管式裂解炉及裂解部分工艺流程.
乙烯裂解炉工作流程
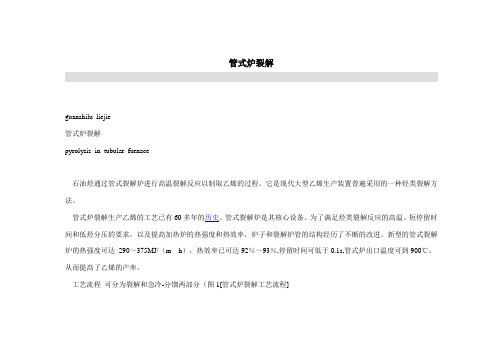
管式炉裂解guanshilu liejie管式炉裂解pyrolysis in tubular furnace石油烃通过管式裂解炉进行高温裂解反应以制取乙烯的过程。
它是现代大型乙烯生产装置普遍采用的一种烃类裂解方法。
管式炉裂解生产乙烯的工艺已有60多年的历史。
管式裂解炉是其核心设备。
为了满足烃类裂解反应的高温、短停留时间和低烃分压的要求,以及提高加热炉的热强度和热效率,炉子和裂解炉管的结构经历了不断的改进。
新型的管式裂解炉的热强度可达290~375MJ/(m h),热效率已可达92%~93%,停留时间可低于0.1s,管式炉出口温度可到900℃,从而提高了乙烯的产率。
工艺流程可分为裂解和急冷-分馏两部分(图1[管式炉裂解工艺流程]①裂解裂解原料经预热后,与过热蒸汽(或称稀释蒸汽)按一定比例(视原料不同而异)混合,经管式炉对流段加热到500~600℃后进入辐射室,在辐射炉管中加热至780~900℃,发生裂解。
为防止高温裂解产物发生二次反应,由辐射段出来的裂解产物进入急冷锅炉,以迅速降低其温度并由换热产生高压蒸汽,回收热量。
②急冷-分馏裂解产物经急冷锅炉冷却后温度降为350~600℃,需进一步冷却,并分离出各个产品馏分。
来自急冷锅炉的高温裂解产物在急冷器与喷入的急冷油直接接触,使温度降至200~220℃左右,再进入精馏系统,并分别得到裂解焦油、裂解柴油、裂解汽油及裂解气等产物。
裂解气则经压缩机加压后进入气体分离装置。
裂解原料和产品分布最初,美国管式炉裂解原料是用天然气、油田伴生气和炼厂气中回收的轻质烃,其中主要含有乙烷、丙烷、丁烷及碳五馏分。
50年代,西欧和日本的石油化工兴起,由于缺乏石油及天然气资源,因而采用石脑油作裂解原料。
60年代后,又相继开发以轻柴油、重柴油和减压瓦斯油为原料的裂解技术,扩大了裂解原料来源。
对于不同的原料,裂解工艺参数不同、在适宜条件下的裂解产品分布也各异(见表[不同原料管式炉裂解产品分布(质量%)])。
乙烯的生产-裂解

2.环烷烃的断链(开环)反应
环烷烃的热稳定性比相应的烷烃好。
环烷烃热裂解时,可以发生C-C链的断裂(开 环),生成乙烯、丁烯和丁二烯等烃类。 环烷烃脱氢生成芳烃优于开环生成烯烃
侧链烷基断裂比开环容易。带短侧链时,先断 侧链再裂解;带长侧链,先在侧链中间断裂。
3.芳烃的断侧链反应
芳环不断裂 断侧链生成苯、甲苯、二甲苯
2.停留时间的选择
裂解温度:温度越高, 乙烯的峰值收率越高, 相应的最适宜停留时 间越短。
裂解原料:在一定的反应温度下,如裂解原料 较重,则停留时间应短一些,原料较轻则可稍 长一些;
三、裂解原料的性质及评价
族组成 氢含量
芳烃指数
1、族组成-PONA值
PONA值指各族烃的质量百分含量。 适用于表征石脑油、轻柴油等轻质馏分油
烷烃P (paraffin)
烯烃O (olefin)
环烷烃N (naphthene) 芳烃A (aromatics)
同条件下,P 越大,乙烯收率越高; 分子量愈大,(N+A)量愈大,乙烯收率愈小, 液态产物量愈大。 乙烯收率:P>N>A
(一)一次反应
1.烷烃裂解的一次反应
2.环烷烃的断链(开环)反应 3.芳烃的断侧链反应 4.烯烃的断链反应
1.烷烃裂解的一次反应
(1)断链反应
C-C键断裂,反应产物是烷烃和烯烃。 通式为:Cm+nH2(m+n)+2 →CnH2n+ CmH2m+2 (2)脱氢反应 C-H键断裂。 通式为:CnH2n+2 → CnH2n+H2
项目二
裂解(裂化)工艺简介

19
20
(二)停留时间
1. 停留时间 指裂解原料由进
入裂解辐射管到离 开裂解辐射管所经 过的时间。
6
2.环烷烃裂解的一次反应 原料中的环烷烃可以发生断链和脱氢反应,生成
乙烯、丁烯、丁二烯、芳烃等。 例如环己烷裂解:
C6H12 C6H12
C2H4 + C4H8 C2H4 + C4H6+H2 C4H6 + C2H6 3/2C4H6 + 3/2H2
C6H6+3H2
7
(二)烃类裂解的二次反应
所谓二次反应是在裂解反应条件下,一次反应生成的烯 烃都可以继续反应,转化成新的产物。
裂解(乙烯)工艺简介
第一节 概述 第二节 烃类热裂解 第三节 烃类裂解工艺过程 第四节 裂解气的净化与分离
1
第一节 概述
石油化学工业的发展,促进了国民经济的巨大进步。乙烯、 丙烯、丁二烯(三烯)、苯、甲苯、二甲苯(三苯)等是石油 化工最基本的原料,是生产各种重要的有机化工产品的基础。 所以生产“三烯”、“三苯”的乙烯装置是石油化学工业的龙 头,它的生产规模、产量、和技术标志着一个国家石油化学工 业的发展水平。
24
3. 水蒸汽作为稀释剂的优点 (1)易于从裂解气中分离; (2)水蒸气热容大,使系统有较大“热惯性”,可
以稳定裂解温度,保护炉管; (3)可脱除炉管的部分结焦,延长运转周期; (4)减轻了炉管中铁和镍对烃类气体分解生碳的催
化作用; (5)可以抑制原料中的硫对合金钢管的腐蚀。
管式裂解炉及裂解部分工艺流程

管式裂解炉及裂解部分工艺流程裂解炉的工艺流程包括以下几个关键步骤:1. 加热和预热:原油首先经过预热换热器加热到裂解反应温度(通常在500-700摄氏度之间)。
这样可以降低原油的粘度,使得裂解反应更加容易进行。
2. 进料和裂解反应:加热后的原油进入裂解炉,在高温和催化剂的作用下,分子发生断裂,生成较小碳数的烃类化合物。
这里的催化剂通常是沸石、硅铝酸盐或金属氧化物等物质,能够促进裂解反应的进行。
3. 产物分离:裂解反应生成的产物包括汽油、石油醚、轻柴油和重柴油等。
这些产物会经过凝结器等设备进行冷却,并分离成不同碳数的化合物。
轻质产物通常会通过蒸馏分离,而较重的产物则会通过汽液分离等工艺进行分离。
整个裂解工艺流程需要精密的控制和监测,以确保裂解反应能够稳定进行,并且产物的质量符合要求。
此外,裂解炉还需要定期清理和更换催化剂,以保持裂解反应的高效性。
这些措施可以帮助提高炼油厂的产能和产物质量,满足市场需求。
裂解炉是炼油工业中非常重要的装备,其主要作用是将重质石油馏分(如燃料油)经过高温裂解成轻质石油产品(如汽油和润滑油),以提高炼油产品的产率和价值。
裂解炉通常分为管式裂解炉和流化床裂解炉两种类型,而管式裂解炉是其中常用的一种。
在管式裂解炉中,原油通过预热器预热后,进入到裂解炉内部的反应管道,沿着管道逐步加热,进入高温区进行裂解反应。
裂解反应主要发生在高温下、加热方式有内、外加热两种,通常使用的是外加热方式。
在高温和催化剂的作用下,大分子烃类会发生裂解、重排和重组,生成较小分子量的烃类产品。
这些裂解产物包括乙烯、丙烯、丁烷、丁烯等烃类物质,从而增加了汽油和润滑油产品的产量。
裂解炉内部的温度、压力和催化剂的选择都是影响裂解过程的关键因素。
例如,适当的温度可以促进分子的断裂和转化,而过高或过低的温度都会影响反应的进行。
催化剂的选择也会影响裂解反应的产物分布和产率。
在裂解炉操作过程中,需要实时监测和调整这些参数,以确保裂解反应的稳定进行和产物的质量。
乙烯生产工艺流程及设备认知 管式裂解炉

燃烧器
辐射段
SRT型管式裂解炉结构
炉管
对流管 管内物料被管外的高温烟道气以对流方式 进行加热并气化,达到裂解反应温度。
辐射管 热量经辐射管管壁传给物料,裂解反应在 该管内进行,故辐射管又称为反应管。
SRT型管式裂解炉结构
燃烧器(烧嘴)
作用:
提供管式炉所需的热量。
烧嘴因其所安装的位置不同分为底部 烧嘴和侧壁烧嘴。
目
CONTENTS
录
01 管式裂解炉的结构 02 管式裂解炉的传热方式 03 管式裂解炉的优缺点
01
管式裂解炉的结构
SRT型管式裂解炉结构
炉体 炉管
对流段(或称对流室) 辐射段(或称辐射室) 耐高温合金钢
燃料燃烧器
SRT型管式裂解炉结构
炉体
对流段
换热管
预热
对流段
辐射段
耐火砖(里层) 隔热砖(外层)
管式裂解炉的优缺点
缺点
重质原料的适应性还有一定限制; 原料利用不高; 燃料油消耗增加; 公用工程费大; 反应过程的结焦。
小
结
1.管式裂解炉的结构 2.管式裂解炉的传热方式 3.管式裂解炉的优缺点
裂解反应设备—— 管式裂解炉
烃类裂解装置
管式炉裂解工艺是目前较成熟的生产乙烯工艺技术。 管式炉炉型结构简单,操作容易,便于控制和能连
续生产,乙烯、丙烯收率较高,动力消耗少,热效 率高,裂解气和烟道气的余热大部分可以回收。
管式炉裂解技术的反应设 备是裂解炉,它既是乙烯 装置的核心,又是挖掘节 能潜力的关键设备。
02
管式裂解炉的传热方式
管式裂解炉的传热方式
辐射室中燃 料燃烧产生
的火焰
辐射
炉管的外 表面
乙烯生产方法选择—烃类热裂解制乙烯
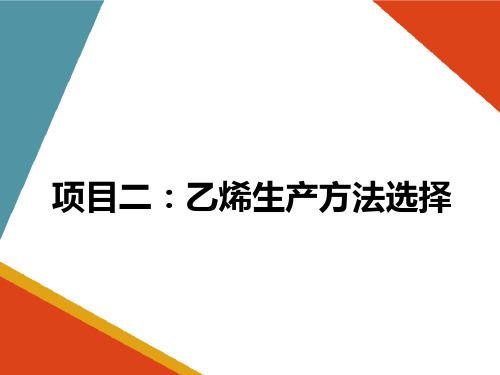
任务二 烃类热裂解制乙烯
1、原料加热及反应系统
由原料罐区来的石脑油等原料换热后,与DS (180℃, 0. 55MPa)按相应的油汽比混合进入裂解 炉对流段加热后进入辐射段。
物料在辐射段炉管内迅速升温进行裂解反应(以控 制辐射炉管出口温度COT的方式控制裂解深度, COT大约为800~900℃)。裂解气出口温度COT通 过调节每组炉管的烃进料量来控制,要求高于裂 解气的露点(裂解气中重组分的露点),若低于露点 温度,则裂解气中的较重组分有一部分会冷凝, 凝结的油雾黏附在急冷换热器管壁上形成流动缓 慢的油膜,既影响传热,又容易发生二次反应。
任务二 烃类热裂解制乙烯
4、水急冷和稀释水蒸气系统
油冷塔顶的裂解气,通过和水冷塔中的循环 急冷水进行直接接触进行冷却和部分冷凝, 温度冷却至28℃,水冷塔的塔顶裂解气被送 到裂解气压缩工段。
任务二 烃类热裂解制乙烯
4、水急冷和稀释水蒸气系统
急冷水和稀释水蒸气系统的生产目的是用水 将裂解气继续降温到40°C左右,将裂解气 中所含的稀释蒸汽冷凝下来,并将油洗时没 有冷凝下来的一部分轻质油也冷凝下来,同 时也可回收部分热量。稀释蒸汽发生器接收 工艺水,发生稀释蒸汽送往裂解炉管,作为 裂解炉进料的稀释蒸汽,降低原料裂解中烃 分压。
任务二 烃类热裂解制乙烯
二.世界乙烯原料情况
平均下来石脑油是最主要的,占了43%,排 第二名是乙烷占36%。但是具体到各国或地 区的情况却不同。欧洲、中国、日本一样主 要采用石脑油作原料。
任务二 烃类热裂解制乙烯
二.世界乙烯原料情况
典型的是西欧乙烯71%来自石脑油,来自轻 烃和LPG的各占11%仅7%来自乙烷。而美 国恰恰相反,主要使用乙烷作原料。它的乙 烯52%来自乙烷,22%来自轻烃5%来自石 脑油。
乙烯生产—管式炉裂解流程

• 目的:
• 提高分离操作温度,节约低温能量和材料。
• 除去部分水份和重质烃,减少后面干燥和低温的负担。
• 要求:
• P↑,设备材料要求增加,动力消耗也增加。
• P↑,精馏塔釜温↑,不饱和烃及重组分聚合
• P↑,α↓,分离困难。
∴生产中一般控制30~40atm。
• 采用多段压缩:
压缩升温时二烯烃、烯烃易聚合,∴为防止结焦,控制排气温度<100℃,采
侧壁烧嘴
管式裂解炉的炉型
( 二
1.鲁姆斯裂 解炉
)
管 式
2.凯洛格毫
裂
秒裂解炉
解
炉
的
炉 型
C裂解炉
SRT型裂解炉即短停留时间炉,是美国鲁姆
斯(Lummus)公司于1963年开发,1965
年工业化,以后又不断地改进了炉管的炉型
超伯的解选斯一温及裂缩的中司的超洛一下0解致.择特种度1炉解短收应,乙短(种,炉使秒性(炉和子炉停率用扬烯K停炉使。裂S毫(裂S型烃eR的,留,最子生留型物解秒lt5Tlo解,分o0结 该时 对 多 石 产时。料炉炉n型g~U炉 压e构炉间不的油装间1在结g由炉S19)简条&,型,同炉化置裂炉构0C7于是08公称件W裂先的改的型工均解管复毫年管目司e的U解后不善裂。公采炉内杂秒开径b前S在选技s推断裂解中司用简的,C)发较t世6e择术炉出改解原国和此称停投,0成小r界),年是。了进选料的齐种留资U所功,上公使S代根它,择有燕鲁裂S时相以所,R大R司生开据是是性较山石解间对T也需在T型在炉成始停美-为,大石油炉缩较称炉高乙7,的研留国Ⅰ了提的油化。短高为0管裂烯是产年究时斯~进高灵化工到。毫数解装美品代开间通Ⅵ一乙活工公因0秒量温置.国中开发、-0型步烯性公司裂裂多度5凯乙发的裂韦~。解, 烷等管副是产一品程较,少没,有乙弯烯头收,率阻较力高降而小命,名烃的分。压低,
管式裂解炉工艺流程

裂解炉是乙烯生产装置的重要设备,其能耗约占乙烯装置总能耗70~75%。
4.6 管式裂解炉工艺流程
2) 急冷换热器
换热方式、作用和任务
① 间接急冷换热 采用高压热水作为换热介质,与来自裂解炉出口的裂解气进行间接快速换热。 间接换热的优点:不影响产品的质量,可回收高品位热能。产生约10MPa的超 高压蒸汽,被送入蒸汽管网用于驱动后续流程中的压缩机等动 力设备。 裂解气经间接急冷换热后,温度降到约400~500℃(停留时间控制在小于0.04
预分馏系统
急冷换热器
终止二次反应 回收能量
裂解炉
辐射段
裂解反应
图4-14 SRT-I立式管式裂解炉工艺流程图
3. 管式炉工艺主要设备
裂解炉和急冷换热器是该工艺的重要且关键设备。
1)管式裂解炉及炉管的结构
管式裂解炉 是通过外部加热的管式反应器, 结构通常为立式厢式炉。由炉体和裂解炉管
裂解 原料
两部分组成。大部分裂解炉炉体外观相似。
裂解 炉体
急冷换热器
裂解气
裂解 原料
裂解 原料
裂解
东方化工厂裂解炉外观照片
炉管
(荷兰GK公司)
炉管形式(结构) 辐射段内炉管结构形式多样, 专利商根据原料特性、生产规模和乙烯收率等 设计并制造出结构、排布形式不同的炉管。 例如,图4-14-1是4组各8程的炉管。
图4-14-1 SRT-I立式管式 裂解炉及炉管图
结焦 是裂解炉和急冷换热器常遇到的问题,主要来源于二次反应。 危害 直接影响裂解炉的操作周期。
i) 使炉管出口压差增大; 炉内有过热现象发生,光亮点; 燃料量增大; 裂解气中乙烯含量降低 ii) 使急冷换热器出口温度升高,压降增大,系统压力增大影响裂解炉正 常运转,甚至不能终止二次反应。 清焦 清焦的方法比较简单。(略)
化工工艺学-第三章
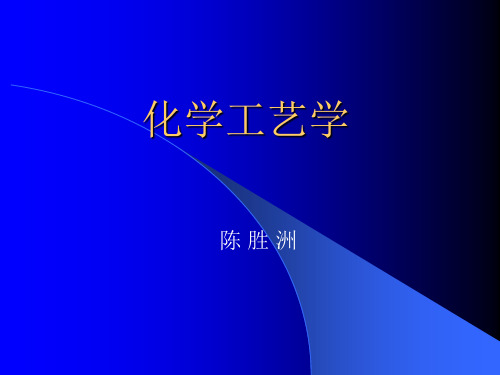
烃类裂解过程的一次反应
(1)烷烃热裂解 烷烃热裂解的一次反应主要有: ①脱氢反应:RCH2-CH3↔CH=CH2+H2 ②断链反应:RCH2-CH2-R′↔RCH=CH2+R′H 不同烷烃脱氢和断链的难易,可以从分子结构中键能 数值的大小来判断。 a 同碳数的烷烃,断链比脱氢容易; b烷烃的相对稳定性随碳链的增长而降低; c脱氢难易与烷烃的分子结构有关,叔氢最易脱去,仲 氢次之,伯氢最难;
辽化二级急冷技术 第一急冷锅炉:选用入口端带引射蒸汽的套管式换热器,特点是裂 解气第一急冷器直接与裂解炉辐射炉管出口Y型管道相接,由于裂 解气在第一急冷器中质量流速大,能在极短的时间内(大约30µ s), 把裂解气急冷至600℃以下,终止二次反应,保证烯烃收率; 第二急冷器:采用薄管板管壳式结构,管程走裂解气,由于第二急 冷器设计合理,即使在轻柴油裂解时也不至严重结焦。
乙醇胺法
当裂解气中含硫量较高时,用碱NaOH洗,碱液不能回收, 且耗碱量大,在这种情况下可采用乙醇胺法或其它吸收法。
特点:
再生吸收剂,循环使用; 可逆反应:温度低、压力高时反应向右进行,吸收酸性气体, 放热;当温度高、压力低时反应向左进行,吸热。 不宜处理含COS量较高的气体:醇胺与COS反应不能再生; 醇胺吸收剂在较高温度下易挥发和分解,循环使用能耗大; 醇胺吸收剂较贵。
烃类裂解过程的二次反应
(1)烯烃裂解 如大分子烯烃裂解为小分子烯烃
2)烯烃聚合、环化、缩合反应
(3)烯烃加氢和脱氢反应,如
(4)烯烃分解生碳反应,如
烃类裂解反应机理
(1)链引发:烷烃引发主要是断裂C—C键,而对C一H键的引发较小。 链引发反应的活化能较大,290~330KJ/mol范围。 (2)链的增长反应:自由基的分解反应和自由基的夺氢反应。分 解反应的活化能在120~178KJ/mol范围内,夺氢反应的活化能在 29 ~45KJ/mol的范围内。两种链传递反应的活化能都比链引发的活化 能小,而反应是生成烯烃的反应,能使小分子烯烃的收率增多,还 可提高裂解反应的转化率。 (3)链终止反应:自由基与自由基结合成分子的反应。
烃类管式炉裂解制乙稀-第一章 烃类热裂解
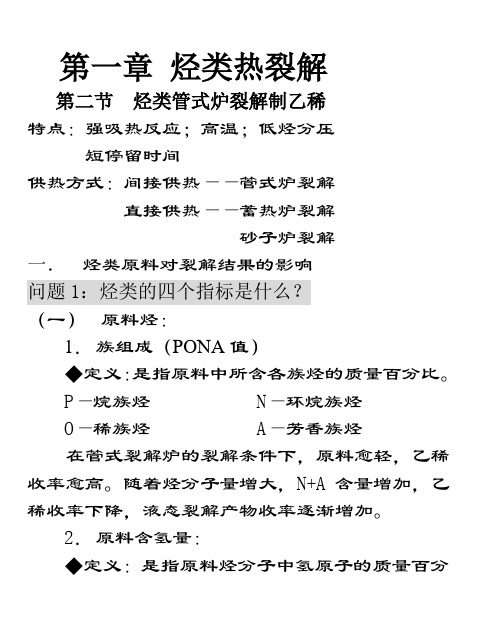
第一章烃类热裂解第二节烃类管式炉裂解制乙稀特点:强吸热反应;高温;低烃分压短停留时间供热方式:间接供热——管式炉裂解直接供热——蓄热炉裂解砂子炉裂解一.烃类原料对裂解结果的影响问题1:烃类的四个指标是什么?(一)原料烃:1.族组成(PONA值)◆定义:是指原料中所含各族烃的质量百分比。
P—烷族烃 N—环烷族烃O—稀族烃 A—芳香族烃在管式裂解炉的裂解条件下,原料愈轻,乙稀收率愈高。
随着烃分子量增大,N+A含量增加,乙稀收率下降,液态裂解产物收率逐渐增加。
2.原料含氢量:◆定义:是指原料烃分子中氢原子的质量百分比;不包含溶解的H2。
相同碳原子时,含氢量:烷烃> 环烷烃> 芳烃含氢量高的原料,裂解深度可深一些,产物中乙稀收率也高。
表1-9各种烃和焦的含氢量对重质烃的裂解,按目前技术水平,原料含氢量控制在大于13%(质量),气态产物的含氢量控制在18%(质量),液态产物含氢量控制在稍高于7~8%(质量)为宜。
因为液态产物含氢量低于7~8%(质量)时,就易结焦,堵塞炉管和急冷换热设备。
3.芳烃指数(BMCI):◆定义:BMCI=48640/Tv+473.7*d—456.8Tv=(T10+T30+T50+T70+T90)/5基准:n—C6H14的BMCI=0的BMCI=100当BMCI<35时,才能做裂解原料。
4.特性因子K:K=1.216(T立/d15.6度)^(1/3)T立=[0.1t10^(1/3)+0.2t30^(1/3)+0.2t50^(1/3)+0.2t70^(1/3)+0.2t90^(1/3)+0.1t100^(1/3)]^3小结:原料烃参数对裂解结果的影响:(1)当PONA增大,乙烯收率增大;(2)当氢含量增大,乙烯收率增大;(3)当BMCI减小,乙烯收率增大;(4)当K增大,乙烯收率增大。
几种原料裂解结果比较可知,原料不同,裂解产物组成不同,裂解条件不同。
表1-12生产1吨乙烯所需原料及连副产物量*B、T、X为苯、甲苯、二甲苯。
3.3管式裂解炉及裂解工艺过程

反应管材料
过去,一般采用主 要成分为含镍20%、 铬25%的HK-40合 金钢作为裂解反应 管材料 。 70年代以后又改用 含镍35%、铬25% 的HP-40合金钢, 用离心浇铸法制成, 内部经机械加工平 整以减少反应过程 的结焦。
裂解炉炉型
▪ 目前国际上应用较广的管式裂解炉有: ▪ 短停留时间炉(SRT型炉) ▪ 超选择性炉(USC型炉) ▪ Linde-Selas炉(LSCC) ▪ 超短停留时间炉。(USRT炉)
简介
• 早期的管式裂解炉是沿用石油炼制工业的加热 炉的结构采用横置裂解炉管的方箱炉。反应管 放置在靠墙内壁处,采用长火焰烧嘴加热,炉 管表面热强度低。
• 20世纪50年代,炉管位置由墙壁处移至辐射室 中央,并采用短焰侧壁烧嘴加热,提高了炉管 表面热强度和受热均匀性。
• 20世纪60年代,反应管开始由横置式改为直立 吊装式。采用单排管双面辐射加热和多排短焰 侧壁烧嘴,提高了反应的径向和轴向温度分布 的均匀性。
3.3.3.2 SRT型裂解炉的优化及改进措施
热裂解的工艺方法改进的目标
提高设备生产能力 获得最大的乙烯产率 付出最少的能量
提高反应温度 缩短停留时间 降低烃分压
▪ 不同辐射盘管裂解工艺性能 ▪ 不同SRT炉型的裂解产品收率 ▪ 变径管分析 ▪ 不变径与变径反应管的比较
3.3.1.3 其它管式裂解炉
3.3.1 管式裂解炉
60年代初期 SRT-Ⅰ型炉
双辐射立管 实现了高温、短停留时间
60年代中期 SRT-Ⅱ型炉
分叉变径炉管 降低烃分压
70年代中期 SRT-Ⅲ型炉
材质 炉内管排增加 提高热强度 提高生产能力
80年代
SRT-Ⅳ、Ⅴ、Ⅵ型炉
管式裂解炉及其工艺流程介绍

管式裂解炉及其工艺流程管式裂解炉是用于烃类裂解制乙烯及其联产品的一种生产设备,为目前世界上大型石油化工厂所普遍采用。
组成管式裂解炉是在炉管内进行烃类裂解反应的设备。
主要由辐射室(炉膛)、对流室、烟囱和供给热源的喷嘴组成。
燃料油从喷嘴喷到炉膛内燃烧,生成的烟气流经对流室后从烟囱排出。
辐射室、对流室内均装有炉管,原料油在炉管内加热到所需温度进行裂解反应生成裂解气(烯烃),裂解气经急冷后进入分离装置。
炉管选用合金钢浇铸管。
由于温度和流速对炉管内裂解反应产品有重大的影响,因而要求严格控制炉管长度方向的温度分布及产品在炉管内的停留时间,对炉型选择、喷嘴及炉管的布置都有特别的要求。
发展早期的管式裂解炉是沿用石油炼制工业的加热炉的结构采用横置裂解炉管的方箱炉。
反应管放置在靠墙内壁处,采用长火焰烧嘴加热,炉管表面热强度低,约为85~125MJ/(mh)。
20世纪50年代,裂解炉结构有较大改进,炉管位置由墙壁处移至辐射室中央,并采用短焰侧壁烧嘴加热,提高了炉管表面热强度和受热均匀性。
热强度可达210MJ/(mh)。
至60年代,反应管开始由横置式改为直立吊装式,这是管式炉的一次重大技术改进。
它采用单排管双面辐射加热,进一步把炉管表面热强度提高到约250MJ/(mh),并采用多排短焰侧壁烧嘴,以提高反应的径向和轴向温度分布的均匀性。
美国鲁姆斯公司短停留时间裂解炉(简称SRT炉)是初期立管式裂解炉的典型装置。
现在世界上大型乙烯装置多采用立式裂解反应管。
种类早年使用裂解管水平布置的方箱式炉,由于热强度低,裂解管受热弯曲,耐热吊装件安装不易,维修预留地大等原因,已被淘汰。
由于裂解管布置方式和烧嘴安装位置及燃烧方式的不同,管式炉的炉型有多种。
管式裂解炉种类较多,按炉型分为方箱炉、立式炉、梯台炉等;按炉管布置方式分为横管式和竖管式裂解炉;按燃烧方式分为直焰式和无焰辐射式裂解炉等。
近年各国竞相发展垂直管双面辐射管式裂解炉,炉型各具特色,其中美国炉姆斯公司开发的短停留时间裂解炉采用的国家较多。
烃类管式炉裂解制乙稀-第一章 烃类热裂解
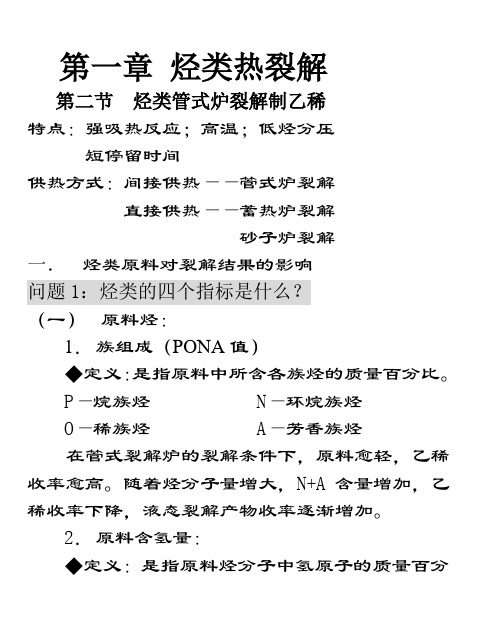
第一章烃类热裂解第二节烃类管式炉裂解制乙稀特点:强吸热反应;高温;低烃分压短停留时间供热方式:间接供热——管式炉裂解直接供热——蓄热炉裂解砂子炉裂解一.烃类原料对裂解结果的影响问题1:烃类的四个指标是什么?(一)原料烃:1.族组成(PONA值)◆定义:是指原料中所含各族烃的质量百分比。
P—烷族烃 N—环烷族烃O—稀族烃 A—芳香族烃在管式裂解炉的裂解条件下,原料愈轻,乙稀收率愈高。
随着烃分子量增大,N+A含量增加,乙稀收率下降,液态裂解产物收率逐渐增加。
2.原料含氢量:◆定义:是指原料烃分子中氢原子的质量百分比;不包含溶解的H2。
相同碳原子时,含氢量:烷烃> 环烷烃> 芳烃含氢量高的原料,裂解深度可深一些,产物中乙稀收率也高。
表1-9各种烃和焦的含氢量对重质烃的裂解,按目前技术水平,原料含氢量控制在大于13%(质量),气态产物的含氢量控制在18%(质量),液态产物含氢量控制在稍高于7~8%(质量)为宜。
因为液态产物含氢量低于7~8%(质量)时,就易结焦,堵塞炉管和急冷换热设备。
3.芳烃指数(BMCI):◆定义:BMCI=48640/Tv+473.7*d—456.8Tv=(T10+T30+T50+T70+T90)/5基准:n—C6H14的BMCI=0的BMCI=100当BMCI<35时,才能做裂解原料。
4.特性因子K:K=1.216(T立/d15.6度)^(1/3)T立=[0.1t10^(1/3)+0.2t30^(1/3)+0.2t50^(1/3)+0.2t70^(1/3)+0.2t90^(1/3)+0.1t100^(1/3)]^3小结:原料烃参数对裂解结果的影响:(1)当PONA增大,乙烯收率增大;(2)当氢含量增大,乙烯收率增大;(3)当BMCI减小,乙烯收率增大;(4)当K增大,乙烯收率增大。
几种原料裂解结果比较可知,原料不同,裂解产物组成不同,裂解条件不同。
表1-12生产1吨乙烯所需原料及连副产物量*B、T、X为苯、甲苯、二甲苯。
乙烯的生产—管式炉裂解工艺流程的组织

四、结焦与清焦
裂解炉和急冷锅炉的清焦方法:
①停炉清焦法 是将进料及出口裂解气切断(离线)后,将裂解炉和 急冷锅炉停车拆开,分别进行除焦,用惰性气体和水蒸汽清扫管线, 逐渐降低炉温,然后通入空气和水蒸汽烧焦。(周期较长,操作繁琐) ②在线清焦法 不停炉清焦是一个改进。它有交替裂解法、水蒸汽法、 空气清焦法等(周期短,节能) ③其它方法:加入助剂,起到抑制作用。 在裂解炉进行清焦操作时,废热锅炉均在一定程度上可以清理部分 焦垢,管内焦炭不能完全用燃烧方法清除,所以一般需要在裂解炉 1~2次清焦周期内对废热锅炉进行水力清焦或机械清焦。
设置原则:一般先间接急冷,即裂解产物先进急冷换热器, 后直接急冷,即油洗和水洗来降温。
三、急冷换热器
裂解装置五大关键设备之一
1、急冷要求(设备作用)
快速降温终止裂解反应,即在极短时间(0.01~0.1s内)骤 降到露点温度附近,传热强度约达418.7MJ/m2h左右。操作 苛刻。(在一定压力下判断:
烧焦过程主要反应为: C+O2→CO2 C+H2O→CO+H2 CO+H2O→CO2+H2
检测出口尾气中CO2 <0.2%,可以认为在此温度 下清焦基本结束。
2、急冷的方式 ②间接急冷 急冷废热锅炉(急冷换热器(常以TLE或TLX表示)与汽 包构成的发生蒸汽系统) 用换热器回收大量的热量,冷却介质用高压热水。
二、急冷的目的和方式
2、急冷的方式 ③急冷方式比较
直接急冷 设备费用少 ; 操作简单 传热效果好 产生大量含油污水,难分离 不能回收高品位的热能
间接急冷 回收高品位的热能 不如直接方式中冷热物流接触空间大 无污水 能量利用合理 结焦比较严重
裂解炉有哪几部分组成? 炉体(对流室、辐射室),炉管,燃烧器。
精选管式裂解炉及裂解部分工艺流程课件

解决办法
提高压力
实现
压缩机
绝热过程
95页图3-26
问题2:为什么要多级压缩?
①节约压缩功耗
压缩段数越多
越接近等温压缩
②降低出口温度
控制压缩后温度≦100℃。(聚合)
③段间净化分离
水、
C3及C3以上重组分
减少负荷,节省冷量。
T2=T1(P1/P2)(-1)/
绝热指数:
油水分离器
裂解汽油
水
冷却器
稀释蒸汽发生器
冷却器
管式裂解法的优缺点
历史:
油品加热炉
油品热裂化炉
油品裂解炉
多年历史的成熟工艺
优点:
①炉型结构简单;
②操作容易;
③便于控制;
④能连续生产;
⑤乙烯、丙烯收率高;
⑥产物浓度高;
⑦动力消耗小,
⑧热效率高;
⑨原料的使用范围日渐扩大;
⑩多台组合大型化。
缺点:
①重质原料的适应性还有一定限制;
5、腐蚀性小;
6、来源丰富
(2)吸收剂
NaOH溶液、
乙醇胺、
N-甲基吡咯烷酮
√
选择依据:
①酸性气体含量多少
②净化程度要求
③酸性气体是否回收
(3)反应原理自学89页图3-20
(4)碱洗法流程
①2~3%
②5~7%
③18~20%
④水
(5)操作条件
压力:1·0MPa;
塔内温度:40℃;
浓度:30% NaOH
3、不饱和烃
①原料所带
②反应生成
主要存在于C2馏分和C3馏分
四、措施
方法和对应流程
③处理过程引入
《有机化工生产工艺》 学案 第二章

第二章乙烯工业——烃类热裂解本章学习要求了解烃类裂解的一次反响和二次反响以及其对乙烯收率影响;熟悉管式炉裂解的生产工艺流程并掌握各个工艺参数和原料性质对乙烯收率的影响;熟悉不同深冷别离流程并掌握裂解气的各种净化方法、原理和工艺条件;了解生产中的异常现象和节能措施。
1.何谓烃类热裂解?2.查资料了解乙烯的其它生产方法及未来世界乙烯工业开展趋势。
第一节烃类管式炉裂解生产乙稀工业上烃类热裂解制乙烯,虽然各生产装置所用原料和生产技术有所差异,相应的工艺流程也不完全相同,但均包括和两个重要局部。
一、管式炉裂解工艺流程1.裂解工艺流程包括系统,系统、系统以及系统。
2.画出轻柴油裂解主物料流的工艺流程方框示意图。
二、烃类热裂解过程中的化学反响1.什么叫烃类热裂解过程的一次反响和二次反响?它们对烃类热裂解过程有何影响?2.烃类热裂解的一次反响主要有哪几个?烃类热裂解的二次反响主要有哪几个?3.简述各族烃热裂解一次反响规律。
理想的裂解原料是何样的?4.什么叫焦,什么叫碳?结焦与生碳的区别有哪些?第二节管式裂解炉和烃类裂解的操作条件一、管式裂解炉1.管式裂解炉〔1〕管式裂解炉主要由和两大局部组成。
用钢构体和耐火材料砌筑,分为对流室和辐射室。
安装在对流室内,布置在辐射室内,在辐射室的炉侧壁和炉顶或炉底安装了一定数量的烧嘴〔燃料喷嘴、火嘴等〕。
〔2〕由于和及的不同,管式炉的炉型有多种。
2.裂解炉的结焦与清焦〔1〕裂解炉的结焦的表现有哪些?〔2〕裂解炉为什么要清焦?如何清焦?〔3〕查资料了解目前我国采用的清焦方法有哪几种?二、裂解气急冷与急冷换热器1.裂解气急冷的目的是什么?它具有什么意义?2.急冷的方法的哪两种?对这两种急冷方法进行比拟。
3.对急冷换热器的结构要求是什么?4.防止急冷换热器结焦应控制哪些指标?三、烃类裂解的操作条件1.衡量裂解结果的指标有哪些?2.影响化学反响速度和化学平衡的因素有哪些?在生产实际中为提高产品的收率应如何做?3.烃类热裂解反响的特点是什么?4.分析温度对裂解反响的影响,并确定适宜的温度。
乙烯裂解工艺流程

裂解气至压缩、分离装遥2因1 管式炉裂解工艺況程1裂解炉对流室2裂解炉辐射室3感冷锅炉4汽包5息冷器6、7分馆塔裂解原料烟公气铝炉绐水图2乙烯裂解炉示意图I高压棊汽卜 裂解气COT 燃科裂解炉结构图I ••艺流程为,稀禅蒸汽i 次注入裂解原料,裂解原斛经对流段预热后再与对流段中过热的稀釋蒸汽混合•注入稀释裁汽后的裂解原料油耳经对流段预热至物料衡跨温 度后送入辐射盘管.庄辐射段,管内物料迅速升温,同时进行原料的裂解反应,生成 乙晞、丙烯、丁二烟、甲烷、乙烷等众多组分的裂解气。
在裂解炉的出口处设有急冷 锅炉对裂解炉进行急冷,以抑制裂解气二次反应的发生。
急冷锅炉出口的幾解气经过 进一步冷却后进入下一道生产工序进行压缩和分离。
裂解炉工艺流程裂解原料通过流星控制送到裂解炉每组炉符,在裂解炉对流段彊上层盘管内进行 预热,然后由流量仪表控制喷入未经过过热的一次稀释蒸汽.混合后一起进入到 上部预热段,进一步预热后再喷入经对流段过热的二次稀释蒸汽,一起进入到喷 咀混合器,原料在喷咀混合器中全部汽化,使其温度升高至稍低于裂解及应的温 度,然后进入裂解炉的高温区——辐射盘管,在反应管内的炷类原料迅速升温, 同时发生产生乙烯、丙烯、丁二烯、甲烷、乙烷等联产品的裂紡反应。
六组辐射 盘管的流出物(裂解气)在燃烧室外成对合并,进入三台废热锅炉.三台废热锅炉共 用一个汽包.然后裂解气通过注入激冷油被进一步激冷后送入汽油分饴塔.雄科油IRHirtW4S 怙衣M 炉册M-K»l|\\ \AAAVV \M N夕・\、•#1*裂解炉的对流段,设有预热炷类原料、锅炉给水、过热稀释蒸汽等一系列的加热器,以满足工艺的需要和回收热量。
图中,1・辐射室2.对流室 3 ■急冷锅炉4.引风机 5 •底部燃烧器6 •侧壁燃烧器7 •进口管 &岀口管9 .高温横跨管该裂解炉包括:辐射室1,设在辎射室上方的对流室2、设在辐射室1上方并与出口管8相连的急冷锅炉3、引风机4、垂直布置在辐射室1内的辐射炉管及安装在辐射室1侧壁的侧壁燃烧器6及布置在辐射室1底部旳底部燃烧器5o本实用新型的工作过程如下:使用本实用新塑时*原料首先在对流室2中进行预热I然后进入辐射室】内的2T或1-1型珞射炉管,在辐射炉管内发主裂解反应,产生的裂解气进入急冷锅炉3,裂解气被冷却到要求的温度,裂解反应所需耍的热量由底部燃烧器5及侧壁燃烧器6提供,燃料在辐射室1内撚烧后产生的烟气进入对流室,烟气的余热在对流室2中通过预热原料及锅炉给水等物料被进一步地回收.烟气通过引颯机4排入大气°(-)製歸和急妙从耀区來的滾休原料经总冷水预ftJSitt人袭解炉,见ffl 1-16.備坏乙烷在深冷系统中cT 1 - 16製解加魚挣祁井朮盘图i-s*炉;2—直旅抚因I —务拎术坏;—祐邀用劇用螯製解削奏盂.在冷箱巾用丙帰冷剂再加热,然宕与新鮮乙烷除御幌令°原料存琲人裂酢炉前用急冷水预热、热水加梢,再在对流段fi±*盘管中预符,加人(乙烷与稀释嫌汽虜耳比为6萄、井注人微最以防炉營管壁催化效应和炉管澹熱对于Cf蒸汽在濒議控制下,加现想的裂解炉进料申左4泾与最汕的混仟物再返回对克段,在进入輻射段之前进1步预热°四组辐射證炉管出口在护嵋内两组相连后,进劃毎台裂解炉的两台急冷爾炉(TLE)中*每台裂解炉的TLE,均连接到一个共用汽包上的热虹吸系统。
烃类裂解设备与工艺

烃类裂解设备与工艺(一) 管式裂解炉管式裂解炉主要由炉体和裂解管两大部分组成。
炉体用钢构体和耐火材料砌筑,分为对流室和辐射室.原料预热管及蒸汽加热管安装在对流室内,裂解管布置在辐射室内。
在辐射室的炉侧壁和炉顶或炉底安装了一定数量的烧嘴(燃料喷嘴、火嘴等)。
由于裂解管布置方式和烧嘴安装位置及燃烧方式的不同,管式炉的炉型有多种。
早年使用裂解管水平布置的方箱式炉,由于热强度低,裂解管受热弯曲,耐热吊装件安装不易,维修预留地大等原因,已被淘汰。
近年各国竞相发展垂直管双面辐射管式裂解炉,炉型各具特色,其中美国炉姆斯公司开发的短停留时间裂解炉采用的国家较多。
1. 鲁姆斯SRT—Ⅲ型炉(Lummus Short Residence Time—Ⅲ Type )SRT型炉,即短停留时间裂解炉,是60年代开发的,最先为SRT—Ⅰ型,后为SRT—Ⅱ型。
近来发展到SRT—Ⅲ、SRT —Ⅳ、SRT—V、SRT—VI型等。
SRT各型裂解炉外形大体相同,而裂解炉的管径及排布方法则不相同:Ⅰ型为均径管,Ⅱ、Ⅲ、Ⅳ型为变径管。
炉型示意图见图1-10,SRT—Ⅰ、Ⅱ、Ⅲ型工艺特性见表1-18。
从炉型和炉管工艺特性的变化,可以看到裂解技术的进步:1) 实现了高温、短停留时间、低烃分压的原理为了在短停留时间内使原料能迅速升到高温进行裂解反应,必须有高热强度的辐射炉管,因此采用双面辐射的单排管,能最大限度的接收辐射热量。
最初使用的SRT-I型裂解炉,炉管是均径的。
采用均径炉管的主要缺点:①反应初期通热量小;②采用均径炉管不适用于体积增大的反应(后部阻力大,烃分压大);③停留时间长,有利于二次反应,乙烯收率降低;④容易结焦,操作周期缩短。
SRT—Ⅱ型炉采用变径炉管,克服了上述缺点。
管径排列为4-2-1-1-1-1,管径先细后粗。
小管径有利于强化传热(传热面积增大),使原料迅速升温,缩短停留时间。
管裂后部管径变粗,有利于减少△P,降低烃分压,减少二次反应的发生,二次反应的焦量也减少,不会很块阻塞管道和炉管,因而延长操作周期,提高乙烯收率。
管式裂解炉及裂解部分工艺流程

管式裂解炉及裂解部分工艺流程引言管式裂解炉是炼油行业中常见的一种设备,用于将原油或其他石油产品进行热分解,以获得更有价值的产品。
本文将介绍管式裂解炉的基本原理和工艺流程。
管式裂解炉的基本原理管式裂解炉是通过将原油或其他石油产品加热至高温,并在催化剂的作用下,将长链分子分解为短链分子的过程。
该过程中产生的短链分子可用于制备汽油、柴油、润滑油等产品。
管式裂解炉通常由加热炉、催化剂床、蒸发器和冷凝器等部分组成。
其中,加热炉用于将原油加热至裂解温度,催化剂床用于裂解原油,蒸发器用于将裂解产物中的液体成分蒸发,冷凝器用于将蒸发后的气体冷凝为液体。
裂解部分工艺流程管式裂解炉的裂解部分工艺流程一般包括以下几个步骤:1. 原油预热原油从储罐中提取后,经过暖交换器预热至适宜的温度。
预热有助于提高裂解效率,并减少能源消耗。
2. 催化剂床预热后的原油进入催化剂床,与催化剂接触。
催化剂通常是由酸性氧化物和活性金属组成,能够催化热分解反应。
在催化剂的作用下,长链分子被裂解为短链分子。
3. 裂解产物分离裂解产物由裂解床出口进入分离装置,分离装置通常包括快速冷凝器和减压闪蒸器。
快速冷凝器用于将裂解床出口的气体迅速冷却,使其转化为液体。
减压闪蒸器用于降低液体的压力,从而使其能够闪蒸,进一步分离出液体和气体。
4. 液体处理分离后的液体通常需要经过一系列处理步骤,以获得所需产品。
这些处理步骤可能包括脱酸、脱硫、降磷等操作,以提高产品的质量。
5. 气体回收裂解部分产生的气体通常包含大量的炭氢化合物,可用于再加工。
气体通常经过凝结和压缩等处理后,用于生产液化石油气(LPG)、石化原料等。
结论管式裂解炉是炼油行业中重要的设备之一,通过热裂解原油或其他石油产品,可以获得更有价值的短链分子。
裂解部分工艺流程包括原油预热、催化剂床、裂解产物分离、液体处理和气体回收等步骤。
通过合理控制裂解温度、催化剂选择以及后续处理操作,可以获得高质量的石化产品。
- 1、下载文档前请自行甄别文档内容的完整性,平台不提供额外的编辑、内容补充、找答案等附加服务。
- 2、"仅部分预览"的文档,不可在线预览部分如存在完整性等问题,可反馈申请退款(可完整预览的文档不适用该条件!)。
- 3、如文档侵犯您的权益,请联系客服反馈,我们会尽快为您处理(人工客服工作时间:9:00-18:30)。
流程:①
②
③
④
2、裂解和高压蒸气系统 设备: ①裂解炉对流段 ②裂解炉辐射段 ③急冷换热器 ④油洗塔
反应 分离准备
高压蒸气流程:
蒸汽包 11MPa,447℃
①
③
①
入管网
3、急冷油和燃料油系统 急冷油设备: 油急冷器:
分离
塔顶为氢、气态烃、裂解汽油、 油洗塔: 稀释蒸汽和酸性气体。 裂解轻柴油汽提塔: 燃料油汽提塔: 问题: 急冷油系统结焦 指标:
4、急冷水和稀释水蒸气系统
设备:
水冷塔: 分离槽: 换热器: 污水:120 7~8吨 工艺水汽提塔: 水蒸气循环好处: ①节约了新鲜的锅炉给水
指标: 釜水中含油100ppm
缓蚀剂
②减少了污水的排放量
裂解部分原则工艺流程
轻柴油裂解装置原则工艺流程图 轻柴油 裂解气 水 洗 塔 油 洗 塔 储罐 泵 预热 急冷器 裂 解 炉 换热器
% ,mol 成分
13.1828
% ,mol 成分 % ,mol
C3H8 0.3558
1,3丁二烯
C2H4 29.0363
0 . 1751 21.2489
0 . 3688
C2H6
丙二烯+丙炔
7.7953 0.5419 11.4757
2. 4194
2. 7085
异丁烯 正丁烷
C2H2
C3H6
0.0754
表面热处理后形成涂层。
已经成熟投产。
②使用结焦抑制剂(FSI)
Forest Star International 实验证明: 两次清焦运行期增加3倍, 由原来每45天清焦一次的100小时 135天费时2~4小时。
任务:
1、开发耐高温的裂解管材
2、寻找耐高温、高选择性催化剂
轻柴油裂解气组成
成分
H2 CO CH4
溶剂吸收分离甲烷
无需脱甲烷塔、低温甲烷、乙烯制冷系统
对原有的油吸收进行改进: A:加氢和前脱丙烷结合起来;
B:先除去C4及C4+馏分; C:再进入油吸收脱甲烷系统; D:最后从甲烷和轻质组分中分离C2以上组分。
②膜分离技术 1994Kellogg公司提出用于乙烯裂解。 中空纤维分离出部分氢,
减少乙烯制冷的负荷。
轻柴油裂解气组成(续)
成分 % ,mol 成分 % ,mol 成分 C9~ 200℃ CO2 % ,mol
C5
0 .5147
甲苯 0 .9296 C8 苯乙烯
0.3578
0.2397
C6~ C8 0 .6941 非芳烃 苯
2.1398
0 .0578
0 .2192
硫化物 0.0272
H2O:
5. 04 %
①炉型结构简单; ②操作容易; ⑧热效率高; ③便于控制; ⑩多台组合大型化。 ④能连续生产; ⑤乙烯、丙烯收率高;
⑥产物浓度高; ⑦动力消耗小,
缺点:
①重质原料的适应性还有一定限制;
降低裂解深度
结焦问题
原料利用不高、燃料油增加、 公用工程费大等 ②满足裂解原理
继续研究
耐合金刚 ③急冷器 ④油冷塔 ⑤水冷塔 ⑥沉降槽
√ √
2、各设备所起的作用
3、主要操作条件
155℃; 180℃水蒸气、 540℃、800℃、 τ=0.5s; 450℃~550℃; 185℃急冷油、230℃、N=23、 109℃裂解汽油、裂解气和水蒸气; 冷却水37℃、N=16、40℃、80℃、裂解气; 裂解汽油、水。
4、目的产物
裂解气
5、副产物
裂解汽油 裂解燃料油
3.3管式裂解炉及裂解部分工艺流程
1、原料油供给和预热系统
2、裂解和高压蒸气系统
3、急冷油和燃料油系统
4、急冷水和稀释水蒸气系统
1、原料油供给和预热系统
设备:
①原料油储罐 ②原料油泵 ③原料油急冷水预热器
④原料油急冷油预热器
准备
去 裂 解 炉 对 流 段
汽油
油水 分离罐
燃料油
汽 提 塔
水
馏分油裂解装置裂解气预分馏过程流程图(86)
裂解汽油
原料
裂 解 炉
废热锅炉
急 冷 器
油 洗 塔
水 洗 塔
裂解气
冷却器
稀释蒸汽 发生器
冷却器
油水分离器
水
管式裂解法的优缺点
历史: 油品加热炉 油品热裂化炉 油品裂解炉
多年历史的成熟工艺
优点:
⑨原料的使用范围日渐扩大;
50℃以下的运动粘度:
4· 5~5· 0×10-5m2/s
措施:急冷油系统设过滤网
急冷方式: 水直接急冷
直接急冷
间接急冷
油直接急冷
急冷方式的比较: 直接急冷: 设备费少、 操作简单、 系统阻力小、 传热效果好、大量污水、 油水分离困难、
难以回收能量。
√ 间接急冷: 能量利用合理、 无污水产生。
经济性好、
规模
20
30
45
60
80~90
(二)生产新技术的研究开发 1、KBR和埃克森
Kellogg Brown & Root
提高收率、 提高选择性、降低投资、 原料适应性相对较强。 100万吨乙烯生产厂的裂解炉: 9~10个 5 ~ 6个
2、新的工艺技术 ①ALCET技术 低投资乙烯技术 Brown&Root 新建和扩建均有利。
目标: ①扩大重质原料的应用 和裂解炉对原料改变的适应能力; ②减小能耗、降低成本; ③新的裂解技术研究 采用燃气透平、提高炉子热效率
乙烯工业的发展趋势
(一)乙烯建设规模继续向大型化发展 800、 900、 1000、 1200 单炉产量:
年代 60
90、 120、 140
70 80 90 21世纪
提高生产能力。
裂解汽油的选择性或全部加氢。 ③催化精馏加氢技术 Lummus公司提出 加氢和产物分离 同一个精馏塔 精馏段:
全部或部分被含有催化剂的填料代替。 用途:
①C3馏分选择性加氢; ②C4馏分选择性或全部加氢; ③C4和C5混合馏分全加氢。
3、抑制裂解炉结焦技术 ①使用涂覆技术降低炉管结焦
3.4裂解气的净化
§3· 4· 1裂解气的净化 一、有害物质 1、酸性气体 H2S、 CO2和CO、 少量有机物
18%~20%
水洗
5%~7%
2%~3%
2、H2O H 2O 操作条件下结冰
CH4 C 2H C 6 3H8
与低碳原子烷烃形成水合物 6H2O 7H2O 8H2O
裂解单元原则流程图
450℃~550℃
155℃
急冷器
800℃
185℃急冷油 N=23
原料
预热器
裂解气去压缩 40℃
裂 540℃ 油 解 冷 180℃ τ=0.5s 炉 塔 水蒸气
冷却水37℃
230℃
裂解汽油 沉降槽
水 冷 塔
80℃
裂解燃料油
N=16 109℃裂解汽油、裂解气 和水蒸气入底部
水
裂解单元原则流程图