压力容器工艺工序过程卡
压力容器工艺过程流转卡

件号
第
3
页
1
共 13
页
控制 标记
序 号
工序
工艺内容及技术要求
R
1
核查
看 清
有裂纹、凹凸、分层、表面无锈蚀。检验员签字确认后划线下料
2
划线
毛 坯 标
W
3 4 5
检验 定位
记 检 验 对
焊 焊接
拼 对 拼 笔
标
φ
划
2
线
1±1㎜ 错边量
W
6 7
检验
检 验 委
托
H
8
检验
1 )
内表面形状偏差:外凸≤1.25% Di 即≤ 25.00 mm
坡口表面不得有裂纹、分层、夹渣等缺陷,清理坡口两侧不小于20㎜范围内污物,打磨见金属光
泽。
6 滚圆 按要求对钢板进行卷筒制作,要求筒节内径Φ444mm。
7
定位 焊
对卷筒完毕后的件进行定位焊,焊道长度10~20mm,间隔50mm,要求错边量b≤3mm,对接间隙
1±1㎜;
W
8
焊接
对筒节的纵焊缝分别进行焊接,清除焊接熔渣及飞溅物,焊接参数见对应的焊接工艺卡,焊接完 成后,
进行标识移植。
W 4 检验 按图纸及工艺检查下料几何尺寸。
W 5 坡口 进行坡口加工,要求按图加工单边V型坡口,坡口角度35°±2°,钝边高度:1±1mm。 坡口表面不得有裂纹、分层、夹渣等缺陷,清理坡口两侧不小于20㎜范围内污物,打磨见金属光 泽。
6 卷制 按要求对钢板进行卷筒制作,要求卷制零件内径Φ2036mm。
文件编号:ZB2005
产品编号 R20-01
管口位置 共
压力容器焊接工艺设计装配卡

(2)埋弧自动焊焊接上瓶体和下瓶体。
焊接车间
采用手弧焊和单丝埋弧弧焊、焊接材料及各种必要的量具
3
钳
矫正焊后变形,打磨掉氧化层,去毛刺、打件号。
钳工车间
4
热处理
执行再结晶退火、正火等处理。
热处理车间
设计(日期)
审核(日期)
标准化(日期)
会签(日期)
标期
压力容器装配工艺过程卡片
产品型号
零件图号
A3
产品名称
压力容器
零件名称
压力容器
共1页
第1页
工序号
工序名称
工序内容
装配部门
设备及工艺装备
辅助材料
工时定额(min)
1
备料
备齐各件,并检查各件尺寸。
备料车间
切割机、冲压机、各种必要的量具
2
分焊
将分部件按图样要求尺寸进行点焊接固定好,并焊接。(防上变形过大及氧化过严重)
标记
处数
更改文件号
签字
日期
压力容器制造工艺流程图

检验员
电焊工
检验员
电焊工、抛光工
检验员
压力试验责任人耐压试验A类项目
确认通知书
试压员、检验员耐压试验检验记录卡
压力试验责
成品入库清单
[此文档可自行编辑修改,如有侵权请告知删除,感谢您的支持,我们会努力把内容做得更好]
压力容器制造工艺流程图
责任部门流程图相关说明使用表单
材料责任人材料入库验收
生产管理部通知书
冷作工检验员制造工艺过程卡
检验员
冷作工
冷作工、电焊工、检验员
产品焊接试板B类项目
确认通知书
电焊工焊缝射线探伤报告
抛光工焊缝探伤合格通知
探伤工
冷作工
电焊工
探伤工
冷作工
检验员
压力容器制造工艺流程图
责任部门流程图相关说明使用表单
容器制造工序过程卡(全套)
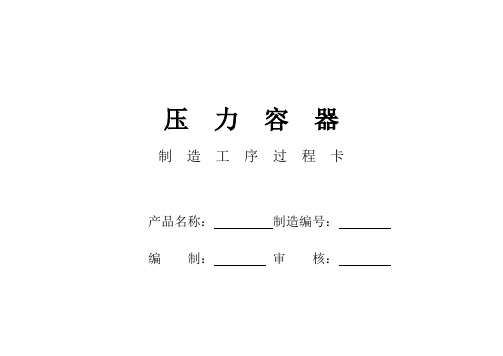
压力容器制造工序过程卡产品名称:制造编号:编制:审核:总装工序过程卡产品名称:工令号材料牌号标准容器类别图号检验序号工序名称工序内容及工序要求操作责任人项目结论签字1筒节组焊筒节与筒节组对,按焊接工艺施焊,控制环缝错边量b≤ mm,纵向棱角度e≤ mm,环缝 %X射线探伤,合格2封头组焊封头与筒体组对,按焊接工艺施焊,控制环缝错边量b≤mm,环缝 %X射线探伤,合格错边量3整体划线按设备总图及管口方位图划出各接管、支座方位及位置,注意使开孔及支座位置避开筒体纵缝开口方位及位置4内件组对按图纸要求组对内件,尺寸方位符合要求,按图纸要求焊接方位及位置5人孔法兰与人孔接管组焊法兰与接管组对,控制环缝错边量b≤mm,法兰面与接管轴线垂直偏差c≤mm,按焊接工艺施几何尺寸焊,环缝%X射线探伤,合格总装工序过程卡产品名称:工令号材料牌号标准容器类别图号检验序号工序名称工序内容及工序要求操作责任人项目结论签字6接管法兰与接管组焊接管法兰与接管组对,控制环缝错边量b≤mm,法兰面与接管轴线垂直偏差c≤法兰外径1/100且不大于3mm,按焊接工艺施焊,环缝 %X射线探伤,合格几何尺寸7设备法兰与筒体组焊设备法兰与筒体组对,控制环缝错边量b≤mm,法兰面与筒体轴线垂直偏差c≤mm ,按焊接工艺施焊,环缝%X射线探伤,合格几何尺寸8筒体与人孔组件组焊划出人孔法兰中心线,与筒体中心线对(跨)中布置,并使法兰平面与壳体中心线的水平和垂直偏差≤ mm,按焊接工艺施焊,角焊缝腰高H= mm9接管法兰与按管法兰与筒体组对,法兰面与接管轴线垂方位及位置筒体组对直偏差c≤法兰外径的1/100且不大于3mm,焊接工艺施焊,环缝 %X射线探伤,合格总装工序过程卡产品名称:工令号材料牌号标准容器类别图号检验序号工序名称工序内容及工序要求操作责任人项目结论签字10支座(支脚)与筒体组焊按设备总图及管口方位图组对方位,保证地脚螺栓孔尺寸符合图纸要求,被支座(支腿)垫板覆盖的焊缝应100%X,射线探伤,级合格,并打磨至与筒体平,按焊缝工艺施焊,与筒体焊缝相交部位留出不焊。
压力容器制造工艺检验流转卡

铆 工
划线尺寸Φ=
坡口角度α°
坡口钝边P
标记移植
划线尺寸Φ=
坡口角度α°
坡口钝边P
标记移植
E
3
对 接
点 焊
(1)按标号组对。
(2)对坡清理坡口及其两侧各20mm范围内溶渣飞边、除锈 、去污
(3)拼板的对口错边量b不应大于材料厚度δs的10%,且不大于1.5mm。
(4)点固封头拼板。
焊缝代号
A -----筒体及接管等纵缝
B -----筒体及接管等环缝
C-----法兰、平板与筒体及接管等焊缝
D -----接管、凸缘、补强圈等与壳体的焊缝
E -----非受压元件与受压元件的焊缝
BDJL6-03
BDJL6-04
某某
有限公司
容器排版图
名称
压缩空气罐
型号
DN2200
材质
Q345R
编号
R15-0xx
批准手续
返修次数
增探比例
返修结论
批准手续
返修次数
增探比例
返修结论
焊接责任人
签字
E
质控符号:E----检查点H----停止点
筒体制造工艺检验流转卡
BDJL6-06
产品编号
XXXX
材料
Q345R
材料移植号
代用材料
质
控
符号
零部件名称
筒体
规格
DN2200X12
件号
12-2
件数
1
状态
序号
工序
名称
工序内容及工艺要求
质控符号:E----检查点 H----停止点
筒体制造工艺检验流转卡
压力容器出厂检验报告及组装件工艺记录卡
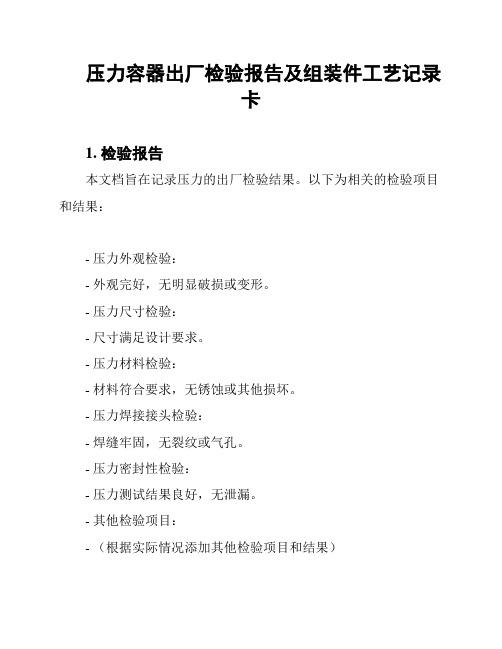
压力容器出厂检验报告及组装件工艺记录
卡
1. 检验报告
本文档旨在记录压力的出厂检验结果。
以下为相关的检验项目和结果:
- 压力外观检验:
- 外观完好,无明显破损或变形。
- 压力尺寸检验:
- 尺寸满足设计要求。
- 压力材料检验:
- 材料符合要求,无锈蚀或其他损坏。
- 压力焊接接头检验:
- 焊缝牢固,无裂纹或气孔。
- 压力密封性检验:
- 压力测试结果良好,无泄漏。
- 其他检验项目:
- (根据实际情况添加其他检验项目和结果)
根据以上检验结果,本压力合格出厂,并可投入使用。
2. 组装件工艺记录卡
本文档旨在记录压力组装过程中的工艺细节。
以下为相关的组装步骤和记录:
1. 准备工作:
- 确保所需组装件齐全。
- 清洁工作区域,确保卫生和安全。
2. 组装步骤:
1. (详细描述组装步骤)
2. (详细描述组装步骤)
3. (详细描述组装步骤)
- (根据实际情况添加更多组装步骤)
3. 检查和测试:
- 对组装完成的压力进行外观检查。
- 进行密封性测试,确保无泄漏。
- (根据实际情况添加其他检查和测试步骤)
4. 验收和记录:
- 完成组装后,对压力进行验收。
- 记录组装日期、验收人员和相关检查结果。
以上为组装件工艺记录卡的简要内容。
具体的组装步骤和记录应根据实际情况进行详细记录。
压力容器氨渗漏(B类)试验工艺卡

试验介质 氨气
介质温度℃ ≥5℃
编制/日期 :
压力容器氨渗漏(B 类)试验工艺卡
编号:
产品名称
试压部位
序 工序
号
主体材料 压力试验过程
技术要求
1 受理 液压试验合格的容器,才能进行氨气(B 类)气密性试验
1)要求试验场地宽敞清洁,试验设备完好,试压仪表经检定合 格,安全设施完备; 2 准备 2)容器各连接部位的紧固密封件必须装配齐全,紧固妥当,严 禁少装螺栓、不按要求使用螺栓和盲板。 3)容器内充氨气(20%到 30%)与氮气的混合气体。 1)缓慢升压至试验压力(设计压力) MPa,保压≥XXXmin,对 有 密 封 要 求 的 连接部位,无漏气,无可见变形,为合格。 3 实施 2)用检漏试验纸检查,检查试纸有无变色。 3)严禁带压紧固螺栓或向受压元件施加外力,严禁带压焊补。
4 卸压 压力试验合格后,卸压到表压为零。
试验标准
5 保护 试压完成后,按要求除锈密封保护。
6 确认 填写气密性试验报告并转存。
审核/日期:
压力容器表卡单样本
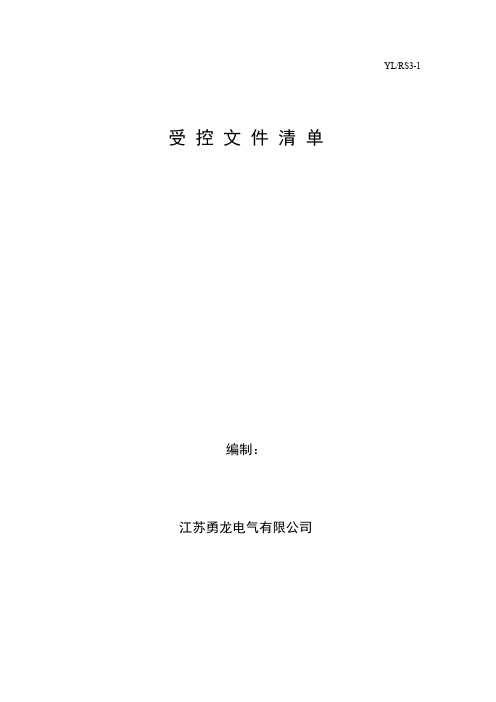
受控文件清单编制:江苏勇龙电气有限公司受控文件清单YL/RS3-2 文件资料发放登记表YL/RS3-3 压力容器法规、标准目录编制:审核:日期:江苏勇龙电气有限公司YL/RS3-3 压力容器法规、标准目录第页YL/RS3-4 质量体系文件修改通知单YL/RS3-5 文件资料档案销毁处理单YL/RS4-1 合同评审表合同登记台帐YL/RS4-2YL/RS5-1 审图记录YL/RS5-2 设计图纸、工艺文件发放记录第页YL/RS5-3 设计工艺更改通知单YL/RS5-4 设计变更、图纸代用申请单工艺文件YL/RS7-1产品编号:产品名称:编制:日期::审核:日期:焊接会签:日期:主要受压元件发放(下料)记录单位:mmYL/RS7-3 材料消耗定额汇总表第页共页外购、外协件明细表第页共页YL/RS7-4容器排版图YL/RS7-5制造工序过程卡YL/RS7-6K为控制点符号H为停止点符号编制:年月日审核:年月日装配工艺卡YL/RS7-7K为控制点符号H为停止点符号编制:年月日审核:年月日工艺纪律检查记录工艺纪律检查台帐YL/RS7-10 工装验证记录工装台帐生产指令单YL/RS7-13成品入库通知单成品入库通知单YL/RS6-1 合格供方调查评审表分包方调查评审表合格供方名录年月日江苏勇龙电气有限公司YL/RS6-3合格供方名录YL/RS6-4 材料采购计划单材料、外购件到货验收单材料入库发放台帐YL/RS6-6YL/RS6-7 材料代用单钢板入库排版发放台帐领料单一、存根;二、保管员;三、材料会计;四、车间领料单一、存根;二、保管员;三、材料会计;四、车间YL/RS6-10 焊材到货验收入库通知单检验验收记录焊材合格标签YL/RS6-11焊材合格标签YL/RS6-11焊接材料入库发放登记台帐江苏勇龙电气有限公司HY/RS6-12YL/RS6-13 焊材一级库温、湿度记录二级库烘焙记录二级库焊材发放记录焊接工艺评定项目一览表焊接工艺指导书YL/RS8-3.2YL/RS8-3.2焊接工艺评定报告YL/RS8-3.3YL/RS8-3.3。
压力容器制造工序过程卡
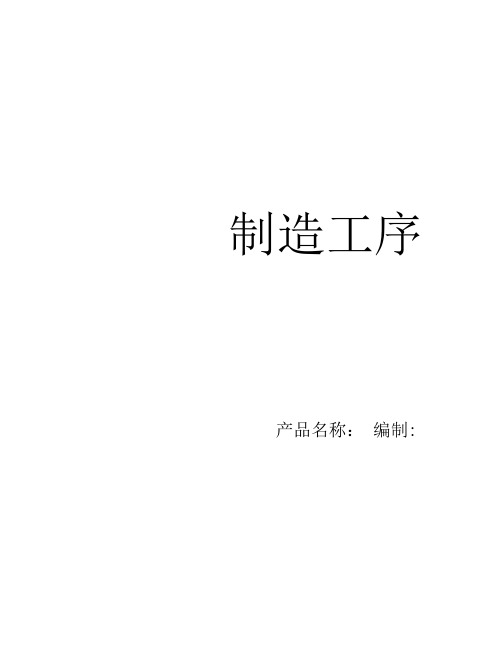
制造工序产品名称:编制:
过程卡制造编号:审核:
制造工序过程卡
注:不锈钢可用等离子体切割编制:年月曰审核:年月日
制造工序过程卡
产品名称:序号:共页第2页
注:不锈钢可用等离子体切割编制:年月曰审核:年月日
序号:共页第4页
产品名称:
编制:年月曰审核:年月日
编制:年月曰审核:年月日
产品名称:序号:共页第7页
编制:年月曰审核:年月日
制造工序过程卡
产品名称:序号:共页第8页
注:不锈钢可用等离子体切割编制:年月曰审核:年月日
序号: 共页第9页
制造工序过程卡
产品名称:
产品名称:序号:共页第10页
编制:年月曰审核:年月日
产品名称:序号:共页第11页
编制:年月曰审核:年月日
产品名称:序号:共页第12页
编制:年月曰审核:年月日
平焊管法兰一览表
编制:年月曰审核:年月日
组装工序过程卡
编制:年月曰审核:年月日
接管安装焊接工序过程卡产品名称:
编制:年月曰审核:年月日
产品名称:序号:共页第页
编制:年月曰审核:年月日
产品名称:序号:共页第页
编制:年月曰审核:年月日
压力容器外观及几何尺寸检验报告产品编号:共页第18页
产品编号: 胀管操作记录: 胀管机型号:
不锈钢产品酸洗钝化处理工艺卡。
压力容器-焊接工艺指令卡

压力容器焊接工艺指令卡冀PV焊09产品名称BCC纤维过滤器制造编号JG11-25-03 容器类别位置示意图:焊缝代号材料牌号、规格接头及坡口型式通用焊接工艺卡编号焊工合格项目1-3B 1-4A Q235-B δ=12 对接I型T-1 5-6A Q235-B δ=10 V型坡口T-2 7A Q235-B δ=12 V型坡口T-3 D5-8.D10-13.D20 Φ89.×4 T型插入T-5 D4 Φ273×8 T型插入T-4D9. D18.19 D14-17 Φ35×3 Φ38.×3 Φ133.×4T型插入T-6D1 .D3 Φ530/630.×10 T型插入T-7D2 Φ480.×12 T型插入T-8C1-4 管壁厚度8-12 T型插入T-9C5-17 管壁厚度3-8 T型插入T-10:当无通用焊接工艺卡时,亦应填写焊缝代号等栏目,并根据相应的焊接工艺评定,编制压力容器焊接工艺卡。
编制:审核: 监检员:日期:日期: 日期:产品名称 蒸汽冷凝液回收罐 制造编号 091706R- 容器类别 Ⅰ位置示意图:C 10C 9C 8C 7C 6C 5C 4C 3C 2C 1D 11D 10D 9D 8D 7D 6D 5D 4D 3D 2D 15B4B3B2B1B3A2A1A焊缝代号 材料牌号、规格 接头及坡口型式通用焊接 工艺卡编号焊工合格项目注:当无通用焊接工艺卡时,亦应填写焊缝代号等栏目,并根据相应的焊接工艺评定,编制压力容器焊接工艺卡。
编制: 审核: 监检员:日期: 日期: 日期:产品名称压缩空气缓冲罐制造编号RQ111702R-0006 容器类别Ⅰ位置示意图:焊缝代号材料牌号、规格接头及坡口型式通用焊接工艺卡编号焊工合格项目注:当无通用焊接工艺卡时,亦应填写焊缝代号等栏目,并根据相应的焊接工艺评定,编制压力容器焊接工艺卡。
编制:审核: 监检员:日期:日期: 日期:产品名称连续排污扩容器制造编号RQ111702-0007 容器类别Ⅱ位置示意图:焊缝代号材料牌号、规格接头及坡口型式通用焊接工艺卡编号焊工合格项目注:当无通用焊接工艺卡时,亦应填写焊缝代号等栏目,并根据相应的焊接工艺评定,编制压力容器焊接工艺卡。
压力容器制造工艺卡

压力容器制造工艺卡Last updated on the afternoon of January 3, 2021
封头制造
件号
名称规格 数量 材料 备注
设备名称
广口口编
号
编制
审核
日 期
广口口编号
产品名称 罐体
产品图号
件号 编制年月日审核年月日
筒体加工检验
卡
共页
第页
单台数量
序 号 工
序 1T-
工序内容及技术要求 备 工
装 检验数 据
操作/
员验/
因期
1 备料 库 房 a.按本厂压力容器用材料进厂检验程 序进行入厂检验,须有材质证明 书,材料标记应清晰明确,否则应
作材料复验。
b.材料外观应光滑,无锈蚀麻坑,无
裂纹、划伤等影响外观质量的可见 缺陷。
c.筒体外直径偏差为:±1%D,且不 大于 0.75mm 。
2 下料
铆 焊 筒体按图纸理论尺寸下料,预留5~ 8mm 机加工余量。
氧快
3 抛光 铆 焊 筒体内壁除锈、抛光,无杂质、焊接 飞溅、锈蚀等。
抛光
机
材料
热轧
20g
材料状
态。
压力容器制造工艺卡
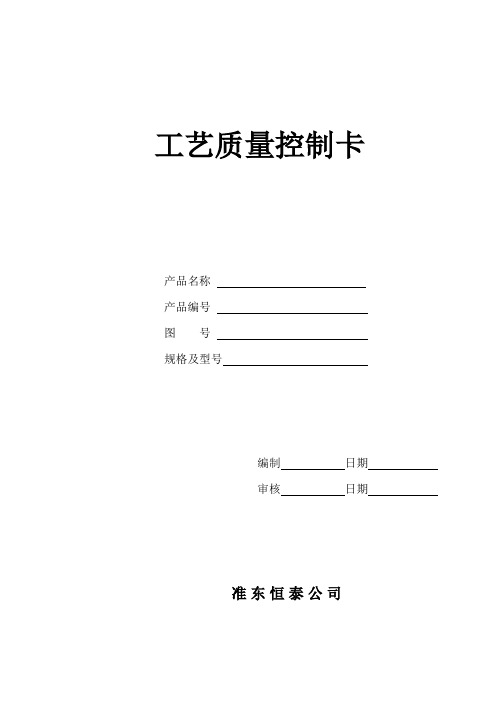
2、
3、≤
3、
4、≤
4、
5、≤
5、
环向错边量
1、≤3
1、
2、≤
2、
3、≤
3、
4、≤
4、
5、≤
5、
备
注
补强圈加工工艺过程及质量控制检验卡
HT/R工艺控08-C/3
产品编号
件号
材质及厚度
数量
工艺
检验
工序名称
控制项目
技术要求mm
检测记录mm
操作者
日期
检验员
日期
下料
质证书及标记确认
物证相符
按图样尺寸下料
纵缝焊接
按焊接工艺
见焊接记录
/
/
试板探伤
按焊接工艺
见探伤报告
/
/
校圆
最大、最小直径差
1、<2.5
1、
2、<2.5
2、
3、<2.5
3、
4、
4、
5、
5、
环向棱角度
1、<3
1、
2、<3
2、
3、<3
3、
4、
4、
5、
5、
环缝
组对
组对间隙
0~2
环缝对口错边量
1、<2.5
1、
2、<2.5
2、
3、
3、
4、
4、
纵向棱角度
审查记录
审查结论
材
料
审
查
材料标准性审查
□符合□不符合
材料与介质的相容性
□符合□不符合
材料的经济合理性
□符合□不符合
其它
□符合□不符合
材料责任工程师:日期:
压力容器焊接工艺卡样本
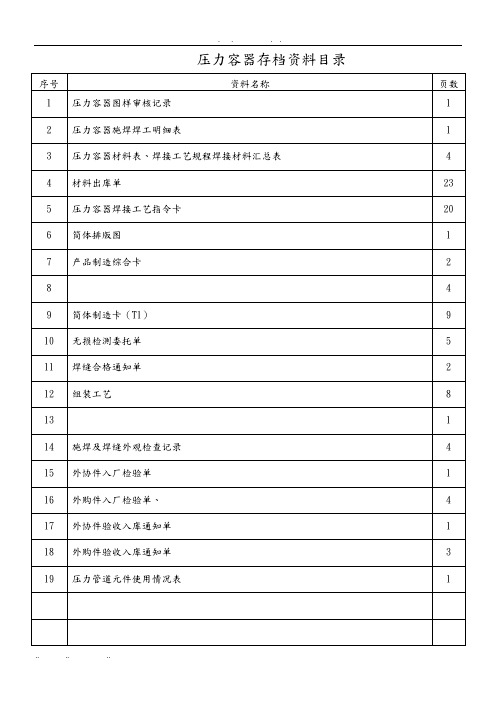
压力容器存档资料目录压力容器外来图样审核记录 DM/JS07压力容器施焊焊工明细表编制日期审核日期 C检监员日期压力容器材料明细表第1页共2页.. .. ..焊接材料汇总表共20页第2页.. .. .... .. ..焊接工艺指令卡.. .. ..焊接工艺指令卡接头焊接工艺卡共20页第5页接头焊接工艺卡共20页第6页坡口角度(℃) 60°焊接工艺评定报告编号HPSMAW-II-1G-6钝边(mm) 1~2 焊缝余高(mm)焊工持证项目SMAW-II-3G-12-F3J组装间隙(mm) 2~3 备注:焊接位置焊接层次焊接方法填充材料焊接电流电弧电压(V)焊接速度(cm/min)气体流量(L/min)线能量KJ/min预热温度(℃)型(牌)号直径(mm) 极性电流(A)层间温度(℃) ≤150焊后热处理消除应力正1 焊条焊电弧焊J507 ф3.2 直反90~120 20~22 8~9 12~19.8 后热正2 焊条焊电弧焊J507 ф4.0 直反160~180 20~22 10~12 16~23.8 钨极直径(mm) 反1 焊条焊电弧焊J507 ф3.2 直反90~120 20~22 8~9 12~19.8 喷嘴直径(mm)气体成份接头焊接工艺卡共20页第7页焊接层次顺序示意图:母材1 Q345R 厚度(mm) 8 焊接工艺卡编号DMH-Ⅱ-1-3-8母材2 Q345R 厚度(mm) 8 图号SB25-83-1母材3 厚度(mm) 接头名称管箱筒体纵缝、与封头环缝焊接顺序正1、正2、正3 接头型式对接坡口型式V 接头编号C2坡口角度(℃) 60°焊接工艺评定报告编号2011HP-25钝边(mm) 1~2 焊缝余高(mm)焊工持证项目SMAW-II-3G-12-F3J组装间隙(mm) 2~3 备注:焊接位置焊接层次焊接方法填充材料焊接电流电弧电压(V)焊接速度(cm/min)气体流量(L/min)线能量KJ/min预热温度(℃)型(牌)号直径(mm) 极性电流(A)层间温度(℃) ≤150焊后热处理正1 焊条焊电弧焊J507 ф3.2 直反90~120 20~22 8~9 12~19.8 后热正2 焊条焊电弧焊J507 ф4.0 直反160~180 20~22 10~12 16~23.8 钨极直径(mm) 反1 焊条焊电弧焊J507 ф3.2 直反90~120 20~22 8~9 12~19.8 喷嘴直径(mm)气体成份接头焊接工艺卡共20页第8页焊接层次顺序示意图:母材100Cr17Ni14Mo2 厚度(mm)焊接工艺卡编号DMH-Ⅶ2-1-5-4母材200Cr17Ni14Mo2Ⅱ厚度(mm) 3.5~4.5 图号SB25-83-1 母材3 厚度(mm) 接头名称接管与法兰焊接顺序正1、正2 接头型式对接接头坡口型式V 接头编号C3、C4坡口角度(℃) 60 焊接工艺评2011 HP -14接头焊接工艺卡共20页第9页母材2 20# 厚度(mm)3.54.5图号SB25-83-1母材3 厚度(mm) 接头名称接管与法兰焊接顺序正1、反1、正2 接头型式角接坡口型式接头编号C5~C12坡口角度(℃) 50°焊接工艺评定报告编号2011 HP -10钝边(mm) 焊缝余高(mm) 4 焊工持证项目SMAW-Ⅱ-6FG-9/18-F3J组装间隙(mm) 0.5~1 备注:焊接位置焊接层次焊接方法填充材料焊接电流电弧电压(V)焊接速度(cm/min)气体流量(L/min)线能量KJ/min预热温度(℃)型(牌)号直径(mm) 极性电流(A)层间温度(℃) ≤50焊后热处理消除应力正1 焊条电弧焊J427 ф3.2直流反接90~120 20~22 8~9 12~19.8接头焊接工艺卡共20页第10页坡口角度(℃) 50°焊接工艺评定报告编号2010 HP -05钝边(mm) 焊缝余高(mm) 4 焊工持证项目SMAW-Ⅱ-6FG-9/18-F3J组装间隙(mm) 0.5~1 备注:焊接位置焊接层次焊接方法填充材料焊接电流电弧电压(V)焊接速度(cm/min)气体流量(L/min)线能量KJ/min预热温度(℃)型(牌)号直径(mm) 极性电流(A)层间温度(℃) ≤50焊后热处理正1 焊条电弧焊J427 ф3.2直流反接90~120 20~22 8~9 12~19.8 后热正2 焊条电弧焊J427 ф3.2直流反接90~120 20~22 8~9 12~19.8 钨极直径(mm) 反1 焊条电弧焊J427 ф3.2直流反接90~120 0~22 8~9 12~19.8喷嘴直径(mm) 反2 焊条电弧焊J427 ф3.2直流反接90~120 0~22 8~9 12~19.8 气体成份接头焊接工艺卡共20页第11页焊接层次顺序示意图:母材1 Q345R 厚度(mm) 8 焊接工艺卡编号DMH-Ⅰ/Ⅱ-2-3-4/8母材2 20# 厚度(mm)3.54.5图号SB25-83-1母材3 厚度(mm) 接头名称接管与封头焊接顺序正1、正2、正3、反1 接头型式角接坡口型式V 接头编号D6坡口角度(℃) 50±5°焊接工艺评定报告编号2011 HP -10 2010HP-08钝边(mm) 0.5~1.5 焊缝余高(mm)焊工持证项目SMAW-Ⅱ-6FG-9/18-F3J 组装间隙(mm) 2~2.5 备注:接头焊接工艺卡共20页第12页母材2 20# 厚度(mm)3.54.5图号SB25-83-1 母材3 厚度(mm) 接头名称接管与封头焊接顺序正1、正2、反1 接头型式角接坡口型式V 接头编号D9坡口角度(℃) 50±5°焊接工艺评定报告编号2010HP-13 2010HP-08钝边(mm) 0.5~1.5 焊缝余高(mm)焊工持证项目SMAW-Ⅱ-6FG-9/18-F3J组装间隙(mm) 2~2.5 备注:焊接位置焊接层次焊接方法填充材料焊接电流电弧电压(V)焊接速度(cm/min)气体流量(L/min)线能量KJ/min预热温度(℃)型(牌)号直径(mm) 极性电流(A)层间温度(℃) ≤50焊后热处理正1 焊条电弧焊J427 ф3.2直流反接90~120 20~22 8~9 12~19.8 后热正2、3 焊条电弧焊J427 ф4.0 直流160~180 20~22 10~12 16~23.8反接钨极直径(mm) 反1 焊条电弧焊J427 ф4.0直流反接160~180 20~22 10~12 16~23.8 喷嘴直径(mm)气体成份接头焊接工艺卡共20页第13焊接层次顺序示意图:母材1Q345R 厚度(mm) 8焊接工艺卡编号DMH-Ⅰ/Ⅱ-2-3-8/30母材2 20#厚度(mm) 图号SB25-83-1母材3 厚度(mm) 接头名称设备法兰与筒体焊接顺序正1、正2、正3、反1、接头型式角接坡口型式V 接头编号D3~D4坡口角度(℃) 50±5°焊接工艺评定报告编号2011HP-10 2010HP-08接头焊接工艺卡共20页第14页焊接层次顺序示意图:母材1 Q345R 厚度(mm) 8焊接工艺卡编号DMH-Ⅰ/Ⅱ-2-3-8/30母材2 20#厚度(mm) 图号SB25-83-1母材3 厚度(mm) 接头名称设备法兰与筒体焊接顺序正1、正2、正3、反1、接头型式角接坡口型式V 接头编号D10~17坡口角度(℃) 50±5°焊接工艺评定报告编号2010HP-13 2010HP-08钝边(mm) 0.5~1.5 焊缝余高(mm)焊工持证项目SMAW-Ⅱ-6FG-12/18-F3J组装间隙(mm) 2~2.5 备注:焊接位置焊接层次焊接方法填充材料焊接电流电弧电压(V)焊接速度(cm/min)气体流量(L/min)线能量KJ/min预热温度(℃)型(牌)号直径(mm) 极性电流(A)层间温度(℃) ≤50焊后热处理正1 焊条电弧焊J427 ф3.2 直流90~120 20~22 8~9 12~19.8接头焊接工艺卡共20页第15页焊接顺序正1、正2、正3、反1、接头型式角接坡口型式V 接头编号D1、D2坡口角度(℃) 50±5°焊接工艺评定报告编号HP 2011-12 2011HP-232010HP-05钝边(mm) 0.5~1.5 焊缝余高(mm)焊工持证项目SMAW-IV-6FG(K)-9/18-F4组装间隙(mm) 2~2.5 备注:焊接位置焊接层次焊接方法填充材料焊接电流电弧电压(V)焊接速度(cm/min)气体流量(L/min)线能量KJ/min预热温度(℃)型(牌)号直径(mm) 极性电流(A)层间温度(℃) ≤50焊后热处理正1 焊条电弧焊A022 ф3.2直流反接90~120 20~22 8~9 12~19.8 后热正2 焊条电弧焊A022 ф4.0直流反接160~180 20~22 10~12 16~23.8 钨极直径(mm) 正3 焊条电弧焊A022 ф4.0直流反接160~180 20~22 10~12 16~23.8喷嘴直径(mm) 正4 焊条电弧焊A022 ф4.0直流反接160~180 20~22 10~12 16~23.8 气体成份接头焊接工艺卡共20页第16页焊接层次顺序示意图:母材100Cr17Ni14Mo2厚度(mm) 8 焊接工艺卡编号DMH-Ⅶ2-2-3-4/6母材200Cr17Ni14Mo2Ⅱ厚度(mm)3.54图号SB25-83-1母材3 厚度(mm) 接头名称接管与筒体焊接顺序正1、正2、正3、反1 接头型式角接坡口型式V 接头编号D3、D4、D5、D6坡口角度(℃) 50±5°焊接工艺评定报告编号2011 HP-12 2010HP-05钝边(mm) 0.5~1.5 焊缝余高(mm)焊工持证项目SMAW-Ⅱ-6FG-9/18-F3J接头焊接工艺卡共20页第17页Mo2母材200Cr17Ni14Mo2Ⅱ厚度(mm) 2.5 图号SB25-83-1母材3 厚度(mm) 接头名称换热管与管板焊接顺序正1、正2 接头型式角接坡口型式接头编号D17~18坡口角度(℃)焊接工艺评定报告编号2011 HP -15钝边(mm) 焊缝余高(mm) 4 GTAW-Ⅳ-6FG-3/18-02组装间隙(mm) 备注:焊接位置平位焊接层次焊接方法填充材料焊接电流电弧电压(V)焊接速度(cm/min)气体流量(L/min)线能量KJ/min预热温度(℃)型(牌)号直径(mm) 极性电流(A)层间温度(℃) ≤50焊后热处理正1 钨极氩弧焊ER316L ф2.5直流正接80~100 12~13 10~13 6~7 4.4~7.8直流后热正2 钨极氩弧焊ER316L ф2.580~100 12~13 10~13 6~7 4.4~7.8正接钨极直径(mm) Φ2.5喷嘴直径(mm) Φ8.0气体成份接头焊接工艺卡共20页第18页-焊接层次顺序示意图:母材1 Q345R 厚度(mm) 焊接工艺卡编号DMH-Ⅱ-2-3-10/8母材2 Q345R 厚度(mm) 图号SB25-83-1母材3 厚度(mm) 接头名称隔板与封头焊接顺序1、2、3 接头型式角接坡口型式接头编号D12焊接工艺评坡口角度(℃)2011HP-10定报告编号接头焊接工艺卡共20页第19页Mo2母材200Cr17Ni14Mo2Ⅱ厚度(mm) 图号SB25-83-1母材3 厚度(mm) 接头名称底座板与筒体焊接顺序1、2、3 接头型式角接坡口型式接头编号D13、D14坡口角度(℃)焊接工艺评定报告编号2011 HP -12钝边(mm) 焊缝余高(mm)焊工持证项目SMAW-IV-6FG(K)-9/18-F4组装间隙(mm) 0~1 备注:焊接位置焊接层次焊接方法填充材料焊接电流电弧电压(V)焊接速度(cm/min)气体流量(L/min)线能量KJ/min预热温度(℃)型(牌)号直径(mm) 极性电流(A)层间温度(℃) ≤50焊后热处理 1 焊条电弧焊A022 ф3.2 直流90~120 20~22 8~9 14.5~20.8接头焊接工艺卡共20页第20页。
压力容器制造工序流转卡
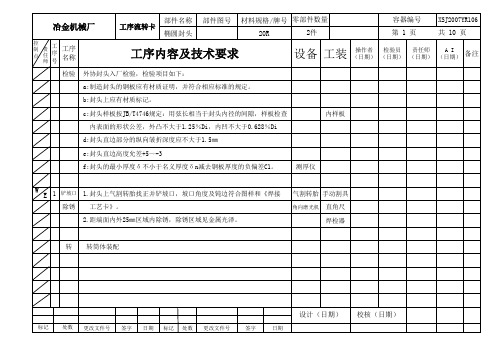
工序 名称
部件名称 部件图号 工序流转卡
附件
工序内容及技术要求
容器编号 第9页
XSJ2007YR106 共 10 页
设备 工装 操作者 (日期)
检验员 (日期)
责任师 (日期)
AI (日期)
备注
1 备料 领取经检验合格的管座 DN50、DN20、DN40、DN25、DN80接管, 铭牌,
支座等集中到装配现场。
5.定位焊缝长30~50㎜,间距50~200㎜,定位焊缝无气孔、夹渣、
裂纹等缺陷,且表面一致。
6.筒节端面倾斜度≤ 2 ㎜
7.筒节长度偏差2000±1.5㎜、 1000±1.5㎜。
8.同一截面上最大内径与最小内径之差随筒体直径的大小确定。
W E 6 装配 1.在筒节纵缝的一端装焊100×100㎜的引弧板,另一端装焊600×300㎜ 电焊机 定位焊 产品焊接试板一块及100×100㎜引弧板一块。 (焊条J427/φ3.2) 2.收、引弧板与筒节板等厚。 3.收、引弧板与筒节组对边缘偏差≤1.0㎜。 4.产品焊接试板焊缝与筒节纵缝应在同一直线上。
容器编号 第 10 页
XSJ2007YR106 共 10 页
设备 工装 操作者 (日期)
检验员 (日期)
责任师 (日期)
AI (日期)
工序流转卡
筒体
δ=8、20R
2节
容器编号 第5页
XSJ2007YR106 共 10 页
控
制 点
责 任 师
工 序 号
工序 名称
工序内容及技术要求
设备 工装 操作者 (日期)
检验员 (日期)
责任师 (日期)
AI (日期)
备注
W E 11 组对 1.筒节与筒节、筒节与封头,按焊缝排版图进行组对。
压力容器热处理工艺卡片

编制人:年月日审核人:年月日
热处理工艺卡
共1页第1页
产品名称
二级分液罐
材料牌号
Q345R+S32168
产品规格
δ10+3
工艺过程卡编号
—
零件名称
—
零件规格
—
材料编号
—
制造编号
R12-25~26
热处理后
性能
σsMPa
σbMPa
δ%
ψ
AkvJ
硬度
冷变型
—
—பைடு நூலகம்
—
—
—
≤217HBW
—
热处理类别
设备
热处理规范
随炉试板
炉内PWHT
□炉外PWHT
□局部PWHT
□分段PWHT
热处理炉
入炉温度
(℃)
升温速度
(℃/h)
保温温度
(℃)
保温时间
(h)
降温速度
(℃/h)
冷却方式
出炉温度(℃)
□有
□无
<400
>55<150
600~610
0.6
>55<220
出炉空冷
<400
附图及工艺说明
说明:1、严格按热处理规范执行,防止焊件过度氧化和变形。
2、应控制热处理炉内气氛以免材料增碳或脱碳。应控制炉中气体硫、卤素和其它损坏材料的物质含量,
所有机械加工表面均应进行防护以防止氧化和损坏。
3、采用温度—时间曲线自动记录,记录纸每炉一张。
4、应在被热处理的设备两端最厚部位和其它部位的最高点及最低点安装记录热电偶。
5、温度的测定方法,符合NB/T47015中有关焊后热处理的规定。
压力容器焊接工艺卡

焊接层次顺序示意图:母材116厚度()16焊接工艺卡编号母材216厚度()16图号母材3厚度()接头名称筒体纵缝焊接顺序接头型式对接坡口型式V接头编号A1、A2、A3、A4坡口角度(℃)60°焊接工艺评定报告编号钝边() 2-6焊缝余高()焊工持证项目组装间隙()2~31、在坡口与坡口边缘各20范围内,将油、污、锈、垢、氧化皮清除,直至呈现金属光泽。
2、定位焊缝为8条,每2条定位焊缝间距为250,定位焊缝长度为30、厚度为6-10。
3、焊完进行100%无损探伤。
焊接方法直通焊焊接层次焊接方法填充材料焊接电流电弧电压(V)焊接速度()气体流量()预热温度(℃)型(牌)号直径()极性电流(A)层间温度(℃)焊后热处理定位焊H10ф2直流反接80-11512-1410-168-10焊剂烘干温度250℃封底焊H10ф2.5直流反接115-1512-1410-168-10焊 接 工 艺卡 .:1焊 接 工 艺卡 .: 2钨极直径() 正面焊H10431ф4交流600-65034-3748喷嘴直径() 气体成份编制日期 年 月 日审核日期 年 月 日焊接层次顺序示意图:母材1 16 厚度() 16 焊接工艺卡编号母材2 16厚度() 16图 号母材3厚度()接头名称 筒体环缝 焊接顺序接头型式 对 接 坡口型式 V接头编号B1、B2、B3、B4、B5坡口角度(℃) 60°焊接工艺评定报告编号钝边() 2-6焊缝余高() 焊工持证项目组装间隙()2~31、在坡口与坡口边缘各20范围内,将油、污、锈、垢、氧化皮清除,直至呈现金属光泽。
2、定位焊缝为28条,每2条定位焊缝间距为12°,定位焊缝长度为30、厚度为6-10。
焊 接 工 艺卡 .:33、焊完进行100%无损探伤。
焊接方法 直通焊焊接 层次 焊接方法填充材料焊接电流 电弧 电压(V) 焊接速度() 气体流量() 预热温度(℃) 型(牌)号直径() 极性 电流(A) 层间温度(℃)焊后热处理 定位焊 H10 ф2 直流反接 80-115 12-14 10-16 8-10 焊剂烘干温度 250℃封底焊 H10 ф2.5 直流反接 115-150 12-14 10-16 8-10钨极直径() 正面焊H10431ф4交流600-65034-3748喷嘴直径() 气体成份编制日期年 月 日审核日期年 月 日焊接层次顺序示意图:母材1 16 厚度() 16 焊接工艺卡编号母材2 16厚度() 8图 号母材3厚度()接头名称 接管与壳体 焊接顺序接头型式对 接卡 .:4焊接层次顺序示意图:母材116厚度()16焊接工艺卡编号母材216厚度()8图号母材3厚度()接头名称人孔与壳体焊接顺序接头型式对接坡口型式单边V接头编号D4坡口角度(℃)60°焊接工艺评定报告编号钝边()2-6焊缝余高()焊工持证项目组装间隙()2~31、在坡口与坡口边缘各20范围内,将油、污、锈、垢、氧化皮清除,直至呈现金属光泽。
压力容器焊接工艺卡
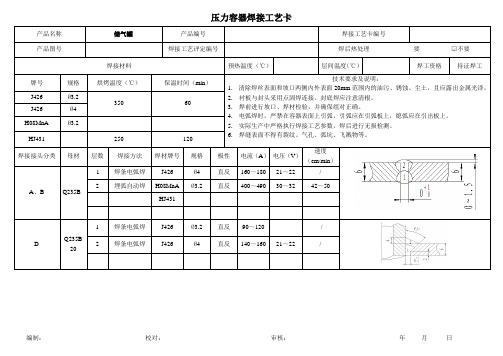
4.电弧焊时,严禁在容器表面上引弧,引弧应在引弧板上,熄弧应在引出板上。
5.实际生产中严格执行焊接工艺参数,焊后进行无损检测。
6.焊缝表面不得有裂纹、气孔、弧坑、飞溅物等。
J426
Ø3.2
350
60
J426
Ø4
H08MnA
Ø3.2
HJ431
250
120
焊接接头分类
产品名称
储气罐
产品编号
焊接工艺卡编号
产品图号
焊接工艺评定编号
焊后热处理要不要
焊接材料
预热温度(℃)
层间温度(℃)
焊工资格
持证焊工
牌号
规格
烘烤温度(℃)
保温时间(min)
技术要求及说明:
1.清除焊丝表面和坡口两侧内外表面20mm范围内的油污、锈蚀、尘土,且应露出金属光泽。
2.衬板与封头采用点固焊连接。封底焊应注意清根。
母材
层数
焊接方法
焊材牌号
规格
极性
电流(A)
电压(V)
速度(cm/min)
A、B
Q235B
1
焊条电弧焊
J426Ø4直反来自160~18021~22
/
2
埋弧自动焊
H08MnA
Ø3.2
直反
400~490
30~32
42~50
HJ431
D
Q235B
20
1
焊条电弧焊
J426
Ø3.2
直反
90~120
/
2
焊条电弧焊
J426
Ø4
直反
140~160
21~22
/
- 1、下载文档前请自行甄别文档内容的完整性,平台不提供额外的编辑、内容补充、找答案等附加服务。
- 2、"仅部分预览"的文档,不可在线预览部分如存在完整性等问题,可反馈申请退款(可完整预览的文档不适用该条件!)。
- 3、如文档侵犯您的权益,请联系客服反馈,我们会尽快为您处理(人工客服工作时间:9:00-18:30)。
产品名称:Ф1200×5104反应釜
产品编号:06WY1—601
编制:王鹉2005年12月14日
校审:2005年12月15日
批准:张中伟2005年12月16日
中国长城铝业公司建设公司
NO.2
产品名称
Ф1200反应釜
压力容器主要零部件制造工艺(工序)过程卡
容器类别
Ⅱ类
件号
1
产品编号
材质、标记
3.实测钢板厚度,用超声波逐张进行检验,Ⅲ级合格。
厚度
二
筒节排料划线
1.按(封头内径+55)×3.14159展开长度划下料线、检查线、加工线,划线公差≯1.5mm,宽误差≯1.5mm,对角线误差≯2mm,长=3943mm,宽=2100mm,对角线=4467mm。
划线尺寸(长)
划线尺寸(宽)
06WY1--601
主材牌号
16MnR
规格
φ1200×55
图号
06WY1--0
部件名称
首节筒体
序号
工序
工艺内容与技术要求
工装
设备
检验项目
自检值
操作者
专检值
检验员
时间
备注
一
领料
检验
1.检查材料表面状况,不允许有裂纹、结疤、折叠、夹渣、分层、麻坑等缺陷。
表面质量
2.核对出厂标记与质量证明书是否一致,打材料标记,填写记录。
2.移植材料标记,打产品编号钢印。
标记移植
3.检查员复验划线尺寸、打确认钢印。
尺寸
4.确认
检验责任工程师确认:
三
下料
按下料线切割下料,清除毛刺、熔渣。
半自动切割机
四
加工
坡口
按焊接工艺细则卡编号()焊缝形式图加工坡口。要求:坡口表面不得有裂纹、分层、夹渣等缺陷,表面粗糙度为25μm。
刨边机
坡口角度
表面质量
错边量
2.按焊接工艺细则卡()要求施焊。
代号钢印
3.内纵缝焊后,用碳弧气刨清根并用角向磨光机修磨坡口及坡口两侧25mm内污物、氧化铁、毛刺等。
4.外焊缝采用自动埋弧焊机施焊,焊缝余高:外焊缝为0~4mm内焊缝为0~3mm。
焊缝余高
5.内外焊缝均不应有气孔、裂纹、弧坑、夹渣等可见缺陷。
外观质量
6.焊缝咬边深度≯0.5mm,连续长度≯100mm,两侧咬边长度累计不得超过220mm。
标记
精度
3.冲击试件:a)用药品腐蚀焊缝,按焊缝中心划线,图4、图5
b)试件应采用万能铣加工或平面磨加工,应防止表面硬化或材料过热。
c)试件标记应打在试样的端面、侧面或缺口背面距端面15mm内,不得打在支承面上。
d)试样缺口处若发现有肉眼可见的气孔、夹渣、裂纹等缺陷时,应报废,重新加工。
e)冲击试件外观、尺寸检验合格后送容管办在投影仪上检查缺口形状,尺寸合格后方可认为机械加工结束。
划线尺寸(长)
划线尺寸(宽)
2.移植材料标记,打产品编号钢印。
标记
3.检查员复验划线尺寸,打确认钢印。
确认
4.确认
检验责任工程师:
二
下料
按下料线切割下料,清除毛刺、熔渣。
自动切割机
三
加工
坡口
按焊接工艺细则卡编号()焊接形式图加工坡口,要求坡口表面不得有裂纹、分层、夹渣等缺陷,表面粗糙度为25μm。
刨边机
检验报告
2.检测结果书面通知检验责任工程师和生产车间,若有超标缺陷,由原持证焊工按返修工艺要求返修。
返修外观
检验责任工程师确认:
第1页共1页
NO.5
产品名称
Ф1200反应釜
压力容器主要零部件制造工艺(工序)过程卡
容器类别
Ⅱ类
件号
3
产品编号
06WY1--601
主材牌号
16MnR
规格
φ1200×52
图号
焊缝余高
4.内外焊缝均不应有气孔、裂纹、弧坑、夹渣等可见缺陷。
外观质量
5.焊缝咬边深度≯0.5mm,连续长度≯100mm,焊缝两侧咬边总长度累计不超过该条焊缝长度的10%=210mm。
咬边深度
咬边长度
6.清除焊接熔渣、飞溅物等,打上焊工代号钢印,填施焊记录。
飞溅物
八
校圆
校圆时用弦长300mm的内样板检查,棱角度应≯5mm。椭圆度≯12mm
Ф1200反应釜
压力容器主要零部件制造工艺(工序)过程卡
容器类别
Ⅱ类
件号
4
产品编号
06WY1--601
主材牌号
16MnR
规格
φ1200×52
图号
06WY1--0
零件名称
上椭圆封头
序号
工序
工艺内容与技术要求
工装设备
检验项目
自检值
操作者
专检值
检验员
时间
备注
一
领料
1.检查材料表面状况,不允许有裂纹、结疤、折叠、夹渣、分层等缺陷。
引焊弧板
第1页共2页
NO.2
序号
工序
工艺内容与技术要求
工装
设备
检验项目
自检值
操作者
专检值
检验员
时间
七
纵缝
焊接
1.按焊接工艺细则卡编号()要求施焊。
埋弧焊机
代号钢印
2.内纵缝焊后,外纵缝用碳弧气刨清根,并用角向磨光机修磨坡口及坡口两侧25mm内污物、氧化铁、毛刺等。
坡口两侧
坡口宽度
3.外焊缝采用自动埋弧焊机施焊,焊缝余高:外焊缝为0~4mm,内焊缝为0~3mm
1.按焊接工艺卡()的要求用角向和内圆磨光机打磨坡口内外表面20mm范围内油绣污物,使之露出金属光泽。
检查坡口打磨情况
2.按照图纸要求组装各接管,使之和封头垂直轴线平行,不平行度<2mm。
检查接管垂直度
3.按照焊接工艺卡()的要求进行焊接。
4.焊后敲掉渣壳,剔除飞溅物。
外观检查
第1页共1页
NO.6
产品名称
标记
四
下料
用氧-乙焰炔切割下料,并去除熔渣。
五
机加工
1.拉伸试件:首先去除8mm热影响区,后去除焊缝余高,再按图(2)画加工线,因试件太厚,分成二片,最后按线加工,按图纸尺寸测量,保证加工精度。
标记
精度
2.弯曲试件:先去除8mm热影响区和焊缝余高,使焊缝与木材表面齐平,因试件太厚,分成二片,而后按图(3)加工并倒圆角,圆角半径为2mm。
错边量
2.采用埋弧自动焊时对口间隙0-1mm。
对口间隙
3.清理坡口及坡口两侧20mm范围内污物,见金属光泽。
坡口两侧
4.定位点焊,焊点必须牢固,一般点焊长度≮40mm。
点焊质量
5.第一节筒节纵缝延长线上加焊产品试板(规格:500×125mm)两块,厚度、材质与筒节相同。
产品试板
6.埋弧焊时焊缝两端加焊引弧板、熄弧板。
检查坡口
4.用角向砂轮机修磨坡口,去除氧化皮和淬硬层。
七
组装各接管
1.按焊接工艺卡()的要求用角向和内圆磨光机打磨坡口内外表面20mm范围内油绣污物,使之露出金属光泽。
06WY1--0
零件名称
下椭圆封头
序号
工序
工艺内容与技术要求
工装设备
检验项目
自检值
操作者
专检值
检验员
时间
备注
一
领料
1.检查材料表面状况,不允许有裂纹、结疤、折叠、夹渣、分层等缺陷。
外观
2.核对材料标记,并实测钢板厚度。用超声波逐块复检。
标记
二
排料
划线
1.下料尺寸:厚度δ=55mm,D=1600mm。划下料线、加工线和复查线。
几何尺寸
检查
4.确认
检验责任工程师:
五
齐口
1.按焊接工艺卡()坡口角度加工坡口。
角度
2.坡口表面不得有裂纹、分层、夹渣等缺陷。
坡口表面质量
六
封头上开管口
1.按图示位置在上封头上画出各接管的开孔线。
开孔方位和尺寸
2.检查员对各接管开孔线进行检查确认。
尺寸
3.用氧-乙炔焰开孔,并将管口修成焊接工艺卡()规定的坡口形式。
核对
2.检查封头编号。
资料
3.检查封头表面状况,形状偏差,按封头检验记录表所要求的项目和标准检查并如实填写检验接果。其封头的标准几何尺寸为:
a)封头总高325mm允差+7.2,-2.4 b)直边高50mm允差-2.5,+5 c)表面凹凸量:外凸≤15mm内凹≤7.5mm.。d)封头最小厚度51.75mm e)直径允差+4,-3mm f)最大最小直径差6mm。
坡口角度
表面质量
四
压头
卷圆
1.卷圆前现在专用胎具上压头予弯,予弯长度>200mm,用弦长大于300mm的内样板检查压头弧度。
弧度
2.控制进料端部与卷板机上辊外圆母线平行。
平行度
3.上辊分多次均匀下压,使焊口自然靠拢,自然对齐。不圆度≯12mm。
不圆度
五
纵缝
焊接
1.控制对口错边量:δs≦55mm时纵缝错边量≤3.5mm。
收到时间
7.试验室力学组接到试验件和委托单后,两天内将实验结果报告交特管办2份,委托单位检验员1份。
试验数据
8.确认:
检验责任工程师确认:
第2页共2页
NO.3
产品名称
Ф1200反应釜
产品试板加工试验工艺(工序)过程卡
容器类别
Ⅱ类
件号
产品编号
06WY1--601
主材牌号