金属切削基本理论的应用
金属切削原理的应用意义

金属切削原理的应用意义概述金属切削是制造过程中常用的一种加工方法。
其基本原理是利用刀具与工件相对做旋转和直进运动,通过切除金属材料来得到所需形状和尺寸的工件。
金属切削原理是机械制造的重要基础,广泛应用于各个行业中的零部件加工和产品制造中。
本文将探讨金属切削原理的应用意义。
提高生产效率金属切削作为一种高效的加工方法,可以大大提高生产效率。
切削加工可以通过选择适当的切削参数来实现高速切削,从而缩短加工周期。
此外,金属切削还可以同时进行多个刀具的加工,实现多工序的联合加工,减少工序数,提高生产效率。
获得高精度的工件金属切削可以获得高精度的工件,满足各行业对于工件精度的要求。
切削加工通过控制刀具的切削轨迹和切削参数,可以实现对工件形状和尺寸的精确控制。
同时,金属切削还可以获得平整的表面质量,提高工件的外观和使用性能。
实现多样化的加工需求金属切削可以实现多样化的加工需求,适应不同行业的生产需求。
金属切削加工可以通过改变刀具的类型、切削速度和切削深度等参数来实现对不同材料的加工。
它可以加工钢材、铜材、铝材等多种金属材料,也可以加工复杂结构的工件,满足不同行业的加工要求。
创新产品设计和开发金属切削的应用意义不仅体现在加工过程中,还可以促进产品设计和开发的创新。
通过金属切削可以制造出更加复杂、精密的工件,为产品的设计和开发提供了更多的可能性。
金属切削的应用可以帮助设计师实现更加创新的产品设计,提高产品的质量和竞争力。
节约资源和保护环境金属切削作为一种高效的加工方法,可以节约资源和保护环境。
相比其他加工方法,金属切削消耗更少的能源和材料。
由于金属切削是直接切除金属材料,相对于其他加工方法,金属切削产生的废料和污染更少。
因此,金属切削不仅可以减少对资源的浪费,还可以减少对环境的污染。
提高工人劳动条件金属切削的应用意义还在于提高工人的劳动条件。
金属切削可以实现自动化和智能化的生产,减少了工人的劳动强度和劳动风险。
通过机械和自动化设备的应用,可以减少工人的体力劳动,提高工作效率和工作安全性。
金属切削原理与刀具的应用

金属切削原理与刀具的应用1. 金属切削原理金属切削是通过机床上的刀具对金属工件进行切削、铣削、车削、钻孔等加工过程。
在金属切削过程中,刀具与工件之间的相对运动产生切削力,使刀具将工件上的金属材料去除,从而实现对工件的加工。
以下是金属切削的基本原理:1.切削速度:切削速度是指刀具切削工件的速度。
切削速度的选择应根据工件材料、刀具材质和切削类型等因素来确定。
高速切削可以提高生产效率,但也会对刀具和工件产生一定的热影响。
2.进给量:进给量是指刀具在单位时间内前进的距离。
进给量的选择取决于工件表面的粗糙度要求、切削力和刀具的耐久度等因素。
3.切削深度:切削深度是指刀具切削时的最大切削量。
切削深度的选择应根据工件材料的硬度、刀具的尺寸和工艺要求来确定。
4.切削力:切削力是指刀具对工件施加的力。
切削力的大小受到切削参数、刀具材质和刀具几何形状的影响。
2. 刀具的应用刀具是金属切削过程中起到切削作用的工具。
不同的工件和切削任务需要选择合适的刀具来进行加工。
以下是常见的刀具及其应用:1.钻头:钻头用于钻孔加工,适用于加工圆孔和柱形孔。
常见的钻头有直柄钻头和 Morse 锥柄钻头两种。
2.车刀:车刀用于车削加工,常用于加工圆柱形工件的外轮廓。
车刀有内刀和外刀之分,可以用于精细车削和粗车削等不同工艺要求。
3.铣刀:铣刀用于铣削加工,可以用于多种铣削操作,如平面铣削、立体铣削、开槽铣削等。
铣刀可分为立铣刀、面铣刀和球形铣刀等。
4.刨刀:刨刀用于刨削加工,可以进行铺刨、面刨和纵切削等操作。
刨刀可根据切削刃的数量和类型来分类,如单刃刨刀、多刃刨刀和筷子刨刀等。
5.刀片:刀片用于各种切削加工,如割断、倒角、切割等。
刀片的种类繁多,根据刀片的应用需求和加工材料的类型来选择合适的刀片。
3. 刀具材料选择刀具材料选择是决定刀具性能的关键,不同的刀具材料有着不同的加工性能和适用范围。
以下是常见的刀具材料及其特点:1.高速钢(HSS):高速钢具有良好的耐磨性和耐热性,适用于中等切削速度和较硬的工件材料。
金属切削原理的应用

金属切削原理的应用1. 引言金属切削是一种常见的加工方法,广泛应用于制造业中。
本文将介绍金属切削的基本原理及其在工程领域中的应用。
2. 金属切削的基本原理金属切削是通过切削工具与工件之间的相对运动,在切削力作用下,将工件上的金属材料剥离、断裂,从而进行加工的一种方法。
其基本原理包括以下几个关键要素:2.1. 切削工具切削工具通常由硬质合金等耐磨材料制成,具有尖锐的切削边缘。
常见的切削工具有刀具、钻头、铣刀等。
2.2. 切削速度切削速度是指切削工具与工件接触面上的相对运动速度。
切削速度的选择需要考虑材料的硬度、切削工具的材料等因素。
2.3. 切削力切削力是指切削过程中作用在切削工具上的力,通常由切向力和径向力组成。
切削力的大小会影响切削过程中的工件变形和切削工具的磨损情况。
2.4. 切削液切削液是常用的辅助材料,用于冷却和润滑切削区域,减少切削工具和工件的摩擦,提高切削效率。
3. 金属切削的应用金属切削广泛应用于制造业中的各个领域,下面将分别介绍金属切削在机械加工、航空航天以及汽车制造等领域的具体应用。
3.1. 机械加工在机械加工领域中,金属切削常用于制造零件的精密加工。
通过金属切削可以实现零件的形状加工、孔加工、螺纹加工等。
3.2. 航空航天航空航天是对材料、工艺等要求非常高的领域,而金属切削正是满足这些高要求的一种可行方式。
在航空航天领域,金属切削应用于制造飞机零部件、火箭发动机等。
3.3. 汽车制造汽车制造过程中需要大量的零部件加工,金属切削可以满足对零部件精度、质量的要求。
金属切削在汽车制造中应用广泛,包括发动机零部件、车身零部件等。
4. 金属切削的优势和挑战金属切削作为一种常用的加工方法,具有以下优势:•可以实现高精度加工,满足不同领域对零部件精度的要求;•可以加工各种金属材料,具有较广的适用性;•可以进行批量生产,提高生产效率。
然而,金属切削也面临一些挑战:•切削工具的磨损和损伤会影响加工精度和质量;•切削过程中产生的高温和切屑可能对工件造成损害。
金属切削原理及其应用领域解析

金属切削原理及其应用领域解析金属切削是一项广泛应用于工业制造领域的加工方法,包括机械加工、制造工程等领域。
本文将探讨金属切削的原理及其在不同应用领域的应用。
金属切削原理:金属切削是通过运用切削工具对金属材料进行切削、磨削或抛光的一种加工处理技术。
切削工具通常采用硬质材料制成,比如钢、硬质合金等。
金属切削主要通过应用切削工具对金属工件进行剪切、切割、连续切削以及排屑等操作,切削工具在金属工件上施加力量形成切削力,将工件上的金属层切下来或切割成所需的形状。
金属切削可以分为两个主要的原理:单一切削原理和多点切削原理。
1. 单一切削原理:单一切削原理是在切削过程中,只有一个切削齿刃与工件接触并切削,通过旋转切削工具,将工件上的金属物质切削掉。
单一切削原理的常见切削工具有铣刀、车刀、刨刀等。
这种切削原理常用于对平面、曲线、斜面以及不同形状的表面进行切削加工。
2. 多点切削原理:多点切削原理是在切削过程中,多个切削齿刃同时与工件接触并切削,提高了切削效率和加工精度。
常见的多点切削工具有铣刀、钻头、切削刃等。
这种切削原理可用于进行孔加工、螺纹加工、齿轮加工等。
金属切削应用领域:金属切削技术在工业制造领域具有广泛的应用。
下面将介绍几个主要的应用领域:1. 汽车制造:金属切削技术在汽车制造中起着至关重要的作用。
通过金属切削技术,可以对汽车零部件进行精确加工,包括发动机零部件、车体零部件、变速器零部件等。
金属切削技术可以提高零部件的质量和精度,确保汽车的性能和安全。
2. 航空航天:航空航天领域对金属切削技术的需求非常高。
金属切削被广泛应用于制造飞机引擎零部件、飞行控制系统、主轴承等关键部件。
金属切削技术在航空航天领域的应用也要求具有高精度和高性能。
3. 电子设备制造:金属切削技术在电子设备制造中扮演着重要的角色。
通过金属切削技术,可以对电子设备的外壳、散热器、连接器等进行加工。
金属切削能够满足电子设备对精度和尺寸要求,确保电子设备的可靠性和性能。
金属切削原理的基本原理与应用探析

金属切削原理的基本原理与应用探析金属切削是指在机械加工过程中,通过刀具对金属材料进行切削加工的一种方法。
切削加工是现代工业生产中非常重要的一环,广泛应用于制造业的各个领域,如汽车制造、航空航天、机械制造等。
本文将探析金属切削原理的基本原理和应用。
一、金属切削原理的基本原理1. 切削力与材料性质的关系切削力是刀具和工件之间产生的力,它直接影响到切削加工的效率和质量。
切削力与金属材料的性质有密切关系,例如硬度、韧性和塑性等特性。
一般来说,材料硬度越高,切削力越大。
2. 切削热的生成与影响在切削过程中,由于刃口与工件接触产生摩擦,会产生大量的切削热。
切削热的大小和分布对切削加工有着重要影响。
过高的切削热可能导致刀具磨损加剧、工件变形,甚至热裂纹的产生。
因此,有效控制切削热对于提高切削加工质量至关重要。
3. 切削液的作用切削液在切削过程中起到冷却、润滑和防腐的作用。
通过降低切削热,它可以有效地控制切削加工过程中的温度,减少工件表面的热变形,提高切削加工质量和效率。
4. 切削刃部分的结构与刀具磨损切削刃是切削工具的重要部分,其结构设计直接影响到切削加工的效果。
一般来说,切削刃的设计要使切削力分布均匀,降低切削热和切削力,延长切削工具的寿命。
此外,选择合适的材料和硬度对切削刃的寿命也有很大影响。
二、金属切削的应用探析1. 汽车制造汽车制造是金属切削应用的重要领域之一。
在汽车制造中,金属切削广泛应用于发动机、底盘、车身等零部件的加工。
通过金属切削,可以精确加工出复杂形状的零部件,提高汽车的质量和性能。
2. 航空航天工业航空航天工业对金属切削的要求更为严格。
在航空航天工业中,金属切削应用于航空发动机、机翼、航天器等部件的加工。
金属切削技术的发展和应用,推动了航空航天工业的进步和发展。
3. 机械制造金属切削在机械制造领域中扮演着重要角色。
在机械制造中,金属切削应用于制造各种机床、工具以及零部件等。
通过金属切削技术,可以提高机械制造的精度和效率,满足不同行业和领域的生产需求。
金属切削原理及其在现代加工中的应用

金属切削原理及其在现代加工中的应用金属切削是工业生产中常见的一种加工方法,广泛应用于制造业的各个领域。
金属切削原理主要涉及切削力、金属材料的塑性变形和剪切变形等方面,充分理解切削原理对于合理选择工具、刀具、切削参数以及提高切削加工质量和效率具有重要意义。
金属切削原理的基本概念是在切削加工过程中,利用刀具切割工件,将金属材料从工件上去除,形成所需要的形状和尺寸。
在切削过程中,刀具对金属材料施加力,导致金属材料的塑性变形和剪切变形,最终实现金属材料的去除。
在金属切削过程中,切削力是一个重要的参数,它直接影响切削加工的稳定性、工具寿命和加工质量。
切削力的大小与切削材料的物理性质、工具几何因素、切削参数等因素有关。
通过合理选择刀具材料、切削液以及控制切削参数,可以降低切削力的大小,提高切削加工的效率和质量。
金属材料的塑性变形和剪切变形是切削原理的重要内容。
在金属切削过程中,刃口与工件接触,通过刀具的旋转和移动,刀具对工件产生强大的剪切力,导致金属材料的剪切变形。
同时,金属材料还会经历塑性变形,即在切削过程中,金属材料发生的弯曲和伸长现象。
这些塑性变形和剪切变形共同作用,实现了金属材料的切削。
金属切削原理在现代加工中得到了广泛的应用。
首先,金属切削加工可以实现复杂形状和高精度的加工需求。
通过选择合适的刀具和切削参数,可以在金属材料上精确地切割出所需要的形状和尺寸,满足现代制造领域对产品高精度的要求。
其次,金属切削可以用于加工各种金属材料,包括常见的钢铁、铜、铝等金属材料,同时也包括一些高强度、高温合金等特殊材料。
采用不同的刀具和切削参数,可以适应不同金属材料的切削需求,并实现高效率的加工。
另外,金属切削在现代制造中有着广泛的应用领域,如汽车制造、航空航天、电子设备等。
在汽车制造中,金属切削被广泛应用于发动机、底盘、车身等零部件的加工过程。
在航空航天领域,金属切削则常用于航空发动机、飞机构件等的加工中。
在电子设备制造中,金属切削则被应用于手机、电脑等设备的加工。
第5章金属切削基本理论的应用

一、切削用量的选择原则
通常根据工件材料、刀具材料、技
术要求、工艺过程、工艺系统状态 等,通过查工艺手册,或根据实际 情况和实践经验予以确定
选择切削用量必须遵循以下原则
合理选择前角的原则
工件材料:加工塑性材料前角宜大,加 工脆性材料前角宜小;材料强度和硬度 越高,前角越小,甚至取负值。 刀具材料:高速钢可选较大的前角;硬 质合金应选用较小的前角;陶瓷刀具前 角更小。 加工要求:粗加工和断续切削应选用较 小的前角;精加工选较大的前角。
特定要求选择前角:
三、主偏角及副偏角的选择
主偏角及副偏角的功用
影响表面粗糙度
已加工表面的残留面积高度
Rmax
f Ctgkr Ctgkr
'
影响刀尖强度和刀具耐用度:kr、kr’小, 则切削刃增长,散热好,T↗ 影响切削分力比例:kr↘ Ff↘,Fp↗
影响切削层尺寸以及排屑、断屑效果
合理和工件已加工表面质量下降。过大
或过小,均使其切削加工性变差 导热性好,切削加工性好,但加工尺 寸精度会发生变化 导热性差,加工性差。
材料的化学成分
Cr、Ni、V、Mo、W、Mn等提高钢 的强度和硬度,使其切削加工性差 Si、Al与氧化合后使刀具磨损加快 合金元素(如镍Ni)降低导热系数 Pb[铅]、P[磷] 、S[硫]等降低塑性(发 生热脆、冷脆现象),改善切削性 碳的石墨化使切削加工性变好(硬度 下降、润滑性变好) Fe4C3使硬度增加,磨损加快
水溶液
水溶液是以水为主要成分的切削 液。在水中加入一定含量的油性、防锈等添 加剂制成水溶液,改善水的润滑、防锈性能。 水溶液是一种透明液体。 乳化剂 是将乳化油用水稀释而成 。 切削油 切削油的主要成分是矿物油,少 数采用矿物油和动、植物油的复合油。适用 于精加工和加工复杂形状工件(如成形面、 齿轮、螺纹等)时,润滑和防锈效果较好。
金属切削的原理和应用

金属切削的原理和应用1. 前言金属切削是一种常见的金属加工方式,广泛应用于制造业领域。
本文将从金属切削的原理和应用两个方面进行介绍。
2. 原理金属切削的原理是通过将刀具与工件之间相对运动,在工件表面切削出所需形状。
金属切削过程中主要包括以下几个要素:•刀具:刀具是进行金属切削的关键工具,可以根据切削材料的不同选择不同种类的刀具。
常见的刀具有平头刀、圆头刀、金属锯等。
•工件:工件是需要进行切削加工的金属材料,可以是铁、铜、铝等金属。
•切削速度:切削速度是指单位时间内切削刃通过工件表面的长度。
切削速度的选择需要考虑切削材料的硬度、刀具的耐磨性等因素。
•进给量:进给量是指切削刃在切削过程中每次进给到工件表面的量。
进给量的选择需要考虑切削材料的硬度、刀具的耐磨性等因素。
•切削力:切削力是切削过程中作用在刀具上的力,由切削材料的硬度、切削速度、刀具的材质等因素影响。
3. 应用金属切削广泛应用于制造业领域,以下是几个常见的应用场景:3.1 汽车制造金属切削在汽车制造中起着重要的作用。
汽车零部件的加工过程中,金属切削是一个关键部分,例如轮毂、车架等核心零部件的加工都需要通过金属切削来完成。
3.2 机械制造机械制造是金属切削的另一个重要领域。
在机械制造过程中,金属切削常用来加工各种类型的零部件,如轴、套、齿轮等。
金属切削可以实现精确的加工要求,能够提高机械制造产品的质量。
3.3 航空航天航空航天领域也广泛应用金属切削技术。
航空航天产品对材料要求较高,需要采用高精度的金属切削技术来加工各种复杂形状的零部件,如飞机轴承、发动机零件等。
3.4 制造设备金属切削还广泛应用于制造设备的生产中。
制造设备的加工过程中,金属切削技术可以实现对各种材料的精确加工,如钣金加工、零件加工等。
4. 总结金属切削是一种常见的金属加工方式,通过刀具与工件之间的相对运动,切削出所需形状。
金属切削在汽车制造、机械制造、航空航天和制造设备等领域都有广泛的应用。
第三讲第一章金属切削加工基本知识金属切削基本知识的应用
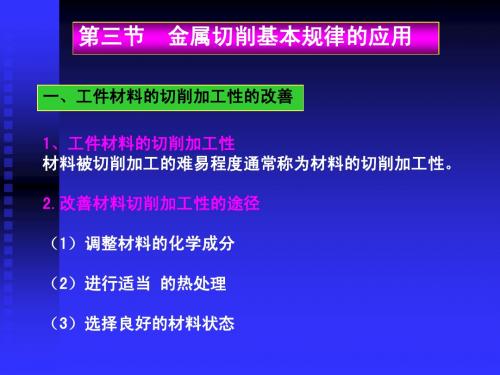
刀具材料在切削时要承受高温、高压、摩擦、冲击、 振动,金属切削过程中的加工质量、加工效率、 加工成本,在很大程度上取决于刀具材料的合理选择。
二、刀具材料的合理选择
1. 刀具材料应具备的性能
(1)高的硬度和耐磨性
刀具材料抵抗摩擦和磨损的能力,必须 高于工件硬度。常温硬度60HRC以上。
(2)足够的强度和韧性
3.硬质合金
硬质合金(carbides)是由高硬度和高熔点的金属碳 • 化物(碳化钨WC、碳化钛TiC、碳化钽TaC、碳化铌NbC 等)和金属粘结剂(Co、Mo、Ni等)用粉末冶金工艺制成。 •硬质合金刀具常温硬度为89~93HRA,化学稳定性好, 热稳定性好,耐磨性好,耐热性达800~1000°C。硬 质合金刀具允许的切削速度比高速钢刀具高5~10倍 。 •但强度、韧度均较高速钢低,工艺性也不如高速钢。 •常制成各种型式的刀片,焊接或机械夹固在车刀、 刨刀、端铣刀等的刀柄(刀体)上使用。
2).高速钢
•高速钢是一种加入较多钨、钼、铬、钒等合金元素
的高合金钢。 •热处理后硬度可达62~66HRC, 抗弯强度约3.3GPa, 有较高的热稳定性 、耐磨性 、耐热性。切削温度 在500~650°C时仍能进行切削。 •适合于制造结构和刃型复杂的刀具,如成形车刀、 铣刀、钻头、插齿刀、剃齿刀、螺纹刀具和拉刀等。
4.先进刀具材料
(1)陶瓷刀具材料 (2)金刚石刀具材料
以氧化铝或以氮
化硅为基体再添加 少量金属,在高温 下烧结而成的一种 刀具材料。
碳的同素异形体,在高温、
高压下由石墨转化而成,是目 前人工制造出的最坚硬物质。
(3)立方氮化硼
立方氮化硼(CBN)是一种人工合成
的新型刀具材料,它由六方氮化硼在 高温、高压下加入催化剂转化而成。
金属切削原理及其应用领域深度剖析

金属切削原理及其应用领域深度剖析金属切削是指通过切削工具对金属材料进行加工和切割的一种制造工艺。
这种切削工艺广泛应用于诸如机械制造、金属加工、航空航天、汽车制造等多个领域。
本文将深入探讨金属切削的原理和其在各个应用领域的具体应用。
金属切削的原理主要基于材料塑性变形与材料去除两个基本过程。
当刀具施加在金属工件上时,会使其产生塑性变形。
随着刀具的移动,金属工件的组织结构被剪切、拉伸和压缩,从而使材料被去除,完成切削加工。
在这个过程中,刀具和工件之间的相互作用是至关重要的。
因此,刀具的选择、切削速度、进给速度和切削液等参数都对金属切削过程的效果有影响。
金属切削可以应用于各种材料的加工,包括普通碳钢、合金钢、不锈钢、铜、铝和钛合金等。
不同材料的硬度和强度会对切削过程产生不同的影响。
为了达到理想的切削效果,需要根据具体材料的特性选择合适的切削工具和参数。
例如,对于硬度较高的材料,可以选择刀具材料更坚硬的硬质合金刀具进行切削。
此外,切削液的使用也是金属切削过程中重要的因素之一,它可以冷却工件和刀具、润滑切削面,并防止切削过程中产生的金属屑积聚在切削区域。
金属切削技术广泛应用于机械制造领域。
在机械零部件的制造过程中,往往需要对金属材料进行切割、车削、铣削、钻孔等工艺。
通过金属切削技术,可以实现加工精度更高、表面质量更好的产品。
在汽车制造领域,金属切削工艺用于加工发动机零部件、底盘组件等。
航空航天领域对于金属材料的切削加工要求更高,因为航空航天行业需要使用轻质高强度的金属材料制造飞机和发动机等关键部件。
随着科技的发展,金属切削技术不断创新和改进,涌现出许多新的应用。
例如,微切削技术是利用先进的加工设备和工艺对微尺度金属零件进行加工的一种技术。
微切削技术的应用领域广泛,包括微机械、微电子、生物医药等。
另外,快速切削技术是一种高效快速的切削加工技术,可以大幅提高生产效率。
这种技术主要应用于批量加工,如汽车制造、机械制造等领域。
金属切削基本理抢的应用
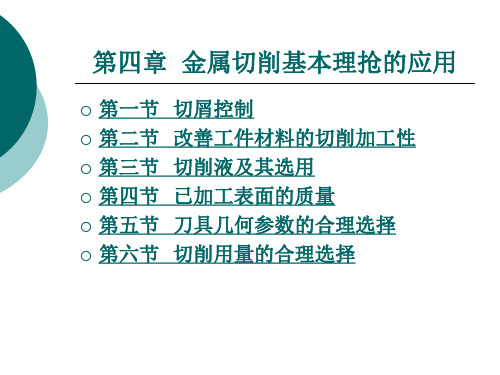
第五节 刀具几何参数的合理选择
(4)负前角单面型和负前角双面型如图4-19(d),(e)所示, 切削高强度、高硬度材料时,为使脆性较大的硬质合金刀片 承受压应力,而采用负前角。
3.卷屑槽与切屑控制 前刀面磨出卷屑槽可以使切屑卷曲,这是生产中经常采用的
方法。经卷曲的切屑就不易缠绕在工件和刀具上。 (1)切屑的卷曲为使切屑卷曲,需在前刀面磨出卷屑槽,其
上-页 下-页 返回
第一节 切屑控制
吃刀量,最小为切削速度进给量增大,使切屑厚度气h增大, 当受到碰撞后切屑容易折断。 3.改变刀具角度 主偏角是影响断屑的主要因素。主偏角增大,切屑厚度气h 增大,容易断屑。 刃倾角使切屑流向改变后,使切屑碰到加工表面上或刀具后 面上造成断屑
上-页 返回
第二节 改善工件材料的切削加工 性
第四章 金属切削基本理抢的应用
第一节 切屑控制 第二节 改善工件材料的切削加工性 第三节 切削液及其选用 第四节 已加工表面的质量 第五节 刀具几何参数的合理选择 第六节 切削用量的合理选择
第一节 切屑控制
一、切屑形状的分类 生产中由于加工条件不同,形成的切屑形状多种多样。根据
ISO规定、并由我国生产工程学会切削专业委员会推荐的国 标GB/T16461-19%的规定,切屑的形状与名称分为八 类,如表4-1所列。 二、切屑的流向、卷曲和折断 1.切屑的流向 为了不损伤已加工表面和方便处理切屑,必须有效地控制切 屑的流向。如图4-1所示,车刀除主切削刃起主要切削作用 外,倒角刀尖和副切削刃处也有非常少的部分参加切削,由 于切屑流向是垂直于各切削刃的方向,因此最终切屑的流向 是垂直于主副切削刃的终点连线方向,通常该流出方向与正 交平面夹角为称为流屑角。
切削基本理论的应用PPT课件

切塑性材料:
↓γ0 ↓v ↑ac
带状切屑
↑γ0↑v↓ac
切削平稳,力波动小
加工面光洁,断屑难
↓γ0 ↓v ↑ac
节状切屑
↑γ0↑v↓ac
粒状切屑
滑移量较大,局部 切削不平稳,力波动大
剪应力达断裂强度
加工表面粗糙 少见
5
切脆性材料:崩碎切屑
13.11.2020
影响断屑的主要参数:槽宽Lbn,槽深hBn。槽宽Lbn应保证
切屑在流出槽时碰到断屑台,以使切屑卷曲折断。进给量
大,切削厚时,可以适当增加槽宽LBn。
11
13.11.2020
断屑槽在前刀面的位置有三种型式:
(a)外斜式;(b)平行式;(c)内斜式。 其中外斜式最常用,平行式次之。内斜式主要用
于背吃刀量ap较小的半精加工和精加工。
12
● 选择合适切削用量
13.11.2020
切削用量的变化
对断屑产生影响,选
择合适的切削用量,
能增强断屑效果。
在切削用量参数中,进给量f对断屑影响 最大。进给量f增大,切削厚度也增大,碰撞 时容易折断。
切削速度υc和背吃刀量ap对断屑影响较小, 不过,背吃刀量ap增加,切削层宽度增加, 断屑困难增大;切削速度提高,断屑效果下
大时将产生什么切屑?
4、如前角进一步减小,再降低切削速度, 或加大切削厚度,则得到什么切屑?
7
二、切屑流向和折断
1、切屑流向
A点:主刃参与切削终了点 B点:副刃终了点 Vch⊥AB
流屑角ηc=Vch VS P0 影响Vch 方向参数: λs κr γ0
13.11.2020 8
金属切削原理及其在工业生产中的应用

金属切削原理及其在工业生产中的应用摘要:金属切削是一种常见的金属加工方式,利用刀具对金属材料进行切削来加工成所需形状和尺寸。
本文将介绍金属切削的原理及其在工业生产中的应用。
一、引言金属切削是制造业中常见的加工方式之一,广泛应用于机械制造、航空航天、汽车制造等领域。
通过切削加工,可以将原始金属材料加工成精确的形状和尺寸,满足各种工业产品的需求。
二、金属切削原理金属切削的原理基于机械切削,利用锋利的刀具对金属进行切削,从而使其形成所需的形状和尺寸。
1. 切削力的产生金属切削时,刀具施加在工件上产生力,刀具的刃口与工件接触产生摩擦力和切削力。
摩擦力使刀具表面磨损,切削力则将刀具切入金属材料。
2. 切削区域的变形切削过程中,工件与刀具接触的区域发生塑性变形,金属材料被切削掉,形成切屑。
3. 切屑的形成切屑是金属切削过程中形成的金属碎屑,其形状与切削方式和金属材料有关。
常见的切屑形态有连续螺旋切屑、断续螺旋切屑、剪切切屑等。
三、金属切削工艺金属切削工艺包括切削速度、进给量、切削深度等参数的选择。
不同材料、不同形状的工件都需要根据具体情况调整切削工艺参数。
1. 切削速度切削速度是刀具切削过程中,刀具刃口与工件接触点的移动速度。
切削速度的选择要考虑刀具材料、刀具的耐磨能力以及金属材料的硬度等因素。
2. 进给量进给量是工件相对于刀具刃口的移动距离,进给量的选择要根据切削速度和切削深度等参数合理确定,以保证切削过程的稳定性和加工效率。
3. 切削深度切削深度是切削过程中,刀具刃口进入工件的深度。
切削深度的选择要根据工件的要求和刀具的性能来确定,太浅的切削深度可能导致刀具磨损不均匀,太深的切削深度可能导致切削过程不稳定。
四、金属切削的应用1. 机械制造机械制造领域是金属切削应用最广泛的领域之一。
通过金属切削可以生产出各种机床、汽车零部件、机械配件等产品。
2. 航空航天航空航天领域对金属切削要求较高,需要加工出精确的形状和尺寸。
金属切削原理与其在刀具设计中的应用
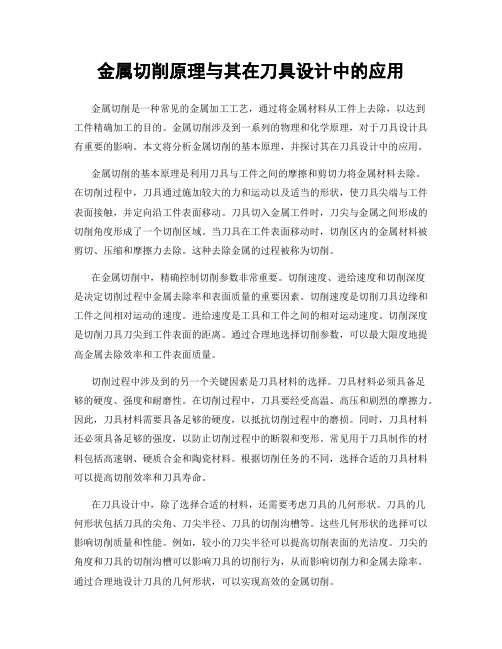
金属切削原理与其在刀具设计中的应用金属切削是一种常见的金属加工工艺,通过将金属材料从工件上去除,以达到工件精确加工的目的。
金属切削涉及到一系列的物理和化学原理,对于刀具设计具有重要的影响。
本文将分析金属切削的基本原理,并探讨其在刀具设计中的应用。
金属切削的基本原理是利用刀具与工件之间的摩擦和剪切力将金属材料去除。
在切削过程中,刀具通过施加较大的力和运动以及适当的形状,使刀具尖端与工件表面接触,并定向沿工件表面移动。
刀具切入金属工件时,刀尖与金属之间形成的切削角度形成了一个切削区域。
当刀具在工件表面移动时,切削区内的金属材料被剪切、压缩和摩擦力去除。
这种去除金属的过程被称为切削。
在金属切削中,精确控制切削参数非常重要。
切削速度、进给速度和切削深度是决定切削过程中金属去除率和表面质量的重要因素。
切削速度是切削刀具边缘和工件之间相对运动的速度。
进给速度是工具和工件之间的相对运动速度。
切削深度是切削刀具刀尖到工件表面的距离。
通过合理地选择切削参数,可以最大限度地提高金属去除效率和工件表面质量。
切削过程中涉及到的另一个关键因素是刀具材料的选择。
刀具材料必须具备足够的硬度、强度和耐磨性。
在切削过程中,刀具要经受高温、高压和剧烈的摩擦力。
因此,刀具材料需要具备足够的硬度,以抵抗切削过程中的磨损。
同时,刀具材料还必须具备足够的强度,以防止切削过程中的断裂和变形。
常见用于刀具制作的材料包括高速钢、硬质合金和陶瓷材料。
根据切削任务的不同,选择合适的刀具材料可以提高切削效率和刀具寿命。
在刀具设计中,除了选择合适的材料,还需要考虑刀具的几何形状。
刀具的几何形状包括刀具的尖角、刀尖半径、刀具的切削沟槽等。
这些几何形状的选择可以影响切削质量和性能。
例如,较小的刀尖半径可以提高切削表面的光洁度。
刀尖的角度和刀具的切削沟槽可以影响刀具的切削行为,从而影响切削力和金属去除率。
通过合理地设计刀具的几何形状,可以实现高效的金属切削。
金属切削原理及其应用领域分析
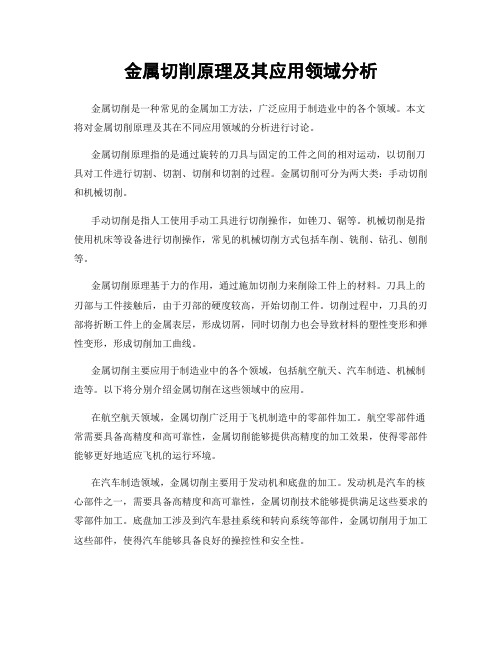
金属切削原理及其应用领域分析金属切削是一种常见的金属加工方法,广泛应用于制造业中的各个领域。
本文将对金属切削原理及其在不同应用领域的分析进行讨论。
金属切削原理指的是通过旋转的刀具与固定的工件之间的相对运动,以切削刀具对工件进行切割、切割、切削和切割的过程。
金属切削可分为两大类:手动切削和机械切削。
手动切削是指人工使用手动工具进行切削操作,如锉刀、锯等。
机械切削是指使用机床等设备进行切削操作,常见的机械切削方式包括车削、铣削、钻孔、刨削等。
金属切削原理基于力的作用,通过施加切削力来削除工件上的材料。
刀具上的刃部与工件接触后,由于刃部的硬度较高,开始切削工件。
切削过程中,刀具的刃部将折断工件上的金属表层,形成切屑,同时切削力也会导致材料的塑性变形和弹性变形,形成切削加工曲线。
金属切削主要应用于制造业中的各个领域,包括航空航天、汽车制造、机械制造等。
以下将分别介绍金属切削在这些领域中的应用。
在航空航天领域,金属切削广泛用于飞机制造中的零部件加工。
航空零部件通常需要具备高精度和高可靠性,金属切削能够提供高精度的加工效果,使得零部件能够更好地适应飞机的运行环境。
在汽车制造领域,金属切削主要用于发动机和底盘的加工。
发动机是汽车的核心部件之一,需要具备高精度和高可靠性,金属切削技术能够提供满足这些要求的零部件加工。
底盘加工涉及到汽车悬挂系统和转向系统等部件,金属切削用于加工这些部件,使得汽车能够具备良好的操控性和安全性。
在机械制造领域,金属切削被广泛应用于各种机械设备的制造和加工。
例如,传统的机床制造需要使用金属切削来进行加工,从而提供精确的零部件来组装机床。
此外,金属切削还应用于模具制造、压力容器加工等领域,为各行各业提供所需的零部件和设备。
金属切削的应用领域还包括船舶制造、电子设备制造等。
船舶制造中,金属切削技术用于加工船体结构和推进系统等部件。
电子设备制造中,金属切削用于加工电子设备外壳和连接器等零部件。
模块五:金属切削的基本理论与应用
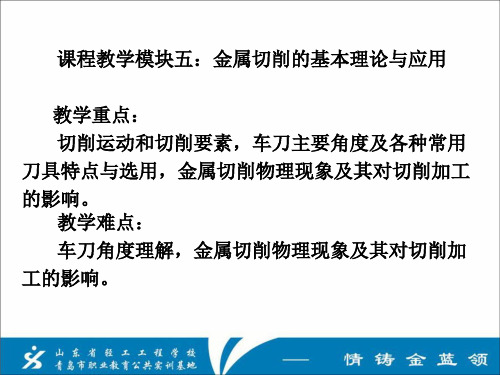
(1)高速钢 高速钢是含有较多W、Mo、Cr、V等合金元素的高合金 工具钢。其抗弯强度较高,韧性较好,常温硬度在 62~66HRC,其耐热性约为600~660℃。刃磨时切削刃易锋 利,故在生产中常称为“锋钢”,磨光的高速钢亦称白钢。 高速钢综合性能较好,故广泛用于制作刀具。其具有高的 强度(抗弯强度为3~3.4GPa)和高的韧性(180~320kJ/ ㎡),具有一定的硬度、良好的耐磨性和热处理变形小的特 点,适用于制造各种结构复杂的成形刀具、孔加工刀具等。 高速钢按化学成分可分为钨系高速钢和钼系高速钢(含 Mo2%以上);高速钢按切削性能可分为普通高速钢和高性能 高速钢;按制造工艺方法不同,又可分为熔炼高速钢和粉末冶 金高速钢。 (2)硬质合 硬质合是由硬度很高的难熔金属碳化物和金属粘接剂用粉 冶金工艺烧结而成。
1)按加工方式分:
车刀、铣刀、钻头、铰刀、拉刀、砂轮等。 2)按结构方式分: 整体式、焊接式、机夹式、可转位式等。 3)按刀具的刃形分: 单刃刀具、多刃刀具、成形刀具等。 4)按国家标准分: 标准刀具、非标准刀具等。 2、刀具材料 1)刀具材料应具备的性能 刀具切削部分的材料应满足下列要求: (1)高的硬度和耐磨性 (2)足够的强度和韧性 (3)高的耐热性与化学稳定性 (4)良好的工艺性和经济性 2)常用刀具材料 常用金属材料主要有工具钢、硬质合金、陶瓷、超硬材料 四大料,其中应用最多的是高速钢和硬质合金。
三、切削热 金属切削过程中所消耗的功,绝大部分在切削刃附近转化 为热,称为切削热。 1、切削热的主要来源 是被切削金属的变形、切屑与前刀面的摩擦和工件与刀具 后面的摩擦。 2、切削温度 切削区域的平均温度。 3、切削热的传散 切削热通过切屑、工件、刀具以及周围介质传散。 4、减少切削热,降低切削温度的措施 增大刀具前角,减小主偏角;优先采用大的背吃刀量和进 给量,再确定合理的切削速度;使用切削液都能减少和带走切 削热,降低切削温度。 四、刀具的磨损和耐用度 在切削过程中,刀具在高压、高温和强烈摩擦条件下工 作,切削刃由锋利逐渐变钝以至失去正常切削能力。磨损超过
- 1、下载文档前请自行甄别文档内容的完整性,平台不提供额外的编辑、内容补充、找答案等附加服务。
- 2、"仅部分预览"的文档,不可在线预览部分如存在完整性等问题,可反馈申请退款(可完整预览的文档不适用该条件!)。
- 3、如文档侵犯您的权益,请联系客服反馈,我们会尽快为您处理(人工客服工作时间:9:00-18:30)。
流屑角 刃倾角对切屑 流向的影响
金属切削基本理论的应用
切屑的卷曲机理 ➢ 切屑的卷曲是由于切屑内部变形或碰到
断屑槽等障碍物造成的。 遇到障碍时卷曲
通常未遇障碍时切屑也会由于 内部应力和温度作用自行卷曲
金属切削基本理论的应用
a) 变形差引起 b) 力矩引起 c) 断屑器作用引起
切屑卷曲机理
金属切削基本理论的应用
➢合理选择刀具材料、刀具几何参数、 切削用量
➢采用新的切金削属切加削基本工理论技的应用术
金属切削加工及装备——第五章
第三节
切削液 及其选用
金属切削基本理论的应用
一、切削液的功用
在切削过程中,合理使用切削液可以减小切削 力和降低切削温度,改善刀-工、刀-屑之间摩擦状况, 从而改善已加工表面质量,延长刀具寿命,降低动 力消耗。切削液应具有抗泡性、抗霉菌变质能力, 不污染环境、对人体无害,使用经济性合理。
➢冷却作用:切削液是以热传导、对流和汽
化等方式,把切屑、工件和刀具上的热量带 走,降低了切削温度,起到冷却作用,减小 了工艺系统的热变形,减少了刀具磨损。切 削液冷却性能的好坏取决于导热系数、比热 容、汽化热、汽化速度、流量和流速等。
金属切削基本理论的应用
➢润滑作用:切削液中带油脂的极性分子吸
附在刀具新鲜的前、后刀面上,形成物理或 化学吸附膜。减小刀-屑、刀-工摩擦或粘结及 刀具磨损,提高加工表面质量。
切屑的折断机理
➢ 切屑经第I、第II
变形区的严重变形
后,硬度增加,塑
性降低,性能变脆。
当切屑经变形自然
卷曲或经断屑槽等
障碍物强制卷曲产
生的拉应变超过切
屑材料的极限应变
值时,切屑即会折
断。
切屑折断时的受力及弯曲
金属切削基本理论的应用
三、断屑措施 磨制断屑槽
断屑槽的形式
金属切削基本理论的应用
断屑 槽的 位置
金属切削基本理论的应用
第一节
金属切削加工及装备——第五章
切屑控制
金属切削基本理论的应用
一、切屑形状的分类
根据ISO规定、并由我国生产工程学 会切削专业委员会推荐的国标 GB/T16461—1996的规定,切屑的形 状与名称分为八类,如表5-1所列。
切屑形状有:带状、管状、盘旋状、环
形螺旋、锥形螺旋、弧形、单元、针形。
削刃破损加剧和工件已加工表面质量下降。过大 或过小,均使其切削加工性变差
➢导热性好,切削加工性好,但加工尺 寸精度会发生变化 导热性差,加工性差。
金属切削基本理论的应用
材料的化学成分 ➢Cr、Ni、V、Mo、W、Mn等提高钢
的强度和硬度,使其切削加工性差 ➢Si、Al与氧化合后使刀具磨损加快
➢合金元素(如镍Ni)降低导热系数
Kv=v60/(v60)j
当Kv>1时,表示该材料比45钢易 切削
当Kv<1时,表示该材料比45钢难
切削
金属切削基本理论的应用
二、影响切削加工性的因素
金属材料的物理力学性能
➢硬度和强度:常温以及高温的硬度和 强度高、硬质点多,切削加工性差
➢塑性、冲击韧性:材料的塑性和韧性高,刀
具容易磨损,切削加工性差;若是过低,刀具切
➢Pb[铅]、P[磷] 、S[硫]等降低塑性(发 生热脆、冷脆现象),改善切削性
➢碳的石墨化使切削Biblioteka 工性变好(硬度 下降、润滑性变好)
➢Fe4C3使硬度金属切增削基加本理论,的应磨用 损加快
金相组织 ➢钢 的 金 相 组 织 : 铁 素 体 、 奥 氏 体 易
粘结;珠光体加工性好;索氏体、马 氏体硬度、强度高,加工性差 ➢铸铁的金相组织:灰口铁、白口铁、 麻口铁、球墨铸铁性能各异
➢清洗作用:清除细碎切屑和磨粒等。清
洗性能的好坏与切削液的渗透性、流动性和 使用压力有关。
➢ 刃倾角λs使切屑流向改变后,使切屑碰到 加工表面上或刀具后面上造成断屑。
金属切削基本理论的应用
其它断屑方法
➢附加断屑装置:为了使切屑流出时可靠 断屑,可在前刀面上固定附加断屑挡块, 使流出切屑碰撞挡块而折断。
➢间断进给断屑
采用振动切削 装置,使切削 厚度变化,获 得不等截面切 屑,在狭小截 面处断屑。 金属切削基本理论的应用
金属切削基本理论的应用
➢通常用来衡量材料切削加工性 的指标为一定耐用度下的切削 速度vT
含义是:当刀具耐用度为T时, 切削某种材料所允许的切削速 度vT。νT越高,加工性越好。
金属切削基本理论的应用
通常以强度σb=0. 637GPa的45钢 的v60作为基准,写作(v60)j;而把 其它各种材料的v60同它相比,这 个比值Kv称为相对加工性,即
金属切削基本理论的应用
二、切屑的流向、卷曲和折断
切屑的流向
➢ 为了不损伤已加工表面和方便处理切屑, 必须有效地控制切屑的流。
➢ 由于切屑流向是垂直于各切削刃的方向, 因此最终切屑的流向是垂直于主副切削刃 的终点连线方向,通常该流出方向与正交 平面夹角为ηc,ηc称为流屑角。
➢ 刀具上影响流屑方向的主要参数是λs。 金属切削基本理论的应用
金属切削基本理论的应用
三、改善难加工材料切削加工性的途径 ➢调整材料化学成分 调整材料化学成分也
是改善其切削加工性的重要途径。如钢中加S、P、 Pb、Ca等元素;铸铁中加Si、Al等元素。
➢合理选择材料的供应状态
➢通过适当热处理 用热处理方法改变材料
金相组织,低碳钢正火,高碳钢、工具钢退火
➢选用易切削钢
改变切削用量
在切削用量参数中,对断屑影响最大 的是进给量f,其次是背吃刀量ap,最小为 切削速度vc。进给量增大,使切屑厚度hch 增大,当受到碰撞后切屑容易折断。背吃 刀量增大时对断屑影响不明显,只有当同 时增加进给量时,才能有效地断屑。
金属切削基本理论的应用
改变刀具角度
➢ 主偏角kr是影响断屑的主要因素。主偏角 kr增大,切屑厚度hch增大,容易断屑。断 屑良好的车刀均选取较大的主偏角>60º
金属切削加工及装备——第五章
金属切削基本理论的应用
一、切削加工性的概念及评定指标
切削加工性是指工件材料被切削加工的 难易程度
切削加工性的标志方法有如下几个: ➢考虑生产和刀具耐用度的标志方法 ➢考虑已加工表面质量的标志方法 ➢考虑安全生产和工作稳定性的标志方法
某材料被切削时,刀具的耐用度大,允许的切削速 度高,表面质量易保证,切削力小,易断屑,则这 种材料的切削加工性好;反之,切削加工性差。