标准作业时间表汇总0
标准作业时间订定 表

标准作业时间订定表日期审核分析人美文欣赏1、走过春的田野,趟过夏的激流,来到秋天就是安静祥和的世界。
秋天,虽没有玫瑰的芳香,却有秋菊的淡雅,没有繁花似锦,却有硕果累累。
秋天,没有夏日的激情,却有浪漫的温情,没有春的奔放,却有收获的喜悦。
清风落叶舞秋韵,枝头硕果醉秋容。
秋天是甘美的酒,秋天是壮丽的诗,秋天是动人的歌。
2、人的一生就是一个储蓄的过程,在奋斗的时候储存了希望;在耕耘的时候储存了一粒种子;在旅行的时候储存了风景;在微笑的时候储存了快乐。
聪明的人善于储蓄,在漫长而短暂的人生旅途中,学会储蓄每一个闪光的瞬间,然后用它们酿成一杯美好的回忆,在四季的变幻与交替之间,散发浓香,珍藏一生!3、春天来了,我要把心灵放回萦绕柔肠的远方。
让心灵长出北归大雁的翅膀,乘着吹动彩云的熏风,捧着湿润江南的霡霂,唱着荡漾晨舟的渔歌,沾着充盈夜窗的芬芳,回到久别的家乡。
我翻开解冻的泥土,挖出埋藏在这里的梦,让她沐浴灿烂的阳光,期待她慢慢长出枝蔓,结下向往已久的真爱的果实。
4、好好享受生活吧,每个人都是幸福的。
人生山一程,水一程,轻握一份懂得,将牵挂折叠,将幸福尽收,带着明媚,温暖前行,只要心是温润的,再遥远的路也会走的安然,回眸处,愿阳光时时明媚,愿生活处处晴好。
5、漂然月色,时光随风远逝,悄然又到雨季,花,依旧美;心,依旧静。
月的柔情,夜懂;心的清澈,雨懂;你的深情,我懂。
人生没有绝美,曾经习惯漂浮的你我,曾几何时,向往一种平实的安定,风雨共度,淡然在心,凡尘远路,彼此守护着心的旅程。
沧桑不是自然,而是经历;幸福不是状态,而是感受。
6、疏疏篱落,酒意消,惆怅多。
阑珊灯火,映照旧阁。
红粉朱唇,腔板欲与谁歌?画脸粉色,凝眸着世间因果;未央歌舞,轮回着缘起缘落。
舞袖舒广青衣薄,何似院落寂寞。
风起,谁人轻叩我柴扉小门,执我之手,听我戏说?7、经年,未染流殇漠漠清殇。
流年为祭。
琴瑟曲中倦红妆,霓裳舞中残娇靥。
冗长红尘中,一曲浅吟轻诵描绘半世薄凉寂寞,清殇如水。
标准作业管理规定(含表格)
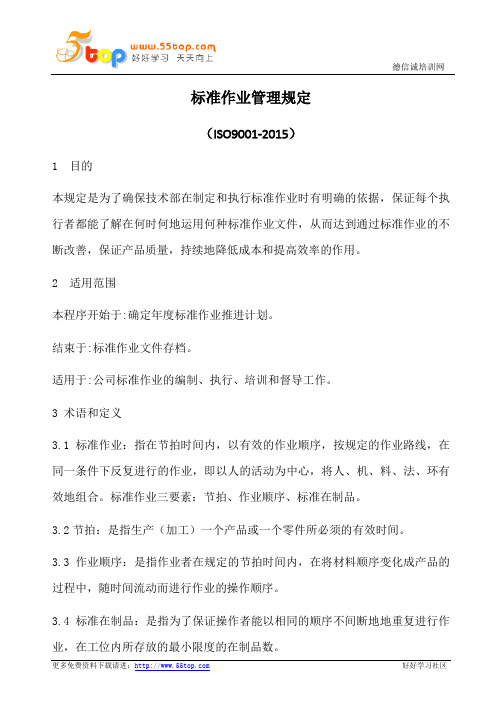
标准作业管理规定(ISO9001-2015)1 目的本规定是为了确保技术部在制定和执行标准作业时有明确的依据,保证每个执行者都能了解在何时何地运用何种标准作业文件,从而达到通过标准作业的不断改善,保证产品质量,持续地降低成本和提高效率的作用。
2 适用范围本程序开始于:确定年度标准作业推进计划。
结束于:标准作业文件存档。
适用于:公司标准作业的编制、执行、培训和督导工作。
3 术语和定义3.1标准作业:指在节拍时间内,以有效的作业顺序,按规定的作业路线,在同一条件下反复进行的作业,即以人的活动为中心,将人、机、料、法、环有效地组合。
标准作业三要素:节拍、作业顺序、标准在制品。
3.2节拍:是指生产(加工)一个产品或一个零件所必须的有效时间。
3.3作业顺序:是指作业者在规定的节拍时间内,在将材料顺序变化成产品的过程中,随时间流动而进行作业的操作顺序。
3.4标准在制品:是指为了保证操作者能以相同的顺序不间断地地重复进行作业,在工位内所存放的最小限度的在制品数。
3.5标准作业文件:是指导作业人员进行正确的装配作业,和管理人员检查标准作业符合度的依据。
标准作业文件包括《测时表》、《负荷平衡山积表》、《要素山积表》、《标准作业组合表》、《标准作业卡》、《标准作业要领书》等。
3.6作业路线:是指作业者在规定的节拍时间内,能以最高的效率进行装配作业的行走线路。
3.7测时表:用来记录操作者每一操作顺序的作业时间。
在测时的同时,记录者还要注意将当时的现场要素尽可能详细地记录在案,以展示操作者当时的作业环境和可能影响标准作业的因素,以便以后进行改善时用。
3.8负荷平衡山积表:记录生产线上各操作者的作业时间和节拍时间,可用来查找生产线的瓶颈点,通过现场改善,达到提高瓶颈的通过能力、平衡各操作者的作业时间和劳动负荷目的。
3.9要素山积表:记录生产线上各操作者的单元时间和节拍时间,通过在各操作者之间取消、转移、重排、合并装配作业的单元,达到消除生产线的瓶颈,平衡各操作者的作业时间和劳动负荷的目的。
IE标准工时表

#DIV/0!
實際人數: 實際産能: 實際人均産量:
達標率:
原因分析:
文件编号:
版 本:
A1
观测日期:
宽放时间
项目
私事宽 作业 疲劳 管理 放 宽放 宽放 宽放
时间 10分 20分 10分 10分
比率 2.1% 4.2% 2.1% 2.1%
123
工时观测表
评比系数
標準産量: 人均産能:
#DIV/0!
損失比率
#DIV/0! #DIV/0!
0人 #DIV/0! #DIV/0!
#DIV/0!
實際人數: 實際産能: 實際人均産量:
達標率:
原因分析:
123
工时观测表
评比系数
特殊宽放
熟练 环境 努力 程度 条件 程度
一致性
10分 2.1%
2.0% 2.0% 2.0%
2.0%
观测次数(秒表)
4 5 6 7 8 9 10
型 号:
0
规 格:
0
观测人:
刘杰
不良 比率
线外 人员 比率
系 数
总工作时 间(8小时
制)
部门
1.0% 1.0% 1.090 480分
#DIV/0!
#DIV/0!
######
#DIV/0!
#DIV/0!
######
#DIV/0!
不平衡損失時間: 觀測時間小計: 標準時間小計: 標準人數小計: 標準産量: 人均産能:
#DIV/0!
損失比率
#DIV/0! #DIV/0!
0人 #DIV/0! #DIV/0!
#DIV/0!
班长标准作业表-参考
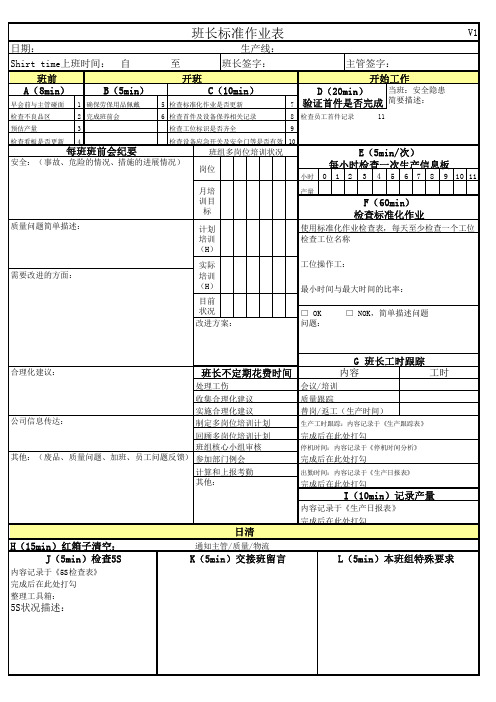
质量问题简单描述:
月培 训目
标
计划 培训 (H)
产量
F(60min) 检查标准化作业
使用标准化作业检查表,每天至少检查一个工位 检查工位名称
需要改进的方面:
实际 培训 (H)
目前 状况 改进方案:
工位操作工:
最小时间与最大时间的比率:
□ OK 问题:
□ NOK,简单描述问题
合理化建议:
班长不定期花费时间
2 完成班前会 3
6 检查首件及设备保养相关记录 检查工位标识是否齐全
8 检查员工首件记录
11
9
检查看板是否更新 4
每班班前会纪要
检查设备应急开关及安全门等是否有效 10
班组多岗位培训状况
安全:(事故、危险的情况、措施的进展情况) 岗位
小时
E(5min/次) 每小时检查一次生产信息板
0 1 2 3 4 5 6 7 8 9 10 11
完成后在此处打勾
计算和上报考勤 其他:
出勤时间:内容记录于《生产日报表》
完成后在此处打勾
I(10min)记录产量
内容记录于《生产日报表》
日清
完成后在此处打勾
H(15min)红箱子清空: J(5min)检查5S
通知主管/质量/物流
K(5min)交接班留言
L(5min)本班组特殊要求
内容记录于《5S检查表》
G 班长工时跟踪
Hale Waihona Puke 内容工时处理工伤
会议/培训
收集合理化建议
质量跟踪
公司信息传达:
实施合理化建议 制定多岗位培训计划
替岗/返工(生产时间)
生产工时跟踪:内容记录于《生产跟踪表》
回顾多岗位培训计划 班组核心小组审核 其他:(废品、质量问题、加班、员工问题反馈) 参加部门例会
MOD标准时间表

第n颗单颗螺丝时间≧2.6445 连续锁第n颗时间
注意:1.误差10%左右 2.各工序动作不包含特殊作业。(eg:料件拿取时间与包装方式密切相关,此表格中不包含特殊包装方式 3.BD表示这只手什么动作也没有做,即停止状态,不给时间值。H表示保持。 UT表示有效时间。 4.当左右手同时作业,且都需要注意力,不可同时进行时,默认为左手先做。 5.模特分析值所得的时间值就是标准时间值,不需要计算宽放率。
)
编写:
审核锁螺丝为例)
MOD预定时间标准表 Item 主要动作 左后作业 操作说明 MOD符号 BD 1 贴胶带 捏住被贴物体 取螺丝 放螺丝到起子头 对准孔位 锁 BD BD M3G3 M3G1 M3P5 H (E2D3) H BD BD 取螺丝 2 锁螺丝 放螺丝到起子头 对准孔位 锁 M3G1 M3P5 H (E2D3) H BD BD BD BD BD BD 有效操作 MOD符号 M3G1 M2G3M2P0 M3P0 M3G3M2G3M2P2 M4G1 M3P5 M3P5M2P0 (E2D3) 0 1/2M1P0 M4P2 M3G1 M3P5 M3P0 (E2D3) 0 1/2M1P0 右手作业 MOD符号 M3G1 M2G3M2P0 M3P0 M3G3M2P2 M4G1 H M3P5M2P0 (E2D3) H 1/2M1P0 M4P2 H H M3P0 (E2D3) H 1/2M1P0 起子头至螺孔处 对准孔位 锁 放射时间 起子头至螺孔处 对准孔位 锁 放射时间 放回起子 操作说明 伸手抓取胶带 撕胶带 胶带移至机台上方 贴胶带 拿起子 Rev:R00 修改日期: MOD数值 预定标准时间(s) 4 7 3 15 5 8 10 5 0 0.5 6 4 8 3 5 0 0.5 20.5 20.5 20.5 20.5 9.74 12.38 15.03 17.67 连续锁第三颗时间 连续锁第四颗时间 连续锁第五颗时间 连续锁第六颗时间 7.10 连续锁第二颗时间 4.45 单独锁一颗时间 3.74 备注
标准工时和计算标准管理规范(含表格)
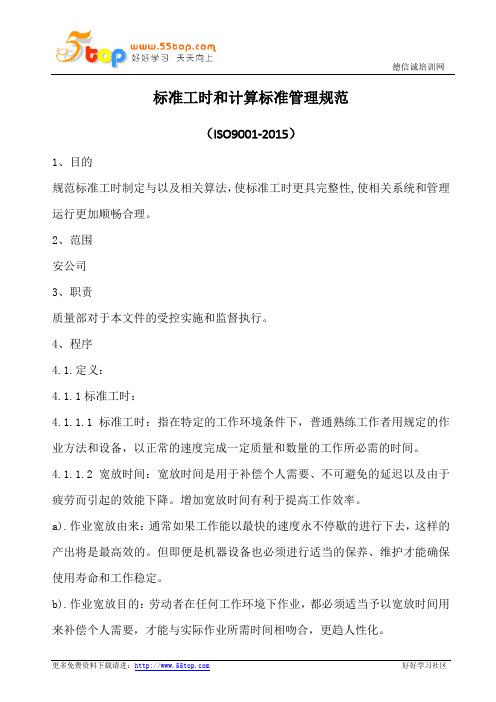
标准工时和计算标准管理规范(ISO9001-2015)1、目的规范标准工时制定与以及相关算法,使标准工时更具完整性,使相关系统和管理运行更加顺畅合理。
2、范围安公司3、职责质量部对于本文件的受控实施和监督执行。
4、程序4.1.定义:4.1.1标准工时:4.1.1.1标准工时:指在特定的工作环境条件下,普通熟练工作者用规定的作业方法和设备,以正常的速度完成一定质量和数量的工作所必需的时间。
4.1.1.2宽放时间:宽放时间是用于补偿个人需要、不可避免的延迟以及由于疲劳而引起的效能下降。
增加宽放时间有利于提高工作效率。
a).作业宽放由来:通常如果工作能以最快的速度永不停歇的进行下去,这样的产出将是最高效的。
但即便是机器设备也必须进行适当的保养、维护才能确保使用寿命和工作稳定。
b).作业宽放目的:劳动者在任何工作环境下作业,都必须适当予以宽放时间用来补偿个人需要,才能与实际作业所需时间相吻合,更趋人性化。
4.1.1.3标准速度:没有过度体力和精神疲劳状态下,每天能连续工作,只要努力就容易达到标准作业成果的速度。
4.1.2员工定义:4.1.2.1直接人员:指生产产线上从事生产操作人员。
包括装配、调整、检查检测和不良品维修人员。
他们是生产线上直接从事生产劳动的人员。
4.1.2.2间接人员:指不直接从事生产操作的人员,此处包括车间班长,物料配送人员、设备保养人员、工具保养人员。
间接员工虽然不从事直接的生产操作,但对于提升生产效率具有很大的影响。
4.1.3时间定义:4.1.3.1正常作业时间:指以每天8小时为基准的作业时间,其单位为分钟。
正常作业时间包括“前准备时间”和“净作业时间”。
4.1.3.1.1前准备时间(95分钟):a).早会(早会,交接班)10分钟b).清洁(工治具、设备、车间、更衣)30分钟c).中餐时间15分钟d).间隙时间(上午15分钟,下午15分钟)30分钟e).首检时间10分钟4.1.3.1.2净作业时间:指对作业对象作业的内容,规则地、周期性地重复进行的作业部分的时间。
标准工时制定规范(含表格)
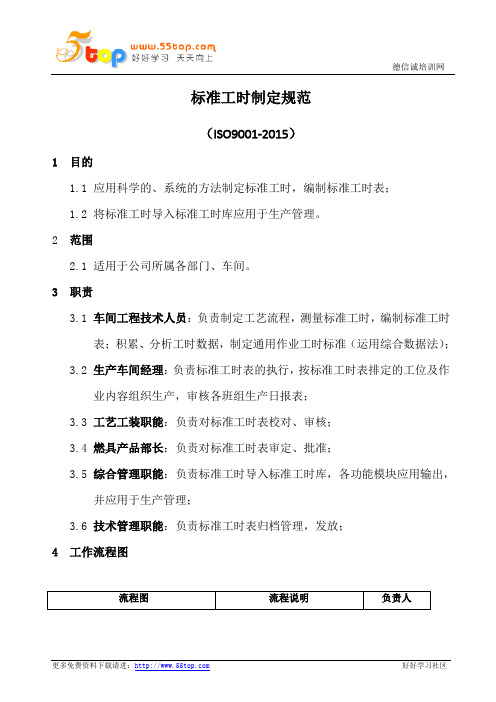
标准工时制定规范(ISO9001-2015)1目的1.1应用科学的、系统的方法制定标准工时,编制标准工时表;1.2将标准工时导入标准工时库应用于生产管理。
2范围2.1适用于公司所属各部门、车间。
3职责3.1车间工程技术人员:负责制定工艺流程,测量标准工时,编制标准工时表;积累、分析工时数据,制定通用作业工时标准(运用综合数据法);3.2生产车间经理:负责标准工时表的执行,按标准工时表排定的工位及作业内容组织生产,审核各班组生产日报表;3.3工艺工装职能:负责对标准工时表校对、审核;3.4燃具产品部长:负责对标准工时表审定、批准;3.5综合管理职能:负责标准工时导入标准工时库,各功能模块应用输出,并应用于生产管理;3.6技术管理职能:负责标准工时表归档管理,发放;4工作流程图5工作程序5.1标准工时制定原则5.1.1在产产品:所有在一年内生产的产品必须制定相应品名的标准工时,超过3年未生产产品的标准工时表可以不维护更新,但保留旧版电子档,以备查看;5.1.2新增产品:新产品试产时需制定一个临时工艺流程图,在批量生产后5个工作日须发行新版正式标准工时表;新版标准工时表版本号统一定为“00”版;5.1.3工艺变更:当生产工艺发生变更时,须调整相应变更工位的工时数据,并升级发行新的标准工时表,版本号为原版本号加“1”,并在表上相应位置注明升级原因。
例:原版为“00”版,升级后发行版本为“01”版,以此类推。
5.1.4制程改善:当对生产制程进行改善时,改善成果将通过“标准工时”的降低,“线平衡率”的提高来体现;改善完成后须升级标准工时表,以进行相应措施的固化;5.1.5与实际差异过大:当正式版标准工时表投入使用后,若发现与生产实际存在较大差异时,需要就部分或全部工位进行重新观测分析,再升级发行新版标准工时表;差异过大的标准为:在去除外部影响与内部问题后的产出工时与投入工时的差异超过10%;5.2数据测量标准工时制定初期阶段以秒表法为主,待积累了大量的作业单元数据进行分析后,再运用综合数据法制定常用作业的工时标准参数表,以在后期制定标准工时时直接取用,提高制作效率。
标准工时统计表-新

T:代表"夹具/机器具/机器"(4)各部门认为标准工时不能真实体现作业状况时,可向有关部门申请重新测评。
总之,标准工时是实施现场管理的重要基础9 牢记要点计算标准工时要了解以下内容: _ 明确标准工时的作用 _ 做好标准工时测定准备 _ 计算标准工时 _ 修表真实的情况,故此应加以修正,乘上一定的评价系数,求得实际时间作为标准时间的主体,而实际时间应考虑一定的宽放,作为疲劳、等待、喝水、上厕所等必因素包括:操作者的熟练程度,设备工具的完善度,操作者的教育程度,工作的困难度。
时合理。
在计算标准工时时,要了解以下内容: 1.明确标准工时的作用利用标准时间,生产管制部门可以更精确地做生产计划,如在进度控制上有了问题,也可依标准时间来做人力调整。
水线生产的平衡。
一条流水线有很多工序,可依各工序的标准时间来配置人力,使生产线平衡、流畅。
业内容、达到什么精度、制定时间标准的费用等。
准时间资料法、计划估算法、实际成绩资料法、数学法等很多种类。
每个方法各有其特点,企业可以根据使用目的和测定的对象作业性质选择适当的方法。
3进行测算,并连续测试20个以上的周期时间。
参照的作业人员,其劳动熟练程度与中等熟练人员的比较系数称为评核系数。
系数越大表示其劳动熟练程度越高。
劳宽放时间 宽放率= ×100%=管理宽放率+生理宽放率+疲劳宽放率 其中:管理宽放率一般取3%~10%; 疲劳宽放率一般取5%~20%; 生理产趋于稳定时(一般为生产一周以上),工艺人员应再次测评标准工时;必要时应予以修改,并发出变更通知。
应予以修改,并发出变更通知。
,并发出变更通知。
施现场管理的重要基础,准确的标准工时可以平衡生产线,有效分配工作人员,生产各部门都要依据标准工时制定相应的工作计划。
标准工时 _ 修改标准工时喝水、上厕所等必须要项的预备,这样才得到标准时间。
当的方法。
3.计算标准工时 (1)测算作业时间~20%; 生理宽放率一般取2%~5%。
有限空间危险作业记录表(标准版)

有限空间危险作业记录表物业服务中心:有限空间危险作业记录表(标准版)使用说明一、文件概述有限空间危险作业记录表(标准版)是一份旨在规范有限空间作业过程、确保作业安全的重要管理工具。
它详细记录了作业前的准备、作业中的监测以及作业后的收尾工作,确保作业人员、监护人员及作业负责人能够全面掌握作业情况,及时发现并消除安全隐患。
二、表格结构与内容基本信息填写作业单位:明确执行作业的单位或部门。
设施名称:记录进行作业的具体设施或场所名称。
作业人员:列出参与作业的所有工作人员姓名。
填报人员与监护人员:分别填写负责填写表格的人员和现场监护人员姓名。
进入前检测数据该部分要求在作业人员进入有限空间前,对空间内的氧含量、易燃易爆物质浓度、有毒有害气体(粉尘)浓度等进行全面检测,并记录检测数据及检测时间。
检测项目的完整性和数据的准确性对于保障作业安全至关重要。
安全措施与确认表格列出了多项主要安全措施,包括但不限于作业人员作业安全教育、连续测定的仪器和人员、测定用仪器准确可靠性、呼吸器等抢救器具准备、通风排气情况、氧气浓度及有害气体检测结果、照明设施、个人防护用品及防毒用具、通风设备等。
每项措施均需确认符合要求,并由相关人员签名确认。
特别强调了连续监测和通风设备的重要性,这是防止有限空间内有毒有害气体积累、保障作业人员安全的关键措施。
开工时间与作业负责人意见记录每次作业的开工时间,以及作业负责人对作业安全措施的审核意见和签名。
作业负责人的签名标志着安全措施已得到确认,作业可以正式开始。
工作结束确认作业结束后,由作业负责人进行确认并签名,同时记录结束时间。
这标志着整个作业过程的圆满结束,也确保了作业结束后现场的安全恢复。
三、使用注意事项全面性:在填写记录表时,应确保所有项目均已涵盖,无遗漏。
特别是安全措施的确认,必须逐项检查并签名确认。
准确性:检测数据应准确可靠,避免因数据错误导致的安全风险。
同时,填写时应字迹清晰,易于辨认。
IE(工业工程)标准工时

13
HI-13
Insert L901.L301.F1.D901
2 31.87 28.56 27.39 26.88 29.55 31.87 26.88 14.43
14
HI-14
Insert SK.CR1.CX1.CX2
2 31.67 30.59 31.64 29.68 30.14 31.67 29.68 15.37
26
T U-04
Total inspection
1 15.99 15.34 14.28 13.48 10.38 15.99 10.38 13.89
27
ICT
Testing components of main board
1 10.23 12.34 11.25 13.88 14.22 14.22 10.23 12.38
UPH(units per hour)单位小时产能,产能的指标。
UPH=年生产量/(12*月工作日*日工作小时)或 UPH=日生产量/日工作小时
计算当前整机cell 线UPPH?
常用术语—生产力、生产效率
常用术语— OPE
OPE(Overall Plant Efficiency)整体工厂效率
用来衡量工厂经营管理的整体效率,包含:设计者效率,管理者 效率,作业效率。反应工厂综合能力。
五、标准工时的制定方法
标准工时的制定方法有很多,归纳起来有如下几种: 1)秒表观测法俗称“马表法”或时间观测法(我司采用的方法) 2)标准时间预定法(PTS法) a、WF法(Work Factor) b、MTM法(Methods Time Measurement) C、MODAPTS法(Modular Arrangement of PTS) 3)标准资料法 4)经验法 5)VTR法(摄影法)
铁路列车及货车技术作业过程和时间标准

铁路列车及货车技术作业过程和时间标准列车在始发站、终到站及运行途中的技术站,在到发线上所办理的各项技术作业,称为列车技术作业。
货车自到达车站时起,至由车站发出时止,在车站所办理的各项技术作业,称为货车技术作业。
这些作业项目、顺序与时间标准,统称为列车及货车的技术作业过程。
车站技术作业过程是《车站行车工作细则》的重要组成部分.是指导车站日常运输生产活动的重要技术文件,是调度指挥工作的重要依据。
车站技术作业过程应根据列车运行图、列车编组计划、《铁路技术管理规程》和一定时期内的到发列车情况和车流量,经过写实查定并经上级批准。
凡遇列车运行图、列车编组计划、车站技术设备以及到发车流发生巨大变化时,均应及时修订或重新编制车站技术作业过程。
为了缩短车站办理列车及货车技术作业时间,提高作业效率,保证作业安全,车站应加强作业的计划与指挥,提前做好准备;广泛采用先进作业方法,缩短单项作业时间;最大限度地组织流水作业和平行作业,减少作业的延续时间;加强各部门、各工种之间的联劳协作,避免作业中断,减少等待时间。
一、货物列车技术作业过程为了保证列车运行的安全和货物的完整,货物列车在技术站需由检车员、车号员、货检员等有关人员,为列车进行一定的技术作业。
货物列车技术作业,按其作业性质的不同,可分为无调中转列车、解体列车、始发列车和部分改编中转列车四种,如图2-5所示。
1.无调中转列车技术作业过程无调中转列车是指在技术站不进行改编调车作业,只在到发线上进行必要的技术检查后继续运行的列车。
一般为直达、直通列车。
这种列车在技术站没有解体和编组作业,而只需在到发线上进行列车的到发作业、车辆的技术检查、列尾技术作业、货运检查、核对现车、列车及票据交接、换挂机车和换乘等技术作业。
其作业过程如表2-3所示。
表2-3无调中转列车技术作业过程2.解体列车技术作业过程解体列车是指列车到达车站后要进行解体作业的列车。
为给解体作业提供条件,列车的技术作业除需进行车列的技术检查、货运检查、站车交接等作业外,调车人员还要进行排风、摘管等解体前的准备工作。
产品工时额定标准
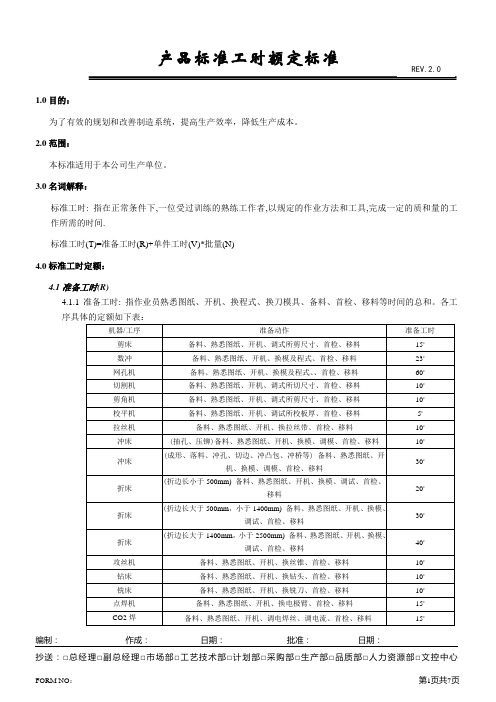
1.0目的:为了有效的规划和改善制造系统,提高生产效率,降低生产成本。
2.0范围:本标准适用于本公司生产单位。
3.0名词解释:标准工时: 指在正常条件下,一位受过训练的熟练工作者,以规定的作业方法和工具,完成一定的质和量的工作所需的时间.标准工时(T)=准备工时(R)+单件工时(V)*批量(N)4.0标准工时定额:4.1准备工时(R)4.1.1准备工时: 指作业员熟悉图纸、开机、换程式、换刀模具、备料、首检、移料等时间的总和。
各工4.1.2在工时定额时,可根据实际情况对以上的准备工时作以适当的调整。
4.2 单件工时(V)4.2.1 单件工时(V): 一位熟练工作者以规定的作业方法和工具完成一件合格料品所需的时间.单件工时(V)=上下料时间(Ts)+机器/人加工效率(Vr)*(1+宽放率(Aw))+辅助时间(F)4.2.24.2.34.2.4各工序/机器单件工时具体定额4.2.4.1剪床:(均以标准板材(4尺,8尺)计算,则有剪条料单件工时=(材料长/条料宽+1)*12"/N剪净料单件工时V=[(A+1)*12”+(C+1)*Vr]/N*(1+Aw) B DA=材料长B=工件长C=材料宽D=工件宽N=一张板加工工件数量Vr=单刀时间(当工件L<5000时,Vr=0.1’; 当工件500>L>1000时,Vr=0.15’;当工件L>1000时,Vr=0.2’)4.2.4.2数冲:a. V=Ts+ [(C+D)/*Vr+E*H+F*K]*(1+Aw)C=工件外周长D=工件内孔周长(孔径大于60mm)E=换刀次数F=孔数(孔径等于或小于60mm)Vr=切边速度0.15'/1000mm(按刀长为60算)H=自动换刀速度0.15'/次K=冲孔速度(松散孔1”/下冲一次,密集孔1”/下冲6次(液压AMADA))b. 覆膜与去毛刺时间=数冲单件工时(V)。
c. 当加工工件板材厚度大于2.0时,其单件工时须乘以1.2的系数.4.2.4.3切割机:a.平台切割机:V=Ts+Vr*N*(1+Aw)+F (可根据材料截面的大小对其机器工效率作以适当的调整)N=下切刀数b.等离子切割机:V=Vr*L*(1+Aw)+FL=切割缝长4.2.4.4网孔机:V=Ts+Vr*N*(1+Aw)+FN=下冲次料=孔总数一次冲孔数4.2.4.5冲床:a.抽孔、压铆:V=Ts+Vr*N*(1+Aw)+FN=压铆数量或抽孔数量当N>15时,其单件工时(V)须乘以0.8系数;b.成形、落料、冲孔、切边、冲凸包、冲桥等:V=Ts+Vr*N*(1+Aw)+FN=下冲次数剪条料后落料的单件时间须乘以0.6系数;c.当料件长大于1200mm,宽大于500mm时,其机床加工效率应乘以2。
标准工时产能表

标准工时表依据公司近期内实际生产和目标,制定如下标准:补充说明:一﹑优化生产线1.降低生产成本:包括人工成本﹑管理成本及物料搬运成本等﹐并且由于产量之提高﹐使分摊之各项间接费用也随之降低﹒2.提高工作效率:由于各站工作之固定化﹐不必要之寻找﹑思考等心力工作大幅减少﹐使工作效率提高﹒3.简化管理工作:包括人员训练﹑工作督导﹑产量计算﹑品质追踪等等管理工作都能简化.4.减少物料搬运:由于生产线之制造流程和搬运路径相同﹐并且常使用定路径之搬运设备(例如输送带﹑定轨式吊车﹑台车﹑吊蓝)搬运﹐因此物料搬运量减少﹒5.能满足大量生产之需要:在各种复杂性产品之生产技术中以生产线技术之大量生产投资及单位生产成本最低﹒除衣衫五项以外,采用生产线还可以节省厂房面积﹐减少半成品中间库存﹐并且还可以使员工容易产生认同感和归属感之优点﹒二、生产线有关名词之解说﹕生产线有关名词极多﹐以下仅选择较常用的名词说明﹕1、工作站(WORK STATION)﹕又称作业站﹐是在生产线上执行一项工作或一组工作之工作单位,生产线系由若干工作站所组成﹐在工作站上执行工作之人员称为工作员﹐作业员或操作员,每作业站之作业人员通常为一人和一组作业员﹐视实际需要调派﹐生产线上所含工作站之数目以K代表﹒2、单元(WORK ELEMENT OR WORK UNIT)﹕生产线上每一工作站通常都包括若干工作项目,每一工作项目称为一个工作单元﹒一般而言公共单元之划分以能够独立成一工作为原则.常用之代号U或E﹐第I个工作单元称为Ui或Ei,大的工作单元有部分可划分为较小工作单元﹐部分则较困难﹒3、作单元时间(performance time):每一工作单元执行一件工作所需之时间称为工作单元时间﹐常用代号为ti.工作单元时间一般受制造程序之影响﹐当程序之安排足以影响该工作单元之执行时﹐工作时间将增加﹒4、作业站时间(station time): 指每一工作生产一件产品所需要之时间而言,亦即一工作站处理所含工作单元所需时间之总和﹐使用之代号为T﹒5、周期时间(cycle time):生产线生产一件产品所需之时间,亦即两产品进入(或离开)生产线之间隔时间﹐常用代号C﹒生产线周期通常等于生产线上最长作业站时间﹐亦即:C=Tmax.6、线长(line length):指生产线之长度而言﹐单位为呎或米﹐采用之代号为L.7、线速(line speed):产品在生产线上移动之速度,单位为每分钟若干米或若干呎﹒通用代号为S﹒8、在线制品:在生产线上流通之产品﹐以N代表﹒在线制品通常均较工作站数为多﹐即N大于K﹒9、呆滞在线制品:生产线上之在线制品理论上只有K件(即每一工位只有一件)﹐但实际作业上往往大于K.大于之理由有以下几个﹕(1)在生产线上往往有复合作业站存在﹐若一复合作业站拥有五个工作单元﹐则在生产作业中可能同时拥有五个在线制品﹒(2)有空白作业站存在,在生产线中若输送带过长或作业站过少时﹐生产线上会发生闲置之在线制品.(3)生产线上制品之输送以批次搬运(以集中搬运方式搬运)时﹐在线制品将大于生产线之站数,在线制品大于作业站部分称为呆滞在线制品﹐以I为代号﹒10、在线时间:任何一产品自进入至离开生产线所花之时间﹒若欲求平均在线时间则尚需视批次(lot)之多寡而定﹒生产线上线速﹑线长﹑在线制品﹑在线时间之相关性如下﹕(1)线速=线长/(在线制品*周期)即S=L/CN(2)线长=周期*在线制品*线速即L=CNS(3)周期=线长/(在线制品*线速)即C=L/NS(4)在线制品=线长/(线速*周期)即N=L/CS=I+K=在线呆滞制品+作业站数(5)在线时间=(在线存货+在线制品)/线速=(B+K+I)/S11、作业顺序圈(Procedure diagram):制品制造程序表示法之一种﹐与一般制程分析圈相似﹒(1) (2) (3)(0) (4) (6) (7) (9) (10)(12) (11) (13) (14) (15) (16)(8)12、瓶颈(Bottleneck)﹕在生产线中最慢之工作站﹐亦即是生产联机操作粘时间最长之作业粘﹐称为生产线之瓶颈﹒瓶颈在一般生产线中几乎永远存在﹐消除一个瓶颈又产生另一个瓶颈﹐而瓶颈之宽窄决定生产线之产量及效率﹒13、闲置时间(idle time):任一工作站执行一工作(即生产一件产品)所浪费的时间﹒闲置时间常用代号为D﹒限制时间等于生产线周期减去各作业粘之站时间﹐即D=C-T ﹒14、平衡(Balance)﹕生产线各工作站工作速度相近情形﹐称为生产线平衡﹐或指生产线达到所需生产速度而言﹒理论上﹐完全之平衡绝对无法存在﹐因此通常所谓平衡多指合乎需要之生产速度﹐或合乎需要之生产效率而言﹒研究﹑分析或处理生产线平衡之工作称为生产线平衡作业﹒15、平衡闲置时间(balance delay)﹕在生产线平衡状况下各站闲置时间常用代号BD.平衡闲置时间与总生产时间之比率称为平衡闲置时间率﹐常用代号为d﹒计算公式如下﹕BD=KC-ΣtiD=TBD/K.C=(KC-Σti)/(K.C)16、平衡系数(smoothness index):表示平衡状况之系数﹐亦即各作业粘时间之标准差﹐但一般标准差之计算方法是以平均值为基础﹐平衡系数之计算则以工作站时间之最大值(即生产线周期)为基础﹒计算公式如下﹕Σ(C-Ti)2S.I.=K三、生产线之设计与建立1﹑生产过程之考虑﹕以生产线制造的产品﹐其制造过程基本上是属于流程型工厂)FLOW SHOP)之生产类型﹒这种生产过程我们可以再加以细分成下列三种﹕(1)线型过程﹕这是比较简单的产品制造过程﹐较常见于制造型生产线﹐这种生产过程中没有分支﹐也没有中间投入之物料零件(如图2-1A)﹒(2)构型生产过程﹕这种过程最为常见﹐一般装配性发品之制造都可以属于这一种(如图2-1B)﹒(3)网络型生产过程﹕生产过程为网络型﹐见于较复杂产品之制造(如图2-1C)﹒直线型生产过程1 2 3 4 11 13 16 17 5 6 7 9一般生产线之设计及平衡编排﹕2﹑一般型生产线设计之参考原则﹕生产线设计以能增加生产产量,提高机器使用率,简化管理﹐工作降低生产成本为目的﹐因此在设计工作中应循下列原则﹕(1)可能减少产品在线上之移动距离﹒(2)持产品在生产线上稳定之流通﹒(3)个作业站工作分配合理﹐尽可能做到责任分明﹑工作分配平均之程度﹒(4)尽可能一条生产线生产一种产品或一个产品系统﹒(5)各站各工作单元之作业顺序尽可能固定﹒(6)线上产品愈少愈佳﹐产品在线上时间愈短愈好﹐必要时可使用支线﹒(7)各站之作业时间愈接近愈好﹐并尽可能使各作业站是工作接近同步﹒(8)生产线调整弹性良好﹒四﹑生产线改善技术﹕1.产品布置平衡的先决条件﹕在研讨产品布置的平衡时﹐必须先研究下列三个先决条件﹕(1)测定标准工时﹒各操作应先将方法标准化,然后利用各种测时的技术,订出各操作的标准工时﹐作为计算平衡时的依据﹒(2)决定不平衡率﹒虽然目的是在求其平衡,然而欲使不平衡率达0%,事实上是不可能的﹐但如大于30%-40%,则时间的损失亦甚为惊人,故通常应订出一允许不平衡率,作为调整平衡时的参考﹒一般求不平衡的公式为﹕不平衡率=(3)管理者的观念﹒有人重视控制产品周期时间于某一定值,如此当可稳定一天的产量,但也有人注意控制作业人数于某一定数,如此则分派人员时必须尽量能获得最小的周期时间,亦即能有较多的产出﹒2.生产线布置平衡常用的方法﹒生产线布置的平衡,并无任何公式能计算设备特殊的平衡,可是工作的经验,以及工作情形的分析常是最好的求平衡的方法﹐至于一般的求平衡的方法约有下列几种﹕(1)改善工作方法﹕对各费时较多的工作站,利用改善工作方法的技巧改善其工作方法,并设计夹具与改良工具﹐以缩短其所需时间﹒(2)调整工作﹕将整个程序内的各操作重予组合﹐以求其平衡﹒(3)需时间较长者分割﹕凡工作站需时较长者,分由两台或两台以上的机器或人员去作,以求各工作站间时间的平衡﹒(4)最小公倍数法﹕求各工作站所需时间的最小公倍数,为调整机器设备或人员的根据,此法常须增添机器设备与人员﹐且增加其产量﹐故须视资金及市场状况才能决定﹒(5)将若干需时较少者合并﹕将需时较少的若干工作站合并,不但可获得较佳的平衡,同时亦可获得较少工作人员的结果﹒(6)工作人员的选择﹕选用效率特优人员担任工作较多需时较多工作站的工作,效率较差人员担任工作较少工作站的工作﹒(7)增加其它零碎工作﹕如对工作较少的工作站,确无其它方法平衡时,则可增加其它零碎工作,一面操作人员发生等待﹒(8)设置替班人员﹕最好能设置副线长或线长助理等替班人员,平时可协助线长担任线上工作的督导并可担任领料发料等供应工作,遇有人员缺勤时可临时替补,以免影响整个线上平衡.通常因无替班人员的设置,常将缺勤人员的工作,分配其前后工作点担任,如此﹐则势必将影响整个线上的平衡及产出﹒3、生产线编成效率改善例举:假设某一生产线之各工作站之作业顺序及发生工时如下:13+4+4+7+7+8+9+58个人每人的工作时间;a)此共8工作站8人的分业作业生产方式,暂存与特料随之发生相当多,Line编成效率非常坏.一般Line编成效率或不平衡率,如前述之计算公式:(8*13)-(13+4+4+7+7+8+9+5) 104-57Line不平衡率= = *100﹪8*13 104=45.2%(2)若将上叙之各工程加以分配,使人员之负荷增加,则Line之可能组合有下列几种情况,而平衡率之变化也因此产生差异:请试算当中上个工作站分割时,则其Line编成效率为何?(3)由上叙一中,假设1人1日每日实际作业时间为7HR/日则1人1日之生产量与Line 之总生产量之变化如下: (表二)●由上叙二中,2人编成之总生产量为8人编成之总生产量之868÷1936=44.8%●由表二中,若2人编成之Line以4条Line生产即8人生产再与8人编成之Line比较: (868×4)÷1936=3472÷1936=179%即产量可UP179%(4)由表一与表二中可发现:○1Line之编成效率与Line之Neckpoint(瓶颈)有关○2产量之多寡与人员之编成有关○3要提高Line之效率,必须使Line Balance○4要提高总产量,则以效率高之组合来编成○5Line之编成,必须以产量为基准,求出时间标尺实际作时间7×60×60时间标尺===13sec产量193813+4+4+7+7+8+9+5 57人员数===4.4人13 1314也即以5人编成Line较合理,较具弹性,四、合理化重点改善:(1)由Line编成效率之流程图中,显而易见此工作站系整个Line瓶颈(Neckpoint)若将A工作站加以作业改善或设备性能使之降为9sec,则整个Line之效率变化为:(与8人之改善前比较)9+4+4+7+7+8+9+5○1Line效率==73.6%9×8比较:来54.8% 73.6% UP 18.8%○2产量:7×60×60÷9=2800台/日比较:2800-1936=864台/日UP 864台/日。
生产能力计算标准

生产能力计算标准企业查定能力的核定,应该从基层开始。
一般说来,可以分为两个阶段:一、各个生产车间内部生产能力的核算根据因素,计算一组同类设备组的生产能力,其一般计算公式如下:设备生产能力=设备数量(台)*单位设备有效工作时间(小时)*单位时间产量定额(实物量/台时)或设备生产能力=设备数量(台)*单位设备有效工作时间(小时)/单位产品台时定额(台时+单位产品)式中:单位设备有效工作时间=全年制度工作日数*每日工作小时数*(1--设备修理必要停工率)在生产能力主要决定于生产面积的条件下,生产能力计算公式为:生产面积生产能力=生产面积数量(平方米)*生产面积利用的延续时间(小时)*单位时间单位面积的生产定额(实物量/平方米/小时)二、企业生产能力的确定1、各个生产环节的生产能力核定,还要进一步加以综合平衡,核定企业的生产能力,也称综合生产能力。
综合平衡工作主要包括两个方面。
一是各个基本生产车间之间的能力综合;二是查明辅助生产部门的生产能力对基本生产部门的配合情况,并采取相应的措施。
2、当各个基本生产车间(或生产环节)之间的能力不一致时,整个基本生产部门的生产能力,通常按主导的生产环节来核定。
主导环节一般是指产品生产的主要工艺加工环节,当企业的主导生产环节同时有几个时,如果它们之间的能力不一致,它们之间综合生产能力的核定,则应当同上级主管部门结合起来研究,主要根据今后的市场需求量来确定。
如果该产品需要量大,则可以按较高能力的主导生产环节来定,其他能力不足的环节,可以组织外部生产协作或进行技术改造来解决。
否则,可以按薄弱环节的能力来核定。
对于能力富裕的环节,可以将多余的设备调出,或者可以较长期接受外协订货。
3、当基本生产部门的能力与辅助生产部门的能力不一致时,一般地说,企业的综合生产能力应当按基本生产部门的能力来定。
⑴、查定、验算辅助、附属部门的生产能力还是必要的。
如果辅助生产部门能力低于基本生产部门能力,要采取措施,提高其供应和服务能力,以保证基本生产部门的能力得到充分发挥。
标准时间的设定完整版
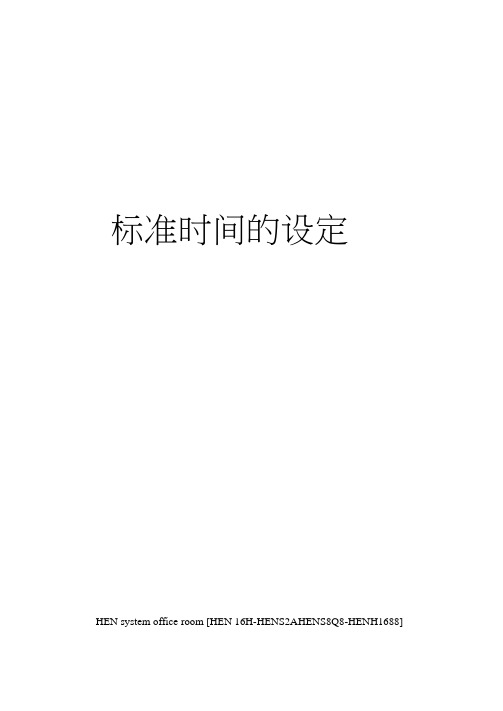
标准时间的设定HEN system office room [HEN 16H-HENS2AHENS8Q8-HENH1688]标准时间的设定一、标准工时概要1、标准工时含义标准工时是在正常的操作条件下,以标准的作业方法及合理的劳动强度和速度完成符合质量要求的工作所需的作业时间。
它具有以下五项主要因素:(1)正常的操作条件:工具条件及环境条件都符合作业内容要求并且不易引起疲劳。
(2)熟练程度:大多数中等偏上水平作业者的熟练度,作业员要了解流程,懂得机器和工具的操作与使用。
(3)作业方法:作业标准规定的方法。
(4)劳动强度与速度:适合大多数普通作业者的强度与速度。
(5)质量标准:以产品的质量标准为准,基本原则是操作者通过自检及互检完成。
2、标准工时的构成大多数的标准时间是由“标准主体作业时间”和“标准准备时间”构成。
此两项又分别由净作业时间和宽放时间构成。
如下图(1)标准主体作业时间与标准准备时间是完成匚作所必须进行的作业包括有效的机械作业以及事前准备和中间准备所消耗的时间。
两项净时间总和称为正常时间。
宽放时间普遍以相对于正常时间的比率,即宽放率的形式表示,标准时间的表述公式如下:图示:标准时间的构成标准时间二正常作业时间+宽放时间二正常作业时间*(1+宽放率)二净作业时间* (1+评定系数)* (1+宽放率)二、标准时间的设定标准时间的设定方法总体大致分为经验佔算及科学的时间分析与时间预置(PTS) 法等 对观测时间进行评比求得正常作业时间;对正常作业时间进行宽放,求得标准时间。
公式如下:标准时间二正常作业时间*(1+宽放率)二观测时间*评比系数* (1+宽放率)1、时间评比(Rating) (1) 时间评比介绍时间评比是一种判断与评价的技术,其U 的在于把实际作业时间修正到合理的作 业速度下的时间,消除因被测量人个人的工作态度、熟练度及环境因素对实测时间的 影响。
具体影响作业者的因素如图(2)所示。
作业标准化和标准作业组合表

SOP的制作要领
制作前准备 制作SOP SSOPP的的管管理理
1.SOP制作完成后,须经由上级确认,再由部门主管确认。(除制作者以 外,签名部分不可使用计算机打印)。
2. 每一个机种的SOP皆须有一份版本的目录,用以标明该机种于当时各 工作站最新SOP的版本情况。
3. 须有一份该机种SOP的变更记事,包含该机种全部SOP所有变更的事 项目录。
・对全员实施培训:要能按标准作业时间来做 ・在生产线的作业中尽量消除周期外作业 ・对于作业时间容易产生偏差的作业内容、对治具等下夫, 消除作业时间的偏差
(2)按要素作业单位,努力使标准作业时间 进一步缩短
技能图
作业流程
2005年 3月现在
1
2
3
【难易度和品质水平的例子】
卷
扎
绕
A : 难易度高,品质高
・完全不定期动作 例:不良的修改
时间观测
使用秒表和时间观测用紙
对象工程 No.
要素作业
时间观测用纸
观测年月日 观测时间
1 2 3 4 5 6 7 8 9 10 11 12 13 14 15 要素作业时间
分解号码
/
观测者
着眼点(机种更换时间)
・左手拿秒表和观测用纸 ・测量者能在一条直线上看到秒表和操作者
② 为了控制在节拍时间之内,按要素作業単位来进行作业的分 配
・节拍时间(秒/台)=稼动时间/计划生产台数
*通过①所计算出的人员(提高8%程度)增加的情况较多(由 于生产线平衡损失所带来的影响)
人员配置图
表示出现场的每天的人员配置图。
照片
使用标准作业表的改善的推进
(1)尽量能按标准作业时间来进行改善
10 胶带准备
安全生产标准化日程表

安全生产标准化日程表
一、安全生产标准化概述
安全生产标准化是指通过建立安全生产责任制,制定安全管理制度和操作规程,排查治理隐患和监控重大危险源,建立预防机制,规范生产行为,使各生产环节符合有关安全生产法律法规和标准要求,人、机、料、法、环处于良好的生产状态,并持续改进,不断加强企业安全生产规范化建设。
二、安全生产标准化日程表
XXXX年XX月XX日至XX月XX日
时间活动内容负责人
XX月XX日至XX日安全教育培训,包括安全生产法律法规、标准规范、规章制度等。
XX
XX月XX日至XX日现场检查,排查治理隐患,确保生产设备、设施安全运行。
XX
XX月XX日至XX日应急预案演练,提高应对突发事件的能力。
XX
XX月XX日至XX日安全绩效评估,对安全生产标准化工作进行总结和反思。
XX
三、安全生产标准化要求
1. 建立完善的安全生产责任制,明确各级管理人员和从业人员的安全职责。
2. 制定安全管理制度和操作规程,规范作业人员的行为。
3. 加强现场安全管理,排查治理隐患,确保生产设备、设施安全运行。
4. 建立应急预案体系,提高应对突发事件的能力。
5. 开展安全教育培训,提高从业人员的安全意识和技能。
6. 定期进行安全绩效评估,不断加强企业安全生产规范化建设。
四、安全生产标准化总结
通过本次安全生产标准化工作,企业应总结经验教训,不断完善安全管理体系,提高安全生产水平。
同时,要加强对从业人员的培训和教育,提高其安全意识和技能水平,确保企业安全生产稳定。