水玻璃模壳解决裂壳的方法讲述讲解
提高墙体强度的裂缝修补方法
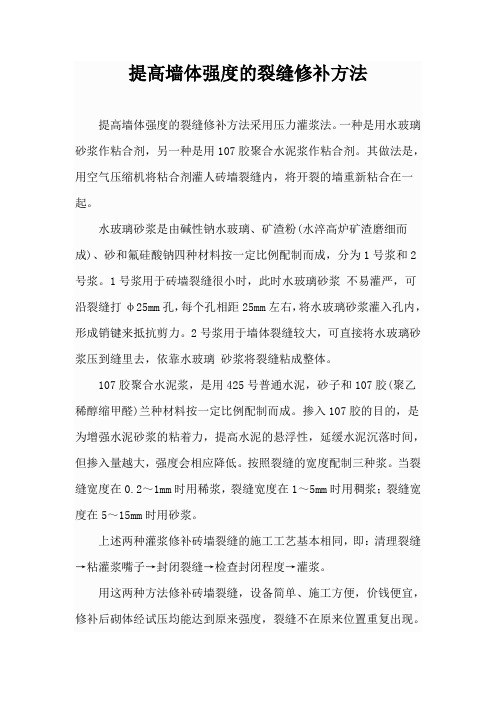
提高墙体强度的裂缝修补方法
提高墙体强度的裂缝修补方法采用压力灌浆法。
一种是用水玻璃砂浆作粘合剂,另一种是用107胶聚合水泥浆作粘合剂。
其做法是,用空气压缩机将粘合剂灌人砖墙裂缝内,将开裂的墙重新粘合在一起。
水玻璃砂浆是由碱性钠水玻璃、矿渣粉(水淬高炉矿渣磨细而成)、砂和氟硅酸钠四种材料按一定比例配制而成,分为1号浆和2号浆。
1号浆用于砖墙裂缝很小时,此时水玻璃砂浆不易灌严,可沿裂缝打φ25mm孔,每个孔相距25mm左右,将水玻璃砂浆灌入孔内,形成销键来抵抗剪力。
2号浆用于墙体裂缝较大,可直接将水玻璃砂浆压到缝里去,依靠水玻璃砂浆将裂缝粘成整体。
107胶聚合水泥浆,是用425号普通水泥,砂子和107胶(聚乙稀醇缩甲醛)兰种材料按一定比例配制而成。
掺入107胶的目的,是为增强水泥砂浆的粘着力,提高水泥的悬浮性,延缓水泥沉落时间,但掺入量越大,强度会相应降低。
按照裂缝的宽度配制三种浆。
当裂缝宽度在0.2~1mm时用稀浆,裂缝宽度在1~5mm时用稠浆;裂缝宽度在5~15mm时用砂浆。
上述两种灌浆修补砖墙裂缝的施工工艺基本相同,即:清理裂缝→粘灌浆嘴子→封闭裂缝→检查封闭程度→灌浆。
用这两种方法修补砖墙裂缝,设备简单、施工方便,价钱便宜,修补后砌体经试压均能达到原来强度,裂缝不在原来位置重复出现。
水玻璃注浆施工方案

水玻璃注浆施工方案1. 引言水玻璃注浆施工是一种常用于建筑工程中的修复方法,通过注入水玻璃浆料来加固和修复混凝土结构的裂缝和空洞。
本文将介绍水玻璃注浆施工的具体方案和步骤,以及施工前的准备工作和注意事项。
2. 施工准备在进行水玻璃注浆施工前,需要进行以下准备工作:2.1 施工材料准备•水玻璃浆料:根据具体工程需要选取合适的水玻璃浆料,要求浓度适宜;•注浆设备:包括注浆泵、注浆管道等;•注浆辅材:注浆管接头、止水带、胶带等。
2.2 施工工具准备•钻孔机:用于打孔,选择适合的孔径和深度;•喷枪和钢丝刷:用于清理钻孔孔壁和修复区域表面;•测量工具:用于测量孔深和孔径。
2.3 施工人员准备•注浆施工人员:具备相关施工经验和操作技能;•安全防护人员:负责施工现场的安全管理和监督。
3. 施工步骤水玻璃注浆施工的步骤如下:3.1 孔洞处理根据设计要求和实际情况,确定需要进行注浆修复的孔洞的位置和数量。
在施工前,先进行孔洞处理,包括以下步骤:1.使用钻孔机在需要修复的混凝土结构上钻孔,孔的直径和深度根据设计要求确定;2.清理钻孔孔壁的灰尘和碎块,确保孔洞的内壁干净;3.检查钻孔孔径和深度是否符合设计要求,如不符合,则进行调整。
3.2 样板制作在施工前,需要制作样板,用于控制注浆的位置和流动方向。
制作样板的步骤如下:1.根据设计要求,制作与钻孔孔径一致的样板;2.预留与注浆管道连接的孔口;3.将样板固定在需要修复的结构上,确保其位置准确。
3.3 注浆施工注浆施工是整个水玻璃修复过程中最重要的一步。
施工步骤如下:1.连接注浆设备,确保设备完好并处于正常工作状态;2.将注浆管道插入到预留的孔口中,确保与孔洞之间无泄漏;3.开启注浆设备,将水玻璃浆料注入到孔洞中;4.注浆时,应逐渐提高注浆压力,控制注浆流速;5.注浆过程中,注浆管道应保持稳定不动,确保注浆材料填充整个孔洞;6.注浆完毕后,检查注浆点的固化情况,确保修复效果良好。
水玻璃型壳熔模铸造制壳工艺过程控制

水玻璃型壳熔模铸造制壳工艺过程控制作者:董丽华来源:《中国科技纵横》2018年第21期摘要:近年来,随着中国的铸造业发展迅速。
其中由于熔模铸造可以做到少切削,不切削,复杂件成型率高,生产工艺水平越来越高,其市场也越来越大。
而大部分的铸件生产任然采用的是水玻璃工艺,这种工艺最大的问题就是不稳定性,所以对水玻璃制壳质量控制要求和生产管理要点的讨论就显得很有必要。
实践证明,通过加强关键工序的控制和质量因素的综合控制,产品质量和成品率会有了显著的提高。
关键词:水玻璃;熔模铸造;制壳;工艺;控制中图分类号:TG249.5 文献标识码:A 文章编号:1671-2064(2018)21-0086-02由于水玻璃粘结剂的价格低廉,制壳周期短,因此在我国广泛采用水玻璃工艺精密铸造。
但是,与传统砂型铸造相比,水玻璃壳型铸造成本高,工艺复杂,生产周期长。
型壳是影响铸件质量的重要因素之一。
如何控制其质量具有重要意义。
本文结合生产实践,对壳的原材料控制和管理和制壳工艺的改善,改善型壳强度及稳定性,从而提高铸件质量及其成品率。
1 原材料的选择与控制1.1 水玻璃硅酸钠的水溶液俗称水玻璃,南方一般被称为水玻璃,北方一般被称为泡化碱。
硅酸钠的形态可分为液体、固体和水淬三种形态。
水玻璃可分为钾水玻璃和钠水玻璃。
熔模铸造中一般采用的是钠水玻璃。
水玻璃中二氧化硅和氧化钠(或氧化钾)的摩尔比通常称为模数(M)。
硅酸钠是水分散体系中的无色、浅色透明或半透明粘稠液体。
固体硅酸钠是一种无色和浅色的透明或半透明玻璃。
硅酸钠在的凝固与石灰非常相似。
主要通过碳化、脱水、固化三个工序来实现。
随着二氧化硅含量的增加,游离水蒸发,硅胶脱水成固体SiO2并固化。
由于空气中CO2浓度低,碳化反应和固化过程非常缓慢。
1.2 水玻璃的特性熔模铸造生产时水玻璃应为液态,纯净的水玻璃是一种外观显无色透明的粘滞性溶液,含有杂质时则显青灰色或者淡黄色。
水玻璃溶液显碱性,一般高、中模数的水玻璃的PH值为11~13。
水玻璃模壳解决裂壳的方法

水玻璃模壳解决裂壳的方法-1;1.水玻璃模壳裂壳的概述;1.1低温蜡蜡模,水玻璃制壳工艺的裂壳行为;1.2由于冬天气温低,原材料的化学特性随着气温而;溶液都会变得黏稠;1.3天气温度降低,浆料的粘度相同粉液比低;硬化;为溶液黏稠而渗透效果变差,导致结晶氯化铝的硬化能;另外也不排除操作的因素导致模壳开裂;1.4实践证明,水玻璃模壳裂壳与气温有直接关系;制做的模水玻璃模壳解决裂壳的方法-11.水玻璃模壳裂壳的概述1.1低温蜡蜡模,水玻璃制壳工艺的裂壳行为。
1.2由于冬天气温低,原材料的化学特性随着气温而变化。
水玻璃溶液、氯化铝溶液都会变得黏稠。
1.3天气温度降低,浆料的粘度相同粉液比低;硬化液的溶解度也低、同时也因为溶液黏稠而渗透效果变差,导致结晶氯化铝的硬化能力显著下降。
另外也不排除操作的因素导致模壳开裂。
1.4实践证明,水玻璃模壳裂壳与气温有直接关系。
上个星期,气温接近零度,制做的模壳,每晚浇注都有裂壳的发生。
而这几天的气温有所回升,最低温度在3~5℃,晚上浇注的模壳裂壳就莫名其妙地消失了。
1.5熔模铸造用的是碱性水玻璃(硅酸钠)。
其理化指标:①外观:白灰色或淡青色,均匀分散相,无团絮状。
目测,要求一致性。
②PH值:11~13,用广泛试纸检测,色差对照,一般PH值是12.③密度:要求D=1.35~1.37.用玻璃密度计检测,密度多为1.36.2.工艺解决水玻璃模壳裂壳的方法2.1原水玻璃制壳参数①面层水玻璃密度1.30,9#石英粉,浆料45~55S,国标量杯,撒40~70目精白石英砂。
氯化铵溶液硬化,硬化时间10~15min。
②二层水玻璃密度1.35,200目莫来粉浆料,35~45S,国标量杯,撒30~6 0目莫来砂。
氯化铵溶液硬化,硬化时间15~25min。
③三层水玻璃密度1.35,200目莫来粉浆料,38~48S,国标量杯,撒16~30目莫来砂。
氯化铝溶液硬化,硬化时间35min以上。
④四、五、六层水玻璃密度1.35,耐火泥4:石英粉1混合浆料,50~60S,国标量杯,撒8~16目红砂。
水玻璃熔模铸造介绍

水玻璃熔模铸造介绍变量和公差熔模铸造又称“失蜡铸造”,通常是在蜡模表面涂上数层耐火材料,待其硬化干燥后,将其中的蜡模熔去而制成型壳,再经过焙烧,然后进行浇注,而获得铸件的一种方法。
由于获得的铸件具有较高的尺寸精度和表面光洁度,故又称“熔模精密铸造”。
可用熔模铸造法生产的合金种类有碳素钢、合金钢、耐热合金、不锈钢、精密合金、永磁合金、轴承合金、铜合金、铝合金、钛合金和球墨铸铁等。
熔模铸件的形状一般都比较复杂,铸件上可铸出孔的最小直径可达0.5mm,铸件的最小壁厚为0.3mm。
在生产中可将一些原来由几个零件组合而成的部件,通过改变零件的结构,设计成为整体零件而直接由熔模铸造铸出,以节省加工工时和金属材料的消耗,使零件结构更为合理。
熔模铸件的重量大多为零点几十牛(即几十克到几公斤),太重的铸件用熔模铸造法生产较为麻烦,但目前生产大的熔模铸件的重量已达800牛左右。
溶膜铸造是用易熔材料制成模型,然后在模型上涂挂耐火材料,经硬化后,在将模型熔化排出型外,从而获得无分型面的铸型,铸型焙烧后即浇注。
一. 工艺过程:1. 蜡模制作1) 压型:制蜡模的专用模具、钢、铜、铝、切削而成2) 蜡模的压制:石蜡、峰蜡、硬脂酸、松香等,将熔化的蜡料压入压型中,冷凝后取出,修去毛刺,得到蜡模3) 蜡模组装:若干蜡模焊在一个直浇棒上2. 结壳:蜡模涂上涂料、硬化、干燥等1) 浸涂料(石英粉+粘结剂的糊状物)表面光洁2) 撒砂(粗石英砂)的目的:增厚型壳3) 硬化(水玻璃+NH4CL—SIO2)化学硬化3. 脱蜡、焙烧1) 脱蜡:热水或水蒸气2) 焙烧:加热800~1000℃提高型壳强度4. 填砂:浇注1) 填砂:型壳放入铁箱中,周围干砂充填2) 浇注:趁热(600~700℃)进行浇注5. 落砂清理冷却后,破坏型壳,取出铸件,去浇口、毛刺、退火或正火,以便得到所需机械性能1) 铸造精度、光洁度高、且可浇注形状复杂的件2) 能铸造各种合金(型壳是高级耐火材料)3) 单件、小批、大批量生产均可4) 少无切削加工(Ra3.2~1.6um)稍磨5) 材料贵,工艺过程繁杂,生产周期长应用:使用高熔点合金精密铸件的成批、大量生产,形状复杂,难以切削加工的小零件。
熔模铸造水玻璃型壳质量控制

熔模铸造水玻璃型壳质量控制许晓兰,高明轩,陈学敏(霍州煤电集团机电修配分公司,山西霍州031400)摘 要:全过程论述了铸造水玻璃型壳的质量控制要点。
实践证明,通过对型壳质量影响因素的综合控制,使铸件的质量有了明显的提高。
关键词:铸造;水玻璃;型壳;质量中图分类号:T Q171 文献标识码:A 文章编号:1008-8725(2003)10-0084-021 水玻璃粘结剂的质量控制(1)水玻璃种类的选择:市场供应的水玻璃有两种,一种是纯碱与石英粉在1300~1400℃温度下反应得到的,杂质含量少,性能稳定;另一种是采用芒硝生产,杂质含量较高。
通常第一种方法生产的水玻璃较适合熔模铸造选用。
(2)水玻璃模数(M)、密度(ρ),控制M取决于S iO2和Na2O的相对含量,而ρ的高低又决定着S iO2的含量。
M和ρ直接影响型壳的表面强度、常温强度、高温强度及残留强度。
在我厂生产中,控制面层涂料水玻璃的M=3.0~3.2,ρ=1.27~1.29。
加固层M=3.0~3.2,ρ=1.30~1.34。
当M和ρ不符合要求时,用酸或碱来调整M,用水或高密度的水玻璃调整ρ,使用效果良好,既保证了壳体的各种常温、高温性能,又有较低的溃散强度。
在实际生产中,水玻璃的假模数对型壳高温强度的影响很大。
当M>310时,水玻璃存放时间越长粘度越大。
由于水玻璃中有游离的S iO2存在,储存一定时间后,S iO2沉积在容器的底部,导致水玻璃模数下降,严重影响型壳的高温强度。
这主要是由于生产厂制做水玻璃时,S iO2和Na2O不是以化合态存在,或者为了提高模数,加入细石英粉造成的。
所以,在使用过程中,为了防止游离S iO2存在使模数高的假象,当水玻璃卸车时化验一次,存放24h后再化验一次。
以保证型壳的质量。
对于沉积于容器底部的杂质,必须在一定时间内予以清理,一般容量在15~20t的储罐,每二年要清理一次。
2 粉料粒度分布对型壳质量的影响与控制生产中,较粗的粉料(手感)所制得的涂料沉淀快,流杯粘度大,工艺稳定性差,生产出的铸件表面粗糙。
熔模铸造型壳六大缺陷分析 入木三分
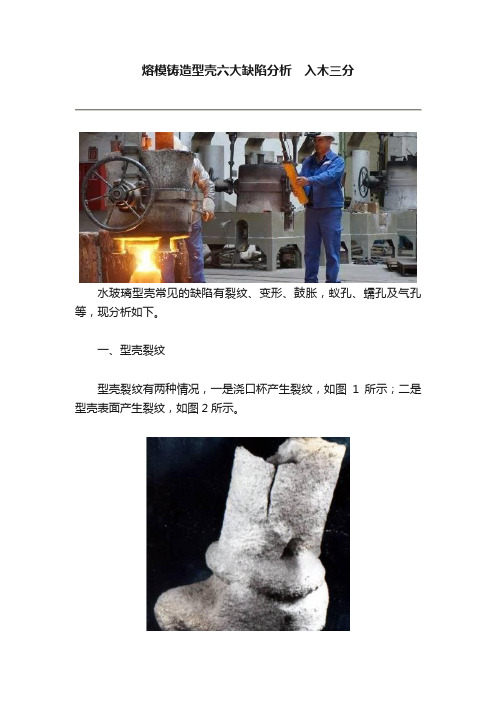
熔模铸造型壳六大缺陷分析入木三分水玻璃型壳常见的缺陷有裂纹、变形、鼓胀,蚁孔、蠕孔及气孔等,现分析如下。
一、型壳裂纹型壳裂纹有两种情况,一是浇口杯产生裂纹,如图1所示;二是型壳表面产生裂纹,如图2所示。
图1 浇口杯裂纹图2 型壳表面裂纹浇口杯裂纹特征:型壳的浇口杯有裂纹,严重时浇口杯开裂。
型壳表面裂纹:在型壳的表面上有弯曲的、深浅不等的裂纹。
1.产生原因(1)涂料中水玻璃的模数、密度过高或过低;涂料中的粉液比过低;或硬化剂的浓度、温度和硬化时间不当,硬化不充分;或型壳在硬化前的自然风干时间不够,不利于硬化剂的继续渗透硬化,影响了硅凝胶的连续性和致密性;或型壳的层数不够等原因,导致型壳的强度低,出现了裂纹。
(2)涂料层涂挂的不均匀,或撒砂层厚薄不均;尤其是浸涂料后没有撒上砂的部位,硅凝胶在收缩时受力不均匀,导致型壳产生裂纹。
(3)脱蜡液的温度低,脱蜡时间太长。
由于蜡料的热膨胀系数大于型壳的热膨胀系数,脱蜡缓慢将导致型壳在脱蜡的过程中受到各种应力的作用;如果超过此时型壳的强度极限,就会产生裂纹,甚至开裂。
(4)焙烧时,型壳入炉温度高,升温过快,或高温出炉急冷;或型壳多次焙烧,产生微裂纹,甚至裂纹,降低了强度;或型壳的高温强度低,使型壳在焙烧时产生裂纹。
(5)清理浇口杯时,机械损伤浇口杯。
2.防止措施(1)采用下列措施,型壳的高温强度就高。
①水玻璃的模数M=3.0~3.4,密度ρ=1.30~1.33 g/cm3配制的加固层涂料。
②采用合理的涂料配制工艺,并执行涂料的“配比-温度-粘度”曲线。
③采用合理的硬化工艺,控制硬化剂的“浓度-温度-硬化时间”;或选用氯化铝代替氯化铵硬化型壳。
④合理的制壳工艺,如涂料粘度与撒砂粒度的合理配合,硬化工艺参数要确保型壳充分硬化。
⑤采取措施增加型壳强度,如常用的增加型壳层数,或采用复合型壳等;必要时大件型壳可用铁丝加固等。
(2)蜡模浸入检验合格的涂料中,上下移动和不断地转动,提起后滴去多余的涂料,使涂料均匀地覆盖在模组的表面上;不能出现涂料的局部堆积或缺少涂料(漏涂);并及时、均匀撒砂。
水玻璃注浆施工方案

水玻璃注浆施工方案水玻璃注浆施工方案为了解决某建筑物的裂缝问题,需要进行水玻璃注浆施工。
本文将详细介绍该施工方案。
一、施工准备工作1.安全措施:在施工现场设置明显的警示标志,并佩戴好安全帽、防护手套等个人防护设备。
2.清理现场:清理施工现场,清除周围的杂物和尘土,确保施工区域的整洁。
3.准备材料:准备好水玻璃注浆所需的材料,包括水玻璃、注浆泵、注浆管等。
二、施工步骤1.检查裂缝情况:对建筑物的裂缝进行检查,确定裂缝的位置、长度和宽度。
2.清洁裂缝:用清洁剂和刷子清洁裂缝,确保裂缝表面干净无尘。
3.注浆准备:将水玻璃按照比例与清水混合,搅拌均匀,制成均质的注浆液。
4.注浆施工:使用注浆泵将注浆液注入裂缝中,从裂缝的底部开始注入,逐渐向上注满整个裂缝。
三、验收及保养1.施工完毕后,对注浆施工的质量进行验收,检查注浆是否充实、均匀,无漏注现象。
2.保养施工区域,防止施工后再次出现裂缝。
在注浆完成后,尽量避免人员和设备的碰撞,确保注浆得以充分固化。
3.定期对施工区域进行巡检,发现及时处理可能出现的问题。
四、施工注意事项1.施工人员必须具备一定的工程质量监督经验,了解水玻璃注浆施工技术和过程,能够熟练操作注浆设备。
2.在施工过程中,要注意注浆液的比例和搅拌均匀度,确保注入裂缝的注浆液质量合格。
3.施工现场必须保持干燥,避免水或雨水进入裂缝,影响注浆质量。
4.注意施工区域的通风,避免注浆液散发的气味对施工人员造成伤害。
通过以上施工方案,可以有效地解决建筑物裂缝问题,提高建筑物的稳定性和安全性。
同时,在施工过程中必须严格按照安全操作规程进行,确保施工人员的人身安全。
水玻璃的作用和使用方法

水玻璃的作用和使用方法水玻璃是一种无机盐,在化学上也被称为硅酸钠。
它是一种具有粘合性的液体,常常用于粘接、封闭和防水处理。
本文将介绍水玻璃的作用和使用方法。
1.粘合作用水玻璃能够形成一种黏性胶质,并能黏合非常多的材料,如陶瓷、水泥、木材、纸张等。
因此,水玻璃常用于建筑、制陶、纸张等工业领域。
2.防水作用水玻璃具有防水性,因此可以作为涂料、防水剂使用。
将水玻璃涂在建筑物表面,可以有效地减少水的渗入,从而防止建筑物内部受到损害,延长建筑物寿命。
3.填充作用水玻璃常常被用来填充漏洞和裂痕,填缝宽度可以达到1cm左右。
当填充物干燥后,水玻璃不会收缩或裂开,也不受冻融交替影响。
填补后的材料硬度较高,可以使建筑物结构更加稳固。
4.耐火作用将等量的水和水玻璃搅拌均匀,然后放置几分钟,直至形成黏稠胶液。
将胶液涂在需要粘合的材料上,然后将它们压在一起并等待几小时。
水玻璃之间的黏性会在几小时内逐渐加强,并且在凝固的过程中会生成热量,这有助于材料更紧密地结合。
将水玻璃与水按照1:1的比例混合均匀,使用喷涂或刷涂的方式涂抹在需要防水的表面上。
通常,涂层需要在干燥后涂抹第二次,以获得更好的防水效果。
3.填补空隙和裂缝将水玻璃倒入裂缝或孔洞中,使用刮刀将其压实并平整,然后等待约24小时使其干燥。
当水玻璃干燥后,它形成的填充材料具有很高的硬度,非常适合用于填补混凝土或其他硬质材料的裂缝。
总之,水玻璃广泛应用于建筑、制陶、纸张、车辆工业等领域,具有粘合、防水、填充、耐火等多种作用。
使用时,注意避免过量使用,并遵循正确的使用方法,以充分发挥其作用。
水玻璃的防水用法

水玻璃的防水用法
水玻璃是一種具有防水性質的材料,可用於多種防水工程和日常生活中的防水需求。
下面列舉一些常見的水玻璃防水用法:
1. 地下室和地下空間防水:將水玻璃與水或水泥混合,形成一種防水的撒布材料,塗抹在地下室牆壁和地板上,可以有效地防止地下室和地下空間的水損害。
2. 屋頂和屋面防漏:使用水玻璃與沙子、水泥和纖維混合,形成一種防水塗層,塗抹在屋頂或屋面上,可以防止雨水滲透和屋頂漏水。
3. 浴室和廚房防水:將水玻璃與瓷磚膠或水泥混合,用於浴室牆壁、地板和廚房台面等需要防潮的地方,可以防止水分進入牆體和地板,避免潮濕和漏水。
4. 屋外牆防水:將水玻璃直接塗抹在建築外牆上,形成一層防水障礙,可以保護建築不受風雨侵蝕和潮濕影響。
5. 園林和池塘防水:將水玻璃與砂和水泥混合,塗抹在花園、庭院和池塘的牆壁和底部,可以防止土壤中的水分滲透,保持整體乾燥。
6. 補漏和修復:將水玻璃直接塗抹在漏水的縫隙、裂紋或破損的地方,可以迅速封住漏水點,修復漏水問題。
需要注意的是,使用水玻璃進行防水時,應詳細閱讀產品說明和使用方法,確保正確使用和效果。
此外,防水工程所需的混合比例和材料應根據實際需求和環境條件進行調整。
水玻璃防水施工方法
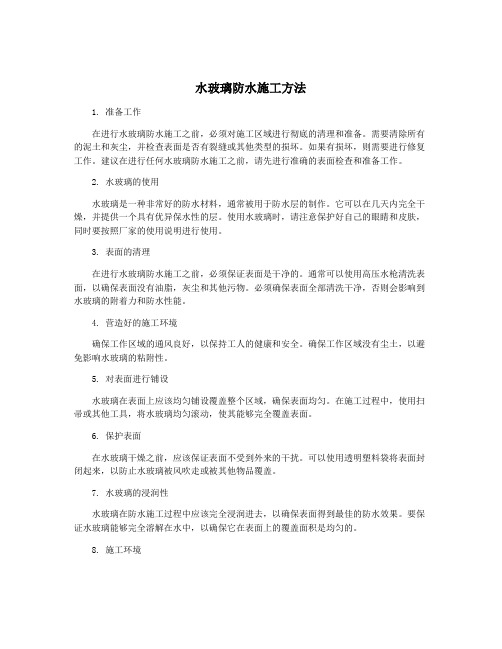
水玻璃防水施工方法1. 准备工作在进行水玻璃防水施工之前,必须对施工区域进行彻底的清理和准备。
需要清除所有的泥土和灰尘,并检查表面是否有裂缝或其他类型的损坏。
如果有损坏,则需要进行修复工作。
建议在进行任何水玻璃防水施工之前,请先进行准确的表面检查和准备工作。
2. 水玻璃的使用水玻璃是一种非常好的防水材料,通常被用于防水层的制作。
它可以在几天内完全干燥,并提供一个具有优异保水性的层。
使用水玻璃时,请注意保护好自己的眼睛和皮肤,同时要按照厂家的使用说明进行使用。
3. 表面的清理在进行水玻璃防水施工之前,必须保证表面是干净的。
通常可以使用高压水枪清洗表面,以确保表面没有油脂,灰尘和其他污物。
必须确保表面全部清洗干净,否则会影响到水玻璃的附着力和防水性能。
4. 营造好的施工环境确保工作区域的通风良好,以保持工人的健康和安全。
确保工作区域没有尘土,以避免影响水玻璃的粘附性。
5. 对表面进行铺设水玻璃在表面上应该均匀铺设覆盖整个区域,确保表面均匀。
在施工过程中,使用扫帚或其他工具,将水玻璃均匀滚动,使其能够完全覆盖表面。
6. 保护表面在水玻璃干燥之前,应该保证表面不受到外来的干扰。
可以使用透明塑料袋将表面封闭起来,以防止水玻璃被风吹走或被其他物品覆盖。
7. 水玻璃的浸润性水玻璃在防水施工过程中应该完全浸润进去,以确保表面得到最佳的防水效果。
要保证水玻璃能够完全溶解在水中,以确保它在表面上的覆盖面积是均匀的。
8. 施工环境水玻璃在高温环境下会消失得更快,也不太建议在潮湿的环境下进行施工。
这两种环境都会影响水玻璃的附着性和防水效果。
在施工之前,请确保周围环境的温度和湿度是适合施工的。
9. 保持均匀的厚度在水玻璃防水层的施工过程中,请保持层的厚度均匀。
如果有坑洼或过厚的地方,它们将会降低水玻璃的防水性能。
均匀覆盖材料,可确保表面得到完全覆盖,建议在指定的厚度内施工。
10. 检查和清理一旦防水层形成,必须进行定期检查和清洗,以确保其能够持续地维护其防水性能。
水玻璃类防腐蚀工程表面起皮、起砂-施工通病防治
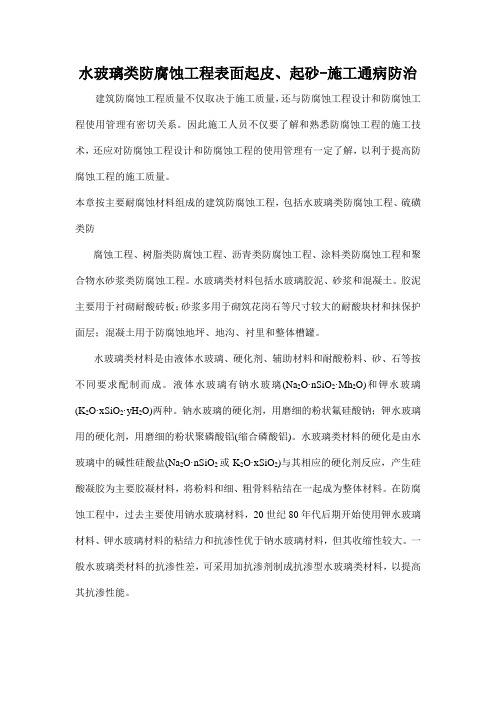
水玻璃类防腐蚀工程表面起皮、起砂-施工通病防治建筑防腐蚀工程质量不仅取决于施工质量,还与防腐蚀工程设计和防腐蚀工程使用管理有密切关系。
因此施工人员不仅要了解和熟悉防腐蚀工程的施工技术,还应对防腐蚀工程设计和防腐蚀工程的使用管理有一定了解,以利于提高防腐蚀工程的施工质量。
本章按主要耐腐蚀材料组成的建筑防腐蚀工程,包括水玻璃类防腐蚀工程、硫磺类防腐蚀工程、树脂类防腐蚀工程、沥青类防腐蚀工程、涂料类防腐蚀工程和聚合物水砂浆类防腐蚀工程。
水玻璃类材料包括水玻璃胶泥、砂浆和混凝土。
胶泥主要用于衬砌耐酸砖板;砂浆多用于砌筑花岗石等尺寸较大的耐酸块材和抹保护面层;混凝土用于防腐蚀地坪、地沟、衬里和整体槽罐。
水玻璃类材料是由液体水玻璃、硬化剂、辅助材料和耐酸粉料、砂、石等按不同要求配制而成。
液体水玻璃有钠水玻璃(Na2O·nSiO2·Mh2O)和钾水玻璃(K2O·xSiO2·yH2O)两种。
钠水玻璃的硬化剂,用磨细的粉状氟硅酸钠;钾水玻璃用的硬化剂,用磨细的粉状聚磷酸铝(缩合磷酸铝)。
水玻璃类材料的硬化是由水玻璃中的碱性硅酸盐(Na2O·nSiO2或K2O·xSiO2)与其相应的硬化剂反应,产生硅酸凝胶为主要胶凝材料,将粉料和细、粗骨料粘结在一起成为整体材料。
在防腐蚀工程中,过去主要使用钠水玻璃材料,20世纪80年代后期开始使用钾水玻璃材料、钾水玻璃材料的粘结力和抗渗性优于钠水玻璃材料,但其收缩性较大。
一般水玻璃类材料的抗渗性差,可采用加抗渗剂制成抗渗型水玻璃类材料,以提高其抗渗性能。
钠和钾水玻璃材料在技术性能上虽有不同,但在防腐蚀工程中出现的质量通病和防治措施基本相同,在本节中综合介绍。
1.现象表面不光滑、起皮、起砂,用脚搓动或用硬物刮划表面时,有粉或砂粒脱落。
2.原因分析(1)水玻璃的模数低,密度小,产生硅酸凝胶少,强度不够。
(2)硬化剂用量不够。
水玻璃耐酸混凝土龟裂、不规则裂纹-施工通病防治

水玻璃耐酸混凝土龟裂、不规则裂纹-施工通病防治能防止或抵抗酸性介质腐蚀作用的混凝土,称为耐酸混凝土。
建筑工程中常用的耐酸混凝土有水玻璃耐酸混凝土、沥青混凝土和硫磺混凝土三种。
使用时应根据具体承受酸性骨料介质的种类和浓度,选择和确定耐酸混凝土的类别。
水玻璃耐酸混凝土是以水玻璃为胶结料,氟硅酸钠为硬化剂,加入一定级配的粉料(如石英粉、辉绿岩粉等)和粗细骨料配制而成的混凝土。
具有较好的耐酸性能,强度高,材料来源广,价格低。
但耐稀酸、耐水性和抗渗性欠佳。
1.现象同干缩微裂的相应部分内容。
2.原因分析(1)水玻璃密度大,用量多,收缩变形大。
(2)拌合物搅拌不均匀,致使混凝土硬化速度不一致,造成某些部分所能承受的拉应力不一,薄弱部分便出现裂纹、开裂现象。
(3)混凝土暴露面积大,由于温度变化和温差影响,造成胀缩变形不一,形成裂纹。
(4)粗细骨料中含泥量和泥块含量大。
(5)振捣抹压不实,养护期间受雨水侵袭和太阳暴晒。
3.预防措施(1)使用密度适宜的水玻璃(p=1.38~1.42g/cm3),对密度过大的水玻璃,在常温下用水调整。
当环境温度低于10℃时,宜用40~50℃的温水调整。
(2)水玻璃用量以满足强度、耐酸性能和施工和易性为准,不宜多用,一般以控制在250~300kg/m3为宜。
(3)采用强制式搅拌机搅拌,搅拌时间应较水泥混凝土延长30s左右,直至搅拌均匀为止。
(4)所用材料应洁净,含泥量和泥块含量超过规定的骨料,应冲洗干净,符合标准后方可使用。
(5)大面积施工时,要防止环境温度的差异过大,必要时,应采取措施,如通风、加强室内空气的对流、局部热源予以隔离等。
(6)混凝土振捣、抹压要实。
养护时为防止雨水侵袭或太阳暴晒,应采取遮盖措施。
遇刮风天气,尚应加纸袋或用塑料薄膜覆盖,防止水分失散过快。
4.治理方法。
(1)宽度小于0.1mm的发丝裂纹可以不予处理。
(2)对于肉眼明显可见的裂纹,应先用钢丝刷清除混凝土表面的浮层,并将表面清理干净,然后用耐酸胶泥(去除原配合比中的粗细骨料)涂刷、抹压至混凝土表面平整。
水玻璃型壳
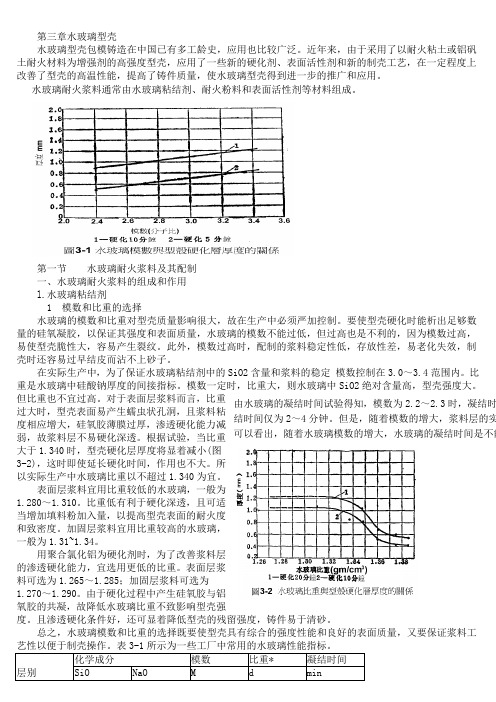
第三章水玻璃型壳水玻璃型壳包模铸造在中国已有多工龄史,应用也比较广泛。
近年来,由于采用了以耐火粘土或铝矾土耐火材料为增强剂的高强度型壳,应用了一些新的硬化剂、表面活性剂和新的制壳工艺,在一定程度上改善了型壳的高温性能,提高了铸件质量,使水玻璃型壳得到进一步的推广和应用。
第一节 水玻璃耐火浆料及其配制一、水玻璃耐火浆料的组成和作用l.水玻璃粘结剂1 模数和比重的选择水玻璃的模数和比重对型壳质量影响很大,故在生产中必须严加控制。
要使型壳硬化时能析出足够数量的硅氧凝胶,以保证其强度和表面质量,水玻璃的模数不能过低,但过高也是不利的,因为模数过高,易使型壳脆性大,容易产生裂纹。
此外,模数过高时,配制的浆料稳定性低,存放性差,易老化失效,制壳时还容易过早结皮而沾不上砂子。
在实际生产中,为了保证水玻璃粘结剂中的SiO2含量和浆料的稳定 模数控制在3.0~3.4范围内。
比重是水玻璃中硅酸钠厚度的间接指标。
模数一定时,比重大,则水玻璃中SiO2绝对含量高,型壳强度大。
但比重也不宜过高。
对于表面层浆料而言,比重过大时,型壳表面易产生蠕虫状孔洞,且浆料粘度相应增大,硅氧胶薄膜过厚,渗透硬化能力减弱,故浆料层不易硬化深透。
根据试验,当比重大于1.340时,型壳硬化层厚度将显着减小(图3-2),这时即使延长硬化时间,作用也不大。
所以实际生产中水玻璃比重以不超过1.340为宜。
表面层浆料宜用比重较低的水玻璃,一般为1.280~1.310。
比重低有利于硬化深透,且可适当增加填料粉加入量,以提高型壳表面的耐火度和致密度。
加固层浆料宜用比重较高的水玻璃,一般为1.31~1.34。
用聚合氯化铝为硬化剂时,为了改善浆料层的渗透硬化能力,宜选用更低的比重。
表面层浆料可选为1.265~1.285;加固层浆料可选为1.270~1.290。
由于硬化过程中产生硅氧胶与铝氧胶的共凝,故降低水玻璃比重不致影响型壳强度。
且渗透硬化条件好,还可显着降低型壳的残留强度,铸件易于清砂。
水玻璃型壳的缺陷及防止措施
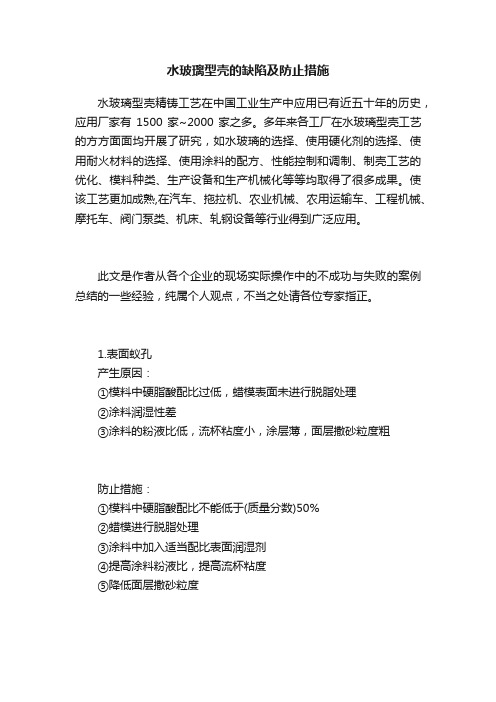
水玻璃型壳的缺陷及防止措施水玻璃型壳精铸工艺在中国工业生产中应用已有近五十年的历史,应用厂家有1500家~2000家之多。
多年来各工厂在水玻璃型壳工艺的方方面面均开展了研究,如水玻璃的选择、使用硬化剂的选择、使用耐火材料的选择、使用涂料的配方、性能控制和调制、制壳工艺的优化、模料种类、生产设备和生产机械化等等均取得了很多成果。
使该工艺更加成熟,在汽车、拖拉机、农业机械、农用运输车、工程机械、摩托车、阀门泵类、机床、轧钢设备等行业得到广泛应用。
此文是作者从各个企业的现场实际操作中的不成功与失败的案例总结的一些经验,纯属个人观点,不当之处请各位专家指正。
1.表面蚁孔产生原因:①模料中硬脂酸配比过低,蜡模表面未进行脱脂处理②涂料润湿性差③涂料的粉液比低,流杯粘度小,涂层薄,面层撒砂粒度粗防止措施:①模料中硬脂酸配比不能低于(质量分数)50%②蜡模进行脱脂处理③涂料中加入适当配比表面润湿剂④提高涂料粉液比,提高流杯粘度⑤降低面层撒砂粒度2. 表面圆珠状小孔产生原因:①表面层涂料搅拌时卷入过多气体而产生气泡②未加消泡剂防止措施:①用发泡力低的表面润湿剂①料中加入适量消泡剂③用毛笔刷涂或用压缩空气喷吹气泡3.桔子皮和皱疤产生原因:①熔模表面局部涂料堆积,涂层过厚,且未经自然干燥,致使涂料在化学硬化时,表层因硅凝胶形成急剧收缩,而涂料内层未经充分硬化,故而在表面形成皱皮②在面层涂料与熔模表面之间常有盐类和水分浓集,导致硬化不良,脱蜡时型壳内表面松散并出现突起和凹坑,形似桔皮状防止措施:①表面层涂料粘度不要太高,增加涂料流动性②避免蜡模表面及局部涂料堆积,应使涂料分布均匀③表面层浸涂料撒砂后,先经一定时间的自然干燥后,再进行化学硬化④表面层的化学硬化要充分4. 型壳分层和鼓胀产生原因:①涂料撒砂后,表面有浮砂②表面层撒砂的粒度过细,砂中粉尘过多或砂粒受潮含水分过多③型壳表面层化学硬化后风干时间过短,残留硬化剂过多④涂料粘度过大涂层过厚,涂层中间未硬化防止措施:①表面层撒砂要干燥,无粉尘,(水的质量分数小于0.3%)②表面层撒砂粒度不要太细,并防止浮砂堆积③表面层涂料粘度不宜太大,防止涂料堆积,涂层要充分硬化④表面层硬化后的干燥时间要充分,残留硬化剂要少⑤以氯化铝和氯化镁硬化的型壳在浸第二层涂料前须进行冲水,晾干,以增强层间结合5. 型壳裂纹产生原因:①浸涂料后未能撒上砂粒的部位易产生裂纹②涂料粘度过低,粉料加入量少,涂层过薄③涂层未经充分硬化④脱蜡水温度低,脱蜡时间过长⑤水玻璃模数低,密度小⑥型壳层数不足防止措施:①控制水玻璃的模数、密度及涂料粉液比和粘度②控制硬化剂的浓度、温度及硬化时间等工艺参数③提高脱蜡水温度至95-98℃,缩短脱蜡时间④适当增加型壳层数⑤大件型壳在制壳时可用铁丝加固,以增加高温强度6. 型壳变形(高温)产生原因:型壳变形大多在脱蜡、焙烧或浇注时产生①涂料的粘度过大,涂层过厚,涂料堆积②硬化剂浓度低,温度低,硬化时间太短,硬化不足③脱蜡水温度低,脱蜡时间过长④焙烧时型壳受挤压或温度过高防止措施:①控制涂料粉液比和粘度②避免涂料局部堆积③控制硬化剂浓度、温度和硬化时间等工艺参数④缩短脱蜡时间,适当提高脱蜡水温度(95-98℃)7. 表面析出物(茸毛状析出物、瘤状、鹿角状析出物)产生原因:①氯化铵硬化的型壳,脱蜡后干燥时,型壳内在硬化反应时生成的盐分及残留的氯化铵硬化剂,随水分蒸发扩散迁移到型壳表面上来,并沿析出孔道堆集生长成茸毛状物质,其中4∕5是氯化钠,约1∕5是氯化铵②氯化铝硬化的型壳(尤其是聚含氯化铝硬化),硬化反应时产生铝胶氢氧化铝,通常氢氧化铝以弥散状态分布于型壳中,若硬化时间不足,在脱蜡时脱蜡水的PH值高,就可能使残留的氯化铝析出难溶的氢氧化铝附于型壳内外表面上,形成析出物防止措施:①型壳脱蜡后存放时间不要太长,应及时焙烧浇注②水玻璃密度不宜过大③涂料粘度不要过高④氯化铝硬化剂的PH值要适当,硬化时间要充足⑤脱蜡水应保持酸性————————。
水玻璃型壳产生分层和鼓胀机理研究
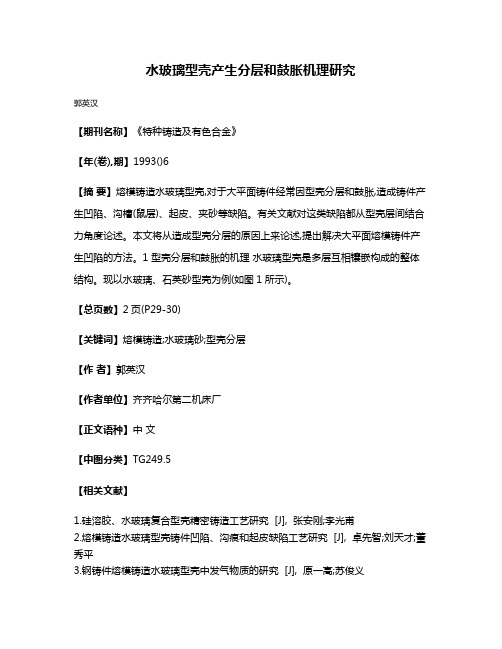
水玻璃型壳产生分层和鼓胀机理研究
郭英汉
【期刊名称】《特种铸造及有色合金》
【年(卷),期】1993()6
【摘要】熔模铸造水玻璃型壳,对于大平面铸件经常因型壳分层和鼓胀,造成铸件产生凹陷、沟槽(鼠层)、起皮、夹砂等缺陷。
有关文献对这类缺陷都从型壳层间结合力角度论述。
本文将从造成型壳分层的原因上来论述,提出解决大平面熔模铸件产生凹陷的方法。
1 型壳分层和鼓胀的机理水玻璃型壳是多层互相镶嵌构成的整体结构。
现以水玻璃、石英砂型壳为例(如图1所示)。
【总页数】2页(P29-30)
【关键词】熔模铸造;水玻璃砂;型壳分层
【作者】郭英汉
【作者单位】齐齐哈尔第二机床厂
【正文语种】中文
【中图分类】TG249.5
【相关文献】
1.硅溶胶、水玻璃复合型壳精密铸造工艺研究 [J], 张安刚;李光甫
2.熔模铸造水玻璃型壳铸件凹陷、沟痕和起皮缺陷工艺研究 [J], 卓先智;刘天才;董秀平
3.钢铸件熔模铸造水玻璃型壳中发气物质的研究 [J], 原一高;苏俊义
4.硅溶胶——水玻璃砂复合型壳工艺的研究 [J], 崔海茹
5.水玻璃型壳热变形特征研究 [J], 赵恒义;宝音;佟天夫
因版权原因,仅展示原文概要,查看原文内容请购买。
- 1、下载文档前请自行甄别文档内容的完整性,平台不提供额外的编辑、内容补充、找答案等附加服务。
- 2、"仅部分预览"的文档,不可在线预览部分如存在完整性等问题,可反馈申请退款(可完整预览的文档不适用该条件!)。
- 3、如文档侵犯您的权益,请联系客服反馈,我们会尽快为您处理(人工客服工作时间:9:00-18:30)。
水玻璃模壳解决裂壳的方法-1;1.水玻璃模壳裂壳的概述;1.1低温蜡蜡模,水玻璃制壳工艺的裂壳行为;1.2由于冬天气温低,原材料的化学特性随着气温而;溶液都会变得黏稠;1.3天气温度降低,浆料的粘度相同粉液比低;硬化;为溶液黏稠而渗透效果变差,导致结晶氯化铝的硬化能;另外也不排除操作的因素导致模壳开裂;1.4实践证明,水玻璃模壳裂壳与气温有直接关系;制做的模水玻璃模壳解决裂壳的方法-11.水玻璃模壳裂壳的概述1.1低温蜡蜡模,水玻璃制壳工艺的裂壳行为。
1.2由于冬天气温低,原材料的化学特性随着气温而变化。
水玻璃溶液、氯化铝溶液都会变得黏稠。
1.3天气温度降低,浆料的粘度相同粉液比低;硬化液的溶解度也低、同时也因为溶液黏稠而渗透效果变差,导致结晶氯化铝的硬化能力显著下降。
另外也不排除操作的因素导致模壳开裂。
1.4实践证明,水玻璃模壳裂壳与气温有直接关系。
上个星期,气温接近零度,制做的模壳,每晚浇注都有裂壳的发生。
而这几天的气温有所回升,最低温度在3~5℃,晚上浇注的模壳裂壳就莫名其妙地消失了。
1.5熔模铸造用的是碱性水玻璃(硅酸钠)。
其理化指标:①外观:白灰色或淡青色,均匀分散相,无团絮状。
目测,要求一致性。
②PH值:11~13,用广泛试纸检测,色差对照,一般PH值是12.③密度:要求D=1.35~1.37.用玻璃密度计检测,密度多为1.36.2.工艺解决水玻璃模壳裂壳的方法2.1原水玻璃制壳参数①面层水玻璃密度1.30,9#石英粉,浆料45~55S,国标量杯,撒40~70目精白石英砂。
氯化铵溶液硬化,硬化时间10~15min。
②二层水玻璃密度1.35,200目莫来粉浆料,35~45S,国标量杯,撒30~6 0目莫来砂。
氯化铵溶液硬化,硬化时间15~25min。
③三层水玻璃密度1.35,200目莫来粉浆料,38~48S,国标量杯,撒16~30目莫来砂。
氯化铝溶液硬化,硬化时间35min以上。
④四、五、六层水玻璃密度1.35,耐火泥4:石英粉1混合浆料,50~60S,国标量杯,撒8~16目红砂。
氯化铝溶液硬化,硬化时间60min以上。
⑤半层水玻璃密度1.35,耐火泥4:石英粉1混合浆料,30~35S,国标量杯。
氯化铝溶液硬化,硬化时间60min以上.⑥半层后过4h进行脱蜡。
2.2涂层硬化指标氯化铵溶液的密度1.10,PH 6.0~6.5,硬化模壳涂层前搅动,然后再硬化壳层。
结晶氯化铝溶液的密度1.18~1.20之间,低于1.18就补加氯化铝,PH值2.5~3.0之间。
PH值高于3.0就加入盐酸降低PH值。
另补加润湿剂降低氯化铝的粘稠度,润湿剂的加入量0.1%。
每个星期加入一次。
2.3改进水玻璃制壳参数面层石英粉浆料,撒40~70目石英砂。
氯化铵硬化。
二层石英粉浆料,撒20~40目石英砂,氯化铵硬化。
三层耐火泥+石英粉浆料,撒16~30目红砂,氯化铝硬化。
四层、五层耐火泥+石英粉浆料,做8~16目红砂,氯化铝硬化。
半层耐火泥+石英粉浆料,浆料要稀,能够黏住砂子即可,氯化铝硬化。
注:这种改进后的参数制壳,对于裂壳有好转,但是还有裂壳的。
2.4用复合工艺做找出裂壳的原因所在前三层用硅溶胶制壳,后面加固层用水玻璃制壳。
用复合工艺找出裂壳的原因所在。
3.导致水玻璃模壳裂壳的因素3.1裂壳检查:①秋天的时候,裂壳的模壳敲开看,壳层用力可以搓碎。
而现在冬天的裂壳壳层强度很高,用手搓不碎的,要使劲才可以扳断,证明冬天的模壳刚性比较大。
②将开裂的模壳敲开看检查:A,边角部位比其他部位要薄一些(而模壳开裂也都是边角部位)。
并且模壳开裂处是有规律性的,都是大法兰面的棱角开裂的。
B,用一片模壳,由面层向外折,用力才可以折断;从半层往里折,一折就断。
同一片模壳,加固层断面结构疏松,强度低。
注:对于模壳太酥,强度低。
明显是硬化不好,也证明前三层氯化铵硬化效果比加固层氯化铝的硬化效果好的多。
3.2裂壳因素①在细砂做层数多的情况下,而模壳层数也多,模壳就容易裂壳。
②加固层浆料浓有两个缺点:一是浆料浓导致模壳高温时收缩过大而开裂;二是浆料浓导致氯化铝硬化不透而硬化不好,导致壳层强度低。
③加固层硬化后的干燥时间短,导致硬化液没有有效地渗透以及涂层表面有残留的硬化液妨碍层间有效结合。
④氯化铝硬化液,加盐酸后,模壳会变脆,变脆后,容易裂壳。
⑤加固层用氯化铝溶液硬化,硬化时间太长导致模壳的刚性加大,也会发生裂壳。
⑥如果裂壳部位是规律性在棱角处,一是操作的时候将砂擦掉了一部分,二是棱角部位的浆砂粘的比较少。
⑦模壳入炉初始的火力不能太猛,火力太旺也会导致裂壳。
⑧白天脱蜡的模壳,随即在晚上焙烧、浇注,模壳也会开裂(这是因为水脱蜡的模壳,壳层中的水分还未来得及挥发,模壳入炉后,水分快速蒸发从而产生急剧收缩,产生应力收缩而导致模壳开裂)。
⑨还有一种可能,就是前三层的耐火粉、耐火砂的膨胀系数比加固层的耐火粉、耐火砂的膨胀系数大,在高温时,前三层因为膨胀率比加固层大,所以将加固层撑胀开裂了。
4.裂壳原因及改进措施4.1浆料没有充分搅拌润湿的生料也会导致裂壳。
改进措施:①新配浆料充分搅拌;补充浆料每次在制壳之前进行搅拌均匀后再做涂层。
②每次做加固层之前,将浆料表面的结皮、结块和杂物捞掉。
4.2浆料粘度不正确引起的裂壳:①加固层的浆料太浓,硬化时导致涂层硬化不透,焙烧时导致涂层收缩过剧,模壳就会开裂。
改进措施:浆料不能浓,也不能稀,让下一层的砂子能够钻进本层的浆料、上层的砂子的空隙中去(浆料浸涂后,可以看到上层的砂子露出尖率30%)。
②半层浸浆后进入硬化池硬化,拿出后发现,模壳表面会产生裂隙(纹),浆料越浓裂隙越大(这是粉粒聚集收缩产生的裂隙)。
改进措施:半层的浆料应该稀薄,只要能够糊住砂子就可以了,避免裂隙的发生。
4.3加固层浆料中的粉料比例不当引起的裂壳:①如果耐火泥有问题:改进措施:换质量好的耐火泥,或者换河包粉配制浆料。
②粉料比例不当:改进措施加固层配浆是用耐火泥+石英粉,提高石英粉的比例,或者改为耐火泥+莫来粉(石英粉在高温时会产生相变,容易裂壳)。
4.4浆料温度低导致粘滞加大引起的裂壳:改进措施:①寒冷的冬季,为防止浆料结冰和影响使用。
浆料一般须是放在有暖气的房屋内,或者用绝热材料进行保温。
②如果浆料在室外,须给浆料加温后再进行制做涂层。
4.5用砂不当引起的裂壳:①加固层砂子粒度太细引起的裂壳:改进措施:选用粒度粗的型砂。
②加固层撒红砂只做一层半导致裂壳:改进措施:从三层就使用红砂,这样会使加固层在高温时收缩一致,表面壳层开裂。
4.6正确选用粉砂①由于淮北莫来砂粉,杂质含量低,在高温时不能再次烧结,所以模壳强度低会开裂。
改进措施:使用章丘产的C 级莫来粉和C级莫来砂。
②加固层使用红砂,由于红砂属于生料,在高温时会产生相变,导致壳层收缩不一致而裂壳。
改进措施:实践证明,水玻璃制壳用再生回用的粉砂,模壳就不会开裂(因为再生的粉砂是经过高温焙烧过,性能稳定)。
③实践证明,前三层使用石英粉浆料,加固层使用莫来粉浆料,这二者在高温时的膨胀系数不同,往往会导致裂壳。
改进措施:从二层起就使用莫来粉、莫来砂。
4.7氯化铵氯化铝溶液硬化不当引起的裂壳①面层、二层氯化铵溶液硬化的时间不能过长,过长会导致壳层开裂。
改进措施:缩短面层、二层氯化铵溶液的硬化时间。
②冬天气温低,氯化铝的粘滞性加大;加上氯化铵、氯化铝的溶解度随温度降低而降低,都会造成硬化速度慢和硬化不透。
改进措施:A, 氯化铝池子里定期加入润湿剂,以期提高氯化铝的渗透效果。
B, 氯化铝溶液在硬化前加热。
C, 加固层加长在氯化铝溶液里的硬化时间,半层在氯化铝硬化池里过夜。
D, 涂层硬化后风干时间也要延长。
③控制氯化铝溶液的质量:A,单纯用密度、酸碱度控制硬化液浓度是有偏差的,随着硬化液里氯化钠溶解量的增加,硬化液比重虽然不变但有效硬化剂含量却减小了,硬化效果也越来越差。
因此须根据生产情况定期整体更换硬化液。
B, 氯化铝硬化液长期使用,钠盐含量越来越多,须检测氯化钠的浓度,当浓度超过8%,就需要彻底更换硬化液(重配新液)。
C,氯化铵溶液、氯化铝溶液的密度和PH每天都检测。
如不合格,调整到正常后使用。
4.8涂层硬化效果的检测:当模壳(涂层)进入硬化池,硬化的过程中,拿起模壳,用手指抠涂层或者用手搓浇口杯边上的涂层,如果还是软化的,表示涂层没有硬化透。
5.其他解决裂壳的方法5.1蜡模边角是直角,面层二层浆粘不上;边角锋利,导致浆砂粘附的很少,局部壳层就很薄在高温时就会开裂。
改进措施:将蜡件的边角在模具上做出R角,模具上做不出的,就要求工人将边角倒角。
5.2由于模壳棱角部位浆砂粘附的比较少, 在四层或者五层后绑铁丝加固。
棱角处砂子粘得少,在制壳时撒砂须撒匀,尖角处轻轻按上撒的砂子。
5.3对于容易裂壳的产品,组树时,将蜡模(产生裂隙)的两边平面上组焊长方形的工艺钉,使壳层在高温时收缩受阻(定位钉阻碍壳层收缩),防止裂壳。
5.4用氯化铵、氯化铝交替硬化涂层:面层氯化铵硬化,二层用氯化铝硬化;三层氯化铵硬化,四层氯化铝硬化。
这样交替硬化各层涂层,其硬化效果可能会好一些。
5.5加固层用氯化铝和氯化铵混合溶液(氯化铵与氯;硬化,这样硬化的壳层强度会更好一些(氯化铝内掺氯;5.6模壳制好,须在8小时后脱蜡;5.7焙烧模壳时不要一直升温,升到350度左右保;850℃保温;5.8下班前洒水在浆料表面解决结皮,此法操作不当;为给浆料桶加盖;6.裂壳的补救措施;6.1焙烧后裂开的模壳,将模壳拿到一边,让模壳稍;层的稀浆料浸渍一下,让浆料5.5加固层用氯化铝和氯化铵混合溶液(氯化铵与氯化铝按照一定的比例配制)硬化,这样硬化的壳层强度会更好一些(氯化铝内掺氯化铵或氯化镁做复合型硬化剂进行硬化)。
5.6模壳制好,须在8小时后脱蜡。
另外模壳焙烧前最好先风干。
5.7焙烧模壳时不要一直升温,升到350度左右保温0.5~1小时,然后再升温至850℃保温。
5.8下班前洒水在浆料表面解决结皮,此法操作不当会造成型壳强度降低,须改为给浆料桶加盖。
6.裂壳的补救措施6.1焙烧后裂开的模壳,将模壳拿到一边,让模壳稍稍冷却之后,用水玻璃加固层的稀浆料浸渍一下,让浆料渗进裂开的缝隙之中去,然后就可以拿去接钢水。
6.2模壳焙烧后发生裂隙,从焙烧炉内拿出,让模壳浇口杯朝下防置,让其冷却到常温后,用塑料袋将浇口杯口套住,然后将模壳按进水玻璃溶液中,让水玻璃溶液进入裂隙中,拿出、风干,再将模壳在加固层浆料中补做一层涂层,再做一下半层,半层硬化后,自然晾干,然后就可以直接浇注钢水了,当然能够烘烤一下更好。
6.3裂壳的模壳用树脂砂胶合剂直接修补,烘烤下就可以浇注,效果很好。
7.结论语水玻璃模壳裂壳,是熔模铸造行业的一个通病,在生产过程中时有发生,给企业造成了不小的损失。