生产异常工时单
异常工时扣款单
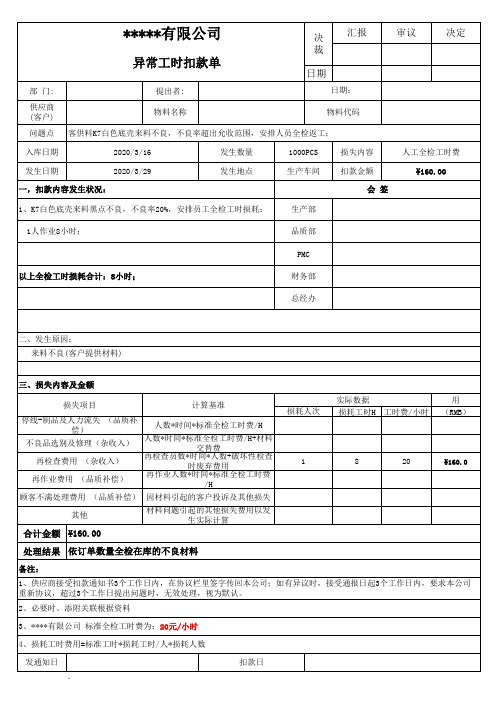
3、****有限公司 标准全检工时费为:20元/小时
4、损耗工时费用=标准工时*损耗工时/人*损耗人数
发通知日 .
扣款日
合计金额 ¥160.00
损耗人次 1
损耗工时费
实际数据
用
损耗工时H 工时费/小时 (RMB)
8
20
¥160.0
处理结果供应商接受扣款通知书3个工作日内,在协议栏里签字传回本公司;如有异议时,接受通报日起3个工作日内,要求本公司 重新协议,超过3个工作日提出问题时,无效处理,视为默认。
部 门:
供应商 (客户)
问题点
*****有限公司
异常工时扣款单
提出者:
决
汇报
裁
日期
日期:
物料名称
物料代码
客供料K7白色底壳来料不良,不良率超出允收范围,安排人员全检返工;
审议
决定
入库日期
2020/3/16
发生数量
1000PCS
损失内容
人工全检工时费
发生日期
2020/3/29
一,扣款内容发生状况:
发生地点
不良品选别及修理(杂收入)
人数*时间*标准全检工时费/H+材料 交替费
再检查费用 (杂收入)
再检查员数*时间*人数+破坏性检查 时废弃费用
再作业费用 (品质补偿)
再作业人数*时间*标准全检工时费 /H
顾客不满处理费用 (品质补偿) 因材料引起的客户投诉及其他损失
其他
材料问题引起的其他损失费用以发 生实际计算
生产车间
扣款金额 会签
¥160.00
1、K7白色底壳来料黑点不良,不良率20%,安排员工全检工时损耗:
生产异常反馈单完整版
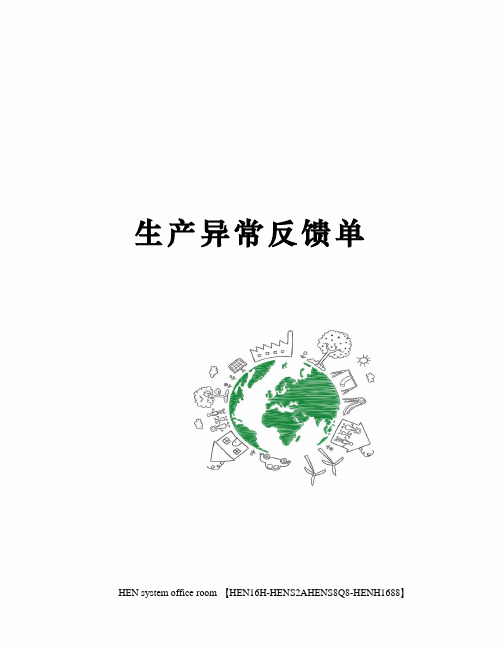
2、原因分析:
确认: 审核:
责任部门填写
3、临时或立即改善解决方案:
确认: 审核:
4、最终处理结果:
确认:审核:
5、防止再次发生解决方案:
确认: 审核:
反馈流程:
1、生产组长在发生生产异常时应立即报告车间主管,并通知现场技术或品质人员进行确认,以及提交【生产异常反馈单】。
2、各部门在接到【生产异常反馈单】后应及时进行原因分析和采取改善方案,及时解决或改善异常问题以保障正常生产。
生产异常反馈单
生产异常反馈单
生产订单
产品型号
物料名称
反馈部门
发生时间
反馈人
数量
不良数
不良率
影响度
较严重 一般轻微
待工人数
停工人数
停工时间
异常工时
异常类型
计划异常
设备异常
物料异常
工艺异常
其它
1、异常情况描述:
确认:审核:
原因分析与建议
材料/零件来料不良 设备模具异常
作业人员操作不当
工艺问题
设计问题
质量问题
品质异常工时单
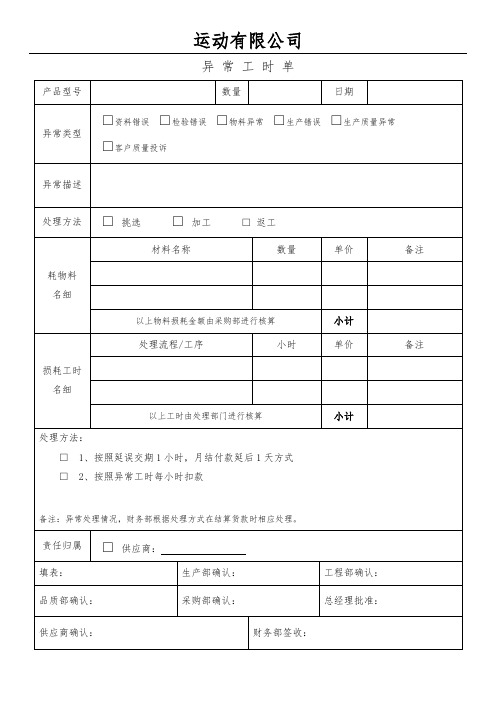
产品型号
数量
日期
异常类型
□资料错误□检验错误□物料异常□生产错误□生产质量异常
□客户质量投诉
异常描述
处理方法
□挑选□加工□返工
耗物料
名细
材料名称
数量
单价
备注
以上物料损耗金额由采购部进行核算
小计
损耗工时
名细处理流程/工序小时 Nhomakorabea单价
备注
以上工时由处理部门进行核算
小计
处理方法:
□1、按照延误交期1小时,月结付款延后1天方式
□2、按照异常工时每小时扣款
备注:异常处理情况,财务部根据处理方式在结算货款时相应处理。
责任归属
□供应商:
填表:
生产部确认:
工程部确认:
品质部确认:
采购部确认:
总经理批准:
供应商确认:
财务部签收:
【质量部】异常工时处理规范

1目的明确电器事业部异常工时责任归属,提升各部门协同处理异常的响应速度,特制订本制度。
2定义2.1生产异常:指造成生产停工或生产进度延迟的情形。
2.2异常工时:由生产异常造成的超过标准工时的无效工时,称为异常工时。
供应商方面,0.5小时以上的计入异常工时统计,内部0.5小时以上的计入异常工时的统计。
3职责3.1供应部生产处3.1.1产线班长:负责填写《异常工时费用承担表》,保证异常描述和工时数的准确性并通知相关人员到异常发生地现场确认。
3.1.2生产部异常工时统计员:负责异常数据初步审核及录入。
3.2质量部3.2.1巡检:第一时间对生产过程中出现的质量异常进行处理,不能给出处理结果的及时反馈相关工程师及上级,以及作为第三方对产线产生的异常工时数据进行核实。
3.2.2质量工程师:对质量问题引起的异常工时责任进行初判,推进质量异常问题改善闭环。
3.3电器部总经理:负责有争议的异常工时责任判定,促进异常工时制度正常运行。
3.4供应部采购处:负责跟踪各产品线供应商异常工时费用回馈情况,至账务费用抵冲发生产部门人力成本,处理进度及时反馈成本专员。
3.5财务部:负责月度异常工时费用抵冲工作;负责异常工时补偿款的到账确认。
3.6成本专员:负责公司内外部损失工时台账建立及费用执行情况跟踪。
4程序/规定/要求/4.1生产异常处理流程4.1.1异常发生时,生产部应立即通知相关部门前来确认处理,并报告直属上级。
a)因质量问题引起的异常由产线巡检第一时间确认处理,并通知质量工程师现场解决(如本人出差无法现场确认,须指定代理人处理)。
b)因待料引起的停线由生产班长第一时间通知计划专员,由计划处回复产线复产信息并判定责任部门。
4.1.2生产班长填写《异常工时费用承担表》,当日下班时将费用承担表交于车间主任处。
质量异常由巡检判定责任部门,待料异常由计划专员判定;4.1.3判定为外部供方问题,由采购部当日通知供应商确认信息,24H内无回复的默认同意判定;采购部依据接收到的处罚明细执行处罚并回复成本员。
4.异常工时管理细则
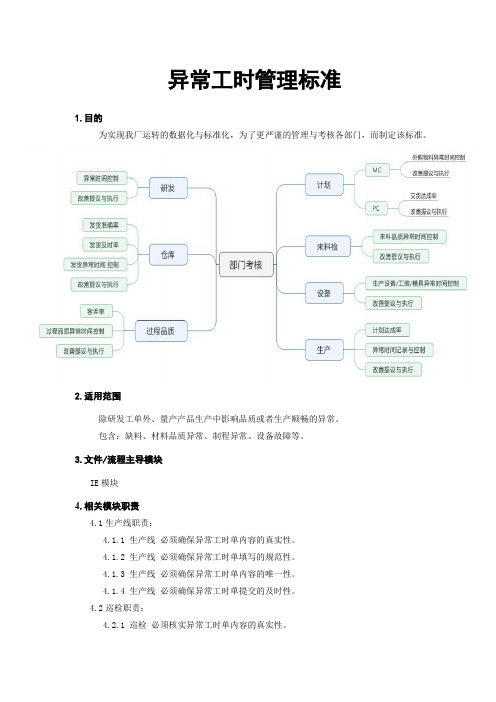
异常工时管理标准1.目的为实现我厂运转的数据化与标准化,为了更严谨的管理与考核各部门,而制定该标准。
2.适用范围除研发工单外、量产产品生产中影响品质或者生产顺畅的异常。
包含:缺料、材料品质异常、制程异常、设备故障等。
3.文件/流程主导模块IE模块4.相关模块职责4.1生产线职责:4.1.1 生产线必须确保异常工时单内容的真实性。
4.1.2 生产线必须确保异常工时单填写的规范性。
4.1.3 生产线必须确保异常工时单内容的唯一性。
4.1.4 生产线必须确保异常工时单提交的及时性。
4.2巡检职责:4.2.1 巡检必须核实异常工时单内容的真实性。
4.2.2 巡检必须确保结束时间填写的规范性与准确性。
4.2.3 巡检必须确保补充内容的明确性与具体性。
4.2.4 巡检必须确保通知异常相关部门的及时性。
4.3 MC职责:4.3.1 MC必须确保缺料异常工时单原因分析内容的具体详尽。
4.3.2 MC必须在规定时间范围内完成异常工时单原因的分析。
4.3.3 MC必须在规定时间范围内对异常情况提出永久改善对策。
4.4生技部职责:4.4.1 生技部必须第一时间到达现场处理设备模具异常。
4.4.2 生技部必须确保制程异常工时单原因分析内容的具体详尽。
4.4.3 生技部必须在规定时间范围内完成异常工时单原因的分析。
4.4.4 生技部必须在规定时间范围内对异常情况提出永久改善对策。
4.5 品质部职责:4.5.1 品质部必须确保来料不良异常工时单原因分析内容的具体详尽。
4.5.2 品质部必须在规定时间范围内完成异常工时单原因的分析。
4.5.3 品质部必须在规定时间范围内对异常情况提出永久改善对策。
4.6其余相关部门职责:4.6.1其余相关部门必须确保设备故障异常工时单原因分析内容的具体详尽。
4.6.2其余相关部门必须在规定时间范围内完成异常工时单原因的分析。
4.6.3其余相关部门必须在规定时间范围内对异常情况提出永久改善对策。
异常损失工时(时间)数据收集分析表(函数自动分析)

E-其它问题
损耗工时代码表
代码
小类别
A1 供应商送料不及时
A2 领料不及时
A3 发料不及时
A4 损耗未及时提报
A5 损耗未及时补回
B1 来料异常
B2 首件NG
B3 SIP错误
B4 不良率高停线
C1 SOP错误
C2 BOM错误
C3 结构装配问题
D1 部装生产线欠料
D2 部装生产线不良
D3 物料配送不及时
D4 制程不良返工
D5 人员出勤异常
D6 生产线物料使用错误
D7 生产物料丢失
D8 生产管理调配不合理
E1 工程资料准备提供错误/不及时
E2 PMC排配不合理
E3 工单错误
EC非计划性换线
E7 停电、停气、断网络
E8 换线时间损失
描述 因供应商送料延迟导致生产线停线 产线未及时给领料单到仓库 仓库未在规定时间内发料给产线物流 生产制程有物料损耗,但是没有提报或者未在规定时间周期内提报,导致生产欠料停线 生产有及时提报,但是物控未提报超损补料至供应商,或供应商未发料,导致生产线停线 物料来料已经SQE分析属于品质问题,影响产线停线或返工 订单生产首件错误,品质未检出异常,导致开线受阻 品质检验指导书提供错误,导致开线首件和产品检验错误,问题确认产品返工 不良导致停线或者不良导致停线调整损失工时(作业不良、产品设计问题、装配问题) 工程SOP提供错误,导致产线依此作业产品制程不良,问题确认工时损耗 BOM错误导致生产线不能正常生产,停机; 因结构装配问题导致生产作业不顺畅,需要额外人员加工的; 由于部装生产线作业不及时等问题导致组装线体待投入 由于部装生产线不良等原因造成组装投入不良比率高影响产出/拆机维修等造成的工时损耗 物料员未及时将部装物料及时送至产线对应工位,导致产线生产不连续 生产作业不良及未按要求作业产生的不良导致返工; 员工旷工、自离,导致其他员工的等待 生产线领料错误,造成误用 生产物料未管理好,导致物料丢生影响生产 由于生产管理、调度调配不合理造成生产线停线; 产品提供的作业指导书/BOM等信息错误,导致开线受阻; 未依据到料计划安排生产/未预留合理的物料周转上线时间; 工单开立错误导致领用物料错误或延时,未及时添加需手工添加物料; 工程的工装、夹治具未及时到位/数量不足,或者新进资源未检查直接上线导致的生产异常; 机台/设备故障异常调试或者更换 原有计划跳单,导致物料异常及换线损失工时 未提前通知的停电、停气、断网络故障或处理时间超出预计承诺时间,影响产出 生产产品切换时,换线造成的损失时间
工时异常原因分析与改善表
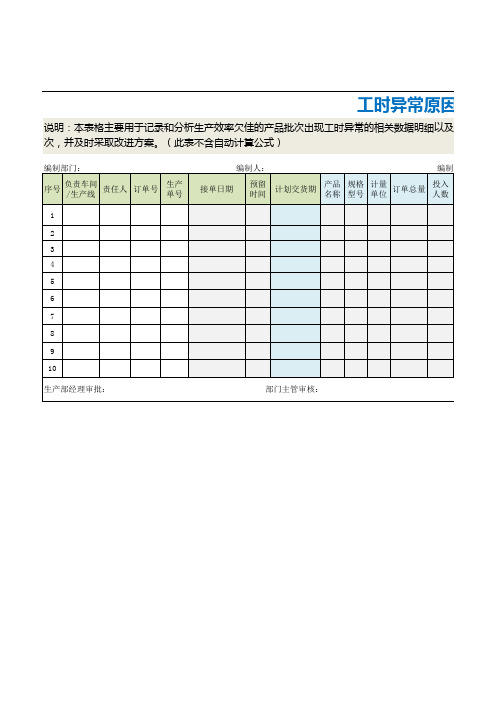
常原因分析与改善表
据明细以及具体原因,并提出相应的改进措施。可以帮助生产管理者集中性的分析生产效率偏低的产品批
编制日期: 标准 标准工时 所需天 实际交货日期 日产能 (H) 数 挡产 实际使用 生产效率 超用工时 时间 工时 超期 天数 差异率
制表:
产效率偏低的产品批原因分析改进措施备注工时异常原因分析与
说明:本表格主要用于记录和分析生产效率欠佳的产品批次出现工时异常的相关数据明细以及具体原因, 次,并及时采取改进方案。(此表不含自动计算公式)
编制部门: 序号 1 2 3 4 5 6 7 8 9 10 生产部经理审批: 部门主管审核: 制表: 负责车间 生产 责任人 订单号 /生产线 单号 接单日期 编制人: 预留 时间 计划交货期 编制日期: 产品 规格 计量 投入 订单总量 名称 型号 单位 人数
异常工时责任划分与责任判定标准参照表

产品研发中心开发的产品在分公司试产产生的异常工时(记录异常工时需要注明)
正常费用补偿、 只做统计不考核
产品结构不良
产品工程部 因产品结构改良设计、产品结构不良等造成的异常;
工程问题
开发遗留问题点-开发部
开发部
研发部负责开发的产品,其产品未释放,在产品开发过程中遗留未能解决的问题造成的 异常(《新产品试(生)产问题改善一览表》中记录的且未改善完成问题点)
异常工时责任划分与责任判定标准参照表
异常大类 异常小类
具体细项
责任部门
异常产生原因概述
备注
换产品工时
换产品工时
生产部
生产线切换产品生产造成多能工岗位训练
人力闲置-总装部
生产部
产品切换,导致多余人力无法外借
人力闲置-综合部(取消)
生产部
综合部招人多出公司配置人员
人员不足-总装部
生产部
人员离职、请假、旷工、自离导致生产时人力不足
人
人员状态
人员内部借调-产品工程部 人员内部借调-开发部 人员内部借调-PMC部
产品工程部 开发部 PMC部
产品工程部从总装部借调直接人员 开发部从总装部借调直接人员 PMC部从总装部借调直接人员
人员内部借调-IE部
IE部
IE部从总装部借调直接人员
塑胶件缺料(发外)
PMC部
塑胶件供应不及时,供应商为PMC部发外厂家
排程提前-主计划员
主计划员 突然的大单/急货而总装提前生产造成的缺料
排程提前-PMC
PMC部
大单/急货而总装提前生产,主计划已提前通知,造成的缺料
物料结构缺陷或规格变更-产品 工程部
产品工程部
物料规格临时变更等造成的异常(如﹕来料需做加工才能上线等)
异常工时损失管理规范(含表格)
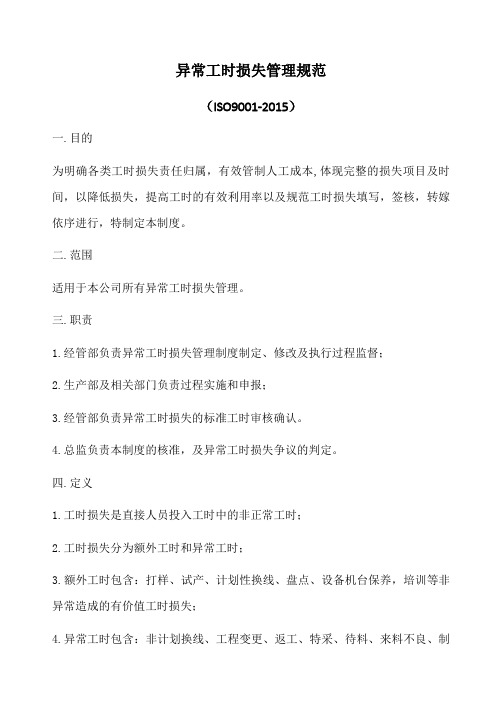
异常工时损失管理规范(ISO9001-2015)一.目的为明确各类工时损失责任归属,有效管制人工成本,体现完整的损失项目及时间,以降低损失,提高工时的有效利用率以及规范工时损失填写,签核,转嫁依序进行,特制定本制度。
二.范围适用于本公司所有异常工时损失管理。
三.职责1.经管部负责异常工时损失管理制度制定、修改及执行过程监督;2.生产部及相关部门负责过程实施和申报;3.经管部负责异常工时损失的标准工时审核确认。
4.总监负责本制度的核准,及异常工时损失争议的判定。
四.定义1.工时损失是直接人员投入工时中的非正常工时;2.工时损失分为额外工时和异常工时;3.额外工时包含:打样、试产、计划性换线、盘点、设备机台保养,培训等非异常造成的有价值工时损失;4.异常工时包含:非计划换线、工程变更、返工、特采、待料、来料不良、制程异常、设备/工具异常因异常造成的无价值工时损失。
五.作业内容1.工时损失类别及责任界定2.异常损失申报/复核/确认流程:2.1.生产部门在生产过程中异常工时损失发生0.5小时以上,线长如实填写《异常工时损失申报表》,交主管审核确认后交工程部进行标准工时确认,最后递交经管部存档。
2.2.工程部收到生产部门《异常工时损失申报表》后,在4小时内同相关责任部门进行确认,必要时到生产现场确认,工时确认由经管提供标准工时评估异常损失工时。
无标准工时的新产品按工程部初定的标准工时的1.5倍计算或按实际工投入时计算.异常确认后责任单位在《异常工时损失申报表》上签名核实后送总监审批。
对未能确认责任,争议较大的异常损失,由工程部记录后交总监仲裁。
2.3.工程部将当天核实确认后的《异常工时损失申报表》提报异常工时损失统计员,统计员将核实后的异常损失工时录入异常工时损失汇总报表中,并定时发给经管部。
2.4.异常工时损失统计员必须如实按确认后的“异常工时申报表”记录异常损失工时,如发现有瞒报,乱报,虚报工时者,经核实后对虚报部门申报人进行严重惩罚,同时追究所在部门主管的管理责任。
异常工时统计流程和方法说明0930
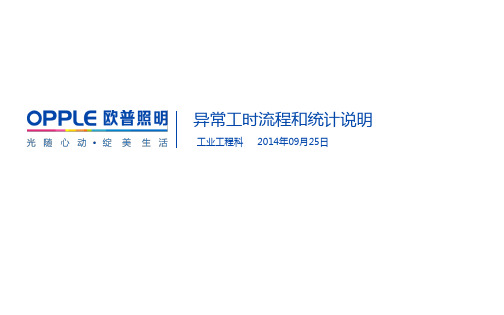
生产异常单
异常单号:XD-1409002
异常类型: 来料不良
品质异常
欠料
试产
设备异常
人员异动
ETO
成品返工
其它
车间
拉别
发单人
发单日期 发单时间
订单号
产品型号
影响产品数量
小灯
1拉
彭小燕
2014/9/17
10:30
40006237
MQ3030铂雅
生 产 填 写 异常
描述
物料代码 130022998
物料描述 MQ3030面板
换线费用
在线返工:针对设备异 常造成的不良品组织在
线返工
克服生产:使用不良设 备生产,但影响了生产
效率
材料报废
材料库存
开始返工
返工费用
换线 返工完成
效率损失费用
工票标准结束时间
实际完成时间
下一步处理人
ME
工时统计方法5
异常报警(生产)
异常处理(生产)
工时统计(生产)
下一步处理人
试产(小试、中试):
异常工时流程和统计说明
工业工程科 2014年09月25日
异常工时统计流程
异常发生时
异常发生
异常报警
异常判定
下一步 处理人
异常发生后
数据统计
费用评估
费用索赔
异常分类
➢ 来料不良 ➢ 品质异常 ➢ 欠料 ➢ 设备异常 ➢ 试产 ➢ ETO ➢ 人员异动 ➢ 返工 ➢ 其他
拉长报警并 填单
报警时机:
1出现错、混料; 2连续3PCS产品出现 致命性质量缺陷; 3严重质量缺陷功能 (或性能)不良率超 过1%;结构不良超过 3%; 4轻微质量缺陷不良率 超过5%时; 5.注塑,吹塑,冲压 铆接,丝印,喷涂, 元件整形,AI和SMT: 不良率超过5%; 6.波峰焊:焊点缺陷 超过1500DPPM,其 它缺陷不良率超过3%.
制造业车间管理异常分析(精)
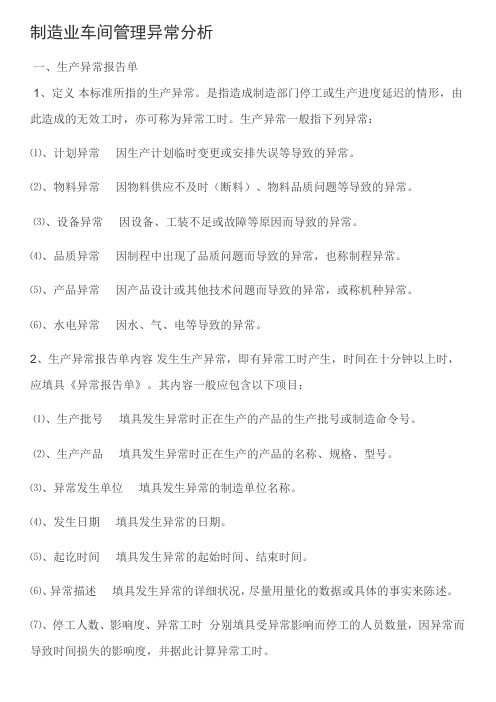
制造业车间管理异常分析一、生产异常报告单1、定义本标准所指的生产异常。
是指造成制造部门停工或生产进度延迟的情形,由此造成的无效工时,亦可称为异常工时。
生产异常一般指下列异常:⑴、计划异常因生产计划临时变更或安排失误等导致的异常。
⑵、物料异常因物料供应不及时(断料)、物料品质问题等导致的异常。
⑶、设备异常因设备、工装不足或故障等原因而导致的异常。
⑷、品质异常因制程中出现了品质问题而导致的异常,也称制程异常。
⑸、产品异常因产品设计或其他技术问题而导致的异常,或称机种异常。
⑹、水电异常因水、气、电等导致的异常。
2、生产异常报告单内容发生生产异常,即有异常工时产生,时间在十分钟以上时,应填具《异常报告单》。
其内容一般应包含以下项目:⑴、生产批号填具发生异常时正在生产的产品的生产批号或制造命令号。
⑵、生产产品填具发生异常时正在生产的产品的名称、规格、型号。
⑶、异常发生单位填具发生异常的制造单位名称。
⑷、发生日期填具发生异常的日期。
⑸、起讫时间填具发生异常的起始时间、结束时间。
⑹、异常描述填具发生异常的详细状况,尽量用量化的数据或具体的事实来陈述。
⑺、停工人数、影响度、异常工时分别填具受异常影响而停工的人员数量,因异常而导致时间损失的影响度,并据此计算异常工时。
⑻、临时对策由异常发生的部门填具应对异常的临时应急措施。
⑼、填表单位由异常发生的部门经办人员及主管签核。
⑽、责任单位对策(根本对策)3、使用流程⑴、异常发生时,发生部门的第一级主管应立即通知技术部门或相关责任单位,前来研究对策,加以处理,并报告直属上级。
⑵、制造部门会同技术部门、责任单位采取异常的临时应急对策并加以执行,以降低异常的影响。
⑶、异常排除后,由制造部门填具《异常报告单》一式四联,并转责任单位。
⑷、责任单位填具异常处理的根本对策,以防止异常重复发生,并将《异常报告单》的第四联自存,其余三联退生产部门。
⑸、制造部门接责任单位的异常报告单后,将第三联自存,并将第一联转财务部门,第二联转生产部门。
标准工时异常反馈&变更通知单
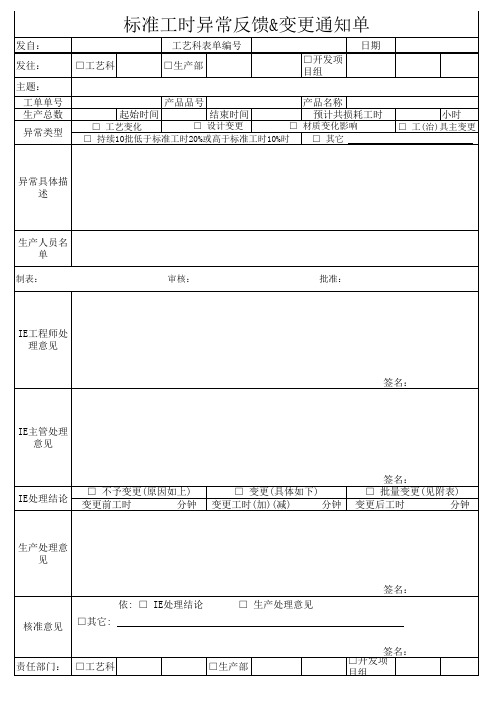
异常具体描 述
生产人员名 单
制表: 审核: 批准:
IE工程师处 理意见
签名:
IE主管处理 意见
IE处理结论
□ 不予变更(原因如上) 变更前工时 分钟
□ 变更(具体如下) 变更工时(加)(减) 分钟
签名: □ 批量变更(见附表) 变更后工时 分钟
生产处理意 见 签名: 依: □ IE处理结论 核准意见 □其它: 签名: 责任部门: □工艺科 □生产部 □开发项目组 □ 生产处理意见
标准工时异常反馈&变更通知单
发自: 发往: 主题: 工单单号 生产总数 异常类型 产品品号 起始时间 结束时间 产品名称 预计共损耗工时 小时
□ 工(治)具主变更
□工艺科
项目组
□ 设计变更 □ 材质变化影响 □ 工艺变化 □ 其它 □ 持续10批低于标准工时20%或高于标准工时10%时
总装工厂异常工时分析报告
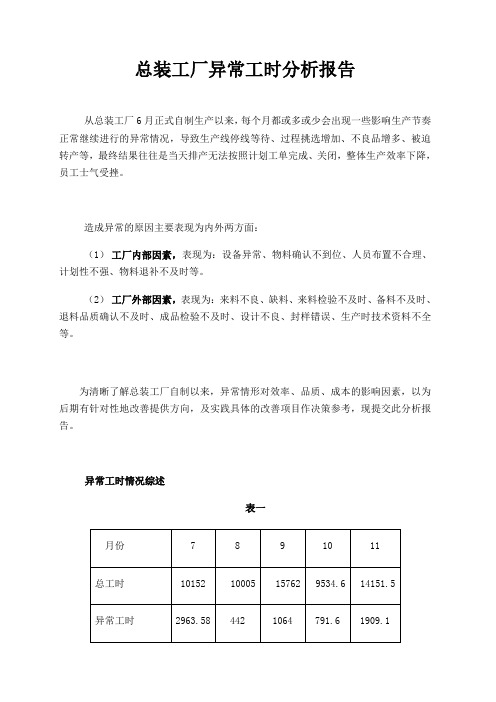
总装工厂异常工时分析报告从总装工厂6月正式自制生产以来,每个月都或多或少会出现一些影响生产节奏正常继续进行的异常情况,导致生产线停线等待、过程挑选增加、不良品增多、被迫转产等,最终结果往往是当天排产无法按照计划工单完成、关闭,整体生产效率下降,员工士气受挫。
造成异常的原因主要表现为内外两方面:(1)工厂内部因素,表现为:设备异常、物料确认不到位、人员布置不合理、计划性不强、物料退补不及时等。
(2)工厂外部因素,表现为:来料不良、缺料、来料检验不及时、备料不及时、退料品质确认不及时、成品检验不及时、设计不良、封样错误、生产时技术资料不全等。
为清晰了解总装工厂自制以来,异常情形对效率、品质、成本的影响因素,以为后期有针对性地改善提供方向,及实践具体的改善项目作决策参考,现提交此分析报告。
异常工时情况综述表一异常工时比例29%4%7%8%13%图一分析总装工厂各月份的异常工时比例都比较高,而且从8月份开始异常工时呈现逐月增长的趋势。
随着生产产量的提升,异常工时将会是影响生产的主要因素。
换句话说,减少异常工时也是提升效率的一种有效手段。
一、异常不良原因分析表二7月异常原因来料不良缺料其它——异常工时比例20% 77% 4% ——8月异常原因来料不良缺料机器故障——异常工时比例37% 45% 18% ——分析:各月份中,因为缺料停产的比例每个月都是最高的,且比例都超过了30%以上,其次为来料不良,这些异常都属于工厂外部原因造成。
缺前段工序的物料(如支架的电源线、绝缘纸、铝条等,吸顶灯的底盘、海绵条、箭头标贴等)会导致整条生产线停产,损失工时量较大。
线体异常工时分布表三吸顶灯2079 324.9 195 408.5 522.2 支架348 112.5 814 351.5 1334 吹塑536.5 5 4 30 52.5图二图三分析:从图二和图三可以看出,吸顶灯和支架的异常工时和比例都较高,平均异常工时比例占班组总工时的8%至9%左右,吹塑的异常工时相对比较平稳,但也在呈逐月上升的趋势。
异常工时
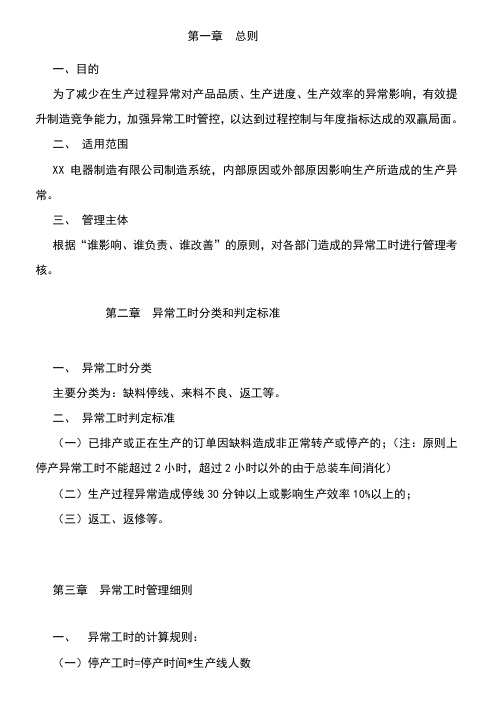
第一章总则一、目的为了减少在生产过程异常对产品品质、生产进度、生产效率的异常影响,有效提升制造竞争能力,加强异常工时管控,以达到过程控制与年度指标达成的双赢局面。
二、适用范围XX电器制造有限公司制造系统,内部原因或外部原因影响生产所造成的生产异常。
三、管理主体根据“谁影响、谁负责、谁改善”的原则,对各部门造成的异常工时进行管理考核。
第二章异常工时分类和判定标准一、异常工时分类主要分类为:缺料停线、来料不良、返工等。
二、异常工时判定标准(一)已排产或正在生产的订单因缺料造成非正常转产或停产的;(注:原则上停产异常工时不能超过2小时,超过2小时以外的由于总装车间消化)(二)生产过程异常造成停线30分钟以上或影响生产效率10%以上的;(三)返工、返修等。
第三章异常工时管理细则一、异常工时的计算规则:(一)停产工时=停产时间*生产线人数(二)非正常转产工时=转产时间*生产线人数注:转产时间=最后一台产品下线到下一机型第一台产品下线的时间(转产时间在30分钟内不计)(三)物料全选或加工工时=挑选或加工时间*参与挑选或加工人数(四)效率损失工时=(标准产出-实际产出)/标准产出*生产时间*生产线人数(五)返工工时=返工时间*返工人数二、各类异常工时的界定细则(一)采购员(供应商)造成的异常工时1、由于欠料或来料不及时(包括未及时进仓)而导致生产线停产或非正常转产的异常工时(设计原理:采购员必须从发出订单开始,跟踪到物料合格上线);2、物料需生产线挑选或加工后方可生产的,从而造成降低生产效率或占用人力的异常工时。
注:所有供应商造成的异常工时均属于采购员责任,并纳入采购中心异常工时考核;(二)生产管理中心造成的异常工时1、计划排产不合理导致生产线无法正常安排生产导致的异常;2、计划变更未及时通知相关部门造成的生产异常;(三)前工序车间(冲压车间&喷涂车间&焊接车间)造成的异常工时1、由于前工序车间未能及时生产提供物料而造成生产线停产或非正常转产所产生异常工时;2、前工序车间的物料需生产线挑选或加工后方可生产的,从而造成降低生产效率或占用人力的异常工时。
异常工时报告

填写
批准
会签
事业部
管理部
总裁办
备注
1、发生异常第一时间应通报责任部门,以及责任判定部门确认。 2、异常判定由工程部(必要时也可增加品质部)承担。 3、异常判定后,异常责任部门必须配合确认并签字。
发 文
客户名称
异常工时报告
表单编号:HTIT-IM-GL-FM-0027 版本:A0
报告编号:
.
型号
品名规格
工单号
订单数量
异常时间
口停工待料 口设备故障 口计划临时变更 口成品批退返工 异常类别
口物料不良挑选 口不良返修 口停电 口停气 口其它
口品质异常 .
异常原因描述(因为什么停线?造成停线时间段?多少人xH=?H)
原因描述:
拉长:
生产主管:
生产经理:
事业部副总:
异常 归类
口换线 口停线待料
口停线放假
口其它
口限度生产(口挑选 口返工 口直接限度生产)
工程部确认
责任 外部:口客户 口项目 口PMC 口采购 口供应商 口销售 口品保
判定 内部:口品质部 口工程部 口PMC 口仓库 口其它
.
责任部门确认:
原
异常工时管理规范(含表格)
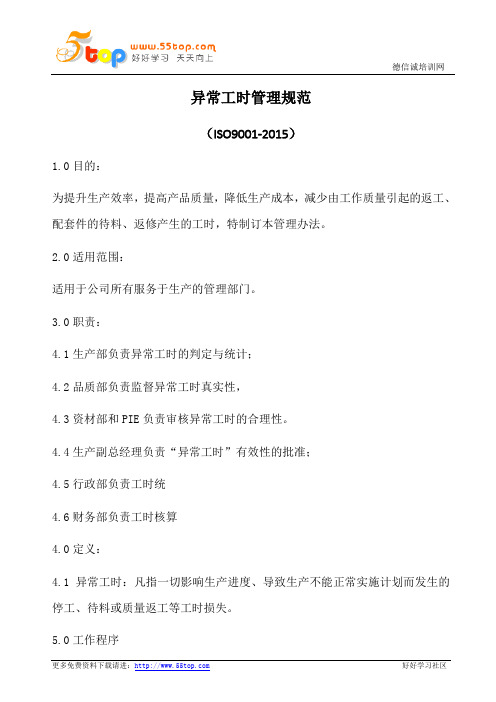
异常工时管理规范(ISO9001-2015)1.0目的:为提升生产效率,提高产品质量,降低生产成本,减少由工作质量引起的返工、配套件的待料、返修产生的工时,特制订本管理办法。
2.0适用范围:适用于公司所有服务于生产的管理部门。
3.0职责:4.1生产部负责异常工时的判定与统计;4.2品质部负责监督异常工时真实性,4.3资材部和PIE负责审核异常工时的合理性。
4.4生产副总经理负责“异常工时”有效性的批准;4.5行政部负责工时统4.6财务部负责工时核算4.0定义:4.1异常工时:凡指一切影响生产进度、导致生产不能正常实施计划而发生的停工、待料或质量返工等工时损失。
5.0工作程序5.1异常的处理5.1.1生产部按生产计划排期提前到仓库领料并安排做首件并量产。
5.1.2生产部在生产过程中发现产品、物料与要求不符,生产的成品达不到标准要求或来料无法使用等现象,5分钟内上报部门负责人、工程、资材部、品质部等相关人员确认。
5.1.3工程部、品质部确认异常可接受,通知生产继续生产,如确认异常不能接收,则由生产部或品质IPQC在接到需特别加工或退货信息10分钟内开出《品质异常处理单》进行跟踪处理。
5.1.4经品质分析,给出初步分析结果,结果为工艺问题,设计问题,来料问题。
5.1.5由品质分析,如果需要返工或改变工艺则由工程部更改样品给品质部确认,品质判定方案可行后,工程必须在现场跟进指导产线员工作业方法。
品质判定是否符合要求,工程等员工生产出2件合格品后方可离开现场,品质部跟踪监控过程确认。
5.1.6如果确认是来料问题,按照解决方案的意见,找供应商沟通协助处理或由我司加工挑选扣除供应商相应费用并要求在一个工作日内对来料问题给予回复处理意见(临时解决办法),生产部要给予相应的配合,和支持。
同时品质应协助。
5.1.7如果由于制程异常原因造成的,则由相关责任部门协助处理。
5.1.8待工,返工工时,由生产线记录,并填定在《车间导常工时申报表》,并在当天的《生产日报表》上备注。
异常工时

第一章总则一、目的为了减少在生产过程异常对产品品质、生产进度、生产效率的异常影响,有效提升制造竞争能力,加强异常工时管控,以达到过程控制与年度指标达成的双赢局面。
二、适用范围XX电器制造有限公司制造系统,内部原因或外部原因影响生产所造成的生产异常。
三、管理主体根据“谁影响、谁负责、谁改善”的原则,对各部门造成的异常工时进行管理考核。
第二章异常工时分类和判定标准一、异常工时分类主要分类为:缺料停线、来料不良、返工等。
二、异常工时判定标准(一)已排产或正在生产的订单因缺料造成非正常转产或停产的;(注:原则上停产异常工时不能超过2小时,超过2小时以外的由于总装车间消化)(二)生产过程异常造成停线30分钟以上或影响生产效率10%以上的;(三)返工、返修等。
第三章异常工时管理细则一、异常工时的计算规则:(一)停产工时=停产时间*生产线人数(二)非正常转产工时=转产时间*生产线人数注:转产时间=最后一台产品下线到下一机型第一台产品下线的时间(转产时间在30分钟内不计)(三)物料全选或加工工时=挑选或加工时间*参与挑选或加工人数(四)效率损失工时=(标准产出-实际产出)/标准产出*生产时间*生产线人数(五)返工工时=返工时间*返工人数二、各类异常工时的界定细则(一)采购员(供应商)造成的异常工时1、由于欠料或来料不及时(包括未及时进仓)而导致生产线停产或非正常转产的异常工时(设计原理:采购员必须从发出订单开始,跟踪到物料合格上线);2、物料需生产线挑选或加工后方可生产的,从而造成降低生产效率或占用人力的异常工时。
注:所有供应商造成的异常工时均属于采购员责任,并纳入采购中心异常工时考核;(二)生产管理中心造成的异常工时1、计划排产不合理导致生产线无法正常安排生产导致的异常;2、计划变更未及时通知相关部门造成的生产异常;(三)前工序车间(冲压车间&喷涂车间&焊接车间)造成的异常工时1、由于前工序车间未能及时生产提供物料而造成生产线停产或非正常转产所产生异常工时;2、前工序车间的物料需生产线挑选或加工后方可生产的,从而造成降低生产效率或占用人力的异常工时。
异常工时单

以上工时由处理部门进行核算
小计
合计金
额:
万
千百 拾
元
角
分
备注:异常工时费用统一按每小时25元人民币收取,财务部根据责任归属在结算货款时扣 除。
责任归
属 □供应商:
填表: 品质部确认: 供应商确认:
□责任部门:
生产部确认:
工程部确认:
采购部确认:
总经理批准:
Байду номын сангаас
财务部签收:
产品型 号
生产异常工时单
数量
日期
□ □ □ □ □ □ 异常类
资料错误 检验错误 物料异常 生产错误 生产质量异常 客户
型 质量投诉
异常描 述
处理方 法
□挑选
□加工
□返工(检查外观和检测功能)
材料名称
数量 单价 金额(元)
耗物料 名细
以上物料损耗金额由采购部进行核算
小计
损耗工 时名细
处理流程/工序
小时 单价 金额(元)
- 1、下载文档前请自行甄别文档内容的完整性,平台不提供额外的编辑、内容补充、找答案等附加服务。
- 2、"仅部分预览"的文档,不可在线预览部分如存在完整性等问题,可反馈申请退款(可完整预览的文档不适用该条件!)。
- 3、如文档侵犯您的权益,请联系客服反馈,我们会尽快为您处理(人工客服工作时间:9:00-18:30)。
以上工时由处理部门进行核算
小计
合计金额:
万
千
百
拾
元
角
分
备注:异常工时费用统一按每小时25元人民币收取,财务部根据责任归属在结算货款时扣除。
责任归属
□供应商:□责任部门:
填表:Βιβλιοθήκη 生产部确认:工程部确认:品质部确认:
采购部确认:
总经理批准:
供应商确认:
财务部签收:
生产异常工时单
深圳市电子有限公司
生产异常工时单
产品型号
数量
日期
异常类型
□资料错误□检验错误□物料异常□生产错误□生产质量异常□客户质量投诉
异常描述
处理方法
□挑选□加工□返工(检查外观和检测功能)
损耗物料名细
材料名称
数量
单价
金额(元)
以上物料损耗金额由采购部进行核算
小计
损耗工时名细
处理流程/工序
小时
单价