钢的最佳切削速度
丝锥切削参数 表 新
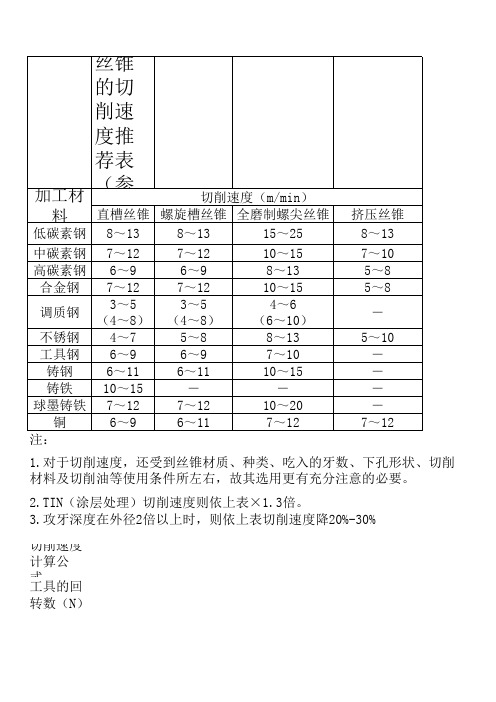
N:转速rpm
例:加工碳钢,直槽,M22的丝锥,转速=1000*8/3.14*22~1000*13/3.14*22=115 加工合金钢,螺旋槽M22的丝锥,转速=1000*7/3.14*22~1000*12/3.14*22=1
.14*22=115~188(转/分) /3.14*22=101~173(转/分)
2.TIN(涂层处理)切削速度则依上表×1.3倍。 3.攻牙深度在外径2倍以上时,则依上表切削速度降20%-30%
切削速度 计算公 式: 工具的回 转数(N)
பைடு நூலகம் N=1000v/ πd(转/ 分钟)
D:加工孔径mm
d:丝锥直径mm v:切削速度 m/min
切削速度 (V)
V=π dN/1000( 米/分钟)
丝锥
的切
削速
度推
荐表
加工材 (参
切削速度(m/min)
料 直槽丝锥 螺旋槽丝锥 全磨制螺尖丝锥
低碳素钢 8~13
8~13
15~25
中碳素钢 高碳素钢 合金钢
7~12 6~9 7~12
7~12 6~9 7~12
10~15 8~13 10~15
调质钢
3~5 (4~8)
3~5 (4~8)
4~6 (6~10)
不锈钢 工具钢
4~7 6~9
5~8 6~9
8~13 7~10
铸钢 铸铁
6~11 10~15
6~11 ―
10~15 ―
球墨铸铁 铜
注:
7~12 6~9
7~12 6~11
10~20 7~12
挤压丝锥 8~13 7~10 5~8 5~8
―
5~10 ― ― ― ―
7~12
各材料常用刀具转速进给参数对照表

各材料常用刀具转速进给参数对照表在机械加工领域,刀具的转速和进给参数对于加工质量、效率和成本都有着至关重要的影响。
不同的材料具有不同的物理和机械性能,因此需要根据材料的特性来选择合适的刀具转速和进给参数。
下面是一份常见材料的刀具转速进给参数对照表,希望能为您的加工工作提供一些参考。
一、铝合金铝合金是一种广泛应用于航空航天、汽车制造和电子工业等领域的轻质材料。
由于其良好的导热性和较低的强度,加工时需要较高的转速和较快的进给速度。
1、粗加工刀具:硬质合金立铣刀转速:3000 5000 rpm进给速度:800 1500 mm/min切削深度:2 5 mm切削宽度:刀具直径的 70% 80%2、半精加工刀具:硬质合金立铣刀转速:5000 8000 rpm进给速度:500 1000 mm/min切削深度:05 15 mm切削宽度:刀具直径的 50% 60%3、精加工刀具:硬质合金球头铣刀转速:8000 12000 rpm进给速度:200 500 mm/min切削深度:01 03 mm切削宽度:刀具半径的 20% 30%二、钢材钢材是机械加工中最常见的材料之一,其种类繁多,性能各异。
以下是常见钢材的加工参数。
1、低碳钢粗加工刀具:硬质合金涂层立铣刀转速:1500 2500 rpm进给速度:300 600 mm/min切削深度:3 6 mm切削宽度:刀具直径的 60% 70%半精加工刀具:硬质合金涂层立铣刀转速:2500 4000 rpm进给速度:200 400 mm/min切削深度:1 2 mm切削宽度:刀具直径的 40% 50%精加工刀具:硬质合金涂层球头铣刀转速:4000 6000 rpm进给速度:100 200 mm/min切削深度:01 02 mm切削宽度:刀具半径的 15% 20% 2、中碳钢粗加工刀具:硬质合金涂层立铣刀转速:1000 1800 rpm进给速度:200 400 mm/min切削深度:2 4 mm切削宽度:刀具直径的 50% 60%半精加工刀具:硬质合金涂层立铣刀转速:1800 3000 rpm进给速度:150 300 mm/min切削深度:05 10 mm切削宽度:刀具直径的 30% 40%精加工刀具:硬质合金涂层球头铣刀转速:3000 5000 rpm进给速度:80 150 mm/min切削深度:005 015 mm切削宽度:刀具半径的 10% 15% 3、高碳钢粗加工刀具:硬质合金涂层立铣刀转速:800 1200 rpm进给速度:100 200 mm/min切削深度:1 3 mm切削宽度:刀具直径的 40% 50%半精加工刀具:硬质合金涂层立铣刀转速:1200 2000 rpm进给速度:80 150 mm/min切削深度:03 08 mm切削宽度:刀具直径的 20% 30%精加工刀具:硬质合金涂层球头铣刀转速:2000 3500 rpm进给速度:50 100 mm/min切削深度:003 008 mm切削宽度:刀具半径的 8% 12%三、不锈钢不锈钢具有良好的耐腐蚀性和耐磨性,但加工难度较大,需要较低的转速和较慢的进给速度。
超高速加工技术

(2)汽车制造。
1
2
3
4
钻孔 表面倒棱 内侧倒棱 铰孔
高速钻孔 表面和内侧倒棱
专用机床 5轴×4工序 = 20轴(3万件/月)
刚性(零件、孔数、孔径、孔型固 定不变)
高速加工中心 1台1轴1工序(3万件/月)
柔性(零件、孔数、孔径、 孔型可变)
图12 汽车轮毂螺栓孔高速加工实例(日产公司)
(3)模具制造。
b)高速模具加工的过程
图14 两种模具加工过程比较
生产剃须刀的石墨电极
生产球形柄用的铜电极
图15 高速切削加工电火花加工用工具电极
(4)难加工材料领域。硬金属材料(HRC55~62),可 代替磨削,精度可达IT5~IT6级,粗糙度可达0.2~1um。
(5)超精密微细切削加工领域。
粗铣整体铝板; •精铣去口; •钻680个直径为3mm的小孔。 时间为32min。
在机床的主轴上,定子安装在主轴单元的壳体中,采用水冷 或油冷。精度高、振动小、噪声低、结构紧凑。
高速加工技术的发展与应用
图5 HSM600U型数控五轴高速加工中心
生产厂家:瑞士Mikron 主轴转速:最高42000 rpm
主轴功率:13 KW 进给速度:最高40 m / min
定位精度:0.008 mm
重复定位精度:0.005mm
图6 HSM 系列高速五轴联动小型立式加工中心
图7 HSM800 图9 HSM400
• Bremen大学在高效深磨的研究方面取得了世界公 认的高水平成果,并积极在铝合金、钛合金、铬镍 合金等难加工材料方面进行高效深磨的研究。
近年来,我国在高速、超高速加工的各关键领域 (如大功率高速主轴单元、高加减速直线进给电机、 陶瓷滚动轴承等方面)也进行了较多的研究并有相应 的研究成果。
不锈钢车削参数

不锈钢车削参数不锈钢车削参数是指在车削加工过程中,针对不锈钢材料的特性和要求所设定的一系列切削参数。
这些参数对于保证加工质量和提高生产效率具有重要意义。
以下是一些建议的不锈钢车削参数:1. 切削速度(Vc):切削速度是刀具在旋转时与工件接触点的速度。
对于不锈钢材料,切削速度应适当降低,以防止刀具过热和磨损。
一般推荐切削速度为20-60m/min。
2. 进给量(f):进给量是指刀具在每次切削行程中沿工件轴向移动的距离。
对于不锈钢材料,进给量应适当降低,以减小刀具磨损和切削力。
一般推荐进给量为0.1-0.3mm/r。
3. 切削深度(ap):切削深度是指刀具在每次切削行程中切入工件的深度。
对于不锈钢材料,切削深度应适当降低,以减小刀具磨损和切削力。
一般推荐切削深度为0.1-0.5mm。
4. 刀具前角(γo):刀具前角是指刀具主切削刃与工件表面的夹角。
对于不锈钢材料,刀具前角应适当增大,以提高切削性能和减少刀具磨损。
一般推荐前角为10-20°。
5. 刀具后角(αo):刀具后角是指刀具主切削刃与工件表面的夹角。
对于不锈钢材料,刀具后角应适当增大,以提高切削性能和减少刀具磨损。
一般推荐后角为8-12°。
6. 切削液:不锈钢车削过程中,应使用适当的切削液来冷却和润滑刀具和工件,以降低切削温度和减少刀具磨损。
常用的切削液有水溶性切削液、油溶性切削液和乳化液等。
7. 刀具材质:不锈钢车削过程中,应选择具有良好耐磨性和抗腐蚀性的刀具材质,如硬质合金、陶瓷和高速钢等。
8. 机床刚性:不锈钢车削过程中,应选择具有较高刚性的机床,以保证加工精度和表面质量。
9. 工艺路线:不锈钢车削过程中,应根据工件的形状和尺寸选择合适的工艺路线,以减少切削力和热量对加工质量的影响。
总之,不锈钢车削参数的选择应根据具体的工件材料、形状和尺寸以及加工要求进行综合考虑,以达到最佳的加工效果。
白钢铣刀切削参数

白钢铣刀的切削参数主要包括刀具直径、刀具转速、进给量、吃刀深度、进给速度和切削液等。
这些参数的选择对于切削效果、刀具磨损和加工效率具有重要影响。
1. 刀具直径:刀具直径是铣刀切削时的主要参数之一,它决定了铣刀的切削深度和切削宽度。
在选择刀具直径时,需要根据加工零件的尺寸和形状来选择合适的直径。
2. 刀具转速:刀具转速是指铣刀每分钟旋转的次数,它直接影响铣刀的切削效果。
如果转速过高,会导致刀具磨损加剧;如果转速过低,会导致切削效率下降。
因此,在选择刀具转速时,需要根据刀具材料、工件材料、加工要求等因素进行综合考虑。
3. 进给量:进给量是指铣刀每转过一圈,工件相对于铣刀轴线移动的距离。
进给量的选择需要考虑工件材料、加工精度、刀具材料等因素。
4. 吃刀深度:吃刀深度是指每次切削时,铣刀相对于工件表面切削的深度。
吃刀深度的选择需要根据工件材料、机床刚度、刀具材料等因素来确定。
5. 进给速度:进给速度是指刀具每分钟切削的距离,一般以毫米/转或英寸/转来表示。
对于白钢等硬度较高的材料,一般采用较低的进给速度,以确保刀具切削稳定。
6. 切削液:切削液是指在切削过程中用来冷却和润滑刀具和工件的液体。
切削液的选择需要考虑工件材料、刀具材料、加工要求等
因素。
总之,在选择白钢铣刀的切削参数时,需要根据具体情况综合考虑各种因素,以达到最佳的切削效果和加工效率。
20号低碳钢车削参数

20号低碳钢车削参数
低碳钢的车削参数会受到多种因素的影响,包括材料的硬度、刀具的类型和几何形状、加工条件以及所需的加工质量等。
以下是一些常见的20 号低碳钢车削参数范围供参考:
1. 切削速度(Vc):通常在50 至150 米/分钟之间,具体速度取决于刀具材料和工件的硬度。
2. 进给量(f):一般在0.1 至0.5 毫米/转之间,进给量的选择要考虑刀具的耐磨性和加工表面质量。
3. 切削深度(ap):通常在1 至5 毫米之间,具体深度取决于工件的直径和加工要求。
需要注意的是,以上参数仅为一般范围,实际的车削参数应根据具体的加工情况进行调整和优化。
在选择车削参数时,建议参考刀具制造商的建议、实际加工经验以及工件的要求,以获得最佳的加工效果和刀具寿命。
此外,还应注意刀具的选用、冷却液的使用以及加工过程中的安全措施等方面,以确保高效、安全地进行车削加工。
如果你有具体的车削需求,建议咨询专业的机械加工工程师或相关技术人员,以获得更准确和适合的参数建议。
40cr钢通用切削速率
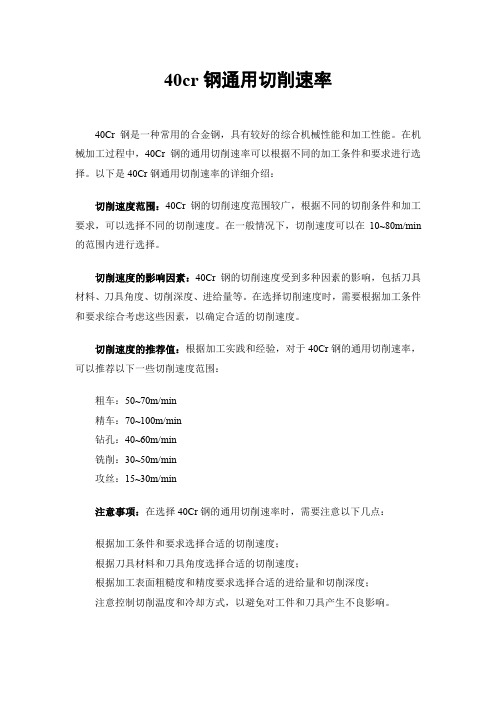
40cr钢通用切削速率
40Cr钢是一种常用的合金钢,具有较好的综合机械性能和加工性能。
在机械加工过程中,40Cr钢的通用切削速率可以根据不同的加工条件和要求进行选择。
以下是40Cr钢通用切削速率的详细介绍:
切削速度范围:40Cr钢的切削速度范围较广,根据不同的切削条件和加工要求,可以选择不同的切削速度。
在一般情况下,切削速度可以在10~80m/min 的范围内进行选择。
切削速度的影响因素:40Cr钢的切削速度受到多种因素的影响,包括刀具材料、刀具角度、切削深度、进给量等。
在选择切削速度时,需要根据加工条件和要求综合考虑这些因素,以确定合适的切削速度。
切削速度的推荐值:根据加工实践和经验,对于40Cr钢的通用切削速率,可以推荐以下一些切削速度范围:
粗车:50~70m/min
精车:70~100m/min
钻孔:40~60m/min
铣削:30~50m/min
攻丝:15~30m/min
注意事项:在选择40Cr钢的通用切削速率时,需要注意以下几点:
根据加工条件和要求选择合适的切削速度;
根据刀具材料和刀具角度选择合适的切削速度;
根据加工表面粗糙度和精度要求选择合适的进给量和切削深度;
注意控制切削温度和冷却方式,以避免对工件和刀具产生不良影响。
总之,40Cr钢的通用切削速率需要根据不同的加工条件和要求进行选择,综合考虑多种因素,以达到最佳的加工效果和经济效益。
CBN刀具车削加工淬火钢件的切削参数范围

CBN刀具车削加工淬火钢件的切削参数范围CBN刀具车削加工淬火钢件,已经是非常普遍的一种现象,采用CBN刀具以车代磨加工淬火钢件效率成倍提高,而且干式切削,车削加工过程中不添加切削,绿色环保,更适合制造业的绿色制造。
CBN刀具虽然广泛应用于淬火钢件的车削加工,但很多工人还不太了解CBN刀具的切削参数,经常刚上去就出现崩刀、打刀现象。
主要就是不了解CBN刀具的切削参数,用硬质合金刀具的参数测试,效果不好。
小编在机械加工行业摸爬滚打了十几年,还算是有一点小心得,今天分享给大家。
在先介绍CBN刀具车削加工淬火钢件的切削参数范围之前,先来了解一下淬火钢都有哪些难加工问题。
1、淬火钢件的粗加工:车削加工淬火过的齿轮,齿圈的生产过程中,一些齿轮、齿圈淬火或渗碳淬火后,硬度一般在HRC55以上,而且变形严重,如高铁齿轮,工程机械大齿圈,重工行业用大齿圈等,这些大型齿轮齿圈淬火后变形量非常大,这就涉及到淬火钢粗加工。
同样,在模具钢生产过程中,淬火钢的粗加工也经常看到,但很多厂家采取的措施也五花八门,有的先把大余量线切割掉,有的用硬质合金刀具慢慢啃,有的用立方氮化硼(PCBN)刀具多次走刀才能完成加工,工人感慨粗加工淬火钢是有劲使不出,干着急,没办法。
2、淬火钢件的断续加工:间断切削加工一直是个难题,何况是动辄HRC60左右的淬火钢。
特别是在高速车削淬火钢时,刀具在间断车削淬火钢时会以每分钟100次以上的冲击来完成加工,对刀具的抗冲击性能是个很大的挑战。
以汽车齿轮加工为例,淬硬齿轮以车代磨已经成为一种趋势,据了解,作为齿轮产业的三大市场之一,车辆齿轮占据了齿轮市场总额的62%,其中汽车齿轮又占据了车辆齿轮市场份额的62%。
也就是说,汽车所用齿轮占有了整个齿轮市场近40%的比重,可见齿轮对于汽车产业的重要性。
虽然淬火钢的以车代磨和硬车削已经很普及,其实汽车淬硬齿轮加工过程中仍然遇到很多问题,如一些汽车齿轮内孔有油孔,这就出现间断切削加工难题,很多CBN刀具在高速运转时期遇到油孔容易崩刀,齿轮的位置公差难以保证,等等3、淬火钢件的切槽加工:举一个简单的例子,同步器滑套啮合槽淬火后的硬车削加工,虽然立方氮化硼刀具厂家开发出了同步器滑套专用立方氮化硼切槽刀具,但PCBN刀具的寿命仍然不尽如人意。
切削用量选择

卧式数控车床切削用量选择作者:杨树诚单位:沈阳第一机床厂技术部日期:2005年09月本文着重提醒读者1.不要轻易按刀具样本的推荐值确定切削速度,那样刀具寿命很低。
一般情况下,硬质合金刀片可按刀具样本推荐值的0.64~0.71倍选择切削速度。
2.确定精加工和半精加工的进给量着眼于工件的表面粗糙度。
它还和刀尖半径有关。
文中列表表明三者对应关系,供选择进给量参考。
3.条件允许时希望粗加工吃刀深尽量大。
一方面有效提高生产率;一方面也为了消除表面硬皮.切除砂眼等缺陷,从而保护刀尖不与毛坯接触。
精加工时也不希望吃刀深太小,以免产生刮擦对粗糙度不利。
4.表5~表12列举了外圆.端面.内孔加工,切槽,车螺纹的切削用量推荐值。
供一般情况下采用。
目录一.原始资料 (1)二.选择切削用量的原则 (1)三.吃刀深αp (2)四.进给量f (2)五.切削速度V (4)六.切削用量推荐值 (5)切削用量选择关键词: 刀具耐用度 切削速度 表面粗糙度 进给量 吃刀深在售前服务编制加工工序卡以及调装设计中,都需要确定切削用量及计算节拍时间。
本文就卧式数控车床如何合理选择切削用量进行探讨。
一. 原始资料:无论编制加工工序卡-即制定工艺方案还是调装设计都需要掌握以下资 料,做为刀具选择.卡具设计以及选择切削用量的依据。
.1 工件图:包括形状.尺寸.公差.形位公差.粗糙度和其他技术要求。
特别强调的是本序 加工的部位必须明确,用于及可能影响装卡部位的形状要表示清楚。
2.毛坯图:毛坯形状.尺寸,加工余量,材料.硬度等。
3.生产纲领:即年产量或单件时间,这对招标项目尤为重要。
4.验收要求:机床验收时对工件考核什麽项目,有无Cp 值和其它要求。
5.用户对工件定位基准.卡紧面.辅助支承 等要求,或指定参考的卡具样式。
6. 对刀具选择要求:用国产刀具或国外指定厂家 的刀具,特殊刀具是否自备等。
7. 用户单位,件名.件号等也应标明,以便管理。
二 选择切削用量的原则:1. 总的要求:保证安全,不致发生人身事故或设备事故;保证加工质量。
45钢刀具切削参数
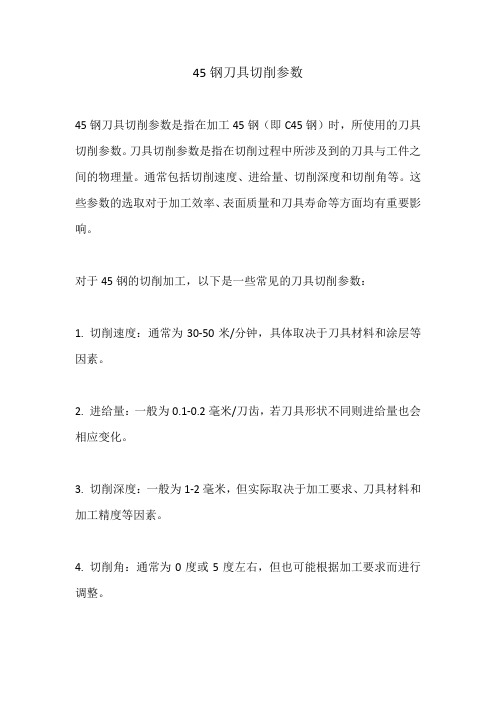
45钢刀具切削参数
45钢刀具切削参数是指在加工45钢(即C45钢)时,所使用的刀具切削参数。
刀具切削参数是指在切削过程中所涉及到的刀具与工件之间的物理量。
通常包括切削速度、进给量、切削深度和切削角等。
这些参数的选取对于加工效率、表面质量和刀具寿命等方面均有重要影响。
对于45钢的切削加工,以下是一些常见的刀具切削参数:
1. 切削速度:通常为30-50米/分钟,具体取决于刀具材料和涂层等因素。
2. 进给量:一般为0.1-0.2毫米/刀齿,若刀具形状不同则进给量也会相应变化。
3. 切削深度:一般为1-2毫米,但实际取决于加工要求、刀具材料和加工精度等因素。
4. 切削角:通常为0度或5度左右,但也可能根据加工要求而进行调整。
在选择刀具切削参数时,需要考虑刀具材料、涂层、刀具形状、加工要求等因素,以使切削过程顺利进行,且达到最佳的加工效果。
同时,也需要注意切削参数的合理性,避免切削参数过高或过低,导致刀具寿命的缩短或加工效率的降低。
车削切削用量选取参考表

190-215
0。4
不锈钢
奥氏体
135~275
1
18-34
0。18
58—105
67-120
0。18
YG3X,YW1
84-60
0.18
275—425
0.13
>225HBS时宜用W12Cr4V5Co5及W2Mo9Cr4VCo8
4
15-27
0.4
49—100
58-105
0.4
YG6,YW1
76—135
275—335
0.25
8
17-21
0。5
66-72
82-90
0。75
YT5
105-120
0.5
215-245
0。4
高强度钢
225~350
1
20-26
0.18
90-105
115—135
0。18
YT15
150-185
0。18
380-440
0.13
>300HBS时宜用W12Cr4V5Co5及W2Mo9Cr4VCo8
0.7~1
0。6~0.8
0。5~0。6
—
20×3025×25
20
0。3~0.4
-
—
—
—
40
0。4~0。5
0.3~0.4
-
—
—
60
0。6~0.7
0。5~0.7
0。4~0。6
—
-
100
0.8~1
0.7~0。9
0.5~0。7
0.4~0。7
—
400
1。2~1。4
1~1.2
0。8~1
车削切削用量选取参考表

0.75
YT5
170-220
0.5
335-490
0.4
中碳
175~225
1
52
0.2
165
200
0.18
YT15
305
0.18
520
0.13
4
40
0.4
125
150
0.5
YT14
200
0.4
395
0.25
8
30
0.5
100
120
0.75
YT5
160
0.5
305
0.4
碳 钢
低碳
100~200
4、加工淬硬钢时,进给量应减小。硬度为HRC45-56时,乘以修正系数:0.8, 硬度为HRC57-62,乘以修正系数:k=0.5。
三、按表面粗糙度选择进给量的参考值
工件材料
粗糙度等级(Ra)
切削速度(m/min)
刀尖圆弧半径
0.5
1
2
进给量fmm/r
碳钢及合金碳钢
10~5
≤50
0.3~0.5
0.45~0.6
1
0.3
1.1
0.3
—
—
—
—
>18~30
1
0.3
1
0.3
1.1
0.3
1.3
0.4
1.4
0.4
—
—
>30~50
1.1
0.3
1
0.3
1.1
0.4
1.3
0.5
1.5
0.6
1.7
0.6
>50~80
1.1
cnc不锈钢加工刀具切削参数表【免下载】

不锈钢(即含镍量>8%或者含铬量>12%的合金钢)目前被广泛应用于石油、化工、航空、航天、食品以及冶金等领域,因此,探讨不锈钢的切削加工具有较大的实际意义。
因为切削加工性差,不锈钢为难加工材料。
依据不锈钢切削加工的实际特点,从刀具本身、刀具几何角度、切削用量等三名方面的选择论述了不锈钢切削加工中刀具切削参数的合理选择问题。
论文关键词:不锈钢切削加工;切削参数;合理选择1 不锈钢切削加工的实际特点1.1 具有很强的加工硬化趋势,极易磨损刀具大部分不锈钢材料(马氏体类不锈钢例外)具有很强的加工硬化趋势,同时,因为加工硬化层具有很高的硬度(通常高于原有硬度2倍左右,表面硬度HV能够达到400-570kg/mm2)。
不同的切削条件与不锈钢工件材料,会让加工硬化层深度从数十μm一直深入到数百μm(通常为100μm-200μm)。
1.2 切屑不易折断或者卷曲切削过程中切屑不易卷曲和折断。
特别是镗孔、钻孔、切断等工序的切削过程中,排屑困难,切屑易划伤已加工表面。
在数控机床上切削不锈钢时,断屑与排屑是重点考虑的问题。
1.3 切屑具有很强的粘附性,极易造成刀瘤不锈钢材料具有很高的韧性,尤其是对其它金属材料具有较强的亲和力,加工过程非常容易造成刀瘤。
1.4 “三高”(高温度、高硬度、高强度)不易分离切屑不锈钢的特性之一就是高温度、高硬度、高强度。
例如温度维持在700°C的奥氏体类不锈钢的机械性能仍不会显着降低。
2 合理选用加工刀具合理选用加工刀具是进行不锈钢材料加工的重要先决条件。
不锈钢加工刀具的必须具有以下特点:较高的强度、硬度、韧性、耐磨性以及较低的不锈钢亲和力。
常用的刀具材料有硬质合金和高速钢两大类,形状复杂的刀具主要采用高速钢材料。
由于高速钢切削不锈钢时的切削速度不能太高,因此影响生产效率的提高。
对于车刀类较简单的刀具,刀具材料应选用强度高、导热性好的硬质合金,因其硬度、耐磨性等性能优于高速钢。
常用的硬质合金材料有:钨钴类((YW1、YW2)。
数控车削加工切削速度、进给量、背吃刀量选取参考表

0.6
1.5
0.6
>180~260 1.3 0.5 1.3 0.6 1.4
0.6
1.6
0.7
>260~360 1.3 0.6 1.4 0.6 1.5
0.7
1.7
0.7
>360~500 1.4 0.7 1.5 0.7 1.5
0.8
1.7
0.8
1、粗加工,表面粗糙度为 Ra50~12.5 时,一次走刀应尽可能切除全部余量。
1
高速钢
200~ 225
4
8
15--24 0.13-0.18 76-105 85-125 12--20 0.25-0.4 60-84 69-100
9--15 0.4-0.5 46-64 53-76
0.18 YW1,YT15 115-160 0.18 420-460 0.4 YW2,YT14 90-130 0.4 250-275
8 24-27 0.5
84-95 105-115 0.75
YT5 135-145 0.5 275-335 0.4
合 金 钢
中 175~ 碳 225
1 4 8
34-41 26-32 20-24
0.18 0.4 0.5
105-115 85-90 67-73
130-150 0.18 105-120 0.4-0.5 82-95 0.5-0.75
0.18 0.5 0.75
YT15 YT14 YT5
175-190 135-150 105-120
0.18 0.4 0.5
460-520 275-335 215-245
0.13 0.25 0.4
1 高强度 225~ 4
钢 350 8
20-26 15-20 12--15
钻头加工参数公式

钻头加工参数的选择通常涉及到钻头直径、材料类型、切削速度、进给速度和切削深度等 因素。以下是一些常见的钻头加工参数公式:
1. 切削速度(Vc)公式: - D为钻头直径(单位为毫米),n为转速(单位为转/分钟)。
2. 进给速度(Vf)公式: - Vf = f × n - 其中,f为进给量(单位为毫米/转),n为转速(单位为转/分钟)。
钻头加工参数公式
3. 切削深度(Ap)公式: - Ap = D × α - 其中,D为钻头直径(单位为毫米),α为切削角度(单位为度)。
请注意,以上公式仅供参考,实际应用中还需要根据具体情况和材料特性进行调整。此外 ,为了确保钻头加工质量和安全性,建议参考钻头制造商提供的技术数据和建议。
机械加工工艺手册切削速度表

机械加工工艺手册切削速度表
机械加工工艺手册中的切削速度表是用来指导机械加工过程中
切削速度的选择和调整。
切削速度表通常包括不同材料和刀具类型
的推荐切削速度范围,以确保在加工过程中获得最佳的切削效果和
工件质量。
首先,切削速度表会列出各种常见材料(如钢、铝、铜等)的
推荐切削速度范围。
这些推荐数值是根据材料的硬度、塑性、热导
率等特性来确定的,以确保在加工过程中既能够有效地去除材料,
又不会造成刀具磨损过快或者工件表面质量不佳的问题。
其次,切削速度表也会考虑不同类型的刀具,比如钻头、铣刀、车刀等,针对不同刀具的材料、涂层、刃数等特点,给出相应的推
荐切削速度范围。
这些推荐数值能够帮助操作人员根据具体的加工
任务选择合适的刀具和切削参数,以提高加工效率和工件精度。
另外,切削速度表也可能会考虑到不同加工方式(如车削、铣削、钻削等)对切削速度的影响,因为不同的加工方式会对刀具和
工件产生不同的切削力和热量,需要相应地调整切削速度以获得最
佳的加工效果。
总之,切削速度表是机械加工过程中的重要参考依据,能够帮
助操作人员根据材料、刀具、加工方式等因素选择合适的切削速度,从而确保加工质量和效率。
操作人员在使用切削速度表时应该根据
实际情况综合考虑各种因素,灵活调整切削参数,以满足具体加工
任务的要求。
高锰钢加工

一、高锰钢的特性和切削加工性
高锰钢是一种机械行业常用的耐磨钢,有些衬板类无需加工,但有些零件,由于其设计需要又不得不加工。高锰钢常采用水韧处理,即把铸件加热到1000-1100°C后,急速水冷,使碳化物来不及从奥氏体中析出,从而获得单一均匀奥氏体金相组织,这时的高锰钢才具有较好的使用性能;如高强度,高韧性,高耐磨性。其重要性能是,在较大的冲击或接触应力的作用下,表层迅速产生加工硬化,能承受很大的冲击载荷。
(2)后角:为了减小后面的摩擦与磨损,减轻加工表面的加工硬化,后角α0=6 °-13 °,粗车时取小值,精车时取大值。
(3)切削用量
1.吃刀量,加工高锰钢时,吃刀量宜取中等数值,既避免切削力过大,又避免加速刀具磨损。一般我们选用:粗车ap=5-6mm,精车ap=0.5-1mm。2.进给量。由于加工高锰钢时硬化层深度较大,因而进给量宜选较大值。一般取f=0.2-0.3mm/r。3.切削速度,用硬质合金刀具加工高锰钢时,切削力大,切削温度高,刀具磨损快,所以切削速度不宜太快。一般取Vc=20-30m/min,其中较低的速度用于粗车,较高的速度用于半精车或精车。
三、高锰钢的合理切削条件
经过多达十多种盘类零件和轴类零件的车削加工,我们总结出了高锰钢的合理加工工艺。
(一)刀具材料:优先采用YM052,YM053刀具材料
(二)刀具几何参数及角度如下:
(1)前角:针对高锰钢切削力大和导热性差的特点,刀具的前角应选用较小值,以增强切削刃强度和散热体积。一般前角γ0=-5 °-8°,粗车时取小值,精车时取大值。
高锰钢的切削加工性很差,具有以下特点:
1.切削时,塑性变形大,加工硬化严重。致使单位切削力很大,车外圆时比加工45号钢增大60%以上。2.由于切削力大,使单位切削功率增大,单位时间内产生的热量多,而高锰钢自身导热性能又差,致使切削区温度高达1000°C以上,刀具磨损严重,刀具寿命低。3.高锰钢塑性大,切削时易形成积屑瘤和鳞刺。4.切屑强度大,韧性高,不易折断。
刀具材料应具备的基本性能

刀具材料应具备的基本性能:1硬度2耐磨性3耐热性4强度和韧性5减磨性6导热性热膨胀系数7工艺性和经济性高速钢的特点和功用:W, Mo, Cr, V提高了钢的耐磨性和淬透性高速钢经淬火并三次高温回火后,由于弥散效应进一步提高了硬度和耐磨性。
600摄氏度以上时,其硬度下降而失去切削性能,切削中碳钢时,切削速度可达30m/min左右。
优点:强度,韧性,工艺性好,而且价格便宜,应用广泛,主要应用于复杂刀具和小型刀具的制造。
对于强度硬度较高的难加工材料,切削速度不超过30m/min,而且切削效果不理想,解决方法:1改变高速钢的结构成分(使之变成高性能高速钢,可用于切削高强度钢,高温合金,钛合金等)2采用粉末冶金技术(粉末冶金高速钢的韧性和硬度较高,可磨削性能显著改善,材质均匀,热处理变形小,适合于制造各种精密刀具和复杂刀具)3采用表面深入法(渗C,表面硬度、耐磨性高,脆性增加;渗硼可降低脆性并提高粘结性;渗硫可减小表面摩擦;渗氮可提高热硬性)4采用表面涂覆硬质膜技术(经涂层后的刀具耐磨性和使用寿命大大提高(3—7倍)切削效率提高30%,用于制造复杂的刀具,如:钻头、丝锥、铣刀和齿轮刀具等)切削速度对积屑瘤的影响:Ⅰ区:切削速度很低,形成粒状或节状屑,没有积屑瘤生成Ⅱ区:形成带状切屑,冷焊条件逐渐形成,随着切削速度的提高积屑瘤高度也上升,若T(推屑力)<Ff(摩擦阻力),积屑瘤高度继续上升,当T>Ff时,积屑瘤被推走,T==F积屑瘤高度为临界高度。
在这个区域内,积屑瘤生长的基础比较稳定,此时能代替刀具切屑,并保护刀具。
Ⅲ区:积屑瘤高度随切削速度上升而下降,当达到区域右边界时,积屑瘤消失。
随着切削速度进一步提高,切屑底部由于切削温度上升而开始软化剪切屈服极限下降,摩擦阻力下降,切屑的滞留倾向减弱。
在此区域,脱落的积屑瘤硬块不断滑擦刀面,使刀具磨损加快。
Ⅳ区:切削速度进一步提高,由于切削温度较高而冷焊消失,积屑瘤不再存在了。
40cr钢通用切削速率
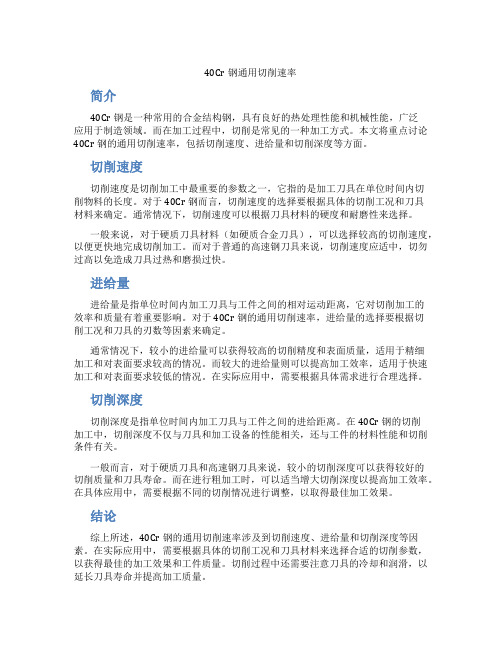
40Cr钢通用切削速率简介40Cr钢是一种常用的合金结构钢,具有良好的热处理性能和机械性能,广泛应用于制造领域。
而在加工过程中,切削是常见的一种加工方式。
本文将重点讨论40Cr钢的通用切削速率,包括切削速度、进给量和切削深度等方面。
切削速度切削速度是切削加工中最重要的参数之一,它指的是加工刀具在单位时间内切削物料的长度。
对于40Cr钢而言,切削速度的选择要根据具体的切削工况和刀具材料来确定。
通常情况下,切削速度可以根据刀具材料的硬度和耐磨性来选择。
一般来说,对于硬质刀具材料(如硬质合金刀具),可以选择较高的切削速度,以便更快地完成切削加工。
而对于普通的高速钢刀具来说,切削速度应适中,切勿过高以免造成刀具过热和磨损过快。
进给量进给量是指单位时间内加工刀具与工件之间的相对运动距离,它对切削加工的效率和质量有着重要影响。
对于40Cr钢的通用切削速率,进给量的选择要根据切削工况和刀具的刃数等因素来确定。
通常情况下,较小的进给量可以获得较高的切削精度和表面质量,适用于精细加工和对表面要求较高的情况。
而较大的进给量则可以提高加工效率,适用于快速加工和对表面要求较低的情况。
在实际应用中,需要根据具体需求进行合理选择。
切削深度切削深度是指单位时间内加工刀具与工件之间的进给距离。
在40Cr钢的切削加工中,切削深度不仅与刀具和加工设备的性能相关,还与工件的材料性能和切削条件有关。
一般而言,对于硬质刀具和高速钢刀具来说,较小的切削深度可以获得较好的切削质量和刀具寿命。
而在进行粗加工时,可以适当增大切削深度以提高加工效率。
在具体应用中,需要根据不同的切削情况进行调整,以取得最佳加工效果。
结论综上所述,40Cr钢的通用切削速率涉及到切削速度、进给量和切削深度等因素。
在实际应用中,需要根据具体的切削工况和刀具材料来选择合适的切削参数,以获得最佳的加工效果和工件质量。
切削过程中还需要注意刀具的冷却和润滑,以延长刀具寿命并提高加工质量。
- 1、下载文档前请自行甄别文档内容的完整性,平台不提供额外的编辑、内容补充、找答案等附加服务。
- 2、"仅部分预览"的文档,不可在线预览部分如存在完整性等问题,可反馈申请退款(可完整预览的文档不适用该条件!)。
- 3、如文档侵犯您的权益,请联系客服反馈,我们会尽快为您处理(人工客服工作时间:9:00-18:30)。
钢的最佳切削速度文档编制序号:[KK8UY-LL9IO69-TTO6M3-MTOL89-FTT688]
45号钢的最佳切削速度
1.切削速度的选取
切削速度快慢直接影响切削效率。
若切削速度太快,虽然可以缩短切削时间,但不可避免刀具产生高热现象,影响刀具的寿命。
若切削速度过小,则切削时间会加长,效率低,刀具无法发挥其功能;决定切削速度的因素很多,概括起来有:
(1)刀具材料。
刀具材料是影响切削速度的最主要因素。
刀具材料不同,允许的最高切削速度也不同。
高碳钢刀具的切削速度约为5m/min,高速钢刀具的切削速度约为20m/min,硬质合金刀具的切削速度约为
80m/min,涂层硬质合金刀具的切削速度约为200m/min,陶瓷刀具的切削速度可高达1000m/min。
(2)工件材料。
工件材料硬度高低会影响刀具切削速度,同一刀具加工硬材料时切削速度应降低,而加工较软材料时,切削速度可以提高。
表4
工件材料刀具材料硬度耐热度(℃)切削速度(m/min)
45号钢高速钢 HRC66~70 600~645 3
硬质合金 HRA90~92 800~1000 100~150
2.切削深度的选取
切削深度要根据机床、工件和刀具的刚度来决定,主要受机床刚度的制约。
在机床刚度允许的情况下,切削深度应尽可能大,如果不受加工精度的限制,可以使切削深度等于零件的加工余量。
这样可以减少走刀次数,提高生产效率。
为了保证加工表面质量,应根据加工余量确定,留少量精加工余量,一般粗加工时,一次进给应尽可能切除全部余量。
背吃刀量不均匀时,粗加工要分几次进给,并且应当把第一,二次进给时的切削深度尽量取得大一些;在中等功率的机床上,切削深度取为8~10mm。
半精加工时,切削深度选取为0.5~2mm。
精加工时,切削深度选取0.2~0.5mm。
总之,切削深度的具体数值应根据机床性能、相关的手册并结合实际经验用类比方法确定。
3.进给量的选取
进给量是数控机床切削用量中的重要参数,根据零件的表面粗糙度,零件的加工精度要求,及刀具材料、工件材料等因素来决定,可以参考切削用量手册选取。
最大的进给量受到机床刚度和进给驱动以及数控系统的限制。
此外在切削时,刀尖半径与进给量、表面粗糙度的理论值存在一定关系,此关系可以用公式
三、切削用量的选择
在数控铣削中,切削用量有切削深度、主轴转速、进给速度,在指导学生的过程中,往往是一个难点。
1.切削深度ap的选择原则:在粗加工中,往往是在刀具允许的前提下,尽量一次切完,但是前面提到切削深度H<(1/4-1/6)ρmin在需要做两次切削的情况下,第一次切削去掉加工余量的2/3或者3/4,采用递减的原则。
考虑切削深度还要考虑工件材料的易切削加工性及刀具材料的性能。
2.切削速度的选择:切削速度越大,加工效率越高,刀具的耐用度越低;当切削塑性材料时,如果采用中速切削最容易产生积屑瘤,增加工件的粗糙度。
应该避免在这个区间内选择切削速度。
当刀具材料为硬质合金时,切削速度可以比高速钢刀具更高,因为硬质合金刀具的红硬性更好。
在同样刀具情况下,工件材料的易切系数大时,可以采用较高的速度切削,如铝合金的易切系数大,当其切削速度选择300m/min时,45号正火钢的易切系数比铝合金小,其切削速度则选择100m/min。
3.进给速度Feedrate和Plunge的选择:首先是选择每个刀齿的进给深度f,刀齿数为Z,则每转进给量为fZ,每分钟进给量则为F=fZS,式中S为主轴转速。
Feedrate与Plunge都是进给速度,Feedrate是水平方向的,而Plunge是垂直方向的。
由于垂直方向的切削排屑更困难,往往取更小值
主轴转速的计算式为:S=1000V/DЛ
式中单位:V-切削速度,m/min D-刀具直径,mm S-r/min
确定切削用量的一般步骤为:首先确定背吃刀量,再根据工件和刀具材料确定切削速度,然后计算出主轴转速,最后确定每分钟进给速度F。
特别要注意的是,程序中的转速S发生改变时,其进给速度也要随着改变。
进给速度不是一个孤立的参数。
在自动编程过程中要特别注意每个参数都要经过认真的计算之后再填入,不可忽略任何一个参数的计算,如果任凭软件自动生成的默认数据,可能会造成非常严重的后果,计算机只是辅助工具,不可完全依赖编程软件!
45号钢是典型的中碳钢,含碳0.45%;
45号钢通常是调质状态的,硬度HRC20-30;
背吃刀量ap不是对某一种类的钢而言的,而是一个加工单位,45钢的背吃刀量没有定量,根据加工要求和机床性能而定
背吃刀量ap指主刀刃与工件切削表面接触长度在主运动方向和进给运动方向所组成平面的法线方向上测量的值。
对于外圆车削,背吃刀量ap (mm)等于工件已加工表面与待加工表面间的垂直距离,即ap=(dw-dm)/2,式中dw—工件待加工表面的直径(mm);dm—工件已加工表面的直径(mm)。
对于平面刨削,背吃刀量也是工件待加工表面与已加工表面间的垂直距离。