水泥厂工艺设计概况修订稿
日产4000吨水泥熟料工厂设计
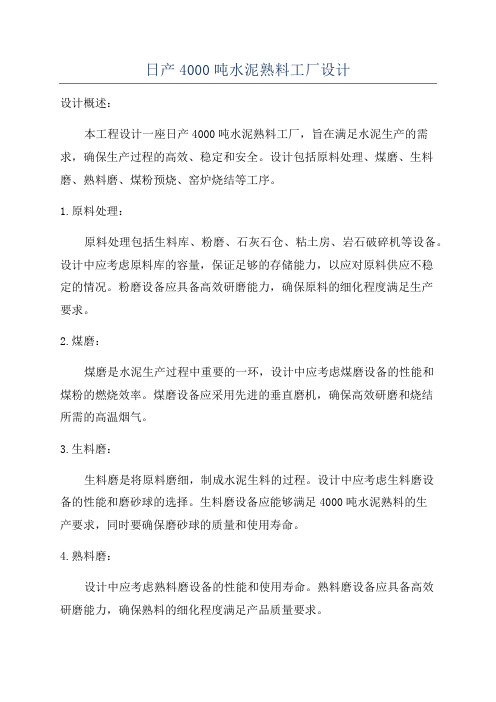
日产4000吨水泥熟料工厂设计设计概述:本工程设计一座日产4000吨水泥熟料工厂,旨在满足水泥生产的需求,确保生产过程的高效、稳定和安全。
设计包括原料处理、煤磨、生料磨、熟料磨、煤粉预烧、窑炉烧结等工序。
1.原料处理:原料处理包括生料库、粉磨、石灰石仓、粘土房、岩石破碎机等设备。
设计中应考虑原料库的容量,保证足够的存储能力,以应对原料供应不稳定的情况。
粉磨设备应具备高效研磨能力,确保原料的细化程度满足生产要求。
2.煤磨:煤磨是水泥生产过程中重要的一环,设计中应考虑煤磨设备的性能和煤粉的燃烧效率。
煤磨设备应采用先进的垂直磨机,确保高效研磨和烧结所需的高温烟气。
3.生料磨:生料磨是将原料磨细,制成水泥生料的过程。
设计中应考虑生料磨设备的性能和磨砂球的选择。
生料磨设备应能够满足4000吨水泥熟料的生产要求,同时要确保磨砂球的质量和使用寿命。
4.熟料磨:设计中应考虑熟料磨设备的性能和使用寿命。
熟料磨设备应具备高效研磨能力,确保熟料的细化程度满足产品质量要求。
5.煤粉预烧:煤粉预烧是水泥熟料工厂的重要工序。
在设计中应考虑煤粉预烧设备的性能和热能利用率。
煤粉预烧设备应能够稳定地完成预烧过程,并满足熟料窑炉的需求。
6.窑炉烧结:窑炉烧结是将熟料烧结成水泥的关键过程。
设计中应考虑窑炉的尺寸、结构和热能利用率。
窑炉应具备高温下的稳定运行能力,并确保高质量的烧结过程。
7.环保设施:在设计中应考虑环保设施的设置,确保工厂的环境保护和资源利用。
环保设施包括粉尘收集装置、烟气治理装置等,以达到国家和地方的环保标准。
8.自动化控制系统:工厂的自动化控制系统应实现全生产线的自动控制和监测。
通过PLC、DCS等自动化设备,实现工厂的高效运行和可持续发展。
总结:以上是一座日产4000吨水泥熟料工厂设计的简要概述。
设计中需要考虑原料处理、煤磨、生料磨、熟料磨、煤粉预烧、窑炉烧结等工序,并配置相应的设备和环保措施。
通过合理的设计和高效的设备,确保生产过程的稳定、高效和安全,提高产品质量和工厂的竞争力。
水泥制品生产工艺改善与控制技术研究

水泥制品生产工艺改善与控制技术研究一、水泥制品生产工艺改善的必要性水泥制品作为基础建材,在国民经济中占有重要地位。
随着经济发展和人民生活水平提高,对建筑美观度和品质的需求也逐渐增强。
传统的水泥制品生产工艺已经无法满足新时代的要求,因此需要对其生产工艺进行改进和优化,以提高水泥制品的质量和生产效率。
二、水泥制品生产工艺改善的途径1. 原材料的优化选择水泥制品生产中,原材料的质量和配比是影响产品质量的重要原因。
因此,对原材料进行优化选择,选择高品质的天然石材或工业废渣作为原材料,严格控制配比,能够有效提高产品质量和减少生产成本。
2. 精细加工及工艺流程的优化在水泥制品生产中,通过优化工艺流程和提高加工精度来改善产品质量。
例如,在制管过程中,采用高效的管机设备和专业的数控加工系统,使管子的强度和尺寸精度得到提高,从而提高产品的质量。
3. 先进设备的应用随着科技的发展,水泥制品生产设备也得到了不断的更新换代。
先进设备的应用,能够实现自动化生产,并且能够大幅降低操作成本和提高产品质量。
三、水泥制品生产控制技术1. 温度控制技术水泥制品加工过程中,粘土需要在特定的温度下进行加工。
因此,掌握温度控制技术可以有效提高产品的质量。
在定制水泥制品加工中,为了适应不同的加工条件,需要对温度控制系统进行调整。
控制系统需要身体热胀冷缩等温度变化,维持粘土在合适的温度下进行加工。
2. 湿度控制技术水泥制品生产过程中,湿度的控制也是一个非常关键的环节。
如果湿度过高或过低,都会影响产品的质量。
因此,掌握湿度控制技术,控制加工环境的湿度保持在正常范围内,也是非常重要的。
3. 产品质量检测技术产品质量检测技术是保障产品质量的重要手段。
通过建立科学规范的质量检测流程,对制品进行严格的检测,确保产品符合国家和行业标准。
四、结论随着经济发展和技术创新,水泥制品生产工艺和控制技术也在不断升级。
通过对原材料的优化选择、精细加工和工艺流程的优化及先进设备的应用,能够提高产品的质量和生产效率。
水泥生产工艺的设计【整理精品范本】
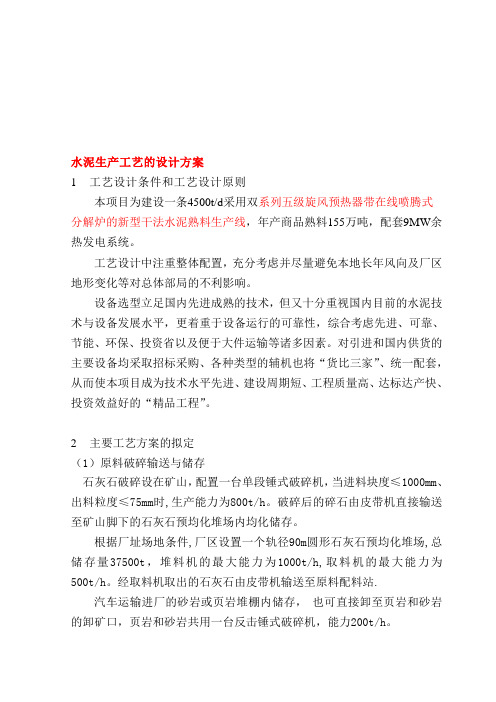
水泥生产工艺的设计方案1 工艺设计条件和工艺设计原则本项目为建设一条4500t/d采用双系列五级旋风预热器带在线喷腾式分解炉的新型干法水泥熟料生产线,年产商品熟料155万吨,配套9MW余热发电系统。
工艺设计中注重整体配置,充分考虑并尽量避免本地长年风向及厂区地形变化等对总体部局的不利影响。
设备选型立足国内先进成熟的技术,但又十分重视国内目前的水泥技术与设备发展水平,更着重于设备运行的可靠性,综合考虑先进、可靠、节能、环保、投资省以及便于大件运输等诸多因素。
对引进和国内供货的主要设备均采取招标采购、各种类型的辅机也将“货比三家”、统一配套,从而使本项目成为技术水平先进、建设周期短、工程质量高、达标达产快、投资效益好的“精品工程”。
2 主要工艺方案的拟定(1)原料破碎输送与储存石灰石破碎设在矿山,配置一台单段锤式破碎机,当进料块度≤1000mm、出料粒度≤75mm时,生产能力为800t/h。
破碎后的碎石由皮带机直接输送至矿山脚下的石灰石预均化堆场内均化储存。
根据厂址场地条件,厂区设置一个轨径90m圆形石灰石预均化堆场,总储存量37500t,堆料机的最大能力为1000t/h,取料机的最大能力为500t/h。
经取料机取出的石灰石由皮带机输送至原料配料站.汽车运输进厂的砂岩或页岩堆棚内储存,也可直接卸至页岩和砂岩的卸矿口,页岩和砂岩共用一台反击锤式破碎机,能力200t/h。
钢渣或铁矿石尾矿进厂粒度≤40mm,无需破碎。
破碎后的页岩和砂岩由胶带输送机送至辅助原料长型预均化堆场,侧式悬臂堆料机的堆料能力400t/h(与原煤共用一台堆料机),侧式刮板取料机的能力110t/h。
进厂钢渣或铁矿石尾矿堆于堆棚内储存,铲车取料后由皮带机直接送至原料配料站。
原料配料站设石灰石、页岩、砂岩及铁矿石尾矿或钢渣四个仓。
(2)原煤卸车输送与储存进厂原煤堆于原煤堆棚内储存,铲车取料送入原煤预均化堆场的进料皮带机。
原煤和辅助原料共用一台堆料机。
水泥工艺设计

水泥工艺设计一、前期准备1.1 原材料采购水泥生产的原材料主要包括石灰石、粘土、铁矿石和煤等。
在采购原材料时,要注重品质、价格和供货周期等方面的考虑。
1.2 设备采购水泥生产需要使用各种设备,如球磨机、旋转窑、冷却机等。
在采购设备时,要根据生产规模和技术要求进行选择。
1.3 土地选址和环评审批水泥生产需要选取适宜的土地,并进行环境影响评价审批,以确保生产过程对环境的影响最小化。
二、原材料处理2.1 石灰石的处理将采集到的石灰石送入颚式破碎机进行初步粉碎,再送入圆锥式细碎机进行细碎,最后通过振动筛分离出所需颗粒大小的物料。
2.2 粘土的处理将采集到的粘土送入圆盘式制粒机进行制粒,然后送入回转窑干燥,并通过振动筛分离出所需颗粒大小的物料。
2.3 铁矿石的处理将采集到的铁矿石送入颚式破碎机进行初步粉碎,再送入圆锥式细碎机进行细碎,最后通过振动筛分离出所需颗粒大小的物料。
2.4 煤的处理将采集到的煤送入颚式破碎机进行初步粉碎,然后送入球磨机进行细碎,并通过振动筛分离出所需颗粒大小的物料。
三、生产流程3.1 原材料预处理将经过处理后的原材料按一定比例混合,并送入球磨机进行混合和细碎。
3.2 烧成过程将已经混合好的原材料送入旋转窑中,在高温下进行反应,形成水泥熟料。
在旋转窑出口处,通过冷却机对水泥熟料进行冷却。
3.3 粉末制备将冷却后的水泥熟料送入球磨机中进行细碎,最终得到所需颗粒大小的水泥粉末。
3.4 包装和储存将制备好的水泥粉末包装成袋或散装,并存放在干燥通风的仓库中。
四、环保措施4.1 烟气处理在旋转窑出口处设置烟气处理设备,将烟气中的二氧化硫等污染物进行吸收和净化。
4.2 垃圾处理生产过程中产生的垃圾要进行分类处理,有机垃圾进行堆肥处理,非有机垃圾送入垃圾焚烧设备进行焚烧。
4.3 水资源利用对生产过程中产生的废水进行回收和利用,减少对水资源的浪费。
五、安全措施5.1 设备维护定期对生产设备进行检查和维护,确保设备运行正常。
水泥生产工艺改进与优化
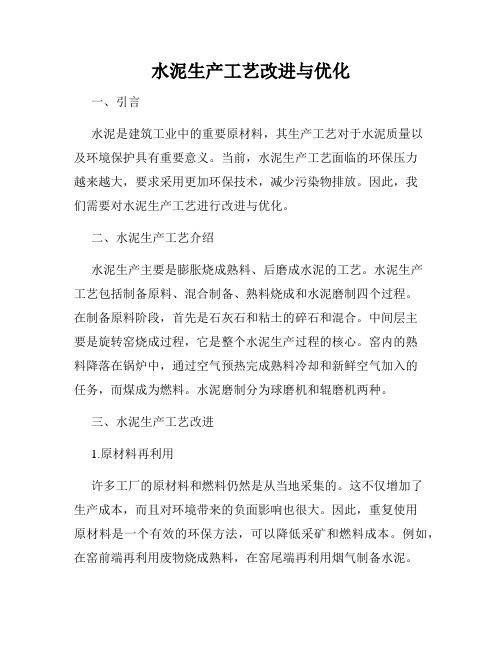
水泥生产工艺改进与优化一、引言水泥是建筑工业中的重要原材料,其生产工艺对于水泥质量以及环境保护具有重要意义。
当前,水泥生产工艺面临的环保压力越来越大,要求采用更加环保技术,减少污染物排放。
因此,我们需要对水泥生产工艺进行改进与优化。
二、水泥生产工艺介绍水泥生产主要是膨胀烧成熟料、后磨成水泥的工艺。
水泥生产工艺包括制备原料、混合制备、熟料烧成和水泥磨制四个过程。
在制备原料阶段,首先是石灰石和粘土的碎石和混合。
中间层主要是旋转窑烧成过程,它是整个水泥生产过程的核心。
窑内的熟料降落在锅炉中,通过空气预热完成熟料冷却和新鲜空气加入的任务,而煤成为燃料。
水泥磨制分为球磨机和辊磨机两种。
三、水泥生产工艺改进1.原材料再利用许多工厂的原材料和燃料仍然是从当地采集的。
这不仅增加了生产成本,而且对环境带来的负面影响也很大。
因此,重复使用原材料是一个有效的环保方法,可以降低采矿和燃料成本。
例如,在窑前端再利用废物烧成熟料,在窑尾端再利用烟气制备水泥。
2.新型窑壁结构熟料反应的核心区域在旋转窑内,其周围是一个多孔的熟料层,这是热反应的主要场所。
因此,窑壁对熟料的热传递和物料运动至关重要,窑壁的设计结构可以改进传热和物料运动,提高熟料反应的质量和效率。
3.煤粉喷吹技术燃料是水泥生产中的一个重要因素。
传统的燃烧技术采用浮动煤粉,其不仅能降低环境质量,而且燃烧效率也不尽如人意。
因此,煤粉喷吹代替浮动煤粉,能有效改善环境问题,并且可以提高燃烧效率。
四、水泥生产工艺优化1.降低能耗水泥生产中能耗较大,其中约90%的能量都用于熟料的烧成。
因此,优化窑炉操作和减少浪费燃料能有效降低能耗,从而达到减轻污染物排放并提高经济效益的目的。
2.减少污染物排放烟气处理是水泥工厂中的重要问题之一。
减少烟气排放,防止水泥厂对周围环境造成污染是水泥生产中必须重视的问题。
可以采取建立废气处理系统和循环利用废气中的热能等方法,减少污染物排放和提高水泥质量。
水泥厂工艺设计概论
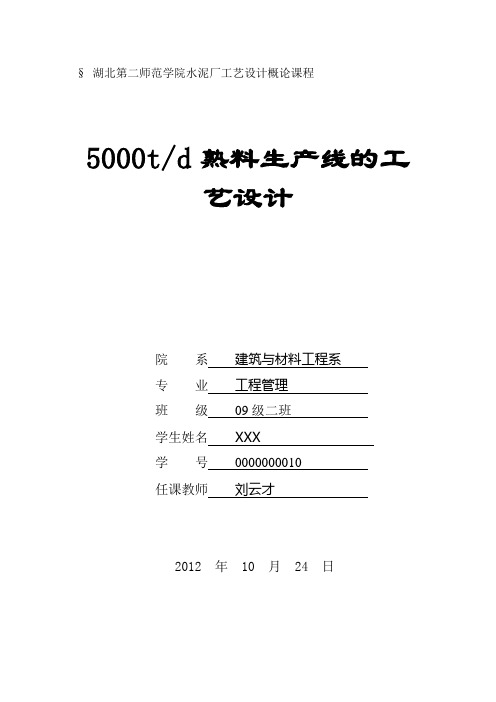
§湖北第二师范学院水泥厂工艺设计概论课程5000t/d熟料生产线的工艺设计院系建筑与材料工程系专业工程管理班级09级二班学生姓名XXX学号**********任课教师刘云才2012 年 10 月 24 日5000t/d熟料生产线的工艺设计专业工程管理学生XXX学号0000000010摘要:本文以5000t/d水泥熟料生产线为对象,从原材料、燃料的选择开始,对水泥熟料生产线的生产工艺进行了详细的介绍,并在文中给出了工艺平衡计算和水泥厂生产线的平面图。
关键词:物料平衡;热耗;物料均化;预分解窑Abstract:Based on the 5000 t/d cement clinker production line for object, begin with raw materials, fuel choice, production process to cement clinker production line were introduced in detail, and in this paper presents the process balance calculation and cement production line of the plan.Key words:Material balance; heat rate; Material homogenization; Precalcining kiln目录1 前言 (3)2 原材料、燃料的选择 (3)2.1 生料 (3)2.2 燃料 (3)2.3 水泥 (4)3 配方 (4)4 生产工艺 (4)4.1 生产线选择 (4)4.2 热耗 (4)4.3 生产线布置 (4)4.4 水泥原料、燃料所采用的预均化措施 (5)4.5 生料、水泥的均化与贮存措施 (5)4.5.1 均化 (5)4.5.2 贮存 (5)4.6 环境保护、节能降耗措施 (5)4.6.1 环境保护 (5)4.6.2 节能降耗 (5)4.7 电力、运输措施 (6)5 工艺平衡设计 (6)5.1 1吨熟料的生料需要量 (6)5.2 1吨熟料需要的原材料 (6)5.3 1吨熟料需煤量、熟料热耗 (6)5.4 1吨熟料制成水泥需要的石膏、粉煤灰 (6)5.5 物料平衡表 (6)5.6 各个工艺环节的储存量 (7)5.7 设备选型与库房类型 (7)5.7.1 设备选型 (7)5.7.2 库房类型 (8)5.8 总图布置 (10)6 结语 (10)参考文献 (11)1 前言水泥是国民经济的基础材料,在日常生活中随处可见,水泥工业是重化工工业,它的特点是对矿产资源的依存性大,物料储运量多,能量消耗高,在设计工作中对这些问题必须予以足够的认识。
水泥制品的生产工艺改进
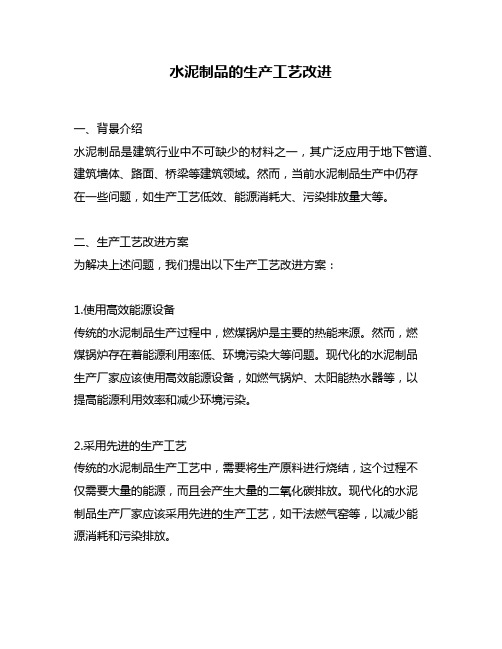
水泥制品的生产工艺改进一、背景介绍水泥制品是建筑行业中不可缺少的材料之一,其广泛应用于地下管道、建筑墙体、路面、桥梁等建筑领域。
然而,当前水泥制品生产中仍存在一些问题,如生产工艺低效、能源消耗大、污染排放量大等。
二、生产工艺改进方案为解决上述问题,我们提出以下生产工艺改进方案:1.使用高效能源设备传统的水泥制品生产过程中,燃煤锅炉是主要的热能来源。
然而,燃煤锅炉存在着能源利用率低、环境污染大等问题。
现代化的水泥制品生产厂家应该使用高效能源设备,如燃气锅炉、太阳能热水器等,以提高能源利用效率和减少环境污染。
2.采用先进的生产工艺传统的水泥制品生产工艺中,需要将生产原料进行烧结,这个过程不仅需要大量的能源,而且会产生大量的二氧化碳排放。
现代化的水泥制品生产厂家应该采用先进的生产工艺,如干法燃气窑等,以减少能源消耗和污染排放。
3.使用高效的热轧设备在水泥制品生产过程中,需要对原材料进行热轧处理。
传统的热轧设备存在着能源消耗大、工艺复杂等问题。
现代化的水泥制品生产厂家应该使用高效的热轧设备,如电热炉、感应炉等,以提高生产效率和减少能源消耗。
4.采用智能化控制系统传统的水泥制品生产过程中,需要大量的人力进行操作和监测。
现代化的水泥制品生产厂家应该采用智能化控制系统,以实现生产过程的自动化、智能化,提高生产效率和质量。
5.使用环保原材料传统的水泥制品生产过程中,主要使用的是石灰石、粘土等原材料。
这些原材料存在着开采成本高、污染排放量大等问题。
现代化的水泥制品生产厂家应该使用环保原材料,如废弃物、废旧钢材等,以减少对环境的影响。
三、实施效果评估通过实施上述生产工艺改进方案,可以达到以下效果:1.减少能源消耗采用高效能源设备、先进的生产工艺和高效的热轧设备可以减少能源消耗,降低生产成本。
2.减少污染排放采用先进的生产工艺、智能化控制系统和环保原材料可以减少污染排放,提高企业形象。
3.提高生产效率采用智能化控制系统和高效的热轧设备可以提高生产效率,增加企业盈利。
水泥厂设计范文
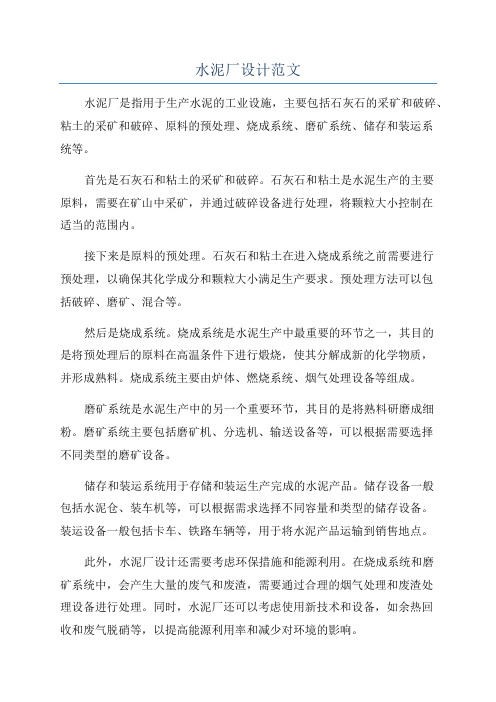
水泥厂设计范文水泥厂是指用于生产水泥的工业设施,主要包括石灰石的采矿和破碎、粘土的采矿和破碎、原料的预处理、烧成系统、磨矿系统、储存和装运系统等。
首先是石灰石和粘土的采矿和破碎。
石灰石和粘土是水泥生产的主要原料,需要在矿山中采矿,并通过破碎设备进行处理,将颗粒大小控制在适当的范围内。
接下来是原料的预处理。
石灰石和粘土在进入烧成系统之前需要进行预处理,以确保其化学成分和颗粒大小满足生产要求。
预处理方法可以包括破碎、磨矿、混合等。
然后是烧成系统。
烧成系统是水泥生产中最重要的环节之一,其目的是将预处理后的原料在高温条件下进行煅烧,使其分解成新的化学物质,并形成熟料。
烧成系统主要由炉体、燃烧系统、烟气处理设备等组成。
磨矿系统是水泥生产中的另一个重要环节,其目的是将熟料研磨成细粉。
磨矿系统主要包括磨矿机、分选机、输送设备等,可以根据需要选择不同类型的磨矿设备。
储存和装运系统用于存储和装运生产完成的水泥产品。
储存设备一般包括水泥仓、装车机等,可以根据需求选择不同容量和类型的储存设备。
装运设备一般包括卡车、铁路车辆等,用于将水泥产品运输到销售地点。
此外,水泥厂设计还需要考虑环保措施和能源利用。
在烧成系统和磨矿系统中,会产生大量的废气和废渣,需要通过合理的烟气处理和废渣处理设备进行处理。
同时,水泥厂还可以考虑使用新技术和设备,如余热回收和废气脱硝等,以提高能源利用率和减少对环境的影响。
总之,水泥厂设计需要综合考虑原料的采矿和破碎、预处理、烧成系统、磨矿系统、储存和装运系统等各个环节,同时还需要考虑环保和能源利用等因素,以确保水泥生产的高效性和可靠性。
日产2500吨水泥熟料干法水泥厂设计资料
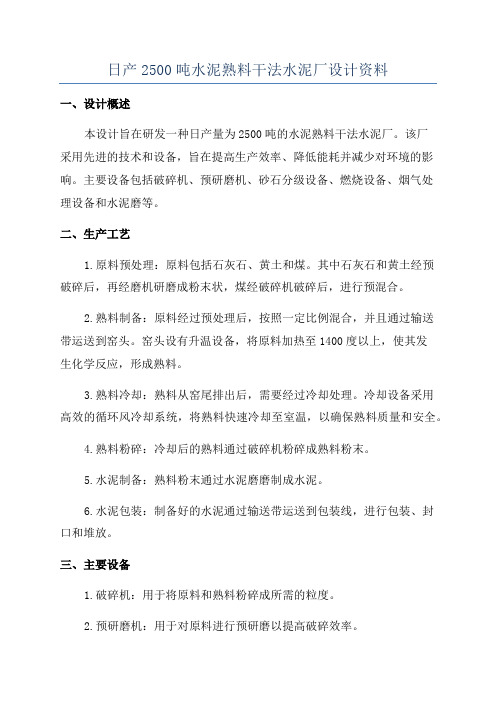
日产2500吨水泥熟料干法水泥厂设计资料一、设计概述本设计旨在研发一种日产量为2500吨的水泥熟料干法水泥厂。
该厂采用先进的技术和设备,旨在提高生产效率、降低能耗并减少对环境的影响。
主要设备包括破碎机、预研磨机、砂石分级设备、燃烧设备、烟气处理设备和水泥磨等。
二、生产工艺1.原料预处理:原料包括石灰石、黄土和煤。
其中石灰石和黄土经预破碎后,再经磨机研磨成粉末状,煤经破碎机破碎后,进行预混合。
2.熟料制备:原料经过预处理后,按照一定比例混合,并且通过输送带运送到窑头。
窑头设有升温设备,将原料加热至1400度以上,使其发生化学反应,形成熟料。
3.熟料冷却:熟料从窑尾排出后,需要经过冷却处理。
冷却设备采用高效的循环风冷却系统,将熟料快速冷却至室温,以确保熟料质量和安全。
4.熟料粉碎:冷却后的熟料通过破碎机粉碎成熟料粉末。
5.水泥制备:熟料粉末通过水泥磨磨制成水泥。
6.水泥包装:制备好的水泥通过输送带运送到包装线,进行包装、封口和堆放。
三、主要设备1.破碎机:用于将原料和熟料粉碎成所需的粒度。
2.预研磨机:用于对原料进行预研磨以提高破碎效率。
3.砂石分级设备:用于对原料和熟料进行分级,以确保所需粒度的熟料。
4.燃烧设备:用于产生燃烧所需的高温。
5.烟气处理设备:用于处理燃烧产生的废气,以满足环保要求。
6.水泥磨:用于将熟料粉末磨制成所需粒度的水泥。
7.包装线:用于将水泥进行包装、封口和堆放。
四、环保考虑为了减少对环境的影响,设计中采用了一系列环保措施,包括有限压入装置、除尘设备、废气回收利用系统等。
通过这些措施,可以减少燃烧过程中的氮氧化物、二氧化硫等有害气体的排放,并且降低能耗,提高能源利用效率。
五、总结本设计概述了一种日产2500吨水泥熟料干法水泥厂的设计资料,包括生产工艺、主要设备以及环保考虑。
通过先进的技术和设备,该厂旨在提高生产效率、降低能耗并减少对环境的影响。
这一设计有望为水泥生产厂的建设和改造提供参考,并为相关领域的技术研发提供指导。
水泥制品的生产工艺改进
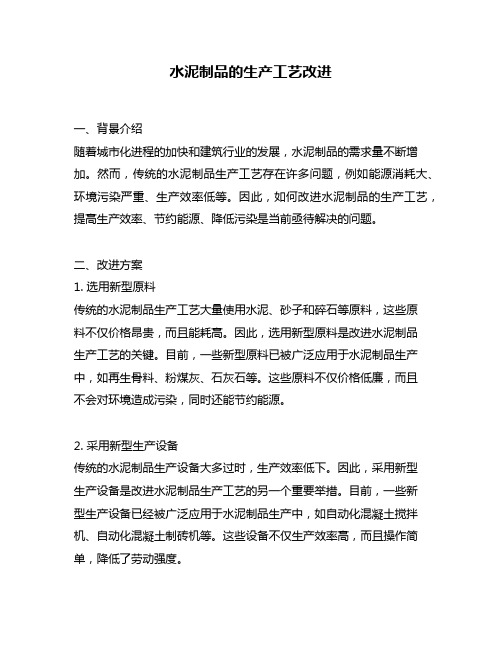
水泥制品的生产工艺改进一、背景介绍随着城市化进程的加快和建筑行业的发展,水泥制品的需求量不断增加。
然而,传统的水泥制品生产工艺存在许多问题,例如能源消耗大、环境污染严重、生产效率低等。
因此,如何改进水泥制品的生产工艺,提高生产效率、节约能源、降低污染是当前亟待解决的问题。
二、改进方案1. 选用新型原料传统的水泥制品生产工艺大量使用水泥、砂子和碎石等原料,这些原料不仅价格昂贵,而且能耗高。
因此,选用新型原料是改进水泥制品生产工艺的关键。
目前,一些新型原料已被广泛应用于水泥制品生产中,如再生骨料、粉煤灰、石灰石等。
这些原料不仅价格低廉,而且不会对环境造成污染,同时还能节约能源。
2. 采用新型生产设备传统的水泥制品生产设备大多过时,生产效率低下。
因此,采用新型生产设备是改进水泥制品生产工艺的另一个重要举措。
目前,一些新型生产设备已经被广泛应用于水泥制品生产中,如自动化混凝土搅拌机、自动化混凝土制砖机等。
这些设备不仅生产效率高,而且操作简单,降低了劳动强度。
3. 推广先进生产工艺传统的水泥制品生产工艺存在许多弊端,如生产效率低、能耗高、污染严重。
因此,推广先进生产工艺是改进水泥制品生产工艺的另一重要途径。
目前,一些先进生产工艺已经被广泛应用于水泥制品生产中,如混凝土预制块生产工艺、石膏制品生产工艺等。
这些生产工艺不仅能够提高生产效率,而且能够节约能源,降低污染。
4. 加强环保意识水泥制品生产工艺存在污染环境的问题,因此,加强环保意识是改进水泥制品生产工艺的关键。
企业应该认识到环保的重要性,采用环保的生产工艺和设备。
同时,严格遵守环保法律法规,做好废水、废气、废渣的处理工作,减少环境污染。
三、改进效果通过以上改进措施,水泥制品生产工艺得到了明显的改进,主要表现在以下几个方面:1. 生产效率提高了。
采用新型原料和生产设备,能够大大提高生产效率,降低劳动强度。
同时,推广先进生产工艺,也能够提高生产效率。
2. 能源消耗降低了。
水泥厂工艺设计概论课程设计
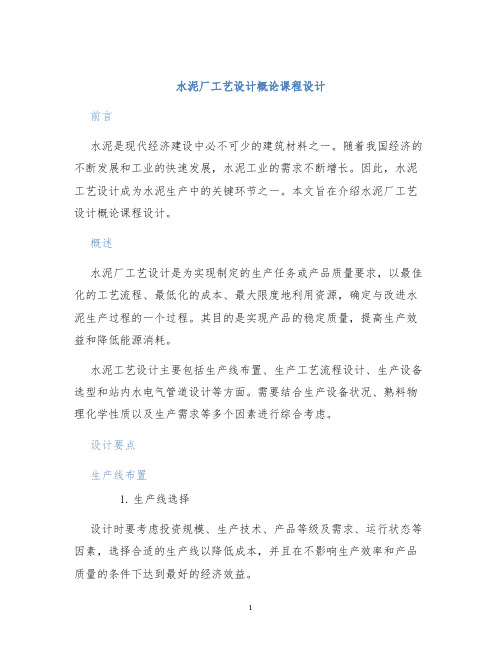
水泥厂工艺设计概论课程设计前言水泥是现代经济建设中必不可少的建筑材料之一。
随着我国经济的不断发展和工业的快速发展,水泥工业的需求不断增长。
因此,水泥工艺设计成为水泥生产中的关键环节之一。
本文旨在介绍水泥厂工艺设计概论课程设计。
概述水泥厂工艺设计是为实现制定的生产任务或产品质量要求,以最佳化的工艺流程、最低化的成本、最大限度地利用资源,确定与改进水泥生产过程的一个过程。
其目的是实现产品的稳定质量,提高生产效益和降低能源消耗。
水泥工艺设计主要包括生产线布置、生产工艺流程设计、生产设备选型和站内水电气管道设计等方面。
需要结合生产设备状况、熟料物理化学性质以及生产需求等多个因素进行综合考虑。
设计要点生产线布置1.生产线选择设计时要考虑投资规模、生产技术、产品等级及需求、运行状态等因素,选择合适的生产线以降低成本,并且在不影响生产效率和产品质量的条件下达到最好的经济效益。
2.生产线布局要根据调度的要求、物料和能量流动的传递、工艺路线的选择、人员配备以及职业健康和安全要求等因素进行整体规划,从而完善布局的设计,保证生产线的稳定运行和高效执行。
生产工艺流程设计1.熟料生产熟料生产是整个水泥生产过程的核心环节,同时也是消耗能量和原材料最大的一个部分。
因此,熟料工艺流程的设计直接决定了生产成本和产品质量。
2.水泥生产水泥生产过程是通过在炭、膨胀剂和水等掺合材料的作用下形成“熟土”状的物料,并通过磨粉设备将其细磨成线毫米级以下的水泥粉末,在磨煤机或者气流磨机中进行磨粉。
在整个水泥工艺流程中,水泥磨粉环节的加工费用是最大的,也是后期工艺流程的重点环节。
生产设备选型1.设备选择在设备选择时,要考虑设备能力符合生产规模、设备的技术水平、设备的经济性以及设备的可靠性等问题。
对于不同型号的设备,还要进行综合考虑,包括单位能耗、使用寿命、安全性、维护保养费用以及设备使用时的反应等因素。
2.设备布置设备布置时要根据设备功能、管道系统、气流所在的位置、设备水平度和垂直度等因素进行综合考虑,使得设备之间的生产连续性高,并且避免安全事故和环境污染。
年产230万吨P.S.A42.5水泥生产线制成车间工艺设计_毕业设计 精品
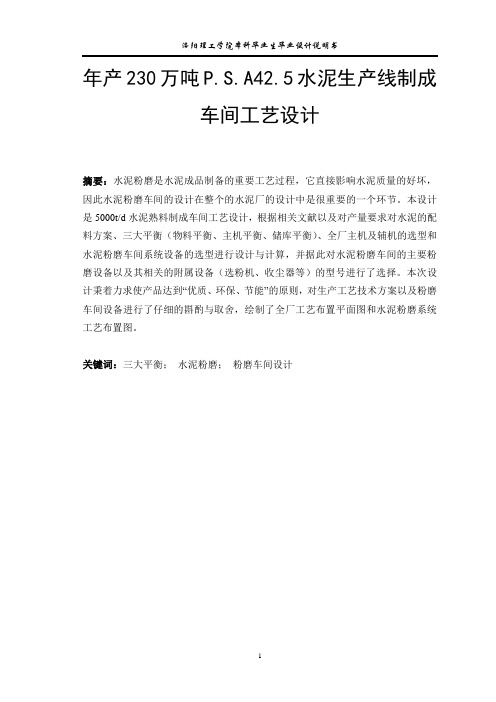
该系统具有易操作、使用维护简单的特点,原煤经全密闭计量给煤机喂入辊式磨烘干粉磨。烘干所需要的热源取自窑头篦冷机的废气。在入磨物料粒度≤50mm,水分≤10%,出磨物料细度200目筛80%通过,水分≤1%的条件下,系统设计产量为40~48t/h,配置电机功率500KW。设有煤粉仓2个,1个为分解炉供煤,1个为回转窑供煤。窑头和分解炉喂煤采用菲斯特秤计量。窑与分解炉用煤比例为40%和60%。
Keyword: three great balances, cement grinding, the design of cement grinding plant
第1章绪论
1.1引言
新型干法水泥生产自问世以来倍受世界各国的关注,特别是上世纪80年代以来得到了突飞猛进的发展,国际水泥工业以预分解技术为核心,将现代科学技术和工业化生产的最新成果广泛应用于水泥生产的全过程,形成了一套具有现代高科技为特征和符合优质、高效、节能、环保以及大型化、自动化的现代生产方法。新型干法水泥技术代表了现阶段最高的水泥烧成技术,可以提高窑单位容积产量、提高窑砖衬寿命和运转率,且自动化水平高、生产规模大,可以选用低质燃料或低价废物燃料,节省燃料,降低热耗和电耗,减小设备和基建投资费用、CO和NOx生成量少和事故率低,操作稳定。发展新型干法水泥技术是环境保护和资源综合利用的必然结果。同时,新型干法水泥技术涵盖了许多丰富的理论和科研成果,指导着水泥工业设计、研发、生产等工作的不断完善、优化和提升。近年来,我国新型干法水泥生产技术也得到了飞速发展。尤其是进入21世纪,大批4000,5000t/d熟料新型干法水泥生产线的建成、投产,标志着我国新型干法水泥生产技术已经成熟。
同时对原煤设置矩形预均化堆场,原煤成分的波动对烧成工艺、热工制度的稳定性及熟料质量等影响极大,外购煤的质量难以完全预先控制,同时多点供应原煤的可能性是存在的,并且考虑将来使用低品位原煤的需要,故设置原煤预均化设施(储存10天)。原煤预均化堆场规格为35×109m,堆场有效储量7094.59t。
华新水泥_西藏_公司1000t_d水泥生产线工艺设计
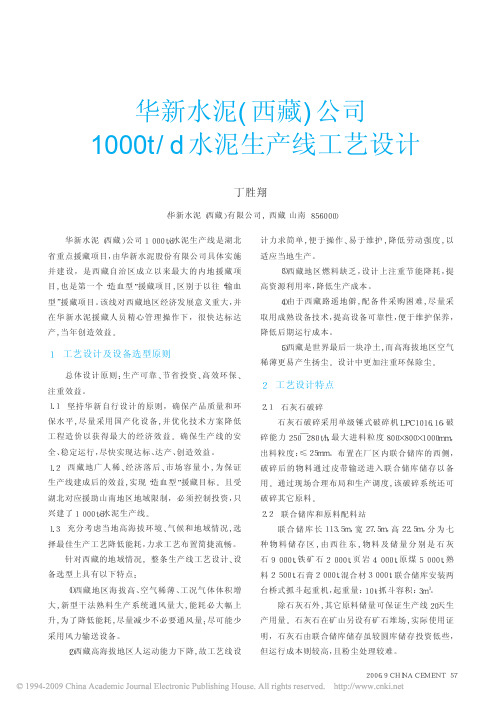
配料站配好物料, 进入华新自主设计制造的 !3.8m×9m双滑履磨粉磨。磨机采用开流生产, 粉磨出 的生料通过空气输送斜槽输送, 经入库斗式提升机提 升进入均化库储存。
西藏由于气候干燥, 原料含水率低, 采用开流磨 生产在本地区能满足生产要求, 但磨机产能受季节和 原料水份的影响较大。 2.4 窑磨废气处理
冷 却 机 采 用 第 三 代 空 气 梁 篦 式 冷 却 机 LBT6×28 , 篦床有效面积26.5m2, 三段篦床, 一段传动。出冷却机 熟料温度设计为环境温度+25℃, 在冷却机前部下料 处安装有四台自动控制喷吹的空气炮, 防止 “堆雪 人”。在冷却机后部侧壁装有三对喷头, 喷水雾化降 低了入电收尘空气温度, 改善气体比电阻, 提高收尘 效率。
增湿塔和窑尾袋除尘器收下的窑灰, 均由螺旋输 送机输送, 经入库斗式提升机入均化库。ID风机采取 前置式布置。
由于高海拔地区空气稀薄, 为保证系统内合理风 速, 利于热传递, 降低热耗, 窑径和管道均较海平面同 等生产企业大, 系统表面散热加大, 实际运行中增湿 塔喷水量极小。 2.5 生料入窑
从均化库出来的生料, 经空气斜槽输送、通过斗 式提升机提升进入称重仓。出称重仓物料通过冲板 式流量计计量, 经斗式提升机提升, 由空气斜槽输送 入窑。 2.6 熟料烧成系统
除石灰石外, 其它原料储量可保证生产线20天生 产用量。石灰石在矿山另设有矿石堆场, 实际使用证 明, 石灰石由联合储库储存虽较圆库储存投资低些, 但运行成本则较高, 且粉尘处理较难。
日产5000吨熟料水泥生产线工艺设计参数设计

日产5000吨熟料水泥生产线工艺设计参数设计
1.原料特性
水泥生产过程中主要使用的原料包括石灰石、粘土和铁矿石等。
在设
计参数中需要考虑原料的质量、成分、粒度等特性。
这些参数将影响到熟
料的品质和水泥的性能。
2.熟料生产过程
熟料的生产过程包括原料的破碎、磨煤、入窑煅烧和冷却等。
在这些
过程中,需要合理选择破碎设备、磨煤设备和烧结设备等。
设计参数中需
要确定适当的产能和加料量,以确保生产过程的稳定性和效率。
3.能耗
水泥生产是一个能耗较大的过程,因此在工艺设计参数中需要考虑能
耗的降低。
可以通过优化工艺流程、改善设备效率、使用低能耗材料等方
式来实现。
例如,可以采用热电联供、余热回收和高效燃烧等技术手段,
降低能耗并减少对环境的影响。
4.水泥品质
水泥的品质直接影响到建筑物的质量和持久性。
在设计参数中需要考
虑水泥的强度、凝结时间、收缩性等指标。
可以通过控制原料成分、熟料
烧成温度和冷却速度等方式,确保水泥的品质达到要求。
5.环保要求
水泥生产过程中会产生大量的废气、废水和固体废物。
在设计参数中
需要考虑环保要求,采取相应的措施进行处理和治理。
可以通过装置废气
净化设备、废水处理系统和固体废物处理设施等手段,减少对环境的影响。
以上是对日产5000吨熟料水泥生产线工艺设计参数设计的一般性建议。
具体设计时还需要根据实际情况进行合理的细化和调整,以实现经济、环保和可持续发展。
水泥车间工艺设计
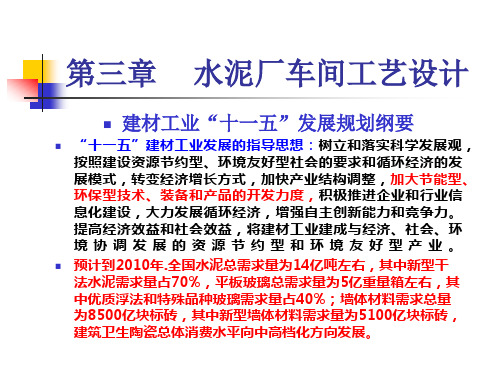
建材行业十一五回顾
国家技术发明二等奖2项,科技进步一等奖1项、二等奖4项;建材行业 科学技术奖一等奖40项、二等奖102项、三等奖88项。
1.一批产业技术装备成为国家竞争力代表
以SINOMA品牌为代表的中国新型干法水泥技术已成为国际上“中国制 造”形象和国家竞争力的优秀代表; 中国中材、中国建材向包括欧美发达国家在内的数十个国家出口大型成 套生产技术装备,并成为国际上最大的水泥生产线建设工程总承包商; 洛玻集团“超薄浮法玻璃成套技术与关键设备在电子玻璃工业化生产开 发应用”,开启了我国浮法玻璃技术生产超薄玻璃、满足信息产业发展 需求的先河,获得2006年国家科技进步一等奖; 中国玻纤开发了年产12万吨超大型玻璃纤维池窑拉丝技术,其规模创造 了玻纤行业世界纪录; 以中国建材国际工程公司为代表的“中国洛阳浮法”玻璃生产技术装备 与工程总承包得到国际市场高度认可,出口许多国家。
4.行业技术创新基础建设与资源开拓取得较大进步
建材行业拥有国家级企业技术中心、工程技术研究中 心20余家,拥有重点实验室5家; 大中型企业基本上建立了企业技术中心; 中国建筑材料联合会从项目组织申报、课题论证、科 技成果评审鉴定和推介、建材行业科学技术奖和技术 革新奖评奖、国家科学技术奖的推荐、行业科技发展 报告、行业创新平台建设等方面建立系统的工作体系, 与国家科技部、发改委、工信部、环保部等政府主管 部门建立了工作关系,为行业和企业技术创新发展提 供了有效服务。
科技创新方向及重点领域
(三)大型节能粉磨技术与装备 以非金属矿业和原材料制造业的绿色节能和资源可持 续为重点,大力发展大型高效节能粉磨、无球化粉磨 等先进节能粉磨技术与装备,加快现有矿物粉磨技术 装备的节能改造和技术升级。 (四)支撑战略性产业发展的新材料技术 加强无机非金属新型晶体材料、特种结构与功能陶瓷 材料、高性能微晶陶瓷材料、纤维增强热塑性复合材 料、高端纤维增强复合材料、环保型高性能摩擦密封 材料的研究开发,突破关键材料制备和装备技术瓶颈, 在节能环保、新能源、信息产业、新材料、国防军工 等战略性产业领域中,以及在冶金、电力、交通运输、 建筑节能、煤炭、石化等领域发挥关键支撑作用。
2019年水泥厂设计说明设计.doc
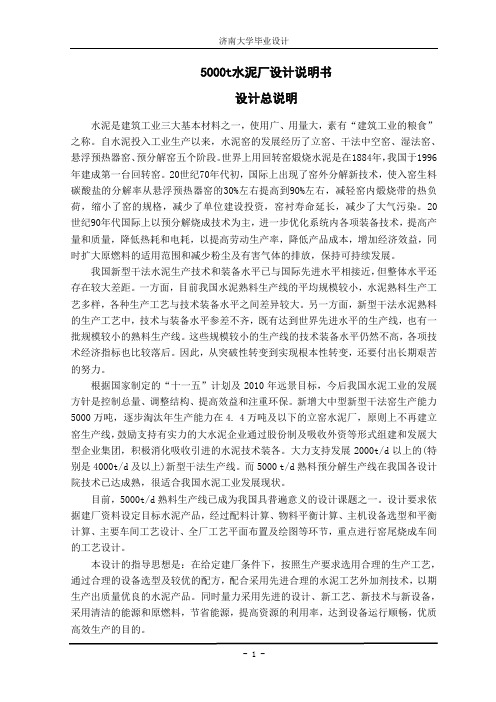
The design guidelines are: under the conditions of a given plant, select an appropriate production process in accordance with production requirements, through the rational and optimum equipment selection formula, with the use of advanced technology and reasonable cement additive process to produce good quality of cement products. At the same time as more as possiblely use advanced design, new processes, new technology and new equipment, the use of clean energy and raw fuel, save energy, improve resource utilization, to achieve high quality and high purpose and make the equipments go smoothly.
- 1、下载文档前请自行甄别文档内容的完整性,平台不提供额外的编辑、内容补充、找答案等附加服务。
- 2、"仅部分预览"的文档,不可在线预览部分如存在完整性等问题,可反馈申请退款(可完整预览的文档不适用该条件!)。
- 3、如文档侵犯您的权益,请联系客服反馈,我们会尽快为您处理(人工客服工作时间:9:00-18:30)。
水泥厂工艺设计概况 WEIHUA system office room 【WEIHUA 16H-WEIHUA WEIHUA8Q8-上图为水泥厂工艺流程水泥厂主要的生产车间包含:物料的破碎(石灰石、黏土、砂岩、页岩、铁矿石、原煤、石膏等),熟料储存,熟料散装,煤粉制备,原、燃料储存或预均化,混合材及石膏的储存,原料配料站,水泥配料站,原料粉磨及废气处理,水泥粉磨,水泥储存,生料均化库,水泥散装、包装及发运,生料入窑,压缩空气站,烧成窑尾,化验室,中央控制室,烧成窑中,矿渣微粉粉磨系统,烧成窑头等。
物料的破碎在水泥生产中,大部分的物料都需要先经过破碎,如石灰石、粘土、砂岩、粉砂岩、铁矿石、煤、熟料、石膏、混合材等等,破碎的目的是为后续的粉磨、输送、储存等工序创造良好条件。
水泥厂破碎车间一般设有石灰石破碎、辅助原料破碎车间。
原煤破碎、石膏破碎等根据具体工厂来料情况决定是否设置。
水泥厂中破碎量最大的物料是石灰石,每生产1吨熟料大约需要石灰石~吨左右。
破碎机选用:常用于石灰石破碎的破碎机种类有:锤式破碎机、反击式破碎机、颚式破碎机、旋回式破碎机、园锥式破碎机等,锤式破碎机、反击式破碎机一段破碎即可满足要求,颚式破碎机、旋回式破碎机用于二段破碎的一级破碎,圆锥破用于二段破碎的二级破碎。
粘土破碎采用齿辊破碎机、冲击式破碎机等。
砂岩、粉砂岩破碎采用反击式破碎机,也有采用颚式破碎机、锤式破碎机等。
原煤破碎采用环锤式破碎机、立轴式破碎机、颚式破碎机等。
石膏破碎采用锤式破碎机、颚式破碎机等。
物料的储存水泥厂是连续运行的工厂,为了避免外部运输的不均衡、设备能力之间的不平衡、上下工序间生产班制的不同,质量检验的要求以及由于其它原因造成物料供应的中断,保证工厂正常地进行生产,要求各种原材料、燃料、半成品、成品在工厂内部都要有一定的储存量。
某物料的储存量所能满足工厂生产需要的天数,称为该物料的储存期。
物料的储存方式:露天堆场:未破碎的大块的石灰石、石膏等。
简易堆棚:辅助原料、原煤、石膏、混合材等。
联合储库:辅助原料、原煤、石膏、混合材等。
圆库(仓) :含水量小的小块状、颗粒状、粉状等非粘性物料,如碎石灰石、粉煤灰、干矿渣(粉) 、熟料、水泥等。
预均化堆场:石灰石、辅助原料、原煤等。
物料的均化生料化学成分的均齐性,不仅直接影响熟料的质量,而且对窑的产量、热耗、运转周期、耐火材料的寿命等都有较大的影响,这些影响对现代大型干法回转窑尤其敏感。
为了保证窑的稳产高产,必须进行生料的均化,减少入窑生料的化学成分波动,保证入窑生料化学成分的稳定。
由于水泥厂是以天然矿物作为原料,随着矿山开采层位、开采地段的不同,原料的成分波动在所难免,除应注意选择合理开采方案,尽量减少进厂原料成分波动以外,在要求配制成分稳定的生料方面,当然又不能苛求于矿山。
因此,还应对原料、生料采取有效的均化措施以满足生产要求。
原料的预均化原料的预均化是在堆料和取料过程中在预均化堆场内实现的。
水泥厂根据原料成分波动情况一般对石灰石、硅质原料(粘土、砂岩等)、燃料(煤)分别进行预均化。
也有厂将石灰石与粘土混合预均化的。
预均化堆场的型式常用的预均化堆场有长形预均化堆场、圆形预均化堆场。
长形预均化堆场:长形预均化堆场设置两个堆料区,一个区堆料,另一个区取料,两区交替使用。
长形预均化堆场具有扩建方便的优点。
长形预均化堆场(桥取)用于石灰石、原煤。
长形预均化堆场(侧取)用于辅助原料、原煤。
圆形预均化堆场:只有一个料堆,连续堆料和取料。
同等储量的条件下,圆形堆场占地面积小,设备的费用和维护费用均较低。
但由于有出料隧道,当地下水位较高时也有其不利之处,另外,无法扩建。
圆形预均化堆场的均化效果不如长形预均化堆场。
2500t/d直径为60000。
2500t/d、3200t/d、 5000t/d直径为80000。
5000t/d、6000t/d直径为90000。
6000t/d、 10000t/d直径为110000。
生料的均化出磨的生料其化学成分总难免有波动,必须经过均化以至调整,才能满足入窑生料控制指标的要求,一般入窑生料碳酸钙含量的标准偏差控制在±%。
新型干法水泥生产线都采用连续均化库系统。
其优点是流程简单、操作管理方便、便于自动控制等。
常用的生料均化库型式有:MF库、IBAU库、CP库、CF库等。
常用生料均化库的规格:2500t/d、3200t/d:Ф16 X 48m,储量:7000t。
5000t/d、6000t/d :Ф20 X 64m,储量:17600t。
6000t/d、7000t/d :Ф X 66m,储量:20000t。
10000t/d: 2 ?- Ф20X 64m,储量:2 × 17600t。
常用熟料库的规格:Ф15 X 36 m,储量:7500t。
Ф18 X 40 m,储量:10000t。
Ф22 X 50 m,储量:20000t。
Ф32 X 28m,储量:25000t。
Ф45 X 38m,储量:50000t。
Ф60 X 41m,储量:100000t。
常用水泥库的规格及储量:Ф12 X 30 m,储量:3500t。
Ф15 X 35 m,储量:6500t。
Ф18 X 45m,储量:10000t。
Ф22 X 60 m,储量:20000t。
物料的粉磨水泥工厂是能源消耗大户,而物料在粉磨过程中要消耗大量的电能。
在水泥生产过程中,磨制生料、制备煤粉和制成水泥,都要进行粉磨作业。
用煤作燃料的水泥厂,每生产一吨水泥需要粉磨的物料量约~吨。
在全厂生产用电中,由于采用的粉磨设备的不同,电耗也不同,一般而言,生料粉磨电耗为16~22kWh/t ,煤磨电耗为30~35 kWh/t,水泥电耗为30~40kWh/t。
全厂粉磨电耗占全部电耗的60%以上。
因此,合理的选择粉磨流程和设备,保证粉磨产品的质量并降低粉磨电耗,对于水泥厂的生产有着重要的意义。
随着现代干法窑规格的日益扩大,单台窑的产量已达到10000t/d以上,与窑配套的磨机规格也在朝着大型化方向发展,原料磨的台时产量已达到500t/h 以上,水泥磨的台时产量已达到250t/h 以上。
另外,磨机也在朝着节能方向发展,现在,在大中型水泥厂,原料粉磨越来越多地采用了辊式磨(立磨)和辊压机终粉磨系统,煤磨根据煤质情况尽可能地选用立磨系统,水泥粉磨系统则越来越多地采用了辊压机、辊式磨等节能的粉磨系统。
新型干法水泥厂目前有朝全厂无球化方向发展趋势。
即原料磨采用立磨或辊压机终粉磨、煤磨采用立磨、水泥磨采用立磨终粉磨。
辊压机终粉磨用于水泥粉磨的很少,主要是由于成品的颗粒形状及级配与球磨机有区别,影响水泥的性能。
原料粉磨新型干法水泥生产线中,原料粉磨常用以下几种粉磨流程:辊式磨、中卸磨、辊压机终粉磨。
辊式磨(立磨):在2500t/d以上规模的生产线中,原料磨采用辊式磨的占绝对的多数。
主要优点是:体积小、占地面积小、噪声低、利用废气余热处理湿原料能力好、烘干物料水分大,台时产量大、入磨物料粒度大,而最大的优点在于粉磨电耗低(比管磨系统低6kWh/t生料)。
它的缺点是对磨琢性物料和金属夹杂物较敏感,磨辊及磨盘易磨损,不很适应研磨硬质物料等。
辊式磨的电耗一般在16~20 kWh/t生料。
球磨机(管磨):常用的球磨机系统有风扫磨、中卸磨及尾卸磨等。
常用于2500t/d及以下规模。
2500t/d规模以上用管磨系统的不多。
球磨机系统具有投资低、对原料的适应性强、生产可靠、运转率高产品细度均匀等优点。
缺点是流程复杂,电耗高。
风扫磨的电耗一般在20~24 kWh/t生料,中卸磨的电耗一般在19~22 kWh/t生料。
辊压机终粉磨系统:辊压机终粉磨系统近几年在国内水泥厂使用的越来越多,7000t/d等水泥厂均采用辊压机终粉磨系统。
优点是节能,电耗12~14kWh/t-生料,比立磨系统低。
缺点是设备运转率有待提高,此外,系统烘干能力不如立磨系统。
几种原料粉磨系统对原料的适用范围粉磨系统:原料的物理特性适用范围。
中卸磨:水分宜<6%,易磨性及磨蚀性均不限。
辊式磨:水分宜<8%,易磨性中等,磨蚀性正常。
辊压机终粉磨:水分宜<5%,易磨性及磨蚀性均不限。
原料粉磨系统入磨物料的粒度要求原料粉磨系统入磨物料的粒度要求应根据采用的原料磨的类型和系统确定:钢球磨系统(包括中卸磨、尾卸磨、风扫磨等)入磨物料粒度应≤25mm;辊式磨系统宜为≤75mm;辊压机系统的入磨物料粒度宜为≤50mm。
原料粉磨系统的选择原料粉磨系统的选择主要考虑下列因素:原料的物理特性,如入磨物料的粒度、水分、易磨性等;系统的产量要求;节能;操作及自控水平;系统的可靠性及运转率;投资和生产成本。
煤粉制备煤粉制备所用的设备,目前大都采用烘干风扫磨及辊式磨系统。
现代干法水泥窑的热耗与窑的规格有关,产量越高热耗越低,一般在730 ~ 850 kcal/kg-熟料。
折算到标煤为107 ~ 121kg/t-熟料。
相当于电耗~ kWh/t熟料。
煤粉制备系统的电耗对水泥的总电耗影响不是很大。
烟煤和无烟煤无烟煤和含煤矸石较多的烟煤不适合采用立磨粉磨。
无烟煤挥发份低(小于5%) ,热值一般较高,可达到23450 ~ 27885kJ/kg。
由于挥发份低,煤粉着火温度高,燃烬时间长。
烟煤着火温度410 ~430℃,燃烧延续时间约10min,在600~650℃燃烬。
无烟煤着火温度550℃,燃烧延续时间约14min,在850℃燃烬。
粉磨烟煤和无烟煤在细度也有区别:烟煤煤粉细度为88μm筛筛余8%~15%,无烟煤煤粉细度为88μm筛筛余3%~5%。
随着煤粉细度的变化,无烟煤着火温度和燃烬温度的变化幅度比烟煤大,这主要是无烟煤中挥发份低、固定碳含量高的缘故。
无烟煤的热量主要来自固定碳,无烟煤的着火温度和燃烧时间主要取决于固定碳的燃烧性能。
固定碳是固体颗粒,结构致密,与烟煤中较多的可烟气体(挥发份)相比,其燃点较高,燃烧速度慢。
煤粉细度的改变主要是改变了固定碳的粒度,使燃烧面积发生变化。
水泥粉磨水泥粉磨流程:水泥粉磨系统流程种类较多,目前常用的有以下几种流程:①管磨开流;②管磨圈流;③辊压机开流+管磨开流;④辊压机圈流+管磨开流;⑤辊压机开流+管磨圈流;⑥辊压机圈流+管磨圈流;⑦辊式磨终粉磨等。
目前常用的水泥粉磨流程有:辊压机圈流+管磨开流、辊压机圈流+管磨圈流系统。
立磨预粉磨系统国内水泥厂用的不多、立磨终粉磨系统也不多,但是未来发展的趋势。
圈流水泥粉磨系统的优点:与开流水泥磨相比,圈流水泥磨具有如下优点:有利于降低水泥温度,防止石膏脱水;调节水泥细度方便;小于45微米的细粉较多,有利于提高28天的水泥强度;粉磨电耗低一些。
辊压机+管磨水泥粉磨系统的优点:与管磨圈流水泥磨相比,具有如下优点:产量高,电耗低。