
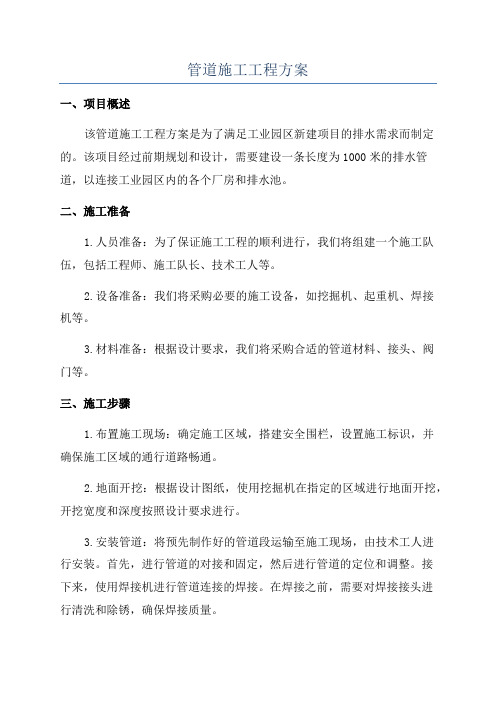
管道施工工程方案一、项目概述该管道施工工程方案是为了满足工业园区新建项目的排水需求而制定的。
该项目经过前期规划和设计,需要建设一条长度为1000米的排水管道,以连接工业园区内的各个厂房和排水池。
二、施工准备1.人员准备:为了保证施工工程的顺利进行,我们将组建一个施工队伍,包括工程师、施工队长、技术工人等。
2.设备准备:我们将采购必要的施工设备,如挖掘机、起重机、焊接机等。
3.材料准备:根据设计要求,我们将采购合适的管道材料、接头、阀门等。
三、施工步骤1.布置施工现场:确定施工区域,搭建安全围栏,设置施工标识,并确保施工区域的通行道路畅通。
2.地面开挖:根据设计图纸,使用挖掘机在指定的区域进行地面开挖,开挖宽度和深度按照设计要求进行。
3.安装管道:将预先制作好的管道段运输至施工现场,由技术工人进行安装。
首先,进行管道的对接和固定,然后进行管道的定位和调整。
接下来,使用焊接机进行管道连接的焊接。
在焊接之前,需要对焊接接头进行清洗和除锈,确保焊接质量。
4.管道测试:安装完毕后,将进行一系列的管道测试。
首先,进行压力测试,通过增加管道内的水压,检测是否存在漏水现象。
同时也需要做管道的渗透性测试,以确保管道的防渗透性能良好。
5.管道保护:为了确保管道使用寿命,需要对管道进行保护。
我们将在管道外层加装保护层,以及安装防腐涂料,减少外界环境对管道的腐蚀。
6.施工记录:在施工过程中,我们将做好施工记录,包括材料进场记录、安装记录、测试记录等。
以备施工结束后的验收和总结使用。
四、施工安全措施1.施工现场应搭建安全围栏,设置明显的施工标识,避免非施工人员进入施工区域。
2.工人应佩戴安全帽、防滑鞋等个人防护装备,并遵守相关安全操作规程,严禁酒后施工。
3.对挖掘机等施工设备进行定期检查和维护,确保设备正常运行,防止事故发生。
4.在开挖过程中,要进行地质勘测,了解施工区域的地质状况,以减少意外风险。
5.施工现场应配备灭火器材,确保在火灾发生时能够及时进行灭火。
- 1、下载文档前请自行甄别文档内容的完整性,平台不提供额外的编辑、内容补充、找答案等附加服务。
- 2、"仅部分预览"的文档,不可在线预览部分如存在完整性等问题,可反馈申请退款(可完整预览的文档不适用该条件!)。
- 3、如文档侵犯您的权益,请联系客服反馈,我们会尽快为您处理(人工客服工作时间:9:00-18:30)。
联合装置工艺管道安装施工技术方案编制:施工技术审核:安全管理审核:质量管理审核:批准:************************************目录1 工程概况 (2)2 编制依据 (2)3 施工准备 (2)4 材料管理 (3)5 施工技术要求 (5)5.1管道预制 (5)5.2管道焊接 (8)5.3焊接质量检验 (10)5.4管道安装 (10)5.5管道系统试验 (14)5.6管道防腐绝热工程 (15)5.7交工技术文件 (15)6质量保证措施 (16)7 安全技术要求 (19)8 人力资源需求 (22)9 措施用料、施工机具需求 (22)10风险评价(JHA)分析 (24)1 工程概况1.1 工程概述C4联合装置由12万吨/年丁二烯抽提、8万吨/年MTBE/3.5万吨/年丁烯一组成,由******************总承包,**************监理有限责任公司负责工程监理,我公司负责装置工艺管道安装工程的施工,本装置初步计算工程量:工艺管道合计为34894m,其中12万吨/年丁二烯抽提为23500m、8万吨/年MTBE/3.5万吨/年丁烯一为11394m,低温钢为560m、不锈钢管道为568m,其管道最大管径为36″/DN900,平均管径为6″/DN150,总吋径为16.6万,设计压力0.2~2.8Mpa。
为安全、优质、高效地完成本装置工艺管道的施工,特编制此施工技术方案。
1.2 工程特点1.2.1管道材质有不锈钢、低温钢、碳钢等多种材质,焊接技术要求高,焊接施工具有一定难度;1.2.2框架内设备、管道的布置复杂,施工的有效作业面较小,交叉作业多,人员和机具的布置困难;1.2.3 装置面积狭小、设备多、管道预制、安装工作量大,施工难度高,工期短等,应在预制厂预制场地内必须尽可能加大预制深度,减少现场焊接工程量。
2 编制依据2.1 ********施工图纸2.2 ****************签署的各项合同文件2.3 管道质量检查标准2.4 《石油化工剧毒、可燃介质管道工程施工及验收规范》(SH3501-2002)2.5 《工业金属管道工程施工及验收规范》(GB50235-97)2.6 《现场设备、工业管道焊接工程施工及验收规范》(GB50236-98)2.7 《石油化工钢制通用阀门选用、检验及验收规范》(SH/T3064-2003)2.8 《石油化工工程铬钼耐热钢管道焊接技术规程》(SH3520-2004)2.9 《石油化工异种钢焊接规程》(SH/T3526-2004)2.10 《工业设备及管道绝热工程施工及验收规范》(GBJ126-89)2.11 《石油化工企业设备管道表面色和标志》(SH3043-2003)2.12 《石油化工施工安全技术规程》(SH3505-1999)2.13《压力容器无损检测》(JB/T4730-2005)2.14《石油化工静电接地设计规程》(SH3097-2000)2.15《石油化工钢制管道工程施工工艺标准》(SH/T3517-2001)2.16《压力管道安装质量程序文件》(QG/SH132524.00-2005)2.17《安全、环境与健康(HSE)管理手册、HSE管理程序文件》(QG/SH132526.00-2004)3 施工准备施工工序按下图进行。
4.1管道及组成件的检验4.1.1材质、规格、型号、质量符合设计文件的规定;4.1.2无裂纹、缩孔、夹渣、折叠、重皮等缺陷;衬胶管道应保证表面光滑,无裸露、裂纹等,衬胶厚度符合其要求;4.1.3锈蚀、凹陷及其他机械损伤的深度,不应超过产品相应标准允许的壁厚负偏差;4.1.4螺纹、密封面、坡口的加工精度及粗糙度应达到设计要求或制造标准;4.1.5管道组成件(管子、阀门、管件、法兰、补偿器、安全保护装置等)必须具有质量证明书或合格证,无质量证明书或合格证不得使用;4.1.6螺栓、螺母的螺纹应完整、无划痕、毛刺等缺陷,螺栓、螺母应配合良好,无松动或卡涩现象。
4.1.7密封垫片应按照产品标准进行抽样检查验收,每批不得少于1件。
缠绕式垫片钢带与填充带应紧密贴合,层次均匀,无断裂,重迭、空隙、弯曲等缺陷;密封面平整光洁,填料丰满并均匀突出金属带。
4.1.8检验合格的管子、管件的材料色标按《色标管理规定》执行。
4.1.9管件应分区存放,不锈钢管道组成件及支承件在储存及施工期间不得与碳钢接触,所有暂时不用的管子均应封闭管口;4.1.10所有管道组成件,均应有产品标识;4.1.11任何材料代用必须经设计部门同意。
4.2管道弹簧支、吊架要求:4.2.1应有合格证明书;4.2.2弹簧表面不应有裂纹、折叠、分层、锈蚀等缺陷;4.2.3尺寸偏差应符合设计要求;4.2.4在自由状态下,弹簧各圈节距应均匀,其偏差不得超过自由高度的2%。
4.3 阀门检验4.3.1 阀门的检验,应专门成立阀门检验、试验小组,其成员应由施工班组、相关技术人员和质量检查人员组成。
4.3.2 阀门试验、检验前,必须进行专门的技术交底,并配置相应的工装设备。
阀门检验、试验程序见图-4.3.2。
图4.4-1 阀门检验、试验工序4.3.3凡阀门安装前应逐个对阀体进行液体压力试验,凡按API标准制造并有相应认证标志,且用户到制造厂监造和验收的阀门,每批可按5%且不少于一个进行抽查,若有一件不合格,必须按原规定数加倍抽查,若仍有不合格,则该批所有阀门进行压力检验,并应做好标记和隔离。
4.3.4阀门壳体试验压力为公称压力的1.5倍,达到试验压力后停压5min,以壳体及壳体填料无渗漏为合格;试验介质使用洁净工业水。
不锈钢阀门液体压力试验时,水中氯离子含量不得超过100mg/L。
4.3.5阀门密封性试验介质为水时,试验压力为阀门公称压力的1.1倍;试验介质为气体时,试验压力为0.6MPa。
液体采用洁净水,气体采用压缩空气。
做密封试验时,阀门密封试验保压时间按表4.3.5执行。
4.3.6进行密封试验时,没有规定介质流向的阀门(如闸阀、球阀、蝶阀等)应分别沿每端引入介质和施加压力;规定介质流向的阀门(如截止阀)等应按规定介质流向引入介质和施加压力;止回阀类应沿使阀瓣关闭的方向引入介质和施加压力;在保压时间内,阀瓣、阀座、静密封面和蝶阀的中间轴处不允许有可见的泄漏,阀门结构不得损伤。
4.3.7试验合格的阀门,及时排净内部积水、吹干密封面并应涂防锈油,关闭阀门,封闭出入口。
并作出标识,合格阀门用油漆或油性记号笔进行标记并填写阀门试验记录。
4.3.8阀门试验、检验应有独立的作业场地,并划分出待检区、检验区、合格区和不合格区。
试验场地应平整、光线充足、道路通畅、通风良好,当环境温度低于5℃时,应采取防冻保护措施。
4.3.9安全阀由相应资质的单位进行调试。
5 施工技术要求5.1管道预制5.1.1施工准备(1)施工班组在预制施工时,仔细核对单线图与平面图,核对基础、设备、管架、预埋件是否正确,对于最后封闭的管段应考虑组焊位置和调节裕量,尽量减少固定焊口的数量。
(2)管道预制按单线图规定的数量、规格、材质选配管道组成件,预制过程中的每一道工序均核对管子的标记,并做好标记的移植,做到用料正确、尺寸准确、标识明显。
5.1.2管道切割及坡口加工(1)钢材的切割方法及管道坡口形式见下表—5.1.2.1,承插焊等其它形式角焊接头形式和组队尺寸见下表(5.1.2.2)钢材对接形式的坡口形式和切割方法分类表表—5.1.2.1注:管子壁厚不大于3mm时,可不开坡口钢材角焊接形式坡口形式和组对尺寸表-5.1.2.2(2)切割后用专门的砂轮片修磨。
大直径碳钢管及低合金钢管用氧乙炔气割后进行打磨。
管子切口表面平整、无裂纹、重皮、毛刺、凹凸、缩口、熔渣、氧化物、铁屑等,切口端面倾斜偏差不大于管子外径的1%,且不超过3mm。
5.1.3坡口形式及加工要求管道的坡口,必须用磨光机磨去影响焊接质量的表面层,并打磨平整。
坡口加工完毕,要检查坡口表面质量,以保证焊接质量。
坡口形式见图-5.1.3。
5.1.4 管道组对(1) 壁厚相同的管道组成件组对时,使内壁平齐,其错边量不超过壁厚的10 ,且内 壁不大于2.0mm ,外壁不大于3.0mm 。
(2) 壁厚不同的管道组成件组对,当管道内壁差大于2mm ;或外壁差超过3mm 时,应按 图-4.3.2要求进行加工、组对。
(3) 管道焊缝的设置及对口规定管道焊缝的设置应便于焊接、热处理及检验,并符合下列要求。
① 除采用无直管段的定型弯头外,管道焊缝的中心与弯管起弯点的距离不小于管子的外径,且不小于100mm。
② 焊缝与支吊架边缘的净距离不小于50mm 。
需要热处理的焊缝距支、吊架边缘的净距离大于焊缝宽度的五倍,且不小于100mm 。
③ 管道两相邻焊缝中心的间距:直管段间距不小于100mm ,且不小于管子外径;除定型管件外,其它任意两焊缝间的距离不小于50mm 。
④ 在焊接接头及其边缘上不应开孔,否则被开孔周围一倍孔径范围内的焊接接头,应进行100%RT 。
5.1.5 预制件的存放、保护与运输(1) 预制好的管段,做好标识,并用塑料布将管口封闭捆扎结实后,按单元或区域摆放整齐,以便于运输和安装。
(2) 不锈钢管道使用专门的场地存放,与碳钢管道严格区分开。
图5.1.3管道焊接坡口形式V 型图-4.4.2不同壁厚管子坡口加工、组对要求b 外壁尺寸不相等a 内壁尺寸不相等5.2管道焊接5.2.1 焊接工艺准备5.2.1.1根据装置管道材料的具体情况,初步制定了管道焊接采用的焊接方法及选用焊材一览表,如表-5.2.1所列。
焊材选用一览表表5.2.15.2.1.2 管道施焊前,每名焊工按监理、业主要求进行焊工考试,考试合格的方可上岗。
5.2.1.3 所有焊接工艺规程都有焊接工艺评定记录(PQR)的支持,否则对无评定记录的焊接工艺重新进行评定。
5.2.1.4 焊接工作进行前,将焊接工艺规程以卡片形式下发到有关焊接人员。
5.2.1.5 对接焊缝管径<3英寸(DN80)的采用氩弧焊,管径≥3英寸(DN80)的采用氩电联焊,管径≥3英寸(DN500)易采用单面焊接双面成行的焊接工艺或在焊缝内侧根部进行封底焊。
5.2.2焊接人员和机具准备5.2.2.1 本装置管道的焊接工作,必须由按《锅炉压力容器焊工考试规则》规定考取相应焊接资格并在有效期内的焊工担任。
5.2.2.2 要求焊接作业人员必须严格按焊接工艺卡和本方案的要求施工。
并在焊接过程中,按照焊接方法和焊接位置要求,对焊工实施持证施焊管理。
5.2.2.3 需用的焊接设备准备充分,能够满足工程施工高峰期的需要。
及早对所有焊接设备进行检查调试,确保性能、状况良好。
5.2.3 焊接材料管理5.2.3.1 焊接材料必须具有质量证明书或产品合格证,并经检验合格。