连铸生产工艺的发展
连铸技术国内外现状及发展趋势

连铸技术国内外现状及发展趋势
连铸技术是钢铁工业中的重要技术之一,它可以实现高效连续生产,提高生产效率,降低成本。
目前,国内外的连铸技术都在不断发展和完善中。
在国内,连铸技术已经实现了从单流到双流、三流、四流等多流程的升级。
同时,还出现了带分段式结晶器、上下扫描式结晶器等新型结晶器,提高了连铸成材率和质量。
此外,国内的连铸技术还在不断推广智能化生产、绿色环保等方面的应用。
在国外,美国、日本等发达国家在连铸技术方面也有很多创新。
例如,美国的Hazelett连铸技术可以实现高品质的铝合金连铸,日本的CCS连铸技术则可以实现高浓度的钢水连铸。
此外,欧洲的一些连铸厂还在探索使用第三方能源进行加热,以实现更高的能源利用效率。
未来,随着新材料、新工艺、新技术的不断涌现,连铸技术将继续发展和创新。
同时,环保、智能化、自动化等方面也将成为连铸技术发展的重要方向。
- 1 -。
连铸生产工艺

连铸生产工艺
连铸是指采用连续浇铸工艺将熔融金属连续浇铸成长条状的铸件,常用于生产铜、铝等金属材料。
连铸工艺相比传统离散铸造工艺具有高效、节能、高质量等优势,被广泛应用于现代金属材料的生产。
首先,连铸工艺的核心是焊接,由于金属的熔点通常很高,因此需要在高温环境下进行。
在连铸过程中,金属先经过一组预热炉,使其温度达到熔点以上,并保持恒定。
然后,熔融金属经过调漏口进入连铸机的浇注坑,通过直径大小不同的浇口,将金属流注到已经加热和涂有抗粘涂料的铸模中。
接下来,金属在连铸机中由于连铸速度以及冷却系统的作用,逐渐冷却凝固,在冷却过程中逐渐形成金属栅格状的微晶结构。
冷却速度的控制是连铸工艺中至关重要的一环,过快的冷却速度会导致过早的凝固,产生气孔和其他缺陷,而过慢的冷却速度则会影响生产效率。
因此,连铸工艺中通常通过调节冷却水的流量和温度以及调整浇注速度来控制冷却速度。
最后,凝固后的铸坯经过拉伸机进行拉拔,使其变为所需要的尺寸和形状。
拉拔是通过对铸坯施加轴向拉力来实现的,拉拔过程中金属的晶粒结构逐渐细化,从而提高了材料的强度和韧性。
拉拔机通常由一组连续的牵引辊和摩擦刹车组成,牵引辊以恒定的速度运转,将铸坯拉伸成所需尺寸。
在拉拔过程中,还可以通过在线热处理和表面处理,对材料进行进一步的改性和提高其耐腐蚀性。
总之,连铸生产工艺是一种高效、节能的金属材料生产工艺。
通过连续浇注和拉拔,可以大大提高生产效率,减少人工操作和能源消耗,同时还能提高材料质量和性能。
随着技术的不断进步,连铸工艺将继续发展,为金属材料的生产提供更好的解决方案。
连铸工作中的改进方案和总结
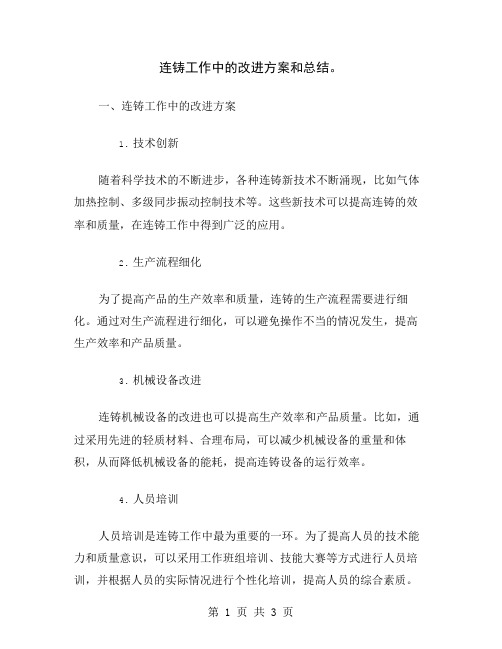
连铸工作中的改进方案和总结。
一、连铸工作中的改进方案1.技术创新随着科学技术的不断进步,各种连铸新技术不断涌现,比如气体加热控制、多级同步振动控制技术等。
这些新技术可以提高连铸的效率和质量,在连铸工作中得到广泛的应用。
2.生产流程细化为了提高产品的生产效率和质量,连铸的生产流程需要进行细化。
通过对生产流程进行细化,可以避免操作不当的情况发生,提高生产效率和产品质量。
3.机械设备改进连铸机械设备的改进也可以提高生产效率和产品质量。
比如,通过采用先进的轻质材料、合理布局,可以减少机械设备的重量和体积,从而降低机械设备的能耗,提高连铸设备的运行效率。
4.人员培训人员培训是连铸工作中最为重要的一环。
为了提高人员的技术能力和质量意识,可以采用工作班组培训、技能大赛等方式进行人员培训,并根据人员的实际情况进行个性化培训,提高人员的综合素质。
二、连铸工作中的总结1.高品质的原材料在连铸工作中,高品质的原材料是保证产品质量的基础。
因此,在原材料采购时,一定要选择质量好、纯度高的原材料。
2.加强管理和监控为了确保连铸工作的正常进行,必须要加强对生产过程的管理和监控。
通过实时监测,可以及时发现和解决生产过程中的问题,避免问题扩大并影响生产效率和产品质量。
3.用先进技术提升质量为了确保连铸生产的高效率和高质量,必须使用先进技术。
只有掌握了先进技术,才能不断提升连铸生产的效率和质量。
4.确保生产安全安全是连铸工作中最为重要的一环。
为了确保生产过程的安全,必须严格遵守生产规程,在工作过程中注意安全,提高员工的安全意识,加强设备的安全保障。
连铸工作中的改进方案和总结可以提高生产效率和产品质量,以适应市场需求的不断增长。
通过不断探索和发展,连铸技术和生产工艺将会得到更加广泛的应用,为实现精准制造和高质量发展做出贡献。
薄板坯连铸连轧工艺技术发展的概况

薄板坯连铸连轧工艺技术发展的概况摘要:薄板坯连铸连轧工艺问世这么多年来发展迅速,CSP、ISP、FTSR为代表的各种工艺技术的发展各具特色。
总的发展趋势是,提高铸机生产能力充分发挥后部连轧机的生产能力;改进品种质量,提高产品的市场覆盖率;采用无头轧制工艺、生产超薄规格产品,以取代部分冷轧产品的市场;应用范围扩大,越来越多的在以高炉铁水为原料的大型联合企业中得到应用,为该工艺的发展开拓了更广阔的前景。
关键词:薄板坯连铸连轧发展趋势1 前言薄板坯连铸连轧是20 世纪80 年代末开发成功的生产热轧板卷的新技术,该项技术发展很快,世界各钢铁发达国家已相继开发了各具特色的薄板坯连铸连轧技术,主要有SMS 开发的CSP(CompactStrip Production)、DEMAG 的ISP(Inline Strip Production)、日本住友的QSP(Quality Slab Production)、达涅利的FTSR(Flexible Thin Slab Rolling)和VAI 的CONROLL(Continue Rolling)以及美国蒂金斯(Tippins)的TSP(Thin Slab Production)等6 种类型。
图2典型的薄板坯连铸—连轧热带钢生产线薄板连铸连轧工艺与常规的工艺相比,由于它具有节能、投资省、生产周期短、劳动成本低及适应性强等优点,故引起了全世界的重视。
据统计全球各地已建成投产及在建的薄板坯连铸共约50流,总生产能力为5228万t/a。
2 几种主要类型的技术特点及其发展2.1 CSP工艺技术世界第一条CSP生产线薄板坯连铸连轧生产线已于1989年建成投产,因其工艺开发早,技术成熟,工艺及设备相对较简单可靠,故实际应用也最多。
至1997年末,SMS已签定的合同已有27流铸机。
CSP技术的主要特点是采用立弯式铸机漏斗形结晶器,最初的铸坯很薄,一般为40~50mm,未采用液芯压下,后部设辊底式隧道炉作为铸坯的加热均热及缓冲装置,采用5~6架精轧机,成品带钢最薄为1~2mm。
连铸连轧
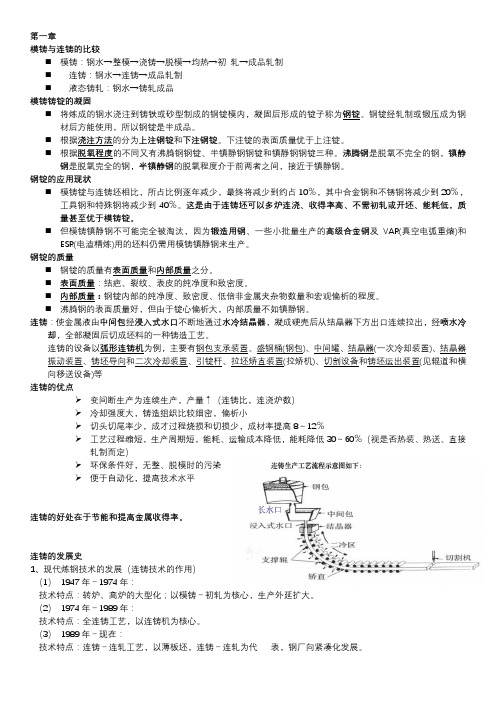
第一章模铸与连铸的比较⏹模铸:钢水→整模→浇铸→脱模→均热→初轧→成品轧制⏹连铸:钢水→连铸→成品轧制⏹液态铸轧:钢水→铸轧成品模铸铸锭的凝固⏹将炼成的钢水浇注到铸铁或砂型制成的钢锭模内,凝固后形成的锭子称为钢锭。
钢锭经轧制或锻压成为钢材后方能使用,所以钢锭是半成品。
⏹根据浇注方法的分为上注钢锭和下注钢锭。
下注锭的表面质量优于上注锭。
⏹根据脱氧程度的不同又有沸腾钢钢锭、半镇静钢钢锭和镇静钢钢锭三种。
沸腾钢是脱氧不完全的钢,镇静钢是脱氧完全的钢,半镇静钢的脱氧程度介于前两者之间,接近于镇静钢。
钢锭的应用现状⏹模铸锭与连铸坯相比,所占比例逐年减少,最终将减少到约占10%,其中合金钢和不锈钢将减少到20%,工具钢和特殊钢将减少到40%。
这是由于连铸坯可以多炉连浇、收得率高、不需初轧或开坯、能耗低,质量甚至优于模铸锭。
⏹但模铸镇静钢不可能完全被淘汰,因为锻造用钢、一些小批量生产的高级合金钢及VAR(真空电弧重熔)和ESR(电渣精炼)用的坯料仍需用模铸镇静钢来生产。
钢锭的质量⏹钢锭的质量有表面质量和内部质量之分。
⏹表面质量:结疤、裂纹、表皮的纯净度和致密度。
⏹内部质量:钢锭内部的纯净度、致密度、低倍非金属夹杂物数量和宏观偏析的程度。
⏹沸腾钢的表面质量好,但由于锭心偏析大,内部质量不如镇静钢。
连铸:使金属液由中间包经浸入式水口不断地通过水冷结晶器,凝成硬壳后从结晶器下方出口连续拉出,经喷水冷却,全部凝固后切成坯料的一种铸造工艺。
连铸的设备以弧形连铸机为例,主要有钢包支承装置、盛钢桶(钢包)、中间罐、结晶器(一次冷却装置)、结晶器振动装置、铸坯导向和二次冷却装置、引锭杆、拉坯矫直装置(拉矫机)、切割设备和铸坯运出装置(见辊道和横向移送设备)等连铸的优点变间断生产为连续生产,产量↑(连铸比,连浇炉数)冷却强度大,铸造组织比较细密,偏析小切头切尾率少,成才过程烧损和切损少,成材率提高8~12%工艺过程缩短,生产周期短,能耗、运输成本降低,能耗降低30~60%(视是否热装、热送、直接轧制而定)环保条件好,无整、脱模时的污染便于自动化,提高技术水平连铸的好处在于节能和提高金属收得率。
绪论
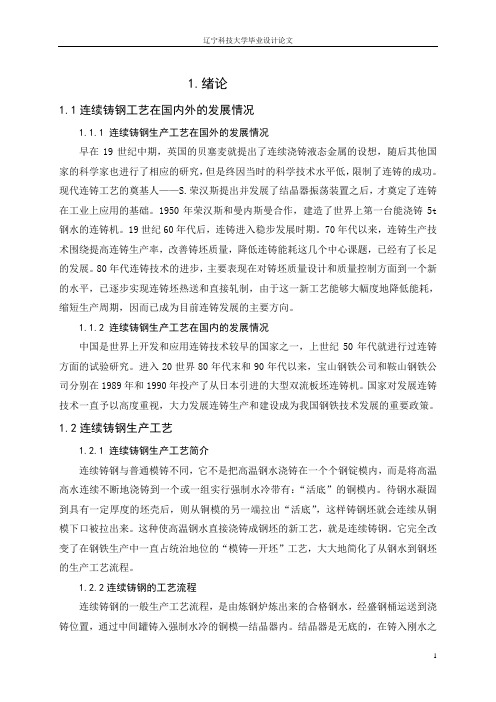
1.绪论1.1连续铸钢工艺在国内外的发展情况1.1.1 连续铸钢生产工艺在国外的发展情况早在19世纪中期,英国的贝塞麦就提出了连续浇铸液态金属的设想,随后其他国家的科学家也进行了相应的研究,但是终因当时的科学技术水平低,限制了连铸的成功。
现代连铸工艺的奠基人——S.荣汉斯提出并发展了结晶器振荡装置之后,才奠定了连铸在工业上应用的基础。
1950年荣汉斯和曼内斯曼合作,建造了世界上第一台能浇铸5t 钢水的连铸机。
19世纪60年代后,连铸进入稳步发展时期。
70年代以来,连铸生产技术围绕提高连铸生产率,改善铸坯质量,降低连铸能耗这几个中心课题,已经有了长足的发展。
80年代连铸技术的进步,主要表现在对铸坯质量设计和质量控制方面到一个新的水平,已逐步实现连铸坯热送和直接轧制,由于这一新工艺能够大幅度地降低能耗,缩短生产周期,因而已成为目前连铸发展的主要方向。
1.1.2 连续铸钢生产工艺在国内的发展情况中国是世界上开发和应用连铸技术较早的国家之一,上世纪50年代就进行过连铸方面的试验研究。
进入20世界80年代末和90年代以来,宝山钢铁公司和鞍山钢铁公司分别在1989年和1990年投产了从日本引进的大型双流板坯连铸机。
国家对发展连铸技术一直予以高度重视,大力发展连铸生产和建设成为我国钢铁技术发展的重要政策。
1.2连续铸钢生产工艺1.2.1 连续铸钢生产工艺简介连续铸钢与普通模铸不同,它不是把高温钢水浇铸在一个个钢锭模内,而是将高温高水连续不断地浇铸到一个或一组实行强制水冷带有:“活底”的铜模内。
待钢水凝固到具有一定厚度的坯壳后,则从铜模的另一端拉出“活底”,这样铸钢坯就会连续从铜模下口被拉出来。
这种使高温钢水直接浇铸成钢坯的新工艺,就是连续铸钢。
它完全改变了在钢铁生产中一直占统治地位的“模铸—开坯”工艺,大大地简化了从钢水到钢坯的生产工艺流程。
1.2.2连续铸钢的工艺流程连续铸钢的一般生产工艺流程,是由炼钢炉炼出来的合格钢水,经盛钢桶运送到浇铸位置,通过中间罐铸入强制水冷的铜模—结晶器内。
连铸技术国内外现状及发展趋势

连铸技术国内外现状及发展趋势
随着钢铁工业的不断发展,连铸技术作为钢铁生产中的重要工艺技术,也在不断发展和改进。
本文旨在探讨连铸技术的国内外现状和发展趋势。
一、连铸技术国内外现状
1. 国内现状
目前我国连铸技术已经成为钢铁生产中的主要工艺技术之一,国内的连铸设备和技术水平也不断提高。
目前,我国铸造模具、连铸机、冷却系统等连铸设备已经实现国产化,并且在连铸技术的研究和应用方面也取得了不少成果。
然而,与国外相比,我国的连铸技术仍然存在一定的差距。
2. 国外现状
国外的连铸技术相对较为成熟,特别是在技术水平和设备精度方面已经达到了相当高的水平。
目前,欧美等发达国家的连铸技术已经开始向高端化、多功能化方向发展,能够适应更加复杂的钢铁材料生产需求。
二、连铸技术的发展趋势
1. 高端化
随着我国钢铁产业的不断发展,钢铁材料的品质和精度要求也越来越高。
因此,连铸技术也需要不断提升,向高端化方向发展。
2. 多功能化
在连铸技术的应用过程中,还需要考虑人工智能、大数据、机器
视觉等技术的应用。
未来,连铸技术将朝着多功能化的方向发展。
3. 绿色化
连铸技术的发展也需要考虑环保和资源节约。
因此,在设备制造和生产过程中,需要更多地考虑环保和资源节约问题,实现连铸技术的绿色化。
综上所述,连铸技术作为钢铁生产中的重要工艺技术,其国内外现状和发展趋势也在不断变化。
随着技术的不断提升和应用范围的扩大,连铸技术有望在未来实现更加高端化、多功能化和绿色化的发展。
铝带连续铸轧工艺的现状及研究进展

铝带连续铸轧工艺的现状及研究进展高性能铝板带材广泛用于航天、交通运输、信息、包装、印刷、建筑等领域,市场需求巨大.铝板带材坯料主要生产方式为热轧和连续铸轧<1> .热轧产品深加工性能好,可轧制各系铝合金,其最先进的方式是热连轧,但投资巨大,我国尚无铝热连轧生产线,已有的最好的生产方式为双机架热轧,在产品精度、性能上均有一定局限.相比热轧,连续铸轧投资大幅减少,流程短、能耗低.二十世纪八十年代以来在我国迅速发展,成为我国主要的铝板带材坯料生产方式.但是常规铸轧板组织不均匀、深加工性能差,可铸轧的合金品种少,主要用于铝箔毛料和对深加工性能要求不高的部分薄板.我国高性能铝板带材仍需大量进口.1 连续铸轧工艺所面临的关键问题铝带坯连续铸轧是一种低投入、低成本、节能型的短流程生产工艺,其铸轧区的熔体受到激烈的冷却,冷却速度可达10 2~1 0 3℃s,比常规水冷半连续铸锭约高2个数量级<1> .它的组织具有快速凝固与定向结晶的特点,晶体生长的方向性很强.目前用这种方法生产的铝板带各向异性严重,深加工性能远比热轧板差,这就限制了铸轧板的使用范围.连续铸轧是一个很复杂的过程,金属一方面连续散热与凝固,另一方面还受到轧制,而不是铸造过程与热轧过程的简单混合,它们互相影响着.在连续铸轧过程中金属凝固涉及到的学科有材料学、热力学、动力学、振动理论、流体理论、晶体生长理论等问题.它们涉及到两个重大科学问题:(1)铝在连续轧制过程中的凝固规律;(2 )金属凝固过程中的晶体生长与控制.金属凝固过程主要由两部分组成,一是形核过程,它对金属材料晶粒的大小起着至关重要的作用.受金属熔体结构复杂性以及人们对其认识程度的限制,形核理论与控制形核过程的手段还没有达到人们所想象的程度,故金属凝固中的形核问题仍然是金属凝固行为研究的前沿课题之一.金属凝固过程中另一个重要问题是形核后的晶体生长,它关系到凝固后金属组织组成物的形态.由于组成金属材料的晶体形态直接与金属材料的性能有关,如何控制晶体生长,已经成为控制金属材料性能的一个重要手段<2> .因此研究在铸轧过程中铝溶液的晶体凝固规律,对提高铝带材的组织性能与机械性能都具有非常重要的意义.铝带坯连铸技术作为冶金及材料研究领域内的一项前沿技术,目前在工业化应用方面面临的一个主要间题是薄带的质量较差和质量不稳定.其中,薄带的凝固组织对薄带的质量有非常重要的影响,但目前国内外还不能定量阐明工艺因素变化对薄带凝固组织的影响.由于双辊薄带连铸过程中工艺参数间的匹配较复杂,如果采用实验的方法来研究工艺因素变化对薄带凝固组织的影响,则难度高、工作量大.而采用数值模拟的办法,则可以大幅度减少工作量.此外,双辊薄带的凝固组织结构(晶区的几何特征)以及不同晶区内晶粒的几何特征还在很大程度上决定着薄带的工艺性能和使用性能.因此,对双辊薄带凝固组织的数值模拟和薄带凝固组织中各晶区的分布特征、晶区内晶粒几何特征的尺寸表征展开研究具有重要的理论意义和实用意义.2国内外研究现状195 1年,美国亨特—道格拉斯(Hunter-Douglas)公司首次铸轧成了铝带坯,制成了双辊式连续铸轧机.随后,法国彼西涅(Pechiney)公司研制的3C水平式双辊铸轧机也获得成功,从那以后,铝带坯双辊连续铸轧技术和设备得到了迅速的发展.根据Frishchknecht和Maiwald统计目前世界上约有20 %的铝带材的坯料由双辊连续铸轧法生产,大约有1 70多台双辊铸轧机正在工业上应用,其中约有60 %是在北美和欧洲<3> .在2 0世纪70年代以前,铸轧机多为标准型,铸轧辊直径为Φ60 0~70 0mm ,铸轧带坯厚度7mm 左右,铸轧速度小于1 .5m min .80年代以后出现了超型铸轧机,铸轧辊直径可达1 0 0 0mm ,带坯厚度5~1 2mm ,铸轧速度3m min左右,铸轧合金已有纯铝扩大到3 0 0 0系列、5 0 0 0系列软合金.90年代初出现了改进型超型铸轧机,铸轧带坯厚度3mm ,铸轧速度5mm min .由于铸轧带坯尺寸薄和铸轧速度快能进一步发挥快速凝固的特点,使铸轧带坯的晶粒细化,从而获得更好的冶金质量,使这一生产方式为人类带来更大的效益.从90年代以来,国际上开展了对快速超薄铸轧技术的研究<4~6> ,主要有意大利的法塔—亨特(Fata-Hunter)公司、法国的彼西涅(Pechiney )公司、英国的戴维(Davy)公司以及挪威的海德洛(Hydro)公司,他们共同的做法是先在研究开发中心与大学合作进行小型试验,在取得一定成果和经验后,进行中试和大型工业试验,英国Davy公司和牛津(Oxford)大学合作,于1991年推出了第一台快速超薄铝带坯铸轧试验机.1 996年以来,意大利Fata -Hunter 公司、英国Davy公司以及法国Pechiney公司都相继研制出超薄铸轧工业样机<7> ,能铸轧出1mm厚的铸带坯,铸轧速度达1 5m min ,应该说,这是铸轧技术发展中的又一次飞跃.但是由于各国(美国、英国、法国、意大利、挪威) 对快速超薄技术的研究均处于工业试验阶段,试验条件(如装备参数、功能、工艺环境条件等)各不相同,所得结果也有差别,甚至相反,如:Fata-Hunter的试验与Hydro-Lauener公司的试验,对快速超薄铸轧的组织与性能的认识与结果几乎完全相反;在快速超薄铸轧的铸轧机型选择上也存在不同的主张:如Fata-Hunter 采用二辊铸轧机型,英国Davy公司则采用四辊铸轧机型,同时各试验铸轧机的工艺环境条件、设备参数及其范围的确定也不一致(力学参数、辊径、有无外部冷却、铸轧区长度、大小、铸咀开口度大小等).在主要技术规律上尚未形成共识.我国铝带坯连续铸轧技术研究开发工作始于2 0世纪60年代<16 > ,1 964年初进行了双辊下注式铝带坯连续铸轧模拟实验,并于同年铸轧出厚8mm ,宽 2 5 0mm和40 0mm的铝板,1 965年铸轧出宽70 0mm的铝带坯,1 971年由东北轻合金加工厂研制成我国第一台80 0mm水平式下注式双辊铸轧机,1 975年,用铝带坯生产的冷轧板基本上满足了一般深冲制品和箔材毛料的性能要求.1 979年由华北铝加工厂研制成65 0mm×1 3 0 0mm我国第一台亨特式倾斜铸轧机,并于1 981年和1 983年相继研制成65 0mm×1 60 0mm和980mm×1 60 0mm 铸轧机,并通过部级鉴定,标志着我国铸轧技术进入成熟阶段.1 984年中日诼神有色金属加工专用设备有限公司成立,并于1 993年诼神公司为其母公司华北铝业有限公司试制成功我国第一台仿3C 960mm×1 5 5 0mm超型铸轧机.至此国产铸轧机发展成为具有标准型和超型这两种机型,而且铸轧机逐步实现标准化、系列化.随着我国微电子、信息、机械、食品、包装、建筑产业的迅猛发展,我国已成为铝材生产及消费大国,如何提高铝材生产率、降低生产成本、提高我国铝材质量、扩大铝材使用范围已成为迫在眉睫的问题.而快速超薄铸轧的冷却速度远高于现有常规铸轧,铸坯结晶组织的晶粒度和枝晶间距将明显减少,溶质元素在固熔体中的过饱和度提高,因此板带的深冲性能和机械性能得到改善,可生产出具有优良冶金组织和表面质量的优质板带材;同时,可铸轧合金范围也可拓展(如30 0 0系列等铝合金) ,可使铸轧产品的应用市场范围扩大.例如:高精度PS版基,计算机硬盘的铝质基板,高层建筑幕墙板,高精烟箔以及空调箔等.另外,由于铸轧板厚度减薄后,不仅大大减轻了对后面工序———冷轧的压力,解放冷轧机的生产力,大大节省了铝箔生产的投资和能源,而且提高了生产效率,增加了产品的市场竞争力.我国科技界和国际铝加工同行一样已认识到快速超薄铸轧代表了新一代铝加工发展的重要方向和铝加工技术的制高点,我国必须加入到这一研究领域中去.由国内学者钟掘院士担纲技术指导的“铝及铝合金铸轧新技术及设备研制开发”作为国家计委的重大科研项目于1999年初启动,经过以钟掘为首的科研课题组经过一年多的攻关,于2 0 0 0年7月在实验机上成功地铸轧出铸速为1 3 .2m min ,厚度为2mm的铸坯,并开发了铜基合金新型辊套材料、具有在线布流控制技术的新型铸咀、新型复合外冷润滑技术等一系列相关的新技术、新装置、新材料,这些都标志着我国在快速超薄铸轧技术领域已经达到世界领先水平,填补了国内空白.目前用连续铸轧法生产的铝板带在国内已占铝板带生产总量的70% ,在国际上约占铝板带生产总量的40 %左右<7> .国内的连续铸轧设备已由十多年前的3 0多台套,增至目前的5 0多台套.但是,常规的连续铸轧生产工艺目前还只局限于1 系列和3 系列、8 系列的一部分,连续铸轧板带的深拉性能明显地低于热轧开坯板带.这是目前连续铸轧生产工艺必须解决的技术难题.显然,能突破这一难题,将使铝带坯的生产结构发生根本型变化,带来巨大的社会效益与经济效益.对金属凝固规律,国内外都已进行了比较多的研究,如50年代初Tiller,Jackson和Rutter提出的成分过冷理论<8> ,首次将传质和传热因素耦合起来分析凝固过程的组织形态问题,以后发展起来的理论有Jacks on和Hunt提出的枝晶和共晶合金凝固过程扩散场的理论解,Flemings提出局部溶质再分配方程等理论模型,这些理论为控制金属组织奠定了基础,20世纪60年代以来形成了快速凝固技术、定向凝固技术、半固态铸造等先进铸造工艺和技术<9> .3国内开展相关研究的基础与条件据统计,我国现有的铝带坯连续铸轧生产线已超过1 1 0条,总生产能力超过90万吨/年.其中有引进的生产线1 2条,合计生产铝箔毛料质量的重要性和技术标准要求铝箔毛料质量的重要性和技术标准要求Technology Standard and Qualitative Importance of Aluminium Foil Stock黄金法张学平HUANG Jin-fa ZHANG Xue-ping(兰州铝业股份有限公司西北铝业加工有限公司,甘肃陇西748111)摘要:从四个方面阐述铝箔毛料质量对生产高质量铝箔的重要性;指出了在订购铝箔毛料时应提出的技术要求内容。
特殊钢连铸技术的发展及关键技术研究

结晶器液面自动控制 结晶器自动加渣 结晶器漏钢预报 结晶器振动在线检测
3、特殊钢连铸关键技术
3.1 全程保护浇注
全程保护浇注:连铸过程中 为避免钢水二次氧化而采取的 保护措施。钢水运行轨迹为:
钢包-中间包-结晶器 具体环节包括:
——大包液面的保护 —— 大包至中包间注流的保护: —— 中包液面的保护 —— 中包至结晶器间注流的保护 —— 结晶器液面的保护 全程保护浇注示意图
连铸技术优化发展阶段(1980~至今)
主要技术包括: 间包冶金技术 结晶器冶金技术(流动控制、空心保护渣) 结晶器热流成像及漏钢预报 非正弦振动技术 连铸机辊列设计技术(液芯压下、末端压下) 现代电磁技术应用(电磁制动、电磁搅拌) 无缺陷铸坯生产技术等。
1.2 特殊钢模铸与连铸生产流程的比较
—— 能源消耗解析
省去了脱模、整模、钢锭均热、初轧开坯等 工序。由此可节省基建投资费用约40%,减少占地 面积约30%,劳动力节省约70%。
提高了金属收得率 采用模铸工艺,从钢水到钢坯,金属收得率 为84-88%,而连铸工艺则为95-96%,金属收得率 提高10-14%。
—— 连续铸钢的优越性
降低了能源消耗
采用连铸工艺比传统工艺可节能1/4-1/2。
装备; 科技前沿:航空航天、核能、海洋开发。
国内现状及存在的问题
发展现状:生产装备进步,产能大国,总体技术水平相对落后。 主要问题:
—— —— —— —— ——
产品结构不合理,高端品种不足; 工艺技术差距明显,产品质量欠稳定; 资源和能源消耗高,制约可持续发展; 产业集中度与专业化程度低,缺少规模经济效益 基础研究薄弱,共性关键技术自主研发能力不足
铝带连铸连轧生产线精炼铸造工艺的改进措施
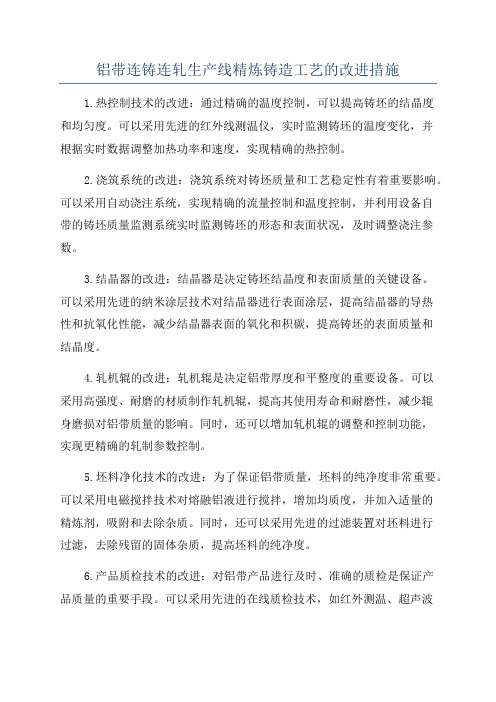
铝带连铸连轧生产线精炼铸造工艺的改进措施1.热控制技术的改进:通过精确的温度控制,可以提高铸坯的结晶度和均匀度。
可以采用先进的红外线测温仪,实时监测铸坯的温度变化,并根据实时数据调整加热功率和速度,实现精确的热控制。
2.浇筑系统的改进:浇筑系统对铸坯质量和工艺稳定性有着重要影响。
可以采用自动浇注系统,实现精确的流量控制和温度控制,并利用设备自带的铸坯质量监测系统实时监测铸坯的形态和表面状况,及时调整浇注参数。
3.结晶器的改进:结晶器是决定铸坯结晶度和表面质量的关键设备。
可以采用先进的纳米涂层技术对结晶器进行表面涂层,提高结晶器的导热性和抗氧化性能,减少结晶器表面的氧化和积碳,提高铸坯的表面质量和结晶度。
4.轧机辊的改进:轧机辊是决定铝带厚度和平整度的重要设备。
可以采用高强度、耐磨的材质制作轧机辊,提高其使用寿命和耐磨性,减少辊身磨损对铝带质量的影响。
同时,还可以增加轧机辊的调整和控制功能,实现更精确的轧制参数控制。
5.坯料净化技术的改进:为了保证铝带质量,坯料的纯净度非常重要。
可以采用电磁搅拌技术对熔融铝液进行搅拌,增加均质度,并加入适量的精炼剂,吸附和去除杂质。
同时,还可以采用先进的过滤装置对坯料进行过滤,去除残留的固体杂质,提高坯料的纯净度。
6.产品质检技术的改进:对铝带产品进行及时、准确的质检是保证产品质量的重要手段。
可以采用先进的在线质检技术,如红外测温、超声波检测等,实时监测铝带的温度、厚度和表面状况。
同时,还可以建立完善的质检标准和操作规程,并进行人员培训,提高质检人员的专业水平。
通过以上改进措施,可以进一步提高铝带连铸连轧生产线的精炼、铸造工艺,实现更高的生产效率和产品质量。
同时,还可以减少能源消耗,降低生产成本,为企业创造更大的经济效益。
连铸连轧生产工艺
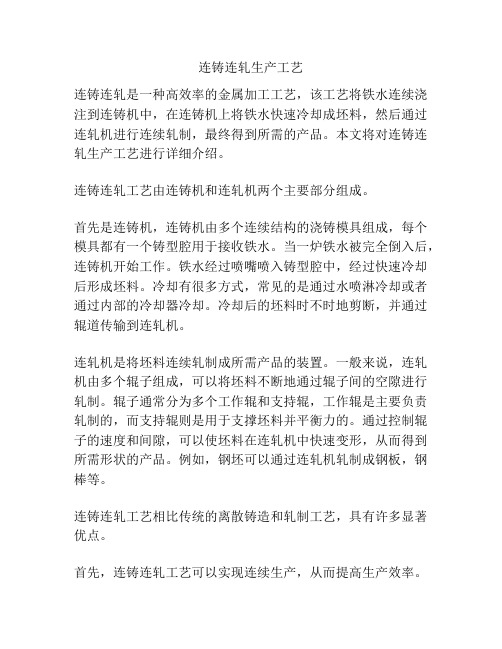
连铸连轧生产工艺连铸连轧是一种高效率的金属加工工艺,该工艺将铁水连续浇注到连铸机中,在连铸机上将铁水快速冷却成坯料,然后通过连轧机进行连续轧制,最终得到所需的产品。
本文将对连铸连轧生产工艺进行详细介绍。
连铸连轧工艺由连铸机和连轧机两个主要部分组成。
首先是连铸机,连铸机由多个连续结构的浇铸模具组成,每个模具都有一个铸型腔用于接收铁水。
当一炉铁水被完全倒入后,连铸机开始工作。
铁水经过喷嘴喷入铸型腔中,经过快速冷却后形成坯料。
冷却有很多方式,常见的是通过水喷淋冷却或者通过内部的冷却器冷却。
冷却后的坯料时不时地剪断,并通过辊道传输到连轧机。
连轧机是将坯料连续轧制成所需产品的装置。
一般来说,连轧机由多个辊子组成,可以将坯料不断地通过辊子间的空隙进行轧制。
辊子通常分为多个工作辊和支持辊,工作辊是主要负责轧制的,而支持辊则是用于支撑坯料并平衡力的。
通过控制辊子的速度和间隙,可以使坯料在连轧机中快速变形,从而得到所需形状的产品。
例如,钢坯可以通过连轧机轧制成钢板,钢棒等。
连铸连轧工艺相比传统的离散铸造和轧制工艺,具有许多显著优点。
首先,连铸连轧工艺可以实现连续生产,从而提高生产效率。
相比离散铸造和轧制工艺,连铸连轧工艺减少了产品在生产过程中的停留时间,有效减少生产周期,提高了生产效率。
其次,连铸连轧工艺可以减少产品的变形和出现缺陷的可能性。
在连铸连轧过程中,坯料的变形是在连续产生的,产品形状相对稳定,因此可以减少变形和出现缺陷的可能性。
同时,由于坯料在连轧过程中受到很大压力的作用,使其内部结构更加紧密,提高了产品的强度和硬度。
最后,连铸连轧工艺还可以减少能耗并降低生产成本。
连续生产可以减少能耗浪费,同时由于工艺参数的控制更加精准,可以减少废品率,降低了生产成本。
总之,连铸连轧是一种高效率的金属加工工艺,通过连续的铸造和轧制过程,可以快速地生产出所需的产品。
其优点包括高生产效率,减少变形和缺陷的可能性,降低能耗和生产成本等。
2024年连铸坯市场分析现状

2024年连铸坯市场分析现状1. 引言连铸坯是指通过连铸工艺从铁水中直接浇铸而成的钢坯,它具有高品质、高效率等优势,在钢铁行业中得到了广泛应用。
本文将对当前连铸坯市场进行分析,探讨其现状。
2. 连铸坯市场概况近年来,全球钢铁行业发展迅猛,推动了连铸坯市场的增长。
据统计数据显示,全球连铸坯产量逐年增加,市场规模不断扩大。
中国作为世界上最大的钢铁生产国,其连铸坯产量在全球市场占据较大份额。
3. 连铸坯市场竞争态势目前,全球连铸坯市场竞争激烈,主要集中在少数大型钢铁企业之间。
这些企业拥有先进的连铸设备和技术,可以实现高效、高质量的生产。
随着市场竞争的加剧,企业之间不仅在价格上竞争,还在产品质量、交货时间等方面展开竞争,以提升市场份额。
4. 连铸坯市场的发展趋势未来连铸坯市场存在一些发展趋势:4.1 技术进步与创新随着科技的发展,连铸技术不断创新和进步,不仅提高了生产效率,还提升了产品质量。
例如,电磁搅拌技术的应用,在连铸过程中可以有效消除浮渣,提高坯料质量。
4.2 环保要求的提高全球对环境问题的关注度不断提高,连铸坯市场也不例外。
未来,环保要求将成为连铸坯市场发展的重要动力。
企业需要加强环保意识,改进生产工艺,减少污染排放,提升可持续发展能力。
4.3 市场结构调整连铸坯市场结构将进一步调整。
随着市场竞争的加剧,一些低效益的小型铸造企业可能面临淘汰。
同时,一些中型和大型企业将通过并购、兼并等方式扩大规模,提高市场集中度。
5. 连铸坯市场的挑战连铸坯市场面临一些挑战:5.1 市场需求波动全球经济形势的不稳定性,可能导致连铸坯市场需求波动。
市场需求的不确定性将对企业的生产计划和投资决策产生一定影响。
5.2 原材料价格波动连铸坯的主要原材料是铁矿石和煤炭,而这两种原材料价格波动较大。
原材料价格的不确定性使得企业难以进行准确的成本控制,增加了市场不确定性。
6. 总结连铸坯市场作为钢铁行业的关键环节之一,其发展形势和市场竞争态势对于行业发展至关重要。
高效连铸和近终型连铸生产技术
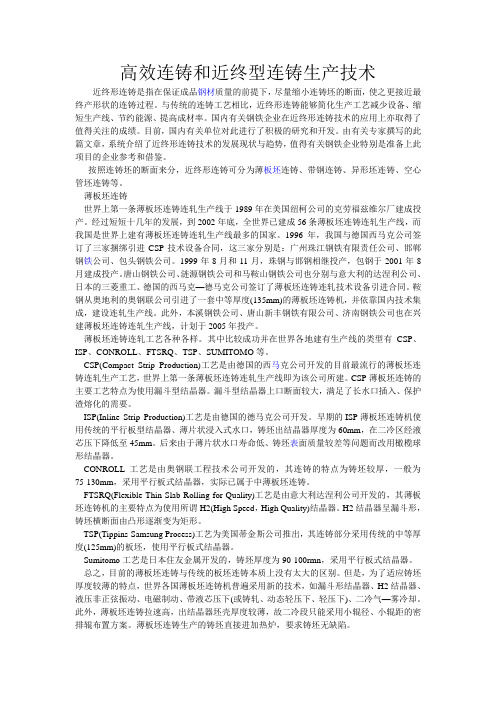
高效连铸和近终型连铸生产技术近终形连铸是指在保证成品钢材质量的前提下,尽量缩小连铸坯的断面,使之更接近最终产形状的连铸过程。
与传统的连铸工艺相比,近终形连铸能够简化生产工艺减少设备、缩短生产线、节约能源、提高成材率。
国内有关钢铁企业在近终形连铸技术的应用上亦取得了值得关注的成绩。
目前,国内有关单位对此进行了积极的研究和开发。
由有关专家撰写的此篇文章,系统介绍了近终形连铸技术的发展现状与趋势,值得有关钢铁企业特别是准备上此项目的企业参考和借鉴。
按照连铸坯的断面来分,近终形连铸可分为薄板坯连铸、带钢连铸、异形坯连铸、空心管坯连铸等。
薄板坯连铸世界上第一条薄板坯连铸连轧生产线于1989年在美国纽柯公司的克劳福兹维尔厂建成投产。
经过短短十几年的发展,到2002年底,全世界已建成56条薄板坯连铸连轧生产线,而我国是世界上建有薄板坯连铸连轧生产线最多的国家。
1996年,我国与德国西马克公司签订了三家捆绑引进CSP技术设备合同,这三家分别是:广州珠江钢铁有限责任公司、邯郸钢铁公司、包头钢铁公司。
1999年8月和11月,珠钢与邯钢相继投产,包钢于2001年8月建成投产。
唐山钢铁公司、涟源钢铁公司和马鞍山钢铁公司也分别与意大利的达涅利公司、日本的三菱重工、德国的西马克—德马克公司签订了薄板坯连铸连轧技术设备引进合同。
鞍钢从奥地利的奥钢联公司引进了一套中等厚度(135mm)的薄板坯连铸机,并依靠国内技术集成,建设连轧生产线。
此外,本溪钢铁公司、唐山新丰钢铁有限公司、济南钢铁公司也在兴建薄板坯连铸连轧生产线,计划于2005年投产。
薄板坯连铸连轧工艺各种各样。
其中比较成功并在世界各地建有生产线的类型有CSP、ISP、CONROLL、FTSRQ、TSP、SUMITOMO等。
CSP(Compact Strip Production)工艺是由德国的西马克公司开发的目前最流行的薄板坯连铸连轧生产工艺,世界上第一条薄板坯连铸连轧生产线即为该公司所建。
连铸技术国内外现状及发展趋势

连铸技术国内外现状及发展趋势
连铸技术是一种现代化的钢铁生产工艺,旨在提高钢铁生产效率与质量。
自上世纪80年代起,连铸技术在全球范围内得到广泛应用,并不断发展。
当前,连铸技术已成为钢铁工业中的主流生产工艺之一。
国内,随着钢铁行业的不断发展,连铸技术也发展壮大。
目前,国内的连铸机数量和产量均居世界前列。
同时,国内企业也在不断引进新的技术和设备,以提高生产效率和质量。
此外,国内的连铸技术也在不断创新,如微量元素控制技术、智能化控制技术等,为生产提供更多的选择。
国外,欧美、日本等工业发达国家一直处于连铸技术的领先地位。
他们在研究和应用连铸技术方面投入巨大,不断创新。
如今,一些新的连铸技术已经应用于生产中,比如脱氧合金化技术、超细化技术等。
同时,在连铸技术的数字化、智能化方面,国外也取得了一定的进展和成果。
这些技术的应用,使得钢铁生产效率和质量得到了进一步提高。
总的来说,连铸技术已经成为了钢铁生产的主流工艺之一,国内外的企业都在不断发展和创新。
未来,随着科技的不断进步和工业的不断发展,连铸技术将会更加完善和智能化,为钢铁生产带来更多的发展机遇。
- 1 -。
连铸技术的现状及发展趋势

连铸技术的现状及发展趋势摘要:随着科学技术的发展,连铸技术的发展也越来越趋向于成熟。
本文主要介绍了连铸技术在国内外的发展现状和趋势,用到电磁冶金、终形连铸、中间包的加热、结晶器液压振动、在线调宽、摩擦力监控和中间包连续测温等技术,在介绍技术的同时,又联系现实的生产状况,分析了它的发展状况。
关键词:连铸技术;现状;发展;趋势一、近终形连铸技术的介绍近终形连铸技术就是一种集连铸、轧制和热处理为一体的可以生产特殊新材料的一种技术,它最大的特点就是快速凝固,这样可以生产出传统轧制工艺无法生产的材料。
连铸技术分为多种,下面介绍薄板坯连铸和薄带连铸技术。
对于薄板坯连铸技术,薄板坯连铸技术早在1989年就开始投产,在美国最先兴起,结合了德国当时最先进的生产技术。
随着时代的发展,薄板坯连铸技术也日渐成熟,早先只有国外公司拥有这种生产技术,现在,中国已经成为薄板坯连铸产能最大、生产线最多的国家。
对于薄带连铸技术,它相对于其它连铸技术更为先进,它属于冶金领域中一项前沿技术。
它又分为前期传统的技术和现代薄带连铸技术,区别于以前它最大的特点就是薄带连铸技术更加综合,它集连铸、轧制和热处理技术为一体,生产的薄带坯更加精细,并且可以一次成型。
现在的连铸技术中最受关注还有就是双辊薄带连铸技术,它广受关注的原因就是此种高效的生产工艺可以提高生产效率,增加高额的经济效益[1]。
双辊薄带连铸这种工艺非常复杂,所以至今没有完全掌握,虽然近些年有些突破性进展,但是,想要达到商业化量产阶段是不可能的,还是需要大量的研究和探索工作。
其中有几大问题,第一就是生产中的裂纹,这是制约此项技术发展的重大原因之一。
第二就是厚度不均匀的问题,现在能实现的厚度就是在小范围内波动,但还是不利于冷轧过程的进行。
第三就是连铸的速度,上面也提到,现在的技术不足,生产成品的速率低下,不能满足商业化需求。
第四就是薄带的宽度小,并且侧封还不理想。
剩下的还有铸辊的材质问题、钢液的氧化问题、二次冷却问题等等。
- 1、下载文档前请自行甄别文档内容的完整性,平台不提供额外的编辑、内容补充、找答案等附加服务。
- 2、"仅部分预览"的文档,不可在线预览部分如存在完整性等问题,可反馈申请退款(可完整预览的文档不适用该条件!)。
- 3、如文档侵犯您的权益,请联系客服反馈,我们会尽快为您处理(人工客服工作时间:9:00-18:30)。
连铸生产工艺的发展
近年来,我国经济的快速增长,特别是工业和基本建设的加速,促进了钢铁工业的发展。
我国已成为世界上钢铁消费和钢铁生产大国,粗钢产量和消费量占世界总量的比例分别由1992年的11.2%和11.9%跃升到2002年的20.1%和25.8%,2002年钢产量达到1.82亿t。
由于连铸技术具有显著的高生产效率、高成材率、高质量和低成本的优点,近二三十年已得到了迅速发展,目前世界上大多数产钢国家的连铸比超过90%。
连铸技术对钢铁工业生产流程的变革、产品质量的提高和结构优化等方面起了革命性的作用。
我国自1996年成为世界第一产钢大国以来,连铸比逐年增加,2003年上半年连铸比已经达到了94.65%。
连铸即为连续铸钢(英文,Continuous Steel Casting)的简称。
在钢铁厂生产各类钢铁产品过程中,使用钢水凝固成型有两种方法:传统的模铸法和连续铸钢法。
而在二十世纪五十年代在欧美国家出现的连铸技术是一项把钢水直接浇注成形的先进技术。
与传统方法相比,连铸技术具有大幅提高金属收得率和铸坯质量,节约能源等显著优势。
从上世纪八十年代,连铸技术作为主导技术逐步完善,并在世界各地主要产钢国得到大幅应用,到了上世纪九十年代初,世界各主要产钢国已经实现了90%以上的连铸比。
中国则在改革开放后才真正开始了对国外连铸技术的消化和移植;到九十年代初中国的连铸比仅为30%。
连续铸钢的具体流程为:钢水不断地通过水冷结晶器,凝成硬壳后从结晶器下方出口连续拉出,经喷水冷却,全部凝固后切成坯料的铸造工艺过程。
统计数字显示,2002年我国连铸比为93.7%,2003年上半年全国连铸比达到94.65%,已超过了世界8970%平均连铸比的水平;我国连铸比已达到发达国家的水平,连铸比将要达到饱和状态。
全球已建成54流连铸-连轧生产线,年生产能力为5500万t;我国已建和在建13流生产线,年生产能力达到1400万t(见表2),占全球总产量的1/4;中国CSP钢产量(1050万t)与美国CSP产量(1000万t)相当。
提高连铸机拉速连铸机拉速的提高受出结晶器坯壳厚度、液相穴长度(冶金长度)、二次冷却强度等因素的限制。
要针对连铸机的不同情况,对连铸机进行高效化改造。
小方坯连铸机高效化改造的核心就是提高拉速。
拉速提高后,
为了保证出结晶器坯壳不漏钢,其核心技术就是优化结晶器锥度,开发新型结晶器,包括:Concast的凸模结晶器(CONVEX MOLD);Danieli自适应结晶器(DANAM);V AI的钻石结晶器(DIAMOLD);Paul Wurth的多锥度结晶器。
虽然结晶器名称不相同,但其实质就是使结晶器锥度与坯壳收缩相一致,不致于产生气隙而减慢传热,影响坯壳均匀性生长。
小方坯铸机拉速的提高,表现为单流产量的提高。
从世界连铸发展的历程来看,20世纪70、80、90年代连铸机的单流年产量分别为5~6、8~10、15~16万t。
我国钢材生产结构是长型材较多,板材比较低(约40%),反映在连铸机建设上是中小型钢厂建设小方坯连铸机较多。
据统计,我国共建小方坯连铸机280台978流,年产量近6000万t,平均单流年产量约为6万t。
与国外比较,连铸机生产率还较低。
为提高连铸机生产率,从20世纪90年代以来,我国对旧有小方坯连铸机进行了高效化改造,如120mm×120mm方坯拉速由2.0m/min提高到3.0~4.0m/min,150mm×150mm方坯拉速由1.5m/min提高到2.5~3.0m/min。
目前,我国不少钢厂的小方坯连铸机经过高效化改造后,单流年产量已达到15~20万t的国际水平。
板坯连铸机拉速的水平目前板坯厚度为200~250mm的拉速在 1.6~2.0m/min左右,单流年产量达到200万t。
如果说提高拉速是小方坯连铸机高效化的核心,那么板坯连铸机高效化的核心就是提高连铸机作业率。
这是因为板坯连铸机的拉速受炉机匹配条件及铸机本身冶金长度的限制不可能有较大的变化,以及由于过高拉速所造成的漏钢危害,对板坯连铸机的影响远远高于小方坯连铸机。
从原则上讲,连铸机提高拉速措施有:结晶器优化技术;结晶器液面波动检测控制技术;结晶器振动技术;结晶器保护渣技术;铸坯出结晶器后的支掌技术;二冷强化冷却技术;铸坯矫直技术;过程自动化控制技术。
拉速提高了,铸坯内部疏松、偏析缺陷加重,夹杂物增加。
高拉速与高质量是相互矛盾的,因此应根据钢种和产品用途,采取相应的技术措施,把高拉速和高质量的矛盾统一起来,以获得最佳经济效益。
国外有不少钢厂板坯连铸机拉速不高,而单流产量却很高,如美国A.K.Ashland钢厂的板坯铸机,浇240mm×1160~1750mm板坯,工作拉速为1.78m/min,单流年产量达到220万t,连铸机有钢作业率为98%。
这说明对板坯连铸机高效化改造核心不是提高拉速,而是要设法提高铸机作业率以提高
连铸机的生产率。
提高连铸机作业率的技术有:
(1)长时间浇注多炉连浇技术:异钢种多炉连浇;快速更换长水口;在线调宽;结晶器在线快速调厚度(只需25~30min);在线更换结晶器(小方坯);中间包热循环使用技术;防止浸入式水口堵塞技术。
(2)长时间浇注连铸机设备长寿命技术:长寿命结晶器,每次镀层的浇钢量为20~30万t;长寿命的扇形段,上部扇形段每次维修的浇钢量100万t,下部扇形段每次维修的浇钢量300~400万t。
(3)防漏钢的稳定化操作技术:结晶器防漏钢预报系统;结晶器漏钢报警系统;结晶器热状态运行检测系统。
(4)缩短非浇注时间维护操作技术:上装引锭杆;扇形段自动调宽和调厚技术;铸机设备的快速更换技术;采用各种自动检测装置;连铸机设备自动控制水平。
提高板坯连铸机设备坚固性、可靠性和自动化水平,达到长时间的无故障在线作业,是提高板坯连铸机作业率水平的关键。
连铸坯的质量概念包括:铸坯洁净度(钢中非金属夹杂物数量,类型,尺寸,分布,形态);铸坯表面缺陷(纵裂纹,横裂纹,星形裂纹,夹渣);铸坯内部缺陷(中间裂纹,角部裂纹,中心线裂纹,疏松,缩孔,偏析)。
连铸坯质量控制战略是:铸坯洁净度决定于钢水进入结晶器之前的各工序;铸坯表面质量决定于钢水在结晶器的凝固过程;铸坯内部质量决定于钢水在二冷区的凝固过程。
提高铸坯表面质量的控制技术铸坯表面质量好坏是热送热装和直接轧制的前提条件。
铸坯表面缺陷的产生主要决定于钢水在结晶器的凝固过程。
要清除铸坯表面缺陷,应采用以下技术:结晶器钢液面稳定性控制;结晶器振动技术;结晶器内凝固坯壳生长均匀性控制技术;结晶器钢液流动状况合理控制技术;结晶器保护渣技术。
提高连铸坯内部质量的控制技术连铸坯内部缺陷一般情况在轧制时能焊合消除,但严重时会使中厚板力学性能恶化,使管线钢氢脆和高碳硬线脆断。
铸坯内部缺陷的产生主要决定带液芯的铸坯在二冷区的凝固过程。
要消除铸坯内部缺陷,可采用以下技术措施:低温浇注技术;铸坯均匀冷却技术;防止铸坯鼓肚变形技术;轻压下技术;电磁搅拌技术;凝固末端强冷技术;多点或连续矫直技术;压缩铸造技术。
综上所说我们可以得出结论:
(1)我国连铸比已超过世界平均水平,接近工业发达国家水平,连铸比可以说接近饱和状态。
(2)我国小方坯连铸机高效化改造取得很大成绩。
小方坯连铸机单流产量已达到国际先进水平。
但我国连铸机平均作业率与世界连铸机平均水平还存在较大差距。
提高连铸机作业率以增加连铸机产量还有较大发展潜力。
(3)经过近10多年来的努力,我国连铸在高效化改造、新技术的应用等方面取得了很大成就,就大中型企业连铸机装备水平来看已与国外钢厂水平相当。
要重视工艺软件技术开发与创新,新技术要用出实效来。
(4)要依靠传统的板坯和大方坯连铸机来生产和解决高品质、高附加值的连铸坯质量问题。
薄板坯连铸连轧技术已引入大中型企业,我国薄板坯连铸/连轧生产已跨入世界先进行列,它对改变我国钢材产品结构,提高板带比,改变热轧带卷的市场竞争力起重大的变革作用。
(5)在今后2~3年内,要密切注意薄带连铸领域取得的进展。