带电流截止负反馈转速单闭环直流调速系统建模与仿真
转速反馈单闭环直流调速系统仿真
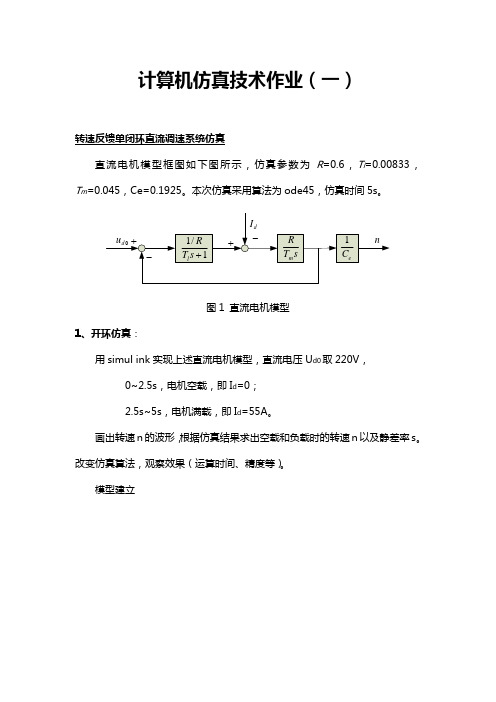
计算机仿真技术作业(一)转速反馈单闭环直流调速系统仿真直流电机模型框图如下图所示,仿真参数为R=0.6,T l=0.00833,T m=0.045,Ce=0.1925。
本次仿真采用算法为ode45,仿真时间5s。
图1 直流电机模型1、开环仿真:用simul ink实现上述直流电机模型,直流电压U d0取220V,0~2.5s,电机空载,即I d=0;2.5s~5s,电机满载,即I d=55A。
画出转速n的波形,根据仿真结果求出空载和负载时的转速n以及静差率s。
改变仿真算法,观察效果(运算时间、精度等)。
模型建立1)Ode45算法空载转速为1142n/min,负载转速为972n/min,运算时间为T=9.134*10^-7s。
分析:这可以看出来在加入负载之后,电机的转速开始下降。
根据电机转差率的公式s=(n0-n)/ n0=(1142-972)/1142=0.149。
转差率还是比较小的,说明该电机效率比较高。
通过观察该仿真的时间,其运算时间为T=9.134*10^-7s。
2)Ode23算法分析:由图我们可以看出来,结果基本上和计算方法为ode45的结果一样,但是运算时间却不一样,该算法的运算时间为T=3.636*10^-7s。
运算时间比ode45的时间短。
但是ode23的计算精度不太高,所以ode23一般用于计算精度不太高的场合。
在求解的不太难的时候ode23可能比ode45有效。
3)Ode113算法仿真结果也大致和上面两种运算方法的结果一致。
ode113是一种阶数可变的解法器,它在误差容许要求严格的情况下通常比ode45有效。
ode113是一种多步解法器,也就是在计算当前时刻输出时,它需要以前多个时刻的解。
运算时间为T=3.593*10^-8s。
运算时间比上述两种方法的运算时间都要短。
这种计算方法使用于高低精度的运算。
总结:对mat lab中不同的计算方法,其结果基本上相差不多,但是其计算精度却是不相同的,此时我们就可以根据我们所需要的精度选择我们需要的运算方法。
转速、电流反馈控制直流调速系统的仿真-(终极版)
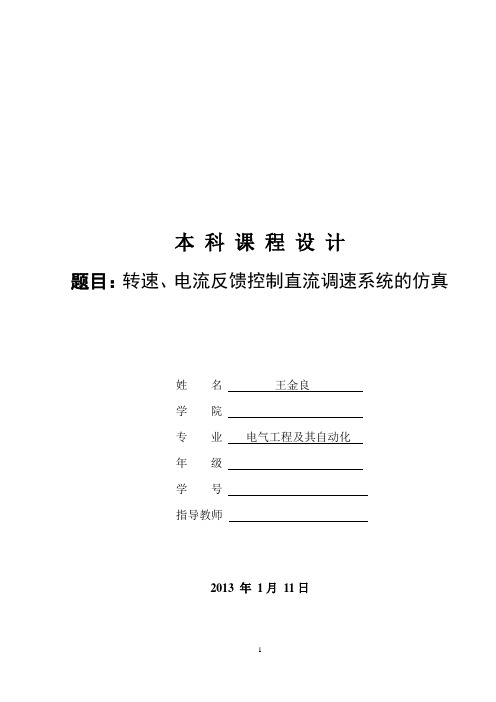
本科课程设计题目:转速、电流反馈控制直流调速系统的仿真姓名王金良学院专业电气工程及其自动化年级学号指导教师2013 年1月11日转速、电流反馈控制直流调速系统仿真摘要转速、电流反馈控制的直流调速系统是静、动态性能优良、应用最广泛的直流调速系统,对于需要快速正、反转运行的调速系统,缩短起动、制动过程的时间成为提高生产效率的关键。
为了使转速和电流两种负反馈分别起作用,可在系统里设置两个调节器,组成串级控制。
本文介绍了双闭环调速系统的基本原理,而且用Simulink 对系统进行仿真。
关键词:双闭环调速、转速、电流、Simulink一、 设计的题目及任务〔一〕概述本次仿真设计需要用到的是Simulink 仿真方法,Simulink 是Matlab 最重要的组件之一,它提供一个动态系统建模、仿真和综合分析的集成环境。
在该环境中,无需大量书写程序,而只需要通过简单直观的鼠标操作,就可构造出复杂的系统。
Simulink 具有适应面广、结构和流程清晰及仿真精细、贴近实际、效率高、灵活等优点,并基于以上优点Simulink 已被广泛应用于控制理论和数字信号处理的复杂仿真和设计。
〔二〕仿真题目某晶闸管供电的双闭环直流调速系统,整流装置采用三相桥式电路,基本数据如下:直流电机参数为:额定电压220V U =,额定电流136I A =; 额定转速n 1460rpm =,0.132min/e V r C =⋅, 允许过载倍数 1.5λ=; 晶闸管装置放大系数40s K =; 电枢回路总电阻0.5R =Ω; 时间常数0.03,0.18l m s s T T ==; 电流反馈系数0.05/V A β=; 转速反馈系数α=0.00666Vmin/r 。
〔三〕要完成的任务1〕用MATLAB建立电流环仿真模型;2〕分析电流环不同参数下的仿真曲线;3〕用MATLAB建立转速环仿真模型;4〕分析转速环空载起动、满载起动、抗扰波形图仿真曲线。
【设计】自动控制系统课程设计转速单闭环直流电机调速系统设计与仿真
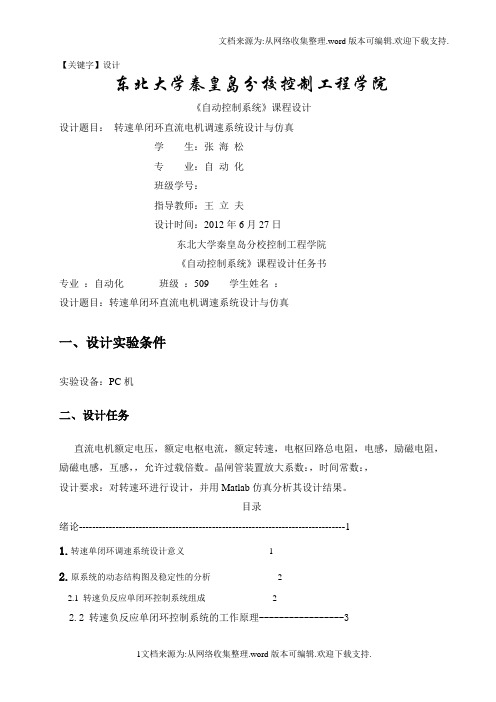
【关键字】设计东北大学秦皇岛分校控制工程学院《自动控制系统》课程设计设计题目:转速单闭环直流电机调速系统设计与仿真学生:张海松专业:自动化班级学号:指导教师:王立夫设计时间:2012年6月27日东北大学秦皇岛分校控制工程学院《自动控制系统》课程设计任务书专业:自动化班级:509 学生姓名:设计题目:转速单闭环直流电机调速系统设计与仿真一、设计实验条件实验设备:PC机二、设计任务直流电机额定电压,额定电枢电流,额定转速,电枢回路总电阻,电感,励磁电阻,励磁电感,互感,,允许过载倍数。
晶闸管装置放大系数:,时间常数:,设计要求:对转速环进行设计,并用Matlab仿真分析其设计结果。
目录绪论--------------------------------------------------------------------------------11.转速单闭环调速系统设计意义-----------------------------12.原系统的动态结构图及稳定性的分析-----------------------22.1 转速负反应单闭环控制系统组成-----------------------22.2 转速负反应单闭环控制系统的工作原理-----------------33.调节器的选择及设计-------------------------------------33.1调节器的选择- --------------------------------------33.2 PI调节器的设计--- ---------------------------------44.Mat lab仿真及结果分析----------------------------------74.1 simulink实现上述直流电机模型-----------------------74.2 参数设置并进行仿真---------------------------------74.3结果分析--------------------------------- ---------155.课设中遇到的问题--------------------------------------166.结束语- ---------------------------------------------17参考文献- ---------------------------------------------17转速单闭环直流电机调速系统设计与仿真绪论直流电动机由于调速性能好,启动、制动和过载转矩大,便于控制等特点,是许多高性能要求的生产机械的理想电动机。
转速反馈单闭环直流调速系统仿真
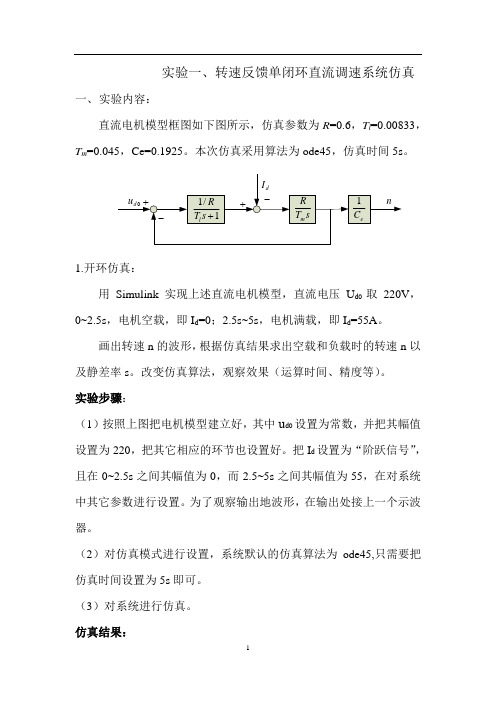
实验一、转速反馈单闭环直流调速系统仿真一、实验内容:直流电机模型框图如下图所示,仿真参数为R=0.6,T l=0.00833,T m=0.045,Ce=0.1925。
本次仿真采用算法为ode45,仿真时间5s。
1.开环仿真:用Simulink实现上述直流电机模型,直流电压U d0取220V,0~2.5s,电机空载,即I d=0;2.5s~5s,电机满载,即I d=55A。
画出转速n的波形,根据仿真结果求出空载和负载时的转速n以及静差率s。
改变仿真算法,观察效果(运算时间、精度等)。
实验步骤:(1)按照上图把电机模型建立好,其中u d0设置为常数,并把其幅值设置为220,把其它相应的环节也设置好。
把I d设置为“阶跃信号”,且在0~2.5s之间其幅值为0,而2.5~5s之间其幅值为55,在对系统中其它参数进行设置。
为了观察输出地波形,在输出处接上一个示波器。
(2)对仿真模式进行设置,系统默认的仿真算法为ode45,只需要把仿真时间设置为5s即可。
(3)对系统进行仿真。
仿真结果:(1)仿真算法为ode45:图1 上图即为电机转速的仿真结果图,同图上我们可以看出来分为了两个阶段,其中第一个阶段(0~2.5s)为空载转速,第二阶段(2.5~5s)为满载转速。
空载转速为1142n/min。
在2.5s时加入了负载,通过仿真结果我们可以看出来,负载转速为972n/min。
这可以看出来在加入负载之后,电机的转速开始下降。
根据电机转差率的公式s=(n0-n)/ n0=(1142-972)/1142=0.149。
转差率还是比较小的,说明该电机效率比较高。
通过观察该仿真的时间,其运算时间为T=9.134*10^-7s。
(2)仿真算法为ode23:仿真结果图如图2所示,由图我们可以看出来,结果基本上和计算方法为ode45的结果一样,但是运算时间却不一样,该算法的运算时间为T=3.636*10^-7s。
运算时间比ode45的时间短。
带电流截止负反馈的转速单闭环直流调速系统

实验八带电流截止负反馈的转速单闭环直流调速系统一、实验目的(1)了解单闭环直流调速系统的原理、组成及各主要单元部件的原理。
(2)掌握晶闸管直流调速系统的一般调试方法及电流截止负反馈的整定。
(3)通过实验,加深理解负反馈原理及转速负反馈电流截止负反馈的在调速系统中的作用。
二、实验所需挂件及附件三、实验线路及原理为了提高直流调速系统的动静态性能指标,通常采用闭环控制系统(包括单闭环系统和多闭环系统)。
对调速指标要求不高的场合,采用单闭环系统,而对调速指标较高的则采用多闭环系统。
按反馈的方式不同可分为转速反馈,电流反馈,电压反馈等。
在单闭环系统中,转速单闭环使用较多。
在本装置中,转速单闭环实验是将反映转速变化的电压信号作为反馈信号,经“速度变换”后接到“速度调节器”的输入端,与“给定”的电压相比较经放大后,得到移相控制电压U Ct,用作控制整流桥的“触发电路”,触发脉冲经功放后加到晶闸管的门极和阴极之间,以改变“三相全控整流”的输出电压,这就构成了速度负反馈闭环系统。
电机的转速随给定电压变化,电机最高转速由速度调节器的输出限幅所决定,速度调节器采用P(比例)调节对阶跃输入有稳态误差,要想消除上述误差,则需将调节器换成PI(比例积分)调节。
这时当“给定”恒定时,闭环系统对速度变化起到了抑制作用,当电机负载或电源电压波动时,电机的转速能稳定在一定的范围内变化。
在电流单闭环中,将反映电流变化的电流互感器输出电压信号作为反馈信号加到“电流调节器”的输入端,与“给定”的电压相比较,经放大后,得到移相控制电压U Ct,控制整流桥的“触发电路”,改变“三相全控整流”的电压输出,从而构成了电流负反馈闭环系统。
电机的最高转速也由电流调节器的输出限幅所决定。
同样,电流调节器若采用P(比例)调节,对阶跃输入有稳态误差,要消除该误差将调节器换成PI(比例积分)调节。
当“给定”恒定时,闭环系统对电枢电流变化起到了抑制作用,当电机负载或电源电压波动时,电机的电枢电流能稳定在一定的范围内变化。
单闭环直流调速系统的设计与仿真

大学本科毕业设计单闭环直流调速系统的设计与仿真学生姓名院系名称专业名称电气工程及其自动化班级级学号指导教师完成时间年月日单闭环直流调速系统的设计与仿真内容摘要:在对调速性能有较高要求的领域,如果直流电动机开环系统稳态性能不满足要求,可利用速度负反馈提高稳态精度,而采用比例调节器的负反馈调速系统仍是有静差的,为了消除系统的静差,可利用积分调节器代替比例调节器。
通过对单闭环调速系统的组成部分可控电源、由运算放大器组成的调节器、晶闸管触发整流装置、电机模型和测速电机等模块的理论分析,比较原始系统和校正后系统的差别,得出直流电机调速系统的最优模型。
然后用此理论去设计一个实际的调速系统,并用MATLAB仿真进行正确性的验证。
关键词:稳态性能稳定性开环闭环负反馈静差The design and simulation ofSingle loop dc speed control systemAbstract :In the higher demand for performance of speed, if the open loop dc system's steady performance does not meet the requirements, can use speed inverse feedback to improve steadystate precision, but although the speed inverse feedback system adopts proportion regulator,it still have off, in order to eliminate static, can use integral regulator to replace proportion regulator.Based on the theoretical analysis of the single closed loop system which is made up of controllable power, the regulator which is made up of operational amplifier, a rectifier triggered by thyristor , motor model and tachogenerators module, compare the difference of the open loop system and the closed loop system,the original system and the this paper compares the theory of open loop system and the closed-loop system, the difference of primitive system and calibrated system, conclude the optimal model of the dc motor speed control system. Then use this theory to design a practical control system, and verify the validity with MATLAB simulation.Key words: steady-statebehaviour stability open loop Close-loop feedback offset目录1绪论 (1)1.1直流调速系统概述 (1)1.2 MATLAB简介 (1)2 单闭环控制的直流调速系统简介 (2)2.1 V—M系统简介 (2)2.2转速控制闭环调速系统的调速指标 (2)2.3闭环调速系统的组成及静特性 (3)2.4反馈控制规律 (4)2.5主要部件 (5)2.5.1 比例放大器 (5)2.5.2 比例积分放大器 (5)2.5.3额定励磁下直流电动机 (7)2.6稳定条件 (8)2.7稳态抗扰误差分析 (8)3 单闭环直流调速系统的设计及仿真 (10)3.1参数设计及计算 (10)3.1.1参数给出 (10)3.1.2 参数计算 (10)3.2有静差调速系统 (11)3.2.1有静差调速系统的仿真模型 (11)3.2.2主要元件的参数设置 (12)3.2.3仿真结果及分析 (12)3.2.4 动态稳定的判断,校正和仿真 (13)3.3无静差调速系统 (15)3.3.1 PI串联校正的设计 (15)3.3.2无静差调速系统的仿真模型 (17)3.3.3主要元件的参数设置 (18)3.3.4仿真结果及分析 (18)3.4有静差调速系统和无静差调速系统的动态分析设计 (19)3.4.1有静差调速系统的仿真模型 (19)3.4.2参数设置 (19)3.4.3仿真结果及分析 (19)参考文献 (23)致谢 (24)1绪论1.1直流调速系统概述从生产机械要求控制的物理量来看,电力拖动自动控制系统有调速系统、位置随动系统、张力控制系统等多种类型,而各种系统往往都是通过控制转速来实现的,因此调速系统是最基本的拖动控制系统。
(完整word版)实验四转速、电流反馈控制直流调速系统的仿真(word文档良心出品)
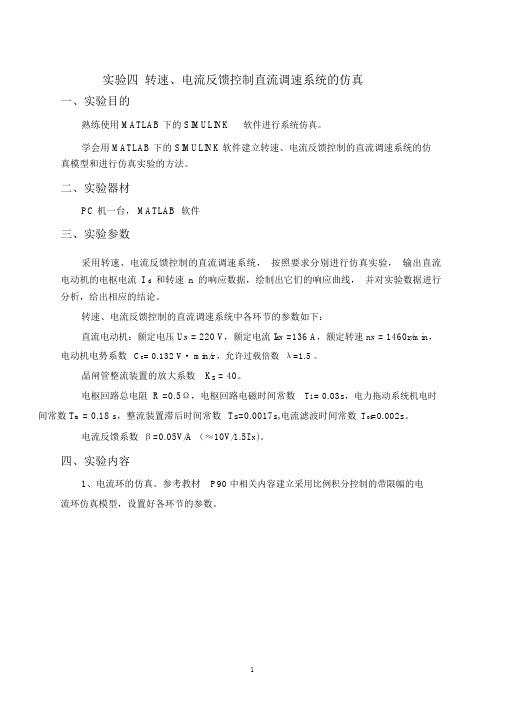
实验四转速、电流反馈控制直流调速系统的仿真一、实验目的熟练使用 MATLAB 下的 SIMULINK软件进行系统仿真。
学会用 MATLAB 下的 SIMULINK 软件建立转速、电流反馈控制的直流调速系统的仿真模型和进行仿真实验的方法。
二、实验器材PC 机一台, MATLAB 软件三、实验参数采用转速、电流反馈控制的直流调速系统,按照要求分别进行仿真实验,输出直流电动机的电枢电流I d和转速n 的响应数据,绘制出它们的响应曲线,并对实验数据进行分析,给出相应的结论。
转速、电流反馈控制的直流调速系统中各环节的参数如下:直流电动机:额定电压 U N = 220 V,额定电流 I dN =136 A,额定转速 n N = 1460r/min,电动机电势系数C e= 0.132 V· min/r ,允许过载倍数λ=1.5 。
晶闸管整流装置的放大系数K s = 40。
电枢回路总电阻 R =0.5Ω,电枢回路电磁时间常数T l = 0.03s,电力拖动系统机电时间常数 T m = 0.18 s,整流装置滞后时间常数Ts=0.0017s,电流滤波时间常数T oi=0.002s。
电流反馈系数β=0.05V/A (≈10V/1.5I N)。
四、实验内容1、电流环的仿真。
参考教材P90 中相关内容建立采用比例积分控制的带限幅的电流环仿真模型,设置好各环节的参数。
140 2 0.5-K-0.002s+1 0.0017s+1 0.03s+1 0.18sStep Transfer Fcn Gain Saturation Transfer Fcn1 Transfer Fcn2 Transfer Fcn31-K-sGain1 Integrator0.050.002s+1Transfer Fcn4 Scope图 1 电流环的仿真模型2、按照表 1 中的数据分别改变电流环中比例积分控制器的比例系数K p和积分系数K i,观察电流环输出电枢电流I d的响应曲线,记录电枢电流I d的超调量、响应时间、稳态值等参数,是否存在静差?分析原因。
带电流截止负反馈的转速单闭环直流调速系统设计与仿真运动控制实验报告

带电流截止负反馈的转速单闭环直流调速系统设计与仿真 一、设计要求系统稳定并无静差 二、给定参数17,220,3000/min N N N P kw U V n r ===,I N =87.3A ,电枢回路电阻0.087a R =Ω,电感0.0032a L H =,励磁回路电阻181.5Ω,电动机的转动惯量20.76.J Kg m =三、闭环直流调速系统稳态参数的计算 1)额定负载时的稳态速降应为:m i n/12.6min /)02.01(1002.03000)1(r r s D s n n N cl =-⨯⨯≤-=∆2)闭环系统应有的开环放大系数:计算电动机的电动势系数: r V r V n R I U C N a N N e min/071.0min/3000087.03.87220⋅=⋅⨯-=-=闭环系统额定速降为:min /97.106min /071.0087.03.87r r C R I n e N op =⨯==∆闭环系统的开环放大系数为:5.16112.697.1061=-≥-∆∆=clop n n K003.0/max max n ==n U α3)计算运算放大器的放大系数和参数 运算放大器放大系数K p 为:5.16/e p ≥=s K KC K α电枢回路的总电感为0.0032H电磁时间常数为037.0/l ==R L T 27/1l ==τK4)电流截止负反馈 四加电网扰动(第8s电压220→240)负载扰动给定值扰动五、将PI调节器参数改变1.电网扰动(第8s电压220→240)2.负载扰动3.给定值扰动转速、电流双闭环直流调速系统设计与仿真一、设计要求系统稳定并无静差 二、给定参数17,220,3000/min N N N P kw U V n r ===,I N =87.3A ,电枢回路电阻0.087a R =Ω,电感0.0032a L H =,励磁回路电阻181.5Ω,电动机的转动惯量20.76.J Kg m =三、电流调节器ACR 参数计算允许电流过载倍数λ=2;设调节器输入输出电压im nm **U U ==10V ,电力电子开关频率为f=l kHz .首先计算电流反馈系数β和转速反馈系数α:06.0 I n im *==ββλU N U n nm *α= α=0.003s T 001.0s = ,电流环小时间常数为s T T T oi 002.0s i =+=∑电流调节器超前时间常数为s T K l i 015.0/1i ===τ 而对电流环开环增益局l K =250/5.0=∑i T ,于是ACR 的比例系数为:94.4/i l i ==s K R K K βτ 四、转速调节器ASR 参数计算 选中频段宽度h=5。
带电流截止负反馈地转速直流调速matlab仿真
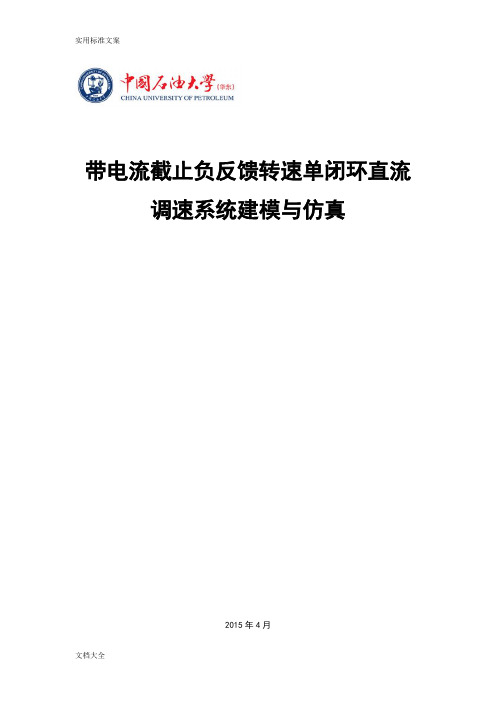
带电流截止负反馈转速单闭环直流调速系统建模与仿真2015年4月目录一、设计参数 (1)二、设计背景 (1)2.1问题的提出 (1)2.2解决办法 (1)三、带电流截止负反馈闭环直流调速系统 (2)3.1总原理图 (2)3.2电流截止反馈环节 (2)3.3带电流截止负反馈闭环直流调速系统结构框图和静特性 (3)四、参数设计 (5)4.1基本参数的计算 (5)4.2判别系统稳定性 (6)4.3PI调节器的设计 (7)4.4取样电阻的选择 (10)五、Matlab建模与仿真 (10)5.1带P I调节器的闭环直流调速系统 (10)5.2加入电流截止负反馈 (11)六、波形分析及结论 (16)6.1没有电流截止负反馈 (16)6.2加上电流截止负反馈 (16)6.3结论 (16)一、设计参数电动机:额定数据为3kW P N =,220V U N =,17.5A I N =,1500r/min n N =,电枢电阻Ω=1.2R a ,22m 3.53N GD ⋅=;晶闸管触发整流装置:三相桥式可控整流电路,整流变压器Y/Y 联结,二次线电压230V U 2l =,二次线电压电压放大系数44K s =;V-M 系统电枢回路总电阻2.8Ω;要求:生产机械要求调速范围10D =,静差率2%S ≤,21A I 2.1N ==dcr I ,A I I N dbl 3177.1==,10V U *n =二、设计背景2.1问题的提出众所周知,直流电动机全电压起动时,如果没有限流措施,会产生很大的冲击电流,这不仅对电机换向不利,对过载能力低的电力电子器件来说,更是不能允许的。
采用转速负反馈的闭环调速系统突然加上给定电压时,由于惯性,转速不可能立即建立起来,反馈电压仍为零,相当于偏差电压,差不多是其稳态工作值的 1+K 倍。
这时,由于放大器和变换器的惯性都很小,电枢电压一下子就达到它的最高值,对电动机来说,相当于全压起动,当然是不允许的。
带电流截止负反馈环节的单闭环直流调速系统设计

带电流截⽌负反馈环节的单闭环直流调速系统设计带电流截⽌负反馈环节的单闭环直流调速系统设计1设计⽬的(1)了解带电流截⽌负反馈的转速单闭环直流调速系统的⼯作原理,熟悉组成环节及每个环节的作⽤。
(2)应⽤所学的交、直流调速系统的基本知识与⼯程设计⽅法,结合⽣产实际,确定系统的性能指标与实现⽅案,进⾏运动控制系统的初步设计。
(3)应⽤计算机仿真技术,通过在MATLAB软件上建⽴运动控制系统的数学模型,对控制系统进⾏性能仿真研究,掌握系统参数对系统性能的影响。
2设计参数采⽤晶闸管三相桥式全控整流电路供电,基本数据如下:直流电动机UN=220V, IN=65A,nN =1000r/min,电枢电阻Ra=0.15Ω,电枢电感La=0.0002H,励磁电压Uf=220V,励磁电流If=1.5A,电枢绕组和励磁绕组互感Laf=0.82H,供电电源电压U2=130V;晶闸管装置Ts=0.00167s,放⼤系数Ks=40;电枢回路总电阻R=0.5Ω;电枢回路总电感L=15mH;电动机轴上的总飞轮惯量GD2=12.5N·m2;转速调节器最⼤给定值*nmU=10V;3 设计任务(1)分析电流截⽌负反馈环节的⼯作原理,画出系统稳态结构图;(2)在MATLAB中建⽴带电流截⽌负反馈环节的单闭环直流调速系统;(3调节控制器参数,确定最佳调节参数。
将Simulink仿真模型,以及启动过程中的电流、转速波形图附在设计说明书中。
⽐较带电流截⽌负反馈环节和不带电流截⽌负反馈环节启动过程的差异。
4设计要求1.稳态指标:转速⽆静差;2.动态指标:启动电流的最⼤值150 A。
空载启动到额定转速的转速超调量σn≤15%。
4 设计基本内容4.1问题的提出在转速反馈控制直流调速系统中存在⼀个问题,在启动、制动过程和堵转状态时,电枢电流会过⼤。
为了解决反馈闭环调速系统的起动和堵转时电流过⼤的问题,系统中必须有⾃动限制电枢电流的环节。
引⼊电流负反馈,可以使它不超过允许值。
直流调速控制系统的分析及仿真
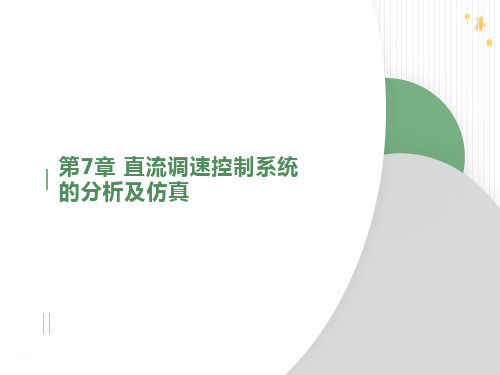
当电流负反馈环节起主导作用时的自动调节过程如图7-1-8所示。
7.1.4系统的性能分析
代入图7-1-5中,由图可见,它是一个二阶系统,已知 二阶系统总是稳定的。但若考虑到晶闸管有延迟,晶 闸管整流装置的传递函数便为
相反。
5.电流截止负反馈环节
当 时,(亦即 ),则二极管VD截止,电流截止负反馈不起作用。当 时,(亦即 ),则二极管VD导通, [此处略去二极管的死区电压],电流截止负反馈环节起作用,它将使整流输出电压 下降,使整流电流下降到允许最大电流。 的数值称为截止电流,以 表示。调节电位器RP3即可整定 ,亦即整定 的数值。一般取 〔 为额定电流〕。 由于电流截止负反馈环节在正常工作状况下不起作用,所以系统框图上可以省去。
在图7-1-1中,主电路中串联了一个阻值很小的取样电阻
(零点几欧)。电阻
上的电压
与
成正比。比 较阈值电压
是由一个辅助电源经电位器RP3提供的。电 流反馈信号(
图7-1-7调速系统的“挖土机”机械特性
当电流负反馈环节起主导作用时的自动调节过程如图7-1-8所示。 机械特性很陡下垂还意味着,堵转时(或起动时)电流不是很大。 这是因为在堵转时,虽然转速n=0,反电动势E=0,但由于电流 截止负反馈的作用,使
大大下降,从而
不致过大。此时 电流称为堵转电流
⑥ 晶闸管整流电路的调节特性为输出的 平均电压
与触发电路的控制电压
之间的关系,即
图7-1-4为晶闸管整流装置的调节特性。
由图可见,它既有死区,又会饱和。 (当全导通以后,
再增加, 也不会再 上升了),且低压段还有弯曲段。面对 这非线性特性,常用的办法是讲它“看 作”一条直线,即处理成
为
单闭环直流调速系统的设计与仿真实验报告4.doc
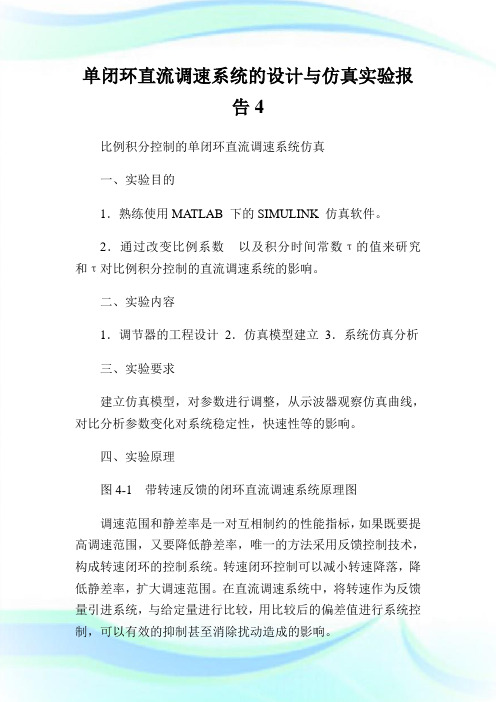
单闭环直流调速系统的设计与仿真实验报告4比例积分控制的单闭环直流调速系统仿真一、实验目的1.熟练使用MATLAB 下的SIMULINK 仿真软件。
2.通过改变比例系数以及积分时间常数τ的值来研究和τ对比例积分控制的直流调速系统的影响。
二、实验内容1.调节器的工程设计2.仿真模型建立3.系统仿真分析三、实验要求建立仿真模型,对参数进行调整,从示波器观察仿真曲线,对比分析参数变化对系统稳定性,快速性等的影响。
四、实验原理图4-1 带转速反馈的闭环直流调速系统原理图调速范围和静差率是一对互相制约的性能指标,如果既要提高调速范围,又要降低静差率,唯一的方法采用反馈控制技术,构成转速闭环的控制系统。
转速闭环控制可以减小转速降落,降低静差率,扩大调速范围。
在直流调速系统中,将转速作为反馈量引进系统,与给定量进行比较,用比较后的偏差值进行系统控制,可以有效的抑制甚至消除扰动造成的影响。
当t=0时突加输入时,由于比例部分的作用,输出量立即响应,突跳到,实现了快速响应;随后按积分规律增长,。
在时,输入突降为0,=0,= ,使电力电子变换器的稳态输出电压足以克服负载电流压降,实现稳态转速无静差。
五、实验各环节的参数及和1/τ的参数的确定5.1各环节的参数:直流电动机:额定电压=220V,额定电流=55A,额定转速=1000r/min,电动机电动势系数=0.192V •min/r。
假定晶闸管整流装置输出电流可逆,装置的放大系数=44,滞后时间常数=0.00167s。
电枢回路总电阻R=1.0Ω,电枢回路电磁时间常数=0.00167s 电力拖动系统机电时间常数=0.075s。
转速反馈系数=0.01V •min/r。
对应额定转速时的给定电压=10V。
稳态性能指标D=20,s 5% 。
5.2 和1/τ的参数的确定:PI调节器的传递函数为其中,。
(1)确定时间常数1)整流装置滞后时间常数;2)转速滤波时间常数;3)转速环小时间常数;(2)计算参数按跟随和抗扰性都较好的原则,取h=5,则调节器超前时间常数,即积分时间常数:,则由此可得开环增益:于是放大器比例放大系数:六、仿真模型的建立如图6-1为比例积分控制的无静差直流调速系统的仿真框图,根据仿真框图,利用MATLAB下的SMULINK软件进行系统仿真,建立的仿真模型如图6-2所示。
带电流截止负反馈的转速直流调速matlab仿真
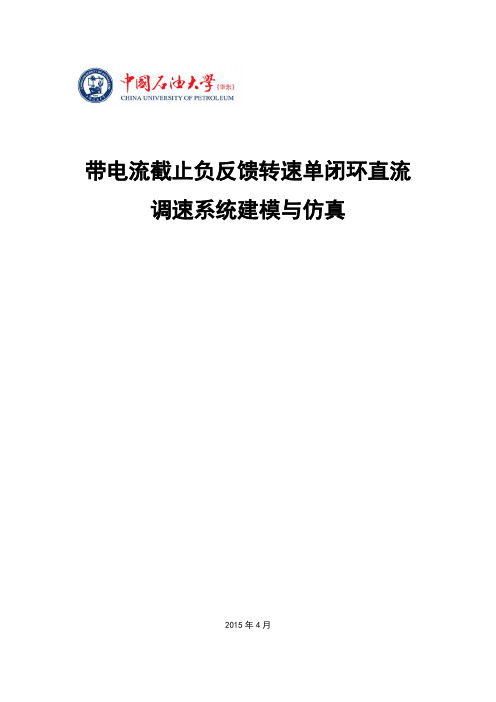
带电流截止负反馈转速单闭环直流调速系统建模与仿真2015年4月目录一、设计参数 (1)二、设计背景 (1)2.1问题的提出 (1)2.2解决办法 (1)三、带电流截止负反馈闭环直流调速系统 (2)3.1总原理图 (2)3.2电流截止反馈环节 (2)3.3带电流截止负反馈闭环直流调速系统结构框图和静特性 (3)四、参数设计 (5)4.1基本参数的计算 (5)4.2判别系统稳定性 (6)4.3PI调节器的设计 (7)4.4取样电阻的选择 (10)五、Matlab建模与仿真 (10)5.1带P I调节器的闭环直流调速系统 (10)5.2加入电流截止负反馈 (11)六、波形分析及结论 (16)6.1没有电流截止负反馈 (16)6.2加上电流截止负反馈 (16)6.3结论 (16)一、设计参数电动机:额定数据为3kW P N =,220V U N =,17.5A I N =,1500r/min n N =,电枢电阻Ω=1.2R a ,22m 3.53N GD ⋅=;晶闸管触发整流装置:三相桥式可控整流电路,整流变压器Y/Y 联结,二次线电压230V U 2l =,二次线电压电压放大系数44K s =;V-M 系统电枢回路总电阻2.8Ω;要求:生产机械要求调速范围10D =,静差率2%S ≤,21A I 2.1N ==dcr I ,A I I N dbl 3177.1==,10V U *n =二、设计背景2.1问题的提出众所周知,直流电动机全电压起动时,如果没有限流措施,会产生很大的冲击电流,这不仅对电机换向不利,对过载能力低的电力电子器件来说,更是不能允许的。
采用转速负反馈的闭环调速系统突然加上给定电压时,由于惯性,转速不可能立即建立起来,反馈电压仍为零,相当于偏差电压,差不多是其稳态工作值的 1+K 倍。
这时,由于放大器和变换器的惯性都很小,电枢电压一下子就达到它的最高值,对电动机来说,相当于全压起动,当然是不允许的。
转速反馈控制直流调速系统仿真

转速反馈控制直流调速系统的仿真一、不带电流负反馈的转速反馈控制直流调速系统仿真根据课本的操作步骤可得到如下的仿真框图:根据课本的操作步骤可得到如下的仿真框图:图1.仿真框图运行仿真模型结果如下:运行仿真模型结果如下:图2.电枢电流随时间变化的规律由图可知电流的最大值为230A左右,显然不满足实际要求,故后面需对此进行处理,采用带电流截止负反馈环节的直流调速系统。
采用带电流截止负反馈环节的直流调速系统。
图3. 电机转速随时间变化的规律二、带电流负反馈的转速反馈控制直流调速系统仿真采用以下结构实现电流截止负反馈环节中的二极管功能:当输入小于0时,输出为0;当输入大于0时,输出等于输入。
时,输出等于输入。
图4. 原理图根据电机的额定参数:A 55IN =。
取。
取.57155*.31.3I1INdcr === 9955*.81I*.81IN 1db ===又根据又根据s com*N 1db R U U I +»s dcr com R *I U =同时V 10U *N =,可解得:364.0R s =,26U com =仿真框图如下所示:仿真框图如下所示:图5.仿真框图运行仿真模型结果如下:运行仿真模型结果如下:图6.电枢电流随时间变化的规律图7.电机转速随时间变化的规律。
三、结论将不带电流负反馈的模型与带电流负反馈的模型进行比较,我们看到,前后两个scope1中的曲线的最大值相差很大。
第一个scope1中最大值达到了250左右,而第二个只有100左右。
而前后两个scope 中,曲线都在1000左右稳定,而第一个scope 是在0.1秒左右就开始进入稳态,而第二个是在0.2秒左右才开始进入稳态。
秒左右才开始进入稳态。
可知,引入电流负反馈,可以解决转速反馈闭环调速系统起动时电流过大的问题,可以解决转速反馈闭环调速系统起动时电流过大的问题,而且而且这种作用只在起动时存在,这种作用只在起动时存在,在正常的稳速运行时又取消了,在正常的稳速运行时又取消了,在正常的稳速运行时又取消了,电流随着负荷的增减而变化,电流随着负荷的增减而变化,电流随着负荷的增减而变化,只只有当电流大到一定程度时才开始起作用。
带电流截止负反馈的转速闭环的数字式直流调速系统的仿真与设计

带电流截止负反馈的转速闭环的数字式直流调速系统的仿真与设计一、设计目的应用所学的交、直流调速系统的基本知识与工程设计方法,结合生产实际,确定系统的性能指标与实现方案,进行运动控制系统的初步设计。
应用计算机仿真技术,通过在MATLAB软件上建立运动控制系统的数学模型,对控制系统进行性能仿真研究,掌握系统参数对系统性能的影响。
在原理设计与仿真研究的基础上,应用PROTEL进行控制系统的印制板的设计,为毕业设计的综合运用奠定坚实的基础。
二、设计参数1、直流电动机各参数如下:输出功率为:7.5Kw,电枢额定电压220V电枢额定电流 36A,额定励磁电流2A额定励磁电压110V,功率因数0.85电枢电阻0.2欧姆,电枢回路电感100mH电机机电时间常数2S,电枢允许过载系数1.5额定转速1430rpm2、环境条件:电网额定电压:380/220V,电网电压波动:10%环境温度:-40~+40摄氏度,环境湿度:10~90%3、控制系统性能指标:电流超调量小于等于5%空载起动到额定转速时的转速超调量小于等于30%调速范围D=20,静差率小于等于0.03.三、反馈控制闭环直流调速系统的工作原理1、限流保护—电流截止负反馈为了解决反馈闭环调速系统的起动和堵转时电流过大问题,系统中必须有自动限制电枢电流的环节。
根据反馈控制原理,要维持哪一个物理量基本不变,就应该引入那个物理量的负反馈。
那么引入电流负反馈,应该能够保持电流基本不变,使它不超过允许值。
但是这种作用只应在起动和堵转时存在,在正常运行时又得取消,让电流自由地随着负载增减,这样的当电流大到一定程度时才出现的电流负反馈叫做电流截止负反馈,简称截流反馈。
为了实现截流反馈,须在系统中引入电流截止负反馈环节。
如图1所示,电流反馈信号取自串人电动机电枢回路的小阻值电阻R S,IdR S 正比于电流。
设Idcr为临界的截止电流,当电流大于Idcr时将电流负反馈信号加到放大器的输入端,当电流小于Idcr时将电流反馈切断。
带电流截止负反馈的转速单闭环直流调速系统设计

一、 绪论 科学技术的发展日新月异,科技产品涵盖着我们生活的方方面面。
电动机作为一种便利的带动工具,是我们生活和工业生产中重要的不可缺少的一部分,人类的生产生活已经离不开它。
对于我们来说,如何高效精确地控制电机的运转,并且最低的成本去实现,才是我们最值得深入研究的课题。
直流电动机具有良好的起、制动性能,方便控制,易于实现,宜于在大范围内平滑调速,并且直流调速系统在理论和实践上都比较成熟,是研究其它调速系统的基础。
在直流电动机中,带电流截止负反馈直流调速系统应用也较为广泛,其广泛应用于轧钢机、冶金、印刷、金属切割机床等很多领域的自动控制中,虽然,在调速的高效性方面存在着局限性,但综合各方面来看,它任然有它独特的运用前景。
1.1设计的目的和意义(1)应用所学的直流调速系统的基本知识与工程设计方法,结合生产实际,确定系统的性能指标与实现方案,进行运动系统的初步设计。
(2)学会应用MATLAB 软件,建立数学模型对控制系统进行仿真研究,掌握系统参数对系统性能的影响;(3)在理论设计与仿真研究的基础上,应用Protel 进行控制系统的设计,为毕业设计打下基础。
1.2设计要求本课程设计的对象是: 直流电机:2.2kW ,220V ,12.5A ,1500 转/分。
电枢电阻1.2Ω ,整流装置内阻1.5Ω,触发整流环节的放大倍数为35,堵转电流 N dbl I I 2≤,临界截止电流N dcr I I 2.1≥。
要求设计一个带直流截止负反馈的转速 单闭环调速系统。
其主要内容为:(1)测定综合实验中所用控制对象的参数(由实验完成);(2)根据给定指标设计带电流截止负反馈的转速调节器,并选择调节器参数和具体实现电路。
(3)按设计结果组成系统,以满足给定指标。
(4)研究参数变化对系统性能的影响。
(5)在时间允许的情况下进行调试。
1.3设计对象及有关数据(1)完成理论分析:a.调速范围D=20,静差率S≤10%;b.转速超调σn≤10%(在额定转速时);c.动态速降小于10%。
带电流截止负反馈的转速单闭环直流调速系统的设计和仿真

带电流截止负反馈的转速单闭环直流调速系统的设计和仿真1.设计原理带电流截止负反馈的转速单闭环直流调速系统由速度反馈环和电流反馈环组成。
其基本原理是,通过测量电机驱动器的输出转速,并与给定的转速进行比较,从而产生误差信号。
误差信号经过比例、积分和微分三个环节进行处理后,作为电机驱动器的控制量,用于调节电机的输入电压。
具体的设计步骤如下:(1)确定电机的调速要求和性能指标,包括稳态误差、调速范围、动态响应时间等。
(2)根据电机的参数和特性曲线,确定理想的速度控制系统传递函数。
(3)选择合适的调节器类型和参数,并确定反馈信号的获取方式。
(4)设计速度环和电流环的控制回路,包括比例、积分和微分环节的参数设置。
(5)进行系统稳态和动态性能的仿真和分析。
2.仿真过程在进行仿真前,需要先确定电机的参数和特性曲线,并建立相应的数学模型。
然后,在Simulink等软件中搭建整个调速系统的模型。
具体步骤如下:(1)根据电机的特性曲线确定电机的传递函数模型,例如:Gs=1/(Js+B)其中,Gs为电机的机械转速传递函数,J为转动惯量,B为阻尼系数。
(2)设计速度环的控制回路,包括比例环节、积分环节和微分环节。
通常采用PID控制器,其传递函数为:Gc=Kp+Ki/s+Kd*s其中,Kp、Ki和Kd分别为比例、积分和微分环节的增益。
(3)设计电流环的控制回路,采用电流截止负反馈的方式。
电流环的控制器传递函数为:Gc=Kc*(1+s*Rf)其中,Kc为增益,Rf为电流截止反馈的滤波器。
(4)将速度环和电流环相连接,构成整个闭环控制系统。
(5)进行系统的仿真,观察系统的稳态和动态响应,并根据需要进行参数调整和优化。
3.仿真结果和分析根据以上步骤进行仿真后,可以得到系统的稳态和动态响应曲线。
通过观察和分析这些曲线,可以评估系统的性能和效果。
首先,可以通过误差曲线来评估系统的稳态性能,即在给定转速下是否存在稳态误差。
如果误差较大,需要调整PID控制器的参数来改善系统的稳定性。
- 1、下载文档前请自行甄别文档内容的完整性,平台不提供额外的编辑、内容补充、找答案等附加服务。
- 2、"仅部分预览"的文档,不可在线预览部分如存在完整性等问题,可反馈申请退款(可完整预览的文档不适用该条件!)。
- 3、如文档侵犯您的权益,请联系客服反馈,我们会尽快为您处理(人工客服工作时间:9:00-18:30)。
课程设计任务书学生:丁志辉专业班级:电气1005班指导教师:饶浩彬工作单位:自动化学院题目: 带电流截止负反馈转速单闭环直流调速系统建模与仿真初始条件:1.技术数据直流电动机:P N=3KW , U N=220V , I N=17.5A , n N=1500r/min , R a=1.25Ω堵转电流I dbl=2I N,截止电流I dcr=1.5I N,GD2=3.53N.m2三相全控整流装置:K s=40 , R rec=1. 3Ω平波电抗器:R L=0. 3Ω电枢回路总电阻R=2.85Ω,总电感L=200mH ,2.技术指标稳态指标:无静差(静差率s≤2%, 调速围D≥10)动态指标:系统稳定要求完成的主要任务:1.技术要求:(1) 该调速系统能进行平滑的速度调节,负载电机不可逆运行,具有较宽的调速围(D≥10),系统在工作围能稳定工作(2) 根据指标要求进行动态校正,选择调节器的参数,并确定电流截止负反馈环节的相关参数,(3) 系统在5%负载以上变化的运行围电流连续2.设计容:(1) 根据题目的技术要求,分析论证并确定主电路的结构型式和闭环调速系统的组成,画出系统组成的原理框图(2) 根据带电流截止负反馈转速单闭环直流调速系统原理图, 分析转速调节器和电流截止负反馈的作用,(3) 通过对调节器参数设计, 得到转速和电流的仿真波形,并由仿真波形通过MATLAB 来进行调节器的参数调节。
(4) 绘制带电流截止负反馈转速单闭环直流调速系统的电气原理总图(要求计算机绘图)(5) 整理设计数据资料,课程设计总结,撰写设计计算说明书时间安排:课程设计时间为一周半,共分为三个阶段:(1)复习有关知识,查阅有关资料,确定设计方案。
约占总时间的20% (2)根据技术指标及技术要求,完成设计计算。
约占总时间的40% (3)完成设计和文档整理。
约占总时间的40%指导教师签名:年月日系主任(或责任教师)签名:年月日目录摘要 (4)1.闭环调速控制系统构成 (5)1.1 主电路 (5)1.2 原理框图 (6)2带电流截止负反馈的转速负反馈的分析 (7)2.1电流截止负反馈的提出 (7)2.2 电流截止负反馈环节 (7)2.3 带电流截止负反馈调速系统结构框图和静特性 (8)3 参数设计 (10)3.1整体分析 (10)3.2稳定性参数计算和判断 (11)3.3 转速调节器校正 (12)3.3.1 PI调节器结构 (12)3.3.2 调节器的选择 (13)3.4 电流截止负反馈参数设计 (17)4. 电流MATLAB仿真 (17)4.1 将设计的参数进行仿真 (17)4.2 调节器参数调整 (19)5.电气总图 (19)6.结束语 (20)参考文献 (21)摘要为了提高直流调速系统的动态、静态性能,通常采用闭环控制系统(主要包括单闭环、双闭环)。
而在对调速指标要求不高的场合,采用单闭环即可。
闭环系统较之开环系统能自动侦测把输出信号的一部分拉回到输入端,与输入信号相比较,其差值作为实际的输入信号;能自动调节输入量,能提高系统稳定性。
在对调速系统性能有较高要求的领域常利用直流电动机,但直流电动机开环系统稳定性不能够满足要求,可利用转速单闭环提高稳态精度,而采用比例调节器的负反馈调速系统仍是有静差的,为了消除系统静差,可采用积分调节器代替比例调节器。
关键词:直流调速单闭环稳态精度比例调节带电流截止负反馈转速单闭环直流调速系统建模与仿真1.闭环调速控制系统构成1.1 主电路本控制系统采用含电流截止负反馈的转速负反馈主电路结构,其原理图如图1所示。
+--+图1 含电流截止负反馈的转速负反馈原理图图中的电动机的电枢回路由晶闸管组成的三相桥式整流电路供电,通过与电动机同轴刚性连接的测速发电机TG 检测电动机的转速,并经转速反馈环节分压后取出合适的转速反馈信号n U ,此电压与转速给定信号*n U 经速度调节器ASR 综合调节,ASR 的输出作为移相触发器的控制电压c U ,由此组成转速负反馈单闭环直流调速系统。
改变*n U 即可调节电动机的转速。
在本系统中ASR 采用比例积分调节器,属于无静差调速系统。
为了防止在起动和运行过程中出现过大的电流冲击,系统引入了电流截止负反馈以限止电流不超过其允许的最大值。
1.2 原理框图将开环系统改为单闭环转速负反馈调速系统,并采用PI调节器,就既保证动态性能,又能作到转速的无静差,较好的解决开环系统的不足,此闭环系统的工作原理是:将直流电动机转速变化信号反馈到触发环节,来自动增大或减小触发角α来自动调节整流输出电压Uds,即可达到稳定,其系统结构框图与系统原理图如图2所示图2 单闭环转速负反馈系统框图转速单闭环实验是将反映转速变化的电压信号作为反馈信号,经“速度变换”后接,到“速度调节器”的输入端,与“给定”的电压相比较经放大后,得到移相控制电压UCt 用作控制整流桥的“触发电路”,触发脉冲经功放后加到晶闸管的门极和阴极之间,以改变“三相全控整流”的输出电压,这就构成了速度负反馈闭环系统。
电机的转速随给定电压变化,电机最高转速由速度调节器的输出限幅所决定,速度调节器采用P(比例)调节对阶跃输入有稳态误差,要想消除上述误差,则需将调节器换成PI(比例积分)调节。
这时当“给定”恒定时,闭环系统对速度变化起到了抑制作用,当电机负载或电源电压波动时,电机的转速能稳定在一定的围变化。
2带电流截止负反馈的转速负反馈的分析2.1电流截止负反馈的提出(1)起动的冲击电流---直流电动机全电压起动时,如果没有限流措施,会产生很大的冲击电流,这不仅对电机换向不利,对过载能力低的电力电子器件来说,更是不能允许的。
(2)闭环调速系统突加给定起动的冲击电流---采用转速负反馈的闭环调速系统突然加上给定电压时,由于惯性,转速不可能立即建立起来,反馈电压仍为零,相当于偏差电压,差不多是其稳态工作值的 1+K 倍。
这时,由于放大器和变换器的惯性都很小,电枢电压一下子就达到它的最高值,对电动机来说,相当于全压起动,当然是不允许的。
(3)堵转电流---有些生产机械的电动机可能会遇到堵转的情况。
例如,由于故障,机械轴被卡住,或挖土机运行时碰到坚硬的石块等等。
由于闭环系统的静特性很硬,若无限流环节,硬干下去,电流将远远超过允许值。
如果只依靠过流继电器或熔断器保护,一过载就跳闸,也会给正常工作带来不便。
为了解决反馈闭环调速系统的起动和堵转时电流过大的问题,系统中必须有自动限制电枢电流的环节。
根据反馈控制原理,要维持哪一个物理量基本不变,就应该引入那个物理量的负反馈。
那么,引入电流负反馈,应该能够保持电流基本不变,使它不超过允许值。
2.2 电流截止负反馈环节通过对电流负反馈和转速负反馈的分析。
考虑到,限流作用只需在起动和堵转时起作用,正常运行时应让电流自由地随着负载增减,采用电流截止负反馈的方法,则当电流大到一定程度时才接入电流负反馈以限制电流,而电流正常时仅有转速负反馈起作用控制转速。
电流截止负反馈环节如图3和图4所示.图3 利用独立直流电源作比较电压图4 利用稳压管产生比较电压图5 封锁运算放大器的电流截止负反馈环节图6 电流截止负反馈环节的I/O特性电流截止负反馈环节输入输出特性如图6所示。
图3中用独立的直流电源作为比较电压,其大小可用电位器调节,相当于调节截止电作比较电压,线路要简单得多,但不能平滑的流。
图4中利用稳压管VS的击穿电压Ubr调节截止电流值。
图5是反馈环节与运放的连接电路。
2.3 带电流截止负反馈调速系统结构框图和静特性带电流截止负反馈的闭环直流调速系统结构框图如图7所示:图7 带电流截止负反馈的闭环直流调速稳态系统结构框图系统两段静特性的方程式:当d dcr I I ≤时,电流负反馈被截止,静特性与转速负反馈相同当d dcr I I >时,引入电流负反馈,静特性变为:静特性的几个特点:(1)电流负反馈的作用相当于在主电路中串入一个大电阻 KpKsRs ,因而稳态速降极 大,使特性急剧下垂。
(2)比较电压 Ucom 与给定电压 Un* 的作用一致, 好象把理想空载转速提高到(3)两段式静特性常称作下垂特性或挖土机特性。
当挖土机遇到坚硬的石块而过载时,电动机停下,电流也不过是堵转电流,在式(1)中,令 n = 0,得一般p s s K K R R >>,因此 (4)最大截止电流dbl I 应小于电机允许的最大电流,一般取 :I dbl =(1.5~2.0) I N)1()()1()(e d s s p e com *n s p K C I R K K R K C U U K K n ++-++=)1()1(e de *n s p K C RI K C U K K n +-+=)1()('e com *n s p 0K C U U K K n ++=s s p com *ns p dbl )(R K K R U U K K I ++=scom *n dblR U U I +≈从调速系统的稳态性能上看,希望稳态运行围足够大,截止电流大于电机的额定电流,一般取:Idcr ≥(1.1~1.2)IN(5)调速系统的起动过程如图8图9所示图8带电流截止负反馈单闭环调速系统图9理想的快速启动过程3 参数设计3.1整体分析本题目要求设计带电流截止负反馈转速单闭环直流调速系统,为满足以上技术要求和性能指标的要求,选择以下方案设计系统:1) 系统要求平滑调速,可采用调压调速方式。
因为调压调速系统是在保持他励直流电动机的磁通为额定值的情况下,将电枢两端的电压(电源电压)降低为不同的值时,可以获得与电动机固有机械特性相互平行的人为机械特性,调速方向是基速以下,属于恒转矩调速方法。
只要输出的电压是连续可调的,即可实现电动机的无级调速,调速围可以达到很宽。
2) 系统静特性良好,无静差。
在参数设置合理的情况下,带电流截止负反馈转速单闭环直流调速系统本身可以做到系统的稳定运行。
3) 本设计中的电力电子变换装置采用三相桥式控制的晶闸管整流装置,应用题目要求中给定的参数进行设计,其R rec =0.5Ω,K s =40。
4) 在带电流截止负反馈环中,截止电流的上限选择需要根据电机的品牌和参数论证,以保证电机不至于因电流过大而烧毁。
3.2稳定性参数计算和判断为了满足D=10,s≤2%,额定负载时调速系统的稳态速降为:22017.5 1.250.132min/1500N N a e N U I R C V r n --⨯===⋅ ()17.5(1.25 1.3)338/min 0.132N a rec op e I R R n r C +⨯+∆===15000.02/min 3.06/min (1)10(10.02)N cl n s n r r D s ⨯∆=≤=-⨯-根据cl n ∆,求出系统的开环放大系数:33811109.463.06op cln K n ∆=-≥-=∆ 计算测速反馈环节的放大系数和参数:设在额定转速下稳态时的给定电压为*10nU V =,则须有*10n n U U V == 故转速反馈环节的放大系数100.006671500n N U n α=== 计算运算放大器的放大系数和参数:109.460.13254.160.0066740e p s KC K K α⨯=≥=⨯ 验证系统在此控制器下的稳定性: 电枢回路电磁时间常数0.20.072.85l L T sR ===电力拖动机电时间常数222.85 3.530.161303753750.132m e m GD R T sC C π⨯===⨯⨯三项桥式整流电路的失控时间常数 s T s 00167.0=为保证系统稳定,开环放大系数应满足sl s s l m T T T T T T K 2)(++<按动态性能指标,得98.73K <,而按稳态性能指标有109.46K ≥,说明比例控制闭环系统的动态稳定性和稳态性能要矛盾的,此系统不稳定。