电化学还原技术从废旧锂离子电池中浸出钴酸锂
碳热还原—浸出法回收废旧锂电池中的镍、钴、锰
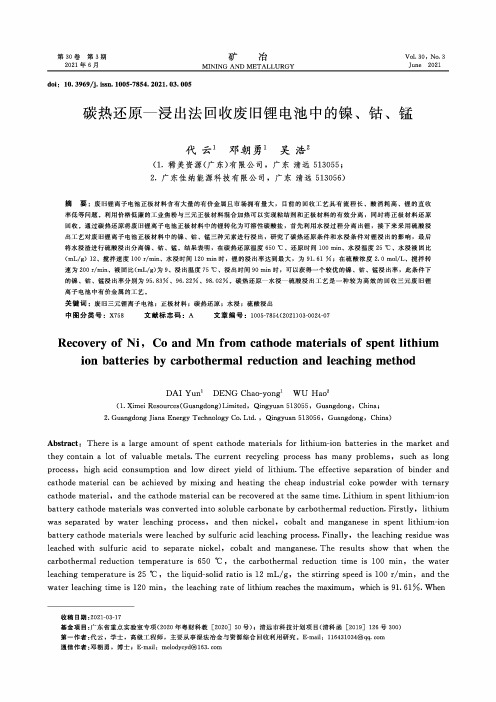
第30卷第3期2021年6月Vol.30,No.3June2021矿冶MINING AND METALLURGYdoi:10.3969/j.issn.1005-7854.2021.03.005碳热还原一浸出法回收废旧锂电池中的镰、钻、猛代云1邓朝勇1吴浩彳(1.稀美资源(广东)有限公司,广东清远513055;2.广东佳纳能源科技有限公司,广东清远513056)摘要:废旧锂离子电池正极材料含有大量的有价金属且市场拥有量大,目前的回收工艺具有流程长、酸消耗高、锂的直收率低等问题。
利用价格低廉的工业焦粉与三元正极材料混合加热可以实现粘结剂和正极材料的有效分离,同时将正极材料还原回收。
通过碳热还原将废旧锂离子电池正极材料中的锂转化为可溶性碳酸盐,首先利用水浸过程分离出锂,接下来采用硫酸浸出工艺对废旧锂离子电池正极材料中的镰、钻、猛三种元素进行浸出,研究了碳热还原条件和水浸条件对锂浸出的影响,最后将水浸渣进行硫酸浸出分离鎳、钻、猛。
结果表明,在碳热还原温度6509、还原时间100min.水浸温度259、水浸液固比(mL/g)12.搅拌速度100r/min.水浸时间120min时,锂的浸出率达到最大,为91.61%;在硫酸浓度2.0mol/L.搅拌转速为200r/min.液固比(mL/g)为9、浸出温度75匸、浸出时间90min时,可以获得一个较优的镰、钻、猛浸出率,此条件下的镰、钻、猛浸出率分别为95.83%、96.22%.9&02%。
碳热还原一水浸一硫酸浸出工艺是一种较为高效的回收三元废旧锂离子电池中有价金属的工艺。
关键词:废旧三元锂离子电池;正极材料;碳热还原;水浸;硫酸浸出中图分类号:X758文献标志码:A文章编号:1005-7854(2021)03-0024-07Recovery of Ni,Co and Mn from cathode materials of spent lithium ion batteries by carbothermal reduction and leaching methodDAI Yun1DENG Chao-yong1WU Hao2(1.Ximei Resources(Guangdong)Limited,Qingyuan513055,Guangdong,China;2.Guangdong Jiana Energy Technology Co.Ltd.,Qingyuan513056,Guangdong,China)Abstract:There is a large amount of spent cathode materials for lithium-ion batteries in the market and they contain a lot of valuable metals・The current recycling process has many problems,such as long process,high acid consumption and low direct yield of lithium・The effective separation of binder and cathode material can be achieved by mixing and heating the cheap industrial coke powder with ternary cathode material,and the cathode material can be recovered at the same time.Lithium in spent lithium-ion battery cathode materials was converted into soluble carbonate by carbothermal reduction.Firstly,lithium was separated by water leaching process,and then nickel,cobalt and manganese in spent lithium-ion battery cathode materials were leached by sulfuric acid leaching process・Finally,the leaching residue was leached with sulfuric acid to separate nickel?cobalt and manganese.The results show that when the carbothermal reduction temperature is650°C,the carbothermal reduction time is100min,the water leaching temperature is25°C,the liquid-solid ratio is12mL/g,the stirring speed is100r/min,and the water leaching time is120min,the leaching rate of lithium reaches the maximum,which is91・61%・When收稿日期:2021-03-17基金项目:广东省重点实验室专项(2020年粤财科教[2020]50号);清远市科技计划项目(清科函[2019]126号300)第一作者:代云,学士,高级工程师,主要从事湿法冶金与资源综合回收利用研究。
废旧锂离子电池正极材料回收工艺研究

废旧锂离子电池正极材料回收工艺研究徐源来;徐盛明;池汝安;王成彦;邱定蕃【摘要】废旧锂离子电池含有大量的钴、铜等紧缺有色金属元素和六氟磷酸锂等有毒有害物质,必须对其进行资源化回收及无害化处理.本文采用"拆解→NMP浸泡正极材料→钴酸锂粉末的浸出→P204萃取除杂→P507萃取分离钴、锂离子"流程处理废旧锂离子电池,获得了合格的氯化钴溶液.该工艺的特点在于:正极片中的铝箔以单质形态回收,而正极材料中97.33%的钴以氯化钴的形式回收,成功地实现了锂离子电池正极材料中有色金属的分离与回收利用.【期刊名称】《武汉工程大学学报》【年(卷),期】2008(030)004【总页数】5页(P46-50)【关键词】废旧锂离子电池;正极材料;回收;钴【作者】徐源来;徐盛明;池汝安;王成彦;邱定蕃【作者单位】武汉工程大学湖北省新型反应器与绿色化学工艺重点实验室,湖北,武汉,430074;清华大学核能与新能源技术研究院,北京,100084;清华大学核能与新能源技术研究院,北京,100084;武汉工程大学湖北省新型反应器与绿色化学工艺重点实验室,湖北,武汉,430074;北京矿冶研究总院,北京,100044;北京矿冶研究总院,北京,100044【正文语种】中文【中图分类】X7050 引言锂离子电池是具有一系列优良性能的绿色电池,问世10多年以来,已被广泛应用于移动电话、笔记本电脑、摄像机、数码相机等民用及军事应用领域.但其寿命大约只有3年左右,随着锂离子电池的广泛应用,已大量进入失效、回收阶段,如何回收废旧锂离子电池和资源化循环利用已成为社会普遍关注的问题.回收处理废旧锂离子电池不仅可以解决废旧电池所带来的一系列环境问题,而且对电池中有色金属进行了回收利用,能有效缓解资源的紧缺.我国是钴资源极为缺乏的国家,一直长期依赖从民主刚果、南非和摩洛哥等非洲国家进口钴精矿等弥补国内缺口.而锂离子电池中钴的质量分数约为15%,远高于钴矿山的可开发品位,且原料相对集中.随着矿产资源这种不可再生资源的耗竭,有色金属今后的重点将转向废弃物中有色金属的回收利用,废旧电池就是其中一个重要来源[1~2].1 实验方法1.1 实验原料及试剂锂离子电池由外壳和内部电芯组成.电池的外壳为不锈钢或镀镍钢壳,有方形和圆柱形等不同的型号.内部电芯为卷式结构,由正极、电解液和负极等主要部分组成,正极片主要由铝箔、有机粘结剂和钴酸锂构成;而负极片主要为铜箔和石墨,负极材料的成分单一、容易分离.由于钴金属价格高,且成分较为复杂,废旧锂离子电池正极材料的回收利用成为人们研究的重点.本文试验采用的废旧锂离子电池正极片是由广东省佛山市南海某公司提供.本试验过程中采用的化学试剂:N-甲基吡咯烷酮(NMP)、硫酸、盐酸、过氧化氢等均为分析纯试剂;萃取剂(P204和 P507)为工业品,而试验过程中使用的水均为去离子水.1.2 实验原理及检测方法在参考国内外文献的基础上[3~9],本研究提出的工艺流程为:拆解废旧锂离子电池→NMP浸泡正极材料→钴酸锂粉末的浸出→P204萃取除杂→P507萃取分离钴、锂离子→(得到)氯化钴溶液.锂离子电池正极材料中有作为集流体的铝箔,而铝离子对萃取剂具有毒性,故预处理中除铝的效果直接影响到后续分离步骤.依据有机溶剂能溶解掉正极材料中的粘结剂,本实验采用有机溶剂(N-甲基吡咯烷酮)浸泡处理正极钴锂膜,使钴酸锂粉末与铝箔分离,在不改变铝箔的金属形态的前提下直接回收得到含铝的废料.得到钴酸锂与石墨黑色的混合粉末经过滤、洗涤、烘干后在硫酸与过氧化氢的体系中浸出,得到用于萃取分离操作的浸出液.浸出过程的化学方程式为:2LiCoO2 + 3H2SO4 + H2O2=2CoSO4+O2↑+Li2SO4+4H2O含钴、锂离子的浸出液先经过萃取剂P204萃取操作除去其中的杂质离子,然后使用萃取剂P507萃取操作分离水相中的钴、锂离子,得到的富钴有机相使用2mol/L的盐酸溶液反萃,可以得到最终产品氯化钴溶液.溶液中金属离子的分析:常量分析采用滴定法,微量分析则采用原子吸收分光光度法(SP-3520AAPC原子吸收分光光度计,上海光谱仪器有限公司);而浸出液成分全分析,则采用ICP-OES电感耦合等离子体-原子发射光谱仪(Optima 5300DV).2 实验结果与讨论2.1 正极材料预处理拆解电池后得到的正极片主要由铝箔、有机粘结剂和钴酸锂构成,预处理的目的是使钴酸锂粉末从铝箔上脱掉.实验中,将剥离开的正极片钴锂膜剪成约2 cm2大小,放入有机溶剂NMP(N-甲基吡咯烷酮)中,在100 ℃下加热并磁力搅拌,约1 h后,钴酸锂和石墨的黑色混合粉末与铝箔能完全脱离,取出铝箔,使用真空抽滤将黑色粉末和有机溶剂分开.在这个过程中,待有机溶剂NMP完全饱和(每100 mL NMP 中约能处理70 g钴锂膜)后可以蒸馏再生重复使用.预处理前的正极材料钴锂膜和分离后得到的铝箔如图1、图2所示.图1 正极材料钴锂膜(预处理前)Fig.1 The positive electrode materials LiCoO2 foils(before pretreatment)图2 NMP预处理后分离出的铝箔(预处理后)Fig.2 The Al foils from NMP treating process (after pretreatment)由图1、2可以看出,钴酸锂粉末能从铝箔上完全脱落,钴酸锂进入有机溶剂NMP,铝箔能以含铝废料形式回收,分离过程中不改变原料的形态也不产生新的污染物,即钴锂能达到分离目的,使用此方法,不仅能使有色金属资源得到了最大的回收利用,同时也大大的减轻了后续萃取步骤中除铝的工作.2.2 酸浸出和P204萃取净化过程2.2.1 钴酸锂的浸出洗涤预处理操作中得到的黑色粉末(包括钴酸锂、石墨和少量的粘结剂),干燥后,将黑色混合粉末投入三口烧瓶,加入硫酸和双氧水,在80 ℃的水浴中搅拌使其发生还原浸出反应,得到待萃取分离的浸出液.LiCoO2电极中使用的是+3价的钴离子,但Co3+不易溶于水,且具有强氧化性.而钴离子在水溶液中一般是以Co2+的形式存在,因此LiCoO2电极中Co的浸出是个还原浸出过程,只有在具备还原条件的体系中才有较好的浸出效果.实验使用的试剂是2.0 mol/L的硫酸、30%的双氧水,将三者在80 ℃的水浴中混合加热.钴和锂的浸出率在10 min内即可达到90%以上,15 min后可达95%以上,90 min后锂和钴可以完全进入酸浸出液.酸浸出后溶液呈紫红色,有少量的不溶渣,渣呈黑色胶状,为正极材料中的粘结剂和碳粉等.得到浸出液成分如表1所示.表1 P204萃取除杂结果Table 1 The results of P204 extract impurity ions质量浓度/mg·L-1CoLiAlFeCuMgCaMnZn浸出液402452130147.511558.48.67.630.15萃余液39196208052.10.58.655.50.800由表1中浸出液的成分分析可以看出,选择双氧水作为还原剂,不会带入任何杂质,且还原效果好,但由于双氧水易分解,故需对滴加速度进行控制.除钴、锂两种金属离子,其他杂质离子的浓度都是微量的,特别是对萃取剂有毒性的铁、铝、离子含量少,这样极大的减轻了后续萃取分离操作的难度.2.2.2 P204萃取净化过程萃取剂P204、萃取剂P507属于酸性萃取剂,其对各种金属阳离子的萃取平衡pH值都不同.根据此特性,实验通过控制水相中不同的pH 值来实现金属离子的萃取分离[10~11].使用萃取剂P204萃取操作除去浸出液中的杂质离子,操作条件为:相比1∶1,萃取平衡pH值为2.6,P204的浓度(体积分数,下同)为25%、皂化率为75%,稀释剂使用磺化煤油,萃取级数两级.由表1可以看出,在此操作条件下,大部分的杂质离子Al3+、Fe3+、Cu2+、Ca2+、Mn2+等都能进入有机相,而Co2+、Li+仍留在水相,净化效果明显.但也可以看到,Mg2+的除去量不足一半,这是因为在湿法冶金中,从溶液中除镁至今仍是一个难题,因此,寻找除镁新方法是值得深入研究的重要课题.2.3 P507萃取分离钴、锂为了水相中钴离子与锂离子分离,采用萃取剂P507进行此分离操作.由课题组的前期试验得知:在pH<5时,钴的萃取率随pH值增大急剧增加;锂在pH<5.5时几乎不发生萃取,pH>5.5时有少部分萃入有机相;pH=5.5时,钴和锂的分离因子βCo/Li可高达1×104.所以,本论文中将钴锂分离的水相pH值固定为5.5[12~13].2.3.1 考查萃取混合时间在室温下,考查萃取混合时间对钴萃取率的影响,如图3所示.萃取剂P507的浓度为25%、稀释剂为磺化煤油、萃取剂的皂化度为75%、水相pH为5.50、相比为1∶1.图3 混合时间对钴萃取率的影响Fig.3 Effect of mixing time on the extracted rate of cobalt由图3可以看出,在振荡器上混匀时间达到25 s后,萃取率趋于平衡.故后续实验的混合时间均选择为30 s,以保证萃取操作的完全平衡.2.3.2 考查相比在室温下,相比与钴离子萃取率的关系如图4所示.萃取剂P507的浓度为25%、稀释剂为磺化煤油、萃取剂的皂化度为75%、水相pH=5.50、相比分别取为0.5∶1、1∶1、1∶2和1∶3.图4 相比对钴萃取率的影响Fig.4 Effect of the ratio of water phase to organic phase on the extracted rate of copper由图4可以看出,随着相比的增大,钴离子的萃取率随之增加.当相比大于1后,两相分层速度明显变慢,但两相的分界仍是清晰的.2.3.3 考查萃取级数使用萃取剂P204净化后的浸出液,用P507进行萃取分离钴锂离子,在pH值为5.5时,锂是不被萃取的,重点考察钴离子的萃取率.在相比为1∶1时,萃取条件为:P507的浓度为25%、稀释剂使用磺化煤油、萃取剂的皂化度为75%,混合时间控制为30 s.表2 P507的萃取结果(相比1∶1)Table 2 The result of P507 extraction (O/A∶ 1/1)萃取级数一级二级三级Co萃取率/%42.6280.4799.94由表2可知,三级萃取操作后,钴离子的萃取率能达到99.94%,基本能将浸出液中的钴离子完全回收,达到工艺预定的目的.在相比为1∶2时,萃取条件为:P507的浓度为25%、稀释剂使用磺化煤油、萃取剂的皂化度为75%,混合时间控制为30 s.得到的结果如表3所示.表3 P507的萃取结果(相比1∶2)Table 3 The result of P507 extraction (O/A∶ 1/2)萃取级数一级二级Co萃取率/%85.8899.63同样,在相比为1∶2的条件下,二级也能达到同样的效果,但由表3中的数据能够看出,在第二级的萃取操作中,有机相未能达到其饱和容量,且分层速度变慢,故选择相比为1∶1更经济合理.2.3.4 考查反萃混合时间在电化学性能方面的应用中,氯化钴是优于硫酸钴的,考虑到产品的应用,采用2 mol/L的盐酸溶液来反萃富钴有机相,得到的产品为氯化钴溶液.图5 混合时间对钴反萃率的影响Fig.5 Effect of mixing time on the stripped rate of copper对于反萃操作,首先考察的是混匀时间,取富钴有机相和盐酸溶液的体积比为1∶1,在室温下考察混合平衡时间.由图5可以看出,在振荡器上混匀时间超过20 s时,反萃就可达平衡.平衡时间短、且速度快,利于操作.2.3.5 考查反萃级数在室温下,取相比为1∶1,混合时间为20 s,得到的实验结果如表4所示.可以看出,一级反萃就可基本反萃出有机相中的钴离子,二级能达到100%.所得到的水相反萃液中钴离子的浓度为13.54 g/L.表4 盐酸反萃的结果Table 4 The result of HCl stripping反萃级数一级二级Co 反萃率/%99.801003 讨论a. 正极材料钴锂膜投入NMP(N-甲基吡咯烷酮)中,在100 ℃下磁力搅拌约1 h后,黑色粉末能从铝箔上脱离,铝箔以金属形态回收,得到钴酸锂和石墨混合粉末;b. 使用硫酸-双氧水体系,钴酸锂混合粉末在80 ℃的水浴中反应约90 min后,钴和锂的金属离子能完全进入浸出液.浸出液主要成分为Co2+和Li+.在水相pH为2.6时,使用萃取剂P204萃取除杂.室温下,萃取剂浓度为25%,皂化度为75%,相比为1∶1时,两级萃取能除去浸出液中大部分的Al3+、Fe3+、Mn2+、Ca2+、Mg2+等杂质离子;c. 使用萃取剂P507可以实现钴锂的较好分离,其最佳操作条件为:室温下,水相pH值为5.5,相比为1∶1,混合时间控制为30 s,三级的萃取率能达到99.94%. 富钴相用2 mol/L的盐酸溶液反萃,两级便能反萃完全,水相中钴离子的浓度为13.54 g/L;d. 通过该工艺,正极材料中钴的回收率为97.33%,铝箔以单质形态回收,达到锂离子电池正极材料中有色金属分离回收的目的.参考文献:[1]徐盛明,刘晓步,徐刚,等.二次电池及其材料循环利用的研究进展[J].中国有色金属学报,2005,15(专刊2):20-24.[2]牛冬杰,马俊伟,赵由才.电子废弃物的处理处置与资源化[M].北京:冶金工业出版社,2007:5-28.[3]申勇峰.从废锂离子电池中回收钴[J].有色金属,2002,54(4):70-71,77.[4]Lee Churl Kyoung,Rhee Kang-In.Reductive leaching of cathodic active materials from lithium ion battery wastes[J].Hydrometallurgy,2003,68(1-3):5-10.[5]钟海云,李荐,柴立元.从废锂离子电池中铝-钴膜碎片中回收钴[J].稀有金属与硬质合金,2001,(1):1-4.[6]王晓峰,孔祥华,赵增营.从从废锂离子电池中回收贵重金属[J].电池,2001,31(1):14-15.[7]童东革,赖琼钰,吉晓洋.废旧锂离子电池正极材料钴酸锂的回收[J].化工学报,2005,(10):1967-1970.[8]温俊杰,李荐.废旧锂离子二次电池回收有价金属工艺研究[J].环境保护,2001,12(6):39-40.[9]Contestabile M,Panero S,Scrosati B.A laboratory-scale lithium-ion battery recycling process[J].Journal of Power Sources,2001,92:65-69.[10]徐光宪,王文清,吴瑾光,等.萃取化学原理[M].上海:上海科学技术出版社,1984:24-27.[11]杨佼庸,刘大星.萃取[M].北京:冶金工业出版社,1988:1-14.[12]Wu Fang,Xu Shengming,Liu Xiaobu,et al.Hydrometallurgical process of waste cathodic materials from lithium ion batteryplants[A].Proceedings of Earth 2005 symposium[C]. Beijing:International Academic Publisher,2005:386-389.[13]吴芳.从废旧锂离子二次电池中回收钴和锂[J].中国有色金属学报,2004,14(4):697-701.。
废旧锂离子电池钴酸锂正极材料回收研究进展

废旧锂离子电池钴酸锂正极材料回收研究进展摘要:随着我国不断出台相关环境保护治理政策,环保压力与日俱增。
相关研究人员愈发重视开发合适的锂离子电池处理技术和电池部件的回收利用技术,特别是针对地壳中储量较低的元素(如Co、Li等元素)。
在近些年对废旧锂离子电池回收的研究方向进行了高度概括,提出3R策略和4H原则,即再设计、再使用、再循环策略和高效、高经济收益、高环境效益、高安全性能原则。
锂离子电池的总造价很大程度取决于正极材料,因此合理、高效地回收废旧电池中的正极材料具有巨大的潜在经济价值。
关键词:锂离子电池;钴酸锂正极材料;回收引言锂离子电池具有体积小、质量轻、使用寿命长、安全性能好等特点,因此广泛用于移动电子设备、医疗设备和新能源设备。
但是,随着锂离子电池使用量的增加,锂离子电池也面临着巨大的再循环压力。
目前,废旧锂离子电池回收行业发展迅速,可以减少资源过度消耗和环境污染等问题,市场发展前景广阔,经济和社会效益也很好。
在这方面,必须加强废旧锂离子电池回收技术的研究和应用。
1废旧钴酸锂回收的主要工艺LiCoO2在锂离子电池市场中占据了非常大的比例。
因此,随着新能源产业的不断发展,LiCoO2的退役量也会随之增加。
同时,考虑到Co是一种稀有元素,具有潜在的经济价值,但处理不当会对环境有不利影响,所以提出一些有效的方法来回收和再生废弃的LiCoO2极为重要。
关于从废旧LiCoO2中再生LiCoO2正极材料的相关研究已经开展了许多。
按照回收结果分为两大类,回收“元素”和回收“材料”。
回收“元素”,即将废旧钴酸锂正极材料通过一系列回收工艺处理后得到的回收产品是含有价金属的离子化合物(如Co3O4、Co O、CoCO3等)。
回收“材料”,即废旧钴酸锂正极材料经回收工艺处理后得到的回收产品是可用于直接装配电池的再生正极材料(如LiCoO2、LiNi x Co y Mn z O2等)。
废旧钴酸锂正极材料回收的主要工艺路线有3种:①湿法冶金工艺,将废旧钴酸锂电池的正极材料进行粉碎并煅烧,然后经过碱浸、酸浸以及萃取等工艺得到有价金属化合物;②火法冶金提取金属元素工艺,主要是在高温熔融状态下通过添加碳还原剂获得有价金属合金,然后结合湿法工艺对其进行分离;③直接再生正极材料工艺,主要是通过添加一定的元素以及包覆材料对混合浆料进行焙烧,在修复废旧正极材料的晶体结构的同时对其进行改性,使得到的再生正极材料满足电池的再次装配要求。
一种废三元锂电池强化还原浸出的方法[发明专利]
![一种废三元锂电池强化还原浸出的方法[发明专利]](https://img.taocdn.com/s3/m/03ff59e6b8f3f90f76c66137ee06eff9aff84962.png)
(19)中华人民共和国国家知识产权局(12)发明专利申请(10)申请公布号 (43)申请公布日 (21)申请号 201710251706.9(22)申请日 2017.04.18(71)申请人 中科过程(北京)科技有限公司地址 100190 北京市海淀区中关村南三街6号五层5328号(72)发明人 王雪 (51)Int.Cl.H01M 10/54(2006.01)(54)发明名称一种废三元锂电池强化还原浸出的方法(57)摘要本发明提供了一种废三元锂电池强化还原浸出的方法,该方法将废旧电池经焙烧分选所得的正极粉料进行强化气体还原,还原过程中采用曝气等方式将还原性气体通入浸出混合液,所产生的气泡与正极粉料发生反应,极大的增加反应速率,得到溶于浸出液的金属离子,曝气还原后进行萃取分离或沉淀分离,得到正极材料前驱体和钴产品;该发明极大地缩短了电池正极材料的还原浸出时间,提高了钴、锰的还原效率,降低了还原剂使用量,避免了还原剂储存和失效的问题,为三元锂电池还原浸出提供了新的回收工艺,具有良好的工业应用前景。
权利要求书1页 说明书3页 附图1页CN 107046154 A 2017.08.15C N 107046154A1.一种废旧三元锂电池强化还原浸出的方法,其特征在于,包括以下步骤:(1)将废电池焙烧分选所得的电池正极材料粉末进行碱法除铝,得到镍钴锰酸锂残渣;(2)步骤(1)所得镍钴锰酸锂残渣球磨得到粉料;(3)步骤(2)所得粉料在酸性浸出液中进行强化气体还原,还原得到镍钴锰离子和锂离子混合液;(4)步骤(3)所得浸出混合液进行萃取分离,过滤得到含有镍和钴的混合酸液;(5)步骤(4)所得含有镍和钴的混合酸液用于制备正极材料前驱体或者钴产品。
2.根据权利要求1所述方法,其特征在于,步骤(1)将废电池焙烧分选所得的含有铝、铁、锂的电池材料粉末进行碱法除铝,得到镍钴锰酸锂残渣;优选的,可通过将废旧电池粉料加入到碱溶液中,溶解铝及铝的氧化物,得到含铁含锂残渣。
萃取法从废旧锂离子电池正极材料浸出液中提取锂

第10卷第1期 2 0 19年2月有色金属科学与工程Nonferrous Metals Science and EngineeringY〇1.10,N〇.1Feb(201;9文章编号%1674-9669(2019)01-0049-05 DOI:10.13264/ki.ysjskx.2019.01.008引文格式:赵天瑜,宋云岭,李永立,等.萃取法从废旧锂离子池正极材料浸出液中提取锂[J].有色金属科学与 工程,2019,10(1):49-53.萃取法从废旧锂离子电池正极材料浸出液中提取锂赵天瑜a,宋云峰a,李永立b,赵中伟a,何利华a,陈星宇a,刘旭恒a(中南大学,a.冶金与环境学院;b.材料科学与工程学院,长沙410083)摘要:废旧锂离子电池正极材料浸出后,溶液中的镍、钴等有价金属十分容易回收,但一直没有很 好的方法来回收锂.实际上,这种浸出液和i j k水都为锂i溶液,所不同的只是i j k水中锂的浓 度往往要低一些,并有大量的氯化钠、氯化镁伴生,因此可将废旧锂离子电池浸出液看做一种特殊的 “盐湖卤水”,并一步调整其Cl-的浓度,进而成功地采用盐湖提锂中常用的萃取法.该方法以磷酸 三丁酯(TBP)为萃取剂,磺化煤油为 ,在三氯化铁(FeC1=)存在的条件下,实现选择性提取锂.TBP与FeC1=-NaC1的酸性溶液接触,锂的专属 '并将浸出液中氯化钠的浓度进一步调整到250 g/L,在相比(!〇/!A)为3,温度为室温条件下萃取5 min,锂的单级萃取率可达到75 K左右,而Ni2+、Co2+、Mn2+几乎没有被萃取.根据平衡等温线,通过4级逆流萃取,锂的萃取率可达到99 K.关键词:锂离子电池;正极材料;浸出液;萃取;锂中图分类号:TF826.3 文献标志码:ARecovery of lithium from leaching solution of anode materials in waste lithium-ion batteries by solvent extraction method ZHAO Tianyua, SONG Yunfenga, LI Yongli7, ZHAO Zhongweia, HE Lihuaa,CHEN Xingyua, LIU Xuhenga(a. School of Metallurgy and Environment; b. School of Materials Science and Engineering,Central South University, Changsha 410083, China)Abstract:After the cathode materials of spent lithium-ion battery have been leached,valuable metals such as nickel and cobalt in solution are easily recycled,but there's been no good way to recycle lithium.In fact,this leaching solution is similar to Salt Lake Brine,the difference is that the concentration of lithium in the Brine is lower,and there is a large amount of sodium chloride,magnesium chloride associated in the Brine.We can treat the leaching solution as a special"Salt Lake Brine",adjusting its chlorine concentration,and then the widely accepted method for extracting lithium from Salt Lake Brine can be successfully applied.With tributyl phosphate(TBP)used as the extractant,sulfonated kerosene as the diluent and ferric chloride(FeCl3)as the co-extractant,lithium is selectively extracted.TBP firstly reacts with the acidic solution of FeCl3-NaCl to form the exclusive extractant for lithium.Then adjust the concentration of NaCl in the leaching solution to more than250 g/L and conduct the extraction experiment for 5 minutes at room temperature with the organic/收稿日期:2018-10-24基金项目:国家自然科学基金资助项目(U1407137) #中南大学博士后基金资助项目(10500-140050020)通信作者:赵中伟(1966-),男,教授,博导,主要从事湿法冶金方面的研究,E-mail'.50有色金属科学与工程2019年2月aqueous volume ratio(0/A)of3.It turns out that the extraction rate of single-stage lithium stands at 75 %, while Ni2+,Co2+and Mn2+are hardly extracted.According to the equilibrium isotherm,extraction rate of lithium can reach 99 %through four-stage countercurrent extraction.Keywords:lithium-ion battery;anode material;leaching solution;extraction;lithium由于锂离子电池具有电压高、比能量大、循环寿 命长、自放电小等一系列的优良性能,已被广泛地应 用于新能源汽车、移动电话、数码相机、笔记本电脑等 诸多领域!1#2%.随着锂离子电池的广泛应用,废旧电池 的量也不断增加!1,3,4].废旧锂离子电池的回收利用不 仅可以减少环境污染,还能从废旧电池中回收有价金 属,从而有效地缓解资源短缺.然而,电池三元材料 中、钴、的整体回收 50 %以,而锂的回收 率还不足1 %15,61.,于锂离子电池材料的回收利用进行了大量的研究工作.废旧锂离子电池一般经过拆解、NMP浸泡正极材料、浸等步骤后,材料浸[7'V浸 中的锂量2~5g/L_,高于湖中锂的含量0.016~2 g/L!11].但是,一直以 有一的从电池浸 中回收锂.随着锂电池 的,锂离子电池价格的不断上升,废旧锂电池中锂的回收越来越受到人们的 .浸出液的主要成分为Li+、Ni2+、Co2+、Mn277,12],而 的Li'Mg'K'Na7113-151.:锂 ,的浸中锂的 :高 离子 离子浓度较低.而盐淑有一定量的 锂,还有大量的、,离子 相 也 高.,由于/锂性质相,中锂的利用困.大量的研究工作,开发了多种选择性提锂的 !151.中TBP一 有效的提锂方法,用T B P作为萃取剂,FeCl'作,作 [13,16,171.过中,大量的Cl"Fe37FeCl(-,进而 Li7结合形成LiFeCl(,而T B P上的P=0与LiFeCl(金属络合 的配位 子通过氢键作用现萃取,有效地离!111.,含锂浸出液也可以看做一种特殊的“盐湖 $.由于一般不含镁,并无镁锂分离之虞..外,由于浸出液中含有相 少甚至 离子,Fe37与Cl-的效应相当微弱,无 充分的LiFeCl(来保证 过程的 .因此,在这种浸 :中,TBP看 无效的.而 一:常廉价的工材料,如果将 加人浸出液中,可以很容易地将氯调节到足够高的浓度,使其与真实的 加相.那么有可能借鉴锂的T B P萃处理.针 一思路,开展了 T B P萃取法从废旧锂离子电池 材料浸 中选择性回收锂的可能性与工艺条件研究.1实验1.1实验原料及分析方法实验用的水相 工合成的模拟锂离子电池正极三元材料LiCNiMCO^M n y O i浸出液,模拟液各离 子浓度如表1所列. 验所用磷酸三丁酯、化学纯,其余试剂均为分析纯.表1模拟液各离子浓度Table 1The concentration of ions insimulated solution离子名称Li7Ni27C o27M n27Cl-浓度/(g.L-1) 3.0008.4568.4917.91630.650实验采用电感耦合等离子光谱生仪检测相Li7、Na7、Fe37、Ni27、Co27、Mn27的含量,并分析水相中水 相各离子量的变,通过差减 计算有机相中各离子含量的变化.1.2实验原理及方法中有FeCl3存在时,以下阳离子被T B P共 萃取的顺序为'H+xL^FM ghNa71181.Li7被共萃的能力强于Na7.为了防止在电池浸出液中引入Fe37杂质,避免对 后续Ni27,Co27,Mn27的提取增加难度,本实验 2个步 :有机相负载Fe37Li7.而 机理可采用以下 [19,20].有机相负载Fe37:Fe3++Cl-!TeCl27⑴Fe3+72Cl-!^FeCl27(2)Fe3773Cl-!FeCl3(3)Fe3++4Cl-;!FeCU-⑷)+FeCl4 (aq)+2TBP((>r g)!N aFeCl4.2TBP(01g)(5)萃取Li 7:2.3相比(!〇/!A)的影响如图3 ,Li +的萃取率随着相比的不断增加而增加.相(!〇/!,) 3时,种上的趋势逐渐缓, 味萃取效率下降.在实际 中,以采相 (F 〇/FA )为3来保证萃取的萃取效率,并过萃取来一步高萃取率.405060708090100T B P 浓度/%注:水相为加入!50 g/L的N a C l 的模拟液;相比(!〇/!,)为3; 温度为30 !;振荡频率为!!0 r/min;振荡时间为10 min.图2 TBP 浓度对锂的萃取率的影响Fig. 2 Effect of TBP concentration on theextraction rate of Li+示,随着T B P 浓度的不断增加,锂的萃取率是不断上 升的,T B P 浓度到100 4时,的萃取率达到最 高.得注的,在整个T B P 浓度范围内 实 验,萃取完后分相过程均在30 e 内完成.纯TBP250 g/L N aC l 溶液的密度分别为0.98 g /cm 3和 1.16 g /cm 3,可见密度相差较分相来说是十分 有利的.50-10100200300丄NaCl 浓度 /(g.L-1)注:有机相为1004负载铁后的T B P ;相比(!〇/!,)为3;温度为30 !;振荡频率为220 r/min;振荡时间为10 min.图1 NaCl 浓度对铁损失率及锂萃取率的影响Fig. 1 Effect of NaCl concentration on the loss rate of F e=+ and the extraction rate of Li+707060Li +(a q )+NaFeCl 4.2TBP (o r g )!L iF e C l 4.2TBP (O T g )+Na +(a q )( 6)在有机相负载Fe 3+的过程中,以氯化钠的形式 向FeCl 3溶液中补充Cl -,以确保Fe 38与Cl -充分络 合,使之完全转化为FeCl <-;为了防止Fe 3+在高pH 条件下发生水解,实验过程中在溶液里加入适量的 盐酸.在从模拟料液里萃取Li 8的过程中,为了防止 低氯浓度条件下有机相的Fe 38损失,在模拟浸出液 中加入一定量的氯化钠来补充Cl -,起到了很好的 效果.以上2个实验过程在分液漏斗中进行,由恒温 水浴振荡器来振荡,使分.2结果和讨论在从模拟料液中萃取锂之前,通过T B P 负载Fe 38来制备了锂的专属萃取N aFeClr 2TBP ,通过实验,获得了有机相负载Fe 38的较优实验条件:水相 分为 FeCl3 0.4 mol /L ,NaCl 4.5 mol /L ,HCl 0.1 mol /L ; 有机相为100 4 TBP ;相比(F 0/!a )为1.2;温度为 30 !;振荡频率为220 r /min ;振荡时间为5 min .在 此条件下,铁的 萃取率高 99 4以上.过使以上实验备的专属萃取剂,并依此进行了萃取的.2.1水相中氯化钠浓度的影响图1显示了 N aC l 浓度对Li 8萃取率和对有机相中Fe 38损失率的影响.上 得的专属萃取萃取模拟浸液时,Li 8的萃取率相较低, 有量Fe 38从有机相 到水相中. 化程式(1)〜式(6),氯 浓度高时,化向 .此,适的Cl -浓度防止有机相中Fe 38损失 高Li 8萃取率的 .过实验发现,加的NaCl,有机相中Fe 38损失率 ,时Li 8的萃取率 高.1, NaCl 浓度 到 200 g/L 时, N aC l 浓度的一高,条有的化,到了较优条件,下仍有量的Fe 38从有机相 到溶液中,对后 Ni 28、Co 28、Mn 28的取,此需要实验条件来进一防止有机相中Fe 38的.当继续把溶液中N aC l 浓度调整到250 g /L 时,可以发有机相中的铁不再损失.2.2有机相中T B P 浓度的影响为 了 解 有 机 相 中 TBP 浓 度 萃 取 率 的响, 化与负载铁后的TBP的充分合后来萃取实验,结果2 f第10卷第1期 赵天瑜,等:卒取法从废旧裡离子电池正极材料浸出液中提取裡51%/讲铥擗%/讲张喝t 'ioooo4 3 2 15o66%/讲赵齡一5552有色金属科学与工程2019年2月30Fig. 3123 45才目比$〇/$A注:水相为加人250 g/L的N a C l 的模拟液;有机相为 萃铁后的100 , T B P ;温度为30 !;振荡频率为220 r/min;振荡时间为10 min.图3相比(!〇/!$)对锂的萃取率的影响Effect of organic/aqueous volume ratio (V 〇/VA)on the extraction rate of Li+2.4温度的影响图6所示的实验结果表明,温度越高的萃取率越低.由参考文献[2 +,22]可知,该萃取过程是放热 反应,低温条件下有利于的萃取.为了保证萃取率 的同时更加节能环保,室温为合理的萃取条件.0 12 3[Li]A/(g*L-1)图5萃取平衡等温线Fig. 5 Extraction equilibrium isotherm3结论1) 由于锂离子电池正极材料浸出液和盐湖齒水实为 液,可 离子电出液的“ 水”,并液中离浓度,应用 中常用的萃取.(TBP )为萃取,铁(FeCl 3)为萃剂,取.2) T BP FeCl 3-N a C l 的酸性溶液接触,形成锂的专属萃取. 出液中的浓度 ^250 g/L ,在相比(F 〇/F a )为3,温度为室温条 件下萃取,的单级萃取率可75%而Ni 2+、C 〇2+、Mn 2+有萃取.由式(8)〜式(10)可得,Li +/Ni 2+、Li +/C 〇2+、Li +/Mn 2+的分离系数分别为:S "L i /N i =3038、S "L i /C >=151.9、S "L i /M n = 75.95.A B# o r g y c r g ^# a q F a q(7)!"L i /N i BA L i /A N i(8)!"L i /C o B A N i /A C o(9)!"L i /M n BA L i /A M n (10)其中A 代表分配比,S "代表分离系数,C >r g 代 表有机相中的浓度,$>rg 代表有机相体积、#aq 代表水相 中的浓度,F aq 代表相体积.所,该体系于Li <有很好的选择性.2.6萃取平衡等温线和理论萃取级数同相比(F 〇/F a )条件得出的两相平衡数据,得出相比为3时的等温 线,如图5所示.由 图5可见,在相比(F 〇/F a )为3时米用4级逆流萃取, 萃取率可99 %.203040 5060温度/#C注:水相为加入250 g/L的N a C l 的模拟液;有机相为 萃铁后的100 % T B P ;相比(F 〇/F a )为3;振荡频率为220 r/min;振荡时间为10 min图4温度对锂萃取率的影响Fig. 4 Effect of temperature on theextraction rate of Li+2.5萃取体系对于锂的选择性在较优实验条件下,Li<的萃取率为75.24 %,而Ni2+、Co2+、Mn2+的萃取率分别为 0.10 %。
一种从废弃钴酸锂电池中浸出钴和锂的方法
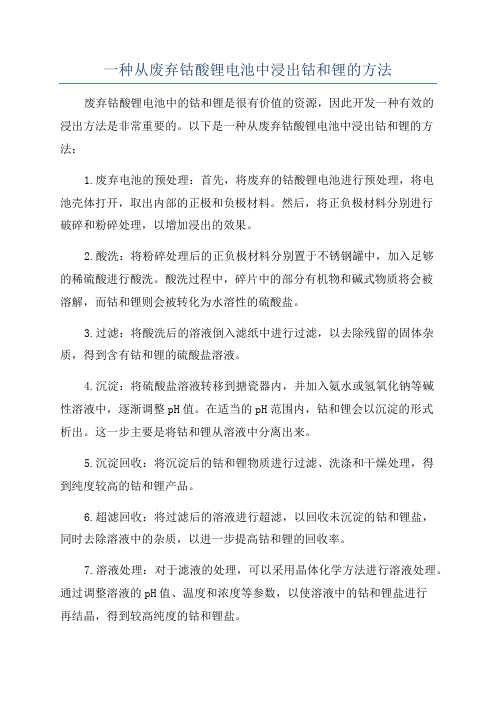
一种从废弃钴酸锂电池中浸出钴和锂的方法废弃钴酸锂电池中的钴和锂是很有价值的资源,因此开发一种有效的浸出方法是非常重要的。
以下是一种从废弃钴酸锂电池中浸出钴和锂的方法:1.废弃电池的预处理:首先,将废弃的钴酸锂电池进行预处理,将电池壳体打开,取出内部的正极和负极材料。
然后,将正负极材料分别进行破碎和粉碎处理,以增加浸出的效果。
2.酸洗:将粉碎处理后的正负极材料分别置于不锈钢罐中,加入足够的稀硫酸进行酸洗。
酸洗过程中,碎片中的部分有机物和碱式物质将会被溶解,而钴和锂则会被转化为水溶性的硫酸盐。
3.过滤:将酸洗后的溶液倒入滤纸中进行过滤,以去除残留的固体杂质,得到含有钴和锂的硫酸盐溶液。
4.沉淀:将硫酸盐溶液转移到搪瓷器内,并加入氨水或氢氧化钠等碱性溶液中,逐渐调整pH值。
在适当的pH范围内,钴和锂会以沉淀的形式析出。
这一步主要是将钴和锂从溶液中分离出来。
5.沉淀回收:将沉淀后的钴和锂物质进行过滤、洗涤和干燥处理,得到纯度较高的钴和锂产品。
6.超滤回收:将过滤后的溶液进行超滤,以回收未沉淀的钴和锂盐,同时去除溶液中的杂质,以进一步提高钴和锂的回收率。
7.溶液处理:对于滤液的处理,可以采用晶体化学方法进行溶液处理。
通过调整溶液的pH值、温度和浓度等参数,以使溶液中的钴和锂盐进行再结晶,得到较高纯度的钴和锂盐。
总之,该方法综合利用了化学反应和物理分离技术,可以实现废弃钴酸锂电池中钴和锂的高效浸出和回收。
同时,该方法在材料处理和溶液处理等方面也将对环境造成较小的影响。
然而,该方法仍然需要进一步的实验研究和工程化实施,以提高钴和锂的回收率和纯度,并优化工艺条件,减少废水和废气的排放。
回收废旧锂离子电池中金属材料的电化学方法
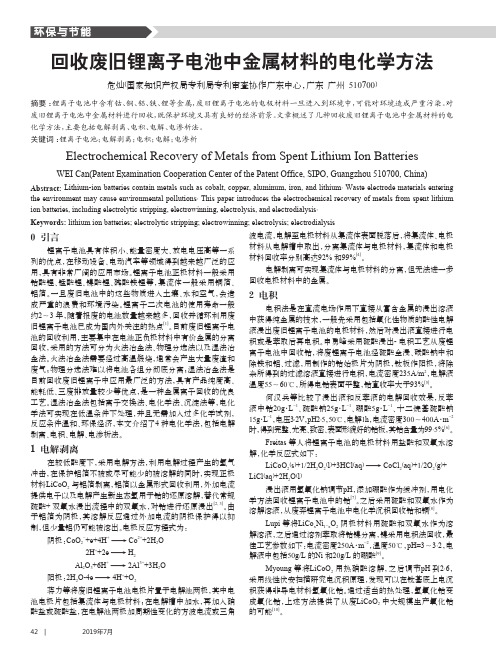
环保与节能42 |2019年7月波电流,电解至电极材料从集流体表面脱落后,将集流体、电极材料从电解槽中取出,分离集流体与电极材料,集流体和电极材料回收率分别高达92%和99%[4]。
电解剥离可实现集流体与电极材料的分离,但无法进一步回收电极材料中的金属。
2 电积电积法是在直流电场作用下直接从富含金属的浸出溶液中获得纯金属的技术,一般先采用包括氧化性物质的酸性电解液浸出废旧锂离子电池的电极材料,然后对浸出液直接进行电积或是萃取后再电积。
申勇峰采用硫酸浸出-电积工艺从废锂离子电池中回收钴,将废锂离子电池经硫酸全浸、碳酸钠中和除铁和铝、过滤,用制作的钴始极片为阴极,钛板作阳极,将除杂所得到的过滤溶液直接进行电积,电流密度235A/m 2,电解液温度55~60℃,所得电钴表面平整,钴直收率大于93%[5]。
何汉兵等比较了浸出液和反萃液的电解回收效果,反萃液中钴20g ·L -1、硫酸钠25g ·L -1、硼酸5g ·L -1、十二烷基硫酸钠15g ·L -1,电压3.2V ,pH2.5,50℃,电解1h ,电流密度300~400A ·m -2时,得到完整、光亮、致密、表面形貌好的钴板,其钴含量为99.5%[6]。
Freitas 等人将锂离子电池的电极材料用盐酸和双氧水溶解,化学反应式如下:LiCoO 2(s)+1/2H 2O 2(l)+3HCl(aq)→CoCl 2(aq)+1/2O 2(g)+LiCl(aq)+2H 2O(l)浸出液用氢氧化钠调节pH ,添加硼酸作为缓冲剂,用电化学方法回收锂离子电池中的钴[7]。
之后采用硫酸和双氧水作为溶解溶液,从废弃锂离子电池中电化学沉积回收钴和铜[8]。
Lupi 等将LiCo x Ni 1-x O 2阴极材料用硫酸和双氧水作为溶解溶液,之后通过溶剂萃取将钴镍分离,镍采用电积法回收,最佳工艺参数如下:电流密度250A ·m -2,温度50℃,pH=3~3.2,电解液中包括50g/L 的Ni 和20g/L 的硼酸[9]。
酸浸—萃取—沉淀法回收废锂离子电池中的钴

酸浸—萃取—沉淀法回收废锂离子电池中的钴张新乐;徐金球;张晓琳【摘要】采用酸浸—萃取—沉淀法回收废锂离子电池中的钴.实验结果表明:废锂离子电池在600℃下煅烧5h可将正极材料上的有机黏结剂与正极活性物质分离;正极活性物质在NaOH溶液浓度为2.0 mol/L、n(NaOH)∶n(铝)=2.5、碱浸温度为20℃的条件下碱浸反应1h后,铝浸出率达99.7%;已除铝的正极活性物质在硫酸浓度为2.5 mol/L、H2O2质量浓度为7.25 g/L、液固比为10、酸浸温度为85℃的条件下酸浸反应120min,钴浸出率高达98.0%;酸浸液在pH为3.5、萃取剂P507与Cyanex272体积比为1∶1的条件下,经2级萃取,钴萃取率为95.5%;采用H2SO4溶液反萃后在硫化钠质量浓度为8 g/L、反萃液pH为4的条件下沉淀反应10 min,钴沉淀率达99.9%.【期刊名称】《化工环保》【年(卷),期】2016(036)003【总页数】6页(P326-331)【关键词】酸浸;萃取;沉淀;废锂离子电池;钴【作者】张新乐;徐金球;张晓琳【作者单位】上海第二工业大学环境与材料工程学院,上海201209;上海第二工业大学环境与材料工程学院,上海201209;上海第二工业大学环境与材料工程学院,上海201209【正文语种】中文【中图分类】X705锂离子电池具有较高的工作电压和能量密度,自放电率低,无记忆效应,被广泛应用于移动电子设备[1]。
我国是锂离子电池的消费和出口大国,但对锂离子电池的回收率较低[2],大量废锂离子电池处于被暂存或遗弃的状态,不仅浪费资源,也对环境造成污染。
锂离子电池中含镍5%~10% (w)、锂5%~7%(w)、钴5%~20%(w)[3-4]。
锂离子电池主要由正极、电解液和负极组成,其中正极主要由LiCoO2活性物质、炭黑、铝箔集流体和黏结剂组成。
回收废锂离子电池就是对其正极物质进行回收[5-6]。
生物浸出法回收废旧锂离子电池中有价金属的方法

生物浸出法回收废旧锂离子电池中有价金属的方法随着电子技术的不断发展,电子产品的更新换代速度也越来越快,电子废弃物的日益增多已经成为了一个全球性问题。
其中,废旧锂离子电池是其中的一种重要废弃物。
废旧锂离子电池中含有大量的有价金属元素,如钴、镍、锂等,其回收利用具有重要的经济意义和环保意义。
生物浸出法是一种有效的废旧锂离子电池中有价金属回收利用的方法。
本文将就生物浸出法回收废旧锂离子电池中有价金属的方法进行探讨。
废旧锂离子电池中含有大量的有价金属元素,如钴、镍、锂等,这些元素不仅具有重要的工业价值,还具有重要的经济意义和环保意义。
(一)钴钴是锂离子电池中最昂贵的金属,其含量约占电池重量的10%~20%。
钴具有高延展性、高强度和高耐腐蚀性等特性,具有广泛的应用价值,如用于制造合金、切削工具、军工材料和电池材料等。
(二)镍(三)锂锂是锂离子电池中最重要和最基本的金属元素,其含量约占电池重量的1%~2%。
锂具有轻质、高放电密度和长循环寿命等特性,广泛应用于制造移动电源、电动汽车和电子设备等。
二、生物浸出法的原理(一)生物浸出法的定义生物浸出法是利用微生物或其代谢产物作用于矿石或矿渣,将其中的金属元素浸出于浸出液中,从而实现金属元素的回收。
生物浸出法的原理基于微生物对矿物中金属元素的化学活性。
微生物通过酶的作用,将矿物中的金属元素转化成可溶性的金属离子,并以此作为生长和代谢所需的营养物质。
在生物浸出过程中,微生物和金属离子之间的相互作用是决定浸出效率和浸出速率的重要因素。
生物浸出法已经被广泛应用于矿物处理、冶金工业和环境污染治理等领域。
随着废旧锂离子电池的日益增多,生物浸出法逐渐成为了一种重要的废旧锂离子电池中有价金属的回收方法。
生物浸出法具有浸出效率高、操作简单、环保节能等优点。
与传统的化学浸出法相比,生物浸出法不需要使用强酸和高温,能够减少废弃物的产生和化学物质对环境的影响。
生物浸出法的效果和其所用的浸出菌密切相关。
高温烧结法回收废弃锂离子电池中的钴酸锂
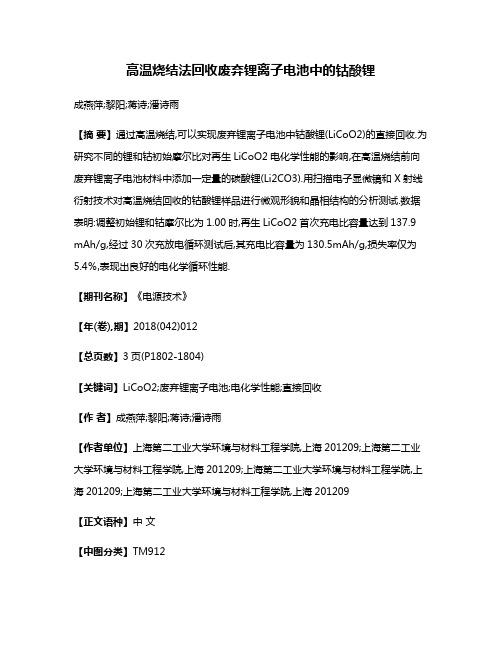
高温烧结法回收废弃锂离子电池中的钴酸锂成燕萍;黎阳;蒋诗;潘诗雨【摘要】通过高温烧结,可以实现废弃锂离子电池中钴酸锂(LiCoO2)的直接回收.为研究不同的锂和钴初始摩尔比对再生LiCoO2电化学性能的影响,在高温烧结前向废弃锂离子电池材料中添加一定量的碳酸锂(Li2CO3).用扫描电子显微镜和X射线衍射技术对高温烧结回收的钴酸锂样品进行微观形貌和晶相结构的分析测试.数据表明:调整初始锂和钴摩尔比为1.00时,再生LiCoO2首次充电比容量达到137.9 mAh/g,经过30次充放电循环测试后,其充电比容量为130.5mAh/g,损失率仅为5.4%,表现出良好的电化学循环性能.【期刊名称】《电源技术》【年(卷),期】2018(042)012【总页数】3页(P1802-1804)【关键词】LiCoO2;废弃锂离子电池;电化学性能;直接回收【作者】成燕萍;黎阳;蒋诗;潘诗雨【作者单位】上海第二工业大学环境与材料工程学院,上海201209;上海第二工业大学环境与材料工程学院,上海201209;上海第二工业大学环境与材料工程学院,上海201209;上海第二工业大学环境与材料工程学院,上海201209【正文语种】中文【中图分类】TM912锂离子电池由于其能量密度高、循环寿命长和无记忆效应等优点,广泛应用于手机、笔记本电脑和数码相机等便携设备中。
随着信息技术的发展,电子设备更新换代速度越来越快,锂离子电池用量日趋增加。
锂离子电池的寿命期过后,会产生大量的废弃锂离子电池。
锂离子电池行业的迅猛发展导致对钴的需求也急剧攀升,但是钴资源稀缺,废弃电池中的钴对环境有一定的潜在危害。
当今提倡可持续发展的理念,废弃锂离子电池中钴的回收再利用显得尤为重要。
国内外学者已经开展了锂离子电池中钴的回收技术研究,回收技术包括火法、湿法和生物法。
其中,火法[1]就是通过热处理的方式来回收电极材料;湿法包括溶解-沉淀[2]、溶剂萃取[3]和电化学[4]等方法;生物法[5]是利用一些能够氧化分解矿物晶格的微生物,将矿物晶格破坏,使其中的有价金属元素释放出来,然后予以富集。
- 1、下载文档前请自行甄别文档内容的完整性,平台不提供额外的编辑、内容补充、找答案等附加服务。
- 2、"仅部分预览"的文档,不可在线预览部分如存在完整性等问题,可反馈申请退款(可完整预览的文档不适用该条件!)。
- 3、如文档侵犯您的权益,请联系客服反馈,我们会尽快为您处理(人工客服工作时间:9:00-18:30)。
电化学还原技术从废旧锂离子电池中浸出钴酸锂基于电化学还原技术,提出在低酸度溶液中电解浸出废旧锂离子电池正极片(LiCoO2)的新方法。
线性伏安扫描结果表明:LiCoO2 的还原峰电位为0.30 V(vs SC E),验证了此方法的可行性。
通过条件实验对影响钴和铝浸出率的各因素进行考察得到电解浸出的最佳条件电流密度15.6 mA/cm 2 、硫酸浓度40 g/L、柠檬酸浓度36 g/L、温度45 ℃、时间120 min。
在此优化条件下,钴和铝的浸出率分别为90.8%和7.9%。
电解浸出后,可直接回收铝箔,用扫描电子显微镜(SEM)对铝箔表面进行观察,结果表明:铝箔在浸出过程中的腐蚀深度远小于其表面原有点蚀坑的深度前,环境和资源问题日益突出,而大量废弃的锂离子电池对环境和资源所产生的力均不可估量。
如何高效低能耗地回收废旧电池中的有价金属成为面临的重要课题。
目前已经有较多文献对废旧锂离子电池的回收进行报道,但未充分考虑工艺技术与生产成本之间的矛盾平衡,导致工业化进程长期停滞不前。
对废旧锂离子电池进行回收,其关键在于正极片的处理工艺。
铝箔与正极粉用粘接剂牢牢粘结在一起,常规剥离十分困难,其典型分离工艺为直接酸浸和碱煮−酸浸工艺,但其浸出液中成分复杂、净化过程压力较大,且回收的氢氧化铝价值偏低。
后来用有机溶剂溶解分离活性物质和集流体的方法可以回收完整的铝箔,但有机溶剂成本高、毒性大,且存在有机溶剂的循环利用问题。
所以,低成本处理正极片LiCoO2 兼顾回收铝箔成为技术难题之一。
另一方面,在湿法回收工艺中,浸出过程是整个工艺流程的核心,大多以酸浸为主,而H2SO4−H2O2 法在浸出体系中长期占据重要位置。
高浓度强酸作为浸出剂,且加入H2O2 等还原剂,从价格而言不具有优势。
为此,本文作者利用电化学还原法,直接以钴酸锂极片为电解池阴极,在低酸度溶液体系中,一步完成LiCoO2 的选择性浸出以及正极粉与铝箔的分离。
由外加电源提供电子,不仅可取代双氧水,而且可对铝箔施以阴极保护,使其剥离后以单质的形式回收。
该工艺流程简单可控性强,且能有效避免引起二次污染,是一种绿色环保工艺。
1 实验1.1 实验材料及试剂实验所用废旧锂离子电池来自湖南某回收公司。
先对其进行放电处理,之后手工拆解金属外壳,再将电池芯剥离,即可得到电池正极。
电池正极片的主要化学成分见表1。
实验所用化学试剂包括浓硫酸、浓盐酸、无水硫酸钠和柠檬酸,均为分析纯。
表1 废旧锂离子电池正极片的化学成分1.2 实验方法实验中使用300 mL 烧杯作为电解池,截取 2.5cm×10 cm 的正极片经压平后作为电解池阴极,以0.5 cm×0.5 cm 的铂片为对电极,进行恒电流电解,电解液中硫酸钠作为支持电解质,它与硫酸的浓度之和固定为0.5 mol/L。
电解浸出后,经蒸馏水冲洗即可回收完整的铝箔,残渣则用体积比为1:1 的HCl 溶解。
其中,钴浸出率η(Co )和铝浸出率(Al)分别按下式计算:1.3 分析方法及仪器采用亚硝基R 盐分光光度法测定钴含量;采用铬天青S 分光光度法测定铝含量;采用PS−2 真空型ICP−AES 对试样进行全元素分析;使用RST5000 电化学工作站测试线性扫描伏安曲线,其中工作电极表观面积为1 cm 2,辅助电极为大片铂电极,参比电极为饱和甘汞电极,扫描速率为 5 mV/s ;采用荷兰Quanta−200 型扫描电子显微镜分析铝箔表面形貌。
2 结果与讨论2.1 电化学还原工艺原理将失效钴酸锂粉末、乙炔黑和聚偏氟乙烯(PVDF)按质量比8:1:1 研磨混匀,以N−甲基吡咯烷酮(NMP)为溶剂,将其均匀地涂覆在铂片电极上,烘干后置于30 g/L H2SO4 +28.9 g/L Na2SO4 溶液中进行线性伏安扫描,结果如图1 所示。
由图 1 中曲线 1 可知,铂电极在0.68~−0.26 V 电位窗口内几乎不发生电极反应,最大电流为 3 mA,相对于曲线 2 中最大电流( 28 mA),可忽略。
而电位由−0.26 V 继续负移,H2 开始析出,还原电流急剧增大。
曲线2 中,在电极电位为0.30 V 左右出现了一个明显的还原峰,因为在本研究的电位范围内,考虑到溶液体系为强酸环境,LiCoO2 只能被还原为Co2+,即此峰是LiCoO2 还原为Co 2+ 的特征峰,从而证明LiCoO2 能够通过阴极电解进行浸出。
铝箔作为正极片的一部分,在电解浸出过程中同样作为阴极,在外加电流作用下进行阴极极化,从而减缓在硫酸溶液中的溶解速率,简言之,铝箔是受阴极保护的。
将正极片的钴锂膜剥离,得到集流体铝箔,对其进行线性伏安扫描,结果如图 2 所示。
由图 2 可以看出,在电极电位0.48 V 附近出现一个氧化峰,对应于铝阳极活性溶解过程。
当扫描至−0.53 V 时,腐蚀电流为0,铝箔得到了完全保护,此电位为铝箔最小保护电位。
综上可以得到电化学还原工艺的电极反应如下:阴极,2.2 电化学还原工艺2.2.1 电流密度对钴和铝浸出率的影响在H2SO4 浓度为40 g/L、C6H8O7H2O 浓度为36 g/L、反应温度为25 ℃和反应时间为120 min 的条件下,考察电流密度对钴、铝浸出率的影响,结果如图3 所示。
由图 3 可知,电流密度增加,Co2+浸出率先随之增加,当电流密度高于15.6 mA/cm 2时,Co2+浸出率出现大幅下降,这主要是由LiCoO2 和H+在阴极还原时相互竞争、此消彼长引起。
电流密度偏低时,随电流密度的增加,LiCoO2 的还原作用加强,因为LiCoO2比H +更容易得电子,其中LiCoO2/Co 2+的标准电极电位为 2.08 V,H+ /H2 的标准电极电位为0 V。
当电流密度大于15.6 mA/cm 2时,阴极极化严重,而LiCoO2的还原过电位更高,H+阴极放电的竞争优势加大。
从图3中还可以看出,铝浸出率在电流密度为12.5~18.7 mA/cm 2 的范围内的变化趋缓。
综上所述,电流密度的最佳值选为15.6 mA /cm 2 。
2.2.2 硫酸浓度对钴、铝浸出率的影响在电流密度为15.6 mA/cm 2、C6H8O7∙H2O 浓度为36 g/L、反应温度为25 ℃和反应时间为120 min 的条件下,研究硫酸浓度对钴、铝浸出率的影响,结果如图4 所示。
由图4 可知,钴浸出率随硫酸浓度的增大先升高再降低,当硫酸浓度为40 g/L 时,钴浸出率达到最大,为86.6%。
维持一定的pH 值,使LiCoO2 直接还原为Co 2+进入溶液,需要足够高的硫酸浓度,但当硫酸浓度过高时,H + 阴极还原加剧。
大量析氢造成铝箔表面局部碱化,破坏钴锂膜与铝箔的粘结作用,二者相互剥离;另一方面,析氢量较大,H2 不能及时排出,使钴锂膜鼓破。
最终,由于钴锂膜在溶液体系中不能有效转移电荷而使钴浸出率偏低。
从图4 中还可以看出,随硫酸浓度的增加,铝浸出率增加较快,但在硫酸浓度为40 和50 g/L 时出现持平。
综合以上分析,最佳硫酸浓度确定为40 g/L。
2.2.3 柠檬酸浓度对钴、铝浸出率的影响添加柠檬酸是实验的关键技术之一,主要是为了避免电解浸出过程中溶液失稳而变得浑浊。
分别配制3 种不同溶液,测试铂电极在不同溶液体系中的线性扫描伏安曲线以考察电解浸出中的阳极行为,结果如图5所示。
由图5 中曲线 2 与3 可看出,相同电位下,添加柠檬酸溶液体系的氧化电流明显减小。
在电解过程中,LiCoO2 还原为Co2+ 进入电解液,随Co 2+浓度的升高,Co 2+ 在阳极被氧化为Co3+的概率越来越大;而 1 g/L 的Co 3+在pH>0.5 时就会发生水解反应,生成Co(OH)3沉淀((Co(OH) 3 的溶度积为3×10 −41 )。
同时需要强调的是,电解生成的Co3+的稳定时间为30 min 左右[10],且其水解也是逐渐进行的,所以浑浊的电解液经抽滤澄清后静置一定时间还会变浑浊。
基于以上分析,柠檬酸之所以可防止电解液浑浊,是因为它能抑制Co2+的阳极氧化,即使有少量Co 3+生成,就会立即被还原成Co2+。
在电流密度为15.6 mA/cm 2、硫酸浓度为40 g/L反应温度为25 ℃和反应时间为120 min 的条件下,柠檬酸浓度对钴、铝浸出率的影响如图6 所示。
由图6 可知,当柠檬酸浓度为36 g/L 时,钴浸出率较其他的略大。
值得注意的是,当柠檬酸浓度在12~48 g/L 的范围内时,随柠檬酸浓度的增加,铝浸出率逐渐降低。
柠檬酸是三元有机酸,在铝表面的吸附能力极强,而且这种吸附能力与pH 值无关,从而对铝箔腐蚀起到一定防护作用。
选取柠檬酸浓度36 g/L 为最佳值。
2.2.4 温度对钴、铝浸出率的影响在电流密度为15.6 mA/cm 2、硫酸浓度为40 g/L、C6H8O7∙H2O 浓度为36 g/L、反应时间为120 min 的条件下,反应温度对钴、铝浸出率的影响如图7 所示。
由图7 可知,15 ℃时钴浸出率较低,随温度的升高,钴浸出率逐渐增大,当温度达到45 ℃时出现最高峰后,钴浸出率随温度的变化不再明显。
升高温度可明显促进LiCoO2 的阴极还原。
同时,铝浸出率随温度的升高增加比较明显。
综合实验结果,取温度45 ℃为最佳值,此时钴浸出率达到90.8%,铝浸出率为7.9%。
2.2.5 电解时间对钴、铝浸出率的影响在电流密度为15.6 mA/cm 2、硫酸浓度为40 g/L、C6H8O7∙H2O 浓度为36 g/L、反应温度为45 ℃的条件下,研究电解时间对钴、铝浸出率的影响,结果如图8 所示。
由图8 可知,钴浸出率随电解时间的延长明显增大,且增大的速率越来越慢,时间超过120 min 后变化不明显。
这主要是由于在电解过程中正极片的表面状态是变化的,从而影响其表面阴极反应。
电解初期,电极粉颗粒间以面接触为主,有利于电子的传递,LiCoO2 的还原占主导地位;但随着电解时间的延长,LiCoO2 脱离钴锂膜,电子传递的通道受阻;至电解后期,钴锂膜与铝箔相剥离由于活性物质的导电性远不如金属铝的,电荷转移受到阻滞,终造成LiCoO2 浸出阻力变大,析氢加剧。
从图8 还可以看出,铝浸出率随着电解时间的延长逐渐升高。
综上可得出电解时间的最佳值为120 min。
2.3 铝箔的阴极腐蚀铝箔电解浸出前后的SEM 像如图9 所示。
由图9(a)可见,铝基体表面存在大量形状不规则的小孔,尺寸为3~8 μm。
这是由于铝集流体在多次充放电循环后,出现了点蚀现象。
由图9(b )可见,铝基体表面分布有较多大小坑洞,大坑洞为电解浸出过程中产生的腐蚀坑,小坑洞为图9(a)所示点蚀坑的残余部分。