厚板埋弧焊焊接工艺(适合厚板和超厚板、非常珍贵)
(整理)厚板焊接工艺

资料简介(钢结构厚板焊接作业指导书)一、目的/使用范围在钢结构加工过程中,会涉及到板厚大于40mm板材的焊接,由于大于40mm的板材焊接难度较大,焊接成型后检验也较难,特制定厚板焊接作业指导书,以保证焊接质量和控制其焊接所带来的变形。
本作业指导书适应于钢结构焊连接中板厚大于40mm板材焊接。
二、作业前的准备1、人员的准备明确现场管理人员与操作者对焊接施工各工序的责任人,明确工作内容及责任范围,焊接作业前要对焊接人员进行培训,必须持证上岗,并对焊接作业人员进行必要的安全保护措施,各相关部门对作业前对质量、安全、环保方面进行技术交底。
2、材料的准备所有钢材进厂前必须附有出厂质量说明书和检验报告单,分批抽取试件进行相关试验,以确定是否合格,严禁不经检验就进厂进行加工作业,对焊接过程中所使用的各种焊条、焊剂要严格按照要求之规定进行使用。
(详见具体施工方案)3、机具的准备进行焊接作业前各种焊机工作性能进行检查,防止存在安全隐患,尽量采用低噪声、低污染的焊接器具,且专门的焊机要由专人负责管理及使用。
三、操作工艺1、概述以往我们接触到的钢结构焊接件板厚一般≤40mm,但是有些工程中也有时会出现板厚大于40mm的情况,根据具体的工程情况特制定合理的焊接参数既满足焊接质量又应最大限度控制焊接变形。
2、焊接要求①、所有厚板对接要求全熔透,即国内Ⅰ级焊缝质量。
②、应极大限度地控制焊接变形,厚钢板一旦变形,矫形将非常困难。
3、焊接方法厚板焊接采用埋弧自动焊焊机进行,辅助采用手工电弧焊机、电弧气刨和角向磨光机等工具。
4、焊接特点①、≥40mm板要求开双面X型破口,随钢板厚度的增加,坡口增大(如厚80mm、70mm钢板坡口开到了70º)②、厚板焊接前必须预热100~120℃③、厚板需采用多层多道焊接,应严格控制层间温度,防止钢板收缩过大,导致变形量增大④、焊接前坡口用角磨机打磨干净⑤、为防止第一遍焊接击穿,采用Φ3.2焊条手工打底。
50mm厚板焊接工艺

关于银子湖箱型柱50mm厚板主焊缝焊接工艺一、焊接材料的选择:考虑到本工程的箱型柱主材的材质为Q345C、Q390,选择焊材时请注意:1、CO2焊丝选择¢1.2的ER50-6.2、埋弧焊选择的焊丝与焊剂: SJ101——H10Mn2(H08MnA), SJ101使用前应经300℃烘焙2小时.二、对接焊缝的坡口形式1. 钢板对接坡口形式:2. 箱型端面对接坡口形式:全熔透焊缝部分熔透焊缝三、焊接工艺:1.切割坡口.1.1.中厚板坡口在切割前先划好三条线,即轨道线、角度线、坡口宽度线,如图所示.1.2.一律采用半自动切割机进行打坡口, 打坡口前,应检查半自动切割机行走轨道的直线度≤2mm, 对轨道直线度超标的应重新校直或重新制做.1.3.对切割后的坡口进行打磨, 打磨范围为坡口及周边30mm区域.如图所示.2.钢板组对.2.1.组对前应打通线检测钢板的直线度, 对整板直线度每米超过1mm且总长超过10mm的应进行校直.2.2.对箱型全熔透焊缝,在组对前要对腹板坡口的背面加焊衬垫, 在加衬垫时一要保证间隙均匀,二要满足腹板整体宽度尺寸符合图纸要求.2.3. 钢板在组对时,应控制对口错边量≤2mm.2.4.为防止厚板焊后产生角变形.50mm的对接钢板在施焊面的背面垫上一块8-12mm厚的垫板或小槽钢 ,借用反变形措施来减小焊后的角变形量.2.5.为确保原材料在厚度方向上的质量,50mm厚钢板在焊接前要对坡口两边100mm范围内进行UT探伤,确认无夹渣、夹层等缺陷时再进行焊接.用ER50-6型的CO2气保焊先进行定位焊.定位焊时.调节定位焊电流比正式焊接时大20%~25%,焊接速度不宜太快.定位焊缝长度50-70mm,焊脚尺寸: Hf=4-5mm,焊道间距为300mm.定位焊缝作为正式焊缝的一部分不得有未焊透、裂纹等缺陷.定位焊缝上若出现气孔或裂纹时,必须及时清除后重焊.2.6.必须加焊与坡口形状一致的引弧板、引出板.引弧板和引出板宽度不小于坡口的坡度面宽度,长度如图所示,厚度10mm,以照顾埋弧焊盖面的引收弧.焊接完毕后,必须用气割切除被焊工件上的引弧、引出板,并修磨平整,严禁用锤将其击落.钢板对接箱型对接3.焊接3.1.焊前预热.为便于预热温度的撑控,实际操作中将预热温度统一规定在100℃. 预热的加热区域应在焊接坡口的两侧各100mm范围区,如图所示. 预热时将烤枪喷嘴与构件应保持80mm距离,用中性焰加热,让火焰沿预热带慢慢往复均匀移动,使热量尽量渗透至钢板的全厚度.预热停止后,用测温仪对正面加热区进行选点检测.3.2. 钢板对接焊接.3.2.1. 正式焊接开始前或正式焊接中,发现定位焊有弧坑裂纹的,应彻底清除定位焊后,再进行正式焊接.焊丝对接头焊缝进行打底和填充, 填充时应将上3.2.2.用¢1.2的ER50-6型CO2层焊接残留在焊缝上的氧化皮(可借用钢丝刷清除)及焊道两侧的飞溅物(用角砂轮机去除)彻底清理干净,并用测温计控制好层间温度200-220℃.因层间焊接中断导致层间温度底于焊前预热温度的,续焊前应重新采取预热处理.应控制最后一层的填充高度距离坡口面2-3mm,以利埋弧焊一次性盖面. 埋弧焊采用¢4.0的H10Mn2配SJ101进行施焊。
奥氏体不锈钢厚板埋弧自动焊工艺

图 1 人 塔 预 热器 简图 1一上管板 2一换热管 3一下管板 4一球形封头 5一小筒体 6一裙座
的设计要求 ,结合生产实际 ,制定合理 、先进 的焊接工艺 ,对于确保产品焊接质量、提高工 效、缩短工期、降低制造成本等都有十分重要
的意义 。
奥 氏体 不锈 钢厚 板埋 弧 自动 焊 工 艺
奥氏体不锈钢厚板埋弧 自动焊工艺
苗 磊 ’ 郭晓春 李 波
(黑龙江省大庆市建材公 司金属结构 厂)
摘 要 对大庆甲醇厂改造工程 中入塔器预热器壳体所采用的奥氏体不锈钢厚板的 焊接性进行 了分析,确定了焊接工艺。实践证明,该焊接工艺是可行的。
关键词 厚板 奥氏体不锈钢 理弧 自动焊 焊接工艺评定
,张敬忠 ,男 ,1970年生 ,助理工程师 。滕州市 ,2775270
矛卜 资卜 i于一汗 弓于 弓小 弓升 弓卜一汁 弓"f 矛卜 i于刊于 一条冬 子卜 矛卜 i十弓于一汗 才卜 矛卜 佬于 兮卜弓于一朴 州 于 i千 才卜弓 卜弓于一孟小一卜卜 子卜 子卜弓于-汁一级子 tf--i于 i于 号卜一汁 -iF 朴州 幸
万方数据
6D32压缩机连杆螺检断裂的原 因及预 防措施
6D32压缩机连杆螺栓断裂的原 因及预防措施
张敬忠‘ 刘 林 杜衍锋
(充矿鲁南化肥厂 )
摘 要 就 6D32压缩机连杆螺检 断裂的原 因进行 了分析 ,并提 出了具体 的预 防和
改进 措 施
关键 词 压缩机 连杆螺检 断裂
充矿 鲁 南 化肥厂第一氮肥厂是设计生产能 力为 6万 t/a合成氨,11万 t/a尿素的中型化 工企业,1971年试车投产 ,1978年达到并超过 原设计能力。近些年来 ,通过不断改造、深人挖 潜,合成氨已达到并超过 9万 t/a的水平。该厂 合成氨系统配备 6D32氮氢气压缩机三台,H22 1氮氢气压缩机一台。投产初期压缩机运行方 式为两台 6D32或两台 6D32加一台H22l[ ,现 在以三台 6D32氮氢气压缩机运行为主。
厚板埋弧焊焊接工艺(适合厚板和超厚板、非常珍贵)
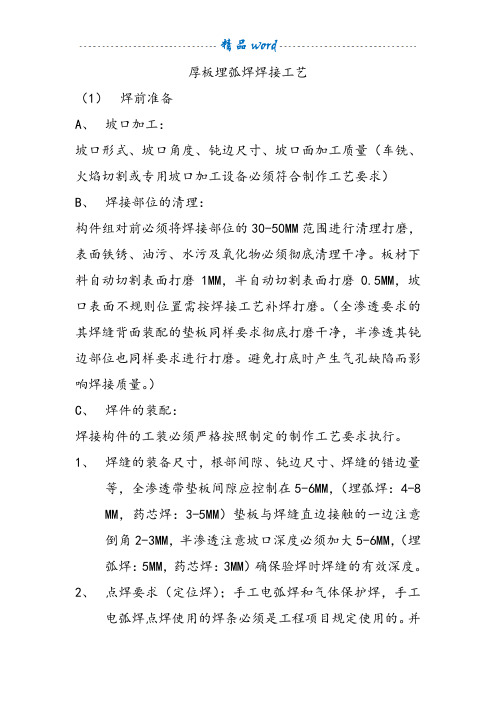
厚板埋弧焊焊接工艺(1)焊前准备A、坡口加工:坡口形式、坡口角度、钝边尺寸、坡口面加工质量(车铣、火焰切割或专用坡口加工设备必须符合制作工艺要求)B、焊接部位的清理:构件组对前必须将焊接部位的30-50MM范围进行清理打磨,表面铁锈、油污、水污及氧化物必须彻底清理干净。
板材下料自动切割表面打磨1MM,半自动切割表面打磨0.5MM,坡口表面不规则位置需按焊接工艺补焊打磨。
(全渗透要求的其焊缝背面装配的垫板同样要求彻底打磨干净,半渗透其钝边部位也同样要求进行打磨。
避免打底时产生气孔缺陷而影响焊接质量。
)C、焊件的装配:焊接构件的工装必须严格按照制定的制作工艺要求执行。
1、焊缝的装备尺寸,根部间隙、钝边尺寸、焊缝的错边量等,全渗透带垫板间隙应控制在5-6MM,(埋弧焊:4-8 MM,药芯焊:3-5MM)垫板与焊缝直边接触的一边注意倒角2-3MM,半渗透注意坡口深度必须加大5-6MM,(埋弧焊:5MM,药芯焊:3MM)确保验焊时焊缝的有效深度。
2、点焊要求(定位焊);手工电弧焊和气体保护焊,手工电弧焊点焊使用的焊条必须是工程项目规定使用的。
并且经过彻底烘烤,使用时必须放置在通上电源的保温桶随取随用,点焊的长度80MM及点焊间距800MM,点焊位置坡口磨深5MM,焊角尺寸根据构件的装配要求而定,全渗透带垫板焊角与垫板厚度相同,垫板与焊缝背面必须完全贴紧后再点焊,并且垫板两侧点焊时注意对称点焊,半渗透点焊应注意点焊的焊角尺寸,(必须两层三道,焊角10-12MM),箱梁构件注意在箱量内增加工艺板,(工艺板可以角焊焊接(角焊6MM),且必须四边全部焊满)工字钢构件组对后焊前须加横撑固定。
(装配工艺板与横撑要求可以根据构件的实际长度而定,间隔距离1000-1200MM),所有点焊必须焊工操作,厚件定位焊质量较为重要,焊接要求与正式焊缝相同。
厚件点焊时注意不得在构件上构件上随意引弧,焊工点焊时注意每个点焊收弧部位的收弧方式,不允许有弧坑,且弧坑必须填满(可往回焊10-20MM或划圈收弧)。
50mm厚钢板双丝埋弧焊焊接工艺DOC

50mm厚钢板双丝埋弧焊焊接工艺母材钢号:Q345GJC板厚:50mm焊接形式:平板对接焊丝:H10Mn2焊剂:SJ101(350 ℃,2 小时)预热温度:80-150℃层间温度:80-200℃造船用单丝埋弧焊常用焊接工艺参考1 焊接形式:平板对接焊剂:SJ101焊丝:H08MnA造船用单丝埋弧焊常用焊接工艺参考2 工艺特点:反面无需清根中厚板I型对接双丝双弧埋弧焊工艺参考焊接形式:I 型平板对接无间隙船厂用双丝埋弧焊工艺(一)(本工艺适用于对接间隙较小的平板对接焊)MZ-1250BM 双丝双电埋弧焊机技术规格书唐山开元自动焊接装备有限公司日期:2007 年11 月目录一、产品概要二、产品构成三、产品参数四、使用方法五、应用案例一、产品概要双丝埋弧自动焊是一种高效的焊接方法,可以获得较高的熔敷效率,可以实现在很高的焊速下获得合理的焊缝成形和良好的焊接质量,可以有效提高焊缝的抗气孔能力。
在埋弧焊焊接过程中,当熔深要求一定时,提高焊接速度,电弧对熔池中液体金属的后排作用加剧,焊缝成形恶化,易于出现两侧凹陷咬边,中心有尖峰的山峰形焊缝,使焊速受到制约;另一方面,厚板焊接时,提高焊接电流虽然可以使熔深增加,但容易生成气孔、裂缝等缺陷,使单弧埋弧焊的电流受到制约。
双丝埋弧焊接过程中,前丝和后丝共同决定了热输入、和最终的组织状态和使用性能,而前、后丝的作用又不尽相同。
通过调整前丝直流电弧的极性、焊接电流、焊接电压、焊接速度来保证焊缝的熔深,一般前丝的焊接电流较大而电压较小,后丝交流电弧的作用是保证熔池的宽度和焊缝的形状,一般后丝的焊接电流较小而电压较高。
另外双丝焊时,双电弧共同作用于一个熔池,熔池受电弧的搅拌作用增强可有效消除焊缝边缘的未熔合,同时焊接时形成的熔池较长,金属在其固熔态时时间较长,相对于单电弧时的冷却速度和热循环过程较慢,焊缝中的微量元素由较长时间进行扩散,熔池的底部面积扩展,不易形成梨形焊道(见图1),可减少焊缝根部热裂纹的产生概率,同时也有效的避免了气孔的形成。
厚板焊接工艺
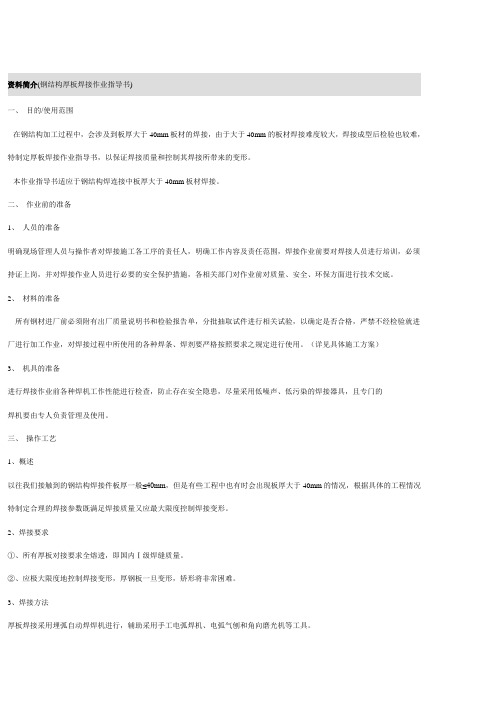
明确现场管理人员与操作者对焊接施工各工序的责任人,明确工作容及责任范围,焊接作业前要对焊接人员进行培训,必须持证上岗,并对焊接作业人员进行必要的安全保护措施,各相关部门对作业前对质量、安全、环保方面进行技术交底。
2、材料的准备
所有钢材进厂前必须附有出厂质量说明书和检验报告单,分批抽取试件进行相关试验,以确定是否合格,严禁不经检验就进厂进行加工作业,对焊接过程中所使用的各种焊条、焊剂要严格按照要求之规定进行使用。(详见具体施工方案)
2.1.3边缘刨加工的零件,其未注公差尺寸的极限偏差应符合GB1804-49《公差与配合未注公差尺寸的极限偏差》的Js14或js14的规定。
2.1.4零件经矫正后的形位公差应符合下列规定。
2.1.4.1型钢、钢板的平面度、垂直度、不扭曲度应符合表4的规定。
2.1.4.2钢板零件刨边后,边棱的直线度不得大于边棱长度的0.5/1000,且不大于1.5毫米。
b.其中一侧是奥氏体不锈钢时,可选用含镍、铬量比不锈钢更高的焊条(焊丝)。
1.4焊前准备。
1.4.1焊接前必须根据材料的可焊性、结构特点、设计要求、设备能力、使用条件及施工环境等因素编制合理的焊接工艺。
1.4.2首次使用的钢种以及改变焊接材料类型、焊接方法和焊接工艺,必须在施工前进行焊接工艺试验。并按有关标准进行工艺评定。
1.4.2.4在焊工考试和工程施焊前,必须具有合格的试验评定结果,该结果应由技术负责人验证。
1.4.3焊接材料的使用。
1.4.3.1焊条应根据说明规定进行烘干,烘干的焊条应在100~150℃保温,随用随取。烘干的焊条位置于空气中超过四小时,重新烘干,重新烘干次数不超过两次。
1.4.3.2焊丝表面不得有油污、水、铁锈等,不得有小角度弯曲。
海洋工程厚板双丝埋弧焊焊接工艺研究

海洋工程厚板双丝埋弧焊焊接工艺研究摘要:海上工程具有资源丰富、发电利用小时数高、不占用土地、不消耗水资源和适宜大规模开发的特点,近几年许多国家把风电开发重点转向海上,许多大型风电开发企业、设备制造企业正积极探索海上风电发展之路。
随着海上工程项目的蓬勃发展,直缝焊管作为海上风机基础的重要组成构件被广泛应用。
由于海上服役的特性,对于焊管的性能(尤其是低温冲击韧性)的要求特别高。
此外由于需求量大、工期紧,需要对直缝焊管进行焊接工艺研究,以满足上述要求。
基于此,本篇文章对海洋工程厚板双丝埋弧焊焊接工艺进行研究,以供参考。
关键词:海洋工程;厚板双丝;埋弧焊;焊接工艺引言随着海洋工程由几十米的浅水水域进入到300m以上水深的深海领域,海洋装备结构物也朝着大型化发展,这在导致钢板厚度增大的同时,也使厚板所占的比例越来越大。
作为占海洋工程导管架焊接工作量约40%的卷管接长工作,焊接效率的高低将影响整个项目的建造进度。
埋弧焊因其具有焊接速度快、焊缝质量好、成形美观及熔覆效率高等优点,一直以来在钢管卷制接长工作中占有重要的地位,是卷管接长的主要焊接方法。
伴随着越来越多的厚板卷管接长工作量,亟需开发更高效的埋弧焊工艺来提升施工效率。
提高埋弧焊的焊接效率有多种方法,比如增加焊丝数量、减小熔敷金属面积、提高熔敷速度等方法。
根据我公司的实际情况,选用双丝埋弧焊工艺作为提升焊接效率的方法。
1海洋工程项目质量管理体当一个企业取得ISO9001质量管理体系认证,标志着这个企业向质量管理的规范化和专业化有了极大的迈进,但认证成功本身并不意味着高枕无忧,而是标志着另一个新的开端,重要的是企业的管理体系在实际生产经营过程中的有效运用,特别是与具体的工程项目质量管理实践有机结合,才能真正发挥出先进管理体系的优势和效能。
在海洋石油工程企业大的质量管理框架之下,每一个独立的工程项目可以视作另一个子企业,也须建立一套属于自己的行之有效的质量管理体系,项目的子体系脱胎于企业的主体系但又不尽相同,可以说,企业体系是项目体系的前提和基础,项目体系是企业体系的延续和深化。
埋弧焊接工艺

埋弧自动焊接工艺本工艺适用于板厚6~22mm的碳钢及高强度低合金钢焊接。
一.焊前准备1.所焊产品的钢种及板材厚度按工艺要求选择焊丝牌号,焊丝直径及焊剂牌号,选用焊接规范。
2.检查埋弧焊机是否完好,电流表、电压表的正确性。
3.检查焊缝两端的始终点引弧板及灭弧板,其规格尺寸为80×80(mm)厚度≥母材。
4.焊件边缘加工和装配要求高,焊件边缘必须打磨清洁干净至光洁金属为止(距焊件边缘20mm处),用砂轮机进性打磨。
5.焊件边缘加工必须平直,装配间隙均匀一致,高低平整,装配间隙<1mm,两板高低差<0.5mm。
6.定位焊缝间距300~400mm,焊缝长度15~20mm,A3钢使用J427焊条,16Mn钢使用J507焊条,并清除点焊焊渣。
二.焊丝与焊剂选用1.焊丝与焊剂根据不同钢种的焊件进行选用(如表1)。
表12.焊丝直径根据板厚不同选用,<10mm板厚选用直径4mm,≥12mm板厚选用5mm。
.1.3.焊丝外表不得有油、锈存在,且应在干燥室存放。
4.焊剂使用前必须进行烘焙150~200℃×2后使用,使用剩余焊剂应重新烘焙。
三.焊接规范参数:1.本规范适应于双面焊接板厚≤14mm可不开坡口焊接,板厚≥16mm应开坡口,焊接坡口为65°±5°,根部8mm。
2. 板厚≥16mm正面焊后,反面进行用气刨扣槽,碳棒φ10mm,扣槽深度为6~7mm。
3.焊接规范参数如表2,船形角焊(平对接焊)如表3,平角焊如表4。
表2 焊接规范参数注:以上规格指间隙在标准范围内,如间隙超差则焊接电流及速度应相应调整。
四.焊接(纵缝焊接):1.根据不同板厚用试板调试焊接规范,不允许在产品上边焊接边调试,防止未焊透现象生。
2.开始焊前应校核焊丝与焊缝对中,焊丝伸出长度应等于焊接时长度,并把.2.指针纠正与焊丝对一直线。
3.起、熄弧应在引、熄弧板上进行,其起、熄焊缝长度不少于60mm。
厚钢板免清根埋弧自动焊施工工法(2)
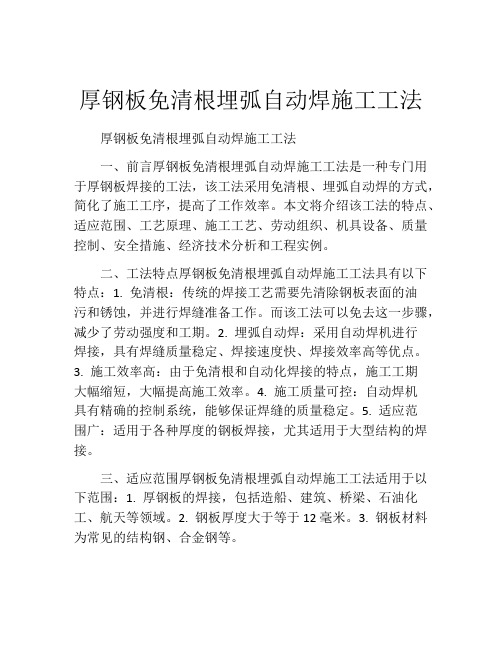
厚钢板免清根埋弧自动焊施工工法厚钢板免清根埋弧自动焊施工工法一、前言厚钢板免清根埋弧自动焊施工工法是一种专门用于厚钢板焊接的工法,该工法采用免清根、埋弧自动焊的方式,简化了施工工序,提高了工作效率。
本文将介绍该工法的特点、适应范围、工艺原理、施工工艺、劳动组织、机具设备、质量控制、安全措施、经济技术分析和工程实例。
二、工法特点厚钢板免清根埋弧自动焊施工工法具有以下特点:1. 免清根:传统的焊接工艺需要先清除钢板表面的油污和锈蚀,并进行焊缝准备工作。
而该工法可以免去这一步骤,减少了劳动强度和工期。
2. 埋弧自动焊:采用自动焊机进行焊接,具有焊缝质量稳定、焊接速度快、焊接效率高等优点。
3. 施工效率高:由于免清根和自动化焊接的特点,施工工期大幅缩短,大幅提高施工效率。
4. 施工质量可控:自动焊机具有精确的控制系统,能够保证焊缝的质量稳定。
5. 适应范围广:适用于各种厚度的钢板焊接,尤其适用于大型结构的焊接。
三、适应范围厚钢板免清根埋弧自动焊施工工法适用于以下范围:1. 厚钢板的焊接,包括造船、建筑、桥梁、石油化工、航天等领域。
2. 钢板厚度大于等于12毫米。
3. 钢板材料为常见的结构钢、合金钢等。
四、工艺原理厚钢板免清根埋弧自动焊施工工法的工艺原理是基于埋弧焊的工艺技术。
具体来说,该工法采取措施将熔化焊丝送入焊缝中,产生熔化焊缝,同时利用电弧的热量使焊缝两侧的钢板熔化并形成新的金属结合。
采用自动焊机进行焊接,保证了焊接的稳定性和一致性。
五、施工工艺厚钢板免清根埋弧自动焊施工工法包括以下施工阶段:1. 准备工作:对焊接设备进行检查和调试,准备焊接材料和辅助材料。
2. 钢板定位:将待焊的钢板准确定位,并进行调整和固定。
3. 清洁处理:对焊缝两侧的钢板进行清洁处理,除去油污和锈蚀物。
4. 焊缝设计:根据设计要求和施工方案进行焊缝设计,确定焊接参数。
5. 预热处理:对厚钢板进行预热处理,以提高焊接质量。
6. 焊接施工:运用自动焊机进行焊接,实现埋弧自动焊接。
一种304L不锈钢厚板的埋弧焊焊接工艺[发明专利]
![一种304L不锈钢厚板的埋弧焊焊接工艺[发明专利]](https://img.taocdn.com/s3/m/9ada0f1e2bf90242a8956bec0975f46526d3a759.png)
(19)中华人民共和国国家知识产权局(12)发明专利申请(10)申请公布号 (43)申请公布日 (21)申请号 202010789193.9(22)申请日 2020.08.07(71)申请人 江南造船(集团)有限责任公司地址 201913 上海市崇明区长兴江南大道988号(72)发明人 王敬 龚海磊 汤文 (74)专利代理机构 上海光华专利事务所(普通合伙) 31219代理人 周涌贺(51)Int.Cl.B23K 9/18(2006.01)B23K 9/235(2006.01)(54)发明名称一种304L不锈钢厚板的埋弧焊焊接工艺(57)摘要本发明提供一种304L不锈钢厚板的埋弧焊焊接工艺,该埋弧焊焊接工艺步骤包括:一、焊接坡口加工;二、焊前准备;三、焊接:采用焊接小车对正面坡口进行打底层焊接,完成后再进行正面埋弧焊焊接;将完成正面埋弧焊的两304L不锈钢厚板翻身,然后对反面坡口进行等离子碳弧气刨清根;采用焊接小车对完成清根的反面坡口进行背面埋弧焊焊接;四、焊后处理,本发明根据304L 不锈钢的成分及性能,对焊接坡口尺寸和焊接工艺进行优化,并合理匹配焊材,以保证焊接接头的质量,防止收缩变形、夹渣、气孔、晶粒粗大等缺陷的产生,在零下20℃时具有良好的力学性能,尤其是具有良好的低温冲击韧性。
权利要求书2页 说明书6页 附图3页CN 111843132 A 2020.10.30C N 111843132A1.一种304L不锈钢厚板的埋弧焊焊接工艺,其特征在于,所述埋弧焊焊接工艺步骤包括:一、焊接坡口加工:将待焊接的304L不锈钢厚板加工出双面X型坡口,正面坡口角度为60°±5°,钝边长度为4mm~5mm,坡口间隙为0mm~1mm,反面坡口角度为70°±5°,反面坡口深度为1/3t mm~2/5t mm,其中,t为待焊接的304L不锈钢厚板的厚度;二、焊前准备:选用与待焊接的304L不锈钢厚板相匹配的焊丝和碱性焊剂,并对碱性焊剂进行烘培处理,烘培温度为300℃~350℃,烘培时间为2h;三、焊接:A、采用焊接小车对正面坡口进行打底层焊接,完成后再进行正面埋弧焊焊接;所述打底层焊接的工艺参数为:焊接电流390A~420A,焊接电压32V~35V,焊接速度27cm/min~30cm/min,焊接热输入27.6KJ/cm~32.3KJ/cm;所述正面埋弧焊焊接的工艺参数为:焊接电流400A~430A,焊接电压34V~37V,焊接速度25cm/min~30cm/min,焊接热输入27KJ/cm~36KJ/cm;B、将完成正面埋弧焊的两304L不锈钢厚板翻身,然后对反面坡口进行等离子碳弧气刨清根;C、采用焊接小车对完成清根的反面坡口进行背面埋弧焊焊接;所述背面埋弧焊焊接的工艺参数为:焊接电流400A~430A,焊接电压34V~37V,焊接速度25cm/min~30cm/min,焊接热输入27KJ/cm~36KJ/cm。
埋弧焊40mm厚板焊接工艺探究
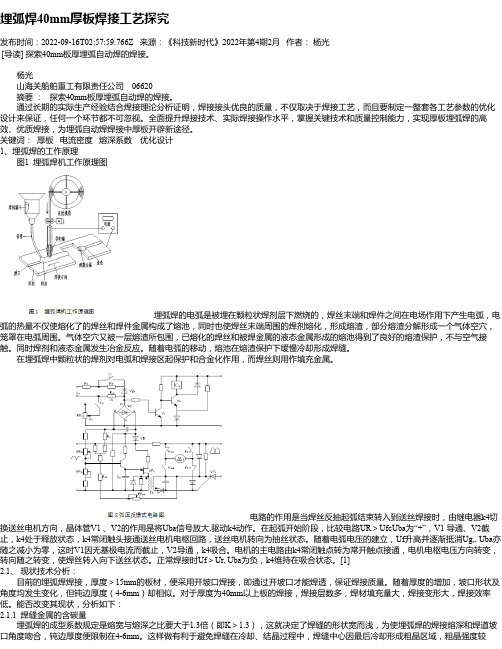
埋弧焊40mm厚板焊接工艺探究发布时间:2022-09-16T02:57:59.766Z 来源:《科技新时代》2022年第4期2月作者:杨光[导读] 探索40mm板厚埋弧自动焊的焊接。
杨光山海关船舶重工有限责任公司 06620摘要:探索40mm板厚埋弧自动焊的焊接。
通过长期的实际生产经验结合焊接理论分析证明,焊接接头优良的质量,不仅取决于焊接工艺,而且要制定一整套各工艺参数的优化设计来保证,任何一个环节都不可忽视。
全面提升焊接技术、实际焊接操作水平,掌握关键技术和质量控制能力,实现厚板埋弧焊的高效、优质焊接,为埋弧自动焊焊接中厚板开辟新途径。
关键词:厚板电流密度熔深系数优化设计1、埋弧焊的工作原理图1 埋弧焊机工作原理图埋弧焊的电弧是被埋在颗粒状焊剂层下燃烧的,焊丝末端和焊件之间在电场作用下产生电弧,电弧的热量不仅使熔化了的焊丝和焊件金属构成了熔池,同时也使焊丝末端周围的焊剂熔化,形成熔渣,部分熔渣分解形成一个气体空穴,笼罩在电弧周围。
气体空穴又被一层熔渣所包围,已熔化的焊丝和被焊金属的液态金属形成的熔池得到了良好的熔渣保护,不与空气接触。
同时焊剂和液态金属发生冶金反应。
随着电弧的移动,熔池在熔渣保护下缓慢冷却形成焊缝。
在埋弧焊中颗粒状的焊剂对电弧和焊接区起保护和合金化作用,而焊丝则用作填充金属。
电路的作用是当焊丝反抽起弧结束转入到送丝焊接时,由继电器k4切换送丝电机方向,晶体管V1 、V2的作用是将Uba信号放大,驱动k4动作。
在起弧开始阶段,比较电路UR>UfcUba为“+”,V1 导通、V2截止,k4处于释放状态,k4常闭触头接通送丝电机电枢回路,送丝电机转向为抽丝状态。
随着电弧电压的建立,Uf升高并逐渐抵消Ug,, Uba亦随之减小为零,这时V1因无基极电流而截止,V2导通,k4吸合。
电机的主电路由k4常闭触点转为常开触点接通,电机电枢电压方向转变,转向随之转变,使焊丝转入向下送丝状态。
50mm厚钢板双丝埋弧焊焊接工艺要点

50mm厚钢板双丝埋弧焊焊接工艺母材钢号:Q345GJC板厚:50mm焊接形式:平板对接焊丝:H10Mn2焊剂:SJ101(350 ℃,2 小时)预热温度:80-150℃层间温度:80-200℃造船用单丝埋弧焊常用焊接工艺参考1 焊接形式:平板对接焊剂:SJ101焊丝:H08MnA造船用单丝埋弧焊常用焊接工艺参考2 工艺特点:反面无需清根中厚板I型对接双丝双弧埋弧焊工艺参考焊接形式:I 型平板对接无间隙船厂用双丝埋弧焊工艺(一)(本工艺适用于对接间隙较小的平板对接焊)MZ-1250BM 双丝双电埋弧焊机技术规格书唐山开元自动焊接装备有限公司日期:2007 年11 月目录一、产品概要二、产品构成三、产品参数四、使用方法五、应用案例一、产品概要双丝埋弧自动焊是一种高效的焊接方法,可以获得较高的熔敷效率,可以实现在很高的焊速下获得合理的焊缝成形和良好的焊接质量,可以有效提高焊缝的抗气孔能力。
在埋弧焊焊接过程中,当熔深要求一定时,提高焊接速度,电弧对熔池中液体金属的后排作用加剧,焊缝成形恶化,易于出现两侧凹陷咬边,中心有尖峰的山峰形焊缝,使焊速受到制约;另一方面,厚板焊接时,提高焊接电流虽然可以使熔深增加,但容易生成气孔、裂缝等缺陷,使单弧埋弧焊的电流受到制约。
双丝埋弧焊接过程中,前丝和后丝共同决定了热输入、和最终的组织状态和使用性能,而前、后丝的作用又不尽相同。
通过调整前丝直流电弧的极性、焊接电流、焊接电压、焊接速度来保证焊缝的熔深,一般前丝的焊接电流较大而电压较小,后丝交流电弧的作用是保证熔池的宽度和焊缝的形状,一般后丝的焊接电流较小而电压较高。
另外双丝焊时,双电弧共同作用于一个熔池,熔池受电弧的搅拌作用增强可有效消除焊缝边缘的未熔合,同时焊接时形成的熔池较长,金属在其固熔态时时间较长,相对于单电弧时的冷却速度和热循环过程较慢,焊缝中的微量元素由较长时间进行扩散,熔池的底部面积扩展,不易形成梨形焊道(见图1),可减少焊缝根部热裂纹的产生概率,同时也有效的避免了气孔的形成。
15CrMoR厚板埋弧焊工艺试验与结果分析

0.4~0.5
温度 250~300℃。⑦层间熔渣清理干净,背面清根时,用
埋弧焊是通过电弧对焊丝和母材进行加热,使其熔 碳弧气抛抛净背部熔渣后,用砂轮对抛后的表面进行打
化进行连接的方法。焊接过程中焊丝、电弧和焊缝均被 磨处理。
焊剂覆盖,无任何飞溅,焊缝表面光洁、成形美观,焊后无
2.4 焊后热处理
需进行表面的修磨。熔化的焊剂还起到隔离空气,保护
Zheng Kang He Yongliang Zhang Hongchang Li Xin (Kaifeng Air Separation Group Co., LTD,Kaifeng Henan 475004)
Abstract: On the basis of analyzing the characteristics of the 15CrMoR welding steel, the 40mm thick plate sub⁃ merged arc welding process test, and choose the appropriate welding parameters, make effective technological mea⁃ sures to prevent the formation of the welding defects such as cracks, the experiment has achieved satisfactory results, the quality of products is guaranteed. Keywords: 15CrMoR;thick plate;craze;submerged arc welding;process test
收稿日期:2017-06-02 作者简介:郑康(1988-),男,本科,助理工程师,研究方向:焊接工艺研发。
焊接厚钢板方法

焊接厚钢板方法
焊接厚钢板是一项非常重要的工艺,它在很多领域都有着广泛的应用,比如船舶、桥梁、建筑等领域。
焊接厚钢板的方法有很多种,下面就
来介绍一下其中比较常用的几种方法。
1.手工电弧焊接
手工电弧焊接是一种比较常见的焊接方法,它适用于焊接厚度在3mm 以上的钢板。
这种方法的优点是操作简单,成本低,适用范围广,但
是它的缺点也很明显,就是焊接速度慢,焊缝质量不够稳定。
2.埋弧焊接
埋弧焊接是一种比较高效的焊接方法,它适用于焊接厚度在10mm以上的钢板。
这种方法的优点是焊接速度快,焊缝质量稳定,但是它的
缺点也很明显,就是需要专门的设备和操作技能,成本较高。
3.气体保护焊接
气体保护焊接是一种比较高端的焊接方法,它适用于焊接厚度在3mm 以上的钢板。
这种方法的优点是焊接速度快,焊缝质量稳定,但是它
的缺点也很明显,就是需要专门的设备和操作技能,成本较高。
4.激光焊接
激光焊接是一种比较新颖的焊接方法,它适用于焊接厚度在3mm以
上的钢板。
这种方法的优点是焊接速度快,焊缝质量稳定,但是它的
缺点也很明显,就是需要专门的设备和操作技能,成本较高。
总的来说,焊接厚钢板的方法有很多种,每种方法都有其优点和缺点,具体选择哪种方法要根据实际情况来决定。
在选择焊接方法的时候,
需要考虑到焊接的材料、厚度、要求等因素,以及设备和操作技能的
条件。
只有选择合适的焊接方法,才能保证焊接质量和效率。
40mm厚板Q355NHB耐候钢埋弧焊接技术
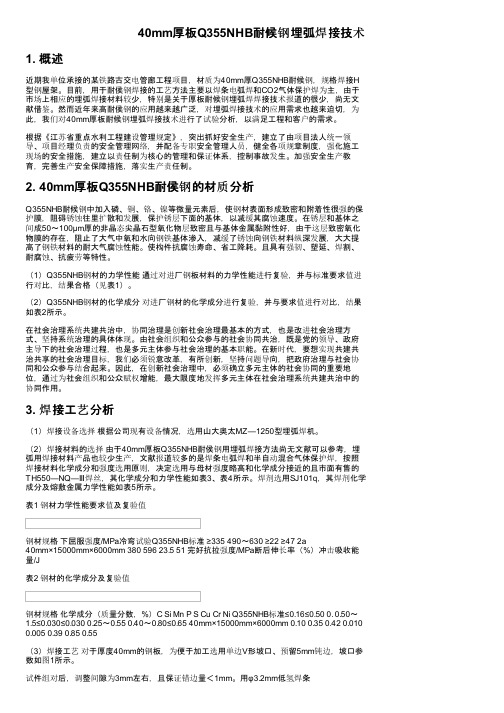
40mm厚板Q355NHB耐候钢埋弧焊接技术1. 概述近期我单位承接的某铁路古交电管廊工程项目,材质为40mm厚Q355NHB耐候钢,规格焊接H 型钢屋架。
目前,用于耐侯钢焊接的工艺方法主要以焊条电弧焊和CO2气体保护焊为主,由于市场上相应的埋弧焊接材料较少,特别是关于厚板耐候钢埋弧焊焊接技术报道的很少,尚无文献借鉴。
然而近年来高耐侯钢的应用越来越广泛,对埋弧焊接技术的应用需求也越来迫切,为此,我们对40mm厚板耐候钢埋弧焊接技术进行了试验分析,以满足工程和客户的需求。
根据《江苏省重点水利工程建设管理规定》,突出抓好安全生产,建立了由项目法人统一领导、项目经理负责的安全管理网络,并配备专职安全管理人员,健全各项规章制度,强化施工现场的安全措施,建立以责任制为核心的管理和保证体系,控制事故发生。
加强安全生产教育,完善生产安全保障措施,落实生产责任制。
2. 40mm厚板Q355NHB耐侯钢的材质分析Q355NHB耐候钢中加入磷、铜、铬、镍等微量元素后,使钢材表面形成致密和附着性很强的保护膜,阻碍锈蚀往里扩散和发展,保护锈层下面的基体,以减缓其腐蚀速度。
在锈层和基体之间成50~100μm厚的非晶态尖晶石型氧化物层致密且与基体金属黏附性好,由于这层致密氧化物膜的存在,阻止了大气中氧和水向钢铁基体渗入,减缓了锈蚀向钢铁材料纵深发展,大大提高了钢铁材料的耐大气腐蚀性能。
使构件抗腐蚀寿命、省工降耗。
且具有强韧、塑延、焊割、耐腐蚀、抗疲劳等特性。
(1)Q355NHB钢材的力学性能通过对进厂钢板材料的力学性能进行复验,并与标准要求值进行对比,结果合格(见表1)。
(2)Q355NHB钢材的化学成分对进厂钢材的化学成分进行复验,并与要求值进行对比,结果如表2所示。
在社会治理系统共建共治中,协同治理是创新社会治理最基本的方式,也是改进社会治理方式、坚持系统治理的具体体现。
由社会组织和公众参与的社会协同共治,既是党的领导、政府主导下的社会治理过程,也是多元主体参与社会治理的基本职能。
厚板(16mm)双丝埋弧焊(tandemwire)的再实验

厚板(16mm)双丝埋弧焊(tandemwire)的再实验一.前言:我们知道在焊接厚板时,若采用单丝埋弧焊,加大焊接电流和电弧电压,虽然可以增加焊丝填充量,提高焊接速度,但是由于热输入量大,热循环过程快,会引起焊缝金属组织粗大,冲击性能降低。
而且,熔化金属可能来不及摊开,造成焊缝成型不美观;采用双丝双弧埋弧焊由于是双电弧单熔池,不仅实现高速焊接,而且热循环过程相对较慢,有利于焊缝中微量元素的扩散,提高焊缝性能,目前网上关于,双丝双弧的工艺类文章可以搜索一大堆;阅读每一篇都会发现一些新的东西;我想分享的是另外一下东西。
也为了方便富科斯调试人员及用户提供结合实际的焊接工艺参数参考数据。
实验基准:工件厚度为16mm板二试验设备:前焊丝Lincoln DC-1000直流电源,后丝Lincoln AC-1200 交流电源。
三.焊接材料及焊接坡口:1.试验材料及规格:δ=16mm Q235A试板;。
衬板厚度为14mm。
采用H08MnAφ4焊丝。
焊剂采用HJ431。
2.焊接坡口:对厚度16mm板设计两种形式坡口。
为了提高生产效率,减少焊丝填充量,以及减少立板侧的表层焊缝宽度,采用单面带钝边坡口,将坡口开在腹板上。
坡口和接头组合形式见图1-3。
考虑到箱形梁生产过程一般采用气割下料,留钝边不易保证尺寸,因而又设计了另一种无钝边的坡口形式。
坡口和接头组合形式见图4-6。
四. 焊接工艺(一)试验:双丝双弧埋弧焊前后焊丝距离试验:前后焊丝距离对焊缝成形及电弧稳定性有一定影响。
试验采用平板,在相同的焊接参数下,进行不同丝距的比较试验。
焊接规范参数如下:前后焊丝直φ4mm前丝伸出长度: 30mm 后丝伸出长度: 35mm后焊丝倾角: 15度前丝焊接电流 700A前丝电弧电压 35V后丝焊接电流:500A后丝电弧电压:39-40V 焊接速度:28.2/m.h-1不同焊丝距离对焊缝成形的影响列于表1。
表1. 不同焊丝距离对焊缝尺寸的影响从表中数据可见,焊缝宽度随丝距加大而减小。
埋弧焊焊接工艺
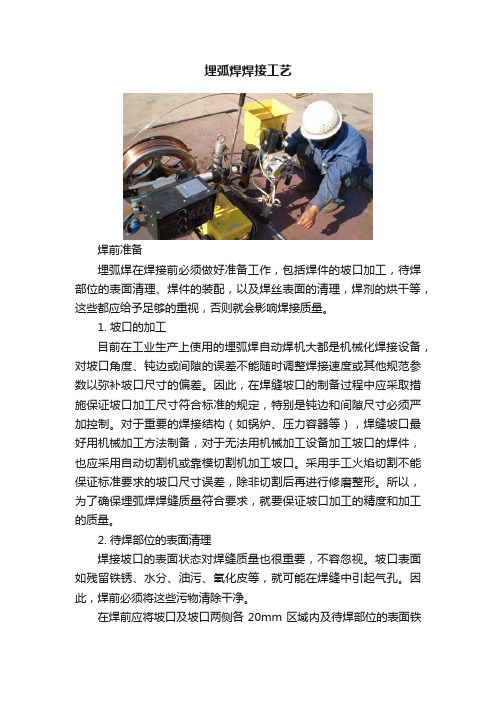
埋弧焊焊接工艺焊前准备埋弧焊在焊接前必须做好准备工作,包括焊件的坡口加工,待焊部位的表面清理、焊件的装配,以及焊丝表面的清理,焊剂的烘干等,这些都应给予足够的重视,否则就会影响焊接质量。
1. 坡口的加工目前在工业生产上使用的埋弧焊自动焊机大都是机械化焊接设备,对坡口角度、钝边或间隙的误差不能随时调整焊接速度或其他规范参数以弥补坡口尺寸的偏差。
因此,在焊缝坡口的制备过程中应采取措施保证坡口加工尺寸符合标准的规定,特别是钝边和间隙尺寸必须严加控制。
对于重要的焊接结构(如锅炉、压力容器等),焊缝坡口最好用机械加工方法制备,对于无法用机械加工设备加工坡口的焊件,也应采用自动切割机或靠模切割机加工坡口。
采用手工火焰切割不能保证标准要求的坡口尺寸误差,除非切割后再进行修磨整形。
所以,为了确保埋弧焊焊缝质量符合要求,就要保证坡口加工的精度和加工的质量。
2. 待焊部位的表面清理焊接坡口的表面状态对焊缝质量也很重要,不容忽视。
坡口表面如残留铁锈、水分、油污、氧化皮等,就可能在焊缝中引起气孔。
因此,焊前必须将这些污物清除干净。
在焊前应将坡口及坡口两侧各20mm区域内及待焊部位的表面铁锈、水分、油污、氧化皮等清除干净。
氧化皮及铁锈可用砂轮机、风动砂轮、钢丝刷、喷丸处理等清除,油污和水分可用火焰加热烘干。
在低合金钢和不锈钢的焊接中,焊接坡口的清理更为重要,坡口表面的锈蚀和水分油污不但会引起气孔,而且可能促使氢致裂纹、焊缝增碳,甚至降低不锈钢焊接接头的耐蚀性和低合金钢接头的力学性能,故应特别注意3. 焊件的装配埋弧焊接头的组装状况对焊接质量有很大影响。
焊接接头的间隙和错边在很大程度上影响着焊缝的熔透和外表成形,焊前应仔细检查。
焊接接头要求装配间隙均匀,高低平整、错变量小,接头的组装误差主要决定与划线、下料、成形和坡口加工的精度。
因此,接头的装配质量是通过严格控制前道工序的加工偏差来保证的。
特别是单面焊双面成形焊时,因接头的装配间隙是决定熔透深度的重要因素,装配间隙应严格控制,同一条焊缝上装配间隙的误差不应超过1mm。
50mm厚板焊接工艺
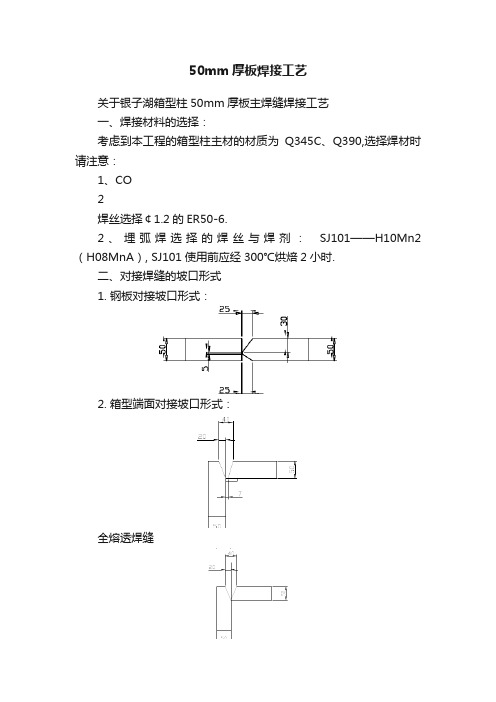
50mm厚板焊接工艺关于银子湖箱型柱50mm厚板主焊缝焊接工艺一、焊接材料的选择:考虑到本工程的箱型柱主材的材质为Q345C、Q390,选择焊材时请注意:1、CO2焊丝选择¢1.2的ER50-6.2、埋弧焊选择的焊丝与焊剂:SJ101——H10Mn2(H08MnA), SJ101使用前应经300℃烘焙2小时.二、对接焊缝的坡口形式1. 钢板对接坡口形式:2. 箱型端面对接坡口形式:全熔透焊缝部分熔透焊缝三、焊接工艺:1.切割坡口.1.1.中厚板坡口在切割前先划好三条线,即轨道线、角度线、坡口宽度线,如图所示.1.2.一律采用半自动切割机进行打坡口, 打坡口前,应检查半自动切割机行走轨道的直线度≤2mm, 对轨道直线度超标的应重新校直或重新制做.1.3.对切割后的坡口进行打磨, 打磨范围为坡口及周边30mm区域.如图所示.2.钢板组对.2.1.组对前应打通线检测钢板的直线度, 对整板直线度每米超过1mm且总长超过10mm的应进行校直.2.2.对箱型全熔透焊缝,在组对前要对腹板坡口的背面加焊衬垫, 在加衬垫时一要保证间隙均匀,二要满足腹板整体宽度尺寸符合图纸要求.2.3. 钢板在组对时,应控制对口错边量≤2mm.2.4.为防止厚板焊后产生角变形.50mm的对接钢板在施焊面的背面垫上一块8-12mm厚的垫板或小槽钢,借用反变形措施来减小焊后的角变形量.2.5.为确保原材料在厚度方向上的质量,50mm厚钢板在焊接前要对坡口两边100mm范围内进行UT探伤,确认无夹渣、夹层等缺陷时再进行焊接.用ER50-6型的CO2气保焊先进行定位焊.定位焊时.调节定位焊电流比正式焊接时大20%~25%,焊接速度不宜太快.定位焊缝长度50-70mm,焊脚尺寸: Hf=4-5mm,焊道间距为300mm.定位焊缝作为正式焊缝的一部分不得有未焊透、裂纹等缺陷.定位焊缝上若出现气孔或裂纹时,必须及时清除后重焊.2.6.必须加焊与坡口形状一致的引弧板、引出板.引弧板和引出板宽度不小于坡口的坡度面宽度,长度如图所示,厚度10mm,以照顾埋弧焊盖面的引收弧.焊接完毕后,必须用气割切除被焊工件上的引弧、引出板,并修磨平整,严禁用锤将其击落.钢板对接箱型对接3.焊接3.1.焊前预热.为便于预热温度的撑控,实际操作中将预热温度统一规定在100℃. 预热的加热区域应在焊接坡口的两侧各100mm范围区,如图所示. 预热时将烤枪喷嘴与构件应保持80mm距离,用中性焰加热,让火焰沿预热带慢慢往复均匀移动,使热量尽量渗透至钢板的全厚度.预热停止后,用测温仪对正面加热区进行选点检测.3.2. 钢板对接焊接.3.2.1. 正式焊接开始前或正式焊接中,发现定位焊有弧坑裂纹的,应彻底清除定位焊后,再进行正式焊接.焊丝对接头焊缝进行打底和填充, 填充时应将上3.2.2.用¢1.2的ER50-6型CO2层焊接残留在焊缝上的氧化皮(可借用钢丝刷清除)及焊道两侧的飞溅物(用角砂轮机去除)彻底清理干净,并用测温计控制好层间温度200-220℃.因层间焊接中断导致层间温度底于焊前预热温度的,续焊前应重新采取预热处理.应控制最后一层的填充高度距离坡口面2-3mm,以利埋弧焊一次性盖面. 埋弧焊采用¢4.0的H10Mn2配SJ101进行施焊。
厚板焊接、低温焊接工艺
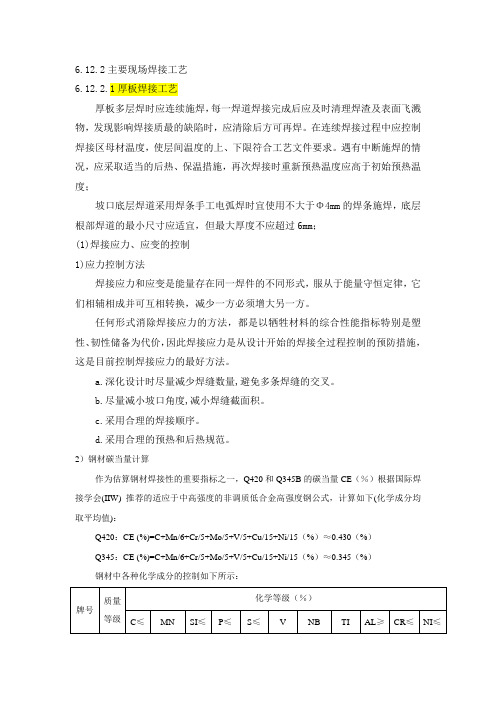
6.12.2主要现场焊接工艺6.12.2.1厚板焊接工艺厚板多层焊时应连续施焊,每一焊道焊接完成后应及时清理焊渣及表面飞溅物,发现影响焊接质最的缺陷时,应清除后方可再焊。
在连续焊接过程中应控制焊接区母材温度,使层间温度的上、下限符合工艺文件要求。
遇有中断施焊的情况,应采取适当的后热、保温措施,再次焊接时重新预热温度应高于初始预热温度;坡口底层焊道采用焊条手工电弧焊时宜使用不大于Φ4mm的焊条施焊,底层根部焊道的最小尺寸应适宜,但最大厚度不应超过6mm;(1)焊接应力、应变的控制1)应力控制方法焊接应力和应变是能量存在同一焊件的不同形式,服从于能量守恒定律,它们相辅相成并可互相转换,减少一方必须增大另一方。
任何形式消除焊接应力的方法,都是以牺牲材料的综合性能指标特别是塑性、韧性储备为代价,因此焊接应力是从设计开始的焊接全过程控制的预防措施,这是目前控制焊接应力的最好方法。
a.深化设计时尽量减少焊缝数量,避免多条焊缝的交叉。
b.尽量减小坡口角度,减小焊缝截面积。
c.采用合理的焊接顺序。
d.采用合理的预热和后热规范。
2)钢材碳当量计算作为估算钢材焊接性的重要指标之一,Q420和Q345B的碳当量CE(%)根据国际焊接学会(IIW) 推荐的适应于中高强度的非调质低合金高强度钢公式,计算如下(化学成分均取平均值):Q420:CE (%)=C+Mn/6+Cr/5+Mo/5+V/5+Cu/15+Ni/15(%)≈0.430(%)Q345:CE (%)=C+Mn/6+Cr/5+Mo/5+V/5+Cu/15+Ni/15(%)≈0.345(%)钢材中各种化学成分的控制如下所示:牌号质量等级化学等级(%)C≤MN SI≤P≤S≤V NB TI AL≥CR≤NI≤Q420 C 0.20 ≤1.60 0.55 0.035 0.035 0.02~0.200.015~0.060.02~0.200.015 0.40 0.70Q345 B 0.2 1.0~1.6 0.55 0.040 0.040 0.02~0.150.015~0.0600.02~0.20——碳当量Ceq<0.4%时,淬硬倾向不大,焊接性良好,当碳当量Ceq=0.4~0.6,钢材易淬硬,说明焊接性已变差,焊接时需预热,随着板厚的增大,预热温度也适当的提高。
- 1、下载文档前请自行甄别文档内容的完整性,平台不提供额外的编辑、内容补充、找答案等附加服务。
- 2、"仅部分预览"的文档,不可在线预览部分如存在完整性等问题,可反馈申请退款(可完整预览的文档不适用该条件!)。
- 3、如文档侵犯您的权益,请联系客服反馈,我们会尽快为您处理(人工客服工作时间:9:00-18:30)。
厚板埋弧焊焊接工艺
(1)焊前准备
A、坡口加工:
坡口形式、坡口角度、钝边尺寸、坡口面加工质量(车铣、火焰切割或专用坡口加工设备必须符合制作工艺要求)B、焊接部位的清理:
构件组对前必须将焊接部位的30-50MM范围进行清理打磨,表面铁锈、油污、水污及氧化物必须彻底清理干净。
板材下料自动切割表面打磨1MM,半自动切割表面打磨0.5MM,坡口表面不规则位置需按焊接工艺补焊打磨。
(全渗透要求的其焊缝背面装配的垫板同样要求彻底打磨干净,半渗透其钝边部位也同样要求进行打磨。
避免打底时产生气孔缺陷而影响焊接质量。
)
C、焊件的装配:
焊接构件的工装必须严格按照制定的制作工艺要求执行。
1、焊缝的装备尺寸,根部间隙、钝边尺寸、焊缝的错边量
等,全渗透带垫板间隙应控制在5-6MM,(埋弧焊:4-8 MM,药芯焊:3-5MM)垫板与焊缝直边接触的一边注意倒角2-3MM,半渗透注意坡口深度必须加大5-6MM,(埋弧焊:5MM,药芯焊:3MM)确保验焊时焊缝的有效深度。
2、点焊要求(定位焊);手工电弧焊和气体保护焊,手工
电弧焊点焊使用的焊条必须是工程项目规定使用的。
并
且经过彻底烘烤,使用时必须放置在通上电源的保温桶
随取随用,点焊的长度80MM及点焊间距800MM,
点焊位置坡口磨深5MM,焊角尺寸根据构件的装配要
求而定,全渗透带垫板焊角与垫板厚度相同,垫板与焊
缝背面必须完全贴紧后再点焊,并且垫板两侧点焊时注
意对称点焊,半渗透点焊应注意点焊的焊角尺寸,(必
须两层三道,焊角10-12MM),箱梁构件注意在箱量
内增加工艺板,(工艺板可以角焊焊接(角焊6MM),
且必须四边全部焊满)工字钢构件组对后焊前须加横撑
固定。
(装配工艺板与横撑要求可以根据构件的实际长
度而定,间隔距离1000-1200MM),所有点焊必须焊
工操作,厚件定位焊质量较为重要,焊接要求与正式焊
缝相同。
厚件点焊时注意不得在构件上构件上随意引
弧,焊工点焊时注意每个点焊收弧部位的收弧方式,不
允许有弧坑,且弧坑必须填满(可往回焊10-20MM或
划圈收弧)。
咬边缺陷同样要严格控制,大于1MM必
须补焊。
所有点焊在焊前必须预热(火焰加热
100-150°)。
临时固定去处时不得割伤母材。
3、引弧板与引出板,每条焊缝两端必须装配引弧板和引出
板,引弧板和引出板的大小应足以堆积焊剂并使引弧点
和弧坑落在正常焊缝之外。
装配要求与正式焊缝相同,
(引弧板和引出板长度在100-150MM之间,注意与坡口面和根部间隙必须平齐一致,同样必须经过打磨后在装配)
(2)焊接要求:
A、预热措施:
采用电加热器(加热板)控制,焊前预热、焊接过程中的层间温度控制及焊后消氢处理。
预热温度:100°-150°;
焊接层间温度:150°-250°;
焊后消氢温度:300°-350°1-2H;
B、焊接材料
焊接使用的所有材料必须是工程项目规定使用的,未经过项目工程师同意不得随意更换焊接材料。
使用的焊接材料必须按规定进行烘烤发放,每天的烘烤记录、发放记录、回收记录必须完整。
(埋弧焊剂与定位焊使用焊条烘烤时间必须按要求执行,以确保焊接质量。
)
当天未使用完的焊条和焊剂必须在下班前归还焊接材料管理员,焊接材料管理员对归还的焊条必须单独与其它区分放置烘烤保温,第二天应首先发放第二次烘烤的焊条。
注意焊条重复烘烤不应超过二次。
(二次烘烤的焊剂可与新烤的混合在一起使用。
)
焊条烘烤温度:LB-52 300°-350°0.5-1小时;
焊剂烘烤温度:参考制造工艺
C、焊接工艺参数:
埋弧焊焊接工艺参数,(焊接设备不同,提供Φ5MM焊丝大致范围。
焊丝型号规格:CHW-S3 焊剂:CHF-101
焊丝直径:Φ5.0
打底:450-550A 27-32V 26-32CM/MIN
填充:550-850A 33-40V 20-28CM/MIN
盖面:650-750A 32-38V 25-30CM/MIN
注意要求:必须根据每台焊机的实际使用特性及焊前调试规范为准,在保证焊接质量的前提下电压不要太高。
a、焊接位置:平焊、船型焊
b、焊前工艺参数调试;根据焊接位置,焊接层次选择合适
的工艺参数。
(焊前在试板预先调试)
c、工艺参数的匹配,电流、电压与焊接速度之间的匹配关
系是埋弧焊操作最主要的参数。
焊丝对中的角度及焊丝外伸长度要根据焊缝坡口形式和每道焊接层次而定。
埋弧焊打底第一层注意电压不易过大,且不宜焊的太厚(根部悍道截面较窄,如焊的太厚易产生裂纹)。
d、焊接层次,厚板埋弧焊焊接层次对焊缝内部质量和构件
的焊接变形控制有很大的影响。
必须多层多道,注意:每道焊接厚度、焊接方向、焊道内层次间布局,要有一
个合理的安排。
(每层焊道成型控制为内凹为最佳,分道时注意控制坡口两侧的所留的余量)。
构件焊接方向,方通、工字钢四条焊缝的焊接方向应控制一致,并注意对称焊接,根据构件的变形尺寸随时调整。
单道焊缝的熔宽(焊丝直径Φ4熔宽≤25MM,焊丝直径Φ5≤30MM)(限制焊道的熔宽和焊接厚度是控制焊接线能量一种有效手段,也是控制构件焊接变形的一种有效措施。
)e、焊接过程中注意焊剂的覆盖厚度,太厚将增加焊渣熔化
量,焊后清渣较困难。
且旱道成型较差。
太薄电弧保护不好,影响焊接质量。
焊剂覆盖厚度应控制在30-40MM之间。
f、加强焊接过程中焊剂的筛选,焊剂回收过程中注意清理
焊剂中夹杂物,焊渣颗粒及其它杂物对焊缝质量有直接影响。
g、注意焊接过程中使用风铲,厚板焊接加强风铲的使用对
焊缝的内部应力有一定的释放作用。
每个焊接部位配备两把风铲使用,并要求焊接人员每焊完一道必须用风铲锤击焊道一遍。
(盖面后不用锤击)
h、整个焊接过程必须使用行走指针,焊缝成型与否行走指
针的使用是关键,行走指针是埋弧焊焊接质量的保证。
它决定了焊缝温度场在焊道中的温度是否分布均匀,打底、填充、盖面都以行走指针为基准,焊工操作时注意
力应高度集中,根据指针与基准线出现的左右偏差和杆
丝长度而随时调整。
(焊接过程中注意指针与基准线的
距离3-4MM,太高观察角度易产生偏差。
)
i、盖面要求,控制盖面预留深度2-3MM,并要确定整个
焊道的深浅一致,必要时应补焊或打磨。
注意控制每条
盖面焊道的直线度,每道与每道之间应覆盖1/2处为标
准,必须覆盖到前一道焊缝的最高点,则易产生凹沟。
盖面余高应控制在2-3MM,最高不大于5MM,焊缝
盖面注意盖面顺序,(焊接方通由内向外)
j、焊后热处理,构件焊接完毕后通过加热器将温度升到300-350度1-2小时消氢处理,随后保温棉覆盖缓冷。