汽车轮毂的制造工艺
钢制轮毂生产工艺
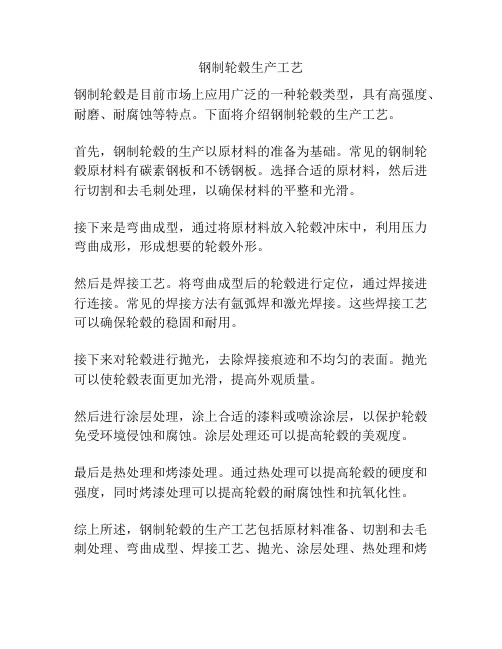
钢制轮毂生产工艺
钢制轮毂是目前市场上应用广泛的一种轮毂类型,具有高强度、耐磨、耐腐蚀等特点。
下面将介绍钢制轮毂的生产工艺。
首先,钢制轮毂的生产以原材料的准备为基础。
常见的钢制轮毂原材料有碳素钢板和不锈钢板。
选择合适的原材料,然后进行切割和去毛刺处理,以确保材料的平整和光滑。
接下来是弯曲成型,通过将原材料放入轮毂冲床中,利用压力弯曲成形,形成想要的轮毂外形。
然后是焊接工艺。
将弯曲成型后的轮毂进行定位,通过焊接进行连接。
常见的焊接方法有氩弧焊和激光焊接。
这些焊接工艺可以确保轮毂的稳固和耐用。
接下来对轮毂进行抛光,去除焊接痕迹和不均匀的表面。
抛光可以使轮毂表面更加光滑,提高外观质量。
然后进行涂层处理,涂上合适的漆料或喷涂涂层,以保护轮毂免受环境侵蚀和腐蚀。
涂层处理还可以提高轮毂的美观度。
最后是热处理和烤漆处理。
通过热处理可以提高轮毂的硬度和强度,同时烤漆处理可以提高轮毂的耐腐蚀性和抗氧化性。
综上所述,钢制轮毂的生产工艺包括原材料准备、切割和去毛刺处理、弯曲成型、焊接工艺、抛光、涂层处理、热处理和烤
漆处理等环节。
这些工艺都是为了生产出质量稳定、耐用且美观的钢制轮毂。
轮毂的轮毂制造工艺的选择

轮毂的轮毂制造工艺的选择轮毂是汽车的重要部件,负责承载车辆的重量和保持车辆稳定性。
不同的车辆需要不同类型的轮毂,因此轮毂制造具有多样性。
轮毂的制造工艺也是影响轮毂质量和性能的一个重要因素。
本文将讨论轮毂制造工艺的选择。
轮毂材料的选择轮毂的材料对其质量和性能有着重要的影响。
通常,轮毂材料需要满足以下要求:1.足够强度和硬度;2.足够的韧性;3.耐腐蚀性良好;4.易于制造。
常用的轮毂材料有铝合金、镁合金、钢铁等。
铝合金轮毂数量较多,其优点是轻质、强度高、耐腐蚀性好,可以降低车辆的燃油消耗。
镁合金轮毂也具有轻质、强度高的优点,但容易腐蚀。
钢铁轮毂强度较高,但重量较大,不适合要求节油的车辆。
轮毂制造工艺轮毂制造工艺涉及到轮毂的成型、加工和表面处理等环节。
制造轮毂的常用工艺有以下几种:1.铸造铸造是将熔融金属注入模具中成型的方法,铸造成本较低,但轮毂强度较低,且容易出现气孔、缺陷等问题。
2.锻造锻造是将金属通过力量的作用进行变形,得到所需形状与尺寸的方法。
锻造轮毂具有材料均匀、强度高的特点,但成本较高。
3.压铸压铸通过受力作用把熔融金属压入模具里形成制品。
压铸轮毂表面质量较好,但强度和韧性低。
4.钣金成形钣金成形是通过将金属板材经过冲压、折弯、压模等多道工艺步骤处理得到所需形状与尺寸的方法。
钣金制造成本较低,但轮毂强度较低。
5.机加工机加工是通过机床或精密加工设备对金属材料进行切削、冲孔、车削、铣削等方法制造轮毂。
机加工工艺复杂,成本较高,但轮毂质量和精度均较高。
轮毂表面处理轮毂表面处理是为了保护轮毂表面免受腐蚀和氧化,提高轮毂的美观度。
常见的轮毂表面处理方法有以下几种:1.电镀处理电镀处理是将金属放入电解液中,通过电流的作用,在金属表面形成一层保护膜的方法。
电镀处理可以提高轮毂表面的硬度和外观质量,但对环境的污染比较严重。
2.喷涂处理喷涂处理是通过将喷涂油漆或表面处理材料喷涂在轮毂表面的方法。
喷涂处理可以改善轮毂的外观和防腐性能,但需要定期维护。
汽车轮毂制造工艺
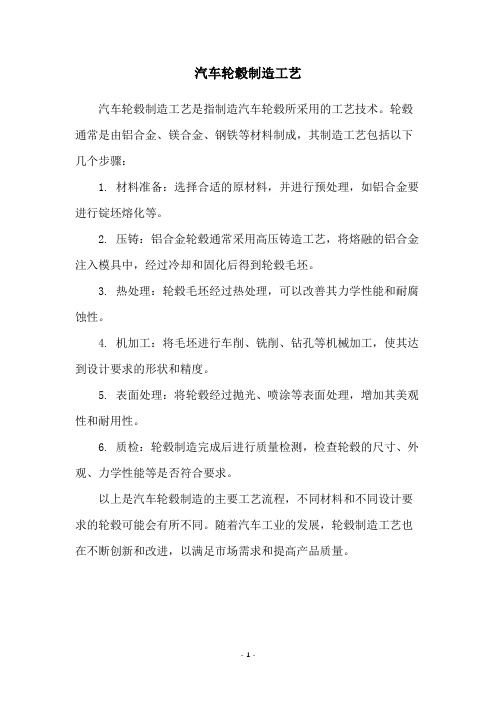
汽车轮毂制造工艺
汽车轮毂制造工艺是指制造汽车轮毂所采用的工艺技术。
轮毂通常是由铝合金、镁合金、钢铁等材料制成,其制造工艺包括以下几个步骤:
1. 材料准备:选择合适的原材料,并进行预处理,如铝合金要进行锭坯熔化等。
2. 压铸:铝合金轮毂通常采用高压铸造工艺,将熔融的铝合金注入模具中,经过冷却和固化后得到轮毂毛坯。
3. 热处理:轮毂毛坯经过热处理,可以改善其力学性能和耐腐蚀性。
4. 机加工:将毛坯进行车削、铣削、钻孔等机械加工,使其达到设计要求的形状和精度。
5. 表面处理:将轮毂经过抛光、喷涂等表面处理,增加其美观性和耐用性。
6. 质检:轮毂制造完成后进行质量检测,检查轮毂的尺寸、外观、力学性能等是否符合要求。
以上是汽车轮毂制造的主要工艺流程,不同材料和不同设计要求的轮毂可能会有所不同。
随着汽车工业的发展,轮毂制造工艺也在不断创新和改进,以满足市场需求和提高产品质量。
- 1 -。
汽车轮毂知识简介

工艺:铸造模具使用范围:汽车、摩托车等铝合金配件。
加工方式:来图来样加工;汽车轮毂模具种类包括重力模、低压模、差压模。
摩轮是属于重力模,如汽车法兰盘,属于高压模;模具有单边浇和双边浇,重力模边模属于两边开,低压模、差压模、高压模边模是四边开;每一套模具配两件卡规,同时附上一份产品合格证书和一个光盘。
加工部件:底模、边模、上模、承座、冒口、材面售后服务:产品提供维修。
锻造铝轮圈成本高锻造铝合金轮圈和通俗卡车铁圈阐发及对比:1、自身轻。
锻造铝圈的重量只相当于铁圈的二分之一重,以22.5X8.5的为例;锻造铝圈为25公斤,铁圈为至少45公斤。
2、节流燃油。
安装锻造铝圈今后,因为整车的重量降低,削减了车轮的动弹惯性,使汽车加快机能提高,并响应削减了制动能量的需求,从而降低了油耗,再加上锻造铝圈特有的空气流动及滚动阻力,所以百公里测试节流率为每百公里起码节流2升油(改换锻造铝圈并利用空调今后的百公里油耗比未换锻造铝圈并未开空调的油耗测试,前者比后者低2.5升油耗)。
3、轮胎磨损降低26%。
因为锻造圈的特征,它的均衡值为0,不轻易变形,散温快(正常行驶温度比铁圈低20-30度)对吊挂系统的庇护较佳,所以对轮胎的磨损大大降低,使每条轮胎多跑5-8万公里不等)。
4、刹车的维修费用降低。
因为锻造铝圈的特征散温快,正常行驶温度低,所以对刹车系统不耐高温的材料及配件有极佳的庇护结果,从而大大降低了刹车系统的维修费用。
5、承载能力高,锻造圈的承载能量是通俗铁圈的5倍。
锻造车轮在承受71200公斤后才变形5厘米。
铁圈只承受13600公斤后已变形5厘米,换句话说,锻造车圈的强度是超越钢圈的5倍。
6、提高驾驶的舒适性。
因为锻造车轮的特征,安装后行车感受偏向较轻,高速行驶出格平稳,从而提高了驾驶乐趣。
7、平安性好。
对于高速行驶的汽车来说,因轮胎着地摩擦、制动等发生的高温爆胎、制动效能降低等现象不足为奇。
而铝合金的热传导系数是钢、铁等的三倍,加上铝合金车轮因其布局的特征,极易将轮胎、车底盘所发生的热量排散在空气中。
旋压轮毂工艺原理
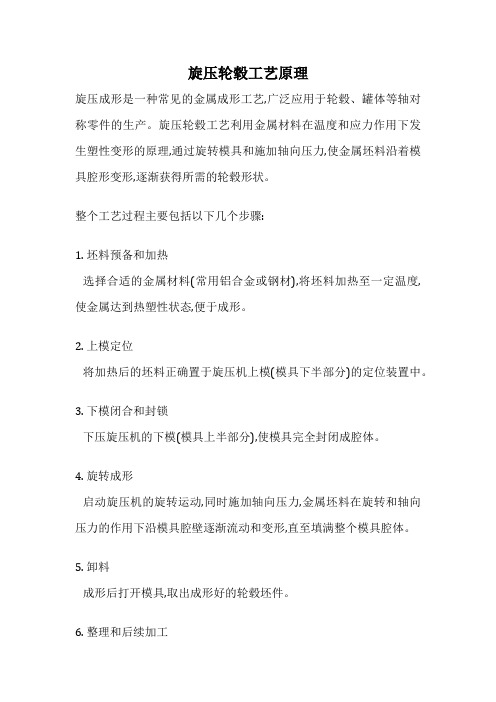
旋压轮毂工艺原理
旋压成形是一种常见的金属成形工艺,广泛应用于轮毂、罐体等轴对称零件的生产。
旋压轮毂工艺利用金属材料在温度和应力作用下发生塑性变形的原理,通过旋转模具和施加轴向压力,使金属坯料沿着模具腔形变形,逐渐获得所需的轮毂形状。
整个工艺过程主要包括以下几个步骤:
1. 坯料预备和加热
选择合适的金属材料(常用铝合金或钢材),将坯料加热至一定温度,使金属达到热塑性状态,便于成形。
2. 上模定位
将加热后的坯料正确置于旋压机上模(模具下半部分)的定位装置中。
3. 下模闭合和封锁
下压旋压机的下模(模具上半部分),使模具完全封闭成腔体。
4. 旋转成形
启动旋压机的旋转运动,同时施加轴向压力,金属坯料在旋转和轴向压力的作用下沿模具腔壁逐渐流动和变形,直至填满整个模具腔体。
5. 卸料
成形后打开模具,取出成形好的轮毂坯件。
6. 整理和后续加工
对轮毂坯件进行切边、去毛刺等整理,并根据需要进行热处理、机加工等后续工序。
旋压工艺的优点在于能高效生产出具有良好力学性能和尺寸精度的轴对称零件,并且材料利用率较高,适用于批量生产。
同时,通过调整加工参数如旋转速度、轴向压力等,可以优化成形质量。
因此,旋压轮毂工艺在汽车制造等行业广受应用。
轮毂铸造知识点总结
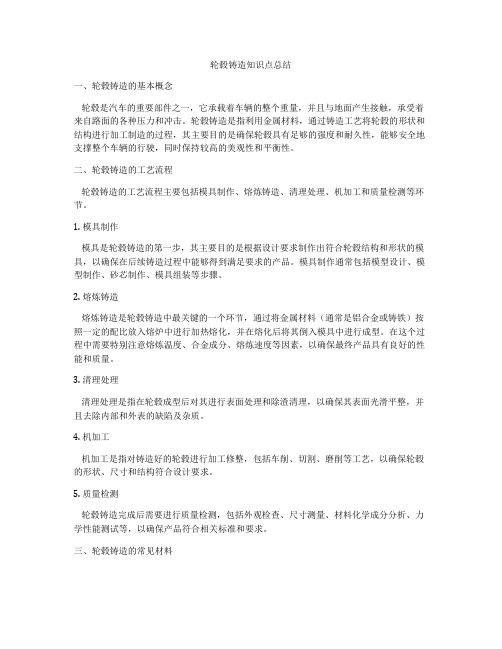
轮毂铸造知识点总结一、轮毂铸造的基本概念轮毂是汽车的重要部件之一,它承载着车辆的整个重量,并且与地面产生接触,承受着来自路面的各种压力和冲击。
轮毂铸造是指利用金属材料,通过铸造工艺将轮毂的形状和结构进行加工制造的过程,其主要目的是确保轮毂具有足够的强度和耐久性,能够安全地支撑整个车辆的行驶,同时保持较高的美观性和平衡性。
二、轮毂铸造的工艺流程轮毂铸造的工艺流程主要包括模具制作、熔炼铸造、清理处理、机加工和质量检测等环节。
1. 模具制作模具是轮毂铸造的第一步,其主要目的是根据设计要求制作出符合轮毂结构和形状的模具,以确保在后续铸造过程中能够得到满足要求的产品。
模具制作通常包括模型设计、模型制作、砂芯制作、模具组装等步骤。
2. 熔炼铸造熔炼铸造是轮毂铸造中最关键的一个环节,通过将金属材料(通常是铝合金或铸铁)按照一定的配比放入熔炉中进行加热熔化,并在熔化后将其倒入模具中进行成型。
在这个过程中需要特别注意熔炼温度、合金成分、熔炼速度等因素,以确保最终产品具有良好的性能和质量。
3. 清理处理清理处理是指在轮毂成型后对其进行表面处理和除渣清理,以确保其表面光滑平整,并且去除内部和外表的缺陷及杂质。
4. 机加工机加工是指对铸造好的轮毂进行加工修整,包括车削、切割、磨削等工艺,以确保轮毂的形状、尺寸和结构符合设计要求。
5. 质量检测轮毂铸造完成后需要进行质量检测,包括外观检查、尺寸测量、材料化学成分分析、力学性能测试等,以确保产品符合相关标准和要求。
三、轮毂铸造的常见材料轮毂铸造使用的主要材料包括铝合金、铸铁和钢铁等,它们各自具有不同的特性和适用范围。
1. 铝合金铝合金轮毂具有较高的强度和耐腐蚀性能,重量轻、抗冲击能力强,因此广泛应用于汽车等交通工具。
但相对而言成本较高,所以市场份额相对较小。
2. 铸铁铸铁轮毂价格低廉、强度高,广泛用于商用车和农用车等重载车辆上。
但密度较大,重量较重,对车辆的燃油经济性影响较大。
汽车轮毂制造工艺流程

汽车轮毂制造工艺流程一、原料准备汽车轮毂的制造过程首先需要准备原料。
常见的轮毂材料包括铝合金、镁合金和钢材等。
在选材时需要考虑轮毂的重量、强度和耐腐蚀性能等因素。
原料准备的关键是确保原料质量和规格的一致性,以保证后续加工的精度和质量。
二、铸造铸造是制造轮毂的主要工艺之一。
铸造可以分为压铸和重力铸造两种方式。
在压铸过程中,将预热的金属材料注入金属模具中,然后施加压力使其充分填充模具腔体,并通过冷却使其凝固。
重力铸造则通过重力作用使熔化金属流入模具中,并在冷却后形成轮毂的初步形状。
铸造工艺需要控制好铸件的凝固过程,以确保轮毂的内部结构和尺寸的精度。
三、精密加工精密加工是对铸造好的轮毂进行后续加工和整形的过程。
首先是去除铸造过程中产生的毛刺和气孔等缺陷,常用的方法包括研磨、修整和喷砂等。
接下来是通过车削、铣削和钻孔等工艺对轮毂进行精确的加工和成形。
精密加工工艺需要保证轮毂的尺寸和形状的精度,以满足汽车的使用要求。
四、热处理热处理是一种通过加热和冷却来改变材料的物理和化学性质的工艺。
对于轮毂的制造而言,常见的热处理工艺包括退火、淬火和时效等。
退火可以消除材料内部的应力和组织缺陷,提高其塑性和韧性。
淬火则可以使材料获得更高的硬度和强度。
时效是指将材料在一定温度下保持一段时间,使其组织和性能稳定。
热处理过程需要控制好温度和时间的参数,以确保轮毂的性能和寿命。
五、表面处理表面处理是对轮毂进行表面涂层或处理的过程,旨在提高其耐腐蚀性和美观度。
常见的表面处理方法包括电镀、喷涂和阳极氧化等。
电镀可以在轮毂表面形成一层金属保护层,提高其耐腐蚀性。
喷涂则可以给轮毂涂上一层防锈漆,增加其使用寿命。
阳极氧化是一种通过电解氧化使轮毂表面形成氧化膜的方法,使其具有更好的耐磨性和耐腐蚀性。
表面处理工艺需要控制好涂层的厚度和均匀性,以确保轮毂的质量和外观。
六、质量检测质量检测是轮毂制造过程中的重要环节。
通过对轮毂进行尺寸测量、表面检查和力学性能测试等,以确保轮毂的质量符合要求。
rays 轮毂生产工艺
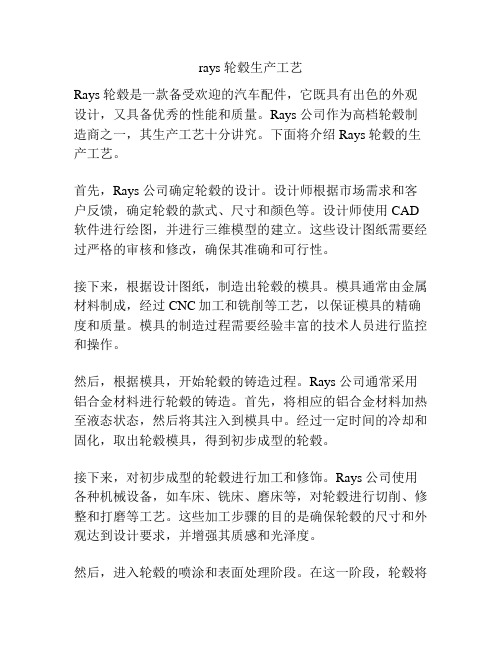
rays 轮毂生产工艺Rays 轮毂是一款备受欢迎的汽车配件,它既具有出色的外观设计,又具备优秀的性能和质量。
Rays 公司作为高档轮毂制造商之一,其生产工艺十分讲究。
下面将介绍 Rays 轮毂的生产工艺。
首先,Rays 公司确定轮毂的设计。
设计师根据市场需求和客户反馈,确定轮毂的款式、尺寸和颜色等。
设计师使用CAD 软件进行绘图,并进行三维模型的建立。
这些设计图纸需要经过严格的审核和修改,确保其准确和可行性。
接下来,根据设计图纸,制造出轮毂的模具。
模具通常由金属材料制成,经过CNC加工和铣削等工艺,以保证模具的精确度和质量。
模具的制造过程需要经验丰富的技术人员进行监控和操作。
然后,根据模具,开始轮毂的铸造过程。
Rays 公司通常采用铝合金材料进行轮毂的铸造。
首先,将相应的铝合金材料加热至液态状态,然后将其注入到模具中。
经过一定时间的冷却和固化,取出轮毂模具,得到初步成型的轮毂。
接下来,对初步成型的轮毂进行加工和修饰。
Rays 公司使用各种机械设备,如车床、铣床、磨床等,对轮毂进行切削、修整和打磨等工艺。
这些加工步骤的目的是确保轮毂的尺寸和外观达到设计要求,并增强其质感和光泽度。
然后,进入轮毂的喷涂和表面处理阶段。
在这一阶段,轮毂将经过清洗、除锈和喷涂等工艺。
首先,轮毂表面将进行清洗和除锈,以去除任何污垢和氧化物。
然后,喷涂底漆和表面涂层,以增加轮毂的耐用性和外观质感。
通常,Rays 公司会采用多种颜色和材质的涂层,以满足不同客户的需求。
最后,轮毂经过严格的质量检测和包装流程。
Rays 公司会对轮毂进行各项性能测试,如承载能力、抗冲击性和耐腐蚀性等。
只有通过了这些测试,轮毂才能被认可。
之后,轮毂将进行包装,通常使用泡沫塑料和纸板箱进行包装,以防止在运输过程中受到损坏。
综上所述,Rays 轮毂的生产工艺经过了精心设计和精细加工。
从轮毂的设计、模具的制造、铸造、加工、喷涂到质量检测和包装,每个步骤都非常重要,以确保生产出具有卓越外观和优秀性能的高质量轮毂。
轮毂铸造工艺流程

轮毂铸造工艺流程
《轮毂铸造工艺流程》
轮毂铸造是制造汽车轮毂的重要工艺过程之一。
其工艺流程包括模具制造、熔炼、浇注、清理和表面处理等环节。
首先是模具制造,根据轮毂的设计图纸制作模具,模具一般由砂型和金属型组成。
接下来是熔炼,将铁水加热至一定温度,然后将铝合金装入炉中进行熔炼。
浇注环节是将熔化的金属倒入模具中,使其填满整个模具,形成轮毂的初步形态。
清理环节是将轮毂从模具中取出,然后进行余砂清理和修整工艺。
最后是表面处理,包括喷涂、研磨、抛光等环节,使轮毂表面光洁、亮丽。
整个轮毂铸造工艺流程需要严格控制每个环节的工艺参数,以保证最终产品的质量和性能。
同时,还需要注意环境保护和能源消耗等方面的问题,确保生产过程的环保和可持续发展。
随着汽车工业的不断发展,轮毂铸造工艺也在不断创新和改进,为汽车轮毂的质量和外观提供了更好的保障。
我们相信,在技术的不断进步和工艺的不断改进下,轮毂铸造工艺将为汽车工业的发展贡献更多的力量。
轮毂制造工艺流程
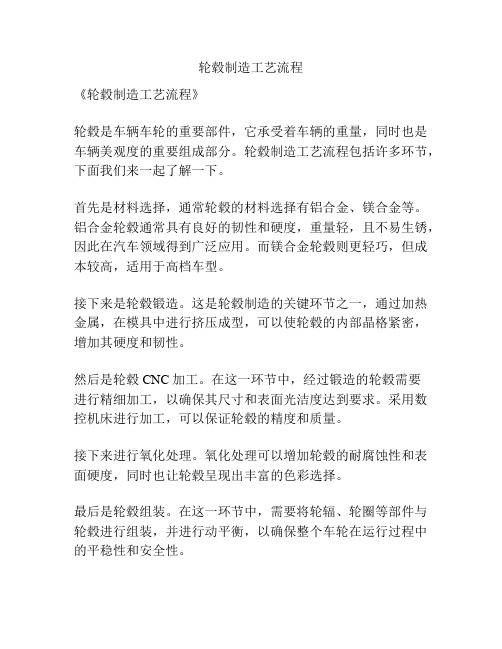
轮毂制造工艺流程
《轮毂制造工艺流程》
轮毂是车辆车轮的重要部件,它承受着车辆的重量,同时也是车辆美观度的重要组成部分。
轮毂制造工艺流程包括许多环节,下面我们来一起了解一下。
首先是材料选择,通常轮毂的材料选择有铝合金、镁合金等。
铝合金轮毂通常具有良好的韧性和硬度,重量轻,且不易生锈,因此在汽车领域得到广泛应用。
而镁合金轮毂则更轻巧,但成本较高,适用于高档车型。
接下来是轮毂锻造。
这是轮毂制造的关键环节之一,通过加热金属,在模具中进行挤压成型,可以使轮毂的内部晶格紧密,增加其硬度和韧性。
然后是轮毂CNC加工。
在这一环节中,经过锻造的轮毂需要
进行精细加工,以确保其尺寸和表面光洁度达到要求。
采用数控机床进行加工,可以保证轮毂的精度和质量。
接下来进行氧化处理。
氧化处理可以增加轮毂的耐腐蚀性和表面硬度,同时也让轮毂呈现出丰富的色彩选择。
最后是轮毂组装。
在这一环节中,需要将轮辐、轮圈等部件与轮毂进行组装,并进行动平衡,以确保整个车轮在运行过程中的平稳性和安全性。
通过上述工艺流程,我们可以看出,轮毂的制造过程需要经过多个环节的精细加工和处理,以确保最终产品达到优质的标准。
而随着技术的不断进步,轮毂制造工艺也在不断优化和改进,以满足不同车型和需求的要求。
轮毂工艺流程
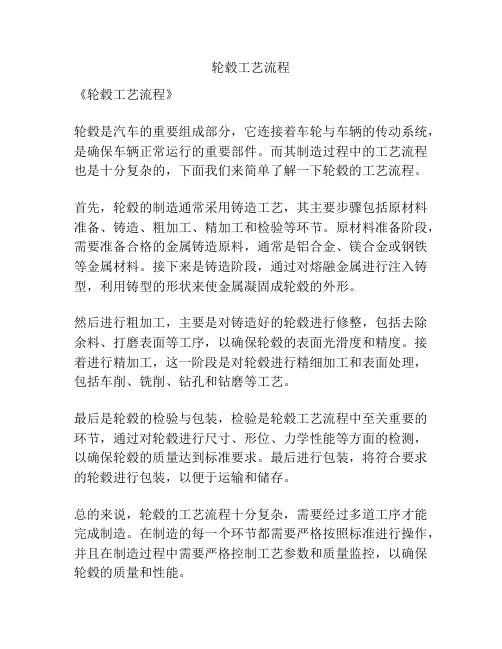
轮毂工艺流程
《轮毂工艺流程》
轮毂是汽车的重要组成部分,它连接着车轮与车辆的传动系统,是确保车辆正常运行的重要部件。
而其制造过程中的工艺流程也是十分复杂的,下面我们来简单了解一下轮毂的工艺流程。
首先,轮毂的制造通常采用铸造工艺,其主要步骤包括原材料准备、铸造、粗加工、精加工和检验等环节。
原材料准备阶段,需要准备合格的金属铸造原料,通常是铝合金、镁合金或钢铁等金属材料。
接下来是铸造阶段,通过对熔融金属进行注入铸型,利用铸型的形状来使金属凝固成轮毂的外形。
然后进行粗加工,主要是对铸造好的轮毂进行修整,包括去除余料、打磨表面等工序,以确保轮毂的表面光滑度和精度。
接着进行精加工,这一阶段是对轮毂进行精细加工和表面处理,包括车削、铣削、钻孔和钻磨等工艺。
最后是轮毂的检验与包装,检验是轮毂工艺流程中至关重要的环节,通过对轮毂进行尺寸、形位、力学性能等方面的检测,以确保轮毂的质量达到标准要求。
最后进行包装,将符合要求的轮毂进行包装,以便于运输和储存。
总的来说,轮毂的工艺流程十分复杂,需要经过多道工序才能完成制造。
在制造的每一个环节都需要严格按照标准进行操作,并且在制造过程中需要严格控制工艺参数和质量监控,以确保轮毂的质量和性能。
汽车轮毂加工方法与工艺分析

本文以深槽轮辋为例,阐述兼具使用性能优点和加工成本优势的压力成形制造工艺。
通过分析轮毂的材料、结构及加工方法,详细介绍了轮辋生产过程及所用装备,并展望未来生产技术的特点和发展方向。
1 序言汽车作为现代化的交通工具,其数量越来越多。
车轮是汽车必须的、基本的和重要的部件,其安全性、经济性及外观质量是目前使用者关注的主要指标。
不同车辆的轮毂结构不同、材料不同,其加工工艺也不相同。
通过分析车辆轮毂常使用的材料及加工方法,着重介绍具有深槽结构的家用汽车铝合金轮毂加工工艺及其特点。
2 汽车轮毂的材料及制造现状2.1 轮毂结构与材料轮毂是汽车支撑轮胎的圆形结构,由轮辋和轮辐组成,轮辋和轮辐可以是整体式的、永久联接式的和可拆卸式的。
轮辋常使用的结构有深槽轮辋和平底轮辋,并在此结构上有不同的改进,比如对开式轮辋、半深槽轮辋、平底宽轮辋及全斜底轮辋,用于不同的场合。
深槽轮辋如图1所示,断面中部呈凹槽形,有凸缘结构,用于安放轮胎,肩部向中间倾斜4°~6°。
该结构简单,刚度大,质量较小,对于尺寸小、弹性大的轮胎安装比较方便,因此适用于轿车及轻型越野车。
平底轮辋是货车常用的结构形式。
图1 深槽轮辋常见的汽车轮毂有钢质轮毂和铝合金轮毂。
钢质轮毂强度高,常用于大型载货汽车,质量较重;铝合金轮毂质量相较要轻很多,相同体积的铝合金轮毂比钢质轮毂轻2/3左右,符合如今低碳的使用理念,且导热快,散热性能好。
图2永久联接式轮毂结构2.2 轮毂常用加工方法目前铝合金轮毂的生产方法有铸造法、锻造法、冲压法和旋压法。
我国铝合金轮毂仍然以低压铸造为主,随着技术的发展,其加工工艺不断进行变革。
铝合金的铸造工艺主要有4种:重力铸造、低压铸造、反压铸造和挤压铸造。
大部分的铝合金车轮采用低压铸造生产,这是铝合金车轮铸造工艺中的主要技术。
铸造车轮需要准备铸型,熔炼金属,浇筑冷却凝固成形后取出铸件,工序多、设备大,产品容易出现缩孔、缩松等质量缺陷,特别是铸件尺寸较薄的情况下,更容易出现质量问题。
轮毂铝合金生产工艺
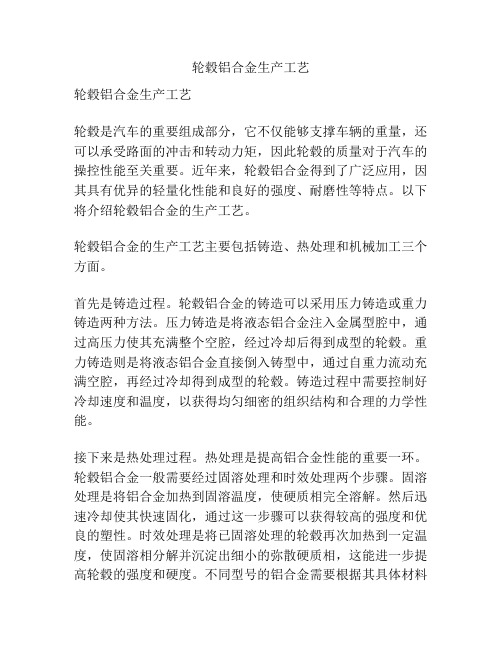
轮毂铝合金生产工艺轮毂铝合金生产工艺轮毂是汽车的重要组成部分,它不仅能够支撑车辆的重量,还可以承受路面的冲击和转动力矩,因此轮毂的质量对于汽车的操控性能至关重要。
近年来,轮毂铝合金得到了广泛应用,因其具有优异的轻量化性能和良好的强度、耐磨性等特点。
以下将介绍轮毂铝合金的生产工艺。
轮毂铝合金的生产工艺主要包括铸造、热处理和机械加工三个方面。
首先是铸造过程。
轮毂铝合金的铸造可以采用压力铸造或重力铸造两种方法。
压力铸造是将液态铝合金注入金属型腔中,通过高压力使其充满整个空腔,经过冷却后得到成型的轮毂。
重力铸造则是将液态铝合金直接倒入铸型中,通过自重力流动充满空腔,再经过冷却得到成型的轮毂。
铸造过程中需要控制好冷却速度和温度,以获得均匀细密的组织结构和合理的力学性能。
接下来是热处理过程。
热处理是提高铝合金性能的重要一环。
轮毂铝合金一般需要经过固溶处理和时效处理两个步骤。
固溶处理是将铝合金加热到固溶温度,使硬质相完全溶解。
然后迅速冷却使其快速固化,通过这一步骤可以获得较高的强度和优良的塑性。
时效处理是将已固溶处理的轮毂再次加热到一定温度,使固溶相分解并沉淀出细小的弥散硬质相,这能进一步提高轮毂的强度和硬度。
不同型号的铝合金需要根据其具体材料特性和应用要求来确定热处理工艺参数。
最后是机械加工过程。
机械加工包括车削、磨削、铣削、冲压等工艺,用于对轮毂进行细节加工和提供特定形状。
机械加工可以去除铸造过程中的缺陷和表面粗糙度,提高轮毂的精度和表面质量。
同时,机械加工还可以进行孔加工、螺纹加工等特殊工艺,以方便安装和使用。
综上所述,轮毂铝合金的生产工艺主要包括铸造、热处理和机械加工三个方面。
通过合理控制工艺参数和工艺流程,可以获得质量优良、性能稳定的轮毂铝合金产品。
随着材料科学和生产技术的不断进步,相信轮毂铝合金在未来会有更广泛的应用。
精选轮毂锻造工艺全

3,热处理:
1)提高铸件的力学性能,改善合金的切削性能;消除内应力;稳定铸件的尺寸 和组织,改善合金的组织和力学性能。 2)本工序控制要点:退火时间和温度(60-85℃,3min)。
4,机加工流程
1)数控机床加工工序划分的特点为:先粗后精,先面后孔,刀具集中 。
2)加工顺序: 按由内到外、又粗到精、由近到远的原则确定。毛坯——孔加工粗加工——孔半精加工— —孔精加工——外圆面加工——外圆面半精加工——阶梯面粗加工——阶梯面半精加 工——内圆加工——退刀面加工——不规则孔加工——型孔加工——气门孔加工——去 毛刺——零件最终热处理——清洗——终检 重点控制项目:中心孔直径、PCD位置度、端径跳、动平衡。
3)中心孔加工:按设计钻孔, 如PCD 5*120,CB 72.50等 等。先钻后车,以产品中心 孔定位,车削转速至少 2500r/min(粗糙度)
4)表面处理
5)检查
6)涂装: 铝合金车轮涂装的目的: 首先是提高车轮的运行可靠性和耐久性;其次是提高它的外观装饰性。
本工序控制要点:前处理槽液参数、调漆参数和固化参数。
外圆表面
型孔 中心孔 外倒角
2,功能
3,审美
4,轮毂受力
结构决定造型,结构决定受力,轮毂受力主要在轮辐上
加 工工 艺
1,加工结构及技术要求
1)轮毂技术要求: 孔与外圆一般具有 较高的同轴度要求; 端面与孔轴线的垂 直度要求;内孔表 面本身的尺寸精度、 形状精度及表面粗 糙度要求;外圆表 面本身的尺寸、形 状精度及表面粗糙 度要求等。
力学性能 6061的极限抗拉强度为124 MPa 受拉屈服强度 55.2 MPa 延伸率25.0 % 弹性系数68.9 GPa 弯曲极限强度228 MPa Bending Yield Strength 103 MPa 泊松比0.330 疲劳强度 62.1 MPa
汽车轮毂生产工艺

汽车轮毂生产工艺
汽车轮毂生产工艺分为铸造工艺、塑性加工工艺以及热处理工艺三个主要工艺环节。
首先是铸造工艺,铸造工艺是轮毂生产中最基础、最关键的工艺环节。
铸造工艺主要分为砂型铸造和压铸两种方式。
砂型铸造是一种传统的铸造方式,通过制作铁质砂型,将液态金属浇注到砂型中,经过凝固和冷却后,获得轮毂的基础形态。
而压铸则是将液态金属压入金属模具中进行成型,相比砂型铸造更加精细和高效。
在铸造工艺中,还需要进行砂型制作、充型、冷却、脱脆等环节,以确保轮毂的成型质量。
其次是塑性加工工艺,塑性加工工艺是对轮毂进行精细加工和成型的过程。
主要包括锻造和旋压两种方式。
锻造是将加热的金属料通过锻压设备,使其在一定的模具中受到压力和变形,最终获得所需的形状和尺寸。
旋压则是通过旋转和挤压的方式,将金属料塑成圆形的轮毂。
塑性加工工艺可以使轮毂具有更好的强度和耐久性,并且提高轮毂的整体质量。
最后是热处理工艺,热处理工艺主要通过对轮毂进行加热、保温和冷却等过程,以改变轮毂的组织结构和性能。
热处理工艺主要包括退火、淬火和回火等方式。
通过不同的热处理工艺,可以改变轮毂的硬度、强度、韧性和耐磨性等性能,以提高轮毂在使用过程中的性能和寿命。
综上所述,汽车轮毂的生产工艺包括铸造工艺、塑性加工工艺
和热处理工艺等环节。
通过这些工艺的精心设计和操作,可以生产出具有良好性能和质量的轮毂产品。
汽车轮毂涂装工艺流程
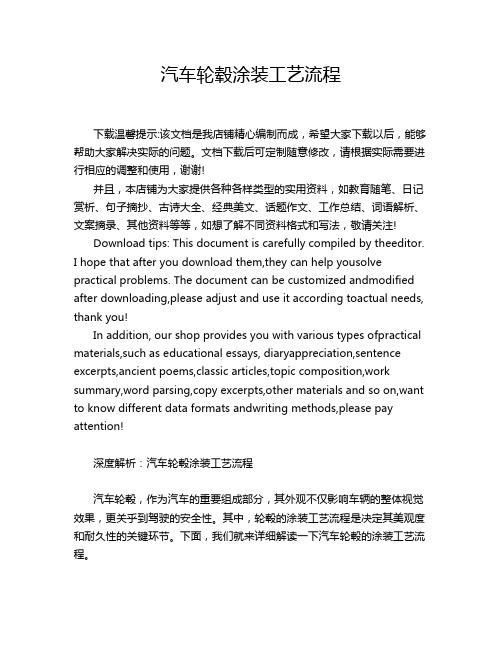
汽车轮毂涂装工艺流程下载温馨提示:该文档是我店铺精心编制而成,希望大家下载以后,能够帮助大家解决实际的问题。
文档下载后可定制随意修改,请根据实际需要进行相应的调整和使用,谢谢!并且,本店铺为大家提供各种各样类型的实用资料,如教育随笔、日记赏析、句子摘抄、古诗大全、经典美文、话题作文、工作总结、词语解析、文案摘录、其他资料等等,如想了解不同资料格式和写法,敬请关注!Download tips: This document is carefully compiled by theeditor.I hope that after you download them,they can help yousolve practical problems. The document can be customized andmodified after downloading,please adjust and use it according toactual needs, thank you!In addition, our shop provides you with various types ofpractical materials,such as educational essays, diaryappreciation,sentence excerpts,ancient poems,classic articles,topic composition,work summary,word parsing,copy excerpts,other materials and so on,want to know different data formats andwriting methods,please pay attention!深度解析:汽车轮毂涂装工艺流程汽车轮毂,作为汽车的重要组成部分,其外观不仅影响车辆的整体视觉效果,更关乎到驾驶的安全性。
汽车轮毂制造工艺

汽车轮毂制造工艺
汽车轮毂制造工艺是指制造汽车轮毂的技术和方法。
汽车轮毂是汽车的重要部件之一,它承载着车辆的重量并与轮胎紧密配合,同时也是车辆外观的重要组成部分。
汽车轮毂的制造工艺包括以下几个方面:
1.材料选择:汽车轮毂的材料选择对轮毂的质量和性能有着重要的影响。
常用的材料包括铝合金、镁合金、钢等。
2.铸造:铸造是制造轮毂的主要工艺之一。
常用的铸造方法包括压铸、砂型铸造、气压铸造等。
3.机加工:机加工是对铸造完成的轮毂进行加工和修整的过程。
机加工包括车削、钻孔、磨削等。
4.表面处理:表面处理是为了增强轮毂的抗腐蚀性和美观度。
表面处理的方法包括电泳涂装、喷涂、阳极氧化等。
5.组装与检测:轮毂组装需要进行精确的配合和安装,同时也需要进行严格的质量检测,以确保轮毂的品质。
以上就是汽车轮毂制造工艺的相关内容。
制造一款优质的汽车轮毂需要多个环节的精细操作和严格检测。
随着汽车工业的不断发展,轮毂的材料和制造工艺也在不断创新,以适应汽车市场的不断变化。
- 1 -。
- 1、下载文档前请自行甄别文档内容的完整性,平台不提供额外的编辑、内容补充、找答案等附加服务。
- 2、"仅部分预览"的文档,不可在线预览部分如存在完整性等问题,可反馈申请退款(可完整预览的文档不适用该条件!)。
- 3、如文档侵犯您的权益,请联系客服反馈,我们会尽快为您处理(人工客服工作时间:9:00-18:30)。
汽车轮毂制造技术班级:机电1302班学号:姓名:师世健指导教师:邢书明目录一、摘要 (3)二、汽车轮毂的选材 (3)1、钢铁材料 (3)1、1 球墨铸铁 (3)1、2 其她钢铁材料 (3)2、合金材料 (3)3、复合材料 (3)三、铸造方法 (3)1、压力铸造 (3)2、金属型铸造 (4)3、熔模铸造 (4)4、低压铸造 (5)5、离心铸造 (5)四、工艺方案 (6)1、零件图 (6)2、浇注位置 (6)3、分型面 (7)4、砂芯 (7)5、浇注系统 (7)6、主要工艺参数的确定 (7)7、冒口 (7)8、铸造工艺图 (8)汽车轮毂制造技术一、摘要轮毂,作为汽车一个重要组成结构,起着支撑车身重量的作用,对汽车节能、环保、安全性、操控性都有着极其重要的影响。
对其工作环境及使用要求予以充分分析,对其结构进行合理设计,选取性能优良的材料及适当的加工方法,都就是汽车轮毂制造中不可或缺的环节。
二、汽车轮毂的选材1.钢铁材料1、1 铸铁、铸钢球墨铸铁以其优良的综合力学性能应用在轮毂上,如铁素体球墨铸铁、高韧性球墨铸铁等。
但就是,由于类似碳素钢轮毂的缺点,以及铸造过程的复杂性与铸造模型所限,轮毂形状难于控制,限制了其应用。
1、2 其她钢铁材料一些合金钢如加入钛元素的低合金钢,合金元素可以细化晶粒,提高钢的力学性能,使钢具有强度高、塑韧性好、加工成形性与焊接性良好,可以作为轮毂用钢;此外,低合金高强度双相钢,如低碳含铌钢,提高贝氏体含量,可以提高屈服强度,提高扩孔率,也可以用作轮辐与轮辋用钢。
在实际应用中的多数钢制轮毂就是通过已成型的轮缘与轮盘焊接而成,尽量使自重降低。
2.合金材料汽车采用铝合金轮毂后减重效果明显,轻型车使用铝合金轮毂比传统钢制轮毂轻30%-40%,中型汽车可轻30%左右。
美国森特来因·图尔公司用分离旋压法制出的整体板材(6061合金)车轮,比钢板冲压车轮重量减轻达50%,旋压加工时间不到90s/个,不需要组装作业,适宜大批量生产。
另外,相同外径尺寸的轮毂使用铝合金轮毂抗压强度还有所提高。
3.复合材料复合材料就是应现代科学技术发展而出现的具有强大生命力的材料。
由于复合材料具有特殊的振动阻尼特性,可减振与降低噪声、抗疲劳性能好,损伤后易修理,便于整体成形,故可用于制造汽车车身、受力构件、传动轴、发动机架及其内部构件。
三、铸造方法1、压力铸造压力铸造的实质就是使液态金属在高压作用下以极高的速度充填型腔,并在压力作用下凝固而获得铸件的一种方法。
采用压铸工艺生产的铸件组织致密、机械性能好、强度与表面硬度较高、铸件的尺寸精确、表面光洁。
但传统压铸工艺生产的铝轮毂最大的缺点就是不能通过热处理来进一步提高性能,由于液体金属充型速度极快,型腔中的气体很难完全排除,常以气孔形式存留在铸件中,这些铸件孔隙中的气体在热处理过程中会发生膨胀,使得铸件“起泡”。
为使压铸件也能适用于汽车保安件。
近年来出现了一些无气孔压铸新工艺,最有代表的就是充氧压铸法。
充氧压铸法就是使压室与压型型腔内的金属液相间的空间充氧置换,并在高速高压下进行压铸,当液体金属充填时,一方面通过排气槽排出氧气,另一方面喷散的铝液与未排出的氧气发生反应,形成氧化铝小微粒,分散在铸件内部,使铸件内不产生气孔。
用充氧压铸法生产的铸件,含气量为只有普通压铸法的1/10,可进行固溶处理与焊接。
与传统压铸法相比,充氧压铸的铝轮毂具有成品率高,组织致密,良好的拉伸强度与耐疲劳性能等优点。
国外该方法已广泛用于铝轮毂的生产,日本轻金属株式会社于1983年开始用此方法大批量生产轿车铝合金轮毂,较采用其它铸造方法生产的同类产品重量减少了15%机加工切削量由原来的2~3mm减少到0、75mm,轮毂价格降低了10%。
美国铸锻公司于1982年开始用充氧压铸法生产汽车铝合金轮毂,代替了原来的低压铸造法,并使铝轮毂的重量减轻了18%。
由于有较高的机械性能与较轻的重量,充氧压铸铝轮毂用于紧急救援车与高级车辆就是十分理想的。
2、金属型铸造金属型铸造又称硬模铸造,它就是将液体金属浇入金属铸型,以获得铸件的一种铸造方法。
铸型就是用金属制成,可以反复使用多次(几百次到几千次)。
金属型铸造目前所能生产的铸件,在重量与形状方面还有一定的限制,如对黑色金属只能就是形状简单的铸件;铸件的重量不可太大;壁厚也有限制,较小的铸件壁厚无法铸出。
与砂型铸造比较:在技术上与经济上有许多优点。
金属型生产的铸件,其机械性能比砂型铸件高。
同样合金,其抗拉强度平均可提高约25%,屈服强度平均提高约20%,其抗蚀性能与硬度亦显著提高;铸件的精度与表面光洁度比砂型铸件高,而且质量与尺寸稳定;铸件的工艺收得率高,液体金属耗量减少,一般可节约15~30%;不用砂或者少用砂,一般可节约造型材料80~100%;此外,金属型铸造的生产效率高;使铸件产生缺陷的原因减少;工序简单,易实现机械化与自动化。
金属型铸造虽有很多优点,但也有不足之处。
如:金属型制造成本高;金属型不透气,而且无退让性,易造成铸件浇不足、开裂或铸铁件白口等缺陷;金属型铸造时,铸型的工作温度、合金的浇注温度与浇注速度,铸件在铸型中停留的时间,以及所用的涂料等,对铸件的质量的影响甚为敏感,需要严格控制。
解决这些缺陷可以尽量选用成本较低的金属制造模型,并在型腔内留出透气孔,但因为其制造成本太高,还就是不宜应用于汽车轮毂的制造。
3、熔模铸造熔模铸造又称失蜡法。
失蜡法就是用腊制作所要铸成器物的模子,然后在蜡模上涂以泥浆,这就就是泥模。
泥模晾干后,在焙烧成掏模。
一经焙烧,蜡模全部熔化流失,只剩陶模。
一般制泥模时就留下了浇注口,再从浇注口灌入铜液,冷却后,所需的器物就制成了。
熔模铸件尺寸精度较高,当然由于熔模铸造的工艺过程复杂,影响铸件尺寸精度的因素较多,例如模料的收缩、熔模的变形、型壳在加热与冷却过程中的线量变化、合金的收缩率以及在凝固过程中铸件的变形等,所以普通熔模铸件的尺寸精度虽然较高,但其一致性仍需提高。
压制熔模时,采用型腔表面光洁度高的压型,因此,熔模的表面光洁度也比较高。
此外,型壳由耐高温的特殊粘结剂与耐火材料配制成的耐火涂料涂挂在熔模上而制成,与熔融金属直接接触的型腔内表面光洁度高。
所以,熔模铸件的表面光洁度比一般铸造件的高。
熔模铸造最大的优点就就是由于熔模铸件有着很高的尺寸精度与表面光洁度,所以可减少机械加工工作,只就是在零件上要求较高的部位留少许加工余量即可,甚至某些铸件只留打磨、抛光余量,不必机械加工即可使用。
由此可见,采用熔模铸造方法可大量节省机床设备与加工工时,大幅度节约金属原材料。
熔模铸造方法的另一优点就是,它可以铸造各种合金的复杂的铸件,特别可以铸造高温合金铸件。
如喷气式发动机的叶片,其流线型外廓与冷却用内腔,用机械加工工艺几乎无法形成。
用熔模铸造工艺生产不仅可以做到批量生产,保证了铸件的一致性,而且避免了机械加工后残留刀纹的应力集中。
熔模铸造的缺点就是工序繁杂,生产周期长,原辅材料费用比砂型铸造高,生产成本较高,铸件不宜太大、太长,一般限于25kg以下。
而且铸造出来的零件强度不高,所以该方法不适合制造汽车轮毂。
4、低压铸造低压铸造就是用干燥、洁净的压缩空气将保温炉中的铝液自下而上通过升液管与浇注系统平稳地向上压到铸造机模具型腔中,保持一定压力,一般为20~60kPa直到铸件凝固后释放压力。
因在压力下充型与凝固,所以充填性好、铸件缩松少、致密性高。
该法中,坩埚表面的氧化膜不会被破坏,与其它铸造方法比较,气孔与夹渣缺陷少,产品内部质量好。
由于低压铸造利用压力充型与补充,大大简化了浇冒系统的结构,使金属液收得率大大提高,一般可达90%,而金属型重力铸造仅40%~60%。
目前低压铸造已成为铝轮毂生产的首选工艺、日本的丰田汽车公司、东京轻合金制作所、美国福特汽车公司等均采用此工艺生产铝轮毂,国内的铝合金轮毂制造企业多数也采用此工艺生产,现有数十家企业用低压铸造工艺生产铝合金汽车及摩托车轮毂。
低压铸造法的缺点就是铸造时间较长、加铝料、换模具费时间、设备投资大、低压铸造机使用的升液管成本较高且易损坏。
5、离心铸造离心铸造就是将液体金属注入高速旋转的铸型内,使金属液在离心力的作用下充满铸型与形成铸件的技术与方法。
离心力使液体金属在径向能很好地充满铸型并形成铸件的自由表面;不用型芯能获得圆柱形的内孔;有助于液体金属中气体与夹杂物的排除;影响金属的结晶过程,从而改善铸件的机械性能与物理性能。
优点就是几乎不存在浇注系统与冒口系统的金属消耗,提高工艺出品率;生产中空铸件时可不用型芯,故在生产长管形铸件时可大幅度地改善金属充型能力,降低铸件壁厚对长度或直径的比值,简化套筒与管类铸件的生产过程;铸件致密度高,气孔、夹渣等缺陷少,力学性能高;便于制造筒、套类复合金属铸件,如钢背铜套、双金属轧辊等;成形铸件时,可借离心力提高金属的充型能力,故可生产薄壁铸件。
缺点就是用于生产异形铸件时有一定的局限性。
铸件内孔直径不准确,内孔表面比较粗糙,质量较差,加工余量大;铸件易产生比重偏析,因此不适合于合金易产生比重偏析的铸件(如铅青铜),尤其不适合于铸造杂质比重大于金属液的合金。
所以不适合汽车轮毂的制造。
四、工艺方案1、零件图:2.浇注位置:为了保证铸件质量,必须把最重要的加工面在浇注时向下或直立状态。
由于零件内部安装轴承,尺寸精度比较高,因此,应将两圆柱面呈直立状态,同时从顺序凝固的原则出发,将厚大部位放在上面,以便于安放冒口,得到顺序凝固。
所以本件的浇注位置如图所示。
冷却位置与浇注位置一致。
3.分型面:如图所示铸件大部分在同一铸型内,能够保证其尺寸精度,下芯也便于检查,同时满足合箱,浇注,冷却位置一致,采用侧浇,切向引入改善了浇注时的充型不平稳,减少了冲击,防止了冲砂缺陷的产生,上、下箱相差不大,造型简单。
缺点就是有一个砂芯复杂,要求高,模样加工困难。
4.砂芯:根据铸件结构与已选定的分型面,必用两个5、主要工艺参数的确定:根据实际生产情况,确定该件的收缩率为2%。
由于铸件的精度要求较高,确定该件的精度为Ⅰ级,尺寸偏差为±2、5mm,重量偏差8%。
按一级精度铸件并考虑实际情况,确定加工余量,具体数值见铸件工艺图。
按零件图尺寸采用增厚法,确定拔模斜度为1º30'-2º。
6、浇注系统:浇注系统由浇口杯、直浇道、横浇道与内浇道组成。
浇注系统截面积大小对铸件质量影响很大,截面积太小,浇注时间长,可能产生浇不足、冷隔、砂眼等缺陷;截面积过大,浇注速度快,又可能收起冲砂,带入熔潭与气体,使铸件产生渣孔、气孔等缺陷。
为了使金属液以适宜的速度充填铸型,就必须合理确定浇注系统的面积。
7、冒口:铸件法兰与轮毂体交接处形成热节,容易产生分散性的缩松,严重降低铸件的机械强度。