圆钢成品缺陷
圆钢常见缺陷及原因

调整成品前料型正确
6
折叠
沿轧制方向呈直线状分布,外形似裂纹,边缘有时呈锯齿状,连续或断续分布,深浅不一,内有氧化铁皮,在横断面上看,一般呈折角
1、前某一道次出耳子
2、前某道次产生划伤、轴错、轧槽损坏或磨损严重、飞边等
3、原料表面有尖锐棱角或裂纹
检查前部道次料型和原料情况
消除前道次缺陷
检查轧槽磨损情况,酌情换槽
2
结疤
一般呈舌形或指甲形,宽而厚的一端和基体相连;有时其外形呈一封闭的曲线,嵌在钢材表面上。
1、前一孔型轧槽损坏破损或磨损严重。
2、外界金属落在轧件上被带入孔型,压入钢材表面。
3、前一道次轧件表面有深度较大的凹坑。
检查前一道次孔型的磨损程度及轧件表面有无大的凹坑
3
耳子
出现于成品的两旁辊缝处,呈平行于轴线的突起条状。有两侧耳子、单侧耳子、全长出耳、局部出耳和周期出耳等
1、孔型设计不良,宽展估计过小
2、成品前料型高度较大
3、成品孔辊缝小
4、终轧温度低,宽展增加
5、成品导板安装不正、尺寸大或磨损严重
6、横梁或导板盒松动
7、轧槽更换错误或轧机轴承损坏
修改孔型
压下成品前料,减小辊缝
放大成品辊缝
压K2高度
更换导轮减小夹铁宽度
固定横梁及导板盒
换槽或换辊
4
弯曲
有头部弯曲、局部弯曲、全长弯曲等
1、出口导卫安装过高或过低
2、温度不均
3、上下辊径差过大
4、连接轴丢转
5、冷床拨爪不齐
调整导卫合适
调整钢温均匀
换辊
更换连接轴
调整拨爪一致
5
扭转
绕纵轴呈螺旋状旋转
圆钢剪切缺陷原因分析及改进措施
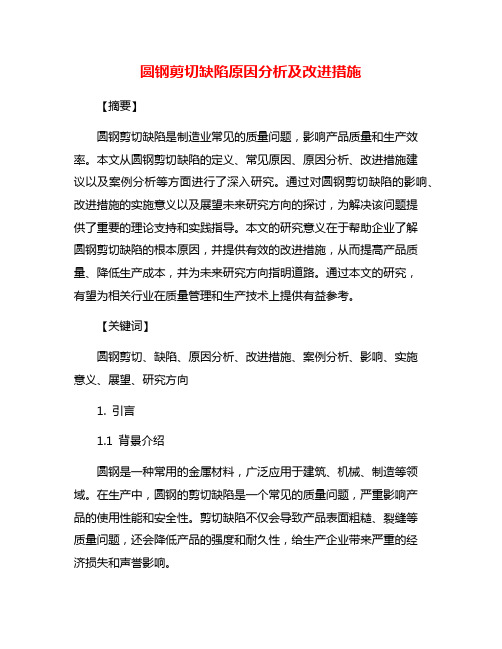
圆钢剪切缺陷原因分析及改进措施【摘要】圆钢剪切缺陷是制造业常见的质量问题,影响产品质量和生产效率。
本文从圆钢剪切缺陷的定义、常见原因、原因分析、改进措施建议以及案例分析等方面进行了深入研究。
通过对圆钢剪切缺陷的影响、改进措施的实施意义以及展望未来研究方向的探讨,为解决该问题提供了重要的理论支持和实践指导。
本文的研究意义在于帮助企业了解圆钢剪切缺陷的根本原因,并提供有效的改进措施,从而提高产品质量、降低生产成本,并为未来研究方向指明道路。
通过本文的研究,有望为相关行业在质量管理和生产技术上提供有益参考。
【关键词】圆钢剪切、缺陷、原因分析、改进措施、案例分析、影响、实施意义、展望、研究方向1. 引言1.1 背景介绍圆钢是一种常用的金属材料,广泛应用于建筑、机械、制造等领域。
在生产中,圆钢的剪切缺陷是一个常见的质量问题,严重影响产品的使用性能和安全性。
剪切缺陷不仅会导致产品表面粗糙、裂缝等质量问题,还会降低产品的强度和耐久性,给生产企业带来严重的经济损失和声誉影响。
圆钢剪切缺陷的产生原因复杂多样,可能涉及原材料质量、生产工艺、设备状况等多个方面。
为了提高圆钢的质量和生产效率,减少剪切缺陷对产品质量的影响,有必要对圆钢剪切缺陷的原因进行深入分析,提出有效的改进措施。
本文将针对圆钢剪切缺陷的定义、常见原因、原因分析、改进措施建议以及案例分析等方面展开讨论,旨在为相关生产企业提供参考和借鉴。
通过对圆钢剪切缺陷的研究,不仅可以提高产品质量,还可以提升生产效率,促进产业升级和转型发展。
1.2 研究意义研究圆钢剪切缺陷的意义在于提高生产效率和产品质量,减少浪费和损失。
通过深入分析圆钢剪切缺陷的原因和改进措施,可以及时发现和解决生产中出现的问题,提高生产线的稳定性和可靠性,进而提升产品的竞争力和市场占有率。
2. 正文2.1 圆钢剪切缺陷的定义圆钢剪切缺陷是指在圆钢剪切过程中出现的各种问题和缺陷,例如断面不平整、锯齿状边缘、裂纹等现象。
圆钢常见缺陷及原因

序号
名称
特征
形成原因
消除方法
1
划伤
一般呈直线型沟痕,可见沟底,长度由肉眼刚刚可见到几毫米不等,长度自几毫米至几米不等,可断续分布,也可能通长分布
1、导卫表面不光滑,有毛刺或磨损严重。
2、滚动导轮不转或磨损严重
3、翻钢板表面不光滑刮伤
4、在运输过程中辊道盖板等刮伤
在造成划伤的地方,过钢时常出现火花,并可以找到残留的丝状金属,据此可以找到原因,然后根据情况进行处理
1、孔型设计不良,宽展估计过小
2、成品前料型高度较大
3、成品孔辊缝小
4、终轧温度低,宽展增加
5、成品导板安装不正、尺寸大或磨损严重
6、横梁或导板盒松动
7、轧槽更换错误或轧机轴承损坏
修改孔型
压下成品前料,减小辊缝
放大成品辊缝
压K2高度
更换导轮减小夹铁宽度
固定横梁弯曲、全长弯曲等
调整温度均匀
调整成品前料型正确
6
折叠
沿轧制方向呈直线状分布,外形似裂纹,边缘有时呈锯齿状,连续或断续分布,深浅不一,内有氧化铁皮,在横断面上看,一般呈折角
1、前某一道次出耳子
2、前某道次产生划伤、轴错、轧槽损坏或磨损严重、飞边等
3、原料表面有尖锐棱角或裂纹
检查前部道次料型和原料情况
消除前道次缺陷
检查轧槽磨损情况,酌情换槽
1、出口导卫安装过高或过低
2、温度不均
3、上下辊径差过大
4、连接轴丢转
5、冷床拨爪不齐
调整导卫合适
调整钢温均匀
换辊
更换连接轴
调整拨爪一致
5
扭转
绕纵轴呈螺旋状旋转
1、轧辊不平行或有轴向窜动
圆钢剪切缺陷原因分析及改进措施

圆钢剪切缺陷原因分析及改进措施圆钢是一种常见的金属材料,广泛应用于机械制造、建筑工程、汽车制造等领域。
在生产过程中,圆钢剪切缺陷是一个常见的问题,不仅会影响产品质量,还可能导致安全事故。
对圆钢剪切缺陷的原因进行分析,并提出改进措施,具有重要的实际意义。
一、圆钢剪切缺陷的原因分析1. 设备问题:圆钢剪切过程中使用的设备如果存在磨损、老化或者不合理的设计,都会导致剪切缺陷的产生。
比如刀具磨损不均匀、切割速度过快等问题都可能引起剪切缺陷。
2. 材料问题:圆钢的质量和性能会直接影响到剪切的效果,如果材料本身存在缺陷或者不符合标准要求,也会导致剪切缺陷的产生。
比如材料硬度不均匀、内部夹杂物等都可能引起剪切不良。
3. 操作问题:操作人员的技术水平和工作细节也是引起剪切缺陷的重要原因之一。
比如操作不规范、工作失误、操作疏忽等都可能导致剪切不良。
4. 环境问题:生产环境的干扰和影响也会对剪切缺陷产生影响。
比如温度、湿度、粉尘等环境因素都可能引起剪切不良。
二、圆钢剪切缺陷的改进措施1. 加强设备维护:定期对剪切设备进行检查和维护,确保刀具的锋利度和机器的正常运行。
对设备进行合理的调整和改进,能够提高剪切的效果。
2. 优化材料选择:对圆钢的材料选择和采购过程进行严格把控,保证材料的质量和性能符合标准要求。
对材料的质量进行检测,排除有缺陷的材料。
3. 加强操作培训:提高操作人员的技术水平和工作细节,确保操作的规范和精准。
对操作人员进行相关知识和技能的培训,提高其对剪切工艺的认识和理解。
4. 控制生产环境:加强生产现场的管理,保证生产环境的整洁、安全和稳定。
对生产环境的温度、湿度等参数进行严格的控制,减少外部环境对剪切的影响。
三、结语圆钢剪切缺陷是一个需要引起重视的问题,只有通过对其产生原因进行深入分析,并采取相应的改进措施,才能够有效地解决这一问题。
通过加强设备维护、优化材料选择、加强操作培训和控制生产环境等措施,可以有效地减少圆钢剪切缺陷的产生,提高产品的质量和安全性。
圆钢剪切缺陷原因分析及改进措施

圆钢剪切缺陷原因分析及改进措施工业是我国第二产业,在社会经济发展中占据着重要的经济地位。
而钢和铸铁则是工业中应用最广泛的金属材料。
在钢铁具体的生产工艺中,存在着一定的缺陷。
本文对造成圆钢剪切缺陷的原因进行分析,并提出相应的改进措施。
标签:剪切;缺陷;原因;改进措施小棒线是上世纪90年代末投入生产,冷床后使用冷剪将棒材切成不同长度的定尺,在用冷剪进行剪切时,圆钢在剪切端面质量很容易出现诸多类型的剪切缺陷,而其中最重要的剪切缺陷则是圆钢剪切裂纹。
1 小棒线生产工艺简介小棒线采用的坯料断面为150 mm×150mm×9000mm 连铸坯一火成材,或者采用130×150mm×9000mm 轧制坯二火成材工艺。
小棒线生产规格为Φ13mm~Φ60mm直条棒材,定尺的长度是4~12m。
主导产品轴承钢、齿轮钢、弹簧钢、易切削非调质钢、优质碳素结构钢、合金结构钢、锚链及系泊链钢、高压及油井管坯等钢种广泛应用于汽车、工程机械、铁路、石油和矿山、船舶和海洋工程、军工等领域。
全线共18架短应力轧机与4架减定径轧机,并以单线无扭连续布置,最大的轧制速度可达每秒18米;采用12.5*120m 步进式冷床;定尺剪使用450吨冷剪。
2 圆钢剪切缺陷原因分析小棒线出冷床后通过梳形器引导轧件顺利进行孔型剪刃定尺剪切,剪切过程中出现端部剪切质量缺陷,增加了后部处理,容易产生质量隐患,使生产成本、产品形象都产生影响[1]。
2.1 端部剪切弯曲原因分析在剪切低碳钢时如20#钢、20CrMo等,在端部剪切端部容易使端部产生弯曲,此弯曲锯端部长约100~200mm,弯曲度超过4‰,超过国标要求。
矫直机也无法进行矫直,只能通过后部二次锯切进行处理,增加了后续处理成本。
2.2 端部毛刺原因分析首先,由于剪切刀片之间存在过大的缝隙,使得钢材在接受剪切的过程中发生了滑移,进而从缝隙中带出了舌头状的毛刺。
其次,在采用平剪剪切工藝时,受到轧件弯曲的影响,使得压扁的金属体积沿着轧件纵向堆积在了剪刃口处,并最终造成轧件在剪切时发生分离撕裂形成毛刺。
圆钢质量缺陷及其优化

的质量情况 ,在 了解零件加工工艺后 ,我们对 数量大 、出现频次高 的缺陷组织开展攻关 ,希
望制 定有 效 的措施 予 以解决 。
产生原因 : ()在高温 区可能产生划伤位 1 置和工序 :由于导卫装置加工不 良,安装偏斜 , 磨损严重 ,或粘有氧化铁皮而造成的划伤 ;活
同的刮 伤源 ,通过合理 优化工艺 ,改进设备 , 从根源上解决刮伤隐患,具体措施 : ()对导 1 卫板进行打磨处理 ,要求 内腔必须光滑 ,优化
规 范 导 卫 安装 方 法 ,同时 ,重 新 设 计 出 口导 卫 形 式 ,采 用 倒 喇 叭 口形 状 。 以上 无 法 解 决 的 问 题 ,则 采 用 出 口导 轮装 置 进 行 扶 持 导 正 。 () 2 重 新 设 计 中间 导槽 和导 板 ,采 用 可 调 宽度 式 立 轮 装 置 对 圆钢进 行 引导 ,消 除 轧 件 运 输 过 程 中 辊 道侧 壁 对轧 件 的刮 伤 。 () 中 间输 送辊 道 平 3
产 品表 面 的检 查 。
圆钢加工后零件表面强度是影响疲劳强度
黩
的 重要 因 素 。表 面热 处 理 和 表 面 冷 塑 性 形 变 加
陷
_
i ■
优化措施 : ( 1 )完善孔 型设计 ,加强轧制
调 整 及 存 在 的 规 范 性 ; () 提 高 钢 坯 加 热 质 2 量 ;经常 检查 料 形 尺寸 ; () 寻 找合 理 张力 的 3 参 数 ; () 检 查 导 卫 情 况 ; () 加 大 检 验 力 4 5 度 ,及 时发 现 问题 并及 时解 决 。
工对提高疲劳强度 十分 有效 ,因此我 们也对用
圆钢剪切缺陷原因分析及改进措施

圆钢剪切缺陷原因分析及改进措施圆钢是工程领域中常用的一种材料,但在生产过程中容易出现缺陷,其中剪切缺陷是一种较为常见的现象,剪切缺陷会对材料的性能和安全产生不良影响,因此对圆钢剪切缺陷的原因进行分析并采取改进措施具有一定的实践意义。
1.材料本身问题圆钢本身存在裂纹、夹杂物等缺陷,这些缺陷在剪切过程中可能会放大,导致剪切缺陷的产生。
2.剪切刃口形状问题刀口受到磨损影响后,可能会导致刀口直径变小,切割角度过大等问题,这些问题会影响圆钢的切口质量,从而形成剪切缺陷。
3.操作人员技术问题操作人员的技术水平和操作技巧可能会影响到圆钢的切割质量,过大的切割力、不当的切割速度和切割频繁会导致剪切缺陷的发生。
4.设备问题如果设备的切割机械结构设计不合理、维护不当或者自身存在故障,那么就会对圆钢剪切质量产生影响,进而导致剪切缺陷的产生。
1.选择优质材料针对圆钢本身存在的缺陷,选择高质量的材料,可以有效地降低缺陷的产生率。
2.注意保养切割设备定期对设备进行保养维护,确保设备在工作过程中处于最佳状态可以有效地避免因设备自身问题而引起的剪切缺陷。
3.控制切割力度控制好切割力度,避免过度施力,可以有效降低剪切缺陷的产生率。
4.正确操作设备操作人员需要接受专业培训,熟悉设备的使用方法和操作要点,减少人为操作失误引起的问题。
5.升级及更新设备增加设备的实用性和更新率,使用性能更佳的高新技术设备直接影响圆钢剪切质量的提高,从而降低剪切缺陷的发生率。
三、结论经过分析,圆钢剪切缺陷的形成原因是比较复杂和多方面的。
解决剪切缺陷的关键是全面分析原因,有针对性地采取科学的改进措施,不断优化设备、人员和材料等方面的问题,提高圆钢的切割质量,使其达到更高的使用效果和性能。
圆钢剪切缺陷原因分析及改进措施

圆钢剪切缺陷原因分析及改进措施圆钢剪切是指将圆钢进行切割加工,常用于机械零配件的加工生产中。
然而在实际生产中,常常会出现一些圆钢剪切缺陷,如切口不规整、切口处出现裂纹等,影响了产品的质量和使用效果。
对圆钢剪切缺陷的原因进行分析,并采取改进措施,是非常必要的。
本文将对圆钢剪切缺陷原因进行分析,并提出相应的改进措施。
一、圆钢剪切缺陷原因分析1.刀具磨损严重圆钢剪切过程中,刀具的磨损情况直接影响着切口的质量。
如果刀具磨损严重,就会导致切口不规整、出现裂纹等缺陷。
刀具磨损的原因主要是由于切割过程中的摩擦和磨损,以及刀具材质的选择不当等。
2.切割速度过快在圆钢剪切过程中,切割速度过快会导致切口处温度升高,从而引起材料的退火现象,造成形变或裂纹。
切割速度过快还会导致刀具与工件之间产生的摩擦增大,刀具的使用寿命减少,造成切口质量不佳。
3.材料质量不良圆钢在生产过程中,如果材料自身质量不良,比如含有太多的夹杂物、气泡或者杂质,会导致切口处出现裂纹或不规整的情况。
材料的硬度、韧性不匹配,也会影响切口的整体质量。
4.切削工艺参数不当切削工艺参数不当可能是导致圆钢剪切缺陷的另一个重要原因。
刀具的切削角度、切割深度、进给速度等参数的选择不当,都会导致切口质量不佳。
二、改进措施1.选用优质刀具为了避免刀具磨损导致的切口质量不佳,可以选择质量较好的刀具进行剪切加工。
常用的刀具材料有高速钢、硬质合金等,可以根据实际生产需要选用合适的刀具材料,延长刀具的使用寿命,提高切口质量。
在进行圆钢剪切时,需要对切割速度进行适当控制,避免过快的切割速度导致切口处温度升高,从而影响切口的质量。
可以根据材料的硬度、切割深度等因素进行合理的速度选择,确保切口质量。
在生产加工之前,对圆钢的材料质量进行严格检测,确保材料质量良好。
可以采用超声波探伤、X射线检测等技术手段,排除不良材料的使用,从而避免材料质量不良导致的切口质量问题。
对于切削工艺参数不当导致的切口质量问题,可以利用专业的数控设备,进行优化切削工艺参数的选择。
圆钢轧制缺陷分析与处理
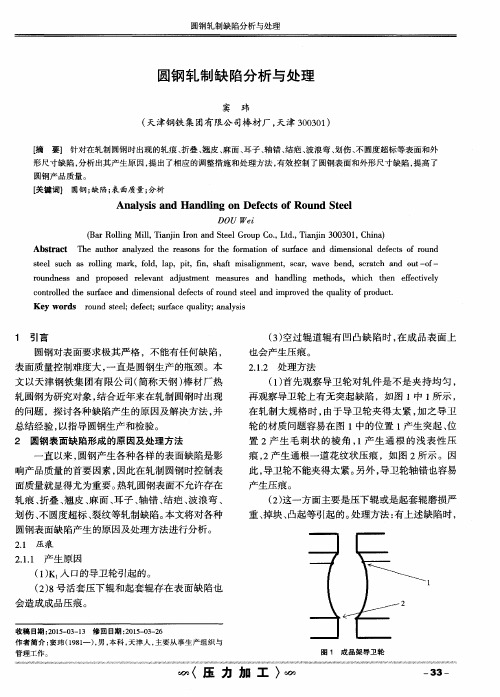
形尺寸缺 陷, 分析出其产 生原 因 , 提 出了相应 的调整措施 和处理方法 , 有效控制 了圆钢表 面和外形 尺寸缺陷 , 提高 了
圆钢 产 品质 量 。
【 关键词】 圆钢 ; 缺 陷; 表面质 量; 分析 An a l y s i s a n d Ha ndl i ng o n De f e c t s o f Ro un d St e e l
直以来 , 圆钢产生各种各样 的表面缺陷是影
响产品质量 的首要因素 , 因此在轧制圆钢时控制表
面质量 就显 得尤 为重 要 。 热轧 圆钢 表 面不允 许存 在 轧痕 、 折叠 、 翘皮 、 麻面 、 耳子 、 轴错 、 结疤 、 波浪 弯 、 划伤 、 不 圆度超标 、 裂 纹等 轧制 缺 陷。 本 文将 对各 种 圆钢表 面 缺 陷产 生 的原 因及处 理方 法进 行分 析 。
( 2 ) 8 号活套压下辊和起套辊存在表面缺陷也
会 造成 成 品压 痕 。
收稿 日期 : 2 0 1 5 — 0 3 — 1 3 修 回日期 : 2 0 1 5 — 0 3 — 2 6
作者简 介 : 窦 玮( 1 9 8 1 一) , 男, 本科 , 天津人 , 主要从 事生产组 织与
DoU We i
( B a r R o l l i n g Mi l l , T i a n j i n I r o n a n d S t e e l G r o u p C o . , L t d . , T i a n j i n 3 0 0 3 0 1 , C h i n a )
圆钢 轧制缺 陷分析与处理
圆钢 轧 制缺 陷分 析 与 处 理
窦 玮
( 天津钢铁集团有限公司棒材厂 , 天津 3 0 0 3 0 1 )
圆钢产品主要缺陷和产生原因六翘皮

6.1缺陷特征在圆钢的表面基本沿轴线方向上出现的有规律或无规律分布,形状有成鱼鳞或指甲状的痕迹或翘起的薄皮。
一般来讲,缺陷的顶部或尖端和轧制延伸的方向一致。
缺陷的尾部大多和圆钢的基体相连。
当翘皮被轧制得很薄时,其尖端部分可出现翘起,或用工具很容易的翘起,形成表面损伤。
在自然光下用放大镜观察,可以看到缺陷的边缘实际是明显的连续裂纹。
酸洗后可以用肉眼明确看出。
沿轧制方向将缺陷剖开,经过抛光后在100倍显微镜下观察,有的可以看到非金属夹杂物的分布和缺陷的关系,这是分辨缺陷产生因素比较关键的手段之一。
一般来讲,圆钢轧制过程中由于机械因素导致轧件表面形成破损而出现局部金属堆积,并在其后又被压入而形成的翘皮缺陷,在显微镜下,缺陷的根部干净,和非金属夹杂物的分布无关。
而在连铸坯生产过程中由于皮下气泡等铸造缺陷导致的翘皮缺陷,都可以看到非金属夹杂物分布和缺陷的产生有直接关系。
一般车削用圆钢,当翘皮的深度不超过国家标准规定的公差之半时,一般不影响使用。
翘皮缺陷拉拔用圆钢很大影响。
在冷拉拔过程中,翘起的金属颗粒会在拉拔磨具的润滑区或工作区积聚,使拉拔后圆钢(钢丝)表面损坏。
对于冷镦用的圆钢,翘皮是不允许出现得缺陷之一。
特别是由连铸坯缺陷形成的翘皮。
在冷镦过程中,由于缺陷造成的表面损坏和应力集中,将直接造成冷镦开裂,出现废品。
6.2 产生原因轧制过程中的机械损伤:a导卫装置加工不善和安装不良,活套有尖锐棱角,刮伤轧件表面形成点状金属堆积,在下一轧制道次中被压入基体;b输送辊道或导槽表面粗糙,刮伤轧件表面形成点状金属堆积,再轧后造成翘皮;c轧槽磨损严重,轧件在孔型内打滑;刮伤轧件表面形成点状金属堆积并在下一轧制道次中被压入基体。
连铸坯缺陷a.原料表面精整不良,凹坑深度比较大;b.原料内部有较大的皮下气泡,轧制后破裂形成翘皮。
圆钢剪切缺陷原因分析及改进措施
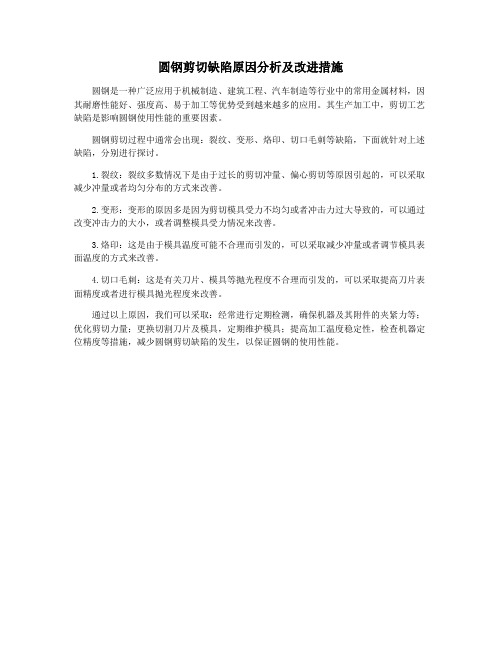
圆钢剪切缺陷原因分析及改进措施
圆钢是一种广泛应用于机械制造、建筑工程、汽车制造等行业中的常用金属材料,因其耐磨性能好、强度高、易于加工等优势受到越来越多的应用。
其生产加工中,剪切工艺缺陷是影响圆钢使用性能的重要因素。
圆钢剪切过程中通常会出现:裂纹、变形、烙印、切口毛刺等缺陷,下面就针对上述缺陷,分别进行探讨。
1.裂纹:裂纹多数情况下是由于过长的剪切冲量、偏心剪切等原因引起的,可以采取减少冲量或者均匀分布的方式来改善。
2.变形:变形的原因多是因为剪切模具受力不均匀或者冲击力过大导致的,可以通过改变冲击力的大小,或者调整模具受力情况来改善。
3.烙印:这是由于模具温度可能不合理而引发的,可以采取减少冲量或者调节模具表面温度的方式来改善。
4.切口毛刺:这是有关刀片、模具等抛光程度不合理而引发的,可以采取提高刀片表面精度或者进行模具抛光程度来改善。
通过以上原因,我们可以采取:经常进行定期检测,确保机器及其附件的夹紧力等;优化剪切力量;更换切割刀片及模具,定期维护模具;提高加工温度稳定性,检查机器定位精度等措施,减少圆钢剪切缺陷的发生,以保证圆钢的使用性能。
圆钢成品主要缺陷

圆钢成品主要缺陷一、擦伤1、特征又称刮伤,、划痕,一般呈直线型沟痕,可见沟底,其深度自肉眼刚能看到至几毫米,长度自几毫米至几米以上,断续地或连续地出现于钢材的局部或全长,如图8——6图所示。
2、产生原因1)导卫加工不良,安装偏斜,磨损严重,或粘有氧化铁皮。
2)围盘边缘不光滑,轧件跳套时被刮伤。
3)钢材在生产运输过程中与粗糙的辊道、地板、冷床等设备接触,均会造成擦伤。
3、消除方法在造成擦伤的地方,过钢时,常会出现火花,并可找到残留的丝状金属物,据此可找出产生擦伤的原因,再根据具体情况进行处理。
二、结疤1、特征一般呈舌头形或指甲形,其宽而厚的一端与钢材基体相连。
有时结疤外形呈一封闭曲线,嵌在钢材表面上,面积较大。
2、产生原因1)成品孔前某一孔型因故损坏或辊环破缺,当轧件通过改孔型后,表面形成凸块,再轧后,在成品表面上,产生周期性的生根结疤。
2)在轧制过程中,由于外界金属物落在轧件表面上,并被带入孔型内,压入轧件表面,在钢材表面形成结疤。
这种结疤是不生根的,无规律的。
3)轧件在孔型内打滑,使金属堆积于变形区周围的表面上,再轧时造成结疤。
4)轧槽刻痕不良,在轧件表面形成较高的凸块,再轧时,产生周期性的结疤。
5)钢锭表面有较大的冷溅、翻皮、结疤等缺陷,当用钢锭一次成材时,则在成品表面上产生结疤。
6)原料表面处理不当,留有尖锐的棱边或者说深宽比较大的凹坑,经轧制后形成结疤。
三、耳子1、特征耳子出现于圆钢成品的两旁辊缝处,呈平行于轴线的凸起条状。
有两侧出耳子、一侧出耳子、全长出耳子、局部出耳子和周期出耳子等多种情况。
两侧出耳如图8——7所示。
2、产生原因及消除方法1)两侧出耳(1)由于成品孔设计不当,对宽展估计过小,应修改孔型设计。
(2)由于K2(成品前孔)孔型磨损严重,无法压下,以致进入成品孔的轧件太大,应更换K2轧槽。
(3)由于K2辊缝过大,压下量太小,使进入成品孔的轧件大,应压K2。
(4)由于K1(成品孔)辊缝过小,压下量过大,应放K1。
圆钢剪切缺陷原因分析及改进措施

圆钢剪切缺陷原因分析及改进措施
圆钢剪切缺陷通常是由于材料本身的问题、操作不当或设备故障引起的。
以下是圆钢剪切缺陷的常见原因分析及改进措施。
1. 剪切时出现裂纹:这可能是由于材料强度不足、内部应力过大或材料含有过多杂质引起的。
改进措施包括:
- 选择具有良好强度的材料;
- 降低材料的内部应力,可以通过退火等热处理方式实现;
- 控制杂质含量,可以通过优化材料的制备工艺和环境来降低杂质的含量。
2. 剪切边缘出现毛刺:这主要是由于刀具磨损不均匀或刀具质量差引起的。
改进措施包括:
- 定期检查和更换刀具,确保刀具的锋利度;
- 选择质量可靠的刀具供应商,保证刀具的质量;
- 做好刀具的维护和保养工作,延长刀具的使用寿命。
3. 剪切边缘出现错位:这可能是由于设备调整不当或操作人员技术不熟练引起的。
改进措施包括:
- 设备操作前进行调整和校准,确保设备的切割位置准确;
- 加强对操作人员的培训,提高其操作技术和质量意识;
- 加强对设备维护和保养的管理,确保设备的正常运行和工作效率。
4. 剪切面出现不平整:这可能是由于设备刀口不平整或切割速度过快引起的。
改进措施包括:
- 定期检查和维护设备刀口,确保其平整度;
- 控制切割速度,避免过快过急,影响切割质量;
- 对于较高要求的工件,可以采用其他加工方式,如磨削等,以获得更好的切割质量。
圆钢剪切缺陷的原因和改进措施是多方面的,需要综合考虑材料、设备、工艺和操作等因素,以提高圆钢剪切的质量和效率。
圆钢剪切缺陷原因分析及改进措施

圆钢剪切缺陷原因分析及改进措施【摘要】本文旨在探讨圆钢剪切缺陷的原因分析及改进措施。
在将介绍研究的背景和目的。
正文将重点讨论圆钢剪切缺陷的概述,分析造成该缺陷的原因,并提出改进措施,包括加强生产管理和优化设备技术。
结论部分将总结改进措施带来的效果,并展望未来的发展方向。
通过这篇文章,读者将了解圆钢剪切缺陷的问题及相应的解决方案,为圆钢生产企业提供参考和指导。
【关键词】圆钢、剪切、缺陷、原因分析、改进措施、生产管理、设备技术、效果、展望1. 引言1.1 研究背景圆钢剪切是金属加工过程中常见的工艺之一,但在实际生产中常常会出现各种剪切缺陷,影响产品质量。
由于圆钢在建筑、汽车、机械等领域具有广泛的应用,因此圆钢剪切缺陷问题的解决显得尤为重要。
在实际生产中,圆钢剪切缺陷主要表现为裂纹、毛刺、变形等现象,这些缺陷不仅影响了产品的外观质量,还可能导致产品的功能性能下降,甚至对生产安全造成隐患。
对圆钢剪切缺陷进行深入研究,找出产生缺陷的原因,并提出有效的改进措施,对于提高产品质量、降低生产成本具有积极意义。
本文旨在通过对圆钢剪切缺陷的深入分析,探讨其产生的原因,并结合加强生产管理和优化设备技术等方面提出改进措施,期望能够取得一定的效果,提高圆钢剪切的质量和效率。
中,我们将重点探讨圆钢剪切缺陷的现状及对生产的影响,为后续的研究提供必要的背景支撑。
1.2 研究目的研究目的:本文旨在探讨圆钢剪切缺陷的原因分析及改进措施,以提高生产效率和产品质量。
通过深入分析圆钢剪切过程中可能出现的缺陷原因,找出造成这些问题的根源,从而制定有效的改进措施。
本研究旨在加强生产管理和优化设备技术,提高生产过程的可靠性和稳定性,减少圆钢剪切过程中的缺陷发生率,提升产品附加值。
通过对圆钢剪切缺陷改进效果的评估,为今后类似问题的解决提供参考和借鉴。
未来展望将进一步完善对圆钢剪切缺陷的探索,实现圆钢生产过程的持续改进和优化,为行业发展提供有益的参考依据。
棒线材常见表面缺陷及成因

棒线材常见表面缺陷及成因线材常见的表面缺陷有裂纹、耳子、折叠、结疤(翘皮或鳞皮)、划痕、麻面、分层、氧化及脱碳等。
表面缺陷最大的危害就是降低线材的断面收缩率等塑性指标,从而影响冷拉加工性能。
1裂纹裂纹是指线材表面沿轧制方向有平直或弯曲、折曲,或以一定角度向线材内部渗透的缺陷。
主要典型缺陷为表面细小裂纹簇、单道长条裂纹、平行裂纹等,如图1[1]。
表面裂纹簇形貌单道线缺陷形貌平行裂纹形貌图1典型裂纹形貌图表面裂纹的形成与钢的化学成分和炼钢、轧制控制均有关系[2]-[4]。
轧制方面的原因:①轧槽表面磨损或损坏;②粗轧前几道导位划伤;③氧化铁皮被轧入轧件;④导位尺寸不合适或偏离轧制线;⑤高压水除鳞的冷却水路堵塞或偏离;⑥错辊;⑦表面保护、吊装方法不当等储运过程中的擦伤。
冶炼方面的原因:钢坯上未消除的裂纹、皮下气泡及非金属夹杂物,它们都会在线材表面造成裂纹。
炼钢时钢液未得到净化,在连铸坯加工中形成皮下夹杂,轧前加热,表层氧化,皮下夹杂逐渐裸露,随后轧制中脱落形成裂纹。
2耳子线材表面沿轧制方向的凸起称为耳子,根据生成的位置可分为:单边耳子、双边耳子及错边耳子[3]-[7]。
图2是实际生产中的耳子[3]。
图2耳子耳子主要是由于轧制方面的原因引起的[2]-[7]。
轧制方面的原因:①过充满,坯料尺寸过大,压下量过大;②入口导卫偏离轧制线、磨损严重或烧坏;③上下辊偏移量不合适引起错辊;④轧件温度不均匀引起变形不均匀;⑤连轧机设置不当引起的堆钢、拉钢。
炼钢方面的原因:冶炼-铸造引起坯料的缩孔、偏析、分层及外来夹杂等,轧制时,影响正常变形,也会导致耳子的出现。
3折叠钢铁表面形成沿轧制方向的各种角度的折线,一般为在横断面与表面呈小角度交角状缺陷,两侧一般伴有脱碳层或部分脱碳层,中间常存在氧化铁夹杂,图3[3]是典型的折叠。
图3折叠轧件折叠的很大一部分原因是前面轧制时形成的各种耳子。
此外,轧辊轴向固定不佳发生窜动;入口导卫磨损严重或烧损时钢坯咬入不稳定;炼钢提供的坯料存在缺陷,未清理等也会导致折叠[2]-[5]、[7]。
三棒圆钢微裂纹、刮伤缺陷的检验与分析

产 ,现具备生产 1 4 m各个规格 的圆钢 6~ 0 m
能力 。
根 据 用 户 的质 量 反 馈 和 生 产 检 验 统 计 ,三 棒 生 产 的 圆钢 主 要 质 量 问题 :微 裂 纹 、刮 伤 、
耳子 、超椭 圆。其 中 ,耳子和超椭 圆比较容 易
检 测 出来 ;微 裂 纹 和 刮 伤 较 难 检 测 ,往 往 在 深 加 工 时 对 工 件 造 成 损 害 后 才 发 现 ,这 种 缺 陷 也
W U n Ya
( a n o lb t a t I s e t n a d d tr n t n fr mi r - a n c a c fr u d se l t e s a e a tru — s r c : n p ci n e e mi ai c o f w a d s r th o o n t e , h h p f p o o o l e s t n e t g a d a ay i meh d o ol g d f c sw r u e t g t si n n l ss t o fr l n ee t e e s mma ie n n r d c d i n i r da d it u e . z o Ke o d : Ro n a ; Mir - a yW r s u dB r c o f w; S r th; Up e t g T s ; Dee t l cac stn et i fcs
件 有影 响 。
象 ( 耳子) ,在下道次轧制时形成折叠 ;还有一
些 微 裂 纹 是 中 间道 次 轧 件 上 出现 较 深 的划 沟 或
轧件 “ 肉”等 因素形成 凹沟 ,经下道次 轧制 缺
作者 :吴 焰 ,大专学历 ,工程师 ,现从事质量调整
圆钢缺陷

a.轧制过程中,轧件在成品孔前某一孔型因故损坏或辊环破缺,当轧件通过该孔型后,表面形成凸块,在后面的轧制过程中,凸块被压入基体并随轧件延伸,最终在成品表面上,产生周期性的生根结疤;
b.在轧制过程中,由于外界金属物落在轧件表面上,并被带入孔型内,压入轧件表面,在钢材表面形成结疤。这种结疤是不生根的,无规律性;
连铸坯缺陷
a.原料表面精整不良,凹坑深度比较大;
b.原料内部有较大的皮下气泡,轧制后破裂形成翘皮。
1 表面划伤
1.1 特征
表面划伤又称擦伤、刮伤、划痕。是圆钢表面轴线方向出现的单条或多条平行的直线形机械损伤。目视或在放大镜下观看可见沟底。由于划伤的温度不同,沟痕会呈现不同的颜色。因此可以用来判断产生划伤缺陷的大概工序位置。
一般高温状态下形成的划伤,(600℃以上)整个沟痕均被氧化;在蓝脆温度区形成的划伤,其沟痕呈蓝色;低温划伤时沟痕现铁基体亮白色。铁皮其深度目视能见几毫米,长度自几毫米至几米以上,宽度也不等,多数的划伤沟痕的都是等宽的,断续地出现于钢材的局部或全长。在显微镜下,划伤的沟槽底部光滑,沟槽边部和底部基本没有脱碳现象。
1.2 产生原因
在高温区可能产生划伤位置和工序是:由于导卫装置加工不良,安装偏斜,磨损严重,或粘有氧化铁皮而造成的划伤;活套、跑槽等因安装、加工因素形成粗糙表面或突起,使轧件跳套时被划伤;
在中温或低温区可能形成的划伤的位置和工序是:钢材在生产运输过程中与粗糙的辊道、地板、冷床等设备接触等
1.3 消除方法
c 轧件温度不均匀,或送往圆孔的椭圆轧件形状不正确,造成轧件宽度上延伸不一致;
d 成品钢材冷却不均,精整操作不当。
6.1 缺陷特征
圆钢表面质量缺陷与优化措施

125管理及其他M anagement and other圆钢表面质量缺陷与优化措施沈 荣,冯昊苏,吴振忠(安徽富凯特材有限公司,安徽 宣城 245300)摘 要:总结介绍了表面折叠、裂纹、麻点、翘皮、耳子及公差尺寸出格等质量缺陷的特征,产生原因,优化措施,完善轧制工艺及设备改进,确保产品质量的建议。
关键词:折叠,裂纹,麻点,翘皮,耳子及公差尺寸,圆钢中图分类号:TG335.62 文献标识码:A 文章编号:11-5004(2021)15-0125-2收稿日期:2021-08作者简介:沈荣,男,生于1984年,汉族,浙江湖州人,大专,工程师,研究方向:金属材料及加工。
1 主要质量问题圆钢表面缺陷中的折叠、裂纹、麻点、翘皮、耳子及公差出格等,是影响圆钢后续加工的主要因素,我厂在2020年中收到投诉无数,退货近1000吨,退货率占比5%以上,针对客户投诉提出的质量问题,对整个轧制过程进行工艺调整及设备改进,着重对现有的缺陷开展攻关,采取强有力的措施逐个突破。
对缺陷类别进行统计,并绘制帕累托图如图1。
图1 圆钢表面缺陷的帕累托图2 原因分析及优化措施2.1 折叠特征:沿轧制方向呈直线状分布,外形似裂纹,边缘有时呈锯齿状,连续或断续分布,深浅不一,内有氧化皮,在横截面上看,一般呈折角。
如图2。
原因:(1)孔型设计固有缺陷及轧机调整不当。
(2)孔型磨损严重后料形不正、扭转产生飞边或刮伤被压入。
(3)原料表面有尖角、裂纹及夹杂等缺陷。
措施:(1)完善孔型设计,加强轧机调整工艺,防止前道次产生耳子经后道次被压入,要求每炉钢对各道次卡量记录,同时用竹片烧红钢进行检测,并关注主控各机架张力是否正常。
图2 折叠(2)对轧制槽孔设定轧制量,每天停机对槽孔磨损观察,并采用现场样板进行核对,避免料形不正产生扭转飞边及刮伤等缺陷。
(3)严格控制好加热工艺,保证钢坯加热均匀,减小阴阳面在轧制过程弯曲擦伤产生折叠。
(4)对轧线导卫板进行材质改造,使用球墨铸铁材质,防止导板粘铁划伤轧件后被压入产生折叠。
- 1、下载文档前请自行甄别文档内容的完整性,平台不提供额外的编辑、内容补充、找答案等附加服务。
- 2、"仅部分预览"的文档,不可在线预览部分如存在完整性等问题,可反馈申请退款(可完整预览的文档不适用该条件!)。
- 3、如文档侵犯您的权益,请联系客服反馈,我们会尽快为您处理(人工客服工作时间:9:00-18:30)。
圆钢成品主要缺陷和产生原因一编辑:冶金质量网来自:冶金质量网[字号大中小]时间:2010-4-27 浏览:221表面划伤1.1特征表面划伤又称擦伤、刮伤、划痕。
是圆钢表面轴线方向出现的单条或多条平行的直线形机械损伤。
目视或在放大镜下观看可见沟底。
由于划伤的温度不同,沟痕会呈现不同的颜色。
因此可以用来判断产生划伤缺陷的大概工序位置。
一般高温状态下形成的划伤,(600℃以上)整个沟痕均被氧化;在蓝脆温度区形成的划伤,其沟痕呈蓝色;低温划伤时沟痕现铁基体亮白色。
铁皮其深度目视能见几毫米,长度自几毫米至几米以上,宽度也不等,多数的划伤沟痕的都是等宽的,断续地出现于钢材的局部或全长。
在显微镜下,划伤的沟槽底部光滑,沟槽边部和底部基本没有脱碳现象。
一般车削用圆钢,当划伤的深度不超过国家标准规定的公差之半时,一般不影响使用。
明显的划伤对拉拔用圆钢有一定的影响。
在冷拉拔过程中,圆钢表面的划伤沟痕,会恶化圆钢和拉拔磨具之间的润滑状态,使拉拔后圆钢(钢丝)表面损坏加剧,严重的可导致拉拔模具的损坏。
对于冷镦用的圆钢,划伤是不允许出现得缺陷之一。
在冷镦过程中,由于划伤造成的表面损坏和应力集中,将直接造成冷镦开裂,出现废品。
1.2产生原因在高温区可能产生划伤位置和工序是:由于导卫装置加工不良,安装偏斜,磨损严重,或粘有氧化铁皮而造成的划伤;活套、跑槽等因安装、加工因素形成粗糙表面或突起,使轧件跳套时被划伤;在中温或低温区可能形成的划伤的位置和工序是:钢材在生产运输过程中与粗糙的辊道、地板、冷床等设备接触等1.3消除方法凡能在形成划伤的地点和工序,常会出现火花或尖利声响,并可找到残留的丝状金属物。
据此可找出产生擦伤的位置,再根据具体情况进行处理。
圆钢成品主要缺陷和产生原因二结疤编辑:冶金质量网来自:冶金质量网[字号大中小]时间:2010-4-28 浏览:972结疤圆钢的一种表面缺陷。
是在原料或轧件表面出现多余金属,在下一道次轧制时又被压入基体所形成的。
2.1特征结疤一般出现在圆钢的表面上,较粗大和厚些的结疤,一般用肉眼或低倍的放大镜即可看到。
有些薄的细小的要经过酸洗后甚至扭转后才能看到。
结疤一般呈舌状或指甲状,厚度往往不一致。
尖端较薄,有时可以翘起,宽而厚的一端与钢材基体相连。
在表面氧化铁皮较厚的情况下,甚至只能看到一条封闭的曲线,嵌在基体上。
由轧制过程中由于轧辊缺陷造成的结疤,会在圆钢的表面的轴线上出现周期性分布。
其间距约等于轧辊周长和延伸系数的乘积。
除非沿圆钢的轴线做出剖面,一般对有结疤的圆钢横截面进行金相检验室,不容易看到结疤的根部和基体的连接情况。
当横截面只穿过舌体部分时,在显微镜镜下只能看到多余的金属压入基体。
基体和多余金属见有氧化层存在。
基体下面一般无破坏。
如果沿轧制方向将纵剖面穿过舌根部,在显微镜下可观察到多余金属和基体相连的情况。
在连接面上有氧化层存在。
结疤是多余金属在基体中的压入。
对车削用钢来说,当结疤的深度不超过圆钢国标规定的公差之半时,对车削后的零件影响不大。
拉拔用圆钢表面不允许有结疤缺陷存在,拉拔过程中,特别是舌尖和拉拔方向一致时,多余的金属就会翘起、脱落,堵塞模具,使拉拔后的圆钢表面产生更多的划伤(俗称道子),严重可导致拉拔断裂。
对镦制(冷、热)用圆钢,当变形区内有结疤缺陷时,该缺陷会翘起或脱落。
严重的会影响镦制工件的外形,造成废次品量增加。
2.2结疤产生原因a.轧制过程中,轧件在成品孔前某一孔型因故损坏或辊环破缺,当轧件通过该孔型后,表面形成凸块,在后面的轧制过程中,凸块被压入基体并随轧件延伸,最终在成品表面上,产生周期性的生根结疤;b.在轧制过程中,由于外界金属物落在轧件表面上,并被带入孔型内,压入轧件表面,在钢材表面形成结疤。
这种结疤是不生根的,无规律性;c.轧件在孔型内打滑,使金属堆积于变形区周围的表面上,在轧时造成结疤;d.轧槽刻痕不良,在轧件表面上形成较高的凸块,再轧时,产生周期性的结疤;e.钢坯表面有较大的冷溅、翻皮、结疤等缺陷,当用钢锭一火轧成材时,则在成品表面上产生结疤;f.原料表面处理不当,留有尖锐的棱边或深宽比较大的凹坑,经轧制后形成结疤。
注意:由于钢坯因素在圆钢成品表面形成的结疤相对来说比较大或长,其出现的位置无规律,这是判定缺陷是炼钢或轧钢工序产生的基本标志之一。
圆钢成品主要缺陷和产生原因三耳子编辑:冶金质量网来自:冶金质量网[字号大中小]时间:2010-5-13 浏览:193耳子3.1主要特征在圆钢成品表面的非加工面上出现条状金属凸起。
平行于轴线。
根据出现的位置和形状,一般有两侧出耳、一侧出耳、全长出耳、局部出耳和周期出耳等多种情况。
出现耳子的圆钢,一般都要判为废品。
少量可以作为切削加工用原料。
3.2产生原因及消除方法a两侧出耳子a1由于孔型设计不当,对宽展估计过小,应修改孔型设计;a2由于成品前道孔型磨损严重,无法压下,以致进入成品孔的轧件过大出现耳子。
a3成品前道辊缝过大,压下量太小,使进入成品孔的轧件过大。
a4成品道次辊缝过小,压下量过大。
a5由于终轧温度过低,宽展量增加,造成成品道次出耳子。
a6原料有严重的缩孔或夹杂,金属的完整性被破坏,金属的延伸减小而宽展增大。
b一侧出耳一侧椭未充满b1由于成品道次进口夹板安装不正。
b2由于成品架进口夹板尺寸过大,或磨损严重,轧制时造成轧件往一边倒b3由于固定夹板顶丝失效,夹板松动;b4由于成品架进口横梁不平,应放平横梁。
c一侧出耳子一侧圆由于成品道次进口夹板不正,同时来料较大。
d无规律性断续出耳子由于轧辊窜动、跳动、轴瓦烧坏、辊脖磨坏,进口夹板加工不良或固定不劳,夹板盒松动等原因造成,此时应找出具体原因进行处理。
e周期出耳子,即有规律断续出耳子e1由于成品前道次的轧辊偏心,来料上下尺寸波动较大;e2由于成品道次轧辊偏心,来料上下尺寸波动较大。
圆钢成品主要缺陷和产生原因四弯曲编辑:冶金质量网来自:冶金质量网[字号大中小]时间:2010-6-10 浏览:844弯曲4.1特征弯曲是比较明显的外形缺陷。
有头部弯曲、局部弯曲或全长弯曲等多种情况。
4.2产生原因a出口导卫板安装过高或过低;b轧件温度不均,金属延伸不一致,轧件向温度低的一放弯曲;c轧辊倾斜跳动,有阴阳面,上下辊径差过大;两轧辊轴线不在同一垂直平面内。
d轧件前端被障碍物顶住;e输送辊道速度小于成品出辊速度,易使断面较小的钢材产生弯曲;f输送辊道速度过大,易使钢材端部撞弯;g冷床不平,成品在冷床上排列不齐,移动速度不一致,翻钢设备不良或操作不当;h冷却水分布不均,成品冷却不均;i精整操作不良,堆放不良。
运输装卸不良。
圆钢成品主要缺陷和产生原因五扭转编辑:冶金质量网来自:冶金质量网[字号大中小]时间:2010-6-11 浏览:155扭转5.1特征扭转是一种比较明显的外形缺陷。
特征是圆钢绕其纵轴扭转成螺旋状。
5.2产生原因a成品轧辊的中心线不在同一垂直平面内或互不平行,或在轧制过程中有轴向错动现象;b成品进口夹板安装偏斜,或磨损严重,夹板扶持能力弱使进入圆孔型的椭圆轧件发生倾倒;c轧件温度不均匀,或送往圆孔的椭圆轧件形状不正确,造成轧件宽度上延伸不一致;d成品钢材冷却不均,精整操作不当。
圆钢产品主要缺陷和产生原因六翘皮编辑:冶金质量网来自:冶金质量网[字号大中小]时间:2010-6-12 浏览:866.1缺陷特征在圆钢的表面基本沿轴线方向上出现的有规律或无规律分布,形状有成鱼鳞或指甲状的痕迹或翘起的薄皮。
一般来讲,缺陷的顶部或尖端和轧制延伸的方向一致。
缺陷的尾部大多和圆钢的基体相连。
当翘皮被轧制得很薄时,其尖端部分可出现翘起,或用工具很容易的翘起,形成表面损伤。
在自然光下用放大镜观察,可以看到缺陷的边缘实际是明显的连续裂纹。
酸洗后可以用肉眼明确看出。
沿轧制方向将缺陷剖开,经过抛光后在100倍显微镜下观察,有的可以看到非金属夹杂物的分布和缺陷的关系,这是分辨缺陷产生因素比较关键的手段之一。
一般来讲,圆钢轧制过程中由于机械因素导致轧件表面形成破损而出现局部金属堆积,并在其后又被压入而形成的翘皮缺陷,在显微镜下,缺陷的根部干净,和非金属夹杂物的分布无关。
而在连铸坯生产过程中由于皮下气泡等铸造缺陷导致的翘皮缺陷,都可以看到非金属夹杂物分布和缺陷的产生有直接关系。
一般车削用圆钢,当翘皮的深度不超过国家标准规定的公差之半时,一般不影响使用。
翘皮缺陷拉拔用圆钢很大影响。
在冷拉拔过程中,翘起的金属颗粒会在拉拔磨具的润滑区或工作区积聚,使拉拔后圆钢(钢丝)表面损坏。
对于冷镦用的圆钢,翘皮是不允许出现得缺陷之一。
特别是由连铸坯缺陷形成的翘皮。
在冷镦过程中,由于缺陷造成的表面损坏和应力集中,将直接造成冷镦开裂,出现废品。
6.2 产生原因轧制过程中的机械损伤:a导卫装置加工不善和安装不良,活套有尖锐棱角,刮伤轧件表面形成点状金属堆积,在下一轧制道次中被压入基体;b输送辊道或导槽表面粗糙,刮伤轧件表面形成点状金属堆积,再轧后造成翘皮;d轧槽磨损严重,轧件在孔型内打滑;刮伤轧件表面形成点状金属堆积并在下一轧制道次中被压入基体。
连铸坯缺陷a.原料表面精整不良,凹坑深度比较大;b.原料内部有较大的皮下气泡,轧制后破裂形成翘皮。