煤基直接还原铁综述
煤基直接还原炼铁

煤基直接还原炼铁展望来源:廖建国1 前言使用天然气的直接还原炼铁法(Midrex法和HYL法等)的设备投资规模比高炉炼铁法小,且无需焦炭,因此,以盛产天然气的发展中国家为主,把使用天然气的直接还原炼铁法作为生产铁水的设备进行了建设。
最近,在发达国家出现了电炉短流程钢厂使用直接还原铁作为替代废钢的清洁铁源,因此对直接还原铁(以下简称DRI)的需求越来越高。
以天然气为基础的DRI生产厂一般建在盛产天然气的地区,但是最近利用分布范围广、储量大、且输送方便的煤生产DRI的量不断增加。
煤基直接还原炼铁法大部分使用以SL/RN 为主的回转窑进行生产。
使用回转窑生产DRI时,必须将窑温抑制在不会发生明显的回转窑结圈的温度(1000℃~1100℃)内,因此还原需要12h,每座回转窑的年产量仅为15万t~25万t,作为钢铁生产设备来说产量低,人们希望有一种替代的生产方法。
在这种情况下,神户制钢公司与Midrex在美国的子公司共同开发了使用转底炉(Rotary Hearth Furnace,以下简称RHF)的煤基炼铁法。
其工艺是在RHF炉底上全部铺上碳复合球团矿(球团矿或块矿),在静态下进行加热和还原处理,因此炉温(1300℃~1400℃)可以比回转窑的高,还原速度快、生产率高。
尤其是原料的适应性高,可以使用粉矿、粉尘和一般用烟煤等。
本文就神户制钢公司使用RHF对碳复合球团矿进行还原的煤基直接还原法的特征和开发情况进行介绍,同时根据钢铁行业面临的确保原料供应和环保的问题,对煤基直接还原法所能发挥的作用进行了展望。
2 碳复合球团矿还原法特征与受外部还原气体控制的普通球团矿和烧结矿的还原不同,碳复合球团矿的还原法是将粉矿和磨细的煤混合制成球团矿或块矿,利用高温加热后球团矿或块矿中生成的CO气体,从内部对氧化铁进行还原。
因此,还原速度比从外部进行还原的方法快。
此时发生了如下的反应。
FexOy+yC→xFe+yCO(吸热反应)(1)CO2+C→2CO(吸热反应)(2)FexOy+yCO→xFe+yCO2(放热反应)(3)即在铁矿石没有发生熔融的温度范围内,煤和焦粉等固体碳与铁矿石的直接还原反应少(反应式1),但在1000℃以上的高温下,碳复合球团矿内部会因碳素溶解损失反应而生成CO气体(反应式2)和生成的CO气体使氧化铁发生间接还原反应(反应式3)的连锁反应。
煤基直接还原炼铁技术分析

鞍 钢 技 术
ANGANG TECHNOLOGY 总 第 3 9期 6
一. 专 ~ 冢
~ 一 论 坛一
、 ~,
,
I●
,
煤 基直 接 还原 炼铁 技 术 分 析
庞 建 明 , 培 民 , 沛 郭 赵
( 国钢 研科 技 集 团有 限公 司低 温 冶金 及 资 源高效 利 用 中心 , 中 北京 1 0 8 ) 0 0 1
a to e e a u e nd a e u tma i g 1 t n o le r n r q r sa o t1 0 g C as r m c in t mp r t r .a s a r s l k n o fmo tn io e uie b u 0 k O l .F o 0
下 。可见 , 目前 的 煤 基 直 接 还 原 炼 铁 工 艺 , 离低 能 耗 、 污 染 的 炼 铁 目标 相 差 甚 远 , 大 的 问题 低 最
是 固态条件 下的还 原反应 效 率过低 , 高铁 矿 的低 温反 应性 能是 煤基 直接 还 原 炼铁 走 向成 功 、 提
高 效 、 保 的 关键 所 在 。 环
pr c s ,t e h a r nse r m he t n s c nti ng b e z s c n b a re u n y by me ns o o e s h e tta f r fo t a k o ani r e e a e c rid o to l a f
Ab ta t o l b s d d r c e u t n i n k n r c s e r n l z d h o a y k l s s r c :C a — a e i t d c i r ma i g p o e s s a e a ay e .T e r tr i i e r o o n o e ai g w t o r r a t n k n t s l n e ci n t n i h rl s f h a u o i o e p r t i p o e c i i e i , o g r a t i a d h g e o s o e td e t t l w r — n h o c o me s
煤基直接还原铁工艺在中国的市场前景
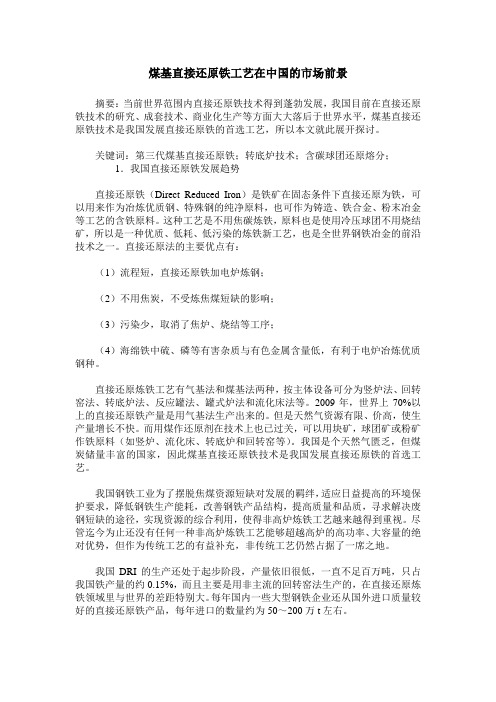
煤基直接还原铁工艺在中国的市场前景摘要:当前世界范围内直接还原铁技术得到蓬勃发展,我国目前在直接还原铁技术的研究、成套技术、商业化生产等方面大大落后于世界水平,煤基直接还原铁技术是我国发展直接还原铁的首选工艺,所以本文就此展开探讨。
关键词:第三代煤基直接还原铁;转底炉技术;含碳球团还原熔分;1.我国直接还原铁发展趋势直接还原铁(Direct Reduced Iron)是铁矿在固态条件下直接还原为铁,可以用来作为冶炼优质钢、特殊钢的纯净原料,也可作为铸造、铁合金、粉末冶金等工艺的含铁原料。
这种工艺是不用焦碳炼铁,原料也是使用冷压球团不用烧结矿,所以是一种优质、低耗、低污染的炼铁新工艺,也是全世界钢铁冶金的前沿技术之一。
直接还原法的主要优点有:(1)流程短,直接还原铁加电炉炼钢;(2)不用焦炭,不受炼焦煤短缺的影响;(3)污染少,取消了焦炉、烧结等工序;(4)海绵铁中硫、磷等有害杂质与有色金属含量低,有利于电炉冶炼优质钢种。
直接还原炼铁工艺有气基法和煤基法两种,按主体设备可分为竖炉法、回转窑法、转底炉法、反应罐法、罐式炉法和流化床法等。
2009年,世界上70%以上的直接还原铁产量是用气基法生产出来的。
但是天然气资源有限、价高,使生产量增长不快。
而用煤作还原剂在技术上也已过关,可以用块矿,球团矿或粉矿作铁原料(如竖炉、流化床、转底炉和回转窑等)。
我国是个天然气匮乏,但煤炭储量丰富的国家,因此煤基直接还原铁技术是我国发展直接还原铁的首选工艺。
我国钢铁工业为了摆脱焦煤资源短缺对发展的羁绊,适应日益提高的环境保护要求,降低钢铁生产能耗,改善钢铁产品结构,提高质量和品质,寻求解决废钢短缺的途径,实现资源的综合利用,使得非高炉炼铁工艺越来越得到重视。
尽管迄今为止还没有任何一种非高炉炼铁工艺能够超越高炉的高功率、大容量的绝对优势,但作为传统工艺的有益补充,非传统工艺仍然占据了一席之地。
我国DRI的生产还处于起步阶段,产量依旧很低,一直不足百万吨,只占我国铁产量的约0.15%,而且主要是用非主流的回转窑法生产的,在直接还原炼铁领域里与世界的差距特别大。
直接还原炼铁

一 直接还原炼铁简介
7、世界直接还原铁生产概况 2012年,全球直接还原铁产量达到7402万吨,其中
印度位居第一,2005万吨。伊朗第二,1158万吨。
全球主要直接还原铁生产大国/MT
国家
印度
伊朗
墨西 哥 委内 瑞拉 中国
2004 9.37 6.41 6.54
7.83 0.43
2005 2006 2007 2008 2009 2010 2011 2012 12.04 14.74 19.06 21.20 22.03 23.42 21.97 20.05 6.85 6.85 7.44 7.46 8.20 9.53 10.37 11.58 5.98 6.17 6.26 6.01 4.15 5.37 5.85 5.59
2.4 Fastmet转底炉法工艺
2.5 CODIR煤基回转窑法工艺
➢该工艺原料可为球团矿、块矿,也可为粉矿,还原剂采用挥 发分较小的高活性煤 ,脱硫剂用石灰石或白云石。炉料、还 原煤和脱硫剂从回转窑尾部进入窑内后在与炉气逆向运动 过程中将矿石还原为海绵铁。
➢CODIR 回转窑工艺流程中约占总量 70 %的还原煤由窑头 用压缩空气喷入 ,因此较好地抑制了再氧化和结圈现象。冷 却筒采用间接和直接水冷相结合的方式 ,提高了设备的作业 率 ,有利于回转窑的连续、 稳定生产 ,在多种回转窑工艺中 具有较突出的优势。
目前投入工业应用的直接还原工艺主要有Midrex工艺、HYLIII工艺、Finmet工艺、SL/RN工艺等。2012年全球DRI产量达 到7402万吨,Midrex工艺和HYL-III工艺生产的DRIDRI所占比 例达到76.3%。
2.1 Midrex(米德兰)法工艺
➢ Midrex 法具有工艺成熟、操作简单、生产率高、热耗低、 产品质量高等优点, 因此在直接还原工艺中占统治地位。
熔融还原炼铁技术综述

目录1.概述 (1)2.国际熔融还原技术发展 (3)2.1.工业化的COREX工艺 (5)2.2.进入示范性工厂试验的Hismelt技术 (7)2.3.FINEX技术 (8)2.4.第三代炼铁法--ITmk3 (9)3.国内熔融还原(非高炉炼铁)技术发展现状 (11)3.1.概述 (11)3.2.2T/h的半工业联动热态试验装置-COSRI (11)3.3.宝钢Corex 3000 (14)3.4.20万吨纯氧非高炉炼铁工业试验装置 (14)3.5.8m3一步法熔融还原试验装置 (18)3.6.基于氢冶金的熔融还原炼铁新工艺 (20)3.6.1.万吨级两级循环流化床示范装置-营口中板厂 (21)3.6.2.宝钢万吨级两级冷态循环流化床装置建设 (24)3.7.直接还原在国内的发展 (24)3.8.几种非高炉炼铁的综合分析 (26)4.炼铁技术的发展方向 (28)4.1.欧盟——ULCOS超低CO2排放钢铁技术研究 (28)4.2.日本——COURSE50技术研究 (30)4.3.中国——新一代可循环钢铁流程工艺技术技 (30)5.具有自主知识产权的熔融还原炼铁技术发展建议 (31)5.1.建立长期开发组织机构与募集资金 (31)5.2.加强合作、充分利用现有成果深入研究 (31)5.3.新一代具有自主知识产权的熔融还原流程建议 (32)熔融还原炼铁技术综述全强1.概述改革开放30年来,中国钢铁冶炼技术取得了巨大的进步。
在炼铁领域,技术进步的主要表现是装备的大型化、操作的自动化信息化、生产的高效与清洁化,高风温技术、富氧技术、喷煤技术、煤气干式除尘技术、煤气余压发电、煤气燃气技术、高炉长寿技术、与高炉废弃物的综合利用等方面的应用取得明显的进步。
据2010年的统计,国内炼铁产量已超过5.9亿吨,约占世界产量的40%。
其中大于1000m3以上高炉的产量约为60%,也就是说,按照国家产业政策的要求,有40%的产能需要进行技术改造。
直接还原炼铁

炉内压力: 250KPa左右 天然气能耗:
10.2~11t/GJ 炉料在整个炉内停 留时间:10h左右
还原区温度: 850℃左右
金属化率:>92%
H 2 C O 1
C4 H 1/22 O催 化 剂 CO 2H 2
C4 H C2 O 催 化 剂 2CO 2H A2
12
2.2 HYL-III(Energiron)法工艺
A
13
2.2 HYL-III(Energiron)法工艺
C4 H H 2 O 催 化 3剂 2H CO
炉内压力:600KPa 天然气能耗:
10~11.3t/GJ 炉料在整个炉内停留
时间:大于10h 还原区温度:
900~960℃ 金属化率:>91%
H 2 C> O 2
A
14
2.3 HYL-ZR法工艺
直接还原炼铁
A
1
一 直接还原炼铁简介
1 、定义 直接还原炼铁(Direct Reduction Iron)是一种采用
天然气、煤气、非焦煤粉作燃料和还原剂, 使用球团矿、 块矿、粉矿在在软化温度以下直接还原生产固体直接还原 铁( DRI /HBI) 的炼铁工艺技术。
2 、优点 ① 使用非焦煤,取消了炼焦和烧结等高能耗高污染工序 ② DRI/HBI 中P、S和和有色杂质(Cu、Ni、Cr、Mo、Sn等)
➢ HYL-ZR是在原HYL工艺系列上发展起来的一种新型气基自 重整直接还原工艺,HYL-ZR技术可在其工艺和设备无任何改 动情况下使用焦炉煤气、Corex熔融还原炉产生的煤气或者 合成气 ,而其他技术大都需要对其基本配置进行重大改动 。目前开始在我国和印度等地区应用。
➢在竖炉内通过对还原气进行控制而产生合乎要求的还原气 体 ,其还原气体经过不完全燃烧 ,以及在还原反应器内经 过金属铁的催化作用在现场重整而生成 ,从而对铁矿石进 行还原;而传统HYL-Ⅲ 工艺是在添加蒸汽条件下使天然气 在催化重整装置中裂解。
“一步法”煤基直接还原技术探讨_图文

四、结论
4结论
直接还原铁技术将是未来钢铁工业的重要发展方向。煤基“一步
法”符合我国国情,生产实践证明其仍然具备一定的生命力,可 以作为DRI生产的补充,应该得到认可和重视。
“一步法” 的两个瓶颈技术是结圈和产量小。通过开发回转窑测
中国直接还原铁产 量/万吨
中国直接还原铁占 总铁量比例%
2004 5460 7.56
43 0.16
2005 5699 7.29
41 0.11
2006 2007 2008 2009 2010 5979 6722 6845 6200 7040
6.85 7.12 7.38 6.80 6.83
41
60
60
60
氧化焙烧固结的球团在还原过程中产生体积膨 胀,导致粉化较严重、回转窑易结圈
针对上述问题,采用多功能复合粘结剂,开发相匹配的球团制 备技术和新型回转窑热工体系,实现一步高温过程生产直接还 原铁。
2.2 “一步法”的优势
密云冶金矿山公司直接还原铁厂
指标
单位窑容产量 (t/m3·d)
氧化球团直接还原的 国际先进水平*
窑身仅由10台左右二次风喷嘴供风,沿窑身方向温度场波 动大,易结圈;
2.4 “一步法”的发展瓶颈
富蕴生产实践经验,还原煤的综合理化指标以及稳定性是制约工艺顺畅 的主要因素;由于原设计不完善,设备故障率高、操作经验不足,以及 经济危机和企业重组等影响,大部分时间处于停产状态。但从生产运行 结果,特别是2012年改造后的生产实践证明:“一步法” 仍然具备很强的 生命力,将是未来我国DRI生产的重要补充。
一次元件、信号处理单元与隔热装置
直接还原炼铁分析

一 直接还原炼铁简介
7、世界直接还原铁生产概况 2012年,全球直接还原铁产量达到7402万吨,其中 印度位居第一,2005万吨。伊朗第二,1158万吨。
全球主要直接还原铁生产大国/MT
国家 印度
伊朗 墨西 哥 委内 瑞拉 中国
2004 9.37
6.41 6.54 7.83 0.43
2005 12.04
HYL-ZR是在原HYL工艺系列上发展起来的一种新型气基自 重整直接还原工艺,HYL-ZR技术可在其工艺和设备无任何改 动情况下使用焦炉煤气、Corex熔融还原炉产生的煤气或者 合成气 ,而其他技术大都需要对其基本配置进行重大改动。 目前开始在我国和印度等地区应用。 在竖炉内通过对还原气进行控制而产生合乎要求的还原气 体 ,其还原气体经过不完全燃烧 ,以及在还原反应器内经 过金属铁的催化作用在现场重整而生成 ,从而对铁矿石进 行还原;而传统HYL-Ⅲ 工艺是在添加蒸汽条件下使天然气 在催化重整装置中裂解。
2.2 HYL-III(Energiron)法工艺
HYL-III是墨西哥某公司开发成分的连续式移动床罐式法, 这一工艺的前身是该公司早期 开发的间歇式固定床罐式法 (HYL-I、HYL-II)。以水蒸气为裂化气(这是与MIDERX的 最大区别),以天然气为原料通过催化反应制取。还原气 转化炉以天然气和部分炉顶煤气味燃料。 主要设备由两部分 ①制气部分(转化炉):炉内有许多不锈钢管,管内涂有 催化剂 ②还原部分
2.1 Midrex(米德兰)法工艺
炉内压力: 250KPa左右 天然气能耗: 10.2~11t/GJ 炉料在整个炉内停 留时间:10h左右 还原区温度: 850℃左右 金属化率:>92%
H 2 CO 1
CH 4 1/2O2 催化剂 CO 2H 2 CH 4 CO2 催化剂 2CO 2H 2
煤基直接还原铁生产技术的发展

一、工艺流程
Fastmelt 工艺是 Fastmet 工艺和炼铁电炉的综合。来自回 转窑的直接还原铁在炼铁电炉中熔化生产铁水。
ITmk3 工艺是在回转窑中生产粒状铁。团块在回转炉中 加热到 1450℃, 在还原和熔化之后, 炉渣在回转窑中分离。铁 水和炉渣被冷却并从回转窑中排出。
0.00 GJ
2.47 GJ
4.10 GJ
燃气
( 0 kg- CO2 ) ( 141 kg- CO2 ) ( 234 kg- CO2 )
1.54 GJ
2.95 GJ
0.00 GJ
电能
( 103 kg- CO2 ) ( 198 kg- CO2 ) ( 0 kg- CO2 )
0.00 GJ
0.07 GJ
表 8 研究 A 研究结果概括
高炉( 50 万吨 / Fastmelt 工艺( 50 ITmk3 工艺( 50
年铁水) 万吨 / 年铁水) 万吨 / 年粒状铁)
消耗
31.47GJ
14.26 GJ
14.09 GJ
煤
( 2936kg- CO2 ) ( 1330kg- CO2) ( 1314kg- CO2)
技术与装备纵横
煤基直接还原铁生产
技术的发展
□袁 文
目前, 世界炼铁生产的主流是高炉工艺, 但该工艺需要 一些原料准备设备, 如焦炉、烧结设备等, 而其会给环境带来 很大影响。气基直接还原铁如 MIDREX 工艺是高炉炼铁工艺 的替代方法之一, 然而, 该工艺受到以经济方式获得天然气 的限制。在这一背景下, 对可以使用更广泛的原料和燃料, 且 对环境更加友好的新炼铁工艺的需求日益增加。为了满足这 种 需 求 , 人 们 开 发 出 3 种 煤 基 直 接 还 原 铁 生 产 工 艺— —— Fastmet 工艺、Fastmelt 工艺和 ITmk3 工艺。采用这些工艺可以 通过粉矿和煤生产出高质量的铁, 如直接还 原 铁 、铁 水 和 粒 状铁。而且, 这 3 种工艺在能耗和环保方面可以与高炉竞争。
煤基直接还原炼铁技术及非高炉炼铁能耗分析

煤基直接还原炼铁技术及非高炉炼铁能耗分析摘要:非高炉炼铁技术或称非焦炼铁技术是当今钢铁生产工艺中最受关注的技术之一。
依产品的形态不同,非高炉炼铁技术可分为熔融还原与直接还原两种工艺方法。
直接还原是以非焦煤为能源,在不熔化不造渣的条件下,原料保持原有物理形态,铁的氧化物经还原获得以金属铁为主要成分的固态产品的技术方法。
直接还原炼铁工艺分为气基直接还原和煤基直接还原,气基直接还原炼铁工艺是最主要的直接还原炼铁技术,其产量占到直接还原炼铁的90%左右,煤基直接还原炼铁,目前以回转窑为主,也是最主要的煤基直接还原炼铁工艺。
关键词:非高炉炼铁;直接还原;熔融还原;煤基;气基近代高炉已有数百年历史,其工艺已达到相当完善的地步。
高炉反应器的优点是热效率高、技术完善,设备已大型化、长寿化,单座高炉年产铁最高可达400 万t左右,一代炉役的产铁量可达5000万t以上,可以说,没有现代化的大型高炉就没有现代化的钢铁工业大生产。
但是在它日益完善和大型化的同时,也带来了流程长、投资大以及污染环境等问题。
高炉工艺流程存在以下问题:一是高炉必须要用较多焦炭,而炼焦煤越来越少,焦炭越来越贵;二是环境污染严重,特别是焦炉的水污染物粉尘排放烧结的SO2粉尘排放,高炉的CO2排放很高;三是传统炼铁流程长,投资大;四是从铁、烧、焦全系统看重复加热、降温,增碳、脱碳,资源、能源循环使用率低,热能利用不合理。
高炉法虽然仍是当今炼铁生产的主体流程,但非高炉炼铁法已成为炼铁技术发展的方向。
非高炉炼铁技术或称非焦炼铁技术是当今钢铁生产工艺中最受关注的技术之一。
依产品的形态不同,非高炉炼铁技术可分为熔融还原与直接还原两种工艺方法。
随着世界上废钢铁积累日益减少,电炉流程迅速发展,这就要求采用直接还原新工艺,生产出的海绵铁供电炉炼钢。
此外,由于炼焦煤资源日渐短缺,焦炉逐渐老化以及人们对焦炉污染日益关注,八十年代以来,各发达国家纷纷谋求开发另外的无焦炼铁工艺——熔融还原,其中Corex流程已实现工业化生产。
我国煤基直接还原炼铁工艺发展
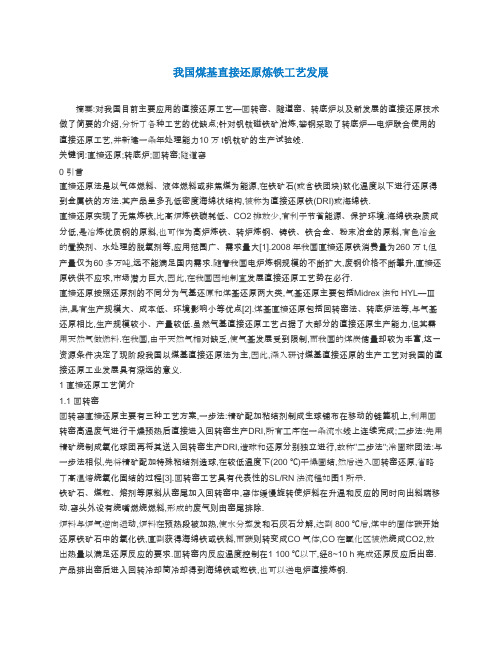
我国煤基直接还原炼铁工艺发展摘要:对我国目前主要应用的直接还原工艺—回转窑、隧道窑、转底炉以及新发展的直接还原技术做了简要的介绍,分析了各种工艺的优缺点;针对钒钛磁铁矿冶炼,攀钢采取了转底炉—电炉联合使用的直接还原工艺,并新建一条年处理能力10万t钒钛矿的生产试验线.关键词:直接还原;转底炉;回转窑;隧道窑0 引言直接还原法是以气体燃料、液体燃料或非焦煤为能源,在铁矿石(或含铁团块)软化温度以下进行还原得到金属铁的方法.其产品呈多孔低密度海绵状结构,被称为直接还原铁(DRI)或海绵铁.直接还原实现了无焦炼铁,比高炉炼铁碳耗低、CO2排放少,有利于节省能源、保护环境.海绵铁杂质成分低,是冶炼优质钢的原料,也可作为高炉炼铁、转炉炼钢、铸铁、铁合金、粉末冶金的原料,有色冶金的置换剂、水处理的脱氧剂等,应用范围广、需求量大[1].2008年我国直接还原铁消费量为260 万t,但产量仅为60多万吨,远不能满足国内需求.随着我国电炉炼钢规模的不断扩大,废钢价格不断攀升,直接还原铁供不应求,市场潜力巨大,因此,在我国因地制宜发展直接还原工艺势在必行.直接还原按照还原剂的不同分为气基还原和煤基还原两大类,气基还原主要包括Midrex法和HYL—Ⅲ法,具有生产规模大、成本低、环境影响小等优点[2].煤基直接还原包括回转窑法、转底炉法等,与气基还原相比,生产规模较小、产量较低.虽然气基直接还原工艺占据了大部分的直接还原生产能力,但其需用天然气做燃料.在我国,由于天然气相对缺乏,使气基发展受到限制,而我国的煤炭储量却较为丰富,这一资源条件决定了现阶段我国以煤基直接还原法为主,因此,深入研讨煤基直接还原的生产工艺对我国的直接还原工业发展具有深远的意义.1 直接还原工艺简介1.1 回转窑回转窑直接还原主要有三种工艺方案,一步法:精矿配加粘结剂制成生球铺布在移动的链篦机上,利用回转窑高温废气进行干燥预热后直接进入回转窑生产DRI,所有工序在一条流水线上连续完成;二步法:先用精矿烧制成氧化球团再将其送入回转窑生产DRI,造球和还原分别独立进行,故称"二步法";冷固球团法:与一步法相似,先将精矿配加特殊粘结剂造球,在较低温度下(200 ℃)干燥固结,然后送入回转窑还原,省略了高温焙烧氧化固结的过程[3].回转窑工艺具有代表性的SL/RN法流程如图1所示.铁矿石、煤粒、熔剂等原料从窑尾加入回转窑中,窑体缓慢旋转使炉料在升温和反应的同时向出料端移动.窑头外设有烧嘴燃烧燃料,形成的废气则由窑尾排除.炉料与炉气逆向运动,炉料在预热段被加热,使水分蒸发和石灰石分解,达到800 ℃后,煤中的固体碳开始还原铁矿石中的氧化铁,直到获得海绵铁或铁料,而碳则转变成CO气体,CO在氧化区被燃烧成CO2,放出热量以满足还原反应的要求.回转窑内反应温度控制在1 100 ℃以下,经8~10 h完成还原反应后出窑.产品排出窑后进入回转冷却筒冷却得到海绵铁或粒铁,也可以送电炉直接炼钢.与高炉工艺相比较,回转窑工艺设备简单,投资少,适用于地方钢铁工业,弥补了高炉—转炉工艺的不足,此外,回转窑还适用于复合矿冶炼,冶金灰尘及各种工业废渣的回收利用,减少环境污染,降低了钢铁生产能耗.同时,回转窑工艺也存在一些缺点,包括窑内结圈、还原温度低(1 100 ℃以下)、流程长、对块矿或球团矿冷强度要求高、要求使用低硫煤等[4].我国山东鲁中矿山公司通过采取提高冷固烧结球团的冷热态强度、加强还原煤的选择和管理、优化回转窑的送风、抛煤、控温温度等措施,预防并降低回转窑结圈,取得了较好的收效.图1 SL/RN法工艺流程1.2 隧道窑隧道窑工艺即将精矿粉、煤粉、石灰石粉,按照一定的比例和装料方法,分别装入还原罐中,然后把罐放在罐车上,推入条形隧道窑中或把罐直接放到环形轮窑中,料罐经预热到1 150 ℃加热焙烧和冷却之后,得到直接还原铁.目前江苏永钢集团拥有两条260 m长煤气隧道窑,为亚洲最长隧道窑.隧道窑生产海绵铁工艺流程如图2所示.图2 隧道窑生产海绵铁工艺流程煤基隧道窑直接还原工艺具有技术成熟、作简单的特点,可因地制宜采用此工艺,利用当地小型分散的铁矿及煤矿资源优势,发展直接还原铁生产,为电炉提供优质原料.但是,总体上讲,我国隧道窑直接还原中存在生产规模较小、能耗高、污染严重、缺乏稳定的原料供应渠道等问题[5],所以,提高机械化程度、改变原料入炉方式、改进燃料及其燃烧、增设余热回收等成为各厂家不断努力改进工艺的方向.我国已建成或正在建设的隧道窑有100多座,约70多个单位规划建设产能5~30 万t/a的隧道窑直接还原铁厂,在不断总结实践经验的基础上,改进现行工艺,开发出诸如大型隧道窑直接还原、AMR—CBI隧道窑直接还原工艺、宽体球状海绵铁隧道窑、L-S快速还原工艺等多种新技术,掀开了隧道窑工艺规模扩大、产能提高、机械及自动化提升的序幕.1.3 转底炉转底炉煤基直接还原是最近几十年间发展起来的炼铁新技术,代表工艺为Fastmet,它由美国Midrex公司与日本神户制钢于20世纪60年发,是采用环形转底炉生产直接还原铁的一种方法.经过多年的半工业性试验和深入的可行性研究,现已完成工艺作参数和装置设计的优化.Fastmelt和ITmk3工艺是在此基础上增加对直接还原铁的处理.图3显示了这三种以转底炉为主体的直接还原工艺流程.图3 转底炉直接还原工艺流程煤粉与铁精粉按比例混匀制成球团,干燥后以1~3层球铺放在转底炉床面,随着炉底的旋转,炉料依次经过预热区、还原区和冷却区.还原区内球团被加热到1 250~1 350 ℃,由于煤粉与铁氧化物紧密接触,铁氧化铁被碳迅速还原成DRI,成品在800~1 000 ℃左右连续从转底炉卸出.球团矿在炉底停留8~30 min,这取决于原料特性、料层厚度及其他因素,成品可作电炉热装炉料或者转炉炉料,也可冷却或生产热压块(HBI).Fastmet工艺技术特点:①在高温敞焰下加热实现快速还原,反应时间只需10~20 min,生产效率高;②原料来源广泛,铁原料方面,除使用高品位粉矿、精矿外,还可用氧化铁皮、代油铁泥、炼钢粉尘、含En、Pb、As等有害杂质的铁矿等;还原剂方面,除煤以外焦末、沥青均可利用,不必担心出现结圈问题;③炉料相对炉底静止,对炉料强度要求不高;④废气中含有大量显热,可用作预热空气、干燥原料等[6]. Fastmelt工艺流程基本与Fastmet一致,只是在后续添加一个熔炉来生产高质量的液态铁水.Itmk3工艺是使金属化球团在转底炉中还原时熔化,生成铁块(Nuggets),同时脉石也熔化,形成渣铁分离.当然转底炉也存在着设备复杂、炉内气氛难控制、传热效率低以及对还原剂硫含量要求严格的缺点.就目前转底炉工艺开发的水平和规模而论,与高炉还有较大差距,但仍存在发展的广阔空间,天津荣程联合钢铁集团已兴建一条100万t级Fastmet生产线,建成目前世界最大的转底炉.另外,用转底炉可处理一些特殊铁矿,如含锌、铅、砷等有害杂质,或含镍、钒、钛等有用元素,均可利用转底炉的工艺优势,或高温挥发,或选择性还原,配合后续工艺,实现资源综合利用.马钢尘泥脱锌转底炉工程项目于2008年5月开工建设,2009年7月6日正式竣工投产,建成了整套转底炉(RHF)脱锌工艺技术装置,不仅解决了含锌尘泥循环利用的后顾之忧,而且将综合利用技术上升到高品质资源化水平.1.4 其他新工艺1.4.1 PF法煤基竖炉直接还原工艺中冶集团北京冶金设备研究设计总院,结合国内情况创新发明了PF法竖炉直接还原工艺.PF法是在吸收K-M法外热式竖炉煤基直接还原工艺的经验基础上,设计的以一种中国特色的罐式还原炉为主反应器的直接还原法.这种工艺技术可靠,技术经济指标在各种煤基直接还原工艺中属先进水平.PF法直接还原工艺流程如图4所示.图4 PF法直接还原工艺流程PF法直接还原工艺主要特点[1]:1)主体设备选用外热式竖炉,预热、还原、冷却三段根据不同的作用和温度选用不同材质和结构,便于传热和化学反应进行,提高热效率和设备寿命.2)原燃料适用性强,对精矿、还原剂和燃料没有特殊要求.3)采用外配碳工艺,还原剂适当过量,扩大了煤的选用范围,造球工艺也因不定量配入煤粉而简化,球团强度较高,DRI质量较好.4)多个反应罐可并列组成任意规模的还原设备,设计和组织生产灵活.1.4.2 低温快速还原新工艺2004年钢铁研究总院提出了低温快速冶金新工艺.新工艺利用纳米晶冶金技术的特点将铁矿的还原温度降低到700 ℃以下.新流程分为气基和煤基两种方法,工艺流程如图5、图6所示.图5 煤基低温快速还原新工艺图6 气基低温快速还原新工艺煤基法使用煤粉为还原剂,在700℃左右快速还原铁精矿粉;气基法使用还原性气体还原铁精矿粉,还原温度可低于600℃.新工艺具有能耗低、环境友好等特点,省去了烧结或造球工艺,缓解了钢铁行业对焦煤的依赖,符合我国国情[7].2 攀钢现状钒钛磁铁矿是攀西地区的特色资源,与普通矿相比,钒钛矿直接还原温度较高、还原时间较长,还原过程产生特有的膨胀粉化现象,因此,存在竖炉结瘤、流化床失流和黏结、回转窑结圈等技术难题.高炉流程冶炼钒钛矿,只回收了铁和钒,钛进入高炉渣没有回收,造成钛资源的大量流失.2005年以来,攀钢科研人员在充分吸收、借鉴新流程及相关研究成果的基础上,通过大量的试验研究,针对钒钛磁铁矿特点,提出并验证了钒钛磁铁矿"转底炉直接还原—电炉深还原—含钒铁水提钒—含钛炉渣提钛"工艺路线,彻底打通了钒钛矿资源综合利用新工艺流程,稳定获得了质量满足要求的低碳生铁、达到GB3283-87要求的片状V2O5和PTA121质量要求的钛白产品.依托该研究成果,攀钢集团攀枝花钢铁研究院于2008年5月4日正式启动了攀钢10 万t/a钒钛矿资源综合利用新工艺中试线工程项目,新建一条转底炉—熔分电炉联合使用,年处理能力10万t钒钛矿的试验生产线,为更深入地研究实践,实现转底炉处理钒钛矿的规模化生产提供了广阔的平台.中试线工艺流程如图7所示.本流程采用硫含量较低的白马铁精矿,还原剂采用无烟煤煤粉,粘结剂为有机粘结剂,原料混合后经高压压球机压球,生球烘干后进入转底炉系统.球团在转底炉内停留10~30 min后出料,金属化球团直接热装进入熔分电炉,在一定温度下还原后,产出含钒铁水及含钛炉渣.继续对铁水进行脱硫、提钒后,得到半钢、脱硫渣及钒渣,半钢进入铸铁机铸铁,生产出铸铁块.钛渣制取钛白,实验室条件下钛回收率达到80%以上;钒渣制取钒氧化物(V2O5),实验室条件下,钒回收率达到65%以上.与高炉流程相比,转底炉流程采用100%钒钛矿冶炼,克服了高炉流程必须配加普通矿的不足,在当前铁资源紧张的形势下,有助于充分发挥攀西地区资源优势,拉动区域经济发展.此外,转底炉流程的铁精矿不需烧结处理,不使用焦炭,从根本上避免了烧结烟气脱硫、焦煤资源采购困难以及环保压力大等问题.3 结语图7 资源综合利用中试线工艺流程煤炭资源总量丰富、焦煤短缺,铁矿资源储量大、富矿少、贫矿和共生矿多是中国钢铁工业面临的现实状况.这种能源、资源结构给煤基直接还原法生产海绵铁的发展提供了机遇.转底炉直接还原技术由于在生产率、规模化、投资费用、单位成本等方面都占有明显的优势,可作为发展直接还原技术的首选工艺.鉴于转底炉处理钒钛磁铁矿技术尚属世界首创,并无较多的经验借鉴,因此要大力开展针对钒钛磁铁矿直接还原的基础研究工作,在实践中借鉴各种直接还原方法已取得的成果,开拓创新,开创钒钛矿直接还原新纪元.参考文献[1] 陈守明,黄超,张金良.煤基竖炉直接还原工艺//2008年非高炉炼铁年会文集.中国金属学会,2008:132-135.[2] 杨婷,孙继青.世界直接还原铁发展现状及分析.世界金属导报,2006.[3] 刘国根,邱冠周,王淀佐.直接还原炼铁中的粘结剂.矿产综合利用,2001(4):27-30.[4] 韩跃新,高鹏,李艳军.白云鄂博氧化矿直接还原综合利用前景.金属矿山,2009 (5):1-6.[5] 魏国,赵庆杰,沈峰满,等.非高炉生产技术进步//2004年全国炼铁生产技术暨炼铁年会文集.2004:878-882.[6] 陶晋. 环形转底炉直接还原工艺现状及发展趋势. 冶金信息工作, 1997.6.[7] 郭培民,赵沛,张殿伟.低温快速还原炼铁新技术特点及理论研究.炼铁,2007,26(1): 57-60.来源:攀枝花钢铁研究院网站。
我国煤基隧道窑直接还原铁生产现状及发展
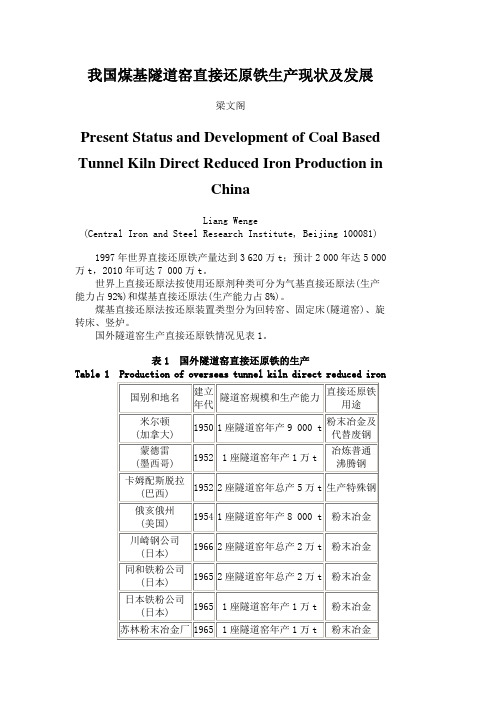
我国煤基隧道窑直接还原铁生产现状及发展梁文阁Present Status and Development of Coal Based Tunnel Kiln Direct Reduced Iron Production inChinaLiang Wenge(Central Iron and Steel Research Institute, Beijing 100081)1997年世界直接还原铁产量达到3 620万t;预计2 000年达5 000万t,2010年可达7 000万t。
世界上直接还原法按使用还原剂种类可分为气基直接还原法(生产能力占92%)和煤基直接还原法(生产能力占8%)。
煤基直接还原法按还原装置类型分为回转窑、固定床(隧道窑)、旋转床、竖炉。
国外隧道窑生产直接还原铁情况见表1。
表1 国外隧道窑直接还原铁的生产Table 1 Production of overseas tunnel kiln direct reduced iron我国在50年代末和60年代初粉末冶金工业普遍采用倒焰窑和反射炉等小批量地生产直接还原铁,用于生产还原铁粉。
1965年上海粉末冶金厂建立我国第1座38.5 m隧道窑开始成批量地生产直接还原铁。
70年代最长的隧道窑为68 m。
80年代武钢粉末冶金公司建成1座105 m 隧道窑,90年代武钢粉末冶金公司又建成1座154 m隧道窑。
1997年马钢铁合金厂建成1座166 m隧道窑,到目前为止国内建有约40座小型隧道窑。
1994年全国生产直接还原铁约5万t用于生产还原铁粉。
我国煤基回转窑直接还原法于1989年在福州特钢厂40 m回转窑工业试验成功后,先后在辽宁喀左、天津钢管公司、山东鲁中矿公司、吉林桦甸、北京密云铁矿建设6座回转窑,总生产能力为46.2万t。
回转窑法工艺成熟、机械化自动化水平高,产品质量好,能耗低,但是由于投资大,在经济不发达地区其发展受到一定限制。
直接还原铁技术

直接还原铁技术直接还原铁是铁矿在固态条件下直接还原为铁,可以用来作为冶炼优质钢、特殊钢的纯净原料,也可作为铸造、铁合金、粉末冶金等工艺的含铁原料。
这种工艺是不用焦碳炼铁,原料也是使用冷压球团不用烧结矿,所以是一种优质、低耗、低污染的炼铁新工艺,也是全世界钢铁冶金的前沿技术之一。
直接还原炼铁工艺有气基法和煤基法两种,按主体设备可分为竖炉法、回转窑法、转底炉法、反应罐法、罐式炉法和流化床法等。
目前,世界上90%以上的直接还原铁产量是用气基法生产出来的。
但是天然气资源有限、价高,使生产量增长不快。
用煤作还原剂在技术上也已过关,可以用块矿,球团矿或粉矿作铁原料(如竖炉、流化床、转底炉和回转窑等)。
但是,因为要求原燃料条件高(矿石品位要大于66%,含SiO2+Al2O3杂质要小于3%,煤中灰分要低等),规模小,设备寿命低,生产成本高和某些技术问题等原因,致使直接还原铁生产在全世界没有得到迅速发展。
因此,高炉炼铁生产工艺将在较长时间内仍将占有主导地位。
1.直接还原铁的质量要求直接还原铁是电炉冶炼优质钢种的好原料,所以要求的质量要高(包括化学成份和物理性能),且希望其产品质量要均匀、稳定。
1.1 化学成份直接还原铁的含铁量应大于90%,金属化率要>90%。
含SiO2每升高1%,要多加2%的石灰,渣量增加30Kg/t,电炉多耗电18.5kwh。
所以,要求直接还原铁所用原料含铁品位要高:赤铁矿应>66.5%,磁铁矿>67.5%,脉石(SiO2+Al2O3)量<3%~5%。
直接还原铁的金属化率每提高1%,可以节约能耗8~10度电/t。
直接还原铁含C<0.3%,P<0. 03%,S<0.03%,Pb、Sn、As、Sb、Bi等有害元素是微量。
1.2 物理性能回转窑、竖炉、旋转床等工艺生产的直接还原铁是以球团矿为原料,要求粒度在5~30mm。
隧道窑工艺生产的还原铁大多数是瓦片状或棒状,长度为250~380mm,堆密度在1.7~2. 0t/m³。
直接还原炼铁工艺技术综述

2 直接还原工 艺技术发展 的动 因与障碍
推动 直接 还原 工艺 技术 发展 的客 观原 因有 :
观需 要 发展 直接 还原 铁 来 补 充 。 与使 用 废 钢 相 比 ,
电炉使用直接还原铁的好处有 :①还原铁有害元素 (u i r o n s b i 含量很 低 , C 、N 、C 、M 、S 、A 、P 、B ) 能够稀释 、降低钢 中的有害元素;②使用直接还原
表 1 直 接 还 原 工 艺 分 类表
T b 1 T e i c e sn t t ft e o t u fDR n t e wol a . h n r a i g sa e o h u p to Ii h rd
收 稿 日期 :20 一 0 2 06 l— 4
作者简介 : 全
缺陷及工业化进展情况 ,分析了世界直接还原工艺技术发展的动因 、现状与趋势 。 关键词 :直接还原 ;D I B R ;H I 中图分类号 :T 5 3 文献标识 码 :A 文章编号 :10 - 3 8 ( 07 2 0 7 5 F 3 0 6 0 0 2 0 )0 - 5 - 0 0
Su m a y o r c d to Pr c s o r n m e tng m r fDie tRe uc i n o e sflrya dm nn cd n ,K n igMe l ryC l e , Mea ug n iigA a ay u m n t l g o gg l au l K n ig u n n6 0 3 ,C ia u m n ,Y n a 5 0 3 hn )
铁 可 实现 连续 装料 、成 渣迅 速 、连续 融 化及 熔池 沸
1 )世界多数国家严重 缺乏焦煤 ,但其 中不少 国家拥有优质丰富 的铁矿 以及 天然气和非焦煤 资
煤基竖炉直接还原技术

武汉科思瑞迪科技有限公司(以下简称“科思瑞迪”)坐落于武汉市东湖新技术开发区,是以武汉桂坤科技有限公司为主体,整合相关社会资源,汇集了冶金、工业炉、机电技术等各专业技术人才,集数十年研发、工程及生产经验,组建的一家专业从事煤基竖炉直接还原技术的开发、推广及应用的科技公司。
该公司的技术及成套核心设施已经在中国、越南、缅甸等国的工程项目中得到了应用,取得了良好的社会及经济效益。
煤基竖炉直接还原技术李森蓉李建涛(武汉科思瑞迪科技有限公司)摘要:本文对煤基竖炉直接还原技术从工艺流程、技术指标、技术特点等方面进行了较为详实的介绍和分析;该技术生产海绵铁的质量有保证,市场发展前景可期,市场竞争力强。
关键词:煤基竖炉直接还原铁技术特点产品质量直接还原是指铁矿石或含铁氧化物在低于熔化温度下还原成金属产品的炼铁过程;其所得的产品称为直接还原铁,简称DRI(Direct Reduction Iron),也称海绵铁。
优质DRI由于其成分稳定,有害元素含量低,粒度均匀,不仅可以补充废钢资源的不足,而且还可以作为电炉炼钢的原料以及转炉炼钢的冷却剂,对保证钢材的质量特别是合金钢的质量,起着不可替代的作用,是冶炼特钢的优质原料;同时,高品位DRI还可以供粉末冶金行业使用【1】。
直接还原铁生产方法中,主要分为气基法和煤基法。
由于我国天然气资源缺乏,但是煤炭资源丰富,煤基直接还原技术成为我国直接还原铁生产的重要工艺方法【2】。
煤基直接还原是指直接以廉价的非焦煤作还原剂生产直接还原铁的方法。
在我国煤基直接还原技术主要是回转窑法和隧道窑法【3】,近几年也相继建设了多座转底炉装置,同时也建设了一些煤基连续式竖炉装置。
在直接还原技术日益发展、大力提倡环保节能减排的今天,一些新的更先进的直接还原工艺及设备被迫切需要【4,5】。
煤基竖炉直接还原技术是一项符合中国能源结构特点的可大型化生产高品质海绵铁的直接还原铁生产技术【6】,可广泛用于处理高品位铁精粉制取高纯度还原铁粉用于粉末冶金领域,也可用于处理普通品位的铁精粉制取炼钢用海绵铁,处理复合铁矿生产普通铁水及提取钒、钛、硼等高附加值资源。
011-天津钢管直接还原铁生产回顾与炼钢应用陶江善汇总

一、天津钢管直接还原铁生产情况回顾 二、直接还原铁在炼钢厂中的使用
天津钢管煤基回转窑直接还原生产线是原冶金部“九五”重大 科技攻关项目,全套设备技术从英国戴维公司(DAVY)引进 ,设计年产直接还原铁30万吨,建有两条φ5×80m的回转窑 生产线,是我国最大的煤基回转窑还原铁生产基地,由于采用 了国外先进工艺技术和关键设备,其生产水平和自动控制系统 世界一流。 该项目于1993年9月通过国家级审批,95年完成工厂设计, 96年9月完成设备安装,1996年11月直接还原铁项目开始热 负荷试车,1997年10月完成了对外合同规定的技术性能指标 的考核,1999年4月,直接还原铁工程项目通过了国家总体验 收。 2008年10月,因国外长协矿合同终止,缺乏优质低价原料供 应而停产至今。
4.1海绵铁最优加入量的确定
⑴2004年,炼钢厂具备了废钢、铁水、海绵铁三大料型进行 配料的条件,为了取得高效的产能和低廉的制造成本,炼钢厂 以优化配料作为切入点,降低冶炼成本。 ⑵在铁水固定(单罐重~40吨)的情况下,通过加入不同量的 海绵铁进行冶炼过程指标测算,以低电耗、短周期为最终确定 最优海绵铁加入量。 方案1 废钢+铁水+海绵铁(1870炉数据统计)
项目 年份
1997 1998 1999 2000 2001 2002 2003 2004 2005 2006
表1 天津钢管还原铁厂历年直接还原铁产量及物耗指标 DRI产量 矿耗 煤耗 电耗 金属化率 Wt Kg/t Kg/t Kwh/t % 6.02 8.39 10.6 13.58 11.25 22.04 28.55 33.23 31.42 21.23 1490 1570 1560 1466 1440 1446 1480 1490 1489 1486 950 1040 1026 930 970 919 868 900 900 900 143.3 155.6 161.9 133.6 114 95.86 86.75 90.12 89.46 91.3 92.6 93.8 93.7 92.3 92.8 93.1 92.21 911.3 配煤比例调整
煤基直接还原铁综述

低品位铁矿石煤基直接还原铁摘要:文章介绍介绍了直接还原铁的两种生产方法,并联系国内实际着重介绍煤基直接还原法,联系我国铁矿石的供需现状,通过分析近年来直接还原铁发展状况,提出低品位铁矿石用褐煤半焦做还原剂生产直接还原铁的思路。
直接还原是指用气体或固体还原剂在低于铁矿石软化温度下,在反应装置内将铁矿石还原成金属铁的方法。
其产品称直接还原铁,这种铁保留了失氧前的外形,因失氧形成了大量微孔隙,显微镜下形似海绵结构,故又称海绵铁。
[4]直接还原铁(DRI)因质地纯净、成分稳定,是一种替代废钢、冶炼优质钢和特殊钢的理想原料。
很多用废钢不能生产的特种钢都能用海绵铁生产出来[3].一、直接还原铁的生产方法直接还原工艺根据还原剂不同可分为气基直接还原和煤基直接还原。
气基直接还原工艺以天然气为主要还原剂,包括竖炉、反应罐和流化床流程。
煤基直接还原以煤为主要能源,主要是使用回转窑为主体设备的流程[1]。
目前运行中的气基直接还原设备有三种。
第一种是竖炉,是成熟的主导工艺,以MIDREX 流程为代表,具有容易控制、产品质量好、能耗低、环境污染轻、生产率高等特点,竖炉流程占据了大部分直接还原生产能力[6]。
第二种是反应罐,使用反应罐的流程只有HYL法。
反应罐采用落后的固定床非连续生产模式,证处于被逐渐淘汰的过程中。
第三种是流化床,目前唯一的代表是FIOR法[1]。
煤基直接还原法工艺主要包括回转窑法、转底炉法、隧道窑法。
只有回转窑流程拥有可观的生产能力,具有代表性的回转窑流程是SL-RN法。
推动直接还原工艺技术发展的客观原因主要有以下几点;1)世界多数国家严重缺少焦煤,但其中不少国家拥有优质丰富的铁矿以及天然气和非焦煤资源,可以因地制宜地发展直接还原来解决生铁资源问题。
委内瑞拉、墨西哥、伊朗等国具有丰富的天然气及优质铁矿,主要发展竖炉气基直接还原工艺,而南非、印度、新西兰等国家具有丰富的烟煤及优质铁矿,则主要发展回转窑煤基直接还原工艺。
煤基竖炉直接还原技术

武汉科思瑞迪科技有限公司(以下简称“科思瑞迪”)坐落于武汉市东湖新技术开发区,是以武汉桂坤科技有限公司为主体,整合相关社会资源,汇集了冶金、工业炉、机电技术等各专业技术人才,集数十年研发、工程及生产经验,组建的一家专业从事煤基竖炉直接还原技术的开发、推广及应用的科技公司。
该公司的技术及成套核心设施已经在中国、越南、缅甸等国的工程项目中得到了应用,取得了良好的社会及经济效益。
煤基竖炉直接还原技术李森蓉李建涛(武汉科思瑞迪科技有限公司)摘要:本文对煤基竖炉直接还原技术从工艺流程、技术指标、技术特点等方面进行了较为详实的介绍和分析;该技术生产海绵铁的质量有保证,市场发展前景可期,市场竞争力强。
关键词:煤基竖炉直接还原铁技术特点产品质量直接还原是指铁矿石或含铁氧化物在低于熔化温度下还原成金属产品的炼铁过程;其所得的产品称为直接还原铁,简称DRI(Direct Reduction Iron),也称海绵铁。
优质DRI由于其成分稳定,有害元素含量低,粒度均匀,不仅可以补充废钢资源的不足,而且还可以作为电炉炼钢的原料以及转炉炼钢的冷却剂,对保证钢材的质量特别是合金钢的质量,起着不可替代的作用,是冶炼特钢的优质原料;同时,高品位DRI还可以供粉末冶金行业使用【1】。
直接还原铁生产方法中,主要分为气基法和煤基法。
由于我国天然气资源缺乏,但是煤炭资源丰富,煤基直接还原技术成为我国直接还原铁生产的重要工艺方法【2】。
煤基直接还原是指直接以廉价的非焦煤作还原剂生产直接还原铁的方法。
在我国煤基直接还原技术主要是回转窑法和隧道窑法【3】,近几年也相继建设了多座转底炉装置,同时也建设了一些煤基连续式竖炉装置。
在直接还原技术日益发展、大力提倡环保节能减排的今天,一些新的更先进的直接还原工艺及设备被迫切需要【4,5】。
煤基竖炉直接还原技术是一项符合中国能源结构特点的可大型化生产高品质海绵铁的直接还原铁生产技术【6】,可广泛用于处理高品位铁精粉制取高纯度还原铁粉用于粉末冶金领域,也可用于处理普通品位的铁精粉制取炼钢用海绵铁,处理复合铁矿生产普通铁水及提取钒、钛、硼等高附加值资源。
- 1、下载文档前请自行甄别文档内容的完整性,平台不提供额外的编辑、内容补充、找答案等附加服务。
- 2、"仅部分预览"的文档,不可在线预览部分如存在完整性等问题,可反馈申请退款(可完整预览的文档不适用该条件!)。
- 3、如文档侵犯您的权益,请联系客服反馈,我们会尽快为您处理(人工客服工作时间:9:00-18:30)。
低品位铁矿石煤基直接还原铁摘要:文章介绍介绍了直接还原铁的两种生产方法,并联系国内实际着重介绍煤基直接还原法,联系我国铁矿石的供需现状,通过分析近年来直接还原铁发展状况,提出低品位铁矿石用褐煤半焦做还原剂生产直接还原铁的思路。
直接还原是指用气体或固体还原剂在低于铁矿石软化温度下,在反应装置内将铁矿石还原成金属铁的方法。
其产品称直接还原铁,这种铁保留了失氧前的外形,因失氧形成了大量微孔隙,显微镜下形似海绵结构,故又称海绵铁。
[4]直接还原铁(DRI)因质地纯净、成分稳定,是一种替代废钢、冶炼优质钢和特殊钢的理想原料。
很多用废钢不能生产的特种钢都能用海绵铁生产出来[3].一、直接还原铁的生产方法直接还原工艺根据还原剂不同可分为气基直接还原和煤基直接还原。
气基直接还原工艺以天然气为主要还原剂,包括竖炉、反应罐和流化床流程。
煤基直接还原以煤为主要能源,主要是使用回转窑为主体设备的流程[1]。
目前运行中的气基直接还原设备有三种。
第一种是竖炉,是成熟的主导工艺,以MIDREX 流程为代表,具有容易控制、产品质量好、能耗低、环境污染轻、生产率高等特点,竖炉流程占据了大部分直接还原生产能力[6]。
第二种是反应罐,使用反应罐的流程只有HYL法。
反应罐采用落后的固定床非连续生产模式,证处于被逐渐淘汰的过程中。
第三种是流化床,目前唯一的代表是FIOR法[1]。
煤基直接还原法工艺主要包括回转窑法、转底炉法、隧道窑法。
只有回转窑流程拥有可观的生产能力,具有代表性的回转窑流程是SL-RN法。
推动直接还原工艺技术发展的客观原因主要有以下几点;1)世界多数国家严重缺少焦煤,但其中不少国家拥有优质丰富的铁矿以及天然气和非焦煤资源,可以因地制宜地发展直接还原来解决生铁资源问题。
委内瑞拉、墨西哥、伊朗等国具有丰富的天然气及优质铁矿,主要发展竖炉气基直接还原工艺,而南非、印度、新西兰等国家具有丰富的烟煤及优质铁矿,则主要发展回转窑煤基直接还原工艺。
2)随着电炉短流程生产线的兴起,对废钢的需求日益增长,而发展中国家由于废钢量不足,客观需要发展直接还原铁来补充[12]。
与使用废钢相比,电炉使用直接还原铁的好处有:①还原铁有害元素(Cu、Ni、Cr、Mo、Sn、As、Pb、Bi)含量很低,能够稀释、降低钢中的有害元素;②用直接还原铁可实现连续装料、成渣迅速、连续融化及熔池沸腾,促进脱气,降低钢中N含量,利于快速形成泡沫渣,从而减少钢中夹杂物;③缩短电炉精炼周期,提高Ni、Mo等有价元素的收率。
3)直接还原低碳海绵铁可用于直接生产电工纯铁、铁氧体及工业铁料,有利于电炉钢厂发展精品、提高产品附加值[7]。
4)直接还原—电炉—连铸—轧制的短流程生产规模小、建设周期短、投资省、生产灵活,便于按市场调整产品种类和数量[11],可为资金和技术缺乏的发展中国家提供可以代替传统资金和技术密集型的高炉—转炉长流程,因地制宜地发展本国的钢铁工业,不仅对发展中国家有极大的吸引力,而且对为解决地区性钢材需求和品种调剂的发达国家也有吸引力。
二、我国铁矿石资源供需现状2001年我国铁矿石资源量581.19亿吨,居世界第四位,但是铁矿石品位比世界品位低11%,而且难采难选。
我国铁矿石资源的特点:一是贫矿多,贫矿储量占总储量的80%;二是多元素共生的复合矿石较多;三是磁铁矿多。
此外矿体复杂,有些贫矿床上部为赤铁矿,下部为磁铁矿。
我国铁矿石资源无法满足钢铁行业迅猛发展的需要,近几年我国铁矿进口呈高比率增长,2005年我国钢产量为34936万吨,生铁33040万吨,自产铁矿石42050万吨,进口铁矿石27256万吨。
进口矿来自18个国家,进口国家按数量依次为澳大利亚、巴西、印度、南非、秘鲁等国。
虽然海外供应商不断扩张其矿石开采能力,但其扩张速度依然满足不了中国市场对铁矿石需求的急剧增长。
从全球范围来考虑铁矿石资源供应,优化矿石资源配置,建立长期、稳定的供应基地,锁定供应渠道,应该是中国钢铁工业重点思考解决的问题。
近年来,铁矿石开采供应出现规模巨大的并购活动,基本形成了巴西淡水河谷(CVRD)、英澳合资的必拓和必和力拓三分天下的局面。
三大公司总生产规模35540万吨,约占世界矿石总量的35%,掌控了世界铁矿石海运量的70%[2]。
三、国内外直接还原铁的发展现状Ⅰ世界直接还原工艺发展状况近年来,随着“电炉炼钢短流程”的兴起,作为废钢替代品和生产优质钢不可或缺原料的直接还原铁发展迅速。
从1987年到2006年,世界还原铁的产量如下图所示。
世界直接还原铁产量(资料来源:Midrex公司)直接还原工艺技术发展到现在,无论从产量还是产能看,气体直接还原工艺均占主导地位,约90%,煤基直接还原工艺占10%左右,形成以Midrexa工艺和HYL—Ⅲ工艺为主流的势态[9]。
综观直接还原工艺的历史发展过程及其不同直接还原工艺在世界各地的分布规律,结合世界资源特点、经济形势和环保要求,直接还原工艺发展趋势主要体现在以下几个方面: (1)气基流程日趋成熟以Midrex、HYL一l流程为代表的气基流程,从1970~2002年,长达30多年占据世界直接还原铁产量的90%以上,在取得了极大的成功的同时,为降低成本,提高竞争力,人们孜孜以求的开展了对气基更深入的研究:a)生产设备的大型化是降低生产成本的有效手段,Midrex公司开发了直径7.5m,年产量超过200万t的Midrex气基竖炉。
b)Midrex法的煤气重整设备是十分昂贵的,且易损坏,因而对矿石和煤气的含硫量提出了严格的要求。
针对此难题,委内瑞拉奥里偌科黑色冶金公司利用热海绵铁的催化性和脱硫能力,开发了Midrex的改进型工艺,称为Jex工艺。
Arex工艺无重整炉,竖炉集气体重整与矿石还原于一体。
c)HYL一111可处理含硫量较高的铁矿石,在此基础上,仍在墨西哥进一步开发了改进型HYL一ZR,该工艺没有单独的重整装置,利用新生热海绵铁自身的催化能力进行气体重整。
d)由于Midrex、HYL一m等气基竖炉工艺必须使用块矿或氧化球团,为扩大原料的来源,以铁矿粉为原料的Firunct气基流化床脱颖而出。
利用该工艺生产的直接还原铁HBI曾占到世界直接还原铁产量的5.2%。
虽然采用Flnmet工艺、位于澳大利亚年产250万t由于爆炸事故而永久关闭,但人们致力于开发原料来源广、生产成本低的气基流化床直接还原工艺的热情并未消退。
(2)煤基流程日渐发展从世界能源结构来看,天然气的总储量相当于1200亿t标煤,而世界煤总储量为80000~90000亿t,为天然气的70~80倍,尽管天然气用于直接还原铁能耗最低,但天然气价格和来源不稳定,即使天然气丰富的国家也严格限制天然气的使用。
因此,从能源结构来看,煤基工艺无疑具有更持久的生命力。
近年世界直接还原铁的发展趋势也证明了这一点[10]。
近年来,天然其价格上涨导致煤基直接还原得到更多的关注。
印度近几年新增的直接还原生产能力主要以煤基回转窑工艺为主。
20世纪,直接还原铁快速发展,但煤基工艺占世界直接还原铁产量的比例长期低于10%,2003年达到了10.2%,2006年已达到了19.7%。
预计,随着天然气资源的紧缺,煤基流程比例仍将上升。
Ⅱ中国直接还原工艺发展状况由于我国天然气资源稀缺,且大部分天然气资源集中在西部或西南部,必须优先供城市居民生活使用。
国资委的最新统计资料表明,我国煤炭资源可开采量为天然气的316倍,且煤炭资源分布相对广泛,资源特点决定我国发展直接还原工艺宜以煤基(包括煤制气)为主。
我国煤基工艺发展趋势包括::(1)强化煤基回转窑工艺研究煤基工艺中最成熟的工艺为氧化球团煤基回转窑直接还原工艺(俗称“二步法”),即以氧化球团作为炉料进行直接还原,氧化球团以高品位铁精矿为原料,制备的生球先在高温(1200一1300℃)氧化固结而成。
其优点是在工艺上比较稳妥可靠,生产中影响因素较单一,管理也比较方便。
近年来,由中南大学研发的“一步法”直接还原工艺,减短了工艺流程,省去了高温氧化过程,耐高温设备较少,投资少,工艺流程短,按此工艺设计建厂的北京密云直接还原铁厂,设备运行稳定、效益较好。
(2)完善转底炉工艺转底炉工艺采用精矿(或粉尘、杂料)加还原剂造块、干燥后进行还原,具有反应速度快,原料适应性广的优点,其流程简单、投资低,如能解决产品含硫高和机械设备的稳定性问题,其推广应用值得重视。
(3)积极开展非焦煤制气研究以非焦煤为原料,实现低成本、经济制取还原气是我国发展气基流程的基础,国内已开展过相关研究。
如果能在以煤制气方面取得新的突破,将具有巨大的推广应用价值。
煤基直接还原工艺的特点主要有:①有利于节能和降低对生态环境污染;②不需要炼焦炉和烧结设备,工艺流程简单,故可遏制初期投资;其运行成本也低;③可以利用种类宽泛的原料与煤炭,选址限制少;④煤基直接还原的产品具有高炉生铁同等的品质自上世纪50年代开始,中国对直接还原工艺技术进行了大量研究,但主要集中在回转窑煤基直接还原工艺上。
1989年,原冶金部组织东北工学院、钢铁研究总院、鞍山矿山院等5个单位在福州特殊钢厂2·9 m×40 m回转窑上进行了工业试验,连续运行30天,取得容积利用系数0·413 t/ (m3·d),吨铁煤耗850 kg, DRI中TFe92% ~ 95%,MFe82% ~85%, S<0·03%,金属化率>91%的良好效果。
20世纪70~80年代,在攀枝花钢铁公司410厂 3·4×30m链篦机一回转窑(1万t/a)上进行过多年的钒钛磁铁矿直接还原新流程试验,但最终未能转入工业生产, 1990年曾采用过普通铁矿生产DRI,但也未能继续生产下去。
首钢1986~1987年建成 4·7×74 m回转窑,1988年曾连续生产三个月,容积利用系数达到0·30 t/ (m3·d),金属化率>90%。
2000年,这条直接还原铁生产线通过截窑改造,变成国仙首条年产120万t氧化球团生产线。
中南工业大学80年代末研究开发出复合粘结剂冷固球团“一步法”煤基直接还原工艺。
1991年6月~1993年2月间,中南工业大学、长沙冶金设计研究院、辽宁喀左县三方合作,在攀钢410厂 3·4×30 m链篦机一回转窑上进行900℃预热球团直接入窑的“一步法”煤基直接还原工业试验,并于1994年11月在喀左建成投产一座年产能力为2·5万t、采用一步法链篦机—回转窑的直接还原铁厂,产品TFe>90%,金属化率94%, S<0·03%。
于1997年在山东鲁中冶金矿山公司建设采用该工艺的年产5万tDRI的直接还原铁厂,但后来未能正常生产。