粉末冶金新技术-烧结
粉末冶金烧结工艺
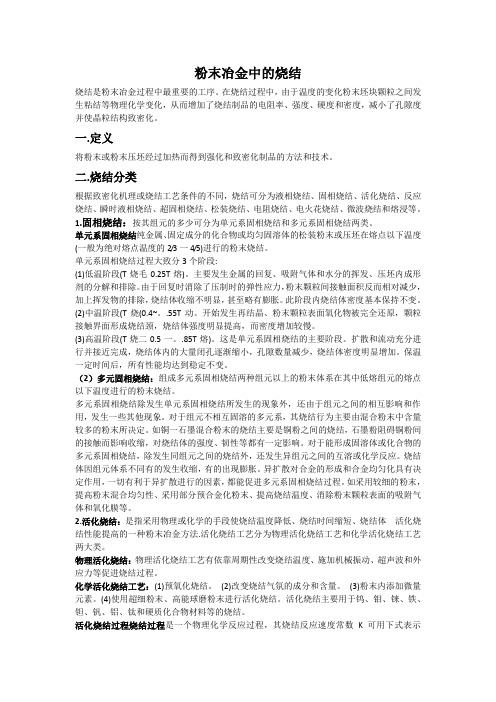
粉末冶金中的烧结烧结是粉末冶金过程中最重要的工序。
在烧结过程中,由于温度的变化粉末坯块颗粒之间发生粘结等物理化学变化,从而增加了烧结制品的电阻率、强度、硬度和密度,减小了孔隙度并使晶粒结构致密化。
一.定义将粉末或粉末压坯经过加热而得到强化和致密化制品的方法和技术。
二.烧结分类根据致密化机理或烧结工艺条件的不同,烧结可分为液相烧结、固相烧结、活化烧结、反应烧结、瞬时液相烧结、超固相烧结、松装烧结、电阻烧结、电火花烧结、微波烧结和熔浸等。
1.固相烧结:按其组元的多少可分为单元系固相烧结和多元系固相烧结两类。
单元系固相烧结纯金属、固定成分的化合物或均匀固溶体的松装粉末或压坯在熔点以下温度(一般为绝对熔点温度的2/3一4/5)进行的粉末烧结。
单元系固相烧结过程大致分3个阶段:(1)低温阶段(T烧毛0.25T熔)。
主要发生金属的回复、吸附气体和水分的挥发、压坯内成形剂的分解和排除。
由于回复时消除了压制时的弹性应力,粉末颗粒间接触面积反而相对减少,加上挥发物的排除,烧结体收缩不明显,甚至略有膨胀。
此阶段内烧结体密度基本保持不变。
(2)中温阶段(T烧(0.4~。
.55T动。
开始发生再结晶、粉末颗粒表面氧化物被完全还原,颗粒接触界面形成烧结颈,烧结体强度明显提高,而密度增加较慢。
(3)高温阶段(T烧二0.5一。
.85T熔)。
这是单元系固相烧结的主要阶段。
扩散和流动充分进行并接近完成,烧结体内的大量闭孔逐渐缩小,孔隙数量减少,烧结体密度明显增加。
保温一定时间后,所有性能均达到稳定不变。
(2)多元固相烧结:组成多元系固相烧结两种组元以上的粉末体系在其中低熔组元的熔点以下温度进行的粉末烧结。
多元系固相烧结除发生单元系固相烧结所发生的现象外,还由于组元之间的相互影响和作用,发生一些其他现象。
对于组元不相互固溶的多元系,其烧结行为主要由混合粉末中含量较多的粉末所决定。
如铜一石墨混合粉末的烧结主要是铜粉之间的烧结,石墨粉阻碍铜粉间的接触而影响收缩,对烧结体的强度、韧性等都有一定影响。
粉末烧结原理

粉末烧结原理粉末冶金是一种重要的金属材料制备技术,而粉末烧结则是粉末冶金中的一项关键工艺。
粉末烧结是指将金属或非金属粉末在一定的温度、压力和时间条件下进行加热压制,使粉末颗粒之间发生冶金结合,从而形成致密的块状材料的工艺过程。
下面将详细介绍粉末烧结的原理。
首先,粉末烧结原理的第一步是粉末的预处理。
通常情况下,粉末材料需要经过混合、干燥和成型等工艺步骤,以确保粉末颗粒的均匀性和成型性。
在混合过程中,不同种类的粉末可以被混合在一起,以获得特定性能的材料。
然后,干燥工艺可以去除粉末中的水分,有利于后续的成型工艺。
最后,成型工艺将粉末压制成特定形状的坯料,为后续的烧结工艺做好准备。
其次,粉末烧结的第二步是烧结过程。
在烧结过程中,粉末坯料被置于高温环境中,通常伴随着一定的压力。
在高温下,粉末颗粒之间会发生扩散和结合的过程,从而形成致密的晶粒结构。
在烧结过程中,温度、压力和时间是三个重要的参数,它们将直接影响到烧结后材料的密度、晶粒大小和性能。
最后,粉末烧结的第三步是后处理工艺。
烧结后的材料通常需要进行热处理、表面处理和精加工等工艺步骤,以进一步提高材料的性能和精度。
热处理可以消除烧结过程中产生的残余应力和缺陷,提高材料的强度和韧性。
表面处理可以改善材料的耐腐蚀性能和外观质量。
精加工则可以使材料达到特定的尺寸和形状要求。
总之,粉末烧结是一种重要的材料制备工艺,它通过预处理、烧结和后处理三个步骤,将粉末材料转化为致密的块状材料。
粉末烧结工艺可以制备出具有特定性能和形状的材料,广泛应用于汽车、航空航天、电子、医疗器械等领域。
通过对粉末烧结原理的深入了解,可以更好地掌握这一重要工艺,为材料制备和应用提供技术支持。
为什么高温烧结是粉末冶金的关键步骤?

为什么高温烧结是粉末冶金的关键步骤?一、高温烧结是粉末冶金的基本过程之一高温烧结在粉末冶金中扮演着至关重要的角色。
粉末冶金是利用金属或非金属粉末经过成型与烧结等工艺制得工件的一种工艺方法。
而高温烧结是这一过程中的核心环节之一,它通过高温和压力作用下,使得粉末颗粒间发生结合,从而实现零件的成型和性能的提升。
二、高温烧结有利于提高材料的致密性和机械性能高温烧结过程中,粉末颗粒在高温下经过热塑性变形,颗粒间的结合点逐渐增多,从而形成致密的结构。
通过这种高温烧结,粉末冶金材料的孔隙率可以得到有效的减小,同时材料的密度也会得到相应的提高。
致密的结构不仅有利于提高材料的强度和硬度,还可以提高其耐腐蚀和耐磨性能,从而增加零件的使用寿命。
三、高温烧结有利于改善材料的组织和相结构高温烧结过程中,粉末颗粒会发生晶粒长大、晶界迁移和晶界再稳定等过程,从而使材料的晶粒尺寸得到增大。
晶粒长大可以改变材料的力学性能和电磁性能等特性,比如提高材料的韧性和导电性能。
同时,烧结过程中还会发生相变现象,从而改变材料的相组成和相比例。
相变可以使材料的性能得到进一步的优化,比如提高材料的热稳定性和化学稳定性。
四、高温烧结有利于提高材料的物理和化学性能高温烧结过程中,粉末颗粒在高温下发生熔融和扩散等过程,从而使材料的物理和化学性能发生改变。
熔融和扩散可以使材料中的杂质得到排除,提高材料的纯度和均匀性。
同时,熔融还可以改变材料的晶结构和晶格缺陷,从而影响其热导率和磁性等物理性能。
此外,高温烧结还有助于改善材料的化学反应性和催化性能,促进材料在化学工程和催化工艺中的应用。
综上所述,高温烧结是粉末冶金的关键步骤之一。
通过高温烧结,可以提高材料的致密性和机械性能,改善材料的组织和相结构,以及提高材料的物理和化学性能。
因此,在粉末冶金制备材料时,必须充分重视高温烧结的过程控制和优化,以提高材料的质量和性能,满足工程应用的需求。
烧结工艺介绍

烧结工艺介绍烧结工艺是一种常见的冶金工艺,用于将粉末状物质加热至接触点熔融,形成固态结合体的过程。
本文将介绍烧结工艺的原理、应用范围以及工艺流程。
一、原理烧结是通过热量作用使粉末颗粒表面融合,而形成较强的固态接触的过程。
烧结过程中,粉末颗粒相互接触,颗粒表面由于温度升高而软化或熔化,粒子间形成了弥散相和连续相,使颗粒间形成了较强的结合力。
通过控制加热温度、时间以及加压力度等工艺参数,使颗粒状物质在相互接触的同时,形成致密且高强度的结构体。
二、应用范围烧结工艺在冶金、陶瓷、粉末冶金、高分子材料等领域有着广泛的应用。
1. 冶金领域烧结工艺在冶金领域广泛应用于粉末冶金制品的制备,如金属粉末冶金零件、冶金陶瓷、高合金材料等。
2. 陶瓷领域烧结是陶瓷领域中常用的制备工艺之一,通过烧结工艺可以制备出具有高强度和良好耐磨性的陶瓷制品,如瓷砖、陶瓷碗碟等。
3. 粉末冶金领域粉末冶金是一种以粉末为原料,通过烧结工艺制备制品的工艺。
烧结工艺可以将金属粉末制备成各种零件,如齿轮、凸轮等。
4. 高分子材料领域烧结工艺在高分子材料领域中用于制备具有特殊性能的塑料制品,如高强度塑料零件、高耐磨塑料制品等。
三、工艺流程烧结工艺的基本流程包括原料制备、粉末颗粒的装填、加热烧结和冷却等步骤。
1. 原料制备:首先需要根据所需制品的要求,选择合适的原料并对其进行加工和处理。
这一步骤可以包括粉末的混合、筛分以及添加特定添加剂等。
2. 粉末颗粒的装填:将经过处理的粉末颗粒通过特定的装填方式填入烧结模具中。
装填要求均匀且适量,以确保烧结过程中的热量传导均匀。
3. 加热烧结:将装有粉末颗粒的模具放入烧结炉中,加热至一定温度并保持一定时间。
温度和时间的选择根据所需制品的要求来确定。
4. 冷却:烧结结束后,需要进行冷却处理。
冷却可以通过自然冷却或者采用特殊的冷却方法来进行。
四、工艺优势烧结工艺相对于其他加工方式具有以下优势:1. 提高材料的致密度和强度。
粉末冶金烧结的原理是什么

粉末冶金烧结的原理是什么
在粉末冶金烧结过程中,需要选择适当的还原气氛。
还原气氛可以通
过控制烧结过程中的气氛组成和气氛温度来实现。
正确选择还原气氛对于
提高烧结过程中的烧结密度和机械性能非常重要。
目前常用的还原气氛有氢气气氛、氮气-氢气混合气氛、氩气气氛等。
选择适当的还原气氛要考虑以下几个方面:
1.烧结物质的物理和化学性质:不同的物质对于还原气氛的需求是不
同的。
例如,一些物质在氢气气氛中容易发生返还反应,从而产生高纯度
的材料。
而一些物质在氢气气氛中容易脱氧,使材料中的氧含量降低。
2.烧结温度:烧结温度也会影响还原气氛的选择。
一般来说,高温下
需要使用高活性的还原气氛,以确保物质能够进行有效的还原反应。
同时,还原气氛的选择也要避免过高温度会导致烧结物质溶解和气体的浪费。
3.烧结压力:一些还原反应需要一定的压力才能进行,因此在烧结过
程中需要考虑烧结的压力。
一般来说,较高的烧结压力可以增加材料的烧
结密度,同时也可以促进还原反应的进行。
4.烧结时间:不同的还原气氛对烧结时间的要求也不同。
一些气氛需
要较长的烧结时间来实现完全的还原反应,而一些气氛则可以在较短的时
间内完成还原。
总的来说,选择适当的还原气氛是粉末冶金烧结过程中非常重要的一步。
需要综合考虑烧结物质的性质、烧结温度、烧结压力和烧结时间等因素,以确保烧结过程中所需的还原反应能够进行,并获得高质量的烧结材料。
粉末烧结技术
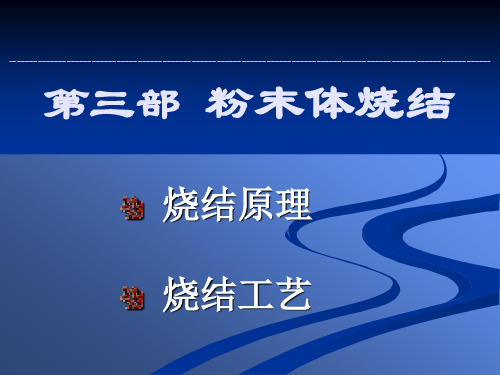
加压烧结—加压和加热同时并用,以达到消除孔
隙的目的,从而大幅度提高粉末制品的性能。常用
的加压烧结工艺有热压、热等静压及烧结-热等静压。
热压—将粉末装在压模内,在加压的同时把粉末加热到熔
点以下,使之加速烧结成比较均匀致密的制品。
热等静压—把粉末压坯或把装入特制容器内的粉末置于热
等静压机高压容器内,使其烧结成致密的材料或零件的过 程。
烧结-热等静压—把压坯放入烧结-热等静压设备的高压容
器内,先进行脱蜡、烧结,再充入高压气体进行热等静压。
反应烧结—先将原材料(如制备Si3N4时使用Si粉)
粉末以适当方式成形后,在一定气氛中(如氮气)
加热发生原位反应合成所需的材料并同时发生烧结。
微波烧结—材料内部整体地吸收微波能并被加热,
使得在微波场中试样内部的热梯度和热流方向与常规 烧结的试样相反。
电火花等离子烧结—也叫等离子活化烧结或电火
花等离子烧结,是利用粉末间火花放电多产生的等
离子活化颗粒,同时在外力作用下进行的一种特殊
烧结方法。
真空热压烧结炉图
微波生物陶瓷烧结炉图
微波烧结炉图
热等静压烧结炉图
放电等离子烧结炉图
物理 化学变化
烧结后期还可能出现二次再结还可能发生固相的溶解与析出。
烧结驱动力
烧结的驱动力----一般为体系的表面能和缺陷能。烧
结实际上是体系表面能和缺陷能降低的过程。通常体
系能量的降低靠的是高温热能激活下的物质传递过程。
烧结原动力----烧结颈部与粉末颗粒其它部位之间存 在化学位差。
扩散机制将发生孔隙的孤立、球化及收缩。
氧化铝陶瓷典 型的不同烧结 阶段显微结构
粉末冶金的烧结技术

粉末冶金的烧结技术粉末冶金是一种通过将金属或非金属粉末在一定条件下,加工成具有一定形状和尺寸的零部件的方法。
烧结技术是粉末冶金中的关键步骤之一,它将粉末颗粒通过加热并施加压力使其质点之间结合得更加牢固,形成一体化的零部件。
本文将对粉末冶金的烧结技术进行深入探讨。
一、烧结技术的基本原理和过程烧结技术是将粉末颗粒通过加热至其熔点以下,但高于材料的再结晶温度,同时施加压力,使粉末颗粒发生结合,形成一体化的零部件。
其基本原理是利用了粉末颗粒与粉末颗粒之间的扩散作用和表面张力降低效应。
烧结过程中,颗粒间的间隙先得到迅速消除,然后颗粒之间产生再结晶,通过扩散使粒间结合更为牢固。
整个烧结过程可以分为初期活化期、再结晶期和液相期三个阶段。
初期活化期是指在烧结过程开始的阶段,颗粒发生活化并形成结合,此时烧结坯体变得更为致密。
再结晶期是指烧结坯体中增强再结晶的发生。
液相期是指在达到受结合的颗粒之间的最小距离后,材料产生液相,并通过液相扩散加快了颗粒间的结合。
在这个过程中,烧结坯体结构的致密度和强度会显著提高。
二、烧结技术的主要参数在进行粉末冶金的烧结过程中,有许多参数需要注意和控制,如温度、压力、时间和气氛等。
这些参数会对烧结过程和烧结产品的质量产生重要影响。
1. 温度:温度是烧结过程的关键参数之一。
合适的温度能够使粉末颗粒迅速熔结,并形成均匀的结构。
过高或过低的温度都会影响烧结效果和质量。
2. 压力:在烧结过程中,施加的压力可以使粉末颗粒更加紧密地结合在一起。
增加压力可以提高烧结物品的致密度和强度。
3. 时间:烧结时间是烧结过程中的一个重要参数。
适当的烧结时间可以使粉末颗粒充分结合并形成致密的结构。
时间过长或过短都会影响产品的质量。
4. 气氛:烧结过程中的气氛对烧结质量和产品性能有很大影响。
不同的气氛可以对不同材料产生不同的效果。
常用的烧结气氛有氢气、氮气、氧气和真空等。
三、烧结技术的应用和优点烧结技术在现代工业中有着广泛的应用,尤其是在金属材料和陶瓷材料的制备过程中。
粉末冶金材料的烧结
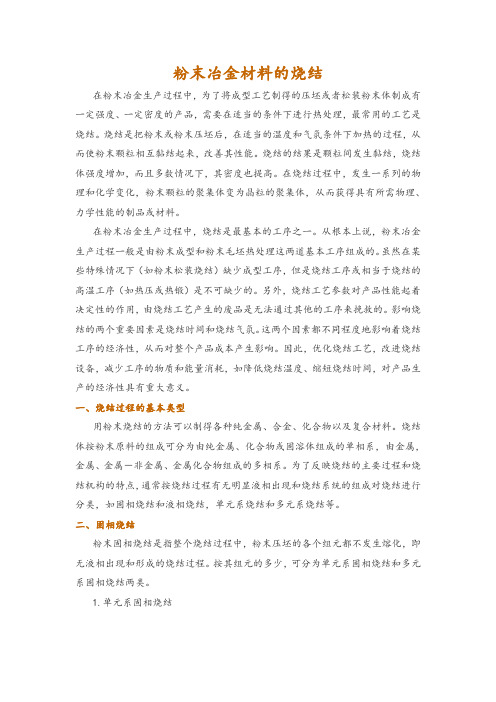
粉末冶金材料的烧结在粉末冶金生产过程中,为了将成型工艺制得的压坯或者松装粉末体制成有一定强度、一定密度的产品,需要在适当的条件下进行热处理,最常用的工艺是烧结。
烧结是把粉末或粉末压坯后,在适当的温度和气氛条件下加热的过程,从而使粉末颗粒相互黏结起来,改善其性能。
烧结的结果是颗粒间发生黏结,烧结体强度增加,而且多数情况下,其密度也提高。
在烧结过程中,发生一系列的物理和化学变化,粉末颗粒的聚集体变为晶粒的聚集体,从而获得具有所需物理、力学性能的制品或材料。
在粉末冶金生产过程中,烧结是最基本的工序之一。
从根本上说,粉末冶金生产过程一般是由粉末成型和粉末毛坯热处理这两道基本工序组成的。
虽然在某些特殊情况下(如粉末松装烧结)缺少成型工序,但是烧结工序或相当于烧结的高温工序(如热压或热锻)是不可缺少的。
另外,烧结工艺参数对产品性能起着决定性的作用,由烧结工艺产生的废品是无法通过其他的工序来挽救的。
影响烧结的两个重要因素是烧结时间和烧结气氛。
这两个因素都不同程度地影响着烧结工序的经济性,从而对整个产品成本产生影响。
因此,优化烧结工艺,改进烧结设备,减少工序的物质和能量消耗,如降低烧结温度、缩短烧结时间,对产品生产的经济性具有重大意义。
一、烧结过程的基本类型用粉末烧结的方法可以制得各种纯金属、合金、化合物以及复合材料。
烧结体按粉末原料的组成可分为由纯金属、化合物或固溶体组成的单相系,由金属,金属、金属-非金属、金属化合物组成的多相系。
为了反映烧结的主要过程和烧结机构的特点,通常按烧结过程有无明显液相出现和烧结系统的组成对烧结进行分类,如固相烧结和液相烧结,单元系烧结和多元系烧结等。
二、固相烧结粉末固相烧结是指整个烧结过程中,粉末压坯的各个组元都不发生熔化,即无液相出现和形成的烧结过程。
按其组元的多少,可分为单元系固相烧结和多元系固相烧结两类。
1.单元系固相烧结单元系固相烧结,即单一粉末成分的烧结。
例如各种纯金属的烧结、预合金化粉末的烧结、固定成分的化合物粉末的烧结等,均为单元系固相烧结。
阀座粉末冶金烧结

阀座粉末冶金烧结
阀座是指阀门与阀体之间的连接部分,通常由金属制成。
阀座粉末冶金烧结是一种利用粉末冶金技术制备阀座的方法。
具体步骤如下:
1. 原材料准备:根据阀座需要的材料特性,选择合适的金属粉末,如不锈钢粉末等。
2. 混合:将金属粉末与一定比例的添加剂混合均匀,添加剂通常包括润滑剂和浸润剂,目的是提高粉末的流动性和后续烧结过程中的浸润性。
3. 压制:将混合后的粉末填入模具中,并施加高压进行压制,以使粉末颗粒之间结合成固体形状。
4. 烧结:将压制得到的绿坯放入高温炉中进行烧结,烧结过程中,金属粉末颗粒发生结合和熔融,形成致密的结构。
5. 加工:经过烧结后的坯体还需要进行后续的加工工艺,如车削、铣削等,以获得最终的阀座形状和尺寸。
阀座粉末冶金烧结具有以下优点:
- 产品性能均匀:采用粉末冶金工艺可以获得致密的结构,产品性能均匀、稳定。
- 精度高:粉末冶金烧结可以实现复杂形状的加工,尺寸精度高。
- 材料利用率高:粉末材料可以充分利用,减少浪费。
- 生产效率高:粉末冶金烧结工艺高效,生产效率高,可以批量生产。
阀座粉末冶金烧结在阀门制造领域得到广泛应用,可以提供高质量、高性能的阀座产品。
粉末冶金的工艺流程-粉末的烧结

粉末的烧结定义烧结:压坯置于基体金属熔点以下温度(约0.7~0.8T,单位K)加热保温,粉末颗粒之间产生原子扩散、固溶、化合和熔接,致使压坯收缩并强化,这一过程称为烧结。
烧结对粉末冶金材料和制品的性能有着决定性的影响。
烧结的结果是粉末颗粒之间发生粘接,烧结体的强度增加,密度提高。
在烧结过程中,压坯要经过一系列的物理化学变化。
开始是水分或有机物的蒸发或挥发,吸附气体的排除,应力的消除,粉末颗粒表面氧化物的还原;继之是原子间发生扩散,粘性流动和塑性流动,颗粒间的接触面增大,发生再结晶和晶粒长大等。
出现液相时,还可能有固相的溶解和重结晶。
这些过程彼此之间并无明显的界限,而是穿插进行,互相重叠,互相影响。
加之一些其它烧结条件,使整个烧结过程变得很复杂。
用粉末烧结的方法可以制得各种纯金属、合金、化合物以及复合材料。
在烧结过程中,固体颗粒表面能的减小是烧结的“推动力”,也即热力学条件。
烧结是一个自发的不可逆过程。
粉末烧结用填料(packing material for powder sintering)粉末烧结时在烧舟内充填于产品间的,起均热、保护作用和防止成分挥发的粉状或粒状材料。
将粉末压坯埋入惰性粉末或者装入密封盒内进行烧结是一种极简单的烧结技术,从生产粉末冶金零件的早期起,它就得到了广泛的应用。
采用装有填料的密封盒,则在烧结时可以不必使用还原气氛。
含于填料内的空气中的氧,在烧结开始阶段会与压坯表面起反应,如果填料中含有还原剂,则不足以引起严重的氧化。
适合于用作填料材料的有Al2O3粉、ZrO2粉以及石墨粉、炭黑、木炭粉、铸铁屑等以及它们的混合物。
对铁粉压坯的烧结,为了防止脱碳,填料中含有少量的碳是必不可少的。
在有色金属粉末冶金中,黄铜压坯的烧结总与一定程度的锌的挥发联系在一起,如果黄铜压坯放入密封盒内进行烧结,则盒内气氛很快充满锌的蒸气而可防止合金的进一步脱锌。
在氢气中烧结硬质合金时,为减少和防止硬质合金压坯脱碳而使合金性能下降,通常使用Al2O3粉并在其中加入少量炭黑作填料等等。
粉末冶金的烧结技术

粉末冶金的烧结技术粉末冶金是一种重要的金属材料加工技术,其烧结技术是其中的关键环节之一。
烧结是指将金属粉末在高温和压力下进行加工,使其粒子间发生结合,形成致密坚固的材料。
烧结技术主要包括前期制备、烧结过程和后期处理三个阶段。
前期制备主要是选用合适的原料并进行预处理;烧结过程是指将粉末加热至一定温度下,使其颗粒形成熔连和扩散,从而实现颗粒间的结合;后期处理则是通过热处理和机械加工等方式对烧结材料进行改性和加工。
在烧结过程中,主要涉及到的问题包括热传导、粒子熔融和扩散等。
热传导是指热能在颗粒间的传递,它直接影响到烧结过程中的温度分布和物理性质的演化。
热传导主要受到粉末细度、烧结温度和热处理时间等因素的影响。
粒子熔融是指粉末颗粒在高温下发生熔化并与周围颗粒结合。
熔融过程中,粒子表面的氧化物会被还原,同时金属原子也会扩散到颗粒间,从而实现结合。
扩散是指金属原子在颗粒间的迁移和交换,它是烧结过程中颗粒结合的重要机制。
在烧结技术中,常用的烧结方法包括热压烧结、等静压烧结和电子束烧结等。
热压烧结是指将粉末加热至高温后进行压实,它可以在较短时间内获得高致密度的烧结材料。
等静压烧结是指在恒定温度下进行压实,它可以获得均匀的压力分布和高度致密的材料。
电子束烧结则是利用电子束的热效应进行烧结,它具有快速和局部加热的优势。
烧结技术在粉末冶金中具有广泛的应用。
一方面,它可以制备各种金属材料和合金,包括高温合金、硬质合金、不锈钢、铜陶瓷等。
另一方面,它还可以制备复杂形状和微细结构的材料,如蜂窝结构、多孔材料和纳米颗粒等。
此外,烧结技术还可以用于制备金属陶瓷复合材料、金属纤维和金刚石等高性能材料。
总之,粉末冶金的烧结技术是一项重要的金属材料加工技术,它通过热传导、粒子熔融和扩散等机制实现了金属粉末的结合,从而获得高致密度和高强度的材料。
烧结技术在金属材料研究和工业生产中具有广泛的应用前景,将为人们提供更多种类和性能的金属材料。
粉末冶金原理烧结

(3)粉末颗粒内晶格畸变得消除。
对烧结过程,特别就是早期阶段,作用较大得主要就是表 面能。
烧结后颗粒得界面转变为晶界面,由于晶界能更低,故总 得能量仍就是降低得。随着烧结得进行,烧结颈处得晶 界可以向两边得颗粒内移动,而且颗粒内原来得晶界也 可能通过再结晶或聚晶长大发生移动并减少。因此晶界 能进一步降低就成为烧结颈形成与长大后烧结继续进行 得主要动力
散 ● 细粉末得表面扩散作用大 ● 烧结早期孔隙连通,表面扩散得结果导致小孔隙得缩小与
消失,大孔隙长大 ● 烧结后期表面扩散导致孔隙球化 ● 金属粉末表面氧化物得还原,提高表面扩散活性
表面扩散与体积扩散得扩散激活能差别不大,
但 D v o>D so,故D v>Ds 烧结动力学方程: Kuczynski: x7/a3=(56Dsγδ4/k T)▪t Rocland: x7/a3=(34Dsγδ4/k T )▪t
1)稳定液相烧结系统如:
2)瞬时液相烧结系统如:
合金等。
对烧结过程得分类,目前并不统一。盖彻尔(就是把金属 粉得烧结分为1)单相粉末(纯金属、固溶体或金属化合 物)烧结;2) 金属或金属非金属)固相烧结; 3)多相粉末液 相烧结;4) 熔浸。她把固溶体与金属化合物这类合金粉 末得烧结瞧为单相烧结,认为在烧结时组分之间无再溶 解,故不同于组元间有溶解反应得一般多元系固相烧结。
√Cabrera:x6/a2 = k/▪t
δ为表面层厚度,采用强烈机械活化可提高有效表面活性 得厚度,从而加快烧结速度。
烧结铜粉得自扩散系 数与温度得关系
(五)晶界扩散(GB diffusion)
晶界扩散:原子或空位沿晶界进行迁移 晶界就是空位得“阱”(Sink),对烧结得贡献体现在: ● 晶界与孔隙连接,易使孔隙消失 ● 晶界扩散激活能仅为体积扩散得一半,D gb》Dv ● 细粉烧结时,在低温起主导作用,并引起体积收缩
2024年粉末冶金的烧结技术(三篇)

2024年粉末冶金的烧结技术⑴按原料组成不同分类。
可以将烧结分为单元系烧结、多元系固相烧结及多元系液相烧结。
单元系烧结是纯金属(如难熔金属和纯铁软磁材料)或化合物(Al2O3、B4C、BeO、MoSi2等)熔点以下的温度进行固相烧结。
多元系固相烧结是由两种或两种以上的组元构成的烧结体系,在其中低熔成分的熔点温度以下进行的固相烧结。
粉末烧结合金多属于这一类。
如Cu-Ni、Fe-Ni、Cu-Au、W-Mo、Ag-Au、Fe-Cu、W-Ni、Fe-C、Cu-C、Cu-W、Ag-W等。
多元系液相烧结以超过系统中低熔成分熔点的温度进行的烧结。
如W-Cu-Ni、W-Cu、WC-Co、TiC-Ni、Fe-Cu(Cu10%、Fe-Ni-Al、Cu-Pb、Cu-Sn、Fe-Cu(Cu10%)等⑵按进料方式不同分类。
分为为连续烧结和间歇烧结。
连续烧结烧结炉具有脱蜡、预烧、烧结、制冷各功能区段,烧结时烧结材料连续地或平稳、分段地完成各阶段的烧结。
连续烧结生产效率高,适用于大批量生产。
常用的进料方式有推杆式、辊道式和网带传送式等。
间歇烧结零件置于炉内静止不动,通过控温设备,对烧结炉进行需要的预热、加热及冷却循环操作,完成烧结材料的烧结过程。
间歇烧结可依据炉内烧结材料的性能确定合适的烧结制度,但生产效率低,适用于单件、小批量生产,常用的烧结炉有钟罩式炉、箱式炉等。
除上述分类方法外。
按烧结温度下是否有液相分为固相烧结和液相烧结;按烧结温度分为中温烧结和高温烧结(1100~1700℃),按烧结气氛的不同分为空气烧结,氢气保护烧结(如钼丝炉、不锈钢管和氢气炉等)和真空烧结。
另外还有超高压烧结、活化热压烧结等新的烧结技术。
2.影响粉末制品烧结质量的因素影响烧结体性能的因素很多,主要是粉末体的性状、成形条件和烧结的条件。
烧结条件的因素包括加热速度、烧结温度和时间、冷却速度、烧结气氛及烧结加压状况等。
⑴烧结温度和时间烧结温度的高低和时间的长短影响到烧结体的孔隙率、致密度、强度和硬度等。
粉末冶金烧结时间

粉末冶金烧结时间
粉末冶金是一种通过粉末压制、烧结、加工等方法制造复杂形状、高精度、高性能金属件的技术。
在粉末冶金中,烧结是一个至关重要
的生产工序。
烧结是将金属粉末在高温高压环境下加热,使其部分熔
化或固态扩散,并在晶界处形成结合,从而实现金属粉末颗粒的互相
连接,最终形成高密度的金属坯体。
在进行粉末冶金烧结工艺的时候,烧结时间是一个非常重要的参数,它直接关系到烧结效果的好坏。
当烧结时间较短时,粉末烧结不
充分,金属结晶粗大,致使制品的力学性能变差,外观品质也难以达
到要求。
如果烧结时间过长,则会使粉末过度烧结,导致材料性能退化、变形、氧化等问题,从而影响制品质量甚至使制品弃用。
烧结时间的长短取决于许多因素,例如加热速率、热处理温度、
材料成分等。
一般来说,粉末冶金烧结时间在30分钟到120分钟之间
比较合适。
在实际生产中,应根据所使用的金属粉末以及工艺要求等
因素来确定烧结时间,以保证所制作的金属件能够满足客户的各种需求。
总之,烧结时间是粉末冶金工艺中重要的参数之一,它对制品的
性能、外观等方面都有着直接的影响。
为了制作出高质量的金属制品,我们需要根据材料的性质和工艺要求来科学合理地确定烧结时间,以
求达到最佳的加工效果。
粉末冶金原理-烧结
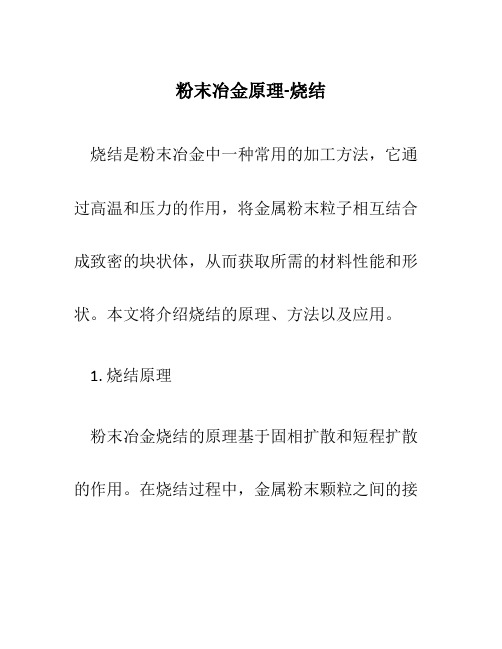
粉末冶金原理-烧结烧结是粉末冶金中一种常用的加工方法,它通过高温和压力的作用,将金属粉末粒子相互结合成致密的块状体,从而获取所需的材料性能和形状。
本文将介绍烧结的原理、方法以及应用。
1. 烧结原理粉末冶金烧结的原理基于固相扩散和短程扩散的作用。
在烧结过程中,金属粉末颗粒之间的接触面发生原子间的扩散,使得粒子之间形成更强的结合力,从而实现粉末的聚结。
烧结过程中,首先是金属粉末颗粒之间的接触,原子开始扩散。
随着温度的升高,扩散速率也随之增加。
当粉末颗粒之间的接触点扩散到一定程度后,开始形成颗粒之间的原子键合。
键合的形成使得颗粒间的结合力增强,同时形成新的晶体结构或弥散态结构。
2. 烧结方法2.1 传统烧结传统烧结是指采用外加热源和压力来实现烧结过程。
该方法通常包括以下几个步骤:1.装料:将金属粉末和所需添加剂按照一定比例混合,并形成一定的装料形状,如坯料或颗粒。
2.预压:将装料放入模具中,并施加一定的压力,使装料初步固结成形。
3.高温烧结:将装料放入烧结炉中,在一定的温度下暴露一段时间,使装料中的金属粉末颗粒扩散、晶粒长大并结合。
4.冷却:烧结完成后,将烧结块从炉中取出,经过冷却以稳定材料结构。
5.表面处理:根据需求,对烧结块进行加工、修整和处理,以得到最终所需的形状和表面特性。
2.2 反应烧结反应烧结是指在烧结过程中引入化学反应,利用固相反应进行金属粉末的结合。
相较于传统烧结,反应烧结可以实现更高的烧结温度,加快晶粒生长和结合的速度。
反应烧结的具体步骤包括:1.装料:将金属粉末和反应剂按照一定比例混合,并形成装料。
2.高温烧结:将装料放入烧结炉中,在一定的温度下暴露一段时间。
在高温下,反应剂与金属粉末发生固相反应,生成新的物质并结合金属粉末颗粒。
3.冷却:烧结完成后,将烧结块从炉中取出,经过冷却以稳定材料结构。
4.表面处理:根据需求,对烧结块进行加工、修整和处理,以得到最终所需的形状和表面特性。
3. 烧结应用烧结方法在粉末冶金中具有广泛的应用。
粉末冶金的烧结技术规程

粉末冶金的烧结技术规程一、前言粉末冶金是一种现代工艺技术,其主要应用于各种含金属、非金属和合金的粉末烧结制备。
粉末冶金技术具有独特的优势,例如可以生产出细粒度、高密度、高强度、耐磨、耐腐蚀的零件等。
在本文中,将介绍粉末冶金的烧结技术规程。
二、烧结原理烧结是将粉末冶金材料在高温下加热压实,使其形成致密的固体块材料的过程。
烧结时,原粉末经过初步加工处理,如混合、压制等工艺。
而后再放入保护气氛的烧结炉中加热,使粉末颗粒在融合时形成块状材料。
烧结的原理是粉末团聚过程的加快,通过在高温下加压使粉末颗粒间形成连接,形成致密的物理结构,从而提高材料的密度和强度。
三、不同材料的烧结温度烧结温度取决于使用材料的种类、成分和形状。
以下列出一些典型的烧结温度范围:1. 硬质合金烧结烧结温度为1300-1520°C,可以使硬质合金材料的密度达到99%以上,从而提高硬度和耐磨性能。
2. 钨合金烧结烧结温度为1400-1600°C,可以使钨合金材料的密度达到90%以上,从而提高硬度和抗腐蚀性能。
3. 不锈钢烧结烧结温度为1250-1350°C,可以使不锈钢材料的密度达到95%以上,从而提高耐腐蚀性能。
4. 铜烧结烧结温度为700-900°C,可以使铜材料的密度达到90%以上,从而提高材料的导电性能和强度。
五、烧结工艺流程1. 原料制备粉末冶金材料的粉末需要在专业的设备中进行初步处理,如混合、筛分等,以满足烧结的要求。
2. 压制将初步处理过的粉末加入模具中,进行压制。
压缩时需要控制压实的压力和时间,以确保形成高密度的材料坯。
3. 烘干将压制后的材料坯进行烘干,以去除多余的水分和其他杂质。
4. 烧结将烘干的材料坯放入烧结炉中,在高温下进行保护气氛烧结。
烧结温度需要根据材料的种类、形状和成分来确定,以确保形成高密度、高强度的材料。
5. 冷却待烧结完成后,将材料坯从烧结炉取出放凉,并在不同温度下进行降温,以防止材料的变形或裂纹。
粉末冶金原理烧结
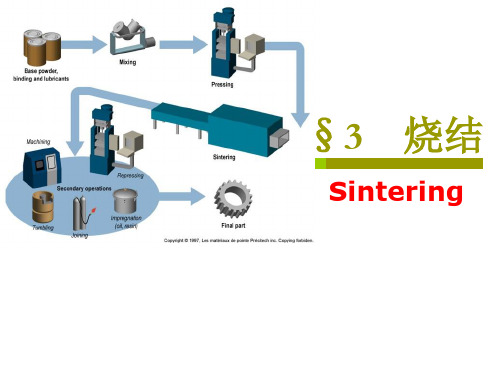
很小 sin
AB x sin
Fx F x
垂直作用于ABCD上旳合力
F
2(Fx sin
F
sin
)
2 (
x)
2
2
ABCD旳面积为 xθ×ρθ,作用在上面旳应力为
F
x 2
2 ( x) x 2
(1 1) x
因为烧结颈半径x远不小于曲率半径 x>>
烧结动力是表面张力造成旳一种机械力,它垂直作用于烧结颈曲面上, 使烧结颈向外长大。
多元系烧结根据烧结温度下有无液相出现又提成:
1)多元系固相烧结:烧结温度在其中低熔成份旳熔点温 度下列。根据系统旳组元之间在烧结温度下有无固相溶解 存在又分为:
a)无限固溶系:在相图上有无限固溶区旳系统,如Cu-Ni Fe-Ni、W-Mo等。
b)有限固溶系:在相图上有有限固溶区旳系统,如Fe-C Fe-Cu、W-Ni等。
假如颗粒半径2m x=0.2μ ρ=10-8~10-9m 则σ=107 N/m2
在形成孔隙中气体阻止孔隙收缩和烧结颈长大,有效力: Ps Pv
开孔: Pv=1atm =105 N/m2
闭孔:
Ps
Pv
2
r
r-孔隙半径 孔隙收缩使Pv增大,到达一种平衡值 ∴仅延长烧结时间不能消除孔隙
物质扩散旳角度
孔隙球化
等温烧结三个阶段旳相对长短主要由烧结温度决定:温度 低,可能仅出现第一阶段;在生产条件下,至少确保第二 阶段接近完毕;温度越高,出现第二甚至第三阶段就越早。
在连续烧结时,第一阶段可能在升温过程中就完毕。
1.粉末发生烧结旳主要标志是坯体旳强度增长,导电性能 提升,表面积减小,而不是意味着烧结体产生收缩。
粉末冶金的烧结技术
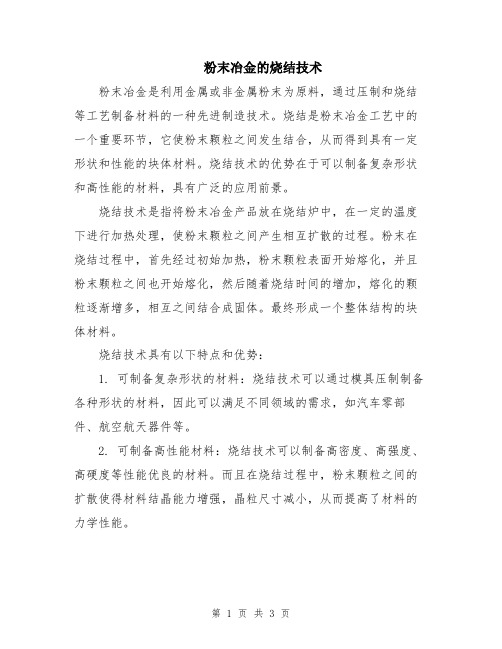
粉末冶金的烧结技术粉末冶金是利用金属或非金属粉末为原料,通过压制和烧结等工艺制备材料的一种先进制造技术。
烧结是粉末冶金工艺中的一个重要环节,它使粉末颗粒之间发生结合,从而得到具有一定形状和性能的块体材料。
烧结技术的优势在于可以制备复杂形状和高性能的材料,具有广泛的应用前景。
烧结技术是指将粉末冶金产品放在烧结炉中,在一定的温度下进行加热处理,使粉末颗粒之间产生相互扩散的过程。
粉末在烧结过程中,首先经过初始加热,粉末颗粒表面开始熔化,并且粉末颗粒之间也开始熔化,然后随着烧结时间的增加,熔化的颗粒逐渐增多,相互之间结合成固体。
最终形成一个整体结构的块体材料。
烧结技术具有以下特点和优势:1. 可制备复杂形状的材料:烧结技术可以通过模具压制制备各种形状的材料,因此可以满足不同领域的需求,如汽车零部件、航空航天器件等。
2. 可制备高性能材料:烧结技术可以制备高密度、高强度、高硬度等性能优良的材料。
而且在烧结过程中,粉末颗粒之间的扩散使得材料结晶能力增强,晶粒尺寸减小,从而提高了材料的力学性能。
3. 可制备复合材料:烧结技术可以制备具有多种材料组成的复合材料。
通过将不同种类的粉末混合压制和烧结,可以得到具有多种性能的复合材料,如耐磨、耐腐蚀、导热等。
4. 生产效率高:烧结技术可以批量生产材料,具有高效、节能的特点。
而且在烧结过程中,由于粉末颗粒之间的扩散使得材料的致密度提高,从而减少了后续的加工工序。
5. 环境友好:烧结技术是一种无需溶剂和液相的制备工艺,不会产生废水、废气、废渣等环境污染问题,相对于传统冶金工艺更加环保。
然而,烧结技术也存在一些挑战和限制:1. 粉末的选择和处理:不同材料的烧结温度和烧结方式各不相同,粉末的选择和处理对于烧结成型的工艺参数和性能有着重要影响。
2. 烧结过程中的缺陷:烧结过程中可能会出现气孔、裂纹等缺陷,这些缺陷对材料性能有着重要影响。
因此,烧结工艺控制和参数优化是关键。
3. 设备成本高:烧结设备的成本较高,特别是对于大型和高精度的烧结设备,成本更高。
- 1、下载文档前请自行甄别文档内容的完整性,平台不提供额外的编辑、内容补充、找答案等附加服务。
- 2、"仅部分预览"的文档,不可在线预览部分如存在完整性等问题,可反馈申请退款(可完整预览的文档不适用该条件!)。
- 3、如文档侵犯您的权益,请联系客服反馈,我们会尽快为您处理(人工客服工作时间:9:00-18:30)。
用SPS制取块状纳米晶Fe90Zr7B3软磁的过程是: 先将由非 晶薄带经球磨制成的50~150μm非晶粉末装入WC/Co合金 模具内,并在SPS烧结机上烧结(真空度1×10-2Pa以下、升温 速度0.09~1.7K/s、温度673~873K、压力590MPa), 再把所 得的烧结体在1×10-2Pa真空下、以3 7K/s速度加热到923K、 保温后而制成。材料显示较好的磁性能:最大磁导率29800、 100Hz下的动态磁导率3430, 矫顽力12A/m。
3
双频微波烧结炉 生产用大型微波烧结炉 已烧结成多种材料:如陶瓷和铁氧体等材料。另 外,在日本又开发出相似的毫米波烧结技术,并成功 地在2023K下保温1h烧结成全致密的AlN材料。
4
2.爆炸压制技术 爆炸压制又称冲击波压制是一种有前途的工艺
方法,它在粉末冶金中发挥了很重要的作用, 爆炸压 制时,只是在颗粒的表面产生瞬时的高温,作用时间 短,升温和降温速度极快。适当控制爆炸参数,使得 压制的材料密度可以达到理论密度的90%以上,甚至 达到99%。
3)快速脉冲电流的加入, 无论是粉末内的放电部位还是焦耳 发热部位, 都会快速移动, 使粉末的烧结能够均匀化。
11
与传统的粉末冶金工艺相比,SPS工艺的特点是:
• 粉末原料广泛:各种金属、非金届、合金粉末,特别是 活性大的各种粒度粉末都可以用作SPS 烧结原科。
• 成形压力低:SPS烛结时经充分微放电处理,烧结粉末表 面处于向度活性化状态.为此,其成形压力只需要冷压烧 结的l/10~1/20。
17
SPS制备软磁材料 通常用急冷或喷射方法可得到FeMe(Nb、Zr、Hf)B的非 晶合金,在稍高于晶化温度处理后, 可得到晶粒数10nm,具有 体心立方结构,高Bs 、磁损小的纳米晶材料。但非晶合金目 前只能是带材或粉末, 制作成品还需要将带材重叠和用树脂固 结, 这使得成品的密度和Bs均变低。近年, 日本采用SPS工艺研 究FeMeB块材的成形条件及磁性能。
13
SPS可加工材料
14
SPS技术制备梯度功能材料 通过SPS技术可以制造陶瓷/金属、聚合物/金属以及其 他耐热梯度、耐磨梯度、硬度梯度、导电梯度、孔隙度梯 度等材料。梯度层可到10多层。
15
美国国立标准技术研究所和机械工程实验室与日本国际 贸易工业部门合作, 共同开发了高效发动机用的大尺寸耐热、 高强梯度材料。现已能批量生产 150mm, 厚15mm, 11层的 ZrO2 梯度材料。采用的SPS工艺参数是: 压力20~40MPa, 温 度1243~1293K, 升温速率50K/Min, 真空度10Pa。
19
SPS制备块状纳米晶FeMeB系永磁材料 日本开展了用SPS 制备Fe66Co20Nd2Pr7B5异向性永磁的研 究。将急冷制作的非晶薄带球磨成37~105μm的粉末, 装入 WC/Co合金模具内, 在SPS烧结机上烧结(压力374~636MPa, 温度673~873K), 然后将烧结体在真空1×10-2Pa下、于973K 进行180s处理。结果表明: 烧结温度873K、压力636MPa时, 烧结体的相对密度达97 6%~98 4%。经磁性测定表明, 烧结 加压方向的最大磁能积比平行方向的要大,并且随着SPS烧结 温度和压力的升高, 异向性增加。
从测量结果可以看出, 爆炸压制钕铁硼磁体的磁 性能保持了原始磁粉的性能, 最大磁能积没有太大的 变化。这是常规粘结NdFeB磁体无法达到的。
7
3.放电等离子烧结(SPS) 放电等离子烧结是将金属等粉末装入由石墨等材
质制成的模具内,利用上、下模冲和通电电极将特定 烧结电源和压制压力施加在烧结粉末。经放电活化、 热塑变形和冷却阶段完成制取高性能材料或制件的一 种方法。它是粉末冶金的一种新的烧结技术,是将电 能和机械能同时赋于烧结粉末的一种新工艺。
5
爆炸压制装置示意图
6
国内用NdFeB磁粉进行了爆炸压制技术的研究。 用磁粉的性能为:磁感矫顽力Hcb=453.08kA/m, Br=0.783T, (BH)max =89.9kJ/m3。爆炸压制后得到的 NdFeB磁体性能为:Hcb=403kA/m,Br=0.805T, (BH)max=90.7kJ/m3。
• 烧结时间短:烧结小型制件时一般只需要数秒至数分钟, 其加热速度可以高达106℃/s,自动化生产小型制件时的生 产率可达400件/h。
12
• 采用石墨模具,成本低,加工方便。 • 大气下烧结:电火花烧结时一般是在大ห้องสมุดไป่ตู้下进行,甚至高 活性铍制件也可以在大气下烧结。 • 脉动电源,通常采用的足直流与交流叠加的脉动电源。 • 节约能源,热效率高,耗电量只相当于电阻烧结的1/10。
采用SPS烧结得到了两头分别是100%的玻璃与100%的 304不锈钢, 而中间呈4层的梯度材料。烧结温度1073K,保持 时间15Min, 真空下进行。
16
SPS技术制备电磁材料 通过SPS技术可以制造SiGe/PbTe/BiTe/FeSi/CoSb3系热 电转换元件,以及广泛用于电子领域的各种功能材料, 如超 导材料、磁性材料、靶材、介电材料、贮氢材料、形状记 忆材料、固体电池材料、光学材料等。
8
SPS烧结原理示意图
9
SPS原理是利用强脉冲电流加在粉末颗粒上产生的诸多 有利于快速烧结的效应: 1)由于脉冲放电产生的放电冲击波以及电子、离子在电场
中反方向的高速流动, 可使粉末吸附的气体逸散, 粉末表 面的起始氧化膜在一定程度上可被击穿, 使粉末得以净 化、活化;
10
2)由于脉冲是瞬间、断续、高频率发生, 在粉末颗粒未接触 部位产生的放电热, 以及粉末颗粒接触部位产生的焦耳热, 都大大促进了粉末颗粒原子的扩散, 其扩散系数比通常热 压条件下的要大得多,而达到粉末烧结的快速化;
粉末冶金新技术
烧结新技术
1
三、烧结新技术 在普通烧结技术的基础上,通过改进加 热源、施加外力等作用在较短的时间里 使粉体致密化的过程,主要有微波烧结 技术和电火花烧结技术等。
2
1.微波烧结技术 微波烧结是通过被烧结粉体吸收微波,将电磁
波能量直接转化成物质中粒子的能量,使其内部产 生热而烧结的方法。它热效率高,可急速升温缩短 烧结时间,加上微波与粒子间的交互作用,降低了 粒子间的活化能,加速材料的致密化。它比传统电 炉以热传导、热对流和热辐射的外部加热方式有更 高的效率。避免了外部加热由于内外温度梯度而造 成烧结体裂痕或大幅度变形等缺陷。