规整化铁碳微电解填料制备方法
铁炭填料-铁炭微电解填料
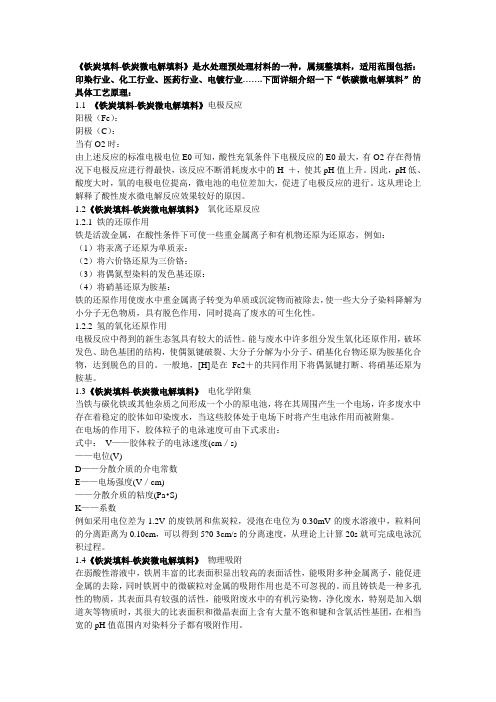
《铁炭填料-铁炭微电解填料》是水处理预处理材料的一种,属规整填料,适用范围包括:印染行业、化工行业、医药行业、电镀行业…….下面详细介绍一下“铁碳微电解填料”的具体工艺原理:1.1 《铁炭填料-铁炭微电解填料》电极反应阳极(Fe):阴极(C):当有O2时:由上述反应的标准电极电位E0可知,酸性充氧条件下电极反应的E0最大,有O2存在得情况下电极反应进行得最快,该反应不断消耗废水中的H +,使其pH值上升。
因此,pH低、酸度大时,氧的电极电位提高,微电池的电位差加大,促进了电极反应的进行。
这从理论上解释了酸性废水微电解反应效果较好的原因。
1.2《铁炭填料-铁炭微电解填料》氧化还原反应1.2.1 铁的还原作用铁是活泼金属,在酸性条件下可使一些重金属离子和有机物还原为还原态,例如:(1)将汞离子还原为单质汞:(2)将六价铬还原为三价铬:(3)将偶氮型染料的发色基还原:(4)将硝基还原为胺基:铁的还原作用使废水中重金属离子转变为单质或沉淀物而被除去,使一些大分子染料降解为小分子无色物质,具有脱色作用,同时提高了废水的可生化性。
1.2.2 氢的氧化还原作用电极反应中得到的新生态氢具有较大的活性。
能与废水中许多组分发生氧化还原作用,破坏发色、助色基团的结构,使偶氮键破裂、大分子分解为小分子、硝基化台物还原为胺基化合物,达到脱色的目的。
一般地,[H]是在Fe2+的共同作用下将偶氮键打断、将硝基还原为胺基。
1.3《铁炭填料-铁炭微电解填料》电化学附集当铁与碳化铁或其他杂质之间形成一个小的原电池,将在其周围产生一个电场,许多废水中存在着稳定的胶体如印染废水,当这些胶体处于电场下时将产生电泳作用而被附集。
在电场的作用下,胶体粒子的电泳速度可由下式求出:式中:V——胶体粒子的电泳速度(cm/s)——电位(V)D——分散介质的介电常数E——电场强度(V/cm)——分散介质的粘度(Pa•S)K——系数例如采用电位差为1.2V的废铁屑和焦炭粒,浸泡在电位为0.30mV的废水溶液中,粒料间的分离距离为0.10cm,可以得到5?0-3cm/s的分离速度,从理论上计算20s就可完成电泳沉积过程。
微电解铁碳填料工艺流程

新效【铁碳微电解】普茵沃润行业资讯----介绍:普茵沃润微电解填料----铁碳填料----内电解填料---污水处理填料------ 用于染料废水、焦化废水、石油化工废水、皮革废水、造纸废水、木材加工废水、电镀废水、印刷废水、采矿废水、含重金属废水、农药废水目录1基本内容1基本内容微电解填料新型【微电解填料】和传统【微电解填料】的比较微电解处理技术各单元可作为单独处理方法使用,也可作为生物处理的前处理工艺,利于污泥的沉降和生物挂膜。
新产品的面世,相信所有用户在关心效果的同时还关注着产品价格,下面将说明下本产品的市场价格以及定价的依据,并将新型填料的使用成本和传统填料作个对比。
一、传统铁碳床微电解填料1、铁屑刨花(含碳量约2%):如今市场价格在3000元/吨上下浮动,折合3.5〜4.0吨/立方,市场价格在 1.0〜1.2万元/立方;2、维持初始的处理效果的时间只能1〜2月;3、带来板结、钝化、铁泥堵塞,对设备带来损伤,并需要更换新的填料,实际使用成本高得惊人二、铁碳床微电解新型填料:(1)原料99%高纯铁粉、高纯碳粉、多种活性金属等;(2)工艺:高温烧结难度极高,铁粉烧结的同时保存碳粉,还要在规整化的填料表面产生无数的微孔,使之比表面结最大化,微电解效果显著,让生物挂膜容易。
(3)价格计算:高纯铁粉、碳粉进来市场价格上涨很多,算上人工成本及能耗等加工成本,价格初步定在12000〜15000 之间。
2014全国一级建造师资格测试备考资料真题集锦建筑工程经济建筑工程项目管理建筑工程法规专业工程管理和实务(4)新型填料的消耗量:每年只需补充少量即可,但没有传统填料更换的麻烦和上述三大问题,而且对设备损害减少。
和传统填料相比,在实际使用中,新型填料增长了使用寿命,减少了对设备的损耗,延长了设备的使用寿命,且无需大量人力更换填料,节约了劳动力,总体费用会比使用传统填料节约大笔费用。
微电解法用于废水的处理微电解技术是目前处理高浓度有机废水的一种理想工艺,又称内电解法.新型活性催化微电解填料:铁碳一体化,不会产生钝化、板结,长期使用持久高效。
新型铁碳微电解填料制备及其脱氮除磷研究
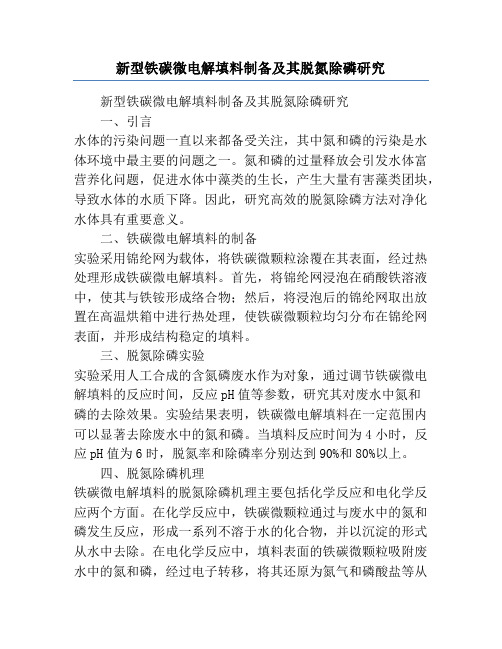
新型铁碳微电解填料制备及其脱氮除磷研究新型铁碳微电解填料制备及其脱氮除磷研究一、引言水体的污染问题一直以来都备受关注,其中氮和磷的污染是水体环境中最主要的问题之一。
氮和磷的过量释放会引发水体富营养化问题,促进水体中藻类的生长,产生大量有害藻类团块,导致水体的水质下降。
因此,研究高效的脱氮除磷方法对净化水体具有重要意义。
二、铁碳微电解填料的制备实验采用锦纶网为载体,将铁碳微颗粒涂覆在其表面,经过热处理形成铁碳微电解填料。
首先,将锦纶网浸泡在硝酸铁溶液中,使其与铁铵形成络合物;然后,将浸泡后的锦纶网取出放置在高温烘箱中进行热处理,使铁碳微颗粒均匀分布在锦纶网表面,并形成结构稳定的填料。
三、脱氮除磷实验实验采用人工合成的含氮磷废水作为对象,通过调节铁碳微电解填料的反应时间,反应pH值等参数,研究其对废水中氮和磷的去除效果。
实验结果表明,铁碳微电解填料在一定范围内可以显著去除废水中的氮和磷。
当填料反应时间为4小时,反应pH值为6时,脱氮率和除磷率分别达到90%和80%以上。
四、脱氮除磷机理铁碳微电解填料的脱氮除磷机理主要包括化学反应和电化学反应两个方面。
在化学反应中,铁碳微颗粒通过与废水中的氮和磷发生反应,形成一系列不溶于水的化合物,并以沉淀的形式从水中去除。
在电化学反应中,填料表面的铁碳微颗粒吸附废水中的氮和磷,经过电子转移,将其还原为氮气和磷酸盐等从水中释放。
五、优化参数为了进一步提高铁碳微电解填料的脱氮除磷效果,实验对反应时间、反应pH值等参数进行了优化。
结果表明,填料反应时间延长可以增加脱氮除磷效果,但达到一定时间后效果逐渐饱和。
反应pH值对脱氮效果影响较大,当pH值为6时,脱氮效果最好。
而对于除磷效果,pH值对其影响较小。
六、结论本研究使用了一种新型的铁碳微电解填料,并对其制备方法进行了研究。
实验证明,该填料能够有效地脱氮除磷,对废水中的氮和磷具有很高的去除率。
铁碳微电解填料的脱氮除磷机理主要包括化学反应和电化学反应。
一种铁碳微电解填料及其制备方法与流程
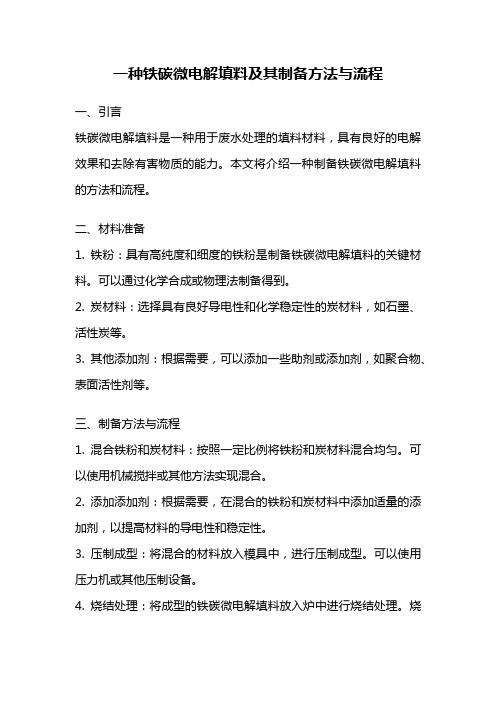
一种铁碳微电解填料及其制备方法与流程一、引言铁碳微电解填料是一种用于废水处理的填料材料,具有良好的电解效果和去除有害物质的能力。
本文将介绍一种制备铁碳微电解填料的方法和流程。
二、材料准备1. 铁粉:具有高纯度和细度的铁粉是制备铁碳微电解填料的关键材料。
可以通过化学合成或物理法制备得到。
2. 炭材料:选择具有良好导电性和化学稳定性的炭材料,如石墨、活性炭等。
3. 其他添加剂:根据需要,可以添加一些助剂或添加剂,如聚合物、表面活性剂等。
三、制备方法与流程1. 混合铁粉和炭材料:按照一定比例将铁粉和炭材料混合均匀。
可以使用机械搅拌或其他方法实现混合。
2. 添加添加剂:根据需要,在混合的铁粉和炭材料中添加适量的添加剂,以提高材料的导电性和稳定性。
3. 压制成型:将混合的材料放入模具中,进行压制成型。
可以使用压力机或其他压制设备。
4. 烧结处理:将成型的铁碳微电解填料放入炉中进行烧结处理。
烧结温度和时间应根据具体材料和要求进行调整。
5. 表面处理:烧结后的铁碳微电解填料可以进行表面处理,以增加其活性和去除有害物质的能力。
可以使用化学方法或物理方法进行表面处理。
6. 检测与包装:对制备的铁碳微电解填料进行检测,包括导电性、稳定性和去除有害物质的能力等指标。
符合要求的填料可以进行包装和存储。
四、应用前景铁碳微电解填料具有良好的应用前景,可以广泛应用于废水处理、环境治理和资源回收等领域。
通过不断改进制备方法和流程,可以进一步提高铁碳微电解填料的效果和性能。
五、结论本文介绍了一种制备铁碳微电解填料的方法和流程。
这种方法简单易行,可以制备出具有良好电解效果和去除有害物质能力的铁碳微电解填料。
铁碳微电解填料在废水处理和环境治理中具有广泛的应用前景。
通过进一步研究和改进,可以提高铁碳微电解填料的性能和效果,为废水处理和环境保护做出更大的贡献。
铁碳填料生产工艺
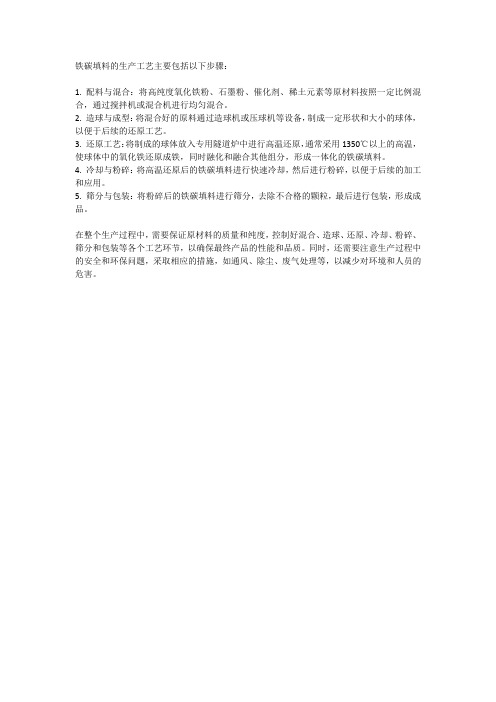
铁碳填料的生产工艺主要包括以下步骤:
1. 配料与混合:将高纯度氧化铁粉、石墨粉、催化剂、稀土元素等原材料按照一定比例混合,通过搅拌机或混合机进行均匀混合。
2. 造球与成型:将混合好的原料通过造球机或压球机等设备,制成一定形状和大小的球体,以便于后续的还原工艺。
3. 还原工艺:将制成的球体放入专用隧道炉中进行高温还原,通常采用1350℃以上的高温,使球体中的氧化铁还原成铁,同时融化和融合其他组分,形成一体化的铁碳填料。
4. 冷却与粉碎:将高温还原后的铁碳填料进行快速冷却,然后进行粉碎,以便于后续的加工和应用。
5. 筛分与包装:将粉碎后的铁碳填料进行筛分,去除不合格的颗粒,最后进行包装,形成成品。
在整个生产过程中,需要保证原材料的质量和纯度,控制好混合、造球、还原、冷却、粉碎、筛分和包装等各个工艺环节,以确保最终产品的性能和品质。
同时,还需要注意生产过程中的安全和环保问题,采取相应的措施,如通风、除尘、废气处理等,以减少对环境和人员的危害。
规整化FeAlC多元微电解填料的制备及表征

规整化Fe/Al/C 多元微电解填料的制备及表征杨瑞洪,仇实,罗志臣,吴昌胜(扬州工业职业技术学院化学工程学院,江苏扬州225127)[摘要]以铝作为掺杂成分,在铁、铝和炭最佳质量比为3∶1∶1的条件下,用高温烧结工艺将其烧制成多孔性球形规整化金属合金架构填料,并进行SEM 和EDX 表征。
该填料具有稳定的结构和耐磨抗压能力,同时有较大的比表面积和孔隙率,用于处理炼油废水时达到良好效果。
[关键词]微电解;填料;污水处理[中图分类号]X703[文献标识码]A[文章编号]1005-829X (2020)04-0060-04Preparation and characterization of regular Fe/Al/C multiple micro ⁃electrolysis fillerYang Ruihong ,Qiu Shi ,Luo Zhichen ,Wu Changsheng(College of Chemical Engineering ,Yangzhou Polytechnic Institute ,Yangzhou 225127,China )Abstract :Aluminum is selected as the doping component.With the mass ratio of iron ,aluminum and carbon of 3∶1∶1,the porous spherical structured metal alloy filler is sintered by the high ⁃temperature sintering process and then cha ⁃racterized by SEM and EDX.The filler exhibits stable structure ,wearing capacity ,compressive resistance ,large com ⁃parative area and porosity.Finally ,it is applied in the treatment of refinery wastewater ,which shows excellent effect.Key words :micro ⁃electrolysis ;filler ;wastewater treatment[基金项目]江苏省“青蓝工程”优秀青年骨干教师项目(苏教办师〔2017〕5号);中央高校基本科研业务费(2019B44214);国家自然科学基金面上项目(51979077);江苏省产学研合作项目(BY2019248);江苏省高等学校自然科学研究项目(18KJB430032);扬州工业职业技术学院专业导师工作室项目(2016-01)传统微电解工艺常用铁屑和炭等进行物理混堆作填料,运行一段时间后容易钝化、板结并形成沟流短流,又因铁与炭是物理接触,很容易形成隔离层破坏原电池结构,从而阻碍微电解的继续进行,填料使用寿命短,污水处理成本高,且出水水质不稳定,严重阻碍微电解工艺的工程应用和推广〔1-2〕。
铁碳微电解填料的制备方法[发明专利]
![铁碳微电解填料的制备方法[发明专利]](https://img.taocdn.com/s3/m/413857e80740be1e640e9a26.png)
专利名称:铁碳微电解填料的制备方法专利类型:发明专利
发明人:陈建荣,周敏,方克明,仲淑贤申请号:CN201810291066.9
申请日:20180403
公开号:CN108609694A
公开日:
20181002
专利内容由知识产权出版社提供
摘要:本发明涉及一种铁碳微电解填料的制备方法,包括以下步骤:将铁粉、铝渣和表面活性剂混合,经制粒、焙烧制成铁铝微球,将铜屑和碳粉混合,经制粒、焙烧制成铜碳微球;将铁铝微球和铜碳微球与珍珠岩、云母石、蛭石和高岭土混合并压制成毛坯填料;将毛坯填料经高温煅烧生成铁碳微电解填料。
本发明的铁碳微电解填料的制备方法,制备的铁碳微电解填料孔隙率高,可达93%以上,孔径均匀,能够控制在1.0~1.8mm之间,并且对污水中COD的去除率高,符合绿色生态城市的处理标准。
申请人:浙江师范大学
地址:321004 浙江省金华市迎宾大道688号
国籍:CN
代理机构:北京辰权知识产权代理有限公司
代理人:佟林松
更多信息请下载全文后查看。
铁碳塔微电解填料

铁碳塔微电解填料铁碳塔微电解填料“三步走“《普茵沃润》铁碳微电解填料工艺指导资料”要点“分析;<第一步>微电解原理:当将填料浸入电解质溶液中时,由于Fe和C之间存在1.2V的电极电位差,因而会形成无数的微电池系统,在其作用空间构成一个电场,阳极反应生成大量的Fe2+进入废水,进而氧化成Fe3+,形成具有较高吸附絮凝活性的絮凝剂。
阴极反应产生大量新生态的[H]和[O],在偏酸性的条件下,这些活性成分均能与废水中的许多组分发生氧化还原反应,使有机大分子发生断链降解,从而消除了有机物尤其是印染废水的色度,提高了废水的可生化度。
工作原理基于电化学、氧化—还原、物理吸附以及絮凝沉淀的共同作用对废水进行处理。
<第二步>微电解填料优点:适用范围广,处理效果好,成本低,操作维护方便,不需要消耗电力资源,反应速度快,处理效果稳定,不会造成二次污染,提高废水的可生化性,可以达到化学沉淀除磷,可以通过还原除重金属,也可以作为生物处理的前处理,利于污泥的沉降和生物挂膜。
<第三步>不板结:传统填料的板结现象是因为铁颗粒没有被碳颗粒分散均匀的缘故,铁颗粒之间容易生锈板结。
而新型微电解填料经过特殊的高温烧结工艺使得本填料中的铁和碳以铁碳包容构架的形式存在,铁骨架与碳链相互交叉,这种交叉性使得铁颗粒被碳颗粒均匀的分散了,因此不会板结。
铁碳微电解工艺从开始应用到现今已表现出了许多的优点,具体可概述如下:(1)可同时处理多种毒物,占地面积小,系统构造简单,整个装置易于定型化及设备制造工业化;(2)适用范围广,在多个行业的废水治理中都有应用,如印染废水、电镀废水、石油化工废水等,均取得了较好的效果;(3)处理效果好,从各个厂的实际运行来看,该工艺对各种毒物的去除效果均较理想;(4)使用寿命长,操作维护方便,微电解塔(床)只要定期地添加填料便可。
传统的微电解工艺在实际运行中也暴露了较多的问题,具体可概述如下:(1)铁屑处理装置经一段时间的运行后,铁屑易结块,出现沟流等现象,大大降低处理效果。
- 1、下载文档前请自行甄别文档内容的完整性,平台不提供额外的编辑、内容补充、找答案等附加服务。
- 2、"仅部分预览"的文档,不可在线预览部分如存在完整性等问题,可反馈申请退款(可完整预览的文档不适用该条件!)。
- 3、如文档侵犯您的权益,请联系客服反馈,我们会尽快为您处理(人工客服工作时间:9:00-18:30)。
规整化铁碳微电解填料制备方法CN 101817574 B摘要规整化铁碳微电解填料及其制备方法属污水处理技术领域,本发明填料为铁屑:直径0.1~1mm,重量百分比50~80%;粉末状活性炭:直径小于0.1mm,重量百分比5~17%;粘土:直径小于0.15mm,重量百分比15~35%。
本发明铁碳微电解填料制备方法的步骤:a.将按重量百分比的填料均匀混合;b.加水将混合物制成直径3~10mm的颗粒状填料;c.将上述填料入烘箱,于30~50℃下烘干;d.将填料移入马弗炉,隔绝氧条件下于250~600℃下焙烧2~4小时;e.待填料焙烧结束、冷却后,制得规整化铁碳微电解填料。
本发明可防止铁碳微电解填料板结、钝化,填料易装填,污水处理效果良好,成本低廉,制备简单。
权利要求(1)1. 一种规整化铁碳微电解填料制备方法,其特征在于包括下列步骤:a.将按重量百分比的填料均勻混合,填料为包括下列名称、规格和重量百分比的材料:铁屑:直径为0. 1〜1mm,重量百分比为50〜80% ;粉末状活性炭:直径小于0. 1mm,重量百分比为5〜17% ;粘土:直径小于0. 15mm,重量百分比为15〜35% ;b.逐渐加水,缓慢将混合物摇制成直径为3〜IOmm的颗粒状填料;c.将制得的直径为3〜IOmm的颗粒状填料放入烘箱,于30〜50°C下烘干;d.将填料移入马弗炉中,在隔绝氧的条件下,于250〜600°C下焙烧2〜4小时;e.待填料焙烧结束、冷却后,制得规整化铁碳微电解填料。
说明规整化铁碳微电解填料制备方法技术领域[0001] 本发明属铁碳微电解污水处理方法技术领域,具体涉及一种铁碳微电解填料的制备方法。
背景技术[0002] 微电解法是利用金属腐蚀原理,形成原电池对废水进行处理的良好工艺,又称为内电解法、零价铁法、铁屑过滤法、铁碳法,是一项被广泛研究与应用的废水处理技术,因其工艺简单、操作方便,且可达到“以废治废”的目的,近年来受到广泛重视。
[0003] 但大量研究结果表明,该法在应用中存在诸多缺陷,填料运行一段时间后,由于铁的腐蚀,容易出现结块和沟流,使铁碳微电解填料处理效果降低,同时铁屑表面会生成一层金属氧化物和氢氧化物膜,致使铁屑钝化,进而导致微电解过程中断,影响处理效果。
发明内容[0004] 本发明的目的在于提供一种可防止铁碳微电解填料板结、钝化,对污水有良好处理效果的微电解填料制备方法。
[0005] 本发明的规整化铁碳微电解填料制备方法包括下列步骤:[0006] a.将按重量百分比的填料均勻混合,填料为包括下列名称、规格和重量百分比的材料:铁屑:直径为0. 1〜1mm,重量百分比为50〜80% ;粉末状活性炭:直径小于0. Imm, 重量百分比为5〜17% ;粘土:直径小于0. 15mm,重量百分比为15〜35% ;[0007] b.逐渐加水,缓慢将混合物摇制成直径为3〜IOmm的颗粒状填料;[0008] c.将制得的直径为3〜IOmm的颗粒状填料放入烘箱,于30〜50°C下烘干;[0009] d.将填料移入马弗炉中,在隔绝氧的条件下,于250〜600°C下焙烧2〜4小时;[0010] e.待填料焙烧结束、冷却后,制得规整化铁碳微电解填料。
[0011] 本发明的有益效果在于:可防止铁碳微电解填料板结、钝化,填料装填方便,对污水有良好的处理效果,且成本低廉,制备简单。
具体实施方式[0012] 一、结合实施例进一步详述本发明[0013] 实施例1[0014] 将直径小于Imm的铁屑200g(重量百分比50% )、直径小于0. Imm的粉末活性炭60g (重量百分比15%)和直径小于0. 15mm的粘土140g (重量百分比35%)充分混合均勻,取少许混合物,加入少量水,慢慢摇制成颗粒状,将制备的直径为3〜IOmm的规整化填料放入烘箱中,于40°C下烘干其中的水分,将填料放入马弗炉中,在隔绝氧的条件下,于250°C 焙烧4h,焙烧结束后将填料取出、冷却,即得规整化铁碳微电解填料。
[0015] 实施例2[0016] 将直径小于Imm的铁屑256g(重量百分比64% )、直径小于0. Imm的粉末活性炭340g (重量百分比10%)和直径小于0. 15mm的粘土104g (重量百分比充分混合均勻,取少许混合物,加入少量水,慢慢摇制成颗粒状,将制备的直径为3〜IOmm的规整化填料放入烘箱中,于50°C下烘干其中的水分,将填料放入马弗炉中,在隔绝氧的条件下于400°C焙烧池,焙烧结束后将填料取出、冷却,即得规整化铁碳微电解填料。
[0017] 实施例3[0018] 将直径0. 15〜0. 5mm的铁屑272g (重量百分比68% )、直径小于0. Imm的粉末活性炭68g(重量百分比17% )和直径小于0. 15mm的粘土60g(重量百分比15% )充分混合均勻,取少许混合物,加入少量水,慢慢摇制成颗粒状,将制备的直径为3〜IOmm的规整化填料放入烘箱中,于30°C下烘干其中的水分,将填料放入马弗炉中,在隔绝氧的条件下于600°C焙烧池,焙烧结束后将填料取出、冷却,即得规整化铁碳微电解填料。
[0019] 实施例4[0020] 将直径0. 3〜0. 6mm的铁屑320g(重量百分比80% )、直径小于0. Imm的粉末活性炭20g (重量百分比5%)和直径小于0. 15mm的粘土60g (重量百分比15%)充分混合均勻,取少许混合物,加入少量水,慢慢摇制成颗粒状,将制备的直径为3〜IOmm的规整化填料放入烘箱中,于30°C下烘干其中的水分,将填料放入马弗炉中,在隔绝氧的条件下于600°C焙烧池,焙烧结束后将填料取出、冷却,即得规整化铁碳微电解填料。
[0021] 二、本发明规整化铁碳微电解填料在实验室范围内处理废水的应用情况[0022] 1、应用规整化铁碳微电解填料处理含苯、甲苯、乙苯和二甲苯的废水,在停留时间lOOmin,初始苯、甲苯、乙苯和二甲苯浓度分别为185. llmg/L、77. 81mg/L、37. 17mg/L 和33. 95mg/L,经微电解填料处理后,各物质的去除率可以达到80%以上,经过14天的连续运行,没有发现填料板结现象。
[0023] 2、应用规整化铁碳微电解填料处理含氯苯的废水,在停留时间池,初始氯苯浓度为200mg/L,经过微电解填料处理后,去除率可以达到90%以上,连续运行25天,处理效果稳定。
一种高效能、抗板结微电解材料及其制备方法CN 101838034 B摘要本发明公开了一种高效能、抗板结的微电解材料,孔隙率为0.5-0.8,比表面积为0.4-1.0m2/g。
其制备方法为首先将铁粉、活性炭粉末、钠基膨润土和NH4Cl充分混合后,加水调匀;然后用成球机做成直径为2-5mm的小球,烘干;最后将烘干后的球状材料进行焙烧,自然冷却至室温。
与传统微电解材料相比,本发明的优点在于:利用NH4Cl在高温条件下产生的NH3起到造孔的作用,增大了材料的孔隙率和比表面积,提高了微电解材料对废水中污染物的去除效果;同时,材料为球状规整材料,具有较好的机械强度,避免了材料在使用过程中的压实,不易发生板结和钝化现象,使用寿命较长,从而保证了微电解工艺的长期稳定运行。
权利要求(6)1. 一种高效能、抗板结的微电解材料,其特征在于,按照下述步骤制备:(1)将铁粉、活性炭粉末、钠基膨润土和NH4Cl充分混合后,加水调勻,其中所述铁粉、活性炭粉末、钠基膨润土和NH4Cl的质量比为0.8-3) :(2. 8-3) :(3.8-4) :0.05;(2)用成球机将步骤(1)得到的混合物做成直径为2-5mm的小球,烘干;(3)对经过步骤(¾烘干后的球状材料进行焙烧,所述焙烧机制为在370-420°C下,焙烧10-12分钟,然后升温至1100-1200°C,焙烧15-18分钟,自然冷却至室温;所述微电解材料的孔隙率为0. 5-0. 8 ;所述微电解材料的比表面积为0. 4-1.0m2/g。
2.根据权利要求1所述的一种高效能、抗板结的微电解材料,其特征在于,所述步骤⑴中,铁粉、活性炭粉末、钠基膨润土和NH4Cl的质量比为3 : 3 : 4 :0.05。
3.根据权利要求1所述的一种高效能、抗板结的微电解材料,其特征在于,所述步骤(3)中的焙烧机制为在400°C下,焙烧10分钟,然后升温至1150°C,焙烧15分钟,自然冷却至室温。
4. 一种制备微电解材料的方法,其特征在于,按照下述步骤进行:(1)将铁粉、活性炭粉末、钠基膨润土和NH4Cl充分混合后,加水调勻,其中所述铁粉、活性炭粉末、钠基膨润土和NH4Cl 的质量比为0.8-3) :(2. 8-3) :(3.8-4) :0.05;(2)用成球机将步骤(1)得到的混合物做成直径为2-5mm的小球,烘干;(3)对经过步骤(¾烘干后的球状材料进行焙烧,所述焙烧机制为在370-420°C下,焙烧10-12分钟,然后升温至1100-1200°C,焙烧15-18分钟,自然冷却至室温。
5.根据权利要求4所述的一种制备微电解材料的方法,其特征在于,所述步骤(1)中,铁粉、活性炭粉末、钠基膨润土和NH4Cl的质量比为3 : 3 : 4 :0.05。
6.根据权利要求4所述的一种制备微电解材料的方法,其特征在于,所述步骤(3)中的焙烧机制为在400°C下,焙烧10分钟,然后升温至1150°C,焙烧15分钟,自然冷却至室温。
说明一种高效能、抗板结微电解材料及其制备方法技术领域[0001] 本发明涉及一种材料及其制备方法,更具体地说,涉及一种高效能、抗板结微电解材料及其制备方法。
背景技术[0002] 工业废水因具有污染物浓度高、毒性大、可生化性差等特点,对生态环境造成严重威胁。
微电解技术由于处理效果好、原料简单、来源广泛等特点而成为重要的工业废水污染控制技术。
[0003] 微电解技术又称为内电解法或铁碳法,是电化学污水处理技术中的一种。
在微电解技术中,微电解材料是该技术的核心部分,微电解材料的选择和制备,对污染物的去除效果和运行稳定性具有关键性的影响。
[0004] 目前,传统的微电解技术大多采用铁屑和活性炭粉(或焦炭粉)的简单混合物作为微电解材料,这种微电解材料在运行一段时间后,材料表面会形成钝化膜,同时材料易结块,从而阻碍材料与废水的有效接触,导致微电解对废水的处理效果迅速下降,大大限制了微电解技术的应用。
因此,开发高效能、抗板结的新型材料对于推广应用微电解技术具有重要意义。