混凝土地面施工步骤
常规混凝土地面施工工艺及方法
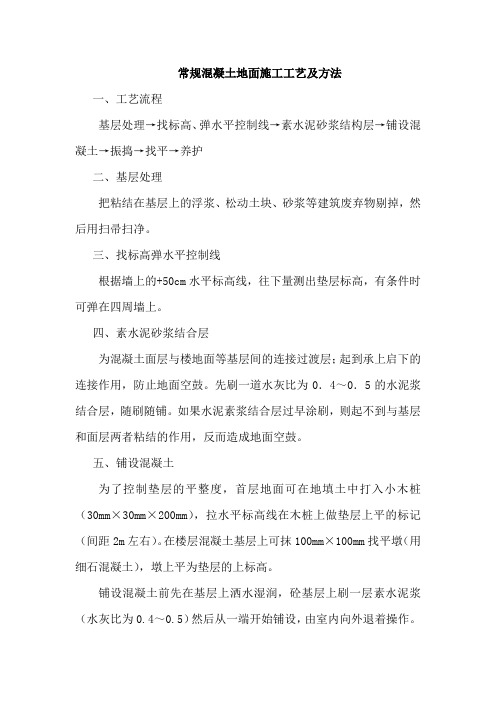
常规混凝土地面施工工艺及方法
一、工艺流程
基层处理→找标高、弹水平控制线→素水泥砂浆结构层→铺设混凝土→振捣→找平→养护
二、基层处理
把粘结在基层上的浮浆、松动土块、砂浆等建筑废弃物剔掉,然后用扫帚扫净。
三、找标高弹水平控制线
根据墙上的+50cm水平标高线,往下量测出垫层标高,有条件时可弹在四周墙上。
四、素水泥砂浆结合层
为混凝土面层与楼地面等基层间的连接过渡层;起到承上启下的连接作用,防止地面空鼓。
先刷一道水灰比为0.4~0.5的水泥浆结合层,随刷随铺。
如果水泥素浆结合层过早涂刷,则起不到与基层和面层两者粘结的作用,反而造成地面空鼓。
五、铺设混凝土
为了控制垫层的平整度,首层地面可在地填土中打入小木桩(30mm×30mm×200mm),拉水平标高线在木桩上做垫层上平的标记(间距2m左右)。
在楼层混凝土基层上可抹100mm×100mm找平墩(用细石混凝土),墩上平为垫层的上标高。
铺设混凝土前先在基层上洒水湿润,砼基层上刷一层素水泥浆(水灰比为0.4~0.5)然后从一端开始铺设,由室内向外退着操作。
六、振捣
用铁锹铺混凝土,厚度略高于找平堆,随即用平板振捣器振捣。
厚度超过20cm时,应采用插入式振捣器,其移动距离不大于作用半径的1.5倍,做到不漏振,确保混凝土密实。
七、找平
混凝土振捣密实后,以墙上水平标高线及找平堆为准检查平整度,高的铲掉,凹处补平。
用水平木刮杠刮平,表面再用木抹子搓平。
有坡度要求的地面,应按设计要求的坡度做。
八、养护
已浇筑完的混凝土垫层,应在12h左右覆盖,一般不得小于7d。
混凝土地坪施工的步骤和注意事项

混凝土地坪施工的步骤和注意事项混凝土地坪施工是一项重要的建筑工程,它在建筑物的基础和地面装修中起着重要的作用。
本文将介绍混凝土地坪施工的步骤和注意事项,以帮助读者更好地了解和理解这一过程。
一、施工步骤1. 准备工作混凝土地坪施工前的准备工作非常重要。
需要对施工现场进行清理和整理,确保地面平整、无杂质。
要进行辅助设备和材料的准备,包括混凝土搅拌机、平整工具、钢筋等。
根据地坪的设计要求,进行施工方案的制定和材料的选择。
2. 基础处理在施工之前,需要对地基进行处理。
清理地面上的杂物和污垢,确保地面干净。
根据设计要求,进行填土或压实处理,以增加地面的稳定性和承载能力。
在处理完基础后,要进行地面的拓高和坡度的调整,确保地面平整且符合设计要求。
3. 钢筋布置在混凝土地坪的施工中,钢筋的作用非常重要。
钢筋能够增加混凝土地坪的强度和韧性,提高其承载能力和抗裂性能。
在布置钢筋时,需要根据设计要求选择合适的规格和间距,并确保钢筋的质量和固定牢固。
4. 浇注混凝土混凝土地坪施工的关键步骤是浇注混凝土。
在浇注混凝土之前,需要将混凝土搅拌均匀并加入适量的水和外加剂,以确保混凝土的质量和流动性。
将混凝土倒入地坪区域,并使用平整工具进行整平和压实,确保混凝土的密实性和平整度。
5. 养护处理混凝土地坪浇筑完成后,需要进行养护处理以确保其强度和耐久性。
养护处理的时间一般为7至14天,期间需要进行适当的浇水和覆盖保护,防止混凝土过早干缩和开裂。
在养护期结束后,可对地坪进行必要的修补和打磨,以提高其表面的平整度和光滑度。
二、注意事项1. 材料选择在混凝土地坪施工中,材料的选择非常重要。
应选择符合国家标准的水泥、砂子、骨料等原材料,并确保其质量和稳定性。
适量使用外加剂以提高混凝土的工艺性能和耐久性。
对于某些特殊环境或要求,还应选择相应的特殊材料,如抗菌材料、耐酸碱材料等。
2. 施工环境混凝土地坪施工需要在适宜的环境条件下进行。
施工环境应保持干燥、无风,并避免极端气温的天气。
混凝土地面施工工艺流程详细

混凝土地面施工工艺流程详细
混凝土地面施工工艺流程分为以下几个步骤:
1. 地面准备:首先需要对施工区域进行清理,清除杂物和污垢。
然后进行地面勘测和标高确定,确定施工时的坡度和平整度要求。
最后根据需要进行地面的修补和加强处理。
2. 布置防水层:对于需要防水的场所,需要在地面上铺设防水层。
常见的防水材料有沥青和聚氯乙烯薄膜等。
3. 等高线施工:在地面的边界线上拔线,确定施工时的高程和坡度要求。
然后根据拔线的位置进行地面的打标,指导混凝土的浇筑和平整。
4. 做楔形槽:在地面的边缘位置进行楔形槽的打磨,用于控制和整理混凝土的边缘形状。
5. 混凝土搅拌和浇筑:按照设计要求,将水泥、砂浆、骨料和水等原材料按比例搅拌均匀。
然后将搅拌好的混凝土倒入施工区域,用振动器进行振捣,使混凝土内部排气,确保混凝土的密实度。
6. 平整和打磨:在混凝土浇筑完成后,使用平整机或批刀进行初步的平整处理,使混凝土表面平整。
然后使用打磨机对混凝土地面进行打磨,去除表面的不平整和毛刺,使其达到光滑的效果。
7. 硬化和防尘处理:使用混凝土固化剂对地面进行硬化处理,增加地面的耐磨性和抗压能力。
然后对地面进行防尘处理,使用防尘剂涂覆地面,防止灰尘的产生和扬尘。
8. 涂装和护理:根据需要,对地面进行涂装处理,如使用地坪漆、蜡等。
然后对地面进行护理保养,定期刷洗、打蜡等,维护地面的光滑和美观。
以上是混凝土地面施工的详细工艺流程,具体的施工步骤还需按照实际情况和设计要求进行调整。
(完整版)混凝土地面施工方案
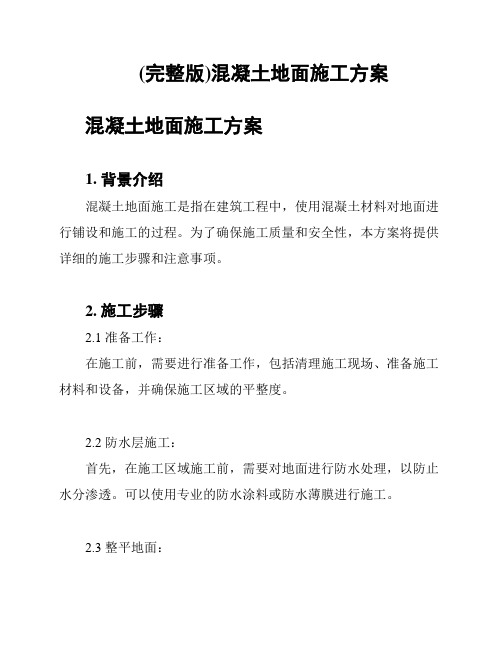
(完整版)混凝土地面施工方案混凝土地面施工方案1. 背景介绍混凝土地面施工是指在建筑工程中,使用混凝土材料对地面进行铺设和施工的过程。
为了确保施工质量和安全性,本方案将提供详细的施工步骤和注意事项。
2. 施工步骤2.1 准备工作:在施工前,需要进行准备工作,包括清理施工现场、准备施工材料和设备,并确保施工区域的平整度。
2.2 防水层施工:首先,在施工区域施工前,需要对地面进行防水处理,以防止水分渗透。
可以使用专业的防水涂料或防水薄膜进行施工。
2.3 整平地面:接下来,需要对地面进行整平,以确保地面的平整度和垂直度。
可以使用水平仪和刮刀等工具进行调整。
2.4 混凝土浇筑:在地面整平后,可以开始进行混凝土的浇筑。
根据设计要求和工程规范,按照适当的配比将混凝土倒入施工区域,并使用振动器进行浇筑和压实。
2.5 处理表面:在混凝土刚浇注完毕后,需要对地面表面进行处理,以提高地面的平整度和光滑度。
可以使用平头刀或砂纸进行打磨,去除杂质和不平整部分。
2.6 养护施工:混凝土地面完成后,需要进行养护工作,以确保混凝土的强度和稳定性。
通常需要进行湿润养护,即在施工区域覆盖湿润的保护膜,并定期喷水以保持湿润。
3. 注意事项3.1 安全措施:在混凝土地面施工过程中,需要注意施工安全。
施工人员应佩戴防护设备,如安全帽、安全鞋等,并遵守相关的安全操作规程。
3.2 施工质量:混凝土地面施工质量对整个建筑工程的质量有着重要影响。
因此,在施工过程中,需要严格按照设计要求和工程规范进行施工,确保混凝土质量达到标准要求。
3.3 养护措施:养护工作对混凝土地面的强度和稳定性至关重要。
施工完成后,需要按照养护要求进行湿润养护,并避免强物理冲击和过早负荷。
4. 结论通过本文档提供的施工方案和注意事项,可以有效指导混凝土地面施工工程,确保施工质量和安全性。
在实施施工过程中,请务必遵守相关规定和操作规程,确保施工的顺利进行。
混凝土楼地面施工步骤与技巧
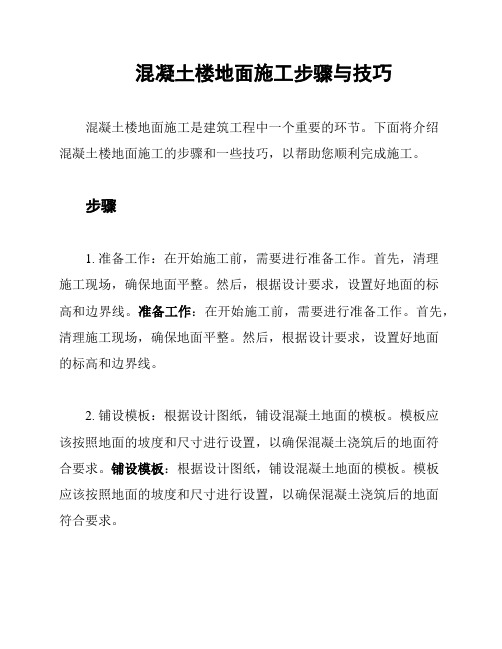
混凝土楼地面施工步骤与技巧混凝土楼地面施工是建筑工程中一个重要的环节。
下面将介绍混凝土楼地面施工的步骤和一些技巧,以帮助您顺利完成施工。
步骤1. 准备工作:在开始施工前,需要进行准备工作。
首先,清理施工现场,确保地面平整。
然后,根据设计要求,设置好地面的标高和边界线。
准备工作:在开始施工前,需要进行准备工作。
首先,清理施工现场,确保地面平整。
然后,根据设计要求,设置好地面的标高和边界线。
2. 铺设模板:根据设计图纸,铺设混凝土地面的模板。
模板应该按照地面的坡度和尺寸进行设置,以确保混凝土浇筑后的地面符合要求。
铺设模板:根据设计图纸,铺设混凝土地面的模板。
模板应该按照地面的坡度和尺寸进行设置,以确保混凝土浇筑后的地面符合要求。
3. 混凝土浇筑:在模板设置好后,开始进行混凝土的浇筑。
首先,根据设计要求,将混凝土材料按照比例混合好。
然后,使用泵车或者倒车机将混凝土倒入模板内。
在倒入混凝土的过程中,需要使用振动棒进行振捣,以确保混凝土的密实性。
混凝土浇筑:在模板设置好后,开始进行混凝土的浇筑。
首先,根据设计要求,将混凝土材料按照比例混合好。
然后,使用泵车或者倒车机将混凝土倒入模板内。
在倒入混凝土的过程中,需要使用振动棒进行振捣,以确保混凝土的密实性。
4. 养护:混凝土浇筑完成后,需要进行养护。
养护的目的是让混凝土逐渐获得足够的强度。
通常情况下,需要对混凝土进行喷水养护,并使用遮阳网等材料保护混凝土表面免受太阳暴晒和风化。
养护:混凝土浇筑完成后,需要进行养护。
养护的目的是让混凝土逐渐获得足够的强度。
通常情况下,需要对混凝土进行喷水养护,并使用遮阳网等材料保护混凝土表面免受太阳暴晒和风化。
5. 修整与抛光:在混凝土达到设计强度后,可以进行修整与抛光。
修整主要是修复混凝土表面的不平整和缺陷,抛光则是提升地面的光滑度和美观度。
修整与抛光:在混凝土达到设计强度后,可以进行修整与抛光。
修整主要是修复混凝土表面的不平整和缺陷,抛光则是提升地面的光滑度和美观度。
混凝土地坪施工工艺完整流程

混凝土地坪施工工艺完整流程一、前期准备工作混凝土地坪施工前需要进行一系列的前期准备工作,包括确定施工地坪的设计方案、准备施工材料和工具等。
设计方案需要根据地坪的用途和要求,确定地坪的厚度、强度等参数,以及施工方法和施工工艺。
准备施工材料包括混凝土、钢筋、膨胀剂等,工具包括振动器、切割机、平整机等。
二、地面处理地面处理是混凝土地坪施工的第一步,主要包括清理、修补和预处理。
清理工作是指清除地面上的杂物和污垢,确保地面干净整洁。
修补工作是指修复地面上的裂缝和坑洞,保证地面平整。
预处理工作是指对地面进行打磨和划痕,增加混凝土与地面的粘接力。
三、铺设隔离层铺设隔离层是为了防止地坪与地基之间的渗水和潮气,同时起到缓冲和保护作用。
隔离层一般使用塑料薄膜或沥青纸进行铺设,覆盖整个地面,并将边缘部分与墙体固定。
四、铺设钢筋网铺设钢筋网是为了增加混凝土地坪的强度和稳定性。
钢筋网的尺寸和间距需要根据设计方案确定,通常是采用焊接钢筋网,将其平铺在地面上,与隔离层固定。
五、浇筑混凝土浇筑混凝土是混凝土地坪施工的关键步骤。
在浇筑前,需要按照设计要求进行混凝土配合比的调整,确保混凝土的强度和流动性。
浇筑时,需要使用振动器进行振捣,以排除混凝土中的气泡和杂质,使混凝土密实均匀。
六、养护处理混凝土地坪施工完成后,需要进行养护处理,以保证混凝土的强度和质量。
养护时间一般为7天至14天,期间需要进行水养护和遮阳保温处理。
水养护是指每天定期浇水,以保持混凝土的湿润。
遮阳保温处理是指在阳光直射的情况下,使用遮阳网或草帘等材料进行遮挡,防止混凝土过早干燥和龟裂。
七、表面处理混凝土地坪施工完成后,可以根据需要进行表面处理,以提高地坪的美观和使用性能。
常见的表面处理方法包括打磨、抛光、喷涂和划线等。
打磨和抛光可以使地坪的表面光滑平整,增加光泽度。
喷涂可以给地坪增加颜色和纹理,使其更具装饰效果。
划线是为了标示出地坪的使用区域和通道,增加地坪的功能性。
地下室混凝土地面施工工艺

地下室混凝土地面施工工艺本文档旨在介绍地下室混凝土地面施工的工艺过程。
施工准备- 确保工地周围的安全,并采取必要的安全措施。
- 清除施工区域内的障碍物和杂物。
- 检查地面平整度,必要时进行修整。
- 准备好所需的施工材料和设备。
地下室混凝土地面施工步骤1. 基础处理:在地下室地面施工之前,首先需要进行基础处理。
这包括清理基础部分,确保无泥土或碎石等杂物。
如果有必要,还可以进行填埋处理以提高地基的稳定性。
2. 防水处理:在进行混凝土浇筑之前,必须进行地面防水处理。
这可以采用刷涂或喷涂防水材料的方式,确保地下室地面具备一定的防水性能。
3. 模板安装:安装模板是地下室混凝土地面施工的重要步骤。
根据设计要求,选择合适的模板材料,并按照地面的形状和尺寸进行精确安装。
确保模板的稳固性和平整度。
4. 钢筋布置:在地下室地面施工之前,需要根据设计要求进行钢筋的布置。
钢筋的数量和布置方式应符合相关标准和规范。
5. 混凝土浇筑:进行地下室混凝土地面施工时,需要按照浇筑顺序和方法进行施工。
确保混凝土的均匀浇筑和充实,避免出现空洞和裂缝。
6. 养护处理:混凝土地面浇筑完成后,需要进行养护处理。
这包括对湿润混凝土表面进行覆盖保护,并保持适当的湿度和温度环境,促进混凝土的早期强度发展。
7. 地面修整:在混凝土地面充分干燥和硬化后,可以进行地面修整。
这包括打磨、抛光或刷涂防尘材料等工序,使地面达到预期的平整度和光滑度。
安全注意事项- 施工过程中,必须遵守相关的安全规范和操作规程。
- 建立安全警示标识,提醒施工人员注意安全事项。
- 使用合适的个人防护装备,并确保施工现场的通风良好。
请注意,本文档提供的仅为地下室混凝土地面施工的一般工艺过程,具体施工细节可能根据实际情况而有所差异。
在施工前应进行详细的方案设计和工程计算,并遵循相关的法律法规要求。
混凝土楼地面施工流程详述

混凝土楼地面施工流程详述
一、前期准备
1. 确定施工地点和楼地面的设计要求。
2. 进行现场勘测,包括地面平整度、土壤承载力等。
3. 安排施工队伍和必要的施工设备。
二、基础处理
1. 清理施工地点,确保地面无杂物和障碍物。
2. 进行地面修整,消除明显的凹凸不平。
3. 对于土质较差的地面,可进行加固处理,如填充砂土或碎石。
三、铺设防水层
1. 在基础处理完成后,进行防水层的铺设。
2. 使用适当的防水材料,如沥青防水卷材或聚合物防水涂料。
3. 严密铺设防水层,确保地面的防水效果。
四、浇筑混凝土
1. 在防水层完成后,进行混凝土的浇筑。
2. 准备混凝土材料,确保材料的质量和比例合适。
3. 使用混凝土搅拌机将混凝土搅拌均匀。
4. 将混凝土倒入地面,并利用振动器进行均匀压实。
五、养护处理
1. 在混凝土浇筑完成后,进行养护处理。
2. 使用喷水器对混凝土地面进行湿润处理,防止过早干燥和开裂。
3. 根据混凝土材料的要求,进行养护时间的控制。
六、检验验收
1. 经过充分养护后,对混凝土地面进行检验验收。
2. 检查地面的平整度、强度和防水效果。
3. 如有问题或不合格部分,进行修复和调整。
以上是混凝土楼地面施工的详细流程,根据实际情况和设计要求,可进行适当的调整和变动。
在施工过程中,需严格按照相关规范和标准操作,确保施工质量和安全。
混凝土地面铺设施工工艺

混凝土地面铺设施工工艺
材料准备
在开始混凝土地面铺设之前,需要准备以下材料:
- 级配合适的混凝土料
- 石英砂和碎石(骨料)
- 水泥
- 适量的水
工艺步骤
以下是混凝土地面铺设的工艺步骤:
1. 准备施工现场:
- 确保施工现场的平整度和干净度,清除任何杂物和障碍物。
- 在需要的地方设置挡板和导向线,以确保混凝土浇筑的准确性。
2. 调配混凝土:
- 将石英砂和碎石按照一定的比例混合,加入适量的水泥。
- 混合时要确保均匀搅拌,以获得一致的混凝土质量。
3. 浇筑混凝土:
- 在施工现场倾倒混凝土,并使用振捣器进行振动。
振动有助于去除气泡和空洞,并提高混凝土的密实度。
- 使用振捣器时,要注意不要过度振动,以免使混凝土流动性过大。
4. 平整混凝土:
- 在混凝土浇筑后,使用平整工具对混凝土表面进行修整。
- 确保混凝土表面平整、光滑,并符合设计要求。
5. 养护混凝土:
- 在混凝土浇筑后,进行适当的养护。
- 使用喷水器进行湿润保养,以防止混凝土表面龟裂和干燥。
总结
混凝土地面铺设施工工艺包括准备施工现场、调配混凝土、浇筑混凝土、平整混凝土和养护混凝土。
按照以上步骤进行施工,可以确保混凝土地面的质量和耐久性。
在施工过程中,要密切注意每个步骤的细节,尽量避免出现问题和缺陷。
如果有任何疑问或需要进一步的指导,请随时告知。
混凝土楼地面施工方案

混凝土楼地面施工方案混凝土楼地面施工方案是指在建筑工程中对混凝土楼地面进行施工的详细计划和步骤。
混凝土楼地面是一个承受重力和使用负荷的重要部分,其质量和施工工艺直接关系到建筑物的安全性和使用寿命。
本文将从施工准备、材料选用、施工步骤和质量控制等方面,详细介绍混凝土楼地面施工方案。
一、施工准备1. 确定施工进度和工期,制定施工计划,并进行时间和资源的合理安排。
2. 保证施工现场的整洁有序,清除杂物,确保施工的安全和顺利进行。
3. 测量现场的地面水平度和高程,并进行必要的调整。
二、材料选用1. 混凝土:选择符合国家标准的优质混凝土,确保其强度和耐久性。
根据设计要求,确定混凝土的配合比和拌合工艺。
2. 骨料和添加剂:选用质量优良的骨料,并根据设计要求,选择合适的添加剂提高混凝土的性能。
3. 钢筋网和模板:根据设计要求,选用符合标准的钢筋网和模板,并进行正确安装和固定。
三、施工步骤1. 模板安装:在地面按照设计要求安装模板,并进行水平校正和固定。
2. 钢筋布置:根据设计要求,在模板内布置钢筋,并进行正确的连接和固定。
3. 混凝土浇筑:在模板内将预先计量好的混凝土倒入,并采取合适的振捣措施,确保混凝土密实均匀。
4. 平整中骨:在混凝土初凝后,采用专用工具对地面进行平整和压实,消除表面的空隙和缺陷。
5. 养护和后处理:在混凝土固化前,在地面进行养护,以保证混凝土的强度和耐久性。
针对施工后可能出现的裂缝和缺陷,进行及时修补和处理。
四、质量控制1. 施工过程中,严格按照设计要求和施工规范进行操作,确保施工质量和安全。
2. 对施工材料进行严格验收,保证其质量和符合标准。
3. 进行必要的检测和监测,如地面平整度、厚度和强度等参数的测量,确保施工质量达到设计要求。
4. 对施工过程中出现的问题和缺陷,及时采取纠正措施,确保施工质量和进度。
以上是混凝土楼地面施工方案的详细介绍。
通过合理的施工准备、材料选用、施工步骤和质量控制,可以确保混凝土楼地面施工的质量和安全。
混凝土地面施工方案(样本)
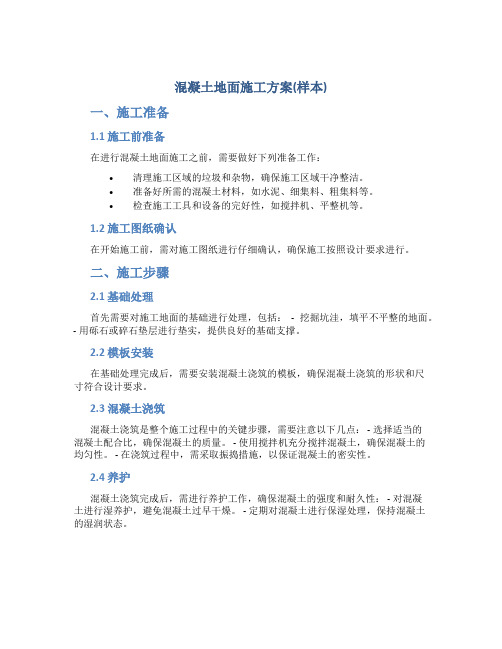
混凝土地面施工方案(样本)一、施工准备1.1 施工前准备在进行混凝土地面施工之前,需要做好下列准备工作:•清理施工区域的垃圾和杂物,确保施工区域干净整洁。
•准备好所需的混凝土材料,如水泥、细集料、粗集料等。
•检查施工工具和设备的完好性,如搅拌机、平整机等。
1.2 施工图纸确认在开始施工前,需对施工图纸进行仔细确认,确保施工按照设计要求进行。
二、施工步骤2.1 基础处理首先需要对施工地面的基础进行处理,包括:- 挖掘坑洼,填平不平整的地面。
- 用砾石或碎石垫层进行垫实,提供良好的基础支撑。
2.2 模板安装在基础处理完成后,需要安装混凝土浇筑的模板,确保混凝土浇筑的形状和尺寸符合设计要求。
2.3 混凝土浇筑混凝土浇筑是整个施工过程中的关键步骤,需要注意以下几点: - 选择适当的混凝土配合比,确保混凝土的质量。
- 使用搅拌机充分搅拌混凝土,确保混凝土的均匀性。
- 在浇筑过程中,需采取振捣措施,以保证混凝土的密实性。
2.4 养护混凝土浇筑完成后,需进行养护工作,确保混凝土的强度和耐久性: - 对混凝土进行湿养护,避免混凝土过早干燥。
- 定期对混凝土进行保湿处理,保持混凝土的湿润状态。
三、施工验收3.1 表面质量检查在混凝土地面施工完成后,需对混凝土地面的表面质量进行检查,确保表面平整、无开裂等缺陷。
3.2 强度检测对混凝土地面的强度进行检测,确保其符合设计要求。
四、施工注意事项4.1 施工中需注意安全在施工过程中需严格遵守安全操作规程,确保施工人员和设备的安全。
4.2 防止天气影响在施工过程中需注意天气变化,避免雨水、大风等不利天气对施工的影响。
以上是混凝土地面施工的基本方案,希望能对您理解混凝土地面施工有所帮助。
混凝土地面施工方案

混凝土地面施工方案混凝土地面施工是一种常见的地面铺设方式,适用于各种场所,如工业厂房、仓库、停车场等。
在进行混凝土地面施工时,需要注意施工前的准备工作、施工过程中的操作方法和施工后的养护措施。
下面是一个关于混凝土地面施工方案的详细介绍。
一、施工前准备1.土壤处理:确保施工地坪土壤的稳定性和承重能力。
如有需要,进行土壤改良或增强处理。
2.底层处理:铺设好底层材料,如砂、碎石等,确保底层平整、坚固。
3.边框设置:在施工区域的四周设置好边框,确保混凝土浇筑时不会流失。
4.钢筋网布置:按照设计要求,将钢筋网进行布置,以增强混凝土的强度和承重能力。
5.基础处理:对于需要在地基上铺设混凝土地面的情况,需要进行地基处理,确保地基的稳定性和排水性能。
二、施工方法1.混凝土配比:按照设计要求,选取适当的水泥、砂、碎石和水进行混合,以达到所需的强度和耐久性。
2.混凝土浇筑:将混凝土均匀地倒入施工区域,并利用振动器进行振捣,以排除空气泡和使混凝土更加紧实。
3.平整施工:使用批刀、直尺等工具,将混凝土表面进行平整处理,确保地面平整度达到设计要求。
4.伸缩胶带安装:在地面伸缩缝位置安装伸缩胶带,防止地面开裂。
5.滑面处理:使用木铲或刮刀等工具将混凝土表面进行抹平,以便后期施工或使用。
三、养护措施1.包覆养护:施工完成后,立即对施工区域进行包覆养护,以防止混凝土过早干燥和开裂。
养护时间一般为7-14天。
2.防水养护:根据需要,对混凝土地面进行防水处理,以提高地面的耐久性和抗渗透能力。
3.表面处理:可以对混凝土地面进行表面处理,如打磨、刷漆等,以提高地面的美观度和防尘性能。
四、质量控制1.施工过程监控:在施工过程中,需要定期进行施工质量的检查,确保各项指标符合设计要求。
2.施工记录备份:对施工过程进行记录和备份,以备后期质量验收和责任追究。
3.质量验收:施工完成后,进行质量验收,检查地面平整度、强度、抗渗透性等指标是否符合要求。
混凝土地坪的施工方法
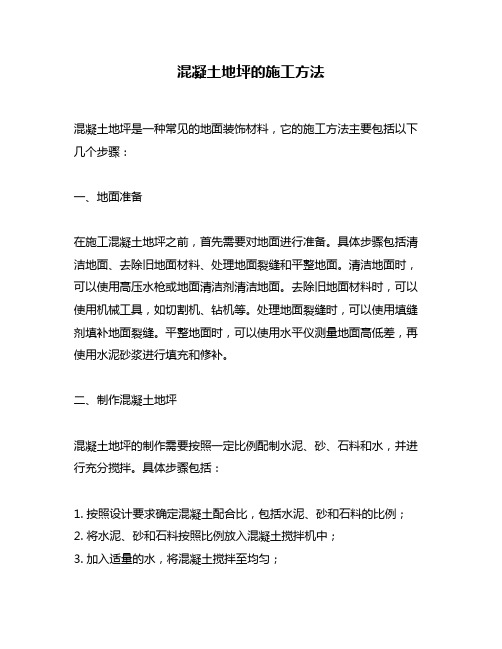
混凝土地坪的施工方法混凝土地坪是一种常见的地面装饰材料,它的施工方法主要包括以下几个步骤:一、地面准备在施工混凝土地坪之前,首先需要对地面进行准备。
具体步骤包括清洁地面、去除旧地面材料、处理地面裂缝和平整地面。
清洁地面时,可以使用高压水枪或地面清洁剂清洁地面。
去除旧地面材料时,可以使用机械工具,如切割机、钻机等。
处理地面裂缝时,可以使用填缝剂填补地面裂缝。
平整地面时,可以使用水平仪测量地面高低差,再使用水泥砂浆进行填充和修补。
二、制作混凝土地坪混凝土地坪的制作需要按照一定比例配制水泥、砂、石料和水,并进行充分搅拌。
具体步骤包括:1. 按照设计要求确定混凝土配合比,包括水泥、砂和石料的比例;2. 将水泥、砂和石料按照比例放入混凝土搅拌机中;3. 加入适量的水,将混凝土搅拌至均匀;4. 搅拌好的混凝土装入卡车中,运输至施工现场。
三、混凝土地坪施工混凝土地坪的施工需要进行以下几个步骤:1. 浇筑混凝土地坪:将混凝土倒入施工区域,并使用抹平机将混凝土抹平,使其均匀分布在地面上;2. 振捣混凝土地坪:使用振动器振捣混凝土地坪,使其更加紧密,减少空隙;3. 铺设骨架:在混凝土地坪上铺设钢筋网或钢筋筋网,以增强混凝土地坪的承载能力;4. 抛光混凝土地坪:在混凝土地坪表面抛光,以增强其光泽度和平滑度;5. 涂装保护材料:在混凝土地坪表面涂装保护材料,以保护其表面免受腐蚀和磨损。
四、维护混凝土地坪混凝土地坪施工完成后,需要进行维护,以确保其使用寿命和美观度。
具体方法包括:1. 在混凝土地坪表面涂装保护材料,以保护其表面免受腐蚀和磨损;2. 定期清洁混凝土地坪表面,以去除灰尘和杂物;3. 定期检查地面裂缝和磨损情况,及时进行修补和维护;4. 避免在混凝土地坪上进行重物拖拉或撞击,以免损坏地面。
总体来说,混凝土地坪的施工方法比较复杂,需要在准备工作、制作混凝土地坪和混凝土地坪施工等方面进行详细的规划,并进行全面的维护和管理,以确保混凝土地坪的质量和使用寿命。
混凝土地坪施工方法
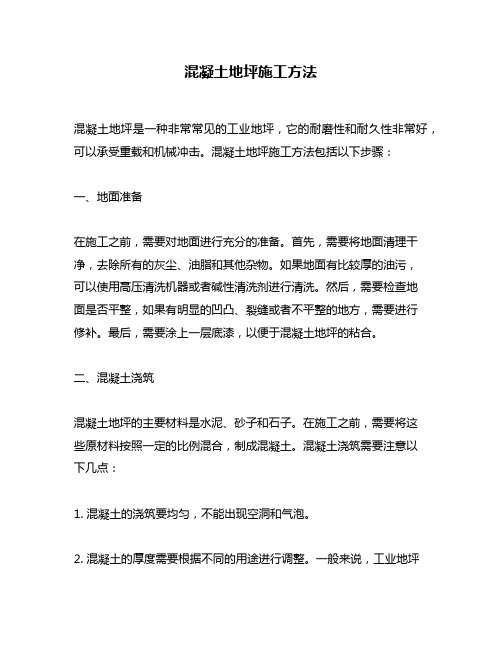
混凝土地坪施工方法混凝土地坪是一种非常常见的工业地坪,它的耐磨性和耐久性非常好,可以承受重载和机械冲击。
混凝土地坪施工方法包括以下步骤:一、地面准备在施工之前,需要对地面进行充分的准备。
首先,需要将地面清理干净,去除所有的灰尘、油脂和其他杂物。
如果地面有比较厚的油污,可以使用高压清洗机器或者碱性清洗剂进行清洗。
然后,需要检查地面是否平整,如果有明显的凹凸、裂缝或者不平整的地方,需要进行修补。
最后,需要涂上一层底漆,以便于混凝土地坪的粘合。
二、混凝土浇筑混凝土地坪的主要材料是水泥、砂子和石子。
在施工之前,需要将这些原材料按照一定的比例混合,制成混凝土。
混凝土浇筑需要注意以下几点:1. 混凝土的浇筑要均匀,不能出现空洞和气泡。
2. 混凝土的厚度需要根据不同的用途进行调整。
一般来说,工业地坪的厚度应该在10-15厘米之间。
3. 混凝土的浇筑需要在温度适宜的时候进行。
如果温度过高或者过低,会影响混凝土的质量。
4. 混凝土浇筑后需要进行充分的抹平和压实,以确保地面的平整度和密实度。
三、地面养护混凝土地坪在浇筑完成后需要进行养护,以确保地坪的质量。
养护的主要目的是防止混凝土过早干燥和龟裂。
具体的养护方法包括:1. 在浇筑完成后,需要覆盖一层薄膜或者湿毛巾,并保持地面湿润。
2. 在混凝土地坪表面喷洒养护剂,以提高混凝土地坪的耐水性和耐磨性。
3. 避免在混凝土地坪表面行走或者施工,以免对地面造成损害。
4. 养护时间一般为7-14天,具体时间需要根据混凝土地坪的厚度和天气条件进行调整。
总之,混凝土地坪施工需要注意细节,包括地面准备、混凝土浇筑和地面养护。
只有在每个环节都做好了工作,才能保证混凝土地坪的质量和使用寿命。
混凝土浇筑地面施工步骤

混凝土浇筑地面施工步骤一、准备工作在开始混凝土浇筑地面之前,需要进行一些准备工作。
首先,确定施工区域的范围和尺寸,清理施工区域内的杂物和障碍物。
其次,测量地面的高程和坡度,确保施工地面的水平度和坡度符合设计要求。
最后,准备好所需的施工工具和材料,如混凝土搅拌机、振动器、水泥、骨料等。
二、基础处理在进行混凝土浇筑之前,需要对基础进行处理。
首先,清理基础表面的灰尘和油脂等杂质,确保基础表面干净。
然后,修补基础上的裂缝和不平整处,以确保基础的稳固性和平整度。
三、模板搭设在混凝土浇筑地面之前,需要搭设模板。
模板的作用是固定混凝土的形状和尺寸,确保浇筑出的地面平整。
首先,根据设计要求和尺寸,在基础上安装木质或金属模板。
然后,使用水平仪和测量工具检查模板的水平度和垂直度,调整模板的位置和高度,使其符合要求。
四、混凝土浇筑混凝土浇筑是地面施工的关键步骤。
首先,将水泥、骨料和适量的水按照一定比例放入混凝土搅拌机中进行搅拌,直到混凝土均匀且无颗粒状物质。
然后,将搅拌好的混凝土倒入模板内,利用振动器震动混凝土,使其充分填充模板内的空隙,排除混凝土中的气泡和空洞。
同时,用木板或扫帚等工具平整混凝土表面,确保地面平整度。
五、养护处理混凝土浇筑完成后,需要进行养护处理以保证混凝土的强度和耐久性。
养护处理包括水养护和覆盖养护两种方式。
水养护是在混凝土浇筑后,使用喷水器或洒水车对地面进行湿润处理,防止混凝土过早干燥和开裂。
覆盖养护是在混凝土浇筑后,使用塑料薄膜或湿棉被等覆盖在地面上,以保持湿润和温度稳定,促进混凝土的硬化和强度发展。
六、验收和完工在混凝土浇筑地面施工完成后,需要进行验收和完工工作。
首先,对浇筑地面的平整度、坡度、强度等进行检查,确保符合设计要求和施工规范。
然后,进行验收记录和资料整理,包括施工记录、质量检测报告等。
最后,进行工地的清理和整理,确保施工现场的整洁和安全。
混凝土浇筑地面是建筑施工中常见的一项工作,施工过程中需要严格按照上述步骤进行操作,确保施工质量和效果。
混凝土地面施工工艺流程

混凝土地面施工工艺流程1. 施工准备- 仔细审查和检查设计图纸和规范要求,确保施工过程符合相关要求;- 准备施工所需的材料和设备,包括混凝土、钢筋、模板、拌合设备、振捣器等;- 清理施工现场,确保工作区域整洁,并进行必要的平整处理。
2. 地基处理- 对地基进行清理和平整,去除杂物和不平整的部分;- 如需要,进行填土和夯实以保证地基的稳定性;- 根据设计要求,在地基上设置相应的支撑,如木板或支脚。
3. 模板安装- 根据设计图纸要求,安装混凝土施工所需的模板;- 确保模板的稳定性和对齐度,以保证混凝土浇筑时能得到所需的形状和尺寸;- 检查模板是否平整,如有不平整的地方,进行必要的处理和调整。
4. 钢筋布置- 根据设计要求,在已安装好的模板内安放钢筋;- 确保钢筋的正确位置和间距,以保证混凝土的强度和承重能力;- 钢筋的连接处要进行绑扎牢固,确保整体结构的稳定性。
5. 混凝土浇筑- 检查模板和钢筋安装是否符合要求,确保施工准备工作完成;- 根据施工现场的尺寸和深度要求,选择合适的混凝土配比和拌合设备;- 将混凝土从拌合设备输送至施工区域,在模板内均匀浇筑,避免混凝土的堆积和气泡的产生;- 使用振捣器对混凝土进行振实,排除混凝土内的空洞和杂质。
6. 养护处理- 混凝土浇筑完成后,及时进行养护处理,以确保混凝土的强度和耐用性;- 使用喷水器或覆盖保护膜对混凝土进行湿润保养,防止过快干燥和开裂;- 根据混凝土类型和气候条件,合理确定养护时间,一般需持续数天至数周。
7. 表面处理- 混凝土养护期结束后,对地面表面进行处理,以提升其美观和耐久性;- 如需要,可以进行打磨、抛光、喷涂等工艺,使地面更加平整、光滑和有纹理;- 根据设计要求进行防水、防尘、耐磨等特殊处理,提高混凝土地面的使用寿命。
以上是混凝土地面施工的基本步骤和流程,根据实际情况可以做适当调整。
在施工过程中,需要严格按照要求进行操作,确保施工质量和安全。
混凝土地坪施工步骤

混凝土地坪施工步骤
一、前期准备工作
1. 确定施工地点和面积
2. 检查地面是否平整,有无裂缝、凸起等缺陷
3. 测量地面高度和坡度,确定施工厚度
4. 准备所需的工具和材料,包括混凝土、水泥、石英砂、石灰石、水等
二、地面处理
1. 清理地面,清除杂物、油污等
2. 修补地面缺陷,如填充裂缝、凸起
3. 打磨地面,使其光滑平整
三、地坪施工
1. 制定混凝土配合比和施工计划
2. 按照配合比将水泥、石英砂、石灰石、水混合制成混凝土
3. 将混凝土倒在地面上,用钢筋拉平
4. 等待混凝土凝固,然后用抛光机进行抛光处理
5. 在混凝土表面涂刷保护剂,防止污染和磨损
四、地坪养护
1. 混凝土凝固后,封闭地坪,保持湿润状态,防止龟裂
2. 等待混凝土完全干燥,然后移除封闭材料
3. 观察地坪表面情况,如有损坏应及时修补
4. 进行定期的维护和清洁,保持地坪的美观和耐用性
五、安全注意事项
1. 操作人员需穿戴好安全装备
2. 操作时应注意防止混凝土喷溅
3. 操作过程中应注意机器和工具的安全使用
4. 在施工现场设置明显的安全警示标志
以上是混凝土地坪施工步骤的详细规格,施工前应认真检查地面情况和准备材料,施工时应按照配合比和施工计划进行操作,并注意安全事项。
施工完成后应进行养护和定期维护,以保持地坪的美观和耐用性。
- 1、下载文档前请自行甄别文档内容的完整性,平台不提供额外的编辑、内容补充、找答案等附加服务。
- 2、"仅部分预览"的文档,不可在线预览部分如存在完整性等问题,可反馈申请退款(可完整预览的文档不适用该条件!)。
- 3、如文档侵犯您的权益,请联系客服反馈,我们会尽快为您处理(人工客服工作时间:9:00-18:30)。
齐峰混凝土地面构造做法:素土压实,300厚级配碎石(30~50mm)铺2cm石粉,0.15mmPE防潮层二层,C25混凝土φ12@200双层双向A区150厚、B区200厚、C区250厚,C25彩色耐磨面层。
一、工程施工重点分析及解决方案1.确保土方压实度满足设计要求,防止出现不均匀沉降。
采用素土分层夯实、碾压,严格控制分层厚度,碾压机械行走速度控制在2km/h,在厂房边轴线以外2m 范围内均需进行素土回填夯实,压实系数符合设计要求。
2.地坪表面平整度误差控制在3mm内。
混凝土振捣梁振捣后,大刮杠及时找平,小刮杠找平再次找平。
3.防止地面裂缝是工程中的重中之重。
本工程厂房长241.2m、宽62.2m,设计未设变形缝,厂房长度方向(1)轴~(17)轴、宽度方向(A)轴~(D)轴墙体一侧留置膨胀缝宽度20mm,纵向缩缝采用平头缝,按纵向6m、横向7.5m分缝,横向缩缝采用假缝,假缝宽度5~10mm,高度为混凝土面层厚度1/3。
二、施工准备1.地面施工前做好各种管线及工艺管路的敷设。
严禁地面成活后二次施工和破坏地面。
2.施工人员经过质量技术交底,施工机具安排到位,施工及检查机具已经落实并到位,混凝土运输设备性能良好并具备连续作业条件。
磨光机性能良好,梁式振捣器设备性能良好,振捣梁钢轨平直,高强铝合金大小刮杠各准备两根,照明设施落实到位,成品保护材料准备到位,应急备用物品有所储备。
3.施工配合比符合要求,坍落度控制在要求范围内。
4.地面施工材料准备充足,确保连续施工。
5.地面混凝土施工前屋面施工已结束,防止漏雨影响地面质量,并掌握天气情况。
三、施工工艺程序定位放线→地面素土整平压实(夯实)→300厚级配碎石(30~50mm)铺2cm石粉→PE膜防潮层→支侧模槽钢→绑扎钢筋→复核侧模标高→地面面层混凝土→人工摊平→振捣梁振捣→大刮杠刮平(刮杠大于纵缝宽度1米)→小刮杠再次找平→按设计要求比例撒耐磨材料第一遍(规定用量2/3)→提浆机提浆→撒耐磨材料第二遍(规定用量1/3)→打磨机压光→养护→割缝四、施工方法(一)素土(回填土料)压实1. 夯实土料含水量控制回填时严格控制填土的含水率,使其保持在最佳含水状态。
回填土料杂质含量不大于5%,填土土料含水量的大小,直接影响到夯实(碾压)质量,含水量过小,夯压(碾压)不实;含水量过大,则易成橡皮土。
当含水量过大,应采取翻松、晾干、换土回填、掺入干土或其他吸水性材料等措施;如土料过干,则应预先洒水湿润。
土料含水量一般以手攥成团、自然落地散开为宜。
工长、质检员现场检查。
检查结果填写检查记录附照片。
2. 回填土料压实振动碾碾压机械行驶速度不超过2km/h。
应采用“薄填、慢驶、多次”的方法,填土厚度每层虚铺300mm,用30T压路机碾压6遍,碾压方向从两边逐渐向中间,碾轮每次重叠宽度约20~30cm。
每层碾压结束,质检员采用压实度检测仪随时抽检压实密实度是否符合要求。
填写检查记录附检查照片。
柱基周围无碾压的部位,用RWH-30C汽油打夯机人工配合夯实。
为确保厂房地坪下土体稳定,在厂房边轴线以外2m范围内均需进行素土回填;压实密实度,除另有规定外,应压至轮子下沉量不超过1~2cm为度。
工长、质检员检查,检查结果填写检查记录附检查照片。
3. 质量控制与检验填土施工过程中应检查每层填铺厚度、含水量控制和压实程序;压实(或夯实)之后,对每层回填土的质量进行检验,一般采用环刀法取样测定土的密实度或采用填土压实度现场检测仪,符合设计要求后,才能填筑上层,取样组数规范要求厂房地面每1000m2取样1组,施工时现场质检员采用填土压实度检测仪随时抽检。
(二) 级配碎石铺设1. 碎石料粒径运至现场的级配碎石粒径及材质必须符合设计要求,粒径级配合理。
2. 碎石压实地面素土(填土)压实后,铺设300厚级配碎石(50~100),碎石粒径符合设计要求,碎石摊铺后须经碾压机械碾压,采用15T振动压路机碾压密实,碾压方向从两边逐渐向中间,压实密实度,除另有规定外,应压至轮子下沉量不超过1~2cm为度。
3. 质量控制与检验质检员对进场碎石粒径观查检查,控制振动压路机行走速度,检查结果填写记录附照片。
(三) 地面混凝土厂房长度方向(1)轴~(17)轴、宽度方向(A)轴~(D)轴墙体一侧留置膨胀缝,纵向缩缝采用平头缝,按纵向6 m、横向7.5m分缝,横向缩缝采用假缝,假缝宽度5~10mm,高度为混凝土面层厚度1/3。
1.支拆侧模薄膜铺设后即可支侧模,按纵向6m分缝支设,采用I16槽钢做地面侧模兼混凝土振捣梁的轨道,支模时用水准仪严格控制槽钢标高,在模板支设后用C25细石混凝土将槽钢下面填实(或用混凝土做侧模支墩)。
先行浇注的混凝土成品在拆除侧模板时均会出现边线不垂直或豁边情况,直接进行其它区域浇注出现施工缝不垂直,采用拆除模板后先弹线切直,再填充混凝土的施工工艺。
2.钢筋绑扎设计要求钢筋采用φ12@200双层双向,钢筋横纵分布,在阴阳角部位增设护角钢筋,布设方法见图,避免混凝土成活后阴阳角处地面裂缝,为防止损坏塑料防潮层,工长或质检员对工人提前交底,要求马凳筋在场外加工完成运至作业面,严禁在作业面焊接钢筋,下层钢筋绑扎时随时注意保护塑料防潮层。
2.混凝土浇注为防止混凝土污染墙面及钢柱,浇注前将该部位用塑料膜防护。
浇注时严格控制混凝土坍落度130~1 60mm,质检员或施工员每隔2小时现场检查一次,检查结果填写检查记录附照片。
混凝土由人工配合摊铺至设计厚度+虚铺高度(虚铺高度根据经验为2~3cm)。
摊铺混凝土时应连续摊铺,不得中断。
设有管沟的地面,管沟盖板上的混凝土垫层厚度不宜小于50mm。
该垫层与管沟处的垫层间应加铺不小于300mm 宽的钢筋网,以免出现裂缝。
砼输送泵在布设管路时要充分考虑到泵管支架处与地面钢筋分开,防止泵管晃动扰动钢筋和管路布设影响成活,其中混凝土泵管的钢管支架下设木板用以保护薄膜,施工人员小心操作严禁硬物碰撞薄膜以保护薄膜免遭破坏。
3.混凝土振捣用水平自行式振动梁进行振捣作业,振动梁就位前先将梁底铺设塑料和白铁皮防止损坏地面,将混凝土振捣密实直至出浆,应注意边角处一定要振实。
砼振捣后使用水准仪及时复测轨道的水平情况,并特制高强度大刮杠来回往返3~4次,达到上表面整平、布满原浆且粗骨料被挤压沉实到水泥混凝土中下部为止,将表面混凝土浆抹平,小刮杠局部再次找平,误差控制在3mm以内。
4.耐磨层施工①检查平整度:对混凝土施工完毕的地面进行平整度检查,采用水平检测仪,测量其表面平整度是否达到要求。
平整度的要求:3000±2mm。
②去泌水:在平整度达到要求后,在混凝土初凝前,应使用橡皮管去除多余泌水。
③在混凝土地面初凝(根据现场情况凝固一段时间后,在脚踩上时下陷2.0mm~4.0mm时),开始耐磨面层的施工,每平方5kg,厚度5mm,施工时先将规定用量的2/3用手工均匀撒布在初凝的混凝土表面。
完成第一撒布作业。
④机器打磨:待耐磨材料吸收一定水分后,进行至少二次加装圆盘的机械镘作业。
⑤第二次撒布耐磨材料:等第一次耐磨材料硬化到一定程度,进行第二次剩余的耐磨面层撒布作业。
⑥机器打磨:第二次撒布材料后,待耐磨材料吸收一定水分,再进行至少四次加装圆盘的机械镘作业。
机械镘作业应纵、横向交错进行。
⑦表面收光:根据地面的硬化情况,进行至少三次不加装圆盘的机械镘作业。
卸下圆盘采用机械磨光片镘磨,机械应纵横交错进行,运转速度和镘磨角度变化视混凝土地面硬化情况而作出调整,直至表面收光为止。
边角等机械难以操作的区域可用手工加工完成。
⑧涂抹地面养护剂:耐磨材料地面完成后5~6小时,为防止其水分蒸发过快,确保耐磨粉强度稳定增长,采用在其表面涂敷养护剂的方法进行前期养护。
5.伸缩缝的设置和施工①缩缝地面混凝土按6×7.5m设置缩缝,根据经验,通常养护3天~5天内并且混凝土抗压强度达到6~10MPa (切缝时间应严格掌握,过早切缝会使石子松动损坏缝缘;过晚切缝困难,且缝两端易产生不规则开裂。
)。
切割时沿纵横向切割,形成6×7.5m缩缝,是分仓浇注的接头缝和后切割缝。
切割深度5mm,缝深度1/3混凝土厚度,根据要求缝内嵌填柔性材料。
切缝操作方法:在拟切缝的水泥混凝土上弹出墨线,安好导轨导向架,将切缝机定位,开动切缝机,放水给切片润滑降温,转动刀架手柄,缓慢进刀,采用5mm厚金刚石锯片切缝,使锯片首先达到设计缝深,然后旋紧螺丝,锁住丝杆并开动行走。
②伸缝厂房长度方向(1)轴~(17)轴、宽度方向(A)轴~(D)轴墙体一侧留置膨胀缝,膨胀缝内填入聚苯乙烯泡沫板,板厚20mm,防止因温度变化引起混凝土变形受到阻碍。
在地坪结束后,外墙下部用弧形塑胶踢脚板镶贴,刚好将此缝隐蔽,达到美观效果。
五、质量保证措施施工时加强重点工序的动态管理,每工序质量检查均附填表附照片,保证混凝土地面施工质量。
(一)严格控制进场材料检验、检测,保证合格产品进入工地。
(二)进场材料、数量必须满足连续施工,禁止施工因无材料、无计划而中断。
(三)进行认真的质量技术交底。
严格控制砼施工前的准备工作的落实和施工设备使用的连续性及操作技术人员的技艺水平、施工方法、施工的环境能保证地面工程的正常进行和保证施工质量。
(四)严格控制侧模板标高,及时用水准仪抄测。
(五)地面钢筋绑扎位置准确,钢筋型号、级别、数量和间距合理并已经过隐蔽验收。
(六)由专人控制砼面层的找平、抹光、成活、成品保护和分格缝的切割。
(七)地面分段浇注时,在下段砼浇注前先切除多余砼,并采用割缝设备分格缝位置切割,同时要保证砼切割时保证有足够的强度和不要切出锯齿和掉角。
(八)砼施工过程中要注意采用严格的过程控制程序。
(九)砼施工前要提前做好设备预埋、管线敷设,严禁地面砼成活后破坏成活地面。
六、成品保护(一)养护:面层抹压结束24h后,用塑料薄膜覆盖保温保湿养护,养护时间至少不少于7d。
(二)地面成活后其它工序施工进入前要注意成活地面的成品保护,防止油柒和涂料污染,防止设备安装等硬性物品砸碰,防止地面运料拖物划伤等。
(三)成活地面上的架体车腿等要用软布包扎,并在下面垫上木板,行走架车等要用胶轮架车。
(四)地面上的焊渣和砂粒线缆头等要及时清理,以防硬粒物的擦伤和划痕。
(五)油柒涂料等工序施工时要在下面铺设防护布(如地毯彩条布等) 。
并设置成品保护警示牌和由专人负责看护,提高成品保护意识。
(六)切割时要随时用水刷子清出缝中泥浆并集中收集后用非金属器具收起,以防收起时地面被划伤。