中国煤基隧道窑法直接还原铁(海绵铁)生产新工艺技术
隧道窑生产直接还原铁工艺研究

po oe l e lc a o e ea i t n a d[ rpsd o o e h ut t not t lai t a t s v t f u i fh m lz o r e n S]oD I f R.
K e or u n lkl ; yW ds t n e i DRI r d c r n ;e u e
从表 1 以看 出 ,1 可 )当还原剂 的C固≤7 % ,s 2 含量为 ≥08 .%时 ,直接还原铁 的M、S 均未达 到国家
通 过试 验得 出 :隧道窑 生产 直接 还原铁 用煤 粉 还原 剂必须达 到c 固≥7 %,S< .%的质量要求 。 5 08 同时还原 剂 的配 比也 要加 于控制 ,以能满足 铁矿粉 还原需要 为准 ,以免带 入更多s 含量 ,本试验还原剂
1 前 言
我 国是一 个 废钢 利 用大 国 ,废 钢 的需求 远 大 于 市场 供 给 ,大 量废 钢需 要 从 国外进 口。直 接还 原铁 替代 废钢 是缓 解炼 钢 过程 中废 钢供 应 紧张 的有 效方 法 。昆 钢建有 隧 道窑 直接 还 原铁 生产 线 ,并致 力 于
开展 转 炉使用 隧 道窑 直接 还原 铁 的工 业性试 验 ,并
取得 一 定 的成效 。但 隧道 窑 生产 的直 接还 原铁 始 终 存在 直 接还 原铁 质量 不稳 定 的 问题 ,其 中主要 是金
属化 率 和含硫 量 的波 动过 大 ,直接 影 响到 炼钢 对直 接还 原 铁 的使 用 。为 了解 决 隧道 窑工 艺生 产 直接 还
直接还原铁生产工艺及发展方向

直接还原铁(海绵铁)生产工艺及发展方向习惯上,我们把铁矿石在高炉中先还原冶炼成含碳高的生铁,而后在炼钢炉内氧化,降低含碳量并精炼成钢,这项传统工艺,称作间接炼钢方法;在低于矿石熔化温度下,通过固态还原,把铁矿石炼制成铁的工艺,称作直接炼铁(钢)法或者直接还原法,用这种方法生产出的铁也就称作直接还原铁(即DRI)。
由于这种铁保留了失氧时形成的大量微气孔,在显微镜下观察形似海绵,所以直接还原铁也称之为海绵铁。
一、直接还原铁(海绵铁)的用途直接还原铁是精铁粉在炉内经低温还原形式的低碳多孔状物质,其化学成分稳定,杂质含量少(碳、硅含量低),主要用作电炉炼钢的原料,也可作为转炉炼钢的冷却剂,如果经二次还原还可供粉末冶金用。
一次还原铁粉(海绵铁)的主要用途有:①作为粉末冶金制品的原料,耗用量约占铁粉总耗用量的60~80%;②作为电焊条的原料,在药皮中加入10~70%铁粉可改进焊条的焊接工艺并显著提高熔敷效率;③作为火焰切割的喷射剂,在切割钢制品时,向氧-乙炔焰中喷射铁粉,可改善切割性能,扩大切割钢种的范围,提高可切割厚度;④还可作为有机化学合成中的还原剂、复印机油墨载体等。
近年来由于钢铁产品朝小型轻量化、功能高级化、复合化方向发展,故钢材中非金属材料和有色金属使用比例增加,致使废钢质量不断下降。
废钢作为电炉钢原料,由于其来源不同,化学成分波动很大,而且很难掌握、控制,这给电炉炼钢作业带来了极大的困难。
如果用一定比例的直接还原铁(30~50%)作为稀释剂与废钢搭配不仅可增加钢材的均匀性,还可以改善和提高钢的物理性质,从而达到生产优质钢的目的。
因此,直接还原铁(海绵铁)不仅仅是优质废钢的替代物,还是生产优质钢材必不可少的高级原料(天津无缝钢管公司国外设计中就明确要求必须配50%的直接还原铁(海绵铁))。
根据国外报导,高功率电炉冶炼时,炉料搭配30~50%直接还原铁,生产率提高10~25%,作业率提高25~30%。
直接还原铁生产工艺
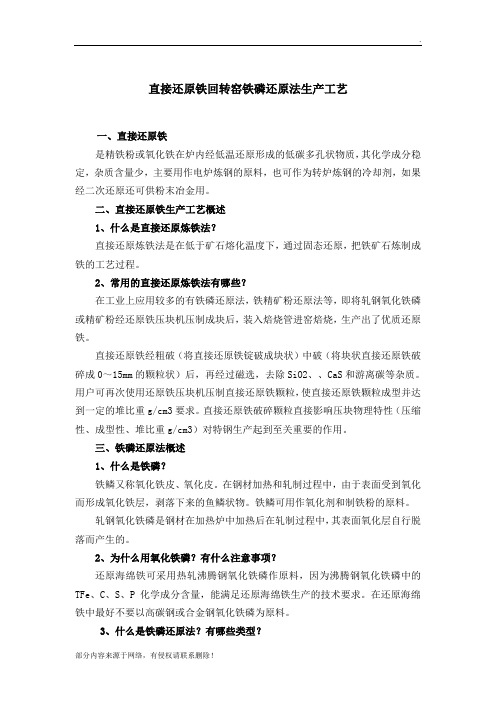
直接还原铁回转窑铁磷还原法生产工艺一、直接还原铁是精铁粉或氧化铁在炉内经低温还原形成的低碳多孔状物质,其化学成分稳定,杂质含量少,主要用作电炉炼钢的原料,也可作为转炉炼钢的冷却剂,如果经二次还原还可供粉末冶金用。
二、直接还原铁生产工艺概述1、什么是直接还原炼铁法?直接还原炼铁法是在低于矿石熔化温度下,通过固态还原,把铁矿石炼制成铁的工艺过程。
2、常用的直接还原炼铁法有哪些?在工业上应用较多的有铁磷还原法,铁精矿粉还原法等,即将轧钢氧化铁磷或精矿粉经还原铁压块机压制成块后,装入焙烧管进窑焙烧,生产出了优质还原铁。
直接还原铁经粗破(将直接还原铁锭破成块状)中破(将块状直接还原铁破碎成0~15mm的颗粒状)后,再经过磁选,去除SiO2、、CaS和游离碳等杂质。
用户可再次使用还原铁压块机压制直接还原铁颗粒,使直接还原铁颗粒成型并达到一定的堆比重g/cm3要求。
直接还原铁破碎颗粒直接影响压块物理特性(压缩性、成型性、堆比重g/cm3)对特钢生产起到至关重要的作用。
三、铁磷还原法概述1、什么是铁磷?铁鳞又称氧化铁皮、氧化皮。
在钢材加热和轧制过程中,由于表面受到氧化而形成氧化铁层,剥落下来的鱼鳞状物。
铁鳞可用作氧化剂和制铁粉的原料。
轧钢氧化铁磷是钢材在加热炉中加热后在轧制过程中,其表面氧化层自行脱落而产生的。
2、为什么用氧化铁磷?有什么注意事项?还原海绵铁可采用热轧沸腾钢氧化铁磷作原料,因为沸腾钢氧化铁磷中的TFe、C、S、P化学成分含量,能满足还原海绵铁生产的技术要求。
在还原海绵铁中最好不要以高碳钢或合金钢氧化铁磷为原料。
3、什么是铁磷还原法?有哪些类型?铁鳞还原法就是以铁鳞为原料的直接还原法生产工艺。
铁鳞还原法生产过程可分为粗还原与精还原。
在粗还原过程中,铁氧化物被还原,铁粉颗粒烧结与渗碳。
增高还原温度或延长保温时间皆有利于铁氧化物还原、铁粉颗粒烧结,但会生产部分渗碳。
鉴于在精还原过程中脱碳困难,在粗还原过程中,控制铁氧化物还原到未渗碳的程度是必要的。
我国煤基直接还原炼铁工艺发展
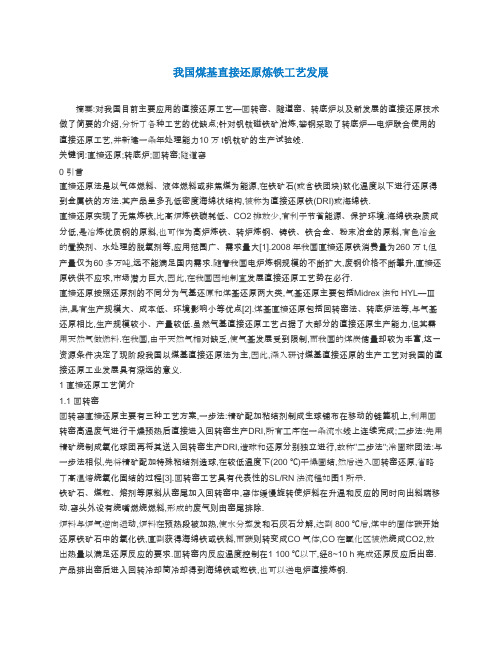
我国煤基直接还原炼铁工艺发展摘要:对我国目前主要应用的直接还原工艺—回转窑、隧道窑、转底炉以及新发展的直接还原技术做了简要的介绍,分析了各种工艺的优缺点;针对钒钛磁铁矿冶炼,攀钢采取了转底炉—电炉联合使用的直接还原工艺,并新建一条年处理能力10万t钒钛矿的生产试验线.关键词:直接还原;转底炉;回转窑;隧道窑0 引言直接还原法是以气体燃料、液体燃料或非焦煤为能源,在铁矿石(或含铁团块)软化温度以下进行还原得到金属铁的方法.其产品呈多孔低密度海绵状结构,被称为直接还原铁(DRI)或海绵铁.直接还原实现了无焦炼铁,比高炉炼铁碳耗低、CO2排放少,有利于节省能源、保护环境.海绵铁杂质成分低,是冶炼优质钢的原料,也可作为高炉炼铁、转炉炼钢、铸铁、铁合金、粉末冶金的原料,有色冶金的置换剂、水处理的脱氧剂等,应用范围广、需求量大[1].2008年我国直接还原铁消费量为260 万t,但产量仅为60多万吨,远不能满足国内需求.随着我国电炉炼钢规模的不断扩大,废钢价格不断攀升,直接还原铁供不应求,市场潜力巨大,因此,在我国因地制宜发展直接还原工艺势在必行.直接还原按照还原剂的不同分为气基还原和煤基还原两大类,气基还原主要包括Midrex法和HYL—Ⅲ法,具有生产规模大、成本低、环境影响小等优点[2].煤基直接还原包括回转窑法、转底炉法等,与气基还原相比,生产规模较小、产量较低.虽然气基直接还原工艺占据了大部分的直接还原生产能力,但其需用天然气做燃料.在我国,由于天然气相对缺乏,使气基发展受到限制,而我国的煤炭储量却较为丰富,这一资源条件决定了现阶段我国以煤基直接还原法为主,因此,深入研讨煤基直接还原的生产工艺对我国的直接还原工业发展具有深远的意义.1 直接还原工艺简介1.1 回转窑回转窑直接还原主要有三种工艺方案,一步法:精矿配加粘结剂制成生球铺布在移动的链篦机上,利用回转窑高温废气进行干燥预热后直接进入回转窑生产DRI,所有工序在一条流水线上连续完成;二步法:先用精矿烧制成氧化球团再将其送入回转窑生产DRI,造球和还原分别独立进行,故称"二步法";冷固球团法:与一步法相似,先将精矿配加特殊粘结剂造球,在较低温度下(200 ℃)干燥固结,然后送入回转窑还原,省略了高温焙烧氧化固结的过程[3].回转窑工艺具有代表性的SL/RN法流程如图1所示.铁矿石、煤粒、熔剂等原料从窑尾加入回转窑中,窑体缓慢旋转使炉料在升温和反应的同时向出料端移动.窑头外设有烧嘴燃烧燃料,形成的废气则由窑尾排除.炉料与炉气逆向运动,炉料在预热段被加热,使水分蒸发和石灰石分解,达到800 ℃后,煤中的固体碳开始还原铁矿石中的氧化铁,直到获得海绵铁或铁料,而碳则转变成CO气体,CO在氧化区被燃烧成CO2,放出热量以满足还原反应的要求.回转窑内反应温度控制在1 100 ℃以下,经8~10 h完成还原反应后出窑.产品排出窑后进入回转冷却筒冷却得到海绵铁或粒铁,也可以送电炉直接炼钢.与高炉工艺相比较,回转窑工艺设备简单,投资少,适用于地方钢铁工业,弥补了高炉—转炉工艺的不足,此外,回转窑还适用于复合矿冶炼,冶金灰尘及各种工业废渣的回收利用,减少环境污染,降低了钢铁生产能耗.同时,回转窑工艺也存在一些缺点,包括窑内结圈、还原温度低(1 100 ℃以下)、流程长、对块矿或球团矿冷强度要求高、要求使用低硫煤等[4].我国山东鲁中矿山公司通过采取提高冷固烧结球团的冷热态强度、加强还原煤的选择和管理、优化回转窑的送风、抛煤、控温温度等措施,预防并降低回转窑结圈,取得了较好的收效.图1 SL/RN法工艺流程1.2 隧道窑隧道窑工艺即将精矿粉、煤粉、石灰石粉,按照一定的比例和装料方法,分别装入还原罐中,然后把罐放在罐车上,推入条形隧道窑中或把罐直接放到环形轮窑中,料罐经预热到1 150 ℃加热焙烧和冷却之后,得到直接还原铁.目前江苏永钢集团拥有两条260 m长煤气隧道窑,为亚洲最长隧道窑.隧道窑生产海绵铁工艺流程如图2所示.图2 隧道窑生产海绵铁工艺流程煤基隧道窑直接还原工艺具有技术成熟、作简单的特点,可因地制宜采用此工艺,利用当地小型分散的铁矿及煤矿资源优势,发展直接还原铁生产,为电炉提供优质原料.但是,总体上讲,我国隧道窑直接还原中存在生产规模较小、能耗高、污染严重、缺乏稳定的原料供应渠道等问题[5],所以,提高机械化程度、改变原料入炉方式、改进燃料及其燃烧、增设余热回收等成为各厂家不断努力改进工艺的方向.我国已建成或正在建设的隧道窑有100多座,约70多个单位规划建设产能5~30 万t/a的隧道窑直接还原铁厂,在不断总结实践经验的基础上,改进现行工艺,开发出诸如大型隧道窑直接还原、AMR—CBI隧道窑直接还原工艺、宽体球状海绵铁隧道窑、L-S快速还原工艺等多种新技术,掀开了隧道窑工艺规模扩大、产能提高、机械及自动化提升的序幕.1.3 转底炉转底炉煤基直接还原是最近几十年间发展起来的炼铁新技术,代表工艺为Fastmet,它由美国Midrex公司与日本神户制钢于20世纪60年发,是采用环形转底炉生产直接还原铁的一种方法.经过多年的半工业性试验和深入的可行性研究,现已完成工艺作参数和装置设计的优化.Fastmelt和ITmk3工艺是在此基础上增加对直接还原铁的处理.图3显示了这三种以转底炉为主体的直接还原工艺流程.图3 转底炉直接还原工艺流程煤粉与铁精粉按比例混匀制成球团,干燥后以1~3层球铺放在转底炉床面,随着炉底的旋转,炉料依次经过预热区、还原区和冷却区.还原区内球团被加热到1 250~1 350 ℃,由于煤粉与铁氧化物紧密接触,铁氧化铁被碳迅速还原成DRI,成品在800~1 000 ℃左右连续从转底炉卸出.球团矿在炉底停留8~30 min,这取决于原料特性、料层厚度及其他因素,成品可作电炉热装炉料或者转炉炉料,也可冷却或生产热压块(HBI).Fastmet工艺技术特点:①在高温敞焰下加热实现快速还原,反应时间只需10~20 min,生产效率高;②原料来源广泛,铁原料方面,除使用高品位粉矿、精矿外,还可用氧化铁皮、代油铁泥、炼钢粉尘、含En、Pb、As等有害杂质的铁矿等;还原剂方面,除煤以外焦末、沥青均可利用,不必担心出现结圈问题;③炉料相对炉底静止,对炉料强度要求不高;④废气中含有大量显热,可用作预热空气、干燥原料等[6]. Fastmelt工艺流程基本与Fastmet一致,只是在后续添加一个熔炉来生产高质量的液态铁水.Itmk3工艺是使金属化球团在转底炉中还原时熔化,生成铁块(Nuggets),同时脉石也熔化,形成渣铁分离.当然转底炉也存在着设备复杂、炉内气氛难控制、传热效率低以及对还原剂硫含量要求严格的缺点.就目前转底炉工艺开发的水平和规模而论,与高炉还有较大差距,但仍存在发展的广阔空间,天津荣程联合钢铁集团已兴建一条100万t级Fastmet生产线,建成目前世界最大的转底炉.另外,用转底炉可处理一些特殊铁矿,如含锌、铅、砷等有害杂质,或含镍、钒、钛等有用元素,均可利用转底炉的工艺优势,或高温挥发,或选择性还原,配合后续工艺,实现资源综合利用.马钢尘泥脱锌转底炉工程项目于2008年5月开工建设,2009年7月6日正式竣工投产,建成了整套转底炉(RHF)脱锌工艺技术装置,不仅解决了含锌尘泥循环利用的后顾之忧,而且将综合利用技术上升到高品质资源化水平.1.4 其他新工艺1.4.1 PF法煤基竖炉直接还原工艺中冶集团北京冶金设备研究设计总院,结合国内情况创新发明了PF法竖炉直接还原工艺.PF法是在吸收K-M法外热式竖炉煤基直接还原工艺的经验基础上,设计的以一种中国特色的罐式还原炉为主反应器的直接还原法.这种工艺技术可靠,技术经济指标在各种煤基直接还原工艺中属先进水平.PF法直接还原工艺流程如图4所示.图4 PF法直接还原工艺流程PF法直接还原工艺主要特点[1]:1)主体设备选用外热式竖炉,预热、还原、冷却三段根据不同的作用和温度选用不同材质和结构,便于传热和化学反应进行,提高热效率和设备寿命.2)原燃料适用性强,对精矿、还原剂和燃料没有特殊要求.3)采用外配碳工艺,还原剂适当过量,扩大了煤的选用范围,造球工艺也因不定量配入煤粉而简化,球团强度较高,DRI质量较好.4)多个反应罐可并列组成任意规模的还原设备,设计和组织生产灵活.1.4.2 低温快速还原新工艺2004年钢铁研究总院提出了低温快速冶金新工艺.新工艺利用纳米晶冶金技术的特点将铁矿的还原温度降低到700 ℃以下.新流程分为气基和煤基两种方法,工艺流程如图5、图6所示.图5 煤基低温快速还原新工艺图6 气基低温快速还原新工艺煤基法使用煤粉为还原剂,在700℃左右快速还原铁精矿粉;气基法使用还原性气体还原铁精矿粉,还原温度可低于600℃.新工艺具有能耗低、环境友好等特点,省去了烧结或造球工艺,缓解了钢铁行业对焦煤的依赖,符合我国国情[7].2 攀钢现状钒钛磁铁矿是攀西地区的特色资源,与普通矿相比,钒钛矿直接还原温度较高、还原时间较长,还原过程产生特有的膨胀粉化现象,因此,存在竖炉结瘤、流化床失流和黏结、回转窑结圈等技术难题.高炉流程冶炼钒钛矿,只回收了铁和钒,钛进入高炉渣没有回收,造成钛资源的大量流失.2005年以来,攀钢科研人员在充分吸收、借鉴新流程及相关研究成果的基础上,通过大量的试验研究,针对钒钛磁铁矿特点,提出并验证了钒钛磁铁矿"转底炉直接还原—电炉深还原—含钒铁水提钒—含钛炉渣提钛"工艺路线,彻底打通了钒钛矿资源综合利用新工艺流程,稳定获得了质量满足要求的低碳生铁、达到GB3283-87要求的片状V2O5和PTA121质量要求的钛白产品.依托该研究成果,攀钢集团攀枝花钢铁研究院于2008年5月4日正式启动了攀钢10 万t/a钒钛矿资源综合利用新工艺中试线工程项目,新建一条转底炉—熔分电炉联合使用,年处理能力10万t钒钛矿的试验生产线,为更深入地研究实践,实现转底炉处理钒钛矿的规模化生产提供了广阔的平台.中试线工艺流程如图7所示.本流程采用硫含量较低的白马铁精矿,还原剂采用无烟煤煤粉,粘结剂为有机粘结剂,原料混合后经高压压球机压球,生球烘干后进入转底炉系统.球团在转底炉内停留10~30 min后出料,金属化球团直接热装进入熔分电炉,在一定温度下还原后,产出含钒铁水及含钛炉渣.继续对铁水进行脱硫、提钒后,得到半钢、脱硫渣及钒渣,半钢进入铸铁机铸铁,生产出铸铁块.钛渣制取钛白,实验室条件下钛回收率达到80%以上;钒渣制取钒氧化物(V2O5),实验室条件下,钒回收率达到65%以上.与高炉流程相比,转底炉流程采用100%钒钛矿冶炼,克服了高炉流程必须配加普通矿的不足,在当前铁资源紧张的形势下,有助于充分发挥攀西地区资源优势,拉动区域经济发展.此外,转底炉流程的铁精矿不需烧结处理,不使用焦炭,从根本上避免了烧结烟气脱硫、焦煤资源采购困难以及环保压力大等问题.3 结语图7 资源综合利用中试线工艺流程煤炭资源总量丰富、焦煤短缺,铁矿资源储量大、富矿少、贫矿和共生矿多是中国钢铁工业面临的现实状况.这种能源、资源结构给煤基直接还原法生产海绵铁的发展提供了机遇.转底炉直接还原技术由于在生产率、规模化、投资费用、单位成本等方面都占有明显的优势,可作为发展直接还原技术的首选工艺.鉴于转底炉处理钒钛磁铁矿技术尚属世界首创,并无较多的经验借鉴,因此要大力开展针对钒钛磁铁矿直接还原的基础研究工作,在实践中借鉴各种直接还原方法已取得的成果,开拓创新,开创钒钛矿直接还原新纪元.参考文献[1] 陈守明,黄超,张金良.煤基竖炉直接还原工艺//2008年非高炉炼铁年会文集.中国金属学会,2008:132-135.[2] 杨婷,孙继青.世界直接还原铁发展现状及分析.世界金属导报,2006.[3] 刘国根,邱冠周,王淀佐.直接还原炼铁中的粘结剂.矿产综合利用,2001(4):27-30.[4] 韩跃新,高鹏,李艳军.白云鄂博氧化矿直接还原综合利用前景.金属矿山,2009 (5):1-6.[5] 魏国,赵庆杰,沈峰满,等.非高炉生产技术进步//2004年全国炼铁生产技术暨炼铁年会文集.2004:878-882.[6] 陶晋. 环形转底炉直接还原工艺现状及发展趋势. 冶金信息工作, 1997.6.[7] 郭培民,赵沛,张殿伟.低温快速还原炼铁新技术特点及理论研究.炼铁,2007,26(1): 57-60.来源:攀枝花钢铁研究院网站。
海绵铁新工艺介绍

书山有路勤为径,学海无涯苦作舟
海绵铁新工艺介绍
1. 工艺流程实现全自动化控制,机械化装卸料,采用快速还原炉进行还原、最后形成冷压块铁的直接还原铁(海绵铁)生产工艺方法。
该工艺的工艺流程可分为如下六个工序:
1.1 原料准备及其烘干破碎工序将脱硫剂、还原剂两种物料装入定量料斗,定量料斗按两种物料的重量比,通过输送机将物料送到烘干室内对两物料进行烘干、混合。
烘干后的物料含水量小于3%,烘干后的物料,通过输送机送到还原剂破碎机内进行粉碎,粉碎粒度为1.5mm 以下。
破碎后的物料,经输送机提升到高位料仓,然后再由输送机送到储存料仓。
精矿粉由输送机直接送入烘干机组进行烘干,烘干后含水量小于3%,烘干后的精矿粉由输送机送入高位料仓,然后再由输送机送至储存料仓。
1.2 自动装料工序本工艺根据需要可生产球状、柱状或瓦片状直接还原铁(海绵铁),从保证产品质量,减少生产环节和有利于实现自动装卸料角度考虑,以生产瓦片状为最好。
本工艺采用瓦片状形式。
装料系统由料仓、定量管和装料头三部分组成,精矿粉和还原剂,经过储存料仓,将料卸到布料仓内,再由装料头装入每个还原坩埚,实现向坩埚布料。
1.3 还原焙烧工序此工序在快速还原炉内完成。
适宜稳定的炉温和还原时间是决定直接还原铁(海绵铁)质量的关键,此工序包括预热、还原、冷却三个阶段。
首先,载车经过传动机构,将载车送入快速还原炉内的预热段,在此间,物料中的水分完全蒸发,脱硫剂分解,温度升至还原温度,进入高温还原段,在此间,氧化铁被充分还原,形成单质铁,然后进入冷却段进行冷却,冷却到200℃以下后出炉。
1.4 自动卸料工序物料出炉后在常温中降到100℃~50℃后进入卸料系统进行。
北京科技大学科技成果——隧道窑反应罐法直接还原炼铁新工艺

北京科技大学科技成果——隧道窑反应罐法直接还
原炼铁新工艺
成果简介
近年来资源供应日益紧张,原材料价格上涨,产品价格竞争激烈,环境保护日趋严格,这三种因素唤起了人们对直接还原铁的热情。
纯净钢的生产,要求优质原料,废钢的不断循环,造成了废钢中有害元素的积累,必须用直接还原铁去稀释废钢中的有害元素,保证电炉能冶炼出合格钢。
长期以来冶金工作者期望改革钢铁工业生产的长流程,降低成本和改善环保。
随着废钢循环量的增加,钢中的有害元素含量必然会积累,必须发展还原铁生产工艺和提高产品质量来保证钢材的质量,这是世界钢铁工业发展的客观规律。
我国目前直接还原铁的生产能力远远满足不了钢铁工业发展的要求,产品质量也不稳定,要生产出优质的还原铁,才能和进口还原铁竞争,开创自己的市场。
日本神户钢铁公司开发了一种炼铁新技术ITmk3,在ITmk3工艺中,用粉矿和煤粉制成的复合生球,装入转炉中,加热到1350-1500℃的温度范围,由于温度高,复合球团迅速还原成铁,并部分熔化,使得铁从球团内生成的液态炉渣中分离出来。
铁粒含铁96%-98%,碳2.5%-4.3%、硅0.2%、锰0.1%,硫和磷都在0.05%-0.06%范围。
铁粒可直接装入电炉或转炉中使用。
我国多数直接还原生产厂采用隧道窑反应罐法,生产工艺落后,能耗高,对环境的污染严重,产品质量稳定性差,且大多是生产海绵
铁。
本研究是在现有主要装备——隧道窑基础上,借鉴日本神户ITmk3技术思想,从直接还原反应的根本理论出发,利用本公司现有隧道窑技术,从试验室系统研究开发隧道窑生产珠铁的工艺,为优化和工业化生产提供确实可行的理论依据。
最新低污染的无焦炼铁新工艺海绵铁

低污染的无焦炼铁新工艺海绵铁低污染的无焦炼铁新工艺---海绵铁海绵铁也叫直接还原铁(DIR),广泛应用于冶金,配重及滤料等行业。
由于能源不用焦炭而用其它还原性气体和煤,是一种短流程、低污染的无焦炼铁新工艺,是我国钢铁行业高新技术和先进适用技术改造传统产业的工作重点之一。
然而,近年来我国钢铁产量即将突破2亿吨,DRI生产能力却停滞在百万吨左右,主要原因是投产海绵铁厂经济效益不够理想。
结合我国的实际情况应该大力发展煤基法。
.最重要的就是选择工艺路线。
目前我国隧道窑,回转窑,内配碳球团等工艺有许多种已经成熟,但不同的工艺实际效果不同,不是成熟的工艺都能取得良好效益。
检验真理的唯一标准是实践,为便于研究、比较DPI工艺,促进我国直接还原铁产业发展,以产品、工艺相近的高炉炼铁技术为基础,提出DRI工艺的几项主要技术经济指标,并按这儿项指标对目前几种主要工艺进行分析、比较,研讨工艺改进方向:1、发展无罐工艺:还原罐在使用初期确实提高了产品质量,提供了稳定的还原气氛并且在一定程度上提高了产量。
但随着技术的不断发展,现在还原罐应经成为了制约工艺发展的瓶颈,必须要突破它。
如果采用无罐工艺,不仅省掉了制罐的成本。
同时能耗也将大幅降低。
现在隧道窑罐式法普遍的能耗是800kg/t,其中罐的蓄热就占了相当大的比重;2、利用系数:(t/d*m3)这是衡量高炉炼铁生产效率的主要指标。
过去高炉的利用系数一般在2.0左右,近年来国内炼铁技术不断优化,一些大型高炉利用系数已经达到4.0。
现在行业平均值也要到3.0左右。
相比之下现在的煤基法就要落后很多了,不管是采用那种工艺。
煤基回转窑利用系数0.4左右,煤基隧道窑罐式法利用系数0.2左右,煤基外热式竖炉利用系数1.3左右。
当务之急是要提高窑体的利用系数,这样才能把生产率提上去;2、能耗:(kJ/吨铁或kgce/t铁)工序能耗kgce/t和焦比kg/t是高炉炼铁能耗主要指标。
随着炼铁技术优化及喷吹煤粉技术的发展这个指标逐年降低,目前焦比大概是460kg,工序能耗13GJ/t。
直接还原铁的生产新工艺[发明专利]
![直接还原铁的生产新工艺[发明专利]](https://img.taocdn.com/s3/m/9ca6565cfd0a79563d1e7249.png)
专利名称:直接还原铁的生产新工艺专利类型:发明专利
发明人:杨春来
申请号:CN200710061406.0
申请日:20070319
公开号:CN101020937A
公开日:
20070822
专利内容由知识产权出版社提供
摘要:本发明涉及有关直接还原铁生产工艺的技术领域。
本发明采用如下新工艺生产直接还原铁:(1)首先进行原料处理将精矿粉用压块设备压制成密度为:2.5—5.0g/cm的压块;(2)将上述制成的精矿粉压块装入还原坩锅内,同时按照如下重量份数比:精矿粉8-12 脱氧剂2-4 脱硫剂0.5-1.5,在坩锅内加入脱氧剂和脱硫剂,然后将坩锅整齐的排放在载车上,通过运转车将将载车平推入还原炉内,在还原炉内经过预热,还原,冷却的三个过程,然后出炉生产出达到国际合格标准的优质直接还原铁,其密度可达到:2.5—4.0g/cm。
本发明具有产量大、能耗低、产品密度大质量好等优点。
申请人:杨春来
地址:053200 河北省冀州市魏屯经济开发区冀州市东瀛公司
国籍:CN
代理机构:石家庄新世纪专利商标事务所有限公司
代理人:张杰
更多信息请下载全文后查看。
我国煤基隧道窑直接还原铁生产现状及发展
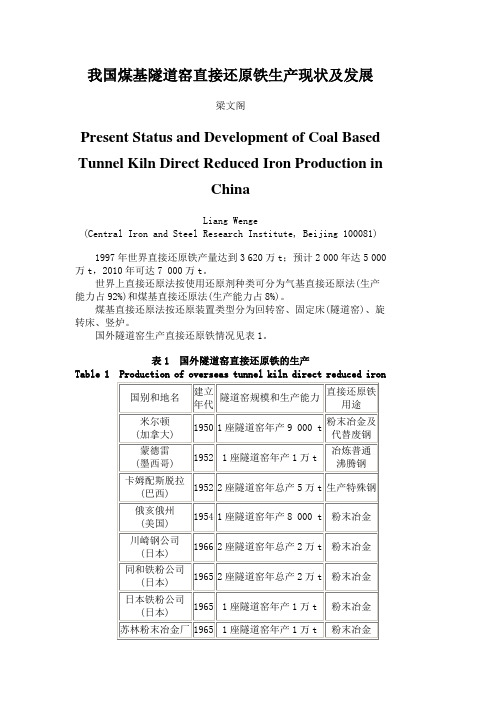
我国煤基隧道窑直接还原铁生产现状及发展梁文阁Present Status and Development of Coal Based Tunnel Kiln Direct Reduced Iron Production inChinaLiang Wenge(Central Iron and Steel Research Institute, Beijing 100081)1997年世界直接还原铁产量达到3 620万t;预计2 000年达5 000万t,2010年可达7 000万t。
世界上直接还原法按使用还原剂种类可分为气基直接还原法(生产能力占92%)和煤基直接还原法(生产能力占8%)。
煤基直接还原法按还原装置类型分为回转窑、固定床(隧道窑)、旋转床、竖炉。
国外隧道窑生产直接还原铁情况见表1。
表1 国外隧道窑直接还原铁的生产Table 1 Production of overseas tunnel kiln direct reduced iron我国在50年代末和60年代初粉末冶金工业普遍采用倒焰窑和反射炉等小批量地生产直接还原铁,用于生产还原铁粉。
1965年上海粉末冶金厂建立我国第1座38.5 m隧道窑开始成批量地生产直接还原铁。
70年代最长的隧道窑为68 m。
80年代武钢粉末冶金公司建成1座105 m 隧道窑,90年代武钢粉末冶金公司又建成1座154 m隧道窑。
1997年马钢铁合金厂建成1座166 m隧道窑,到目前为止国内建有约40座小型隧道窑。
1994年全国生产直接还原铁约5万t用于生产还原铁粉。
我国煤基回转窑直接还原法于1989年在福州特钢厂40 m回转窑工业试验成功后,先后在辽宁喀左、天津钢管公司、山东鲁中矿公司、吉林桦甸、北京密云铁矿建设6座回转窑,总生产能力为46.2万t。
回转窑法工艺成熟、机械化自动化水平高,产品质量好,能耗低,但是由于投资大,在经济不发达地区其发展受到一定限制。
20161025-煤基竖炉直接还原技术

20161025-煤基竖炉直接还原技术D熔化温度下还原成金属产品的炼铁过程;其所得的产品称为直接还原铁,简称DRI(Direct Reduction Iron),也称海绵铁。
优质DRI由于其成分稳定,有害元素含量低,粒度均匀,不仅可以补充废钢资源的不足,而且还可以作为电炉炼钢的原料以及转炉炼钢的冷却剂,对保证钢材的质量特别是合金钢的质量,起着不可替代的作用,是冶炼特钢的优质原料;同时,高品位DRI 还可以供粉末冶金行业使用【1】。
直接还原铁生产方法中,主要分为气基法和煤基法。
由于我国天然气资源缺乏,但是煤炭资源丰富,煤基直接还原技术成为我国直接还原铁生产的重要工艺方法【2】。
煤基直接还原是指直接以廉价的非焦煤作还原剂生产直接还原铁的方法。
在我国煤基直接还原技术主要是回转窑法和隧道窑法【3】,近几年也相继建设了多座转底炉装置,同时也建设了一些煤基连续式竖炉装置。
在直接还原技术日益发展、大力提倡环保节能减排的今天,一些新的更先进的直接还原工艺及设备被迫切需要【4,5】。
煤基竖炉直接还原技术是一项符合中国能源结构特点的可大型化生产高品质海绵铁的直接还原铁生产技术【6】,可广泛用于处理高品位铁精粉制取高纯度还原铁粉用于粉末冶金领域,也可用于处理普通品位的铁精粉制取炼钢用海绵铁,处理复合铁矿生产普通铁水及提取钒、钛、硼等高附加值资源。
1发展历程自2006年至今,已经成功的在中国大陆和国外设计安装了5代炉型五条生产线:1)一条1000吨/年中试生产线;2)一条5万吨/年和两条10万吨/年生产线:图1 5万吨/年产品线图2 10万吨/年产品线1图3 10万吨/年产品线2 4)一条1万吨/年生产线:图4 1万吨/年产品线2工艺流程煤基竖炉直接还原技术(图5)主要设备是以各种煤气(如天燃气、焦炉煤气、混合煤气、发生炉煤气等)为燃料,以经过筛分的块矿或铁精粉等含铁氧化物冷固结制成球团与固体还原剂(无烟煤等)混合成炉料,由炉顶布料系统连续加入炉内煤基立式反应器,燃料通过专用燃烧器在炉内燃烧加热,高温烟气回收用于原燃料的干燥、预热,炉料在封闭的立式反应器中进行“预热→还原”,在反应器内还原区反应15~20h左右,经过输料机对冷却后的混合料进行筛分,废还原剂通过负压输送装置收集到废还原剂收集斗中,还原后的产品DRI球团根据原料不同、用途不同可进行不同的处理,既能够与短流程炼钢工艺配套,也可以与粉末冶金工艺配套。
隧道窑装法生产直接还原铁工艺介绍

隧道窑装法生产直接还原铁工艺介绍隧道窑罐装法生产直接还原铁(海绵铁)是瑞典人在1911年首先用于工业生产直接还原铁(海绵铁)的方法,经过多年的技术发展,已经是一种有效的生产直接还原铁(海绵铁)的方法。
一九九二年河北东瀛有限责任公司在此基础上进行了大量的技术改进和创新,研制开发了新型的隧道窑直接还原铁(海绵铁)生产法。
开创了在我国使用隧道窑生产海绵铁的新纪元,在此后经过不断的改进和完善,形成了无论从投资规模的大与小、无论自动化程度的高与低的系列海绵铁生产工艺,它能满足各种环境、各个区域、各种投资人群的要求,河北东瀛有限责任公司所研制开发的各种工艺无论从投资比例还是投资效益、无论从产品成本还是对原料要求、无论从产品质量还是工艺的成熟性、设备运行的可靠性、稳定性,无论从节能还是环保在我国都是唯一可信赖的、也是遥遥领先的。
它是将精矿粉、煤粉、石灰石粉,按照一定的比例和装料方法,分别装入还原罐中,然后把罐放在罐车上,推入条形隧道窑中或把罐直接放到环形轮窑中,料罐经预热1150℃加热焙烧和冷却之后,使精矿粉还原,得到直接还原铁(海绵铁)的方法。
使用隧道窑直接还原铁(海绵铁)生产工艺已有几十条生产线建成投产。
当精矿粉含铁67%以上时,此法生产的直接还原铁(海绵铁)实物分析结果是:C≥0.04%, S<0.01%, P<0.02%, SiO2<3%, MFe≥86%, TFe≥92% M≥94%。
1.隧道窑生产工艺的特点:(1)原料、还原剂、燃料容易解决此方法所用的原料是精矿粉或品位≥60%的赤铁矿或褐铁矿,这远比富铁块矿好解决,同时,生产中不需要把精矿粉先变成氧化球团,生产费用也低,而且生产中不添加任何粘结剂,这样避免了原料的污染;还原剂是普通无烟煤粉或焦碳末,煤中灰分熔点也不要求很高;供热的燃料是普通动力煤或煤粉,有多余高炉煤气、焦炉煤气、转炉煤气、混和煤气、石油气的地方也可用这些气体做热源,还可使用发生炉煤气或重油作为热源,使用范围十分广阔。
- 1、下载文档前请自行甄别文档内容的完整性,平台不提供额外的编辑、内容补充、找答案等附加服务。
- 2、"仅部分预览"的文档,不可在线预览部分如存在完整性等问题,可反馈申请退款(可完整预览的文档不适用该条件!)。
- 3、如文档侵犯您的权益,请联系客服反馈,我们会尽快为您处理(人工客服工作时间:9:00-18:30)。
中国煤基隧道窑法还原铁(海绵铁)生产最新工艺技术
中国是世界第一大钢产量国,2011 年钢产量突破7 亿吨,年需要废钢9000 多万吨,还原铁需求量为500 万吨。
我国年进口还原铁300万吨,而还原铁(海绵铁)年产量仅为60 万吨。
我国是一个贫铁矿资源丰富的国家,低贫呆矿占铁矿资源97%以上,但每年需要从国外进口6 亿吨的铁矿石,国内大量的低贫呆矿没有得到很好的开发。
另外,我国每年还有上亿吨的硫酸渣、铜渣、除尘灰等含铁废料产生。
现在,我国是一个非焦煤储量丰富的国家,焦煤资源日益频发,因此国家出台相关政策,鼓励发展直接还原铁和非焦炼铁工艺技术开发与应用。
提高还原铁的产量及开发我国大量的低贫呆矿使其资源化迫在眉睫。
我国目前年生产的60 万吨还原铁(海绵铁),主要是由200 余条隧道窑法生产的。
在我国,煤基隧道窑罐式法生产还原铁(海绵铁)走过30 年的历史,其
工艺技术比较稳定、成熟,小项目分布相对比较普遍。
但因传统的煤基隧道窑罐式法,必须采用昂贵的耐火罐;同时具有能耗高;还原时间长;劳动力消耗高;产品质量低下等原因,造成生产成本高、销路不畅等实际问题。
目前造成煤基隧道窑法还原铁生产停顿状态。
2011年,在北京非高炉会议上,许多隧道窑法海绵铁厂家强烈要求专家、教授们能提供一套新的工艺技术,使煤基隧道窑厂家能焕发生机。
因此,沈阳博联特熔融还原科技有限公司与多家与会海绵铁厂家进行了交流后,半年内通过研发和工业试验,为其解决了两大技术问题,可以让煤基隧道窑法海绵铁厂家获得新生。
一. 实现了煤基隧道窑无罐法生产海绵铁甚至砾铁产品将煤基隧道窑烧嘴位置进行改变,采用直接燃煤新技术,彻底去掉昂贵的耐火罐,实现了无罐法生产海绵铁,入炉铁矿可以多种化。
新技术煤基隧道窑法海绵铁的主要特点:
1、降低生产运行成本。
取消了昂贵的耐火罐,可以降低生产运行成本200
多元/ 吨。
2、还原时间大大的缩短。
传统隧道窑罐式法生产还原铁的还原时间,一般为:粘土罐28〜31小时、
碳化硅罐38〜42小时,博联特隧道窑无罐法还原时间一般为8〜12小时。
3、降低能耗。
可以直接采用燃煤燃烧,环保、低运行成本。
4、回收还原剂尾粉中煤焦循环再使用。
传统隧道窑罐式法的还原剂尾粉,绝大多数都被扔掉了,本工艺技术可以回收还原剂中80%以上的煤焦,作为还原剂循环使用,可以降低60%以上的还原煤消耗。
同样也大大降低了生产运行成本。
5、装卸料方便。
6、产品多样化。
因为无需采用昂贵耐火罐生产,入炉原矿可以是粉矿、原矿石;也可以是矿粉压块;也可以是矿粉球团。
所以产品有还原铁(海绵铁)板、压块还原、金属化球团、高密度金属化球团或砾铁。
甚至可以用铁矿粉直接生产铁艺品。
二.可以采用各种难选矿、复合矿、含铁废料还原分离出高品位还原铁。
传统煤基隧道窑罐式法生产海绵铁,一般采用的是TFe> 66%勺高品位铁矿粉,铁矿价格高,生产成本必然高。
采用博联特隧道窑无罐法还原窑炉,结合博联特公司专有的还原工艺技术,可以采用低品位赤铁矿、褐铁矿、鲕状赤铁矿、羚羊石铁口、菱铁矿等难选矿;钒钛磁铁矿、红土镍矿、硼铁矿、锰铁矿等复合矿及除尘污泥、硫酸渣、铅锌渣、铜渣等含铁废料进行还原、分离成TFe> 90%勺还原铁甚至砾铁产品。
三.煤基隧道窑无罐法还原铁(海绵铁)生产工艺技术拥有沈阳博联特公司近十项专利技术。
沈阳博联特熔融还原科技公司是专业从事非高炉中直接还原铁(海绵铁)和熔融还原铁技术研发和转让的科技型公司,拥有多项先进、稳定的工艺技术和装备,可以为每个客户或每种矿的提供独特、适合的工艺技术和装备。
欢迎关注博联特公司,更欢迎来东北大学和沈阳博联特公司考察。