BIQS-22返工返修
质量门
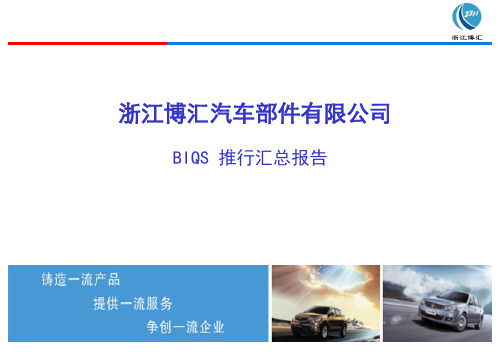
BIQS-14 变更管理-试生产运行 BIQS-19 过程控制文件:PFMEA-CP-WI BIQS-20 按CP 要求实施
BIQS-6 防错验证
BIQS-11 标准化操作
制 造
BIQS-15 暗灯系统
BIQS-16 报警与升级
BIQS-26 维护保养
BIQS-25 异物控制
浙江博汇汽车部件有限公司
BIQS 推行汇总报告
BIQS 要素
BIQS-1 合格/不合格物料区分 BIQS-2 分层审核 BIQS-7 量具校准及测量系统分析 BIQS-8 快速响应 BIQS-9 团队合作解决问题
质 BIQS-10 质量关注点检查 量 BIQS-13 质量门(验证岗位/终检/CARE/GP12)
物 流
BIQS-27 FIFO/物料搬运过程
BIQS-28 认可包装发运
BIQS -13
BIQS-13 质量门
BIQS-13 质量门(验证岗位/终检/CARE/GP12)
标准化质 量门流程
确定零件 清单
发布作业指 导书
WI-PRO-008 早期遏制管理规定 BH/QP-02 记录控制程序 BH/QP-28 看板
GP12检查记录
BIQS-13 质量门(验证岗位/终检/CARE/GP12) 发现问题处理对策
质量异常登记表
BIQS-13 质量门(验证岗位/终检/CARE/GP12) 满足退出条件退出
BIQS-17 感官检验 BIQS-18 感官检验标准-沟通和理解 BIQS-21 过程能力研究 BIQS-22 返工返修 BIQS-23 前馈后馈
管 BIQS-24 培训 理 采 购 BIQS-29 分供方管理
BIQS教材-供应商实施BIQ模块介绍

合格/不合格物料区分 分层审核 PFMEAs PFMEAs - 风险降低和年度回顾 临时替代/偏差管理 防错验证 量具校准及测量系统分析 (新增) 快速响应 团队合作解决问题 质量关注点检查 标准化操作 变更管理 质量门(验证岗位/终检/CARE/GP12) 变更管理-生产试运行(PTR) 暗灯系统
Dat e: Smart # : Family/ RPO: Part # : Serial # : Test Order # : Last Op/ Area: Tagged By: Reason f or SCRAP:
清晰的标识是有效避免不合格品被错误使用的前提!
SDE Module V1.0 2018.3
BIQS
4
4
BIQS-30 安全/Safety
BIQS
常见的安全要求/风险: ➢ 锁定 / 警示标识 ➢ 设备相关安全提示 / 警告 ➢ 滑倒 / 绊倒风险(如管线、地面上的油/水残留) ➢ 空气质量(如粉尘 / 烟雾 / 气味) ➢ 车辆交通事故(如物流叉车、拖车、推车等) ➢ 停车场安全(如结冰 / 绊倒) ➢ 个人安全防护装备(PPE)的有效配置和使用 ➢ 火灾风险(如焊渣飞溅 / 火花 / 熔融材料) ➢ 碰撞风险(如横梁、突出物等) ➢ 挤压风险(移动的料架等) ➢ 夹伤风险(门、工装、物料等) ➢ 其他
快速响应 团队合作解决问题 暗灯系统 合格/不合格物料区分 报警与升级 返工返修 质量门(验证岗位/终检/CARE/GP12) 前馈后馈 先进先出/物料搬运过程 认可的发运包装 标准化操作 维护保养 培训 防错验证 临时替代/偏差管理 分层审核 质量关注点检查 PFMEAs PFMEAs -风险降低和年度回顾 异物管理 分供方管理 变更管理 变更管理-生产试运行(PTR)
BIQS(BuiltInQualitySupply)制造质量供应培训教材PPT

BIQS(BuiltInQualitySupply)制造质量供应培训教材PPT内容导读BIQS的全称是Built-In Quality Supply-based,供应商制造质量体系。
是美国通用汽车供应商质量评估体系QSB+(Quality Systems Basic+)的前身,是通用汽车公司总结的一套用于提升供应商质量体系能力的最佳实践,是根据通用汽车公司全球制造系统GMS(精益生产系统)提炼出来的精华,用于提升供应商的制造质量能力。
BIQS审核条款介绍:BIQS -1 Nonconforming Material / Material Identification 不合格材料与材料标识BIQS-2 Layered Process Audit 过程分层审核BIQS-3 PFMEAs 过程潜在失效模式及后果分析BIQS-4 PFMEAs - Risk Reduction & Annual Review PFMEA-风险降低与年度评审BIQS-5 ByPass Management 应急替代管理BIQS-6 error proofing Verification 防错装置验证BIQS-7 Gage Calib ration / Measurement System Analysis 量检具校准+测量系统分析BIQS-8 Fast Response Problem Solving Process 快速反应问题解决流程BIQS-9 Team Problem Solving Process 团队问题解决流程BIQS-10 质量关注检查BIQS-11 Standardized Work 标准化作业BIQS-12 过程变更控制BIQS-13 验证岗位(最终检测/CARE/GP12)BIQS-14变更控制-量产试运行/PTRBIQS-15 按灯系统实现BIQS-16 报警及逐级上报BIQS-17 Visual Controls 目视化控制BIQS-18 目视化标准-沟通与理解BIQS-19 过程控制BIQS-20 过程控制计划实施BIQS-21过程能力评审BIQS-22 返工 / 返修确认BIQS-23 后馈与前馈BIQS-24 Training 培训BIQS-25 异物要求BIQS-26 Maintenance 维护BIQS-27 先进先出与材料处理流程BIQS-28 批准包装发运BIQS-29供应链管理BIQS-30 Safety 安全什么是质量?质量管理的3个阶段:质量管理是指为了实现质量目标,而进行的所有管理性质的活动,质量管理的发展大致经历了3个阶段:质量检验阶段、统计质量控制阶段和全面质量管理阶段。
BIQS条款最新解读及任务分解(1)
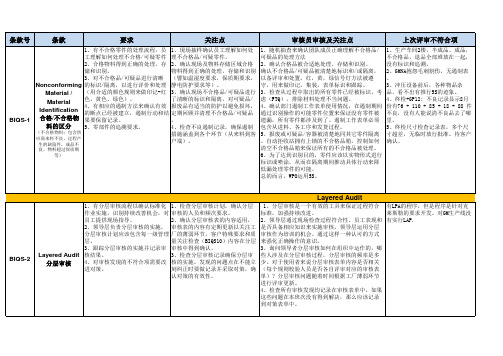
。
2、确认快速响应板上问题,变化 制计划和作业指导书。
PFMEAs - Risk Reduction &
点,客户反馈及内部过程问题相关 3、跨功能产线现场评审来降低RPN。 的内容在PFMEA中得到更新。 3、确认反向PFMEA识别的项目是否
Annual Review
体现在流程图,PFMEA,控制计划
PFMEAs-风险降
和作业指导书的更新中。
低&年度评审
BIQS-5
1、工厂应识别可屏蔽的制造过程 1、确认供应商屏蔽清单(防错及
和防错装置。对所有批准的屏蔽过 生产过程)
程,要评估替代方案的RPN值和风 2、确认FMEA中对屏蔽过程进行了
险,每一个屏蔽过程的替代方案都 RPN风险分析。现场确认屏蔽过程
跨功能小组完成,包括制造团队的 质量,SQ,维护等。
造团队成员。确认RPN值符合严重度、频度和探测 一致。建议按照通用要求根据三种
输入,严重度,频度和探测度打分 2、询问PFMEA是如何用于防错和过 度打分准则。
不同后果打分。
严格遵循SOD表要求。
程控制的,查看相关案例。
2、确认所有材料处理中可能的失效模式均包含在 3、发生度:没有按照AIAG要求根
有LPA的程序,但是程序是针对克 莱斯勒的要求开发。对GM生产线没 有实行LAP.
BIQS-3
Managing Risk
1、运用PFMEA来辨识所有操作存 1、确认PFMEA编制小组包含了不同 1、检查工厂内所有操作工序均包含在PFMEA中。 1、S.O.D打分标准需改善。
在的风险。PFMEA workshop应由 功能团队人员,譬如设计,制造, 确认PFMEA研讨会是由交叉功能小组完成,包括制 2、严重度:同样划伤,严重度不
BIQS教材-模块介绍

只要触发报警就应考虑启动遏制 ; 原材料/分供方; 来料;
标签、标记、色标、划线区域等;
建议标签包含产品名称、发生工位、时间、 数量、发现人、判定人
R eason C hecked:
SDE Module V1.0 2018.3
11
BIQS-1 Nonconforming Material / Material Identification 合格/不合格物料区分
特殊板片错 扁管碰伤 漏冲U型槽
碰伤 管口脏污 U型槽过浅
碰伤
上壳体安装点位置度不过 模式摇臂脱出 温度风门连杆脱出 加热器盖安装点位置度不过 温度拉索阻滞 总成检大漏NG 后风道盖板位置度不过 温度风门堵转 冷却风道安装不到位 钎剂污染 管口有异物 钎剂污染 漏装海绵条 外观碰伤 漏装减震垫 管口划伤 泄漏
通过标准化定义、相关文件等有效配置、有效的培训 BIQS-24 培训
关注对可疑品的定义和识别;
可疑品 - 生产过程中无法直接判定是合格品,也不能直接判定为不符合品的。
报废 报废
缺料
SDE Module V1.0 2018.3
9
标准化的缺陷定义
零件缺陷类型汇总
零件种类 注塑类 零件名称 大壳体 风门 模式盘( SGM308&318) 鼓风机 伺服电机 步进电机 调速电阻 热敏电阻 温度传感器 蒸发器芯体 暖风芯体 暖风芯体进出口管 膨胀阀 密封条 SGM308&318 空调箱总成 总成 GAMMA 空调箱总成 D2UB 空调箱总成 水箱 冷凝器 断裂 断裂 断裂 抖动 异响 异响 电流NG 功能测试NG 电阻值NG 泄漏 泄漏 划伤 划伤 粘贴偏位 下壳体安装点位置度不过 暖风进出口管位置度不过 膨胀阀位置度不过 总成检大漏NG 下壳体安装点位置度不过 双头螺钉位置度不过 温度风门堵转 下壳体安装点位置度不过 双头螺钉位置度不过 漏装橡皮泥 变形 泄漏 变形 双头螺钉松动 抖动 线束插头破损 变形 变形 变形 漏贴海绵条 缺料 异响 堵转 堵转 缺陷类型 缺料 软胶变形 堵转 电流NG 步数NG 飞边 温度风门柱头断裂 电流NG 电流NG 堵孔
BIQS考试题库
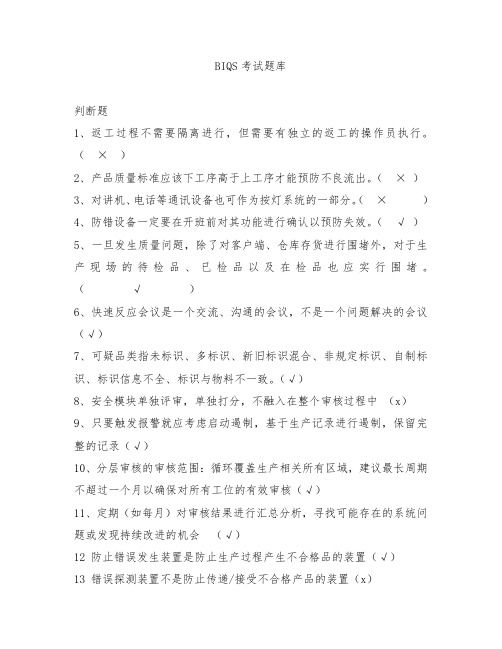
BIQS考试题库判断题1、返工过程不需要隔离进行,但需要有独立的返工的操作员执行。
(×)2、产品质量标准应该下工序高于上工序才能预防不良流出。
(×)3、对讲机、电话等通讯设备也可作为按灯系统的一部分。
(×)4、防错设备一定要在开班前对其功能进行确认以预防失效。
(√)5、一旦发生质量问题,除了对客户端、仓库存货进行围堵外,对于生产现场的待检品、已检品以及在检品也应实行围堵。
(√)6、快速反应会议是一个交流、沟通的会议,不是一个问题解决的会议(√)7、可疑品类指未标识、多标识、新旧标识混合、非规定标识、自制标识、标识信息不全、标识与物料不一致。
(√)8、安全模块单独评审,单独打分,不融入在整个审核过程中(x)9、只要触发报警就应考虑启动遏制,基于生产记录进行遏制,保留完整的记录(√)10、分层审核的审核范围:循环覆盖生产相关所有区域,建议最长周期不超过一个月以确保对所有工位的有效审核(√)11、定期(如每月)对审核结果进行汇总分析,寻找可能存在的系统问题或发现持续改进的机会(√)12 防止错误发生装置是防止生产过程产生不合格品的装置(√)13 错误探测装置不是防止传递/接受不合格产品的装置(x)14 质量关注点是固定不变的(x)15 暗灯系统是一个应用在办公室的实时呼叫控制系统(x)16 感官检验是标准化操作的一部分,相关的要求应在对应的标准化操作指导书中体现(√)17 返工:为使不合格产品或服务符合要求的而对其采取的措施;(√)18 返修:为使不合格产品或服务满足预期用途而对其采取的措施;返修操作不需获得顾客批准;(x)19 SPC、全检、巡检、防错属于特殊特性的管控方式:(x)20 只要是制造工序发生的变更,都需要进行试生产对产品进行重新验证(x)。
21 变更后的产品都有明确标识并隔离放置(√)。
22 所有的变化点都应得到客户批准并形成记录(x)。
23 同一型号之间的生产设备转换不需要得到客户批准(x)。
BIQS基础培训

审核结果决定
产品绩效决定
BIQS1:不合格物料及物料标识
物料标识
“从被动到主动”
废品
可疑品或待处理品
半成品或合格品
标签内容
IN THIS SECTION IS AT LOCAL DISCRETION
BIQS的概要
BIQS 推进目的
“从被动到主动”
通过BIQS的策略运行,能够在项目投产前后的周期内, 提供大批量,稳定,合格的产品给GM(通用汽车) 投 产 前 后 周 期 大 批 量 稳 定 合 格 (标准化作业)
OTS/PPV
35W
SOP
3个月
EOA
大批量:BIQS,QSB 策略的运行
稳 合 定:通过了解PROCESS合格率,CPK,一次下线率等确认工程稳定性 格:对比图面,标准,塑模,SOR(报价单)技术要求确认是否合格
4. 标准化操作
5. 培训 6. 分层审核 7. 风险降低
8. 异物管理
9. 供应链管理 10. 变更管理
2005~2012年版
2013~2014年版
2015年版~
Quality(由品质负责) Manufacturing(由生产负责) Enterprise(全员品质)
初级
中级
高级
BIQS的概要
BIQS 的流程
审核供应商 识别差距 不能自审 (习惯,自满,认知程度)
“从被动到主动”
GM全球供应商BIQS的建立和认证
课堂培训
实施跟踪 预审核
GM对BIQS认证要求:
监控和维护
BIQS条款最新解读及任务分解
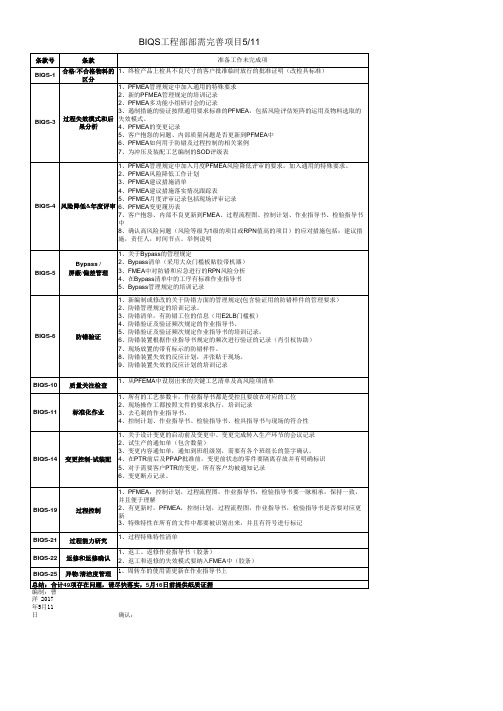
BIQS-5 BIQS-6
Bypass / 屏蔽/偏差管理
防错验证
1、关于Bypass的管理规定 2、Bypass清单(采用大众门槛板贴胶带机器) 3、FMEA中对防错和应急进行的RPN风险分析 4、在Bypass清单中的工序有标准作业指导书 5、Bypass管理规定的培训记录
1、新编制或修改的关于防错方面的管理规定(包含验证用的防错样件的管理要求) 2、防错管理规定的培训记录。 3、防错清单,有防错工位的信息(用E2LB门槛板) 4、防错验证及验证频次规定的作业指导书。 5、防错验证及验证频次规定作业指导书的培训记录。 6、防错装置根据作业指导书规定的频次进行验证的记录(肖引权协助) 7、现场放置的带有标示的防错样件。 8、防错装置失效的反应计划,并张贴于现场。 9、防错装置失效的反应计划的培训记录
过程失效模式和后 失效模式。
果分析
4、PFMEA的变更记录
5、客户抱怨的问题、内部质量问题是否更新到PFMEA中
6、PFMEA如何用于防错及过程控制的相关案例
7、为冲压及装配工艺编制的SOD评级表
1、PFMEA管理规定中加入月度PFMEA风险降低评审的要求,加入通用的特殊要求。 2、PFMEA风险降低工作计划 3、PFMEA建议措施清单 4、PFMEA建议措施落实情况跟踪表 5、PFMEA月度评审记录包括现场评审记录 BIQS-4 风险降低&年度评审 6、PFMEA变更履历表 7、客户抱怨、内部不良更新到FMEA、过程流程图、控制计划、作业指导书、检验指导书 中 8、确认高风险问题(风险等级为1级的项目或RPN值高的项目)的应对措施包括:建议措 施,责任人,时间节点。举例说明
BIQS-14
变更控制-试装配
1、关于设计变更的启动前及变更中、变更完成转入生产环节的会议记录 2、试生产的通知单(包含数量) 3、变更内容通知单,通知到班组级别,需要有各个班组长的签字确认。 4、在PTR前后及PPAP批准前,变更前状态的零件要隔离存放并有明确标识 5、对于需要客户PTR的变更,所有客户均被通知记录 6、变更断点记录。
IATF16949与与QSB+、BIQS对照表

IATF 16949:2016版本与与QSB+、BIQS对照表8.2.1.1顾客沟通-补充QSB+10:变更管理之应急计划BIQS-5:应急替代管理8.2.2 与产品和服务有关要求的确定8.2.2.1 产品和服务要求的确定-补充8.2.3 与产品和服务有关要求的评审8.2.3.1 略8.2.3.1.1 产品和服务要求的评审-补充8.2.3.1.2 顾客指定的特殊特性8.2.3.1.3 组织制造可行性8.2.3.2 略8.2.4 与产品和服务有关要求的更改8.3 产品和服务的设计和开发8.3.1 总则8.3.1.1 产品和服务的设计开发-补充8.3.2 设计和开发策划8.3.2.1 设计和开发策划-补充BIQS-3:过程潜在失效模式及后果分析;BIQS-19:过程控制计划8.3.2.2 产品设计技能8.3.2.3 带有嵌入式软件产品的开发8.3.3 设计和开发输入8.3.3.1 产品设计输入8.3.3.2 制造过程设计输入8.3.3.3 特殊特性BIQS-3:过程潜在失效模式及后果分析;BIQS-19:过程控制计划8.3.4 设计和开发控制8.3.4.1 监视8.3.4.2 设计和开发确认8.3.4.2 原型样件方案BIQS-19:过程控制计划8.3.4.4 产品批准过程8.3.5 设计和开发输出8.3.5.1 设计和开发输出-补充QSB+13:外部物流BIQS-28:批准包装发运8.3.5.2 制造过程设计输出BIQS-21:过程能力评审 8.3.6 设计和开发更改8.3.6.1 设计和开发更改-补充QSB+10:变更管理BIQS-12:过程变更控制 8.4 外部提供过程、产品和服务的控制QSB+13:外部物流8.4.1 总则8.4.1.1 总则-补充8.4.1.2 供应商选择过程QSB+9:供应链管理BIQS-29:供应链管理8.4.1.3 顾客指定的货源QSB+9:供应链管理BIQS-29:供应链管理8.4.2 控制类型和程度8.4.2.1 控制类型和程序-补充8.4.2.2 法律和法规要求8.4.2.3 供应商质量管理体系开发QSB+9:供应链管理BIQS-29:供应链管理8.4.2.3.1 汽车产品-汽车产品相关要求或带有嵌入式软件的汽车产品8.4.2.4 供应商监视QSB+9:供应链管理BIQS-29:供应链管理8.4.2.4.1 第二方审核QSB+9:供应链管理BIQS-29:供应链管理8.4.2.5 供应商开发QSB+9:供应链管理BIQS-29:供应链管理 8.4.3 外部供方的信息8.4.3.1 外部供方的信息-补充QSB+9:供应链管理BIQS-29:供应链管理 8.5 生产和服务提供8.5.1 生产和服务提供的控制QSB+13:外部物流9.2.2.2 质量管理体系审核9.2.2.3 制造过程审核QSB+6:过程分层审核BIQS-2:过程分层审核BIQS-10:质量关注检查9.2.2.4 产品审核QSB+3:验证工位BIQS-13:验证岗位(最终检测/CARE/GP12)9.3 管理评审9.3.1 总则9.3.1.1 管理评审-补充9.3.2 管理评审输入9.3.2.1 管理评审输入-补充9.3.3 管理评审输出9.3.3.1 管理评审输出-补充10 改进10.1 总则QSB+1:快速反应QSB+7:风险降低BIQS-8:快速反应问题解决流程BIQS-4:PFMEA-风险降低与年度评审10.2 不合格和纠正措施 10.2.1 略10.2.2 略10.2.3 问题解决QSB+1:快速反应之有效问题解决BIQS-9:团队问题解决流程10.2.4 防错QSB+3:防错装置验证BIQS-6:防错装置验证 10.2.5 保修管理体系10.2.6 顾客投诉及使用现场失效测试分析10.3 持续改进QSB+1:快速反应QSB+7:风险降低BIQS-8:快速反应问题解决流程BIQS-4:PFMEA-风险降低与年度评审10.3.1 持续改进-补充。
BIQS教材-模块介绍

BIQS-9 团队合作解决问题
BIQS-23 前馈后馈
BIQS-10 质量关注点检查
BIQS-24 培训
BIQS-11 标准化操作
BIQS-25 异物控制
BIQS-12 变更管理
BIQS-26 维护保养
BIQS-13 BIQS-14 BIQS-15
质量门(验证岗位/终检/CARE/GP12) BIQS-27 先进先出/物料搬运过程
返工返修
BIQS- 质量门(验证岗位/终检
13
/CARE/GP12)
BIQS23
前馈后馈
BIQS- 先进先出/物料搬运过程
27
BIQS28
认可的发运包装
QSB- 标准化操
BIQS11
标准化操作
23个细分模 块
4
作
QSB5
培训
BIQS26 BIQS24
维护保养 培训
QSB- 防错验证
BIQS6
防错验证
零件种类
零件名称
大壳体
注塑类 风门
模式盘(SGM308&318)
鼓风机
伺服电机
电器类
步进电机 调速电阻
热敏电阻
温度传感器
蒸发器芯体
芯体类 暖风芯体 暖风芯体进出口管
膨胀阀
其他 密封条
SGM308&318 空调箱总成
总成 GAMMA 空调箱总成
D2UB 空调箱总成
水箱
冷凝器 CRFM
风扇
中冷器 油冷器
合格/不合格物料区分 ➢ 合格/不合格品的定义和识别;
BIQ S
➢ 合格/不合格品的标识、隔离、记录和处置;
➢ 不合格品遏制;
准备
应用
BIQS基础培训
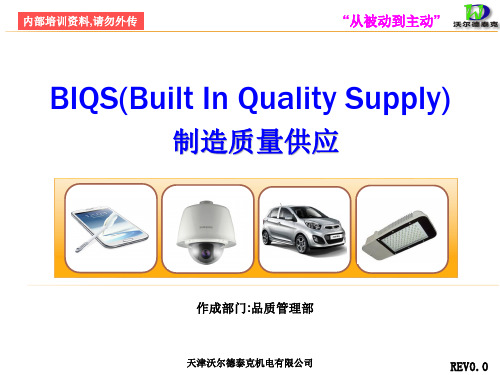
LOCATION
可能存在的 数量
区域 确认人
可疑品 发现数量
Receiving 收货区
500 P.S.
500
Laboratory 实验室
6 K.C.
6
WIP Storage Areas 在制品放置区
1000 P.S.
1000
Outside Processing - (Plating)外加工 1000
1. 快速反应 2. 不合格品控制 3. 验证岗位&防错验证 4. 标准化操作 5. 培训 6. 分层审核 7. 风险降低 8. 异物管理 9. 供应链管理 10. 变更管理 11. 维护
2013~2014年版
Manufacturing(由生产负责)
中级
BIQS(制造质量供应)
1. 不合格物料标识 2. 分层审核 3. 风险管理 4. 防错 5. 量具控制 6. 快速反应 7. 标准化操作 8. 变更管理 9. 求助 10. 目视化管理 11. 过程控制 12. 返工返修控制 13. 沟通 14. 团队建设 15. 异物管理 16. 维护 17. 物料流管理 18. 分供方管理
BIQS的概要
BIQS 的发展
QSB(质量体系基础)
1. 快速反应 2. 不合格品控制 3. 验证岗位&防错验证 4. 标准化操作 5. 培训 6. 分层审核 7. 风险降低 8. 异物管理 9. 供应链管理 10. 变更管理
2005~2012年版
Quality(由品质负责)
初级
“从被动到主动”
QSB+(质量体系基础+)
BIQS 的5大要素
1. PI(人员参与) 2. STD(标准化操作)
质量PRR
制造质量供应BIQS(Built In Quality Supply)
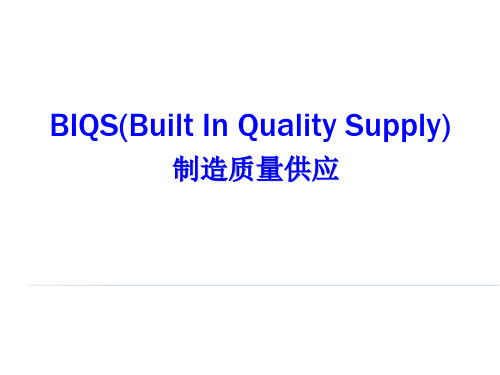
分层审核是一个有效的工具
领导层
过程
审核
1.各工程班及组长 2.部门主任/代理,Part长 3.各部门经理 4.总经理/执行经理/厂长
1.制造、检验过程 2.生产启动,防错验证 3.包装、周转、移动 4.操作者存在处均要分层审核
过程分层审核 流程 选择工位
建立分层审核计划,选择待审核工位
执行审核
建立分层审核检查表
4 顾客抱怨过的事项,改善完成后追加”特定质量关注点”内
5
“是/否”开始,”?”结束 √:符合 0:不符合 N/A:不涉及
6 按照BIQS 5大要素整理审核项目(PI/BIQS/STD/SLT/CI)
BIQS1/BIQS22:不合格物料及物料标识/返工返修
不合格物料 沟通 1.沟通-断点(时间点)
断点沟通前的准备事项:
断点处理的三要素:
1. 熟知缺陷(不合格发生内容) 2. 内外部所有可疑品得到遏制 3. 建立了识别和选别遏制的方法直到改善后的产品出来 4. 100%检验以确保无缺陷/确认后的库存品发运至客户
1. 电子流程 2. 电子表单 3. 企业建立一个系统满足所有客户要求 4. 生产现场符合性≥62%(18/29×100%) 5. 人才开发 6. 通过客户的审核
区分 TS/ISO认证 BIQS 29项
NOT Certified
<62%
2016
2017
2018
2019
Certified Certified Certified
半成品或合格品
标签内容
IN THIS SECTION IS AT LOCAL DISCRETION
PLT001
红标签表示废品,用于报废零件 或废品料箱上 (涂成红色的报废箱可不用标识)
BIQS 审核表要求中文翻译

Layered Audit is an effective tool to confirm the processes are operating at standard, and enhance continuous improvement. Leadership utilizes an audit process by going and seeing on the shop floor to check process compliance, employee behavior and knowledge. Leadership uses Layered Audit as an opportunity for coaching. Recognition is used to reinforce the right behaviors. Ask Leadership how Layered Audit works in the organization, who is involved in the layered audit process, what is the frequency of layered audits. Is the layered audit sheet content relevant for the user (have each principle calibrator review respective part of the audit sheet)? Layered audit questions are reviewed from time to time to focus on the plant weaknesses. Check that all findings are recorded on the audit sheet and those not solved within the shift are transferred to countermeasure sheets. 分层审核是确认过程符合标准化、并强化持续改善的有效工具。 领导层利用审核过程,通过走访车间的形式检查过程的符合性、员工操作和认知。领导层利用 分层审核作为指导的机会。 通过强化员工意识,促进标准化操作。 询问领导层组织内的分层审核运作流程、分层审核参与的人员以及分层审核频度。分层审核清 单的内容是否适用于使用者(让分层审核的检查人员参与评审清单中各自负责检查部分的内容 适宜性)?时不时地对分层审核发现的问题进行评审以关注工厂的薄弱点。 检查所有分层审核发现的问题都已记录在审核清单内,当班没办法解决的问题转记到纠正措施 清单中。 0
制造质量供应BIQS(Built In Quality Supply)
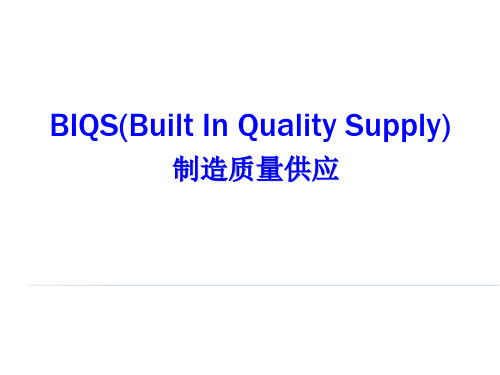
3.沟通-给顾客打电话 什么时候给客户打电话呢?
1. 遏制工作表中显示产品潜在数量超出寻找到的数量(怀疑找不到的产品流出到客户了) 2. 工厂内最早批次的产品含有不合格品 3. 起始点不明确的间歇性问题发生时(断点识别错误,不断发生问题,可能流出道客户)
过程当中发生的问题,可能流出到顾客处,影响到顾客
如不能再离开工位或者之前返回,必须经过批准(质量部最高领导)的返工和检查程序以保证所有 的规格和实验要求的符合性
报废
1. 能够跟踪并防止重新导入生产过程或者正常的产品流 2. 通过持续进行的团队改善努力得到降低
BIQS2/BIQS10:过程分层审核/质量关注检查
过程分层审核 定义 领导层执行过程分层审核
半成品或合格品
标签内容
IN THIS SECTION IS AT LOCAL DISCRETION
PLT001
红标签表示废品,用于报废零件 或废品料箱上 (涂成红色的报废箱可不用标识)
(如果没有用黄色来区分可疑件, 则红色标识要必须使用)
PLT002
PLT003
黄色标签表示可疑产品或待处 理的材料,需要返工的材料或 需要进一步检查的材料
LOCATION
可能存在的 数量
区域 确认人
可疑品 发现数量
Receiving 收货区
500 P.S.
500
Laboratory 实验室
6 K.C.
6
WIP Storage Areas 在制品放置区
1000 P.S.
1000
Outside Processing - (Plating)外加工 1000
围堵 处理的6大要素(制作 围堵确认工作表) 挑选 处理的6大要素(制作选别记录表)
BIQS教材模块介绍

Dat e: Smart # : Family/ RPO: Part # : Serial # : Test Order # : Last Op/ Area: Tagged By: Reason f or SCRAP:
10
BIQS-1 Nonconforming Material / Material Identification 资料仅供参考 合格/不合格物料区分
合格/不合格物料区分 分层审核 PFMEAs PFMEAs - 风险降低和年度回顾 临时替代/偏差管理 防错验证 量具校准及测量系统分析 (新增) 快速响应 团队合作解决问题 质量关注点检查 标准化操作 变更管理 质量门(验证岗位/终检/CARE/GP12) 变更管理-生产试运行(PTR) 暗灯系统
SUSPECT
HOLD
Dat e: Smart # : Family/ RPO: Part # : Serial # : Test Order # : Last Op/ Area: Tagged By: Reason f or SUSPECT:
BIQS
SC-001
Rev: 11/ 12
SCRAP
DO NOT USE!
5
过程能力研究
6
7个新增模块
安全
7
23个细分模块
QSB-1
QSB-2
QSB-3
QSB-4 QSB-5 QSB-6 QSB-7 QSB-8 QSB-9 QSB-10 QSB-11
快速反应
不合格品控制
验证岗位
标准化操作 培训 防错验证 分层审核 风险降低 异物管理 分供方管理 变更管理
BIQS-8 BIQS-9 BIQS-15 BIQS -1 BIQS-16 BIQS-22 BIQS-13 BIQS-23 BIQS-27 BIQS-28 BIQS-11 BIQS-26 BIQS-24 BIQS-6 BIQS-5 BIQS-2 BIQS-10 BIQS-3 BIQS-4 BIQS-25 BIQS-29 BIQS-12 BIQS-14
BIQS 审核重点提炼

团队成员应了解目视化标准的内容。与至少三名操作人员沟通。所有应该满足要求。目视化检验应定义在标准化作业文件中以便参考。
确认目视化标准可明确的将不合格从合格品中区分出来,明确的定义在产品质量标准文件和标准化作业文件中。
条款
要求
参照事项
备注说明
BIQS -19
确认改善措施横向展开执行到类似操作中。
容易出现的问题:
FR会议变成一个问题讨论解决会议(时间太长);
没有定期的反馈,问题解决拖的时间太长;
没有采用why(DrillDeeP)寻找根本原因;
没有经验教训数据库;没有完成水平展开;
条款
要求
参照事项
备注说明
BIQS -9
问题解决流程
有适用于组织各层级明确标准化的问题解决流程。依据标准启动正式的问题解决活动。
查看有关可能启用Bypass流程制造流程和防错装置的列表。确认批准的Bypass流程的RPN被评估且每个Bypass操作有标准化作业文件。供应商有文件批准Bypass操作的记录包括客户通知。
确认Bypass操作在快反上评审以降低和消除Bypass操作为目的。查找Bypass操作检查清单及执行证据。
容易出现的问题:
或者依据过程控制计划验证。
确认防错验证的标准件有明确标识,确认验证记录完整。验证当防错失效是有对应的反应计划,并被团队成员理解。
条款
要求
参照事项
备注说明
BIQS -7
量具校验和测量系统分析
监控和测量量具能力(如,重复性在现行,偏移,线行,稳定性等)被定义。测量设备按照计划和频率标定和校验。
确认量具依据程序和时间计划完成重复性在现性和校验。确认没有量具是过期未校验的。
- 1、下载文档前请自行甄别文档内容的完整性,平台不提供额外的编辑、内容补充、找答案等附加服务。
- 2、"仅部分预览"的文档,不可在线预览部分如存在完整性等问题,可反馈申请退款(可完整预览的文档不适用该条件!)。
- 3、如文档侵犯您的权益,请联系客服反馈,我们会尽快为您处理(人工客服工作时间:9:00-18:30)。
视觉的验收
接受和参与
主 动 的 做
标准化的操作工培训
标准化的操作工培训和跟踪验证方法 ✓ 标准化定义技能相关具体项目并建立培 训清单 • 常规岗位需要学习、了解、理解、掌握 的项目; • 特殊要求(按岗位/技能要求,如有) ✓ 关联到培训阶段的考评要求; • 对知识/要求的理解/掌握程度; • 对标准操作的掌握程度(按要求的符合 性); • 初始节拍能力(人工操作相关); • 质量符合性(人工操作相关); • 验证/考核/跟踪时限(时间/数量)和符 合标准;
标示与追溯 ➢ 所有偏差零件必须作为可疑品进行识别知道客户批准 ➢ 偏差零件的可追溯性供应商必须记录 ➢ 在运输前,得到顾客批准的量检需要被标识(零件或箱子标签或客户批准的数量) ➢ 确立“断点”并通知客户。
示例-返工/返修标准化作业单
示例-返工/返修标准化确认项目
BIQS-23(前馈/后馈)审核表要求
8.7.1.5 返修产品的控制
组织应在决定对产品进行返修之前,利用风险分析(如 FMEA)方法来评估返修过程中的风险。组织应在 开始产品返修之前获得顾客的批准。 组织应有一个形成文件的符合控制计划的返修确认过程,或者其它形成文件的相关信息。 包含了重新检验和可追溯性要求的拆卸或返修指导书,应易于被适当的人员取得和使用。 组织应获得顾客对待返修产品的形成文件的让步授权。 组织应保留与返修产品处置有关的形成文件的信息,包括数量、处置、处置日期及适用的可追溯性信息。
在线 离线 在线 离线 在线 离线
返回的生产线工位
返回的生产线工位
报废零件清单 可回用零件清单
✓ 只有极简单的低风险操作允许在线实施 ✓ 其他操作都应在独立于生产线的返工/ 返修/拆解区域进行进行。
标准化操作
➢ 不论在线或离线操作,都应有对应的标准化操作文件; ➢ 返工/返修/拆解操作必须由技能符合的授权人员实施; ➢ 返工/返修后物料或拆解回用的物料,只有在经过其他授权人员检查合格后才能返回生产线( 第二方检查) ➢ 标准化操作文件至少应包含: ✓ 处置前/后零件的标识,存储要求; ✓ 完整的的拆卸、返工返修操作要求(关注相关的特殊工具要求和配置)
质量警示表单
➢ 问题描述:时间、发生/发现地点、数量、问题详细说明、发生次数等; ✓ 附上能有效识别的缺陷和合格状态的对比照片(或实物); ➢ 对应的控制方法:发生工位&后工位(如需),短期措施和长期措施(如有): ✓ 可附加更详细的标准化操作指导文件(如需); ➢ 断点信息和断点标识(如需) ➢ 预计的期限(或有效期)
标准化的操作工培训和跟踪验证方法 ✓ 基于承认学习法则建立标准化的操作工基础岗位技能培训流程/方法
我们能记多少
通过读能记住10%
能记住听到的20% 能记住看到的30%
能记住听到和看到 的50% 能记住70%说的
90%说的和做的能 记住
我们参与的程度
口头的验收
被 动 的
Step4跟踪 Step3试操作 Step2示范操作 Step1成员准备
IATF16949:2016体系要求 7.2 能力(以下内容为条款原文摘录);
组织应:
a)确定受其控制的工作人员所需具备的能力,这些人员从事的工作影响质量管理体系绩效和有效性; b)基于适当的教育、培训或经历,确保这些人员是胜任的; c)适用时,采取措施获得所需的能力,并评价措施的有效性; d)保留适当的形成文件的信息,作为人员能力的证据。 注:采取的适当措施可包括对在职人员进行培训、辅导或重新分配工作,或者招聘、分包给胜任的人员等。
质量警示卡
➢ “质量警示卡”应当被展示与沟通在生产和检验区域
质量警示卡
沟通:质量问题的快速警报 内容:质量报警卡 ➢ 定义问题、标准和偏差; ➢ 使用含有能方便的解释偏差信息的图片或样件 ➢ 定义问题的范围,如何可能的数量、比例、设 计范围等; ➢ 建立识别和分选缺陷的方法直至改善后的过程 发运至客户; ➢ 判断遏制合格的标记,如做过标记的产品的描 述和图片和增加的标记; ➢ 短期断点和计划的长期断点。 明确清晰的沟通内容是保证有效沟通的前提!
3.操作工技能保持和开发 人员&岗位技能要求的设定和实施; 一人多岗技能的保持管理;
2.人员技能管理 综合技能状态的定义和有效管理; 员工综合技能在生产现场的展示和目视 化管理;
4.组织人员整体能力提升 针对每个员工; 根据其岗位要求,建立相应的培训发展 计划; 按计划跟踪实施;
标准化操作工培训
应用
前馈/后馈: ➢ 以质量警示的方式将信息传递到问题发生前和流出工位是最常见的应用形式; ➢ 质量警示也可以作为临时作业要求,持续到问题被解决并验证关闭; ➢ 确保了不同生产班次,不同班组,不同生产区域间的信息传递。
应用场景:---(例如) ➢ 在验证岗位(包括终检、CARE、或GP-12)和制造班组长及制造团队间快速进行质 量异常信息传递; ➢ 对后工序发现的质量问题,以质量警示的方式反馈到制造工位和关联的有效检验工 位;
组织应在决定对产品进行返工之前,利用风险分析(如 FMEA)方法来评估返工过程中的风险。如顾客有 所要求,组织应在开始产品返工之前获得顾客批准。 组织应有一个形成文件的符合控制计划的返工确认过程,或者其它形成文件的相关信息,用于验证对原始 规范的符合性。 包含了重新检验和可追溯性要求的拆卸或返工指导书,应易于被适当的人员取得和使用。 组织应保留与返工产品处置有关的形成文件的信息,包括数量、处置、处置日期及适用的可追溯性信息。
组织应确保建立、实施并保持一个在制造、材料搬运、物流、工程和设计活动之间沟通服务问题信息的过 程。 注 1:将“服务问题”增加到这个子条款,是为了确保组织知晓可能在顾客地点或使用现场被识别的不合 格品和材料。 注 2:“服务问题”应当在适用时包括使用现场失效试验分析(见第 10.2.6 条)的结果。
可实施性评审
➢ 从项目启动开始,对过程、产品的返工/返修可实施性进行评审; ➢ 在生产过程中,基于生产数据的收集,持续进行完善; ➢ 必须利用FMEA等风险分析方法进行风险评估,作为可行性决策依据; ➢ 在控制计划等文件内体现相关的处置要求; ➢ 建立对应的标准化操作文件,明确具体的操作要求;
返工 返修 拆解回用
BIQS-22(返工/返修/拆解)审核表要求
-无论在线还是离线的返修都需要符合批准的标准化作业指导书。 -返工、返修或是返工回用材料需要有一个额外的独立确认过程(第2个人或 设备)。 返工零件需要返回原取出工位,以确保执行控制计划规定所有检查和测试项 目。
IATF16949:2016体系要求 8.7.1.4 返工产品的控制(以下内容为条款原文摘录);
✓ 可回用/报废零件清单 ✓ 处置后,至少第二授权人或机器的100%检查要求和检查方法; ✓ 必须返回的生产线工位(取出工位或之前的工位); ✓ 可追溯性记录保留要求,如问题描述、数量、可追溯性信息、出资时间、处置负责 人,再检查结果和负责人,返回生产线时间等。
顾客批准
➢ 针对偏差零件在运输前,供应商必须得到客户批准,没有客户批准,不允许有偏差 的零件被运输到顾客端; ➢ 顾客批准仅限于特定的时间段或数量,同时供应商必须管控这部分产品
10.2.6 顾客投诉和使用现场失效试验分析
组织应对顾客投诉和使用现场失效,包括退货零件,进行分析,并且应采取问题解决和纠正措施以预防再 次发生。 在顾客要求的情况下,这应包括最终顾客产品系统内,组织产品嵌入式软件相互作用的分析。 组织应向顾客并且在组织内部传达试验/分问题后快速的将相关信息传递到前面/后面的相关制造/检验工位
前馈/后馈信息的管理
➢ 前馈/后馈的信息应防止在对应工位的项目位置。 ➢ 对前馈/后馈信息的有效培训是保证被有效应用的基础; ➢ 前馈/后馈信息是问题解决过程的重要组成部分; ✓ 如短期遏制、长短期措施有效验证等 ➢ 基于问题解决的进程和验证结果,需要及时评估并更新对应的前馈/后馈信息; ✓ 如更新控制措施 ➢ 需要有效的管控前馈/后馈的信息发布和关闭,如: ✓ 发布时间、数量、设计地点、相关管理负责人; ✓ 执行时间跨度(接着有效期管理) ✓ 关闭后及时的文件回收。
7.2.1 能力 —— 补充
组织应建立并保持形成文件的过程,识别包括意识(见第 7.3.1 条)在内的培训需求,并使所有从事影响 产品要求和过程要求符合性的活动的人员具备能力。从事特定指派任务的人员应按要求进行资格认可,尤
其关注对顾客要求的满足。
7.2.2 能力 —— 在职培训
对于承担影响质量要求、内部要求、法规或法律要求符合性的新的或调整职责的人员,组织应对其进行在
,避免/减少问题的继续流入好/或防止问题流出;
问题来源:
➢ 质量门-检验工位、终检、CARE、验证岗位(包括GP-12): BIQS-13
➢ 现场报警问题:
BIQS-15暗灯系统BIQS-16报警&升级
➢ 来源于分供方、客户、外部(如同行业)、内部(包含各子公司、合作伙伴等)的
报警或预警问题。
➢ 其它
基本概念
➢ 返工:为是不合格产品或服务符合要求的而对其采取的措施; ➢ 返修:为使不合格产品或服务满足预期用途而对其采取的措施;返修操作必须获 得顾客批准; ➢ 拆解回用:将不合格品拆卸到装配前子零件或过程子总成状态,并回用其中的部 分或全部零件。
返工/返修要求:
➢ 返工/返修作业指导书(操作要求、记录要求) ➢ 返工/返修品追溯办法(标识要求、追溯记录、放行授权) ➢ 独立的返工/返修专用区域和相应的工装设备 ➢ 明确返工返修操作授权人员且技能满足要求 ➢ 尽量集中进行返工返修,做好追溯记录 ➢ 建立返工返修信息登记。 ➢ 可能需要客户批准 ➢ 分层审核关注点
-在生产班长/不同班组和验证岗位(终检/CARE/GP-12)之间有快 速的前反馈和反馈信息传递。
-在生产工位发布质量警示,防止问题继续发生或流出。质量警示 可以做为临时的作业指导书使用,知道问题关闭后,相关作业指导 书更新完成。