客户交流会发言材料
客户代表发言稿

客户代表发言稿
尊敬的各位领导、各位同事:
大家好!我是客户代表,很高兴能在这里向大家发言。
作为客户代表,我深知客户是公司的生命线,他们的满意度直
接关系到公司的发展和成长。
因此,我始终把客户利益放在首位,
努力为客户提供优质的服务和产品。
在日常工作中,我始终保持着良好的沟通和协调能力,及时了
解客户的需求和反馈,为客户提供满意的解决方案。
我也注重细节,努力做到每一个环节都符合客户的期望,让客户感受到我们的用心
和诚意。
同时,我也在不断提升自身的专业知识和技能,以更好地为客
户服务。
我会不断学习行业动态和市场趋势,保持敏锐的洞察力,
为客户提供更具竞争力的建议和方案。
在今后的工作中,我将继续努力,不断提升自己的专业素养,
为客户提供更加优质的服务。
同时,我也希望能够与各位同事携手
合作,共同为客户创造更大的价值,推动公司的发展和壮大。
最后,再次感谢各位领导和同事对我的信任和支持,我会继续努力,为公司的发展贡献自己的力量。
谢谢大家!。
客户座谈会发言稿

客户座谈会发言稿首先,我代表公司对大家能抽出宝贵的时间参加今天的座谈会表示衷心的感谢。
在这里,我将就一些公司处理客户投诉、产品服务和未来发展等方面进行交流,同时也欢迎大家对公司提出宝贵的建议和意见。
首先,我想和大家分享一下公司对待客户投诉的态度。
作为一家服务型企业,我们始终坚持以客户为中心,认真对待客户反馈和投诉。
无论是产品质量问题,还是服务不周全,我们都会认真对待,积极解决。
我们注重客户的意见和建议,不断完善我们的产品和服务,确保客户的满意度和信任度。
同时,公司也意识到在产品和服务方面还有不足之处,更需要听取客户的建议和意见。
我们诚挚地希望大家能积极参与公司的产品和服务改进计划,分享您的想法和建议,让我们能更好地为您提供更优质的产品和服务。
为了更好地了解客户的需求和期望,我希望各位能分享您对我们产品的使用体验和感受,以及对我们未来发展的期待和建议。
只有通过密切的沟通和合作,我们才能够更好地满足客户的需求,提高公司的整体服务水平。
接下来,我想着重介绍一下公司的产品服务。
我们一直致力于为客户提供最好的产品和服务,以满足客户不同需求的各种需求。
我们的产品涵盖了各个领域,包括电子产品、家居用品、健康保健品等等,我们的服务团队也配备齐全,随时为客户提供一站式的服务。
在未来的发展规划中,公司将进一步加大研发投入,提升产品的质量和性能。
同时,我们也将加强与客户的沟通和互动,听取客户的需求和建议,及时调整和改进产品和服务,确保客户的满意度和信任度。
最后,我再次感谢各位客户的支持和信任,希望我们能够携手合作,共同开创美好的未来。
同时,也欢迎大家在今天的座谈会上畅所欲言,分享您的想法和建议,让我们更好地为您提供更优质的产品和服务。
谢谢大家!愿我们的合作越来越好!。
客户座谈会演讲稿
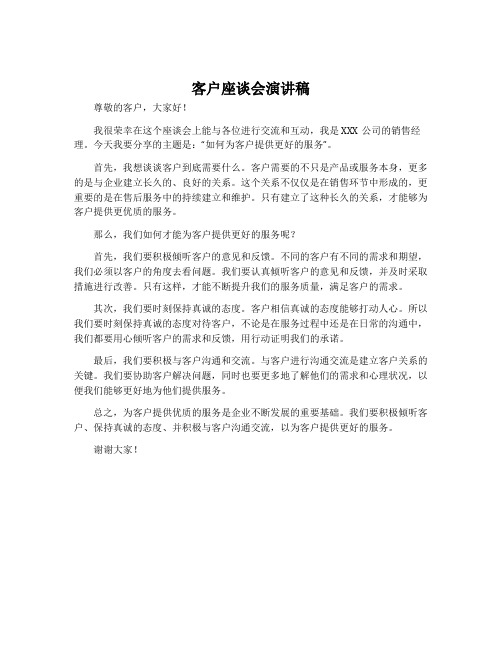
客户座谈会演讲稿
尊敬的客户,大家好!
我很荣幸在这个座谈会上能与各位进行交流和互动,我是XXX公司的销售经理。
今天我要分享的主题是:“如何为客户提供更好的服务”。
首先,我想谈谈客户到底需要什么。
客户需要的不只是产品或服务本身,更多的是与企业建立长久的、良好的关系。
这个关系不仅仅是在销售环节中形成的,更重要的是在售后服务中的持续建立和维护。
只有建立了这种长久的关系,才能够为客户提供更优质的服务。
那么,我们如何才能为客户提供更好的服务呢?
首先,我们要积极倾听客户的意见和反馈。
不同的客户有不同的需求和期望,我们必须以客户的角度去看问题。
我们要认真倾听客户的意见和反馈,并及时采取措施进行改善。
只有这样,才能不断提升我们的服务质量,满足客户的需求。
其次,我们要时刻保持真诚的态度。
客户相信真诚的态度能够打动人心。
所以我们要时刻保持真诚的态度对待客户,不论是在服务过程中还是在日常的沟通中,我们都要用心倾听客户的需求和反馈,用行动证明我们的承诺。
最后,我们要积极与客户沟通和交流。
与客户进行沟通交流是建立客户关系的关键。
我们要协助客户解决问题,同时也要更多地了解他们的需求和心理状况,以便我们能够更好地为他们提供服务。
总之,为客户提供优质的服务是企业不断发展的重要基础。
我们要积极倾听客户、保持真诚的态度、并积极与客户沟通交流,以为客户提供更好的服务。
谢谢大家!。
交流会后的交流发言材料
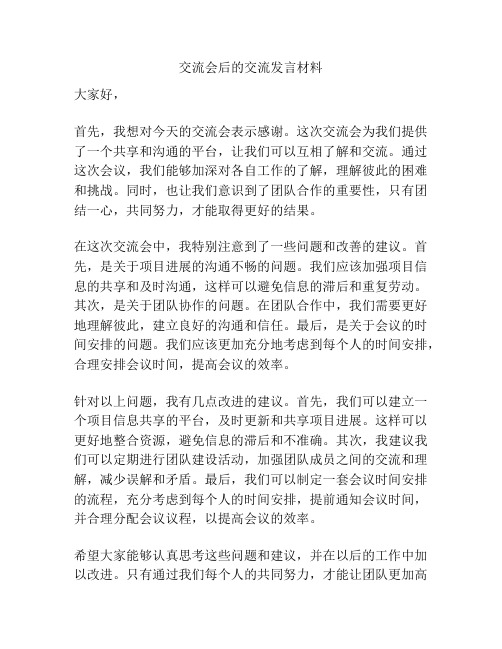
交流会后的交流发言材料
大家好,
首先,我想对今天的交流会表示感谢。
这次交流会为我们提供了一个共享和沟通的平台,让我们可以互相了解和交流。
通过这次会议,我们能够加深对各自工作的了解,理解彼此的困难和挑战。
同时,也让我们意识到了团队合作的重要性,只有团结一心,共同努力,才能取得更好的结果。
在这次交流会中,我特别注意到了一些问题和改善的建议。
首先,是关于项目进展的沟通不畅的问题。
我们应该加强项目信息的共享和及时沟通,这样可以避免信息的滞后和重复劳动。
其次,是关于团队协作的问题。
在团队合作中,我们需要更好地理解彼此,建立良好的沟通和信任。
最后,是关于会议的时间安排的问题。
我们应该更加充分地考虑到每个人的时间安排,合理安排会议时间,提高会议的效率。
针对以上问题,我有几点改进的建议。
首先,我们可以建立一个项目信息共享的平台,及时更新和共享项目进展。
这样可以更好地整合资源,避免信息的滞后和不准确。
其次,我建议我们可以定期进行团队建设活动,加强团队成员之间的交流和理解,减少误解和矛盾。
最后,我们可以制定一套会议时间安排的流程,充分考虑到每个人的时间安排,提前通知会议时间,并合理分配会议议程,以提高会议的效率。
希望大家能够认真思考这些问题和建议,并在以后的工作中加以改进。
只有通过我们每个人的共同努力,才能让团队更加高
效和协作,取得更好的成果。
谢谢大家!。
客户座谈会领导发言稿(通用3篇)
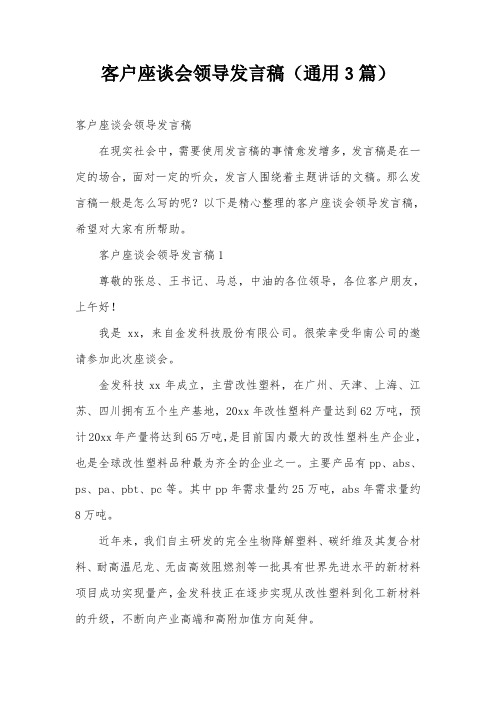
客户座谈会领导发言稿(通用3篇)客户座谈会领导发言稿在现实社会中,需要使用发言稿的事情愈发增多,发言稿是在一定的场合,面对一定的听众,发言人围绕着主题讲话的文稿。
那么发言稿一般是怎么写的呢?以下是精心整理的客户座谈会领导发言稿,希望对大家有所帮助。
客户座谈会领导发言稿1尊敬的张总、王书记、马总,中油的各位领导,各位客户朋友,上午好!我是xx,来自金发科技股份有限公司。
很荣幸受华南公司的邀请参加此次座谈会。
金发科技xx年成立,主营改性塑料,在广州、天津、上海、江苏、四川拥有五个生产基地,20xx年改性塑料产量达到62万吨,预计20xx年产量将达到65万吨,是目前国内最大的改性塑料生产企业,也是全球改性塑料品种最为齐全的企业之一。
主要产品有pp、abs、ps、pa、pbt、pc等。
其中pp年需求量约25万吨,abs年需求量约8万吨。
近年来,我们自主研发的完全生物降解塑料、碳纤维及其复合材料、耐高温尼龙、无卤高效阻燃剂等一批具有世界先进水平的新材料项目成功实现量产,金发科技正在逐步实现从改性塑料到化工新材料的升级,不断向产业高端和高附加值方向延伸。
回顾过去,金发科技与中油的合作历史已超过10年,从最初简单的买卖关系到今天的全面合作,双方不断创造着新的成果,并建立了密切、良好的合作关系。
1)业务层面:20xx年金发对中油的采购量达到xx吨,其中向华南公司采购xx 吨,20xx年总采购量预计超过xx万吨,其中向华南公司预计采购xx 吨,增长率达xx%;远远超过了金发改性产品的增长率;2)技术层面:借助华南公司的业务平台,金发科技与中油研究院成立了联合实验室,打造了一个良好的技术交流与合作平台。
在此平台上,双方共同开发了sp179、780a、1730等一批具有代表性的新产品,开展了实验室检测能力比对项目,并定期安排技术交流。
19年来,金发科技的改性塑料业务取得了快速、健康的发展,喝水不忘挖井人,成绩面前,我们深知离不开中油,尤其是华南公司各位领导和朋友的厚爱和大力支持,在此,请接受我们最真挚的感谢!感谢华南公司多年来为金发科技提供了优良的产品、优质的服务、以及可靠的供应保障,感谢各处室的处长、业务经理们在日常工作中给予的点滴关爱。
来访接待经验交流发言材料
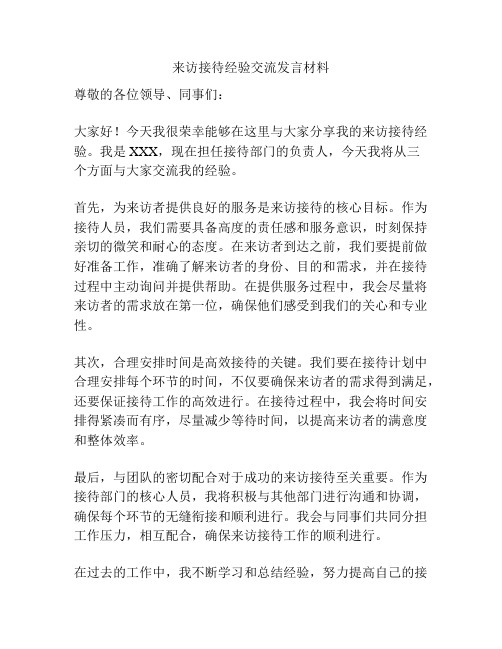
来访接待经验交流发言材料
尊敬的各位领导、同事们:
大家好!今天我很荣幸能够在这里与大家分享我的来访接待经验。
我是XXX,现在担任接待部门的负责人,今天我将从三
个方面与大家交流我的经验。
首先,为来访者提供良好的服务是来访接待的核心目标。
作为接待人员,我们需要具备高度的责任感和服务意识,时刻保持亲切的微笑和耐心的态度。
在来访者到达之前,我们要提前做好准备工作,准确了解来访者的身份、目的和需求,并在接待过程中主动询问并提供帮助。
在提供服务过程中,我会尽量将来访者的需求放在第一位,确保他们感受到我们的关心和专业性。
其次,合理安排时间是高效接待的关键。
我们要在接待计划中合理安排每个环节的时间,不仅要确保来访者的需求得到满足,还要保证接待工作的高效进行。
在接待过程中,我会将时间安排得紧凑而有序,尽量减少等待时间,以提高来访者的满意度和整体效率。
最后,与团队的密切配合对于成功的来访接待至关重要。
作为接待部门的核心人员,我将积极与其他部门进行沟通和协调,确保每个环节的无缝衔接和顺利进行。
我会与同事们共同分担工作压力,相互配合,确保来访接待工作的顺利进行。
在过去的工作中,我不断学习和总结经验,努力提高自己的接
待能力和服务水平。
通过与各位同事的合作与交流,我相信我会在未来的工作中继续不断进步,并为公司的发展和客户的满意度做出更大的贡献。
谢谢大家!。
旅行社交流洽谈会发言材料

旅行社交流洽谈会发言材料
尊敬的各位来宾,
大家好!首先,感谢各位莅临本次旅行社交流洽谈会,我非常荣幸能在这里与各位分享我们旅行社的情况和服务。
我代表XX旅行社,作为本次洽谈会的主持人,我希望通过今天的交流,能够更好地了解各位旅行社的需求,并且提供我们团队的专业服务。
我要着重强调的是,我们旅行社一直以来注重客户体验和服务质量,力求为每一位客户打造出令人满意的旅行体验。
我们拥有一支经验丰富的团队,他们对各个目的地的了解非常深入,并能够根据客户的需求量身定制旅行计划。
除了提供个性化定制服务外,我们旅行社还与众多优质的合作伙伴建立了长期稳定的合作关系,包括航空公司、酒店、景点等。
这些合作伙伴能够为我们的客户提供高质量的服务,确保旅行的舒适和安全。
同时,我们旅行社还非常注重旅行社责任和可持续发展的问题。
我们努力推行环保措施,并且鼓励客户选择环保的旅行方式,以减少对环境的影响。
在未来,我们旅行社将继续秉持着客户至上的原则,不断提高我们的服务质量,以满足客户日益增长的需求。
我们希望能够与各位合作,共同开拓旅游市场,并为更多人带来难忘的旅行
体验。
非常感谢大家的聆听,期待能够与各位建立合作关系!谢谢!。
分行经验交流会发言材料
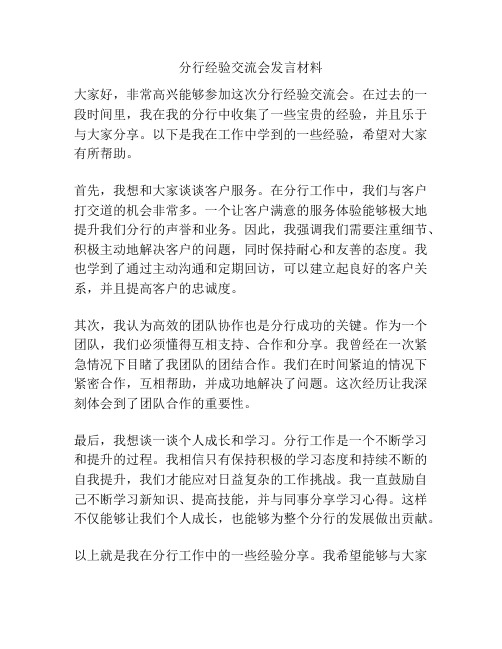
分行经验交流会发言材料
大家好,非常高兴能够参加这次分行经验交流会。
在过去的一段时间里,我在我的分行中收集了一些宝贵的经验,并且乐于与大家分享。
以下是我在工作中学到的一些经验,希望对大家有所帮助。
首先,我想和大家谈谈客户服务。
在分行工作中,我们与客户打交道的机会非常多。
一个让客户满意的服务体验能够极大地提升我们分行的声誉和业务。
因此,我强调我们需要注重细节、积极主动地解决客户的问题,同时保持耐心和友善的态度。
我也学到了通过主动沟通和定期回访,可以建立起良好的客户关系,并且提高客户的忠诚度。
其次,我认为高效的团队协作也是分行成功的关键。
作为一个团队,我们必须懂得互相支持、合作和分享。
我曾经在一次紧急情况下目睹了我团队的团结合作。
我们在时间紧迫的情况下紧密合作,互相帮助,并成功地解决了问题。
这次经历让我深刻体会到了团队合作的重要性。
最后,我想谈一谈个人成长和学习。
分行工作是一个不断学习和提升的过程。
我相信只有保持积极的学习态度和持续不断的自我提升,我们才能应对日益复杂的工作挑战。
我一直鼓励自己不断学习新知识、提高技能,并与同事分享学习心得。
这样不仅能够让我们个人成长,也能够为整个分行的发展做出贡献。
以上就是我在分行工作中的一些经验分享。
我希望能够与大家
互相学习、交流,共同提升分行的业务水平和团队凝聚力。
谢谢大家。
接下来由下一位发言。
接待交流会开场白发言材料

接待交流会开场白发言材料尊敬的各位来宾、亲爱的朋友们:大家下午好!我是今天的主持人,非常荣幸能够站在这个演讲台上,迎接大家莅临本次交流会。
首先,我要向各位嘉宾、代表、专家和朋友们表示热烈的欢迎,感谢你们抽出时间参加这次重要的交流会。
今天,我们齐聚一堂,旨在促进交流、共享经验、拓宽视野。
交流是让人们沟通与互动的桥梁,是增进理解与友谊的纽带。
在这个信息高速发展的时代,交流的重要性更加凸显,我们有责任和义务不断提升自己的交流能力,与人合作,汇聚智慧,共同迈向成功的新时代。
本次交流会的主题是“迈向成功的关键”。
在今天这个充满挑战的世界里,各行各业都在探索一条通向成功的道路。
不论是企业家、科学家、艺术家还是普通上班族,我们都面临各自的困难和压力。
但是,无论我们面对的问题有多大,取得成功的关键往往也在我们自身。
就我个人来说,我深信成功在于创新、发展和坚持。
作为一个开放和包容的平台,本次交流会将为大家提供一个倾听和分享的机会,让我们一起深入交流,相互学习,为迈向成功的道路增添动力。
本次交流会除了演讲和讨论环节外,还安排了互动环节。
通过这个互动环节,我们希望能够拉近与各位嘉宾和朋友们之间的距离,让我们共同参与其中,畅所欲言,展现自我,促进交流与合作。
同时,我们将为大家准备了精美的茶点和文化表演,希望能够给大家带来一次愉快和有意义的经历。
最后,我要再次感谢各位嘉宾、代表、专家和朋友们的到来,感谢你们对本次交流会的关注和支持。
也希望在接下来的时间里,大家能够畅所欲言、积极参与,共同探索成功的关键,分享成功的经验,为我们的个人和组织发展找到更多的机遇和突破。
谢谢大家!祝愿本次交流会取得圆满成功!。
客户到访发言稿范文

大家好!我是来自XX公司的客户,非常荣幸今天能够来到贵公司进行参观和交流。
在此,我代表我们公司向贵公司表示衷心的感谢和崇高的敬意!首先,我要感谢贵公司给予我们这次宝贵的参观机会。
通过实地考察,我对贵公司的企业文化、产品研发、生产流程等方面有了更加深入的了解。
我相信,这次参观将为我们双方的合作奠定坚实的基础。
回顾我们与贵公司的合作历程,不禁让人感慨万分。
自我们首次合作以来,贵公司始终以诚信、专业、创新的精神,为我们提供了优质的产品和服务。
在此,我要对贵公司表示衷心的感谢!首先,感谢贵公司对产品质量的严格把控。
贵公司始终将产品质量视为企业的生命线,从原材料采购到生产加工,每一个环节都严格把关。
这使得我们的产品在市场上赢得了良好的口碑,也为我们的合作奠定了坚实的基石。
其次,感谢贵公司对服务的用心。
贵公司始终坚持以客户为中心,为我们提供了全方位、一对一的服务。
从售前咨询到售后支持,贵公司都给予了我们充分的关注和帮助,使我们感受到了贵公司的真诚与专业。
再次,感谢贵公司对创新的追求。
在市场竞争日益激烈的今天,贵公司始终保持着敏锐的市场洞察力,不断推出具有竞争力的新产品。
这使我们能够紧跟市场步伐,为客户提供更优质的产品和服务。
在这次参观过程中,我深刻感受到了贵公司的实力和魅力。
以下是我对贵公司的几点建议:一、加强品牌建设。
品牌是企业核心竞争力的重要组成部分。
建议贵公司进一步加大品牌宣传力度,提升品牌知名度和美誉度。
二、拓展市场份额。
随着市场的不断变化,建议贵公司积极拓展国内外市场,进一步扩大市场份额。
三、提升创新能力。
创新是企业发展的动力源泉。
建议贵公司继续加大研发投入,培养创新型人才,推动企业持续发展。
最后,我希望我们双方能够继续保持良好的合作关系,携手共进,共创辉煌。
在此,我代表我们公司向贵公司表示诚挚的祝愿:祝愿贵公司事业蒸蒸日上,业绩再创新高!祝愿我们双方合作共赢,友谊长存!谢谢大家!。
保险公司交流会发言材料
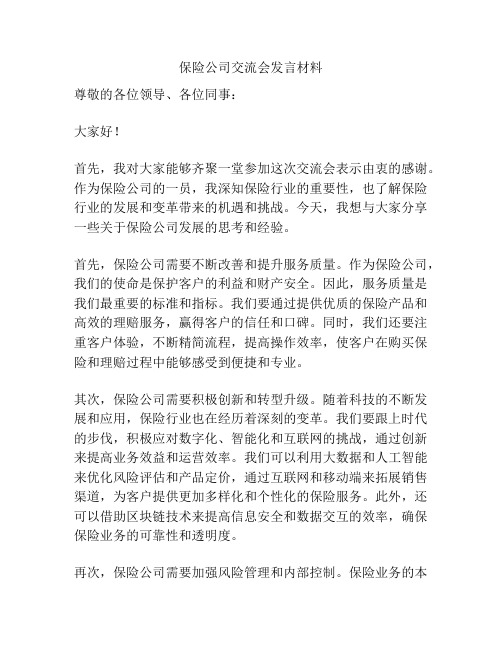
保险公司交流会发言材料尊敬的各位领导、各位同事:大家好!首先,我对大家能够齐聚一堂参加这次交流会表示由衷的感谢。
作为保险公司的一员,我深知保险行业的重要性,也了解保险行业的发展和变革带来的机遇和挑战。
今天,我想与大家分享一些关于保险公司发展的思考和经验。
首先,保险公司需要不断改善和提升服务质量。
作为保险公司,我们的使命是保护客户的利益和财产安全。
因此,服务质量是我们最重要的标准和指标。
我们要通过提供优质的保险产品和高效的理赔服务,赢得客户的信任和口碑。
同时,我们还要注重客户体验,不断精简流程,提高操作效率,使客户在购买保险和理赔过程中能够感受到便捷和专业。
其次,保险公司需要积极创新和转型升级。
随着科技的不断发展和应用,保险行业也在经历着深刻的变革。
我们要跟上时代的步伐,积极应对数字化、智能化和互联网的挑战,通过创新来提高业务效益和运营效率。
我们可以利用大数据和人工智能来优化风险评估和产品定价,通过互联网和移动端来拓展销售渠道,为客户提供更加多样化和个性化的保险服务。
此外,还可以借助区块链技术来提高信息安全和数据交互的效率,确保保险业务的可靠性和透明度。
再次,保险公司需要加强风险管理和内部控制。
保险业务的本质是管理风险,所以我们必须高度重视风险管理和内部控制体系的建立。
我们要不断完善风险评估和风险控制的流程和机制,确保公司在业务拓展和承保风险中能够稳健运营。
同时,我们还要提高员工的风险意识和专业素养,加强员工培训和技能提升,提高员工对风险的识别和管理能力。
最后,我想强调保险公司的社会责任。
作为一家保险公司,我们不仅要追求商业利益,更要承担起社会责任和义务。
我们要积极参与社会公益事业,关注弱势群体的保险需求,努力为社会的稳定和可持续发展做出贡献。
总结一下,保险公司发展需要不断改善和提升服务质量,积极创新和转型升级,加强风险管理和内部控制,承担社会责任。
我希望通过我们的共同努力,我们的保险公司能够在未来的发展中取得可持续的成长和成功。
客户座谈会发言稿

客户座谈会发言稿
尊敬的各位客户:
大家好!我是公司的市场部经理,很荣幸能在此次客户座谈会上为大家发言。
首先,非常感谢各位客户能抽出宝贵的时间参加今天的座谈会,与我们分享使用我们产品的体验和建议。
在今天的座谈会上,我们主要是为了更好地了解各位客户对我们产品的感受和意见,通过与大家的交流,让我们的产品能够更贴近客户的需求,更好地满足大家的需求。
首先,我想就我们产品目前的不足之处向各位客户表示歉意。
在您使用产品的过程中,如果遇到了任何问题或者有任何建议,都请毫不犹豫地告诉我们,我们会认真倾听您的意见,并尽最大努力改进产品,提高服务质量。
同时,我也想向各位客户介绍一下我们公司未来的发展规划。
我们将继续加大研发力度,不断优化产品,提高产品的品质和性能。
同时,我们也会进一步完善售后服务,确保您在使用产品过程中能够得到及时有效的帮助和支持。
除此之外,我们也计划开展更多的客户活动,加强和客户之间的沟通与互动。
我们希望通过不断地倾听客户的声音,与客户建立更紧密的合作关系,共同推动产品的进步和发展。
最后,我想借此机会感谢各位客户对我们公司的支持和信任。
正是因为有了您的支持,我们才能够不断成长壮大,不断完善产
品和服务。
我们会继续努力,不辜负您的信任,为您提供更好的产品和服务。
在此,希望各位客户能够继续保持支持,我们也会一如既往地倾听您的声音,不断改进和创新,为您提供更优质的产品和服务。
谢谢!
谢谢大家!祝各位身体健康、工作顺利!。
用户代表发言稿(共5篇)

用户代表发言稿(共5篇)第1篇:用户代表发言用户代表发言(精选多篇)尊敬的各位领导、尊敬的各位来宾、尊敬的全体与会代表:上午好!非常荣幸,感谢大会让我代表广大用户发言,我表示由衷的感谢。
首先让我们广大用户衷心祝贺北京**技术有限公司成立五周年暨高压变频调速系统百台业绩!这标志着北京**公司迈上了一个新台阶、走上了更加辉煌的腾飞之路,全面提升了**公司的综合竞争力,为**公司争做国内行业领先奠定了更加坚实的基础。
**公司是我们国家拥有自己知识产权的高压变频行业的骨干企业,其产品领域覆盖6kv、10kv电压等级,输出功率可达2021kw的变频器系列产品,满足不同行业广大用户的不同应用需求,目前其产品已应用在自来水、发电等行业,获得用户的好评。
我们天津自来水公司即是其中的一家,而且是第一个吃螃蟹的用户单位。
几年来的实践证明:该产品是可靠的、技术是先进的、在城市供水行业的应用是成功的。
交流电动机变频调速系统技术,尤其是中高压变频调速技术,其在理论研究上早已获得成功,但在实际应用上由于高压电力电子变流器件和高速检测、控制技术在实际制造工艺上的难题多年来未能解决,一直束缚着高压变频调速技术与产品的发展。
但近几年却有长足的发展。
国外出现了rosharll、abb、siemens、robicon、ab等公司的产品。
而该技术产品的国产化也不过是近几年的事情,**公司是生之逢时、恰好赶上这一技术产品开发的步伐,依托清华大学电机工程系,高起点、高速度、高水平,已居于国内同行业领先的地位,这是非常难能可贵的。
希望今后**的产品在性能上、质量上、品种上,尤其是适合中国国情上,百尺竿头、更上一层楼。
在这里我介绍一下北京北开电气股份有限公司在产品生产制造过程中创新提出并坚持执行的“五零”管理,即”研发零隐患、生产零缺陷、管理零失误、服务零投诉、沟通零距离”的新理念。
希望有所借鉴。
我们天津自来水集团多年来一直有幸成为**公司的首家用户,“想用户之所想,急用户之所急”,多年来与天津自来水集团新开河水厂建立了真诚的合作关系,为天津城市供水提供了可靠的高压变频设备、极大的方便了水厂送水泵的调速运行,保障了天津市自来水公司的可靠供水。
在会上作书面交流发言材料

在会上作书面交流发言材料大家好,很高兴能在这次会议上与大家共同交流和分享。
首先,我想重点谈谈我们团队最近的工作进展。
一、项目进展情况我们团队目前正在进行一项重要的项目,项目名称为XXX。
在过去的几个月里,我们团队积极努力,取得了一些重要的进展。
首先,我们成功完成了项目的需求分析和规划阶段。
通过与客户的深入交流和沟通,我们明确了项目的目标和需求,并制定了详细的工作计划。
其次,在设计和开发阶段,我们团队充分发挥各自的专业优势,高效合作,确保项目按时完成。
我们通过不断优化设计方案,提高系统的稳定性和性能,并解决了许多技术难题。
最后,在测试和验收阶段,我们认真对每一个模块进行了全面的测试,确保系统的功能完备和稳定性。
我们也邀请了客户参与系统的验收,确保其满意度和项目的最终成功。
二、团队合作及个人收获在项目的过程中,我们团队展现了良好的团队合作精神。
我们相互协作,相互支持,共同克服了许多困难和挑战。
团队成员之间的密切合作,使得整个项目的推进更加顺利。
同时,通过这次项目的经验,我的个人能力和经验也得到了提升。
我学到了许多新的知识和技能,在解决问题和处理团队合作方面都有了更深入的理解和实践。
三、未来工作展望对于项目的未来,我们将继续努力,确保项目的顺利完成。
我们计划在接下来的几周内完成剩余的任务,并进行系统的最终测试和验收。
我们会继续与客户保持密切的合作和沟通,确保项目的质量和客户的满意度。
此外,我们也会总结这次项目的经验教训,并进行知识分享和团队建设,以提升我们团队的整体能力和竞争力。
最后,我要感谢团队成员的辛勤付出和合作精神,也感谢大家对我们项目的支持和关注。
谢谢大家!。
关于客户座谈会的发言稿

关于客户座谈会的发言稿
尊敬的各位客户,大家好!
今天,我们特地邀请各位客户来参加这次座谈会,与我们共同探讨业务发展的方向。
首先,我代表公司全体员工向大家表示感谢,在此深表敬意。
作为一家创新型企业,我们一直以客户为中心,努力提供优质的产品和服务。
在和大家交流和合作的过程中,我们深刻认识到,只有不断学习和创新,才能更好地满足客户的需求。
在接下来的座谈中,我们将聚焦于企业的业务发展,分享我们的经验和心得,并希望能够倾听大家的意见和建议,让我们一同推动企业发展。
首先,让我和大家分享一下我们近年来的发展方向。
我们始终坚持以人为本,注重企业文化的打造和员工的培养。
同时,我们积极探索新的业务领域,不断开拓新的市场,构建多元化的产品和服务体系。
除此之外,我们还不断加强信息技术的研发和应用,提高企业的智能化程度。
在这个过程中,我们深深认识到,客户就是我们最重要的合作伙伴,是推动我们不断前进的重要力量。
我们需要倾听客户的声音,感受客户的需求,从而更好地为客户服务。
同时,我们也需要不断完善我们的服务体系,提高服务水平,让客户享受到更好的服务体验。
此外,我们还要不断学习和创新,提高企业的核心竞争力。
只有不断进步,才能够抵御市场上的各种风险和不确定因素。
在这个过程中,我们追求的不仅是企业自身的发展,更是推动整个产业的升级和发展。
最后,再次感谢各位客户能够参加本次座谈会,希望我们的交流能够带来更好的合作机会和发展空间。
我们期待与您的再次合作,共同开创美好未来!。
客户经理经验分享交流发言材料

客户经理经验分享交流发言材料
大家好,今天我想分享一些我在客户经理岗位上的经验和心得。
首先,作为一名客户经理,我们的目标是为客户提供最佳的服务,并与他们建立稳固的合作关系。
为了实现这一目标,我们需要加强沟通能力。
在与客户交流时,我们应该始终保持清晰且明确的表达,了解客户的需求和意见,并作出及时的回应和解决方案。
同时,要善于倾听客户的反馈和建议,不断改进自己的工作。
另外,客户经理需要具备良好的人际关系技巧。
我们的工作是与各个层级和部门合作,因此要能够与不同背景和性格的人建立良好的关系。
要学会适应和尊重不同的工作风格和观点,并灵活处理各种复杂的人际关系。
此外,客户经理还应具备一定的专业知识和技能。
我们需要熟悉公司的产品和服务,了解市场动态和竞争对手情况。
只有通过持续学习和提升自己的专业水平,我们才能更好地帮助客户解决问题和满足需求。
最后,一个优秀的客户经理还需要具备良好的时间和压力管理能力。
我们常常面临各种紧急的任务和压力,因此要学会合理规划时间,优先处理重要的工作,并保持冷静和坚定的心态。
总结一下,作为一名客户经理,我们需要加强沟通能力,建立良好的人际关系,提升专业知识和技能,并具备良好的时间和压力管理能力。
只有不断努力和提高,我们才能成为优秀的客
户经理,为客户和公司做出更为卓越的贡献。
谢谢大家!。
客户座谈会领导发言稿范文(通用3篇)

客户座谈会领导发言稿范文(通用3篇)客户座谈会领导发言稿1各位领导、各位嘉宾、各位朋友:今天,____商贸物流园庆中秋商户联谊会在这里隆重举行,这是____入驻__以来的一个重要喜庆日子。
我谨代表入驻____的商户们,对____商贸物流园招商取得初步的成功,表示热烈的祝贺!对前来参加联谊会的各位商户,各界__的朋友表示热烈的欢迎和衷心的感谢!____商贸物流园作为安徽省“__x”重点项目和__市20__年重点项目,斥资30亿元,分五年滚动开发。
引进成功的经营理念、管理模式和知名品牌,打造苏浙皖最大的区域商贸、仓储、物流基地,对提升城市品味,推动安徽经济大发展起到十分重要的作用。
作为商户一员,我被____全新的经营理念和商业模式所吸引;我为____项目如此巨大的规模、以及安徽省政府和__市委市领导对__项目的高度重视,鼎力扶持所动容;我被____高层长远的眼光,专业的运营所征服。
作为商户代表,我们深为__的发展壮大和取得的显著成绩而感到无比喜悦。
在____项目运作过程中,我们商户一定继续给予大力的支持,竭尽全力为____项目的发展、壮大添砖加瓦。
同时,也希望____能借助民营企业的优势,创造更加强大的竞争力,成为全国商业地产一面鲜艳的旗帜。
我相信,用不了多久,一座最具竞争力的大规模、高品质、现代化的展贸大平台,集“交易、展示、仓储、物流、办公、电子商务、品牌孵化”等多种功能与一体,将成为皖东南必不可少的区域商贸、仓储、物流基地,为塑造新徽州商业未来,推动徽州向国际商业化发展起到推波助澜的作用。
最后,预祝____商贸物流园商户联谊会圆满成功!谢谢大家!客户座谈会领导发言稿2尊敬的张总、王书记、马总,中油的各位领导,各位客户朋友,上午好!我是__,来自金发科技股份有限公司。
很荣幸受华南公司的邀请参加此次座谈会。
金发科技1993年成立,主营改性塑料,在广州、天津、上海、江苏、四川拥有五个生产基地,20__年改性塑料产量达到62万吨,预计20__年产量将达到65万吨,是目前国内最大的改性塑料生产企业,也是全球改性塑料品种最为齐全的企业之一。
银行之间相互交流发言材料

银行之间相互交流发言材料银行A:尊敬的各位银行代表,我代表银行A欢迎大家今天的交流会。
在这个竞争激烈的金融市场上,银行之间的合作与交流变得越来越重要。
我们希望通过今天的会议,能够增进彼此的了解,分享经验和最佳实践,共同推动行业的发展。
银行B:非常感谢银行A的热情欢迎。
作为银行B的代表,我非常赞同银行之间的合作与交流对于我们行业的重要性。
我们都面临着相似的挑战,如数字化转型、客户期望的变化等。
只有通过合作,我们才能更好地应对这些挑战并提供更好的服务。
银行C:对于银行C来说,这次交流会是一个非常好的机会。
我们非常期待与各位银行代表的互动,倾听大家的观点和经验。
同时,我们也希望能够与其他银行建立更紧密的合作关系,共同创造更大的价值。
银行D:在这个数字化和全球化的时代,银行之间的交流和合作已经成为不可或缺的一部分。
作为银行D的代表,我们愿意与各位分享我们的创新实践和成功经验,以帮助其他银行在此领域实现突破。
银行E:感谢各位银行代表,今天我们能够聚集在一起,共同探讨行业的未来发展。
我们相信通过加强交流和务实合作,我们能够找到更多的商业机会和相互的利益点,共同实现共赢。
银行F:作为银行F的代表,我们也非常重视与其他银行的合作与交流。
我们鼓励和支持资源的共享和合作项目的推进,以实现更高效、更稳定的金融体系。
银行G:银行G非常感谢今天每位代表的出席。
透过这次交流会,我们希望能够打破信息壁垒,深入了解各位银行的运作模式和策略,以利于我们共同面对市场的挑战,共同实现行业的繁荣与可持续发展。
银行H:对于银行H来说,这次交流会是一个宝贵的机遇。
我们相信,通过分享彼此的经验和洞察,我们能够加深理解,提升自身的竞争力,同时也希望能够促进更加深入和密切的合作关系。
银行I:最后,作为主办方,我们感谢各位银行代表参与这次交流会。
我们希望今天的会议能够成为银行之间进一步合作的起点,推动行业的创新与发展,为客户提供更好的金融服务。
让我们一起携手共进,共同开创未来的成功之路。
银行座谈交流会上发言材料

银行座谈交流会上发言材料尊敬的各位领导、各位同事:大家好!我很荣幸能够在这次银行座谈交流会上发言。
今天,我想与大家分享一些关于银行发展的思考和建议。
首先,我们都知道,金融行业的竞争已经变得异常激烈。
面对市场的竞争压力,银行需要不断提高自身的竞争力,才能够在激烈的市场中立于不败之地。
我认为,要提高银行的竞争力,我们需要从以下几个方面入手。
第一,加大科技创新力度。
随着信息技术的快速发展,银行业务已经进入了数字化、智能化的时代。
我们应该积极应用人工智能、大数据等先进技术,提升银行的业务效率和服务质量。
例如,可以引入智能柜员机,实现24小时无人办理业务,提供更便捷的服务;可以开展移动支付、在线理财等业务,满足客户多样化的需求。
只有不断创新,才能够更好地满足客户的需求,并在市场中抢占先机。
第二,加强风险管理。
作为银行,我们的主要业务是贷款。
然而,贷款业务也是比较风险的,尤其是在当前经济形势不确定的情况下。
因此,我们必须加强风险管理,防范各种风险的发生。
在贷款审核环节,要进行细致、全面的风险评估,合理控制风险的范围和程度。
同时,建立健全的风险管理制度,加强内部审计,及时发现和解决问题。
只有保证风险可控,才能够确保银行的稳定发展。
第三,注重人才培养。
银行作为服务行业,人才是最重要的资源。
我们必须注重人才培养,培养一支高素质、专业化的员工队伍。
一方面,要加强对员工的业务培训,提升他们的专业知识和技能;另一方面,要激励员工的创新意识和团队合作精神,鼓励他们提出新的业务理念和创意方案。
只有培养出一支技术过硬、服务优质的团队,才能够不断提高银行的综合竞争力。
最后,我还想强调一点,那就是银行要积极履行社会责任。
作为金融服务提供者,我们应该以客户为中心,为客户提供更好的服务。
同时,我们还要积极参与社会公益事业,为社会做出应有的贡献。
例如,可以设立专项基金,用于支持教育、环保等公益事业;可以组织员工参与志愿者活动,关注弱势群体的需求。
旅行社交流洽谈会发言材料

旅行社交流洽谈会发言材料尊敬的各位尊贵的客户和同行业的朋友们:大家好!非常荣幸能在这里参加旅行社交流洽谈会,并有机会与各位展开深入的交流和合作探讨。
我代表XXX旅行社向在座的各位介绍一下我们的公司及我们的服务。
XXX旅行社是一家专业从事旅游服务的公司,成立至今已有十年的历史。
我们以为客户提供优质的旅游产品和周到的服务为宗旨,秉持着“诚信、创新、卓越、共赢”的经营理念,不断努力创造更好的旅游体验,赢得客户的满意和信赖。
首先我想强调的是我们的专业团队。
我们拥有一支经验丰富的旅游策划团队和熟悉各类旅游产品的销售团队,他们都是行业内顶尖的专业人才。
我们的团队每年都会进行专业培训和学习,不断提升自己的能力和对旅游市场的了解,以便更好地为客户提供个性化的旅游方案。
同时,我们与许多国内外知名的旅游供应商建立了稳定的合作关系,包括航空公司、酒店、景点等。
这样的合作关系使我们能够获得更好的资源,提供更好的价格和服务,从而给客户带来更多的选择和优惠。
另外,我还要提及我们的创新能力。
在如今激烈竞争的旅游市场中,只有不断创新才能保持竞争力。
我们始终关注旅游市场的新趋势和需求,努力挖掘新的旅游产品和服务。
我们推出了许多特色的主题旅游线路和定制化服务,如文化考察、美食之旅、探险旅行等,以满足不同客户的需求,为他们创造独特且难忘的旅行体验。
最后,我想提醒大家关于我们的售后服务。
我们认为,旅行不仅仅是一个行程,更是一种体验。
因此,我们非常重视旅行结束后的客户反馈和售后服务。
我们设立了专门的客户服务团队,随时为客户解决问题和提供帮助。
我们的目标是使每位客户满意,成为我们的忠实支持者和推荐人。
尊敬的各位,我们相信我们的专业、创新和优质服务能够为您带来满意的旅程和卓越的体验。
我们期待能与您展开合作,共同开拓旅游市场,为旅行者带来更多的美好回忆。
谢谢大家!。
- 1、下载文档前请自行甄别文档内容的完整性,平台不提供额外的编辑、内容补充、找答案等附加服务。
- 2、"仅部分预览"的文档,不可在线预览部分如存在完整性等问题,可反馈申请退款(可完整预览的文档不适用该条件!)。
- 3、如文档侵犯您的权益,请联系客服反馈,我们会尽快为您处理(人工客服工作时间:9:00-18:30)。
胶合板产生脱胶的技术原因分析及生产中容易被忽视的若干问题一、胶合板产生脱胶的技术原因分析胶合板的‘致命缺陷’——脱胶,产生于板中部时叫鼓泡,产生于四边时叫离层。
鼓泡和离层均分为表板脱胶和中板脱胶两种。
产生的原因复杂多样,往往如果对胶合板生产的全过程没有一个完整而有效地监控和记录,很难准确判断。
所以对脱胶的原因分析,要前后左右各方面综合考虑,结合实际情况,尊重事实,切不可主观臆断。
所谓‘技术原因’,就是排除了人员和管理方面的因素,来分析影响产品质量的料,机,法,环四大因素。
1.原材料1.1单板1.1.1表板(面,底板)——太湿:含水率20%以上,比如被水淋湿过;——含油质:树脂,油污染;——材种碱性大或缓冲容量大。
1.1.2中板(芯板,长中板)——太湿:含水率18%以上,如曾被雨水淋湿过或在阴雨潮湿的环境里贮存太久;收购的干中板本身只有半干或干燥机的含水率控制不当。
——太干:含水率5%以下,如干燥机换垛或交接班时中板在机内停留时间过长,蒸汽压高干燥机内温度过高而运行速度未及时对应调整;半干中板与湿板或不同的树种或相差较大的芯,边材均在同一个干燥条件下生产。
——毛刺严重:沟痕深度0.8mm以上或毛刺形成三角棱条形状,如旋切工艺参数调整不当;中板使用前未曾进行有效分选。
——腐朽:木材本身已失去强度和化学活性。
——厚薄:偏薄板热压时本身承受的压力小或不受压,偏薄板涂胶时易引起涂胶量小;偏厚板把旁边正常厚板的表板抬起,造成压力小。
——树皮:树皮‘不吃胶’,即胶合强度低。
——材种含碱性或缓冲容量大。
1.2原胶(生胶)——不合格:如固体含量,粘度,生活期,固化时间,PH值等某项技术指标经检测未达标。
——贮存时间过长或其他原因而变质。
1.3面粉——筋率低,调出的胶达不到预期粘度。
——变质发霉而失效。
2.设备2.1调胶机——转速低或搅拌浆不合适,面团打不开。
——没有双层调温装置。
2.2涂胶机——涂胶辊经长期使用已磨损(要求半年更换一次),造成涂胶不均。
——轴承磨损,造成涂胶量难以控制。
——其他部位损坏。
——不当的设备保养,使胶里含油。
——涂胶辊与挤胶辊间隙调整不当,一头大一头小或整体小。
——挡胶板损坏或内侧有硬胶膜或其他原因造成一头或两头挡胶不严,漏胶多而造成缺胶。
2.3预压机(冷压机)——机械故障,升不了高压或无法预压。
2.4热压机——在装板,待推板,压机闭合或升压过程中,忽遇机械故障或在压机里低压状况时间过长。
3.工艺方法及操作执行3.1调胶——初粘度太低,造成涂胶量小或胶量被板吸收从而造成缺胶或者预压效果差。
——初粘度太高,造成涂胶量过大,后期粘度更高。
——固化剂太多,造成适用期太短而提前干胶。
——固化剂太少,胶粘度在有限的时间里不能有效增长,预压效果差。
——缓冲剂末加或加得少,不能够有效延长适用期。
——缓冲剂加得太多,胶粘度增长太慢,预压效果差。
——午休时间加生胶(或脲素)比例不合适或再开工忘加NH4CL。
3.2一次过胶——湿芯板未及时选出。
——涂胶量小,预压效果差,热压后易离层。
——芯板齐头未对齐或芯板不够宽,造成另一张芯板胶量少或涂不上胶。
——由于芯板重叠或碎板片造成的局部‘没胶’,未能及时补胶。
——组坯动作慢时间长,造成调好的胶在调胶机里或涂胶机里粘度大量增加。
——由于涂胶辊调节间隙太大,或芯板翘曲严重,而造成的涂胶空白点,未能及时补胶。
——由于放胶不及时,造成上胶辊缺胶,一般是两头没胶。
3.3预压:预压效果差,局部不能粘合或缺压后又自开,开口处被风吹干,最终热压胶合失败。
——陈放时间过长。
——预压压力小。
——预压时间短。
3.4二次修补(开刀,开补)——修补时间太长或前等板工或后等板时间太长,造成周转时间加长。
——补条或补边用干板,没有胶。
——修预成型中板未将偏薄单板及脱胶单板割换或补胶效果差。
——预成型中板大的重叠部份,未割除时中间没胶,完全割掉后现出凹陷,均可造成鼓泡(或中空)。
3.5二次过胶(回收)——由于放胶不及时,造成上胶辊缺胶,一般是两头没胶。
——套板两头窜位(没对正),造成另一张芯板胶量少或涂不上胶。
——由于碎板片造成的空白点未及时补胶。
——涂胶量太少,胶液被板子吸收形成缺胶。
——涂胶量太大,对于厚板可能会鼓泡。
3.6涂胶手工铺板——铺板太慢,或收板间隔时间太长,造成周转时间太长。
——铺板过大的重叠或空心。
——不合格长中板料(包括封边,封头,辅板料)未及时挑出。
3.7热压——热压修补存板时间太长,造成在无压下固化。
——热压工艺参数设定不合适。
——厚板未采用‘三段式降压法’以防鼓泡。
——热压误操作。
4.环境冬季温度低,夏季温度高;零晨温度低,下午温度高;雨天温度低,睛天温度高——这些气温上的变化,都会对胶的粘度增长变化率有很大影响,所以要切合每时刻的温度,考虑当时生产的规格需要的周转时间,适当掌握好固化剂和缓冲剂的使用量,使调出来的胶的活性期,满足周转时间的要求。
二、胶合板生产容易被忽视的若干问题加强和改善工艺管理,全面掌握生产过程动态,是胶合板制造过程质量管理的一个重要环节。
合理改善生产工艺,可以提高产品质量。
各级管理人员在认真抓好影响质量因素的各个环节的同时,应充分重视生产工艺对产品质量的影响,以保证产品质量的不断提升。
但以下方面常常被人们所忽略。
1.忽视中板材料的质量差异问题:⑴中板含水率:适宜的含水率一般在8~16%之间,湿板的危害性能人们有一定的认识,但对过干、太干(含水率<5%)的中板往往被忽视了。
中板过干、太干涂胶后胶中的水分很快被中板吸收,增加了胶膜干胶提前固化的风险,对胶合质量不利。
⑵中板温度控制问题常被忽视:干中板使用前的温度不能高于40℃,一般干燥机或晒板的中板要经过至少24小时(有条件的工厂最好存放一周后再使用)的存放降温、平衡含水率后才能使用,以避免带温中板涂胶后增加胶层干胶的风险。
2.胶粘剂调制时常被忽视的问题:⑴忽视对原辅材料质量的检查和反馈,如地下胶池雨天渗水造成胶水变质;胶水贮存时间过长,胶水流动性差,没有严格执行“先进先出”原则,胶水温度过高等。
另外作为填料的面粉质量不稳定:如受潮结团、含较高比例的石粉、加入量异常等;面粉质量的好坏,将直接影响到其加入量和胶水初粘性。
生产实践表明,在原胶粘度相同的情况下,以达到相同的调胶效果(用粘稠度表示)比较,其面粉加入量相差近40%,即用质量差的面粉加入量将增大40%;且含有石粉杂质的面粉较易吸收胶水中的水分,会加剧干胶速度,对胶合质量有重大隐患。
⑵执行调胶配方规定比较随意,物料添加计量不准确或存在严重偏差。
如调胶桶桶壁结胶胶垢影响实际胶水份量,从而影响调胶粘度和质量。
假设桶壁结胶胶垢厚度为4cm,桶径为∮64cm,则结垢后胶桶实际容积只为原容积的76.5%,差别很大。
⑶搅拌时间过长或不足。
时间不足易造成物料混合不均,如面粉有颗粒状,固化剂分布不均,将严重影响调胶质量;时间过长,则易造成混合胶温度上升,面粉熟化发胀,缩短了胶水活性期,严重的甚至造成干胶固化,无法涂布使用。
⑷调胶台卫生较差,调胶质量监控手段单一。
有条件的工厂,必须对调胶后的粘度和PH值进行实时监控,并认真记录备查。
⑸各级管理人员,特别是现场管理人员,都应重视调胶工作,调胶质量好坏对后续工序影响很大。
如粘度过稀,则胶水渗透严重,造成中板缺胶而离层;固化剂加入过多,使胶水活性期缩短,易造成胶层提前干胶固化;固化剂加入量不足,影响冷压时间、冷压效果等。
3.忽视流程时间控制的重要性:在连续工序流程过程中,从一次涂胶(调胶加入固化剂开始)到完成热压的过程时间,就是通常所说的生产流程时间。
生产流程时间应控制在混合胶水的活性期内(此时混合胶仍处在游离状态),否则混合胶水在没有适当压力、温度的作用下提早固化,会造成中板间或中板与底面板间的假胶着现象即称为胶合板离层或胶合不良,影响其物理抗弯性能等。
影响流程时间控制最大的是组坯收台时间,应对收台时间作强制性规定,如规定每班(11小时计)收台不少于5次,这样可尽量缩短板坯的开口陈化时间,减少胶层风干丧失流动性影响冷压效果和胶合质量。
4.忽视热压胶合质量的日常检测:胶合板预成型板坯经过热压后才能成型,胶合质量的好坏经过热压后的初步检查也可见一斑。
可通过对每批次、每班次所生产的板坯抖动、掀压等简易方法进行及时检查,合理调整好三大热压工艺参数,确保产成品质量。
在裁边工序,也可以用折断边条检查木破率的方法判断裁边条的胶合质量,发现异常,及时反馈调整。
有条件的工厂,可按国标要求随机抽样检测其胶合质量,真正做到心中有数。
以上仅是生产过程中质量技术管理的一点心得,仅供参考。
要确保产品质量的稳定,还必须依靠科学有效的手段加以管理方可奏效。
三、生产中常见的质量缺陷:1.冷压效果差,散板:1.1 材料含水率偏高,调胶配比不合理,涂胶量过小干胶(表面缺胶、渗透过多),存放陈化时间不足等。
1.2 胶水:超过贮存期;应了解出厂指标情况,取样分析。
1.3 观察散板状况再作进一步的分析。
2.胶合不良、泡板开胶,如边角离层、面泡、底泡:2.1板芯:材料含水率和三大工艺参数控制情况,了解生产流程流转时间是否过长,空芯、厚薄也会离层。
2.2成品板面泡、底泡:检查贴面调胶后的粘稠度,涂胶量大小等;胶水调的稀(清)易造成:——面板薄容易造成渗透过多,胶量不足而起泡(在砂光面);——底芯面大部分厂家末砂光,高低不平厚薄造成的底泡多;——局部离层,因空芯、厚薄造成的居多。
2.3模板水煮分层:模板胶M加入比例超过10%,可以满足水煮(沸水)4小时的要求,在检查生产工艺的基础上(特别关注冲压次数),加大批量抽样检测。
2.4地板基材浸渍剥离不达标:(与调胶中固化剂加入量、工艺压力、树种等有关)试件经浸渍渍、干燥,由于湿胀与干缩给胶层以应力,根据胶层是否发生剥离及剥离的程度判断其胶合性能。
试件放入70℃±3℃热水中浸渍2h,取出后置于60℃±3℃干燥3h。
结果:每一边的任一胶层开胶的累计长度不超过该胶层长度的三分之一(3mm以下不计),6块试件中,合格试件数大于或等于5块时判为合格。
3.干胶快,初粘性差,粘度小,PH值过高,贮存期短等方面问题这些大部分是由于产品质量指标出现波动引起的,还有一些沟通方面问题,应避免出现;如:存货少——急着出货;出货集中——热胶出货等,一般刚生产的胶经过48小时的存放,对使用方面更加有利。
总之,好板一定要好胶,但好胶不一定出好板,这就涉及到正确使用方面的问题。
出现质量问题时,应按因果分析方法,多方面寻找、排除原因,并第一时间告知业务人员。