机械加工余量实用标准
毛坯余量制定标准

毛坯余量制定标准毛坯余量的制定,必须结合零件的材料、结构尺寸、加工精度及下料成形方式、热处理方法、机械加工方案综合考虑。
合理的毛坯余量,不仅能有效地确保产品质量,而且可以最大限度地降低材料消耗和加工成本,提高生产效率。
现就工作中经常遇到的毛坯余量留放办法提出我们初步意见供大家讨论,欢迎各位领导及专家提出宝贵意见。
1 棒材毛坯余量1.1棒材毛坯外径机械加工余量见表1表1:轧制棒材外径机械加工余量单位:mm注: (1) 台阶轴,大外圆近中部者适用表值,大外圆近端部或凸肩很窄可适当减少;(2) 需要粗加工后去应力回火的零件,应适当增加余量;(3) 长度与直径之比大于20者,按工艺要求规定酌情增加余量。
1.1棒材毛坯长度及余量1.1.1 对于φ≤36mm的棒材毛坯,采用多件下料。
在制造BOM中,毛坯尺寸1按单个零件长度+10mm往上取整计算,毛坯尺寸2为15mm,每件制数为l。
在此,毛坯尺寸2里面的15具有双重意义,一是多件下料,二是留有15mm夹头余量。
1.1.2 对于φ>36mm的棒材毛坯,毛坯尺寸写成“L”形式,可制件数一栏注明可制件数。
对于切深不超过20mm、工件长度不超过60mm(除>M30或11/4″的高温螺母、带槽螺母和罩螺母单件下料)的中空零件,在备注栏内注明:允许多件下料。
根据规定,允许多件下料的零件,毛坯尺寸为单个零件长度+10mm,每件制数为l,坯料总长控制在200mm之内。
1.1.3 可调头加工外圆的单件下料零件,毛坯长度L=单个零件长度+10mm。
1.1.4 不能调头加工外圆的单件下料零件,应根据零件加工所需的夹头量、是否带Ⅳ试样、是否留热处理吊头、是否留顶尖孔余量决定。
1.1.4.1 夹头量见表3注:1.自动和半自动车床夹头留量一般为40mm;2.压花零件、车外螺纹、磨削外圆夹头余量一般留25mm。
1.1.4.2 杆状零件长度大于等于1200mm的均安排在井式炉中热处理(螺栓除外)。
磨削加工余量标准

磨削加工余量标准 Document serial number【KKGB-LBS98YT-BS8CB-BSUT-BST108】·机械加工余量标准25EQY—19-1999 1.主题内容与适用范围本标准规定了磨削加工的加工余量。
本标准适用于磨削各类材料时的加工余量。
2.技术内容加工余量表(一)厚度4以上的平面磨削余量(单面)平面长度平面宽度200以下平面宽度200以上小于100100-250251-500500-800说明:1.二次平面磨削余量乘系数2.三次平面磨削余量乘系数23.厚度4以上者单面余量不小于橡胶模平板单面余量不小于毛坯加工余量表(二)I:园棒类:(1)工件的最大外径无公差要求,光洁度在▽以下,例:不磨外圆的凹模带台肩的凸模、凹模、凸凹模以及推杆、推销、限制器、托杆、各种螺钉、螺栓、螺塞、螺帽外径必须滚花者。
(毫米)工件直径(D)工件长度 L车刃的割刀量和车削二端面的余量(每件)<7071-120121-200201-300301-450直径上加工余量≤32122345-10 33-60233454-6 61-100344454-6 101-200455564-6当D<36时并不适应于调头夹加工,在加工单个工件时,应在L上加夹头量10-15。
(2)工件的最大外径有公差配合要求,光洁度在▽以上,例如:外圆须磨加工的凹模,挡料销、肩台须磨加工的凸模或凸凹模等。
(毫米)工件直径(D)工件长度 L车刃的割刀量和车削二端面的余量(每件)<5051-8081-150151-250251-420直径上加工余量≤15334455-1016-32344565-1033-60445665-861-100555675-8101-200666775-8当D<36时,不适合调头加工,在加工单个零件时,应加夹头量10-15。
毛坯加工余量表(三)Ⅱ:圆形锻件类(不需锻件图)(1)不淬火钢表面粗糙度在▽以下无公差配合要求者,例如:固定板、退料板等。
自由锻造水压机锻件机械加工余量和公差标准

+15
+16
+17
+29
10001~15000
+12
40 − 20 43 − 21
+14
+13
42 − 21 45 − 22
+15
+14
+16
15001~20000
+12
40 − 20
+13
注:⑴有台阶的矩形截面零件,根据最大截面的 A、B 值确定余量和公差; ⑵较短的锻件(L<2500) ,两各加 1a; ⑶宽度大于 1600 的板形锻件的机械加工余量由工艺编制人员自定。 ⑷水压机锻造最小截面厚度为:6000T 水压机为 200,15000T 水压机为 300。
2.4 圆筒形锻件机械加工余量和公差。 2.4.1 加氢大型圆筒型锻件机械加工余量和公差表。
零 件 直 径 D 设备 零件长度 L ≤4500 4501~ 6000 余量及公差 水压机出成品 <4000 90 − 45 80 − 40
+27
+30
≥6001
110 − 55 90 − 45
+30
+37
350/275
495/385
260/220
400/330
注:表中分子为端部法兰用,分母为中间法兰用。
2.2 形状较复杂锻件品种的余量分配 2.2.1 发电机转子的余量分配
2.2.2
汽轮机整体转子的余量分配
A 汽轮发电机转子,汽轮机整体转子长度 lo≤2000 时加 2a。长度 lo≥13000 时加 4a。 B 法兰直径与凹档(相邻小园)直径差大于(或等于)1000 时凹档直径可适当加大余量的 10~20%。 C 凹档下料长度小于窄砧宽度时,可按窄砧宽度计算,加大凹档直径余量。 D 水压机最小砧宽:6000T 水压机最小砧宽 600,15000T 水压机最小砧宽 850 E 凹档直径=√(D1+50mm)×K×6.16÷L 其中 D1:与凹档相邻台阶的直径 K:最小砧宽 L:凹档锻造长度
余量标准

12+40
14+50
16+50
16+50
14+50
14+50
16+50
18+60
16+50
16+50
16+60
18+60
16+50
16+60
20+60
20+60
18+60
18+70
20+70
20+80
20+70
20+70
22+80
22+80
20+80
20+80
22+100
24+100
-
22+100
24+100
0.5a
2a1 0.5a
0.5a 0.5a
图2
5、光轴类锻件形位公差 5.1、对于台阶轴类锻件,台阶的同轴度为 a1(a1 为小直径轴段加工余量)。
图3
5.2、对于方形、六角形、八角形或矩形锻件相邻边之间的夹角形位公差为≦±1°。 5.3、锻件表面直线度(平直度)为≤ 2mm/m,此直线度可在锻件表面任一位置测量。
锻圆轴的机械加工余量、尺寸公差、形位公差。 本标准选用于 L≧1.5D(或 1.5A)、A≦B≦1.5A 的圆轴、方轴和矩形截面类、
台阶轴类锻件。 凡超越本标准规定范围的自由锻件,其余量与公差由供需双方协商确定。
2、规范性引用文件 下列文件中的条款通过本标准的引用而成为本标准的条款。凡是未注日期的
引用文件,其最新版本适用于本标准。 GB/T21469 锤上钢质自由锻件机械加工余量与公差 一般要求 GB/T21471 锤上钢质自由锻件机械加工余量与公差 轴类 JB/T9179.2 水压机上自由锻件机械加工余量与公差 圆轴、方轴、矩形截面类 JB/T9179.2 水压机上自由锻件机械加工余量与公差 台阶轴类 3、光轴类加工余量及尺寸公差 3.1、圆形、方形、六角形、八角形或矩形(B/H≦5)截面的光轴类快锻锻件尺 寸应 L>2.5D(或 A、B、S)。 3.2、光轴类快锻件的机械加工余量与尺寸公差应符合图 1 与表 1 的规定。
机械加工工序间余量

机械加工工序间余量1. 引言机械加工是制造业中常见的一种加工方法,通常需要经过多个工序才能完成最终的产品。
在机械加工过程中,每个工序都有一定的误差和余量。
其中,工序间余量是指在不同的工序之间,为了保证最终产品的尺寸精度和质量要求,在相邻工序之间留下的一定的余量。
工序间余量的设置对于机械加工过程的精度控制非常重要。
合理的余量设计可以确保工序的顺利进行,减少因误差积累导致的尺寸偏差,提高零件的加工精度和质量。
本文将探讨机械加工工序间余量的设定原则和方法,以及对于加工精度的影响。
2. 工序间余量的设定原则在机械加工过程中,工序间余量的设定应遵循以下原则:2.1 渐进原则工序间余量应该采用逐步递减的方式进行设置,即从粗加工到精加工的工序中,余量逐渐减小。
这是因为在粗加工的工序中,材料去除量较大,容易出现尺寸偏差;而在精加工的工序中,材料去除量较小,尺寸控制更为关键。
因此,通过逐步递减的余量设定,可以确保每个工序的精度要求得到满足。
2.2 公差要求原则工序间余量的设定应考虑最终产品的公差要求。
公差是指允许的尺寸偏差范围,是衡量产品质量的重要指标。
根据产品的公差要求,可以确定在每个工序中需要保留的余量范围。
同时,公差范围也反映了不同工序之间的误差传递关系,通过合理设置工序间余量,可以控制误差的传递,保证最终产品的尺寸精度。
2.3 切削力和刚度要求原则工序间余量的大小还应考虑到切削力和刚度的要求。
在机械加工中,切削力是指刀具对工件的力量,而刚度是指工件和加工设备的抗变形能力。
切削力的大小与余量直接相关,过小的余量会导致切削力过大,增加切削工具的磨损和断裂的风险;而过大的余量则会降低刚度,影响加工精度。
因此,通过综合考虑切削力和刚度的要求,可以确定合适的余量范围。
3. 工序间余量的设定方法3.1 按照工序特点设定根据不同工序的特点和加工要求,可以采用不同的方式设定工序间余量。
例如,在粗加工的工序中,由于材料去除量大,可以适当增大余量范围,以防止尺寸偏差过大;而在精加工的工序中,材料去除量小,可以适当减小余量范围,以提高加工精度。
机械加工余量

机械加工余量机械加工余量,通常指零件在加工过程中留下的一定尺寸或形状偏差,它是为了确保零件在加工完成后符合设计要求,以便进行后续的装配、检测,防止零件因加工尺寸不足或过大而无法使用。
机械加工余量是一个重要的概念,对于机械加工工艺的控制和零部件设计起着十分关键的作用。
具体而言,机械加工余量有以下几个方面:1.设计时的余量在机械设计时,就要为加工余量留出一定的设计空间。
这主要包括对零件的几何形状、加工工艺、加工设备等进行考虑。
通常情况下,对于普通的零件,其形状偏差应控制在0.1mm以内,对于精密零件则要在0.01mm以内。
2.加工技术中的余量加工技术中的余量主要指在机床上进行切削或磨削过程中,由于刀具磨损、机床刚度等因素的影响,所导致的零件加工尺寸与设计尺寸的偏差。
在实际操作中,加工技术中的余量可以通过调整刀具切削角度或者加工速度等措施来进行控制。
3.热变形对加工余量的影响在加工加热敏感的金属材料时,由于加热时材料发生热膨胀,会导致加工余量发生偏差。
这时,加工人员可以通过调整加工参数、减少加热时间、加强冷却等方法来调整加工余量。
机械加工余量的控制非常重要,一定程度上,它也是衡量机械加工技术水平的重要标准。
而在实际应用过程中,如何掌握机械加工余量的大小和控制方法,影响着机械零件的质量和生产效率。
以下是一些有关机械加工余量控制的方法:1.合理选择切削工艺参数在进行机械加工时,加工人员应该合理选择切削工艺参数,包括切削速度、进给量、切削深度等方面,以达到减少加工余量的目的。
2.优化刀具设计优化刀具设计也是减小机械加工余量的重要方面。
合理的切削角度可以减少切削力和变形,从而控制加工余量。
此外,刀具的刃磨加工精度也需要达到精度级别,从而减小加工余量。
3.控制机床几何精度机床几何精度是影响加工余量的重要因素之一。
因为机床精度的影响,加工出来的零件在尺寸、直线度、平行度、垂直度等方面都会受到不同程度的影响,进而导致加工余量的产生。
铸钢件机械加工余量、尺寸公差及缺陷评定标准

铸钢件机械加工余量、尺寸公差及缺陷评定标准1、范围本标准规定了铸钢件机械加工余量、尺寸公差及缺陷的评定。
本标准适用于起重机械产品铸钢件尺寸公差测量验收及铸造缺陷评定,也适用于外协铸钢件毛坯的检验验收。
2、引用标准GB/T11350-89 铸件机械加工余量GB6414-86 铸件尺寸公差JB/T6392.2-92 起重机车轮技术条件Q/DQ100-80 普通桥式起重机技术条件3、铸件机械加工余量铸件机械加工件,有毛坯图时,加工余量按毛坯图的规定;没有毛坯图时,按公司的产品特点,选用GB/T11350-89《铸件机械加工余量》中H级加工余量(铸件尺寸公差等级按CT13)数值如表1:表1注:表中每栏的加工余量数值是以一测为基准,进行单侧加工的加工余量值,()内数值为进行双侧加工时,每测的加工余量值。
4、铸件尺寸公差4.1 铸件尺寸公差按设计图纸的规定。
4.2 设计图纸未规定的铸件非加工面的尺寸公差及加工面毛坯尺寸公差,按公司的产品特点,选用GB64414-86《铸件尺寸公差》中规定的CT13级,公差带为对称分布,即一半为正值,一半为负值。
公差数值见表2:表25、技术要求5.1 铸件最终热处理应按图纸规定,铸件毛坯应进行正火或退货处理;5.2 铸件表面应整洁,不得留有明显的型砂、斑疤等缺陷。
浇口、冒口、毛边应气割清除,飞刺应清除,气割应在铸件毛坯热处理前进行。
浇、冒口气割侯,根部残留高度不大于4mm;5.3 铸件毛坯如有气孔、夹渣、机械伤痕等缺陷,除高锰钢外可焊补;5.4 铸件不加工的次要表面,若缺陷在下述范围内允许存在,可不进行焊补:a、缺陷总面积不超过该表面面积的5%;b、单个缺陷面积的直径不超过5mm,深度不超过其壁厚的10%,且绝对值不超过3mm,每100mm×100mm 面积上不超过2个。
5.5 铸件毛坯焊补,应遵循以下条件:a、焊补应在毛坯热处理前进行;b、缺陷必须清除干净,至呈现良好基体金属;c、所用焊条应能保证焊内的机械性能与铸件本身的机械性能相当。
机械精加工余量标准
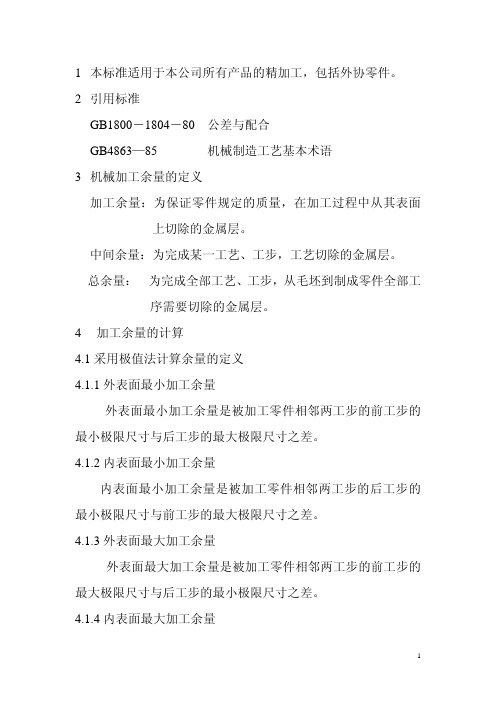
直径余量 t1 1.5
2
2.5
3
3.5
4
5
端面余量 t2
1
1.5
1.5
2
2.5
3
4
公 差 H0
0.15
0.20
0.30
0.40
0.45
0.5
0.6
4
(2) 套类、短轴类 1≤L/D≤2
直径 (mm)
≤50
>
>
>
>
>
50~100 100~200 200~300 300~400 400~500
直径余量 t1
0.8
7
(2) 套类、短轴类 1≤L/D≤2
直 径 ≤50 >50~100 >100~200 >200~300 >300~400 >400~550
直径余量 1.5
2
2.5
3
4
5
端面余量
1
1
1.5
2
2.5
3
公 差 0.15
0.20
0.25
0.3
0.4
0.5
(3) 圈 类(D-d)/d≤0.2,L/D≤0.5
φL δφL δφ L δφL δφL δ
D≤300
1.5 1 0.2 2 1.5 0.2 2.5 1.5 0.3 3 2 0.3 3 2 0.3
300<D≤700
2 1.5 0.3 2.5 1.5 0.3 2.5 1.5 0.3 3 2 0.3 3.5 2.5 0.4
700<D≤1250 2.5 1.5 0.3 3 2 0.3 3 2 0.3 3.5 2.5 0.4 4 3 0.4
4.2.1 最小余量的计算公式:
对于外表面加工:Zbmin=aamin-abmax
机械加工工序间余量

3.2机械加工工序间余量本章规定的常见工序间加工留量作为本公司编制机械加工工序及有关单位确定加工余量的依据,如有特殊情况可由工艺部门另作规定。
3.2.1切料头时留芯部安全尺寸如图3.2-1所示,当工件材料σs=400~450MPa时,切料头留芯部安全尺寸d按表3.2-1选取。
表3.2-1 中数据用公式d3≈5Q l/σs计算,式中的σs材料屈服极限。
如为其它材料时,应根据其σs大小将安全尺寸d应乘上修正系数K,K值按表3.2-2选取。
表3.2-1 mm注:①、切料头安全尺寸d应按h13级精度加工。
②、切料头当接近安全尺寸时严禁啃刀。
③、切料头前床面上必须垫适当数量的枕木,在架中心架或托辊切断时,直径可以适当缩小。
表3.2-23.2.2 各类锯片及铣刀切口宽度及切割规格各类锯片及铣刀宽度及切割规格见表3.2-3。
表3.2-3 mm注:圆锯能切割方料的最大尺寸为圆料的70%。
3.2.3 车床切断刀及插床切口刀的切口宽度及切割深度车床切断刀及插床切口刀的切口宽度及切割深度见表3.2-4。
表3.2-4 mm注:车床、插床的刀具宽度可以适当磨小。
如果设计专用切断刀时宽度可以适当减少。
3.2.4箱体、架体零件粗加工后人工时效余量箱体、架体零件粗加工后人工时效余量见表3.2-5 。
表3.2-5 mm注:①、适用于铸铁件粗加工后人工时效及粗精加工分开如床身、立柱、工作台、箱体等,不适用于容易变形的薄板。
②、自然时效余量为表中数值的0.5~0.6倍。
③、铸钢件可按表中数值增加1~2mm。
3.2.5 平键修配余量平键修配余量见表3.2-6。
表3.2-6 mm注:①、间隙配合的导向键及切向键不留修配余量。
②、斜健的两侧不留修配余量,斜面上一般情况设计时已留有0.3~0.5mm的修配量,如图纸上未留量时,工艺上应留量。
3.2.6 孔的钻、扩、铰余量孔的钻、扩、铰余量见表3.2-7.表3.2-7 mm注:①、大于Φ30mm的孔,可在二次走刀中钻出,先用较小钻头预钻孔。
机械加工余量选择方法

机械加工余量选择方法1.基本余量法基本余量法是机械加工中最常用的一种方法。
根据经验和相关的机械加工标准,确定不同材料或零件类型应有的基本余量值。
例如,在车削加工中,对外圆进行车削时,可选择的基本余量为0.5-1.5mm;而对内圆进行车削时,可选择的基本余量为0.1-0.3mm。
根据实际情况,合理选择基本余量值,以确保零件尺寸的精度和质量。
2.递减余量法递减余量法是根据机械加工过程中的实际情况,逐步减小加工余量的方法。
根据零件尺寸的精度要求和加工工艺的特点,通过试验和实践,逐渐调整和减小加工余量,以满足零件的尺寸要求。
这种方法在一些对尺寸精度要求较高的零件加工中比较常用,可以尽量减小加工余量,提高加工精度。
3.检测修正法检测修正法是一种基于实际测量结果的余量选择方法。
在零件加工结束后,通过测量零件的尺寸,与设计尺寸进行比较。
根据实际测量结果,修正设计尺寸和加工余量,以满足零件尺寸要求。
这种方法相对较为灵活,可以根据实际情况进行调整和修正,适用于对尺寸要求较为严格的零件加工。
4.确定余量法确定余量法是通过实验和计算,根据工艺参数和材料性质,确定加工余量的具体数值。
根据材料的热膨胀系数、强度和硬度等特性,结合机械加工过程中材料的变形和切削刃的磨损等因素,采用数学模型和计算方法,确定合适的加工余量。
这种方法相对较为精细和科学,适用于复杂零件和高精度加工。
在实际机械加工中,选择合适的机械加工余量方法,对于确保零件尺寸的精度和质量至关重要。
工程师和技术人员应根据具体的加工要求、材料特性和加工工艺,合理选择和调整机械加工余量,以获得满足要求的加工结果。
同时,还需要结合实际情况,不断总结和改进机械加工余量的选择方法,提高加工效率和质量。
锻件机械加工余量与公差标准

图3
描写
描校
旧底图总号
底图总号
签字
日期
标记
处数
更改文件号
签字
日期
企业标准
第3页
表3长方体锻件的加工余量与公差mm
零件长度
L
零件截面尺寸 H
~30
>30~80
>80~150
>150~250
>250~400
a
b
a
b
a
b
a
b
a
b
~100
>100~200
>200~300
语种
译文页
译
校
企业标准
锻件机械加工余量与公差标准
共5页第1页
会签
1 范围
本标准是关于黑色金属锻件机械加工余量与公差尺寸要求的规定。
本标准适用于公司产品中含碳量不超过0.9%和其它成分总含量不超过4%的碳素钢和合金钢的自由锻件。
2规范性引用标准
GB/T15826.1-1995锤上钢质自由锻件机械加工余量与公差一般要求
3锻件加工余量与公差的规定
3.1一般规定
3.1.1 自由锻件的形状与位置公差如无特殊要求进,均不得小于本标准规定的公差值。
3.1.2本标准规定的机械加工余量与公差适用于轧制锻造的锻件。采用钢锭锻造时,余量与上偏差(内孔和凹档为下偏差)允许按本标准规定的数值增加50%。
3.1.3本标准规定的余量不包括机加工夹头、热处理夹头、理化检验用料及最终热处理(调质等)在和粗加工余量。这些余量由产品工艺员根据零件加工具体要求另外增加。
8±2.5
7±2
11±3
9±3
8±2.5
机械加工余量等级大全【详述】

机械加工余量等级内容来源网络,由“深圳机械展(11万㎡,1100多家展商,超10万观众)”收集整理!更多cnc加工中心、车铣磨钻床、线切割、数控刀具工具、工业机器人、非标自动化、数字化无人工厂、精密测量、3D打印、激光切割、钣金冲压折弯、精密零件加工等展示,就在深圳机械展.机械加工余量标准,25EQY—19-19991.主题内容与适用范围本标准规定了磨削加工的加工余量。
本标准适用于磨削各类材料时的加工余量。
2.技术内容加工余量表(一)厚度4以上的平面磨削余量(单面)平面长度平面宽度200以下平面宽度200以上小于100 0.3 100-250 0.45 251-500 0.5 0.6 500-800 0.6 0.65 说明:1.二次平面磨削余量乘系数1.5 2.三次平面磨削余量乘系数2 3.厚度4以上者单面余量不小于0.5-0.8 4.橡胶模平板单面余量不小于0.7 毛坯加工余量表(二)3.2I:园棒类: (1)工件的大外径无公差要求,光洁度在▽以下,例:不磨外圆的凹模带台肩的凸模、凹模、凸凹模以及推杆、推销、限制器、托杆、各种螺钉、螺栓、螺塞、螺帽外径必须滚花者。
(毫米)工件直径(D)工件长度L 车刃的割刀量和车削二端面的余量(每件) <70 71-120 121-200 201-300 301-450 直径上加工余量≤32 1 2 2 3 4 5-10 33-60 2 3 3 4 5 4-6 61-100 3 4 4 4 5 4-6 101-200 4 5 5 5 6 4-6 1.6当D<36时并不适应于调头夹加工,在加工单个工件时,应在L上加夹头量10-15。
(2)工件的大外径有公差配合要求,光洁度在▽以上,例如:外圆须磨加工的凹模,挡料销、肩台须磨加工的凸模或凸凹模等。
(毫米)工件直径(D)工件长度L 车刃的割刀量和车削二端面的余量(每件) <50 51-80 81-150 151-250 251-420 直径上加工余量≤15 3 3 4 4 5 5-10 16-32 3 4 4 5 6 5-10 33-60 4 4 5 6 6 5-8 61-100 5 5 5 6 7 5-8 101-200 6 6 6 7 7 5-8 当D<36时,不适合调头加工,在加工单个零件时,应加夹头量10-15。
机械加工余量等级大全【详述】

机械加工余量等级内容来源网络,由“深圳机械展(11万㎡,1100多家展商,超10万观众)”收集整理!更多cnc加工中心、车铣磨钻床、线切割、数控刀具工具、工业机器人、非标自动化、数字化无人工厂、精密测量、3D打印、激光切割、钣金冲压折弯、精密零件加工等展示,就在深圳机械展.机械加工余量标准,25EQY—19-19991.主题内容与适用范围本标准规定了磨削加工的加工余量。
本标准适用于磨削各类材料时的加工余量。
2.技术内容加工余量表(一)厚度4以上的平面磨削余量(单面)平面长度平面宽度200以下平面宽度200以上小于100 0.3 100-250 0.45 251-500 0.5 0.6 500-800 0.6 0.65 说明:1.二次平面磨削余量乘系数1.5 2.三次平面磨削余量乘系数2 3.厚度4以上者单面余量不小于0.5-0.8 4.橡胶模平板单面余量不小于0.7 毛坯加工余量表(二)3.2I:园棒类: (1)工件的大外径无公差要求,光洁度在▽以下,例:不磨外圆的凹模带台肩的凸模、凹模、凸凹模以及推杆、推销、限制器、托杆、各种螺钉、螺栓、螺塞、螺帽外径必须滚花者。
(毫米)工件直径(D)工件长度L 车刃的割刀量和车削二端面的余量(每件) <70 71-120 121-200 201-300 301-450 直径上加工余量≤32 1 2 2 3 4 5-10 33-60 2 3 3 4 5 4-6 61-100 3 4 4 4 5 4-6 101-200 4 5 5 5 6 4-6 1.6当D<36时并不适应于调头夹加工,在加工单个工件时,应在L上加夹头量10-15。
(2)工件的大外径有公差配合要求,光洁度在▽以上,例如:外圆须磨加工的凹模,挡料销、肩台须磨加工的凸模或凸凹模等。
(毫米)工件直径(D)工件长度L 车刃的割刀量和车削二端面的余量(每件) <50 51-80 81-150 151-250 251-420 直径上加工余量≤15 3 3 4 4 5 5-10 16-32 3 4 4 5 6 5-10 33-60 4 4 5 6 6 5-8 61-100 5 5 5 6 7 5-8 101-200 6 6 6 7 7 5-8 当D<36时,不适合调头加工,在加工单个零件时,应加夹头量10-15。
机械加工工序间余量

4、轴类零件粗加工余量
表9
加工直径 零件长度 ≤30 >30-50 >50-120 >120-250 >250-500 >500-800 >800-1200 3 3.5 4 4 5 6 7 3.5 4 4 5 5 6 7 ≤18 >18-30 >30-50 >50-120 >120-250 >250-500 直 4 5 5 5 6 7 7 径 余 5 5 5 6 7 7 8 量 5 5 6 6 7 8 8 a 5 5 6 6 7 8 8
说明:本表摘自《一般工艺规定及指导资料》P10 剪耗规定表
三、轴的加工余量 1、外圆柱表面加工路线及所能达到的精度和表面粗糙度 表6
加工路线
尺寸精度
表面粗糙度 Ra μm
粗车 粗车,半精车 粗车,半精车, 精车 磨 粗车,半精车, 精车,细车(适用于有色金 属及合金) 粗磨,精磨 精车,滚压 粗车,半精车,粗磨,精磨, 镜面磨削 研磨 超精加工 抛光 粗车,半精车,粗磨,精磨, 镜面磨削 精研磨 粗研磨 超精加工 抛光
3、轴类零件采用热轧棒料时外径的选用 表8
零件的长度与公称直径之比 零件的 公称直 径 毛坏直径 5 6 8 10 11 12 14 16 17 18 19 20 零件的 公称直 径 ≤4 >4-8 >8-12 >12-20 7 8 10 12 14 14 16 18 19 20 21 22 14 16 18 19 20 21 22 7 8 10 12 14 8 8 10 13 14 15 17 18 20 21 22 23 8 8 11 13 14 15 18 19 21 22 23 24 21 22 25 27 28 30 32 33 35 36 37 38 零件的 公称直 径 毛坏直径 ≤4 >4-8 >8-12 >12-20 24 25 28 30 32 33 35 36 38 39 40 42 24 25 28 30 32 33 35 38 38 40 42 42 ≤4 >4-8 >8-12 >12-20 零件的 公称直 径 毛坏直径 24 26 28 32 32 34 36 38 39 40 42 42 25 26 30 32 32 34 36 38 39 40 42 43 ≤4 零件的长度与公称直径之比 >4-8 >8-12 >12-20
机械加工余量标准最新版
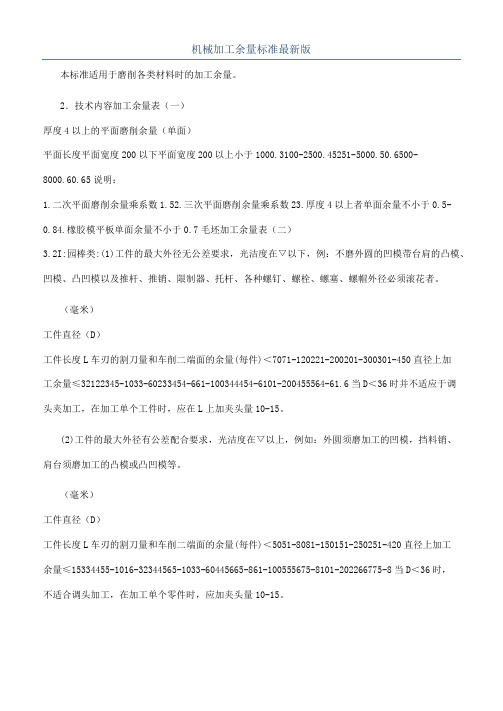
机械加工余量标准最新版本标准适用于磨削各类材料时的加工余量。
2.技术内容加工余量表(一)厚度4以上的平面磨削余量(单面)平面长度平面宽度200以下平面宽度200以上小于1000.3100-2500.45251-5000.50.6500-8000.60.65说明:1.二次平面磨削余量乘系数1.52.三次平面磨削余量乘系数23.厚度4以上者单面余量不小于0.5-0.84.橡胶模平板单面余量不小于0.7毛坯加工余量表(二)3.2I:园棒类:(1)工件的最大外径无公差要求,光洁度在▽以下,例:不磨外圆的凹模带台肩的凸模、凹模、凸凹模以及推杆、推销、限制器、托杆、各种螺钉、螺栓、螺塞、螺帽外径必须滚花者。
(毫米)工件直径(D)工件长度L车刃的割刀量和车削二端面的余量(每件)<7071-120221-200201-300301-450直径上加工余量≤32122345-1033-60233454-661-100344454-6101-200455564-61.6当D<36时并不适应于调头夹加工,在加工单个工件时,应在L上加夹头量10-15。
(2)工件的最大外径有公差配合要求,光洁度在▽以上,例如:外圆须磨加工的凹模,挡料销、肩台须磨加工的凸模或凸凹模等。
(毫米)工件直径(D)工件长度L车刃的割刀量和车削二端面的余量(每件)<5051-8081-150151-250251-420直径上加工余量≤15334455-1016-32344565-1033-60445665-861-100555675-8101-202266775-8当D<36时,不适合调头加工,在加工单个零件时,应加夹头量10-15。
毛坯加工余量表(三)3.2Ⅱ:圆形锻件类(不需锻件图)(1)不淬火钢表面粗糙度在▽以下无公差配合要求者,例如:固定板、退料板等。
(毫米)工件直径(D)工件长度L<1011-2022-4546-100101-250直径上加工余量长度方向上余量150-2022555555657201-3005656565768301-4005757576889401-50078586879910501-6007868687101011注:表中的加工余量为最小余量,其最大余量不得超过厂规定标准。
锻件机械加工余量与公差标准

5±1.5
6±1.5
7±2
8±2.5
9±3
8±2.5
9±3
10±3
11±3.5
12±4
6±1.5
6±1.5
8±2.5
9±3
10±3
9±3
10±3
11±3.5
12±4
13±4
7±2
9±3
10±3
11±3.5
11±3.5
12±4
13±4
14±4.5
企业管理部
质检计量部
物资供应部
试验检测中心
研究院
7±2
8±2.5
10±3.5
11±3.5
12±4
8±2.5
11±3.5
12±4
13±4.5
14±5
8±2.5
10±3.5
11±3.5
12±4
13±4.5
锻件棱边各处圆角不应超过相邻边的最小加工余量。
3.2.3长方体锻件的加工余量与公差
长方体锻件的加工余量与公差按图3及表3的规定。
图3
描写
描校
旧底图总号
a
b
a
b
a
b
a
b
a
b
~100
>100~200
>200~300
>300~400
>400~500
>500~600
4±1
4±1
5±1.5
6±1.5
6±1.5
7±2
6±1.5
7±2
8±2.5
9±3
10±3
11±3.5
5±1.5
5±1.5
6±1.5
6±1.5
7±2
- 1、下载文档前请自行甄别文档内容的完整性,平台不提供额外的编辑、内容补充、找答案等附加服务。
- 2、"仅部分预览"的文档,不可在线预览部分如存在完整性等问题,可反馈申请退款(可完整预览的文档不适用该条件!)。
- 3、如文档侵犯您的权益,请联系客服反馈,我们会尽快为您处理(人工客服工作时间:9:00-18:30)。
机械加工余量标准
25EQY —19-1999
1. 主题内容与适用范围
本标准规定了磨削加工的加工余量。
本标准适用于磨削各类材料时的加工余量。
2. 技术内容
加工余量表(一)
说明:
1.二次平面磨削余量乘系数1.5
2.三次平面磨削余量乘系数2
3.厚度4以上者单面余量不小于0.5-0.8
4.橡胶模平板单面余量不小于0.7
毛坯加工余量表(二)
I:园棒类:
(1)的凸模、凹模、凸凹模以及推杆、推销、限制器、托杆、各种螺钉、螺栓、螺塞、螺帽外径必须滚花者。
(毫米)
当D <36时并不适应于调头夹加工,在加工单个工件时,应在L 上加夹头量10-15。
(2)凹模,挡料销、肩台须磨加工的凸模或凸凹模等。
当D <36时,不适合调头加工,在加工单个零件时,应加夹头量10-15。
毛坯加工余量表(三)
(1)例如:固定板、退料板等。
注:表中的加工余量为最小余量,其最大余量不得超过厂规定标准。
毛坯加工余量表(四)
Ⅲ:矩形锻件类:
表内的加工余量为最小余量,其最大余量不得超过厂规定标准。
平面、端面磨削加工余量表(五)一、平面
二、端面
注:
20-40% 如需磨两次的零件,其磨量应适当增加10-20%
环形工件磨削加工余量表(六)
注:
φ50以下,壁厚10以上者,或长度为100-300者,用上限 φ50-φ100,壁厚20以下者,或长度为200-500者,用上限 φ100以上者,壁厚30以下者,或长度为300-600者,用上限 1.3 0.5
φ6以下小孔研磨量表(七)
注:
本表只适用于淬火件
当长度e 小于15毫米时,表内数值应加大20-30%
导柱衬套磨削加工余量表(八)
镗孔加工余量表(九)
附注:当一次镗削时,加工余量应该是粗加工余量加工精加工余量。
表7-1 模具常用加工方法的加工余量、加工精度、表面粗糙度
前道工序的加工结果等具体情况而定。
1. 加工总余量的确定
(1)加工总余量和工序余量
加工总余量(毛坯余量)—毛坯尺寸与零件图设计尺寸之差。
工序余量—相邻两工序的工序尺寸之差。
某个表面加工余量Z∑为该表面各加工工序的工序余量Zi之和,即
式中n—该表面的加工工序数。
(2)影响加工余量的因素
1)加工表面上的表面粗糙度和表面缺陷层深度。
2)加工前或上工序的尺寸公差。
3)加工前或上工序各表面相互位置的空间偏差。
4)本工序加工时的装夹误差。
(3)查表法确定机械加工余量,总余量和半精加工、精加工工序余量可参考有关标准或工艺手册查得,并应结合实际情况加以修正。
粗加工工序余量减去半精加工和精加工工序余量而得到。
2. 工序尺寸及公差计算
对于各种工序的定位基准与设计基准重合时的表面的多次加工(如外圆和内孔的加工),工序尺寸可由后续加工的工序尺寸加工上(对被包容面)或减去(对包容面)公称工序余量而求得;工序尺寸公差按所用加工方法的经济精度选定。
图4-2 表示外圆加工时加工余量、工序尺寸及其公差的分布,图中Z1、Z2、Z3为粗加工、半精加工、精加工的公称余量;To为毛坯公差。
T1 、T2、T3为粗加工、半精加工、精加工的工序尺寸公差。
当各工序的公称余量和公差确定后,卡按下面顺序计算每一工序的工序尺寸;
终加工(精加工)工序尺寸A3,公差T3由零件图规定。
半精加工的工序尺寸A2=A3+ Z3,公差为T2.
粗加工的工序尺寸A1= A2+ Z2,公差为T1。
毛坯尺寸Ao= A1+Z2。
公差为To。
工序尺寸的公差一般应按“入体原则”标注,而在毛坯的基本尺寸上一般都注以双向偏差。
当基准不重合时,或零件在加工过程中需要多次转换工序基准,或工序尺寸尚需在继续加工的表面上标注时,有关工序的工序尺寸及其公差,则需通过尺寸链的分析,计算得到。
3. 机床及工艺装备的选择
(1)机床的选择
1)机床的加工尺寸范围应与工件的外廓尺寸相适应。
2) 机床的工作精度应与工序要求的精度想适应。
3)机床的生产率应与工件的生产类型相适应。
4)机床的选择应考虑工厂的现有设备条件。
如果工件尺寸太大,精度要求过高,没有相应设备可供选择时,就需改装设备或设计专用机床。
(2)工艺装备的选择
1)夹具的选择,在单件小批生产中,应尽量选用通用夹具或组合夹具,在大批大量生产中,应根据工序要求设计专用高效夹具。
2)刀具的选择,主要取决于工序所采用的加工方法,加工表面的尺寸,工件材料,所要求的加工精度和表面粗糙度、生产率及经济性等,一般应尽量选用标准刀具。
3)量具的选择,主要根据生产类型和要求检验的精度。
在单件小批生产中,应尽量采用通用量具量仪,在大批大量生产中,应采用各种极限量规或高生产率的检查量仪。
4. 时间定额及缩减单件时间的措施
(1)时间定额及其组成,时间定额是在一定的生产条件下,规定生产一件产品或完成一道工序所消耗的时间,用td表示。
根据时间定额可以安排作业计划。
进行成本核算。
确定设备设备数量和人员编制,规划生产面积。
因此,时间定额是工艺规程中的重要组成部分。
时间定额主要利用经过实践而积累的统计资料及进行部分计算来确定。
时间定额由以下部分组成:
1)基本时间定额tj 直接改变生产对象的形状、尺寸、相对位置、表面状态或材料性能等工艺过程所消耗的时间。
基本时间定额通常可用计算的方法求出,具体计算公式详见各加工方法章节。
2)辅助时间定额tf 为实现工艺过程所必须进行的各种辅助动作所消耗的时间。
辅助时间定额可根据统计资料来确定,也可以按基本时间的百分数来估算。
基本时间定额与辅助时间定额的总和称为作业时间定额。
3)布置工作地时间定额tb 为使加工正常进行,工人照管工作地(如更换刀具、润滑机床、清理切屑、收拾工具等)所消耗的时间。
布置工作地时间定额一般按作业时间的百分数计算。
4)休息与生理需要时间定额tx 工人在工作班内为恢复体力和满足生理上的需要所消耗的时间。
休息与生理需要时间一般也按作业时间的百分数估算。
5)准备与终结时间定额tz 工人为生产一批数量为N的产品或零、部件,进行准备和结束工作所消耗的时间。
成批生产时的时间定额:
td=tj+tf+tb+tx+
tz:/N
大量生产时的时间定额:
td=tj+tf+tb+tx (2)缩减单件时间的措施
1)缩减基本时间tj的措施,提高切削用量,减少加工余量,缩短刀具的工作行程,采用多刀多刃和多轴机床加工,或采用其他新工艺,新技术。
2)缩减辅助时间tf的措施,尽量使辅助动作实现机械或自动化,如采用先进夹具,提高机床的自动化程度;使辅助时间与基本时间部分地域或全部地重叠起来,如采用多位夹具或多位工作台,采用主动测量或数字显示自动测量装置。
3)缩减布置工作地时间tb的措施,采用耐用度较高的刀具或砂轮,采用各种快换刀夹、刀具微调装置,专用对刀样板和样件以及自动换刀装置。
4)缩减准备与终结时间的措施,采用成组工艺生产组织形式,使夹具和刀具的调整通用化,采用准备终结时间较短的先进设备及工艺装备。