姓名-精馏单元仿真操作实训报告
精馏系统实验报告
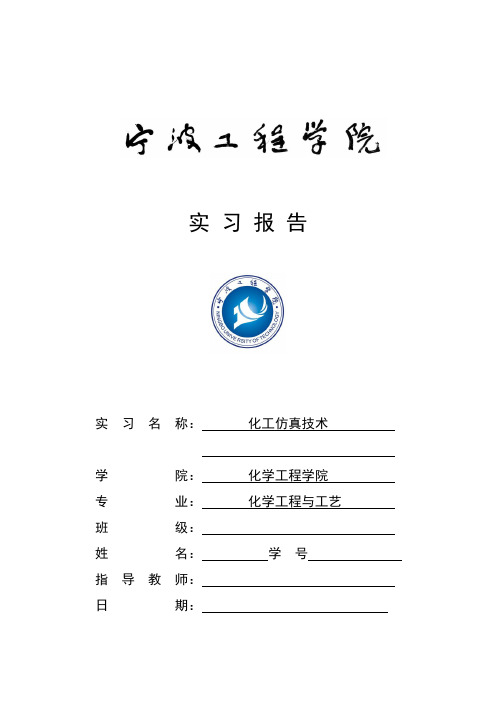
实习报告实习名称:化工仿真技术学院:化学工程学院专业:化学工程与工艺班级:姓名:学号指导教师:日期:第3章精馏系统一、实习目的化工仿真实习是我们大学学习计划的重要组成,解决了大学生的生产实习问题。
仿真实习使得我们不进工厂就能通过计算机得到开车、停车和事故处理操作的机会,使得我们能比较系统的学习生产过程的基本程序和具体操作方法,分析操作参数的合理性、设备及仪表是否运转正常,从而加强我们对基本理论的理解、基本方法的运用和基本技能的训练。
仿真教学有强调工业背景、适用面广、操作与控制界面先进、突出操作实践、内容由浅入深由简到繁、相互呼应、相互补充、附有大量思考题、实用性强、提倡新的教学方法等优点。
能从分发挥学生创造意识的环境。
可很好的将我们所学的理论知识和时间相结合,进一步巩固深化我们的专业知识和技能。
二、实习内容1、工艺流程简介脱丁烷塔是大型乙烯装置中的一部分。
本塔将来自脱丙烷塔釜的烃类混合物(主要有C4、C5、C6、C7等),根据其相对挥发度的不同,在精馏塔内分离为塔顶C4馏分,含少量C5馏分,塔釜主要为裂解汽油,即C5以上组分的其他馏分。
因此本塔相当于二元精馏。
工艺流程为:来自脱丙烷塔的釜液,压力为0.78MPa, 温度为65℃(由TI-1指示),经进料手操阀V1和进料流量控制FIC-1,从脱丁烷塔(DA-405)的第21块塔板进入(全塔共有40块板)。
在本塔提馏段第32块塔板处设有灵敏板温度检测及塔温调节器TIC-3(主调节器)与塔釜加热蒸汽流量调节器FIC-3(副调节器)构成的串级控制。
塔釜液位由LIC-1控制。
塔釜液一部分经LIC-1调节阀作为产品采出,采出流量由FI-4指示,一部分经再沸器(EA-405A/B)的管程汽化为蒸汽返回塔底,使轻组分上升。
再沸器采用低压蒸汽加热,釜温由TI-4指示。
设置两台再沸器的目的是釜液可能含烯烃,容易聚合堵管。
万一发生此种情况,便于切换。
再沸器A的加热蒸汽来自FIC-3所控制的0.35MPa低压蒸汽,通过入口阀V3进入壳程,凝液由阀V4排放。
精馏塔

精馏塔单元仿真实训报告班级:化工 (071)姓名:康华一、工艺流程说明1、工艺说明本流程是利用精馏方法,在脱丁烷塔中将丁烷从脱丙烷塔釜混合物中分离出来。
精馏是将液体混合物部分气化,利用其中各组分相对挥发度的不同,通过液相和气相间的质量传递来实现对混合物分离。
本装置中将脱丙烷塔釜混合物部分气化,由于丁烷的沸点较低,即其挥发度较高,故丁烷易于从液相中气化出来,再将气化的蒸汽冷凝,可得到丁烷组成高于原料的混合物,经过多次气化冷凝,即可达到分离混合物中丁烷的目的。
原料为67.8℃脱丙烷塔的釜液(主要有C4、C5、C6、C7等),由脱丁烷塔(DA-405)的第16块板进料(全塔共32块板),进料量由流量控制器FIC101控制。
灵敏板温度由调节器TC101通过调节再沸器加热蒸汽的流量,来控制提馏段灵敏板温度,从而控制丁烷的分离质量。
脱丁烷塔塔釜液(主要为C5以上馏分)一部分作为产品采出,一部分经再沸器(EA-418A、B)部分汽化为蒸汽从塔底上升。
塔釜的液位和塔釜产品采出量由LC101和FC102组成的串级控制器控制。
再沸器采用低压蒸汽加热。
塔釜蒸汽缓冲罐(FA-414)液位由液位控制器LC102调节底部采出量控制。
塔顶的上升蒸汽(C4馏分和少量C5馏分)经塔顶冷凝器(EA-419)全部冷凝成液体,该冷凝液靠位差流入回流罐(FA-408)。
塔顶压力PC102采用分程控制:在正常的压力波动下,通过调节塔顶冷凝器的冷却水量来调节压力,当压力超高时,压力报警系统发出报警信号,PC102调节塔顶至回流罐的排气量来控制塔顶压力调节气相出料。
操作压力 4.25atm (表压),高压控制器PC101将调节回流罐的气相排放量,来控制塔内压力稳定。
冷凝器以冷却水为载热体。
回流罐液位由液位控制器LC103调节塔顶产品采出量来维持恒定。
回流罐中的液体一部分作为塔顶产品送下一工序,另一部分液体由回流泵(GA-412A、B)送回塔顶做为回流,回流量由流量控制器FC104控制。
精馏装置操作实习报告

实习报告:精馏装置操作实习一、实习背景与目的随着我国化工产业的快速发展,精馏技术在石油、化工、医药等领域得到了广泛应用。
为了提高我国精馏技术的应用水平,培养具有实际操作能力的人才,我参加了为期两周的精馏装置操作实习。
本次实习旨在了解精馏装置的基本结构、掌握精馏过程的基本操作方法,提高分析问题和解决问题的能力,为今后的工作打下坚实基础。
二、实习内容与过程1. 实习前的准备在实习开始前,我们参加了安全教育培训班,学习了化工生产中的安全知识、事故预防及应急处理方法。
同时,我们还学习了精馏装置的基本原理、主要设备和操作流程。
2. 实习过程(1)了解精馏装置在导师的带领下,我们参观了精馏装置现场,了解了精馏塔、加热器、冷却器、泵等主要设备的作用和相互之间的关系。
(2)学习操作流程我们学习了精馏装置的操作流程,包括开车、正常运行、停车等环节。
在操作过程中,我们要严格遵循操作规程,确保设备安全、稳定运行。
(3)操作实践在导师的指导下,我们亲自操作精馏装置。
首先,我们进行了开车操作,包括开启电源、启动泵、调节温度等。
然后,我们进行了正常运行操作,包括调整回流比、控制塔顶和塔底温度等。
最后,我们进行了停车操作,包括关闭电源、停止泵、排放废液等。
(4)数据分析在操作过程中,我们定期采集样品,进行分析。
通过对比理论值和实际值,评估精馏效果,找出操作中存在的问题,并采取措施进行调整。
三、实习收获与反思1. 实习收获通过本次实习,我们掌握了精馏装置的基本操作方法,了解了精馏过程的原理。
同时,我们的团队合作能力、分析问题和解决问题的能力得到了提高。
2. 实习反思在实习过程中,我们认识到理论知识与实际操作的重要性。
只有掌握了扎实的理论知识,才能在实际操作中游刃有余。
此外,我们还意识到在操作过程中要严格遵守操作规程,确保生产安全。
四、总结通过本次精馏装置操作实习,我们对精馏工艺有了更深入的了解,操作技能得到了提升。
我们将以此为契机,继续努力学习,为将来从事相关工作打下坚实基础。
精馏实训实验报告

精馏实训实验报告
实验名称:精馏实训实验报告
实验目的:
通过对精馏实训实验的操作和分析,掌握精馏原理和工艺流程,加深对化工分离技术的理解和掌握,提高实验操作技能和实验报告撰写能力。
实验原理:
精馏是一种化学分离技术,基于液体的不同沸点而进行分离。
在精馏过程中,液体混合物被加热,使其产生汽化并进入冷凝器,被冷却成液态,进一步分离成纯液体。
实验步骤:
1. 将实验设备准备妥当,包括精馏塔、加热装置、冷却器等。
2. 准备洗涤瓶和试管,清洗干净后装入待分离的混合物样品。
3. 开始加热,通过不同气化温度和液态沸点,产生不同的沸点温度,使混合物中的组分分离。
4. 将冷却器中的液体收集起来,观察其纯度和色泽等特征。
实验结果:
通过实验,我们得到了两个不同混合物的分离产物。
通过实验后,我们发现其纯度较高、色泽明亮。
实验分析:
精馏是一种高效的化学分离技术,能够实现高纯度物质的分离,广泛应用于制药、化工、精细化工等领域。
实验结果表明,掌握精馏技术和流程对于提高化工实验能力和实践经验有重要作用。
实验结论:
精馏实训实验结果表明,通过掌握精馏技术和流程对于精细化工的研发和生产具有重要意义。
在实验操作和实验报告撰写方面,也有助于提高实验技能和综合能力。
双塔精馏单元仿真实训报告
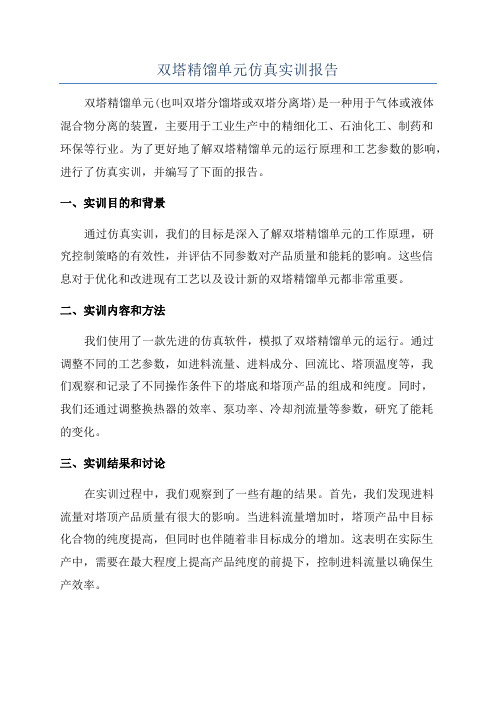
双塔精馏单元仿真实训报告双塔精馏单元(也叫双塔分馏塔或双塔分离塔)是一种用于气体或液体混合物分离的装置,主要用于工业生产中的精细化工、石油化工、制药和环保等行业。
为了更好地了解双塔精馏单元的运行原理和工艺参数的影响,进行了仿真实训,并编写了下面的报告。
一、实训目的和背景通过仿真实训,我们的目标是深入了解双塔精馏单元的工作原理,研究控制策略的有效性,并评估不同参数对产品质量和能耗的影响。
这些信息对于优化和改进现有工艺以及设计新的双塔精馏单元都非常重要。
二、实训内容和方法我们使用了一款先进的仿真软件,模拟了双塔精馏单元的运行。
通过调整不同的工艺参数,如进料流量、进料成分、回流比、塔顶温度等,我们观察和记录了不同操作条件下的塔底和塔顶产品的组成和纯度。
同时,我们还通过调整换热器的效率、泵功率、冷却剂流量等参数,研究了能耗的变化。
三、实训结果和讨论在实训过程中,我们观察到了一些有趣的结果。
首先,我们发现进料流量对塔顶产品质量有很大的影响。
当进料流量增加时,塔顶产品中目标化合物的纯度提高,但同时也伴随着非目标成分的增加。
这表明在实际生产中,需要在最大程度上提高产品纯度的前提下,控制进料流量以确保生产效率。
另外,我们还研究了回流比对分离效率的影响。
当回流比增加时,塔内的液相流动速度增加,分离效率提高。
然而,随着回流比的增加,能耗也显著增加。
因此,在实际操作中,需要找到一个平衡点,以尽可能提高分离效率,并保持合理的能耗水平。
四、结论和建议通过本次仿真实训,我们了解了双塔精馏单元的工作原理和关键参数对产品质量和能耗的影响。
根据实训结果,我们提出了一些建议和改进方案:1.控制进料流量:根据产品纯度和生产效率的要求,合理调整进料流量,以达到最佳性能。
2.优化回流比:找到回流比的平衡点,以提高分离效率和能耗的平衡。
3.定期维护和校准设备:确保换热器、泵和冷却剂等设备处于最佳工作状态,以保证系统性能的稳定和可靠。
另外,我们还注意到本次实训基于理想条件进行模拟,并未考虑到实际生产中的各种因素,如传热传质的限制、潜热和其他非理想性质。
实训报告总结化学精馏

#### 一、实训背景化学精馏作为化工生产中的一种重要单元操作,在石油、化工、医药等领域具有广泛的应用。
为了深入了解化学精馏的原理、过程及操作方法,我们进行了化学精馏实训。
通过本次实训,我们掌握了化学精馏的基本操作技能,加深了对化工生产过程的认知。
#### 二、实训目的1. 理解化学精馏的原理和过程;2. 掌握化学精馏设备的基本操作方法;3. 培养实际操作能力,提高安全意识;4. 增强团队协作能力,提高沟通协调能力。
#### 三、实训内容本次实训主要包括以下内容:1. 化学精馏原理及过程;2. 化学精馏设备介绍;3. 化学精馏操作步骤;4. 化学精馏异常处理及安全注意事项。
#### 四、实训过程1. 理论学习:首先,我们对化学精馏的原理、过程及设备进行了系统学习,了解了精馏的基本概念、操作原理、设备结构及操作方法。
2. 设备参观:随后,我们参观了实训现场,实地了解了精馏塔、冷凝器、再沸器等设备的结构及工作原理。
3. 操作实践:在理论学习和设备参观的基础上,我们开始进行化学精馏操作实践。
具体步骤如下:a. 检查设备状态,确保设备完好;b. 启动设备,进行冷态开车;c. 进料,调整塔内温度、压力等参数;d. 调整回流比,控制塔顶、塔底产品纯度;e. 观察设备运行情况,发现异常及时处理。
4. 异常处理:在实训过程中,我们遇到了一些异常情况,如塔内温度、压力波动等。
通过查阅资料和请教老师,我们学会了如何处理这些异常情况。
5. 总结与反思:实训结束后,我们对本次实训进行了总结和反思,分析了操作过程中存在的问题,并提出了改进措施。
#### 五、实训收获1. 理论知识的巩固:通过本次实训,我们对化学精馏的原理、过程及设备有了更深入的了解,为今后从事相关工作打下了坚实基础。
2. 实际操作能力的提高:在实训过程中,我们掌握了化学精馏的基本操作方法,提高了实际操作能力。
3. 安全意识的增强:通过实训,我们认识到化工生产过程中的安全重要性,增强了安全意识。
化工单元操作仿真实训总结
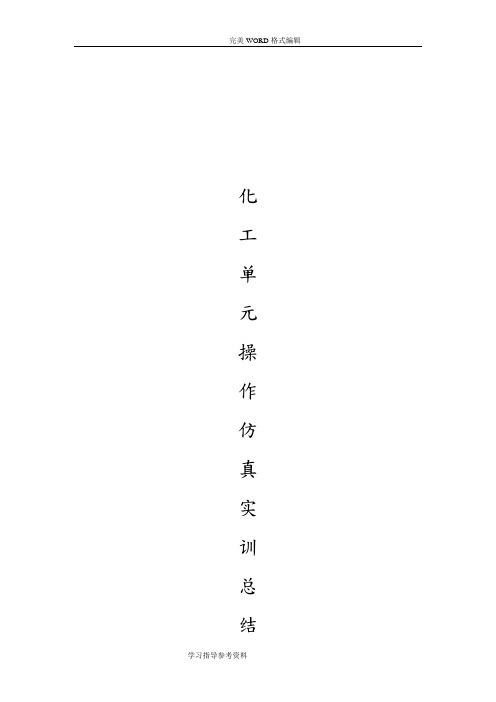
化工单元操作仿真实训总结姓名:XX班级;XX班学号:XXXX目录一、实训内容1、精馏塔仿真2、液位控制仿真3、吸收解吸仿真4、萃取仿真5、灌区仿真6、真空仿真二、仿真总结一、实训内容1、精馏塔仿真1.1操作原理:精馏原理精馏操作迫使混合物的气、液两相在精馏塔体中作逆向流动,在互相接触过程中,液相中的轻组分逐渐转入气相,而气相中的重组分则逐渐进入液相。
精馏过程本质上是一种传质过程,也伴随着传热。
在恒定压力下,对单组分液体在沸腾时继续加热,其温度保持不变。
但对于多组分的理想溶液来说,在恒定压力下,沸腾溶液的温度却是可变的。
一般而言,在恒定压力下,溶液气液相平衡与其组分有关。
高沸点组分的浓度越高,溶液平衡温度越高。
与纯物质的气液平衡相比较,溶液气液平衡的一个特点是:在平衡态下,气相浓度与液相浓度是不相同的。
一般情况下,气相中的低沸点组分的浓度高于它在液相中的数值.对于纯组分的气液相平衡,把恒定压力下的平衡温度称为该压力下的沸点或冷凝点。
但对于处在相平衡的溶液,则把平衡温度称为在该压力下某气相浓度的露点温度或对应的液相浓度的泡点温度。
对于同一气相和液相来说,露点温度与泡点一般是不相等的,前者比后者高。
1.2工艺流程:进料及排放不凝气启动再沸器建立回流调整至正常1.3仿真图:2、液位控制仿真2.1操作原理:缓冲罐V101仅一股来料,8Kg/cm2压力的液体通过调节产供阀FIC101向罐V101充液,此罐压力由调节阀PIC101分程控制,缓冲罐压力高于分程点(5.0Kg/cm2)时,PV101B自动打开泄压,压力低于分程点时,PV101B自动关闭,PV101A自动打开给罐充压,使V101压力控制在5Kg/cm2。
缓冲罐V101液位调节器LIC101和流量调节阀FIC102串级调节,一般液位正常控制在50%左右,自V101底抽出液体通过泵P101A或P101B(备用泵)打入罐V102,该泵出口压力一般控制在9Kg/cm2,FIC102流量正常控制在20000Kg/hr。
双塔精馏单元仿真实训报告

双塔精馏单元仿真实训报告实验目的:1.学习双塔精馏单元的基本原理和工作原理。
2.了解双塔精馏单元的操作过程和优化方法。
3.通过仿真实训,提高学生的实际操作能力和问题解决能力。
实验装置:我们使用了一套虚拟化工厂仿真软件,该软件可以模拟真实的化工装置和操作过程。
双塔精馏单元仿真装置由两个塔和一台加热炉组成。
其中,塔1为粗提塔,塔2为精提塔。
实验步骤:1.设定进料组分和流量,并开启加热炉,使进料加热到所需温度。
2.将加热后的进料引入粗提塔顶部,通过粗提塔内的塔盘进行分离。
塔盘上的液相会向下流动,与上升的蒸汽相进行传质传热,从而实现分离。
3.从粗提塔底部收集出塔床液相产物,以及从塔顶收集出的气相产物。
通过调整收集温度和流量,获取理想的产物组分。
4.将从塔顶收集出的气相产物引入精提塔,进行进一步分离。
精提塔的塔盘和粗提塔相似,但操作条件和设定略有不同。
5.最后,从精提塔底部收集出塔床液相产物和从塔顶收集出的气相产物。
根据实验要求,验证分离效果和产物组分。
实验结果:通过模拟实验,我们成功地实现了双塔精馏单元的分离过程。
在不同的操作条件下,我们获得了不同的产物组分。
通过对产物组分的分析,我们发现随着操作条件的改变,产物组分也发生变化。
在实验过程中,我们还发现了一些问题,如温度的控制、流量的调节等。
通过调整操作条件,我们解决了这些问题,并获得了较好的分离效果。
实验总结:通过该次仿真实训,我们深入了解了双塔精馏单元的原理和操作过程。
同时,我们也发现了一些需要改进的地方。
在以后的学习和实践中,我们将加强对于操作条件和工艺参数的掌握,以实现更好的分离效果。
另外,我们还发现了化工仿真实训的重要性和优势。
通过虚拟仿真实验,我们能够快速理解和掌握复杂的操作过程,大大提高了学习效率。
因此,我们将继续积极参与各类实训,以提升自己的实践能力和问题解决能力。
精馏装置操作实习报告

一、实习目的通过本次精馏装置操作实习,了解精馏装置的基本结构、工作原理和操作流程,掌握精馏过程中的各种参数控制方法,提高化工操作技能,为今后从事化工生产工作打下基础。
二、实习内容1. 精馏装置基本结构及工作原理精馏装置主要由精馏塔、塔釜、塔顶冷凝器、回流罐、原料罐、循环视拌阀、电加热器、回流流量调节阀、塔顶采出流量调节阀等组成。
工作原理是利用不同物质沸点的差异,通过加热、蒸发、冷凝、回流等过程,实现物质的分离。
2. 精馏装置操作流程(1)开车1)开启装置电源、控制电源,启动触摸屏。
2)配好进料液到30V%(体积)的乙醇水溶液,分析出实际浓度,加入原料罐,同时开启原料泵和循环视拌阀VA12使原料混合均匀。
3)打开塔釜加科阀,在塔金加入约10V%(体积)的原料乙醇水溶液,釜液位与塔出料口(也可低于出科口,但液位过低时电加热无法启动)。
4)打开塔顶冷凝器进水阀VA21至最大,流量约7L/min。
5)开启电加热电源,选择加热方式,维持塔釜加热功率在2kW左右合适。
6)打开回流流量调节阀VA04,进行全回流操作。
根据馏分器液位高度调节回流冠回流流量控制在80~150mL/min。
(2)进料稳定阶段1)当塔顶有回流后,维持塔釜压力约0.6~0.7 kPa。
2)全回流操作稳定一定时间后,打开加料泵,将加料流量调至60 mL/min。
3)维持塔顶温度、塔底温度、馏分器液位不变后操作才算稳定。
(3)部分回流1)打开塔顶采出流量调节阀VA03进行部分回流操作,一般情况下回流比控R-L/D4~8范围(此可根据自己情况来定)。
2)分别读取塔顶、塔釜、进料的温度,取样检测酒度,记录相关数据。
3. 精馏装置参数控制(1)温度控制:通过调节加热功率和回流流量,控制塔顶、塔底温度在设定范围内。
(2)压力控制:通过调节回流流量和进料流量,控制塔釜压力在设定范围内。
(3)液位控制:通过调节回流流量和进料流量,控制塔釜液位在设定范围内。
姓名-精馏单元仿真操作实训报告

《化工单元操作技术》仿真实训报告实训项目:精馏单元仿真操作班级:12化工301学号:报告人:王帅林操作成绩:报告成绩:1.精馏工作原理将液体混合物部分气化,利用其中各组分相对挥发度的不同,通过液相和气相间的质量传递来实现对混合物分离。
2. 工艺流程简介本流程是利用精馏方法,在脱丁烷塔中将丁烷从脱丙烷塔釜混合物中分离出来。
将脱丙烷塔釜混合物部分气化,由于丁烷的沸点较低,即其挥发度较高,故丁烷易于从液相中气化出来,再将气化的蒸汽冷凝,可得到丁烷组成高于原料的混合物,经过多次气化冷凝,即可达到分离混合物中丁烷的目的。
原料为67.8℃脱丙烷塔的釜液(主要有C4、C5、C6、C7等),由脱丁烷塔(DA-405)的第16块板进料(全塔共32块板),进料量由流量控制器FIC101控制。
灵敏板温度由调节器TC101通过调节再沸器加热蒸汽的流量,来控制提馏段灵敏板温度,从而控制丁烷的分离质量。
脱丁烷塔塔釜液(主要为C5以上馏分)一部分作为产品采出,一部分经再沸器(EA-418A、B)部分汽化为蒸汽从塔底上升。
塔釜的液位和塔釜产品采出量由LC101和FC102组成的串级控制器控制。
再沸器采用低压蒸汽加热。
塔釜蒸汽缓冲罐(FA-414)液位由液位控制器LC102调节底部采出量控制。
图1 列管换热器DCS流程图图2列管换热器现场图三、主要设备、调节器、各类仪表和阀件1.主要设备2.各类仪表四、实训步骤(一)冷态开车1.进料过程①开FA-408顶放空阀PC101排放不凝气,稍开FIC101调节阀(不超过20%),向精馏塔进料;②进料后,塔内温度略升,压力升高。
当压力PC101升至0.5atm时,关闭PC101调节阀投自动,并控制塔压不超过4.25atm(如果塔内压力大幅波动,改回手动调节稳定压力)。
2.启动再沸器①当压力PC101升至0.5atm时,打开冷凝水PC102调节阀至50%;塔压基本稳定在4.25atm后,可加大塔进料(FIC101开至50%左右);②待塔釜液位LC101升至20%以上时,开加热蒸汽入口阀V13,再稍开TC101调节阀,给再沸器缓慢加热,并调节TC101阀开度使塔釜液位LC101维持在40%-60%。
实训报告心得体会精馏

一、引言精馏是化工领域中一种重要的分离技术,它利用混合物中各组分的沸点差异,通过加热和冷却过程,使混合物分离成各个组分。
本次实训报告以精馏为主题,通过对精馏原理、设备、操作过程等方面的学习,使我对精馏技术有了更深入的了解,现将实训心得体会如下。
二、精馏原理1. 热力学原理:精馏过程基于混合物中各组分的沸点差异,通过加热使低沸点组分蒸发,然后冷凝收集,从而实现分离。
在精馏过程中,混合物中各组分的沸点、蒸汽压、气液平衡等热力学性质起着决定性作用。
2. 分子运动原理:精馏过程中,混合物分子在气液两相之间不断进行热运动和扩散,使低沸点组分向气相转移,高沸点组分向液相转移。
3. 相平衡原理:精馏过程中,混合物在加热和冷却条件下,气液两相达到动态平衡,即气相和液相的组成保持不变。
三、精馏设备1. 精馏塔:精馏塔是精馏过程中的主要设备,其作用是将混合物加热、蒸发、冷凝和分离。
精馏塔分为板式塔、填料塔等类型。
2. 蒸汽发生器:蒸汽发生器用于产生加热混合物的热源,常见的有锅炉、蒸汽发生器等。
3. 冷凝器:冷凝器用于将气相组分冷凝成液相,常见的有冷却水冷凝器、空气冷却器等。
4. 冷却水系统:冷却水系统为冷凝器提供冷却水,保证精馏过程的顺利进行。
5. 控制系统:控制系统用于调节精馏过程中的各项参数,如温度、压力、流量等,确保精馏效果。
四、精馏操作过程1. 原料准备:将混合物加入精馏塔底部,准备加热。
2. 加热:通过蒸汽发生器加热混合物,使低沸点组分蒸发。
3. 蒸汽上升:蒸发后的蒸汽在精馏塔内上升,与塔内液体进行热交换,使高沸点组分留在塔内。
4. 冷凝:上升的蒸汽进入冷凝器,冷凝成液态,收集得到所需组分。
5. 冷却水循环:冷却水在冷凝器中循环,带走热量,降低精馏塔温度。
6. 产品收集:根据组分沸点差异,从精馏塔顶部、中部和底部收集不同组分的产品。
五、实训心得体会1. 理论与实践相结合:通过本次实训,我深刻体会到理论与实践相结合的重要性。
化工单元仿真实习报告

一、实习背景随着我国化工产业的快速发展,化工生产的安全、环保和高效已成为企业关注的焦点。
为了提高化工生产人员的操作技能和安全生产意识,许多高校和科研机构开展了化工单元仿真实习项目。
本次实习旨在通过模拟化工生产过程中的单元操作,让学生了解化工生产的原理、工艺流程、设备操作及安全知识,为今后的实际工作打下坚实基础。
二、实习时间及地点实习时间:2023年X月X日至2023年X月X日实习地点:XX大学化工仿真实验室三、实习内容1. 精馏塔仿真操作(1)学习精馏塔的工作原理和操作流程,掌握精馏塔的工艺参数及影响因素。
(2)通过仿真软件进行精馏塔的操作,实现原料液体的分离。
(3)分析精馏塔的操作数据,优化操作参数,提高分离效果。
2. 吸收/解吸仿真操作(1)学习吸收和解吸过程的原理及影响因素,掌握吸收和解吸设备的操作方法。
(2)通过仿真软件进行吸收和解吸操作,实现气液两相的传质。
(3)分析操作数据,优化操作参数,提高传质效率。
3. 萃取塔仿真操作(1)学习萃取塔的工作原理和操作流程,掌握萃取塔的工艺参数及影响因素。
(2)通过仿真软件进行萃取塔的操作,实现混合物的分离。
(3)分析操作数据,优化操作参数,提高分离效果。
4. 罐区单元仿真操作(1)学习罐区单元的工作原理和操作流程,掌握罐区单元的设备操作方法。
(2)通过仿真软件进行罐区单元的操作,实现物料的储存和输送。
(3)分析操作数据,优化操作参数,提高物料的储存和输送效率。
5. 液位控制仿真操作(1)学习液位控制系统的原理和操作方法,掌握液位控制参数的设置。
(2)通过仿真软件进行液位控制操作,实现液位稳定。
(3)分析操作数据,优化控制参数,提高液位控制效果。
四、实习成果1. 理论知识方面:通过本次实习,我对化工单元操作有了更加深入的了解,掌握了各种单元操作的基本原理、工艺流程、设备操作及安全知识。
2. 实践操作方面:通过仿真软件的操作,提高了我的实际操作能力,为今后从事化工生产工作打下了基础。
精馏塔单元操作实训心得

精馏塔单元操作实训心得
在化工工艺中,精馏塔是一种常见的设备,用于分离液体混合物中的各种组分。
在进行精馏塔单元操作实训的过程中,我收获颇丰,不仅加深了对精馏操作原理的理解,还提升了自己的操作技能。
首先,在实训中我学会了如何正确地操控精馏塔的各种参数,如进料流量、回流比、顶部温度等。
这些参数的调节对于精馏过程的效果起着至关重要的作用,只有在实践中不断调整和优化,才能实现较好的分离效果。
通过手动操作控制面板,我逐渐掌握了如何根据实时数据进行调整,从而达到预期的分离效果。
其次,在实训中我也学会了如何应对突发情况和故障。
精馏塔在长时间运行过程中,难免会出现一些问题,如进料泵失灵、回流比异常等。
在这种情况下,我需要迅速做出反应,找到问题的原因并及时处理,以保证设备的正常运行。
通过实训,我提高了自己的应急处理能力和问题解决能力。
此外,在实训中我还学到了团队合作的重要性。
精馏塔单元操作需要多人协作,每个人都扮演着不同的角色,只有各司其职、密切配合,才能顺利完成操作任务。
在实训中,我与同学们一起分工合作,互相协助,共同完成了一次次的实验,这不仅增强了团队凝聚力,还提升了整体操作效率。
总的来说,精馏塔单元操作实训是我在化工专业学习中的一次重要经历。
通过这次实训,我不仅提升了自己的操作技能,加深了对精馏操作原理的理解,还体会到了团队合作的重要性。
希望在未来的学习和工作中,能够继续保持学习的热情,不断提升自己的专业能力,为将来的发展打下坚实的基础。
酒精精馏操作实训报告
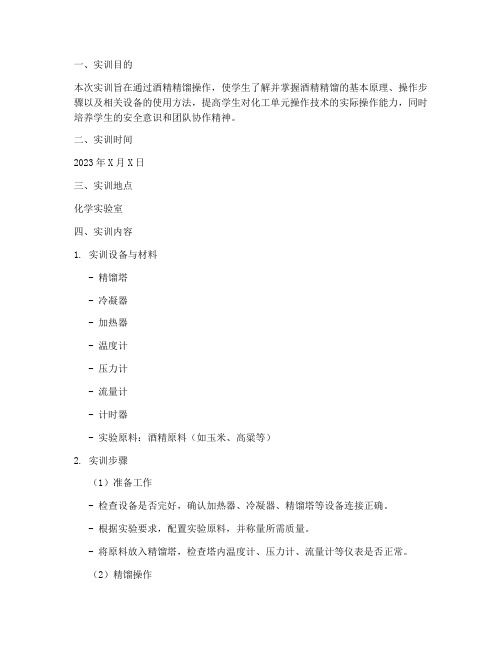
一、实训目的本次实训旨在通过酒精精馏操作,使学生了解并掌握酒精精馏的基本原理、操作步骤以及相关设备的使用方法,提高学生对化工单元操作技术的实际操作能力,同时培养学生的安全意识和团队协作精神。
二、实训时间2023年X月X日三、实训地点化学实验室四、实训内容1. 实训设备与材料- 精馏塔- 冷凝器- 加热器- 温度计- 压力计- 流量计- 计时器- 实验原料:酒精原料(如玉米、高粱等)2. 实训步骤(1)准备工作- 检查设备是否完好,确认加热器、冷凝器、精馏塔等设备连接正确。
- 根据实验要求,配置实验原料,并称量所需质量。
- 将原料放入精馏塔,检查塔内温度计、压力计、流量计等仪表是否正常。
(2)精馏操作- 打开加热器,开始加热原料。
- 观察温度计和压力计,控制加热速度,使原料温度逐渐升高。
- 当原料温度达到一定值时,打开进料阀,使原料开始进入精馏塔。
- 观察精馏塔内液体和蒸汽的变化,调整进料量和加热速度,确保精馏效果。
- 当塔顶温度达到酒精的沸点时,打开塔顶冷凝器,使蒸汽冷凝成液体,收集塔顶馏分。
- 根据实验要求,调整回流比,提高精馏效果。
(3)数据记录与分析- 记录实验过程中温度、压力、流量等数据。
- 分析实验结果,比较实际精馏效果与理论计算值。
(4)实验结束- 关闭加热器,停止加热。
- 清理实验设备,整理实验场地。
五、实训结果与分析1. 实验结果- 通过精馏操作,成功收集到一定量的酒精馏分。
- 实验过程中,温度、压力、流量等数据均在正常范围内。
2. 结果分析- 实验结果表明,酒精精馏操作能够有效地提高酒精的纯度。
- 通过调整加热速度、进料量、回流比等参数,可以优化精馏效果。
六、实训体会1. 理论知识与实践操作相结合通过本次实训,我深刻体会到理论知识与实践操作相结合的重要性。
只有掌握了理论知识,才能在实际操作中游刃有余。
2. 安全意识与团队协作在实验过程中,我严格遵守操作规程,注意安全,并与团队成员密切配合,共同完成实验任务。
精馏塔单元操作实训心得
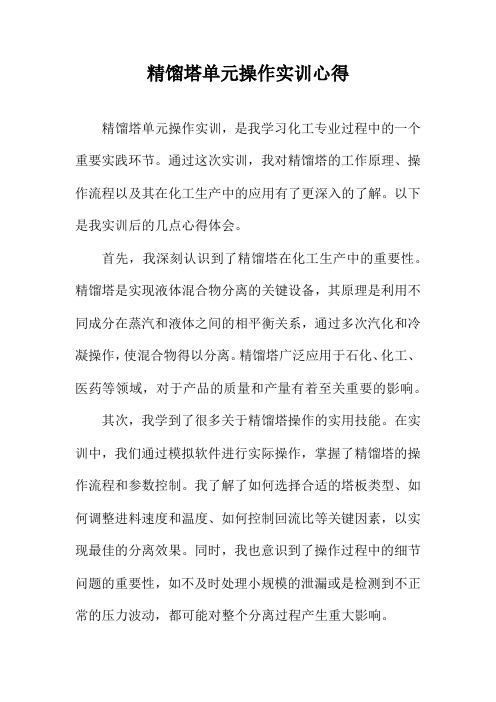
精馏塔单元操作实训心得精馏塔单元操作实训,是我学习化工专业过程中的一个重要实践环节。
通过这次实训,我对精馏塔的工作原理、操作流程以及其在化工生产中的应用有了更深入的了解。
以下是我实训后的几点心得体会。
首先,我深刻认识到了精馏塔在化工生产中的重要性。
精馏塔是实现液体混合物分离的关键设备,其原理是利用不同成分在蒸汽和液体之间的相平衡关系,通过多次汽化和冷凝操作,使混合物得以分离。
精馏塔广泛应用于石化、化工、医药等领域,对于产品的质量和产量有着至关重要的影响。
其次,我学到了很多关于精馏塔操作的实用技能。
在实训中,我们通过模拟软件进行实际操作,掌握了精馏塔的操作流程和参数控制。
我了解了如何选择合适的塔板类型、如何调整进料速度和温度、如何控制回流比等关键因素,以实现最佳的分离效果。
同时,我也意识到了操作过程中的细节问题的重要性,如不及时处理小规模的泄漏或是检测到不正常的压力波动,都可能对整个分离过程产生重大影响。
此外,实训还让我对团队合作有了更深刻的理解。
在精馏塔的模拟操作中,我们小组的成员需要密切配合,共同分析数据、调整参数,以实现稳定高效的分离效果。
每个人都需要发挥自己的专业知识和技能,同时要充分尊重他人的意见和建议,以集体的智慧解决遇到的问题。
这种团队合作的精神,对于我们未来的职业生涯无疑是非常宝贵的。
最后,实训也让我认识到自身的不足之处。
在实际操作中,我发现了自己在理论知识掌握和实际操作能力方面还有很多需要提高的地方。
比如,在处理复杂的分离任务时,如何更快速地调整工艺参数以达到最佳分离效果;在面对突发状况时,如何冷静分析并采取有效的应对措施。
这些都是我在未来的学习和实践中需要进一步努力的方向。
总的来说,这次精馏塔单元操作实训让我收获颇丰。
我不仅学到了很多实用的知识和技能,更重要的是培养了我的实践能力和团队合作精神。
我相信,这次实训的经验和体会将对我未来的学习和工作产生积极的影响。
我会将所学的知识和技能运用到实践中去,不断提升自己的专业素养和能力。
工作报告之精馏仿真实验报告
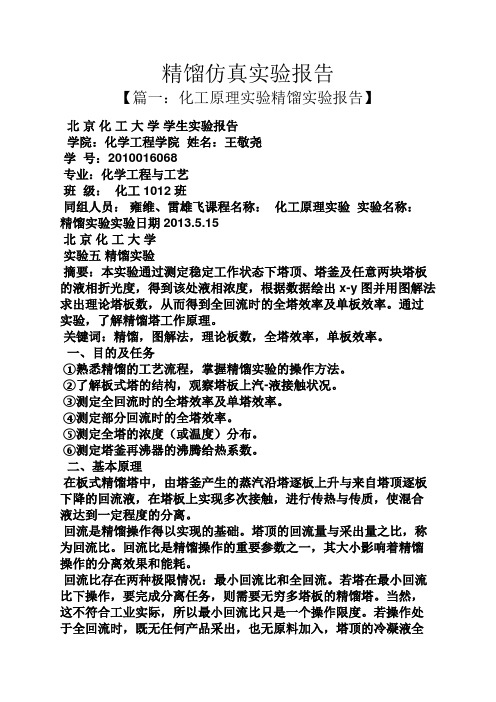
精馏仿真实验报告【篇一:化工原理实验精馏实验报告】北京化工大学学生实验报告学院:化学工程学院姓名:王敬尧学号:2010016068专业:化学工程与工艺班级:化工1012班同组人员:雍维、雷雄飞课程名称:化工原理实验实验名称:精馏实验实验日期2013.5.15北京化工大学实验五精馏实验摘要:本实验通过测定稳定工作状态下塔顶、塔釜及任意两块塔板的液相折光度,得到该处液相浓度,根据数据绘出x-y图并用图解法求出理论塔板数,从而得到全回流时的全塔效率及单板效率。
通过实验,了解精馏塔工作原理。
关键词:精馏,图解法,理论板数,全塔效率,单板效率。
一、目的及任务①熟悉精馏的工艺流程,掌握精馏实验的操作方法。
②了解板式塔的结构,观察塔板上汽-液接触状况。
③测定全回流时的全塔效率及单塔效率。
④测定部分回流时的全塔效率。
⑤测定全塔的浓度(或温度)分布。
⑥测定塔釜再沸器的沸腾给热系数。
二、基本原理在板式精馏塔中,由塔釜产生的蒸汽沿塔逐板上升与来自塔顶逐板下降的回流液,在塔板上实现多次接触,进行传热与传质,使混合液达到一定程度的分离。
回流是精馏操作得以实现的基础。
塔顶的回流量与采出量之比,称为回流比。
回流比是精馏操作的重要参数之一,其大小影响着精馏操作的分离效果和能耗。
回流比存在两种极限情况:最小回流比和全回流。
若塔在最小回流比下操作,要完成分离任务,则需要无穷多塔板的精馏塔。
当然,这不符合工业实际,所以最小回流比只是一个操作限度。
若操作处于全回流时,既无任何产品采出,也无原料加入,塔顶的冷凝液全部返回塔中,这在生产中午实际意义。
但是由于此时所需理论板数最少,又易于达到稳定,故常在工业装置的开停车、排除故障及科学研究时采用。
实际回流比常取最小回流比的1.2~2.0倍。
在精馏操作中,若回流系统出现故障,操作情况会急剧恶化,分离效果也将变坏。
1板效率是体现塔板性能及操作状况的主要参数,有以下两种定义方法。
(1)总板效率ee=n/ne式中e——总板效率;n——理论板数(不包括塔釜);ne——实际板数。
精馏装置操作技术仿真实验报告
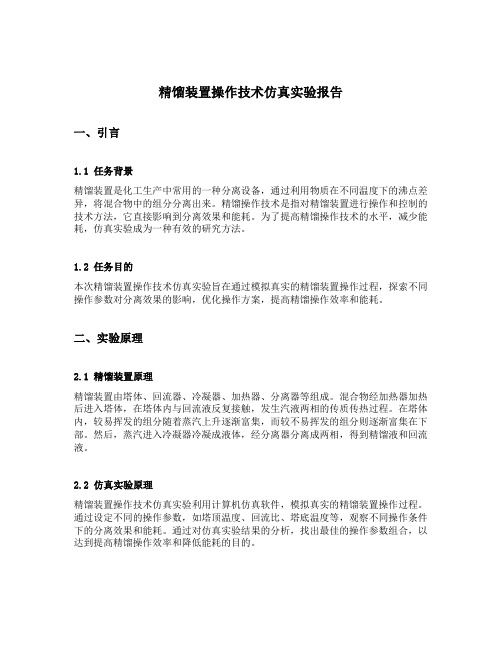
精馏装置操作技术仿真实验报告一、引言1.1 任务背景精馏装置是化工生产中常用的一种分离设备,通过利用物质在不同温度下的沸点差异,将混合物中的组分分离出来。
精馏操作技术是指对精馏装置进行操作和控制的技术方法,它直接影响到分离效果和能耗。
为了提高精馏操作技术的水平,减少能耗,仿真实验成为一种有效的研究方法。
1.2 任务目的本次精馏装置操作技术仿真实验旨在通过模拟真实的精馏装置操作过程,探索不同操作参数对分离效果的影响,优化操作方案,提高精馏操作效率和能耗。
二、实验原理2.1 精馏装置原理精馏装置由塔体、回流器、冷凝器、加热器、分离器等组成。
混合物经加热器加热后进入塔体,在塔体内与回流液反复接触,发生汽液两相的传质传热过程。
在塔体内,较易挥发的组分随着蒸汽上升逐渐富集,而较不易挥发的组分则逐渐富集在下部。
然后,蒸汽进入冷凝器冷凝成液体,经分离器分离成两相,得到精馏液和回流液。
2.2 仿真实验原理精馏装置操作技术仿真实验利用计算机仿真软件,模拟真实的精馏装置操作过程。
通过设定不同的操作参数,如塔顶温度、回流比、塔底温度等,观察不同操作条件下的分离效果和能耗。
通过对仿真实验结果的分析,找出最佳的操作参数组合,以达到提高精馏操作效率和降低能耗的目的。
三、实验步骤3.1 设定初始参数首先,需要设定初始参数,包括初始塔顶温度、回流比、塔底温度等。
根据实际情况和仿真实验的目的,选择合适的初始参数。
3.2 进行仿真实验在设定好初始参数后,开始进行仿真实验。
通过计算机仿真软件,模拟真实的精馏装置操作过程。
观察实验结果,记录下各个操作参数的数值和分离效果。
3.3 分析实验结果根据实验结果,对各个操作参数进行分析。
比较不同操作参数下的分离效果和能耗,找出最佳的操作参数组合。
3.4 优化操作方案根据分析结果,优化操作方案。
调整操作参数,使得分离效果更好,能耗更低。
四、实验结果与分析4.1 实验结果根据仿真实验的结果,得到了不同操作参数下的分离效果和能耗数据。
精馏仿真实验报告
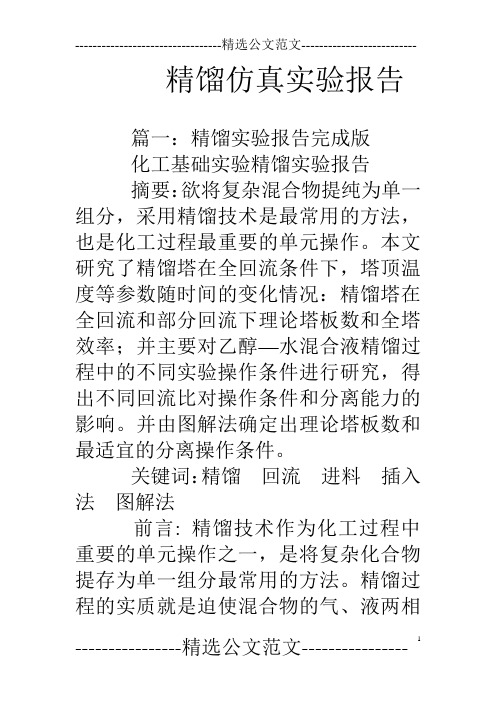
精馏仿真实验报告篇一:精馏实验报告完成版化工基础实验精馏实验报告摘要:欲将复杂混合物提纯为单一组分,采用精馏技术是最常用的方法,也是化工过程最重要的单元操作。
本文研究了精馏塔在全回流条件下,塔顶温度等参数随时间的变化情况:精馏塔在全回流和部分回流下理论塔板数和全塔效率;并主要对乙醇—水混合液精馏过程中的不同实验操作条件进行研究,得出不同回流比对操作条件和分离能力的影响。
并由图解法确定出理论塔板数和最适宜的分离操作条件。
关键词:精馏回流进料插入法图解法前言: 精馏技术作为化工过程中重要的单元操作之一,是将复杂化合物提存为单一组分最常用的方法。
精馏过程的实质就是迫使混合物的气、液两相在塔体中作逆向流动,利用混合液中各组分具有不同的挥发度,在相互接触的过程中,液相中的轻组分转入气相,而气相中的重组分则逐渐进入液相,从而实现液体混合物的分离。
目前发展了膜分离法、吸附分离法和萃取法等分离技术,但其生产操作都产生大量废物,因此通常采用精馏法实现物质分离,而且从技术和经济上考虑,精馏法也是最有价值的。
在实际生产应用时,精馏操作首先需要解决的是精馏塔操作问题。
本文就此研究了全回流和部分回流条件下理论塔板数和全塔效率,同时对不同回流比对操作条件和分离能力的影响,采用图解法求取全回流和不同回流比下部分回流理论塔板数。
通过等板高度(HETP)的大小来评价填料塔的分离能力,并找出最优进料量及回流比,等板高度越小,填料层的传质分离效果越好。
对解决化工生产实际问题有重要意义。
1.实验部分基本原理填料塔属连续接触式传质设备,填料精馏塔与板式精馏塔的不同之处在于塔内气液相浓度前者呈连续变化,后者层逐级变化。
等板高度(HETP)是衡量填料精馏塔分离效果的一个关键参数,等板高度越小,填料层的传质分离效果就越好。
1.等板高度(HETP)HETP是指与一层理论塔板的传质作用相当的填料层高度。
它的大小,不仅取决于填料的类型、材质与尺寸,而且受系统物性、操作条件及塔设备尺寸的影响。
精馏实训报告(2)

精馏实训报告(2)前言为了更好地掌握化学实验技能,提高实验操作水平,本次实训进行了精馏实验。
精馏是一种分离混合物或提纯化合物的重要实验方法,也是化学实验室中常见的操作手段。
本次实训主要研究了精馏法的基本原理和操作流程,同时也了解了一些常见的精馏设备及其使用方法。
一、实验目的1. 掌握精馏法的工作原理和操作流程。
2. 了解常见的精馏设备及其使用方法。
3. 探究纯化液体混合物的最佳精馏条件。
二、实验原理精馏是一种物理手段,是将混合物分离为其组分的过程。
精馏所依据的原理是不同物质的沸点不同,相同物质沸点相同。
当开瓶后放入一个混合物,加热后其中的挥发性成分沸腾,蒸馏出,通过冷凝管冷凝而得到单独的纯质。
在实践中,精馏有两种形式:简单精馏和分馏。
简单精馏主要应用于纯化不易分离或具有不同沸点组分的混合物。
而分馏主要应用于单个混合物中各组分沸点差异较大的情况。
三、实验步骤1. 将装有可调温电热器的精馏烧瓶放在三角架上。
2. 在烧瓶中倒入待纯化的混合物。
3. 将带冷却水管的冷却管插入烧瓶的接口中,将水管接到自来水源上。
4. 将托盘放在冷却管末端,以便收集冷凝的物质。
5. 开始升温,控制加热速率,直至混合物沸腾稳定。
同时,注意调节冷却水温度,使冷却水保持温度不变。
6. 在冷凝管内观察沸腾状况,当颜色和质地发生变化时,表示馏出其他组分,注意收集得到的混合物。
7. 精馏结束后,关闭电热器和自来水源,将得到的纯净化合物分装存储。
四、实验设备和仪器1. 精馏烧瓶:用于加热混合物。
2. 冷却管:用来冷却蒸汽,使其凝结为液体。
3. 托盘:收集凝结的混合物。
4. 可调温电热器。
五、实验数据处理本次实验中,我们实验室使用精馏设备对苯甲酸-对乙醇混合物进行了分离和提纯的实验。
实验结果如下表:| 组分 | 初沸点/℃ | 终沸点/℃ || 苯甲酸 | 122.3 | 122.9 || 对乙醇 | 78.4 | 78.9 |从实验结果可以看出,最终得到的苯甲酸和乙醇均呈透明无色表面光滑的液体。
精馏塔单元操作实训报告
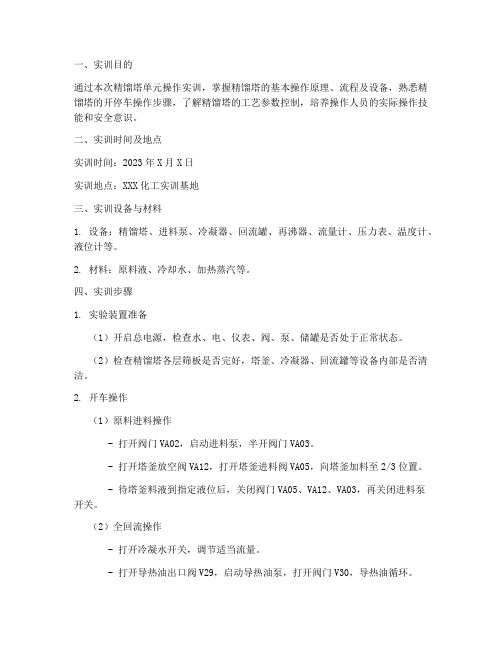
一、实训目的通过本次精馏塔单元操作实训,掌握精馏塔的基本操作原理、流程及设备,熟悉精馏塔的开停车操作步骤,了解精馏塔的工艺参数控制,培养操作人员的实际操作技能和安全意识。
二、实训时间及地点实训时间:2023年X月X日实训地点:XXX化工实训基地三、实训设备与材料1. 设备:精馏塔、进料泵、冷凝器、回流罐、再沸器、流量计、压力表、温度计、液位计等。
2. 材料:原料液、冷却水、加热蒸汽等。
四、实训步骤1. 实验装置准备(1)开启总电源,检查水、电、仪表、阀、泵、储罐是否处于正常状态。
(2)检查精馏塔各层筛板是否完好,塔釜、冷凝器、回流罐等设备内部是否清洁。
2. 开车操作(1)原料进料操作- 打开阀门VA02,启动进料泵,半开阀门VA03。
- 打开塔釜放空阀VA12,打开塔釜进料阀VA05,向塔釜加料至2/3位置。
- 待塔釜料液到指定液位后,关闭阀门VA05、VA12、VA03,再关闭进料泵开关。
(2)全回流操作- 打开冷凝水开关,调节适当流量。
- 打开导热油出口阀V29,启动导热油泵,打开阀门V30,导热油循环。
- 打开导热油罐加热开关,调节加热功率,对导热油进行加热,并通过再沸器给精馏塔提供热量,保持塔釜加热功率维持稳定。
- 开启加热后,每隔五分钟记录一次实验数据(温度、压力、液位、加热功率),实时观测塔内现象。
- 待回流罐有一定料液后,打开回流泵开关,调节回流转子流量计流量,维持回流罐内液位恒定,记录液位恒定后回流转子流量计读数。
(3)部分回流操作- 打开阀门VA02,启动进料泵开关,半开阀门VA03。
- 打开阀门VA08,打开任意一个进料板阀门(根据计算所得),打开进料转子流量计。
3. 实验数据记录与分析(1)记录塔釜、冷凝器、回流罐等设备的温度、压力、液位等参数。
(2)记录回流比、进料量、塔顶、塔底产品量等参数。
(3)分析实验数据,判断精馏塔的分离效果。
4. 停车操作(1)关闭回流泵、进料泵、导热油泵等设备。
- 1、下载文档前请自行甄别文档内容的完整性,平台不提供额外的编辑、内容补充、找答案等附加服务。
- 2、"仅部分预览"的文档,不可在线预览部分如存在完整性等问题,可反馈申请退款(可完整预览的文档不适用该条件!)。
- 3、如文档侵犯您的权益,请联系客服反馈,我们会尽快为您处理(人工客服工作时间:9:00-18:30)。
《化工单元操作技术》仿真实训报告实训项目:精馏单元仿真操作班级:12化工301学号:报告人:王帅林操作成绩:报告成绩:1.精馏工作原理将液体混合物部分气化,利用其中各组分相对挥发度的不同,通过液相和气相间的质量传递来实现对混合物分离。
2. 工艺流程简介本流程是利用精馏方法,在脱丁烷塔中将丁烷从脱丙烷塔釜混合物中分离出来。
将脱丙烷塔釜混合物部分气化,由于丁烷的沸点较低,即其挥发度较高,故丁烷易于从液相中气化出来,再将气化的蒸汽冷凝,可得到丁烷组成高于原料的混合物,经过多次气化冷凝,即可达到分离混合物中丁烷的目的。
原料为67.8℃脱丙烷塔的釜液(主要有C4、C5、C6、C7等),由脱丁烷塔(DA-405)的第16块板进料(全塔共32块板),进料量由流量控制器FIC101控制。
灵敏板温度由调节器TC101通过调节再沸器加热蒸汽的流量,来控制提馏段灵敏板温度,从而控制丁烷的分离质量。
脱丁烷塔塔釜液(主要为C5以上馏分)一部分作为产品采出,一部分经再沸器(EA-418A、B)部分汽化为蒸汽从塔底上升。
塔釜的液位和塔釜产品采出量由LC101和FC102组成的串级控制器控制。
再沸器采用低压蒸汽加热。
塔釜蒸汽缓冲罐(FA-414)液位由液位控制器LC102调节底部采出量控制。
图1 列管换热器DCS流程图图2列管换热器现场图三、主要设备、调节器、各类仪表和阀件1.主要设备2.各类仪表四、实训步骤(一)冷态开车1.进料过程①开FA-408顶放空阀PC101排放不凝气,稍开FIC101调节阀(不超过20%),向精馏塔进料;②进料后,塔内温度略升,压力升高。
当压力PC101升至0.5atm时,关闭PC101调节阀投自动,并控制塔压不超过4.25atm(如果塔内压力大幅波动,改回手动调节稳定压力)。
2.启动再沸器①当压力PC101升至0.5atm时,打开冷凝水PC102调节阀至50%;塔压基本稳定在4.25atm后,可加大塔进料(FIC101开至50%左右);②待塔釜液位LC101升至20%以上时,开加热蒸汽入口阀V13,再稍开TC101调节阀,给再沸器缓慢加热,并调节TC101阀开度使塔釜液位LC101维持在40%-60%。
待FA-414液位LC102升至50%时,并投自动,设定值为50%。
3.建立回流随着塔进料增加和再沸器、冷凝器投用,塔压会有所升高。
回流罐逐渐积液。
①塔压升高时,通过开大PC102的输出,改变塔顶冷凝器冷却水量和旁路量来控制塔压稳定;②当回流罐液位LC103升至20%以上时,先开回流泵GA412A/B的入口阀V19,再启动泵,再开出口阀V17,启动回流泵;③通过FC104的阀开度控制回流量,维持回流罐液位不超高,同时逐渐关闭进料,全回流操作。
4.调整至正常①当各项操作指标趋近正常值时,打开进料阀FIC101;②逐步调整进料量FIC101至正常值;③通过TC101调节再沸器加热量使灵敏板温度TC101达到正常值;④逐步调整回流量FC104至正常值;⑤开FC103和FC102出料,注意塔釜、回流罐液位;⑥将各控制回路投自动,各参数稳定并与工艺设计值吻合后,投产品采出串级。
(二)正常停车操作1.降负荷①逐步关小FIC101调节阀,降低进料至正常进料量的70%;②在降负荷过程中,保持灵敏板温度TC101的稳定性和塔压PC102的稳定,使精馏塔分离出合格产品;③在降负荷过程中,尽量通过FC103排出回流罐中的液体产品,至回流罐液位LC104在20%左右;④在降负荷过程中,尽量通过FC102排出塔釜产品,使LC101降至30%左右。
2.停进料和再沸器在负荷降至正常的70%,且产品已大部采出后,停进料和再沸器。
①关FIC101调节阀,停精馏塔进料;②关TC101调节阀和V13或V16阀,停再沸器的加热蒸汽;③打开塔釜泄液阀V10,排不合格产品,并控制塔釜降低液位;④关FC102调节阀和FC103调节阀,停止产品采出;⑤手动打开LC102调节阀,对FA-114泄液。
3.停回流①停进料和再沸器后,回流罐中的液体全部通过回流泵打入塔,以降低塔内温度;②当回流罐液位至0时,关FC104调节阀,关泵出口阀V17(或V18),停泵GA412A(或GA412B),关入口阀V19(或V20),停回流;③开泄液阀V10排净塔内液体。
4.降压、降温①打开PC101调节阀,将塔压降至接近常压后,关PC101调节阀;②全塔温度降至50℃左右时,关塔顶冷凝器的冷却水(PC102的输出至0)。
(三)正常运行管理和事故处理操作1.正常操作2.事故处理1.热蒸汽压力过高原因:热蒸汽压力过高。
现象:加热蒸汽的流量增大,塔釜温度持续上升。
处理:适当减小TC101的阀门开度。
2.热蒸汽压力过低原因:热蒸汽压力过低。
现象:加热蒸汽的流量减小,塔釜温度持续下降。
处理:适当增大TC101的开度。
3.冷凝水中断原因:停冷凝水。
现象:塔顶温度上升,塔顶压力升高。
处理:(1)开回流罐放空阀PC101保压;(2)手动关闭FC101,停止进料;(3)手动关闭TC101,停加热蒸汽;(7)当回流罐液位为0时,关闭FIC104;(8)关闭回流泵出口阀V17/V18;(11)待塔釜液位为0时,关闭泄液阀V10;(12)待塔顶压力降为常压后,关闭冷凝器。
4.停电原因:停电。
现象:回流泵GA412A停止,回流中断。
处理:(1)手动开回流罐放空阀PC101泄压;(2)手动关加热蒸汽阀TC101;(3)开塔釜排液阀V10和回流罐泄液阀V23,排不合格产品;(4)手动打开LIC102,对FA114泄液;(5)当回流罐液位为0时,关闭V23;(6)关闭回流泵出口阀V17/V18(7)待塔顶压力降为常压后,关闭冷凝器。
(8)手动关进料阀FIC101;(9)手动关出料阀FC102和FC103;5.回流泵故障原因:回流泵GA-412A泵坏。
现象:GA-412A断电,回流中断,塔顶压力、温度上升。
处理:(1)开备用泵入口阀V20;(2)启动备用泵GA412B;(3)开备用泵出口阀V18;(4)关闭运行泵出口阀V17;(5)停运行泵GA412A;(6)关闭运行泵入口阀V19。
6.回流控制阀FC104阀卡原因:回流控制阀FC104阀卡。
现象:回流量减小,塔顶温度上升,压力增大。
处理:打开旁路阀V14,保持回流。
7.低压蒸汽停原因:停蒸汽。
现象:灵敏板温度、塔釜温度下降。
处理:(1)手动开回流罐放空阀PC101泄压;(2)手动关进料阀FIC101;(3)手动关出料阀FC102和FC103;(4)开塔釜排液阀V10和回流罐泄液阀V23,排不合格产品;(5)手动关加热蒸汽阀TC101;(6)手动打开LIC102,对FA114泄液;(7)当回流罐液位为0时,关闭V23;(8)关闭回流泵GA424A/GA424B;(9)关闭回流泵出口阀V17/V18;(10)关闭回流泵入口阀V19/V20;(11)待塔釜液位为0时,关闭泄液阀V10;(12)待塔顶压力降为常压后,关闭冷凝器。
8.塔釜出料调节阀FV102阀卡原因:塔釜出料调节阀FV102阀卡。
现象:塔釜产品无法采出。
处理:(1)将FC102关闭;(2)打开FC102的旁路阀V12,维持塔釜液位在50%。
9.再沸器严重结垢原因:再沸器严重结垢。
现象:塔釜温度降低。
处理:(1)打开备用再沸器EA408B蒸汽入口阀V16;(2)关闭再沸器EA408A蒸汽入口阀V13。
10.仪表风停原因:仪表风管线破裂。
现象:各调节阀、电磁阀不能有效运行。
处理:(1)打开FV101旁通阀V12;(2)打开TV101旁通阀V35;(3)打开LV102旁通阀V38;(4)打开FV102旁通阀V50;(5)打开PV102A旁通阀V15;(6)打开FV104旁通阀V14;(7)打开FV103旁通阀V11;(8)关闭气闭阀PV102A、PV101。
12.进料压力突然增大原因:进料量突然增加。
现象:塔的压力升高、温度降低。
处理:(1)将FIC101投自动;(2)调节FV101,使原料液进料达到正常值14056KG\H后投自动。
13.再沸器积水原因:FA414液位过高。
现象:再沸器出口温度降低,塔釜温度降低。
处理:(1)调节LV102,降低FA414的液位;(2)当灌FA414液位维持在50%左右,投自动,设定值为50%。
14.回流灌液位超高原因:FC103流量降低。
现象:回流灌液位超高。
处理:(1)将FC103设为手动模式,开大阀FV102;(2)打开备用泵GA412B前阀V20,开度50%;(3)启动备用泵GA412B;(4)打开备用泵GA412B后阀V18,开度50%;(5)将FC104设为手动模式;(6)当FA412B液位接近正常液位后,关闭泵GA412B后阀V18;(7)LC103稳定在50%后,FC103设为串级;(8)FC104Z最后稳定在14056KG/H后,将FC104设为自动,设定值为9664KG/H。
15.塔釜轻组分含量偏高原因:回流阀FV104流量高。
现象:塔釜轻组分含量偏高。
处理:(1)手动调节回流阀FV104;(2)当回流流量稳定在9664KG/H时,将FC104投自动,设定值为14056KG/H。
16.原料液进料调节阀卡原因:调节阀损坏。
现象:进料流量降低。
处理:(1)将FIC101设为手动模式;(2)关闭FIC101前截止阀V11;(3)关闭FIC101后止阀V31;(4)打开FIC101旁路阀V32,维持塔釜液位。
五、心得体会本流程是利用物质的沸点不同,把沸点低的先蒸馏出来,在设备运行的时候还要考虑设备的负荷,如果超负荷运行很有可能会发生一些必要的事故,在停车的时候应该先降负荷,然后在停止设备的运行,过程虽然繁琐单易于控制,同时在操作的同时要以严谨的太土来操作,这样减少一些不必要的损失。