产品设计与开发技术
产品开发丶工艺设计和技术选择

产品开发丶工艺设计和技术选择产品开发、工艺设计和技术选择是产品设计过程中不可或缺的环节。
在这个阶段,设计团队需要综合考虑市场需求、技术可行性、成本控制等因素,确定最终的产品形态和生产方式。
本文将从三个方面详细介绍产品开发、工艺设计和技术选择的重要性以及关键考虑因素。
首先,产品开发是指将创意和概念转化为实际产品的过程。
在这个过程中,设计团队需要确定产品的功能、外观设计、材料选择等,以满足市场需求和用户体验。
一个成功的产品开发过程不仅需要理解市场需求,还需要充分考虑技术可行性。
例如,如果产品需要具备特定的制造工艺,设计团队需要确保该工艺可行,并且能够满足产品的功能和质量要求。
其次,工艺设计是指确定产品制造过程中所采用的工艺和方法。
根据产品的不同特性和要求,设计团队需要选择适合的工艺来生产产品。
例如,对于复杂形状的产品,可能需要使用精密加工技术;而对于大批量生产的产品,可能需要采用自动化生产线进行生产。
工艺设计的目标是实现高效、稳定的生产过程,以确保产品的质量和效率。
最后,技术选择是指在产品开发和工艺设计过程中选择合适的技术方案和工具。
技术选择的目标是根据产品的需求和制造过程的特点,选择出最适合的技术来实现产品的设计和生产。
例如,在产品设计中,可以使用CAD软件进行三维建模和分析;在工艺设计中,可以使用模拟软件进行生产过程的模拟和优化。
技术选择的合理性和可行性对于产品的成功开发和生产至关重要。
在进行产品开发、工艺设计和技术选择时,设计团队需要考虑一系列因素。
首先是市场需求和用户体验,设计团队需要了解市场的需求和趋势,以确定产品形态和功能特点。
其次是技术可行性,设计团队需要评估所选技术的可行性和可靠性,以确保产品的质量和稳定性。
另外,成本控制也是一个重要的考虑因素,设计团队需要在保证产品质量的前提下,尽可能降低生产成本。
综上所述,产品开发、工艺设计和技术选择是产品设计过程中不可或缺的环节。
这三个方面的合理选择和考虑将直接影响产品的质量、效率和市场竞争力。
产品设计和开发的技术和策略
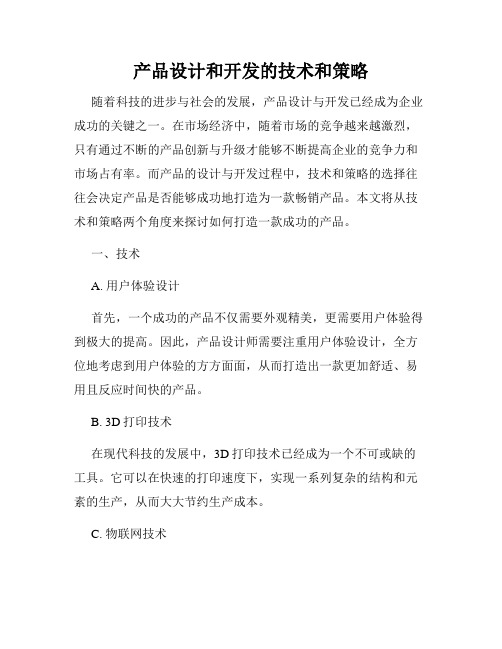
产品设计和开发的技术和策略随着科技的进步与社会的发展,产品设计与开发已经成为企业成功的关键之一。
在市场经济中,随着市场的竞争越来越激烈,只有通过不断的产品创新与升级才能够不断提高企业的竞争力和市场占有率。
而产品的设计与开发过程中,技术和策略的选择往往会决定产品是否能够成功地打造为一款畅销产品。
本文将从技术和策略两个角度来探讨如何打造一款成功的产品。
一、技术A. 用户体验设计首先,一个成功的产品不仅需要外观精美,更需要用户体验得到极大的提高。
因此,产品设计师需要注重用户体验设计,全方位地考虑到用户体验的方方面面,从而打造出一款更加舒适、易用且反应时间快的产品。
B. 3D打印技术在现代科技的发展中,3D打印技术已经成为一个不可或缺的工具。
它可以在快速的打印速度下,实现一系列复杂的结构和元素的生产,从而大大节约生产成本。
C. 物联网技术物联网技术也是一个热门的技术领域,随着智能化逐渐普及,物联网技术也得到了广泛应用,其可以实现设备之间的互联,提高生产效率,降低人工成本,从而更加珍视资源并且提高了企业的可持续发展性。
二、策略A. 用户需求策略一个产品必须要大量的考虑用户需求。
因此,通过市场分析和市场调研,产品设计师才能够了解到哪些产品符合用户需求,从而制定产品开发计划和最终设计方案。
同时,也应该花费大量时间和精力在产品创新方面,一旦产品升级成功,就可以更好地满足用户的需求且扩大市场占有率。
B. 话题互动策略话题互动是一个非常好的策略,通过在社交媒体等平台上与消费者进行互动交流,不仅可以更好地了解产品的优缺点,而且可以进行产品升级的改善及后续服务优化方案的设置,同时也可以对于竞争者有更明确的洞察和分析。
C. 品牌管理策略在市场竞争中,品牌管理也是至关重要的一环。
品牌管理需要考虑产品的特点及市场定位,不仅便于吸引更多的客户及扩大产品的影响力,还可以更加清晰地传达企业的理念和产品定位,提高企业在消费者的心中的地位。
产品设计与开发工作总结汇报

产品设计与开发工作总结汇报尊敬的领导和同事们:
我很荣幸能够在这里向大家总结和汇报我们团队在产品设计与开发方面所取得的成就和进展。
在过去的一年里,我们经历了许多挑战,但也取得了许多成功。
以下是我们团队在产品设计与开发方面的总结汇报。
首先,我们团队在产品设计方面取得了一些重要的进展。
我们不仅成功地完成了多个产品的设计,还在设计过程中引入了新的理念和方法。
我们重视用户体验,注重用户需求,并通过不断的用户测试和反馈来不断改进产品设计。
我们还加强了与市场部门和销售团队的沟通,以确保产品设计符合市场需求。
其次,我们团队在产品开发方面也取得了一些重要的成就。
我们采用了敏捷开发的方法,加快了产品开发的速度。
我们还引入了新的技术和工具,提高了产品的质量和稳定性。
我们在开发过程中注重团队合作,提高了工作效率,减少了开发周期。
最后,我们团队在产品设计与开发方面的成绩得到了认可和肯
定。
我们的产品不仅在市场上取得了良好的销售业绩,还得到了用户和客户的好评。
我们的团队也得到了公司领导和同事们的认可和赞扬。
在未来,我们团队将继续努力,不断提高产品设计与开发的水平,为公司的发展做出更大的贡献。
希望我们的努力能够得到大家的支持和帮助。
谢谢大家!
此致。
产品设计与开发团队敬上。
产品设计与开发技术

产品设计与开发技术产品设计与开发技术是指通过科学的方法和技术手段,对产品进行设计与开发的过程。
在当今快速发展的市场竞争中,产品设计与开发技术对于企业的竞争力和发展至关重要。
本文将从产品设计与开发的概述、技术应用和发展趋势三个方面进行论述。
一、产品设计与开发的概述产品设计与开发是指通过科学的方法和技术手段,将市场需求转化为可行的产品概念,并最终完成产品的设计、制造与交付的过程。
在这个过程中,需要涉及到产品的市场调研、市场分析、产品规划、产品设计、原型制作、试产和批量生产等环节。
产品设计与开发技术的核心任务是满足市场需求,提供具有竞争力的产品。
二、产品设计与开发技术的应用1. 市场调研与分析:通过市场调研和分析,了解和掌握目标市场的需求和竞争环境,为产品设计与开发提供信息支持。
2. 产品规划:根据市场需求和市场调研结果,确定产品的定位、特点和应用场景,制定产品的发展策略和目标。
3. 产品设计:通过创新思维和设计方法,将产品的概念转化为具体的设计方案,包括产品的外观设计、结构设计、功能设计等。
4. 原型制作:通过快速成型技术,制作产品的实物样品,验证产品的设计思路和可行性。
5. 试产和批量生产:在原型验证通过后,进行试产和批量生产,保证产品的质量和交付期。
6. 产品测试和改进:对产品进行各项测试,提供数据支持和改进方向,确保产品的可靠性和性能。
三、产品设计与开发技术的发展趋势1. 智能化:随着人工智能、大数据和物联网等技术的快速发展,产品设计与开发将更加智能化。
通过人工智能技术,可以对市场需求进行更加精准的分析和预测,为产品设计和开发提供更有针对性的解决方案。
2. 可持续发展:在环境保护和资源利用方面的压力越来越大的情况下,产品设计与开发需要注重可持续发展。
通过节能减排和环境友好的设计,减少对环境的影响,提高产品的使用寿命和回收利用率。
3. 创新设计:创新是推动产品设计与开发技术发展的重要动力。
企业需要通过不断创新设计和技术改进,提供差异化的产品和服务,满足不同用户的需求。
先进制造技术下的产品设计与开发
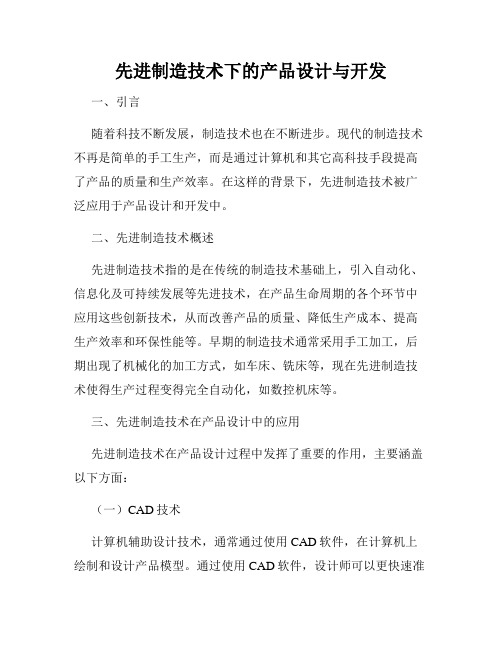
先进制造技术下的产品设计与开发一、引言随着科技不断发展,制造技术也在不断进步。
现代的制造技术不再是简单的手工生产,而是通过计算机和其它高科技手段提高了产品的质量和生产效率。
在这样的背景下,先进制造技术被广泛应用于产品设计和开发中。
二、先进制造技术概述先进制造技术指的是在传统的制造技术基础上,引入自动化、信息化及可持续发展等先进技术,在产品生命周期的各个环节中应用这些创新技术,从而改善产品的质量、降低生产成本、提高生产效率和环保性能等。
早期的制造技术通常采用手工加工,后期出现了机械化的加工方式,如车床、铣床等,现在先进制造技术使得生产过程变得完全自动化,如数控机床等。
三、先进制造技术在产品设计中的应用先进制造技术在产品设计过程中发挥了重要的作用,主要涵盖以下方面:(一)CAD技术计算机辅助设计技术,通常通过使用CAD软件,在计算机上绘制和设计产品模型。
通过使用CAD软件,设计师可以更快速准确地制作产品设计草图、模型和图纸。
这种技术可以提高设计师的工作效率,并减少错误率,确保产品设计质量。
(二)CAM技术计算机辅助制造技术,用于将CAD产品模型转化为CNC控制机床所能识别的G代码。
CAM模块提供了制造设计的自动化,对于复杂曲面的机器雕刻和立体打印等产品制造过程都有很大的帮助。
(三)3D打印技术3D打印技术可以将CAD设计文件快速转换成三维实物。
在产品设计过程中,3D打印技术能够更直观地让设计师看到自己设计出的产品,快速制作出产品的样机检验,减少产品原型的制作周期,从而提高产品开发效率和产品质量。
当然,这种技术的应用受到了一些原材料生产成本的制约,但已经被广泛应用于医疗设备、航空制造、消费品行业。
四、先进制造技术在产品开发中的应用先进制造技术在产品开发过程中的应用是一个循序渐进的过程,主要涵盖以下几个阶段:(一)虚拟原型阶段在虚拟原型阶段,设计师使用CAD、CAM和CAE(计算机辅助工程)等先进技术软件来创建和测试产品的模型和虚拟原型,通过这种方式,可以减少实体原型的制作周期和成本,减少产品设计缺陷,提高产品开发效率。
产品开发设计与生产过程技术介绍

设计评审与优化
总结词
专家评审和反馈意见整合
总结词
持续改进和迭代优化
详细描述
在设计评审阶段,邀请行业专家对产品设计的各个方面进 行评估,提供专业的意见和建议。对评审意见进行整合, 作为优化产品设计的重要参考依据。
详细描述
根据专家评审意见和性能测试结果,对产品设计进行持续 改进和迭代优化。通过不断优化设计,提高产品的竞争力 ,满足市场需求。
制定技术要求
根据竞争产品分析,制定产品的技术要求和性能指标。
编写需求规格书
将产品需求整理成文档,明确产品的各项要求和规格,为后续的 产品开发提供指导和依据。
03
产品设计
概念设计
总结词
初步构思和框架设计
详细描述
概念设计是产品开发流程的起始阶段,主要涉及对产品整 体构思和框架的初步设计。这一阶段需要确定产品的基本 功能、性能参数和外观风格,为后续详细设计提供指导。
01
技术难题
产品更新换代速度快,需要不断进行 技术升级和改造。
03
技术难题
生产过程中出现的技术问题,如设备故障、 工艺不稳定等。
05
02
解决方案
采用先进的研发技术和生产工艺,加强产学 研合作,引进外部专家进行技术指导,提高 技术水平和创新能力。
04
解决方案
建立完善的技术创新体系,加强与供 应商和客户的沟通与合作,及时掌握 市场需求和技术发展趋势。
总结词
创新性和可行性分析
详细描述
在概念设计阶段,设计师需要充分发挥创新思维,提出具 有独特性和吸引力的产品构想。同时,对概念设计的可行 性进行分析,确保产品在技术、经济和制造等方面具备实 现的条件。
总结词
绘制草图和原型制作
技术部产品设计与开发规定
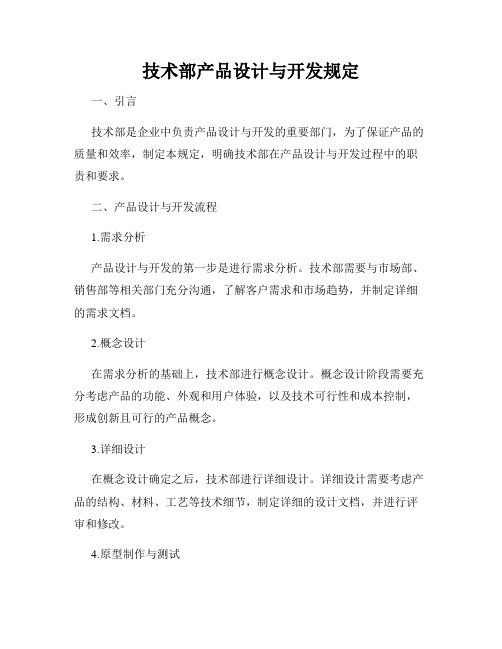
技术部产品设计与开发规定一、引言技术部是企业中负责产品设计与开发的重要部门,为了保证产品的质量和效率,制定本规定,明确技术部在产品设计与开发过程中的职责和要求。
二、产品设计与开发流程1.需求分析产品设计与开发的第一步是进行需求分析。
技术部需要与市场部、销售部等相关部门充分沟通,了解客户需求和市场趋势,并制定详细的需求文档。
2.概念设计在需求分析的基础上,技术部进行概念设计。
概念设计阶段需要充分考虑产品的功能、外观和用户体验,以及技术可行性和成本控制,形成创新且可行的产品概念。
3.详细设计在概念设计确定之后,技术部进行详细设计。
详细设计需要考虑产品的结构、材料、工艺等技术细节,制定详细的设计文档,并进行评审和修改。
4.原型制作与测试根据详细设计文档,技术部制作产品原型,并进行测试。
测试包括功能测试、性能测试、可靠性测试等,以确保产品设计符合需求并达到预期效果。
5.试产与批量生产原型测试通过后,技术部进行试产,并进行小批量生产。
在试产和小批量生产中,需要不断优化产品设计和生产工艺,解决生产过程中的问题,确保产品的质量和产能。
6.持续改进产品设计与开发并非一次性完成,技术部需要对市场反馈进行持续关注和分析,在产品使用过程中发现问题,及时进行改进和优化,提高产品的竞争力和用户满意度。
三、产品设计与开发规范1.需求文档规范需求文档应包括产品功能需求、性能需求、外观需求等,文档应明确、详细、衡量指标可量化,并经过相关部门的审批和确认。
2.设计文档规范设计文档应明确产品结构、材料、工艺等细节,并配以可视化的图纸和模型,以确保设计意图清晰。
3.原型制作与测试规范原型制作需按照设计文档进行,并经过严格的测试和验证,以确保原型符合设计要求和功能需求。
4.试产与批量生产规范试产和批量生产过程中,应建立完善的质量管理体系,包括质量控制点、工序检验、异常处理等,确保产品质量和生产效率。
5.持续改进规范技术部应建立健全的反馈机制,及时收集和分析市场反馈和用户需求,以促进产品的持续改进和创新。
产品研发、技术工作内容

产品研发、技术工作内容
产品研发和技术工作内容是指在产品设计和开发过程中所涉及的工作任务。
以下是一些常见的产品研发和技术工作内容:
1. 需求分析:与客户沟通,了解产品需求和用户需求,并进行需求分析和文档编写。
2. 技术研究:调研相关技术,了解当前市场上的最新技术趋势和发展方向。
3. 原型设计:使用工具进行产品原型设计,包括产品界面设计、交互设计等。
4. 系统设计:根据产品需求,进行系统架构设计和模块设计,确定产品的整体框架和技术方案。
5. 编码实现:根据系统设计,编写产品的核心代码和模块代码。
6. 测试和Debug:对产品进行功能测试、性能测试和安全测试,并修复开发过程中发现的错误和问题。
7. 优化和改进:对产品进行性能优化和功能改进,提高产品的稳定性、可靠性和用户体验。
8. 文档编写:编写产品开发文档、用户手册和技术文档,记录产品开发和实现的过程和细节。
9. 项目管理:负责产品开发的进度管理、团队协作和资源调配,确保项目按时、高质量完成。
10. 技术支持:提供产品上线后的技术支持和维护,解决用户
的技术问题和故障排除。
以上是产品研发和技术工作的一些主要内容,具体工作内容可根据不同公司和项目的需求而有所变化。
移动互联网产品的设计与开发

移动互联网产品的设计与开发在移动互联网行业中,产品的设计和开发是非常重要的环节。
一个优秀的产品,需要在用户体验、技术实现、商业模式等多个方面都能达到卓越水平,才能在市场竞争中占有一席之地。
本文将从几个方面来探讨移动互联网产品的设计和开发。
一、用户体验设计用户体验设计是移动互联网产品设计的核心。
优秀的用户体验设计能够提高用户的满意度和粘性,从而促进产品的推广和发展。
为了达到优秀的用户体验设计,需要从以下几个方面入手:1.用户研究:在进行产品设计之前,需要对目标用户进行研究。
通过调查问卷、用户行为分析等手段,了解用户的需求和痛点,为产品设计提供依据。
2.信息架构设计:信息架构是指产品中信息元素之间的结构和关系。
优秀的信息架构设计能够提高用户浏览效率和准确度。
信息架构设计需要从目录、分类、标签、导航等多个方面入手。
3.界面设计:移动互联网产品的界面设计需要注重美学和用户体验。
设计应该简洁、易懂、直观,避免过多的装饰和复杂的功能。
二、技术实现移动互联网产品的技术实现主要包括前端开发、后台开发和移动端开发。
在进行技术实现时,需要考虑以下几个方面:1.技术选型:在开始开发之前,需要选择适合项目需求的技术栈。
技术选型需要考虑技术的成熟度、稳定性、可扩展性和易用性。
2.代码规范:为了保证代码的可读性和可维护性,需要采用规范的代码编写方式。
代码规范包括变量命名规则、代码缩进、注释规范等。
3.安全性设计:移动互联网产品的安全性设计需要从多个方面入手。
比如,通过数据加密、权限控制、验证码等手段确保用户数据的安全性;通过代码审计、漏洞扫描等手段确保产品的安全性。
三、商业模式设计移动互联网产品的成功不仅仅依赖于技术实现和用户体验设计,还需要具有合适的商业模式。
商业模式设计需要考虑以下几个方面:1.盈利模式:移动互联网产品的盈利模式主要包括广告、用户付费、渠道佣金等方式。
为了设计合适的盈利模式,需要考虑产品定位、用户粘性、竞争情况等。
产品设计与开发总结汇报
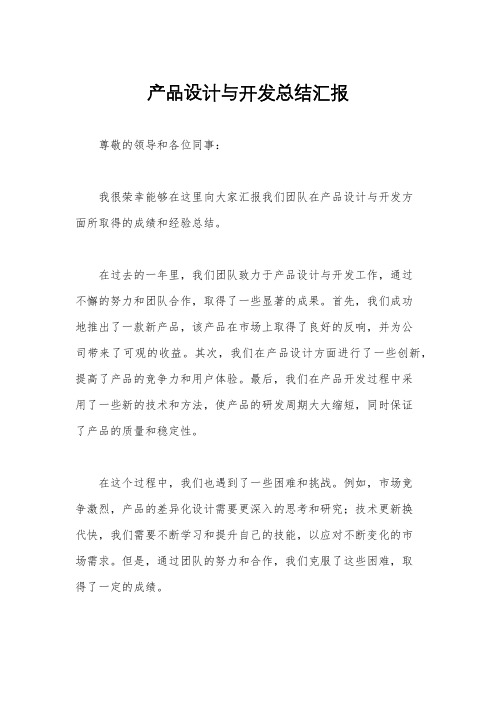
产品设计与开发总结汇报
尊敬的领导和各位同事:
我很荣幸能够在这里向大家汇报我们团队在产品设计与开发方
面所取得的成绩和经验总结。
在过去的一年里,我们团队致力于产品设计与开发工作,通过
不懈的努力和团队合作,取得了一些显著的成果。
首先,我们成功
地推出了一款新产品,该产品在市场上取得了良好的反响,并为公
司带来了可观的收益。
其次,我们在产品设计方面进行了一些创新,提高了产品的竞争力和用户体验。
最后,我们在产品开发过程中采
用了一些新的技术和方法,使产品的研发周期大大缩短,同时保证
了产品的质量和稳定性。
在这个过程中,我们也遇到了一些困难和挑战。
例如,市场竞
争激烈,产品的差异化设计需要更深入的思考和研究;技术更新换
代快,我们需要不断学习和提升自己的技能,以应对不断变化的市
场需求。
但是,通过团队的努力和合作,我们克服了这些困难,取
得了一定的成绩。
在未来的工作中,我们将继续努力,不断提高产品设计与开发的水平。
我们将更加关注用户的需求和市场的变化,不断创新,推出更多更好的产品;我们也将加强团队建设,提高团队的协作能力和创新意识,以更好地应对未来的挑战。
最后,我要感谢所有参与产品设计与开发工作的同事们,是你们的辛勤付出和无私奉献,才有了我们的今天。
同时,也要感谢公司的领导和各位同事对我们工作的支持和鼓励。
有了你们的支持和帮助,我们才能取得今天的成绩。
谢谢大家!。
设计开发过程中的技术和方法总结
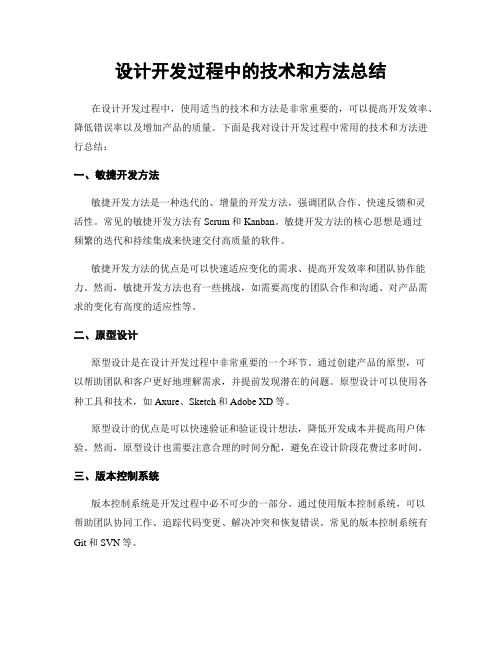
设计开发过程中的技术和方法总结在设计开发过程中,使用适当的技术和方法是非常重要的,可以提高开发效率、降低错误率以及增加产品的质量。
下面是我对设计开发过程中常用的技术和方法进行总结:一、敏捷开发方法敏捷开发方法是一种迭代的、增量的开发方法,强调团队合作、快速反馈和灵活性。
常见的敏捷开发方法有Scrum和Kanban。
敏捷开发方法的核心思想是通过频繁的迭代和持续集成来快速交付高质量的软件。
敏捷开发方法的优点是可以快速适应变化的需求、提高开发效率和团队协作能力。
然而,敏捷开发方法也有一些挑战,如需要高度的团队合作和沟通、对产品需求的变化有高度的适应性等。
二、原型设计原型设计是在设计开发过程中非常重要的一个环节。
通过创建产品的原型,可以帮助团队和客户更好地理解需求,并提前发现潜在的问题。
原型设计可以使用各种工具和技术,如Axure、Sketch和Adobe XD等。
原型设计的优点是可以快速验证和验证设计想法,降低开发成本并提高用户体验。
然而,原型设计也需要注意合理的时间分配,避免在设计阶段花费过多时间。
三、版本控制系统版本控制系统是开发过程中必不可少的一部分。
通过使用版本控制系统,可以帮助团队协同工作、追踪代码变更、解决冲突和恢复错误。
常见的版本控制系统有Git和SVN等。
版本控制系统的优点是可以确保代码的版本安全、方便团队协作和代码复用。
然而,版本控制系统也需要注意合理的分支管理和代码冲突解决。
四、代码审查代码审查是一种重要的质量保证方法。
通过对开发人员编写的代码进行评审,可以发现潜在的问题和错误,提高代码的可读性和可维护性。
代码审查可以使用一些工具和方法,如静态代码分析工具和扫描器等。
代码审查的优点是可以提高代码质量、减少错误和增加团队合作精神。
然而,代码审查也需要合理分配时间和资源,以及平衡审查的严格度和开发速度。
五、测试驱动开发测试驱动开发是一种先写测试用例,再编写代码来满足测试用例的开发方法。
研发新产品与技术创新计划
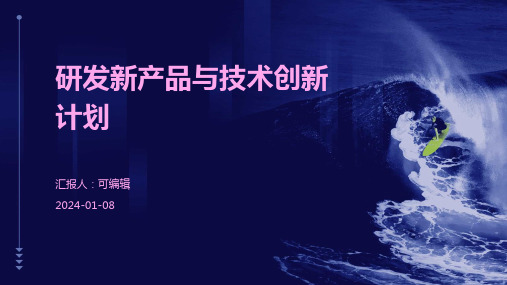
设计与开发
进行产品设计、功能开发、原 型制作等。
发布与推广
将产品推向市场,进行市场推 广和销售。
产品研发的挑战与解决方案
挑战
市场竞争激烈、技术更新迅速、研发 成本高昂、人才短缺等。
解决方案
加强市场调研,紧跟技术趋势,优化 研发流程,降低成本,培养和引进优 秀人才等。
02
新产品研发
新产品创意的产生与筛选
创意来源
通过市场调研、客户需求分析、技术趋势预测等途径,收集新产品创意。
筛选标准
根据市场需求、技术可行性、企业战略目标等因素,筛选出具有潜力的创意进 行进一步开发。
新产品的设计与开发
设计阶段
根据筛选出的创意,进行产品外观设计、功能设计、用户体 验设计等。
开发阶段
将设计转化为实际产品,进行软硬件开发、系统集成等工作 。
重要性
产品研发是企业保持竞争优势、 推动产业升级和实现可持续发展 的重要手段,也是企业创新能力 和核心竞争力的体现。
产品研发的流程与阶段
概念验证
对创意进行初步评估,确定其 可行性。
测试与验证
对产品进行性能测试、安全测 试、用户体验测试等,确保产 品符合要求。
创意产生
收集市场需求、技术趋势等信 息,寻找产品研发的创意点。
要点二
知识产权申请与保护
及时申请相关知识产权,保护团队的研发成果,防止侵权 行为。
05
研发资源与预算
研发资金的筹措与使用
资金来源
企业自有资金、政府资助、风险投资、银行 贷款等。
成本控制
制定预算并监控实际支出,避免超支。
资金使用计划
研发人员薪酬、设备采购、软件购买、试验 材料等。
资金回报
智能制造的智能化产品设计与开发
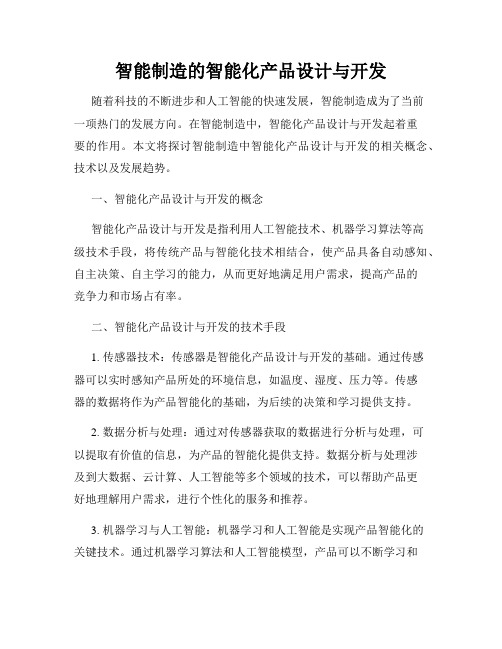
智能制造的智能化产品设计与开发随着科技的不断进步和人工智能的快速发展,智能制造成为了当前一项热门的发展方向。
在智能制造中,智能化产品设计与开发起着重要的作用。
本文将探讨智能制造中智能化产品设计与开发的相关概念、技术以及发展趋势。
一、智能化产品设计与开发的概念智能化产品设计与开发是指利用人工智能技术、机器学习算法等高级技术手段,将传统产品与智能化技术相结合,使产品具备自动感知、自主决策、自主学习的能力,从而更好地满足用户需求,提高产品的竞争力和市场占有率。
二、智能化产品设计与开发的技术手段1. 传感器技术:传感器是智能化产品设计与开发的基础。
通过传感器可以实时感知产品所处的环境信息,如温度、湿度、压力等。
传感器的数据将作为产品智能化的基础,为后续的决策和学习提供支持。
2. 数据分析与处理:通过对传感器获取的数据进行分析与处理,可以提取有价值的信息,为产品的智能化提供支持。
数据分析与处理涉及到大数据、云计算、人工智能等多个领域的技术,可以帮助产品更好地理解用户需求,进行个性化的服务和推荐。
3. 机器学习与人工智能:机器学习和人工智能是实现产品智能化的关键技术。
通过机器学习算法和人工智能模型,产品可以不断学习和优化自身的功能,提高用户体验。
例如,在语音助手产品中,通过深度学习和自然语言处理技术,实现了语音识别和智能问答等功能。
4. 人机交互:智能化产品设计与开发中,人机交互是非常重要的一部分。
通过合理的人机交互方式,可以使产品更加易用和友好,提高用户体验。
目前,声音识别、手势识别、虚拟现实等技术已经被广泛应用于产品设计中,使用户与产品之间的交互更加自然和智能化。
三、智能化产品设计与开发的发展趋势1. 多模态智能产品:随着人机交互技术的不断发展,产品将向多模态智能化方向发展。
即产品不仅能够通过声音、图像等传感器感知信息,还能够通过语音、手势、虚拟现实等方式进行交互。
这将进一步提升产品的智能化水平和用户体验。
产品设计与开发总结汇报

产品设计与开发总结汇报
尊敬的各位领导和同事们:
我很荣幸能在这里向大家汇报我们团队在产品设计与开发方面所取得的成就和经验总结。
在过去的一段时间里,我们团队经历了许多挑战,但也取得了许多成功。
以下是我们的总结汇报:
首先,我们团队在产品设计阶段注重了市场调研和用户需求分析。
我们深入了解了目标用户群的喜好和习惯,从而能够更好地设计出符合用户需求的产品。
通过调研,我们发现了一些潜在的市场机会,并据此进行了产品创新和改进。
其次,我们团队在产品开发阶段注重了团队合作和沟通。
我们充分发挥了各自的专长,共同努力解决了技术难题和生产瓶颈。
同时,我们也与其他部门和供应商进行了密切的合作,确保产品的质量和交付进度。
最后,我们团队在产品上市后注重了市场反馈和产品改进。
我们积极收集用户的意见和建议,不断优化产品的功能和体验。
通过持续改进,我们的产品得到了用户的认可和好评,市场份额也逐渐
提升。
总的来说,我们团队在产品设计与开发方面取得了一定的成绩,但也面临着一些问题和挑战。
未来,我们将进一步加强团队协作,
提升创新能力,不断优化产品,以满足用户的需求和市场的变化。
谢谢大家的支持和关注!
此致。
敬礼。
产品设计及开发流程
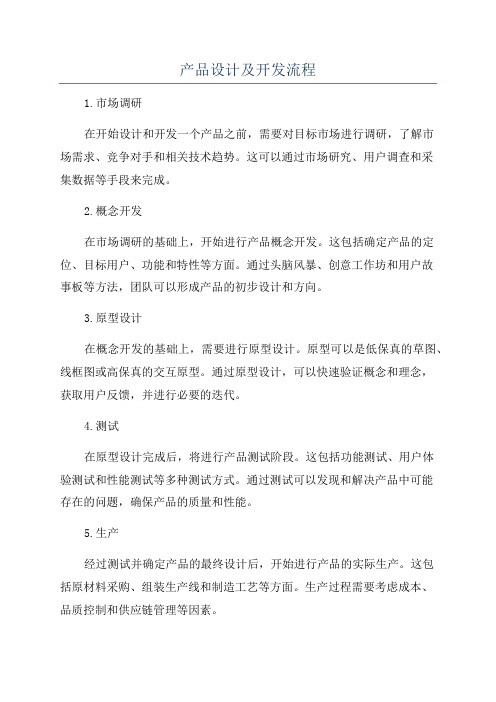
产品设计及开发流程1.市场调研在开始设计和开发一个产品之前,需要对目标市场进行调研,了解市场需求、竞争对手和相关技术趋势。
这可以通过市场研究、用户调查和采集数据等手段来完成。
2.概念开发在市场调研的基础上,开始进行产品概念开发。
这包括确定产品的定位、目标用户、功能和特性等方面。
通过头脑风暴、创意工作坊和用户故事板等方法,团队可以形成产品的初步设计和方向。
3.原型设计在概念开发的基础上,需要进行原型设计。
原型可以是低保真的草图、线框图或高保真的交互原型。
通过原型设计,可以快速验证概念和理念,获取用户反馈,并进行必要的迭代。
4.测试在原型设计完成后,将进行产品测试阶段。
这包括功能测试、用户体验测试和性能测试等多种测试方式。
通过测试可以发现和解决产品中可能存在的问题,确保产品的质量和性能。
5.生产经过测试并确定产品的最终设计后,开始进行产品的实际生产。
这包括原材料采购、组装生产线和制造工艺等方面。
生产过程需要考虑成本、品质控制和供应链管理等因素。
6.市场推广在产品生产完成后,需要进行市场推广。
这包括市场定位、品牌推广、渠道建设和销售推广等方面。
通过适当的市场推广策略,可以增加产品的曝光度,吸引目标用户,并扩大市场份额。
7.用户反馈和改进产品上市后,需要不断收集用户反馈并进行改进。
通过用户反馈,可以了解用户使用产品的体验和问题,并及时做出调整和改进,以提高产品的竞争力和用户满意度。
以上是产品设计及开发流程的一个基本框架。
需要注意的是,每个产品的设计和开发流程可能会有所不同,具体流程可以根据不同产品和行业的特点进行调整和优化。
成功的产品设计和开发需要团队的协作、创新思维和良好的项目管理能力。
产品设计和开发策略

产品设计和开发策略在市场竞争日益激烈的今天,产品设计和开发策略越来越成为企业成功的关键因素之一。
因为产品设计和开发策略直接决定了产品的质量、功能和性能,进而决定了企业未来的利润和市场地位。
一、产品设计产品设计是指通过创新思维和技术手段,把市场需求和用户体验转化为可实现的、具体的产品方案。
良好的产品设计应该满足以下几个方面的要求:1.市场需求:产品设计必须以市场需求为导向,切忌以自我为中心。
了解市场需求,考虑用户体验,才能有效地设计出符合市场需求的产品。
2.用户体验:用户体验是产品设计的核心要求。
一个易用、方便、快捷的产品,可以让用户更加喜欢和推崇,提高市场口碑。
3.功能性:产品设计也要满足基本的功能要求。
产品的基本功能必须能够满足用户的需求,不能过于复杂也不能过于简单。
4.造型设计:造型设计是产品设计中非常重要的一环。
好的造型设计能够增加产品的美感和趣味性,增加用户使用的体验效果。
二、开发策略产品设计只是开发过程中的一部分,开发策略的制订对于产品实现来说也非常重要。
1.技术选型:技术选型通常是通过市场调研、用户需求分析等方式确定的。
开发过程中技术的选择和使用一定要满足产品的要求,能够提供好的功能和体验。
2.开发流程:开发流程分成不同阶段,每个阶段都有相应的开发要求和标准。
好的开发流程应该有有效的沟通和协作机制,能够保证开发进程顺利进行。
3.测试和验收:开发完成后,产品还需要经过测试和验收。
这种测试和验收应该包括用户体验效果和功能效果,能够合理地检验产品的过程和成果,为后期开发提供有效的参考。
三、产品设计和开发的关系产品设计和开发是两个相互依存的过程。
开发的成果往往是基于设计方案的,而设计方案本身又需要开发技术的支持和推动。
对于企业而言,良好的产品设计和开发策略是实现战略目标的关键因素。
良好的产品设计能够提高产品美观度、易用性和性能,增强产品的市场竞争力;良好的开发策略能够保障产品的质量和技术实现,从而有利于提高生产效率和市场占有率。
基于人工智能技术的智能电子产品设计与开发
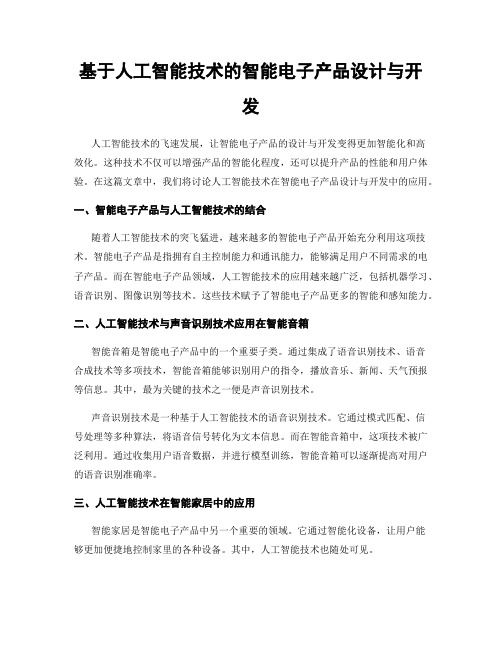
基于人工智能技术的智能电子产品设计与开发人工智能技术的飞速发展,让智能电子产品的设计与开发变得更加智能化和高效化。
这种技术不仅可以增强产品的智能化程度,还可以提升产品的性能和用户体验。
在这篇文章中,我们将讨论人工智能技术在智能电子产品设计与开发中的应用。
一、智能电子产品与人工智能技术的结合随着人工智能技术的突飞猛进,越来越多的智能电子产品开始充分利用这项技术。
智能电子产品是指拥有自主控制能力和通讯能力,能够满足用户不同需求的电子产品。
而在智能电子产品领域,人工智能技术的应用越来越广泛,包括机器学习、语音识别、图像识别等技术。
这些技术赋予了智能电子产品更多的智能和感知能力。
二、人工智能技术与声音识别技术应用在智能音箱智能音箱是智能电子产品中的一个重要子类。
通过集成了语音识别技术、语音合成技术等多项技术,智能音箱能够识别用户的指令,播放音乐、新闻、天气预报等信息。
其中,最为关键的技术之一便是声音识别技术。
声音识别技术是一种基于人工智能技术的语音识别技术。
它通过模式匹配、信号处理等多种算法,将语音信号转化为文本信息。
而在智能音箱中,这项技术被广泛利用。
通过收集用户语音数据,并进行模型训练,智能音箱可以逐渐提高对用户的语音识别准确率。
三、人工智能技术在智能家居中的应用智能家居是智能电子产品中另一个重要的领域。
它通过智能化设备,让用户能够更加便捷地控制家里的各种设备。
其中,人工智能技术也随处可见。
比如,基于人工智能技术的智能家居系统,可以通过学习用户的喜好,自动控制照明、窗帘等设备;还能够依据天气、时间等因素,调整家中空调温度。
此外,智能家居还可以结合语音识别技术,让用户能够通过语音操作智能家居产品,实现更加智能的控制。
四、人工智能技术在智能医疗中的应用基于人工智能技术的智能医疗,也是智能电子产品的一个重要领域。
通过智能设备收集患者的生理数据,并将这些数据上传到云端进行分析,智能医疗产品可以及时为患者提供指导和建议。
硬件产品的设计和开发
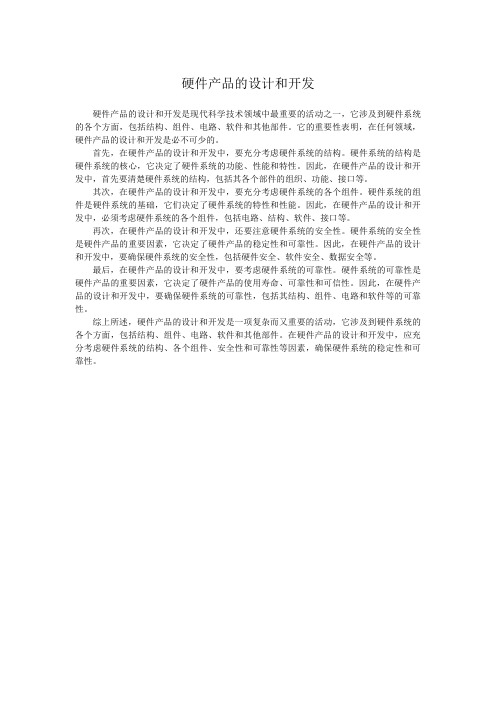
硬件产品的设计和开发
硬件产品的设计和开发是现代科学技术领域中最重要的活动之一,它涉及到硬件系统的各个方面,包括结构、组件、电路、软件和其他部件。
它的重要性表明,在任何领域,硬件产品的设计和开发是必不可少的。
首先,在硬件产品的设计和开发中,要充分考虑硬件系统的结构。
硬件系统的结构是硬件系统的核心,它决定了硬件系统的功能、性能和特性。
因此,在硬件产品的设计和开发中,首先要清楚硬件系统的结构,包括其各个部件的组织、功能、接口等。
其次,在硬件产品的设计和开发中,要充分考虑硬件系统的各个组件。
硬件系统的组件是硬件系统的基础,它们决定了硬件系统的特性和性能。
因此,在硬件产品的设计和开发中,必须考虑硬件系统的各个组件,包括电路、结构、软件、接口等。
再次,在硬件产品的设计和开发中,还要注意硬件系统的安全性。
硬件系统的安全性是硬件产品的重要因素,它决定了硬件产品的稳定性和可靠性。
因此,在硬件产品的设计和开发中,要确保硬件系统的安全性,包括硬件安全、软件安全、数据安全等。
最后,在硬件产品的设计和开发中,要考虑硬件系统的可靠性。
硬件系统的可靠性是硬件产品的重要因素,它决定了硬件产品的使用寿命、可靠性和可信性。
因此,在硬件产品的设计和开发中,要确保硬件系统的可靠性,包括其结构、组件、电路和软件等的可靠性。
综上所述,硬件产品的设计和开发是一项复杂而又重要的活动,它涉及到硬件系统的各个方面,包括结构、组件、电路、软件和其他部件。
在硬件产品的设计和开发中,应充分考虑硬件系统的结构、各个组件、安全性和可靠性等因素,确保硬件系统的稳定性和可靠性。
产品方案及技术方案的区别
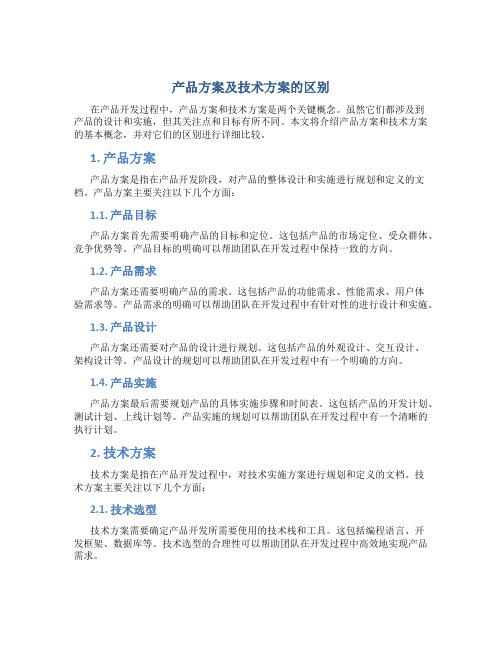
产品方案及技术方案的区别在产品开发过程中,产品方案和技术方案是两个关键概念。
虽然它们都涉及到产品的设计和实施,但其关注点和目标有所不同。
本文将介绍产品方案和技术方案的基本概念,并对它们的区别进行详细比较。
1. 产品方案产品方案是指在产品开发阶段,对产品的整体设计和实施进行规划和定义的文档。
产品方案主要关注以下几个方面:1.1. 产品目标产品方案首先需要明确产品的目标和定位。
这包括产品的市场定位、受众群体、竞争优势等。
产品目标的明确可以帮助团队在开发过程中保持一致的方向。
1.2. 产品需求产品方案还需要明确产品的需求。
这包括产品的功能需求、性能需求、用户体验需求等。
产品需求的明确可以帮助团队在开发过程中有针对性的进行设计和实施。
1.3. 产品设计产品方案还需要对产品的设计进行规划。
这包括产品的外观设计、交互设计、架构设计等。
产品设计的规划可以帮助团队在开发过程中有一个明确的方向。
1.4. 产品实施产品方案最后需要规划产品的具体实施步骤和时间表。
这包括产品的开发计划、测试计划、上线计划等。
产品实施的规划可以帮助团队在开发过程中有一个清晰的执行计划。
2. 技术方案技术方案是指在产品开发过程中,对技术实施方案进行规划和定义的文档。
技术方案主要关注以下几个方面:2.1. 技术选型技术方案需要确定产品开发所需要使用的技术栈和工具。
这包括编程语言、开发框架、数据库等。
技术选型的合理性可以帮助团队在开发过程中高效地实现产品需求。
2.2. 系统架构技术方案需要规划产品的系统架构。
这包括系统的组成模块、模块之间的关系、数据流向等。
系统架构的合理性可以帮助团队在开发过程中实现高效的系统设计和开发。
2.3. 数据库设计技术方案还需要明确产品的数据库设计。
这包括数据库的表结构、数据关系、索引等。
数据库设计的合理性可以帮助团队在开发过程中高效地存储和读取数据。
2.4. 技术实施技术方案最后需要规划具体的技术实施步骤和时间表。
- 1、下载文档前请自行甄别文档内容的完整性,平台不提供额外的编辑、内容补充、找答案等附加服务。
- 2、"仅部分预览"的文档,不可在线预览部分如存在完整性等问题,可反馈申请退款(可完整预览的文档不适用该条件!)。
- 3、如文档侵犯您的权益,请联系客服反馈,我们会尽快为您处理(人工客服工作时间:9:00-18:30)。
第九章技术
产品制造必须有十分广泛的技术支持,所需的大部分知识体系须依生产制造的技术需求决定。
本章将从概述的角度来解释这些技术上的需求。
我们不试图从不同的产品和工业的角度去分不细述,而是着重于生产领域和普遍相关的广泛意义上的技术。
本章是通过对技术体系的每一因素的简要阐述,提供治理和设计,打算及生产技术的指导。
这些因素将按提出新产品设想,研究进展、产品设计、流水线生产等过程的质量操纵和保证的渐进步骤的顺序进行讨论。
本章还包括对生产效率改进和检验标准的简单讨论。
9.1 技术治理
技术治理确实是选用合适的,节约费用的技术应用于产品的研究、设计、测试以及生产,这意味着所有层次的治理人员都必须理解所应用的技术和它们的能力以及限制。
公司应设置一个与公司生产规模和行业相适应的技术机构。
治理需要有一个有效的治理体系以保证适当的技术需求及其应用。
该体系应能有效地治理企业的质量活动、工装资源、设备维护和更新,机器制造及工装设计,直至生产和工艺的改进。
适当的技术关键和工装能支援企业的生产,合适的计量装备和设施将被应用于检查和校准所有的操纵仪器、器具、装置和工具。
技术治理必须理解优秀的技术在产品设计和生产上的长远优势同时努力去最大程度地利用它。
治理应该注意并随时了解技术的改进,并有义务将这些安排给需要的工序和人员,当好“技术监护人”,而不仅仅是熟知能阻碍自身竞争力的技术,这也是其工作职责的一部分。
治理也必须保证能对技术的革新和发明在企业进行赞扬鼓舞和
奖励。
9.2 技术打算
公司应有一个技术路线来讲明产品与工艺的设计目标。
应由一个跨部门小组制订一个技术打算,以确保技术任务完成的平衡与低成本高效率。
技术打算应为长期业务打算的一部分并能定期检查与修订。
技术打算应包括降低产品设计与制作时刻的措施,查找并确保公司以专利品与专有技术的进展的优势压倒竞争者。
应有一个关于工艺过程、设备、辅助工具的正式打算程序。
程序应提供一个跨部门、多学科队伍,以选择和设计工艺过程、设备及辅助工具。
应特不注意将资本投入作为业务量与销售量函数的回报率。
技术打算小组应选择当前产品在成本局限下具有最大灵活性的工艺过程、设备及工装技术。
9.3 技术的获得
每个公司应有一个正式程序监测工艺状况,获得企业的适当技术。
9.4 研究与开发
工作原理:每个公司应努力获得并应用能提供竞争优势的技术。
工作需要:制造商应做产品与工艺的研究和开发工作(R&D)。
(R&D)应有一个目标打算与预算。
打算中应包含提高R&D能力的条款规定,以及一个以适当人力、工具与公司规模、工业部门相适应水平执行的R&D所需的资源方式来表达的预算。
必须保持R&D记录以显示结果与成本效益。
R&D活动的一个重要功能确实是设计相应的R&D信息与技术,不管是在内部依旧与外部的通讯系统。
R&D活动应关心技术转化为提高公司产品与工艺的有效性与竞争力。
一个小型制造公司可能认为研究与进展并不重要。
只是在得出公司不能从R&D中得到好处的结论往常,仍有好几种选择必须探
讨。
第一步是要求公司的技术人员作
为技术守门者。
这意味着他们有责任明白其领域的最新技术并与公司其他人员保持联系。
第二步是与其它公司、本地的或是通过协会或联营一起来赞助研究。
也许有可能讲服一家当地大学来研究公司感兴趣的某个问题,尤其假如某个公司职员是该校的研究生。
更多的情况下小公司从大公司处购买物料,然后大物料供应商将它内部研究结果给一个长期客户。
9.5 产品设计与开发技术
工作原理:制造商必须拥有适于部件与/或系统的设计与进展的技术能力。
它包括专业设计与产品工程人员。
设计与开发技术资源
一个制造商必须有设计和开发部件与产品所需的资源。
需要有足够的人力和工具(自行设计或合作开发)。
在与他人合作设计之时,制造商应当有程序来跟踪与记录合作者的设计过程。
必须有简化、优化和革新设计过程的灵活程序。
制造商应能进行性能/
成本风险研究,失效模式及其效应分析,公差研究等等。
公司应有一个系统来获得和有效使用来自测试、生产和领域支持活动的反馈。
应有专门人员对质量、安全、生产能力以及设计的成本进行评估。
产品设计和分析能力
制造商应有相应的计算机辅助设计(CAD)能力,应具有有经验的人员以及足够的设备来进行设计与分析工作,该工作的关键在于客户与供应商的CAD/CAM系统界面。
制造商还应有一个打算以获得与保持用于执行相应产品设计的产品分析的软件。
分析类型可能包括价值分析(VA),有限元素方法(FEM),失效模式及其效应分析(FMEA),以及装配的公差分析。
原型支持
制造商应有完成原型部件开发程序所需的资源与设备,使用一个跨学科小组来确保成本、制造以及劳动效率的优化配置。
原型开发程序:原型开发应被视作构成完整的产品业务循环所需要的。
只要有可能,应随生产意向或生产工具来生产原型。
制造商应有原型开发的项目治理,访问和跟踪系统以保证满足性能标准和截止期限。
治理部门也应有一个原型开发的进展打算。
产品测试
制造商必须能够对产品的部件与系统进行所有适用的性能测试。
最差不多的性能测试应包括产品寿命、可靠性和耐用性。
应该提供用来进行产品测试的工具与设备,设备应该定期校准。
(见第5章质量)
性能测试
除明显的打算需要外,应当给性能测试制定打算并执行,找出实际产品寿命、性能以及可靠性。
应对性能测试活动提供相应的人力、设备和技术。
当测试在较远的地点时,为确保所有相关测试都被执行,所有数据都被收集并分析,则使用跟踪与报告系统就专门重要了。
测试数据分析及反馈
收集到的测试数据应当定期地分析和报告给相应的人员。
产品寿命测试
必须有专门的经理或小组负责寿命周期测试,找出产品与失效模式的实际平均寿命。
测试数据应与失效模式效应作比较与检查。
9.6 生产技术
执行过程和弹性打算
一个制造商必须拥有一个打算和实施生产的系统性措施,这包括与质量保证和工装设计同样重要的协调工作、生产工业化工程、以及一个系统化的循序渐进的打算。
资本投资:决定资本需求总量的决定因素是包含在企业打算中的流程和设备上的要求。
专门显然,专门多因素会阻碍投资资本的总量,那个问题的关键在于传统的打算过程及选择机械工装和设备的方法不再具有竞争力,生产方案的打算和机器设备的选择对企业的成败是如此重要以至于必须有一个联系生产和财务工作的跨部门的工作组来进行协调。
生产过程的工程:生产商必须组织一个跨部门综合性的(协作工程)工作组来为散件和成品的生产提供进展的打算。
一个成功的制造商关于一个进展打算应有一个系统的安排,首先对各产品有系统性的打算,然后将它整理成文,最后才考虑将其投入生产过程。
这一系列打算须结合整个工作流程来考虑,从工装到质量的总体情形,自动化机器和辅助工具的适当范围,并预留足够的应急生产能力。
质量保证打算:其原则是应把质量的概念贯彻到生产过程而不仅仅是最后的检验工序。
执行质量保证打算的作用是生产打算和进展打算,必须确立严格的生产需求,并特不的加以留意。
那个和质量保证相联系的运作系统,通常由在生产过程中的一系。