电解槽低电压和低效应工作方案(报送稿)
200 kA 铝电解槽低电压生产技术实践
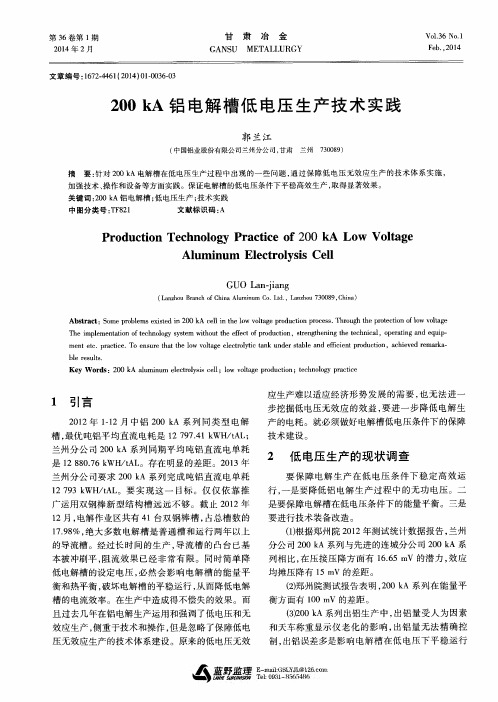
行, 一是要降低铝 电解生产过程 中的无功电压 。二
是要 保 障电解槽 在 低 电压条 件下 的能 量平衡 。三是 要 进行技 术装 备改 造 。 ( 1 ) 根 据郑 州 院 2 0 1 2年测 试统 计数 据报 告 , 兰州 分公 司 2 0 0 k A系列 与先 进 的连城 分公 司 2 0 0 k A 系 列相比, 在 压 接 压 降方 面 有 1 6 . 6 5 mV 的潜力 , 效 应 均 摊压 降有 1 5 m V 的差距 。 ( 2 ) 郑州 院测试 报 告表 明 , 2 0 0 k A系 列在 能 量 平
技 术建设 。
槽, 最优 吨 铝平 均 直流 电耗 是 1 2 7 9 7 . 4 1 k WH / t A L;
Hale Waihona Puke 兰州分公 司 2 0 0 k A系列同期平均吨铝直流电单耗
是 1 2 8 8 0 . 7 6 k WH / t A L 。存 在 明显 的差距 。2 0 1 3年
bl e r e s ul t s .
Ke y Wo r d s:2 0 0 k A a l u mi n u m e l e c t r o l y s i s c e l l ;l o w v o l t a g e p r o d u c t i o n;t e c h n o l o g y p r a c t i c e
1 引言
2 0 1 2年 1 — 1 2月 中 铝 2 0 0 k A 系列 同 类 型 电 解
应 生产难 以适 应 经 济形 势 发 展 的 需要 , 也无 法进 一
步挖掘低 电压无效应 的效益 , 要进一步降低 电解生
电解槽两高一低方案
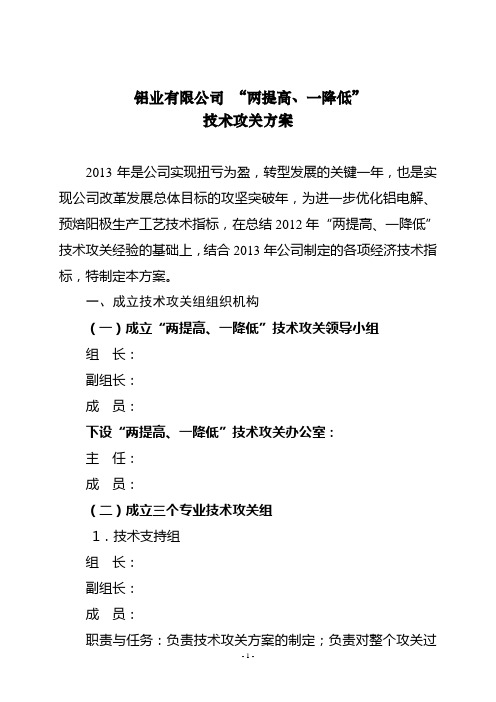
铝业有限公司“两提高、一降低”技术攻关方案2013年是公司实现扭亏为盈,转型发展的关键一年,也是实现公司改革发展总体目标的攻坚突破年,为进一步优化铝电解、预焙阳极生产工艺技术指标,在总结2012年“两提高、一降低”技术攻关经验的基础上,结合2013年公司制定的各项经济技术指标,特制定本方案。
一、成立技术攻关组组织机构(一)成立“两提高、一降低”技术攻关领导小组组长:副组长:成员:下设“两提高、一降低”技术攻关办公室:主任:成员:(二)成立三个专业技术攻关组1.技术支持组组长:副组长:成员:职责与任务:负责技术攻关方案的制定;负责对整个攻关过程技术条件的测试和检测分析;负责对各电解系列的技术状况评估,并及时提出技术条件改善方向和建议;负责每月的技术攻关阶段性总结,组织召开月度小结会议和季度总结会。
2.电解、炭素专业技术攻关组组长:副组长:成员:职责与任务:负责电解、碳素专业技术攻关措施的落实与实施、并对实施过程中出现的问题进行协调处理。
按技术攻关办公室提出的工艺技术路线和改善方向,实施制定的各项攻关措施。
与另外两个攻关专业组协作完成总体攻关方案。
3.能源、设备、原料专业攻关组组长:副组长:成员:职责与任务:负责2013年三个电解系列167台电解槽推广“双钢棒技术”进行电解槽大修的施工,在施工过程中严格执行各项技术规范并达到技术标准;负责动力能耗、装备及供应专业技术措施的落实。
与另外两个攻关专业组协作完成总体攻关方案措施的实施。
二、2013年技术攻关的总体目标:(一)技术攻关总目标1.原铝质量目标:2.电解电流效率目标:3.电解工艺电耗、产品综合电耗目标:(二)技术攻关措施1.深化运营转型,提升管理水平。
持续推进电解二厂一工区,电解四厂二、七工区及炭素厂煅烧、成型、焙烧和组装各环节工艺能力的有效提升。
技术支持组和各专业攻关组强化对电解、炭素生产过程的检测、监控为工艺调整提供强有力的数据支持。
通过对电解槽的氧化铝浓度、电解温度、过热度、上下水平等工艺技术参数的测试,炭素的原料、煅前料、锻后料和阳极炭块理化指标的测试检测分析,确定电解、炭素工艺技术条件的调整方向,并不断完善技术规范,为电解和炭素工艺优化提供数据支持。
铝电解槽低电压低效应系数生产实践
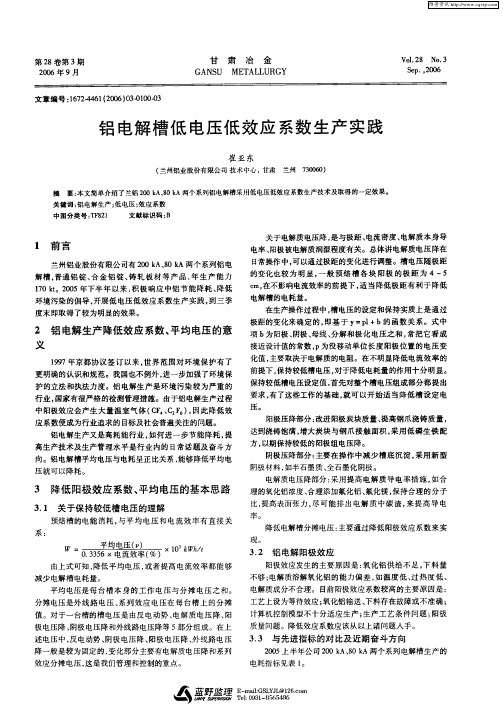
关 于电解质电压 降 , 是与极距 、 电流密度 、 电解质 本身导
l 翮 昌 兰州铝业股份有 限公 司有 20k 8 A两个系列铝电 0 A、0k
电率 、 阳极被 电解质润湿程度有关。总体讲 电解 质电压降在
日常操作 中, 可以通过极距的变化进行调整。槽 电压随极距
分摊 电压是外线 路 电压 、 系列效 应 电压在 每 台槽 上 的分摊
值。对于一台槽的槽电压 是由反 电动势 、 电解质 电压降 、 阳 极 电压降 、 阴极 电压降和外线路电压降等 5部分组成 。在上 述 电压中 , 电动势 、 反 阴极 电压降、 阳极 电压 降 、 线路 电压 外 降一般是较为 固定 的 , 变化部分主要有电解质 电压降和 系列
效应分摊 电压 , 这是我们管理和控制的重 点。
3 3 与先进 指标 的对 比及近 期奋 斗方 向 .
2 0 半 年 公 司 2 0k 8 A两 个 系 列 电解 槽 生 产 的 05上 0 A、0k 电 耗 指 标 见表 1 。
E- aIGS J @ I 6 c m m i: L Y L 2 .0
电解质电压降部分 : 采用提 高电解 质导 电率措 施 , 如合
3 降低 阳极效应 系数 、 平均 电压的基本 思路
3 1 关 于保持 较低 槽 电压 的理解 .
预焙槽的 电能 消耗 , 平均 电压 和 电流效 率有 直接 关 与
系:
理 的氧化铝浓度 、 合理添加氟化铝 、 氟化镁 , 保持合理 的分子 比, 提高表面张 力 , 可能 排 出电解 质 中碳 渣 , 尽 来提 高导 电
在生产操作 过程中 , 槽电压的设定 和保 持实质上 是通过
240kA铝电解槽低电压生产实践分析

电解铝 工业 作 为 高能 耗 产 业 ,近 年来 已成 为 国
家 宏 观 调 控 的 重 点 行 业 。 2009年 5月 ,国 务 院 发 布
了《有 色 金 属 产 业 调 整 和 振 兴 规 划 》,提 出 了 2011
年重 点 骨 干 电解 铝 厂 吨 铝 直 流 电 耗 要 降 到 12 500
摘 要 降 低 槽 电压 是 当前 铝 电 解 行 业 实 现 节 能 生 产 的 主 要 途 径 。 通 过 对 某 企 业 240kA 系 列 电 解 槽 电 压 平 衡 进 行 分 析 ,指 出槽 电 压 下 降 的潜 力 主 要 在 于 电 解 质 压 降 的 降 低 ;而 降 低 电 解 质 压 降 的 主 要 途 径 是 降 低 极 距 及 提 高 分 子 比 。经 过 一 年 的 生 产 实 践 ,该 系 列 平 均 电 压 降 低 至 3.915V,2011年 每 吨 铝 直 流 电耗 相 比 2010年 降 低 了 170 kW ·h,节 电 效 果 明 显 。 关 键 词 电解 槽 ;低 电压 ;电解 质 压 降 ;极 距 ;直 流 电 耗 中 图分 类 号 :TF803.2 7 文 献 标 识 码 :A 文 章 编 号 :1671—3818(2012)03—0004—05
200kA预焙铝电解槽降低工作电压的生产实践

3 提高电解质的导 电性
已知电解质压降 占槽 电压 的 3 % 一 J , 同极距 、 5 4% 它 D 电
关键词 : 电解槽 ; 分子 比; 工作 电压
中 图分 类 号 :F 2 T8 1 文 献标 识 码 : B
Pr c ie n Re cn la e o 0 A e ba ng Al m i i d to ls a tc so du i g Vot g f2 0 k Pr - ki u n um Re uci n面 的原因 , 必须保持较高的工作电压才能维持相应 的 热平衡 , 因而多消耗 了一部分 电能 。
另外一个原 因是 , 由于技术 条件 的匹配不合 理 。 造成 了
两水平 的波动较大 , 表现为铝水的忽高忽低 和电解质水平 的 不稳定 。按 照设计 , 水保持 l 铝 8—2 m, 0c 电解质保持 2 0— 2 m。铝水过 高 , 2c 会造成炉底变冷 , 使炉底容易生成 沉淀或 结壳 , 使炉底压降增大 ; 电解质水平偏低时 , 溶解氧化铝 的能 力降低 , 氧化铝 沉淀生 成 的机率 增加 , 终炉 底 状况 恶化 。 最 由于炉底沉 淀和结 壳均增 加 电压 降, 论是 那种 情 况造 成 不
v la e. otg
Ke r s au nu r u t n c H ;moe ue r t ;v l g y wo d : l mi m e c i e s d o lc l ai o ot e a
1 前 言
浅谈306kA电解槽降低黑电压的生产实践
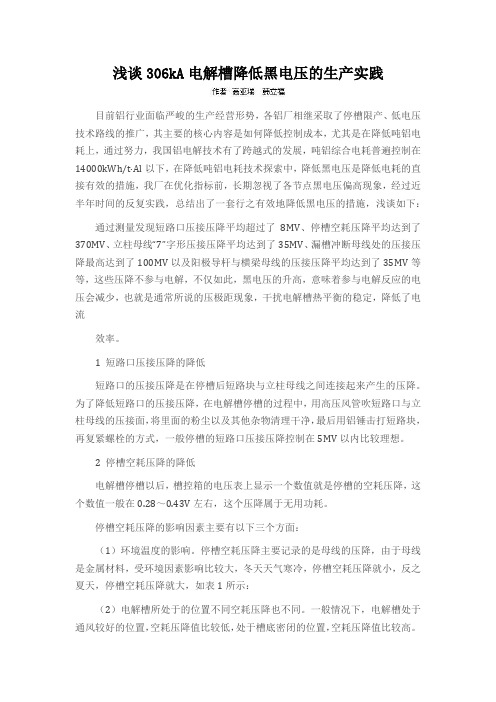
浅谈306kA电解槽降低黑电压的生产实践目前铝行业面临严峻的生产经营形势,各铝厂相继采取了停槽限产、低电压技术路线的推广,其主要的核心内容是如何降低控制成本,尤其是在降低吨铝电耗上,通过努力,我国铝电解技术有了跨越式的发展,吨铝综合电耗普遍控制在14000kWh/t·Al以下,在降低吨铝电耗技术探索中,降低黑电压是降低电耗的直接有效的措施,我厂在优化指标前,长期忽视了各节点黑电压偏高现象,经过近半年时间的反复实践,总结出了一套行之有效地降低黑电压的措施,浅谈如下:通过测量发现短路口压接压降平均超过了8MV、停槽空耗压降平均达到了370MV、立柱母线“7”字形压接压降平均达到了35MV、漏槽冲断母线处的压接压降最高达到了100MV以及阳极导杆与横梁母线的压接压降平均达到了35MV等等,这些压降不参与电解,不仅如此,黑电压的升高,意味着参与电解反应的电压会减少,也就是通常所说的压极距现象,干扰电解槽热平衡的稳定,降低了电流效率。
1 短路口压接压降的降低短路口的压接压降是在停槽后短路块与立柱母线之间连接起来产生的压降。
为了降低短路口的压接压降,在电解槽停槽的过程中,用高压风管吹短路口与立柱母线的压接面,将里面的粉尘以及其他杂物清理干净,最后用铝锤击打短路块,再复紧螺栓的方式,一般停槽的短路口压接压降控制在5MV以内比较理想。
2 停槽空耗压降的降低电解槽停槽以后,槽控箱的电压表上显示一个数值就是停槽的空耗压降,这个数值一般在0.28~0.43V左右,这个压降属于无用功耗。
停槽空耗压降的影响因素主要有以下三个方面:(1)环境温度的影响。
停槽空耗压降主要记录的是母线的压降,由于母线是金属材料,受环境因素影响比较大,冬天天气寒冷,停槽空耗压降就小,反之夏天,停槽空耗压降就大,如表1所示:(2)电解槽所处于的位置不同空耗压降也不同。
一般情况下,电解槽处于通风较好的位置,空耗压降值比较低,处于槽底密闭的位置,空耗压降值比较高。
低电压管理在电解铝生产中的实践与分析

低电压管理在电解铝生产中的实践与分析电解铝生产是现代工业的重要领域之一,其过程需要对电力系统进行严格的管理,以确保产量和安全生产。
低电压管理作为电解铝生产中的一项重要措施,对于保证电力系统的稳定运行及生产效率的最大化具有重要意义。
在电解铝生产中,低电压管理的主要目的是避免电解槽电压过低、电流过大、氧气发生剧烈反应,造成电解槽内的阳极过度腐蚀,从而降低电解槽寿命、增加生产成本和环保压力。
常见的低电压问题包括电解槽电压过低、电解槽电流不稳定、气体发生异常等。
为了解决这些问题,低电压管理需要从以下几个方面入手:1. 对电力系统的监控和维护。
通过实施维护计划,检查和防范电力系统故障,及时解决电网与变电站设备、配电网络、自动化技术等方面的故障问题。
2. 对负荷的调控。
通过对负荷进行有效的调节,合理的安排电力供应,避免负荷过大或过小,从而降低电解槽电压波动。
3. 电解槽操作的管理。
定期对电解槽进行调整和维护,确保电解槽内的阳极和阴极符合标准,防止阳极过度腐蚀和气泡过于积聚等问题。
4. 对气体的管理。
通过合理的气体流量和气波清除,避免气体在电解槽内积聚过多,发生异常反应造成过低的电解槽电压。
上述管理措施需要在实践中不断优化和升级,因为低电压管理不仅要解决当前的问题,还需要预防未来可能出现的问题。
需要注意的是,在实际操作中,还需要做好数据记录和分析,以便及时发现和解决问题。
通过有效的低电压管理措施,可以显著降低电解铝生产中的成本和环保压力,并提高生产效率和安全性。
值得注意的是,低电压管理只是电解铝生产过程中的一个方面,还需要综合考虑其他管理措施,才能实现优化生产和环境保护的平衡。
降低大型铝电解槽压降的技术应用探讨
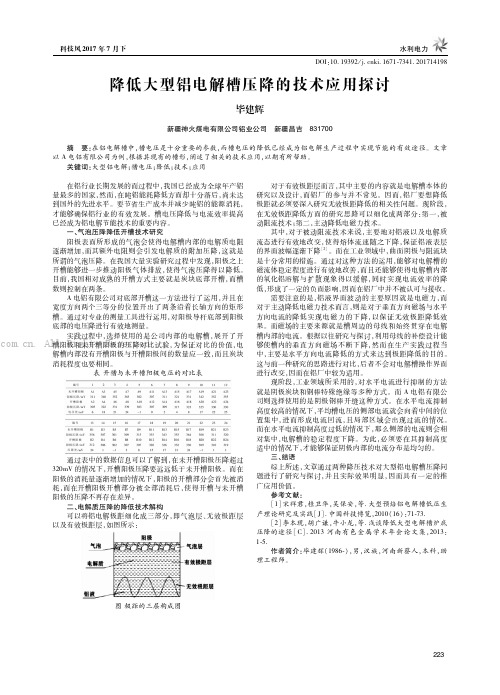
现阶段工业领 域 所 采 用 的 对 水 平 电 流 进 行 抑 制 的 方 法 就是阴极炭块和钢棒特殊绝缘等多种方式 而 ;电铝有限公 司则选择使用的是阴极钢棒开缝这种方式 在水平电流抑制 高度较高的情况下平均槽电压的侧部电流就会向着中间的位 置集中进而形成电流回流且局部区域会出现过流的情况 而在水平电流抑制高度过低的情况下那么侧部的电流则会相 对集中电解槽的稳定程度下降 为此必须要在其抑制高度 适中的情况下才能够保证阴极内部的电流分布是均匀的
关键词大型铝电解槽电压降低技术应用
44在铝行业长期发展的而过程中我国已经成为全球年产铝 量最多的国家然而在吨铝能耗降低方面却十分落后尚未达 到国外的先进水平 要节省生产成本并减少吨铝的能源消耗 才能够确保铝行业的有效发展 槽电压降低与电流效率提高 已经成为铝电解节能技术的重要内容
!科技风 "#$% 年 % 月下
水利电力 !"#$%&$'(') *+&,-./&$01$21(3$&)%$1$3$'9
降低大型铝电解槽压降的技术应用探讨
毕建辉
新疆神火煤电有限公司铝业公司!新疆昌吉!)&#'%%
摘4要在铝电解槽中槽电压是十分重要的参数而槽电压的降低已经成为铝电解生产过程中实现节能的有效途径 文章 以 ;电铝有限公司为例根据其现有的槽形阐述了相关的技术应用以期有所帮助
包头铝业400KA电解槽低电压下提高电流效率节能关键技术研究
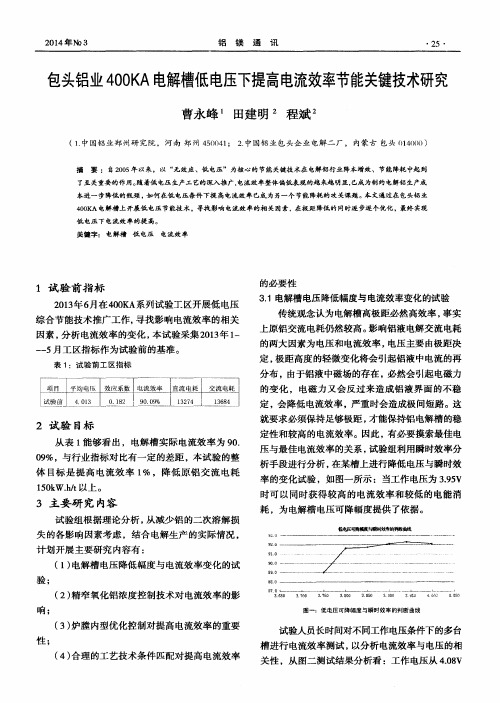
了至关重要 的作用。 随着低 电压生产工艺的深入推广 , 电流效率整 体偏低表现 的越来越 明显 , 已 成 为制约电解铝 生产成 本进一步降低 的瓶 颈 , 如何 在低 电压条件下提 高电流效率 已成 为另一 个节 能降耗 的攻关课题 。本文通过在包头铝业 4 0 0 K A电解槽上 开展 低 电压 节能技 术,寻找影响 电流效 率的相 关 因素 , 在极距 降低 的同时遥 步逐 个优 化 , 最终 实现
低电压 下电流效率的提高。
关键字: 电解槽
低 电压
电流效 率
1 0 0 K A系列试验工 区开展低 电压 综合节能技术推广工作 , 寻找影 响电流效率 的相关
因素 , 分析电流效率的变化 , 本试验采集 2 0 1 3 年1 一
一
的必 要性
失 的各影 响因素考虑 ,结合 电解生产 的实际情况 , 计划开展主要研究 内容有 : ( 1 ) 电解槽 电压降低幅度与 电流效率变化 的试
验;
( 2 ) 精窄氧化铝浓度控制技术对电流效率 的影
响;
图一:低 电压可降幅度与瞬时效率的判断曲线
( 3 ) 炉膛 内型优化控制对提高电流效率的重要
性;
试验人员长时间对不 同工作电压条件下的多台 槽进行电流效率测试 , 以分析 电流效率与电压的相
关性 ,从图二测试结果分析看 :工作 电压从 4 . 0 8 V
( 4 ) 合理 的工艺技术条件匹配对提高 电流效率
2 试 验 目标
从表 1 能 够看 出 ,电解 槽 实 际 电 流效 率 为 9 0 .
探索300KA结构电解槽低电压生产实践
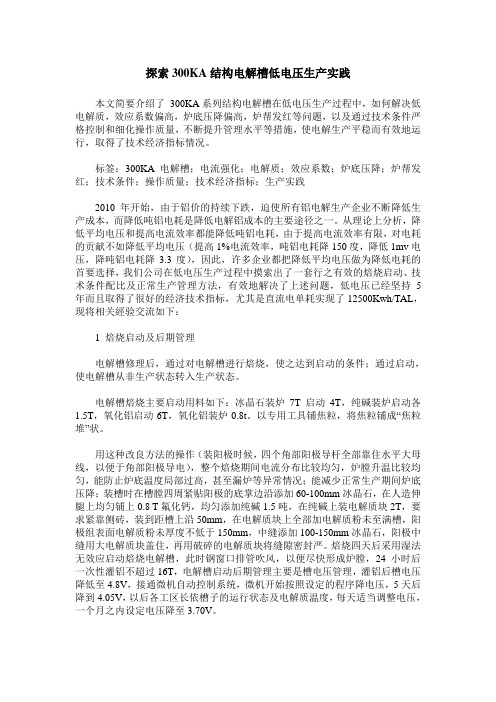
探索300KA结构电解槽低电压生产实践本文简要介绍了300KA系列结构电解槽在低电压生产过程中,如何解决低电解质,效应系数偏高,炉底压降偏高,炉帮发红等问题,以及通过技术条件严格控制和细化操作质量,不断提升管理水平等措施,使电解生产平稳而有效地运行,取得了技术经济指标情况。
标签:300KA电解槽;电流强化;电解质;效应系数;炉底压降;炉帮发红;技术条件;操作质量;技术经济指标;生产实践2010年开始,由于铝价的持续下跌,迫使所有铝电解生产企业不断降低生产成本,而降低吨铝电耗是降低电解铝成本的主要途径之一。
从理论上分析,降低平均电压和提高电流效率都能降低吨铝电耗,由于提高电流效率有限,对电耗的贡献不如降低平均电压(提高1%电流效率,吨铝电耗降150度,降低1mv电压,降吨铝电耗降3.3度),因此,许多企业都把降低平均电压做为降低电耗的首要选择,我们公司在低电压生产过程中摸索出了一套行之有效的焙烧启动、技术条件配比及正常生产管理方法,有效地解决了上述问题,低电压已经坚持5年而且取得了很好的经济技术指标,尤其是直流电单耗实现了12500Kwh/TAL,现将相关經验交流如下:1 焙烧启动及后期管理电解槽修理后,通过对电解槽进行焙烧,使之达到启动的条件;通过启动,使电解槽从非生产状态转入生产状态。
电解槽焙烧主要启动用料如下:冰晶石装炉7T启动4T,纯碱装炉启动各1.5T,氧化铝启动6T,氧化铝装炉0.8t。
以专用工具铺焦粒,将焦粒铺成“焦粒堆”状。
用这种改良方法的操作(装阳极时候,四个角部阳极导杆全部靠住水平大母线,以便于角部阳极导电),整个焙烧期间电流分布比较均匀,炉膛升温比较均匀,能防止炉底温度局部过高,甚至漏炉等异常情况;能减少正常生产期间炉底压降;装槽时在槽膛四周紧贴阳极的底掌边沿添加60-100mm冰晶石,在人造伸腿上均匀铺上0.8 T氟化钙,均匀添加纯碱1.5吨,在纯碱上装电解质块2T,要求紧靠侧砖,装到距槽上沿50mm,在电解质块上全部加电解质粉未至满槽,阳极组表面电解质粉未厚度不低于150mm,中缝添加100-150mm冰晶石,阳极中缝用大电解质块盖住,再用破碎的电解质块将缝隙密封严。
降低铝电解槽停槽电压的生产实践

降低铝电解槽停槽电压的生产实践发布时间:2022-06-07T07:23:01.612Z 来源:《中国电业》2021年第25期作者:闫智勇[导读] 铝电解生产中,电解槽采用直流串联导电的方式连接闫智勇河南中孚铝业有限公司河南郑州451200摘要:铝电解生产中,电解槽采用直流串联导电的方式连接。
生产过程中,通常因产业调整或其它原因,可能需把部分电解槽进行停槽处理,当电解槽停槽时,电流由进电母线导入阳极立柱母线,在阳极立柱母线上设有短接路线,直接将电流导入该电解槽的阴极母线,再通过阴极母线将电流导入下一台电解槽的阳极立柱母线上……。
电流在上述各导电母线中流通时会产生母线电压降,这个电压降属无用电压降,易造成电能损耗,降低铝电解槽停槽电压也就成为了电解铝企业关注的重点。
关键词:铝电解;槽停;槽电压;生产实践;引言随着电解铝工业的发展,铝电解过程的智能控制和专家控制系统成为研究热点。
电解槽电压是唯一能在线实时测量并反映槽状态的参数,因此,对电解槽电压尽可能快速进行滤波跟踪分析至关重要。
对槽电压信号进行分析应尽可能即时获取电解槽运行的状态信息,这有利于及时预防和处理电解槽的不正常工作状态(如电解槽阳极效应),估计电解质中氧化铝浓度变化,从而为调控进料量提供参考依据,提高电解铝效率和节约能源。
1目前国内低电压运行铝电解槽存在的问题我国电解铝工业发展迅速,技术装备和技术水平有了很大提高。
随着电解铝技术的发展和完善,低压运行技术得到了广泛应用。
近年来,国内许多铝厂推广的低电压运行技术,在工业实践中确实达到了降低电耗的目的。
在实际生产中,电解槽运行的平均电压已降至3.8V,吨铝DC电耗达到约12500kWh/t-al。
然而,在实施低电压操作技术的过程中,仍有相当一部分厂家存在电流效率低、电解槽寿命短、无法保持电解槽最佳热平衡、电压波动普遍等问题。
尤其是保护墙的上侧壁和铝液下方的支腿延伸部较薄,电解质分子比越低问题越严重,节电效果不明显。
400kA电解槽低电压下提高电流效率节能关键技术解析

400kA电解槽低电压下提高电流效率节能关键技术解析青海省西宁市 811601摘要:人们生活水平的不断提高,大众对自己生活的环境、生活的质量、资源的使用情况等多个方面都非常关注,并提出诸多的要求。
我国铝电解工业在新时代背景下,获得更好的发展,不同类型的大型电解槽应运而生,出现在工作人员的面前,能耗指标也在不断的优化。
因此,本篇文章主要对 400kA电解槽低电压下提高电流效率节能关键技术进行认真分析,希望能够为相关工作人员起到一些参考和帮助。
关键词:400kA;电解槽;低电压提高;电流效率;节能关键技术;众所周知,在我工业领域当中,电解铝行业发展过程当中会耗费更多能源。
近几年来,铝电解节能技术在国内呈现出高速的发展态势,全新的技术包括:新型结构铝电解槽技术、异形阴极铝电解槽技术、降低水平电流技术等等。
人们生活水平不断提高,环保意识也越来越强,当代铝电解技术需要向着节能、减排的方向所发展和前进。
面对国家节能减排环保政策以及相关要求,国内电解铝企业需要进一步降低铝电解的能耗。
基于此,本文下面主要对400kA电解槽低电压之下提高电流效率节能关键技术展开深入探讨。
1、电解槽电压降低幅度与电流效率试验电解槽高极距一定高效率,这是较为传统的观念,但事实上,原铝交流电耗较高。
电压与电流效率,对铝液电解交流电耗的主要因素。
极距决定电压,极距高度即使发生了轻微的变化,也会导致铝液当中电流的再分布,因为滤铝当中存在着磁场,所以导致电磁力发生了改变。
电磁力又会反过来,导致铝液界面的不稳定,电流效率不断的下降,甚至会出现极间短路问题。
针对于这样的情况,需要保证有足够的极距,只有这样,才能够保证铝电解槽更加的稳定。
2、精窄氧化铝浓度控制技术对电流效率的影响主要依托操控及控制系统,对电解槽氧化铝浓度的控制,才能够真正实现目标。
在操控机控制系统,对氧化铝浓度进行判断的过程当中,主要是将槽电阻的变化率作为重点以及判断的基础,最终实现了判断的目标。
大型预焙电解槽低电压效应启动

大型预焙电解槽低电压效应启动技术研究报告泰山铝业公司2006年12月目录一、课题的提出 (2)二、国内外启动综述 (3)1、干法启动 (3)2、湿法启动 (4)3、无效应湿法启动 (5)三、技术方案的开发 (6)(一)铺焦、挂极 (7)(二)通电分流焙烧 (10)(三)全电流焙烧和抬阳极 (11)(四)电解槽启动 (13)(五)电解槽后期管理技术条件 (15)(六)启动后出铝及换极 (17)(七)取样分析 (17)(八)电解槽测量频次 (18)四、方案实施 (18)五、效果分析 (30)大型预焙电解槽低电压效应启动研究一、课题的提出进入今年下半年以来,随着国内众多氧化铝厂的相继投产和产能释放,氧化铝供需矛盾得以缓解,氧化铝的国内外价格逐步走低。
同时,由于受油价上涨和经济拉动的影响,铝价在高位徘徊,电解铝行业复苏在即。
泰山铝业公司根据市场现状和发展趋势,对盈亏平衡进行了测算,如全部启动现有电解槽将会逐渐接近平衡点,铝业公司扭亏增盈的希望已经出现。
为把握机遇,创造机会,实现扭亏,适时启动全部电解槽。
泰山铝业公司一期工程为124台电解槽,年产能6.4万吨。
由于受市场因素的影响,目前正常生产51台电解槽,年产能2.5万吨,尚未达到设计生产能力。
续建62台电解槽建设完成已达3年,电解槽的碳素内衬长期暴露在空气中,已经发生了变化。
经检查,部分电解槽扎固糊已产生了裂纹、受潮,甚至有些材料超过了保质期。
目前国内铝厂还没有放置3年以上的电解槽再进行启动的成熟经验。
传统的做法是将扎固糊重新更换,对电解槽进行重新扎固,以消除对槽寿命的影响,这势必增加了启动成本。
因此,一期续建电解槽的顺利启动难度相当大,有可能造成启动失败。
目前我们正在组织积极的科研攻关,来解决这个难题。
总之,电解槽放置时间越长,启动风险越大。
国内扎固好的电解槽防止三年后,再进行启动的经验和技术几乎没有。
为了确保续建电解槽的成功启动,铝业公司专门成立了课题组进行了科研攻关。
浅谈330KA平面阴极铝电解槽低电压生产实践
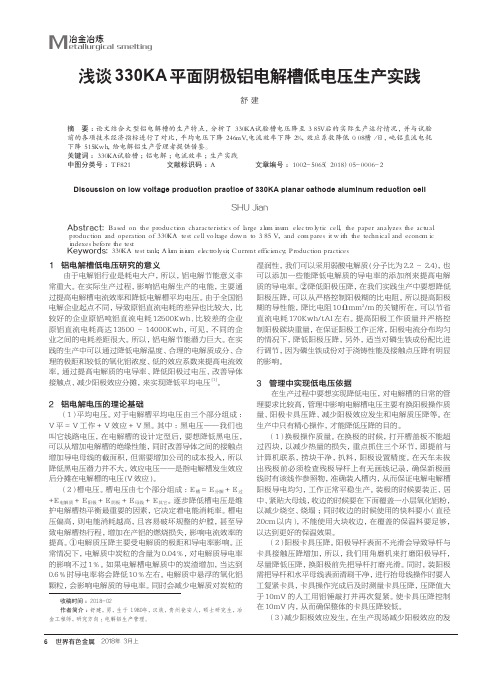
冶金冶炼M etallurgical smelting浅谈330KA平面阴极铝电解槽低电压生产实践舒 建(广西来宾银海铝业有限责任公司,广西 来宾 546135)摘 要:论文结合大型铝电解槽的生产特点,分析了330KA试验槽电压降至3.85V后的实际生产运行情况,并与试验前的各项技术经济指标进行了对比,平均电压下降246mV,电流效率下降2%,效应系数降低0.08槽/日,吨铝直流电耗下降515Kwh,给电解铝生产管理者提供借鉴。
关键词:330KA试验槽;铝电解;电流效率;生产实践中图分类号:TF821 文献标识码:A 文章编号:1002-5065(2018)05-0006-2Discussion on low voltage production practice of 330KA planar cathode aluminum reduction cellSHU Jian(Guangxi Laibin Yinhai Aluminum Co., Ltd.,Laibin 546135,China)Abstract: Based on the production characteristics of large aluminum electrolytic cell, the paper analyzes the actual production and operation of 330KA test cell voltage down to 3.85 V, and compares it with the technical and economic indexes before the test.Keywords: 330KA test tank; Aluminium electrolysis; Current efficiency; Production practices1铝电解槽低电压研究的意义由于电解铝行业是耗电大户,所以,铝电解节能意义非常重大。
200kA预焙铝电解槽低电压控制技术浅析

中图分类号 : T F 8 2 1
近年来 , 我 国 的 电 解 铝 产 业 迅 猛 发 展 ,2 0 1 1
年中国的电解铝 产量达 到 1 8 0 6万 t , 较上 年 同 比
增长 l 1 . 5 3 % … ,2 0 1 2年 一 季 度 电解 铝 产 量 4 5 9 万 t , 增长 1 2 . 1 %, 加快 1 0 . 5个 百 分 点 , 但 铝 市
第2 9卷 第 2期 2 0 1 3年s u S c i e n c e a n d T e c h n
I z . 2 9 N o . 2
J a n . 2 0 l 3
2 0 0 k A预焙 铝 电解 槽 低 电压 控 制 技 术 浅 析
4 l
能够降低的电压降采取对应措施 , 再对控制 系统进
行升级 , 最后随着槽电压的逐步降低 , 对工艺技术条
5 ) 采取有效措施减小能够控制各结点的压降。
4低 电 压 生 产 控 制 技 术 的 具 体 实 施 墨 鬈军 篓 压 降 到 一 定 程 度 后 ’ 使
从技术路线和技术方案可以看 出, 先对各部分 2 0 0 k A系列调整优化后电解工艺技术条件见表 2 。
的空间; 导杆压降、 炉底压降和效应分摊 电压较高 ,
有一定 的降电压 的潜力和空间, 极 问压降的降低空 间最大。综上分析 , 该公司 2 0 0 k A系列 的实施低 电
压控制技术 的方案为:
第2 期
浓度 控 制技术 ;
张立擘 : 2 0 0 k A预焙铝电解槽低电压控制技术浅析
200K A预焙铝电解槽低电压生产实践
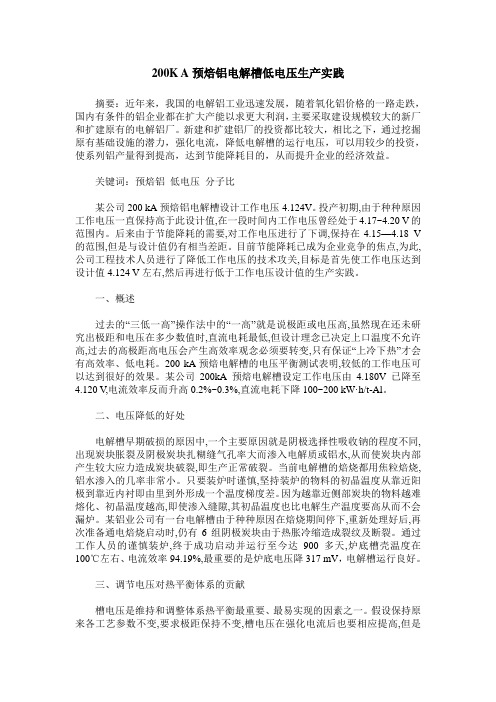
200K A预焙铝电解槽低电压生产实践摘要:近年来,我国的电解铝工业迅速发展,随着氧化铝价格的一路走跌,国内有条件的铝企业都在扩大产能以求更大利润,主要采取建设规模较大的新厂和扩建原有的电解铝厂。
新建和扩建铝厂的投资都比较大,相比之下,通过挖掘原有基础设施的潜力,强化电流,降低电解槽的运行电压,可以用较少的投资,使系列铝产量得到提高,达到节能降耗目的,从而提升企业的经济效益。
关键词:预焙铝低电压分子比某公司200 kA预焙铝电解槽设计工作电压4.124V。
投产初期,由于种种原因工作电压一直保持高于此设计值,在一段时间内工作电压曾经处于4.17~4.20 V的范围内。
后来由于节能降耗的需要,对工作电压进行了下调,保持在4.15—4.18 V 的范围,但是与设计值仍有相当差距。
目前节能降耗已成为企业竞争的焦点,为此,公司工程技术人员进行了降低工作电压的技术攻关,目标是首先使工作电压达到设计值4.124 V左右,然后再进行低于工作电压设计值的生产实践。
一、概述过去的“三低一高”操作法中的“一高”就是说极距或电压高,虽然现在还未研究出极距和电压在多少数值时,直流电耗最低,但设计理念已决定上口温度不允许高,过去的高极距高电压会产生高效率观念必须要转变,只有保证“上冷下热”才会有高效率、低电耗。
200 kA预焙电解槽的电压平衡测试表明,较低的工作电压可以达到很好的效果。
某公司200kA预焙电解槽设定工作电压由4.180V已降至4.120 V,电流效率反而升高0.2%~0.3%,直流电耗下降100~200 kW·h/t-Al。
二、电压降低的好处电解槽早期破损的原因中,一个主要原因就是阴极选择性吸收钠的程度不同,出现炭块胀裂及阴极炭块扎糊缝气孔率大而渗入电解质或铝水,从而使炭块内部产生较大应力造成炭块破裂,即生产正常破裂。
当前电解槽的焙烧都用焦粒焙烧,铝水渗入的几率非常小。
只要装炉时谨慎,坚持装炉的物料的初晶温度从靠近阳极到靠近内衬即由里到外形成一个温度梯度差。
如何有效降低电解槽平均电压
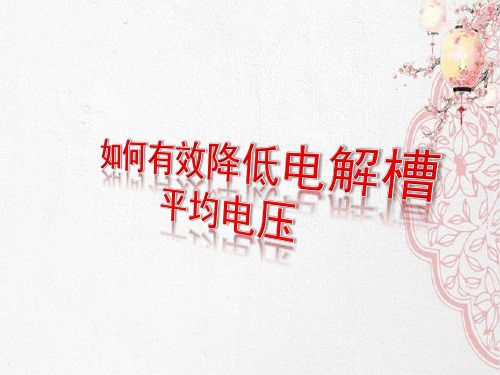
其中阳极压降、阴极压降、效 应分摊压降为可控制,本课题主要 围绕上述3方面开展。
课题名称:降低电解槽平均电压
电小
解组
二 车
概 况
间
活动时间: 2012年2月~2012年11月
4
从人员情况分析
1、小组成员均为本工区技术骨干,理论与实践能力 强; 2、我小组2008年解决了《红炉帮修补》、2009年解 决了《提高原铝质量》、2010年解决了《减少角部 顶断导杆数量》等课题。
结论: 结合理论计算、实际情况、实施条件及人员情况分析得出我们
将目前定为3.9v比较合理,通过全体员工的努力一定能够实现,所 以目标值可行。
节能降耗,降低电解生产成本,实施低成本运营。
电解槽低电压运行
结合2011年我车间四区、五区、六区平均电压对比,我工 区平均电压较高,为3.958v。
工区现状 选定课题
图1 时间:2012.12
工区
一月
二月
三月
四月
五月
六月
七月
八月
九月
十月
十一 月
十二 月
平均
四区 3.971 3.963 3.966 3.958 3.953 3.95 3.953 3.951 3.96 3.96 3.961 3.95 3.958
本QC小组成员通过头脑风暴法经过分析, 判断出导致电解槽平均电压较高的原因 有以下几点。如下图:
人 人员技术水平有限
人员技术培训不到位
电
母线压降高
压接面接触不良 导杆表面不平
解
300kA铝电解槽低电压高效运行生产实践
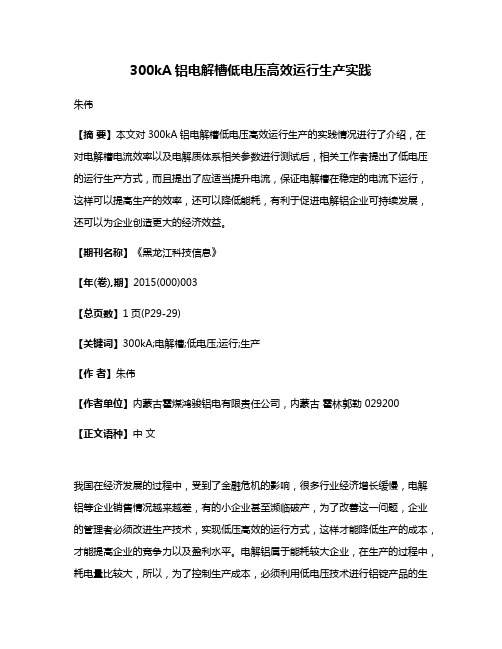
300kA铝电解槽低电压高效运行生产实践朱伟【摘要】本文对300kA铝电解槽低电压高效运行生产的实践情况进行了介绍,在对电解槽电流效率以及电解质体系相关参数进行测试后,相关工作者提出了低电压的运行生产方式,而且提出了应适当提升电流,保证电解槽在稳定的电流下运行,这样可以提高生产的效率,还可以降低能耗,有利于促进电解铝企业可持续发展,还可以为企业创造更大的经济效益。
【期刊名称】《黑龙江科技信息》【年(卷),期】2015(000)003【总页数】1页(P29-29)【关键词】300kA;电解槽;低电压;运行;生产【作者】朱伟【作者单位】内蒙古霍煤鸿骏铝电有限责任公司,内蒙古霍林郭勒 029200【正文语种】中文我国在经济发展的过程中,受到了金融危机的影响,很多行业经济增长缓慢,电解铝等企业销售情况越来越差,有的小企业甚至濒临破产,为了改善这一问题,企业的管理者必须改进生产技术,实现低压高效的运行方式,这样才能降低生产的成本,才能提高企业的竞争力以及盈利水平。
电解铝属于能耗较大企业,在生产的过程中,耗电量比较大,所以,为了控制生产成本,必须利用低电压技术进行铝锭产品的生产,这样才能在提高产量的前提下,降低生产成本,从而达到电解槽低压高效运行生产的目的。
1 技术思路激烈的市场竞争,使得电解铝企业的生存受到严重挑战,如何采取措施降低成本、提高效益成为企业突破困境首要考虑的重点。
作为高能耗产业的电解铝企业,电的成本占总成本的40%以上,有效降低单位产品的电耗是降低生产成本最有效最直接的途径,因此低电压生产技术越来越受到电解铝企业的重视并逐渐成为发展趋势,已有部分大型电解铝企业进行了成功应用,在不影响产量的情况下降低了吨铝电耗,达到了降低成本增加效益的目的。
电解生产的铝液直流电耗计算公式为:由此,我们可以知道,铝电解槽降低电耗的主要途径:一是降低电解槽平均电压;二是提高电流效率。
根据铝液直流电耗公式可以得出:在电流效率一定时,直流电耗的变化幅度与平均电压的变化关系为ΔW=2980*ΔV平/η;按电流效率92.5%计算,槽平均电压每降低0.01 V,铝液直流电耗可阳氏32.2kWh/t-AI,从中可以看出降低电解槽电压的节能效果。
低电压的控制涂全
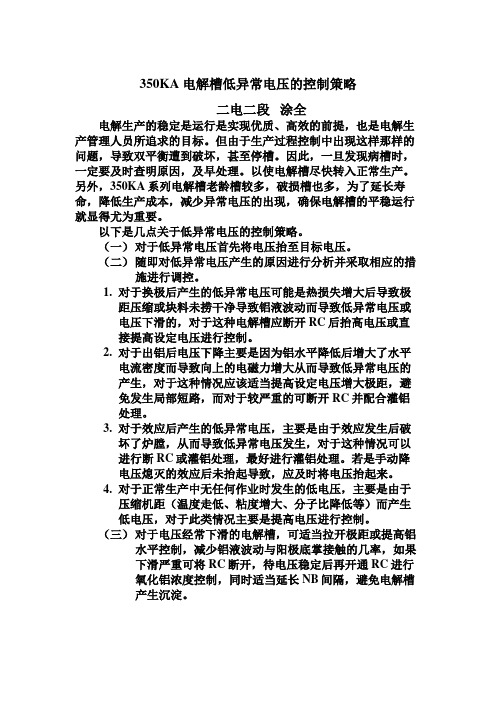
350KA电解槽低异常电压的控制策略二电二段涂全电解生产的稳定是运行是实现优质、高效的前提,也是电解生产管理人员所追求的目标。
但由于生产过程控制中出现这样那样的问题,导致双平衡遭到破坏,甚至停槽。
因此,一旦发现病槽时,一定要及时查明原因,及早处理。
以使电解槽尽快转入正常生产。
另外,350KA系列电解槽老龄槽较多,破损槽也多,为了延长寿命,降低生产成本,减少异常电压的出现,确保电解槽的平稳运行就显得尤为重要。
以下是几点关于低异常电压的控制策略。
(一)对于低异常电压首先将电压抬至目标电压。
(二)随即对低异常电压产生的原因进行分析并采取相应的措施进行调控。
1.对于换极后产生的低异常电压可能是热损失增大后导致极距压缩或块料未捞干净导致铝液波动而导致低异常电压或电压下滑的,对于这种电解槽应断开RC后抬高电压或直接提高设定电压进行控制。
2.对于出铝后电压下降主要是因为铝水平降低后增大了水平电流密度而导致向上的电磁力增大从而导致低异常电压的产生,对于这种情况应该适当提高设定电压增大极距,避免发生局部短路,而对于较严重的可断开RC并配合灌铝处理。
3.对于效应后产生的低异常电压,主要是由于效应发生后破坏了炉膛,从而导致低异常电压发生,对于这种情况可以进行断RC或灌铝处理,最好进行灌铝处理。
若是手动降电压熄灭的效应后未抬起导致,应及时将电压抬起来。
4.对于正常生产中无任何作业时发生的低电压,主要是由于压缩机距(温度走低、粘度增大、分子比降低等)而产生低电压,对于此类情况主要是提高电压进行控制。
(三)对于电压经常下滑的电解槽,可适当拉开极距或提高铝水平控制,减少铝液波动与阳极底掌接触的几率,如果下滑严重可将RC断开,待电压稳定后再开通RC进行氧化铝浓度控制,同时适当延长NB间隔,避免电解槽产生沉淀。
(四)对多次或连续出现电压下滑产生异常电压的电解槽,必须对电解槽进行认真检查分析,作出相应的行之有效的处理。
- 1、下载文档前请自行甄别文档内容的完整性,平台不提供额外的编辑、内容补充、找答案等附加服务。
- 2、"仅部分预览"的文档,不可在线预览部分如存在完整性等问题,可反馈申请退款(可完整预览的文档不适用该条件!)。
- 3、如文档侵犯您的权益,请联系客服反馈,我们会尽快为您处理(人工客服工作时间:9:00-18:30)。
兰州铝业股份有限公司降低电解槽电压和效应系数、缩短效应时间工作实施方案根据中铝公司和我公司节能降耗工作要求,进一步提高我公司电解系列的技术经济指标,降低电解槽电耗,是当前公司生产管理的一项重要工作,而目前开展降低电解槽电压和效应系数的试验具有重要意义。
电解槽工作电压的降低不是单纯地降低极距,而是通过提高电解质的导电率、阴阳极导电性和降低各部分接触压降和降低阳极效应系数和缩短效应时间来实现的,所以这是一个全公司各个工序都应提高自己工作质量的综合工程:包括阳极的质量、导杆修复质量、钢爪修复质量、磷生铁浇铸质量、焊接质量、大修筑炉质量、阴极块的质量、阴极块和阴极棒的连接质量、氧化铝的下料量、氧化铝的质量、打击头的修复、阳极换极质量、导杆与母线的压接质量、供风质量等。
一、成立公司领导小组1、由电解二厂、生产运行部、质量监督部、机修厂、炭素厂和技术中心共同组建。
任务是:计划、实施、现场测试和现场执行。
在电解二厂建立现场测试组。
2、领导小组组长:肖伟峰副组长:杜立中组员:范爱民、郭兰江、肇玉卿、刘连会、杨保仲、马永国、陆惠国、崔亚东、李兴虎、魏世湖、杨青、李美、谷文明、张扬等工程技术人员及相关部门、分厂的操作人员二、降低阳极效应系数工作的实施依据与生产过程管理1、阳极效应发生的主要原因:氧化铝供给不足(下料量偏低);电解质溶解氧化铝能力偏差(温度低、过热度低、电解质成分不合适);电解质传质能力不足(电解质发粘)。
2、发生阳极效应产生的不良影响:发生阳极效应时排放大量温室气体;造成电解槽温度和电解质成分的波动;降低电流效率;增加能耗和氟盐消耗。
3、当前国内阳极效应系数高的主要原因:工艺上人为等待效应;氧化铝输送及下料故障或不准确;控制模型不适应;氧化铝质量不稳定;阳极质量问题;工艺条件问题;限电或供电不足。
4、在条件许可的情况下,选用易于溶解的砂状氧化铝,并且尽量稳定控制-325目的氧化铝在一定范围内,同时提高阳极质量,对于促进氧化铝与熔盐电解质的反应效率有很大帮助,减少了阳极效应产生的几率。
5、氧化铝浓度控制氧化铝浓度控制,应满足电解槽低效应运行的工艺需要,就是要保持氧化铝浓度在低浓度窄范围下的长期稳定运行,这就需要开发更高精度的控制模型,以便对电解槽实现氧化铝下料更加精确的控制,降低阳极效应发生概率。
研究开发新型控制模型和控制策略,提高电解槽控制技术水平,解决氧化铝在低、窄浓度范围(小于3.7%)稳定运行的问题,氧化铝浓度控制在既不发生效应,又不产生沉淀的范围内(可请相关专家进行技术指导)。
6、保持电解槽稳定运行1)电解槽的理想状态:高效、低耗、优质、长寿、环保;2)作业要点:在保证原材料质量的基础上,提高电解生产的操作水平,合理设置工艺参数(两水平、分子比、槽电压、覆盖料),保持合理的电解温度和炉膛内型。
3)全面推行精益化管理和实施以电解槽工艺技术参数稳定为目标的管理模式。
4)制定和完善电解槽考核办法,评价每台电解槽的工艺技术参数的稳定性,并作为工作绩效的重要内容。
建立单槽档案。
技术指标以车间为单位来进行。
5)推行工序质量管理,建立质量异常分析和质量评价制度,按照质量体系对质量管理的基本要求做到可追溯,强化操作人员对异常现象的敏感度,提高产品质量。
全员参与讨论和修订作业指导书。
6)电解槽管理的过程标准以炉膛为中心,保证炉底无沉淀、无电压摆,保持两水平及电流基本不变,调整分子比、覆盖料、槽电压、下料间隔。
7、目前,我公司不具备砂状氧化铝及自行开发氧化铝浓度控制模型的条件。
通过对阳极效应产生及阳极效应系数偏高原因的分析,结合我公司生产现状,在生产实际操作管理中,要降低效应系数,需要拉长效应间隔时间,保证下料量的准确性、减少打壳下料机构的故障,保持电解槽的稳定运行,确保控制模型准确有效运行。
解决好氧化铝过量下料幅度与电解质溶解能力相适应的问题,并解决好低效应操作时,电解槽可能出现的负面影响。
不断减少产生阳极效应所带来的不良反应。
三、低电压节能技术工作实施依据1、试验背景以往的高极距(电压)工艺条件一个主要的出发点就是保证电解槽稳定,减少铝的二次反应,有利于电流效率的提高,但较高的槽电压必然造成直流电耗的上升。
国外专家研究表明,极距超过某一限度(35mm)电流效率变化不大。
国外先进企业的直流电耗一般在13000kwh/t.Al左右,国内一般直流电耗在13700kwh/t.Al以上,主要是由于国外采用了较合理的低极距操作工艺。
国内电解槽由于电流密度比较低,所以极距基本上保持在4.5~5.5cm之间。
随着铝电解操作水平、管理水平、控制水平、装备水平的提高,电解槽运行的稳定性也在逐步提高,因此通过降低极距(3~5mm)、适当降低槽电压(100~150mv)来实现节能的空间比较大。
2、降低槽电压的两种技术方案(1)保持系列电流不变,降低槽电压在保持铝电解生产过程电流效率不下降且电解槽稳定运行的前提下,通过各种方法降低电解槽外围电压降和极间压降,外围压降的降低主要通过细化操作管理来实现;极间压降的降低必须建立新的能量平衡。
减少电解槽的散热,主要通过减少槽上部、侧部的散热,这就需要对上部保温料、槽温、两水平、分子比、作业过程进行调整,必须形成更厚的炉帮。
降低电解槽输入能量,不可避免地带来槽温、极距的相对降低,必须采取相应的生产工艺技术和自动控制技术。
(2)强化系列电流、降低槽电压强化电流的目的主要是增产增效。
其带来的输入能量增加一般是通过降低极间压降来建立电解槽的新的能量平衡。
电流强度每提高1%,槽电压一般应降低10mv。
尽量保持电解槽原有的能量平衡,使电解槽的能量平衡状态不发生实质性的变化。
槽内电流密度提高和极距降低会带来磁场、流速场的变化,必须解决电解槽稳定问题。
阳极、阴极质量需要进一步提高以适合强化后的电流密度。
3、三场测试数据分析以下是中南大学与我公司联合进行的三场测试报告《200KA预焙阳极电解槽物理场综合研究报告》中的部分测试数据:表1 200kA铝电解槽电平衡测试与计算结果表2电压平衡测算结果汇总表(330mV)。
所测三台槽的阳极压降分别为409.94mV、411.93mV、377.27mV,分别超过设计值79.94mV、81.93mV、47.27mV。
超设计值的主要原因是:这主要是钢-碳及碳块压降、斜立母线压接压降偏大所致,生产中应注意采取措施,改善各部分压接质量及磷生铁的浇注质量。
钢-碳压降过高,其中3010#槽、3058#槽、4114#槽的钢-碳压降与碳块压降之和分别超设计值(250mV)86.78mV、82.52mV、57.82mV。
导致钢-碳接触与阳极块压降之和较大的可能原因有:一、钢碳间的磷生铁浇铸质量不佳;二、钢爪上的铁锈清理不够干净;三、电解生产中氧化铝保温不足,造成阳极氧化严重,使钢-碳接触面积减小而压降增大;四、在阳极组装时对碳碗清理不够,碳碗中有粉尘异物;五、阳极质量不佳,其比电阻较大。
三场测试数据分析给出了我们以下建议:a)槽电压计算结果表明槽阳极压降偏高,因此生产中应注意采取措施,改善各部分压接质量及磷生铁的浇注质量。
b)鉴于炉帮形成欠佳,建议多跟踪测定,有可能的话可在槽子大修时逐步推广采用耐蚀性能和导热性能更好的碳化硅侧块。
c)工艺条件方面,一是控制和调整好分子比,适当降低槽温,以便形成规整炉帮;二是注意盖好槽罩、保持良好的炉面覆盖层;三是注意检查槽罩密封性能和调整烟道阀门的开度,以减少无效热损失。
d)所测槽最大流速均在进电侧靠近烟道端,表明这个部位是比较薄弱的区域,有可能由于铝液流速大而产生小旋涡,对槽底和侧衬施以冲刷,导致电解槽早期破损,因此应注意在换极时对这些部位进行适当的边部加工。
四、电解系列现状1、近期平均工作电压和效应系数数据(2005年3月):平均工作电压(v):1车间4.265, 2车间4.307, 3车间4.238, 4车间4.241 效应系数(次/台,日):1车间0.41,2车间0.62,3车间0.23,4车间0.252、试验槽的选定选择四车间一工区5台200KA电解槽(4011~4015#)作为低电压、低效应系数试验的试验槽,取得成果后进行扩大试验及推广应用。
3、初步试验进度和设定试验目标,分阶段降低槽电压和效应系数(1)降低效应系数试验:2005年4~6月分别降到0.20(200KA)、0.35(75KA),效应持续时间控制在5分钟内。
2005年7~12月分别降到0.15(200KA)、0.30(75KA),效应持续时间控制在3分钟内,并在全公司进行推广。
2006年争取降到0.10(200KA)、0.25(75KA),效应持续时间控制在3分钟内,并推广应用至整个电解系列。
(2)降低槽电压(平均电压):2005年4月,对电解槽进行综合测试,根据测试结果进行电压平衡(母线压降、阳极压降、电解质压降、槽底压降)计算,对各部分压降进行分析,评价其合理性;2005年5~6月,根据测试结果分析各部分压降不合理的原因,探讨和提出改进措施,看有哪些地方电压还有潜力,再确定降低工作电压目标,为改善电解槽工艺技术条件,降低槽电压和减少直流电耗提供依据;2005年7~12月,通过改进措施和节能挖潜,将200KA电解槽平均电压降到4.20v以下,各部分电压降到设计值(母线压降0.020v,阳极压降0.330v,电解质压降1.575v,槽底压降0.380v),并在3、4车间进行推广。
75KA电解槽平均电压降到4.24v,并在1、2车间进行推广。
五、低电压及低效应系数工作的预计达到效果、采取的措施、实施单位及时间2005年年内目标:降低工作电压50mv;降电耗160kwh/t.AL;效应系数降低至0.10次/台,日以下,效应持续时间不超过3分钟;降低效应均摊电压10mv;降电耗30 kwh/t.AL。
1、降低电压降试验a、极间电压:保持极距4.2cm-4.5cm,降低电压30mv,适当降低,暂不采用压极距的方法降低电压。
但是不降低极间电压,工作电压是不会降低多少的(电解二厂5月底前基本完成)。
b、阳极压降:通过现场实测及三场测试分析看出我公司阳极压降偏高,需要降低降低铝导杆-钢爪压降、钢爪电压降、钢爪-碳块电压降、碳块本身电压降,要提高阳极质量,降低比电阻(炭素厂、电解二厂年内完成)。
c、阴极压降:计划年内在200KA电解槽大修时,选用50%半石墨质阴极碳块进行2台电解槽工业试验,可以降低炉底压降30mv。
(技术中心、电解二厂按照研发计划时间完成)。
d、添加镁盐,改善电解质成分,提高导电率,降低电解质压降(电解二厂6月底前完成)。
e、在现有基础上,将75KA电解槽电流强度提高到79KA,改善炉底状况,降低极间压降,实现新的能量平衡(生产运行部、动力厂5月底前完成)。