吸塑工艺流程图
吸塑行业生产计划流程表

吸塑行业生产计划流程表吸塑行业生产计划流程表吸塑产品生产工艺一、吸塑产品生产工艺流程图片材原材料->吸塑成型->半成品检验->包装冲切->成品检验->入库二、吸塑原材料简介吸塑原料的识别 1、看环保标识的方法:2. 密度和强度法:以液体为介质,检验其塑料在液体介质中的沉浮,以粗略辨别塑料的大类,如一块塑料放在水中,浮在水面可断定,原料不是PVC(因PVC的密度>1),折压片材手感其强度。
各片材密度和强度如下表:铜模制作流程铝模制作流程吸塑生产工艺流程一、吸塑模具选择吸塑模具一般有石膏模、电镀铜模和铝模三种石膏模:用石膏在半湿的状态下雕刻成型,然后烘干即成模具,石膏模成本低,易于修改,但石膏模精度不够高,表面不光滑而且易碎不耐用,因此它常用来打佯、做电镀铜模的模种或一些要求不高小批量生产的吸塑模具。
铝模:用铝锭通过机械(车床、铣床、C等)加工而成。
铝模精度高、表面光滑而且经久耐用,但价格非常贵,铝模一般用在精度要求较高铜模达不到的吸塑产品上。
电镀铜模:用石膏模种制成样品后,电镀一层铜壳即为电镀铜模,成本相对石膏模高,但比铝模便宜得多,因其表面光洁耐用、低成本的优点,电镀铜模是最常用的一种吸塑模具。
二、吸塑材料的选择吸塑产品的原材料只有塑胶片材,胶片厚度一般不超过1.5MM,常用的片材有:PVC、PET、PP、PS以及在此基础上的植绒片材、镀金片材和防静电片材。
PVC:最常用的吸塑材料,质软、韧性强、可塑性好,可做成透明和各种颜色,常用透明PVC包装电子、化装品、玩具礼品等产品。
PET(A-PET):质硬,韧性好、强度高、表面光亮、环保无毒,有透明和多种颜色的片材。
缺点是PET高周波热合比较困难,价格也比PVC贵很多,此材料常被要求产品高档和环保的用户取代PVC PS:密度小(质轻)、环保无毒,可塑性非常好,韧性差易脆,不可做成通明材料,因此只能做成底托类吸塑,因其易裂,此类吸塑不宜回收PP:材质特别软,韧性好,环保无毒、耐高温,常被做成餐饮器具或其他耐高温产品的包装;但其可塑性差,加工难度大,表面光泽度差,而且加工时颜色会变浅。
吸塑模具制作流程PPT课件

周边12处卡点旋 转180度后不重 合
21
吸塑模具设计步骤
7.导向的设计 TRAY旋转180度叠加后可 以完全重合,叠加后左右不 会移动,起到定位的作用,
导向的半径不小于3mm,
导向的高度=TRAY高
旋转 180度 可完全 重合
精选PPT课件
22
吸塑模具设计步骤
8.脱模角的设计 a).一般穴内作3~5度脱模角,如果要求零件的晃动很小,脱模角 最小设计为3度
b). TRAY的外侧脱模角一般取5~7度
注:f为TRAY在成型冷却后产生的包紧力(如下图所示)
TRAY外侧成型冷却 后产生的包紧力大
于内侧包紧力
精选PPT课件23补 Nhomakorabea说明当模具制作完成后,如需设变,需按设变原则: 1)如果穴位设变加大,在模具空间足够的情况下,可以
在原模上加工. 2)如果穴位需要设变改小,原模报废,需重新开模.
鋁模
鋁模 表面光滑度要求高的,零件小的,間距小的,形狀不 規則的必須以鋁模來制模具 ﹐鋁模使用壽命最长
不论是铝模还是铜模,一旦模具完成,生产过程中不用担心尺寸会有变动
,因为吸塑模是单模,稳定性比较好!
精选PPT课件
10
吸塑模具製作主要過程
設計
加工
打孔拋光
精选PPT课件
11
吸塑模具设计步骤
精选PPT课件
12
吸塑模具设计注意事项
部分產品需要倒扣,即是上下、裏外需緊密扣牢。具體依客戶要 求設計。因為有的扣是圓的,有的倒扣是方的,還有的倒扣是不規 則的。
產品需要折邊、沖孔,也要根據客戶需求來設計。
上口小,底部大的產品,如瓶子形狀,就無法設計。
尺寸標注,這點也是比較關鍵的一部分,主要是整個產品的外部和內部尺 寸要標清。其次是穴位的內部尺寸要求,特殊尺寸另作說明。
吸塑的生产工艺(详细版)

吸塑原料的识别1、看环保标识的方法:2. 密度和强度法:以液体为介质,检验其塑料在液体介质中的沉浮,以粗略辨别塑料的大类,如一块塑料放在水中,浮在水面可断定,原料不是PVC(因PVC的密度>1),折压片材手感其强度。
各片材密度和强度如下表:通称密度强度常用厚度PS 1.06-1.07g/cm3约20Mpa0.17-1.5㎜PP0.97-0.99g/cm3约24Mpa0.25-1.0㎜PVC 1.36g/cm3约54Mpa0.17-0.8㎜APET 1.31-1.35g/cm3约57Mpa0.25-0.8㎜GAG 1.29-1.33g/cm3约57Mpa0.25-0.8㎜PETG 1.27-1.30g/cm3约57Mpa0.25-0.8㎜3.燃烧法:主要考查火焰的颜色和燃烧时发出的气味和烟雾.名称英文燃烧情况燃烧火焰状态离火后情况气味聚苯乙烯PS易燃软化起泡橙黄色,浓黑烟,炭末继续燃烧表面油性光亮特殊乙烯气味聚丙烯PP易燃熔融滴落,上黄下蓝烟少,继续燃烧石油味聚氯乙烯PVC难软化不助燃上黄下绿有烟离火熄灭刺激性酸味聚对苯二甲酸乙二酯PET易燃橙色,有小量黑烟继续燃烧酸味聚合物GAG易燃橙色,有小量黑烟继续燃烧酸味聚合物PETG易燃橙色,有小量黑烟继续燃烧酸味注聚合物是:还已烷二甲醇+对苯二甲酸+乙二醇的聚合体.三、吸塑模具制作简介依图纸石膏模制作流程依实物石膏模制作流程铜模制作流程铝模制作流程四、吸塑成型简介成型四大要素吸塑成型工艺流程进料->加热(300±250C)->塑化->真空吸附->保压->冷却->吹底风->脫模->刀闸裁断->頂出->刀模冲裁成型工艺图(香港电业吸塑机)五、裁切包装简介裁切工艺图(华士裁切机)六、未来发展目标无尘车间树脂模采用树脂模的主要目的:较大程度的减少表面水纹全自动吸塑成型裁切机。
吸塑QC工程图

见仪器操 作
说明书
原材料、片材 受入标准
依AQL
依作业指导 卡尺、直
书
尺
作业指导书
自检
卡尺
目视 实
装
依产品标准 书
目视
依产品标准 书
目视
依照图纸
客户要求
作业指导书 部品检验标准书
作业指导书 部品检验标准书
自检
自检
自检 巡检 自检 巡检
折边
折边机
边位准确、无烫伤 无刮伤
套装边位准确
依产品标准 书
目视
作业指导书 部品检验标准书
PQC 制程巡检报告单 作业员
出货检验报告单 PQC
FQC
出货检验报告单 出厂成绩表
仓管员
担当
化学物质检验
一般公差
±0.5mm或依 照客户
尺寸
要求
同上
外观、尺寸
打样机 吸塑机
恒温410℃ ±30℃
恒压8kg/ ㎝2
±0.5kg/㎝2
恒温410℃ ±30℃
恒压8kg/ ㎝2
±0.5kg/㎝2
裁断机
无拉丝、 无吸不到位
无拉丝、 无吸不到位
厚度均匀 边位及孔位无毛刺、表 面无刮伤
套装孔位准确
依原材料、 片材 受入标准
**塑胶制品有限公司
QC 工 程 图
制造流程 流程图 工程名
主要设备
作业条件
名称 条件名称 设定条件
产品规格 检查项目
测量仪器 规格/允差 及方式
操作、检验 规范
检验 频度
片材外观尺寸重量
进货检验 游标卡尺
厚度、透明度
模具制作 外加工铸
造 首件打样
吸塑盘工艺流程(1)

吸塑盘工艺流程一、吸塑打样客户认可电脑设计稿后,生产调度会根据吸塑产品的复杂程度决定采用哪种方式开发模具(石膏模、铜模、铝模),开发周期3-5天。
吸塑打样以石膏模打样居多。
其操作步骤是:1.先将实物用手工泥糊出成型轮廓;2。
放到吸塑打版机上成型泡壳毛胚;3.用配好的吸塑专用石膏倒入泡壳毛胚中,风干后形成石膏毛胚;4。
采用电动铣床对石膏毛胚和规则形状进行深加工;5.手工打磨和手工添加部件;6。
将各个抛光好的石膏部件粘合成完整的石膏模;7.再放入吸塑打版机吸塑成型完整的样品;8.按成品尺寸,手工切边、封边,完成全部打样过程。
如果有需求,印刷打样部门同时会将吸塑样品所用的纸卡、不干胶或彩盒一起制作,他们会借助全开的印刷数码打样机能将实际印刷结果反映出来。
二、制作生产模具样品被客户认可后,通常会下一定数量的生产订单。
生产调度会根据产量、吸塑成型的复杂程度决定采用哪种模具量产:1、采用石膏模生产模具制作过程类似于吸塑打样,优点在于生产周期短,成本最低,制作一整版(60X110cm)模具只需一到两天时间,不足之处在于吸塑成品表面粗糙,生产中模具容易碎裂,耐用性差无法成型深度大、复杂度高、片材厚的产品。
2、采用电镀铜模其工艺是将打好样的泡壳表面喷上一层导电剂,再放入电解槽内镀上厚厚的铜层,电镀过程需要72小时,接着要对铜模进行灌石膏(增加硬度)、抛光、打气眼处理,采用电镀铜模生产的优点是吸塑制品表面光滑,成本适中,耐用性适中,缺点是模具制作周期长,无法完成精密吸塑制品的生产。
3、采用吸塑铝模生产,模具制作需要先采用电脑设计图纸,再采用CNC数控铣床加工,优点是制作周期适中,后期模具处理时间短(钻气眼工作在CNC加工时完成),吸塑产品尺寸精度高,模具耐用性强,缺点是成本高。
由于全自动高速吸塑成型机的成型范围是66X110cm左右,所以不管是石膏模、铜模还是铝模,都需要将单个的模具拼在一起,达到成型尺寸,我们都称这个过程为拼版,需要拼在打好气孔的铝板或木板上,拼好后的整版模具我们称之为底模。
吸塑生产安全操作规范

吸塑生产安全操作规范吸塑车间生产操作规范与要求一、规范内容,, 机器各部分的使用要求。
, 控制电箱及嵌板的使用要求、指令要求。
, 操作顺序与方法。
, 机器的检查、保养、润滑要求与故障排除。
, 工具的正确使用与保管。
, 岗位培训要求与考核方式。
, 人员工作纪律要求。
, 问题反馈与处理要求。
, 注意事项。
二、规范要求:, 熟悉机器各部分的功能与性能及作业要求。
, 掌握控制面板各按钮的指令及操作要求。
, 了解机器操作流程和各控制钮、气阀、继电器阀的要领。
, 工具的正确使用方法及防护措施。
, 岗位职责与上岗要求, 工位要求与纪律要求。
, 问题反馈途径与措施、对策。
三、具体内容与要求:1、按吸塑成型机功能划分为上料区、加热软化区、真空成型区、冷却固化区、放料储放区五大部分。
1(1成型过程:上料拉片加热真空成型冷却脱模切料放料。
1(1( 1上料架:上料前,清洁上料架的尘渍、污垢、碎物。
确保上料区干净、整洁、无污染物。
然按生产需求取用既定规格片材。
1(1(2、调节拉片链条间的间距,使胶片宽度与两链间隔啮合相匹配。
调节上料挡块,使胶片刚好置于两挡块之间并紧固。
1(1(3、闭合电源、电热开关,调节电炉旋钮使胶片软化达到可成型的适宜温度。
进行预热。
(检查各电流表是否完好、灵敏、有效)。
1(1(4、旋钮切换至手动挡,检查模具是否密封、上模夹具是否紧固、各气路是否畅通并调整拉片拉杆、设定电热时间、真空时间、冷风时间、喷水时间、脱模吹风时间、刀闸时间以及震模频率等。
闭合真空泵开关,并进行相关参数初步调整。
(注意事项:(1)、操作者在操控主面板时,严禁他人在机器成型区域调试 (2)、严禁手伸入刀闸行程区域)。
1(1(5、开机调试(切换至自动挡)视产品具体质量要求,进行调整处理。
经巡检做首件确认后,正式批量生产。
1(1(6、操作员如实做好开机记录、上料记录、生产记录、机器设备点检记录、模具使用状况记录、异常交接记录、半成品标示并签名。
吸塑设计及其制造PPT课件

2021/4/11
9
第9页/共39页
四,机器基本装置 (1)
•
1.夹紧设备
•
塑料片材成型时,片材被固定在夹紧装置上。在真空吸塑成型的通用型机和
复合型的热成型机上多采用便于固定各种尺寸片材的夹紧装置。有的是整个
成型机配一套夹紧框架。
•
夹紧装置可分为两类:一类是框架式,另一类是分瓣式。框架式夹紧
装置由上、下两个框架组成。片材夹在两个框架之间。框架打开时,下框架
• 应用如下:成型材料未受热的区域(如未受热的夹持边缘)不收缩,而成型的部 分则在成型后收缩;但是不同收缩的区域会造成模塑物的变形。
• 对于实际应用的意义:若制件的夹持边缘在脱模后立即就被切断,那么它就不必 进行加热;若夹持边缘留在制件上,夹持边就必须加热到材料的软化温度。
2021/4/11
19
第19页/共39页
2021/4/11
16
第16页/共39页
有效成型压力(2)
图10:成型机器的海拔高 度对真空成型中的空气压 力的影响
•
a 和b 阳模;c 和d 阴模 (+)模具面积,在该面积区域材料的有效成型压力因
接触压力而增加;(-)模具面积,在该面积区域有效成压力因成型材料的反向压
力而降低 .
•
对于模压成型(阳模)通常的成型压力:大面积模制件0.2 ~ 0.3MPa ( 2 ~
第4页/共39页
2021/4/11 4
阳模成型
图4:阳模成型
2021/4/11
真空吸塑阳模成型工艺过程如图4所示。
本法对于制造壁厚和深度较大的制品比较有
利。
制品的主要特点是:与真空阴模成型法一样,
模腔壁贴合的一面质量较高,结构上也比较鲜明
吸塑生产工艺介绍

从材料,模具,吸塑,冲压各环节认识吸塑产品的全过程2021年6月目录CONTENTS01吸塑流程图02常用材料的认识03模具的介绍04吸塑成型介绍05裁切包装吸塑流程图打样流程图量产流程图吸塑工艺流程图与实物试装产品图纸/实物制作/修改石膏模石膏模材料吸塑打样冲压裁切不合格合格铜模/铝模量产1成品检验包装冲切半成品检验吸塑工艺流程图吸塑成型入库吸塑原材料2材料的认识材料种类材料的判认材料特性12345聚对苯二甲酸乙二醇酯Polyethylene terephthalate PET聚苯乙烯PolystyrenePS聚丙烯polypropylenePP聚对苯二甲酸乙二醇酯PETG聚氯乙烯Polyvinyl chloridePVC吸塑常用材料透明度高,不易破边,属环保材料,可周转使用。
优点高度结晶的聚合物,表面平滑有光泽。
耐疲劳性,耐摩擦性,尺寸稳定性好。
性质成型温度:70-80℃ 冷却时间:14-20s 熔化温度:120℃开始溶化温度要求吸塑常用材料易破碎,根据温度不同会有发白现象存在,有同厂家颜色有差异。
缺点用于包装电子、五金、玩具、食品、化妆品、学习用品等。
用途吸塑常用材料2.PS的认识透明度高,不易破边,属环保材料,可周转使用。
优点拉伸强度可达60Mpa 以上,冲击强度小,耐磨性差,力学性随温度升高而变大,收缩率为0.4-0.7%。
性质成型温度:75-85℃ 冷却时间:14-20s 熔化温度:95-150℃开始溶化温度要求易破边,周使用率底,不同厂家生产的颜色有差异。
缺点用于包装电子、五金、玩具、食品、化妆品、学习用品等。
用途吸塑常用材料刚硬有韧性、抗弯强度高、抗疲劳、抗应力开裂;质轻;在100-150℃仍能保持力学性。
优点半结晶性材料,比PE要更坚硬且有更高的熔点。
由于结晶度较高,表面的刚度和抗划痕特性很好。
收缩率为1.8-2.5%。
性质成型温度:140℃以上冷却时间:24-30s溶化温度:150-220℃开始熔化温度要求0℃以下变脆;耐侯性高。
吸塑涂布工艺流程

吸塑涂布工艺流程
一、准备阶段
1.确定产品设计和规格要求
2.准备原材料和生产设备
3.安排生产人员和相关人员
二、材料准备
1.准备吸塑材料和涂布材料
2.对材料进行检验和质量确认
3.根据产品要求进行材料切割和配料
三、吸塑工艺
1.吸塑模具准备
(1)清洁吸塑模具并进行检查
(2)涂抹模具表面润滑剂
(3)调整模具参数和位置
2.材料加热和成型
(1)将吸塑材料放入吸塑机中加热
(2)加热至合适温度后,吸塑成型
(3)控制吸塑时间和温度,确保成型质量
3.冷却和固化
(1)成型后的产品在模具中进行冷却
(2)冷却后,产品固化并脱模
(3)检查产品质量和外观
四、涂布工艺
1.涂布准备
(1)准备涂布设备和工具
(2)调配涂布材料和溶剂
(3)清洁和准备涂布表面
2.涂布操作
(1)将涂布材料均匀涂布在产品表面
(2)控制涂布厚度和均匀度
(3)确保涂布质量和外观
3.干燥和固化
(1)涂布后的产品进行干燥和固化
(2)控制干燥温度和时间
(3)确保涂布层干燥固化完全
五、检验与包装
1.对成品进行质量检验
2.检查产品外观和尺寸是否符合要求
3.进行包装和标识,准备发货。
吸塑生产工艺流程

吸塑生产工艺流程
如下是有关吸塑生产的工艺流程:
吸塑是一种塑料加工工艺,主要原理是将平展的塑料硬片材加热变软后,采用真空吸附于模具表面,冷却后成型,广泛用于塑料包装、灯饰、广告、装饰等行业。
具体生产工艺流程为:
1:模具制作及加工。
2:模具处理干燥完全后进行软化处理。
3:将软化处理好的塑料片连同木柜,置于真空室中,开动吸气开关,将真空室内空气吸抽干净,待塑料片冷却后,即得到与模具相同的凹型包装或工艺模具。
4:泡壳:采用吸塑工艺将透明的塑料硬片制成特定凸起形状的透明塑料,罩于产品表面,起到保护和美化产品的作用。
又名泡罩、真空罩
5:托盘:也叫塑料内托,采用吸塑工艺将塑料硬片制成特定凹槽的塑料,将产品置于凹槽内,起到保护和美化产品的作用。
6:植绒内托:是一种采用特殊材料的吸塑托盘,将普通的塑料硬片表面粘上一层绒质材料,从而使托盘表面有种绒质的手感,用来提高包装品档次。
7:抗静电托盘:是一采用特殊材料的吸塑托盘,该材料表面的电阻值小于10的11次方欧姆。
主要用于电子、IT产品的吸塑托盘。
8:吸塑模具:吸塑生产用的模具,成本最低的是石膏模,其次是电镀铜模,最贵的是铝模。
模具沾有小孔,用于真空吸附热化的硬片,形成吸塑产品。
9:吸塑成型:就是我们常讲的吸塑,采用吸塑成型机将加热软化的塑料硬
片吸附于模具表面,冷却后,形成凹凸形状的塑料。
10:吸塑裁切:吸塑成型后的塑料产品,经过冲床,将大张的片材用刀模分切成单个产品。
吸塑QC工程图

见仪器操 作
说明书
原材料、片材 受入标准
依AQL
依作业指导 卡尺、直
书
尺
作业指导书
自检
卡尺
目视 实
装
依产品标准 书
目视
依产品标准 书
目视
依照图纸
客户要求
作业指导书 部品检验标准书
作业指导书 部品检验标准书
自检
自检
自检 巡检 自检 巡检
折边
折边机
边位准确、无烫伤 无刮伤
套装边位准确
依产品标准 书
目视
作业指导书 部品检验标准书
化学物质检验
一般公差
±0.5mm或依 照客户
尺寸
要求
同上
外观、尺寸
打样机 吸塑机
恒温410℃ ±30℃
恒压8kg/ ㎝2
±0.5kg/㎝2
恒温410℃ ±30℃
恒压8kg/ ㎝2
±0.5kg/㎝2
裁断机
无拉丝、 无吸不到位
无拉丝、 无吸不到位
厚度均匀 边位及孔位无毛刺、表 面无刮伤
套装孔位准确
依原材料、 片材 受入标准
**塑胶制品有限公司
QC 工 程 图
制造流程 流程图 工程名
主要设备
作业条件
名称 条件名称 设定条件
产品规格 检查项目
测量仪器 规格/允差 及方式
操作、检验 规范
检验 频度
片材外观尺寸重量
进货检验 游标卡尺
厚度、透明度
模具制作 外加工铸
造 首件打样
成型
裁切 (冲孔)
铣床、钻 床
CNC
依实物 或图纸
同上
PQC 制程巡检报告单 作业员
出货检验报告单 PQCFra bibliotekFQC
吸塑盘工艺流程(2)

吸塑盘工艺流程
三、吸塑成型生产
采用全自动高速吸塑成型机生产,其基本原理是:
将成卷的片材拉进电炉烘箱内加热至软化状态,乘热再拉到吸塑模具上方,模具上移并抽真空,将软化的片材吸附到模具表面,同时将冷却水以雾状喷于成型片材表面,使其硬化,成型的片材再自动被拉至贮料箱,气动裁刀将成型与未成型片材分离,从而完成全部过程。
吸塑产品出现的主要质量问题大多在此过程发生:
1.吸塑不到位,是指形状变形,没有吸塑成与模具相同形状的产品;
2.吸塑过度,是指产品过薄;
3.拉线,是指成型产品上出现不应有的线痕;
4.厚薄不均。
这些问题都需要在上好模具后,调试到位,包括:片材前进的时间、加热的温度和时间、抽真空的强度和时间、上模下落的位置、时间和深度、拼版中模具的摆放位置、模具间是否加附件等等。
四、冲床加工
吸塑成型的大版面产品必须经过冲床,用一块刀版分割成为单一的产品。
其原理是在冲床的底台上有一大张塑料砧板,将大版面成型产品放在砧板上,并把事先做好的刀模卡在单一产品上,通过冲床的上下运动,裁断出单一的成品,但这种裁断方式的不足之处在于砧板和刀模比较容易损坏,从而造成切边不光滑,有毛边,对于质量要求高的泡壳,需要用冷冲模(一个公模,一个母模)和冷冲床加工。
吸塑工艺流程图

吸塑工艺流程图(总3页) -CAL-FENGHAI.-(YICAI)-Company One1-CAL-本页仅作为文档封面,使用请直接删除吸塑生产工艺流程吸塑生产过程可包括:一.客户询价;二.业务部门报价;三.吸塑模具电脑辅助设计;四.泡壳模具的开发和打样;五.制作泡壳的生产模具;六.吸塑成型生产;七.冲床裁切;八.分检包装;一、客户发出询价请求:途径一打电话询价,途径二发传真询价,途径三发Email询价,途径四通过网络聊天工具询价。
客户必须提供吸塑制品的长、宽、高和所用材料的厚度、颜色和型号(PVC、PET、PS),产品数量和生产周期。
二、业务部门报价:吸塑制品单价的高低跟以下因素有关:吸塑制品的长、宽、高和吸塑成型的复杂程度;所用材料的类型、厚度和颜色;吸塑产品的后道加工工艺(折边、打孔、封边等)、订单数量和订单周期。
报价员会以客户的样品和描述有一个最初报价,最终报价会在打样之后报出。
三、吸塑模具的电脑辅助设计:客户对于报价基本认可后,会将要求、实物或是吸塑样品交到业务部,生产调度会要求电脑设计部将客户的实物扫描并结合印刷品的设计,制作出吸塑制品的平面设计图四、泡壳模具的开发和打样:客户认可电脑设计稿后,生产调度会根据吸塑产品的复杂程度决定采用哪种方式开发模具(石膏模、铜模、铝模),开发周期3-5天。
吸塑打样以石膏模打样居多,其操作步骤是:1.先将实物用手工泥糊出成型轮廓;2.放到吸塑打版机上成型泡壳毛胚;3.用配好的吸塑专用石膏倒入泡壳毛胚中,风干后形成石膏毛胚;4.采用电动铣床对石膏毛胚和规则形状进行深加工;5.手工打磨和手工添加部件;6.将各个抛光好的石膏部件粘合成完整的石膏模;7.再放入吸塑打版机吸塑成型完整的样品;8.按成品尺寸,手工切边、封边,完成全部打样过程。
如果有需求,印刷打样部门同时会将吸塑样品所用的纸卡、不干胶或彩盒一起制作,他们会借助全开的印刷数码打样机能将实际印刷结果反映出来,由深正电业伺服丝杆吸塑机阙龙宇提供,微信号:412152899。
吸塑的工艺流程
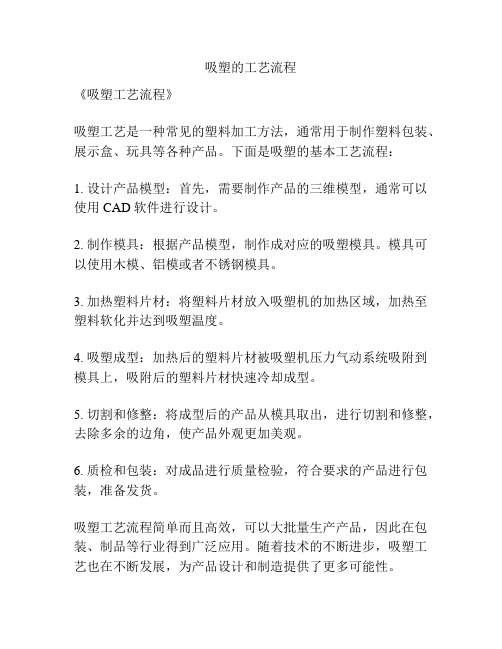
吸塑的工艺流程
《吸塑工艺流程》
吸塑工艺是一种常见的塑料加工方法,通常用于制作塑料包装、展示盒、玩具等各种产品。
下面是吸塑的基本工艺流程:
1. 设计产品模型:首先,需要制作产品的三维模型,通常可以使用CAD软件进行设计。
2. 制作模具:根据产品模型,制作成对应的吸塑模具。
模具可以使用木模、铝模或者不锈钢模具。
3. 加热塑料片材:将塑料片材放入吸塑机的加热区域,加热至塑料软化并达到吸塑温度。
4. 吸塑成型:加热后的塑料片材被吸塑机压力气动系统吸附到模具上,吸附后的塑料片材快速冷却成型。
5. 切割和修整:将成型后的产品从模具取出,进行切割和修整,去除多余的边角,使产品外观更加美观。
6. 质检和包装:对成品进行质量检验,符合要求的产品进行包装,准备发货。
吸塑工艺流程简单而且高效,可以大批量生产产品,因此在包装、制品等行业得到广泛应用。
随着技术的不断进步,吸塑工艺也在不断发展,为产品设计和制造提供了更多可能性。
- 1、下载文档前请自行甄别文档内容的完整性,平台不提供额外的编辑、内容补充、找答案等附加服务。
- 2、"仅部分预览"的文档,不可在线预览部分如存在完整性等问题,可反馈申请退款(可完整预览的文档不适用该条件!)。
- 3、如文档侵犯您的权益,请联系客服反馈,我们会尽快为您处理(人工客服工作时间:9:00-18:30)。
吸塑工艺流程图
标准化文件发布号:(9312-EUATWW-MWUB-WUNN-INNUL-DQQTY-
吸塑生产工艺流程吸塑生产过程可包括:
一.客户询价;
二.业务部门报价;
三.吸塑模具电脑辅助设计;
四.泡壳模具的开发和打样;
五.制作泡壳的生产模具;
六.吸塑成型生产;
七.冲床裁切;
八.分检包装;
一、客户发出询价请求:途径一打电话询价,途径二发传真询价,途径三发Email询价,途径四通过网络聊天工具询价。
客户必须提供吸塑制品的长、宽、高和所用材料的厚度、颜色和型号(PVC、PET、PS),产品数量和生产周期。
二、业务部门报价:吸塑制品单价的高低跟以下因素有关:吸塑制品的长、宽、高和吸塑成型的复杂程度;所用材料的类型、厚度和颜色;吸塑产品的后道加工工艺(折边、打孔、封边等)、订单数量和订单周期。
报价员会以客户的样品和描述有一个最初报价,最终报价会在打样之后报出。
三、吸塑模具的电脑辅助设计:客户对于报价基本认可后,会将要求、实物或是吸塑样品交到业务部,生产调度会要求电脑设计部将客户的实物扫描并结合印刷品的设计,制作出吸塑制品的平面设计图
四、泡壳模具的开发和打样:客户认可电脑设计稿后,生产调度会根据吸塑产品的复杂程度决定采用哪种方式开发模具(石膏模、铜模、铝模),开发周期3-5天。
吸塑打样以石膏模打样居多,其操作步骤是:1.先将实物用手工泥糊出成型轮廓;2.放到吸塑打版机上成型泡壳毛胚;3.用配好的吸塑专用石膏倒入泡壳毛胚中,风干后形成石膏毛胚;4.采用电动铣床对石膏毛胚和规则形状进行深加工;5.手工打磨和手工添加部件;6.将各个抛光好的石膏部件粘合成完整的石膏模;7.再放入吸塑打版机吸塑成型完整的样品;8.按成品尺寸,手工切边、封边,完成全部打样过程。
如果有需求,印刷打样部门同时会将吸塑样品所用的纸卡、不干胶或彩盒一起制作,他们会借助全开的印刷数码打样机能将实际印刷结果反映出来,由深正电业伺服丝杆吸塑机阙龙宇提供,微信号:9。
五、制作生产模具:样品被客户认可后,通常会下一定数量的生产订单。
生产调度会根据产量、吸塑成型的复杂程度决定采用哪种模具量产:采用石膏模生产,模具制作过程类似于吸塑打样,优点在于生产周期短,成本最低,制作一整版(60X110cm)模具只需一到两天时间,不足之处在于吸塑成品表面粗糙,生产中模具容易碎裂,耐用性差无法成型深度大、复杂度高、片材厚的产品。
采用电镀铜模,其工艺是将打好样的泡壳表面喷上一层导电剂,再放入电解槽内镀上厚厚的铜层,电镀过程需要72小时,接着要对铜模进行灌石膏(增加硬度)、抛光、打气眼处理,采用电镀铜模生产的优点是吸塑制品表面光滑,成本适中,耐用性强,缺点是模具制作周期长,无法完成精密吸塑制品的生产。
采用吸塑铝模生产,模具制作需要先采用电脑设计图纸,再采用CNC数控铣床加工,优点是制作周期适中,后期模具处理时间短(钻气眼工作在CNC加工时完成),吸塑产品尺寸精度高,模具耐用性强,缺点是成本高。
由于全自动高速吸塑成型机的成型范围是66X110cm左右,所以不管是石膏模、铜模还是铝模,都需要将单个的模具拼在一起,达到成型尺寸,我们都称这个过程为拼版,需要拼在打好气孔的铝板或木板上,拼好后的整版模具我们称之为底模。
对于吸塑成型深度大的产品,还需要制作上模,在底模将片材真空吸成型的同时,从片材上方施加压力,将片材均匀地拉伸到每一个部位,否则会引起局部厚度过薄。
生产模具的整个制作周期应为5至7天。
六、吸塑成型生产:采用全自动高速吸塑成型机生产,其基本原理是:将成卷的片材拉进电炉烘箱内加热至软化状态,乘热再拉到吸塑模具上方,模具上移并抽真空,将软化的片材吸附到模具表面,同
时将冷却水以雾状喷于成型片材表面,使其硬化,成型的片材再自动被拉至贮料箱,气动裁刀将成型与未成型片材分离,从而完成全部过程。
吸塑产品出现的主要质量问题大多在此过程发生:1.吸塑不到位,是指形状变形,没有吸塑成与模具相同形状的产品;2.吸塑过度,是指产品过薄;3.拉线,是指成型产品上出现不应有的线痕;4.厚薄不均。
这些问题都需要在上好模具后,调试到位,包括:片材前进的时间、加热的温度和时间、抽真空的强度和时间、上模下落的位置、时间和深度、拼版中模具的摆放位置、模具间是否加附件等等。
七、冲床加工:吸塑成型的大版面产品必须经过冲床,用一块刀版分割成为单一的产品。
其原理是在冲床的底台上有一大张塑料砧板,将大版面成型产品放在砧板上,并把事先做好的刀模卡在单一产品上,通过冲床的上下运动,裁断出单一的成品。
八、分检和包装:这是泡壳生产的最后一关,也是把住质量最重要的环节,每一个冲床配备一个包装工,同时也是质检员,对于成型并分切好的泡壳,以目视检验质量,质检的内容主要包括:1.是否按要求成型,2.泡壳上是否有拉线现象,3.泡壳上是否有大的晶点和气泡,4.是否有大的划痕,5.冲出的泡壳边缘是否光滑,没有毛刺.除了质检员外,还配有巡检员,每隔2小时对整个生产过程做一次质量检验,充分保证泡壳的质量合格率。
泡壳生产和包装工艺流程图。