材料轴向拉伸参数测试(基本实验)
材料力学性能测试实验报告
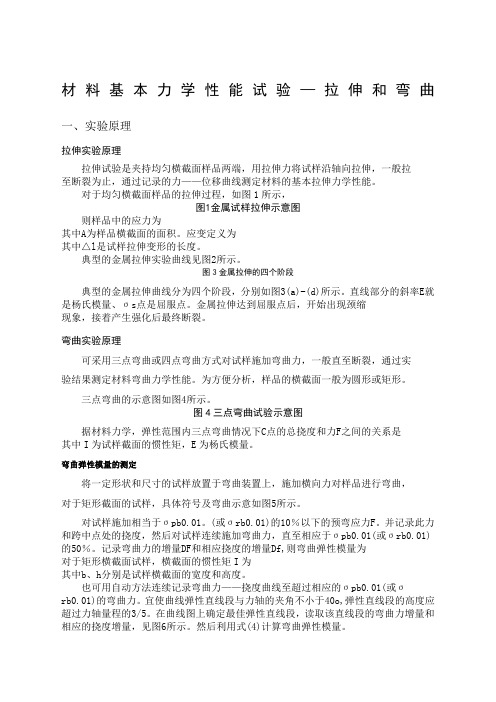
材料基本力学性能试验—拉伸和弯曲一、实验原理拉伸实验原理拉伸试验是夹持均匀横截面样品两端,用拉伸力将试样沿轴向拉伸,一般拉至断裂为止,通过记录的力——位移曲线测定材料的基本拉伸力学性能。
对于均匀横截面样品的拉伸过程,如图1所示,图1金属试样拉伸示意图则样品中的应力为其中A为样品横截面的面积。
应变定义为其中△l是试样拉伸变形的长度。
典型的金属拉伸实验曲线见图2所示。
图3金属拉伸的四个阶段典型的金属拉伸曲线分为四个阶段,分别如图3(a)-(d)所示。
直线部分的斜率E就是杨氏模量、σs点是屈服点。
金属拉伸达到屈服点后,开始出现颈缩现象,接着产生强化后最终断裂。
弯曲实验原理可采用三点弯曲或四点弯曲方式对试样施加弯曲力,一般直至断裂,通过实验结果测定材料弯曲力学性能。
为方便分析,样品的横截面一般为圆形或矩形。
三点弯曲的示意图如图4所示。
图4三点弯曲试验示意图据材料力学,弹性范围内三点弯曲情况下C点的总挠度和力F之间的关系是其中I为试样截面的惯性矩,E为杨氏模量。
弯曲弹性模量的测定将一定形状和尺寸的试样放置于弯曲装置上,施加横向力对样品进行弯曲,对于矩形截面的试样,具体符号及弯曲示意如图5所示。
对试样施加相当于σpb0.01。
(或σrb0.01)的10%以下的预弯应力F。
并记录此力和跨中点处的挠度,然后对试样连续施加弯曲力,直至相应于σpb0.01(或σrb0.01)的50%。
记录弯曲力的增量DF和相应挠度的增量Df,则弯曲弹性模量为对于矩形横截面试样,横截面的惯性矩I为其中b、h分别是试样横截面的宽度和高度。
也可用自动方法连续记录弯曲力——挠度曲线至超过相应的σpb0.01(或σrb0.01)的弯曲力。
宜使曲线弹性直线段与力轴的夹角不小于40o,弹性直线段的高度应超过力轴量程的3/5。
在曲线图上确定最佳弹性直线段,读取该直线段的弯曲力增量和相应的挠度增量,见图6所示。
然后利用式(4)计算弯曲弹性模量。
二、试样要求1.拉伸实验对厚、薄板材,一般采用矩形试样,其宽度根据产品厚度(通常为0.10-25mm),采用10,12.5,15,20,25和30mm六种比例试样,尽可能采用lo =5.65(F)0.5的短比例试样。
材料力学拉伸实验报告(1)
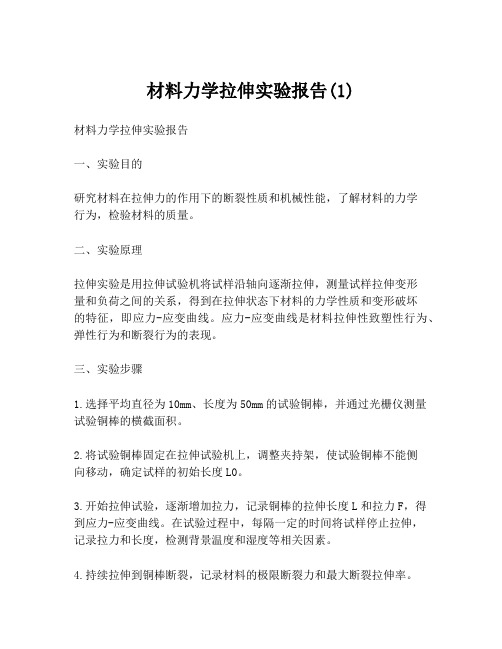
材料力学拉伸实验报告(1)材料力学拉伸实验报告一、实验目的研究材料在拉伸力的作用下的断裂性质和机械性能,了解材料的力学行为,检验材料的质量。
二、实验原理拉伸实验是用拉伸试验机将试样沿轴向逐渐拉伸,测量试样拉伸变形量和负荷之间的关系,得到在拉伸状态下材料的力学性质和变形破坏的特征,即应力-应变曲线。
应力-应变曲线是材料拉伸性致塑性行为、弹性行为和断裂行为的表现。
三、实验步骤1.选择平均直径为10mm、长度为50mm的试验铜棒,并通过光栅仪测量试验铜棒的横截面积。
2.将试验铜棒固定在拉伸试验机上,调整夹持架,使试验铜棒不能侧向移动,确定试样的初始长度L0。
3.开始拉伸试验,逐渐增加拉力,记录铜棒的拉伸长度L和拉力F,得到应力-应变曲线。
在试验过程中,每隔一定的时间将试样停止拉伸,记录拉力和长度,检测背景温度和湿度等相关因素。
4.持续拉伸到铜棒断裂,记录材料的极限断裂力和最大断裂拉伸率。
5.将数据记录到实验记录表中。
四、实验数据处理根据实验数据计算出拉伸试验的机械性能参数,如极限强度、屈服强度、断裂拉伸率等等。
1.极限强度:σmax = Fma x / S其中,Fmax为材料拉伸到断裂的最大力;S为试验铜棒的横截面积。
2.屈服强度:σs = Fs / S其中,Fs为材料开始塑性变形前的单位应力;S为试验铜棒的横截面积。
3.断裂拉伸率:A = (Lmax - L0)/ L0 × 100%其中,Lmax为材料拉伸到断裂时的长度;L0为材料载荷前的长度。
五、实验结果分析根据实验数据计算得到的拉伸试验机械性能参数可以反映出材料的力学行为。
在拉伸实验过程中,材料首先呈现弹性变形,后进入塑性变形阶段,这个过程体现在应力-应变曲线上就是曲线急速上升然后平缓变化,然后在拉伸到达一定程度后,材料会出现颈缩现象,最终断裂。
通过拉伸实验,我们可以得到应力-应变曲线,可以直观的看到材料的力学行为并计算出其力学性能参数。
拉伸压缩实验报告

一、实验目的1. 了解材料力学中拉伸和压缩的基本原理及实验方法。
2. 通过实验观察材料的弹性、屈服、强化等力学行为。
3. 测定材料的屈服极限、强度极限、延伸率、断面收缩率等力学性能指标。
4. 掌握电子万能试验机的使用方法及工作原理。
二、实验原理1. 拉伸实验:将试样放置在万能试验机的夹具中,缓慢施加轴向拉伸载荷,通过力传感器和位移传感器实时采集力与位移数据,绘制F-Δl曲线,分析材料的力学性能。
2. 压缩实验:将试样放置在万能试验机的夹具中,缓慢施加轴向压缩载荷,通过力传感器和位移传感器实时采集力与位移数据,绘制F-Δl曲线,分析材料的力学性能。
三、实验设备1. 电子万能试验机2. 力传感器3. 位移传感器4. 游标卡尺5. 计算机及数据采集软件四、实验材料1. 低碳钢拉伸试样2. 铸铁压缩试样五、实验步骤1. 拉伸实验:1. 将低碳钢拉伸试样安装在万能试验机的夹具中。
2. 设置试验参数,如拉伸速率、最大载荷等。
3. 启动试验机,缓慢施加轴向拉伸载荷,实时采集力与位移数据。
4. 绘制F-Δl曲线,分析材料的力学性能。
2. 压缩实验:1. 将铸铁压缩试样安装在万能试验机的夹具中。
2. 设置试验参数,如压缩速率、最大载荷等。
3. 启动试验机,缓慢施加轴向压缩载荷,实时采集力与位移数据。
4. 绘制F-Δl曲线,分析材料的力学性能。
六、实验结果与分析1. 低碳钢拉伸实验:1. 通过F-Δl曲线,确定材料的屈服极限、强度极限、延伸率、断面收缩率等力学性能指标。
2. 分析材料在拉伸过程中的弹性、屈服、强化等力学行为。
2. 铸铁压缩实验:1. 通过F-Δl曲线,确定材料的强度极限等力学性能指标。
2. 分析材料在压缩过程中的破坏现象。
七、实验结论1. 通过本次实验,我们掌握了拉伸和压缩实验的基本原理及实验方法。
2. 通过实验结果,我们了解了低碳钢和铸铁的力学性能。
3. 实验结果表明,低碳钢具有良好的弹性和塑性,而铸铁则具有较好的抗压性能。
材料力学实验指导书(正文)

实验一材料在轴向拉伸、压缩时的力学性能一、实验目的1.测定低碳钢在拉伸时的屈服极限σs、强度极限σb、延伸率δ和断面收缩率 。
2.测定铸铁在拉伸以及压缩时的强度极限σb。
3.观察拉压过程中的各种现象,并绘制拉伸图。
4.比较低碳钢(塑性材料)与铸铁(脆性材料)机械性质的特点。
二、设备及仪器1.电子万能材料试验机。
2.游标卡尺。
图1-1 CTM-5000电子万能材料试验机电子万能材料试验机是一种把电子技术和机械传动很好结合的新型加力设备。
它具有准确的加载速度和测力范围,能实现恒载荷、恒应变和恒位移自动控制。
由计算机控制,使得试验机的操作自动化、试验程序化,试验结果和试验曲线由计算机屏幕直接显示。
图示国产CTM -5000系列的试验机为门式框架结构,拉伸试验和压缩试验在两个空间进行。
图1-2 试验机的机械原理图试验机主要由机械加载(主机)、基于DSP的数字闭环控制与测量系统和微机操作系统等部分组成。
(1)机械加载部分试验机机械加载部分的工作原理如图1-2所示。
由试验机底座(底座中装有直流伺服电动机和齿轮箱)、滚珠丝杠、移动横梁和上横梁组成。
上横梁、丝杠、底座组成一框架,移动横梁用螺母和丝杠连接。
当电机转动时经齿轮箱的传递使两丝杠同步旋转,移动横梁便可水平向上或相下移动。
移动横梁向下移动时,在它的上部空间由上夹头和下夹头夹持试样进行拉伸试验;在它的下部空间可进行压缩试验。
(2)基于DSP的数字闭环控制与测量系统是由DSP平台;基于神经元自适应PID算法的全数字、三闭环(力、变形、位移)控制系统;8路高精准24Bit 数据采集系统;USB1.1通讯;专用的多版本应用软件系统等。
(3) 微机操作系统试验机由微机控制全试验过程,采用POWERTEST 软件实时动态显示负荷值、位移值、变形值、试验速度和试验曲线;进行数据处理分析,试验结果可自动保存;试验结束后可重新调出试验曲线,进行曲线比较和放大。
可即时打印出完整的试验报告和试验曲线。
材料拉伸实验

实验一:光滑静态拉伸试验金属材料的拉伸试验是人们应用最广泛的测定其力学性能的方法。
试验时取一定的标准试样,在温度、环境介质、加载速度均为确定条件下将载荷施加于试样两端,使试样在轴向拉应力作用下产生弹性变形、塑性变形、直至断裂。
通过测定载荷和试样尺寸变化可以求出材料的力学性能指标。
一、实验数据分析与处理n 0.2721S b290.6534 535.09796e B0.00406 0.17887ψeB-0.00406 -0.178871.1光滑钢1.1.1计算机数据图1—1 钢光滑拉伸试验应力~应变曲线图1—2 钢光滑拉伸试验均匀塑性变形阶段lgS~lge的线性拟合2010-4-5 15:43Linear Regression for A0709032_lgS:Y = A + B * XParameter Value Error------------------------------------------------------------A 2.9417 0.00425B 0.2721 0.00386------------------------------------------------------------R SD N P------------------------------------------------------------ 0.99321 0.00788 70 <0.0001经计算得:K=10A=102.9417=874.38MPan=B=0.27211.1.2坐标纸数据图1—3 钢光滑拉伸试验载荷~位移曲线图1—4 钢光滑拉伸试验应力~应变曲线图1—5 钢光滑拉伸试验均匀塑性变形阶段lgS~lge的线性拟合2010-4-6 20:24Linear Regression for Data1_lgs:Y = A + B * XParameter Value Error------------------------------------------------------------A 3.19016 0.05524B 0.6578 0.06625------------------------------------------------------------R SD N P------------------------------------------------------------ 0.95726 0.02645 11 <0.0001经计算得:K=10A=103.19016=1549.39MPan=B=0.65781.2光滑铸铁1.2.1计算机数据图1—6 铸铁光滑拉伸试验应力~应变曲线1.2.2坐标纸数据图1—7 铸铁光滑拉伸试验载荷~位移曲线图1—8 光滑铸铁拉伸试验应力~应变曲线(注:对于光滑铸铁,没有“均匀塑性变形阶段”,所以不能得到K,n值。
弹性参数测定实验报告(3篇)
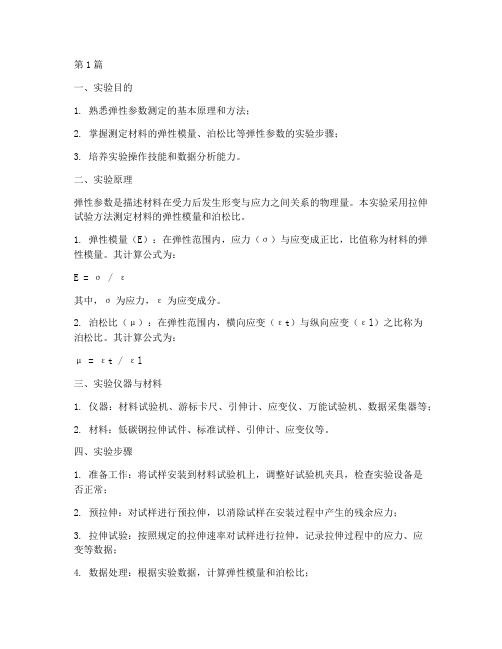
第1篇一、实验目的1. 熟悉弹性参数测定的基本原理和方法;2. 掌握测定材料的弹性模量、泊松比等弹性参数的实验步骤;3. 培养实验操作技能和数据分析能力。
二、实验原理弹性参数是描述材料在受力后发生形变与应力之间关系的物理量。
本实验采用拉伸试验方法测定材料的弹性模量和泊松比。
1. 弹性模量(E):在弹性范围内,应力(σ)与应变成正比,比值称为材料的弹性模量。
其计算公式为:E = σ / ε其中,σ为应力,ε为应变成分。
2. 泊松比(μ):在弹性范围内,横向应变(εt)与纵向应变(εl)之比称为泊松比。
其计算公式为:μ = εt / εl三、实验仪器与材料1. 仪器:材料试验机、游标卡尺、引伸计、应变仪、万能试验机、数据采集器等;2. 材料:低碳钢拉伸试件、标准试样、引伸计、应变仪等。
四、实验步骤1. 准备工作:将试样安装到材料试验机上,调整好试验机夹具,检查实验设备是否正常;2. 预拉伸:对试样进行预拉伸,以消除试样在安装过程中产生的残余应力;3. 拉伸试验:按照规定的拉伸速率对试样进行拉伸,记录拉伸过程中的应力、应变等数据;4. 数据处理:根据实验数据,计算弹性模量和泊松比;5. 结果分析:对比实验结果与理论值,分析误差产生的原因。
五、实验结果与分析1. 弹性模量(E)的计算结果:E1 = 2.05×105 MPaE2 = 2.00×105 MPaE3 = 2.03×105 MPa平均弹性模量E = (E1 + E2 + E3) / 3 = 2.01×105 MPa2. 泊松比(μ)的计算结果:μ1 = 0.296μ2 = 0.293μ3 = 0.295平均泊松比μ = (μ1 +μ2 + μ3) / 3 = 0.2943. 结果分析:实验结果与理论值较为接近,说明本实验方法能够有效测定材料的弹性参数。
实验过程中,由于试样安装、试验机夹具等因素的影响,导致实验结果存在一定的误差。
材料力学拉伸试验

§1-1 轴向拉伸实验一、实验目的1、 测定低碳钢的屈服强度eL R (s σ)、抗拉强度m R (b σ)、断后伸长率A 11.3(δ10)和断面收缩率Z (ψ)。
2、 测定铸铁的抗拉强度m R (b σ)。
3、 比较低碳钢Ø5(塑性材料)和铸铁Ø5(脆性材料)在拉伸时的力学性能和断口特征。
注:括号内为GB/T228-2002《金属材料 室温拉伸试验方法》发布前的旧标准引用符号。
二、设备及试样1、 电液伺服万能试验机(自行改造)。
2、 0.02mm 游标卡尺。
3、 低碳钢圆形横截面比例长试样一根。
把原始标距段L 0十等分,并刻画出圆周等分线。
4、 铸铁圆形横截面非比例试样一根。
注:GB/T228-2002规定,拉伸试样分比例试样和非比例试样两种。
比例试样的原始标距0L 与原始横截面积0S 的关系满足00S k L =。
比例系数k 取5.65时称为短比例试样,k 取11.3时称为长比例试样,国际上使用的比例系数k 取5.65。
非比例试样0L 与0S 无关。
三、实验原理及方法低碳钢是指含碳量在0.3%以下的碳素钢。
这类钢材在工程中使用较广,在拉伸时表现出的力学性能也最为典型。
ΔL (标距段伸长量)低碳钢拉伸图(F —ΔL 曲线)以轴向力F 为纵坐标,标距段伸长量ΔL 为横坐标,所绘出的试验曲线图称为拉伸图,即F —ΔL 曲线。
低碳钢的拉伸图如上图所示,F eL 为下屈服强度对应的轴向力,F eH 为上屈服强度对应的轴向力,F m 为最大轴向力。
F —ΔL 曲线与试样的尺寸有关。
为了消除试样尺寸的影响,把轴向力F 除以试样横截面的原始面积S 0就得到了名义应力,也叫工程应力,用σ表示。
同样,试样在标距段的伸长ΔL 除以试样的原始标距LO 得到名义应变,也叫工程应变,用ε表示。
σ—ε曲线与F —ΔL 曲线形状相似,但消除了儿何尺寸的影响,因此代表了材料本质属性,即材料的本构关系。
轴向拉伸实验报告
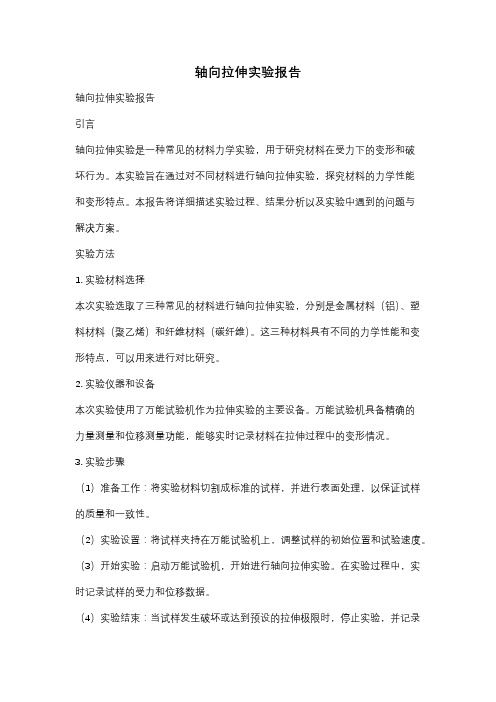
轴向拉伸实验报告轴向拉伸实验报告引言轴向拉伸实验是一种常见的材料力学实验,用于研究材料在受力下的变形和破坏行为。
本实验旨在通过对不同材料进行轴向拉伸实验,探究材料的力学性能和变形特点。
本报告将详细描述实验过程、结果分析以及实验中遇到的问题与解决方案。
实验方法1. 实验材料选择本次实验选取了三种常见的材料进行轴向拉伸实验,分别是金属材料(铝)、塑料材料(聚乙烯)和纤维材料(碳纤维)。
这三种材料具有不同的力学性能和变形特点,可以用来进行对比研究。
2. 实验仪器和设备本次实验使用了万能试验机作为拉伸实验的主要设备。
万能试验机具备精确的力量测量和位移测量功能,能够实时记录材料在拉伸过程中的变形情况。
3. 实验步骤(1)准备工作:将实验材料切割成标准的试样,并进行表面处理,以保证试样的质量和一致性。
(2)实验设置:将试样夹持在万能试验机上,调整试样的初始位置和试验速度。
(3)开始实验:启动万能试验机,开始进行轴向拉伸实验。
在实验过程中,实时记录试样的受力和位移数据。
(4)实验结束:当试样发生破坏或达到预设的拉伸极限时,停止实验,并记录实验结果。
实验结果与分析1. 金属材料(铝)的实验结果金属材料在受力下具有较高的强度和韧性。
实验结果显示,铝试样在拉伸过程中呈现出线性的应力-应变关系,直至达到屈服点。
在屈服点之后,铝试样的应力开始逐渐下降,直至发生破坏。
这种应力-应变曲线表明,铝材料具有较好的可塑性和变形能力。
2. 塑料材料(聚乙烯)的实验结果塑料材料在受力下具有较低的强度和韧性。
实验结果显示,聚乙烯试样在拉伸过程中呈现出非线性的应力-应变关系。
在初期阶段,聚乙烯试样的应力增长较快,但随着应变的增加,应力增长逐渐减缓。
聚乙烯试样的断裂点较低,表明其抗拉强度较弱。
3. 纤维材料(碳纤维)的实验结果纤维材料具有较高的强度和刚度,但韧性较低。
实验结果显示,碳纤维试样在拉伸过程中呈现出线性的应力-应变关系,直至发生破坏。
实验一 拉伸与压缩实验

实验一 拉伸与压缩实验拉伸实验是对试件施加轴向拉力,以测定材料在常温静荷载作用下的力学性能的实验。
它是材料力学最基本、最重要的实验之一。
拉伸实验简单、直观、技术成熟、数据可比性强,它是最常用的实验手段。
由此测定的材料力学性能指标,成为考核材料的强度、塑性和变形能力的最基本的依据,被广泛、直接地用于工程设计、产品检验、工艺评定等方面。
而有些材料的受压力学性能和受拉力学性能不同,所以,要对其施加轴向压力,以考核其受压性能,这就是压缩实验。
一、实验目的1.通过对低碳钢和铸铁这两种不同性能的典型材料的拉伸、压缩破坏过程的观察和对实验数据、断口特征的分析,了解它们的力学性能特点。
2.了解电子万能试验机的构造、原理和操作。
3.测定典型材料的强度指标及塑性指标,低碳钢拉伸时的屈服极限S σ,(或下屈服极限SL σ),强度极限b σ,延伸率δ,截面收缩率ψ,压缩时的压缩屈服极限SC σ,铸铁拉伸、压缩时的强度极限b σ、bC σ。
二.实验设备及试件1. 电子万能试验机:试验机结构与原理――材料力学基本实验设备是静态万能材料试验机, 能进行轴向拉伸、轴向压缩和三点弯曲等基本实验。
试验机主要由机械加载、控制系统、测量系统等部分组成。
当前试验机主要的机型是电子万能试验机,其加载是由伺服电机带动丝杠转动而使活动横梁上下移动而实现的。
在活动横梁和上横梁(或工作台上)安装一对拉伸夹具或压缩弯曲的附件,就组成了加载空间。
伺服控制系统则控制伺服电机在给定速度下匀速转动,实现不同速度下横梁移动或对被测试件加载。
活动横梁的移动速度范围是0.05~500毫米/每分钟。
图1-1 万能材料试验机结构图图1—2 拉伸圆试件 测量系统包括负荷测量、试件变形测量和横梁位移测量。
负荷和变形测量都是利用电测传感技术,通过传感器将机械信号转变为电信号。
负荷传感器安装在活动横梁上,通过万向联轴节和夹具与试件联在一起,测量变形的传感器一般称作引伸计安装在试件上。
拉伸法测金属丝的杨氏模量实验报告

拉伸法测金属丝的杨氏模量实验报告引言:杨氏模量是描述某物质材料在受到拉伸或压缩时,弹性变形程度大小的一个物理量。
在实际应用中,杨氏模量常用于描述金属、合金、非晶态材料等材料的弹性特性。
在本次实验报告中,我们将通过拉伸法测量金属丝的杨氏模量。
实验目的:1. 了解拉伸法测定金属丝杨氏模量的基本原理。
2. 掌握拉伸法测定金属丝杨氏模量的实验方法。
3. 掌握实验数据的处理方法,确定金属丝的杨氏模量。
实验原理:当杆(或丝)在轴向受到拉伸力 F 后,其长度增加ΔL,应变为 E。
定义贯穿力 F、应变 E 和初始长度 L 的比值为一项物理量,称为杨氏模量 Y。
根据杨氏定律可得:$$ Y = \frac {F/A} {\Delta L/L} $$其中 A 为截面面积。
实验步骤:1. 用细钢丝制备试件,长度大于两倍的所需要的长度。
2. 将一个试件端固定,另一端悬挂一重物,使得钢丝呈直线状,测试钢丝的长度L0。
3. 用万能测量仪测试钢丝悬挂重物后的长度 L1。
4. 根据悬挂的重量计算钢丝的拉力 F。
5. 重复以上步骤,重复至少三次,记录不同重量下的拉力及钢丝的长度变化。
6. 计算每个拉力及钢丝长度变化的平均值,并绘制拉力-长度变化曲线。
7. 根据拉力-长度变化曲线计算钢丝杨氏模量 Y。
实验数据及处理:重量(kg)|拉力F(N)|长度变化ΔL(mm)|-|-|-|0.001|0.0098|0.15|0.002|0.0196|0.30|0.003|0.0294|0.45|0.004|0.0392|0.60|0.005|0.0490|0.74|计算钢丝的杨氏模量:平均截面积A = πd^2/4 = π(0.18mm)^2/4 = 2.54×10^(-5)m^2计算平均应变 E 平均长度变化ΔL/L =(0.15mm+0.30mm+0.45mm+0.60mm+0.74mm)/(200mm) = 0.0025E = ΔL/L = 0.0025/5 = 0.0005计算杨氏模量 Y Y = F/A/E =(0.0098N+0.0196N+0.0294N+0.0392N+0.0490N)/(5×2.54×10^(-5)m^2×0.0005) =1.96×10^11 Pa实验结果:经过实验测试,我们得到了金属丝的杨氏模量为 1.96×10^11 Pa。
轴向拉伸实验报告书(共9篇)
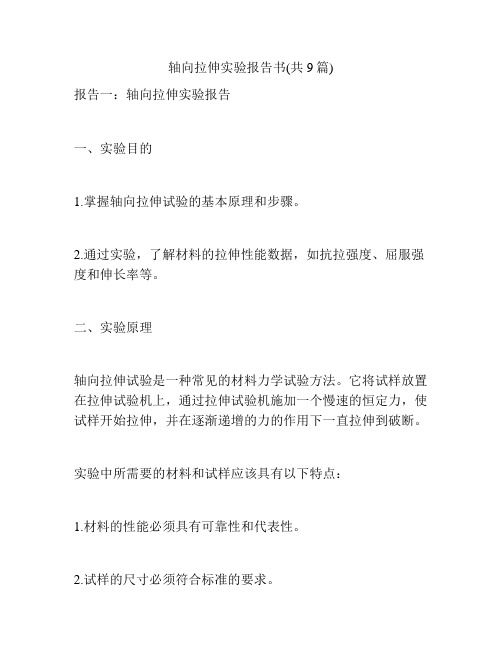
轴向拉伸实验报告书(共9篇)报告一:轴向拉伸实验报告一、实验目的1.掌握轴向拉伸试验的基本原理和步骤。
2.通过实验,了解材料的拉伸性能数据,如抗拉强度、屈服强度和伸长率等。
二、实验原理轴向拉伸试验是一种常见的材料力学试验方法。
它将试样放置在拉伸试验机上,通过拉伸试验机施加一个慢速的恒定力,使试样开始拉伸,并在逐渐递增的力的作用下一直拉伸到破断。
实验中所需要的材料和试样应该具有以下特点:1.材料的性能必须具有可靠性和代表性。
2.试样的尺寸必须符合标准的要求。
3.在测试温度下,试样的畸变应尽可能小。
在轴向拉伸试验中,一般采用的是标准试验方法。
标准试验方法是国家颁布的实验规程和标准测试方法。
标准测试是为了获得所需数据而进行的一系列措施,包括样品的处理、测试设备的标准化、测量和数据处理。
三、实验步骤1.根据所选材料的类型和所需测试数据选择相应的标准试验方法,并详细描述试验过程。
2.按照标准方法的描述准备所需的测试设备和试样。
3.材料标准化和试样的预处理。
4.测试设备校准和校准。
5.测量并记录实验室条件下的试样尺寸。
6.试样的放置与加载。
7.对试样施加稳定的拉力。
8.记录相关数据并进行曲线拟合和计算。
9.拆除试样并清洁测试设备。
四、实验数据处理和分析1.根据试验过程的数据计算试样的实际应力和应变。
2.根据应力-应变曲线可以评估测试材料的机械特性,如弹性模量、屈服强度、抗拉强度、断裂延伸率等。
3.分析实验结果并得出结论。
五、实验结果我们进行了轴向拉伸试验,并得出不同材料的应力-应变曲线。
通过实验,我们可以得到所需的数据,如抗拉强度、屈服强度和伸长率等。
以不锈钢材料为例,做下图,可以看出随着应力的增加,应变也随之增加。
当应力大到一定程度后,材料出现屈服现象,强度值略有下降。
当应力继续增加时,材料的应变继续增加,直到达到极限状态,破断。
我们可以根据应力-应变曲线中的数据计算出材料的力学特性。
六、实验结论与意义1.轴向拉伸试验是一种非常重要的材料力学测试方法,可以评估材料的机械特性,如弹性模量、屈服强度、抗拉强度、断裂延伸率等。
轴向拉伸实验报告

一、实验目的1. 了解轴向拉伸实验的基本原理和操作方法。
2. 学习使用万能材料试验机进行材料力学性能测试。
3. 测定低碳钢在轴向拉伸过程中的应力-应变关系。
4. 计算低碳钢的弹性模量、屈服强度、抗拉强度、延伸率等力学性能指标。
5. 分析低碳钢的拉伸断裂过程和破坏机理。
二、实验原理轴向拉伸实验是材料力学性能测试中最基本、应用最广泛的实验之一。
通过在常温、静载条件下对材料进行轴向拉伸,可以测定材料在拉伸过程中的应力-应变关系,从而得到材料的弹性模量、屈服强度、抗拉强度、延伸率等力学性能指标。
在轴向拉伸实验中,材料受到轴向拉伸力作用,产生轴向应变。
根据胡克定律,在弹性范围内,应力与应变之间存在线性关系,即应力-应变曲线呈直线。
当材料达到屈服点后,应力-应变曲线发生非线性变化,直至材料断裂。
三、实验设备及仪器1. 万能材料试验机:用于施加轴向拉伸力,并测量材料的应力-应变关系。
2. 游标卡尺:用于测量试件尺寸。
3. 引伸计:用于测量试件的轴向应变。
4. 计算机及数据采集系统:用于记录和处理实验数据。
四、实验步骤1. 准备实验材料:选取一定规格的低碳钢试件,并对其进行表面处理,确保试件表面平整、无损伤。
2. 测量试件尺寸:使用游标卡尺测量试件的直径和标距长度,记录数据。
3. 安装试件:将试件安装在万能材料试验机上,确保试件中心线与试验机拉伸方向一致。
4. 设置实验参数:根据试件尺寸和材料特性,设置试验机的拉伸速度、加载速率等参数。
5. 进行实验:启动试验机,使试件在轴向拉伸力作用下产生应变,同时记录应力-应变数据。
6. 分析实验数据:将实验数据导入计算机,绘制应力-应变曲线,计算力学性能指标。
五、实验结果与分析1. 实验数据及曲线(此处插入实验数据表格和应力-应变曲线图)2. 力学性能指标计算根据实验数据,计算低碳钢的弹性模量、屈服强度、抗拉强度、延伸率等力学性能指标:(此处插入力学性能指标计算公式及结果)3. 拉伸断裂过程分析根据应力-应变曲线,分析低碳钢的拉伸断裂过程:(此处插入拉伸断裂过程分析)六、结论1. 通过轴向拉伸实验,成功测定了低碳钢的弹性模量、屈服强度、抗拉强度、延伸率等力学性能指标。
拉伸实验报告总结

拉伸实验报告总结
一、实验目的
1. 学习和掌握拉伸实验的基本原理和方法;
2. 测定材料的拉伸强度、延伸率和断面收缩率等力学性能指标;
3. 分析材料的应力-应变曲线,评估材料的机械性能。
二、实验原理
拉伸实验是材料力学性能测试中最基本的实验之一,主要用于测定材料的拉伸强度、延伸率和断面收缩率等指标。
实验过程中,试样在轴向拉伸力作用下发生变形直至断裂。
通过记录力的变化和试样尺寸的变化,可以计算出材料的各项力学性能指标。
三、实验步骤
1. 准备试样:按照标准制备试样,确保试样的尺寸和形状符合标准要求;
2. 安装试样:将试样安装在拉伸试验机上,确保安装牢固;
3. 设置实验参数:设定拉伸速度、实验力范围等参数;
4. 开始实验:启动拉伸试验机,开始拉伸试样,记录实验数据;
5. 数据处理:根据实验数据计算各项力学性能指标;
6. 结果分析:分析实验数据,评估材料的机械性能。
四、实验结果
通过本次拉伸实验,我们获得了以下实验数据和结果:
序号拉伸力(F) 延伸率(δ) 断面收缩率(Ψ) 拉伸强度(σ)
1 200 10% 50% 20 MPa
2 300 8% 45% 30 MPa
3 400 6% 40% 40 MPa
五、结果分析
根据实验结果,我们可以得出以下结论:
1. 该材料的拉伸强度在20-40 MPa之间,表明该材料具有较好的抗拉性能;
2. 该材料的延伸率在6-10%之间,表明该材料具有一定的塑性变形能力;
3. 该材料的断面收缩率在40-50%之间,表明该材料断裂时断口处会发生较大的收缩。
§4—1材料在拉伸和压缩时力学性能测定实验
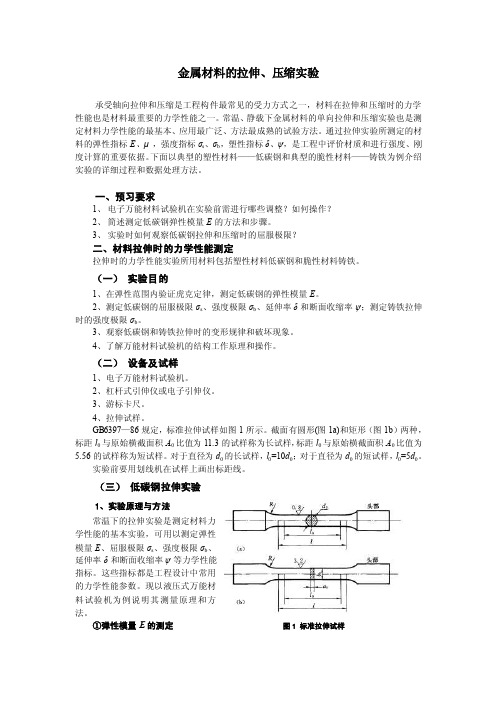
金属材料的拉伸、压缩实验承受轴向拉伸和压缩是工程构件最常见的受力方式之一,材料在拉伸和压缩时的力学性能也是材料最重要的力学性能之一。
常温、静载下金属材料的单向拉伸和压缩实验也是测定材料力学性能的最基本、应用最广泛、方法最成熟的试验方法。
通过拉伸实验所测定的材料的弹性指标E、μ,强度指标σs、σb,塑性指标δ、ψ,是工程中评价材质和进行强度、刚度计算的重要依据。
下面以典型的塑性材料——低碳钢和典型的脆性材料——铸铁为例介绍实验的详细过程和数据处理方法。
一、预习要求1、电子万能材料试验机在实验前需进行哪些调整?如何操作?2、简述测定低碳钢弹性模量E的方法和步骤。
3、实验时如何观察低碳钢拉伸和压缩时的屈服极限?二、材料拉伸时的力学性能测定拉伸时的力学性能实验所用材料包括塑性材料低碳钢和脆性材料铸铁。
(一)实验目的1、在弹性范围内验证虎克定律,测定低碳钢的弹性模量E。
2、测定低碳钢的屈服极限σs、强度极限σb、延伸率δ和断面收缩率ψ;测定铸铁拉伸时的强度极限σb。
3、观察低碳钢和铸铁拉伸时的变形规律和破坏现象。
4、了解万能材料试验机的结构工作原理和操作。
(二)设备及试样1、电子万能材料试验机。
2、杠杆式引伸仪或电子引伸仪。
3、游标卡尺。
4、拉伸试样。
GB6397—86规定,标准拉伸试样如图1所示。
截面有圆形(图1a)和矩形(图1b)两种,标距l0与原始横截面积A0比值为11.3的试样称为长试样,标距l0与原始横截面积A0比值为5.56的试样称为短试样。
对于直径为d0的长试样,l0=10d0;对于直径为d0的短试样,l0=5d0。
实验前要用划线机在试样上画出标距线。
(三)低碳钢拉伸实验1、实验原理与方法常温下的拉伸实验是测定材料力学性能的基本实验,可用以测定弹性模量E、屈服极限σs、强度极限σb、延伸率δ和断面收缩率ψ等力学性能指标。
这些指标都是工程设计中常用的力学性能参数。
现以液压式万能材料试验机为例说明其测量原理和方法。
材料力学拉伸实验实验报告
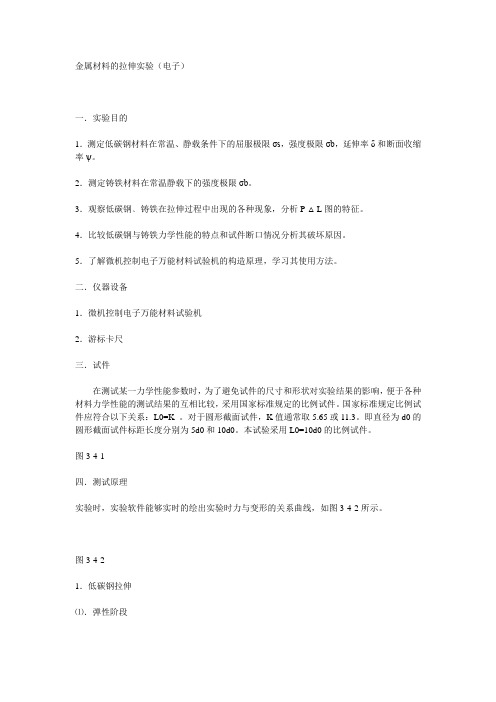
金属材料的拉伸实验(电子)一.实验目的1.测定低碳钢材料在常温、静载条件下的屈服极限σs,强度极限σb,延伸率δ和断面收缩率ψ。
2.测定铸铁材料在常温静载下的强度极限σb。
3.观察低碳钢﹑铸铁在拉伸过程中出现的各种现象,分析P-△L图的特征。
4.比较低碳钢与铸铁力学性能的特点和试件断口情况分析其破坏原因。
5.了解微机控制电子万能材料试验机的构造原理,学习其使用方法。
二.仪器设备1.微机控制电子万能材料试验机2.游标卡尺三.试件在测试某一力学性能参数时,为了避免试件的尺寸和形状对实验结果的影响,便于各种材料力学性能的测试结果的互相比较,采用国家标准规定的比例试件。
国家标准规定比例试件应符合以下关系:L0=K 。
对于圆形截面试件,K值通常取5.65或11.3。
即直径为d0的圆形截面试件标距长度分别为5d0和10d0。
本试验采用L0=10d0的比例试件。
图3-4-1四.测试原理实验时,实验软件能够实时的绘出实验时力与变形的关系曲线,如图3-4-2所示。
图3-4-21.低碳钢拉伸⑴.弹性阶段弹性阶段为拉伸曲线中的OB段。
在此阶段,试件上的变形为弹性变形。
OA段直线为线弹性阶段,表明载荷与变形之间满足正比例关系。
接下来的AB段是一非线弹性阶段,但仍满足弹性变形的性质。
⑵.屈服阶段过弹性阶段后,试件进入屈服阶段,其力与曲线为锯齿状曲线BC段。
此时,材料丧失了抵抗变形的能力。
从图形可看出此阶段载荷虽没明显的增加,但变形继续增加;如果试件足够光亮,在试件表面可看到与试件轴线成45°方向的条纹,即滑移线。
在此阶段试件上的最小载荷即为屈服载荷Ps.⑶.强化阶段材料经过屈服后,要使试件继续变形,必须增加拉力,这是因为晶体滑移后增加了抗剪能力,同时散乱的晶体开始变得细长,并以长轴向试件纵向转动,趋于纤维状呈现方向性,从而增加了变形的抵抗力,使材料处于强化状态,我们称此阶段为材料的强化阶段(曲线CD部分)。
强化阶段在拉伸图上为一缓慢上升的曲线,若在强化阶段中停止加载并逐步卸载,可以发现一种现象——卸载规律,卸载时载荷与伸长量之间仍遵循直线关系,如果卸载后立即加载,则载荷与变形之间基本上还是遵循卸载时的直线规律沿卸载直线上升至开始卸载时的M 点。
低碳钢和铸铁的拉伸实验

实验一 低碳钢和铸铁的拉伸实验一、实验目的要求1.测定低碳钢的流动极限S σ、强度极限b σ、延伸率δ、截面收缩率ψ和铸铁的强度极限b σ。
2.低碳钢和铸铁在拉伸过程中表现的现象,绘出外力和变形间的关系曲线(L F ∆-曲线)。
3.比较低碳钢和铸铁两种材料的拉伸性能和断口情况。
二、实验设备和仪器CMT5504/5105电子万能试验机、游标卡尺等图1-1 CMT5504/5105电子万能试验机三、拉伸试件金属材料拉伸实验常用的试件形状如图所示。
图中工作段长度l 称为标距,试件的拉伸变形量一般由这一段的变形来测定,两端较粗部分是为了便于装入试验机的夹头内。
为了使实验测得的结果可以互相比较,试件必须按国家标准做成标准试件,即d l 5=或d l 10=。
对于一般板的材料拉伸实验,也应按国家标准做成矩形截面试件。
其截面面积和试件标距关系为A l 3.11=或A l 65.5=,A 为标距段内的截面积。
低碳钢拉伸铸铁拉伸图1-2 拉伸试件四、实验原理和方法1.低碳钢拉伸实验低碳钢试件在静拉伸试验中,通常可直接得到拉伸曲线,如图1—3所示。
用准确的拉σ-曲线。
首先将试件安装于试验机的夹头内,之后匀速缓伸曲线可直接换算出应力应变ε慢加载(加载速度对力学性能是有影响的,速度越快,所测的强度值就越高),试样依次经过弹性、屈服、强化和颈缩四个阶段,其中前三个阶段是均匀变形的。
图1-3 低碳钢拉伸曲线OA段,没有任何残留变形。
在弹性阶段,载荷与变形(1) 弹性阶段是指拉伸图上的'是同时存在的,当载荷卸去后变形也就恢复。
在弹性阶段,存在一比例极限点A,对应的应σ,此部分载荷与变形是成比例的。
力为比例极限p(2) 屈服阶段对应拉伸图上的BC段。
金属材料的屈服是宏观塑性变形开始的一种标志,是由切应力引起的。
在低碳钢的拉伸曲线上,当载荷增加到一定数值时出现了锯齿现象。
这种载荷在一定范围内波动而试件还继续变形伸长的现象称为屈服现象。
轴向拉伸实验报告

轴向拉伸实验报告一、实验目的本次实验旨在了解和掌握轴向拉伸试验的原理、方法及结果处理方法,通过实验掌握金属材料的拉伸性能。
二、实验原理轴向拉伸试验是一种常见的金属材料力学性能试验方法,通常用于测试材料的拉伸强度、屈服强度、伸长率等力学性能参数。
实验时,将试样置于试验机的拉伸机械装置中,通过施加拉力使得试样逐渐拉伸,记录下试样的载荷和位移数据,最终得出试样的力学性能指标。
三、实验过程1.准备实验样品,制作试样。
根据实验要求制作试样,并注意试样的尺寸和形状符合要求。
2.安装试样,调整试验机。
将试样装入试验机中,调整试验机的参数和仪器设备,确保实验过程中的安全和准确性。
3.开始实验。
利用试验机施加轴向拉伸载荷,同步记录试样的载荷和位移数据。
在实验过程中,应注意试样的状态和试验机的操作规范。
4.结束实验,处理数据。
试验结束后,将试样取出,记录试样的破坏形态和最终的载荷-位移数据。
根据数据计算出试样的力学性能指标。
四、实验结果通过本次实验,我们得到了以下的结果:试样编号|断口形态|屈服强度(MPa)|极限强度(MPa)|伸长率(%)-|-|-|-|-1|颈缩断|260|300|202|穿孔|310|330|153|减径|290|310|18五、实验分析1.试样的断口形态在本次实验中,试样的断口形态有颈缩断、穿孔和减径等。
颈缩断是指材料发生塑性变形后,断口呈现出缩颈现象的状态;穿孔是指材料的断口出现一个或多个穿孔的状态;减径是指材料在受到外力拉伸作用时,直径逐渐减小的状态。
通过观察试样的断口形态,可以初步判断试样的力学性能状态。
2.试样的屈服强度屈服强度是指材料在受到外力拉伸作用时,材料开始发生塑性变形的最大应力值。
在本次实验中,三个试样的屈服强度分别为260MPa、310MPa和290MPa。
可以看出,试样的屈服强度与试样的形状和尺寸有关,但也受到材料的物理性质等因素的影响。
3.试样的极限强度极限强度是指材料在受到外力拉伸作用时,试样发生破坏的最大应力值。
实验一--低碳钢和铸铁拉伸时力学性能的测定讲解学习

实验一 低碳钢和铸铁拉伸时力学性能的测定一、实验目的1.观察分析低碳钢的拉伸过程,了解其力学性能;绘制拉伸曲线F-△L ,由此了解试样在拉伸过程中变形随载荷的变化规律以及有关物理现象;2.测定低碳钢材料在拉伸过程中的几个力学性能指标:s σ、b σ、δ、ψ;3.了解万能材料试验机的结构原理,能正确独立操作使用。
二、实验设备1.SHT5305拉伸试验机。
2.x —Y 记录仪。
3.游标卡尺。
三、拉伸试样四、实验原理和方法首先将试件安装于试验机的夹头内,之后匀速缓慢加载,试样依次经过弹性、屈服、强化和颈缩四个阶段,其中前三个阶段是均匀变形的。
1.弹性阶段 是指拉伸图上的OA ´段,没有任何残留变形。
在弹性阶段,存在一比例极限点A ,对应的应力为比例极限p σ,此部分载荷与变形是成比例,εσE =。
2.屈服阶段 对应拉伸图上的BC 段。
金属材料的屈服是宏观塑性变形开始的一种标志,是位错增值和运动的结果,是由切应力引起的。
在低碳钢的拉伸曲线上,当载荷增加到一定数值时出现了锯齿现象。
屈服阶段中一个重要的力学性能就是屈服点,对应的屈服应力为0/A F SL S =σ3.强化阶段 对应于拉伸图中的CD 段。
变形强化标志着材料抵抗继续变形的能力在增强。
这也表明材料要继续变形,就要不断增加载荷。
D 点是拉伸曲线的最高点,载荷为F b ,对应的应力是材料的强度极限或抗拉极限,记为b σ0/A F b b =σ4.颈缩阶段 对应于拉伸图的DE 段。
载荷达到最大值后,塑性变形开始局部进行。
这是因为在最大载荷点以后,形变强化跟不上变形的发展,由于材料本身缺陷的存在,于是均匀变形转化为集中变形,导致形成颈缩。
材料的塑性性能通常用试样断后残留的变形来衡量。
轴向拉伸的塑性性能通常用伸长率δ和断面收缩率ψ来表示,计算公式为%100/001⨯-=l l l )(δ%100/010⨯-=A A A )(ψ式中,l 0、A 0分别表示试样的原始标距和原始面积;l 1、A 1分别表示试样标距的断后长度和断口面积。
实验四 金属材料的轴向拉伸实验_2
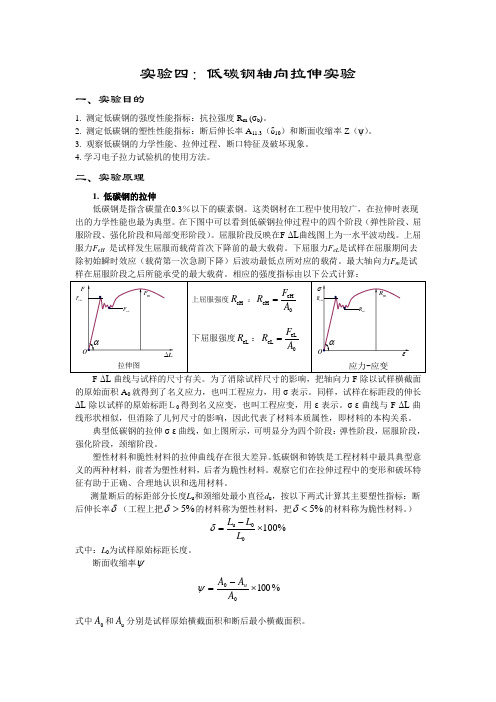
实验四:低碳钢轴向拉伸实验一、实验目的1. 测定低碳钢的强度性能指标:抗拉强度R m (σb )。
2. 测定低碳钢的塑性性能指标:断后伸长率A 11.3(δ10)和断面收缩率Z (ψ)。
3. 观察低碳钢的力学性能、拉伸过程、断口特征及破坏现象。
4. 学习电子拉力试验机的使用方法。
二、实验原理1. 低碳钢的拉伸低碳钢是指含碳量在0.3%以下的碳素钢。
这类钢材在工程中使用较广,在拉伸时表现出的力学性能也最为典型。
在下图中可以看到低碳钢拉伸过程中的四个阶段(弹性阶段、屈服阶段、强化阶段和局部变形阶段)。
屈服阶段反映在F-ΔL 曲线图上为一水平波动线。
上屈服力F eH 是试样发生屈服而载荷首次下降前的最大载荷。
下屈服力F eL 是试样在屈服期间去除初始瞬时效应(载荷第一次急剧下降)后波动最低点所对应的载荷。
最大轴向力F m 是试的原始面积A 0就得到了名义应力,也叫工程应力,用σ表示。
同样,试样在标距段的伸长ΔL 除以试样的原始标距L0得到名义应变,也叫工程应变,用ε表示。
σ-ε曲线与F-ΔL 曲线形状相似,但消除了儿何尺寸的影响,因此代表了材料本质属性,即材料的本构关系。
典型低碳钢的拉伸σ-ε曲线,如上图所示,可明显分为四个阶段:弹性阶段,屈服阶段,强化阶段,颈缩阶段。
塑性材料和脆性材料的拉伸曲线存在很大差异。
低碳钢和铸铁是工程材料中最具典型意义的两种材料,前者为塑性材料,后者为脆性材料。
观察它们在拉伸过程中的变形和破坏特征有助于正确、合理地认识和选用材料。
测量断后的标距部分长度L u 和颈缩处最小直径d u ,按以下两式计算其主要塑性指标:断 后伸长率δ(工程上把%5>δ的材料称为塑性材料,把%5<δ的材料称为脆性材料。
)u 0100%L L L δ-=⨯ 式中:L 0为试样原始标距长度。
断面收缩率ψ%10000⨯-=A A A uψ 式中0A 和u A 分别是试样原始横截面积和断后最小横截面积。
拉伸实验

试验一 拉伸实验拉伸试验是测定材料在静载荷作用下力学性能的一个最基本最重要的试验。
通过拉伸试验所得的力学性能指标,在整个材料力学的强度计算中几乎都要用到。
更重要的是,工程设计中所选用的材料力学性能指标大都是以拉伸试验为主要依据的。
本次试验将选用低碳钢作为塑性材料的代表,做拉伸试验。
一、实验目的1)测定低碳钢的屈服强度s σ,抗拉强度b σ。
断后伸长率δ和断面收缩率ψ2)观察低碳钢在拉伸过程中所出现的各种变形现象(包括屈服、强化和缩颈等),分析力与变形之间的关系,并绘制拉伸图。
3)分析低碳钢力学性能的特点和试件断口情况,分析其破坏原因。
4)学习、掌握万能试验机的使用方法及其工作原理。
二、实验设备(1)试件:材料的力学性能是通过拉伸试验来确定的,因此,必须把所测试的材料加工成能被拉伸的试件。
试验表明,试件的尺寸和形状对试验结果有影响。
为了避免这种影响和便于使各种材料力学性能的测试结果进行比较,国家标准对试件的尺寸和形状作了统一的规定,拉力试件分为比例的和非比例的两种。
比例试件应符合如下的关系:L 0=K ·A 0 (1-1)式中 L 0――标距,用于测量拉伸变形,单位为mm;A 0――标距部分试件的断面积;K ――系数,K =5.56或K =11.3,前者称为短试件,后者称为长试件。
据此,直径为d 0的短、长圆形试件的标距长度L 0分别为5d 0和10d 0;非比例试件的标距与其横截面间则无上述关系,而是根据制品(薄板、薄带、细管、细丝、型材等)的尺寸和材料的性质规定出平行长度L 和标距长度L 0。
长试件见图1-1。
试件两端较粗的部分为装入试验机夹头中的夹持部分,起传递拉力之用。
它的形状及尺寸可根据试验的夹头形式而定。
本实验采用非比例试件。
图1-1 圆形拉伸试件(2)实验装置:万能试验机或拉力试验机。
试验机的夹头有各种形式,一般采用夹板式,如图1-2。
图形截面试件所用的夹板如图1-3所示。
- 1、下载文档前请自行甄别文档内容的完整性,平台不提供额外的编辑、内容补充、找答案等附加服务。
- 2、"仅部分预览"的文档,不可在线预览部分如存在完整性等问题,可反馈申请退款(可完整预览的文档不适用该条件!)。
- 3、如文档侵犯您的权益,请联系客服反馈,我们会尽快为您处理(人工客服工作时间:9:00-18:30)。
材料轴向拉伸参数测试
一、实验目的
1.观察低碳钢和铸铁在拉伸过程中显示的各种现象(屈服、强化、颈缩、断口特征等)。
2.测定低碳钢的上屈服强度、下屈服强度、抗拉强度、弹性模量eH R eL R m R E、断后伸长率、断面收缩率3.11A Z 、最大拉力。
m F 3.绘制低碳钢拉伸曲线图(LFΔ−曲线)。
4.测定铸铁的抗拉强度及最大拉力。
m R m F 5.比较低碳钢与铸铁的力学性能特征。
6.掌握电子万能试验机的工作原理及操作方法。
二、实验设备及试件
1.CSS44100型电子万能试验机(包括EDC100型数字控制器、计算机、打印机)。
2.游标卡尺。
3.引伸计。
4.实验试件,参照国家标准GB/T228–2002采用圆截面比例试件(如图2-5所示),
00S k L=,其中为原始标距;系数=11.3;为原始横截面积。
0L k 0S
图2–5 试件图
试件两端直径较粗的部分为试件的夹持端,中间为试验段,在试验段和夹持端之间为圆弧过渡连接。
三、实验原理及方法
低碳钢拉伸分为弹性、屈服、强化、破坏四个阶段,见图2-6。
试件夹紧后,将变形引伸计正确安装在试件表面,变形引伸计用于测量低碳钢拉伸弹性阶段的变形,试验进入
图中,为整个试件的伸长,试件开始受力时,由于试件两头的夹持端与夹具有相对位移,所以拉伸图最开始是由曲线过渡到直线的。
LΔ低碳钢拉伸到一定值时,负荷突然下降,试件开始屈服,图形出现锯齿状,图中B点为试件发生屈服对应首次下降前的最高应力,即上屈服强度eHR,而负荷首次下降的最低点因为有初始瞬时效应,故不作为强度指标,B′为初始瞬时效应之后的最低应力,即下屈服强度LRe。
屈服阶段过后,进入第Ш阶段即强化阶段。
曲线缓慢上升,试件承受的负荷继续增大,拉伸位移也不断增加,当负荷接近最大值时,拉伸曲线趋于平缓,强化阶段即将过渡到破坏阶段。
当负荷从最大值开始下降时,试件表面某一局部出现“颈缩”现象,随着试件承载能力的急骤下降,“颈缩”越来越明显,试件被迅速拉断。
取下试件,按计算机提示输入低碳钢试件断裂后“颈缩”最细处的直径du 以及断后标距Lu ,并根据试验数据选项要求自动计算试验结果。
ReH =
0eH SF, ReL =0
eL SF
, =m R 0
m SF
3.11A=
00u LLL−-×100%, Z=0
u 0SS
S−×100% 式中:eH R ⎯⎯上屈服强度,/mm Ν2
;
eL R⎯⎯下屈服强度,/mm Ν2
;
Rm ⎯⎯抗拉强度,/mm Ν2
;
F eH ⎯⎯力首次下降前的最大拉力,;
ΝF eL ⎯⎯不计初始瞬时效应时屈服阶段中的最小拉力,; ΝF m ⎯⎯最大拉力,;
Ν0S ⎯⎯试件原始横截面积,mm 2
;
S u ⎯⎯断后最小横截面积,mm 2
; 3.11A ⎯⎯断后伸长率,% ;
L⎯⎯断后标距,mm; 0L⎯⎯原始标距,mm;
Z ⎯⎯断面收缩率,%。
铸铁拉伸试验时变形很小,没有屈服和“颈缩”现象,当载荷达到最大时突然断裂,图
2–7为铸铁拉伸曲线图。
图2–7 铸铁拉伸曲线图
四、实验步骤 1.试件尺寸测量
用游标卡尺分别测量试件试验段上、中、下三个不同截面的直径,每一横截面沿互相垂直的两个方向各测量一次直径,取其平均值作为该截面的直径,最后取三个截面中直径 最小的,计算试件横截面积,同时测出长度作为原始标距。
0S 0L 2.试验机开启、联机
接通电源,打开EDC100型数字控制器的电源开关和计算机、显示器、打印机电源开关,启动控制系统,系统开始自检。
当控制器屏幕上出现PCcontrat 字母后,在Windows 窗口用鼠标双击CSS44100快捷图标,或打开CSS44100程序,进入试验程序界面。
用鼠标左键点击界面左侧的“联机”按钮,稍候,再按下数字控制器前面板上的“ON”按钮,此时整个测控系统已准备就绪。
3.试件安装
先旋松试验机上、下夹头,使试件两头夹持端能放入夹块中。
根据试件长度,操作活动横梁位移摇控器的上(下)箭头按钮,使活动横梁上(下)移动,调整试验空间位置,使试验机上、下两夹头能充分夹住试件两头夹持端,动横梁移动速度可通过遥控器上的旋钮进行无级调节。
低碳钢拉伸试验时,需将引伸计正确安装在试件上,引伸计用于精确测量试件拉伸时的变形大小。
引伸计安装前插上定位销(用于初始定位),再将引伸计两刀口垂直于试件表面,分别用橡皮筋固定在试件上(铸铁拉伸试验不需安装引伸计,切记!),引伸计安装好后必须拔出定位销。
4.试验条件及参数的设定
试验程序主界面包括七组下拉菜单,分别是文件、条件、结果、曲线、试验、横梁、帮助。
试验正式开始前,需进行试验条件和参数的设定,试验条件包括:文件名称、试验类型、试样材料、试样形状、选择计算项目、输入试件尺寸以及打印报告。
在选取计算项目时,铸铁选择最大负荷和抗拉强度,低碳钢除选取最大负荷和抗拉强度外,还需计算弹性模量、上屈服强度、下屈服强度、断后伸长率、断面收缩率。
低碳钢拉伸试验的数据跟踪方式采用“负荷-变形”,铸铁拉伸试验的数据跟踪方式采用“负荷–位移”。
低碳钢和铸铁的拉伸一般采用速度控制方式,低碳钢的加载速度可设为5 mm/min,铸铁的加载速度不超过2 mm/min。
5.正式开始试验
用鼠标右键单击负荷数据显示框,再按左键进行“清零”,位移和变形按同样方式分别清零。
按下“开始试验”按钮,主界面上自动绘制出“负荷–变形”(低碳钢)或“负荷–位移”(铸铁)试验曲线。
低碳钢拉伸试验采用引伸计测变形,当负荷增加到一定值时试件开始屈服,试验曲线下降,此时,用鼠标点击“摘引伸计”按钮,并取下引伸计。
如果当变形达2 mm 时,界面将出现“摘引伸计”提示框,取下引伸计。
试验过程中,应同时注意观察图形和试件的变化,如低碳钢的“颈缩”现象,直到试件断裂,取下试件。
用游标卡尺分别测量两个断口的最小处直径,同一截面相互垂直各测一次并计算出平均值,取两个平均值中的最小值作为断口直径d u 。
将两段试件对齐,测量断后标距L u ,输入计算机。
试验结束后,计算机自动计算并显示结果,打开“结果”菜单中的“打印”,将曲线
坐标选择为“负荷–位移”
,打印试验结果。
6.关闭试验机
退出程序,关闭计算机、显示屏、打印机及数控器电源,清理实验场地。
五、实验结果处理
1.断口位置对断后标距的影响
试验前在标距0L范围,将试件等分刻画10个小格,试件断裂后,分成两段(长段与短段),设短段断口到标线的距离为,当>OA OA 0L/3时,将两段试件对齐在一起,直接测量两标线的距离作为u L;当≤OA 0L/3时,采用图2–8所示的断口移中法。
在长段上从断口量取等于的格数得点,若长段内所余格数为偶数时,取其中央刻线为OA B C点(图2-8 (b)),断后标距为:
Lu =+
ABBC2
图2–8 断口移中示意图
若所余格数为奇数时,取余格中间两刻线分别为C点和C1点(图2-8(c))断后标距为:
u L=+ABBC+1BC
而后用断后标距u L计算伸长率。
当断口位于标距端点或以外时,试验结果无效,应重做试
验。
2.实验报告
实验报告是实验者最后提交的成果,是实验资料的总结,包括下列内容:
(1)实验名称、实验日期、实验者及组员姓名。
(2)实验目的及装置,应画出装置简图。
(3)实验设备,包括使用的机器设备名称、型号、精度等,以及其它量具的名称、精度。
(4)试件尺寸和形状(包括破坏后断口的形状)。
(5)实验数据与图形整理。
(6)在报告的最后部分应对实验结果进行分析,说明本实验的优缺点,主要结果是否正确,并对误差加以分析,回答思考题。
在附录二中,给出了实验报告的参考格式,供实验者参考。
六、注意事项
1.正确操作试验机。
2.试件安装必须正确、防止偏斜和夹入部分过短的现象。
3.试验时听见异常声音或发生故障,应立即按下EDC100型数控器前面板上的红色按钮。
4.试验机活动横梁上禁止放置任何易掉落物件。
七、思考题
1.低碳钢拉伸时安装引伸计的目的?何时摘下?控制方式作何转变?
2.比较低碳钢和铸铁拉伸时的力学性质异同。