摩擦腐蚀基本知识
摩擦与润滑基本知识
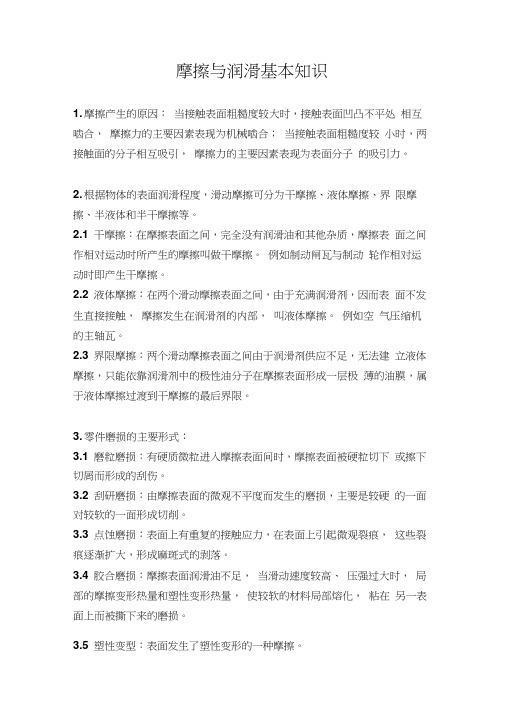
摩擦与润滑基本知识1. 摩擦产生的原因:当接触表面粗糙度较大时,接触表面凹凸不平处相互啮合,摩擦力的主要因素表现为机械啮合;当接触表面粗糙度较小时,两接触面的分子相互吸引,摩擦力的主要因素表现为表面分子的吸引力。
2. 根据物体的表面润滑程度,滑动摩擦可分为干摩擦、液体摩擦、界限摩擦、半液体和半干摩擦等。
2.1 干摩擦:在摩擦表面之间,完全没有润滑油和其他杂质,摩擦表面之间作相对运动时所产生的摩擦叫做干摩擦。
例如制动闸瓦与制动轮作相对运动时即产生干摩擦。
2.2 液体摩擦:在两个滑动摩擦表面之间,由于充满润滑剂,因而表面不发生直接接触,摩擦发生在润滑剂的内部,叫液体摩擦。
例如空气压缩机的主轴瓦。
2.3 界限摩擦:两个滑动摩擦表面之间由于润滑剂供应不足,无法建立液体摩擦,只能依靠润滑剂中的极性油分子在摩擦表面形成一层极薄的油膜,属于液体摩擦过渡到干摩擦的最后界限。
3. 零件磨损的主要形式:3.1 磨粒磨损:有硬质微粒进入摩擦表面间时,摩擦表面被硬粒切下或擦下切屑而形成的刮伤。
3.2 刮研磨损:由摩擦表面的微观不平度而发生的磨损,主要是较硬的一面对较软的一面形成切削。
3.3 点蚀磨损:表面上有重复的接触应力,在表面上引起微观裂痕,这些裂痕逐渐扩大,形成麻斑式的剥落。
3.4 胶合磨损:摩擦表面润滑油不足,当滑动速度较高、压强过大时,局部的摩擦变形热量和塑性变形热量,使较软的材料局部熔化,粘在另一表面上而被撕下来的磨损。
3.5 塑性变型:表面发生了塑性变形的一种摩擦。
3.6 金属表面的腐蚀:金属表面层氧化,变成松软多孔,易于脱落,丢失耐磨强度的状态。
实例一,摩擦的规律:同类纯金属间的摩擦因数比异类纯金属间和同类合金间的摩擦因数大得多。
4. 影响磨损的因素和减小磨损的途径4.1润滑:轴径与轴瓦建立液体摩擦的必要条件是a、合适的间隙配合,确保油膜形成;b润滑油充足,具备必要的压力和速度;c、轴径要有足够的转速;d、轴径与轴承配合表面的加工精度要适当;e、注油孔和油槽要设计在轴承承载区以外。
摩擦副 反应

摩擦副反应
摩擦副在运动过程中,除了物理磨损外,还可能发生化学或电化学反应导致的腐蚀磨损。
这种现象通常称为“摩擦化学”的一部分。
在摩擦副中,两个相对运动的接触表面可能会发生以下几种类型的反应:
1.氧化磨损:摩擦过程中,金属材料与空气中的氧气接触,产生氧化层,该氧化层可能因机械作用而脱落,从而造成磨损。
2.特殊介质腐蚀磨损:当摩擦副处于特定介质(如酸、碱、盐溶液或其他化学物质)中时,这些介质可能会与金属表面发生化学反应,加速磨损过程。
3.气蚀磨损:在流体动力润滑条件下,局部压力降低至饱和蒸汽压以下时,液体瞬间汽化并形成气泡,随后气泡破裂对金属表面造成冲击和疲劳,伴随有化学物质的作用,加剧磨损。
4.电化学腐蚀:在存在电解质的情况下,摩擦副之间的电位差可能引发电化学反应,形成腐蚀电池,使得低电位区域的金属受到腐蚀,增加磨损。
因此,在设计和选择摩擦副材料时,需要考虑材料的耐磨性、耐腐蚀性和在特定工作环境下的稳定性,以减少因化学反应引起的磨损失效,并优化润滑策略以延缓腐蚀磨损的发生。
摩擦、磨损与润滑概述

1、摩擦是引起能量损耗的主要原因。
2、摩擦是造成材料失效和材料损耗的主要原因。
3、摩擦学:
关于摩擦、磨损与润滑的学科(Tribology)
4、润滑是减小摩擦和磨损的最有效的手段。
§4-2 摩 擦
一、摩擦的概念:
正压力作用下,相互接触的两物体受切向外力的影 响而发生相对位移,或有相对滑动的趋势时,在接触 表面上就会产生抵抗滑动的阻力-摩擦。
Ff Ar B
Ar Ari A a b
干摩擦理论:
机械理论: 摩擦力是两表面凸峰的机械啮合力的总和。
分子理论: 产生摩擦的原因是表面材料分子间的吸引力作用。
分子-机械理论: 摩擦力是由两表面凸峰的机械啮合力和表
面分子相互吸引力两部分组成。
粘附理论:
阿蒙顿摩擦定律:
第一定律:摩擦力与法向载荷成正比。
R —0.4两粗糙面3.的0 综合不平混度合摩擦
3~4
流体摩擦
( 1 时,不平度凸峰为总载荷的30%)
流体摩擦:
1、定义:
当两摩擦面间的油膜厚度大到足以将两表面的不平凸峰完全 分开,这种摩擦叫液体摩擦。
2、特点:
3~4
①、油分子大都不受金属表面的吸附作用的支配,而能完全移动。
件上。润滑脂还可以用于简单的密封。
常用的润滑装置
常用润滑装置
一、间歇润滑装置
常用润滑装置
一、间歇润滑装置
常用润滑装置
二、间歇润滑装置
§4-5 流体润滑原理简介
英国的雷诺于1886年继前人观察到的流体动压现象流,体润总滑1 结出流体动压润滑理 论。20世纪50年代普遍应用电子计算机之后,线接触弹性流体动压润滑的理论开 始有所突破。
摩擦学原理(第4章磨损理论)
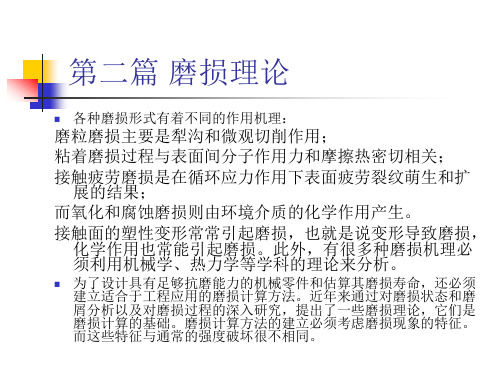
1.机械类 由摩擦过程中表面的机械作用产生的磨损,包括磨粒磨损、表面塑性 变形、脆性剥落等,其中磨粒磨损是最普遍的机械磨损形式。 2.分子-机械类 由于分子力作用形成表面粘着结点,再经机械作用使粘着结点剪切所 产生的磨损,这类磨损的主要形式就是粘着磨损。 3.腐蚀-机械类 这类磨损是由介质的化学作用或电化学作用引起表面腐蚀,而摩擦中 的机械作用加速腐蚀过程,它包括氧化磨损和化学腐蚀磨损。
为了设计具有足够抗磨能力的机械零件和估算其磨损寿命,还必须 建立适合于工程应用的磨损计算方法。近年来通过对磨损状态和磨 屑分析以及对磨损过程的深入研究,提出了一些磨损理论,它们是 磨损计算的基础。磨损计算方法的建立必须考虑磨损现象的特征。 而这些特征与通常的强度破坏很不相同。
第四章 磨损机理
表4.1磨损类型
分类 磨损机理 1.粗糙峰变形或去除 2.犁沟导致的磨损 3.剥层磨损 主要由材料的机械行为引起的磨损 4.粘着磨损 5.磨料磨损 6.微动磨损 7.固体颗粒冲击引起的磨损 1.腐蚀磨损 2.氧化磨损 主要由材料的化学行为引起的磨损 3.扩散磨损 4.表面层溶解引起的磨损 5、高温下的粘着磨损 磨损常数K(范围) 10-4 10-4 10-4 10-4 10-2~10-1 10-6~10-4
第二篇 磨损理论
各种磨损形式有着不同的作用机理:
磨粒磨损主要是犁沟和微观切削作用; 粘着磨损过程与表面间分子作用力和摩擦热密切相关; 接触疲劳磨损是在循环应力作用下表面疲劳裂纹萌生和扩 展的结果; 而氧化和腐蚀磨损则由环境介质的化学作用产生。 接触面的塑性变形常常引起磨损,也就是说变形导致磨损, 化学作用也常能引起磨损。此外,有很多种磨损机理必 须利用机械学、热力学等学科的理论来分析。
第2章摩擦、磨损及润滑概述2知识分享
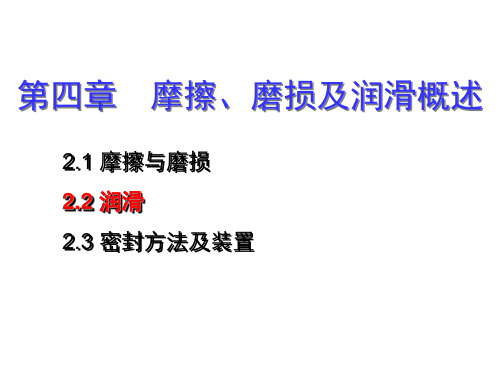
(4)飞溅润滑装置
• 当回转件的圆周速度较大 (5m/s<v<12m/s)时,润 滑油飞溅雾化成小滴飞起 ,直接散落到需要润滑的 零件上,或先溅到集油器 中,然后经油沟流入润滑 部位,这种润滑方式称为 飞溅润滑。
• 齿轮减速器中的轴承常采 用这种润滑方法
粘度与温度和压力的关系
1. 粘度与温度的关系
• 粘度随温度的升高而降低 • 粘度随温度变化小,粘-温性
能好。
2. 粘度与压力的关系
• 只有在压力超过20MPa时,粘 度才随压力的增大而增大, 高压时更明显。
2.2.1.2 润滑脂的分类和主要质量 指标
• 润滑脂是在润滑油中加入稠化剂(如钙、钠、锂等 金属皂基)而形成的脂状润滑剂,又称为黄油或 干油。
2.2.2 润滑方法和润滑装置
• 机械设备的润滑,主要集中在传动件和支承 件上,各零部件的润滑将在相关章节中学习 ,这里仅介绍常见的润滑方法和润滑装置
• 机器的润滑方法有分散润滑和集中润滑两大 类。
• 分散润滑是各个润滑点各自单独润滑,这种 润滑可以是间断的或连续的,压力润滑或无 压力润滑
• 集中润滑是一台机器的许多润滑点由一个润 滑系统同时润滑
恩氏度(˚ Et) ——中国惯用 常用的有: 赛氏通用秒(SUS) ——美国惯用
雷氏秒 ——英国惯用
运动粘度与条件粘度之间的换算关系:
当 1 .3 5 E t≤ 3 .2 时 V t , 8 .0 E t 8 .E 6 t 4cSt 当 E t 3 .2 时, V t 7 .6 E t 4 E .0 t cSt 当 ° E t> 1 .2 时 6 , V t= 7 .1 ° E t4 cSt
摩擦.磨损.润滑及润滑剂概论
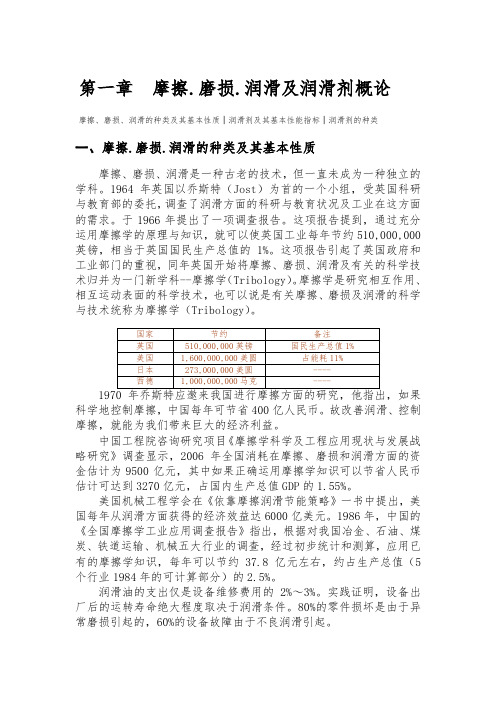
第一章摩擦.磨损.润滑及润滑剂概论摩擦、磨损、润滑的种类及其基本性质│润滑剂及其基本性能指标│润滑剂的种类一、摩擦.磨损.润滑的种类及其基本性质摩擦、磨损、润滑是一种古老的技术,但一直未成为一种独立的学科。
1964年英国以乔斯特(Jost)为首的一个小组,受英国科研与教育部的委托,调查了润滑方面的科研与教育状况及工业在这方面的需求。
于1966年提出了一项调查报告。
这项报告提到,通过充分运用摩擦学的原理与知识,就可以使英国工业每年节约510,000,000英镑,相当于英国国民生产总值的1%。
这项报告引起了英国政府和工业部门的重视,同年英国开始将摩擦、磨损、润滑及有关的科学技术归并为一门新学科--摩擦学(Tribology)。
摩擦学是研究相互作用、相互运动表面的科学技术,也可以说是有关摩擦、磨损及润滑的科学与技术统称为摩擦学(Tribology)。
科学地控制摩擦,中国每年可节省400亿人民币。
故改善润滑、控制摩擦,就能为我们带来巨大的经济利益。
中国工程院咨询研究项目《摩擦学科学及工程应用现状与发展战略研究》调查显示,2006年全国消耗在摩擦、磨损和润滑方面的资金估计为9500亿元,其中如果正确运用摩擦学知识可以节省人民币估计可达到3270亿元,占国内生产总值GDP的1.55%。
美国机械工程学会在《依靠摩擦润滑节能策略》一书中提出,美国每年从润滑方面获得的经济效益达6000亿美元。
1986年,中国的《全国摩擦学工业应用调查报告》指出,根据对我国冶金、石油、煤炭、铁道运输、机械五大行业的调查,经过初步统计和测算,应用已有的摩擦学知识,每年可以节约37.8亿元左右,约占生产总值(5个行业1984年的可计算部分)的2.5%。
润滑油的支出仅是设备维修费用的2%~3%。
实践证明,设备出厂后的运转寿命绝大程度取决于润滑条件。
80%的零件损坏是由于异常磨损引起的,60%的设备故障由于不良润滑引起。
中国每1000美元产值消耗一次性能源(折合石油)为日本的5.6倍,电力为日本的2.77倍,润滑油耗量为日本的3.79倍。
第一章 摩擦学基础知识(润滑)

三、润滑脂及其主要性能 • 组成:基础油+稠化剂+添加剂+澎润土 • 润滑脂的性能指标主要有针入度、滴点、析 油量、机械杂质、灰分、水分等
1)针入度 软硬程度 H(mm)/0.1
h
阻力大小、流动性强弱
标准锥体,150g,25 ℃ ,5s
2)滴点----固体 流体的温度转折点,表示耐热性 3)防水性能; 4)静音性能; 5)种类 A)钙基脂:抗水,适于轻中重载荷; B)钠基脂:高温,但不抗水; C)锂基脂:多用途,最好; D)铝基脂:高度耐水性,航运机械 E)其它特种润滑脂(特种合成油、添加剂、 稠化剂等)
五、添加剂 • 作用越来越大,在润滑脂、合成油中不加添加剂,
六、对润滑剂的要求
较低的摩擦系数 良好的吸附和渗入能力 有一定的黏度 有较高的纯度和抗氧化性 没有腐蚀性 有良好的导热性和较大的热容量
七、润滑装置 单体供油装置 油壶, 油杯,
油枪
油杯
压配式油杯
滴油式油杯
油芯式油杯
油环
油链
• 集中供油装置 a) 简单的少数点位集中供油 b) 设备中心、车间及工厂级集中供油 泵站+(稳压+冷却)+过滤+分配器+工位润滑
η t = η0 ( t0 / t )
m
2、润滑油的粘压特性
• 粘度和压力的关系近 似表示为:
η = η0 e
ap
粘温关系曲线
3、油性—反映在摩擦表面的吸附性能 油性 (边界润滑和粗糙表面尤其重要) 4、闪点—瞬时燃烧和碳化的温度; 闪点 燃点—长时间连续燃烧的温度(高温性能); ; 燃点 5、凝点—冷却,由液体转变为不能流动的临界 凝点 温度; (低温启动性能) 6、极压性(EP), 在重压下表面膜破裂的最大 极压性(EP) 接触载荷,用PB表示,(极限载荷) 7、酸值—限制润滑剂变质后对表面的腐蚀 酸值
摩擦腐蚀测试方法

摩擦腐蚀测试方法嘿,朋友们!今天咱就来聊聊摩擦腐蚀测试方法。
这玩意儿啊,就好比是一场特殊的战斗,只不过战斗的双方不是人,而是各种材料和环境因素。
你想想看,材料在使用过程中,那可不得经常和其他东西摩擦啊。
就像咱走路,鞋底不就老是和地面摩擦嘛。
这一摩擦,要是材料质量不过关,那可就容易出问题啦,就跟咱走路走多了鞋底磨破了一个道理。
摩擦腐蚀测试,就是要看看这些材料能不能经得住这样的考验。
那怎么测试呢?这可得有一套专门的办法。
首先呢,得有个合适的试验装置,这就像是给这场战斗准备一个合适的场地。
这个装置得能模拟出实际使用中的摩擦情况,不能太简单了,不然测出来的数据没啥用呀。
然后呢,选择要测试的材料,这就是咱的“主角”啦。
把它放在装置里,让它开始接受摩擦和腐蚀的双重挑战。
这就好比让一个人去爬山,又要克服陡峭的山路,又要应对多变的天气。
在测试的过程中,可得时刻关注着材料的变化。
看看它表面有没有磨损呀,有没有出现腐蚀的迹象呀。
这就像咱关注自己的身体一样,要是有点不舒服就得赶紧想办法。
测试的时间也很关键哦!太短了可能发现不了问题,太长了又太浪费时间和资源。
这就跟做饭似的,火候掌握不好,饭菜就不香。
而且啊,不同的材料需要不同的测试方法呢。
就像每个人的性格不一样,对待的方式也得不一样。
有的材料可能比较脆弱,那就得小心点测试;有的材料很坚强,那就可以加大点难度。
摩擦腐蚀测试方法可真是个神奇的东西呀!它能帮我们找到那些真正耐用的材料,让我们在使用各种物品的时候更加放心。
你说要是没有这个测试方法,那我们用的东西说不定经常出问题呢。
想象一下,你买了双新鞋,没走几天鞋底就掉了,多烦人啊!或者汽车的零件没用多久就坏了,那多危险呀!所以说呀,摩擦腐蚀测试方法真的太重要啦!咱可得重视这个摩擦腐蚀测试方法,让它为我们的生活保驾护航。
让那些质量不过关的材料无处遁形,让我们用上真正好的东西。
这就是摩擦腐蚀测试方法的魅力所在呀!原创不易,请尊重原创,谢谢!。
摩擦学基本知识

H
4. 润 滑
• 是减少机械零部件磨损、延长使用寿命的有效措施。 • 为了减少机器的磨损和发热,保证安全运转,延长使用寿 命和降低能源的消耗,摩擦副表面间进行润滑。主要的 润滑剂为液体润滑油。 • 据推算,全世界用于动力的能源,约有30%~40%消耗在无
损就是一种复合磨损形式。在实际工程中,应抓住主 要的磨损形式,才能采取有效措施,以减少磨损,延 长寿命。 • 3.2 磨损规律及影响因素 • 机器零件的工作过程分为三个阶段:跑合阶段、稳定 磨损阶段、急剧磨损阶段。应尽可能延长稳定磨损阶 段。
• 磨损的影响因素主要有:材料、表面硬度、滑动速度
、载荷、表面温度、表面粗糙度、表面粘附物以及润 滑等。
(a) 一般情况;(b) 表面平行时
流体摩擦(润滑)
H • ③.边界摩擦:相对运动的表面之间存在极薄分子膜。
• 特点:极薄边界膜(厚度20纳米左右)起润滑作用,有 能力防止表面微凸体之间相互接触而不破坏,起良好的 润滑作用。但强度低,易破裂。
(a) 单分子层边界润滑模型;(b) 边界润滑机理模型 边界摩擦(润滑)
料的极限使用温度;f∝1/Pg,f∝V,而碳石墨和铸铁由于自
润滑性好,其规律与塑性相反。
H
摩擦工况
润滑状态 粘度影响 (μ)
表:各种摩擦状态及其特征对比
干摩擦
无
边界摩擦
分子吸附膜
混合摩擦
部分
流体摩擦
全部
无
无
部分
起决定作用
过程特征
微凸起接触
分子层、分子机 械作用
混合
流体动静压效 应
摩擦系数大小
0.1~0.6
• ④.微动磨损:两个表面之间由于振幅很小的相对运 动而产生的磨损。
金属加工润滑基础知识之一摩擦学

金属加工润滑基础知识之一摩擦学金属加工润滑基础知识之一摩擦学摩擦学的三个方面:摩擦、磨损、润滑摩擦:相互接触的物体在相对运动时或具有相对运动的趋势时,接触面间发生阻碍相对运动的现象,称为摩擦。
所产生阻碍其相对运动的阻力称之为摩擦力。
特征:摩擦阻力、摩擦热量、材料磨损摩擦种类:(按摩擦副表面的润滑状态分类)1、干摩擦:在没有任何润滑剂的条件下,两物体表面间的摩擦。
2、液体摩擦:又称流体摩擦。
是发生在液体内部的一种摩擦现象,包括纯液体流动时的摩擦和液体将金属表面隔开时的摩擦。
一般来讲,这层液体的厚度在2微米以上。
3、边界摩擦:当固体表面不是被一层液体隔开,而是被一层很薄的吸附油膜隔开,或是被一层具有分层结构和润滑性能的边界膜隔开时的摩擦,称为边界摩擦。
这层膜的厚度一般在0.1-1微米以下。
4、混合摩擦:物体相对运动时,由于它的表面粗糙度不同,当凸起较高的部分发生边界摩擦时,凸起较低的部分处于液体摩擦状态或半液体摩擦中,当凸起较低的部分处于边界摩擦时,凸起较高的部分因挤压较剧烈会导致边界膜破烈,其表面直接接触发生局部干摩擦、半干摩擦。
磨损:定义:相互接触的物体在相对运动时,表层材料不断发生的损耗的过程,或者产生残余变形的现象。
磨损的三个阶段:磨合、稳定磨损、急剧磨损磨损的类型:1、粘附磨损:接触表面相对运动时,由于分子间的吸引力作用而产生粘附连接,致使材料从表面脱掉的磨损。
2、磨料磨损:接触表面相对运动时,由于硬质颗粒或较硬表面上的微凸体,在摩擦过程中的“梨削”“切削”“磨削”作用引起表面擦伤,表层材料脱落或分离出碎屑和其他磨粒。
3、疲劳磨损:两个相互作用的摩擦表面,由于表层材料疲劳,产生微观裂纹并分离出磨粒和碎片剥落,形成凹坑,造成磨损。
4、腐蚀磨损:摩擦副在第三介质的作用下发生的腐蚀磨损,比如:润滑油酸化变质产生的酸性油泥;手汗;潮湿空气中的氧、二氧化硫、硫化氢等等。
磨损的影响因素:1、润滑对磨损的影响(降低摩擦系数,液体润滑时能防止粘附磨损,洁净润滑能减少磨料磨损;有防锈性能的润滑剂能减少腐蚀磨损)2、材料性能对磨损的影响(材料的硬度和韧性;硬度决定表面抵抗能力,过高硬度易产生碎屑,产生磨料磨损。
微动摩擦腐蚀 标准
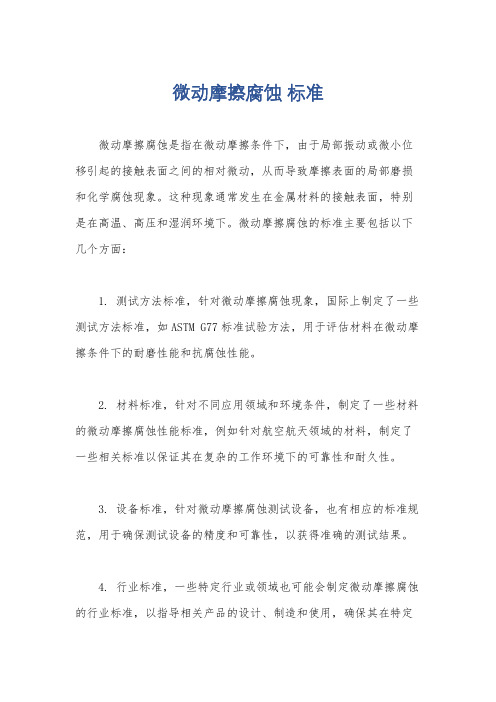
微动摩擦腐蚀标准
微动摩擦腐蚀是指在微动摩擦条件下,由于局部振动或微小位移引起的接触表面之间的相对微动,从而导致摩擦表面的局部磨损和化学腐蚀现象。
这种现象通常发生在金属材料的接触表面,特别是在高温、高压和湿润环境下。
微动摩擦腐蚀的标准主要包括以下几个方面:
1. 测试方法标准,针对微动摩擦腐蚀现象,国际上制定了一些测试方法标准,如ASTM G77标准试验方法,用于评估材料在微动摩擦条件下的耐磨性能和抗腐蚀性能。
2. 材料标准,针对不同应用领域和环境条件,制定了一些材料的微动摩擦腐蚀性能标准,例如针对航空航天领域的材料,制定了一些相关标准以保证其在复杂的工作环境下的可靠性和耐久性。
3. 设备标准,针对微动摩擦腐蚀测试设备,也有相应的标准规范,用于确保测试设备的精度和可靠性,以获得准确的测试结果。
4. 行业标准,一些特定行业或领域也可能会制定微动摩擦腐蚀的行业标准,以指导相关产品的设计、制造和使用,确保其在特定
环境下具有良好的微动摩擦腐蚀性能。
总的来说,微动摩擦腐蚀标准涵盖了测试方法、材料、设备和行业等多个方面,旨在保证材料和设备在微动摩擦条件下具有良好的耐磨性和抗腐蚀性能,以满足不同工作环境的需求。
这些标准的制定和遵循有助于提高产品的质量和可靠性,促进相关行业的健康发展。
机械设计----摩擦

第三章 磨擦、磨损及润滑(一)教学要求掌握摩擦副分类及基本性质、磨损过程和机理及润滑的类型及润滑剂类型。
(二)教学的重点与难点摩擦副基本性质和典型磨损过程(三)教学内容§3—1 摩擦摩擦——两接触的物体在接触表面间相对滑动或有一趋势时产生阻碍其发生相对滑动的切向阻力,——这种现角叫磨擦磨损——由于摩擦引起的摩擦能耗和导致表面材料的不断损耗或转移,即形成磨损。
使零件的表面形状与尺寸遭到缓慢而连续破坏→精度、可靠性↓效率↓直至破坏润滑——减少摩擦、降低磨损的一种有效手段。
摩擦学(Tribology )——包含力学、流变学、表面物理、表面化学及材料学、工程热物理学等学科,是一门边缘和交叉学科。
摩擦 内摩擦——发生在物质内部外摩擦——两个相互接触表面之间的摩擦接运动状态——摩擦 静摩擦——仅有相对滑动趋势时的摩擦动摩擦本节只讨论金属摩擦副的滑动摩擦根据摩擦面间存在润滑剂的状况,干摩擦 ——最不利滑动摩擦 边界摩擦(边界润滑) ——最低要求流体摩擦(流体润滑) ——如图3-1所示混合摩擦(混合润滑) ——最理想各种状态下的摩擦系数见表3-1,图3-2为摩擦特性曲线p v f /ηλ=-的关系。
一、干摩擦——两摩擦表面直接接触,不加入任何润滑剂的摩擦而实际上,即使很洁净的表面上也存在脏污膜和的氧化膜,∴实际f 比在真空中测定值小很多。
摩擦理论:①库仑公式 n f fF F =(n F —法向力)——至今沿用机理:②机械摩擦理论→认为两个粗糙表面接触时,接触点相互啮合,摩擦力为啮合点问切向阻力的总和,表面越粗糙,摩擦力就越大。
但不能解释光滑表面间的摩擦现象——表面愈光滑、接触面越大,f F 越大,且与滑动速度V 有关。
③新理论:分子—机械理论、能量理论、粘着理论—常用简单粘着理论:如图3-3所示,摩擦副真实接触面积Ar 只有表现接触面积A 的百分之一和万分之一,)10000~100/(A Ar =,∴接触面上压力很大,很容易达到材料的压缩屈服极限sy σ→产生塑性流动→接触面↑,∴n F ↑应力并不升高 ∴sy nF Ar σ= (3-1)接触点塑性变形后→脏污膜遭破坏,容易使基本金属产生粘着现象→产生冷焊结点→滑动时,先将结点切开,设结点的剪切强度极限为B τ,则摩擦力为B sy nB r f F A F τστ== (3-2) ∴金属摩擦系数syB n fF F f στ== (3-3) B τ 两接触金属中较软者的剪切强度——剪切发生在软金属站界面的剪切强度极限B f f B ττττ<<=,(脏污表面)——剪切发生在结点金属上 sy σ——较硬的基本材料的压缩屈服极限∵大多数金属sy B στ/很相近,∴f 很相近∴降低摩擦系数的措施:在硬金属基体表面涂覆一层极薄的软金属(使)sy σ取决于基体材料,B τ取决于软金属。
摩擦腐蚀基本知识

22
犁沟变形模型如图:
23
图2-11 因塑性变形发生去除的两种机制 (a)犁沟;(b) 微观切屑;(c)切屑模型
24
图1-4 磨料磨损机制
25
迎角(也叫冲角)是指磨料前面与材料表面间的 夹角(下图示)。 磨料能否切削材料与迎角α有关,只有当迎角大 于临界迎角时,才能产生切屑;反之,如果迎 角小于临界迎角,则只能产生塑性犁沟,将材 料推向沟槽的两侧及前沿。
剧增大。精度降低、间隙增大,温度升高, 产生冲击、振动和噪声,最终导致零部件完 全失效。
43
非典型磨 损曲线
44
磨损特性曲线----浴盆曲线
典型浴 盆曲线
45
1) 粘着磨损的分类
46
五类典型粘着磨损
(1)轻微磨损:
粘着结合强度比摩擦副基体金属抗剪切强度都低, 剪切破坏发生在粘着结合面上,表面转移的材料较 轻微。
40
(1)
磨合阶段:磨损量随时间的增加而增加。出 现在初始运动阶段,由于表面存在粗糙度, 微凸体接触面积小,接触应力大,磨损速度 快。
41
(2)稳定磨损阶段:摩擦表面磨合后达到稳定状
态,磨损率保持不变。标志磨损条件保持相 对稳定,是零件整个寿命范围内的工作过程。
42
(3) 剧烈磨损阶段:工作条件恶化,磨损量急
Why?
当摩擦副材料性能接近,并且摩擦表面硬度较低时,往 往容易产生胶合而导致摩擦副损坏。 采用性能相差较大的材料作摩擦副 如果所采用的摩擦副材料性能接近时,如齿轮摩擦副, 则通常使表面具有较高的硬度。
10
2.表面粗糙度
当摩擦表面的粗糙度发生变化时,会导致摩擦机理 的改变 对于粗糙表面,以机械啮合为主;对于光滑表面, 以黏附为主。 当摩擦副表面非常粗糙时,摩擦系数较大。然而非 常平滑的表面可能摩擦系数更大,这是因为真实接 触面积增大,表面间的分子作用加强。 一般说来,摩擦副存在一最佳粗糙度区间,在这一 间内,所产生的摩擦系数最小。
医疗器械腐蚀的主要原因及处理原则

医疗器械腐蚀的主要原因及处理原则一、定义:金属(通常是铁)由于长期暴露在空气中发生了氧化反应,或者是被水中的氧元素侵蚀而生成红色氧化物的过程,称作为腐蚀。
二、种类:表面腐蚀、外来腐蚀、摩擦腐蚀、点状腐蚀和应力裂纹腐蚀。
(一)表面腐蚀1.概念及主要原因由于与湿气、冷凝水、血液残留或酸性/碱性液体长时间接触,而造成手术器械表层开始出现红色到红棕色,斑点状或片状腐蚀的现象通常称为表面腐蚀。
2.危害表面腐蚀如不做合适的处理则会进一步发展称为点状腐蚀和应力裂纹腐蚀。
3.处理原则清洁润滑(二)外来腐蚀1.概念及主要原因当生锈的器械或设备上的锈(硫松的氧化铁),通过各种途径接触到另一个没有生锈的器械表面时,凹凸不平、易吸收水分的氧化铁颗粒会在器械表面营造处一个潮湿的环境,不锈钢表面的氧化铬钝化层会因此收到破坏,从而使器械表面及内部开始形成新的腐蚀。
2.危害外来腐蚀如不做合适的处理则会进一步发展称为点状腐蚀和应力裂纹腐蚀。
3.处理原则清洁润滑或专业维修机构处理;更换(三)摩擦腐蚀1.概念及主要原因润滑不足或夹带杂物,导致其使用活动时金属面与金属面直接相互摩擦,从而造成金属面的严重磨损并损坏表面钝化层。
2.危害不做合适的处理则会进一步发展,并严重影响器械的正常使用(如手术剪无法正常剪切)。
3.处理原则初期——润滑保养;严重——专业处理。
(四)点状腐蚀1.概念及主要原因手术器械表面出现针孔状的黑色小洞。
2.危害易藏有细菌和细菌芽孢,因此存在卫生学的风险;降低器械的金属机械强度。
3.处理原则及时更换;原因排查(五)应力裂纹腐蚀1.概念存在有腐蚀情况(通常为点状腐蚀)的手术器械因为施加应力的原因,在原有的腐蚀点处出现裂纹或断裂的情况,称为应力裂纹腐蚀。
2.危害手术器械功能的完全丧失;术中器械残片的脱落。
3.处理原则必须立即更换,以避免在术中产生意外风险。
磨损基本类型
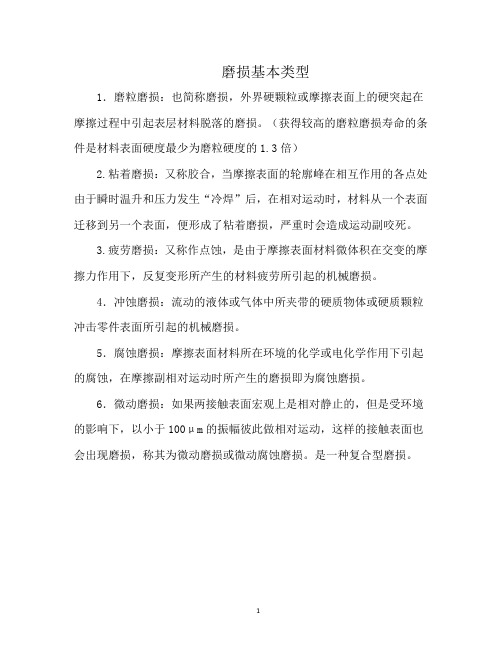
磨损基本类型
1.磨粒磨损:也简称磨损,外界硬颗粒或摩擦表面上的硬突起在摩擦过程中引起表层材料脱落的磨损。
(获得较高的磨粒磨损寿命的条件是材料表面硬度最少为磨粒硬度的1.3倍)
2.粘着磨损:又称胶合,当摩擦表面的轮廓峰在相互作用的各点处由于瞬时温升和压力发生“冷焊”后,在相对运动时,材料从一个表面迁移到另一个表面,便形成了粘着磨损,严重时会造成运动副咬死。
3.疲劳磨损:又称作点蚀,是由于摩擦表面材料微体积在交变的摩擦力作用下,反复变形所产生的材料疲劳所引起的机械磨损。
4.冲蚀磨损:流动的液体或气体中所夹带的硬质物体或硬质颗粒冲击零件表面所引起的机械磨损。
5.腐蚀磨损:摩擦表面材料所在环境的化学或电化学作用下引起的腐蚀,在摩擦副相对运动时所产生的磨损即为腐蚀磨损。
6.微动磨损:如果两接触表面宏观上是相对静止的,但是受环境的影响下,以小于100μm的振幅彼此做相对运动,这样的接触表面也会出现磨损,称其为微动磨损或微动腐蚀磨损。
是一种复合型磨损。
1。
摩擦副磨损腐蚀
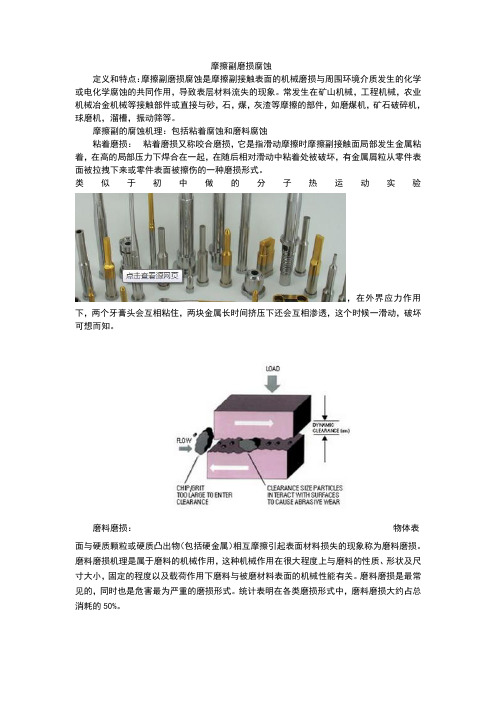
摩擦副磨损腐蚀
定义和特点:摩擦副磨损腐蚀是摩擦副接触表面的机械磨损与周围环境介质发生的化学或电化学腐蚀的共同作用,导致表层材料流失的现象。
常发生在矿山机械,工程机械,农业机械冶金机械等接触部件或直接与砂,石,煤,灰渣等摩擦的部件,如磨煤机,矿石破碎机,球磨机,溜槽,振动筛等。
摩擦副的腐蚀机理:包括粘着腐蚀和磨料腐蚀
粘着磨损:粘着磨损又称咬合磨损,它是指滑动摩擦时摩擦副接触面局部发生金属粘着,在高的局部压力下焊合在一起,在随后相对滑动中粘着处被破坏,有金属屑粒从零件表面被拉拽下来或零件表面被擦伤的一种磨损形式。
类似于初中做的分子热运动实验
,在外界应力作用下,两个牙膏头会互相粘住,两块金属长时间挤压下还会互相渗透,这个时候一滑动,破坏可想而知。
磨料磨损:物体表面与硬质颗粒或硬质凸出物(包括硬金属)相互摩擦引起表面材料损失的现象称为磨料磨损。
磨料磨损机理是属于磨料的机械作用,这种机械作用在很大程度上与磨料的性质、形状及尺寸大小,固定的程度以及载荷作用下磨料与被磨材料表面的机械性能有关。
磨料磨损是最常见的,同时也是危害最为严重的磨损形式。
统计表明在各类磨损形式中,磨料磨损大约占总消耗的50%。
现实生活中,我们在防护金属上使用一层保护膜,保护膜如何被破坏?绝大多数都是依靠我们的机械磨损,只有磨掉了保护膜,其他的电偶腐蚀,点蚀,缝隙腐蚀,晶间腐蚀,选择性腐蚀才能发生,所以说,磨损腐蚀是最牛逼的。
磨蚀 电化学
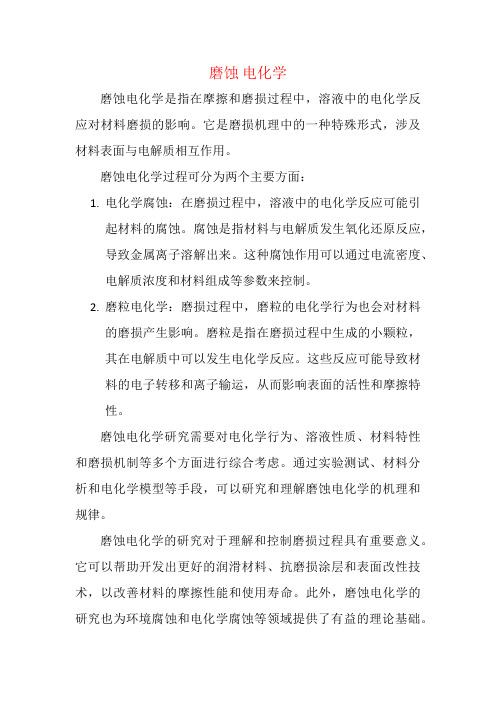
磨蚀电化学
磨蚀电化学是指在摩擦和磨损过程中,溶液中的电化学反应对材料磨损的影响。
它是磨损机理中的一种特殊形式,涉及材料表面与电解质相互作用。
磨蚀电化学过程可分为两个主要方面:
1.电化学腐蚀:在磨损过程中,溶液中的电化学反应可能引
起材料的腐蚀。
腐蚀是指材料与电解质发生氧化还原反应,导致金属离子溶解出来。
这种腐蚀作用可以通过电流密度、电解质浓度和材料组成等参数来控制。
2.磨粒电化学:磨损过程中,磨粒的电化学行为也会对材料
的磨损产生影响。
磨粒是指在磨损过程中生成的小颗粒,
其在电解质中可以发生电化学反应。
这些反应可能导致材
料的电子转移和离子输运,从而影响表面的活性和摩擦特
性。
磨蚀电化学研究需要对电化学行为、溶液性质、材料特性和磨损机制等多个方面进行综合考虑。
通过实验测试、材料分析和电化学模型等手段,可以研究和理解磨蚀电化学的机理和规律。
磨蚀电化学的研究对于理解和控制磨损过程具有重要意义。
它可以帮助开发出更好的润滑材料、抗磨损涂层和表面改性技术,以改善材料的摩擦性能和使用寿命。
此外,磨蚀电化学的研究也为环境腐蚀和电化学腐蚀等领域提供了有益的理论基础。
刷油、防腐蚀、绝热工程的基本知识

刷油、防腐蚀、绝热工程的基本知识一、引言刷油、防腐蚀和绝热工程是在工业领域中常见的技术应用。
它们在许多行业中起着重要的作用,如石油化工、电力、冶金等。
本文将介绍刷油、防腐蚀和绝热工程的基本知识,包括定义、应用范围、原理、材料等方面。
二、刷油工程1. 定义:刷油工程是指利用刷油设备和技术对机械设备表面进行润滑油的涂刷,以减少磨损和摩擦,延长设备寿命的一种工程技术。
2. 应用范围:刷油工程广泛应用于各种机械设备,如发动机、减速器、轴承等。
它可以减少设备在运行过程中的能量损耗和磨损,提高设备的工作效率和可靠性。
3. 原理:刷油工程的原理是通过润滑油的涂刷,形成一层油膜,降低设备表面之间的摩擦系数,减少能量损耗和磨损。
4. 材料:刷油工程使用的润滑油一般为合成油或矿物油,根据设备的要求选择不同的油品。
刷油设备包括刷油器、刷油盘、刷油毛等。
三、防腐蚀工程1. 定义:防腐蚀工程是指在设备和结构表面涂覆一层具有防腐蚀性能的材料,以保护设备和结构不受腐蚀的一种工程技术。
2. 应用范围:防腐蚀工程广泛应用于金属设备和结构,如钢结构、管道、储罐等。
它可以防止设备和结构在恶劣环境中受到腐蚀,延长使用寿命。
3. 原理:防腐蚀工程的原理是通过涂覆防腐蚀材料,形成一层保护膜,隔绝设备和结构与外界环境的接触,防止腐蚀介质的侵蚀。
4. 材料:防腐蚀工程使用的防腐蚀材料有机涂料、无机涂料、防腐蚀涂料等,根据设备和结构的要求选择不同的材料。
四、绝热工程1. 定义:绝热工程是指在设备和管道表面涂覆一层具有隔热性能的材料,以减少能量损失和热传导的一种工程技术。
2. 应用范围:绝热工程广泛应用于热力设备和管道,如锅炉、热交换器、蒸汽管道等。
它可以减少能量损失,提高设备的热效率。
3. 原理:绝热工程的原理是通过涂覆隔热材料,减少设备和管道表面与外界环境之间的热传导,降低能量损失。
4. 材料:绝热工程使用的隔热材料有矿棉、硅酸盐毡、泡沫塑料等,根据设备和管道的要求选择不同的材料。
- 1、下载文档前请自行甄别文档内容的完整性,平台不提供额外的编辑、内容补充、找答案等附加服务。
- 2、"仅部分预览"的文档,不可在线预览部分如存在完整性等问题,可反馈申请退款(可完整预览的文档不适用该条件!)。
- 3、如文档侵犯您的权益,请联系客服反馈,我们会尽快为您处理(人工客服工作时间:9:00-18:30)。
4.速度
当摩擦表面的相对滑动速度发生变化时,表 面微凸体的变形速度、变形程度和表面温度 都将发生受化,从而导致摩擦系数发生变化。 因此,速度对摩擦系数的影响,受多种因素 制约,往往需要针对具体的摩擦副,通过试 验确定。
13
5.表面膜
摩擦副接触表面膜一般由氧化膜、吸附膜和其他污染薄 膜等组成,其存在会极大地影响摩擦副的摩擦特性。 如在干摩擦表面加入润滑油后会使摩擦系数显著降 低。 当摩擦副材料表面存在表面膜时,由于摩擦主要发 生在表面膜之间,同时一般情况下表面膜的剪切强 度小于本体材料的剪切强度,因此摩擦系数较小。 生产中常常在摩擦副材料表面涂覆一层软金属(如铟、 镉、铅等)或表面膜(如硫化膜、氧化膜、磷化膜等)以 降低摩擦系数,减少材料的摩擦与磨损。 表面膜的厚度对摩擦系数有显著影响,通常存在者 一个最佳的膜厚范围,太薄或太厚都会使摩擦增大。
40
(1)
磨合阶段:磨损量随时间的增加而增加。出 现在初始运动阶段,由于表面存在粗糙度, 微凸体接触面积小,接触应力大,磨损速度 快。
41
(2)稳定磨损阶段:摩擦表面磨合后达到稳定状
态,磨损率保持不变。标志磨损条件保持相 对稳定,是零件整个寿命范围内的工作过程。
42
(3) 剧烈磨损阶段:工作条件恶化,磨损量急
20
微切削磨损
图2-2 a) 微切削磨损在钢表面产生的切削痕 b) 钢的微切屑形貌
图2-3 (a) 典型微切屑;
(b) 滑移变形形成的皱褶
21
2.犁沟变形机理
当磨粒的形状与位向不利于切削时,磨粒将使材料 产生犁沟变形,即将材料推向前方或两侧并使沟底 及沟槽附近的材料产生塑性变形。 后继的磨粒可能把堆积起来的材料压平,也可能使 已经犁沟变形的材料遭受再一次的犁沟变形,如此 反复,将导致材料的加工硬化和其他强化作用,最 后产生裂纹、断裂而形成磨屑。
14
2.1.2 磨损基本知识
磨损定义:由于机械作用,有时伴有化学或 电的作用物体工作表面材料作相对运动过程 中不断损耗的现象。 大多数材料配副的摩擦系数介于0.1~1.0之 间,而其磨损率却相差很多数量级。
按磨损机理分四大类:磨料磨损,冲蚀磨损, 粘着磨损和疲劳磨损。
15
表2.1 磨损的基本类型P39
剧增大。精度降低、间隙增大,温度升高, 产生冲击、振动和噪声,最终导致零部件完 全失效。
43
非典型磨 损曲线
44
磨损特性曲线----浴盆曲线
典型浴 盆曲线
45
1) 粘着磨损的分类
46
五类典型粘着磨损
(1)轻微磨损:
粘着结合强度比摩擦副基体金属抗剪切强度都低, 剪切破坏发生在粘着结合面上,表面转移的材料较 轻微。
Why?
当摩擦副材料性能接近,并且摩擦表面硬度较低时,往 往容易产生胶合而导致摩擦副损坏。 采用性能相差较大的材料作摩擦副 如果所采用的摩擦副材料性能接近时,如齿轮摩擦副, 则通常使表面具有较高的硬度。
10
2.表面粗糙度
当摩擦表面的粗糙度发生变化时,会导致摩擦机理 的改变 对于粗糙表面,以机械啮合为主;对于光滑表面, 以黏附为主。 当摩擦副表面非常粗糙时,摩擦系数较大。然而非 常平滑的表面可能摩擦系数更大,这是因为真实接 触面积增大,表面间的分子作用加强。 一般说来,摩擦副存在一最佳粗糙度区间,在这一 间内,所产生的摩擦系数最小。
4.疲劳磨损机理 疲劳磨损机理在一般磨料磨损中起主导作用.即材料表 面在磨粒产生的循环接触应力作用下,因疲劳剥落而形 成磨屑。
29
3) 磨料磨损的主要影响因素
(1)磨料硬度的影响 材料的耐磨性决定于材料硬度Hm 和磨料硬度Ha的比值。 当Hm/Ha<0.5时为硬磨料磨损, 此时增加材料的硬度对其耐磨性增 加不大(无关)。 当Hm/Ha>0.8时为软磨料磨损, 此时增加材料的硬度能迅速地提高 其耐磨性 当H m/Ha在0.5~0.8之间时,要 根据实际情况进行判断。
磨损的金属表面上发生了最大限度的“加工硬化”, 材料耐磨性与其磨损后的表面硬度成正比。
38
高锰钢材料是一个典型的实例。高锰钢经水韧性处 理后,获得单一奥氏体组织,硬度约为HB180~230。 用高锰钢制作的挖掘机斗齿,在挖掘硬的矿心时, 由于高锰钢得到充分的加工硬化,表现出良好的耐 磨性,优于回火马氏体和贝氏体钢。 相反,若将高锰钢斗齿用于挖掘主要含石英砂的砂 土层时,其耐磨性远不如马氏体和贝氏体钢。
31
32
33
(3)磨料脆性的影响
材料的磨料磨损往往需要多次反复才能完成, 在这一过程中,磨料的状态将发生改变
一种表现为尖角和锐边被破坏,即由原来尖锐 的、多角形的磨料变成圆而钝的磨料,使得材 料的磨损率下降。 另一种表现为磨料破碎,生成尖角和锐边,使 得材料的磨损率增大。
34
(4)载荷的影响:
26
不形成切削
形成 切削
图2-18
27
脆性材料
3.微观断裂(剥落)磨损机理
在磨损过程中,大多数材料表面都会发生塑性变形, 但脆性材料(如陶瓷、玻璃、碳化物等)或含有硬而 脆的第二相质点的材料在与磨料作用时,断裂机理 可能占主导地位,脆性材料或脆性相将产生断裂或 剥落,因此磨损量比塑性材料的磨损量大
39
二、粘着磨损
定义:两个接触表面相对运动 时,由于接触点粘着和焊合而 形成的粘着结点被锯切断裂, 被剪断的材料由一个表面转移 到另一个表面,或脱落成磨屑 而产生的磨损。 粘着磨损的主要特征是出现材 料转移,同时沿滑动方向产生 不同程度的磨痕。
磨 损 量
o
a
b
时 间
图2.1 粘着磨损阶段磨损特征
5
2.按摩擦副的运动形式分类
(1)滑动摩擦
物体接触表面相对滑动时产生的摩擦称为滑动 摩擦。
(2)滚动摩擦
在力矩作用下,物体沿接触表面滚动时产生的 摩擦称为滚动摩擦
6
3.按摩擦副表面的润滑状况分类
(1)纯净摩擦 摩擦表面没有任何吸附膜或化合物时产生的摩擦称 为纯净摩擦。这种摩擦只有在接触面产生塑性变形 使表面膜破坏或在真空中摩擦时才能发生。 (2)干摩擦(无润滑摩擦) 在大气条件下,摩擦表面间名义上没有润滑剂存在 时产生的摩擦称为干摩擦,或称无润滑摩擦。 (3)流体(润滑)摩擦 相对运动的两物体表面完全被流体隔开时产生的摩 擦称为流体(润滑)摩擦。当流体为液体时称为液体 摩擦,流体为气体时称为气体摩擦。流体摩擦时摩 擦发生在流体内部。 (4)边界(润滑)摩擦 介于干摩擦和流体(润滑)摩擦之间的一种摩擦形式, 摩擦表面间存在着一层极薄的润滑膜,这层润滑膜 的存在使得边界摩擦较之干摩擦状态有很大改善, 但还不足以将两摩擦表面完全分隔开。
以力的作用特点分类
低应力划伤式磨料磨损、高应力划伤式磨料磨 损、凿削式磨料磨损
18
19
2) 磨料磨损机理
塑性材料
1.微观切削机理 磨粒作用存材料表面上的 力可分解为法向分力(正压 力)和切向分力(摩擦力)。 在法向分力作用下,磨料压 入材料表面形成压痕,在切 向分力作用下,磨粒向前推 进。 形成一次切屑
22
犁沟变形模型如图:
23
图2-11 因塑性变形发生去除的两种机制 (a)犁沟;(b) 微观切屑;(c)切屑模型
24
图1-4 磨料磨损机制
25
迎角(也叫冲角)是指磨料前面与材料表面间的 夹角(下图示)。 磨料能否切削材料与迎角α有关,只有当迎角大 于临界迎角时,才能产生切屑;反之,如果迎 角小于临界迎角,则只能产生塑性犁沟,将材 料推向沟槽的两侧及前沿。
施加载荷较大、磨料尖锐以 及材料的断裂韧度与硬度的 比值愈低时,材料愈趋向于 压痕断裂。材料的硬度决定 了磨料颗粒可能压入的深度 。
28
如果压痕深度大于产生断裂的临界深度时,材料因断 裂机制产生的去除过程就会优先发生。高的断裂韧度 会增加压痕临界深度值,因而减小了因断裂机制去除 的磨损体积。
无论是塑性材料还是脆性材料,均可能同时发 生塑性变形和断裂两种机制,在某种条件下, 某一机制占主导地位。
磨损率与压力成正比,但有一转折点,当 压力达到或超过临界压力时,磨损率随压 力的增加变的平缓。
35
5)材料的基体组织和性能
钢铁材料的基体组织与耐磨性的关系指出, 基体组织的耐磨性—一般按铁素体、珠光体、 贝氏体和马氏体的顺序递增。 在实际工作中选用耐磨材料并不是如此简 单,一个普遍的观念是“硬度越高的材料耐 磨性越好”。适合于较低接触应力、较低滑 动速度的滑动磨料磨损条件。 相反,在高接触应力、高冲击或相对滑动速 度快、磨料硬而锐利的情况下不适用。
36
图2-35 钢与铁的各种基体组织的耐磨料磨损性
37
未经热处理钢的耐磨性单值地决定其宏观硬度。 热处理钢的相对耐磨性随宏观硬度增高而线性地增 加,但比未经热处理钢要慢—些。 耐磨性不仅取决于钢的硬度,而且取决于成分。
不同成分的热处理钢虽然只有相同硬度但耐磨性不 同,说明各种的耐磨性与宏观硬度间并不存在单值 的对应关系。
表面工程 Surface Engineering
第二章 摩擦腐蚀基本知识
授课教师:
马 静
第二章 摩擦腐蚀基本知识
材料破坏的两大破坏形磨损
摩擦学:研究作相对运动表面及有关理论和 实践的科学技术 包括摩擦、磨损和润滑
当两个相互接触的物体在外力作用下产生相 对运动或具有相对运动趋势时,在接触面间 产生的切向运动阻力称为摩擦力,这个阻力 与运动方向相平行,这种现象称之为摩擦。
7
油膜 膜厚 比
8
4. 摩擦副处于高温、高速、低温、真空、 辐射等特殊环境条件下工作,可将摩擦分为 正常工况条件下的摩擦和特殊工况条件下的 摩擦 5. 根据产生摩擦的程度,将摩擦分为轻微 摩擦和严重摩擦等。