精益现场管理实施推动计划
精益管理工作实施方案

精益管理工作实施方案推进精益管理工作实施方案一、项目概况为进一步推进“精益管理”和“卓越绩效评价”工作,公司决定在逐步建立实施企业标准化体系的基础上,系统导入“精益管理”和GB/T-2012《卓越绩效评价准则》。
本方案规定了公司实施精益管理的指导思想、工作目标、进度、步骤、方法和要求等。
精益管理是由日本的XXX生产方式发展而来,它最早于20世纪90年代由XXX数位国际汽车计划组织的专家提出。
精益管理在公司具体体现为精益卷烟营销、精益烟叶管理、精益物流运营、精益执法监管、精益基础保证等方面,从生产、经营、管理等多方面降低所需成本,为顾客提供更高效、优质的服务。
二、指导思想公司精益管理的贯彻实施,从流程优化、管理提升和精益课题三方面入手,由简入繁、先易后难,步步为营、层层推进。
精益导入期:通过多层次的、有针对性的培训,灌输精益思想、研究精益工具。
在充分调研的基础上构建企业合理的精益管理框架结构,并进一步完善标准、提升管理。
精益成长期:对业务流程进行全面分析,实施流程的优化。
在主要业务板块内选择精益课题进行试点,力争实效。
培养企业内部精益专家。
精益成熟期:在试点的基础上全面实施各业务板块的精益化管理,进行全方位的精益与优化。
总结、提炼成果,将精益思想融入日常工作之中,不断改善,尽善尽美。
通过项目的实施,让精益的车轮与公司的发展同步,最终实现企业管理上水平、企业效益快增长、员工能力再提高、工作压力渐减小的美好愿景。
三、工作依据本方案依据XXX(公司)推进企业精益管理工作实施方案和XXX转发《XXX关于2014年度烟草行业标准化重点工作通知》的通知(川烟科〔2014〕1号)。
公司的总体目标是以“1157”精益管理为基础,实现成本的降低和效益的提升。
公司将通过流程优化这一主线,提升管理水平,实施“精益卷烟营销、精益烟叶管理、精益物流运营、精益执法监管和精益基础保障”五个板块的精益转型,消除七大浪费,优化资源配置,提高效率和效益,促进企业管理水平的提升。
关于开展精益生产管理行动计划
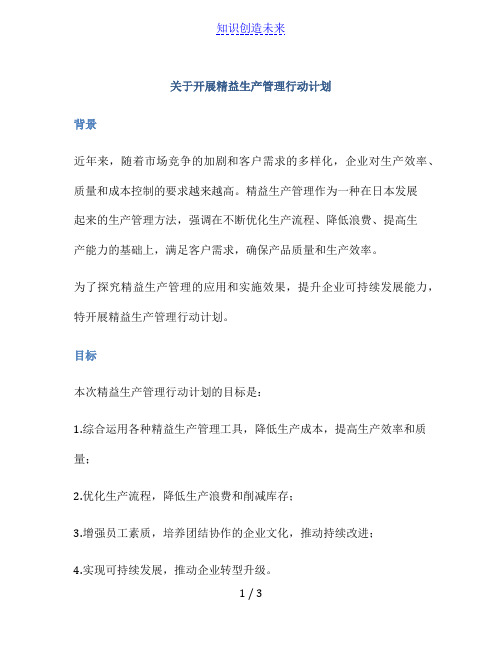
关于开展精益生产管理行动计划背景近年来,随着市场竞争的加剧和客户需求的多样化,企业对生产效率、质量和成本控制的要求越来越高。
精益生产管理作为一种在日本发展起来的生产管理方法,强调在不断优化生产流程、降低浪费、提高生产能力的基础上,满足客户需求,确保产品质量和生产效率。
为了探究精益生产管理的应用和实施效果,提升企业可持续发展能力,特开展精益生产管理行动计划。
目标本次精益生产管理行动计划的目标是:1.综合运用各种精益生产管理工具,降低生产成本,提高生产效率和质量;2.优化生产流程,降低生产浪费和削减库存;3.增强员工素质,培养团结协作的企业文化,推动持续改进;4.实现可持续发展,推动企业转型升级。
实施方案1.制定精益生产管理行动计划,明确目标和任务分工,落实责任;2.开展精益生产管理工具培训,包括价值流图、流程分析、标准化作业等方面。
同时组建精益生产管理小组,定期开展现场改善活动,推动持续改进;3.优化生产流程,减少生产浪费,采用KANBAN系统控制库存,通过滚动周期生产和拉动生产等方式适应市场需求;4.增强员工素质,培养团结协作的企业文化,促进员工自主质量控制和持续改进;5.采用质量管理工具,如Pareto图、故障模式与影响分析、程序执行表等,全面落实检验抽样检查、过程控制和品质管理等质量保证措施。
预期效果通过本次精益生产管理行动计划的实施,预期达到以下效果:1.降低生产成本、提高生产效率和质量,提升企业核心竞争力;2.减少生产浪费,降低库存、杜绝质量问题,改善企业形象和口碑;3.增强员工素质,提高员工满意度和企业文化建设;4.推动持续改进,实现精益生产管理模式的长期应用;5.促进企业可持续发展,实现企业转型升级。
结束语开展精益生产管理行动计划是促进企业现代化管理和可持续发展的有效手段。
希望企业能够充分认识到其重要性,根据自身实际情况制定科学实用的实施方案,全员参与、持续改进,提高企业竞争力和社会影响力。
煤矿精益管理工作计划

一、前言为提高煤矿生产效率,降低生产成本,确保安全生产,根据我国煤矿行业现状和发展趋势,结合我矿实际情况,特制定本精益管理工作计划。
二、工作目标1. 提高生产效率,降低生产成本,实现煤矿经济效益的最大化。
2. 确保安全生产,降低事故发生率,保障职工生命财产安全。
3. 优化生产流程,提高设备利用率,降低设备故障率。
4. 培养一支高素质的职工队伍,提高整体管理水平。
三、工作内容1. 5S现场管理(1)实施5S管理,对生产现场进行整理、整顿、清扫、清洁、素养,优化生产环境,提高工作效率。
(2)建立健全5S管理制度,定期开展5S检查,确保5S管理落到实处。
2. 设备管理(1)加强设备维护保养,定期对设备进行检查、维修,提高设备利用率。
(2)推广应用新技术、新工艺,提高设备自动化水平。
3. 生产流程优化(1)对生产流程进行梳理,查找瓶颈环节,优化生产流程。
(2)加强生产调度,提高生产计划的执行力。
4. 安全管理(1)加强安全教育培训,提高职工安全意识。
(2)严格执行安全操作规程,加强现场安全管理。
(3)定期开展安全检查,及时发现和消除安全隐患。
5. 人才培养(1)加强职工技能培训,提高职工业务水平。
(2)选拔优秀人才,培养一批具有创新精神和实践能力的优秀人才。
四、实施步骤1. 准备阶段(2023年1月-2月)(1)成立精益管理工作领导小组,明确各部门职责。
(2)制定详细的工作计划,明确工作目标、内容、步骤和责任人。
2. 实施阶段(2023年3月-12月)(1)全面推进5S现场管理,开展设备管理、生产流程优化、安全管理等工作。
(2)定期召开工作汇报会,总结经验,查找不足,持续改进。
3. 总结阶段(2024年1月)(1)对精益管理工作进行全面总结,评估工作成效。
(2)制定下一步工作计划,持续改进,不断提高。
五、保障措施1. 加强组织领导。
成立精益管理工作领导小组,负责统筹协调、监督检查和考核评估。
2. 加大资金投入。
精益管理详细工作计划

一、前言为了进一步提高企业内部管理效率,降低成本,提升客户满意度,特制定本精益管理工作计划。
本计划将围绕以下几个方面展开:二、总体目标1. 提高生产效率,降低生产成本;2. 提升产品质量,减少不良品率;3. 优化工作流程,缩短生产周期;4. 提高员工满意度,激发团队凝聚力。
三、具体措施1. 精益生产培训(1)组织全体员工参加精益生产培训,提高员工对精益管理的认识;(2)邀请外部专家进行授课,讲解精益生产工具、方法及实施步骤;(3)鼓励员工积极参与培训,分享学习心得。
2. 5S现场管理(1)对生产现场进行整理、整顿、清扫、清洁、素养活动;(2)建立标准化的现场管理流程,规范员工操作;(3)定期检查5S执行情况,对未达标者进行整改。
3. 精益生产工具与方法(1)推广应用看板管理、快速换模、TPM等精益生产工具;(2)优化生产流程,缩短生产周期;(3)开展价值流分析,识别并消除浪费环节。
4. 质量管理(1)加强质量意识教育,提高员工质量意识;(2)实施全面质量管理,严格把控生产过程中的质量关;(3)对不合格品进行追溯,查找原因并采取措施防止再次发生。
5. 人力资源优化(1)加强员工培训,提高员工技能水平;(2)优化人力资源配置,合理调整人员结构;(3)建立激励机制,激发员工工作积极性。
6. 持续改进(1)设立精益管理推进小组,负责日常工作;(2)定期召开精益管理会议,总结经验,发现问题,持续改进;(3)设立精益管理奖励机制,对优秀团队和个人进行表彰。
四、时间安排1. 第一阶段(1-3个月):开展精益生产培训,实施5S现场管理,推广应用精益生产工具;2. 第二阶段(4-6个月):优化生产流程,加强质量管理,实施人力资源优化;3. 第三阶段(7-9个月):持续改进,总结经验,提升管理水平;4. 第四阶段(10-12个月):总结评估,持续优化,实现精益管理目标。
五、预期效果1. 生产效率提高20%以上;2. 成本降低15%以上;3. 质量不良品率降低30%以上;4. 员工满意度提高20%以上。
精益管理推进策划方案

精益生产推进策划方案第一章精益管理的真意及发展1. 精益管理的简介与定义⑴.精益管理简介:精益管理源于日本,发展于日本,多个国家推广,希望能成功应用与中国。
(目前国内已有多家企业接受、采纳)⑵.精益管理活动强调:一、地/物的明朗化;二、人的规范化地/物的明朗化:即以客人的眼光或新进员工的眼光来看我们的职场,是否能看的清清楚楚,明明白白;人的规范化:即每个员工做事非常用心、严谨,各项工作都能够做到很到位。
⑶.精益管理是一种行动:通过活动来改变人的思考方式,从而改变企业的管理水准,最终达到降低成本,提高效益。
2.精益管理是企业品牌的标志⑴.精益管理活动绝非简单的打扫卫生,它是企业品性的标志⑵.精益管理是企业品性的标志:员工主动遵守规定;员工守时,各项活动能够准时集合;管理状态一目了然;员工的作业速度快捷有序,充满干劲;员工的精神面貌好,彬彬有礼。
3.精益管理对象⑴.精益管理的对象:对人——对员工行动品质的管理;对事——对员工工作方法,作业流程的管理;对物——对所有物品的规范管理。
⑵.正确的管理意识:跑的比竞争对手慢就是退步。
(强调持续进步、持续改善、落后不害怕而在于持续进步)⑶.企业管理的三大支柱:5S+持续改善的团队+技能培训⑷.中国企业精益管理所取得的成效,只是日本的15%,原因是:浮躁,衰减,真意没有学到位。
最主要原因是:只学到形,而没有学到神。
4.精益管理的真意整理的真意为组织化;整顿的真意在于考虑流程的合理化;清扫的真意在于点检;清洁的真意在于彻底改善;素养的真意在于纪律和训练;安全的真意在于尊重生命,排除危险。
5.精益管理精益管理的目标(按6S管理绘制---精益管理的一种)其中:整理、整顿、清扫是动作;安全是基础;清洁要坚持;最终提升素养。
⑵.企业现场6大目标:基本目标:安全(P QCDMS)、效率、成本;在安全基础上提出的:品质、交期、士气。
⑶.五大资源:人、机、料、法、环。
第2章推行组织的有效运作1.如何进行现状的的诊断跟评估先自我诊断,然后推行组织再进去协助和支援,然后进行立项和攻关;推行过程中组织要协调好各部门的工作。
精益生产管理工作年度推进计划

价值流图
持续改进
一种工具,用于识别产品或服务在生产过程 中的所有活动和资源消耗,从而找出浪费并 加以消除。
精益生产的核心思想之一,指不断地查找问 题、解决问题,并通过不断地改进和完善, 提高生产效率和质量。
02
精益生产推进目标
总体目标
提升生产效率
通过优化生产流程、减少浪费 等措施,使整体生产效率提高
计划二:生产流程优化
总结词
生产流程是企业生产的重要环节,通过对生产流程进行 优化,可以提高生产效率、降低成本、提高产品质量和 减少浪费。
详细描述
在进行生产流程优化时,需要对现有的生产流程进行全 面的分析和评估,找出瓶颈和影响生产效率的环节。通 过对生产流程进行改进和优化,可以提高生产效率、降 低成本、提高产品质量和减少浪费。具体的优化措施包 括改进生产线布局、简化生产流程、减少生产过程中的 搬运和等待时间等。
跨部门协作
建立协作机制
明确各部门之间的职责和分工,建立跨部门协作机制。
信息共享
加强各部门的沟通和信息共享,以便更好地协同工作。
培训交流
组织跨部门培训和交流活动,增强员工的沟通和协作能力 。
绩效评估
将跨部门协作的效果纳入绩效评估体系,激励员工积极参 与协作。
04
重点推进计划
计划一:价值流分析
总结词
VS
应急预案应该包括风险事件的识别 、评估、响应、处置和总结等环节 ,同时要明确各部门的职责和协调 机制,确保应急预案的有效性和可 操作性。
08
评估和反馈机制
评估指标体系
01 产品质量
通过产品合格率、废品率等指标 评估产品质量。
03
02
成本效益
生产效率
推进精益管理工作计划方面
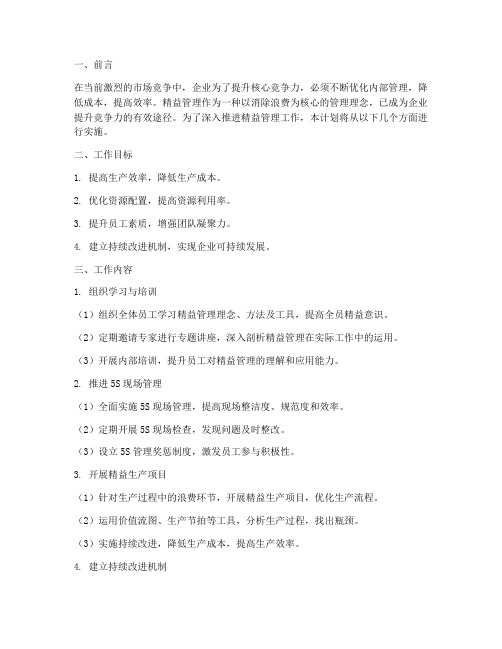
一、前言在当前激烈的市场竞争中,企业为了提升核心竞争力,必须不断优化内部管理,降低成本,提高效率。
精益管理作为一种以消除浪费为核心的管理理念,已成为企业提升竞争力的有效途径。
为了深入推进精益管理工作,本计划将从以下几个方面进行实施。
二、工作目标1. 提高生产效率,降低生产成本。
2. 优化资源配置,提高资源利用率。
3. 提升员工素质,增强团队凝聚力。
4. 建立持续改进机制,实现企业可持续发展。
三、工作内容1. 组织学习与培训(1)组织全体员工学习精益管理理念、方法及工具,提高全员精益意识。
(2)定期邀请专家进行专题讲座,深入剖析精益管理在实际工作中的运用。
(3)开展内部培训,提升员工对精益管理的理解和应用能力。
2. 推进5S现场管理(1)全面实施5S现场管理,提高现场整洁度、规范度和效率。
(2)定期开展5S现场检查,发现问题及时整改。
(3)设立5S管理奖惩制度,激发员工参与积极性。
3. 开展精益生产项目(1)针对生产过程中的浪费环节,开展精益生产项目,优化生产流程。
(2)运用价值流图、生产节拍等工具,分析生产过程,找出瓶颈。
(3)实施持续改进,降低生产成本,提高生产效率。
4. 建立持续改进机制(1)设立持续改进小组,负责精益管理工作的推进和监督。
(2)建立问题反馈机制,鼓励员工积极参与精益管理。
(3)定期对改进项目进行评估,确保改进效果。
四、实施步骤1. 第一阶段:宣传发动,组织学习(1个月)2. 第二阶段:实施5S现场管理,开展精益生产项目(3个月)3. 第三阶段:建立持续改进机制,巩固改进成果(2个月)五、保障措施1. 加强领导,明确责任。
成立精益管理工作领导小组,负责统筹协调和监督推进。
2. 完善制度,规范流程。
建立健全精益管理制度,确保各项工作有序开展。
3. 强化考核,奖惩分明。
将精益管理工作纳入绩效考核体系,对表现突出的单位和个人给予奖励。
4. 沟通协调,形成合力。
加强部门之间的沟通与协作,形成全员参与精益管理的良好氛围。
精益管理的工作计划

一、前言为了提升企业整体管理水平,降低成本,提高效率,增强市场竞争力,我司决定全面推行精益管理。
以下为精益管理工作的计划。
二、总体目标1. 提升企业整体管理水平,降低成本;2. 提高生产效率,缩短生产周期;3. 增强员工综合素质,提高员工满意度;4. 提升客户满意度,提高市场竞争力。
三、工作内容1. 组织学习与培训(1)组织全员参加精益管理培训,提高员工对精益管理的认识和理解;(2)邀请外部专家进行现场指导,针对企业实际情况提供解决方案;(3)开展内部经验分享,推广优秀案例。
2. 5S现场管理(1)开展5S现场管理培训,使员工掌握5S管理方法;(2)对生产现场进行整理、整顿、清洁、清扫、素养活动,提高现场管理水平;(3)建立5S检查制度,定期对现场进行巡查,确保5S管理持续改进。
3. 流程优化与改进(1)对现有流程进行全面梳理,找出瓶颈环节;(2)采用精益工具,如价值流图、因果图等,对瓶颈环节进行分析;(3)制定改进措施,实施流程优化,缩短生产周期。
4. 设备管理(1)开展设备点检、保养培训,提高员工设备维护意识;(2)实施设备预防性维护,降低设备故障率;(3)优化设备布局,提高生产效率。
5. 人员培训与激励(1)开展员工技能培训,提高员工综合素质;(2)建立绩效考核制度,激励员工积极参与精益管理工作;(3)开展团队建设活动,增强团队凝聚力。
6. 持续改进(1)建立持续改进机制,定期对精益管理工作进行评估;(2)针对评估结果,制定改进措施,持续优化工作;(3)推广优秀案例,提高全员精益管理意识。
四、时间安排1. 第一阶段(1-3个月):组织培训,开展5S现场管理,梳理现有流程;2. 第二阶段(4-6个月):实施流程优化与改进,开展设备管理;3. 第三阶段(7-9个月):人员培训与激励,持续改进;4. 第四阶段(10-12个月):全面评估精益管理工作成效,总结经验。
五、预期成果1. 降低成本,提高生产效率;2. 提升客户满意度,增强市场竞争力;3. 增强员工综合素质,提高员工满意度;4. 建立健全精益管理体系,为未来发展奠定基础。
精益生产生产车间现场管理

精益生产车间现场管理:提升效率与品质的关键策略一、现场布局优化,提升空间利用率1. 合理规划生产线布局,减少物料搬运距离。
根据生产流程,将相关工序紧密排列,降低在制品的移动次数,提高生产效率。
2. 采用流线型设计,确保生产流程顺畅。
通过分析生产过程中的瓶颈环节,优化设备布局,使物料流动更加顺畅。
3. 创设整洁、有序的现场环境。
定期清理现场,消除不必要的物品,确保生产空间宽敞,降低安全事故发生的概率。
二、标准化作业,确保生产稳定性1. 制定详细的生产作业指导书,明确各工序操作规程。
让员工按照标准作业,减少人为失误,提高产品质量。
2. 开展技能培训,提高员工操作水平。
针对不同岗位需求,组织专业培训,提升员工技能,降低生产过程中的不良品率。
3. 落实岗位责任制,强化员工责任心。
明确各岗位职责,确保每位员工都能认真负责地完成本职工作。
三、目视化管理,提高现场透明度1. 利用颜色、标识等手段,对现场进行分区、定置。
使员工一目了然,快速找到所需物品,提高工作效率。
2. 设立看板系统,实时展示生产进度、质量状况。
让员工了解生产现状,便于及时调整生产计划。
3. 建立异常反馈机制,鼓励员工发现问题、解决问题。
通过目视化管理,让问题无处藏身,确保生产顺利进行。
四、持续改善,推动现场管理不断提升1. 开展全员参与的质量管理活动,激发员工潜能。
鼓励员工提出合理化建议,不断优化生产流程。
2. 定期组织现场巡查,查找问题根源。
针对发现的问题,制定改进措施,落实整改。
3. 建立持续改善的长效机制,将现场管理纳入日常工作中。
通过持续改进,不断提升车间现场管理水平。
五、库存控制,减少浪费提高响应速度1. 实施准时制生产(JIT),减少在制品和成品库存。
通过精确的需求预测和订单管理,降低库存成本,提高资金周转率。
2. 推行看板管理系统,实现按需生产。
根据生产线的实际消耗情况,动态调整物料供应,避免过量生产。
3. 建立库存预警机制,及时发现潜在问题。
精益生产现场管理工作计划

一、背景及目标随着市场竞争的日益激烈,企业对生产效率的要求越来越高。
为提升企业竞争力,提高生产效率,降低生产成本,本计划旨在通过实施精益生产,优化现场管理,实现以下目标:1. 提高生产效率10%;2. 降低生产成本5%;3. 提升产品质量,减少不良品率;4. 优化现场布局,提高空间利用率;5. 培养一批具有精益生产理念的员工。
二、实施步骤1. 现状调查与分析(1)对现有生产现场进行彻底调查,包括生产线布局、设备状况、人员配置、生产流程等方面;(2)分析生产过程中存在的问题,如生产瓶颈、效率低下、成本高等;(3)制定改进措施,明确改进方向。
2. 精益生产培训(1)组织员工参加精益生产相关培训,提高员工对精益生产的认识;(2)邀请专家进行现场指导,帮助解决实际问题;(3)鼓励员工积极参与,发挥团队协作精神。
3. 5S现场管理(1)开展5S现场管理活动,包括整理、整顿、清扫、清洁、素养;(2)设立5S检查小组,定期对现场进行巡查,发现问题及时整改;(3)加强员工5S意识,培养良好的工作习惯。
4. 流程优化(1)对生产流程进行梳理,找出瓶颈环节;(2)优化生产流程,缩短生产周期;(3)提高设备利用率,减少停机时间。
5. 精益生产工具应用(1)推广应用看板管理、定置定位、快速换模等精益生产工具;(2)建立标准作业指导书,规范操作流程;(3)推广自动化、信息化设备,提高生产效率。
6. 持续改进(1)建立持续改进机制,鼓励员工提出改进建议;(2)定期召开改进成果分享会,推广优秀经验;(3)对改进措施进行跟踪评估,确保效果。
三、保障措施1. 加强组织领导,成立精益生产领导小组,负责统筹协调;2. 制定详细的工作计划,明确责任分工,确保计划落实;3. 加强资源投入,为精益生产提供必要的物质、技术和人力支持;4. 建立激励机制,对表现优秀的员工给予奖励;5. 加强与上级部门的沟通,争取政策支持。
四、实施时间表1. 第一阶段:现状调查与分析(1个月)2. 第二阶段:精益生产培训(2个月)3. 第三阶段:5S现场管理(3个月)4. 第四阶段:流程优化(4个月)5. 第五阶段:精益生产工具应用(5个月)6. 第六阶段:持续改进(6个月)五、预期效果通过实施精益生产现场管理工作计划,预计实现以下效果:1. 生产效率提高10%;2. 生产成本降低5%;3. 产品质量提升,不良品率降低;4. 现场布局优化,空间利用率提高;5. 员工素质提升,团队协作精神增强。
精益管理推行工作计划
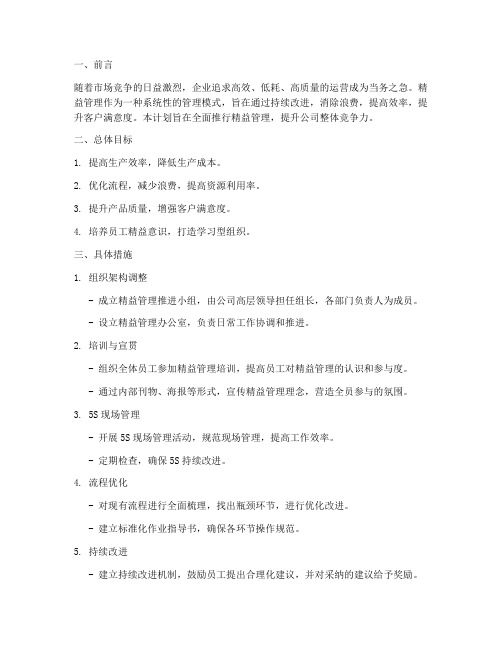
一、前言随着市场竞争的日益激烈,企业追求高效、低耗、高质量的运营成为当务之急。
精益管理作为一种系统性的管理模式,旨在通过持续改进,消除浪费,提高效率,提升客户满意度。
本计划旨在全面推行精益管理,提升公司整体竞争力。
二、总体目标1. 提高生产效率,降低生产成本。
2. 优化流程,减少浪费,提高资源利用率。
3. 提升产品质量,增强客户满意度。
4. 培养员工精益意识,打造学习型组织。
三、具体措施1. 组织架构调整- 成立精益管理推进小组,由公司高层领导担任组长,各部门负责人为成员。
- 设立精益管理办公室,负责日常工作协调和推进。
2. 培训与宣贯- 组织全体员工参加精益管理培训,提高员工对精益管理的认识和参与度。
- 通过内部刊物、海报等形式,宣传精益管理理念,营造全员参与的氛围。
3. 5S现场管理- 开展5S现场管理活动,规范现场管理,提高工作效率。
- 定期检查,确保5S持续改进。
4. 流程优化- 对现有流程进行全面梳理,找出瓶颈环节,进行优化改进。
- 建立标准化作业指导书,确保各环节操作规范。
5. 持续改进- 建立持续改进机制,鼓励员工提出合理化建议,并对采纳的建议给予奖励。
- 定期开展精益管理活动,推动公司持续改进。
6. 绩效考核- 将精益管理纳入绩效考核体系,激发员工积极参与精益管理的热情。
- 对在精益管理工作中表现突出的个人和团队给予表彰和奖励。
四、实施步骤1. 筹备阶段(1个月)- 成立精益管理推进小组,制定工作计划。
- 组织培训,提高员工对精益管理的认识。
2. 实施阶段(6个月)- 开展5S现场管理,优化流程,持续改进。
- 定期检查,确保各项措施落实到位。
3. 评估阶段(2个月)- 对精益管理推行情况进行评估,总结经验,找出不足。
- 对下一阶段工作进行规划。
五、预期效果通过全面推行精益管理,预计可实现以下效果:1. 生产效率提高10%以上。
2. 生产成本降低5%以上。
3. 产品质量提升,客户满意度提高。
精益管理的下一步工作计划

一、前言随着我国经济社会的快速发展,企业竞争日益激烈,精益管理作为一种高效的管理模式,已被越来越多的企业所采用。
为了进一步推动企业精益管理工作的深入开展,提高企业核心竞争力,特制定以下精益管理下一步工作计划。
二、工作目标1. 提高员工精益管理意识,使全体员工充分认识到精益管理的重要性。
2. 深化精益管理实践,优化生产流程,降低成本,提高效率。
3. 建立健全精益管理体系,形成长效机制,确保精益管理工作持续开展。
三、具体措施1. 加强精益管理宣传与培训(1)开展精益管理知识普及活动,提高员工对精益管理的认识。
(2)组织内部培训,邀请外部专家授课,提升员工精益管理技能。
(3)定期举办精益管理经验交流会,分享优秀案例,激发员工参与热情。
2. 深化精益管理实践(1)优化生产流程,减少浪费,提高效率。
(2)开展5S现场管理,改善工作环境,提高员工工作积极性。
(3)实施定置管理,提高物料利用率,降低库存成本。
(4)推广看板管理,实现生产过程的可视化,便于及时发现和解决问题。
3. 建立健全精益管理体系(1)制定精益管理实施计划,明确目标、任务和责任。
(2)建立精益管理考核制度,将精益管理工作纳入绩效考核体系。
(3)设立精益管理专项基金,鼓励员工积极参与精益管理工作。
(4)建立持续改进机制,定期对精益管理工作进行总结和评估。
4. 加强与外部合作(1)与行业内的优秀企业进行交流学习,借鉴先进经验。
(2)与科研机构、高校合作,开展精益管理研究,推动技术创新。
(3)参与行业交流活动,提升企业品牌影响力。
四、工作进度安排1. 第一季度:完成精益管理宣传培训,提高员工精益管理意识。
2. 第二季度:开展5S现场管理、定置管理、看板管理等实践活动。
3. 第三季度:建立精益管理体系,实施精益管理考核制度。
4. 第四季度:总结评估精益管理工作,完善精益管理体系。
五、总结通过实施以上工作计划,我们相信企业的精益管理水平将得到显著提升,为企业创造更大的经济效益和社会效益。
精益管理重点工作计划

一、背景与目标随着我国经济的快速发展,企业面临的市场竞争日益激烈。
为了提高企业核心竞争力,降低成本,提升产品质量,优化生产流程,我单位决定全面推行精益管理。
本计划旨在明确精益管理的重点工作,确保精益管理在我单位顺利实施。
二、工作内容1. 组织学习与培训(1)组织全体员工参加精益管理知识培训,提高员工对精益管理的认识。
(2)邀请专家进行专题讲座,深入讲解精益管理理念、方法及工具。
(3)开展内部培训,培养一批精益管理骨干,负责精益管理工作的推进。
2. 5S现场管理(1)开展5S现场管理活动,整理、整顿、清扫、清洁、素养,提升现场管理水平。
(2)制定5S现场管理标准,规范现场管理流程。
(3)对5S现场管理进行定期检查,确保各项措施落实到位。
3. 流程优化与改进(1)对现有流程进行全面梳理,找出瓶颈环节,制定改进措施。
(2)采用精益工具,如价值流图、鱼骨图等,分析问题,制定解决方案。
(3)对改进措施进行实施,跟踪效果,持续优化流程。
4. 供应链管理(1)优化供应链结构,降低采购成本。
(2)加强供应商管理,提高供应商质量。
(3)推行JIT(及时制)生产,减少库存积压。
5. 质量管理(1)开展质量管理体系培训,提高员工质量意识。
(2)加强过程质量控制,降低不良品率。
(3)实施持续改进,提高产品质量。
6. 成本控制(1)开展成本核算培训,提高员工成本意识。
(2)制定成本控制措施,降低生产成本。
(3)加强成本监控,确保成本控制措施落实到位。
三、实施步骤1. 第一阶段(1-3个月):开展精益管理培训,制定5S现场管理标准,梳理现有流程。
2. 第二阶段(4-6个月):实施5S现场管理,优化流程,降低不良品率。
3. 第三阶段(7-9个月):推进供应链管理,加强质量管理,降低生产成本。
4. 第四阶段(10-12个月):总结评估精益管理工作,持续改进,巩固成果。
四、保障措施1. 建立健全精益管理组织机构,明确责任分工。
2. 制定精益管理考核制度,将精益管理工作纳入绩效考核。
精益生产推进计划
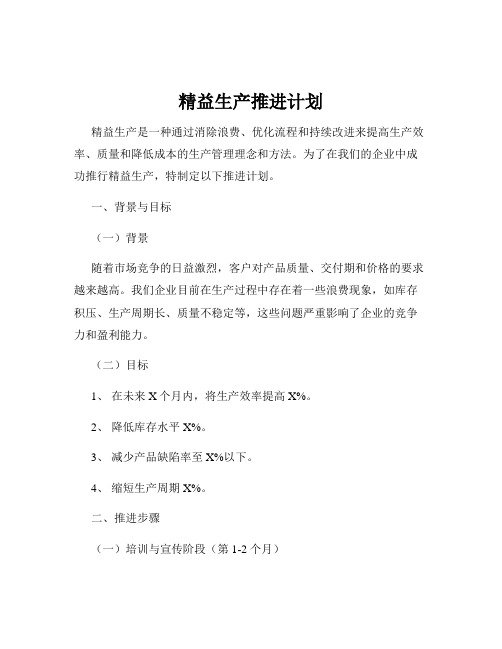
精益生产推进计划精益生产是一种通过消除浪费、优化流程和持续改进来提高生产效率、质量和降低成本的生产管理理念和方法。
为了在我们的企业中成功推行精益生产,特制定以下推进计划。
一、背景与目标(一)背景随着市场竞争的日益激烈,客户对产品质量、交付期和价格的要求越来越高。
我们企业目前在生产过程中存在着一些浪费现象,如库存积压、生产周期长、质量不稳定等,这些问题严重影响了企业的竞争力和盈利能力。
(二)目标1、在未来X个月内,将生产效率提高X%。
2、降低库存水平X%。
3、减少产品缺陷率至X%以下。
4、缩短生产周期X%。
二、推进步骤(一)培训与宣传阶段(第 1-2 个月)1、组织全体员工参加精益生产理念和方法的培训课程,邀请专业的精益生产顾问进行授课,让员工了解精益生产的核心概念和工具,如价值流分析、5S 管理、准时制生产等。
2、在企业内部张贴精益生产的宣传海报,发放宣传手册,营造精益生产的氛围。
3、成立精益生产推进小组,小组成员包括各部门的负责人和骨干员工,负责推进计划的制定和实施。
(二)现状评估阶段(第 3 个月)1、运用价值流分析工具,对企业的主要产品进行价值流图绘制,找出生产过程中的非增值环节和浪费点。
2、对生产现场进行 5S 检查,评估现场管理水平。
3、收集质量数据,分析产品缺陷的类型和原因。
4、与供应商和客户进行沟通,了解上下游环节的需求和问题。
(三)方案制定阶段(第 4 个月)1、根据现状评估的结果,制定具体的改进方案,明确改进的目标、措施、责任人、时间节点等。
2、针对库存管理问题,制定库存优化方案,如采用拉动式生产、设置安全库存等。
3、针对质量问题,制定质量改进计划,如加强过程控制、引入质量管理工具等。
4、针对生产流程优化,制定流程再造方案,消除不必要的工序和等待时间。
(四)实施改进阶段(第 5-8 个月)1、按照改进方案逐步实施改进措施,定期进行检查和评估,确保改进工作按计划进行。
2、推行 5S 管理,保持生产现场的整洁、有序,提高工作效率。
7S精益管理工作任务安排及各专项推进计划
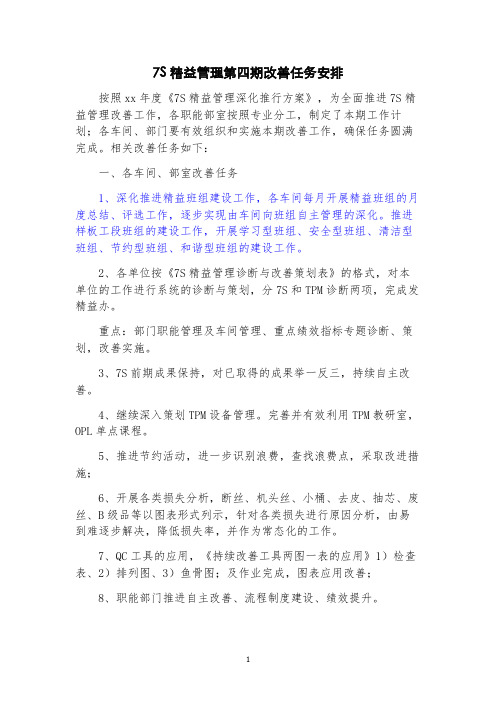
7S精益管理第四期改善任务安排按照xx年度《7S精益管理深化推行方案》,为全面推进7S精益管理改善工作,各职能部室按照专业分工,制定了本期工作计划;各车间、部门要有效组织和实施本期改善工作,确保任务圆满完成。
相关改善任务如下:一、各车间、部室改善任务1、深化推进精益班组建设工作,各车间每月开展精益班组的月度总结、评选工作,逐步实现由车间向班组自主管理的深化。
推进样板工段班组的建设工作,开展学习型班组、安全型班组、清洁型班组、节约型班组、和谐型班组的建设工作。
2、各单位按《7S精益管理诊断与改善策划表》的格式,对本单位的工作进行系统的诊断与策划,分7S和TPM诊断两项,完成发精益办。
重点:部门职能管理及车间管理、重点绩效指标专题诊断、策划,改善实施。
3、7S前期成果保持,对已取得的成果举一反三,持续自主改善。
4、继续深入策划TPM设备管理。
完善并有效利用TPM教研室,OPL单点课程。
5、推进节约活动,进一步识别浪费,查找浪费点,采取改进措施;6、开展各类损失分析,断丝、机头丝、小桶、去皮、抽芯、废丝、B级品等以图表形式列示,针对各类损失进行原因分析,由易到难逐步解决,降低损失率,并作为常态化的工作。
7、QC工具的应用,《持续改善工具两图一表的应用》1)检查表、2)排列图、3)鱼骨图;及作业完成,图表应用改善;8、职能部门推进自主改善、流程制度建设、绩效提升。
9、继续开展改善提案活动。
进一步发动职工参与,力争参与程度和人均提案数都有提高。
10、7S阶段总结工作,每月正常报送PPT总结汇报(诊断策划,记录改善成果,填写总结表格,制作PPT总结报告)。
二、精益办1、对7S管理推行各专业部室工作开展情况进行考评。
2、持续组织改善提案评选与发布会。
3、组织各专业部室月度工作计划的编制,每月28日前报送。
4、各班组形成月度班组建设总结PPT汇报材料,车间开展班组评比工作,参与班组建设的检查、指导工作。
5、组织各专业部室对厂区、办公区持续进行检查,开展红牌作战。
精益现场管理推进工作计划
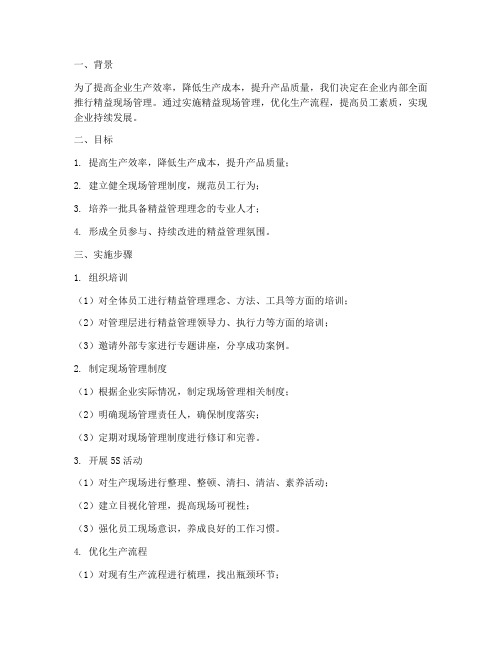
一、背景为了提高企业生产效率,降低生产成本,提升产品质量,我们决定在企业内部全面推行精益现场管理。
通过实施精益现场管理,优化生产流程,提高员工素质,实现企业持续发展。
二、目标1. 提高生产效率,降低生产成本,提升产品质量;2. 建立健全现场管理制度,规范员工行为;3. 培养一批具备精益管理理念的专业人才;4. 形成全员参与、持续改进的精益管理氛围。
三、实施步骤1. 组织培训(1)对全体员工进行精益管理理念、方法、工具等方面的培训;(2)对管理层进行精益管理领导力、执行力等方面的培训;(3)邀请外部专家进行专题讲座,分享成功案例。
2. 制定现场管理制度(1)根据企业实际情况,制定现场管理相关制度;(2)明确现场管理责任人,确保制度落实;(3)定期对现场管理制度进行修订和完善。
3. 开展5S活动(1)对生产现场进行整理、整顿、清扫、清洁、素养活动;(2)建立目视化管理,提高现场可视性;(3)强化员工现场意识,养成良好的工作习惯。
4. 优化生产流程(1)对现有生产流程进行梳理,找出瓶颈环节;(2)优化流程,提高生产效率;(3)实施看板管理,实现生产进度实时监控。
5. 推行TPM(全员生产维修)(1)加强设备维护保养,降低故障率;(2)提高员工设备操作技能,减少人为因素导致的设备故障;(3)建立设备维修保养档案,实现设备全生命周期管理。
6. 持续改进(1)建立问题反馈机制,鼓励员工提出改进建议;(2)定期对现场管理进行评估,找出不足之处;(3)持续优化现场管理,实现企业持续发展。
四、保障措施1. 加强领导,明确责任。
成立精益现场管理推进领导小组,负责统筹协调各项工作;2. 宣传发动,营造氛围。
通过内部刊物、宣传栏、培训等形式,广泛宣传精益现场管理的重要性;3. 强化考核,确保落实。
将精益现场管理纳入绩效考核体系,对工作成效进行奖惩;4. 优化资源配置,保障实施。
根据工作需要,合理安排人力、物力、财力等资源。
5S与精益现场推进计划表

整顿
工具架、文件柜、工作台、更衣柜、餐具柜、清
阶段 9 扫工具、搬运工具、设备、公布栏、看板、消防 5
器具的画线
Байду номын сангаас
10
配电柜、楼梯口、高温处、危险处、台阶、门坎 、开门线、出入线、垃圾桶画线
2
制作各种标识,原材料标识、成品、辅助材料、 工器具、办公用品、资料柜、文件夹、限高标识 11 、离墙距标识、管路颜色、管路名称、流向名称 7 、阀门开关、转动标识、控制仪表颜色标识、安 全警示标识等。
进行物品定量。统计原料每班、每天量清单以及 12 辅料每班每天每周用量,根据用量制作定置管理 3
卡。
13
开展红牌作战,对画线不合格、定位不合格的物 品张贴红牌,限期改正。
2
14 对整顿完毕的责任区进行定点摄影
1
15 开展现场评比会和摄影评比会
2
各车间根据各区域内制定清扫标准(地面、墙面 1 、门窗、设备、模具、工作台等清扫频次\要求 3
7
7 5s培训计划的实施
15
8 5s活动开展所需资源的清单收集
2
9 5s活动开展所需资源的确认和准备
5
1 要和不要物品判定标准的制定、公布
2
2 不要物品处理流程的制定、公布
2
3 各车间划分5s责任区
2
4 查找不要物品,并制作清单
2
5 对不要物品进行处理,并建立处理台账
2
6 起草下发红牌作战制度,并培训
1234123412341234123412341234123412341234
备注
各大区域的规划:如办公区、工作区、原料区、 5 成品区、辅料区、不良区、备件区、车辆通道、 2
关于开展精益生产管理行动计划

关于开展精益生产管理行动计划
通过在本次精益生产培训课上李树青老师对精益生产知识的讲授,使我对精益生产的内涵有了一个更深层次的理解,精益生产不是一段时期内一个人、一个小组的事,而是长期的持久性的与单位每一位员工利益密切相关的事,只有每位员工都认识到精益生产的重要性和紧迫性,具有参与感和责任感,才能积极得参与到单位内部的精益生产中来。
现针对车间的实际生产情况,特制定如下行动计划:目标:根据兵装CSPS管理标准车间2011年精益生产管理达到2.5级标准。
行动计划:
一:加强培训学习,提高员工意识
首先通过各种方式(集体培训、班前会、简报等)对单位全体员工进行精益生产相关知识的培训学习,然后采取闭卷考试等其他强迫性方式让员工认识和提高精益生产意识。
二、规范现场管理
从精益生产出发,对现场的物品从新进行定置定位,对定位的物品做出标识。
然后从6S出发,做好单位的现场管理,使车间的现场管理水平较以前有一个从量到质的改变。
三、班组竞争,树立典型
按照车间现划分的生产小组,根据兵装CSPS管理标准从SQDCME及班组所负责工作区域现场管理七大方面定期进行现场检查、排名,对优秀的班组进行表扬、宣传。
四、持续开展改良改善活动
根据员工在生产管理中发现存在的各种问题,持续开展改良改善活动。
精益管理推进工作计划
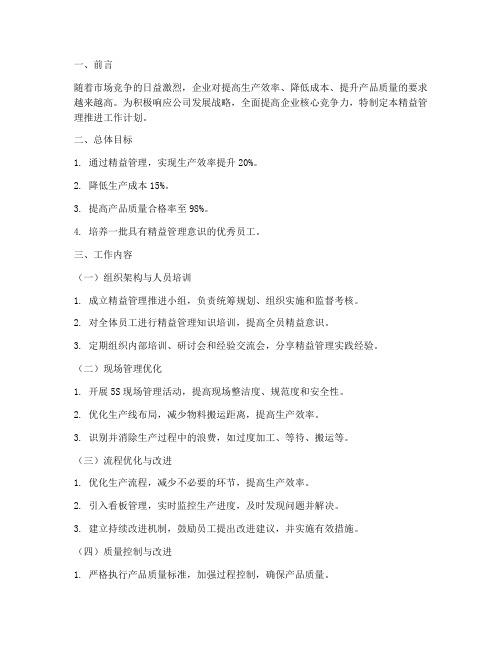
一、前言随着市场竞争的日益激烈,企业对提高生产效率、降低成本、提升产品质量的要求越来越高。
为积极响应公司发展战略,全面提高企业核心竞争力,特制定本精益管理推进工作计划。
二、总体目标1. 通过精益管理,实现生产效率提升20%。
2. 降低生产成本15%。
3. 提高产品质量合格率至98%。
4. 培养一批具有精益管理意识的优秀员工。
三、工作内容(一)组织架构与人员培训1. 成立精益管理推进小组,负责统筹规划、组织实施和监督考核。
2. 对全体员工进行精益管理知识培训,提高全员精益意识。
3. 定期组织内部培训、研讨会和经验交流会,分享精益管理实践经验。
(二)现场管理优化1. 开展5S现场管理活动,提高现场整洁度、规范度和安全性。
2. 优化生产线布局,减少物料搬运距离,提高生产效率。
3. 识别并消除生产过程中的浪费,如过度加工、等待、搬运等。
(三)流程优化与改进1. 优化生产流程,减少不必要的环节,提高生产效率。
2. 引入看板管理,实时监控生产进度,及时发现问题并解决。
3. 建立持续改进机制,鼓励员工提出改进建议,并实施有效措施。
(四)质量控制与改进1. 严格执行产品质量标准,加强过程控制,确保产品质量。
2. 定期进行质量检测,及时发现并解决质量问题。
3. 建立质量追溯体系,确保问题可追溯、可改进。
(五)成本控制与效益提升1. 优化采购流程,降低采购成本。
2. 加强设备管理,提高设备利用率,降低设备维护成本。
3. 优化能源管理,降低能源消耗。
四、实施步骤1. 准备阶段(1个月):成立精益管理推进小组,制定详细的工作计划,组织员工培训。
2. 实施阶段(6个月):开展现场管理优化、流程优化与改进、质量控制与改进、成本控制与效益提升等工作。
3. 总结阶段(1个月):对精益管理推进工作进行总结,评估效果,提出改进措施。
五、保障措施1. 加强领导,提高认识,确保精益管理推进工作顺利进行。
2. 完善激励机制,鼓励员工积极参与精益管理。
精益管理工作计划书

一、前言随着市场竞争的日益激烈,企业对提高生产效率、降低成本、提升产品质量的要求越来越高。
为响应公司发展战略,全面提升企业核心竞争力,特制定本精益管理工作计划。
二、总体目标1. 通过实施精益管理,降低生产成本10%。
2. 提高产品质量合格率至95%以上。
3. 缩短生产周期20%。
4. 提升员工满意度30%。
三、工作内容(一)组织架构与责任分工1. 成立精益管理工作小组,由总经理担任组长,各部门负责人为成员。
2. 各部门负责人为精益管理工作第一责任人,负责本部门精益管理工作的组织实施。
(二)精益管理培训1. 定期组织员工参加精益管理培训,提高员工对精益管理的认识和理解。
2. 邀请专业讲师进行现场指导,针对生产现场、设备管理、流程优化等方面进行培训。
(三)5S现场管理1. 全面实施5S现场管理,规范现场物品摆放,提高工作效率。
2. 定期检查5S实施情况,对不符合要求的部门进行通报和整改。
(四)生产流程优化1. 对现有生产流程进行全面梳理,找出瓶颈环节,提出优化方案。
2. 通过精益生产工具,如价值流图、看板等,对生产流程进行可视化管理和持续改进。
(五)设备管理1. 加强设备维护保养,提高设备运行效率。
2. 定期对设备进行点检,确保设备处于良好状态。
(六)质量控制1. 建立完善的质量管理体系,加强过程控制。
2. 对不合格品进行统计分析,找出原因并采取措施进行改进。
四、实施步骤(一)前期准备阶段(1-2个月)1. 成立精益管理工作小组,明确责任分工。
2. 组织员工参加精益管理培训。
3. 制定5S现场管理方案。
(二)实施阶段(3-6个月)1. 开展5S现场管理,规范现场物品摆放。
2. 对生产流程进行优化,提高生产效率。
3. 加强设备管理,确保设备运行稳定。
4. 实施质量控制,提高产品质量。
(三)评估与改进阶段(7-12个月)1. 对精益管理工作进行阶段性评估,总结经验教训。
2. 根据评估结果,对精益管理工作计划进行调整和改进。
- 1、下载文档前请自行甄别文档内容的完整性,平台不提供额外的编辑、内容补充、找答案等附加服务。
- 2、"仅部分预览"的文档,不可在线预览部分如存在完整性等问题,可反馈申请退款(可完整预览的文档不适用该条件!)。
- 3、如文档侵犯您的权益,请联系客服反馈,我们会尽快为您处理(人工客服工作时间:9:00-18:30)。
项目
主题
内容
推进具体内容
目标/输出
相关岗位
月别
备注
主任
副主任
委员
执行委员
员工
11
12
1
2
3
4
5
6
现场管理
区域选定
前期准备
选定项目拟实施的区域若干个;
确定区域
★
☆
中旬
确定推进区域对应组织---部门领导参与;
区域组织架构及人员
☆
★
☆
☆
推进计划制定。
制定整体推进计划
☆
☆
★
☆
启动会
会议
☆
★
☆
班组数据模式
标准工时、材料、废料数据等管理运营研讨;
班组统计分析数据体系框架
☆
★
☆
下旬
标准工时、材料、废料数据等统计要求出具;
班组统计分析数据体系确定
☆
☆
★
班长/组长考核项目商讨及运营方式;
新建/更新考核项目
☆
☆
★
员工考核项目建立及运营;
定期考核机制建立
☆
☆
★
☆
员工个人别数据采集表建立;
数据表格建立
区域物品清单(检讨后)
☆
☆
★
*车间/班组确定‘待处理区、集中场所’。
区域准备完毕
☆
☆
★
△各区域必要物品三定方案策划;
各区域三定方案草案
☆
☆
★
整顿
△各区域必要物品三定方案评审;
评审会
☆
☆
★
△各区域必要物品三定方案落实;
现场三定实施并运行
☆
☆
★
☆
△车间/班组整体区划线策划;
区划线图
☆
☆
★
△车间/班组整体区划线策划案评审;
评审会
☆
☆
★
△车间/班组整体区划线策划案落实。
区划线画完
☆
☆
★
☆
□现场可视化管理检讨;
现场可视化标准
☆
☆
★
□现场可视化管理改进;
可视化标准落实、检查、改进
☆
☆
★
☆
□5S目视看板建立、运行。
现场目视管理看板
☆
☆
★
我的区域自主点检制度运营。
点检制度建立
☆
☆
☆
★
个别改善
专项活动
班组的课题活动导入,选定课题。
课题导出
☆
☆
★
流失效率/材料成本/品质缺陷细微改善开展;
改善清单
☆
☆
★
改善提案运营方式运作。
本岗位人员提出提案
☆
☆
★
标准化及推广。
标准化内容制作
☆
★
验收
验收
项目验收,现场评议方式。
现场满意度提升
评委会成员
注:1、标注黄色的为计划时间;2、‘★’为主责部门/岗位,‘☆’为辅责部门/岗位。
☆
☆
★
☆
建立班组及个人数据管理看板。
看板建立
☆
☆
★
☆
班组标准管理
制定作业前中后标准内容;
建立作业前中后标准
☆
☆
★
建立作业前中后标准检查方式;
流程建立
☆
☆
★
标准遵守管理方式建立;
PDCA管理方式
☆
☆
★
班组三级(公司、车间、基层)诊断。
诊断流程建立
☆
☆
☆
★
项目
主题
内容
推进具体内容
目标/输出
相关岗位
月别
备注
组织召开项目启动会;
启动会策划、会议召开
★
☆
☆
☆
下旬
措施
项目推动奖惩措施出具。
奖惩措施
☆
★
☆
☆
班组管理
团队班组构建
班组组织结构和职责建立;
班组组织架构及岗位职责确定
☆
★
☆
上旬
班前会流程策划并运营;
运营及评价方式建立、实施
☆
☆
★
班组看板管理;
看板内容策划、建立
☆
☆
★
下旬
班组评定方法。
班组红黄旗评价实施;
主任
副主任
委员
执行委员
员工
11
12
1
2
3
4
5S&目视化活动开展
5S及目视化知识培训
5S活动手册
★
☆
项目区域5S之整理、整顿、目视化改善
—
*车间/班组区域划分,责任到人;
区域6S责任布局图
☆
☆
★
☆
*各区域现状定点拍照,物品清单出具;
现状照片、物品清单
☆
☆
★
☆
整理
*各区域物品要与不要基准对照;