骨架变形的原因分析及其控制措施
吊顶工程质量通病及防治措施

轻钢龙骨吊顶工程1、施工准备(1)技术准备编制轻钢骨架罩面板顶棚工程施工方案,并对工人进行书面技术及安全交底。
(2)材料要求1)轻钢骨架主件为大、中、小龙骨;配件有吊挂件、连接件、插接件。
2)零配件:有吊杆、膨胀螺栓、铆钉。
3)按设计要求选用罩面板,其材料品种、规格、质量应符合设计要求。
(3)作业条件1)吊顶工程在施工前应熟悉施工图纸及设计说明。
2)吊顶工程在施工前应熟悉现场。
A、施工前按设计要求对房间的净高、洞口标高和吊顶内的管道、设备及其支架的标高进行交接验收。
B、对吊顶内的管道、设备的安装及水管试压进行验收。
C、检查材料进场验收记录和复验报告、技术交底记录。
3)吊顶工程在施工中应做好各项施工记录,收集好各种有关文件。
A、进场验收记录和复验报告、技术交底记录。
B、材料的产品合格证书、性能检测报告。
4)安装面板前应完成吊顶内管道和设备的调试及验收。
2、关键质量要点(1)材料的关键要求1)按设计要求选用龙骨及配件和罩面板,材料品种、规格、质量应符合设计要求。
2)吊顶工程中的预埋件、钢筋吊杆和型钢吊杆应进行防锈处理。
(2)技术关键要求弹线必须准确,经复验后方可进行下道工序。
安装龙骨应平直牢固,龙骨间距和起拱高度应在允许范围内。
(3)质量关键要求1)吊顶龙骨必须牢固、平整:利用吊杆或吊筋螺栓调整拱度。
安装龙骨时应严格按放线的水平标准线和规方线组装周边骨架。
受力节点应装订严密、牢固、保证龙骨的整体钢度。
龙骨的尺寸应符合设计要求,纵横拱度均匀,互相适应。
吊顶龙骨严禁有硬弯,如有必须调直再进行固定。
2)吊顶面层必须平整:施工前应弹线,中间按平线起拱。
长龙骨的接长应采用对接,经检查合格后再安装饰面板。
吊件必须安装牢固,严禁松动变形。
龙骨分格的几何尺寸必须符合设计要求和饰面板块的模数。
饰面板的品种、规格符合设计要求,外观质量必须符合材料技术标准的规格。
3)大于3kg的重型灯具、电扇及其他重型设备严禁安装在吊顶工程的龙骨上。
轻钢龙骨纸面石膏板吊顶板缝开裂变形的原因及对策

轻钢龙骨纸面石膏板吊顶板缝开裂变形的原因及对策摘要:轻钢龙骨纸面石膏板吊顶是当前应用十分广泛的一种吊顶技术,不仅整体吊顶质量相对较轻,而且强度和抗震防尘性能等都相对较好,此外还具有一定恒温、隔音功能,得到了用户的喜爱和认可。
但与此同时,轻钢龙骨纸面石膏板吊顶在实际施工过程中比较容易受到施工技术、环境等方面的影响,进而出现质量问题,因此,为保障吊顶质量,加强对其施工技术的分析和探讨是十分有必要的。
关键词:轻钢龙骨纸面石膏板吊顶;板缝开裂变形;原因及对策1施工工艺1.1基层处理吊顶施工前将所有的管道洞口封堵处清理干净,以及顶上的杂物清理干净。
1.2测量放线根据每个房间的水平控制线确定吊顶标高线,并在墙顶上弹出吊顶龙骨线作为安装的标准线,以及在标准线上划好龙骨分档间距位置线。
1.3安装吊杆根据施工设计图纸与现场情况确定吊杆的大小和位置,吊点间距为900mm~1200mm,吊杆间距不超过1200mm,吊杆采用Φ8镀锌钢筋,在吊杆安装前必须先刷防锈漆。
按照主龙骨位置及吊挂间距,用膨胀螺栓与楼板连接固定。
在吊杆长度大于1.5m时,应设置反向支撑,采用40*40*4mm的热镀锌角钢,当吊杆长度大于3m时,还应设置转化层。
1.4安装主龙骨吊顶可采用50*15*1.2mm主龙骨,吊顶主龙骨间距为900~1200mm,沿房间短向布置。
在主龙骨上安装吊挂件,将组装好吊挂件的主龙骨,按分档线位置将吊挂件穿入相应的吊杆螺栓,主龙骨相接处装好连接件,拉线调整标高、起拱和平直。
洞口处附加主龙骨,按设计相应节点构造,设置连接卡固件。
主龙骨吊顶间距,应按设计推荐系列选择,中间部分应起拱,起拱高度应不小于房间短向跨度1/200。
吊杆距主龙骨端部不得超过300mm,否则应增设吊杆,次龙骨应贴紧主龙骨安装。
1.5安装次龙骨吊顶可采用50*19*0.5mm次龙骨,次龙骨间距一般为30mm与40mm,按已弹好的次龙骨分档线,卡放次龙骨吊挂件,将次龙骨固定在主龙骨上,两条相邻次龙骨端头接缝不能在一条直线上,注意在吊灯、窗帘盒、通风口周围必须加设次龙骨。
挡土墙、拱形骨架外观质量控制作业指导书
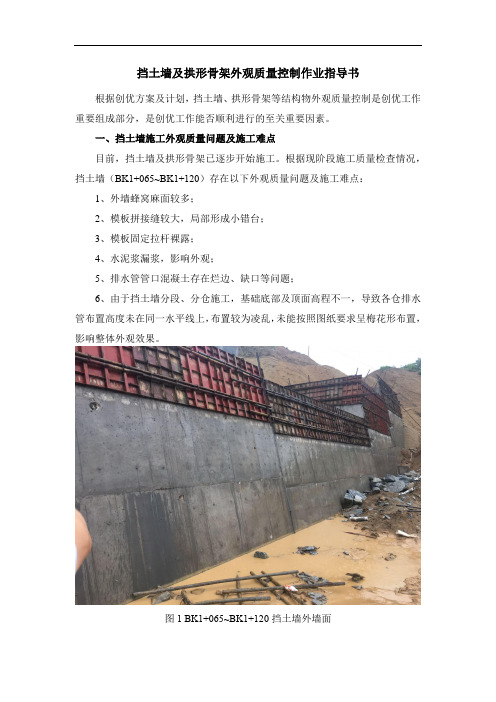
挡土墙及拱形骨架外观质量控制作业指导书根据创优方案及计划,挡土墙、拱形骨架等结构物外观质量控制是创优工作重要组成部分,是创优工作能否顺利进行的至关重要因素。
一、挡土墙施工外观质量问题及施工难点目前,挡土墙及拱形骨架已逐步开始施工。
根据现阶段施工质量检查情况,挡土墙(BK1+065~BK1+120)存在以下外观质量问题及施工难点:1、外墙蜂窝麻面较多;2、模板拼接缝较大,局部形成小错台;3、模板固定拉杆裸露;4、水泥浆漏浆,影响外观;5、排水管管口混凝土存在烂边、缺口等问题;6、由于挡土墙分段、分仓施工,基础底部及顶面高程不一,导致各仓排水管布置高度未在同一水平线上,布置较为凌乱,未能按照图纸要求呈梅花形布置,影响整体外观效果。
图1 BK1+065~BK1+120挡土墙外墙面二、挡土墙外观质量控制措施针对以上问题,制定以下防治措施,用以指导后续施工:1、蜂窝麻面较多问题:(1)成因分析由于我部采用商品混凝土泵送入仓方法施工,可排除塌落度过小、配合比不合理及下料高度过大造成骨料离析等问题;经分析主要存在以下原因:a.模板漏浆或振捣过度,跑浆严重导致出现蜂窝;b.振捣不足,使混凝土不均匀、不密实、和易性差,造成局部浆液较少,或混凝土内气泡未能排出,导致蜂窝。
(2)预防措施a.浇筑前,检查并嵌填模板拼缝,以免浇筑过程跑浆;b.浇筑前,浇水湿润模板,以免混凝土水分被模板吸走;c.振捣工具的性能必须与混凝土工作强度相适应;振捣工人需精心振捣,尤其加强模板边角和结合部位的振捣;d.下料应分层下料,分层振捣,防止漏振;e.振捣是遵守应快插慢拔原则,振捣时间宜为20S为佳,插入下层5~10cm,振捣应在混凝土表面不泛浆、不冒泡、混凝土不再下沉时可停止振捣;f.浇筑过程应随时检查模板支撑情况,防止漏浆。
2、模板拼接缝较大,局部错台、漏浆问题(1)成因分析错台混凝土分缝处上下层错开一定距离,形成台阶或明显缝迹;经分析主要存在以下问题:a.模板设计不合理,安装模板时加固不牢,或在浇筑过程中不注意跟进调整,使模板间产生相对错动;b.模板下部与老混凝土搭接不严密或不牢靠,留下缝隙,引起浇筑时漏浆,造成错台。
纸面石膏板接缝开裂和变形的原因及控制措施

1 轻钢龙骨骨架结构的设计和施工影响 . 2
架不平整 , 石膏板安装在龙骨 上就会产生内应力, 内应
一
8 — 9
维普资讯
建筑与装饰
广东建材 20 年第 1 06 期
要合理错位。对隔墙的接点也同样 力在释 放 的过稗 中必然 导致 板接 缝 处丌裂 。所 以, 设计 在一条直线位置 上,
轻钢龙骨 的刚度和直线度不够, 间距不 膏中添加水, 再次形成二水石膏结构的重要特性 。它从 起变形和裂缝; 必会产 生 开裂变 形 。 石膏 浆 中 分离 出呈 针 毡 状结 晶体 , 卜 过 程 中 , 成 当 , 在 燥 形
了微 孔 , 石 膏建 材 具 有 “ 膏 呼 吸 ” 性 , 使 石 特 即在 空气 湿 度变 化 时 , 以吸 收湿 气 , 可 也能迅 速 地再散 发 出去 。
纸 面 石 膏板 的 构造 是 以石 青芯 子 与护面 纸 牢 吲 地 粘 合在 一起 的板 材 。护面 纸起 到承 受 拉力和 加 固作用 , 护 面纸 层对 板 材质 量 有 很 人 的影 响 ,粘 贴 不牢 的板 材 是不 能使 用 的。面纸 纵横 _向纤维 的强度与 弹性 一 , J 纵 向比横 向大些 , 向的抗 弯和抗 变 形能 力也 强些 。 纵
加强 , 工工 艺也有 差 异 ; 工季 节和 环境 一 。因此 , 施 施 如何 把握 住嵌 缝 工 艺是 十分 重要 的。
1 施工不按顺序、 . 4 不注意成品保护的影响
常 见 当嵌 缝 工序 完成 后 ,甚 至墙 纸 涂 料 贴刷 完 毕 后 , 内吊顶上 的水 、 风 等 安装 作 业 尚未 完 成 , 墙 电、 安装
纸面石膏板具有较强的抗湿性,纸面层可延 长板 人员踩在龙骨架上或把 己固定 的板橇动 ,都会造成接 甚 吸入 水 的 时 间 ,但 并 不 能 阻 止吸水 。在 安装 施 工 过 程 缝 开裂 , 至 使板 面 变形 。有 的 吊顶 设计 是 不上 人 的 , 些 操 作 人 员还 踩在 次 龙骨 上 , 骨 架变 形 产 生挠 度 , 使 中, 于较长时问或连续受潮浸湿 , 对, 会 降低 。因此 , 潮湿 的板 材 决不能 施 工安装 。但 受潮 的 这种情况尤其在抢进度工程屡见不鲜 , 板材 经通 风 干燥 后 ,其 强度 和 抗变 形 能 力 仍 可得 以恢 予 以克 服 。
桥梁结构常见质量问题原因分析及处理措施

桥梁结构常见质量问题原因分析及处理措施第一节下部工程【桩基础】一、如何防治钻孔灌注桩发生偏斜?1、质量问题及现象1)成孔后不垂直,偏差值大于规定的L/100。
2)钢筋笼不能顺利入孔。
2、原因分析1)钻机未处于水平位置,或施工场地未整平及压实,在钻进过程中发生不均匀沉降.2)水上钻孔平台基底座不稳固、未处于水平状态,在钻孔过程中,钻机架发生不均匀变形.3)钻杆弯曲,接头松动,致使钻头晃动范围较大。
4)在旧建筑物附近钻孔过程中遇到障碍物,把钻头挤向一侧。
5)土层软硬不均,致使钻头受力不均,或遇到孤石,探头石等。
3、预防措施1)钻机就位前,应对施工现场进行整平和压实,并把钻机调整到水平状态,在钻进过程中,应经常检查使钻机始终处于水平状态工作。
水上钻机平台在钻机就位前,必须进行安装验收,其平台要牢固、水平、钻机架要稳定.2)应使钻机顶部的起重滑轮槽、钻杆的卡盘和护筒桩位的中心在同一垂直线上,并在钻进过程中防止钻机移位或出现过大的摆。
3)在旧建筑物附近施工时,应提前做好探测,如探测过程中发现障碍物,应采用冲击钻进行施工。
4)要经常对钻杆进行检查,对弯曲的钻杆要及时调整或废弃.5)使用冲击钻施工时冲程不要过大,尽量采用二次成孔,以保证成孔的重直度。
4、处理措施1)当遇到孤石等障碍物时,可采用冲击钻冲击成孔。
2)当钻孔偏斜超限时,应回填粘土,待沉积密实后再重新钻孔.二、在钻孔过程中发生缩孔怎么办?1、质量问题及现象当使用探孔器检查成孔时,探孔器下放到某一部位时受阻,无法顺利检查到孔底。
钻孔某一部位的直径小于设计要求,或从某一部位开始,孔径逐渐缩小。
2、原因分析1)地质构造中含有软弱层,在钻孔通过该层中,软弱层在土压力的作用下,向孔内挤压形成缩孔。
2)地质构造中塑性土层,遇水膨胀,形成缩孔。
3)钻头磨损过快,未及时补焊,从而形成缩孔。
3、预防措施1)根据地质钻探资料及钻井中的土质变化,若发现含有软弱层或塑性土时,要注意经常扫孔。
钢筋绑扎与安装的工程质量通病
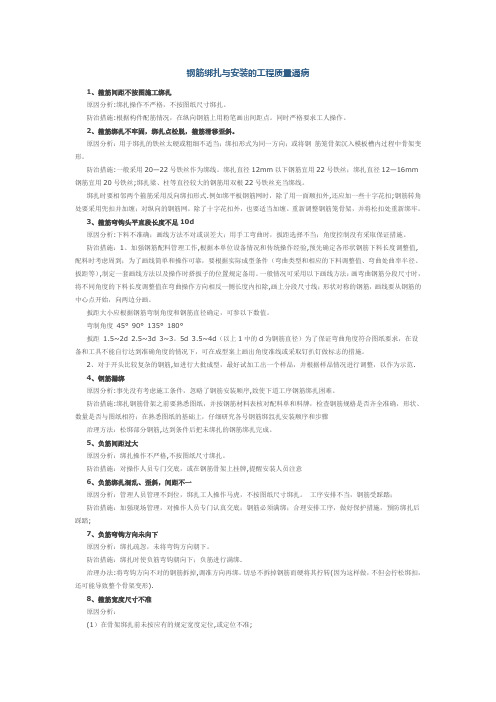
钢筋绑扎与安装的工程质量通病1、箍筋间距不按图施工绑扎原因分析:绑扎操作不严格,不按图纸尺寸绑扎。
防治措施:根据构件配筋情况,在纵向钢筋上用粉笔画出间距点。
同时严格要求工人操作。
2、箍筋绑扎不牢固,绑扎点松脱,箍筋滑移歪斜。
原因分析:用于绑扎的铁丝太硬或粗细不适当;绑扣形式为同一方向;或将钢筋笼骨架沉入模板槽内过程中骨架变形。
防治措施:一般采用20—22号铁丝作为绑线。
绑扎直径12mm以下钢筋宜用22号铁丝;绑扎直径12—16mm 钢筋宜用20号铁丝;绑扎梁、柱等直径较大的钢筋用双根22号铁丝充当绑线。
绑扎时要相邻两个箍筋采用反向绑扣形式.例如绑平板钢筋网时,除了用一面顺扣外,还应加一些十字花扣;钢筋转角处要采用兜扣并加缠;对纵向的钢筋网,除了十字花扣外,也要适当加缠。
重新调整钢筋笼骨架,并将松扣处重新绑牢。
3、箍筋弯钩头平直段长度不足10d原因分析:下料不准确;画线方法不对或误差大;用手工弯曲时,扳距选择不当;角度控制没有采取保证措施。
防治措施:1、加强钢筋配料管理工作,根据本单位设备情况和传统操作经验,预先确定各形状钢筋下料长度调整值,配料时考虑周到;为了画线简单和操作可靠,要根据实际成型条件(弯曲类型和相应的下料调整值、弯曲处曲率半径、扳距等),制定一套画线方法以及操作时搭扳子的位置规定备用。
一般情况可采用以下画线方法:画弯曲钢筋分段尺寸时,将不同角度的下料长度调整值在弯曲操作方向相反一侧长度内扣除,画上分段尺寸线;形状对称的钢筋,画线要从钢筋的中心点开始,向两边分画。
扳距大小应根据钢筋弯制角度和钢筋直径确定,可参以下数值。
弯制角度45°90°135°180°扳距1.5~2d 2.5~3d 3~3。
5d 3.5~4d(以上1中的d为钢筋直径)为了保证弯曲角度符合图纸要求,在设备和工具不能自行达到准确角度的情况下,可在成型案上画出角度准线或采取钉扒钉做标志的措施。
混凝土梁柱变形标准

混凝土梁柱变形标准混凝土结构是目前建筑中最常见的结构形式之一,其主要构件包括梁、柱、板等。
在混凝土结构中,梁柱是其承重骨架的主要构件,其变形标准非常重要,因为它们直接关系到结构的安全性和使用寿命。
本文将介绍混凝土梁柱变形标准,包括梁柱的变形原因、标准分类、具体标准以及检测方法等方面。
一、梁柱变形的原因1. 材料本身的变形:混凝土结构中的梁柱受到荷载作用时,其材料会发生一定程度的变形。
这种变形是由混凝土本身的材料特性决定的,主要包括弹性变形和塑性变形。
2. 荷载作用的变形:除了材料本身的变形以外,混凝土梁柱还会受到荷载作用的变形。
荷载作用的变形主要包括弯曲变形和剪切变形两种。
3. 温度变化的变形:混凝土结构中的梁柱还会受到温度变化的影响,因为温度变化会导致混凝土的体积发生变化,从而引起梁柱的变形。
二、梁柱变形的标准分类混凝土梁柱变形标准可以根据不同的标准分类,主要包括以下几种:1. 弹性变形标准:弹性变形是混凝土结构中梁柱最基本的变形类型。
其变形量相对较小,可以通过简单的计算方法进行预测和控制。
弹性变形标准主要包括挠度限值和挠度控制系数等。
2. 塑性变形标准:塑性变形是混凝土结构中较为复杂的变形类型,其变形量相对较大,难以通过简单的计算方法进行预测和控制。
塑性变形标准主要包括裂缝宽度限值和变形控制系数等。
3. 温度变形标准:温度变形是混凝土结构中最为常见的变形类型之一,其变形量与温度变化的幅度密切相关。
温度变形标准主要包括温度变形系数和温度变形限值等。
三、具体标准1. 弹性变形标准(1)挠度限值:混凝土梁柱在弹性变形阶段的挠度应不超过1/250的跨度。
(2)挠度控制系数:挠度控制系数是指在设计时考虑梁柱挠度控制的程度。
在一般情况下,挠度控制系数应不小于1.0。
2. 塑性变形标准(1)裂缝宽度限值:混凝土梁柱在塑性变形阶段的裂缝宽度应不超过0.3mm。
(2)变形控制系数:变形控制系数是指在设计时考虑梁柱变形控制的程度。
预制梁施工易出现问题及防控措施

预制梁施工易出现问题及防控措施1、钢筋保护层厚度控制不佳(1)现象为预制梁钢筋保护层厚度超出验标允许范围,个别部位甚至出现漏筋。
(2)原因分析【1】保护层垫块不合格,垫块厚度与净保护层厚度不一致,垫块强度不足;【2】垫块数量少、间距大、布局不合理、绑扎不牢固;【3】钢筋下料不精确、安装不规范,钢筋骨架加工尺寸偏大或钢筋绑扎不牢固,混凝土浇筑过程中部分钢筋变形变位;【4】箱梁芯模或T梁钢筋发生偏移,使腹板两侧厚度偏大或偏小,导致保护层厚度不合格;【5】箱梁梁芯模上浮使顶板钢筋骨架随之上浮,在梁高不变的情况下,导致顶板保护层厚度不足。
【6】底板因垫块数量少或布局不合理或钢筋安装不规范导致保护层厚度不足。
(3)整改预防措施【1】根据设计净保护层厚度,选择合适厚度的垫块,确保垫块强度,避免施工过程中被压碎;【2】要求垫块密度每平米不得小于4个,呈梅花形布设,相邻垫块间距不大于60cm,在浇筑前和混凝土浇筑前进行检查验收,发现损坏、翻到的垫块要及时更换或重新调整;【3】严格按照设计尺寸下料,加工尺寸偏差过大的半成品钢筋不得进行绑扎;【4】在两侧腹板钢筋骨架焊接支撑定位钢筋,防止内模偏移和腹板钢筋变形;内模安装就位后检查两侧腹板厚度,内模若出现偏移在调整后绑扎顶绑钢筋;【5】落实防芯模上浮措施,具体措施见芯模上浮治理;【6】底板钢筋安装完成后,对底板钢筋进行检查和调整。
2、保护层垫块印记明显(1)现象为预制梁存在明显的垫块印记(2)原因分析【1】垫块过于干燥,未浸水;【2】垫块被模板油污染。
(3)预防措施【1】垫块宜置于水桶中,饱水浸透后使用;【2】模板油特别是台座模板油不宜过多涂刷,避免污染垫块与钢筋。
3、预埋钢筋位置不准确(1)现象为预制梁伸缩缝预埋筋、防撞护栏预埋筋位置不准确,影响后续防撞护栏施工和伸缩缝安装。
(2)原因分析【1】定位不准确,使定位筋位置随模板出现偏差;【2】焊接定位不牢固,施工过程中由于踩踏、混凝土振捣等原因使钢筋变位。
装修质量通病及防治措施
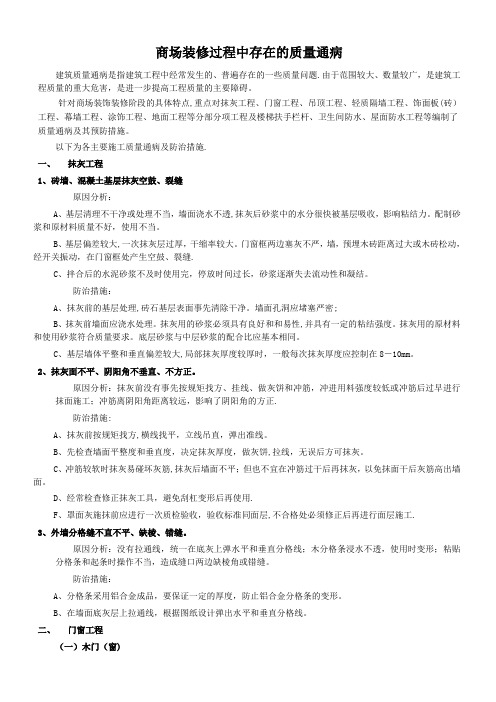
商场装修过程中存在的质量通病建筑质量通病是指建筑工程中经常发生的、普遍存在的一些质量问题.由于范围较大、数量较广,是建筑工程质量的重大危害,是进一步提高工程质量的主要障碍。
针对商场装饰装修阶段的具体特点,重点对抹灰工程、门窗工程、吊顶工程、轻质隔墙工程、饰面板(砖)工程、幕墙工程、涂饰工程、地面工程等分部分项工程及楼梯扶手栏杆、卫生间防水、屋面防水工程等编制了质量通病及其预防措施。
以下为各主要施工质量通病及防治措施.一、抹灰工程1、砖墙、混凝土基层抹灰空鼓、裂缝原因分析:A、基层清理不干净或处理不当,墙面浇水不透,抹灰后砂浆中的水分很快被基层吸收,影响粘结力。
配制砂浆和原材料质量不好,使用不当。
B、基层偏差较大,一次抹灰层过厚,干缩率较大。
门窗框两边塞灰不严,墙,预埋木砖距离过大或木砖松动,经开关振动,在门窗框处产生空鼓、裂缝.C、拌合后的水泥砂浆不及时使用完,停放时间过长,砂浆逐渐失去流动性和凝结。
防治措施:A、抹灰前的基层处理,砖石基层表面事先清除干净。
墙面孔洞应堵塞严密;B、抹灰前墙面应浇水处理。
抹灰用的砂浆必须具有良好和和易性,并具有一定的粘结强度。
抹灰用的原材料和使用砂浆符合质量要求。
底层砂浆与中层砂浆的配合比应基本相同。
C、基层墙体平整和垂直偏差较大,局部抹灰厚度较厚时,一般每次抹灰厚度应控制在8-10mm。
2、抹灰面不平、阴阳角不垂直、不方正。
原因分析:抹灰前没有事先按规矩找方、挂线、做灰饼和冲筋,冲进用料强度较低或冲筋后过早进行抹面施工;冲筋离阴阳角距离较远,影响了阴阳角的方正.防治措施:A、抹灰前按规矩找方,横线找平,立线吊直,弹出准线。
B、先检查墙面平整度和垂直度,决定抹灰厚度,做灰饼,拉线,无误后方可抹灰。
C、冲筋较软时抹灰易碰坏灰筋,抹灰后墙面不平;但也不宜在冲筋过干后再抹灰,以免抹面干后灰筋高出墙面。
D、经常检查修正抹灰工具,避免刮杠变形后再使用.F、罩面灰施抹前应进行一次质检验收,验收标准同面层,不合格处必须修正后再进行面层施工.3、外墙分格缝不直不平、缺棱、错缝。
石膏板吊顶细部质量控制

石膏板吊顶细部质量控制顶棚装饰是室内装饰工程中的重要部分,石膏板吊顶因其施工简单、方便、效果好、成本低且绿色环保的优点而被广泛采用,但在实际应用中,也经常变形和裂缝等质量缺陷。
结合以往的工程经验,试从装饰设计、使用材料、施工工艺等方面分析原因,并寻求控制方法。
标签:质量缺陷;装饰设计;石膏板及线条一、质量缺陷原因分析石膏板吊顶质量缺陷产生的原因主要在以下几个方面:1.装饰设计原因在大房间和过道交接的部位,如设计的两个板块的刚度不同,石膏板很容易在交接部位被拉裂。
2.龙骨设计间距过大或规格过小,在有障碍物体干涉的局部空间未做过桥支架设计或支架刚度不足。
3.双层石膏板吊顶时,在图纸上没有按材料重量计算所需要的吊杆直径和间距及主次龙骨的规格、厚度和间距,没有对其刚度和直线度提出要求。
4.没有根据不同使用要求及部位选用对应的石膏板类型,如卫生间要选用防水型石膏板。
5.石膏线条设计模糊,造成浮雕的厚度、图案深度和安装方法与设计构思大相径庭,实体图案花纹较浅,立体感差,较长的石膏线条弯曲,接头不平顺,线条安装中容易折断。
二、施工原因1.因在施工过程中石膏板受潮,受外力作用,出现已调平的吊顶龙骨在外力作用下起伏不平,石膏板产生拉力变形、裂缝。
2.部分吊顶在完工后,经过短期使用也产生凹凸不平及裂缝。
出现这些问题的主要原因有:①吊件上膨胀螺栓、螺母及固定主龙骨的螺杆、螺母丝接不按规范操作,导致螺栓及螺母扭结,丝扣损坏,部分螺栓假受力。
②膨胀螺丝下部挂吊筋,上口未加固定螺母固定。
③吊筋没有用全牙螺杆,或是全牙螺杆和圆盘钢筋混用,受力不均匀。
④吊顶的龙骨安装后,主、次龙骨在纵横方向上存在着不顺直、扭曲现象;主、次龙骨间有活动间隙。
主龙骨拱度不均匀,个别呈波浪形。
⑤纸面石膏板在有应力状态下进行安装,强行就位。
固定石膏板的自攻螺钉间距过大或部分自攻螺钉假受力。
安装石膏板时,工人不根据龙骨间距尺寸在石膏板上弹线,部分螺钉未固定在龙骨上;在两块石膏板接缝处,自攻螺钉位置不正确,偏向板一侧,导致纸面石膏板爆裂。
钢筋混凝土工程施工的难点及其解决方法

钢筋混凝土工程施工的难点及其解决方法1. 难点1.1 钢筋施工质量控制钢筋是钢筋混凝土结构中的骨架,其质量直接关系到结构的承载能力和安全性。
在施工过程中,钢筋的绑扎、焊接、锚固等环节均可能出现质量问题,如不符合规范要求的钢筋直径、间距、锚固长度等。
1.2 混凝土施工质量控制混凝土是钢筋混凝土结构中的填充材料,其质量对结构的耐久性和使用寿命具有重要影响。
混凝土的配比、搅拌、运输、浇筑、养护等环节均可能影响混凝土的质量,如配比不合理、搅拌时间不足、运输过程中离析、浇筑不密实、养护不足等。
1.3 施工缝处理施工缝是钢筋混凝土结构中的薄弱环节,处理不当容易导致结构裂缝和渗漏。
施工缝的处理需要严格按照规范要求进行,包括清除浮浆、湿润处理、接缝材料的选择和施工等。
1.4 结构变形控制钢筋混凝土结构在施工过程中和在使用过程中都可能产生变形,如不进行有效控制,可能导致结构破坏或使用功能受到影响。
结构变形的原因包括材料性能、施工质量、荷载作用等。
1.5 施工安全钢筋混凝土结构施工过程中,存在高处作业、机械伤害、触电等安全风险。
施工安全管理的不到位可能导致人员伤亡和财产损失。
2. 解决方法2.1 钢筋施工质量控制(1)加强钢筋工人的技能培训,提高钢筋施工质量。
(2)加强对钢筋原材料的检验,确保原材料质量。
(3)加强现场巡查,及时发现并整改钢筋施工质量问题。
2.2 混凝土施工质量控制(1)严格按照混凝土配比进行施工,确保混凝土强度和耐久性。
(2)加强混凝土搅拌时间控制,确保混凝土均匀性。
(3)采取措施防止混凝土在运输过程中离析,如使用防护网等。
(4)加强混凝土浇筑和养护过程的管理,确保混凝土质量。
2.3 施工缝处理(1)严格按照规范要求处理施工缝,确保施工缝质量。
(2)选择合适的接缝材料,提高施工缝的抗渗和抗剪能力。
2.4 结构变形控制(1)合理设计结构,优化结构受力状态。
(2)加强施工质量控制,减少施工过程中的结构变形。
细胞骨架在细胞形态变化中的作用分析

细胞骨架在细胞形态变化中的作用分析细胞形态的变化在生物体内是一个极其常见的现象。
比如,一个受到刺激的单细胞生物会利用它的细胞骨架网络变形,从而反应出生物体对外界刺激的响应。
细胞骨架不断地在细胞内进行改变,这对细胞的功能调整、运动、质量转换和细胞分化起着极其重要的作用。
1. 细胞骨架的概述细胞骨架是一种由微纤维组成的细节系统。
它由三种不同的微管诸如细胞间中质,微纤维和中间纤维等构成。
微管是一种由α-和β-微管蛋白组成的圆柱形结构,长约25纳米,直径约15纳米。
微纤维是由外向内伸长的细支构成的。
中间纤维是一种絮状蛋白纤维,是细胞内细支的重要组成部分。
2. 细胞骨架在细胞运动和细胞肿胀中的作用细胞骨架在细胞运动和细胞肿胀方面的作用与细胞进行构造有极大的关联。
细胞骨架网络可以帮助细胞进行移动,并从外向内产生细胞内力。
细胞内力经常用于细胞间的连接和稳定,尤其是在脆弱的生殖阶段或伤口愈合期间。
3. 细胞骨架在细胞分裂与细胞形态的变化中的作用细胞骨架在细胞分裂和形态变化方面起着至关重要的作用。
在细胞分裂过程中,如果细胞骨架网与其他网络结构皆可呈现分枝现象或失衡,变形和分裂就会停止。
细胞形态的变化与细胞分裂也密不可分,这一参考角度是许多因素激动细胞内网络结构的部分。
例如,在成骨细胞中,细胞内骨架皆可因化学物质的作用而变形。
这种变形可以导致细胞变亮或让它拥有更可控的当前形态。
此外,细胞刺活动也有可能由骨架产生。
4. 细胞骨架组分的调控细胞骨架在几个拉断细胞皆可保证体内絮状蛋白组成的比例以及组成,但现在对它的组成和调节机制是未知的。
不过一条结论是,许多活跃的蛋白会不断地改变肌纤维锁定蛋白的技术和位置来影响骨架的构造和变化。
细胞骨架在细胞内结构和功能上起着不可替代的作用。
对细胞骨架的研究可以探究细胞内部的结构、物理机制和生物力学,并为细胞形态和功能的研究提供参考。
隧道二次衬砌外观质量缺陷原因分析及预防措施
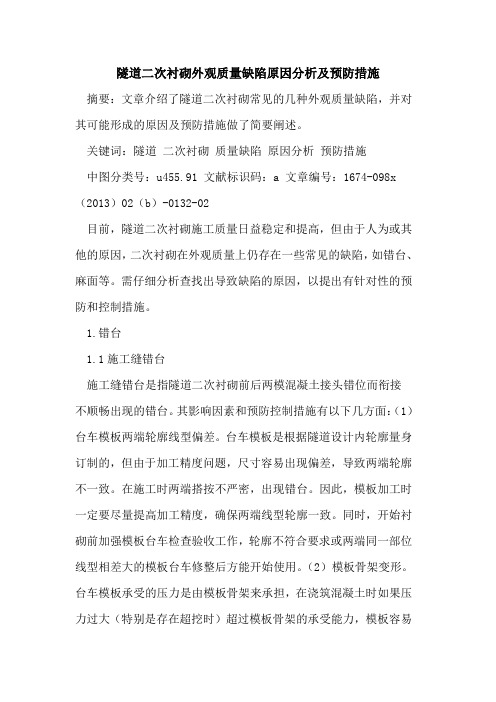
隧道二次衬砌外观质量缺陷原因分析及预防措施摘要:文章介绍了隧道二次衬砌常见的几种外观质量缺陷,并对其可能形成的原因及预防措施做了简要阐述。
关键词:隧道二次衬砌质量缺陷原因分析预防措施中图分类号:u455.91 文献标识码:a 文章编号:1674-098x (2013)02(b)-0132-02目前,隧道二次衬砌施工质量日益稳定和提高,但由于人为或其他的原因,二次衬砌在外观质量上仍存在一些常见的缺陷,如错台、麻面等。
需仔细分析查找出导致缺陷的原因,以提出有针对性的预防和控制措施。
1.错台1.1施工缝错台施工缝错台是指隧道二次衬砌前后两模混凝土接头错位而衔接不顺畅出现的错台。
其影响因素和预防控制措施有以下几方面:(1)台车模板两端轮廓线型偏差。
台车模板是根据隧道设计内轮廓量身订制的,但由于加工精度问题,尺寸容易出现偏差,导致两端轮廓不一致。
在施工时两端搭按不严密,出现错台。
因此,模板加工时一定要尽量提高加工精度,确保两端线型轮廓一致。
同时,开始衬砌前加强模板台车检查验收工作,轮廓不符合要求或两端同一部位线型相差大的模板台车修整后方能开始使用。
(2)模板骨架变形。
台车模板承受的压力是由模板骨架来承担,在浇筑混凝土时如果压力过大(特别是存在超挖时)超过模板骨架的承受能力,模板容易逐渐向内收缩变形。
如果发生在接头处,就导致搭按错台。
因此,在加工模板时,不但要保证模板厚度,更重要的是保证模板骨架要有足够的刚度。
(3)支撑变形。
模板承受的压力通过模板骨架传递给支撑系统,所以每个支撑不同程度的承受着巨大的压力。
如果支撑刚度不够,在浇筑混凝土时会弯曲变形而导致模板收缩。
若发生在接头位置就出现搭接错台。
对于此,加强支撑的刚度是解决问题的效途径。
(4)地基不稳。
浇注混凝土时,台车和混凝土的压力最终由地基来承担。
一般情况下,隧道施作二次衬砌前先施作路面基层,既提供良好的施工条件又达到硬化地面的目的。
但有时工序安排不当又为了赶二次衬砌施工进度会在地基未硬化前施做二次衬砌。
大跨度钢结构施工安装变形控制技术措施
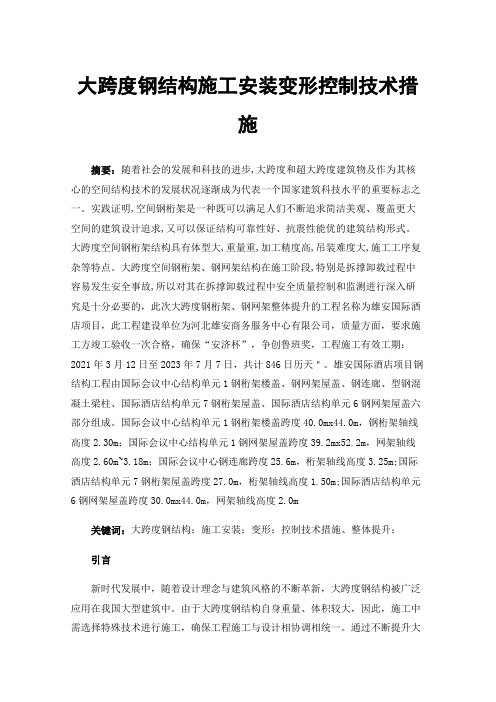
大跨度钢结构施工安装变形控制技术措施摘要:随着社会的发展和科技的进步,大跨度和超大跨度建筑物及作为其核心的空间结构技术的发展状况逐渐成为代表一个国家建筑科技水平的重要标志之一。
实践证明,空间钢桁架是一种既可以满足人们不断追求简洁美观、覆盖更大空间的建筑设计追求,又可以保证结构可靠性好、抗震性能优的建筑结构形式。
大跨度空间钢桁架结构具有体型大,重量重,加工精度高,吊装难度大,施工工序复杂等特点。
大跨度空间钢桁架、钢网架结构在施工阶段,特别是拆撑卸载过程中容易发生安全事故,所以对其在拆撑卸载过程中安全质量控制和监测进行深入研究是十分必要的,此次大跨度钢桁架、钢网架整体提升的工程名称为雄安国际酒店项目,此工程建设单位为河北雄安商务服务中心有限公司,质量方面,要求施工方竣工验收一次合格,确保“安济杯”,争创鲁班奖,工程施工有效工期:2021年3月12日至2023年7月7日,共计846日历天"。
雄安国际酒店项目钢结构工程由国际会议中心结构单元1钢桁架楼盖、钢网架屋盖、钢连廊、型钢混凝土梁柱、国际酒店结构单元7钢桁架屋盖、国际酒店结构单元6钢网架屋盖六部分组成。
国际会议中心结构单元1钢桁架楼盖跨度40.0mx44.0m,钢桁架轴线高度2.30m;国际会议中心结构单元1钢网架屋盖跨度39.2mx52.2m,网架轴线高度2.60m~3.18m;国际会议中心钢连廊跨度25.6m,桁架轴线高度3.25m;国际酒店结构单元7钢桁架屋盖跨度27.0m,桁架轴线高度1.50m;国际酒店结构单元6钢网架屋盖跨度30.0mx44.0m,网架轴线高度2.0m关键词:大跨度钢结构;施工安装;变形;控制技术措施、整体提升;引言新时代发展中,随着设计理念与建筑风格的不断革新,大跨度钢结构被广泛应用在我国大型建筑中。
由于大跨度钢结构自身重量、体积较大,因此,施工中需选择特殊技术进行施工,确保工程施工与设计相协调相统一。
通过不断提升大跨度钢结构的施工技术水平,能够有效实现大跨度钢结构工程的系统性、先进性与经济性,同时使其功能得到充分发挥。
钢筋骨架产生歪斜的原因

钢筋骨架产生歪斜的原因钢筋骨架产生歪斜的原因可以有多种,主要包括以下几个方面。
首先,施工过程中的不当操作会导致钢筋骨架产生歪斜。
施工人员在安装钢筋骨架时,如果没有按照设计图纸和相关规范进行操作,比如搭设的支架不牢固、连接件的安装不稳固等,就容易引起钢筋骨架的不平衡和歪斜。
其次,设计和计算问题也是钢筋骨架产生歪斜的原因之一。
如果在设计阶段没有考虑到结构的承重平衡、应力分布等因素,或者计算有误,就会造成钢筋骨架的不均匀受力,从而导致歪斜。
此外,施工材料的质量问题也可能导致钢筋骨架产生歪斜。
如果使用了质量不合格的钢筋或者焊接材料,其强度和可靠性就无法得到保证,容易出现变形和断裂等情况,进而导致钢筋骨架的歪斜。
另外,外力作用也是导致钢筋骨架歪斜的常见原因。
例如,在建筑物受到强风、地震等自然灾害或者周围环境改变时,外力的作用会引起结构的变形,从而导致钢筋骨架的歪斜现象。
如何避免钢筋骨架产生歪斜呢?首先,在施工过程中要严格按照设计图纸和规范进行操作,遵守施工工艺要求,确保搭设的支架稳固可靠,连接件安装牢固。
其次,设计和计算阶段要充分考虑结构的受力情况,做好相应的承重平衡和应力分析,确保钢筋骨架的受力均衡。
此外,选择优质的施工材料也至关重要,通过正规渠道购买符合质量标准的钢筋和焊接材料,确保施工质量。
最后,加强对外力作用的预测和控制是防止钢筋骨架歪斜的关键。
在设计和施工过程中要考虑到建筑物所处环境和可能受到的自然灾害等因素,合理设计结构的抗风抗震性能,采取相应的加固措施,确保钢筋骨架的稳定。
总之,钢筋骨架产生歪斜的原因主要包括施工操作不当、设计和计算问题、施工材料质量以及外力作用等因素。
为了避免钢筋骨架歪斜,我们需要在施工过程中注重操作规范、质量管控和结构稳定性设计,以确保建筑物的安全可靠。
城际轨道“Y”型墩柱钢筋骨架偏心控制措施

城际轨道“Y”型墩柱钢筋骨架偏心控制措施的探讨一、城际轨道交通工程实例简介广东珠三角城际轨道交通工程桥梁段的墩柱大部分采用单墩,墩柱以流线”Y”型独立墩为主,分为矩形墩,圆端墩,圆墩三种形式,每种墩均有4米高的“Y”型墩帽;跨越道路地段采用框架墩,以保障道路畅通;矩形单墩,按照墩高分为三种型式:A1、A2、A3,A1型墩墩柱立柱矩形截面为1.8m×3m,墩帽顶截面为2.4m×5.4m,曲线型变化,正面形成“Y”型墩柱。
A2型墩墩柱立柱矩形截面为2.4m×3m,墩帽顶截面为2.4m×5.4m,曲线行变化,适用于墩高大于8米,不大于12米的桥墩;A3型墩墩柱立柱矩形截面为3m×3.8m,墩帽顶截面为3m×5.4m,曲线行变化。
圆端墩只有一种形式B1,用于标段内过河流段桥墩,墩柱截面形式为2.4m×5.4m,圆端半径1.2m,墩帽顶部截面2.4m×8.7m,圆端半径1.2m。
框架墩型为两截面形式为2.2m×2.5m的直壁方墩,上架横梁。
二、“Y”型墩柱设计情况“Y”型墩柱在高架区间设计最为常见;横桥向直线段宽一般大于2.2m,墩顶即”Y”字最顶宽度一般大于2.8m;顺桥向直线段宽一般大于4m,墩顶即”Y”字最顶宽度一般大于6m;墩柱钢筋保护层一般设计为3.5cm。
三、“Y”型墩柱施工工藝1. 墩柱施工工艺在承台施工时,首先测量放样,定位、安装墩柱直线段预埋筋,预埋筋的安装位置与墩柱直线段主筋钢筋位置对应一致,纵横中心轴线也必须与墩柱纵横中心轴线相互对应一致。
承台施工完成,墩柱根部范围凿毛,清除灰尘和混凝土浮浆。
然后搭设配合墩柱施工的辅助脚手架,绑扎墩柱钢筋骨架和墩帽“Y”型钢筋,安装保护层垫块,安装预埋件,安装模板,浇筑混凝土,混凝土养护。
2.工艺流程图3.墩台施工容许误差四、导致墩柱钢筋骨架偏心的主要因素1.墩柱预埋筋定位控制措施不当,钢筋固定不牢固,在承台浇筑、振捣混凝土时,预埋筋发生移位,连接后续墩柱钢筋骨架出现偏心。
焊接钢板产生变形的原因及预防措施分析探讨
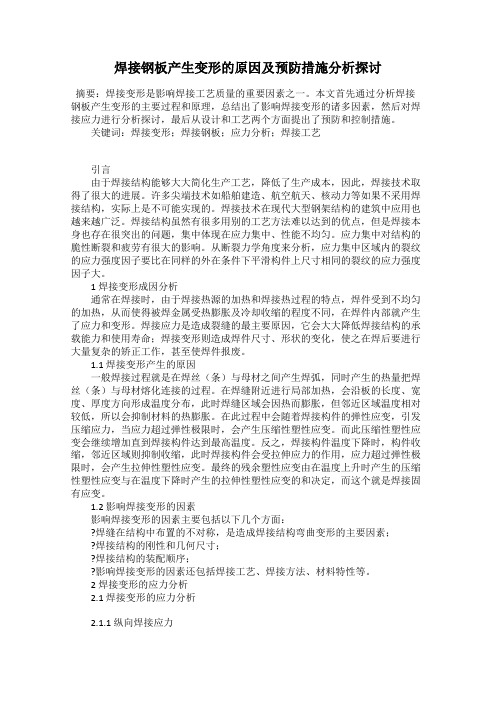
焊接钢板产生变形的原因及预防措施分析探讨摘要:焊接变形是影响焊接工艺质量的重要因素之一。
本文首先通过分析焊接钢板产生变形的主要过程和原理,总结出了影响焊接变形的诸多因素,然后对焊接应力进行分析探讨,最后从设计和工艺两个方面提出了预防和控制措施。
关键词:焊接变形;焊接钢板;应力分析;焊接工艺引言由于焊接结构能够大大简化生产工艺,降低了生产成本,因此,焊接技术取得了很大的进展。
许多尖端技术如船舶建造、航空航天、核动力等如果不采用焊接结构,实际上是不可能实现的。
焊接技术在现代大型钢架结构的建筑中应用也越来越广泛。
焊接结构虽然有很多用别的工艺方法难以达到的优点,但是焊接本身也存在很突出的问题,集中体现在应力集中、性能不均匀。
应力集中对结构的脆性断裂和疲劳有很大的影响。
从断裂力学角度来分析,应力集中区域内的裂纹的应力强度因子要比在同样的外在条件下平滑构件上尺寸相同的裂纹的应力强度因子大。
1 焊接变形成因分析通常在焊接时,由于焊接热源的加热和焊接热过程的特点,焊件受到不均匀的加热,从而使得被焊金属受热膨胀及冷却收缩的程度不同,在焊件内部就产生了应力和变形。
焊接应力是造成裂缝的最主要原因,它会大大降低焊接结构的承载能力和使用寿命;焊接变形则造成焊件尺寸、形状的变化,使之在焊后要进行大量复杂的矫正工作,甚至使焊件报废。
1.1 焊接变形产生的原因一般焊接过程就是在焊丝(条)与母材之间产生焊弧,同时产生的热量把焊丝(条)与母材熔化连接的过程。
在焊缝附近进行局部加热,会沿板的长度、宽度、厚度方向形成温度分布,此时焊缝区域会因热而膨胀,但邻近区域温度相对较低,所以会抑制材料的热膨胀。
在此过程中会随着焊接构件的弹性应变,引发压缩应力,当应力超过弹性极限时,会产生压缩性塑性应变。
而此压缩性塑性应变会继续增加直到焊接构件达到最高温度。
反之,焊接构件温度下降时,构件收缩,邻近区域则抑制收缩,此时焊接构件会受拉伸应力的作用,应力超过弹性极限时,会产生拉伸性塑性应变。
- 1、下载文档前请自行甄别文档内容的完整性,平台不提供额外的编辑、内容补充、找答案等附加服务。
- 2、"仅部分预览"的文档,不可在线预览部分如存在完整性等问题,可反馈申请退款(可完整预览的文档不适用该条件!)。
- 3、如文档侵犯您的权益,请联系客服反馈,我们会尽快为您处理(人工客服工作时间:9:00-18:30)。
客车车身骨架变形的原因分析及其控制措施
客车车身骨架变形是客车生产厂所面临的一个共性的问题,他是提高客车车身质量和焊接装配生产效率的主要瓶颈之一。
骨架变形直接导致客车工艺车身校正工作量加大,而且因校正造成车身骨架局部凸凹不平,直接影响骨架强度。
原因分析
1、由于客车车身结构限制,造成客车车身腰梁上侧焊接部位面积远大于下侧焊接部位面积。
2、侧围骨架在胎具上组合时,由于焊接变形等原因,造成按照图纸要求定位焊接后舱门洞口对角线尺寸超差。
3、侧围从胎具上取出后,在地面进行侧围骨架内侧焊接,加大了洞口对角线的超差。
4、由于调运的原因造成骨架在中间部位变形。
5、车身骨架合装后,在骨架附件焊接时因车身骨架自重等原因
造成工艺车身再次变形。
6、预防控制措施
1、反变形法。
对组焊胎具进行重新调整,按照统计分
析出来的数据有意识的将变形部位反向调整,同时在腰梁、
仓门立柱焊接部位约60mm处安装卡具,以此减少变形。
2、对定位焊进行统一要求。
首先将基准件进行定位焊,
对接面高度平齐,再在型材接头两个拐角处进行点固焊,然
后实施满焊焊接。
3、焊接顺序调整。
针对腰梁处变形,采取按顺序进行
焊接的方式进行预防控制。
首先将左右侧围骨架从前至后分
成五个区域,焊接时每人负责一个区域所有焊接部位的焊
接。
在车身长度方向上统一由左至右或由右至左顺序进行焊
接,在车身高度方向上,统一由上至下进行焊接。
4、三面焊接进行规范。
对于同一根型材的焊接进行规
范,先焊角焊缝,再焊平焊缝,然后再焊侧围骨架附件。
5、加焊工艺支撑。
对于关键部位或者容易因运转变形
之处在侧围骨架未从胎具中取出时加焊工艺型材支撑。
6、起吊方式的改变。
组焊后的骨架从胎具中取出时,
由原中间部位两点受力改变为均布的4~5个点均匀受力。
同时改进吊具,变硬吊具为软吊具
7、左右侧围(先放大一点好放后台阶)----前轮罩----后台阶-----
左右侧围放回实际尺寸-----顶盖----前后围。