典型生产工艺——合成氨化肥厂生产工艺概况
小型合成氨厂的基本工艺

二、冷鼓车间
•目的和任务: • 除去焦炉气中残余粉尘 微粒及焦油后,再经煤气鼓 风机升压后送往洗氨脱萘为 后工序提供洁净的焦炉气。
三、压缩工段
目的和任务: 是把气体输送到各工序
并提供过程进行所需要的压力, 以使这些过程按工艺要求得以 顺利进行。
四、变换岗位
合成岗位
目的和任务:
将经甲烷化后送来的氢氮比合格的气体导入 系统,在一定的温度、压力下在氨催化剂的 作用下使氢氮气合成氨,热后经过水冷、氨 冷使混合气中的大部分气氨冷凝成液氨而分 离出来,并送往氨贮槽。分离出液氨的氢氮 混合气经循环机赠压后与补充的新鲜气在一 起送入合成塔内进行反应,如此循环。
小型化肥厂的工艺简介
小型氮肥厂的整体工艺流程
焦化车间
冷鼓车间
原料气压缩工段
变脱工段
PSA一段
碳化车间
氨回收工段
合成车间
合成压缩工段
PSA二段 精脱工段硫 工段甲烷化
CO2压缩
碳化车间 化肥
一、焦化车间
•主要的工作原理及目的 •原理:原煤经过焦化炉高温干熘后, 产出煤气,并留下了其付产品焦Βιβλιοθήκη 炭、焦油等产品。精脱硫岗位
目的与任务: 除和去有变机脱硫后,原保料证气 气中体少中量硫的化H物2S 总含量小于0.1PPm,满足甲烷 化工艺对硫的要求,同时消除 硫化物对管道和设备的腐蚀。
甲烷化岗位
除<1去.0脱%)碳,气在少适量当的的C温O和度C、O压2(共力 下,通过甲烷化催化剂的作用 将成残触余媒的无C害O的和甲CO烷2转,化出为口对气合体 (CO+CO2<20PPm)。
目的和任务: 将压缩工段送来的焦炉气中
的CO加入水蒸气并在催化剂的作 用 后下工转段化提成供较CO合2,格同的时原获料得气H2。,为
合成氨的工艺流程

合成氨的工艺流程
合成氨是一种重要的化工原料,广泛应用于化肥、医药、塑料等多个领域。
其工艺流程主要包括氮气和氢气的催化反应,下面将详细介绍合成氨的工艺流程。
首先,合成氨的工艺流程是通过哈伯-玻斯曼过程实现的。
在工业上,通常采用铁-铝催化剂进行合成氨的催化反应。
反应的化学方程式为N2 + 3H2 → 2NH3。
在反应过程中,氮气和氢气在催化剂的作用下发生反应,生成氨气。
其次,合成氨的工艺流程需要高温高压条件。
反应温度通常在400-500摄氏度,压力在100-200大气压。
高温高压条件有利于提高反应速率和转化率,从而提高合成氨的产率。
然后,合成氨的工艺流程需要进行氮气和氢气的预处理。
氮气通常来自空分设备,需要进行脱氧、脱水等处理,以保证氮气的纯度和干燥度;而氢气通常来自重整装置,也需要进行脱氧、脱硫等处理,以保证氢气的纯度和干燥度。
此外,合成氨的工艺流程还需要进行氨气的分离和净化。
合成
氨反应产生的氨气中通常伴随着少量的氮气、氢气、水蒸气和杂质气体,需要进行分离和净化,以得到高纯度的合成氨产品。
最后,合成氨的工艺流程还需要进行废气处理。
合成氨反应产生的废气中含有一定量的氮气、氢气和氨气,以及少量的催化剂粉尘和有机物,需要进行处理,以达到环保排放标准。
综上所述,合成氨的工艺流程是一个复杂的化学过程,需要高温高压条件下进行氮气和氢气的催化反应,同时进行氮气和氢气的预处理,以及氨气的分离和净化,最终进行废气处理。
这一工艺流程的稳定运行对设备的稳定性和操作技术都有较高要求,但合成氨作为重要的化工原料,其生产工艺的不断改进和优化将对化工行业的发展起到积极作用。
合成氨工艺流程简述
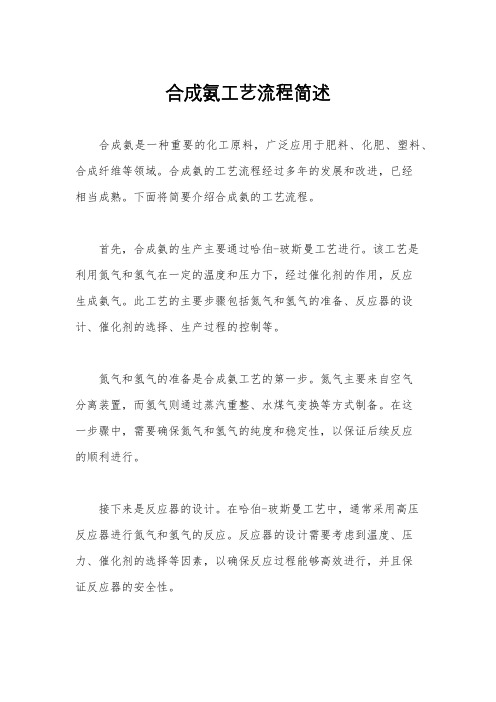
合成氨工艺流程简述合成氨是一种重要的化工原料,广泛应用于肥料、化肥、塑料、合成纤维等领域。
合成氨的工艺流程经过多年的发展和改进,已经相当成熟。
下面将简要介绍合成氨的工艺流程。
首先,合成氨的生产主要通过哈伯-玻斯曼工艺进行。
该工艺是利用氮气和氢气在一定的温度和压力下,经过催化剂的作用,反应生成氨气。
此工艺的主要步骤包括氮气和氢气的准备、反应器的设计、催化剂的选择、生产过程的控制等。
氮气和氢气的准备是合成氨工艺的第一步。
氮气主要来自空气分离装置,而氢气则通过蒸汽重整、水煤气变换等方式制备。
在这一步骤中,需要确保氮气和氢气的纯度和稳定性,以保证后续反应的顺利进行。
接下来是反应器的设计。
在哈伯-玻斯曼工艺中,通常采用高压反应器进行氮气和氢气的反应。
反应器的设计需要考虑到温度、压力、催化剂的选择等因素,以确保反应过程能够高效进行,并且保证反应器的安全性。
催化剂的选择是合成氨工艺中的关键一步。
通常采用铁、铑、钼等金属作为催化剂,以促进氮气和氢气的反应。
催化剂的选择需要考虑到反应速率、选择性、稳定性等因素,以提高氨气的产率和纯度。
生产过程的控制是合成氨工艺中的最后一步。
在反应过程中,需要控制温度、压力、气体流速等参数,以确保反应的高效进行。
此外,还需要对产物进行分离、纯化,以获取高纯度的氨气。
总的来说,合成氨工艺流程包括氮气和氢气的准备、反应器的设计、催化剂的选择和生产过程的控制。
通过这些步骤,可以高效地生产出高纯度的氨气,满足各种工业领域的需求。
合成氨工艺的不断改进和优化,将为化工行业的发展提供重要支持。
化肥厂合成氨装置生产原理及工艺流 共78页
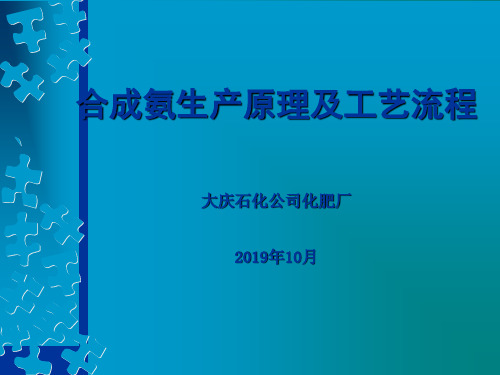
4.4 二段转化反应 二段转化反应是在一个自热式的内衬耐火材料的
圆筒式反应炉内进行的,在此引入空气,空气中的氧 气与一段转化出口气中的氢气发生燃烧,燃烧热用来 进一步转化残余甲烷。控制补入的空气流量,可同时 满足合成氨反应对氮气的需要。 1.氢气与空气中的氧燃烧反应方程式如下:
H2 + 0.5 O2 = H2O + 242 KJ/mol
3.2一段炉炉管透火。 该炉管为2000年更换,使用7年多,10月停车处理
123根泄漏炉管,现在炉顶仍有两处透火,用氮气保护 特护运行,制定事故预案,准备2019年大修更换整炉炉 管。 3.3 二段炉偏烧,出口气体CH4超过设计值,影响装置 能耗,2019年大修检查处理。 3.4 101-CA内漏
4.2 氧化锌脱硫反应 氧化锌脱硫是目前在工业上采用的脱硫效率最高的方
法,它能以极快的速度将H2S和部分有机硫全部“吃掉” ,净化后气体中硫含量可降到0.1ml/m3甚至更低。
合成装置有两台氧化锌反应炉,可以并联、串联,或 任意切除一台,以便正常生产时更换触媒。由于氧化锌实 际参加化学反应,所以其寿命很短,根据油田气含硫量及 生产负荷不同,我厂合成氨装置每年约更换4炉氧化锌触 媒。
4.7 甲烷化反应原理、影响甲烷化反应的因素、甲烷 化催化剂 1.甲烷化反应的化学方程式:
CO + 3 H2 = CH4 + H2O + 206.284KJ/MOL CO2 + 4 H2 = CH4 + 2 H2O + 165.127KJ/MOL 这两个的反应都是强放热反应,造成显著的温升,绝 热温升的数值大体是: 每反应1%CO温升72℃ 每反应1%CO2温升60℃ 甲烷化反应随温度或压力的提高而加速。如果前部反 应不好,会造成甲烷化催化剂超温,烧坏触媒。
合成氨生产工艺

合成氨生产工艺引言合成氨是一种重要的化工原料,广泛应用于农药、肥料、塑料和医药等领域。
合成氨的生产工艺对产品质量和生产效率有着重要影响。
本文将介绍合成氨的生产工艺以及涉及的关键步骤和设备。
原料及制备合成氨的主要原料是氮气和氢气。
氮气的制备可以通过空分设备获得,而氢气的制备可以通过煤气或电解水得到。
在合成氨的制备中,还需要使用催化剂,常用的是铁表面上的催化剂。
学术研究合成氨的生产工艺已经有了较为成熟的研究和应用,但仍然有很多科学家在该领域开展研究。
他们致力于改善合成氨的生产效率、降低能耗、减少环境影响。
在研究中,常常使用工艺模拟和催化剂设计等手段,以提高合成氨生产工艺的可靠性和经济性。
工艺步骤合成氨的生产工艺主要包括以下几个步骤:1. 氨合成塔氨合成塔是合成氨的主要反应设备。
该设备通常是一个高压容器,内部装有催化剂床。
氮气和氢气从塔底部进入,通过与催化剂的接触,在高温高压条件下进行反应生成氨气。
合成氨的产物会随着气流从塔顶部排出。
2. 分离和净化合成氨中常常含有一些杂质,需要通过分离和净化工艺进行处理。
其中一个常用的方法是将合成氨通过凝析,将杂质分离出来。
此外,还可以通过吸附、吸收、蒸馏等方法进行进一步处理,以获得高纯度的合成氨。
3. 氨储存和输送合成氨生产后,需要进行储存和输送。
通常采用液氨储罐和管道输送的方式。
液氨储罐可以用来暂存氨气,而管道输送可以将合成氨送往需要的地方,例如农田、化工厂等。
关键技术及装置在合成氨生产过程中,涉及到许多关键技术和装置,其中一些常见的如下:1. 催化剂催化剂是合成氨反应的关键。
常用的催化剂是铁表面上的催化剂,它能够有效地催化氮气和氢气的反应。
科学家们在催化剂设计和制备方面做了大量的研究,以提高催化剂的活性和稳定性。
2. 反应器反应器是合成氨生产中的核心设备。
反应器需要承受高温高压的环境,并保证氮气和氢气与催化剂充分接触。
优化反应器的设计和操作参数,可以提高合成氨反应的转化率和选择性。
十分钟了解合成氨的生产过程,全面又详细,不得不看!

十分钟了解合成氨的生产过程,全面又详细,不得不看!
合成氨指由氮和氢在高温高压和催化剂存在下直接合成的氨,为一种基本无机化工流程。
现代化学工业中,氨是化肥工业和基本有机化工的主要原料。
合成氨工业在20世纪初期形成,开始用氨作火炸药工业的原料,为战争服务,第一次世界大战结束后,转向为农业、工业服务。
随着科学技术的发展,对氨的需要量日益增长。
今天为大家介绍合成氨工艺,主要内容包括以下几个方面:合成氨概述、原料气的制取、脱硫、变换、脱碳、精制、氨的合成。
合成氨生产工艺流程
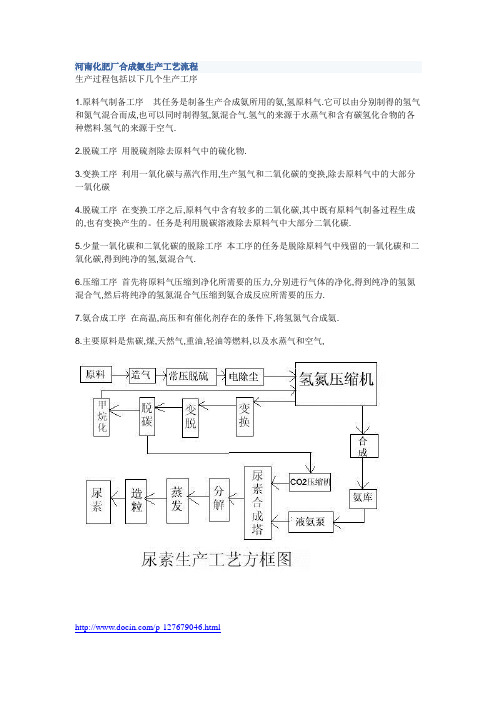
河南化肥厂合成氨生产工艺流程
生产过程包括以下几个生产工序
1.原料气制备工序其任务是制备生产合成氨所用的氨,氢原料气.它可以由分别制得的氢气和氮气混合而成,也可以同时制得氢,氮混合气.氢气的来源于水蒸气和含有碳氢化合物的各种燃料.氢气的来源于空气.
2.脱硫工序用脱硫剂除去原料气中的硫化物.
3.变换工序利用一氧化碳与蒸汽作用,生产氢气和二氧化碳的变换,除去原料气中的大部分一氧化碳
4.脱硫工序在变换工序之后,原料气中含有较多的二氧化碳,其中既有原料气制备过程生成的,也有变换产生的。
任务是利用脱碳溶液除去原料气中大部分二氧化碳.
5.少量一氧化碳和二氧化碳的脱除工序本工序的任务是脱除原料气中残留的一氧化碳和二氧化碳,得到纯净的氢,氨混合气.
6.压缩工序首先将原料气压缩到净化所需要的压力,分别进行气体的净化,得到纯净的氢氮混合气,然后将纯净的氢氮混合气压缩到氨合成反应所需要的压力.
7.氨合成工序在高温,高压和有催化剂存在的条件下,将氢氮气合成氨.
8.主要原料是焦碳,煤,天然气,重油,轻油等燃料,以及水蒸气和空气,
/p-127679046.html
/f/9615566.html
/p-119918719.html
/qk/83719X/200202/6085319.html
合成氨工艺流程
/view/5639a7e2524de518964b7de1.html。
国内典型合成氨装置工艺介绍

103-J改转子;并联101-JA; 净化使用ACT-1活化剂,更换规整填料;
司,成达
合成回路改塔后分氨、增加小合成塔1105-D工程公司 Nhomakorabea10
五大机组电子调 五大机组电子调速器改造,采用ITCC系统进行控制 速器改造
康吉森公 司
投用时 间
1984.4 1986.2
1990.8 1988.9
1993.9 1997.7 2002.7 2005.1 2008.8
每排42根转化管的底部都同一根集气管相连,后者靠近 一段炉的底部,每根集气管的中部有一上升管,这九根上升 管又把气体引到炉顶上一根装有水夹套的输气管线,再由此 把气体送至二段转化炉103-D的入口。一段炉的热量是由 200个顶部烧嘴供应的。部分转化后的混合气含有12.91%的 甲烷。
二段转化炉103-D所需工艺空气由蒸汽透平压缩机101-J (提供约65%的空气量)和电动压缩机101-JA(约35%)提 供。定量中压蒸汽与工艺空气混合,经过一段炉对流段空气/ 蒸汽混合气预热盘管被加热到599℃,经过二段炉的喷嘴与 来自一段炉的工艺气在燃烧室进行混合燃烧(空气中的氧与 一段转化气中的氢燃烧),接着在内衬耐火材料的圆筒式反 应炉内通过镍触媒进一步转化残余甲烷。二段转化炉出口气 含有0.38%的甲烷,温度约为1000℃,进入第一废热锅炉 101-CA/CB、第二废热锅炉102-C,被来自101-F的锅炉水 继续冷却,冷却后的转化气温度降低到371℃。
合成氨工艺的5个过程:
1、油田气脱硫:
R-SH+H2=RH+H2S H2S+ZnO=H2O(汽)+ZnS 2、转化:
CH4+H20(汽)=CO+3H2 CH4+2H2O(汽)=CO2+4H2 3、变换:
化肥厂生产过程及工艺流程

化肥厂生产过程及工艺流程煤制合成氨、尿素C+ 0.5 O2 →COC+ O2 →CO2CO + H2O→CO2+ H2H2+N2→NH3CO2 + 2NH3 →CO (NH2)21 全厂流程简介2 过程工艺描述(1)水煤浆气化制合成气装置由水煤浆制备工序来的水煤浆送入煤浆槽储存待用。
浓度约为63%的水煤浆通过煤浆给料泵加压输送到气化炉顶部工艺烧嘴,并与空分装置来的纯氧分别进入气化炉在6.5MPa(G),约1400℃工艺条件下,水煤浆与纯氧进行部分氧化反应,生成粗合成气。
反应后的粗合成气和溶渣进入气化炉下部的激冷室。
在激冷室中,粗合成气经冷却、洗涤,将粗合成气中的大部分碳黑洗去,并和粗渣分开。
出激冷室的粗合成气直接进入文丘里洗涤器和碳洗塔进一步洗涤,除去粗合成气中残留的碳黑,然后将水蒸汽/干气比约1.3~1.5的合成气送至变换工序。
溶渣被激冷室底部通过破渣机进入锁斗,定期排入渣池,渣池设有捞渣机将粗渣捞出,装车运往园区免烧砖项目。
渣池中含细渣的灰水通过渣池泵送至真空闪蒸器。
碳洗塔的液位通过控制进入塔内的灰水量来维持,碳洗塔内的黑水分两股排出,一股黑水去高压闪蒸器;另一股由灰水循环泵送至气化炉也进入高压闪蒸器,黑水经减压,闪蒸出黑水中溶解的气体并通过变换冷凝液加热器回收闪蒸汽的热量,通过高压闪蒸分离器,闪蒸出的气体至变换或火炬,水送入脱氧水槽。
(2)净化装置a. 变换变换工序主要反应式为:COS+H2O——CO2+H2S+QCO+H2O——CO2+H2+Q由气化送来粗煤气经煤气水分离器分离掉少量的冷凝液及灰尘后,经中温换热器温度升高至250℃,进第一中温变换炉。
第一中温变换炉分上、下两段,炉内装有两段三层耐硫变换触媒,层间配有煤气激冷管线调温,出第一中温变换炉变换气CO含量为24%(干),温度为420℃左右。
变换气经中温换热器降温后进淬冷器,用本工段产生的高温冷凝液淬冷至240℃,然后进入第二中温变换炉,炉内装有两段耐硫变换触媒,出口变换气CO浓度为4.0%(干),温度为358℃左右,进入中变废热锅炉,产生1.0MPa(G)的低压蒸汽,使变换气温度降温进入低温变换炉,低温变换炉装两段耐硫变换触媒,出口变换气CO浓度为1.0%(干),温度升至为222℃左右,进入低变废热锅炉,产生0.4MPa(G)的低压蒸汽,变换气温度降至163℃;经第一水分离器分离出冷凝液后的变换气进入锅炉给水加热器,温度降至140℃,然后进入脱盐水加热器温度降至70℃、进变换气水冷器温度降至为40℃,进水洗塔,在塔底进行气液分离后,气体经塔顶40℃洗涤水洗涤除去NH3后送至甲醇洗工段。
合成氨生产工艺简介

合成氨生产工艺简介目前国内生产合成氨的工艺大同小异,忽略各自的设备差异和工艺上的微小不同,我们可以将氨的生产过程,粗略的讲可分成一下几步:造气;脱硫;变换;变换后脱硫;铜洗;氨合成几个步骤,如下是此类流程的一个极简示意图:图1合成氨的极简化流程1造气工段造气实质上是碳与氧气和蒸汽的反应,原料煤间歇送入固定层煤气发生炉内,先鼓入空气,提高炉温,然后加入水蒸气与加氮空气进行制气。
所制的半水煤气(主要成分为CO 和H 2,另有其他杂质气体)进入洗涤塔进行除尘降温,最后送入半水煤气气柜。
造气工段脱硫工段变换工段煤块 水蒸汽CO, N 2, H 2 H 2S 等其他杂质 CO, N 2, H 2变换气脱硫工段CO 2, N 2, H 2H 2S 等其他杂质 甲醇合成工段少量CO, CO 2, N 2, H 2精炼工段N 2, H 2 极少量CO X 等其他杂质 氨合成工段N 2, H 2冷冻工段NH 3 液氨图2 造气工艺流程示意图2脱硫工段煤中的硫在造气过程中大多以H2S的形式进入气相,它不仅会腐蚀工艺管道和设备,而且会使变换催化剂和合成催化剂中毒,因此脱硫工段的主要目的就是利用DDS脱硫剂脱出气体中的硫。
气柜中的半水煤气经过静电除焦、罗茨风机增压冷却降温后进入半水煤气脱硫塔,脱除硫化氢后经过二次除焦、清洗降温送往压缩机一段入口。
脱硫液再生后循环使用。
图3 脱硫工艺流程图3变换工段气体从脱硫工艺中处理过后,已不含H2S等有毒气体。
变换工段的主要任务是将半水煤气中的CO在催化剂的作用下与水蒸气发生放热反应,生成CO2和H2。
经过两段压缩后的半水煤气进入饱和塔升温增湿,并补充蒸汽后,经水分离器、预腐蚀器、热交换器升温后进入中变炉回收热量并降温后,进入低变炉,反应后的工艺气体经回收热量和冷却降温后作为变换气送往压缩机三段入口。
说明:合成气的中的CO(一氧化碳)经蒸汽转换成CO2(二氧化碳)与H2,转换后气体称为“变换气”。
合成氨工艺及节能分析
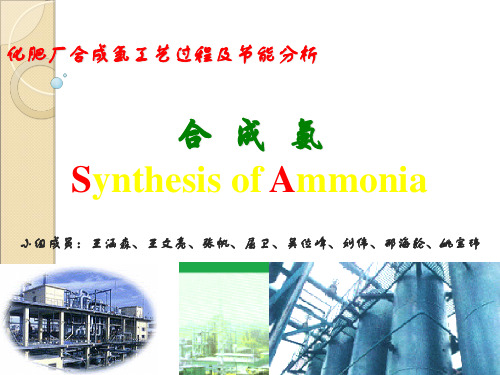
化肥厂合成氨工艺过程及节能分析
合成氨 Synthesis of Ammonia
小组成员:王涵森、王文亮、张帆、屈卫、吴位峰、刘伟、邢海轮、姚宝玮
一、 概 述
1、合成氨的重要性 氨的合成使人类从自然界制取含氮化合物的最重要方法。氮则
是进一步合成含氮化合物的最重要原料,而含氮化合物在人民生活 中都是必不可少的。1977~1978年,世界含氮化合物产量为4935万吨 氮,1980~1981则达6284万吨。
综合化:一方面是多种化工过程(传动过程、传热过程、传 质过程、化学反应过程)有机地组合;另一方面是为了提 高原料和热量的综合利用。这种综合利用常使生产过程中 出现大量物料回流和热量回流,以及不同产品的联合生产。 上述两种综合化出是其他工业生产很少有的。
技术经济分析和综合利用
评论化工生产的标准和其它工业一样,概括地讲 就是高产、优质、低耗、安全生产。联系化工实际, 也可以概括成:物料和能量的综合利用率,减少生产 费用和有利于环境保护等。
典型生产工艺——合成氨化肥厂生产工艺概况
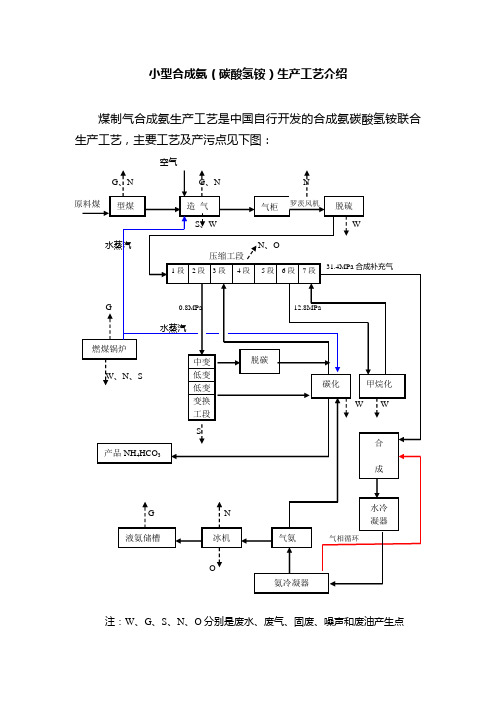
煤制气合成氨生产工艺是中国自行开发的合成氨碳酸氢铵联合生产工艺,主要工艺及产污点见下图:
空气
G、N G、N N
S、W W
水蒸汽N、O
31.4MPa合成补充气
G0.8MPa12.8MPa
水蒸汽
W、N、S
W W
S
G N
O
注:W、G、S、N、O分别是废水、废气、固废、噪声和废油产生点
溶液再生:NaHCO3+NaOH= NaCO3+H2O
脱硫系统主要由罗茨风机、脱硫塔、再生塔等设备组成。
采用湿法脱硫工艺。在脱硫塔内,半水煤气由下而上与脱硫液逆流接触。半水煤气大部份硫化氢被脱除。脱硫后的半水煤气送往压缩工序。氧化生成的单质硫成泡沫状浮在液面上。脱硫液经再生后可循环使用。
⑶变换工段
由于半水煤气中含有26%~30%的CO必须转换为CO2。其化学原理如下:
拟稿:罗俊
校核:李尚科
2010-2-1
⑺合成工段
合成是最后一道工序,在适当的温度、压力和催化剂存在的条件下,将氢、氮混合气按一定比例合成成氨,然后将气氨从未合成的混合气体中冷凝分离出来,循环合成。
化学原理
3H2气,通过压缩机七段加压到31.4MPa,补充到合成工段。合成循环气经循环压缩机升压并被预热至一定温度后,进入合成塔,在合成催化剂的作用下合成氨。
⑷碳化工段
碳化工段采用浓氨水吸收变换气中的二氧化碳,并制成合格的碳酸氢铵。被清除了二氧化碳的原料气送往压缩工段。
NH3+CO2+H2O=NH4HCO3
碳化工段主要由碳化主塔、碳化副塔、分离装置和热交换器组成。
约四分之一变换气进入碳化工段,依次进入碳化主塔、副塔,变换气与吸氨岗位(采用稀氨水水吸收气氨)送来的浓氨水鼓泡接触,变换气中CO2与浓氨水发生碳化反应,在碳化主塔生成NH4HCO3结晶,晶液经取出在稠厚器长大,最后经离心分离水份制得合格产品碳酸氢铵。碳化副塔出来的碳化气进入碳化综合塔,采用软水回收气体中的氨后,合格的碳化气进入压缩三段。
浅谈合成氨工艺[1]
![浅谈合成氨工艺[1]](https://img.taocdn.com/s3/m/4b05ec4accbff121dc368314.png)
浅谈合成氨工艺氮肥生产是高能耗的工业,其生产成本主要取决于系统的能耗,系统能耗除了与采用的工艺流程有关外,在很大程度上取决于系统控制的算法及稳定性,因此,化肥生产过程的控制系统对整个生产成本具有关键意义。
本文比较详细的介绍了合成氨的工艺流程,并对化肥的生产做了介绍,并且从再生产的角度介绍了钢铁厂的副产业——硫酸铵的生产。
最终对我国合成氨技术的发展做了展望。
氨是重要的无机化工产品之一,在国民经济中占有重要地位。
除液氨可直接作为肥料外,农业上使用的氮肥,例如尿素、硝酸铵、磷酸铵、氯化铵以及各种含氮复合肥,都是以氨为原料的。
合成氨是大宗化工产品之一,世界每年合成氨产量已达到1亿吨以上,其中约有80%的氨用来生产化学肥料,20%作为其它化工产品的原料。
本次化工见习,我们参观了玉溪新兴钢铁有限公司和峨山化肥厂,对合成氨工艺,以及化肥生产工艺,有了质的认识。
详细的工业流程又可分为一下几步:(1)以无烟煤为原料合成氨常见的工艺过程是:造气-> 半水煤气脱硫-> 压缩机1,2工段-> 变换-> 变换气脱硫->压缩机3段-> 脱硫->压缩机4,5工段-> 铜洗-> 压缩机6段-> 氨合成-> 产品NH3(2)采用甲烷化法脱硫除原料气中CO. CO2 时, 合成氨工艺流程图如下:造气->半水煤气脱硫->压缩机1,2段->变换-> 变换气脱硫-> 压缩机3段->脱碳-> 精脱硫->甲烷化->压缩机4,5,6段->氨合成->产品NH3一、合成氨工艺德国化学家哈伯1909年提出了工业氨合成方法,即“循环法”,这是目前工业普遍采用的直接合成法。
反应过程中为解决氢气和氮气合成转化率低的问题,将氨产品从合成反应后的气体中分离出来,未反应气和新鲜氢氮气混合重新参与合成反应。
合成氨反应式如下:N2+3H2≈2NH3在合成氨的所有流程中,核心围绕此方程式展开,用最低的能耗量,得到最高质量的产品。
合成氨生产工艺综述
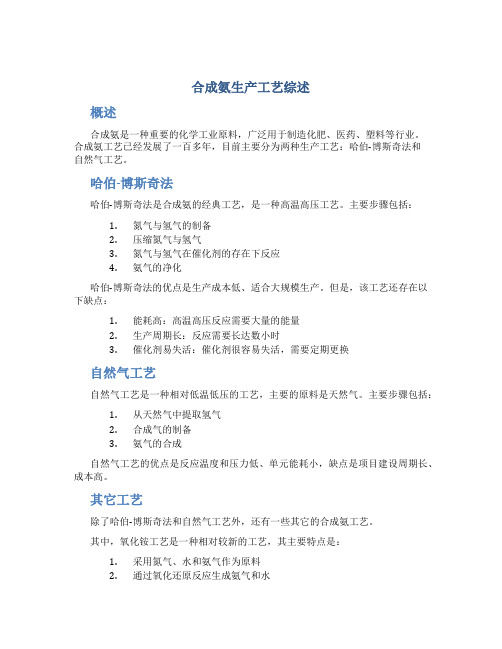
合成氨生产工艺综述概述合成氨是一种重要的化学工业原料,广泛用于制造化肥、医药、塑料等行业。
合成氨工艺已经发展了一百多年,目前主要分为两种生产工艺:哈伯-博斯奇法和自然气工艺。
哈伯-博斯奇法哈伯-博斯奇法是合成氨的经典工艺,是一种高温高压工艺。
主要步骤包括:1.氮气与氢气的制备2.压缩氮气与氢气3.氮气与氢气在催化剂的存在下反应4.氨气的净化哈伯-博斯奇法的优点是生产成本低、适合大规模生产。
但是,该工艺还存在以下缺点:1.能耗高:高温高压反应需要大量的能量2.生产周期长:反应需要长达数小时3.催化剂易失活:催化剂很容易失活,需要定期更换自然气工艺自然气工艺是一种相对低温低压的工艺,主要的原料是天然气。
主要步骤包括:1.从天然气中提取氢气2.合成气的制备3.氨气的合成自然气工艺的优点是反应温度和压力低、单元能耗小,缺点是项目建设周期长、成本高。
其它工艺除了哈伯-博斯奇法和自然气工艺外,还有一些其它的合成氨工艺。
其中,氧化铵工艺是一种相对较新的工艺,其主要特点是:1.采用氮气、水和氨气作为原料2.通过氧化还原反应生成氨气和水3.无需催化剂,反应速度较快4.适用于小规模生产氧化铵工艺的缺点是产品品质不稳定、设备易发生腐蚀,需要增加生产成本。
综合来看,合成氨工艺有其各自的优缺点。
哈伯-博斯奇法适合大规模生产,但成本较高,能耗大。
自然气工艺相对较新,技术尚不成熟,建设周期长、成本高。
氧化铵工艺适合小规模生产,但产品品质不稳定、设备易发生腐蚀。
随着反应工艺的不断发展,合成氨工艺也在不断进步。
未来的合成氨工艺可能会更节能环保、成本更低,能够更好地满足各个行业对于合成氨的需求。
合成氨生产工艺流程演示文稿

合成氨生产工艺流程演示文稿合成氨是一种用于生产肥料、塑料、药品等的重要化学物质。
下面是合成氨生产工艺流程的演示文稿,详细介绍了合成氨的生产过程。
一、引言大家好!我今天将为大家介绍合成氨的生产工艺流程。
合成氨是一种重要的化学原料,广泛应用于农业、化工、制药等领域。
通过合成氨工艺,我们能够高效地生产出大量的氨气。
二、生产工艺流程1.原料准备合成氨的主要原料是氢气和氮气。
氢气通常由天然气蒸气重整或煤气化等方法获得,氮气则可以通过空分设备进行分离。
这两种原料首先需要进行净化和压缩,以满足反应装置的要求。
2.合成反应合成氨工艺的核心是合成反应。
合成反应通常在高温(400-500℃)和高压(20-30MPa)下进行。
反应需要一个催化剂,常用的催化剂是铁-铬体系。
催化剂的作用是降低反应的活化能,促进氨气的生成。
在反应过程中,氢气和氮气以一定的比例进入催化剂床层。
催化剂床层中的铁-铬催化剂将氢气和氮气转化为氨气。
反应产物经过冷却、净化和压缩处理后,得到高纯度的合成氨。
3.副反应控制在合成氨反应中,除了产生氨气外,还会产生一些副产物,如一氧化碳、二氧化碳和甲烷等。
这些副产物会降低氨气的产量和质量,因此需要采取相应的措施进行控制。
一种常用的副反应控制方法是增加氮气的用量。
通过提高氮气的进料比例,可以降低副产物的生成,同时提高氨气的选择性。
此外,也可以通过改进催化剂的配方和反应条件等手段,进一步减少副产物的生成。
4.废气处理合成氨工艺中产生的废气中含有一定量的副产物,如一氧化碳、二氧化碳和氮氧化物等。
这些副产物对环境具有一定的污染作用,因此需要进行处理。
常用的废气处理方法是采用催化燃烧技术。
废气被引入燃烧室,与催化剂进行混合并加热,使副产物发生氧化反应。
经过处理后,废气中的有害物质被还原为无害的二氧化碳和水。
三、总结通过合成氨生产工艺流程,我们可以高效地生产出大量的合成氨。
生产过程中,需要准备原料、进行合成反应、控制副反应和处理废气等环节。
合成氨生产工艺

合成氨生产工艺合成氨,是一种重要的化工原料,广泛用于制造化肥、合成涂料、塑料、化学纤维等。
合成氨的生产工艺主要有哈柏法、洛夫法和庙门法等。
其中,哈柏法是最主要的合成氨生产工艺。
哈柏法是以氮气和氢气为原料,经过一系列反应生成合成氨的工艺。
首先,从空气中获取氮气,经过压缩、除尘等处理后进入合成氨装置。
氢气则主要通过天然气蒸汽重整或煤气重整反应获得。
在合成氨装置中,氮气和氢气通过压缩机加压,然后进入催化转化器。
转化器内装有铁-铁酸催化剂。
氮气和氢气在催化剂的作用下发生反应,生成一氧化氮。
一氧化氮经过再次加压后进入反应塔。
反应塔中存在多个铁-铁酸催化剂层。
一氧化氮在催化剂层间不断与氢气反应生成亚硝酸,然后再与氢气反应生成胺。
胺在反应塔中流动,最终通过冷却器冷却并与废气分离,得到合成氨产品。
合成氨生产过程中,催化剂起到至关重要的作用。
铁-铁酸催化剂由于其高的活性和选择性,被广泛应用于合成氨生产中。
同时,催化剂的选择和设计对反应效率和产品纯度也有着重要影响。
目前,研究人员也在不断探索新型催化剂的开发,以提高合成氨生产过程的效率和环保性。
合成氨生产工艺中,还存在一些技术难题需要克服。
一方面,氮气和氢气为非常活性的气体,对设备和催化剂耐压性能要求较高。
另一方面,合成氨生产过程中产生的废气中含有一定的氨气和一氧化碳等有害物质,需要进行处理和净化,以保护环境和人体健康。
总结起来,哈柏法是目前合成氨生产中最主要的工艺。
通过合理选择催化剂和优化反应条件,可以高效地生产出优质的合成氨产品。
然而,合成氨生产工艺仍面临一些挑战,需要通过技术进步和创新来不断完善。
合成氨工艺流程详解

合成氨工艺流程详解合成氨是一种重要的化工原料,在农药、肥料、塑料、纤维等方面都有广泛应用。
下面我们就来详细解析一下合成氨的工艺流程。
合成氨的工艺流程主要包括气体净化、气体压缩、气体循环、气体转化及气体分离等环节。
首先是气体净化。
合成氨的原料主要是天然气和空气,其中天然气中含有杂质,需要进行净化。
常用的净化方法有吸附、干燥和过滤等。
吸附是利用吸附材料对杂质进行吸附,干燥是将天然气中的水分去除,过滤是通过过滤器过滤掉颗粒杂质。
经过这些处理后,能够得到纯净的原料气体。
接下来是气体压缩。
原料气体需要进行压缩,提高其进入合成反应器的压力。
通常使用压缩机进行气体的压缩,将其压缩到所需的工作压力。
然后是气体循环。
合成氨反应是连续进行的,需要循环利用气体,提高反应的效率。
在循环过程中,气体需要经过冷却、减压和再压缩等处理,以保持合适的温度和压力。
接下来是气体转化。
气体转化是合成氨工艺的核心环节。
主要是通过催化剂催化,将氮气和氢气在一定的温度和压力下,进行化学反应生成氨气。
这个过程中,需要控制好反应的温度、压力、催化剂的选择和反应时间等条件,以提高氨气的产率和质量。
最后是气体分离。
合成氨反应生成的气体中还包括一些未反应的氮气、氢气和其他副产物,需要对其进行分离和回收。
通常使用吸附法、吸收法和膜分离等方法进行气体分离。
吸附法是利用吸附剂对气体进行吸附,吸收法是将气体溶解到溶剂中,膜分离是利用半透膜对气体进行分离。
通过这些分离技术,能够得到纯度较高的合成氨。
总的来说,合成氨的工艺流程包括气体净化、气体压缩、气体循环、气体转化和气体分离等环节。
在每个环节中,都需要进行相应的操作和控制,以确保合成氨的生产过程稳定、高效和安全。
合成氨生产工艺介绍[整理]
![合成氨生产工艺介绍[整理]](https://img.taocdn.com/s3/m/d91ca5ee5122aaea998fcc22bcd126fff7055d8f.png)
合成氨生产工艺介绍[整理]合成氨是现代农业、化学工业、燃料等领域的重要原料。
工业合成氨的生产工艺主要是通过哈-博士过程进行的,简称H-B法。
这种方法是将空气中的氮气与氢气在催化剂的存在下进行化学反应,生成氨气。
1. 哈-博士过程的原理H-B法是将氮气和氢气分别通过加热、压缩和清洗等方式处理后,再将两气混合到催化剂层上进行反应。
催化剂通常选用铁、铑、钼等金属催化剂,也可以采用物理和化学合成的单一和复合催化剂。
在反应过程中,氢气在催化剂层上与氮气发生反应,生成氨气,同时放出大量的热量。
生成氨气后,氢气和氮气的剩余量将被回收再利用。
2. 生产工艺流程H-B法合成氨气的生产工艺流程主要包括氢气制备、氮气制备、氢氮混合、压缩、催化反应、分离纯化和氨气回收等环节。
(1)氢气制备:通过蒸汽重整、水气变换和煤制氢等方法将天然气、石油、煤等原料转化为氢气。
(2)氮气制备:常用的方法有空气分离法和氧化铵法。
空气分离法将空气经过压缩、冷却、除尘、空气分离等步骤制备氮气。
氧化铵法则是将高浓度的氨水与纯碳粉混合后在加热反应生成氮气。
(3)氢氮混合:通过控制氢气和氮气的比例制备合适的混合气体。
(4)压缩:利用压缩机将氢氮混合气体压缩至高压。
(5)催化反应:将高压氢氮混合气体经过加热后,进入催化反应器内,在催化剂作用下氮气和氢气发生化学反应生成氨气。
(6)分离纯化:将合成气中的氨气、氢和氮等组分进行分离和纯化,得到高纯度的氨气。
(7)氨气回收:将产生的氨气收集回收,同时将未反应的氢气和氮气回收再利用。
3. 工艺的优缺点H-B法的主要优点是工艺稳定,生产量大,产品纯度高,而且氨气的制备设备易于实现自动化控制,操作简单。
它是目前世界上最为成熟的合成氨气工艺。
但是,H-B法也存在一些缺点。
首先,该工艺所用的原材料,也就是天然气、石油、煤等等,属于有限资源,且成本较高。
其次,反应过程中可能产生一定的有毒和有害物质,对环境和人体健康造成影响。
- 1、下载文档前请自行甄别文档内容的完整性,平台不提供额外的编辑、内容补充、找答案等附加服务。
- 2、"仅部分预览"的文档,不可在线预览部分如存在完整性等问题,可反馈申请退款(可完整预览的文档不适用该条件!)。
- 3、如文档侵犯您的权益,请联系客服反馈,我们会尽快为您处理(人工客服工作时间:9:00-18:30)。
合成是最后一道工序,在适当的温度、压力和催化剂存在的条件下,将氢、氮混合气按一定比例合成成氨,然后将气氨从未合成的混合气体中冷凝分离出来,循环合成。
化学原理
3H2+N2=2NH3
净化后的精炼气即为新鲜合成气,通过压缩机七段加压到31.4MPa,补充到合成工段。合成循环气经循环压缩机升压并被预热至一定温度后,进入合成塔,在合成催化剂的作用下合成氨。
CO+H2O=CO2+H2+Q
由于该反应是可逆放热反应,因此变换工段必须控制温度和压力,使平衡向有利于产生氢气和二氧化碳方向移动。
变换工段主要由一、二段变换炉、热交换器、热水饱和塔等设备组成。
半水煤气经压缩机一、二段加压至0.8MPa后进入变换饱和热水塔增湿,并在出口管道上再补充蒸汽,经热交换器换热至变换反应所需的温度后进入中温变换炉,采用Fe2O3铁铬催化剂,经两段中温变换,控制适当变换率制得中变气,中变气经换热降温进入第一低变进行低温变换,第一低变后变换气经降温后进入第二低变,制得合格的变换气,变换气经第一加热器,热水塔和第二加热器回收余热后,最后入冷却塔降温至35℃,二次进入干法脱槽变换气进行二次脱硫,脱硫后变换气控制流量分别去碳化工序和脱碳工序。
⑷碳化工段
碳化工段采用浓氨水吸收变换气中的二氧化碳,并制;CO2+H2O=NH4HCO3
碳化工段主要由碳化主塔、碳化副塔、分离装置和热交换器组成。
约四分之一变换气进入碳化工段,依次进入碳化主塔、副塔,变换气与吸氨岗位(采用稀氨水水吸收气氨)送来的浓氨水鼓泡接触,变换气中CO2与浓氨水发生碳化反应,在碳化主塔生成NH4HCO3结晶,晶液经取出在稠厚器长大,最后经离心分离水份制得合格产品碳酸氢铵。碳化副塔出来的碳化气进入碳化综合塔,采用软水回收气体中的氨后,合格的碳化气进入压缩三段。
⑷脱碳工段
脱碳工段是利用二氧化碳在有机溶剂中溶解度大的特点除去变换气中的二氧化碳。此处采用MDEA法,即N-甲基二乙醇胺的水溶液为吸收剂。
脱碳工段主要由吸收塔、常压解吸塔、气提再生塔组成。
约四分之三的变换气进入吸收塔内,在吸收塔内与从上而下MDEA水溶液逆流吸收,脱除二氧化碳等杂质,净化气(CO2<0.1%)送回压缩三段加压。从吸收塔出来的富液进入常压解吸塔,由于压力下降,溶液中的CO2气体被解吸出来。解吸后的半贫液进入气提再生塔进一步解吸,回收MDEA水溶液。
出塔气经水冷凝器、液氨冷凝器二级冷凝分离出液氨,分离后的合成循环气循环使用。液氨通过氨冷凝器蒸发为气氨,一部份气氨送碳化工序吸氨岗位,一部份气氨由冰机制成液氨进入产品贮槽,作为产品出售。
驰放气:合成氨中生产出的液氨溶解有H2、N2、CH4,这部分气体在液氨储槽又释放出来,称为驰放气。
放空气:合成工段在操作、调节、放氨过程中均要跑气或塔后放空,这部分含有大量的氨、以及H2、N2、CH4等可燃气体,称为驰放气。
拟稿:罗俊
校核:李尚科
2010-2-1
⑹甲烷化工段
甲烷化属于精炼工艺,因为原料气经过脱碳后尚含有少量的CO和CO2;碳化工段的原料气,除含有H2、N2和CH4有效气体外,还含有CO、CO2、O2和微量的H2S,必须加以去除制成合格的精炼合成气。该厂采用的是甲烷化工艺。
甲烷化工段主要由甲烷化换热器、甲烷化中间换热器、甲烷化炉氧化锌脱硫槽组成。
主要工艺简述如下:
⑴造气工段
化学原理
C+O2=CO2
C+H20=CO+H2
CO2+C=2CO
C+H20=C02+2H2
造气系统主要由煤气发生炉和燃煤锅炉两部分组成。
原料煤经预选,破碎、筛分后倒入吊斗,提升至煤气发生炉顶部,经自动加焦机定时加入煤气发生炉内煤气发生炉间歇自动操作制取半水煤气。气化后的灰渣由炉底排出,送往燃煤锅炉混合燃煤掺烧。
溶液再生:NaHCO3+NaOH= NaCO3+H2O
脱硫系统主要由罗茨风机、脱硫塔、再生塔等设备组成。
采用湿法脱硫工艺。在脱硫塔内,半水煤气由下而上与脱硫液逆流接触。半水煤气大部份硫化氢被脱除。脱硫后的半水煤气送往压缩工序。氧化生成的单质硫成泡沫状浮在液面上。脱硫液经再生后可循环使用。
⑶变换工段
由于半水煤气中含有26%~30%的CO必须转换为CO2。其化学原理如下:
⑸压缩工段
合成氨生产,原料气的精炼和合成都是在较高压力下进行,因此需要利用混合气压缩机将气体压缩到较高的压力。该厂采用的是七级压缩机,其流程见下:
原料气经除尘、脱硫后,进压缩机,二段出口(0.8MPa)送到变换、分别脱碳、碳化后送入三段,六段出口(12.8MPa)送甲烷化,甲烷化后送入七段,七段出口(32.6MPa)送到合成。
吹风阶段空气由炉底送入,由炉顶出来的吹风气经过旋风除尘后直接排放,未加以回收。
合格的半水煤气经洗气塔洗气,降低温度后进入煤气气柜。气柜中的半水煤气作为原料气由罗茨风机送往脱硫工序。洗气废水经简单处理后直接排放。
⑵脱硫工段
化学原理
脱硫化氢:NaCO3+H2S=NaHS+NaHCO3
氧化析硫:NaHS+1/2O2=NaOH+S
化学原理
CO+3H2=CH4+H2O
CO2+4H2=CH4+2H2O
送来的原料气(CO+CO2<0.7%)经油水分离器分离掉油水后,进入甲烷化换热器预热到200℃,再进入甲烷化中间换热器,利用变换气加热至270℃后进入氧化锌脱硫槽进一步精脱硫,进入甲烷化炉在甲烷化催化剂作用下发生甲烷化,去除CO+CO2,最后经汽水分离器送去压缩工段。
小型合成氨(碳酸氢铵)生产工艺介绍
煤制气合成氨生产工艺是中国自行开发的合成氨碳酸氢铵联合生产工艺,主要工艺及产污点见下图:
空气
G、N G、N N
S、W W
水蒸汽N、O
31.4MPa合成补充气
G0.8MPa12.8MPa
水蒸汽
W、N、S
W W
S
G N
O
注:W、G、S、N、O分别是废水、废气、固废、噪声和废油产生点