模具强度校核公式.
冲压件模具设计常用公式

冲压件模具设计常用公式1. 材料和工艺参数计算公式1.1 冲击力的计算公式冲击力是冲压件模具设计中重要的参考指标之一,它可以用于确定模具的强度和稳定性。
冲击力的计算公式如下:F = K × A × T × σ其中,F表示冲击力,K表示冲击系数,A表示冲压件的有效面积,T表示冲压时间,σ表示材料的抗拉强度。
1.2 冲床力的计算公式冲床力是指冲床在冲压过程中对工件所产生的压力。
冲床力的计算公式如下:P = F / A其中,P表示冲床力,F表示冲击力,A表示冲压件的有效面积。
1.3 冲压时间的计算公式冲压时间是指冲床一次冲压周期所需的时间。
冲压时间的计算公式如下:T = (L / V) + t其中,T表示冲压时间,L表示冲压件的长度,V表示冲床的下行速度,t表示冲程停留时间。
1.4 最大冲床力的计算公式最大冲床力是指冲床所能承受的最大压力。
最大冲床力的计算公式如下:P_max = K × A × σ其中,P_max表示最大冲床力,K表示冲击系数,A表示冲压件的有效面积,σ表示材料的抗拉强度。
2. 模具结构设计公式2.1 模具剪切强度的计算公式模具剪切强度是指模具在剪切过程中所能承受的最大剪切力。
模具剪切强度的计算公式如下:P_shear = F / A_shear其中,P_shear表示模具剪切强度,F表示冲击力,A_shear表示模具剪切面积。
2.2 模具挤压强度的计算公式模具挤压强度是指模具在挤压过程中所能承受的最大挤压力。
模具挤压强度的计算公式如下:P_extrusion = F / A_extrusion其中,P_extrusion表示模具挤压强度,F表示冲击力,A_extrusion表示模具挤压面积。
2.3 模具弯曲强度的计算公式模具弯曲强度是指模具在弯曲过程中所能承受的最大弯曲力。
模具弯曲强度的计算公式如下:P_bending = F / A_bending其中,P_bending表示模具弯曲强度,F表示冲击力,A_bending表示模具弯曲面积。
模具设计与制造专业毕业论文--U型制件冲压工艺及模具设计

目录第1章绪论 (3)1.1现代模具的地位及其重要性 (3)1.2本次模具设计的重点和难点 (3)第2章冲压件形状和工艺方案分析 (4)2.1工艺性分析 (5)2.2技术、经济综合分析比较和工艺方案的选择 (6)2.2.1 技术、经济综合分析 (6)2.2.2 模具结构型式的合理性分析 (7)2.2.3 工艺方案的确定 (7)第3章落料冲孔复合模的设计 (8)3.1复合模总体结构的初步设计 (8)3.2零件的工艺计算 (9)3.2.1 冲压件的尺寸参数 (9)3.2.2 搭边值的确定 (10)3.2.3 毛坯的排样方式 (10)3.2.4 条料宽度的确定 (11)3.3冲裁力的计算及冲压设备的选择 (12)3.4压力中心计算 (13)3.5凸凹模刃口尺寸确定 (14)3.5.1 冲孔时凸凹模刃口尺寸计算 (14)3.5.2 落料时凸凹模刃口尺寸计算 (15)第4章冲压设备的选用及其参数 (18)第5章冲裁模主要零部件的设计及选用 (19)5.1落料凹模的设计 (19)5.2凸凹模的设计 (21)5.3冲孔凸模的设计 (22)第6章其他零部件的设计及选用 (27)6.1卸料装置的尺寸选择 (27)6.1.1 卸料装置的选择 (27)6.1.2 弹性元件的设计 (27)6.1.3 推件装置的选择 (27)6.2定位零件的选取 (28)6.3模架及其它零件的选择 (28)第7章模具的闭合高度 (30)第8章弯曲模的设计 (31)8.1弯曲工艺性分析 (31)8.1.1 材料分析 (31)8.1.2 结构分析 (31)8.2弯曲件毛坯尺寸的计算 (32)8.3弯曲力计算 (33)8.4弯曲模主要工作零部件的设计 (34)8.4.1 凸凹模圆角半径的确认 (34)8.4.2 凹模工作部分深度 (35)8.4.3 凸、凹模间隙的确定 (36)8.4.4 凸、凹模宽度的计算及其公差 (36)8.5弯曲模的结构设计 (37)8.6弯曲模其它零部件的选用 (37)结论 (40)参考资料: (41)致谢......................................................... 错误!未定义书签。
冲压模具课程设计说明书 2
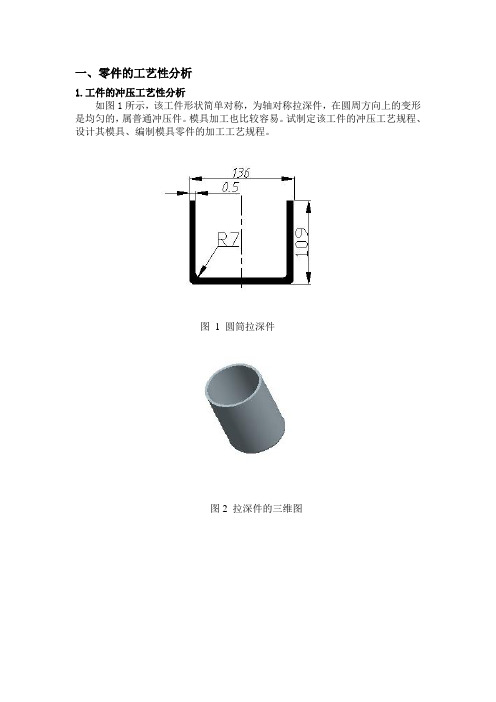
一、零件的工艺性分析1.工件的冲压工艺性分析如图1所示,该工件形状简单对称,为轴对称拉深件,在圆周方向上的变形是均匀的,属普通冲压件。
模具加工也比较容易。
试制定该工件的冲压工艺规程、设计其模具、编制模具零件的加工工艺规程。
图1 圆筒拉深件图2 拉深件的三维图2.工件材料化学成分和机械性能分析(1)材料分析工件的材料为08钢,属于优质碳素结构钢,优质沸腾钢,强度、硬度低,冷变形塑性很好,可深冲压加工,焊接性好。
成分偏析倾向大,时效敏感性大,故冷加工时应采用消除应力热处理或水韧处理,防止冷加工断裂。
08钢的主要机械性能如下:σ(兆帕) 280-390抗拉强度bσ(兆帕) 180屈服强度s抗剪强度(兆帕) 220-310延伸率δ 32%(2)结构分析工件为一窄凸缘筒形件,结构简单,圆角半径为r=7,厚度为t=0.5mm,满足筒形拉深件底部圆角半径大于一倍料厚的要求,因此,零件具有良好的结构工艺性。
(3)精度分析工件上尺寸均为未注公差尺寸,普通拉深即可达到零件的精度要求。
经上述分析,产品的材料性能符合冷冲压加工要求。
在零件工艺性分析的基础上制定其工艺路线如下:零件的生产包括落料、拉深(需计算确定拉深次数)、修边(采用机械加工)等工序,为了提高生产效率,可以考虑工序的复合,经比较决定采用落料与第一次拉深复合。
二、工件的拉深工艺分析及计算1.毛坯尺寸计算(1)计算原则相似原则:拉深前坯料的形状与拉深件断面形状相似;等面积原则:拉深前坯料面积与拉深件面积相等。
(2)计算方法由以上原则可知,旋转体拉深件采用圆形毛坯,其直径按面积相等的原则计算。
计算坯料尺寸时,先将拉深件划分为若干便于计算的简单几何体,分别求出其面积后相加,得拉深件总面积A。
图3 拉深件的坯料计算如图3所示,筒形件坯料尺寸,将圆筒件分成三个部分,每个部分面积分别为:(3)确定零件修边余量由于板料的各向异性和模具间隙不均等因素的影响,拉深后零件的边缘不整齐,甚至出现耳子,需在拉伸后进行修边。
冲压件模具设计的常用公式

冲压件模具设计的常用公式
一、材料力学公式
1.应力公式:σ=F/A,其中σ为应力,F为受力,A为受力面积。
2.应力应变关系公式:σ=E×ε,其中E为杨氏模量,ε为应变。
3.屈服强度公式:σs=F/A0,其中σs为屈服强度,F为屈服点所受力,A0为初始横截面积。
二、材料成形公式
1. 塑性变形公式:ε = ln (h0 / hn) ,其中ε为塑性变形,h0为初始厚度,hn为最终厚度。
2.变形力公式:F=S×σs,其中F为变形力,S为变形面积,σs为屈服强度。
3.针对特定形状的材料成形公式,如直冲材料成形公式、弯曲材料成形公式等。
三、模具设计公式
1.强度计算公式:F=σ×A,其中F为受力,σ为应力,A为受力面积。
2. 弯曲应力公式:σ = M / (W × yc),其中σ为弯曲应力,M为弯矩,W为截面模量,yc为弯曲轴心距离。
四、装配公式
1.装配公差公式:A=A1+A2+A3,其中A为总公差,A1为尺寸公差,
A2为形位公差,A3为相对公差。
五、切削力公式
1. 切削功率公式:P = F × V × kc,其中P为切削功率,F为切
削力,V为切削速度,kc为切削功率系数。
以上是冲压件模具设计中的常用公式,通过这些公式的运用,可以对
冲压件进行力学、成形、模具设计、装配以及切削力等方面的优化和设计。
当然,具体的设计中还需要根据实际情况和不同材料的特性来选择合适的
公式。
模具怎么样确定规格

模具外径确定1.一般在型材外接圆尺寸上加100MM-150MM之间。
(特殊情况除外)2.挤压机的确定多数是按挤压比来计算,这也与铝材厂的要求也有关系,比如一个型材挤压比算下来只有5-10,这种情况设计都会要求铝材厂更换大机台来挤压产品,但是铝材厂对型材只有简单要求,要求模具厂不换压机进行设计。
这时模具厂还是会做下去。
所以现在设计师们很多时候都是按型材厂指定的信息来设计生产模具。
3.对于专用垫的确定,目前有经验的很多设计,都是看下图形就会确定是否开专用垫,但是这个也有理论计算公式。
也就是模具的强度校核。
一般须要开专用垫的模具大多数形状为,半包围形。
7字形。
门字形。
这几类的图型,也就是带有高悬壁的图形,理论计算时超过客户要求的厚度时,设计师们就会要求加做专用垫,现在铝材厂的开模人员,很多都对模具有些了解,他们自己也会注明做专用垫的。
不懂的就只有设计师们提出来了。
其实很多朋友也都知道这些,呵呵不对之处还请各位谅解!新手必备:工业铝型材挤压模具相关培训内容新手必备:工业铝型材挤压模具相关培训内容时间:2011-06-22 16:27来源:aps工业铝型材作者:山东铝型材网www.365a点击: 135 次一、模具的作用模具在挤压成型过程中起着将圆形的铝棒变形为各种形状的铝材的作用。
二、模具的分类铝型材可以分为三大类:一、模具的作用模具在挤压成型过程中起着将圆形的铝棒变形为各种形状的铝材的作用。
二、模具的分类铝型材可以分为三大类:实心材、空心材、半空心材。
◆相应模具按常规也分为平模(实心模),分流模(空心模)◆平模又可分为整体模、导流板+模面(模垫)◆分流模还包括专为半空心材设计的假分流模,封闭台模,还有带前置导流板的三合一分流模。
还根据焊合室在上模还是在下模,又可分为上焊合分流模或下焊合分流模等。
◆根据模孔数目也可以分为单孔模和多孔模。
从图片上进行怎么识别模具类型及其各类型模具的基本结构。
三、挤压模具的结构及要点:◆工作带的高度h定(工作带的高低点) 和直径d定(也称为定径带,即型腔尺寸)工作带是模子中垂直于模具工作端面并用以保证挤压制品的形状、尺寸和表面质量的区段。
冲压模具零部件设计

靠用标准,选择模架的依据。
凹 模 形 式 及 固 定
3.凸凹模 复合模中同时具有落料凸模和冲孔凹模作用的工作零件。 凸凹模的最小壁厚: 正装复合模,内孔不积存废料,胀力小,最小壁厚可以小些; 倒装复合模, 若内孔为直筒形刃口形式,且采用下出料方 式,则内孔积存废料,胀力大,故最小壁厚 应大些。 倒装复合模的凸凹模最小壁厚见表。 正装复合模的凸凹模最小壁厚可比倒装的小些。
3.导柱和导套零件导向装置
(1)导柱 (2)导套
导柱导套的配合间隙:必须小于冲裁间隙 冲裁间隙小的一般应 按H6/h5配合;间隙较大的按H7/h6配合。 导柱导套的长度:据模具闭合高度,一般应符合相关要求。 导柱导套制造、安装要求:采用H7/r6压入模座的安装孔; 材料:20钢表面渗碳,淬火硬度58~62HRC
工作原理:
特点:推件力大,工作可靠
刚性推件装置
1-打杆 2-推板 3-连接推杆 4-推件块
推板
1-打杆 2-模柄 3-推板 4-推杆 5-卸料螺钉 6-凸凹模 7-卸料板 8-落料凹模 9-顶件块 10-带肩顶杆 11-冲孔凸模 12-挡料销 13-导料销
正装式复合模
动画
弹 性 推 件 装 置
1-橡胶 2-推板 3-连接推杆 4-推件块
(2)顶件装置 组成:顶杆、顶件块和装在下模底下的弹顶器 特点:顶件力容易调节,工作可靠,冲件平直度较高 制造、装配要求:①模具处于开启状态时,必须顺利复位,工作 面高出凹模平面,以便继续冲裁; ②模具处于闭合状态时,其背后有一定空间, 以备修磨和调整的需要;
级进模
配合使用: 与挡料销或与侧刃配合使用
后者粗定位,前者精定位
结构组成
导入部分:圆锥形的头部 导正部分:圆柱形的
冲压件模具设计的常用公式

冲压件模具设计的常用公式1. 强度和刚度计算公式1.1 拉伸强度计算冲压件在工作过程中会受到拉伸力的作用,因此计算冲压件的拉伸强度是非常重要的。
拉伸强度的计算公式如下:F = σ × A其中,F表示拉伸力,σ表示材料的抗拉强度,A表示冲压件的截面积。
1.2 刚度计算刚度是指冲压件在受力下的变形程度,计算冲压件的刚度可以确定其在工作过程中是否会发生过度变形。
刚度的计算公式如下:K = (E × A) / L其中,K表示刚度,E表示材料的弹性模量,A表示冲压件的截面积,L表示冲压件的长度。
2. 冲压参数计算公式2.1 冲头压力计算冲头压力是冲压件在冲床上受到的压力,计算冲头压力可以确定冲床的最小压力要求。
冲头压力的计算公式如下:P = F / A其中,P表示冲头压力,F表示冲压件的拉伸力,A表示冲头的截面积。
2.2 厚度计算冲压件的厚度是冲压件的重要参数之一,计算冲压件的厚度可以确定其制备过程中所需的原材料量。
厚度的计算公式如下:t = V / (A × L)其中,t表示冲压件的厚度,V表示冲压件的体积,A表示冲压件的截面积,L表示冲压件的长度。
3. 离型力计算公式冲压件在离型过程中需要克服一定的摩擦力,计算离型力是确定冲压模具设计是否合理的重要指标。
离型力的计算公式如下:F = μ × N其中,F表示离型力,μ表示冲压件和模具之间的摩擦系数,N表示冲压件的法线力。
4. 寿命计算公式冲压模具在工作过程中会受到疲劳载荷的影响,因此计算冲压模具的寿命可以指导模具的选材和使用。
寿命的计算公式如下:N = (S / K) × (F / σf)^b其中,N表示模具寿命的预测次数,S表示冲压次数,K表示对应于S次冲压的磨损系数,F表示冲压力,σf表示冲压件的疲劳强度,b表示指数。
结论以上是冲压件模具设计过程中常用的计算公式。
这些公式可以帮助工程师在设计冲压模具时进行强度、刚度、参数和寿命等方面的计算,以确保模具的设计合理和稳定性。
粉末压制成形模具设计

表1金属粉末压制成形坯料计算
计算内容
定义或计算公式
有关说明
压制坯在垂直于压制
压制坯面积Fp(cm2) 方向的平面的投影面
-
积
压制坯体积Vp(cm3)
Vp=(1+ξ/100)Ve
芯棒磨损余 量
Δd=dn′-dn-δa δa—芯棒尺寸实际偏差量
后续精压芯
=dmax±lrp
棒直径(孔 “+”—精压后回弹使孔径减小时
件) “-”—精压后回弹使孔径增大时
烧结坯内尺 寸
压制坯内尺 寸
ds=drp±ηrp “+”—为负偏差精压时
“-”—为正偏差精压时
dp=ds±ε “+”—烧结后内尺寸减小时 “-”—烧结后内尺寸增大时
2.凹模预应力圈尺寸
为了提高压制成形模具的寿命,并
保证压制件的尺寸精度,凹模常采用预
应力圈结构,如图2所示。其尺寸取决于
压制时凹模内壁所承受的侧压力大小。
对于铁粉末压制,其侧压力可按经验公
式估算:
pc=Ccρmp
(9)
式中Cc=0.00725,m=6.8
而预应力圈的尺寸,必须保证凹模具有最大刚度,设凹模筒内半径为r1, 则有:
其他参数
而在进行压制成形模具设计时,还需知道以下 参数:
(1)预先给定的粉末压制坯的密度ρp; (2)压制(和后续塑性加工)后制件线回弹量,用相 对值αp(αrp)或绝对量lp(lrp)表示; (3)制件烧结后的线收缩量,用相对值β或绝对量 ε表示; (4)烧结氧化或其他原因引起的质量损耗量,用 相对值ζ表示; (5)后续塑性加工引起的制件密度增加量,用相 对值τ表示。
变压器用花瓶外压模具强度校核公式
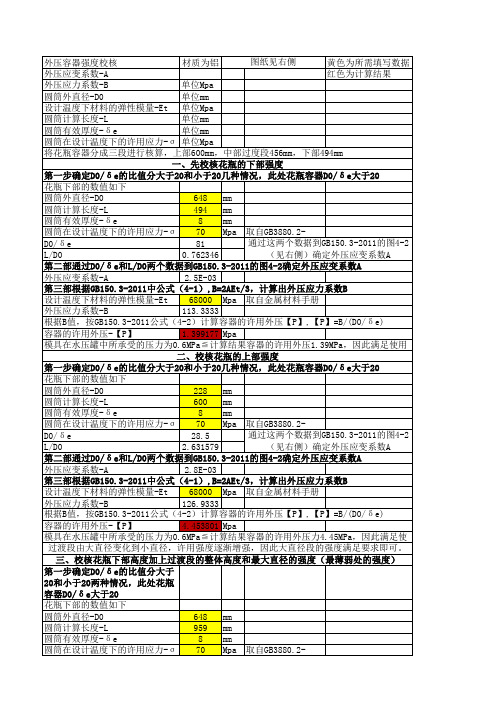
外压容器强度校核材质为铝黄色为所需填写数据外压应变系数-A 红色为计算结果外压应力系数-B 单位Mpa圆筒外直径-D0单位mm设计温度下材料的弹性模量-Et 单位Mpa圆筒计算长度-L 单位mm圆筒有效厚度-δe 单位mm圆筒在设计温度下的许用应力-σt 单位Mpa花瓶下部的数值如下圆筒外直径-D0648mm圆筒计算长度-L 494mm圆筒有效厚度-δe 8mm圆筒在设计温度下的许用应力-σt 70Mpa 取自GB3880.2-2012D0/δe 81L/D00.762346外压应变系数-A 2.5E-03设计温度下材料的弹性模量-Et 68000Mpa 取自金属材料手册外压应力系数-B 113.3333容器的许用外压-【P】 1.399177Mpa花瓶下部的数值如下圆筒外直径-D0228mm圆筒计算长度-L 600mm圆筒有效厚度-δe 8mm圆筒在设计温度下的许用应力-σt 70Mpa 取自GB3880.2-2012D0/δe 28.5L/D0 2.631579外压应变系数-A 2.8E-03设计温度下材料的弹性模量-Et 68000Mpa 取自金属材料手册外压应力系数-B 126.9333容器的许用外压-【P】 4.453801Mpa第一步确定D0/δe的比值分大于20和小于20两种情况,此处花瓶容器D0/δe大于20花瓶下部的数值如下圆筒外直径-D0648mm圆筒计算长度-L 959mm圆筒有效厚度-δe 8mm圆筒在设计温度下的许用应力-σt 70Mpa 取自GB3880.2-2012D0/δe 81L/D0 1.479938将花瓶容器分成三段进行核算,上部600mm,中部过度段456mm,下部494mm图纸见右侧第三部根据GB150.3-2011中公式(4-1),B=2AEt/3,计算出外压应力系数B第二部通过D0/δe和L/D0两个数据到GB150.3-2011的图4-2确定外压应变系数A模具在水压罐中所承受的压力为0.6MPa≦计算结果容器的许用外压1.39MPa,因此满足使用条件一、先校核花瓶的下部强度二、校核花瓶的上部强度通过这两个数据到GB150.3-2011的图4-2(见右侧)确定外压应变系数A 第二部通过D0/δe和L/D0两个数据到GB150.3-2011的图4-2确定外压应变系数A第一步确定D0/δe的比值分大于20和小于20几种情况,此处花瓶容器D0/δe大于20第一步确定D0/δe的比值分大于20和小于20几种情况,此处花瓶容器D0/δe大于20通过这两个数据到GB150.3-2011的图4-2(见右侧)确定外压应变系数A 根据B值,按GB150.3-2011公式(4-2)计算容器的许用外压【P】,【P】=B/(D0/δe)第三部根据GB150.3-2011中公式(4-1),B=2AEt/3,计算出外压应力系数B根据B值,按GB150.3-2011公式(4-2)计算容器的许用外压【P】,【P】=B/(D0/δe)模具在水压罐中所承受的压力为0.6MPa≦计算结果容器的许用外压力4.45MPa,因此满足使用条过渡段由大直径变化到小直径,许用强度逐渐增强,因此大直径段的强度满足要求即可。
机械零件设计强度校核常用计算公式
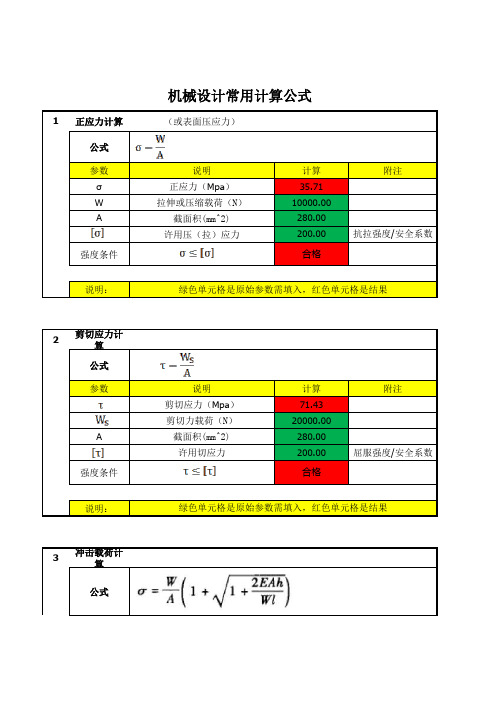
说明 扭转切应力(MPa) 施加在轴上的最大扭矩(N*mm) 扭转截面系数(mm^3)
外径(mm) 内径(mm) 许用切应力
计算 117.38 10000000.00 85191.16 80.00 50.00 200.00
合格
附注 屈服强度/安全系数
说明:
绿色单元格是原始参数需填入,红色单元格是结果
说明 冲击载荷产生的应力(MPa)
冲击力(N) 作用面积(mm^2) 弹性模量(Mpa)
冲击距离(mm) 物体长度(mm)
计算 4.62 4410.00 70650.00 1000.00 1000.00 6000.00
附注 常数
绿色单元格是原始参数需填入,红色单元格是结果
3 轴扭转强度计算
公式
参数
T Wp D d
4 弯曲强度计算 公式 参数
说明 弯曲应力(MPa)
计算 198.94 240.00
附注 圆形截面 矩形截面
WZ D d b h 强度条件
说明:
弯矩(N*mm) 抗弯截面系数(mm^3) 抗弯截面系数(mm^3)
外径(mm) 内径(mm) 宽度(mm) 长度(mm)
许用弯曲应力
10000000.00 50265.48 41666.67 80.00 50.00 100.00 50.00 合格 合格 300.00
圆形截面 矩形截面
屈服强度/安全系数
绿色单元格是原始参数需填入,红色单元格是结果
· · ·
实心圆截面 空心圆截面
•圆截面扭转截面系数
Wp
Ip R
D3 · 16
Wp
ቤተ መጻሕፍቲ ባይዱIp R
I p D3 (1 4 )
模具尺寸及强度估算

本章将介绍型芯变形(弯曲)的基本计算方法。
悬臂梁结构的最大挠度(δmax)利用下式计算。
(1)假定型芯前端有集中负载
δmax= WI3 3EI
δmax:最大挠度(cm) W: 集中负载(kgf) E: 纵向弹性模量(kgf/cm2) I: 截面抗弯惯量(cm4)
【图1】
X
h
台肩
安装螺孔
【图1】中的侧壁厚度h可由下式求得。
h= 12×p×l 4×a 384×E×b×σmax
这里: h: 定模侧壁厚度(mm) p: 定模内压强(kgf/cm2) l : 定模内侧长度(mm) a: 定模内压强p承受部位侧壁的高度(mm) b: 定模高度(mm) E: 纵向弹性模量(杨氏模量)(kgf/cm2) σmax: 最大容许挠度(mm)
L=35mm
h=2.5mm b=12mm 型芯
型芯固定板
垫板 模板
9
第8章 模具零部件的热膨胀
本章将介绍注塑成型模具零部件热膨胀的基本知识。
为了保持适当的定模表面温度,将注塑成型模具保温在30~150℃范围内。 另一方面,熔化树脂流入浇口、流道、定模型腔,模具受到180~300℃左右高温树脂所传来的热量。 通常温度上升时金属发生热膨胀。因此,注塑成型模具的零部件也发生热膨胀。 热膨胀有时会导致:影响导柱导套的配合、侧抽芯滑块滑动不顺畅、型芯尺寸胀大。
p:定模内压强(kgf/cm2)
h:支承板厚度(mm)
E:材料的纵向弹性模量(杨氏模量)(kgf/cm2)
l:定模承受内压p部分的长度(mm) σmax:支承板的最大挠度(mm)
凸凹模强度校核公式
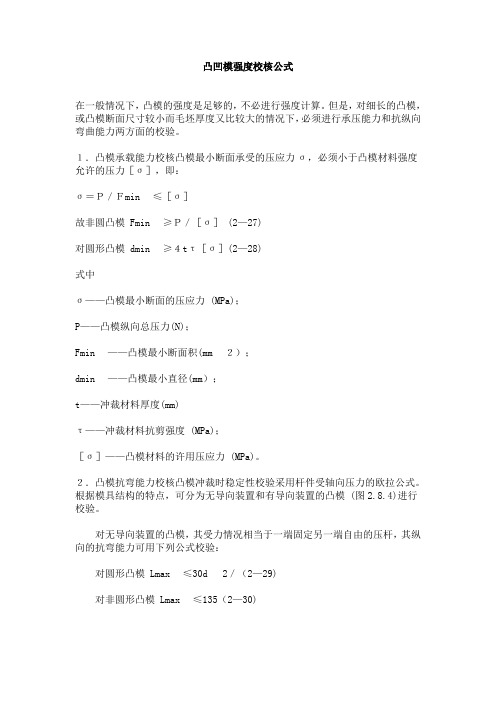
凸凹模强度校核公式在一般情况下,凸模的强度是足够的,不必进行强度计算。
但是,对细长的凸模,或凸模断面尺寸较小而毛坯厚度又比较大的情况下,必须进行承压能力和抗纵向弯曲能力两方面的校验。
1.凸模承载能力校核凸模最小断面承受的压应力σ,必须小于凸模材料强度允许的压力[σ],即:σ=P/Fmin≤[σ]故非圆凸模 Fmin≥P/[σ] (2—27)对圆形凸模 dmin≥4tτ[σ](2—28)式中σ——凸模最小断面的压应力 (MPa);P——凸模纵向总压力(N);Fmin——凸模最小断面积(mm2);dmin——凸模最小直径(mm);t——冲裁材料厚度(mm)τ——冲裁材料抗剪强度 (MPa);[σ]——凸模材料的许用压应力 (MPa)。
2.凸模抗弯能力校核凸模冲裁时稳定性校验采用杆件受轴向压力的欧拉公式。
根据模具结构的特点,可分为无导向装置和有导向装置的凸模 (图2.8.4)进行校验。
对无导向装置的凸模,其受力情况相当于一端固定另一端自由的压杆,其纵向的抗弯能力可用下列公式校验:对圆形凸模 Lmax≤30d2/(2—29)对非圆形凸模 Lmax≤135(2—30)图 2.8.4 凸模的自由长度(a)无导向装置的凸模(b)有导向装置的直通式凸模 (c)有导向装置的阶梯式凸模有导向装置的凸模,其不发生失稳弯曲的凸模最大长度为:对圆形凸模 Lmax≤85d2/P (2—31)对非圆形凸模 Lmax≤380 (2—32)以上各式中, I为凸模最小截面的惯性距(mm4);P为凸模的冲裁力(N);d为凸模最小直径(mm)。
据上述公式可知,凸模弯曲不失稳时的最大长度 Lmax ,与凸模截面尺寸、冲截力的大小、材料机械性能等因素有关。
同时还受到模具精度、刃口锋利程度、制造过程、热处理等影响。
为防止小凸模的折断,常采用如图 2.8.5所示的结构进行保护。
(五)凸模的护套图 2.8.5a、b是两种简单的圆形凸模护套。
图a所示护套1、凸模2均用铆接固定。
模具强度校核公式

2.三板模导柱强度校核
L1 150 L2 25 吊りピンのたわみ量(0.2mm以下のこと) d 縦 横 厚み たわみ量 #REF! 0 #REF! mm 0.042 mm 16 180 150 40
3.侧壁变形量的校核
A 135 L 654 側壁のたわみ量(0.02mm以下のこと) H L/A C:定数 射出圧 たわみ量 #DIV/0! #REF! #REF! mm 0.010 mm 98 4.8 0.142 350
PS
300
4 3
max
PP
(200~) 300
AS
350
PC
(400~) 500
PMMA
300
变性 PPO
350
PC+ABS
400
(200~) (300~) 400 400
400 (~500)
注﹕1>如果是+GF料﹐內压再加 50. 3.计算表格﹕
A 480 B 850 C 450 D 120 E 130
L1 150 L2 25 最大变形量应在0.2MM以下 d 縦 横 厚み #REF! 0 16 180 150 40 变形量 #REF! mm 0.042 mm
计算表格使用说明﹕请双击下列表格﹐请勿拖动﹐直接填上数值﹐填好后在表格外面任意点击一下。
1.计算公式﹕
型腔侧壁的校核
σ
P P
max
=
C。P。A 4 E。h
2>模板变形量应在 0.1mm以下
变形量应在0.1MM以下 F 射出圧 变形量・1 变形量・2 #DIV/0! mm #DIV/0! mm 322 350 0.084 mm 0.152913 mm
计算表格使用说明﹕请双击下列表格﹐请勿拖动﹐真接填上数值﹐填好后在表格外面任意点点一下。
模具强度计算
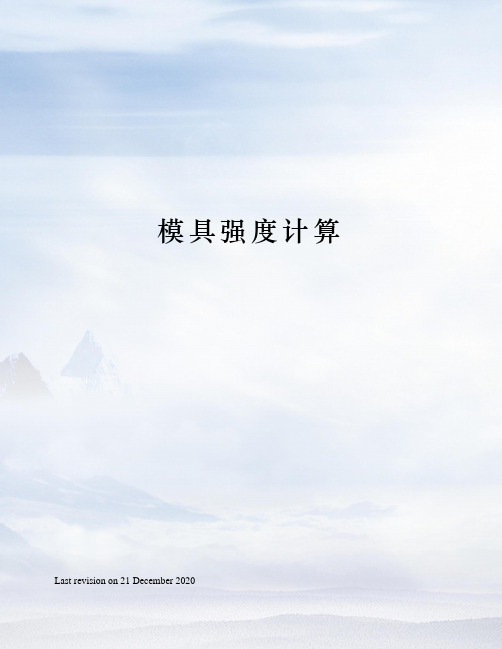
模具强度计算Last revision on 21 December 2020
模具强度计算
1.公,母模仁的水路离成品的铁料至少10mm以上﹐成品到模仁边的铁料至少20mm以上。
2.母模板厚(h)=2倍母模仁厚(H)。
3.公模板厚(h)=倍公模仁厚(H)。
4.公,母模板的模框铁料至少50mm以上。
5.当公模有滑块时﹐公模板上挡模仁(高度方向h) 的铁料至少12mm以上﹐宽度方向的铁料至少5mm以上﹐当整体挡模仁的铁料很少时﹐滑块压块后的铁料应保留﹐做紧配。
母模板上因有滑块束块孔﹐它所剩铁料应为束块伸入高度的倍. 滑块束块伸入高度一般为12~25mm.当铁料越少时﹐伸入值应取小些﹐以保证强度。
附﹕仅供参考。
- 1、下载文档前请自行甄别文档内容的完整性,平台不提供额外的编辑、内容补充、找答案等附加服务。
- 2、"仅部分预览"的文档,不可在线预览部分如存在完整性等问题,可反馈申请退款(可完整预览的文档不适用该条件!)。
- 3、如文档侵犯您的权益,请联系客服反馈,我们会尽快为您处理(人工客服工作时间:9:00-18:30)。
300
樹脂 名 內壓
2.參考表 格﹕
PA
σ
PET PBT
400 (~500)
max
=
=
ABS
350
PP
(200~) 300
AS
350
PC
(400~) 500
PMMA
300
變性 PPO
350
PC+ABS
400
(200~) (300~) 400 400
注﹕1>如果是+GF料﹐內壓再加 50. 3.計算表格﹕
公模板強度校核
公模仁(CORE)
B A
σ
max
D E1 =
5 x 射出壓 x A x C x F 3 4 A x D3 B x E3 384 x 2.1 x10 ( + 12 ) 12 3 5 x 射出壓 x F 32 x 2.1 x10 x E
PS
3004 3=Fra bibliotek5W。I 3 384E。I 5W。I 4 32E。h 4
計算表格使用說明﹕請雙擊下列表格﹐請勿拖動﹐直接填上數值﹐填好后在表格外面任意點擊一下。
計算表格(備份)
1.公模板強度校核表格
コア・プレートのたわみ量(たわみ量・1:0.1mm以下のこと)
射出圧 たわみ量・1
たわみ量・2
480
850
450
120
130
322
350
#DIV/0! mm 0.084 mm
#DIV/0! 0.152913
mm mm
2.三板模導柱強度加核
L1 150 L2 25 吊りピンのたわみ量(0.2mm以下のこと) d 縦 横 厚み たわみ量 #REF! 0 #REF! mm 16 180 150 40 0.042 mm
3.側壁變形量的校核
A 135 L 654 側壁のたわみ量(0.02mm以下のこと) H L/A C:定数 射出圧 たわみ量 #DIV/0! #REF! #REF! mm 98 4.8 0.142 350 0.010 mm
2 1
)
2.計算表格﹕
L1 150 L2 25 吊りピンのたわみ量(0.2mm以下のこと) d 縦 横 厚み たわみ量 #REF! 0 #REF! mm 16 180 150 40 0.042 mm
計算表格使用說明﹕請雙擊下列表格﹐請勿拖動﹐直接填上數值﹐填好后在表格外面任意點擊一下。
型腔側壁的校核
2>模板變形量應在 0.1mm以下
コア・プレートのたわみ量(たわみ量・1:0.1mm以下のこと)
射出圧 たわみ量・1
たわみ量・2
480
850
450
120
130
322
350
#DIV/0! mm 0.084 mm
#DIV/0! 0.152913
mm mm
計算表格使用說明﹕請雙擊下列表格﹐請勿拖動﹐直接填上數值﹐填好后在表格外面任意點擊一下。
導柱的強度校核
T C H
備注﹕ σ
l 200 W
max
: 0.2 mm 以下
/ 64 : πD 4 : 母模板重量 W/4
00
01
S L
1
02
L 2 = H/2
W
ω ﹕ E
: 彈性系數(2.1 x 10 Kgf / mm )
2
4
2
σ
1.計算公 ω 。L 1 式﹕ max = 3E。l
(
1+
3L 2L
P P
1.計算公 式﹕
σ
A
max
=
C。P。A 4 E。h
3
L
2.參考表 格﹕ L/A 1.0 C
0.044
H
1.2
0.062
1.4
0.078
1.6
0.090
1.8
0.102
2.0
0.111
3.0
0.134
4.0
0.140
5.0
0.142
3.參考表格﹕
A 135 L 654 側壁のたわみ量(0.02mm以下のこと) H L/A C:定数 射出圧 たわみ量 #DIV/0! #REF! #REF! mm 98 4.8 0.142 350 0.010 mm