分解炉温度上下倒挂的原因及解决措施
N-MFC型分解炉流化床压床原因及解决措施

12 预 热 器 塌 料 .
预 热 器塌 料 由于操 作 等 方 面 的原 因造 成 预 热 器塌 料 , 问大 量物 料 冲 入分 解 炉 , 坏 了流 化层 , 瞬 破
导致 后 续物 料 在床 层 上不 能 被带 走 , 形成 压床 。
12。 误 操 作 造 成 预 热 器 塌 料 。1
由 5 %降 低 到 4 % , 时 喂 料 量 虽 然 仍 是 2 0/ , 3 8 此 4t h 但 因 为 系 统 风 量 变 小 ,造 成 系 统 塌 料 ,分 解 炉 压 床 , 原 因为 中控 员 操 作 不 熟 练 , 能 及 时 发 现 系 其 未 统变 化 。
12 2 预 热 器 出 口负 压 波 动 造 成 预 热 器 塌 料 __
由于燃 料 在 N— C 内燃 烧 不 完 全 , 料 的沸 MF 物
四 JI水 泥 一 25— l
维普资讯
腾 状 况 又 不 好 , 口温 度 低 , 分 燃 料 到 C 出 部 内继
续 燃烧 ,造 成 N— C 出 口与 C 出 口温 度 倒 挂 的 MF
一
窑 系 统 正 常 喂 料 量 一般 为 2 0/ 右 , 一 旦 4t h左
5 0P 0 0 a降 至 一 00 a 预 热器 各 级 下 料 管 温 度 急 2 0P ,
喂 料 量 波 动 到 20/ 右 时 , 解 炉 负 荷 加 大 , 7t h左 分 承 载 能 力 差 , 解 炉 层 压 就会 急 剧 上 升 , 果采 取 措 分 如 施 不 果 断就 会造 成分 解 炉 流 化床 压 床 的事 故 。 () 化 库 底 罗 茨风 机 皮 带 打 滑 , 成 下 料 不 1均 造
维普资讯
N o. 2OO8 3.
分解窑操作中常见的几个问题和产生问题的原因

分解窑操作中常见的几个问题和产生问题的原因,燃烧机(燃烧器)一、窑尾和预分解系统温度偏高1)核查是否生料kh、n值偏高,熔融相(ai203和fe203)含量偏低生料中是否si02比较高和生料细度偏粗。
如若干项情况属实,则由于生料易烧性差,熟料难烧结,上述温度偏高属正常现象。
但应注意极限温度和窑尾o:含量的控制。
2)窑内通风不好,窑尾空气过剩系数控制偏低,系统漏风产生二次燃烧。
3)排灰阀配重太轻或因为怕堵塞,窑尾岗位工把排灰阀阀杆吊起来,致使旋风筒收尘效率降低,物料循环量增加,预分解系统温度升高。
4)供料不足或来料不均匀。
5)旋风筒堵塞使系统温度升高。
6)燃烧器外流风太大、火焰太长,致使窑尾温度偏高。
7)烧成带温度太低,煤粉后燃。
8)窑尾负压太高,窑内抽力太大,高温带后移。
二、窑尾和预分解系统温度偏低1)对于一定的喂料量来说,用煤量偏少。
2)排灰阀工作不灵活,局部堆料或塌料。
由于物料分散不好,热交换差,致使预热器c,出口温度升高,但窑尾温度下降。
3)预热器系统漏风,增加了废气量和烧成热耗,废气温度下降。
三、烧成带温度太低1)风、煤、料配合不好。
对于一定喂料量,热耗控制偏低或火焰太长,高温带不集中。
2)在一定的燃烧条件下,窑速太快。
3)预热器系统的塌料以及温度低、分解率低的生料窜人窑前。
4)窑尾来料多或垮窑皮时,用煤量没有及时增加。
5)在窑内通风不良的情况下,又增加窑头用煤量,结果窑尾温度升高,烧成带温度反而下降。
6)冷却机一室篦板上的熟料料层太薄,二次风温度太低。
四、烧成带温度太高1)来料少而用煤量没有及时减少。
2)燃烧器内流风太大,致使火焰太短,高温带太集中。
3)二次风温度太高,黑火头短,火点位置前移。
五、二次风温度太高1)火焰太散,粗粒煤粉掺人熟料,人冷却机后继续燃烧。
2)熟料结粒太细致使料层阻力增加,二次风量减少,风温升高大量细粒熟料随二次风一起返回窑内。
3)熟料结粒良好,但冷却机一室料层太厚。
气化炉环形空间温度异常状况分析及总结
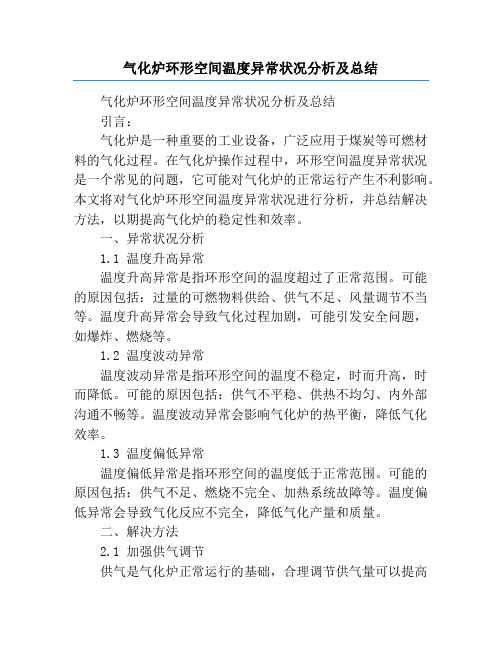
气化炉环形空间温度异常状况分析及总结气化炉环形空间温度异常状况分析及总结引言:气化炉是一种重要的工业设备,广泛应用于煤炭等可燃材料的气化过程。
在气化炉操作过程中,环形空间温度异常状况是一个常见的问题,它可能对气化炉的正常运行产生不利影响。
本文将对气化炉环形空间温度异常状况进行分析,并总结解决方法,以期提高气化炉的稳定性和效率。
一、异常状况分析1.1 温度升高异常温度升高异常是指环形空间的温度超过了正常范围。
可能的原因包括:过量的可燃物料供给、供气不足、风量调节不当等。
温度升高异常会导致气化过程加剧,可能引发安全问题,如爆炸、燃烧等。
1.2 温度波动异常温度波动异常是指环形空间的温度不稳定,时而升高,时而降低。
可能的原因包括:供气不平稳、供热不均匀、内外部沟通不畅等。
温度波动异常会影响气化炉的热平衡,降低气化效率。
1.3 温度偏低异常温度偏低异常是指环形空间的温度低于正常范围。
可能的原因包括:供气不足、燃烧不完全、加热系统故障等。
温度偏低异常会导致气化反应不完全,降低气化产量和质量。
二、解决方法2.1 加强供气调节供气是气化炉正常运行的基础,合理调节供气量可以提高气化炉的稳定性。
通过监测环形空间的温度变化,及时调整供气量,避免温度升高、波动和偏低异常状况的发生。
2.2 优化风量控制风量的调节对于燃烧的均匀性和热平衡至关重要。
通过合理设置风量控制设备,控制环形空间的气流分布,减少温度波动异常的发生。
2.3 定期检查和维护加热系统加热系统是保持环形空间温度稳定的关键设备。
定期检查和维护加热装置,确保其正常工作和高效传热,有效避免温度偏低异常状况的出现。
2.4 强化安全措施针对温度异常可能带来的安全隐患,加强安全措施是至关重要的。
建立完善的安全预警机制,配备温度报警装置和消防设备,及时发现和应对温度异常状况,防范事故发生。
三、总结气化炉环形空间温度异常状况是一个常见但又重要的问题,对气化炉的安全性和效率产生直接影响。
窑预分解系统的问题分析及改进措施

窑预分解系统的问题分析及改进措施摘要:我厂1号RSP窑经过6年多的运转,系统耐火材料呈现出不同程度的磨损、烧坏现象。
SB室下部掉砖,进而壳体烧损;SC室用风不良,导致边壁物料保护层不均衡,局部衬砖磨损严重;斜烟道及鹅颈管侧墙衬砖垮落,由于鹅颈管结构缺陷,经常结皮和堆料;MC室断面物料分布不均,物料稀相区炉壁烧损,直至筒体严重变形;因窑尾缩口处风速低,喷腾能力减弱而塌料;高温级旋风筒分离效率低,导致物料大量返回,内循环增加等。
本文依据热工标定结果,对该预分解系统出现的问题进行分析,并提出改进措施。
1 RSP窑系统工况分析热工标定主要参数对比见表1、表2,窑尾高温区工艺流程见图1。
表1 预热预分解系统温度变化℃表2 RSP炉的分解进程变化注:1997年数据为南京化工大学硅酸地方国营工程研究所的热工标定结果,SC 室出口指斜烟道出进口等同于鹅颈管出口。
图1 窑尾高温区工艺流程1.1 三次风温度及其对SC室工况的影响由表1可见,三次风温度和入炉生料温度分别只有600℃和671℃。
入炉生料温度低主要是由于C4锥体及下料管增开人孔门较多,外漏风量和散热损失增加引起的,通过加强管理,隔热堵漏后完全可以解决;三次风温度目前基本稳定在560~580℃,提高的余地很小。
其原因是:我厂采用单筒冷却机,经过多年的运转,内部装置所遭受的磨损和腐蚀不断加剧,而且增加了砌筑耐火砖的长度,熟料停留时间短(约为30min),出机熟料温度高(~290℃),使热效率本身就不高的单筒冷却机热回收率进一步降低(1997年热工标定结果为56.6%)。
三次风温度是影响分解率和燃尽率的重要因素。
较低的三次风温度导致炉内煤粉着火速度减慢,形成滞后燃烧,特别是SC室内煤粉是在纯助燃空气中燃烧,助燃空气的温度在很大程度上决定了煤粉燃尽率,三次风温度低,即使分解炉多加煤,SC室内温度也不会高,反而会加剧煤粉滞后燃烧。
从表1和表2可以看出,SC室生料出口温度和分解率分别是948℃和43.4%,结合入炉生料表观分解率已达22.6%的实际情况,说明SC室内的分解反应极低,煤粉燃烧状况不理想。
焦炉温度产生波动的原因,提出了进一步稳定炉温的措施

焦炉温度产生波动的原因,提出了进一步稳定炉温的措施2010-04-25 17:57焦炉加热管理包括温度的管理和压力制度的管理。
其任务是按规定的结焦时间、装煤量、装煤水分及加热煤气性状等实际条件,及时测量调整焦炉加热系统各控制点的温度、压力,实现全炉各炭化室在规定时间内各部位均匀成焦, 使焦炉均衡生产并达到稳产、优质、低耗、长寿、高产。
其中焦炉温度的管理贯穿于炼焦生产的始终,它对于降低热耗、提高焦炭质量、延长焦炉寿命有着决定性的意义。
因此加强对炉温的分析,有助于更好地改善操作。
一、炉温产生波动的原因1、换向期间炉温的变化焦炉加热的特点是双联火道、废气循环、焦炉煤气下喷、高炉煤气侧入,每30分钟要改变一次单、双火道的加热方式以保证加热均匀。
焦炉直行温度一般在换向10分钟后测。
由于焦炉的燃烧室较多,在测直行温度时,有的测的早,有的测的晚。
测得早的火道温度下降得少一些,测得晚的火道温度下降得多些,所以测得的温度不能代表火道的真实温度,所测温度换算成换向后20秒的温度,以确定该火道测温点的最高温度。
冷却温度作为一个校正值,其本身受各种复杂因素的影响,如冬夏季节温度变化较大、改变加热煤气种类或结焦时间等情况。
因此应加强测量以减少直行温度换算时的误差。
2、结焦期间炉料状态的变化对炉温的影响直行温度测量中以换算到下降后20秒的温度来消除换向期间温度波动引起的误差,尚不够全面,还应该分析结焦期间炉料状态的变化对炉温的影响。
装入煤在炭化室分层结焦,煤料各层经过干燥、热解、熔融、粘结、固化、收缩等阶段而成焦炭。
在整个结焦时间内,进入燃烧室的热量是保持一定的。
刚装煤时,炭化室墙将大量热传给煤料,使其表面温度急剧下降。
一般从装煤开始后的1~2小时,由1050 C~1100 C降至700 C左右。
因炉墙两侧温差急剧加大,炉墙大量放热,同时提高了火焰和墙面间的温差,使火焰传给炉墙的热量也急剧增加。
以后随着炭化室墙面温度的升高,热量逐渐平稳。
预分解窑烧成温度窑尾温度高低的原因及处理
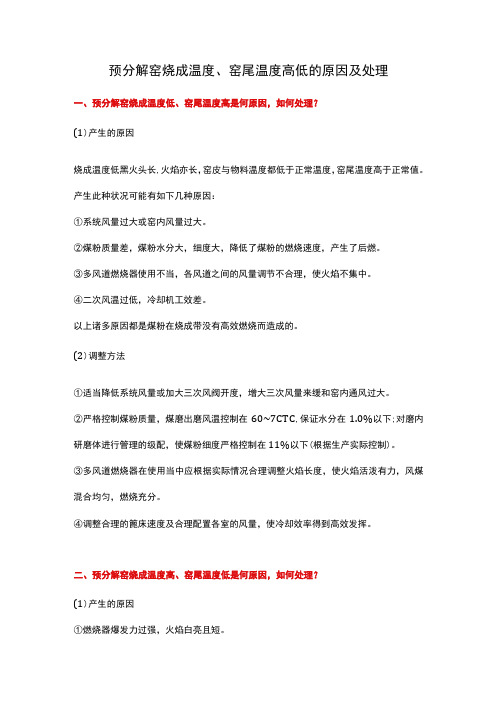
预分解窑烧成温度、窑尾温度高低的原因及处理一、预分解窑烧成温度低、窑尾温度高是何原因,如何处理?(1)产生的原因烧成温度低黑火头长,火焰亦长,窑皮与物料温度都低于正常温度,窑尾温度高于正常值。
产生此种状况可能有如下几种原因:①系统风量过大或窑内风量过大。
②煤粉质量差,煤粉水分大,细度大,降低了煤粉的燃烧速度,产生了后燃。
③多风道燃烧器使用不当,各风道之间的风量调节不合理,使火焰不集中。
④二次风温过低,冷却机工效差。
以上诸多原因都是煤粉在烧成带没有高效燃烧而造成的。
(2)调整方法①适当降低系统风量或加大三次风阀开度,增大三次风量来缓和窑内通风过大。
②严格控制煤粉质量,煤磨出磨风温控制在60~7CTC,保证水分在1.0%以下;对磨内研磨体进行管理的级配,使煤粉细度严格控制在11%以下(根据生产实际控制)。
③多风道燃烧器在使用当中应根据实际情况合理调整火焰长度,使火焰活泼有力,风煤混合均匀,燃烧充分。
④调整合理的篦床速度及合理配置各室的风量,使冷却效率得到高效发挥。
二、预分解窑烧成温度高、窑尾温度低是何原因,如何处理?(1)产生的原因①燃烧器爆发力过强,火焰白亮且短。
②煤粉质量好,灰分小,细度小,水分小。
③系统风量过小或三次风与窑内风量匹配不合理,造成窑内通风过小。
④窑内有结圈或长厚窑皮影响窑内通风,使火焰短,窑尾温下降。
(2)调整方法①合理调节多风道燃烧器各风道间的风量,如火焰温度过高、白亮且短,可适当调节内风与外风的比例,减小内风增大外风,确保火焰形状合理。
②不要过分地追求高质量的煤粉,只要煤粉的控制指标在合理的范围内就可以(细度≤11%,水分≤1.0%,根据生产实际控制),煤粉质量可根据实际情况具体调整。
③可增大系统风量,减小三次风阀开度,增大窑内的通风。
调整合理的系统风量且平衡好三次风与窑内的通风,合理的风量配备是稳定烧成的最基本条件之一。
④窑内有结圈或长厚窑皮且伴有主机电流升高、窑尾有溢料等现象,最直观地反映为窑内通风差,出现此状况应及时处理结圈和长厚窑皮。
分解炉的控制方法

分解炉控制对于窑外分解窑来说,分解炉是其核心部分,它不仅承担了系统中燃料燃烧,气固换热,碳酸盐分解的任务,而且对整个烧成系统的热力分布,热工制度的稳定起着至关重要的作用,虽然现在应用的分解炉型式众多,结构各异,但其特点和具有的功能基本上都是一样的,都属于高温气固多相流反应器,且具有悬浮床的特征。
对于中控窑操作者来说:分解炉温度(包括分解炉本体温度和出口温度)是最重要的检测控制参数之一,因为它不但表征了生料在分解炉内的预分解情况,也就是生料在分解炉中分解率的高低(分解率的高低直接影响着回转窑运转的稳定性和熟料产、质量以及能耗的高低);同时也表征了燃料在分解炉中的燃烧情况。
因此,作为中控窑操作员来说,要想操作好预分解窑,首先必须保证分解炉的热工制度稳定,要想使分解炉的热工制度稳定,就必须搞清楚以下几个问题:(1)燃料在分解炉中的燃烧传热特性及其影响因素;(2)生料在分解炉中的吸热分解速度及其影响因素;(3)气流在分解炉中运动对燃料燃烧放热和生料分解吸热的影响;(4)分解炉温度高低对回转窑煅烧的影响;(5)分解炉温度调节控制的原则与方法;(6)分解炉温度异常情况的原因与处理等。
下面就这几个问题谈一下个人的看法与认识。
不足之处,尚请指正。
一、燃料在分解炉中的燃烧、传热特性及其影响因素1.燃料在分解炉中的燃烧特性在分解炉中,燃料的燃烧传热特性与回转窑内燃料的燃烧传热特性有着本质上的区别。
回转窑内燃料的燃烧是扩散控制的过程,其火焰必须与回转窑内的煅烧制度相适应,即要求有一定的火焰形状、长度和温度。
通常我们所说的火焰形状为“毛笔头状”、“棒槌状”以及不正常时形成的“球形”火焰,“舔料形”火焰等就是这一特征的体现。
而当煤粉颗粒喷入分解炉后,在旋流和喷腾作用的影响下,使得煤粉颗粒浮游于热气流中,经过预热,分解——煤中的挥发分吸收热量放出氮、氢、氧等,燃烧发出光和热,形成一个一个的小火星,无数的煤粉颗粒便形成无数个迅速燃烧的小火星,这些小火星实质上也就是一个个的小火焰,它们在气流的悬浮作用下充满整个分解炉,从而在整个分解炉内都形成燃烧区。
炉底温度两点或多点下降较大表现及处理办法
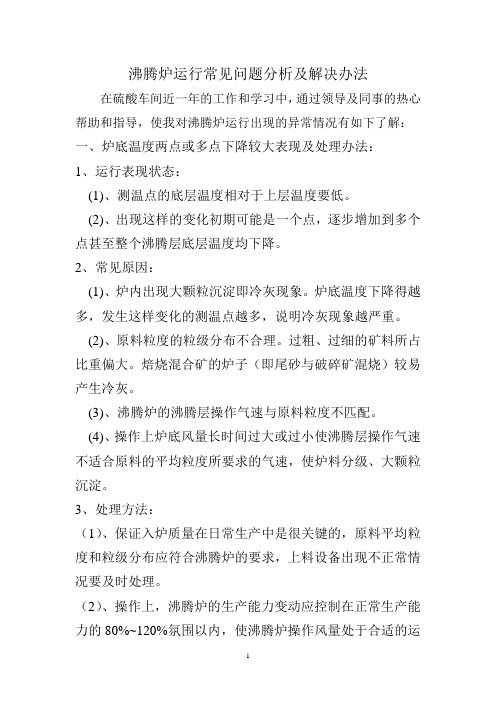
沸腾炉运行常见问题分析及解决办法在硫酸车间近一年的工作和学习中,通过领导及同事的热心帮助和指导,使我对沸腾炉运行出现的异常情况有如下了解:一、炉底温度两点或多点下降较大表现及处理办法:1、运行表现状态:(1)、测温点的底层温度相对于上层温度要低。
(2)、出现这样的变化初期可能是一个点,逐步增加到多个点甚至整个沸腾层底层温度均下降。
2、常见原因:(1)、炉内出现大颗粒沉淀即冷灰现象。
炉底温度下降得越多,发生这样变化的测温点越多,说明冷灰现象越严重。
(2)、原料粒度的粒级分布不合理。
过粗、过细的矿料所占比重偏大。
焙烧混合矿的炉子(即尾砂与破碎矿混烧)较易产生冷灰。
(3)、沸腾炉的沸腾层操作气速与原料粒度不匹配。
(4)、操作上炉底风量长时间过大或过小使沸腾层操作气速不适合原料的平均粒度所要求的气速,使炉料分级、大颗粒沉淀。
3、处理方法:(1)、保证入炉质量在日常生产中是很关键的,原料平均粒度和粒级分布应符合沸腾炉的要求,上料设备出现不正常情况要及时处理。
(2)、操作上,沸腾炉的生产能力变动应控制在正常生产能力的80%~120%氛围以内,使沸腾炉操作风量处于合适的运行范围,从而保证炉料正常的气速。
(3)、出现炉底温度下降的现象后,一种处理方法是先减小排渣量,提高炉底压力,然后加大炉底风量,将沉淀的大颗粒从炉内吹出。
另一种办法是减小风量、提高炉料中的细灰比例,增大排渣量将大粒子带出,从而将冷灰逐步消除。
(4)、沸腾炉操作上要注意控制风量与原料粒度相匹配,操作风速不能太小也不能太大。
(5)、改用细矿,炉底压力维持高一些,把炉温适当地提高些,连续运行2 ~3天一般可将冷灰消除。
(6)、除上述的一些基本方法外,生产中如发现炉温不平衡,可先适当增加炉底风量,使炉内沸腾状况得到改善,如炉温没有得到恢复再进行其它处理。
二、炉底下料口温度或多点温度突然上升后又缓慢下降1、表现状态:(1)、炉内其它炉底测温点温度或中层温度上升后又缓慢下降。
分解炉温度上下倒挂的原因及解决措施
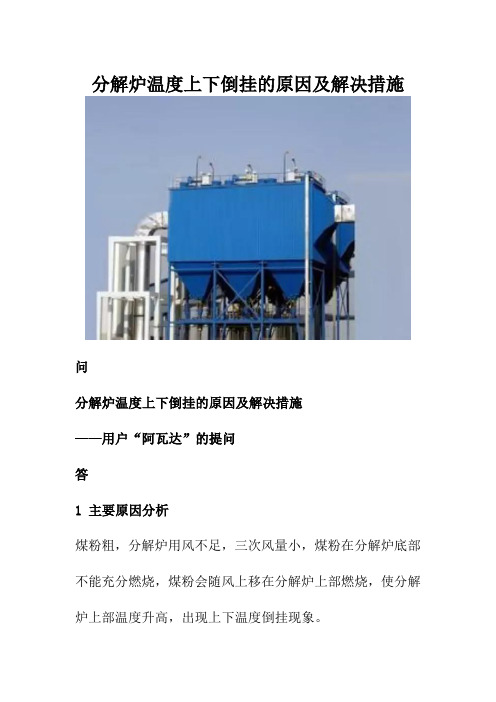
分解炉温度上下倒挂的原因及解决措施
问
分解炉温度上下倒挂的原因及解决措施
——用户“阿瓦达”的提问
答
1 主要原因分析
煤粉粗,分解炉用风不足,三次风量小,煤粉在分解炉底部不能充分燃烧,煤粉会随风上移在分解炉上部燃烧,使分解炉上部温度升高,出现上下温度倒挂现象。
2 如何发现与检测
可在中控室温度显示屏上看出,只要分解炉热电耦不发生故障,显示温度准确,便可准确地进行判断,一般在窑上操作都要随时关注此处温度变化。
3 故障的处理与预防
控制煤粉细度不过粗,在5%以下;三次风的温度要提高,控制在850℃以上;三次风阀的开度不能过小,保持有足够的三次风量,三次风阀开度控制在40%左右,停窑检查三次风进口处结皮积料,并进行清理,检查三次风阀板与四周墙壁的粘结情况,每三个月检查一次,每半年彻底清理一次。
4 故障的影响
分解炉内底部与上部温度出现倒挂现象常有发生,出口温度明显高于低部温度,会造成分解率低,煤在分解炉内燃烧不
充分,且燃烧位置上移,分解炉内高温点也上移,生料在炉内高温区的路径相应缩短,生料的分解受到影响,使五级预热器温度升高,易引起五级锥体产生结皮堵塞现象。
生料入窑分解率和分解炉温度的控制
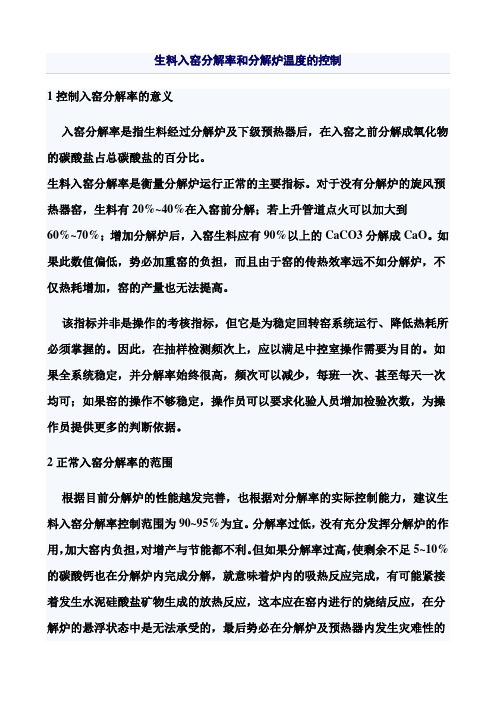
1控制入窑分解率的意义入窑分解率是指生料经过分解炉及下级预热器后,在入窑之前分解成氧化物的碳酸盐占总碳酸盐的百分比。
生料入窑分解率是衡量分解炉运行正常的主要指标。
对于没有分解炉的旋风预热器窑,生料有20%~40%在入窑前分解;若上升管道点火可以加大到60%~70%;增加分解炉后,入窑生料应有90%以上的CaCO3分解成CaO。
如果此数值偏低,势必加重窑的负担,而且由于窑的传热效率远不如分解炉,不仅热耗增加,窑的产量也无法提高。
该指标并非是操作的考核指标,但它是为稳定回转窑系统运行、降低热耗所必须掌握的。
因此,在抽样检测频次上,应以满足中控室操作需要为目的。
如果全系统稳定,并分解率始终很高,频次可以减少,每班一次、甚至每天一次均可;如果窑的操作不够稳定,操作员可以要求化验人员增加检验次数,为操作员提供更多的判断依据。
2正常入窑分解率的范围根据目前分解炉的性能越发完善,也根据对分解率的实际控制能力,建议生料入窑分解率控制范围为90~95%为宜。
分解率过低,没有充分发挥分解炉的作用,加大窑内负担,对增产与节能都不利。
但如果分解率过高,使剩余不足5~10%的碳酸钙也在分解炉内完成分解,就意味着炉内的吸热反应完成,有可能紧接着发生水泥硅酸盐矿物生成的放热反应,这本应在窑内进行的烧结反应,在分解炉的悬浮状态中是无法承受的,最后势必在分解炉及预热器内发生灾难性的烧结堵塞。
应该说,正是这个5%尚未完成分解的生料阻止了完成分解后的温度剧升,那种想象进一步提高分解率,便可以挖掘提高窑产量的潜力,将是很危险的。
3控制分解炉温度的意义⑴可确保分解率高又不烧结的必须。
分解炉温度达到一定数值是实现生料入窑分解率达到90% 以上的最基本条件。
因此,当该温度值偏低时,就应该设法提高它;但是如果此温度过高,则更要警惕炉内出现烧结的可能。
⑵判断煤料混合均匀及煤粉燃烧状态的依据。
通过分解炉温度与上下两级预热器温度的比较,还可以判断分解炉燃烧是否完全。
解决RSP预分解系统温度倒挂的方法

【doc】解决RSP预分解系统温度倒挂的方法解决RSP预分解系统温度倒挂的方法2005.No.8刚T?27?解决RSP预分解系统温度倒挂的方法周本智(新光建材有限责任公司,新疆乌鲁木齐830049)中图分类号:TQ172.622.26文献标识码:B文章编号:1002-9877(2005)08-0027-02我厂l000t/d熟料生产线主要由RSP型分解炉,混合室及四级预热器组成.在生产调试初期,C.,C,C,的温度均超过规定值,C温度比分解炉温度高,出现温度倒挂现象.为确保高温风机及袋除尘器不被高温烟气损坏,只好减煤限产,达标达产工作受到很大的影响.l产生温度倒挂的原因窑尾输煤罗茨风机风量:25.4m/min,风压:39.4kPa,输送煤粉管道的直径:125mm,喷煤嘴内径:170mm,出口风速:18.7m/s,喷煤嘴加有6个旋流叶片,叶片与管道轴间夹角为3O.,旋流叶片的旋向与三次风进分解炉的切向风方向相反.由于煤粉出口风速快,三次风又有很强的卷带作用,部分煤粉在分解炉还没有燃烧的情况下,就被快速带入混合室及C.操作不慎时,C的温度超高,在其下锥体出现结瘤,严重的时候,结焦成板.只有止料,停窑降温后,才能进去用钢钎打焦.2解决方法及效果1)降低分解炉喷煤嘴出口风速减小罗茨风机的电动机皮带轮直径,将风机风量降为22m/min,喷煤嘴出口风速降为16.1m/s,降低风速后,各级预热器温度见表1.表l降低风速后各级预热器温度?时间分解炉混合室CC3C2CI改造前8438978657636l8470改造后9lO降低风速后,预热器温度倒挂的情况有所好转,但还没有彻底解决问题,C下料管的生料分解率仍波动很大.2)改变喷煤嘴旋流叶片的角度将喷煤嘴旋流叶片的角度由3O.改为36.,调整后的预热器各级温度见表2.表2改变喷煤嘴旋流叶片角度后各级预热器温度? 时间分解炉混合室C4C3C2Cl改造前9l4改造后97895l88775363l414改后,分解炉的温度有所上升,料也可以相应的多加.但煤粉的灰分,水分发生波动变差时,分解炉的温度上不去,C的温度超高,在下料管的生料中,可以看见火星.操作不当,也会出现结瘤.3)在喷煤嘴出口增设倒锥体形火焰稳定器喷煤嘴的旋流叶片高3ram,距出口5mm,我们制作了一个直径120mm,高200mm的圆锥体,固定在喷煤嘴的里面用作火焰稳定器,锥体端面同喷煤嘴平齐.尖部朝管内,改造后的喷煤嘴结构见图1.锥体改遣前改遣后图1喷煤嘴结构示意加上倒锥体后,煤粉风的出口风速由16.1m/s提高到32.2m/s.由于出口风速的大幅度提高,煤粉风卷带三次风的能力增强.改前煤粉燃烧集中在分解炉的中部,并随三次风快速进入混合室.改后,煤粉燃烧被强制分成环带,更靠近由三次风卷带生料形成的低浓度料区,吸热反应明显.见图2.?28?.扣T窑头煤秤跑煤时的中控操作方法孙琪勇,于加滨(浩良河水泥有限责任公司,黑龙江伊春153103)中图分类号:TQ172.622.26;TQ172.625文献标识码:B 我公司2000t/t熟料生产线窑头及分解炉喂煤系统采用北京燕山粉研公司生产的粉研秤.生产过程中曾经发生窑头煤秤跑煤,若处理不及时,将造成烟室结皮,预热器堵塞.如果窑操作不当,熟料中fCaO大幅度升高,甚至跑生料.1原因分析粉研秤均压管(收尘管道)压力波动,煤粉仓内煤粉量少,锁风阀内毛毡磨损等原因都能造成跑煤.跑煤时,罗茨风机喂煤压力升高,窑尾温度及预热器各级出口温度迅速升高,C出口O浓度减小,CO浓度增加,窑尾电除尘器高压高报跳停.此时窑前煅烧温度降低,物料涌入烧成带使煅烧进一步恶化,再加上窑前不能加煤,稍稍拖延就造成熟料中fCaO不合格. 2采取措施1)及时停窑头煤秤,不减生料喂料量,适当减少分解炉喂煤量(以防预热器长时间高温),但要保证入窑物料分解率,减轻窑负荷.待预热器温度及窑尾温度降到正常时,再减料至100t/h,分解炉再相应减煤,窑速降低至1.2r/min.同时调节窑尾排风机转速2o05.No.8文章编号:1002—9877(2005)08_oO28-01或风门开度,相应调节冷却机风量和篦速.通知现场岗位工敲打粉研秤收尘管道(跑煤时正压),将喷煤管向窑内伸入20cm,稍开大内风.2)待系统温度和喂煤压力降下来后,启动窑头煤秤和窑尾电除尘器,喂煤1.0t/h,慢慢加煤,加煤幅度0.5t/次.加煤至3.0t/h后,加煤幅度减至0.2t/次,直至正常时的4.0t/h(100t/h生料窑头用煤量),此过程应在较短时间内完成,以保证窑内熟料的煅烧.然后再以0.1t/次向窑头多加煤至4.5t/h(每次加煤以下煤量稳定为原则),并加大系统排风.待物料已过烧成带时,再减煤至正常(4.0t/h).多加煤是为了提高窑前温度,以保证窑内物料的烧成.物料通过烧成带时把煤退回,是为了保护窑皮.这样虽然短时间内熟料烧成热耗会有所增加,但窑趋于正常状态时间较短.待窑电流及烧成温度上升或呈上升趋势时,提速加料. 3效果杜绝了跑生料事故的发生,fCaO合格率得到控制.同时由于是不止料停窑,提高了设备运转率. (编辑王承敏)料雾区料雾区的燃烧范围图2分解炉剖面示意形成环带后,煤粉在更大的空间中与三次风接触,燃烧更加充分.使分解炉温度比C温度高出250,3o0?,在生料进入C时,生料的分解反应基本完成,C下料管的生料分解率始终保持在90%左右. 生料量也可以增加10%,l5%,窑的日产量可达1l00t以上.煤粉的水分,灰分较高时,分解炉的温度降低30,50?,但C温度始终能稳定地控制在(860+30)以内,再也没有出现温度倒挂的现象,见表3.表3增设倒锥体形火焰稳定器后各级预热器温度? 时间对比分解炉混合室CC3C2C1改造前39l改造后ll3590o87674l6l238l4)其他配套措施提高三次风的温度;尽量稳定煤粉的细度和水分;在C,下料管翻板阀的翻板上开月牙孔,保证C, 下料管来料连续,稳定;在分解炉的三次风入口处, 增设散料装置,使生料在三次风的卷带下,充分均匀地形成料幕.(编辑王承敏)。
90KW井式炉上下区温度整定方法
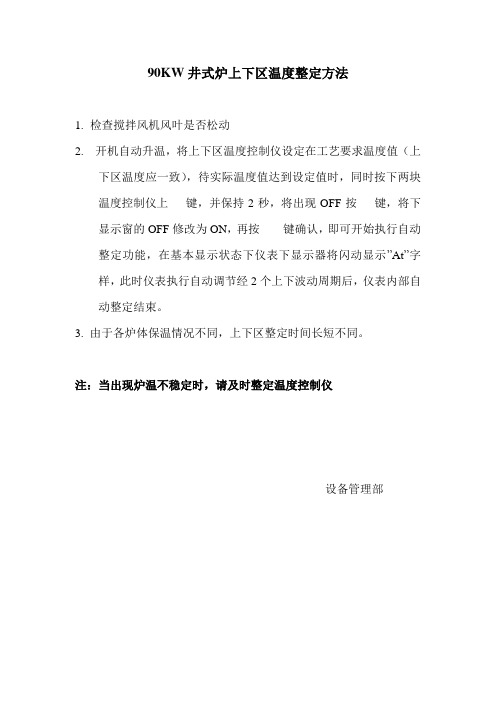
90KW井式炉上下区温度整定方法
1.检查搅拌风机风叶是否松动
2. 开机自动升温,将上下区温度控制仪设定在工艺要求温度值(上
下区温度应一致),待实际温度值达到设定值时,同时按下两块温度控制仪上键,并保持2秒,将出现OFF按键,将下显示窗的OFF修改为ON,再按键确认,即可开始执行自动整定功能,在基本显示状态下仪表下显示器将闪动显示”At”字样,此时仪表执行自动调节经2个上下波动周期后,仪表内部自动整定结束。
3. 由于各炉体保温情况不同,上下区整定时间长短不同。
注:当出现炉温不稳定时,请及时整定温度控制仪
设备管理部。
焙烧窑温度不稳定,忽高忽低怎么处理?
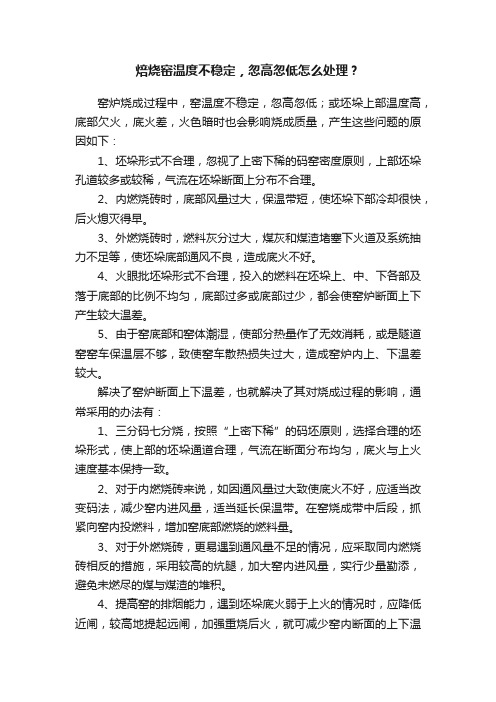
焙烧窑温度不稳定,忽高忽低怎么处理?窑炉烧成过程中,窑温度不稳定,忽高忽低;或坯垛上部温度高,底部欠火,底火差,火色暗时也会影响烧成质量,产生这些问题的原因如下:1、坯垛形式不合理,忽视了上密下稀的码窑密度原则,上部坯垛孔道较多或较稀,气流在坯垛断面上分布不合理。
2、内燃烧砖时,底部风量过大,保温带短,使坯垛下部冷却很快,后火熄灭得早。
3、外燃烧砖时,燃料灰分过大,煤灰和煤渣堵塞下火道及系统抽力不足等,使坯垛底部通风不良,造成底火不好。
4、火眼批坯垛形式不合理,投入的燃料在坯垛上、中、下各部及落于底部的比例不均匀,底部过多或底部过少,都会使窑炉断面上下产生较大温差。
5、由于窑底部和窑体潮湿,使部分热量作了无效消耗,或是隧道窑窑车保温层不够,致使窑车散热损失过大,造成窑炉内上、下温差较大。
解决了窑炉断面上下温差,也就解决了其对烧成过程的影响,通常采用的办法有:1、三分码七分烧,按照“上密下稀”的码坯原则,选择合理的坯垛形式,使上部的坯垛通道合理,气流在断面分布均匀,底火与上火速度基本保持一致。
2、对于内燃烧砖来说,如因通风量过大致使底火不好,应适当改变码法,减少窑内进风量,适当延长保温带。
在窑烧成带中后段,抓紧向窑内投燃料,增加窑底部燃烧的燃料量。
3、对于外燃烧砖,更易遇到通风量不足的情况,应采取同内燃烧砖相反的措施,采用较高的炕腿,加大窑内进风量,实行少量勤添,避免未燃尽的煤与煤渣的堆积。
4、提高窑的排烟能力,遇到坯垛底火弱于上火的情况时,应降低近闸,较高地提起远闸,加强重烧后火,就可减少窑内断面的上下温差。
温度制度是为焙烧制品的产量和质量要求服务的,为了保证隧道窑焙烧的正常运行,烧火工必须做到勤观察、勤分析某些变化因素,以便做到及时进行调控。
防止炉温波动,坚持稳定操作的措施
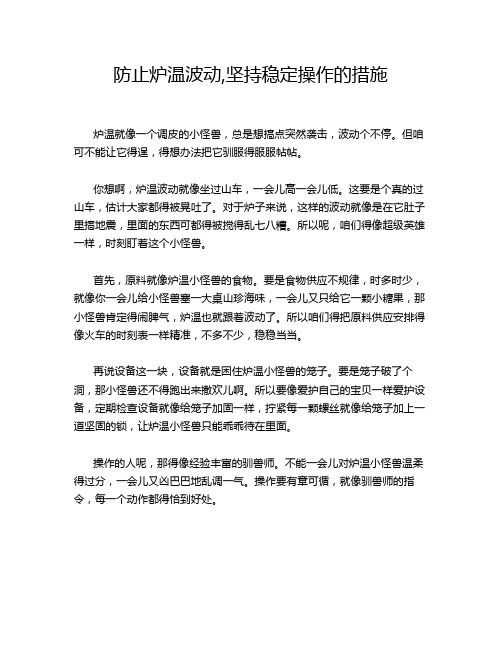
防止炉温波动,坚持稳定操作的措施炉温就像一个调皮的小怪兽,总是想搞点突然袭击,波动个不停。
但咱可不能让它得逞,得想办法把它驯服得服服帖帖。
你想啊,炉温波动就像坐过山车,一会儿高一会儿低。
这要是个真的过山车,估计大家都得被晃吐了。
对于炉子来说,这样的波动就像是在它肚子里搞地震,里面的东西可都得被搅得乱七八糟。
所以呢,咱们得像超级英雄一样,时刻盯着这个小怪兽。
首先,原料就像炉温小怪兽的食物。
要是食物供应不规律,时多时少,就像你一会儿给小怪兽塞一大桌山珍海味,一会儿又只给它一颗小糖果,那小怪兽肯定得闹脾气,炉温也就跟着波动了。
所以咱们得把原料供应安排得像火车的时刻表一样精准,不多不少,稳稳当当。
再说设备这一块,设备就是困住炉温小怪兽的笼子。
要是笼子破了个洞,那小怪兽还不得跑出来撒欢儿啊。
所以要像爱护自己的宝贝一样爱护设备,定期检查设备就像给笼子加固一样,拧紧每一颗螺丝就像给笼子加上一道坚固的锁,让炉温小怪兽只能乖乖待在里面。
操作的人呢,那得像经验丰富的驯兽师。
不能一会儿对炉温小怪兽温柔得过分,一会儿又凶巴巴地乱调一气。
操作要有章可循,就像驯兽师的指令,每一个动作都得恰到好处。
而且啊,周围的环境也会影响这个小怪兽。
环境就像小怪兽的心情调节剂。
要是周围环境忽冷忽热,就像一会儿给小怪兽讲个超级恐怖的鬼故事,一会儿又给它放超级欢快的音乐,那小怪兽能不抓狂吗?所以要保持环境的稳定,让炉温小怪兽在一个舒适的氛围里。
监控系统也很重要,这就像小怪兽身上的追踪器。
我们得时刻通过这个追踪器观察小怪兽的一举一动,一旦发现它有什么异常的波动迹象,就像发现小怪兽要搞破坏了,立马采取措施。
要是大家都齐心协力,把这些事情都做好了,炉温小怪兽就只能听话了。
它会像一只温顺的小猫咪一样,老老实实地待在它该待的地方,炉温也就稳定得像平静的湖水,不再兴风作浪啦。
这样咱们的生产就像开了挂一样顺利,产品质量也像火箭一样蹭蹭往上升呢。
裂解炉热效率降低原因及处理措施
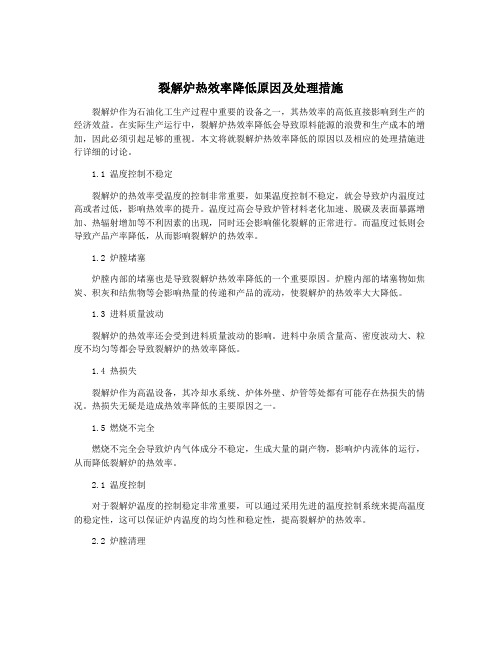
裂解炉热效率降低原因及处理措施裂解炉作为石油化工生产过程中重要的设备之一,其热效率的高低直接影响到生产的经济效益。
在实际生产运行中,裂解炉热效率降低会导致原料能源的浪费和生产成本的增加,因此必须引起足够的重视。
本文将就裂解炉热效率降低的原因以及相应的处理措施进行详细的讨论。
1.1 温度控制不稳定裂解炉的热效率受温度的控制非常重要,如果温度控制不稳定,就会导致炉内温度过高或者过低,影响热效率的提升。
温度过高会导致炉管材料老化加速、脱碳及表面暴露增加、热辐射增加等不利因素的出现,同时还会影响催化裂解的正常进行。
而温度过低则会导致产品产率降低,从而影响裂解炉的热效率。
1.2 炉膛堵塞炉膛内部的堵塞也是导致裂解炉热效率降低的一个重要原因。
炉膛内部的堵塞物如焦炭、积灰和结焦物等会影响热量的传递和产品的流动,使裂解炉的热效率大大降低。
1.3 进料质量波动裂解炉的热效率还会受到进料质量波动的影响。
进料中杂质含量高、密度波动大、粒度不均匀等都会导致裂解炉的热效率降低。
1.4 热损失裂解炉作为高温设备,其冷却水系统、炉体外壁、炉管等处都有可能存在热损失的情况。
热损失无疑是造成热效率降低的主要原因之一。
1.5 燃烧不完全燃烧不完全会导致炉内气体成分不稳定,生成大量的副产物,影响炉内流体的运行,从而降低裂解炉的热效率。
2.1 温度控制对于裂解炉温度的控制稳定非常重要,可以通过采用先进的温度控制系统来提高温度的稳定性,这可以保证炉内温度的均匀性和稳定性,提高裂解炉的热效率。
2.2 炉膛清理保持炉膛内部的清洁对于提高裂解炉的热效率至关重要,可以采取定期清理和清扫的措施,及时清除煤渣和结焦物,防止炉膛内积灰和焦炭的堆积,保证裂解炉热效率的提升。
2.3 进料预处理对于进料的预处理也是提高裂解炉热效率的一种有效措施。
在进料前进行粒度的筛分、密度的控制等预处理工作,可以有效地降低进料质量波动对热效率的影响。
2.4 热损失控制对炉体外壁、炉管等处的热损失进行有效的控制,采用绝热材料对炉体进行包裹,修复炉管的老化裂缝等措施可以有效地减少热损失,从而提高裂解炉的热效率。
NMFC型预分解窑系统温度倒挂原因
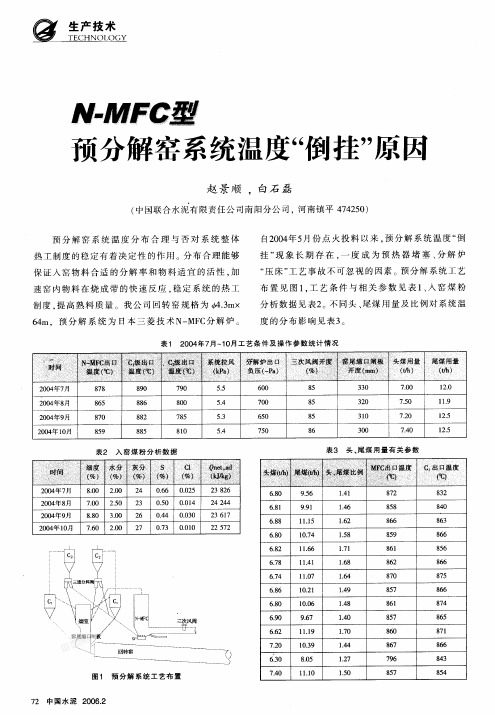
98 . 1. 06 1. 05 1. 02
1. 08
30 3
30 2
30 3
30 3
80 7
88 5
43 . 49 .
50 .
8 0
8 0 8 0
82 6 85 7
30 3 30 5
82 6
95 .
表5 入 窑煤 粉 分 析 数据
时间
20 年1月 04 2
20 年 1 05 月
14 .0
1 0 . 7 1 . 科
12 .7
80 .5
1 .0 11
76 9
87 5
图1 预分解 系统工艺布置 7 中国水泥 2 0 . 2 0 62
74 .0
1 0 . 5
表4 0 4 2 2 0 年5 2 0 年, 月一 0 5 月工艺条件及操作参数统计情况
时间
N MF 出 口 - C
C 温度 , 出口
80 .0 20 .0
25 .0 2 4
06 .6
05 .0 04 .4
00 5 .2 00 4 .1 00 0 .3 00 0 .1
2 86 3 2 2 24 4 4
68 .0
95 .6
1 1 . 4
14 .6
82 7
88 5
82 3
80 4 83 6
70 .0 88 .0 76 .0
2 3 2 6
6m,预分解系统为 日本三菱技术N M C 4 - F 分解炉。
表1 0 4 月一 0 2 0 年7 1 月工艺条件及操作参数统计情况
2 0 年7 04 月 2 0 年8 04 月
2 0 年9 04 月
1t N h fI ( 9) % - l C瓣 9 R 3I fA 1 ' 姗 C (砰 {)9i ( m I l A Nf m } -) z I iQ & 3 a k , M a } P F C ( 4 ( I t C ' , "- Ia C1 Q) )F H i f i ' a l
分解炉温度的操作与控制

分解炉温度的操作与控制赵晓东;乌洪杰【期刊名称】《水泥工程》【年(卷),期】2014(000)003【总页数】2页(P42-43)【作者】赵晓东;乌洪杰【作者单位】重庆电子工程职业学院建筑与材料学院,重庆401331;重庆电子工程职业学院财经学院,重庆401331【正文语种】中文【中图分类】TQ172.620 前言分解炉温度控制的好坏,将直接影响入窑生料分解率的大小,继而将影响预分解窑的产量、质量及能耗等多项指标,因此研究探讨分解炉温度的操作与控制具有现实意义。
笔者根据自己在水泥企业20多年的生产实践经验,就分解炉温度的操作控制作一总结,供同行参考。
1 分解炉的点火操作控制分解炉具备点火的基本条件有两个:炉内有足够氧气含量;炉内温度达到煤粉燃烧的温度。
(1)对于在线型分解炉,只要窑尾废气温度≥800℃,在没有投料的情况下,向分解炉内喷人适当的煤粉,煤粉就会燃烧,完成分解炉的点火操作。
(2)对于离线型分解炉,其点火操作控制方法取决于炉型。
比如:RSP型分解炉,只要将分解炉通往上一级预热器的锁风阀吊起,即可使来自窑尾的高温废气部分短路进入分解炉内而使炉内温度升高,达到煤粉燃烧的温度,就具备了分解炉的点火条件;MFC型分解炉,由于其位置高度低于窑尾高度,要先进行投料操作,靠经过预热后的生料粉将炉内温度提高到煤粉燃烧的温度,然后再进行分解炉的点火操作,且一定要注意控制投料量与炉底的风压、风量,避免发生压炉现象而导致点火失败。
2 入窑生料分解率的控制入窑生料的分解率是衡量分解炉运行正常与否的主要指标,生产控制中,一般控制入窑生料分解率为90%~95%。
如果分解率过低,就没有充分发挥分解炉的分解功效,影响窑的产量、质量及热耗等指标;如果分解率过高,就意味着炉内的最高温度可以达到1200℃,极有可能在炉内发生形成矿物的固相反应,从而在分解炉内、出口部位及下级预热器下料口等部位产生灾难性的烧结结皮及堵塞,这是预分解窑生产最忌讳发生的!所以不能一味追求入窑生料的分解率而盲目地提高分解炉的温度。
分解炉温度和负压异常原因及处理

一、RSP分解炉温度异常是何原因,如何处理?(1)分解炉中部温度偏高炉中部温度偏高往往与煤粉质量、三次风温关系密切,水分小、细度细的煤粉入炉后,在温度较高的三次风中迅速燃烧,使炉中温度高于正常值。
三次风温为800°C左右时,若三次风阀开度过大,此时高速喷出的煤粉与高温纯净的助燃空气相遇,产生强烈的湍流,由于气体旋转进入的结果,在分解炉中部形成低于周围介质的负压区,轴向压力差使周围介质向煤粉喷嘴的根部回流,加热煤粉与空气的混合物,使煤粉的燃烧状态恰如一个多风道喷煤管所造成的煤粉高效燃烧,点火早,致使炉中温度偏高。
据资料介绍,每当三次风温升高70℃,燃烧速率会提高1倍。
可见温度对加速煤粉燃烧的重要作用。
喂料量过小,炉中温度快速升高且分解炉出口温度也随之快速升高,此时应快速减煤,并增加喂料量,不然就会因系统超温而使预热器堵塞,随着料量的增加,应逐渐增加喂煤量使温度正常,在此变化过程中操作人员一定要精心操作,稳定好系统的热工制度。
喂煤量过大,此时伴有分解炉出口温度升高,应及时减煤,稳定系统温度。
(2)分解炉中部、出口温度高当分解炉中部及出口温度过高时,应适当减小喂煤量,如温度还是过高,且分解炉中部及出口温度仍有上升趋势,可判断为预热器堵塞,应及时停煤停料处理。
适当减小喂煤量后温度趋于正常,但随后温度又上升,应开启清堵装置。
系统有塌料产生且喂煤量较正常时有所减小,锥体负压减小,此时可判断为系统堵塞,应停料处理。
系统喂煤不稳定,也是导致分解炉中部及出口温度高的原因之一。
应加强操作人员的责任心,精心调整,并且尽快改善喂煤的不稳定。
系统断料或喂量过小,应及时喂料或增大喂料量,此过程中应及时减煤,以防预热器超温堵塞。
由于喂料系统的不稳定,产生此现象,首先要尽快地处理好喂料的不稳定,操作一定要精心,如喂料量波动过大极不稳定应停窑处理。
(3)分解炉出口温度高、入窑物料温度高煤粉质量是导致分解炉出口温度、入窑物料温度高的重要原因之一。
分解炉温度控制的几个要点
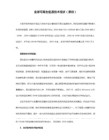
为何对于某特定的预分解窑其燃料用量比例存在一个最佳范围,高于或低于此最佳范围热耗会增加?尽管对于不同的预分解窑相应的最佳范围是不同的,但都应有类似的关联。
当分解炉喂煤量比例增大,即窑头喂煤减少。从表中可知,尽管窑列废气温度A50T1有所降低,但炉列废气温度B50T1都明显增高,炉列的废气量比窑列的废气量大,即总的废气带走的热损失是增加的。另外,分解炉加过多的煤,使废气中CO含量增加。反之,当分解炉喂煤量比例过低,同样也会使热耗增加。窑头烧过多的煤,窑列废气温度A50T1明显上升,废气中CO含量亦增加,导致热耗增加。而且这样做还会影响回转窑耐火材料的寿命,影响安全运转的时间。
ቤተ መጻሕፍቲ ባይዱ
分解炉温度控制的几个问题
分解炉有多种型式,其结构性能虽有差异,但要起的主要作用却是相同的:要使燃料燃烧的放热过程与生料碳酸盐分解的吸热过程在其中以悬浮态或流化态下极其迅速地进行,使入窑生料碳酸盐分解率提高,从而减轻窑的热负荷,提高窑的运转周期,提高产质量。而分解炉的温度控制对整个预分解窑系统的热力分布,热工制度的稳定至关重要。为此,本文对分解炉温度控制的有关几个问题进行讨论。
适当提高及稳定三次风温,亦即提高及稳定了二次风温,对分解炉及窑头的煤粉燃烧有着十分重要的影响。在熟料温度、结粒情况及冷却用风量变化不大的情况,稳定一定的篦冷机篦底压力,意味着可保证篦床上的熟料层厚度一定,从而可得到稳定的二、三次风温,为良好与稳定的燃烧创造条件。
TFD分解炉出现温度倒挂的原因及解决办法
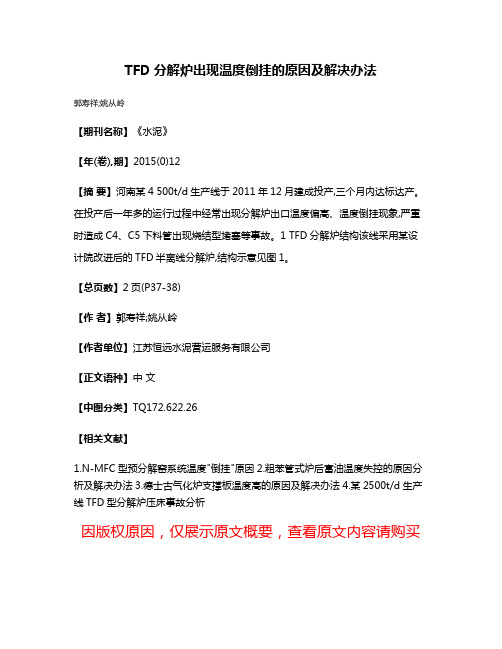
TFD分解炉出现温度倒挂的原因及解决办法
郭寿祥;姚从岭
【期刊名称】《水泥》
【年(卷),期】2015(0)12
【摘要】河南某4 500t/d生产线于2011年12月建成投产,三个月内达标达产。
在投产后一年多的运行过程中经常出现分解炉出口温度偏高、温度倒挂现象,严重时造成C4、C5下料管出现烧结型堵塞等事故。
1 TFD分解炉结构该线采用某设计院改进后的TFD半离线分解炉,结构示意见图1。
【总页数】2页(P37-38)
【作者】郭寿祥;姚从岭
【作者单位】江苏恒远水泥营运服务有限公司
【正文语种】中文
【中图分类】TQ172.622.26
【相关文献】
1.N-MFC型预分解窑系统温度"倒挂"原因
2.粗苯管式炉后富油温度失控的原因分析及解决办法
3.德士古气化炉支撑板温度高的原因及解决办法
4.某2500t/d生产线TFD型分解炉压床事故分析
因版权原因,仅展示原文概要,查看原文内容请购买。
- 1、下载文档前请自行甄别文档内容的完整性,平台不提供额外的编辑、内容补充、找答案等附加服务。
- 2、"仅部分预览"的文档,不可在线预览部分如存在完整性等问题,可反馈申请退款(可完整预览的文档不适用该条件!)。
- 3、如文档侵犯您的权益,请联系客服反馈,我们会尽快为您处理(人工客服工作时间:9:00-18:30)。
分解炉温度上下倒挂的原因及解决措施
问
分解炉温度上下倒挂的原因及解决措施
——用户“阿瓦达”的提问
答
1 主要原因分析
煤粉粗,分解炉用风不足,三次风量小,煤粉在分解炉底部不能充分燃烧,煤粉会随风上移在分解炉上部燃烧,使分解炉上部温度升高,出现上下温度倒挂现象。
2 如何发现与检测
可在中控室温度显示屏上看出,只要分解炉热电耦不发生故障,显示温度准确,便可准确地进行判断,一般在窑上操作都要随时关注此处温度变化。
3 故障的处理与预防
控制煤粉细度不过粗,在5%以下;三次风的温度要提高,控制在850℃以上;三次风阀的开度不能过小,保持有足够的三次风量,三次风阀开度控制在40%左右,停窑检查三次风进口处结皮积料,并进行清理,检查三次风阀板与四周墙壁的粘结情况,每三个月检查一次,每半年彻底清理一次。
4 故障的影响
分解炉内底部与上部温度出现倒挂现象常有发生,出口温度明显高于低部温度,会造成分解率低,煤在分解炉内燃烧不
充分,且燃烧位置上移,分解炉内高温点也上移,生料在炉内高温区的路径相应缩短,生料的分解受到影响,使五级预热器温度升高,易引起五级锥体产生结皮堵塞现象。