浅谈铝质材料在轻轿车发动机连杆上的应用
轻量级材料在汽车工业中的应用
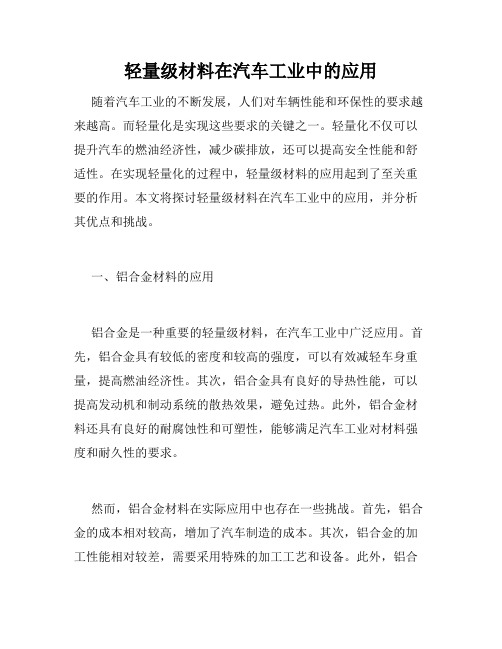
轻量级材料在汽车工业中的应用随着汽车工业的不断发展,人们对车辆性能和环保性的要求越来越高。
而轻量化是实现这些要求的关键之一。
轻量化不仅可以提升汽车的燃油经济性,减少碳排放,还可以提高安全性能和舒适性。
在实现轻量化的过程中,轻量级材料的应用起到了至关重要的作用。
本文将探讨轻量级材料在汽车工业中的应用,并分析其优点和挑战。
一、铝合金材料的应用铝合金是一种重要的轻量级材料,在汽车工业中广泛应用。
首先,铝合金具有较低的密度和较高的强度,可以有效减轻车身重量,提高燃油经济性。
其次,铝合金具有良好的导热性能,可以提高发动机和制动系统的散热效果,避免过热。
此外,铝合金材料还具有良好的耐腐蚀性和可塑性,能够满足汽车工业对材料强度和耐久性的要求。
然而,铝合金材料在实际应用中也存在一些挑战。
首先,铝合金的成本相对较高,增加了汽车制造的成本。
其次,铝合金的加工性能相对较差,需要采用特殊的加工工艺和设备。
此外,铝合金的可靠性和耐久性还需要进一步提升,以满足汽车工业对材料的严格要求。
二、碳纤维复合材料的应用碳纤维复合材料是一种相对较新的轻量级材料,在汽车工业中的应用也越来越广泛。
首先,碳纤维复合材料具有极高的强度和刚性,比钢材重量轻约70%。
采用碳纤维复合材料可以有效降低车身重量,提高燃油经济性和加速性能。
其次,碳纤维复合材料具有优异的耐温性和耐腐蚀性,能够适应各种恶劣环境。
此外,碳纤维复合材料还具有良好的吸能性能,在碰撞事故中可以提供更高的安全保护。
然而,碳纤维复合材料的成本较高,制造和加工过程相对复杂。
目前,大规模应用仍然面临经济和技术挑战。
此外,碳纤维复合材料的可靠性和耐久性还需要进一步研究和改进。
三、镁合金材料的应用镁合金是一种较轻的金属材料,在汽车工业中的应用越来越受到重视。
镁合金具有较低的密度和较高的强度,可以有效减轻车身重量。
与铝合金相比,镁合金还具有更好的加工性能和可塑性。
此外,镁合金具有良好的吸能性能,在碰撞事故中能够减少事故对乘车人员的伤害。
铝镁钛合金材料在汽车发动机中的应用

铝、镁、钛合金材料在汽车发动机中的应用世界铝业协会的报告指出,汽车质量每减少10%,燃油消耗可以降低6%—8%。
由此可见减轻汽车自重是实现汽车节约能源,降低燃油消耗,减少尾气排放的重要措施。
汽车轻量化是当代汽车发展的一个重要课题,其基本要求是:(1)在保证汽车质量和功能不受影响的前提下,最大限度地减轻各零部件的质量,降低燃耗,减少排放污染。
(2)在使汽车减轻质量、降低燃耗、减少排放的同时,努力谋求它的高输出功率、高响应性、低噪声、低振动、良好的操纵性、高可靠性和高舒适性等。
(3)在汽车轻量化的同时,汽车的价格应当下降或保持在合理水平,具有商业竞争能力,即汽车的轻量化技术必须是兼顾质量、性能、价格的技术。
通常占汽车总质量比重较大的部分有发动机、底盘、车身、内外装备等,所占比例如表1所示。
汽车各部分的质量是相互关联的,发动机是汽车的心脏,其质量不容忽视。
如果减轻发动机质量,底盘质量就能相应减轻,而减轻车身零部件的质量,支承它的车架、车桥、车轮、悬架等行走系的负荷就会降低,其质量和尺寸可相应减小,从而使发动机和制动器的质量和尺寸也可相应减小。
但汽车轻量化是具有前提条件的,即在保证汽车整体质量和性能不受影响的前提下,应最大限度地减轻各零部件的质量,努力谋求高输出功率、低噪声、低振动和良好的操纵性、高可靠性等,降低燃油消耗,减少排放污染。
为此,各国的汽车制造厂家为了使发动机轻量化、高速化、高功率化,并且有较高的耐久性,做了大量的工作,大量新材料被应用进来。
1铝合金在汽车发动机上的应用铝是生产汽车的优良材料。
铝代替传统的钢铁制造汽车,可使整车重量减轻30%—40%,研究表明,汽车上每使用1kg铝,便可降低自重2.25kg,减重效应高达125%,同时,在汽车整个使用寿命期内,可减少废气排放20kg。
即用铝的减重和排放效果比为1:2.25:20。
铝回收利用简便,是钢铁以外能最大限度回收利用的材料,几乎90%的汽车用铝可回收并循环使用,在世界环保意识高涨的今天,能高度回收利用的材料和制品日益受到重视。
铝合金在现代汽车轻量化生产中的应用研究

铝合金在现代汽车轻量化生产中的应用研究摘要:伴随着人们经济水平的不断提升以及交通通行的日趋便利性,人们的汽车保有量显著增加,为汽车工业的快速发展提供了重要动力。
同时在科技技术的不断发展中,汽车轻量化生产备受青睐。
因此,文章重点就铝合金在现代汽车轻量化生产中的应用展开分析。
关键词:铝合金;现代汽车;轻量化生产;应用近年来,环境污染引起广泛关注,甚至成为了全球话题。
传统的汽车生产方式以及汽车使用方式乃是导致环境污染的重要因素之一,这显然是有悖于当前的生态环保理念的。
汽车轻量化生产有助于保护环境,并且在国外已经得到实践印证。
目前我国的汽车轻量化生产还处于初步发展阶段,还需要不断提高认识,不断提升轻量化生产水平。
1铝合金的特点铝合金具有耐腐蚀、价格低廉、可回收、易加工、重量轻等优点,其在汽车生产中的使用可以有效地减少能源浪费,已占汽车原料的60%。
在耐腐蚀性方面,铝表面容易产生相应的氧化膜,其强大的耐氧性能有效地降低腐蚀程度,铝合金特别适用于汽车车身不宜采用腐蚀材料,我国目前使用铝作为回收铝材,可以有效地减少能量损失,回收可以有效地减少95%以上的能量损失,符合我国经济和环保的要求。
同时,铝合金在汽车车身生产中的应用可以有效地利用铝挤压技术,从而有效地减少焊缝数量,在一定程度上减少汽车加工工艺,全面提高汽车生产的装配效率。
2汽车轻量化的重要意义2.1降低车辆自重推行轻量化应用代表了轿车的制造将会转变传统的材质,并有更多的车辆制造原料。
轻型轿车的制造必须选用轻质的材质,例如,铝合金是一种轻质的轻质金属,其密度只有2.7g/cm3,应用在现代轿车上可以减轻车辆的重量。
除铝合金外,镁合金和钛合金也是一种重量较低的金属,其具有大约1.74g/cm3至4.51g/cm3的重量。
轻型汽车是目前最流行的、应用最广的一种,在国外,采用轻型材料取得了一些成果,采用了铝合金做车体,可以有效地减轻汽车的自重和车体的部件。
1.2节约油耗和减少排量车辆的油耗和车辆的品质有很大的联系,当车辆的品质达到一定程度后,就会产生大量的燃油,不断地排出废气,造成环境的污染。
简述铝合金、碳纤维复合材料在汽车轻量化上的典型应用,举例说明。

简述铝合金、碳纤维复合材料在汽车轻量化上的典型应用,举例说明概述汽车轻量化是当前汽车工业发展的重要方向之一,通过采用轻量化材料可以减轻车身重量,提高燃油效率,减少尾气排放,增加整车的安全性能和驾驶舒适性。
本文将以铝合金和碳纤维复合材料为例,介绍它们在汽车轻量化领域的典型应用。
铝合金在汽车轻量化的应用铝合金是一种重要的轻量化材料,具有优异的机械性能和热传导性能,广泛应用于汽车制造中。
以下是铝合金在汽车轻量化上的典型应用:车身结构现代汽车的车身结构通常采用多种材料的组合,其中包括铝合金。
铝合金的低密度和高强度使其成为替代钢材的理想选择,可以减轻整车重量并提高燃油效率。
同时,铝合金车身结构具有良好的抗冲击性和扭曲刚度,提高了整车的安全性能。
发动机部件铝合金也广泛应用于汽车发动机的各个部件,如缸体、曲轴箱和散热器等。
铝合金发动机部件具有较低的自重和良好的热传导性能,可有效降低发动机的工作温度,提高动力系统的效率和可靠性。
悬挂系统汽车悬挂系统的组件中常使用铝合金材料,如减震器底座、悬挂臂和转向节等。
与传统的钢材相比,铝合金材料具有更好的强度重量比,可以减轻悬挂系统的重量,提高悬挂系统的响应速度和行驶稳定性。
碳纤维复合材料在汽车轻量化的应用碳纤维复合材料是一种高强度、轻质的材料,由碳纤维与树脂等复合而成。
它具有优良的机械性能、抗腐蚀性和热稳定性,被广泛应用于汽车轻量化领域。
以下是碳纤维复合材料在汽车轻量化上的典型应用:车身组件碳纤维复合材料可以用于制造汽车车身的各个组件,如车顶、车门和车尾等。
由于碳纤维复合材料的高强度和优异的耐磨性,车身组件可以更轻、更坚固,提高整车的燃油效率和行驶稳定性。
刹车系统碳纤维复合材料广泛应用于高性能汽车的刹车系统中,如刹车盘和刹车片。
碳纤维刹车盘具有更好的散热性能和耐高温性能,减少了制动时的热膨胀问题,提高了刹车性能和使用寿命。
轮毂碳纤维复合材料也可以用于制造轮毂,代替传统的铝合金轮毂。
铝型材在汽车上的应用

铝型材在汽车上的应用
铝型材在汽车上的应用非常广泛,主要体现在以下几个方面:
1. 车身结构:铝型材作为轻量化材料的代表,在汽车的车身结构中得到了广泛应用。
通过使用铝型材,可以降低整车重量,提高燃油经济性和驾驶性能。
同时,铝型材具有较好的强度和刚性,能够提供车身所需的结构支撑和抗碰撞保护。
2. 发动机部件:铝型材可以用于汽车发动机部件的制造,例如发动机缸盖、进气歧管等。
铝型材具有良好的导热性能和耐高温性能,可以有效地降低发动机的重量和提高散热效果。
3. 悬挂系统:铝型材可以用于汽车悬挂系统的制造,例如悬挂臂、减震器支架等。
使用铝型材可以减轻悬挂系统的重量,提高悬挂系统的性能和操控稳定性。
4. 内饰装饰:铝型材也可以用于汽车的内饰装饰,例如门把手、中控面板等。
铝型材具有良好的表面处理性能,可以呈现出现代感和高级感,提升车内舒适性和豪华感。
总之,铝型材在汽车上的应用可以带来轻量化、强度高、导热性好等多种优势,符合现代汽车对材料性能的要求,是汽车工业中不可或缺的重要材料之一。
金属铝材料在汽车发动机生产中的应用
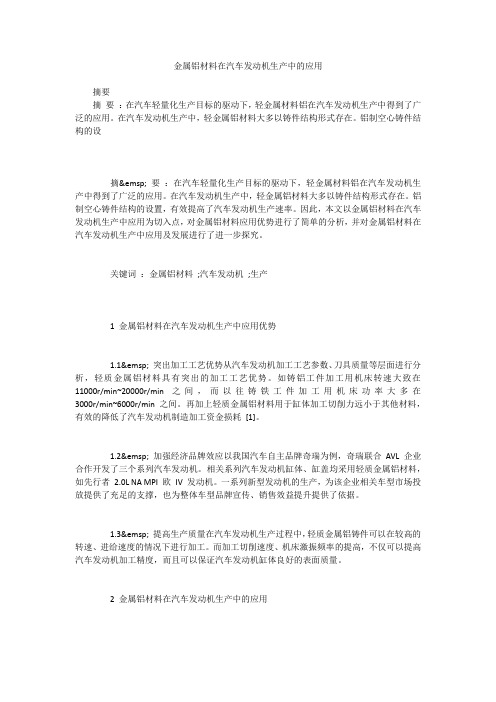
金属铝材料在汽车发动机生产中的应用摘要摘要:在汽车轻量化生产目标的驱动下,轻金属材料铝在汽车发动机生产中得到了广泛的应用。
在汽车发动机生产中,轻金属铝材料大多以铸件结构形式存在。
铝制空心铸件结构的设摘  要:在汽车轻量化生产目标的驱动下,轻金属材料铝在汽车发动机生产中得到了广泛的应用。
在汽车发动机生产中,轻金属铝材料大多以铸件结构形式存在。
铝制空心铸件结构的设置,有效提高了汽车发动机生产速率。
因此,本文以金属铝材料在汽车发动机生产中应用为切入点,对金属铝材料应用优势进行了简单的分析,并对金属铝材料在汽车发动机生产中应用及发展进行了进一步探究。
关键词:金属铝材料;汽车发动机;生产1 金属铝材料在汽车发动机生产中应用优势1.1  突出加工工艺优势从汽车发动机加工工艺参数、刀具质量等层面进行分析,轻质金属铝材料具有突出的加工工艺优势。
如铸铝工件加工用机床转速大致在11000r/min~20000r/min 之间,而以往铸铁工件加工用机床功率大多在3000r/min~6000r/min 之间。
再加上轻质金属铝材料用于缸体加工切削力远小于其他材料,有效的降低了汽车发动机制造加工资金损耗[1]。
1.2  加强经济品牌效应以我国汽车自主品牌奇瑞为例,奇瑞联合AVL 企业合作开发了三个系列汽车发动机。
相关系列汽车发动机缸体、缸盖均采用轻质金属铝材料,如先行者2.0L NA MPI 欧IV 发动机。
一系列新型发动机的生产,为该企业相关车型市场投放提供了充足的支撑,也为整体车型品牌宣传、销售效益提升提供了依据。
1.3  提高生产质量在汽车发动机生产过程中,轻质金属铝铸件可以在较高的转速、进给速度的情况下进行加工。
而加工切削速度、机床激振频率的提高,不仅可以提高汽车发动机加工精度,而且可以保证汽车发动机缸体良好的表面质量。
2 金属铝材料在汽车发动机生产中的应用2.1  轻质金属铝合金材料发动机加工机床选择在轻质金属铝合金材料发动机加工机床选择过程中,需要综合考虑高速加工功能、主动测量功能、断刀检测功能、刀具长度检测功能等因素。
铝合金焊接在汽车轻量化上的应用

铝合金焊接在汽车轻量化上的应用摘要:随着时代的发展和进步,汽车轻量化已经成为发展趋势和方向。
而这其中离不开铝合金复合材料的应用,并通过材料的优化达到更好的应用效果。
基于此,本文就铝合金焊接在汽车轻量化上的应用进行分析,希望可以为汽车轻量化的优化提供借鉴。
关键词:铝合金焊接;汽车轻量化;应用分析一、汽车轻量化的意义随着节能、环保意识逐渐深入人心,汽车生产也朝着绿色化、节能化以及轻量化的方向发展。
汽车轻量化是企业行业发展的必然趋势,符合现代生产的文化价值倾向。
之所以现阶段汽车行业提倡轻量化,是因为各个企业行业察觉到了企业轻量化蕴含着巨大的社会以及经济效益。
汽车轻量化的意义在于以下几个方面:从资源节约、环境保护这个角度来看,汽车轻量化,控制了汽油消耗量,降低了温室气体的排放,减少汽车的使用对于大气环境的污染和破坏,节约了汽油资源;从企业竞争这个角度来看,汽车轻量投资显示了企业长远的投资远见,实现了最大化的经济效益,开辟了汽车行业的营销热点,提升了汽车企业在市场中的核心竞争力;从消费者消费需求来讲,轻量化汽车降低了汽油的消耗,节约了汽车使用成本,支持轻量化汽车的发展,也为节能减排做出了自己的贡献;从社会角度来讲,轻量化汽车实现了更多的运输效益,带动了物流业的发展。
二、汽车轻量化上所使用的铝合金焊接材料1.铸造铝合金铸造铝合金,是最常见的促使汽车轻量化的铝合金焊接材料之一。
铸造铝合金,优势明显,限制较小,因此,可以应用的范围较为广阔。
从汽车发动机、活塞到汽车车轮、零部件,都可以看到铸造铝合金的影子。
但是,即便是使用再广泛,也有不及的范围,就比如在对铸件硬度要求较高的零件中,几乎看不到是以铸造铝合金为原材料的零部件,这也透露出铸造铝合金自身的一个缺陷,耐热性不够。
但是,相关研究人员也在尽量弥补这一缺陷,例如铸造锻造法以及半固态成型法的出现,大大提高了铸造铝合金作为汽车焊接材料的硬度、强度。
2.变形铝合金变形铝合金同样是汽车轻量化上所使用的铝合金焊接材料之一。
铝合金材料在汽车轻量化中的应用分析

铝合⾦材料在汽车轻量化中的应⽤分析铝合⾦材料在汽车轻量化中的应⽤分析2008-04-10 中国汽车⼯业信息⽹1铝合⾦的特点(1)铝作为轻量化⾦属的优势铝的⼒学性能好,其密度只有钢铁的1/3;具有良好的导热性,仅次于铜;机械加⼯性能⽐铁⾼4.5倍,且其表⾯⾃然形成的氧化膜具有良好的耐蚀性;铝的铸造⼯艺性能也⽐较好,可以获得薄壁复杂铸件。
随着铝合⾦技术的发展,铝中添加镁、铬、硅等合⾦元素可获得⾼强度铝合⾦材料。
车⽤普通钢材的强度约为240MPa左右.⾼强度钢为500-700MPa,⽽车⽤铝合⾦的强度现在可以达到500MPa以上,因此铝合⾦的⽐强度(强度/密度)更⾼,在等强度设计条件下,铝合⾦轻得多,可使发动机⽓缸体和⽓缸盖减重30%-40%,全铝车⾝⽐钢车⾝轻40%以上,铝合⾦车轮减重达50%左右。
⽽且,铝合⾦带来的轻量化⼜允许制动器、悬架等零部件减重,即⼆次轻量化,后者轻量化效果⼤概是前者的50%。
美国的⼀项研究报告表明,整备质量为1483.6kg的轿车采⽤铝材料,在保持全部性能的前提下,车⾝质量减重125kg,其次是发动机零部件质量减重54kg,其他总成和零部件减重效果也很明显,如悬架系统减重29kg,传动系减重14.5kg.车轮减重11.8kg.制动系减重10.9kg,燃料系统减重9kg,转向机构减重5kg.排⽓机构减重4kg等,总计减重超过260kg,达到17.5%。
(2)铝吸收冲击的能⼒是钢的2倍。
有⼈称使⽤强度⽐钢铁差的轻质材料⼀定会损害车辆安全性.这是不真实的。
铝材受碰撞后变形模式为前部⼤收缩⽽后部⼏乎不变形,见图1。
由于铝材的吸能性好,在碰撞安全性⽅⾯有明显的优势,汽车前部的变形区在碰撞时会产⽣皱褶,可吸收⼤量的冲击⼒,从⽽保护了后⾯的驾驶员和乘客。
⽽且,由于车⾝质量减轻,可以更快捷地转向或制动,能更好地避免发⽣事故。
即使发⽣碰撞,碰撞时的动能也会减⼩,可相应地降低冲击⼒。
(3)铝易于回收再⽣。
铝合金材料在汽车轻量化中的应用和案例
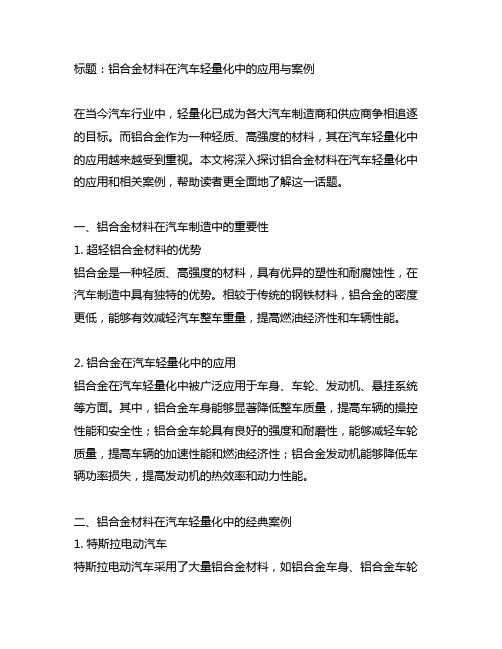
标题:铝合金材料在汽车轻量化中的应用与案例在当今汽车行业中,轻量化已成为各大汽车制造商和供应商争相追逐的目标。
而铝合金作为一种轻质、高强度的材料,其在汽车轻量化中的应用越来越受到重视。
本文将深入探讨铝合金材料在汽车轻量化中的应用和相关案例,帮助读者更全面地了解这一话题。
一、铝合金材料在汽车制造中的重要性1. 超轻铝合金材料的优势铝合金是一种轻质、高强度的材料,具有优异的塑性和耐腐蚀性,在汽车制造中具有独特的优势。
相较于传统的钢铁材料,铝合金的密度更低,能够有效减轻汽车整车重量,提高燃油经济性和车辆性能。
2. 铝合金在汽车轻量化中的应用铝合金在汽车轻量化中被广泛应用于车身、车轮、发动机、悬挂系统等方面。
其中,铝合金车身能够显著降低整车质量,提高车辆的操控性能和安全性;铝合金车轮具有良好的强度和耐磨性,能够减轻车轮质量,提高车辆的加速性能和燃油经济性;铝合金发动机能够降低车辆功率损失,提高发动机的热效率和动力性能。
二、铝合金材料在汽车轻量化中的经典案例1. 特斯拉电动汽车特斯拉电动汽车采用了大量铝合金材料,如铝合金车身、铝合金车轮等,有效实现了车辆轻量化。
特斯拉车辆在加速性能和续航里程方面均表现出色,得益于铝合金材料的应用。
2. 奥迪汽车奥迪汽车在车身和发动机部件中广泛采用铝合金材料,如铝合金车门、铝合金车架、铝合金活塞等,大幅减轻了车辆重量,提升了车辆的燃油经济性和动力性能。
三、个人观点与理解在我看来,铝合金材料在汽车轻量化中的应用具有极大的潜力。
随着汽车工业对节能环保和性能提升的需求不断增加,铝合金作为一种轻质、高强度材料将会在未来得到更广泛的应用。
我认为汽车制造商和供应商在铝合金材料的研发和应用领域还有很大的发展空间,需要不断进行技术革新和创新应用,以满足市场对轻量化汽车的需求。
铝合金材料在汽车轻量化中的应用和案例是一个备受关注的话题,其在汽车制造中的重要性不言而喻。
希望通过本文的内容,读者能够更深入地了解铝合金材料在汽车轻量化中的应用和相关案例,并与我一同探讨这一领域的未来发展方向。
铝合金连接技术在汽车制造中的应用
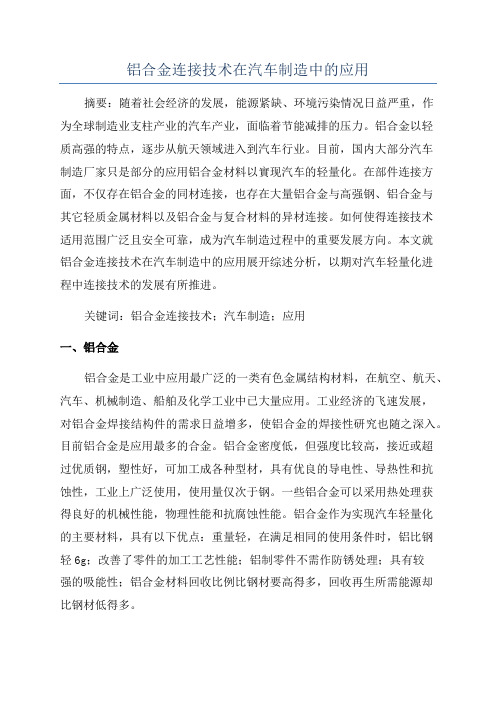
铝合金连接技术在汽车制造中的应用摘要:随着社会经济的发展,能源紧缺、环境污染情况日益严重,作为全球制造业支柱产业的汽车产业,面临着节能减排的压力。
铝合金以轻质高强的特点,逐步从航天领域进入到汽车行业。
目前,国内大部分汽车制造厂家只是部分的应用铝合金材料以實现汽车的轻量化。
在部件连接方面,不仅存在铝合金的同材连接,也存在大量铝合金与高强钢、铝合金与其它轻质金属材料以及铝合金与复合材料的异材连接。
如何使得连接技术适用范围广泛且安全可靠,成为汽车制造过程中的重要发展方向。
本文就铝合金连接技术在汽车制造中的应用展开综述分析,以期对汽车轻量化进程中连接技术的发展有所推进。
关键词:铝合金连接技术;汽车制造;应用一、铝合金铝合金是工业中应用最广泛的一类有色金属结构材料,在航空、航天、汽车、机械制造、船舶及化学工业中已大量应用。
工业经济的飞速发展,对铝合金焊接结构件的需求日益增多,使铝合金的焊接性研究也随之深入。
目前铝合金是应用最多的合金。
铝合金密度低,但强度比较高,接近或超过优质钢,塑性好,可加工成各种型材,具有优良的导电性、导热性和抗蚀性,工业上广泛使用,使用量仅次于钢。
一些铝合金可以采用热处理获得良好的机械性能,物理性能和抗腐蚀性能。
铝合金作为实现汽车轻量化的主要材料,具有以下优点:重量轻,在满足相同的使用条件时,铝比钢轻6g;改善了零件的加工工艺性能;铝制零件不需作防锈处理;具有较强的吸能性;铝合金材料回收比例比钢材要高得多,回收再生所需能源却比钢材低得多。
二、铝合金的应用给汽车制造带来的挑战在应用铝合金减轻车身重量的同时,对汽车焊接技术也带来了挑战。
例如,如车身总成零件普遍采用的MIG/MAG焊将面临以下难题:(1)采用铝合金后,材料厚度比原来的更薄,易出现工件焊穿现象;(2)焊后更易变形;(3)铝合金对热输人更为敏感,易出现焊接裂纹;(4)热影响区母材强度易弱化;(5)钢和铝的异种金属如何连接。
因此,MIG/MAG 焊、点焊、激光焊等作为车身制造的主要焊接工艺,已不能满足铝合金应用的要求,必须要开发更先进的焊接工艺或连接技术,才不会制约汽车轻量化的发展。
铝在汽车上的应用

铝在汽车上的应用随着汽车工业的快速发展,铝材作为一种轻量、高强度的材料,被广泛应用于汽车制造中。
铝的应用不仅在汽车的车身上,还涉及到发动机、悬挂系统、电气系统等各个方面。
本文将从这几个方面介绍铝在汽车上的应用。
一、车身部分铝材在汽车车身上的应用已成为一种趋势。
相比于传统的钢铁材料,铝具有较低的密度和较高的强度,因此可以显著减轻整车重量,提高燃油效率和行驶性能。
此外,铝具有良好的耐腐蚀性,可以有效延长汽车的使用寿命。
二、发动机部分铝材在汽车发动机上的应用主要体现在发动机外壳和散热器上。
铝发动机外壳可以减轻发动机的重量,提高发动机的热效率。
而铝散热器具有较高的导热性能和良好的散热效果,能够有效降低发动机的温度,提高发动机的运行效率。
三、悬挂系统铝合金在汽车悬挂系统中的应用可以提高汽车的操控性能和行驶稳定性。
铝合金制成的悬挂零部件相比于传统的钢铁零部件更轻,可以减轻汽车的非悬挂质量,提高悬挂系统的响应速度和稳定性。
此外,铝合金还具有较好的抗腐蚀性能,能够有效延长悬挂系统的使用寿命。
四、电气系统铝材在汽车电气系统中的应用主要体现在电池外壳和电线材料上。
铝合金制成的电池外壳具有较高的导电性能和较低的电阻,可以提高电池的充放电效率。
而铝制的电线材料具有较低的电阻和较高的导电性能,可以减少电线的能量损失,提高电气系统的效率。
铝在汽车上的应用非常广泛,涉及到车身、发动机、悬挂系统、电气系统等各个方面。
铝材的轻量化、高强度、耐腐蚀性等优势使其成为汽车制造领域不可或缺的材料。
随着科技的不断进步,铝材在汽车领域的应用将会越来越广泛,为汽车工业的可持续发展注入新的动力。
铝合金材料在汽车轻量化中的应用和案例

铝合金材料在汽车轻量化中的应用和案例铝合金材料在汽车轻量化中的应用和案例导语:随着环保意识的不断增强,汽车行业对于减少排放和提高燃油效率的需求也日益迫切。
作为关键材料,铝合金在汽车轻量化领域发挥着重要作用。
本文将以铝合金在汽车轻量化中的应用和案例为主题,从多个角度深入探讨这一问题。
一、背景介绍铝合金是一种具有良好机械性能、低密度和良好耐腐蚀性的材料。
相比于传统的钢材,铝合金具有更轻的重量和更高的比强度,可以有效地降低车身质量并提高汽车整体的燃油效率。
在现代汽车工业中,铝合金已经被广泛应用于车身、引擎和底盘等部件。
二、铝合金在汽车轻量化中的应用1. 车身材料:铝合金的应用可以减轻车身重量,提高车辆的燃油经济性和驾驶性能。
铝合金还具有较好的冲压性能,可以实现更复杂的车身设计,提升整车的外观质量和市场竞争力。
2. 引擎部件:应用铝合金制造引擎部件,如进气歧管、缸盖和缸体等,可以降低整车重量,提高发动机的热传导能力和效率,从而提升汽车的性能和燃油经济性。
3. 底盘和悬挂系统:采用铝合金材料制造底盘和悬挂系统的组件,可以降低车辆的重量、减震效果和操控性能,并提高车辆的驾驶稳定性和舒适性。
三、铝合金在汽车轻量化中的案例分析1. 特斯拉Model S:特斯拉Model S采用铝合金车身,减轻了车身重量,同时提高了车辆的稳定性和行驶里程。
这一设计使得特斯拉Model S成为了全球第一款真正意义上的电动豪华轿车。
2. 奥迪A8:奥迪A8采用全铝车身结构,大幅减少车身重量,提高了悬挂系统的性能和车辆的燃油经济性。
奥迪A8的轻量化设计使得其成为一款既豪华又环保的汽车。
3. 雷克萨斯LFA:雷克萨斯LFA采用碳纤维和铝合金材料制造车身,实现了更轻量化和更高刚性的结构。
这使得LFA成为一款极具激情的超级跑车,同时还保持了高度的安全性和驾驶舒适性。
四、个人观点和理解我认为铝合金材料在汽车轻量化中的应用是一种创新的解决方案,既可以满足环保要求,又可以提高汽车的性能和驾驶体验。
轻质材料铝合金在汽车制造中的应用
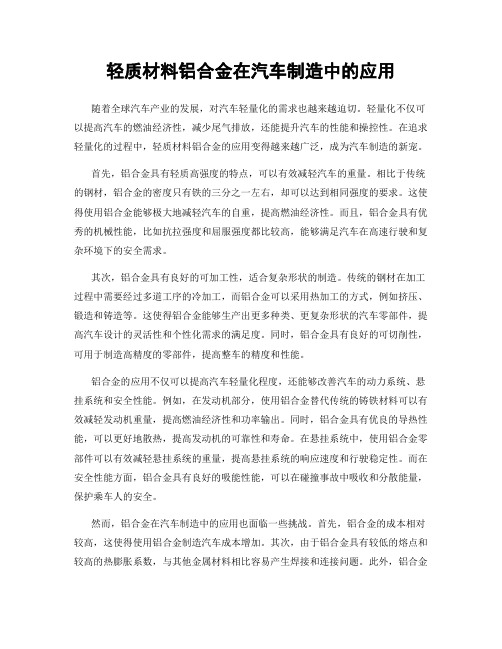
轻质材料铝合金在汽车制造中的应用随着全球汽车产业的发展,对汽车轻量化的需求也越来越迫切。
轻量化不仅可以提高汽车的燃油经济性,减少尾气排放,还能提升汽车的性能和操控性。
在追求轻量化的过程中,轻质材料铝合金的应用变得越来越广泛,成为汽车制造的新宠。
首先,铝合金具有轻质高强度的特点,可以有效减轻汽车的重量。
相比于传统的钢材,铝合金的密度只有铁的三分之一左右,却可以达到相同强度的要求。
这使得使用铝合金能够极大地减轻汽车的自重,提高燃油经济性。
而且,铝合金具有优秀的机械性能,比如抗拉强度和屈服强度都比较高,能够满足汽车在高速行驶和复杂环境下的安全需求。
其次,铝合金具有良好的可加工性,适合复杂形状的制造。
传统的钢材在加工过程中需要经过多道工序的冷加工,而铝合金可以采用热加工的方式,例如挤压、锻造和铸造等。
这使得铝合金能够生产出更多种类、更复杂形状的汽车零部件,提高汽车设计的灵活性和个性化需求的满足度。
同时,铝合金具有良好的可切削性,可用于制造高精度的零部件,提高整车的精度和性能。
铝合金的应用不仅可以提高汽车轻量化程度,还能够改善汽车的动力系统、悬挂系统和安全性能。
例如,在发动机部分,使用铝合金替代传统的铸铁材料可以有效减轻发动机重量,提高燃油经济性和功率输出。
同时,铝合金具有优良的导热性能,可以更好地散热,提高发动机的可靠性和寿命。
在悬挂系统中,使用铝合金零部件可以有效减轻悬挂系统的重量,提高悬挂系统的响应速度和行驶稳定性。
而在安全性能方面,铝合金具有良好的吸能性能,可以在碰撞事故中吸收和分散能量,保护乘车人的安全。
然而,铝合金在汽车制造中的应用也面临一些挑战。
首先,铝合金的成本相对较高,这使得使用铝合金制造汽车成本增加。
其次,由于铝合金具有较低的熔点和较高的热膨胀系数,与其他金属材料相比容易产生焊接和连接问题。
此外,铝合金在高温环境下容易氧化和腐蚀,需要进行防腐蚀处理。
因此,铝合金的使用需要综合考虑成本、性能和可靠性等因素。
铝合金在轻量化车身中的应用及连接技术
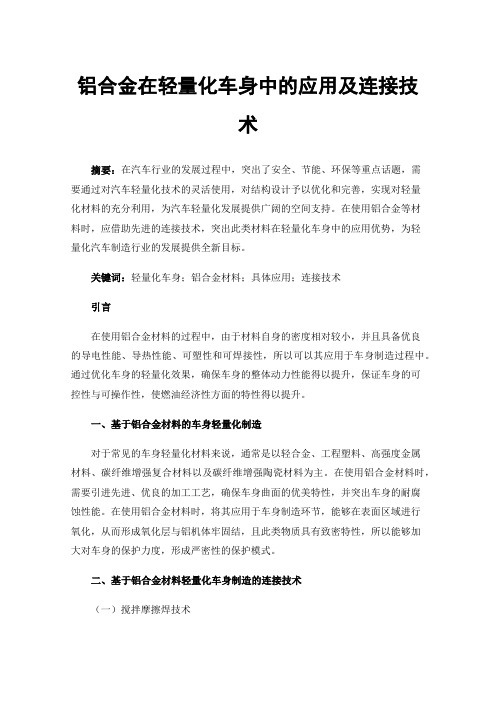
铝合金在轻量化车身中的应用及连接技术摘要:在汽车行业的发展过程中,突出了安全、节能、环保等重点话题,需要通过对汽车轻量化技术的灵活使用,对结构设计予以优化和完善,实现对轻量化材料的充分利用,为汽车轻量化发展提供广阔的空间支持。
在使用铝合金等材料时,应借助先进的连接技术,突出此类材料在轻量化车身中的应用优势,为轻量化汽车制造行业的发展提供全新目标。
关键词:轻量化车身;铝合金材料;具体应用;连接技术引言在使用铝合金材料的过程中,由于材料自身的密度相对较小,并且具备优良的导电性能、导热性能、可塑性和可焊接性,所以可以其应用于车身制造过程中。
通过优化车身的轻量化效果,确保车身的整体动力性能得以提升,保证车身的可控性与可操作性,使燃油经济性方面的特性得以提升。
一、基于铝合金材料的车身轻量化制造对于常见的车身轻量化材料来说,通常是以轻合金、工程塑料、高强度金属材料、碳纤维增强复合材料以及碳纤维增强陶瓷材料为主。
在使用铝合金材料时,需要引进先进、优良的加工工艺,确保车身曲面的优美特性,并突出车身的耐腐蚀性能。
在使用铝合金材料时,将其应用于车身制造环节,能够在表面区域进行氧化,从而形成氧化层与铝机体牢固结,且此类物质具有致密特性,所以能够加大对车身的保护力度,形成严密性的保护模式。
二、基于铝合金材料轻量化车身制造的连接技术(一)搅拌摩擦焊技术在使用搅拌摩擦焊技术的过程中,需要使用铝重金属和钢重金属,将其应用于焊接过程中,突出此类焊接方法的重要作用。
通过设置高效化的搅拌头旋转模式,使其能够与待焊工件之间进行摩擦,从而产生大量的热能,将其作为基本热源,直接应用于焊缝区域的金属处理环节,使金属能够经历热塑性变形、流动、扩散以及在结晶等基本过程,保证冶金结合的牢固性,形成完善的共享连接方法。
通过对搅拌摩擦焊方法予以细致划分,通常还能够将其分为搅拌摩擦点焊与搅拌摩擦焊等两种形式,需要结合铝合金车身轻量化工艺的实施要求,筛选出合适的搅拌摩擦焊操作方法。
铝合金在发动机中的应用
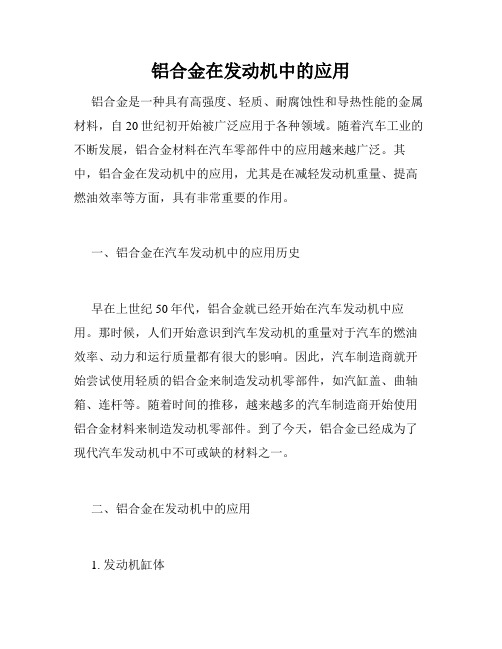
铝合金在发动机中的应用铝合金是一种具有高强度、轻质、耐腐蚀性和导热性能的金属材料,自20世纪初开始被广泛应用于各种领域。
随着汽车工业的不断发展,铝合金材料在汽车零部件中的应用越来越广泛。
其中,铝合金在发动机中的应用,尤其是在减轻发动机重量、提高燃油效率等方面,具有非常重要的作用。
一、铝合金在汽车发动机中的应用历史早在上世纪50年代,铝合金就已经开始在汽车发动机中应用。
那时候,人们开始意识到汽车发动机的重量对于汽车的燃油效率、动力和运行质量都有很大的影响。
因此,汽车制造商就开始尝试使用轻质的铝合金来制造发动机零部件,如汽缸盖、曲轴箱、连杆等。
随着时间的推移,越来越多的汽车制造商开始使用铝合金材料来制造发动机零部件。
到了今天,铝合金已经成为了现代汽车发动机中不可或缺的材料之一。
二、铝合金在发动机中的应用1. 发动机缸体发动机缸体是发动机最重要的部件之一,主要承受气缸压力和温度的影响。
铝合金材料具有高强度、低密度和耐腐蚀性能,非常适合用于制造发动机缸体。
现代汽车发动机中,大部分都采用了铝合金缸体。
这不仅可以减轻发动机的重量,还可以提高发动机的耐久性和动力性能。
2. 发动机缸盖发动机缸盖是发动机缸体的上盖部分,也是发动机中极为复杂的部件之一。
它不仅需要承受气缸压力、高温环境和振动等因素的影响,还需要具备较高的压缩强度和稳定性。
铝合金材料的高强度和耐腐蚀性能使其成为了发动机缸盖的理想材料。
大部分车型的发动机缸盖也采用了铝合金材料,以提高发动机的燃油效率和动力性能。
3. 其他零部件除了缸体和缸盖,铝合金还广泛用于汽车发动机中的其他零部件上,如连杆、曲轴箱、进气道、排气道等。
这些零部件的制造材料不仅需要具有高强度和耐久性,还需要具备较低的质量和耗能成本,这恰恰是铝合金材料所具备的优势。
三、铝合金在发动机中的优势1. 减轻发动机重量铝合金具有低密度和高强度的特点,经过优化设计和工艺处理,相同强度下的铝合金件仅约为同种钢件的1/3重量。
汽车轻量化及铝合金在现代汽车生产中的应用

汽车轻量化及铝合金在现代汽车生产中的应用摘要:汽车属于现今人们生活当中必不可少的交通运输工具,虽然汽车的出现为人们创造了较大的便利性,但是却成为了环境污染与资源消耗的重要源头。
汽车轻量化在一定程度上能够促使汽车排量减少,并且能够节约油耗,铝合金这一材料的应用则能够符合汽车轻量化的要求,对于保护环境、节省资源均能够起到积极的推动作用。
为此,汽车轻量化与铝合金在现代汽车生产中逐渐被重视与应用。
关键词:汽车轻量化;铝合金;汽车生产引言现今时代,我国社会的发展步伐比较快速,人们的生活水平提高较为明显,除了日常的物质要求以外,人们展开了更高质量的生活追求,尤其在汽车这一现代化物流工具方面,人们希望能够在获得便利性的基础上,积极的响应国家节能减排、环境保护等号召。
1汽车轻量化技术实现汽车轻量化的途径主要有以下几个方面:结构优化设计、轻量化材料的应用和先进制造工艺。
1.1 结构优化设计实现轻量化结构优化的主要任务是在满足工艺要求的前提下进行结构形状和尺寸设计,主要包括尺寸优化、形状优化、拓扑优化和多学科设计优化。
1.2 先进制造工艺实现汽车轻量化的先进工艺主要包括液压成型技术和激光焊接技术。
液压成型技术。
20世纪70年代末期,德国率先开始对管材液压成型技术进行基础性研究,并于 20世纪 90年代初率先采用管材液压成型技术制造汽车构件,该技术因1994年的“ULSAB”计划的开展而得到快速发展。
与传统的冲压-焊接工艺相比,液压成型技术可降低11%的零件成本、14%的设备成本、减轻零件7.3%的质量,目前,已有超过50%的汽车底盘装配有液压成型产品。
1.3激光焊接技术该技术是20世纪60年代发展起来的以高能量密度的激光为热源的精密焊接技术。
其应用包括汽车零件的激光焊接、板材的激光焊机、车身激光焊接,激光焊接已成为汽车制造生产中最主要的焊接方法之一。
1.4轻量化材料的应用在轻量化技术中,轻量化材料的开发和应用是当前最主要研究方向。
铝合金汽车轻量化技术

铝合金汽车轻量化技术概述随着环保意识的增强和汽车行业的发展,轻量化成为汽车制造业的重要趋势。
铝合金作为一种轻质、高强度的材料,被广泛应用于汽车制造中,以实现汽车的轻量化。
本文将介绍铝合金汽车轻量化技术的应用、优势和最新发展。
铝合金在汽车制造中的应用铝合金在汽车制造中的应用主要集中在车身和发动机部件上。
车身部件铝合金在车身部件中的应用可以有效地降低车身重量,提高燃油效率和减少尾气排放。
常见的铝合金车身部件包括车门、车顶、引擎盖、车身框架等。
发动机部件铝合金在发动机部件中的应用可以减轻整个发动机系统的重量,提高燃烧效率和散热性能。
铝合金在发动机缸体、缸盖、曲轴箱等部件中的应用已成为现代发动机的主流。
铝合金汽车轻量化的优势铝合金汽车轻量化具有以下优势:轻质高强与传统的钢铁材料相比,铝合金的密度较低,同时具有较高的强度和刚度。
因此,使用铝合金可以在保证结构强度的同时,降低整车的重量,提高燃油经济性。
耐腐蚀铝合金具有良好的抗腐蚀性能,可避免车身和发动机部件由于腐蚀而导致的功能损失和安全隐患。
可塑性铝合金具有良好的可塑性,可以通过模压和挤压等加工工艺实现复杂车身组件的生产。
这有助于降低制造成本,并提高生产效率。
可回收性铝合金可以100%回收再利用,有助于减少资源消耗和环境污染。
铝合金汽车轻量化技术的最新发展为了进一步推动铝合金汽车轻量化,科学家和工程师们在铝合金材料和生产工艺方面不断进行研究和创新。
新型铝合金材料研究人员正在开发新型铝合金材料,以提高其强度和成本效益。
新型材料的研发包括优化合金成分、微观结构设计以及表面处理等方面。
先进的生产工艺为了更好地利用铝合金材料的优势,研究人员正在开发和改进铝合金零件的生产工艺。
这包括改良的铝合金模压工艺、挤压工艺和焊接工艺等。
多材料混合为了在不同部位采用最合适的材料,一些汽车制造商正在开发多材料混合的解决方案。
通过在关键部位使用铝合金,而在其他部位使用其他材料,可以在保证结构强度的同时,进一步降低整车的重量。
铝合金在汽车轻量化中的应用

MANUFACTURING AND PROCESS | 制造与工艺 时代汽车 铝合金在汽车轻量化中的应用王正科四川城市职业学院 四川省成都市 610000摘 要: 铝合金是目前汽车轻量化研发制造应用频率较高的材料,这是因为铝合金的应用能够切实降低汽车自重。
为此,本文首先分析了铝合金在汽车轻量化中的应用优势,其次分析了铝合金在汽车轻量化中的应用技术、分类、方式,旨在为铝合金在汽车轻量化中的应用提供参考,以此来提高汽车轻量化效率和质量。
关键词:铝合金 汽车轻量化 应用技术1 引言汽车是主要交通运输工具,尽管能够给人们的工作及生活提供便利条件,但是也导致了资源消耗和环境污染,而汽车轻量化能够适当降低汽车排量,进而节约汽车消耗资源,减少汽车尾气导致的环境污染。
铝合金属于密度较低的金属材料,其在汽车生产中的应用不但能确保汽车应用性能,还能实现汽车轻量化。
2 铝合金在汽车轻量化中的应用优势2.1 减重效果较为良好据调查结果显示,汽车油耗及尾气排放量与汽车自重有着密切关系,汽车自重每降低1Kg,行驶10000Km的油耗会降低0.7L;汽车自重每降低10%,尾气排放量会降低5-6%,因此,如何实现汽车轻量化已经成为了各大汽车制造企业面临的关键问题[1]。
而铝合金在汽车制造中的应用,便能够达到良好的汽车轻量化效果,具体来讲,铝的密度为2.7g/cm3,为钢铁密度的1/3;铝合金导热性能良好,在金属中仅次于铜;铝合金耐腐蚀性能良好,这是因为其表面能够自动形成一层氧化膜,这些特征使得铝合金成为了汽车制造的主要材料。
2.2 生产材料能够回收利用铝合金属于回收难度较低、回收率较高的金属材料,这是因为铝合金在应用过程中出现腐蚀问题的概率较低。
铝合金材料在制作成产品、使用、回收加工成铝锭、再次制作成产品的循环过程中,损耗率也仅仅为5%,其回收利用价值是所有金属材料中最高的,目前大部分国家应用的汽车制造铝合金为再生铝材料。
此外,铝的熔点较低,流动性能良好,因此能够制作成各种结构复杂、形状不规则的构件,这位汽车制造提供了便利条件,同时也便于铝合金的回收利用。
铝合金等轻金属材料在汽车上的应用
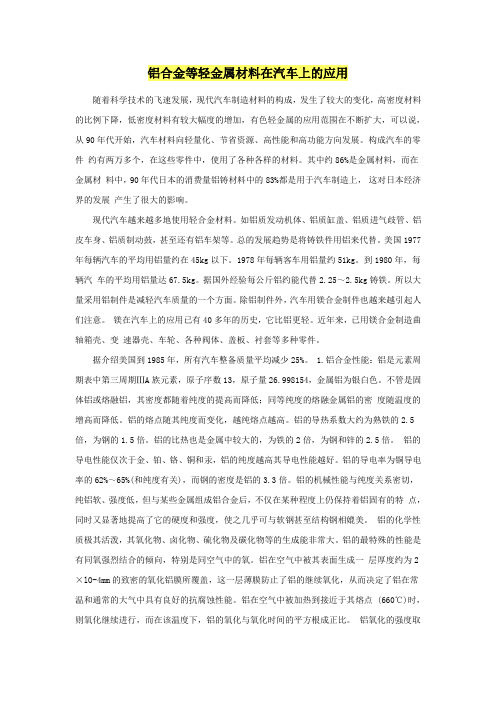
铝合金等轻金属材料在汽车上的应用随着科学技术的飞速发展,现代汽车制造材料的构成,发生了较大的变化,高密度材料的比例下降,低密度材料有较大幅度的增加,有色轻金属的应用范围在不断扩大,可以说,从90年代开始,汽车材料向轻量化、节省资源、高性能和高功能方向发展。
构成汽车的零件约有两万多个,在这些零件中,使用了各种各样的材料。
其中约86%是金属材料,而在金属材料中,90年代日本的消费量铝铸材料中的83%都是用于汽车制造上,这对日本经济界的发展产生了很大的影响。
现代汽车越来越多地使用轻合金材料。
如铝质发动机体、铝质缸盖、铝质进气歧管、铝皮车身、铝质制动鼓,甚至还有铝车架等。
总的发展趋势是将铸铁件用铝来代替。
美国1977 年每辆汽车的平均用铝量约在45kg以下。
1978年每辆客车用铝量约51kg。
到1980年,每辆汽车的平均用铝量达67.5kg。
据国外经验每公斤铝约能代替2.25~2.5kg铸铁。
所以大量采用铝制件是减轻汽车质量的一个方面。
除铝制件外,汽车用镁合金制件也越来越引起人们注意。
镁在汽车上的应用已有40多年的历史,它比铝更轻。
近年来,已用镁合金制造曲轴箱壳、变速器壳、车轮、各种阀体、盖板、衬套等多种零件。
据介绍美国到1985年,所有汽车整备质量平均减少25%。
1.铝合金性能:铝是元素周期表中第三周期ⅢA族元素,原子序数13,原子量26.998154,金属铝为银白色。
不管是固体铝或熔融铝,其密度都随着纯度的提高而降低;同等纯度的熔融金属铝的密度随温度的增高而降低。
铝的熔点随其纯度而变化,越纯熔点越高。
铝的导热系数大约为熟铁的2.5倍,为钢的1.5倍。
铝的比热也是金属中较大的,为铁的2倍,为钢和锌的2.5倍。
铝的导电性能仅次于金、铂、铬、铜和汞,铝的纯度越高其导电性能越好。
铝的导电率为铜导电率的62%~65%(和纯度有关),而钢的密度是铝的3.3倍。
铝的机械性能与纯度关系密切,纯铝软、强度低,但与某些金属组成铝合金后,不仅在某种程度上仍保持着铝固有的特点,同时又显著地提高了它的硬度和强度,使之几乎可与软钢甚至结构钢相媲美。
铝合金在现代汽车轻量化生产中的应用研究
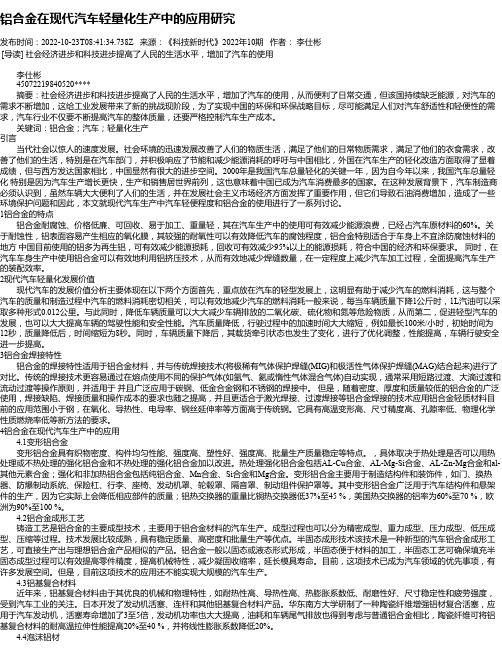
铝合金在现代汽车轻量化生产中的应用研究发布时间:2022-10-23T08:41:34.738Z 来源:《科技新时代》2022年10期作者:李仕彬[导读] 社会经济进步和科技进步提高了人民的生活水平,增加了汽车的使用李仕彬45072219840520****摘要:社会经济进步和科技进步提高了人民的生活水平,增加了汽车的使用,从而便利了日常交通,但该国持续缺乏能源,对汽车的需求不断增加,这给工业发展带来了新的挑战现阶段,为了实现中国的环保和环保战略目标,尽可能满足人们对汽车舒适性和轻便性的需求,汽车行业不仅要不断提高汽车的整体质量,还要严格控制汽车生产成本。
关键词:铝合金;汽车;轻量化生产引言当代社会以惊人的速度发展。
社会环境的迅速发展改善了人们的物质生活,满足了他们的日常物质需求,满足了他们的衣食需求,改善了他们的生活,特别是在汽车部门,并积极响应了节能和减少能源消耗的呼吁与中国相比,外国在汽车生产的轻化改造方面取得了显着成绩,但与西方发达国家相比,中国显然有很大的进步空间。
2000年是我国汽车总量轻化的关键一年,因为自今年以来,我国汽车总量轻化特别是因为汽车生产增长更快,生产和销售居世界前列,这也意味着中国已成为汽车消费最多的国家。
在这种发展背景下,汽车制造商必须认识到,虽然车辆大大便利了人们的生活,并在发展社会主义市场经济方面发挥了重要作用,但它们导致石油消费增加,造成了一些环境保护问题和因此,本文就现代汽车生产中汽车轻便程度和铝合金的使用进行了一系列讨论。
1铝合金的特点铝合金耐腐蚀、价格低廉、可回收、易于加工、重量轻,其在汽车生产中的使用可有效减少能源浪费,已经占汽车原材料的60%。
关于耐蚀性,铝表面容易产生相应的氧化膜,其较强的耐氧性可以有效降低汽车的腐蚀程度,铝合金特别适合于车身上不宜涂防腐蚀材料的地方中国目前使用的铝多为再生铝,可有效减少能源损耗,回收可有效减少95%以上的能源损耗,符合中国的经济和环保要求。
- 1、下载文档前请自行甄别文档内容的完整性,平台不提供额外的编辑、内容补充、找答案等附加服务。
- 2、"仅部分预览"的文档,不可在线预览部分如存在完整性等问题,可反馈申请退款(可完整预览的文档不适用该条件!)。
- 3、如文档侵犯您的权益,请联系客服反馈,我们会尽快为您处理(人工客服工作时间:9:00-18:30)。
14.ON/ram2
硬
度
143HB一149HB
表3不同温度条件下LYl2的疲劳强度数据(m40mm棒材)
试验温度(C)
25
150
疲劳强度(N/ram2)
137
117
试样热处理工艺:495+10 c水冷+25 c×96h,疲劳强度的寿命基数:5×108
。 誊 ≥
、,
馨 R 目
疲劳寿命(N)
图3 LYl2 S—N曲线
24——
表4 几种典型的碳化硅增强铝基复合材料及其基体的拉伸性能数据
基体
增强体含量
(V%)
弹性模量
(103N/ram2)
屈服强度
(N/ram2)
抗拉强度
(N/mm2)
延伸率 (6
7001]16 f
40
40
—
15
()
138 93 69 1 31 107 69
3.2碳化硅增强铝基复合材料 金属基复合材料是以金属或合金为基体,以纤维、晶须或颗粒为增强体的复合材料。由于 这种材料具有强度和弹性模曩高、高温性能好、耐磨性优异等优点,在航空航天、汽车制造等领 域的应用前景十分广阔。目前金属基复台材料发展有铝基、镁基、钛基、铜基等,其中以铝基发 展最快并成为当前金属基复合材料发展和研究工作的主流。金属基复合材料的制备方法有粉 末冶金法、挤压铸造法、喷射沉积法、热压法等,各有其优缺点。以纤维、晶须作为增强体制备的 复合材料虽然具有优异的力学性能,但由于成本高,且材料的制备工艺复杂,限制了它在民用 工业中的发展和应用。而颗粒增强的金属基复合材料因价格相对低廉,具有良好的力学性能、 物理性能和优异的工艺性能,并且具有各向同性的特点,可采用传统的成型工艺进行制备和二 次加工.已为民用工业所接受。颗粒增强金属基复合材料的性能一般取决于增强颗粒的种类、 形状、尺寸和数量,基体金属的种类和性质以及材料的复合工艺等。 颗粒增强金属基复合材料中研究较多、应用最广的是碳化硅颗粒增强铝基复合材料,也是 目前金属基复合材料中最早实现大规模产业化的品种。此种复合材料的密度仅为钢的三分之 ~,与铝合金相近,其比强度与钛合金相近,比铝合金高,比模量略高于钛合金,比铝合金高得 多。此外,碳化硅增强铝基复合材料还具有良好的耐磨性能(与钢相似,比铝台金大1倍),使用 温度最高可达300℃一500C。目前碳化硅颗粒增强铝基复合材料已批量应用于汽车工业和机 械工业中制造大功率柴油发动机的活塞、活塞环以及刹车片等o”u“。 表4给出了几种典型的碳化硅增强铝基复合材料及其基体的拉伸性能数据,与基体合金 相比,碳化硅增强后复合材料的弹性模量和抗拉强度均有所提高,并且随着增强体含量增加, 弹性模量和抗拉强度提高的幅度增加。从拉伸性能上看,颗粒增强的铝基复合材料比常规铝合 金更适用于制造车用发动机连杆。
生产成本。与锻钢连杆相比,铸铁连杆的设计灵活性较大,成品更加接近设计尺寸(其重量偏差 一般在3%~4%)。由于铸铁具有优良的机加工性能,且价格低廉,因而极具竞争力。至1 992 年,美国通用汽车公司已生产了5000多万支铸铁连杆,有11种不同发动机的铸铁连杆实现了 标准化,且汽缸排量小于7I。的发动机均采用铸铁连杆。在欧洲,德国铸造行业每年供应欧洲 汽车制造业需用的铸铁连杆约1000万根以上,其中OPEI。汽车公司是最大的用户之 一:2]-m¨一
较成熟,可靠性高。在现今世界汽车行业每年约2亿多根的连杆产量中约占87%,仍处于绝对
的主导地位“n纠”j。
~21—
20世纪60年代中期,为降低连杆生产成本,珠光体可锻铸铁连杆首先由美国通用汽车公 司应用于汽车发动机,相继有德国的OPEI,汽车公司、VAUXHAI,I。汽车公司等用于轿车发 动机·均成功地取代了部分锻钢连杆。此后又采用球墨铸铁以取代可锻铸铁,并近一步降低了
铸铁连杆成功地取代部分锻钢连杆,极大地激发了人们用粉未冶金锻造法制造发动机连 杆的兴趣。粉末冶金锻造是将常规的粉末冶金工艺与精密锻造工艺相结合而发展起来的一项 颇具竞争力的少、无切削工艺。20世纪70年代中期,德国PORSHE公司率先在其生产的标准 系列汽车上使用粉未锻造连杆,日本丰田汽车公司则于80年代初开始采用,至1992年其产量 已达250万根。美国F()RD公司从1 987年开始大量采用粉末锻造连杆,其1992年的产量为 400万根。德国BMw公司于1991年开始在其新设计的8缸发动机上采用粉锻连杆,当年的 产量即达到65万根。世界各大汽车公司纷纷采用粉锻连杆代替传统的锻钢连杆,与粉锻连杆 优异的使用性能和低廉的生产成本是分不开的。粉锻连杆的重量偏差一般低于0.5%,远小于 锻钢连杆的3%~5%和铸铁连杆的3%~4%,重量为锻钢连杆的80%~90%,生产成本仅为 锻钢连杆的70%左右C5JC6K7 JC83。
工程上用于结构件的比钢铁材料轻的金属材料有铝、镁和钛的舍金及以其为基体的各种 复合材料。仅从比强度和比模量等性能参数看.适用于制作发动机连杆的材料依次是钛、镁、铝 和铁。对于汽车工业而言,价格是制约轻质台金应用的最主要因素。在上述几种轻质合金中, 铝的比价格最低廉,因此也最具有应用前景。
2国内外技术发展概况及趋势
关键词:连杆材料铝
1前言 . 当今世界汽车技术的发展主要是围绕着节约能源、降低公害和提高安全这三大主题,其中
尤以能源问题最为突出,因此,如何制造出经济性更高的车辆是各大汽车商家竞争的主要手 段。影响车辆经济性的因素很多,发动机的性能无疑是最重要的因素之一,为满足车辆经济性 能指标的要求,车用发动机除要求具有高的动力性能,高的燃油经济性、高的工作可靠性和足 够的使用寿命外,还要求具有外形小、重量轻、结构紧凑等特点,即还要求具有高的体积功率和 低的比重量。
连杆是发动机的重要运动件之一,由于运动惯性力的存在,发动机的上述各项性能指标均 受到连杆重量的严重影响。随着连杆重量增加,运动惯性力增加,导致发动机的摩擦损失功率 增加,零部件的机械负荷增大,磨损加快,平衡和振动问题加剧。因此,连杆轻量化对发动机具 有1一分重大的意义。
一般而言,轻量化应从产品设计、制造工艺和材料选用等方面人手。对于车用发动机连杆 而言,要实现大幅度减重,必须彻底改变目前仅限于选用钢铁材料制造车用发动机连杆的现 状,采用比强度和比模量等性能指标更优于钢铁材料的轻质材料。
随着车用发动机向高速化、轻量化方向发展,人们对连杆等运动件提出了更高的轻量化要 求。如今,人们已突破连杆用材仅限于钢铁材料的现状,开始研究采用轻质工程材料制造车用 发动机连杆的新技术。德国一所大学几年前曾采用碳纤维增强工程塑料制造发动机连杆,其重 量仅为锻钢连秆的48%,但价格是锻钢连杆的6.7倍。因生产成本居高不下,这种连杆在汽车 行业大批量应用的前景还十分遥远”]。
的交变载荷,工作温度最高不会超过120U,对于汽油机,其工作温度会更低。因此,对连杆的
基本要求是具有足够的疲劳强度和结构剐度。
分析连杆在实际工作中所承受载荷的特性可知,在某一具体工况条件下,连杆上各截面所
承受的载荷幅值相等且只与气缸内的爆发压力有关,由于连杆本身的质量分布·实际工作中连
杆各截面所承受的平均载荷是不同的,其代数值从大头端到小头端逐渐减小且一般均为负值
受力如表5。该发动机连杆杆部最小截面积实测值约210ram2,则其最大应力幅为84N/ram2。
以减重50%作为设计目标,铝合金的比重仅2.7,而钢铁材料的比重为7.8,则铝连杆的截面
.
颗粒增强铝基复合材料因采用价格低廉的陶瓷颗粒作增强相,是金属基复合材料中价格 唯一为汽车行业所接受的类别。目前采用压力浸渗工艺生产的50%SiC颗粒增强铝基复合材 料已达到弹性模量2×105N/ram2、弯曲强度800N/ram2、弯曲疲劳强度200N/ram2的性能指 标.极具应用前景。
采用常规铝合金生产车用发动机连杆是现今研究的另一方向,人们希望采用这种技术制 造的连杆比锻钢连杆减重50%,价格能够控制在锻钢连杆的】.5倍以内,但由于难以达到 1 50 C时的高温疲劳强度和低膨胀系数要求,目前能够使用的仍是高硅的铝台金材料。但高硅 铝合金材料如采用常规工艺生产,会产生粗大的晶粒,造成其强度和韧性等力学性能下降。现 已研究出将熔融的铝合金熔液进行气雾化,以100K/S以上的快速使之快速冷凝为高硅铝合 金粉未,经粉未热挤压——锻造法制得高硅铝合金材料的新技术。采用这种技术制得的高硅铝 合金,显微组织细小而均匀致密,具有低热膨胀、高耐磨、高强度特性”““““。
~22~
3常规铝合金及以其为基体的颗粒增强铝基复合材料
如前所述,人们已成功地利用碳纤维和不锈钢纤维增强的铝基复合材料制造轿车发动机
连杆,但这种连杆因价格方面的原因距实际应用还十分遥远。为尝试利用价格相对低廉的常规 铝合金或颗粒增强的铝基复合材料制造发动机连杆的可能性,试验测量了目前应用最广泛的 LYl 2的疲劳性能,并收集了一些有关的颗粒增强铝基复合材料的性能数据。 3.1 常规铝合金的疲劳性能试验
试验材料为东北轻合金加工厂生产的巧30mm热挤压棒材,化学成份如表1。试验所用试
样如图1和图2,其热处理工艺为:495+5‘C×0.5h固溶+160 C×6h人工时效。试样加工过
程为:租车、热处理、精车、手工抛光。拉伸试验在济南材料试验机厂生产的WE--300A型液压
式万能材料试验机上进行,疲劳试验在Amsler HFP422型100kN高频疲劳试验机上进行,结
43l 393 276 689 620 ‘627
537 431 310 723 689 675
1.9 5.5 12 1.0 2.5
9
4发动机连杆的使用性能要求
在发动机中,连杆小头与活塞销相连,与活塞一起作往复运动,大头与曲柄销相连,与曲柄
一起作旋转运动。连杆主要承受气缸体内的气体压力以及其自身和活塞组运动惯性力所产生
由于铝具有密度小,强度高的特性,故采用铝基材料制造车用发动机连杆能取到显著的轻 量化效果。日本丰田汽车公司采用体积率为40%的氧化铝长纤维增强铝基复合材料生产发动 机连杆,重量比锻钢连杆减轻了35%。日本本田公司采用不锈钢纤维增强铝基复台材料生产 其轿车发动机连杆,据报道至少已有5万件这种连杆被采用。但这种连杆由于采用了长纤维增 强铝基复合材料,使得其生产成本不为当今的汽车工业所接受o…。