看板过程培训教程
精益生产看板拉动培训PPT

培训员工
对生产线员工进行培训, 使其熟悉看板拉动系统的 操作规则和注意事项。
试运行与调整
在正式实施前进行试运行, 根据试运行结果对系统进 行调整和优化。
持续改进
在实施过程中,不断收集 数据、分析问题,持续优 化改进,提高生产效率和 降低成本。
05
精益生产看板拉动培训效果 评估
培训前后对比评估
培训前
04
培训与推广
对相关人员进行培训和宣传,使其了 解并掌握看板拉动系统的使用方法和 意义。
03
精益生产看板拉动培训内容
基础理论培训
总结词
传授精益生产的基本概念、原则 和实践,为学员打下坚实的理论 基础。
详细描述
介绍精益生产的起源、发展历程 和核心价值,讲解精益生产的基 本原则、工具和方法,使学员全 面了解精益生产的基础知识。
生产效率提升评估
培训前
生产效率低下,经常出现等待和浪费 的现象。
培训后
通过实施精益生产和看板拉动系统, 生产效率得到显著提升,减少了等待 和浪费的现象。
06
精益生产看板拉动培训案例 分享
案例一:某汽车制造企业的看板拉动系统实施
总结词
成功实施,显著提升生产效率
详细描述
某汽车制造企业在精益生产看板拉动培训的指导下,成功实施了看板拉动系统。通过实时监控生产数据,及时调 整生产计划,减少了生产过程中的浪费,显著提升了生产效率。同时,该企业还实现了与供应商之间的有效协同, 确保了原材料的及时供应。
实操技能培训
总结词
通过实际操作和模拟演练,培养学员 解决实际问题的能力。
详细描述
组织学员进行实际操作和模拟演练, 教授如何运用精Байду номын сангаас生产的工具和方法 解决实际问题,培养学员的动手能力 和问题解决能力。
物流看板培训

以看板为主要手段的精益计划物控管理是一种 计划主导型的生产管理方式
13/122 13/122
拉动生产的重要手段--看板 拉动生产的重要手段--看板 -◈ 看板的定义
看板是传递物料需求信号的工具,它是一种揭示牌“卡片” 看板是传递物料需求信号的工具,它是一种揭示牌“卡片”,卡片记录了 补充物料需求的信息。也可以是一种信号, 补充物料需求的信息。也可以是一种信号,更多的情况下是记录生产需求 信息的卡片,一般会装在塑料袋中。 信息的卡片,一般会装在塑料袋中。
14/122 14/122
看板的功能
1、传递生产以及搬送的作业指令 2、物料表-目视管理的工具 物料表- 3、在均衡化原则下实现计划微调 4、防止过量生产和搬送、发现 防止过量生产和搬送、 改善目标 5、改善进度控制器
15/122 15/122
看板拉动系统的基本框架
总体框架
Kanban Loops 看板卡循环路线
BATCH 批量
ABC ABC X ABC YC XY XY
FLOW 连续流 A
ABC ABC ABC
X
A A C
ABC ABC ABC
X
B C
BEH BE BE
B
先流动,后拉动 先流动 后拉动
19/122 19/122
建立看板拉动系统应考虑的要点
案例FASH说明 说明 案例
精益改善物流看板 展示
12/122 12/122
精益生产的生产计划特点
顾客第一, 第一 、顾客第一,生产由需求驱动各工 序只生产后工序所需要的产品, 序只生产后工序所需要的产品, 避免了生产不必要的产品; 避免了生产不必要的产品; 第二、 第二、因为只在后工序需要时才生产避免 过量生产和减少了不急需品的库存 量;实现在滞品库存的目视化管理。 实现在滞品库存的目视化管理。 第三、因生产指令只下给最后一道工序, 第三、因生产指令只下给最后一道工序, 成品数量与生产指令数量( 成品数量与生产指令数量(市场需 求)一致,因此前工序无生产计划。 一致,因此前工序无生产计划。 后 工 序 按 看 板 生 产
精益生产---看板管理运用培训
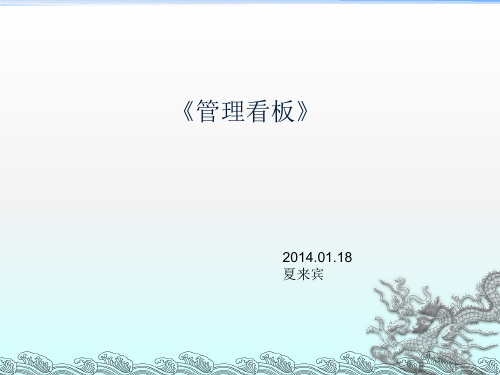
-
工作计划 组织结构 学习培训 点检环节
11
奉献、学习、沟通、 协作
八.管理看板之设计示例(参考)
窗外世界:管理看板案例参考(3)---设备部门
-
指示灯 颜色区分 重点管理项 统计管理
12
奉献、学习、沟通、 协作
八.管理看板之设计示例(参考)
窗外世界:管理看板案例参考(4)
1.目的: 创建“透明的”的工作场所,使任何人站在生人和陌生的角度都可以判断出正常与否, 使问题表面化。只有这样,我们的管理才可以得到落实、改善和提高。 2.意义: 就是把工厂中潜在的问题暴露出来,让任何人一看就知道异常情形的所在。 3.全面而有效的使用管理看板,将在六个方面产生良好的影响: 1、展示改善成绩,让参与者有成就感、自豪感。 2、营造竞争的氛围。
环境
5S标准; ISO14000标 准;作业现 场布置图等。
部品明细; 验收标准; QC工程图; 出入库制度
6
奉献、学习、沟通、 协作
六.管理看板内容要求
抓住重点 —— 重要的 、精华的;
平实简洁
注重内涵 明确职责
——
—— ——
简,易,准;
内容往往是最重要的; 管理规则;
容易遵守
实施彻底 不断完善
11. 作业管理 标准作业票
12.时间别产量 管理 时间别管理表
13. 安全生产日 历 改善前
14. 改善案例 改善后
9
奉献、学习、沟通、 协作
八.管理看板之设计示例(参考)
窗外世界:管理看板案例参考(1)
- 会议管理 - 企业文化体现 - 流程图
10
奉献、学习、沟通、 协作
八.管理看板之设计示例(参考)
TPS看板管理专题培训课件
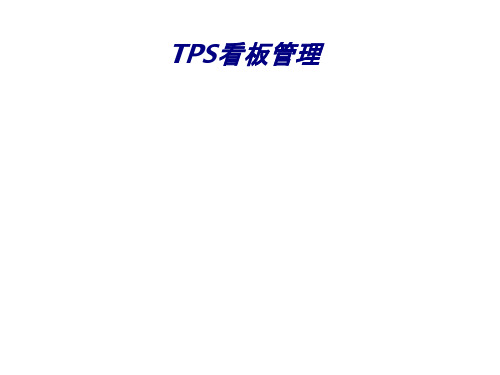
基准在库数 (托架数)
工工程位名名
B
内部代号
基准
3
三角看板的 置放位置
(3パレット目)
完成品仓库
冲压工位 ・G級:自动机 ・A級:大型冲压 ・B級:中型冲压 ・C級:小型冲压
完成品的 置放场所 (成品仓库)
置場:A-1
托架 容纳100个
・ 取了3个以上的 托架
将「三角看板」 取下、 ・准备指示
9
405
15 :55
04 :55
16 :30
05 :30
回收间隔、分 40 40 35 40 40 35 40 40 35 40 40 35
(例)
班次
・白班:08:00~17:00 (休息:10:00~10:10.12:00~13:00.15:00~15:10) ・夜班:21:00~06:00 (休息:23:00~23:10.01:00~02:00.04:00~04:10)
・
・基本原则
看板
(1)・在部品箱上贴上看板
(2)・‘看板’的取出・・使用第一个部件时、 将部品箱上贴的看板取下。
(3)・按照规定时间回收取下的看板 (4)・取下的看板的部品订货按照规定时间进行。 (5)・后工序去取‘看板’张数所包含的部品 (6)・前工序生产被取了的看板张数所包含的部件
10
5:‘看板’的计划
・取件周期 : 1-4-2
A -B - C
〔例題〕:2
・1天的使用量 : 160个 ・1箱容量 : 8个 ・安全係数 : α=0.5
・引取りサイクル : 1-4-5
A -B - C
看板 总张数
=
=
160 8
×
(
1×
看板管理实战培训课程

看板管理实战培训课程概述看板管理是一种敏捷项目管理方法,在工程管理和软件开发中广泛应用。
本文将介绍看板管理的基本原理和实战技巧,并提供一套完整的培训课程,帮助学习者掌握看板管理的核心概念和实施方法。
1. 看板管理简介1.1 什么是看板管理看板管理是一种基于可视化的项目管理方法,通过使用看板板块和卡片来可视化项目的各个任务和状态。
看板管理强调团队协作、可视化和流程优化,能够帮助团队更好地掌握项目进展、及时发现问题并加以解决。
1.2 看板管理的核心原则•可视化:将项目任务和状态可视化通过看板板块和卡片。
•流动:通过优化流程,实现任务的快速推进。
•透明:通过看板的可视化,实时反映项目进展和问题。
•自我组织:团队成员自主负责任务的执行和进度。
2. 看板管理实施步骤2.1 设计看板•确定看板种类:任务看板、项目看板、团队看板等。
•划分看板板块:待办、进行中、已完成等。
•设计卡片模板:包括卡片的名称、描述、负责人等字段。
2.2 管理任务•创建任务卡片:将任务添加到适当的板块。
•更新任务卡片状态:将任务从一个板块移动到另一个板块,反映任务状态变化。
2.3 优化流程•分析瓶颈:通过观察卡片流动的情况,找出流程中的瓶颈。
•改进流程:针对瓶颈问题提出改善措施,并实施优化。
•迭代改进:不断观察流程效果,并根据反馈进行调整和改进。
3. 看板管理实战案例3.1 项目管理看板在项目管理中,看板管理可以帮助团队及时了解项目进展、识别问题和调整资源分配。
通过将不同阶段的任务列在不同板块中,并及时反映任务状态变化,团队成员可以更好地协作和推进项目。
3.2 运维管理看板在运维管理中,看板管理可以帮助团队及时处理运维请求和故障。
将待处理、处理中和已解决的任务列在不同板块中,团队成员可以清晰地了解任务状态,并协作解决问题。
4. 看板管理培训课程4.1 培训目标本课程旨在帮助学习者掌握以下技能:•理解看板管理的基本原理和核心概念;•掌握看板管理工具的使用和操作技巧;•能够设计和实施符合实际需求的看板管理方法;•能够应用看板管理解决项目管理和团队协作中的问题。
物流看板培训讲义
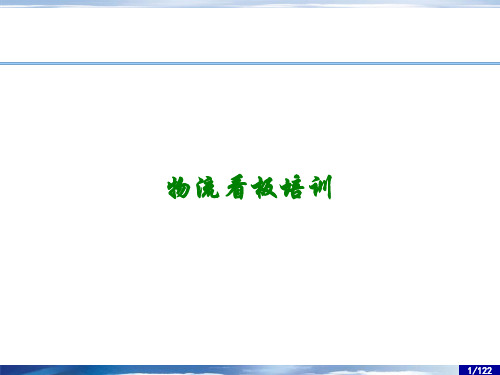
Part #__________________________ Description_____________________ Std. Pack_______________________ Min____________ Max____________ Store Loc_______ Use Loc________ Supplier________________________ Delivery Date - M - T - W - T - F - S Time___________________________
物流看板培训
29/122
改善绩效确认
№ 改善项目
改善前
改善后 改善效果(%)
1 动作浪费 265.7S/台
94.7S/台
64%
2
异常停线 浪费
120.6min/日 94.75min/日
21.4%
3 日产量
72台
90台
25%
4
生产线开 动率
70.8%
91.7%
20.9%
5 平衡率
69.3%
物流看板培训
物流看板培训
12/122
丰田的现场物料管理
物流看板培训
13/122
丰田的现场物料管理
物流看板培训
14/122
丰田的现场物料管理
物流看板培训
15/122
物流标准化设计-专用小批量工位器具
改 善 前
5
设计图 物流看板培训
零件架 1 10 70 1:5 2801-4201-01
改 善 后
16/122
物流看板培训
1/122
典型的工序间看板
物流看板培训
看板生产控制系统培训教材
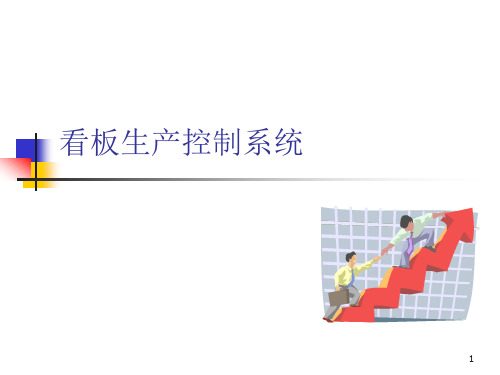
25
看板系统≠零库存
看板系统只是通过控制每种零件的容器数, 以达到控制一次投入工序中的物料数。
无法按时 强 加工零件 适
应 性
存在多余 零件容器
追加容器 去除容器
加看板卡 减看板卡
降低缓冲 库存数
26
看板系统优点
连续生产,不产生待料浪费; 降低库存,推动无纸化办公; 免除采购管理,生产预计; 取消来料检查作业; 促进持续改善等。
7
看板生产控制系统
装配线
容器
搬运看板
零件A 生产看板
零件加工中心
8
搬运看板
用于授权某零件从一个工序转移到另一 个工序。
某工序Ni从前工序Ni-1得到零件经加工后, 再传送到后工序Ni+1之前,予以保留到后 工序Ni+1使用完所有的该加工零件,并向 该工序Ni发出搬运看板索取零件时,方才 发出零件,整个生产循环得以周转。
严格把控质量关,让生产更加有保障 。2020年11月 下午6时 45分20.11.2518:45November 25, 2020
重规矩,严要求,少危险。2020年11月25日 星期三6时45分 59秒18:45:5925 November 2020
好的事情马上就会到来,一切都是最 好的安 排。下 午6时45分59秒 下午6时45分18:45:5920.11.25
12
看板样本举例
零件编号:CI2475 零件名称:钢制垫圈
从: 加工站: M-2
盒子容量:1000 pcs 盒子类型:A 搬运号: 3/5
至: 组装线: A-2
13
课堂练习
请设计出一款生产看板。
14
可视控制
生产指令的发出还可以选择其它可视控 制的方法。
看板管理培训教材(PPT48页)

3.在这种独特的文化氛围中,有关竹 子的诗 词歌赋 层出不 穷,画 竹成为 中国绘 画艺术 中的一 个重要 门类, 封建士 大夫在 私园、 庭院中 种竹养 竹以助 风雅, 亦成为 普遍风 气。 4.历史上东西方香文化交流不可谓不 繁盛。 隋唐时 期,许 多波斯 商人以 贩卖香 药为职 业,收 售由西 域经海 上运来 的香药 ;同时 ,许多 朝鲜留 学生来 到中国 ,将中 国的香 文化传 入朝鲜 ,再由 朝鲜传 入日本 。
看
JIT生产方式是以降低
板 成本为基本目的,在生产
管
系统的各个环节全面展开
理
的一种使生产有效进行的
的 重 要 性
新型生产方式。JIT又采用 了看板管理工具,看板犹 如巧妙连接各道工序的神 经而发挥着重要作用。
看板管理方法是在同一道
工序或者前后工序之间进行物
流或信息流的传递。JIT是一 种拉动式的管理方式,它需要 从最后一道工序通过信息流向 上一道工序传递信息,这种传
5.中国传统香道讲究香品的品质、器 物的精 美、程 序的考 究,直 至精神 境界的 提升; 西方自 从香水 出现以 后,人 们慢慢 习惯使 用香水 掩盖体 味,彰 显个性 和品味 ,直至 成为身 份地位 的象征 。 6.中西方用香的差异源自于思维方式 的不同 。西方 人注重 直观性 ,喜欢 某种气 味就直 接喷洒 ,芬芳 满身, 让别人 直观地 感受到 ;
看板管理培训课程

2、推式生产分析(3)
由于在生产中难免受到多方面因素的困 扰,如:设备故障、质量问题、缺料等, 经常不能做到每道工序都按时完成,且 一般产品通常都是由许多零件组成,同 时零部件的精确提前期又很难确定,最 终导致计划产量和实际产量不符。
二、拉式生产(1)
拉式生产是从市场需求出发,由市场需 求信息决定产品组装,再由产品组装拉 动零部件加工。
拉式生产系统可以真正实现按需生产。
2、拉式生产分析
精益生产采用拉式生产系统,生产指令 由最后一道工序开始,在需要的时候依 次向前传递,这就使得准时化生产成为 可能。
特别是在采用看板这种管理工具之后, 看板就成为精益生产方式中最为显著的 管理工具,在保证适时、适量生产中起 着至关重要的连接作用。
每道工序或每个车间都按照当时的需要 向上一道工序或上游车间提出需求,发 出工作指令,上游工序或车间完全按照 这些指令进行生产。
二、拉式生产(2)
这时物流和信息流是结合在一起的,整 个过程相当于从后工序向前工序拉动, 故这种生产方式被称为拉式生产。
从下图可以看出,生产计划部门只制定 最终产品计划,计划下达到最后车间或 工序,其他车间或工序按照下游车间或 后工序的指令来确定生产。
精益生产 Lean Production
赵林 2011.10
第三章 看板管理
第三章 目录
1、典型生产方式 2、看板概念、类型和功能 3、工序内看板和工序间领取看板 4、信号看板 5、外协领取看板 6、特殊看板 7、看板使用问题
第一节
典型生产方式
两种生产方式
根据生产指令下达方式不同,生产方式 可以分为:
拉式生产模式物流与信息流示意图
生产计划部门
看板管理培训教材(PPT48页)
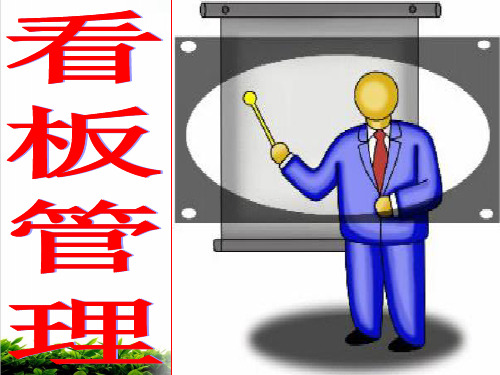
•
6.态度是最根本的问题,态度在某些 时候起 着决定 性的作 用,态 度是行 动的前 提,态 度受价 值观的 指导, 态度是 为人处 世的基 本原则 。凡事 态度积 极,就 已经成 功了一 半!
•
7.客户才是企业真正的老板,如果企 业丧失 了客户 ,就失 去了生 存的基 础,所 以给客 户提供 卓越而 周到的 服务是 企业发 展的重 要策略 ,企业 必须重 视客户 服务。
看板管理作用
看板管理作用
看板管理作用
看板管理作用
1
工序内看板的使用方法
看
板
的 使
2
信号看板的使用方法
用
方
法
3
工序间看板的使用方法
看板管理使用原则
看板管理使用原则
看 板 的 使 用 方 法
看板的使用方法
看板的使用方法
看板现场10s做得好的像片
•
•
8.增加服务意识,不仅对企业有利, 更能提 高员工 自身的 服务技 能,对 个人的 成长和 发展都 有着紧 密的联 系,可 以丰富 职业生 涯,使 自己成 为专业 型服务 人才。
谢谢观看!
看
JIT生产方式是以降低
板 成本为基本目的,在生产
管
系统的各个环节全面展开
理
的一种使生产有效进行的
的 重 要 性
新型生产方式。JIT又采用 了看板管理工具,看板犹 如巧妙连接各道工序的神 经而发挥着重要作用。
看板管理方法是在同一道
Hale Waihona Puke 工序或者前后工序之间进行物
流或信息流的传递。JIT是一 种拉动式的管理方式,它需要 从最后一道工序通过信息流向 上一道工序传递信息,这种传
看 板 管 理 的
看板管理培训ppt课件
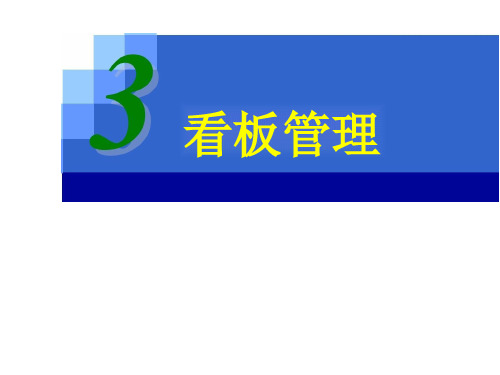
其中,订货周期 和生产过程时间 即,外协领取看板数量
注:α 为一次领取搬运所需的时间(天),不足1天按1天算; b 为一天的搬运次数; d 为一次订货时间内的看板搬运次数,简称搬运间隔。
31
例题: 在
中,看板循环为“1 -8-3”,假设使用量为200个/
基准量为:
M=D(L+T)+S
工序间领取看板数量为:
注:M 为基准量 Ts 为安全库存时间
T 为订货间隔期
17
五、 看板运行案例
一汽轿车公司总装车间看板运行流程由看板回收操作人员工作
流程、物流配货操作人员工作流程、物流发件操作人员工作流程、 生产线操作人员工作流程四个流程组成。
下图为总装车间使用的一种领取看板实例。
。
3.4 信号看板
二、 信号看板的使用方法
以冲压工序为例,介绍信号看板的运行方法。
钣金存放区域
A 冲压生产线 B 冲压生产线 C 冲压生产线
钢板 存放
卷材剪切生产线
冲压各生产线的在制品看板箱 A 生产线 B 生产线 C 生产线
12 3 4
1234
1234
材料剪切生产 线在制品看板箱
材料领三角看板箱 取看板箱
拉式生产原理: 每道工序或每个车间都按照当时的需要向前一道 工序或上游车间提出需求,发出工作指令,上游工序或车间完全 按照指令进行生产。物流和信息流是结合在一起的,整个过程相 当于从后工序向前工序拉动。
生产计划部门
(
2
3
N-1
N
- - 信息流 →物料流
工作点
物流与信息流示意图
5
拉式生产分析: 拉式生产系统真正实现按需生产。每道工序按下道工序的要求,
2023年制造中心看板管理培训教材方案模板

提高实时反馈
1.制造中心看板管理概述
2.看板管理:提高效率、降低成本、透明化生产
3.实时看板管理,生产效率提高40%,成本降低25%
促进快速决策
1.快速决策:制造中心看板管理及其优化生产流程
3.看板管理提高生产效率和减少产品不良率
看板管理的应用
看板管理的优势
1. 提高生产效率:通过看板管理,制造中心可以实现即时的生产状态监控和信息传递,从而有效安排生产任务和资源调配,提高生产效率。
2. 减少资源浪费:看板管理可以帮助制造中心实现对库存和原料的精确控制,避免过度生产和资源浪费,从而降低成本并提高利润率。
看板管理的定义
生产效率
看板管理
精益生产
拉动生产
透明化
视觉化
production efficiency
Kanban Management
Lean production
Visualization
Transparency
Pull production
"看板管理是一种以拉动式系统为基础的生产管理方式,旨在优化供应链和库存管理。"
2.流程优化是看板管理的核心,提高生产效率20%~30%,降低废品率10%~15%流程优化是看板管理的核心。据统计,流程优化可以提高生产效率30%至70%。流程优化的关键在于消除浪费、减少延迟和提高质量。例如,在汽车制造中,看板使用率可以提高生产效率20%至30%,同时减少废品率10%至15%。
3.人员培训是看板管理的重要一环人员培训是实施看板管理的重要一环。培训可以提高员工对看板的理解和熟练度,从而更好地利用看板来提高生产效率和质量。据统计,人员培训可以提高看板使用的效率和准确性,减少废品率5%至10%。
看板管理培训教材

外协领取看板的数量计算与工序间领取看板数量的计算 方法一致。
精益生产(Lean Production)
外协领取看板数量的计算
N
D C
(T
P
Ts )
(3-7)
N为外协领取看板的数量;T为订货周期,也称为看板周
N D (L T Ts ) C
N为材料领取看板的位置,即订货点;D为平均日需求 量;L为采购提前期; Ts为安全库存时间;C为盛放物 料的容器。
精益生产(Lean Production)
四、外协领取看板
与工序间看板类似,“前工序”不是内部的工序而是供 应商(协作厂家)
对外订货看板上必须记载进货单位的名称和进货时间、 每次进货的数量等信息。
看板的类型如表3-1所示。 看板的作用与功能 看板实施的步骤
精益生产(Lean Production)
看板起源--超市如何及时补充商品?
超级市场不仅可 以非常及时地满 足顾客对商品的 需求,而且 可以非常及时地 补充顾客买走的 商品
当计价器将顾客买 走的商品进行计价之 后,载有购走商品数 量、种类的卡片就立 即送往采购部,使商 品得到及时的补充。
精益生产(Lean Production)
工序间生产看板:定期订货法
M D(L T) S
N D (L T Ts ) C
M为基准量;D 为平均日需求量;L为采购提前期;T为定
货间隔期,S为安全库存量;N为看板的数量; Ts为安全
库存时间;C为盛放物料容器的容量。
T为两次领取之间的时间间隔,也叫做看板周期;
精益生产(Lean Production)
- 1、下载文档前请自行甄别文档内容的完整性,平台不提供额外的编辑、内容补充、找答案等附加服务。
- 2、"仅部分预览"的文档,不可在线预览部分如存在完整性等问题,可反馈申请退款(可完整预览的文档不适用该条件!)。
- 3、如文档侵犯您的权益,请联系客服反馈,我们会尽快为您处理(人工客服工作时间:9:00-18:30)。
Line Runner Side 补料面
Kanban Thrown Out Process 看板扔出过程
Another material withdrawal 再一次物料取用
Physical Material Withdrawal 物料取用
Assembly Line Side 流水线旁
Line Runner Side 补料面
Consolidation Process 备料过程
Consolidation directly in Buffer 缓冲区直接备料
Consolidation directly in Buffer 缓冲区直接备料过程
Receive Kanban Info 收到看板信息
Receive Kanban Card 收到看板卡
Office 办公室
Buffer receive Material 内库接收物料
Consolidation directly in Buffer 缓冲区直接备料过程
Verify bin and location 确认料箱及位置
Verify bin 确认料箱
Consolidation directly in Buffer 缓冲区直接备料过程
Take Kanban /Receive Replenishment
拿出看板/收到补给信息
Logistic Worker take Kanban Card to Buffer
物流操作人员把看板送至 缓冲区
Kanban
KANBAN (Card)
看板卡
Material number Material description Quantity per bin
Place empty bins in dedicated shelf
把空箱放在特定的搁板上
Empty Bin 空箱
Assembly Line Side 流水线旁
Line Runner Side 补料面
Kanban Thrown Out Process 看板扔出过程
Place empty bins in dedicated shelf
Kanban
Kanban
Kanban
Consolidation directly in Buffer 缓冲区直接备料过程
Transfer to production line 料箱运输至生产线
Takt 29 to 45 29-45 工位
Kanban
Kanban
Kanban
Kanban
Kanban
Kanban
Material from logistic centre 物流中心拨料
把空箱放在特定的搁板上
Empty Bins 空箱
Assembly Line Side 流水线旁
Line Runner Side 补料面
Kanban Thrown Out Process 看板扔出过程
Take Kanban From collection box 从收集箱中拿出看板
Assembly Line Side 流水线旁
Kanban Process 看板过程
Kanban Thrown Out Process 看板扔出过程
Kanban Thrown Out Process 看板扔出过程
Material Withdrawal
物料取用
Material Withdrawal
物料取用
Assembly Line Side 流水线旁
Takt 29 to 45 29-45 工位
Kanban
Kanban
Kanban
Kanban
Kanban
Kanban
Takt 46 to 64 46-64工位
Kanban
Kanban
Kanban
Kanban
Kபைடு நூலகம்nban
Kanban
Takt 65 to 92 65-92工位
Kanban
Kanban
Kanban
Kanban Thrown Out Process 看板扔出过程
Empty bin? Replenishment
Necessary ! 空箱?必须补料!
Bin empty ! 料箱空了!
Assembly Line Side 流水线旁
Line Runner Side 补料面
Kanban Thrown Out Process 看板扔出过程
Place Kanban 放置看板卡
Kanban Card 看板卡
Consolidation directly in Buffer 缓冲区直接备料过程
Move Box to Cart 料箱移至小车
Consolidation directly in Buffer 缓冲区直接备料过程
Box sorted on carts by Takt 料箱区分工位放置 在不同的小车上
Line Runner Side 补料面
Kanban Thrown Out Process 看板扔出过程
Take Kanban From collection box 从收集箱中拿出看板
Kanban
Assembly Line Side 流水线旁
Line Runner Side 补料面
Kanban Thrown Out Process 看板扔出过程
零件号 零件名称 装箱数
Supply Point Section/Takt/Rack/Compartment 补充点:工段/工位/料架/层
Buffer Info.
内库信息
Logitic Centre Infor. 物流中心信息
Assembly Line Side 流水线旁
Line Runner Side 补料面
Take Kanban and place on collection box 收集看板并放入收集箱内
Kanban
Kanban
Collection Box 看板收集箱
Assembly Line Side 流水线旁
Line Runner Side 补料面
Kanban Thrown Out Process 看板扔出过程
Takt 46 to 64 46-64工位
Kanban
Kanban
Kanban
Kanban
Kanban
Kanban
Takt 65 to 92 65-92工位
Kanban
Kanban
Kanban
Kanban
Kanban
Kanban
Material from logistic centre 物流中心拨料