复合材料界面制备技术的研究发展现状
功能复合材料研究报告
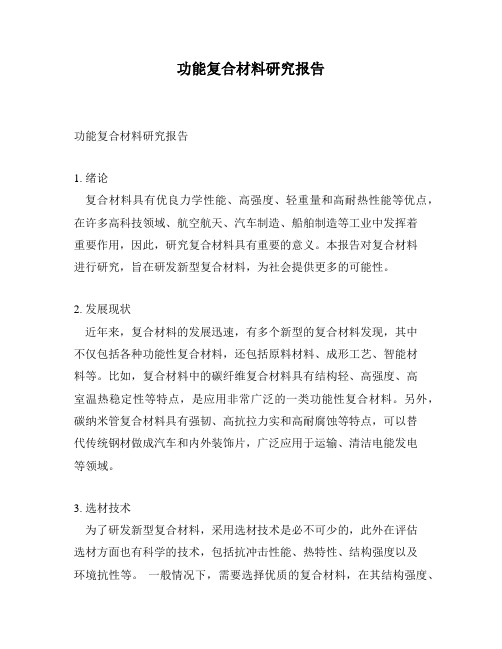
功能复合材料研究报告功能复合材料研究报告1. 绪论复合材料具有优良力学性能、高强度、轻重量和高耐热性能等优点,在许多高科技领域、航空航天、汽车制造、船舶制造等工业中发挥着重要作用,因此,研究复合材料具有重要的意义。
本报告对复合材料进行研究,旨在研发新型复合材料,为社会提供更多的可能性。
2. 发展现状近年来,复合材料的发展迅速,有多个新型的复合材料发现,其中不仅包括各种功能性复合材料,还包括原料材料、成形工艺、智能材料等。
比如,复合材料中的碳纤维复合材料具有结构轻、高强度、高室温热稳定性等特点,是应用非常广泛的一类功能性复合材料。
另外,碳纳米管复合材料具有强韧、高抗拉力实和高耐腐蚀等特点,可以替代传统钢材做成汽车和内外装饰片,广泛应用于运输、清洁电能发电等领域。
3. 选材技术为了研发新型复合材料,采用选材技术是必不可少的,此外在评估选材方面也有科学的技术,包括抗冲击性能、热特性、结构强度以及环境抗性等。
一般情况下,需要选择优质的复合材料,在其结构强度、复位性能等方面能够达到一定程度,以保证研发出新型复合材料能够满足社会对复合材料性能要求的目的。
4. 工艺及加工技术为了能够研发出满足社会环境要求的新型复合材料,制造过程中应考虑到材料的热加工返活性以及生产中容易受到的变形破坏,以选取合适的工艺流程和机床来实现高效的加工,以达到降低成本,提高产品性能的目的。
5. 控制及新技术目前复合材料的研究面临着许多技术上的挑战,比如,多少量产、提高品质和提高运行能力等。
新研发出来的复合材料不仅要求有更优质的性能,而且要求在更短的时间内弥补生产和运行中的损耗,从而改善复合材料的生产效率,增强其应用能力。
6. 结论综上所述,研发复合材料有许多好处,是应用非常普及的。
本文研究报告综述了复合材料的发展现状、选材技术、工艺及加工技术及控制及新技术等,有助于研发新型复合材料,使其应用于社会中,为社会发展做出贡献。
陶瓷纤维复合材料的制备与性能研究
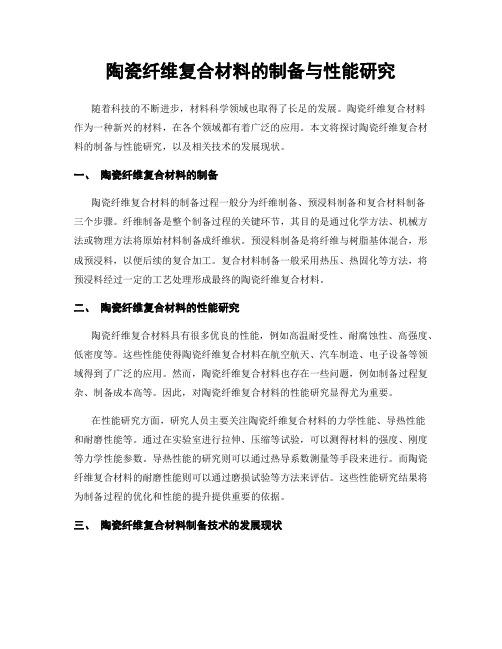
陶瓷纤维复合材料的制备与性能研究随着科技的不断进步,材料科学领域也取得了长足的发展。
陶瓷纤维复合材料作为一种新兴的材料,在各个领域都有着广泛的应用。
本文将探讨陶瓷纤维复合材料的制备与性能研究,以及相关技术的发展现状。
一、陶瓷纤维复合材料的制备陶瓷纤维复合材料的制备过程一般分为纤维制备、预浸料制备和复合材料制备三个步骤。
纤维制备是整个制备过程的关键环节,其目的是通过化学方法、机械方法或物理方法将原始材料制备成纤维状。
预浸料制备是将纤维与树脂基体混合,形成预浸料,以便后续的复合加工。
复合材料制备一般采用热压、热固化等方法,将预浸料经过一定的工艺处理形成最终的陶瓷纤维复合材料。
二、陶瓷纤维复合材料的性能研究陶瓷纤维复合材料具有很多优良的性能,例如高温耐受性、耐腐蚀性、高强度、低密度等。
这些性能使得陶瓷纤维复合材料在航空航天、汽车制造、电子设备等领域得到了广泛的应用。
然而,陶瓷纤维复合材料也存在一些问题,例如制备过程复杂、制备成本高等。
因此,对陶瓷纤维复合材料的性能研究显得尤为重要。
在性能研究方面,研究人员主要关注陶瓷纤维复合材料的力学性能、导热性能和耐磨性能等。
通过在实验室进行拉伸、压缩等试验,可以测得材料的强度、刚度等力学性能参数。
导热性能的研究则可以通过热导系数测量等手段来进行。
而陶瓷纤维复合材料的耐磨性能则可以通过磨损试验等方法来评估。
这些性能研究结果将为制备过程的优化和性能的提升提供重要的依据。
三、陶瓷纤维复合材料制备技术的发展现状随着材料科学的发展,陶瓷纤维复合材料制备技术也在不断创新和完善。
传统的制备方法虽然已经取得了一定的成果,但随着应用需求的不断增加,亟需更高效、节能、环保的制备方法。
近年来,研究人员提出了一系列新的制备技术,例如增强型化学气相沉积技术、溶胶-凝胶法等。
这些新技术能够更好地控制复合材料的结构和性能,提高制备效率和质量。
此外,一些新材料的引入和改性也为陶瓷纤维复合材料的制备提供了更多的选择。
聚乳酸基纳米复合材料的研究现状及其发展前景

聚乳酸基纳米复合材料的研究现状及其发展前景聚乳酸基纳米复合材料是一种由聚乳酸 (PLA) 和其他纳米材料组成的复合材料。
目前,聚乳酸基纳米复合材料的研究现状及其发展前景非常广阔,具体如下:
一、研究现状
1. 材料制备技术:目前,聚乳酸基纳米复合材料的制备技术主要包括溶剂热反应、溶胶 - 凝胶法、电化学沉积法等。
这些方法不仅可以控制复合材料的组成和结构,还可以提高复合材料的性能。
2. 材料性能:聚乳酸基纳米复合材料具有优异的力学性能、光学性能、生物相容性和降解性等。
其中,PLA 纳米复合材料的力学性能比纯 PLA 提高了近10 倍,光学性能也得到了显著提高。
3. 应用领域:聚乳酸基纳米复合材料的应用领域非常广泛,包括生物医学、光学、电子学、环保等领域。
例如,PLA 纳米复合材料可以用于生物传感器、生物医学材料、光学器件等方面。
二、发展前景
1. 生物医学应用:聚乳酸基纳米复合材料在生物医学领域具有广泛的应用前景。
例如,PLA 纳米复合材料可以用于生物传感器、生物医学材料、药物释放系统等。
2. 光学应用:聚乳酸基纳米复合材料在光学领域具有广泛的应用前景。
例如,PLA 纳米复合材料可以用于光学器件、太阳能电池等。
3. 电子学应用:聚乳酸基纳米复合材料在电子学领域具有广泛的应用前景。
例如,PLA 纳米复合材料可以用于电子器件、半导体器件等。
4. 环保应用:聚乳酸基纳米复合材料在环保领域具有广泛的应用前景。
例如,PLA 纳米复合材料可以用于水处理、大气污染治理等方面。
总的来说,聚乳酸基纳米复合材料具有优异的性能和良好的发展前景,将成为未来材料领域的研究热点之一。
(完整word版)镁基复合材料制备技术、性能及应用发展概况

镁基复合材料制备技术、性能及应用发展概况摘要:镁基复合材料因其轻量化和高性能而成为当今高新技术领域中最富竞争力和最有希望采用的复合材料之一。
大致笔述了常用镁基复合材料研究概况、制备技术、性能及应用前景。
关键词:镁基复合材料制备技术性能应用Fabrication,Properties and Application of M agnesium—matrix CompositesDONG Qun CHEN Liqing ZHAO Mingjiu BI Jing(Institute of Metal Research,Chinese Academy of Sciences,Shenyang 110016,China)Abstract Magnesium—matrix composites with lightweight and high performance are becoming one of themost competitive and promising candidates in the applications of high—tech fields.An overview is made on the fabri—ating techniques,mechanical properties and applications for the typical magnesium—matrix composites,and theresearch trend is proposedKey words magnesium matrix composite,fabrication,properties,application. 0引言:镁基复合材料是继铝基复合材料之后又一具有竞争力的轻金属基复合材料【E1】,主要特点是密度低、比强度和比刚度高,同时还具有良好的耐磨性、耐高温性、耐冲击性、优良的减震性能及良好的尺寸稳定性和铸造性能等;此外,还具有电磁屏蔽和储氢特性等,是一类优秀的结构与功能材料,也是当今高新技术领域中最有希望采用的复合材料之一;在航空航天、军工产品制造、汽车以及电子封装等领域中具有巨大的应用前景。
国内外碳纤维复合材料现状及研究开发方向概要

国内外碳纤维复合材料现状及研究开发方向概要碳纤维复合材料是一种具有很高强度和轻质化特性的新型材料。
它由碳纤维和树脂等基质材料组成,具有优异的力学性能和低密度,广泛应用于航空航天、汽车、船舶、体育器材等领域。
本文将对国内外碳纤维复合材料的现状以及研究开发方向进行概述。
首先,国内外碳纤维复合材料的现状可以概括为以下几个方面。
一是碳纤维复合材料在航空航天领域的应用。
由于碳纤维复合材料具有高强度、低密度和热稳定性等特点,被广泛应用于航空航天领域,如飞机机体、发动机和燃气涡轮等部件。
二是碳纤维复合材料在汽车领域的应用。
汽车制造商越来越倾向于采用碳纤维复合材料制作汽车车身和结构件,以提高汽车的燃油效率和减轻车重,提高车辆的性能。
三是碳纤维复合材料在体育器材领域的应用。
碳纤维复合材料制作的高级运动器材,如高尔夫球杆、网球拍和自行车等,具有很高的刚性和强度,能够提高运动员的表现水平。
四是碳纤维复合材料在船舶领域的应用。
船舶结构件的重量和强度对于船舶的性能至关重要。
碳纤维复合材料具有高强度和轻质化特性,因此被广泛应用于船舶制造,可以提高船舶的性能和节能减排。
接下来,本文将重点讨论国内外碳纤维复合材料的研究开发方向。
一是开发新型碳纤维原料。
目前,市场上主要使用的碳纤维原料是聚丙烯腈纤维。
研究人员正在开发新型纤维原料,如石墨烯、纳米碳纤维等,以提高碳纤维的力学性能和热稳定性。
二是改善碳纤维与基质材料的界面粘结性能。
碳纤维与树脂等基质材料的界面粘结性能对复合材料的力学性能和耐久性影响很大。
研究人员正在探索提高界面粘结性能的方法,如表面改性和介入增韧等。
三是提高碳纤维复合材料的制备工艺。
制备工艺是影响碳纤维复合材料质量的关键因素之一、研究人员正在开发新的制备工艺,如预浸法、纺丝法和层合法等,以提高复合材料的力学性能和制造效率。
四是研究碳纤维复合材料的寿命与损伤机理。
碳纤维复合材料容易受到外界环境和应力加载的影响,会出现疲劳和损伤现象。
铝基复合材料的发展现状与研究样本
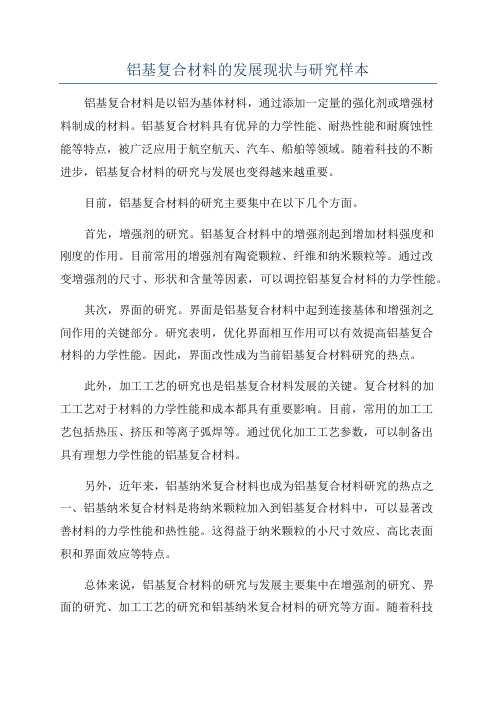
铝基复合材料的发展现状与研究样本铝基复合材料是以铝为基体材料,通过添加一定量的强化剂或增强材料制成的材料。
铝基复合材料具有优异的力学性能、耐热性能和耐腐蚀性能等特点,被广泛应用于航空航天、汽车、船舶等领域。
随着科技的不断进步,铝基复合材料的研究与发展也变得越来越重要。
目前,铝基复合材料的研究主要集中在以下几个方面。
首先,增强剂的研究。
铝基复合材料中的增强剂起到增加材料强度和刚度的作用。
目前常用的增强剂有陶瓷颗粒、纤维和纳米颗粒等。
通过改变增强剂的尺寸、形状和含量等因素,可以调控铝基复合材料的力学性能。
其次,界面的研究。
界面是铝基复合材料中起到连接基体和增强剂之间作用的关键部分。
研究表明,优化界面相互作用可以有效提高铝基复合材料的力学性能。
因此,界面改性成为当前铝基复合材料研究的热点。
此外,加工工艺的研究也是铝基复合材料发展的关键。
复合材料的加工工艺对于材料的力学性能和成本都具有重要影响。
目前,常用的加工工艺包括热压、挤压和等离子弧焊等。
通过优化加工工艺参数,可以制备出具有理想力学性能的铝基复合材料。
另外,近年来,铝基纳米复合材料也成为铝基复合材料研究的热点之一、铝基纳米复合材料是将纳米颗粒加入到铝基复合材料中,可以显著改善材料的力学性能和热性能。
这得益于纳米颗粒的小尺寸效应、高比表面积和界面效应等特点。
总体来说,铝基复合材料的研究与发展主要集中在增强剂的研究、界面的研究、加工工艺的研究和铝基纳米复合材料的研究等方面。
随着科技的不断进步和社会对材料性能的不断需求,铝基复合材料在实际应用中的发展前景将会更加广阔。
航空航天先进复合材料研究现状及发展趋势

1、高强度、高刚度
先进复合材料具有高强度、高刚度的特点,能够承受较大的载荷,并保持结 构的稳定性。
2、重量轻
先进复合材料的密度较低,相较于传统金属材料,其重量轻可达50%-70%。
3、耐腐蚀性强
先进复合材料具有较好的耐腐蚀性,可以在各种恶劣环境中长期使用。
4、可设计性强
先进复合材料可以通过不同的工艺和组合方式,实现各种不同性能和功能的 材料设计。
航空航天先进复合材料研究现 状及发展趋势
目录
01 一、走进航空航天复 合材料
02 二、航空航天先进复 合材料的研究现状
03 三、航空航天先进复 合材料的发展趋势
04 四、总结
05 参考内容
随着航空航天技术的飞速发展,对材料的要求也日益苛刻。作为一种新兴的 材料,先进复合材料在航空航天领域的应用越来越广泛。本次演示将介绍航空航 天先进复合材料的研究现状及其发展趋势。
ቤተ መጻሕፍቲ ባይዱ
3、智能化
未来先进复合材料将朝着智能化方向发展,实现材料的自我感知、自我修复、 自我控制等智能化功能,提高材料的使用效率和安全性。
4、广泛应用化
随着先进复合材料制备技术的不断完善和成本的逐渐降低,未来先进复合材 料将广泛应用于各种领域,包括航空、航天、汽车、船舶、电力、医疗等。
四、结论
先进复合材料作为一种新兴的材料,具有高强度、高刚度、重量轻、耐腐蚀 性强和可设计性强等特点,在航空航天领域有着广泛的应用前景。未来,随着科 技的不断发展和技术的不断完善,先进复合材料将朝着高性能化、绿色环保化、 智能化和广泛应用化方向发展。相信在不久的将来,先进复合材料将在航空航天 领域发挥更大的作用,推动航空航天事业的不断发展。
4.跨领域合作与交流
航空航天先进复合材料研究现状及发展趋势

航空航天先进复合材料研究现状及发展趋势航空航天先进复合材料是用于航空航天领域的高性能材料,由于其优
异的机械、物理和化学性能,在现代航空航天技术中得到了广泛应用。
这
种材料通常由纤维增强聚合物基体组成,具有高强度、低密度、高刚度、
耐热性和抗腐蚀性等特点,因此被广泛用于制造飞机、导弹、航天器等。
目前,航空航天先进复合材料的研究主要集中在以下几个方面:
1.复合材料制备技术:包括预浸料、热成型、自动化制造等多种技术,目的是提高复合材料的质量和生产效率。
2.复合材料性能研究:包括复合材料的强度、刚度、热膨胀系数、热
传导率、阻燃性等多个方面的研究,以满足不同的使用需求。
3.复合材料的形态和结构控制:包括复合材料的制备、表面处理、氧
化层控制、纤维方向控制等多个方面的研究,以控制复合材料的性能和使
用寿命。
4.复合材料的性能评估:通过实验测试和数学建模,评估复合材料的
机械、物理和化学性能,并为材料的应用提供理论依据和技术支持。
未来,航空航天先进复合材料的研究将继续在以上几个方面进行深入
探索,同时还将面临新的挑战和机遇。
例如,需要开发更高性能的复合材料,实现更低成本的生产技术,探索新的材料组合和形态,以适应不断发
展的航空航天技术的需求。
层状金属复合材料制备技术现状及发展方向

e n
a t l D ir
e c
tio
n
fo
r
M
a n u
fa
c
tu
r
in g T e c hn iq u
e o
f L
a m
in
a
r Co m po site
a t l
r a c
Me
t
n
g X ia
pa pe
e s
,
jin
pre
g
s e n
A bst
:T h i s
r
ts t he
,
m a n u
fa
,
延 长零部件
。
1 2
.
固 液连铸法
一
取 得 良好 的 综合 经 济 效 益
是将
。
一
种 金 属 液 体 连续浇 注 到 中 间 有另
,
一
种金
层 状 金 属 复合 材 料 的 生 产 方 法 有 多 种
工 艺 属 性 划 分 可 分 为三
一
按照
、
属 芯 材 的 结 晶器 中
外 层 金 属 凝 固 后 将 芯 材包 覆 形
类 : 固 固相 复 合 法
。
液
。
一
成 复 合铸 坯
。
芯 材 表 面需 要 进 行 表 面 清 理 并 涂上 防
,
固相 复合 法
、
液 液 相 复合 法
一
本文介 绍 后 两 种
锈 涂料
。
复 合铸 坯 结 合 界 面 质 量 较 差
存 在 气孔
、
夹 渣 等缺 陷 (见 图 2 ) j
1
四川复合材料发展现状及未来趋势分析
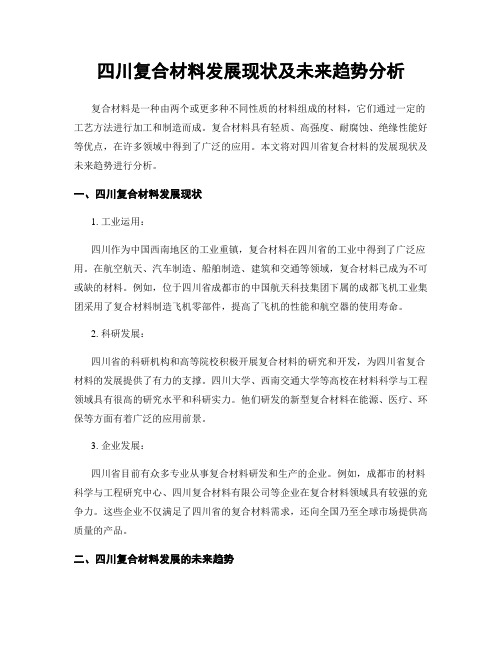
四川复合材料发展现状及未来趋势分析复合材料是一种由两个或更多种不同性质的材料组成的材料,它们通过一定的工艺方法进行加工和制造而成。
复合材料具有轻质、高强度、耐腐蚀、绝缘性能好等优点,在许多领域中得到了广泛的应用。
本文将对四川省复合材料的发展现状及未来趋势进行分析。
一、四川复合材料发展现状1. 工业运用:四川作为中国西南地区的工业重镇,复合材料在四川省的工业中得到了广泛应用。
在航空航天、汽车制造、船舶制造、建筑和交通等领域,复合材料已成为不可或缺的材料。
例如,位于四川省成都市的中国航天科技集团下属的成都飞机工业集团采用了复合材料制造飞机零部件,提高了飞机的性能和航空器的使用寿命。
2. 科研发展:四川省的科研机构和高等院校积极开展复合材料的研究和开发,为四川省复合材料的发展提供了有力的支撑。
四川大学、西南交通大学等高校在材料科学与工程领域具有很高的研究水平和科研实力。
他们研发的新型复合材料在能源、医疗、环保等方面有着广泛的应用前景。
3. 企业发展:四川省目前有众多专业从事复合材料研发和生产的企业。
例如,成都市的材料科学与工程研究中心、四川复合材料有限公司等企业在复合材料领域具有较强的竞争力。
这些企业不仅满足了四川省的复合材料需求,还向全国乃至全球市场提供高质量的产品。
二、四川复合材料发展的未来趋势1. 技术创新:随着科技的不断进步,新型复合材料的研究发展将成为未来的重要方向。
四川省的科研机构和高等院校应加大对复合材料的研发力度,提升复合材料的设计、制备和性能测试等方面的技术水平。
通过技术创新,推动四川省复合材料产业向高端产品方向发展。
2. 行业协同:四川省应该加强与其他相关行业的合作,促进不同领域之间的协同创新。
比如,汽车制造与复合材料的结合,可以提高汽车的安全性和燃油经济性。
建筑与复合材料的结合,可以提高建筑物的抗震能力和节能效果。
通过行业协同,可以拓宽复合材料的市场应用领域,实现产业的多元化、全面化发展。
陶瓷基复合材料的研究现状与发展前景

陶瓷基复合材料的研究现状与发展前景目前,陶瓷基复合材料的研究主要集中在以下几个方面:1.多相复合材料的设计与制备:陶瓷基复合材料通常由陶瓷基质和强化相组成,通过调控两者之间的相互作用,可以实现材料性能的优化。
目前,研究者们通过改变不同相的比例、尺寸和形态,以及引入适量的界面相来实现复合材料的设计。
此外,也有学者通过设计多层结构、梯度结构和纳米结构等方法来增加材料的界面面积和界面结合强度,从而提高材料的力学性能和耐磨性能。
2.陶瓷基复合材料的性能改善:陶瓷基复合材料的一个主要目标是提高其力学性能和耐磨性能。
为此,研究者在陶瓷基复合材料中引入了各种强化相,如碳化硅、碳化硼、氮化硅等,以提高材料的硬度和强度。
此外,还有学者通过控制复合材料的纤维方向、制备多孔材料等方法,来改善材料的韧性和抗撞击性能。
同时,还有部分研究者在陶瓷基复合材料中引入纳米颗粒、纳米管道和纳米纤维等,以提高材料的导电性、导热性和光学性能。
3.陶瓷基复合材料的制备技术:陶瓷基复合材料的制备通常包括两个步骤,即原料的混合和制备过程的选择。
在混合过程中,常用的方法包括干法混合、湿法混合和机械合金化等。
而在制备过程的选择上,常用的方法包括烧结、热压、热等静压、溶胶凝胶法、化学气相沉积等。
在制备技术方面,人们的研究重点主要集中在提高材料的致密性、结晶度和尺寸的控制等方面。
陶瓷基复合材料在各个领域中都有广泛的应用前景。
例如,在航空航天领域,陶瓷基复合材料可以用于制造高温结构件、涡轮叶片和发动机喷嘴等部件,以提高其耐高温和高应力环境下的性能。
在电子设备领域,陶瓷基复合材料可以用于制造封装材料、电阻器和散热器等器件,以提高其耐高温和导热性能。
在汽车制造领域,陶瓷基复合材料可以用于制造发动机和刹车系统等重要零部件,以提高其耐磨和耐蚀性能。
综上所述,陶瓷基复合材料是一种性能优异、应用前景广阔的材料。
通过不断地改进材料的设计和制备技术,陶瓷基复合材料有望在各个领域中得到更广泛的应用。
复合材料界面制备技术的研究发展现状
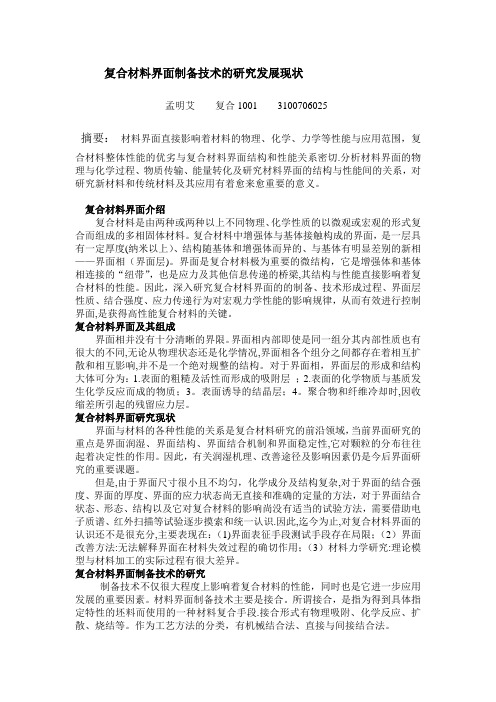
复合材料界面制备技术的研究发展现状孟明艾复合1001 3100706025摘要:材料界面直接影响着材料的物理、化学、力学等性能与应用范围,复合材料整体性能的优劣与复合材料界面结构和性能关系密切.分析材料界面的物理与化学过程、物质传输、能量转化及研究材料界面的结构与性能间的关系,对研究新材料和传统材料及其应用有着愈来愈重要的意义。
复合材料界面介绍复合材料是由两种或两种以上不同物理、化学性质的以微观或宏观的形式复合而组成的多相固体材料。
复合材料中增强体与基体接触构成的界面,是一层具有一定厚度(纳米以上)、结构随基体和增强体而异的、与基体有明显差别的新相——界面相(界面层)。
界面是复合材料极为重要的微结构,它是增强体和基体相连接的“纽带”,也是应力及其他信息传递的桥梁,其结构与性能直接影响着复合材料的性能。
因此,深入研究复合材料界面的的制备、技术形成过程、界面层性质、结合强度、应力传递行为对宏观力学性能的影响规律,从而有效进行控制界面,是获得高性能复合材料的关键。
复合材料界面及其组成界面相并没有十分清晰的界限。
界面相内部即使是同一组分其内部性质也有很大的不同,无论从物理状态还是化学情况,界面相各个组分之间都存在着相互扩散和相互影响,并不是一个绝对规整的结构。
对于界面相,界面层的形成和结构大体可分为:1.表面的粗糙及活性而形成的吸附层;2.表面的化学物质与基质发生化学反应而成的物质;3。
表面诱导的结晶层;4。
聚合物和纤维冷却时,因收缩差所引起的残留应力层。
复合材料界面研究现状界面与材料的各种性能的关系是复合材料研究的前沿领域,当前界面研究的重点是界面润湿、界面结构、界面结合机制和界面稳定性,它对颗粒的分布往往起着决定性的作用。
因此,有关润湿机理、改善途径及影响因素仍是今后界面研究的重要课题。
但是,由于界面尺寸很小且不均匀,化学成分及结构复杂,对于界面的结合强度、界面的厚度、界面的应力状态尚无直接和准确的定量的方法,对于界面结合状态、形态、结构以及它对复合材料的影响尚没有适当的试验方法,需要借助电子质谱、红外扫描等试验逐步摸索和统一认识.因此,迄今为止,对复合材料界面的认识还不是很充分,主要表现在:(1)界面表征手段测试手段存在局限;(2)界面改善方法:无法解释界面在材料失效过程的确切作用;(3)材料力学研究:理论模型与材料加工的实际过程有很大差异。
先进树脂基复合材料技术发展及应用现状

先进树脂基复合材料技术发展及应用现状一、本文概述随着科技的不断进步和工业的快速发展,先进树脂基复合材料作为一种高性能、轻质、高强度的材料,已经在航空航天、汽车制造、建筑、体育器材等众多领域得到了广泛应用。
本文旨在对先进树脂基复合材料技术的发展历程进行深入剖析,并探讨其在各个领域的应用现状。
通过对国内外相关研究的综述,本文将总结先进树脂基复合材料技术的发展趋势,以及面临的挑战和机遇,以期为推动该领域的技术进步和产业发展提供参考。
在文章的结构上,本文首先将对先进树脂基复合材料的定义、分类及特点进行阐述,为后续的研究奠定理论基础。
接着,文章将回顾先进树脂基复合材料技术的发展历程,分析其在不同历史阶段的主要特点和成就。
在此基础上,文章将重点探讨先进树脂基复合材料在各个领域的应用现状,包括航空航天、汽车制造、建筑、体育器材等。
文章还将关注先进树脂基复合材料技术在实际应用中面临的挑战,如成本、性能优化、环保等问题,并提出相应的解决方案。
文章将展望先进树脂基复合材料技术的发展前景,探讨其在未来可能的发展趋势和创新点。
通过对先进树脂基复合材料技术的深入研究和分析,本文旨在为相关领域的科研人员、工程师和管理者提供有益的参考和启示,推动先进树脂基复合材料技术的持续发展和创新。
二、先进树脂基复合材料技术的发展先进树脂基复合材料技术的发展经历了从简单的层压复合材料到高性能、多功能复合材料的演变。
近年来,随着科技的不断进步,该领域取得了显著的突破和进展。
树脂体系的创新:树脂作为复合材料的基体,其性能直接影响着复合材料的整体性能。
传统的树脂体系如环氧树脂、酚醛树脂等,虽然在很多领域有广泛应用,但随着性能要求的提升,新型树脂体系如聚酰亚胺树脂、双马来酰亚胺树脂等逐渐崭露头角。
这些新型树脂具有更高的热稳定性、更低的介电常数和介电损耗,以及更好的机械性能,为先进树脂基复合材料的发展提供了强大的支撑。
增强材料的多样化:增强材料是复合材料中的关键组成部分,其种类和性能直接影响着复合材料的力学性能和功能特性。
铝基复合材料的制造方法、研究现状及发展

铝基复合材料的制造方法、研究现状及发展李杨20090560材料科学与工程学院090201摘要:本文介绍了铝基复合材料的设计与制备、应用,重点讲述了国内外的研究现状和发展趋势。
关键词:铝基复合,设计与制备,应用,研究现状及发展前言复合材料是应现代科学发展需求而涌现出具有强大生命力的材料,在金属基复合材料中表现尤为明显。
金属基复合材料有铝基、镍基、镁基、抬基、铁基复合材料等多种,其中铝基复合材料发展最快而成为主流。
本文主要对国内外铝及复合材料的研究现状进行简要评述,主要包括材料的设计与制备、界面、性能、应用等方面。
一、铝基复合材料的设计与制备1.基体材料的选择铝基复合材料的基体可以是纯铝也可以是铝合金,其中采用铝合金居多。
工业上常采用的铝合金基体有Al-Mg、Al-Si、Al-Cu、Al-Li和Al-Fe等。
如希望减轻构件质量并提高刚度,可以采用Al-Li合金做基体;用高温的零部件则采用Al-Fe合金做基体;经过处理后的Al-Cu合金强度高、且有非常好的塑性、韧性和抗蚀性、易焊接、易加工,可考虑作这些要求高的基体;增强体和基体之间的热膨胀失配在任何复合材料中都难以避免,为了有效降低复合材料的膨胀系数,使其与半导体材料或陶瓷基片保持低匹配常采用Al-Si为基体和采用不同粒径的颗粒制备高体积分数的复合材料。
基体的强度并不是它的强度越高复合材料的性能就越好。
如纤维增强铝基复合材料中,用纯铝或含有少量合金元素的铝合金作为基体,就比用高强度铝合金做基体要好的多,用高强度铝合金作基体组成的碳纤维的性能反而低。
因此,只有当基体金属与增强体合理搭配时,才能充分发挥基体材料和增强相的性能优势。
2.增强材料的选择增强材料主要有纤维、晶须以及颗粒。
为了提高基体金属的性能,增强材料的本身需要具备特殊的性能,如高强度、高弹性模量、低密度、高硬度、高耐磨性、良好的化学稳定性、增强体与基体金属有良好的润湿性等。
B、Al2O3、Si、和C纤维等是最早的纤维材料,该材料的性能优异,但高昂的成本限制了它们的广泛发展及应用。
国内复合材料发展趋势

国内复合材料发展趋势全文共四篇示例,供读者参考第一篇示例:国内复合材料产业正迅猛发展,成为制造业的重要支柱之一。
复合材料是指由两种或两种以上不同性质的材料组合而成的材料,具有优良的力学性能和耐候性,被广泛应用于航空航天、汽车、船舶、建筑、体育用品等领域。
随着技术的不断创新和市场需求的提升,国内复合材料产业正呈现出一些发展趋势。
复合材料在航空航天领域得到广泛应用。
航空航天是复合材料的主要应用领域之一,因为其具有优良的轻质高强度特性。
随着航空航天产业的快速发展和对轻质高强材料需求的增加,复合材料在该领域的应用将会越来越广泛。
我国自主研发的C919大型客机采用了大量的复合材料,大大减轻了飞机的重量,提高了燃油效率。
建筑领域也开始广泛应用复合材料。
传统的建筑材料,如钢、混凝土等,存在重量大、耗能高、施工周期长等问题,而复合材料具有轻质高强、抗腐蚀、易加工等优点,正逐渐成为建筑领域的新宠。
建筑外墙、屋顶、桥梁等结构可以采用复合材料制成,不仅美观大方,还具有较长的使用寿命和较低的维护成本。
随着技术的不断创新和市场需求的增加,国内复合材料产业将迎来更广阔的发展机遇。
未来,随着科技的进步,复合材料的性能将会不断提升,应用领域也会不断拓展。
政府对于节能环保产业的支持力度也将会增加,为复合材料产业的发展提供更多的政策红利。
国内复合材料产业将会迎来更加光明的发展前景。
国内复合材料产业正处于快速发展的阶段,将会在航空航天、汽车、建筑等领域发挥越来越重要的作用。
随着技术的不断创新和市场需求的增加,复合材料产业将迎来更广阔的发展空间,为中国制造业的升级和转型注入新的动力。
相信在不乏合作伙伴的共同努力下,国内复合材料产业一定会取得更加辉煌的成就。
【本文共1306字】第二篇示例:一、国内复合材料发展现状国内复合材料产业始于上世纪80年代,经过几十年的发展,已经形成了一定规模的产业体系。
目前,中国复合材料产业已经广泛应用于航空航天、汽车、建筑、体育器材等领域,成为促进经济发展和技术进步的重要材料之一。
复合材料研究进展和应用现状

复合材料研究进展和应用现状随着科技的发展,越来越多的新材料被开发出来并应用于各个领域。
复合材料便是其中之一,它是指两种或以上的不同材料在某一方面有协同作用的新材料。
复合材料具有轻质、高强度、耐腐蚀、耐磨损、隔热性能好等优点,因此在航空、航天、汽车、船舶、建筑、电子等领域都有广泛的应用。
本文将从复合材料的种类、应用领域、研究进展等方面介绍复合材料的发展现状。
一、种类复合材料广泛存在于我们生活中,既有自然产生的复合材料,如树木、贝壳等,也有人工合成的复合材料。
人工合成的复合材料多为高分子复合材料和无机复合材料。
1.高分子复合材料高分子复合材料是指由高分子基体和增强相组成的复合材料,在高分子基体中嵌入了颗粒、纤维、薄膜等增强相,形成了具有一定力学性能的材料。
常见的高分子复合材料有玻璃纤维增强聚酯树脂、碳纤维增强聚酰亚胺材料等。
2.无机复合材料无机复合材料是指由无机基体和增强相组成的复合材料,无机基体可以为金属、陶瓷或玻璃等,增强相可以为颗粒、纤维、薄膜等。
常见的无机复合材料有碳化硅增强铝基复合材料、碳化硅增强氮化硅基复合材料等。
二、应用领域1.航空航天航空航天是复合材料最早应用的领域之一,航空器和航天器必须具备高度的轻量化和高性能的要求。
复合材料的轻质、高强度、耐腐蚀、耐磨损、耐高温等优点,使其成为替代金属材料的理想选择。
航空器和航天器中常用的复合材料有碳纤维增强聚酰亚胺材料、玻璃纤维增强聚酯树脂、环氧树脂基复合材料等。
2.汽车近年来,汽车行业对复合材料的需求越来越高,主要是为了减轻车身重量,降低燃油消耗和排放。
复合材料的轻质、高强度、抗冲击、耐腐蚀、隔热性能好等优点,使其成为汽车制造的理想材料。
汽车中常用的复合材料有碳纤维增强聚酰亚胺材料、玻璃纤维增强聚酯树脂、环氧树脂基复合材料等。
3.建筑复合材料在建筑领域的应用越来越广泛。
随着建筑设计对于材料轻量化、材料强度、材料可塑性及设计细节方面的要求越来越高,复合材料得到了越来越多的应用。
颗粒增强铝基复合材料制备方法及研究现状
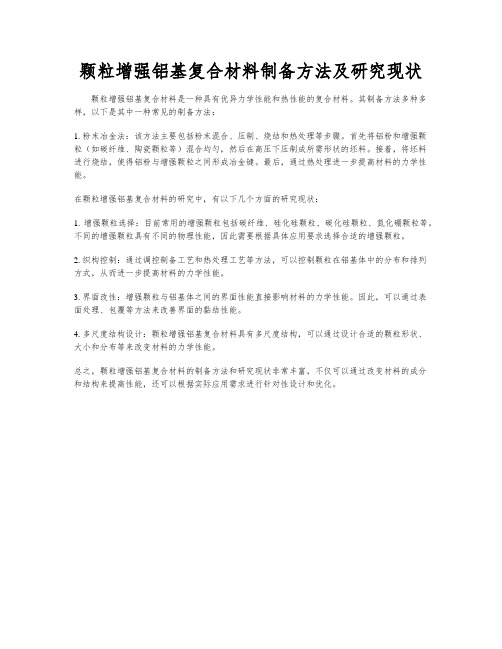
颗粒增强铝基复合材料制备方法及研究现状
颗粒增强铝基复合材料是一种具有优异力学性能和热性能的复合材料。
其制备方法多种多样,以下是其中一种常见的制备方法:
1. 粉末冶金法:该方法主要包括粉末混合、压制、烧结和热处理等步骤。
首先将铝粉和增强颗
粒(如碳纤维、陶瓷颗粒等)混合均匀,然后在高压下压制成所需形状的坯料。
接着,将坯料
进行烧结,使得铝粉与增强颗粒之间形成冶金键。
最后,通过热处理进一步提高材料的力学性能。
在颗粒增强铝基复合材料的研究中,有以下几个方面的研究现状:
1. 增强颗粒选择:目前常用的增强颗粒包括碳纤维、硅化硅颗粒、碳化硅颗粒、氮化硼颗粒等。
不同的增强颗粒具有不同的物理性能,因此需要根据具体应用要求选择合适的增强颗粒。
2. 织构控制:通过调控制备工艺和热处理工艺等方法,可以控制颗粒在铝基体中的分布和排列
方式,从而进一步提高材料的力学性能。
3. 界面改性:增强颗粒与铝基体之间的界面性能直接影响材料的力学性能。
因此,可以通过表
面处理、包覆等方法来改善界面的黏结性能。
4. 多尺度结构设计:颗粒增强铝基复合材料具有多尺度结构,可以通过设计合适的颗粒形状、
大小和分布等来改变材料的力学性能。
总之,颗粒增强铝基复合材料的制备方法和研究现状非常丰富,不仅可以通过改变材料的成分
和结构来提高性能,还可以根据实际应用需求进行针对性设计和优化。
镁基复合材料发展现状

镁基复合材料发展现状
镁基复合材料是一种具有轻质、高强度和耐腐蚀性能的材料,
具有广阔的发展前景。
目前,镁基复合材料的发展现状可以从以下
几个方面来进行分析:
1.材料研发,目前,镁基复合材料的研发主要集中在合金化、
增强相选择、界面处理等方面。
通过合金化可以改善镁基材料的强
度和耐腐蚀性能,增强相的选择和界面处理可以有效提高材料的力
学性能和耐热性能。
2.制备工艺,针对镁基复合材料的制备工艺,目前主要包括挤压、热压、粉末冶金等多种方法。
随着制备工艺的不断改进,镁基
复合材料的生产成本逐渐降低,生产效率逐步提高。
3.应用领域,镁基复合材料在航空航天、汽车制造、电子设备
等领域具有广泛的应用前景。
在航空航天领域,镁基复合材料可以
用于制造飞机结构件和发动机零部件,能够大幅减轻飞机重量,提
高燃油利用率;在汽车制造领域,镁基复合材料可以用于制造车身
结构件和发动机零部件,有望实现汽车轻量化,提高燃油经济性;
在电子设备领域,镁基复合材料可以用于制造轻薄的电子产品外壳,
提高产品的便携性和耐用性。
总的来说,镁基复合材料在材料研发、制备工艺和应用领域都取得了一定的进展,但仍然面临着一些挑战,比如界面反应控制、成本降低等问题。
随着科学技术的不断进步,相信镁基复合材料会在未来得到更广泛的应用和发展。
- 1、下载文档前请自行甄别文档内容的完整性,平台不提供额外的编辑、内容补充、找答案等附加服务。
- 2、"仅部分预览"的文档,不可在线预览部分如存在完整性等问题,可反馈申请退款(可完整预览的文档不适用该条件!)。
- 3、如文档侵犯您的权益,请联系客服反馈,我们会尽快为您处理(人工客服工作时间:9:00-18:30)。
复合材料界面制备技术的研究发展现状孟明艾复合1001 3100706025摘要:材料界面直接影响着材料的物理、化学、力学等性能与应用范围,复合材料整体性能的优劣与复合材料界面结构和性能关系密切。
分析材料界面的物理与化学过程、物质传输、能量转化及研究材料界面的结构与性能间的关系,对研究新材料和传统材料及其应用有着愈来愈重要的意义。
复合材料界面介绍复合材料是由两种或两种以上不同物理、化学性质的以微观或宏观的形式复合而组成的多相固体材料。
复合材料中增强体与基体接触构成的界面,是一层具有一定厚度(纳米以上)、结构随基体和增强体而异的、与基体有明显差别的新相——界面相(界面层)。
界面是复合材料极为重要的微结构,它是增强体和基体相连接的“纽带”,也是应力及其他信息传递的桥梁,其结构与性能直接影响着复合材料的性能。
因此,深入研究复合材料界面的的制备、技术形成过程、界面层性质、结合强度、应力传递行为对宏观力学性能的影响规律,从而有效进行控制界面,是获得高性能复合材料的关键。
复合材料界面及其组成界面相并没有十分清晰的界限。
界面相内部即使是同一组分其内部性质也有很大的不同,无论从物理状态还是化学情况,界面相各个组分之间都存在着相互扩散和相互影响,并不是一个绝对规整的结构。
对于界面相,界面层的形成和结构大体可分为:1.表面的粗糙及活性而形成的吸附层;2.表面的化学物质与基质发生化学反应而成的物质;3.表面诱导的结晶层;4.聚合物和纤维冷却时,因收缩差所引起的残留应力层。
复合材料界面研究现状界面与材料的各种性能的关系是复合材料研究的前沿领域,当前界面研究的重点是界面润湿、界面结构、界面结合机制和界面稳定性,它对颗粒的分布往往起着决定性的作用。
因此,有关润湿机理、改善途径及影响因素仍是今后界面研究的重要课题。
但是,由于界面尺寸很小且不均匀,化学成分及结构复杂,对于界面的结合强度、界面的厚度、界面的应力状态尚无直接和准确的定量的方法,对于界面结合状态、形态、结构以及它对复合材料的影响尚没有适当的试验方法,需要借助电子质谱、红外扫描等试验逐步摸索和统一认识。
因此,迄今为止,对复合材料界面的认识还不是很充分,主要表现在:(1)界面表征手段测试手段存在局限;(2)界面改善方法:无法解释界面在材料失效过程的确切作用;(3)材料力学研究:理论模型与材料加工的实际过程有很大差异。
复合材料界面制备技术的研究制备技术不仅很大程度上影响着复合材料的性能,同时也是它进一步应用发展的重要因素。
材料界面制备技术主要是接合。
所谓接合,是指为得到具体指定特性的坯料而使用的一种材料复合手段。
接合形式有物理吸附、化学反应、扩散、烧结等。
作为工艺方法的分类,有机械结合法、直接与间接结合法。
颗粒增强铝基复合材料是当前研究较多、比较成熟、应用比较广泛的金属基复合材料,SiC p/Al就是其中的一类。
以金属基基复合材料SiC p/Al为例谈谈复合材料界面的制备技术(包括SiC p/Al 复合材料制备方法、存在的技术难题和今后需要完善和进一步研究的方向)。
SiC p/Al复合材料成形技术,按增强颗粒与铝合金混合方式及成型工艺不同,可分为挤压铸造、真空吸铸法、熔融金属浸渗、粉末冶金及喷射沉积等。
1.挤压铸造挤压铸造法就是在用搅棒高速搅动的铝熔液中逐渐加入SiC颗粒增强物,待SiC颗粒得到润湿、分散均匀后将熔体浇入金属型,再用挤压铸造的方法加压成形。
因为通常非金属增强物与金属液是不润湿的,所以用普通搅拌法制造时因相互排斥而使增强物分散不均匀。
对这种方法进行改良,将金属液温度控制在液相线和固相线之间进行搅拌,这时熔液含有一定组分的固相粒子,增强物加进去,即使润湿性不好,由于固相粒子的阻挡和滞留,增强物也不会结集和偏聚,仍能得到较均匀的颗粒分散。
同样,将分散均匀的熔体浇入金属型,用挤压铸造的方法加压成形。
欧阳柳章及隋贤栋等用此方法成功地浇铸了铝基复合材料活塞,台架实验正在进行中。
2.真空吸铸法真空吸铸法是在铸形内形成一定负压条件,使液态金属或颗粒增强金属基复合材料自上而下吸入型凝固后形成固件的工艺方法。
真空吸铸法的工艺过程:将用化学沉积制备的碳化硅纤维装入钢管中,一端用铝塞密封,另一端连接真空系统。
在真空条件下,将装有纤维的钢管部位预热到高温,然后将带有铝塞的一端插入熔融的铝液中,铝塞将立即熔化,而铝液被吸入钢管中渗透到纤维。
冷却后用硝酸腐蚀掉钢管,制成复合材料。
3.熔融金属浸渗法熔融金属浸渗法是通过纤维或纤维预制件浸渍熔融态金属而制成金属基复合材料的方法。
这种方法是预先把颗粒增强材料用适当的粘结剂粘结,做成预制件,放入压型,浇入铝熔液后立即加压,使铝液渗入预制件的间隙,这样在凝固后就得到要求的铝基复合材料。
4 . 粉末冶金法粉末冶金是制取金属或用金属粉末(或金属粉末与非金属粉末的混合物)作为原料,经过成形和烧结,制造金属材料、复合以及各种类型制品的工艺技术。
粉末冶金法与生产陶瓷有相似的地方,因此,一系列粉末冶金新技术也可用于陶瓷材料的制备。
粉末冶金法是用于制备与成型非连续增强型金属基复合材料的一种传统的固态工艺法。
它是利用粉末冶金原理,将基体金属粉末和增强材料(晶须、短纤维、颗粒等)按设计要求的比例在适当的条件下均匀混合,然后再压坯、烧结或挤压成型,也可将混合料压坯后加热到基体金属的固——液相温度区内进行半固态成型,从而获得复合材料或其制件。
基体合金粉末和颗粒(晶须)的混合均匀程度及基体粉末防止氧化的问题是整个工艺的关键。
粉末冶金成型主要包括混合、固化、压制三个过程。
粉末冶金工艺是:首先采用超声波或球磨等方法,将金属粉末与增强体混匀,然后冷压预成型,得到复合坯件,最后通过热压烧结致密化获得复合材料成品。
生产过程为:(1)生产粉末。
粉末的生产过程包括粉末的制取、粉料的混合等步骤。
为改善粉末的成型性和可塑性通常加入机油、橡胶或石蜡等增塑剂。
(2)压制成型。
粉末在15-600MPa压力下,压成所需形状。
(3)烧结。
在保护气氛的高温炉或真空炉中进行。
烧结不同于金属熔化,烧结时至少有一种元素仍处于固态。
烧结过程中粉末颗粒间通过扩散、再结晶、熔焊、化合、溶解等一系列的物理化学过程,成为具有一定孔隙度的冶金产品。
(4)后处理。
一般情况下,烧结好的制件可直接使用。
但对于某些尺寸要求精度高并且有高的硬度、耐磨性的制件还要进行烧结后处理。
后处理包括精压、滚压、挤压、淬火、表面淬火、浸油、及熔渗等。
5.喷射沉积法喷射沉积法是一种将金属熔体与增强颗粒在惰性气体的推动下,通过快速凝固制备颗粒增强金属基复合材料的方法。
其具体工艺过程为:在高速惰性气体流的作用下(以氩氮等非活性气体作为载体),将铝合金在坩埚中熔化,加压流经雾化器后被高速气体分散成极细小的金属液滴,同时通过一个或几个喷嘴向雾化的金属液滴流中喷入增强颗粒Si,使金属液滴和增强颗粒同时沉降在水冷基板上,这样便制得了SiC p/Al复合材料。
SiC p/Al界面制备技术的现状及发展趋势SiC p/Al现有工艺方法虽然成功制造了SiC p/Al复合材料,但距离实际应用还有一定的差距,仅处于实验室阶段。
SiC存在铝液中,使熔液粘度提高,流动性能降低,铸造时充填性能变差,当颗粒含量增加至20%或在较低温度(<730℃)时,流动性急剧降低以致无法浇注。
铸造SiC颗粒复合材料制造过程中,由于颗粒的存在,使冷却和凝固时的温度分布、晶体生长的热力学、动力学过程等发生变化,相应地,复合材料的凝固特性、溶质再分布规律、组织特性以及一二次枝晶间距、偏析等也要发生变化。
颗粒被固溶界面所排斥和推移,聚集在界面前方的液相中。
这些问题,目前的研究还不充分,有必要深入开展工作。
目前SiC p/Al的制备还有许多问题尚待解决。
首先是它的力学性能特别是强度尚离理论值有较大差距,主要是由于SiC p/Al极易发生界面反应,对强度有较大影响。
因此,寻找保护性好又与金属浸润的涂层是十分迫切的。
碳化硅颗粒增强铝是很有发展前途的材料,特别是其界面间需要适当的粘结力才能有最佳的强度的现象,还缺乏从理论上加以定量地说明。
复合材料具有丰富的微观结构组合方式,其与宏观力学的对应性也亟待研究。
由于合金化工艺与变质处理改善界面结合状况,材料的浸润性及化学反应方面存在较大的问题,增强材料SiC与铝的润湿角大于90,因此,在液态成形中,金属液很难浸入到增强材料SiC之间,结果使材料内部形成大量孔洞缺陷。
另外,增强材料和基体材料往往在物理性能(热膨胀性、密度)、化学性能(如电化学势、组元扩散能力)及力学性能(如强度及韧性)存在较大差异,这将影响复合材料的质量。
在基体中加入合金元素,以增加金属液的粘度降低表面张力和改善润湿性及结晶形态的改变,均有利于形成结合良好的界面。
变质处理后的基体材料性能的提高可以弥补复合化以后塑性的降低,从而使所制备材料具有优异的综合性能。
此外,SiC p/Al铝基复合材料含有硬而脆的SiC颗粒,难于切削,其主要表现之一是刀具磨损迅速。
现代精密机器零件绝大多数仍需依靠机加工获得最终形状和精度,切削加工问题是刻不容缓的。
复合材料界面研究前景展望研究界面的组成、结构、性质以及界面区对复合材料的影响,要有以下几大突破:(1)改善测试手段、测得有实际意义的物理参数和对界面化学进行表征;(2)针对材料实际情况建立更好的教学模型,并进一步建立可以使用实测数据的理论模型;(3)建立微观结构和宏观性能之间的联系,理论模型和实验数据相互推动;(4)研究界面制备技术,改善工艺条件,制备性能优异的复合材料。
结束语复合材料是一门涉及到物理、化学、物理化学、传热学、金属学、力学等多学科的典型的边缘学科,目前对基础理论研究,特别是化学分析和处理,对颗粒复合材料的研究很少,各项数据和基础理论有待完善。
SiC/Al复合材料性能优良,制备工艺比较简单,成本较低,可望在机械、冶金、建材、电力等工业部门得到广泛的应用。
铝基复合材料的时代正在到来,它将在更广泛的领域得到应用,在现代化的建设中发挥更大作用。
参考文献(1)冯小明,张崇才. 复合材料. 2004(2)何湘平编译. Al-SiC复合材料铸造发展概况(1)特种铸造及有色合金,1991 (5):28(3) 朱和祥,陈国平. 碳化硅颗粒增强铝基复合材料的发展概况(1)材料导论,1995 (3):73(4) 朱建平,戴鹏芳。
铸造金属基颗粒复合材料(1)机械工程材料,1993,17 (5):1(3)吴锦波,马晓春. 铸造法制金属基复合材料研究进展(1). 材料科学与工程,1996,14 (2): 15(6)张迎远,谢永强,刘希从,SiC/Al重熔铸造复合材料研究进展,材料开发与应用,1998,13(2):40。