钣金箱体外尺寸标准V1.2
钣金行业外观标准

外观检验标准一. 外观表面等级定义结构件外观表面分为三个等级:1 级面、2 级面、3 级面,各表面等级定义如下:1.1 1 级面重要外观表面, 具有装饰性、体现产品外观形象、可以直接正视到的主要外观表面。
包括机柜、插框、盒式结构、拉手条的正面和正面上主要零部件的外表面,机柜前门开门后的正视面。
1.2 2 级面主要外表面、半装饰性的经常可见的外表面。
主要包括机柜(插框)方孔条正面、外侧面、后面、高度不大于1。
8 米的机柜顶面。
小五金件、机柜机箱附件均定义为2 级面。
1.3 3 级面次要外表面和内表面,主要包括机柜(插框)内表面、底面、高度大于1。
8米的机柜顶面以及安装支架、绑线架、内部框架、内部焊件的所有表面。
除1、2级面以外的表面均定义为3 级面。
二. 外观检验条件2.1目视检测条件在自然光或光照度在300-600LX 的近似自然光下(如40W 日光灯、距离500mm 处),相距为500mm,观测时间随不同检测面而不同。
检查者位于被检查表面的正面、视线与被检表面呈45-90°进行正常检验。
要求检验者的校正视力不低于1.2 。
不能使用放大镜用于外观检验。
且检查者位于被检查表面的正面、视线与被检表面呈45-90°进行正常检验。
要求检验者的矫正视力不低于1.2。
不能用放大镜做外观检查。
2.2 检测面积划分检查时,每一表面按其最大外形尺寸划为不同大小类型,表面大小划分标准如下表:2.1可接受的外观缺陷总数如下表三. 可接收的缺陷标准3.1金属表面缺陷类型缺陷定义对照图片模具痕折弯等模具成型过程中在结构件表面产生的压痕、轻微凹坑等摩擦痕加工过程中板材在机床台面运动过程中产生的轻微划痕,无凹入感凹坑由于基体材料缺陷、或在加工过程中操作不当等原因在材料表面留下的小坑状痕迹抛光区对机材上腐蚀、划伤、焊接区、铆接区等部位进行机械打磨抛光后表现出的局部高亮泽、光亮区域、焊接背面所呈现的打磨痕迹焊渣焊接时飞溅到焊缝以外区域的表面残渣和颗粒,牢固地附在表面烧伤拉丝处理时因操作不当造成零件表面过热而留下的烧蚀痕迹无3.1.2金属表面外观缺陷可接受范围一览表提示: L表示单个缺陷长度,单位mm;S表示单个缺陷面积,单位mm2;D表示单个缺陷直径,单位mm;缺陷类型表面大小表面状态合格范围1级面2级面3级面模具痕不限各种不允许可接受可接受磨擦痕小各种L≤10且P≤2 L≤10且P≤3可接受中L≤20且P≤3 L≤20且P≤4大L≤40且P≤4 L≤40且P≤4超大L≤80且P≤5 L≤80且P≤6运动部件摩擦痕不限各种可接受可接受可接受焊渣不限各种不允许不允许不允许烧伤不限各种不允许不允许S≤10 且P≤2凹坑小各种不允许D≤2 且P≤3可接受中D≤2 且P≤3 D≤3 且P≤4大D≤3 且P≤4 D≤3 且P≤5超大D≤3 且P≤5 D≤3 且P≤6抛光区小各种不允许S≤100且P≤2可接受中S≤50 且P≤2可接受大陷面积总和≤5%可接受超大注:1、1级面摩擦痕、镀前划伤间距大于200mm以上;2、1级和2 级表面上凹坑间距大于50mm;3.2喷涂表面缺陷类型缺陷定义对照图片零件间色差同种喷涂层要求的零件分别符合涂层颜色要求,但组装后在相邻零件表面出现涂层颜色差异的现象喷涂保护面色差零部件的喷涂保护表面出现的发黄等和基材表面颜色不一致的现象涂层破损涂层脱落、剥落、开裂等现象孔洞涂层出现的针孔、小孔洞杂质由材料、模具、环境或机器设备中的灰尘、夹杂物、污物等影响而在涂层中形成的不同斑点颗粒因材料杂质或外来物等的影响而在表面形成的粒状凸起现象喷涂保护斑点喷涂保护表面出现的漆点、粉点等涂料堆积结构件孔口边缘积粉、积漆和积瘤等现象毛边在喷涂保护区的分界线上因去除保护材料而出现的附着力牢固的、明显的涂层多余或缺少现象浅划痕锐器在涂层表面产生的划痕,但未伤至底层(即底层未暴露)深划痕锐器在涂层表面产生的划伤,且已伤至底层(即底层已暴露出来)挂具痕喷涂时挂具和结构件接触部位局部无膜层现象压铆印压铆工序正常加工过程中在结构件表面产生的凹凸痕迹凹坑基材受撞击或校形不良、焊接变形、打磨过深而呈现出的明显变形3.2.2喷涂表面外观缺陷可接受范围一览表提示: L表示单个缺陷长度,单位mm;S表示单个缺陷面积,单位mm2;D表示单个缺陷直径,单位mm;P 表示被测表面允许的缺陷最大数量,单位个。
钣金通用检验标准
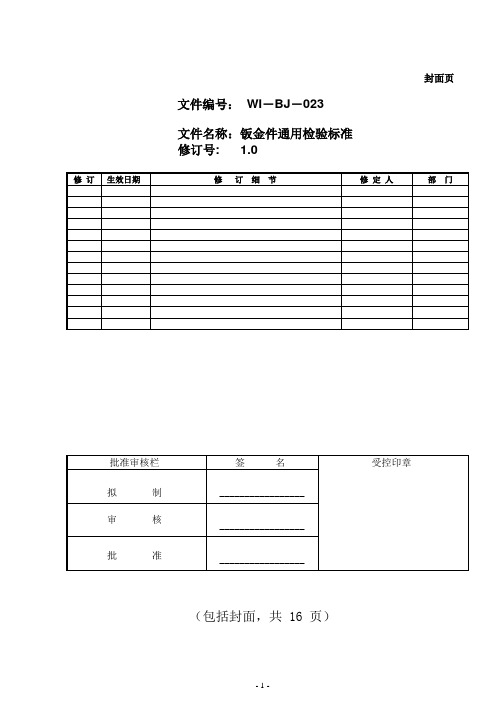
封面页文件编号: WI-BJ-023文件名称:钣金件通用检验标准修订号: 1.0(包括封面,共 16 页)1.0目的为保证我司钣金件产品的质量,又减少图纸对通用要求的描述,特制订本通用检验标准。
2.0范围本标准适用于我司标准以及非标准的钣金产品,本标准侧重范围,规定了钣金件在质量形成过程中各个工序的检验标准,主要从外观、尺寸控制、力度、组装要求作出规定;对钣金件产品的功能、结构特别性能不作规定,我司主要产品要求须参照相关检验标准,特别产品之特殊要求需另外说明。
3.0职责3.1工程部3.1.1设计时应支持本标准,对特别要求应特别说明。
3.1.2与本标准有关的不符合项之特纳。
3.2销售部3.2.1客户特别要求的收集3.2.2与本标准有关的不符合项之特纳3.3生产部按本标准做货及自检。
3.4品管部按本标准检验。
4.0作业内容4.1剪床开料4.1.1外观保证4.1.1.1剪床开料必须用经IQC检验合格之板材,大料平直度、外表面状态必须符合IQC检验标准。
4.1.1.2未经确认不得采用已生锈之SECC和SPCC板料,以及表面严重划伤之SUS板料。
4.1.1.3对胶沙不锈钢应注意开料之纹向要求,不可在不确定情况下作出纹向任意开料,并严格保护表面,以避免刮伤。
4.1.1.4剪床开料之批锋应小于料厚之3%,手摸应无明显刮手现象。
4.1.2尺寸控制4.1.2.1为保证钣金成形尺寸,减少过程累积误差对工件尺寸的影响,剪床开料尺寸允差按下表检验:4.1.2.2对一开几过多的开料件,如单一方向开料数量超过六件(一般应为偶数),应先将料对开,然后再开成单件,以减少误差累积。
4.1.2.3对长度超过1500-2500之开料切边直线度应小于0.3mm/m,宽度大小端误差小于0.5mm。
4.1.2.4开料件之长短边90。
角度允差±3´。
4.2 CNC冲孔4.2.1外观保证4.2.1.1 CNC冲孔应先检查板材是否有划伤,对经剪床放行而有少许划伤之板料,冲孔时应将划伤面尽量放于批锋面,以减少对外观的影响。
钣金加工数据表(包括开孔尺寸、折弯扣料、公制英制管等)
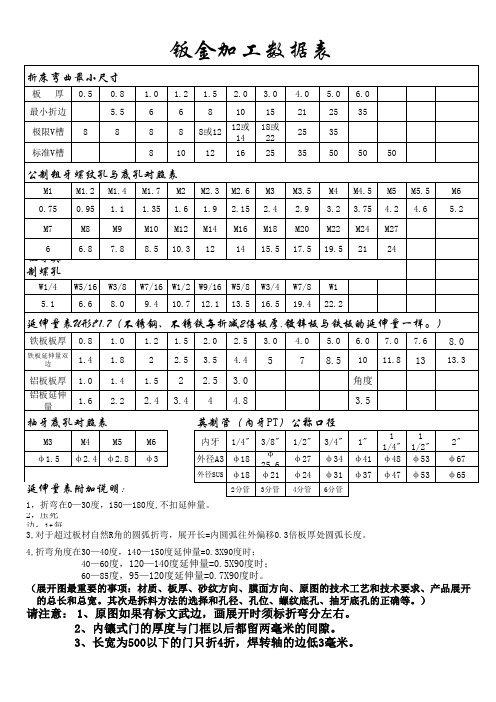
钣金加工数据表
1,折弯在0—30度,150—180度,不扣延伸量。
2,压死边:1t每折扣0.5,2t每折扣0.8,3t每折扣1.2
3,对于超过板材自然R角的圆弧折弯,展开长=内圆弧往外偏移0.3倍板厚处圆弧长度。
4,折弯角度在30—40度,140—150度延伸量=0.3X90度时;
40—60度,120—140度延伸量=0.5X90度时;
60—85度,95—120度延伸量=0.7X90度时。
(展开图最重要的事项:材质、板厚、砂纹方向、膜面方向、原图的技术工艺和技术要求、产品展开 的总长和总宽。
其次是拆料方法的选择和孔径、孔位、螺纹底孔、抽牙底孔的正确等。
)
请注意:1、原图如果有标文武边,画展开时须标折弯分左右。
2、内镶式门的厚度与门框以后都留两毫米的间隙。
3、长宽为500以下的门只折4折,焊转轴的边低3毫米。
双边。
钣金件通用技术条件

钣金件通用技术条件1.主题与范围1.1 本通用技术条件规定了我公司钣金产品(箱、柜、操作台、架等)相关的技术要求。
1.2 本通用技术条件适用以金属板材、带材、标准型材、管材、金属丝材为原料,以剪切、冲压、拉伸、折弯、拼焊等工艺方法成型的钣金件。
1.3 凡设计文件未明确技术要求的钣金件,均应按本通用技术条件的相应要求进行制造和验收。
1.4 在某些工序中采用车削、洗削、刨切、钻孔等机械加工方法时技术要求可参照通用技术条件相应条款或按GB1804公差与配合,GB1804形状和位置公差及相应的粗糙度选用。
2. 钣金零件通用技术条件2.1 总则2.1.1 零件表面上不允许有裂纹、分层、裂口、锈蚀及深度超过零件最小厚度公差的压伤及划伤。
表面上的手汗迹、油痕、斑点、锈蚀、轻微的划伤、压伤等,允许在零件厚度公差范围内进行光滑修磨排除。
2.1.2 零件的内、外边缘应去除毛刺,板厚大于0.5毫米的金属制件要去锐边、倒角或制圆。
2.1.3零件允许变薄后的板厚为钢板最小厚度的90%,其它材料变形后的板厚不得小于最小厚度的85%。
2.1.4零件的表面上允许有模具及夹具留下的痕迹,但不是剧烈的压伤或凹痕(这些地方的最小厚度不得低于2.1.3条规定)。
2.2 钣金零件的公差2.2.1剪切下料的尺寸偏差(表1)剪切后的尺寸偏差及两对角线长度之差值应控制在表中偏差范围内。
(表1)mm注:上述尺寸偏差对包容件应取正值,被包容件取负值。
2.2.2 普冲开角、冲孔的尺寸偏差A) 开角尺寸偏差为+0.3毫米,冲孔孔径尺寸偏差为+0.3毫米。
B) 冲孔的中心距尺寸偏差应符合表2规定(表2)2.2.3钣金零件折弯尺寸公差2.2.3.1图样上未标有尺寸公差的可按以下要求验收,一般零件折弯尺寸公差控制在±0.15/500毫米,折边长度每增加500毫米范围内,公差值递增±0.05毫米,即:±0.20/>500-1000毫米,±0.25/>1000-1500毫米……依此类推。
钣金加工件检验标准
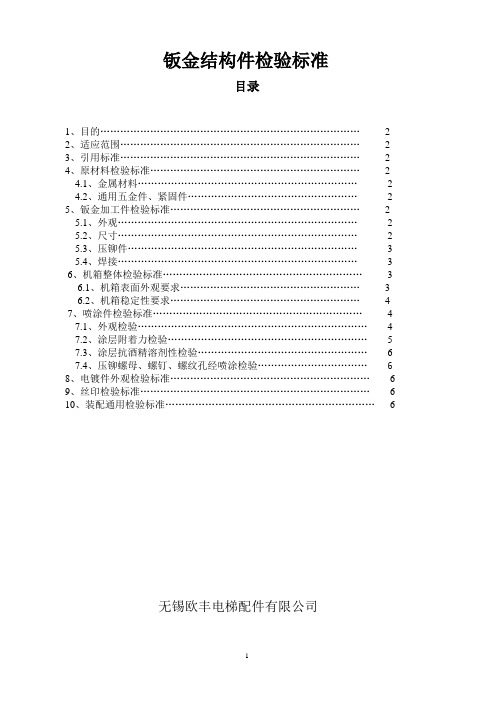
钣金结构件检验标准目录1、目的 (2)2、适应范围 (2)3、引用标准 (2)4、原材料检验标准 (2)4.1、金属材料 (2)4.2、通用五金件、紧固件 (2)5、钣金加工件检验标准 (2)5.1、外观 (2)5.2、尺寸 (2)5.3、压铆件 (3)5.4、焊接 (3)6、机箱整体检验标准 (3)6.1、机箱表面外观要求 (3)6.2、机箱稳定性要求 (4)7、喷涂件检验标准 (4)7.1、外观检验 (4)7.2、涂层附着力检验 (5)7.3、涂层抗酒精溶剂性检验 (6)7.4、压铆螺母、螺钉、螺纹孔经喷涂检验 (6)8、电镀件外观检验标准 (6)9、丝印检验标准 (6)10、装配通用检验标准 (6)无锡欧丰电梯配件有限公司钣金结构件检验标准1.目的规范钣金结构件的检验标准,以使产品的工艺要求和一致性得到有效控制2.适用范围本标准适用于公司各种钣金结构件的检验,图纸和技术文件并同使用。
当有冲突时,以图纸要求为准。
3.引用标准本标准的尺寸未注单位皆为mm,未注公差按国家标准IT13级执行GB/T1800.3-1998 极限与配合标准公差和基本偏差数值表GB/T1800.4 -1998 极限与配合标准公差等级和孔、轴的极限偏差表GB/1804-2000 一般公差未注公差的线性和角度尺寸的公差未注形位公差按GB/T1184 –1996 形状和位置公差未注公差值执行。
4.原材料检验标准(我司有权对厂家生产用原材料进厂抽检)4.1金属材料4.1.1钣材厚度及质量应符合国标,采用的钣材需出示性能测试报告及厂商证明。
4.1.2材料外观:平整无锈迹,无开裂与变形。
4.1.3 尺寸:按图纸或技术要求执行,本司未有的按现行国标执行。
4.2通用五金件、紧固件4.2.1外观:表面无绣迹、无毛刺批锋,整批来料外观一致性良好。
4.2.2尺寸:按图纸与国标要求。
4.2.2性能:试装配与使用性能符合产品要求。
5. 钣金加工件检验标准5.1 外观:钣金件表面平整,加工处无毛刺,凸起,裂痕等5.2 尺寸:尺寸按图纸要求检验,图中公差未标注部分按下表一执行表一:尺寸公差要求5.3 压铆件压铆螺母(柱)、压铆螺钉、涨铆螺母(柱)、拉铆螺母等,压上零部件后,螺纹不得变形(螺母或螺钉能自由进出,顺畅无卡滞现象),压铆件应与板面相平,不允许凸起或凹进(手感触摸应平滑),压铆件与板面垂直(垂直度<0.02),压铆后压铆区无变形、猪嘴现象,拉包的高度、壁厚应均匀一致,顶部不应有毛刺。
配电柜柜体钣金参数标准

配电柜柜体钣金参数标准 Prepared on 24 November 2020非标控制盘柜钣金技术参数标准一、项目概况:□室内□室外三、外形尺寸:(见附表二)□自立式□壁挂式□并联式□仿威图五、材质说明:1)柜体:□冷板□冷板□冷板□不锈钢□不锈钢□其它___________ 2)安装板:□冷板□冷板□冷板□热锌□热锌□热锌3)其它附件:□冷板□冷板□冷板□不锈钢□不锈钢□其它___________六、表面处理:1)柜体及附件表面处理:①喷粉形式:□平纹□橘纹□不喷□其它__________②喷粉颜色:□ RAL7035 □ 5Y7/1 □其它________________2)安装板:□冷板镀白锌□锌板(边缘防锈处理)□其它__________________ 七、结构:1)吊耳:□ 2个□ 4个□无2)通风系统:□百叶窗□风机开圆孔□风机开方孔□无3)出线方式:□底板小圆孔□底板大方孔加挡板□其它_____________ 4)底座样式:□无□柜体一体式□板材折弯焊接□仿威图底座(高度:□ 80mm □ 100mm □ 150mm)□角钢焊接式①角钢规格□ 40*40*3 □ 40*40*4 □ 40*40*5 □ 50*50*4 □ 50*50*5②底座高度□ 200mm □ 300mm □ 400mm □ 500mm □ 600mm□槽钢钢焊接式槽钢规格□ 8# (80*43*43)□ 10# (100*48*48)□ 16# (160*65*65)5)柜门:□单门□双门□单层门□双层门□后门6)框架:□角钢□扁钢□型材□无7)其它可选结构:□防雨顶盖□出线孔橡胶圈□柜内照明系统支架□墙壁挂架□门内侧加强筋□门内侧资料框□底座固定孔和柜体固定孔八、防护等级:(见附表一)柜体外壳要求防护等级为:□ IP54 □ IP53 □ IP52 □ IP44 □ IP43 □ IP42 □其它________ 九、附件:1)锁具:①品牌:□生久□星本□普通②类型:□平面锁□连杆锁□把手锁□圆柱锁□面板锁□搭扣2)铰链:①品牌:□生久□星本□普通②类型:□ 90°□ 110°□ 130°□ 180°□其它______附表一:柜体IP防护等级各要素及含义附表二:钣金生产后完成设计总结。
钣金常用规格尺寸表
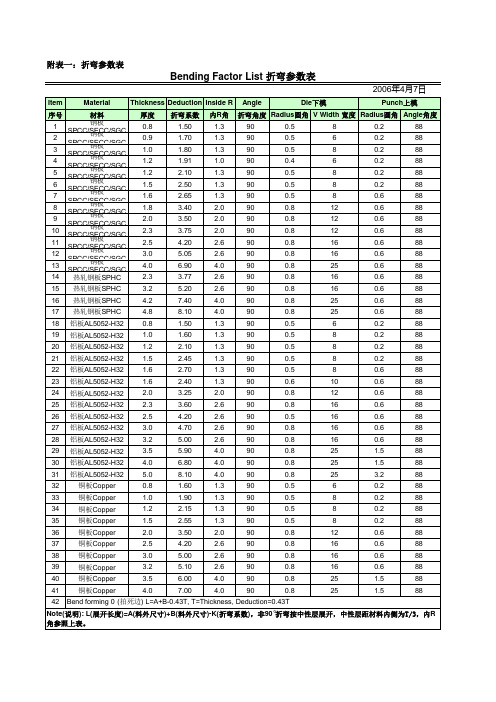
附表一:折弯参数表
Bending Factor List 折弯参数表
V槽为板厚的6-8倍,非90度展开=180度-角度/90度*折弯系数
折弯系数为板厚的1.8倍(铁板),铝板为(1.6倍)
在2mm以下的板材中,K因子为0.432,R=板厚时,展开尺寸能精确到0.05以内
Solidworks 如何设计钣金折弯的K因子(原创)2010-02-04 12:49
一般设计钣金最小内半径r=厚度/2,如果小于这个数,工艺上要开槽解决。
但客户指定的r情况下:用比如客户非要用r4或者r20对应的K因子就不同了。
不管r=多少,对普通Q235钢的K因子可以这样设置
请打开EXCEL用这个公式 K=POWER(内半径/板厚,1/7)*0.41 其他POWER表示某数的乘幂
比如在A1输入板厚"2",A2输入内半径"1",A3输入"=power(a2/a1,1/7)*0.41"
最后会在A3上显示0.371347,这个就是K因子了。
大家注意到0。
41了吗?对不同材料可以用下面的数据。
软黄铜或软铜材料:0.35
半硬铜或黄铜、软钢和铝等材料:0.41
青铜、硬铜、冷轧钢和弹簧钢等材料: 0.45
最后说明:
不同机器折弯的尺寸可能不一样,要更精确的数据要自己根据这个数据的基础上,折几个实物去修正。
钣金箱体生产误差标准

钣金箱体生产误差标准一、尺寸误差1. 长度误差:箱体长度的允许误差应不大于±1.0mm。
2. 宽度误差:箱体宽度的允许误差应不大于±0.5mm。
3. 高度误差:箱体高度的允许误差应不大于±0.5mm。
二、形状误差1. 平面度误差:箱体各平面的平面度误差应不大于0.2mm。
2. 对角线误差:箱体各对角线的允许误差应不大于±1.0mm。
3. 垂直度误差:箱体各立面的垂直度误差应不大于0.2mm/100mm。
4. 水平度误差:箱体各底面的水平度误差应不大于0.1mm/100mm。
三、定位误差1. 孔位误差:箱体上孔位的允许误差应不大于±0.5mm。
2. 平行度误差:箱体上平面的平行度误差应不大于0.2mm/100mm。
3. 垂直度误差:箱体上立面的垂直度误差应不大于0.2mm/100mm。
四、间隙误差1. 配合间隙:箱体各配合面的间隙应符合设计要求,间隙超出范围时应进行修整。
2. 转角间隙:箱体各转角处的间隙应符合设计要求,间隙超出范围时应进行修整。
五、焊接误差1. 焊缝平整度:焊接后的焊缝应平整,焊波高度应控制在0.5mm以内。
2. 焊缝夹角:焊接后的焊缝夹角应符合设计要求,角度偏差应不大于±2°。
3. 焊缝长度:焊接后的焊缝长度应符合设计要求,长度超出范围时应进行修整。
六、材质误差1. 材料厚度:箱体所使用的材料厚度应符合设计要求,厚度偏差应不大于±0.1mm。
2. 材料种类:箱体所使用的材料种类应符合设计要求,不得使用不合格的材料。
七、工艺误差1. 加工工艺:箱体的加工工艺应符合设计要求,不得因加工工艺不当而产生误差。
2. 热处理工艺:箱体在热处理过程中的变形应控制在允许范围内,以保证其精度和质量。
3. 装配工艺:箱体在装配过程中的配合精度和装配顺序应符合设计要求,以保证其正常运转和使用寿命。
4. 检验工艺:对箱体的生产过程应进行严格的检验,包括原材料检验、加工过程检验、成品检验等,以确保产品精度和质量。
钣金件通用技术条件

钣金件通用技术条件1.主题与范围1.1 本通用技术条件规定了我公司钣金产品(箱、柜、操作台、架等)相关的技术要求。
1.2 本通用技术条件适用以金属板材、带材、标准型材、管材、金属丝材为原料,以剪切、冲压、拉伸、折弯、拼焊等工艺方法成型的钣金件。
1.3 凡设计文件未明确技术要求的钣金件,均应按本通用技术条件的相应要求进行制造和验收。
1.4 在某些工序中采用车削、洗削、刨切、钻孔等机械加工方法时技术要求可参照通用技术条件相应条款或按GB1804公差与配合,GB1804形状和位置公差及相应的粗糙度选用。
2. 钣金零件通用技术条件2.1 总则2.1.1 零件表面上不允许有裂纹、分层、裂口、锈蚀及深度超过零件最小厚度公差的压伤及划伤。
表面上的手汗迹、油痕、斑点、锈蚀、轻微的划伤、压伤等,允许在零件厚度公差范围内进行光滑修磨排除。
2.1.2 零件的内、外边缘应去除毛刺,板厚大于0.5毫米的金属制件要去锐边、倒角或制圆。
2.1.3零件允许变薄后的板厚为钢板最小厚度的90%,其它材料变形后的板厚不得小于最小厚度的85%。
2.1.4零件的表面上允许有模具及夹具留下的痕迹,但不是剧烈的压伤或凹痕(这些地方的最小厚度不得低于2.1.3条规定)。
2.2 钣金零件的公差2.2.1剪切下料的尺寸偏差(表1)剪切后的尺寸偏差及两对角线长度之差值应控制在表中偏差范围内。
(表1)mm注:上述尺寸偏差对包容件应取正值,被包容件取负值。
2.2.2 普冲开角、冲孔的尺寸偏差A) 开角尺寸偏差为+0.3毫米,冲孔孔径尺寸偏差为+0.3毫米。
B) 冲孔的中心距尺寸偏差应符合表2规定(表2)2.2.3钣金零件折弯尺寸公差2.2.3.1图样上未标有尺寸公差的可按以下要求验收,一般零件折弯尺寸公差控制在±0.15/500毫米,折边长度每增加500毫米范围内,公差值递增±0.05毫米,即:±0.20/>500-1000毫米,±0.25/>1000-1500毫米……依此类推。
钣金件加工尺寸技术要求
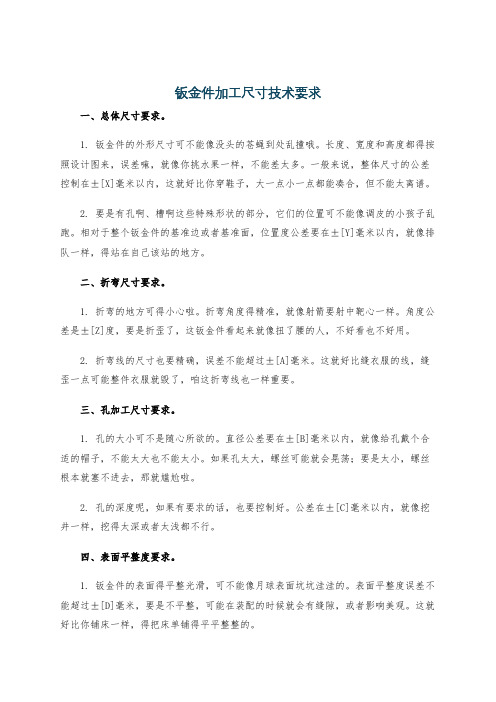
钣金件加工尺寸技术要求一、总体尺寸要求。
1. 钣金件的外形尺寸可不能像没头的苍蝇到处乱撞哦。
长度、宽度和高度都得按照设计图来,误差嘛,就像你挑水果一样,不能差太多。
一般来说,整体尺寸的公差控制在±[X]毫米以内,这就好比你穿鞋子,大一点小一点都能凑合,但不能太离谱。
2. 要是有孔啊、槽啊这些特殊形状的部分,它们的位置可不能像调皮的小孩子乱跑。
相对于整个钣金件的基准边或者基准面,位置度公差要在±[Y]毫米以内,就像排队一样,得站在自己该站的地方。
二、折弯尺寸要求。
1. 折弯的地方可得小心啦。
折弯角度得精准,就像射箭要射中靶心一样。
角度公差是±[Z]度,要是折歪了,这钣金件看起来就像扭了腰的人,不好看也不好用。
2. 折弯线的尺寸也要精确,误差不能超过±[A]毫米。
这就好比缝衣服的线,缝歪一点可能整件衣服就毁了,咱这折弯线也一样重要。
三、孔加工尺寸要求。
1. 孔的大小可不是随心所欲的。
直径公差要在±[B]毫米以内,就像给孔戴个合适的帽子,不能太大也不能太小。
如果孔太大,螺丝可能就会晃荡;要是太小,螺丝根本就塞不进去,那就尴尬啦。
2. 孔的深度呢,如果有要求的话,也要控制好。
公差在±[C]毫米以内,就像挖井一样,挖得太深或者太浅都不行。
四、表面平整度要求。
1. 钣金件的表面得平整光滑,可不能像月球表面坑坑洼洼的。
表面平整度误差不能超过±[D]毫米,要是不平整,可能在装配的时候就会有缝隙,或者影响美观。
这就好比你铺床一样,得把床单铺得平平整整的。
五、边缘加工要求。
1. 边缘要整齐,不能像被狗啃过似的。
切割或者加工后的边缘粗糙度要符合要求,不能有毛刺或者锯齿状。
要是有毛刺,就像刺猬一样,可能会扎到人,而且在装配的时候也可能会刮伤其他零件。
2. 要是有特殊的边缘处理,比如倒角或者倒圆,尺寸也要准确。
倒角或者倒圆的半径公差在±[E]毫米以内,这样看起来才会精致美观。
钣金机箱简介及通用检验标准

钣金机箱简介及通用检验标准钣金机箱简介及通用检验标准一、钣金机箱简介钣金机箱是针对金属薄板(一般在6mm以下)使用综合冷加工工艺,冷却形成后所需要的机箱。
加工工艺包括剪、冲、切、复合、折、焊接、铆接、拼接、成形(如汽车车身)等。
其显著的特征就是同一零件厚度一致。
使用钣金所制作的机箱,既能满足机箱的各种功能和外观的要求,又能使得冲压模具制造,成本低。
钣金具有重量轻、强度高、导电(能够用于电磁屏蔽)、成本低、大规模量产性能好等特点,目前在电子电器、通信、汽车工业、医疗器械等领域得到了广泛应用。
例如在电脑机箱、手机、MP3中,钣金是必不可少的组成部分。
随着钣金的应用越来越广泛,钣金件的设计变成了产品工业开发中很重要的一环。
机械工程师必须熟练掌握钣金件的设计技巧。
常见的钣金机壳有:电力机柜、网络机柜、服务器机柜、户外柜等,三河市华夏恒泰电子技术有限公司主营各类精密钣金产品的加工生产,包括钣金机箱、机柜、铝制机箱等。
这些都是用钣金材料制成的。
按钣金件的基本加工方式,如下料、折弯、拉伸、成形、焊接。
本规范阐述每一种加工方式所要注意的工艺要求。
下料根据加工方式的不同,可分为普冲、数冲、剪床开料、激光切割、风割,由于加工方法的不同,下料的加工工艺性也有所不同。
钣金下料方式主要为数冲和激光切割。
材料弯曲时,其圆角区上,外层收到拉伸,内层则受到压缩。
当材料厚度一定时,内r 越小,材料的拉伸和压缩就越严重;当外层圆角的拉伸应力超过材料的极限强度时,就会产生裂缝和折断,因此,弯曲零件的结构设计,应避免过小的弯曲圆角半径。
拉伸件底部与直壁之间的圆角半径应大于板厚,即r1≥t 。
为了使拉伸进行得更顺利,一般取r1=(3~5)t,最大圆角半径应小于或等于板厚的8倍,即r1≤8t。
拉伸件由于各处所受应力大小各不相同,使拉伸后的材料厚度会发生变化。
一般来说,底部中央保持原来的厚度,底部圆角处材料变薄,顶部靠近凸缘处材料变厚,矩形拉伸件四周圆角处材料变厚。
某公司钣金机箱包装规范
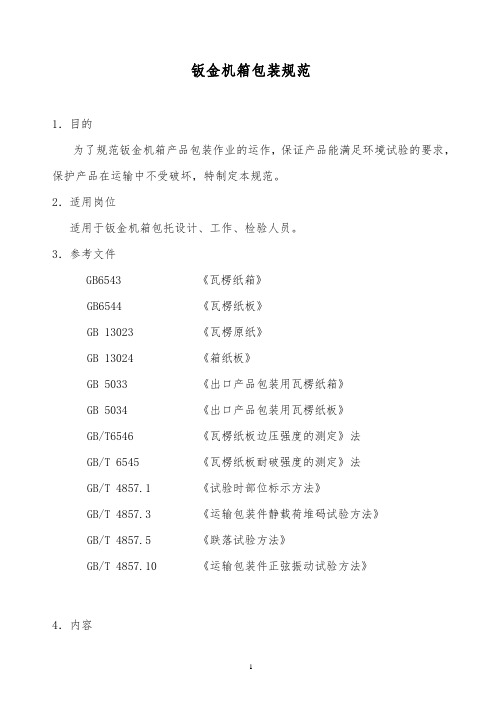
钣金机箱包装规范1.目的为了规范钣金机箱产品包装作业的运作,保证产品能满足环境试验的要求,保护产品在运输中不受破坏,特制定本规范。
2.适用岗位适用于钣金机箱包托设计、工作、检验人员。
3.参考文件GB6543 《瓦楞纸箱》GB6544 《瓦楞纸板》GB 13023 《瓦楞原纸》GB 13024 《箱纸板》GB 5033 《出口产品包装用瓦楞纸箱》GB 5034 《出口产品包装用瓦楞纸板》GB/T6546 《瓦楞纸板边压强度的测定》法GB/T 6545 《瓦楞纸板耐破强度的测定》法GB/T 4857.1 《试验时部位标示方法》GB/T 4857.3 《运输包装件静载荷堆码试验方法》GB/T 4857.5 《跌落试验方法》GB/T 4857.10 《运输包装件正弦振动试验方法》4.内容4.1包装准备4.1.1产品准备产品应是经检验合格可以出货的产品。
4.1.2材料准备以本规范之要求准备相应的包装材料。
4.2基本要求4.2.1为了保护产品之塑料,金属等基本面免受破坏,对产品加胶袋包装。
4.2.2为了缓冲产品在运输过程中产生的冲力,要对产品加强保护,需加衬垫或彩盒包装。
4.2.3按照客户包装要求进行包装5.包装材料5.1 纸箱5.1.1瓦楞纸板技术要求:5.1.2纸箱设计选材标准○1长宽比例超过2:1以及高度超过650mm的纸箱,必须用K=B纸板。
○2针对边压强度远远超出5410N/m,且无法通过堆码试验的产品,请选用其他高强度纸板。
○3若纸箱内装物可完全用来承重,如胶辘,则选用纸板时可降低一个等级。
○4客户规定用白色纸箱的,请用W=B材质纸板。
5.2 包装胶纸5.2.1 透明胶纸○1透明胶纸的规格为50mm±2mm,厚度为0.03mm~0.04mm。
○2透明胶纸的材料为OPP。
○3透明胶纸的初粘性应能粘住5号钢球。
5.2.2 牛皮胶纸○1牛皮胶纸的规格应用60mm±2mm,厚度为0.12mm~0.13mm。
钣金件检验标准

1.1卷尺、万能角度尺、游标卡尺(量程 0~200mm 、精度0.02mm )2.适用范围:2.1本检验规范适用于钣金通用检验标准(外量,尺寸,包装,破坏性试验等)。
3.作业方法: 3.1剪床开料 3.1.1外观保证3.1.1.1剪床开料必须用经IQC 检验合格之板材,大料平直度、外表面状态必须符合IQC 检验标准。
3.1.1.2未经确认不得采用已生锈之SECC 和SPCC 板料,以及表面严重划伤之SUS 板料。
3.1.1.3对胶沙不锈钢应注意开料之纹向要求,不可在不确定情况下作出纹向任意开料,并严格保护表面,以避免刮伤。
3.1.1.4剪床开料之批锋应小于料厚之3%及戴无尘手套检查,来回摸边缘不刮手套,不起毛屑。
3.1.1.5激光开料需要去毛屑,戴无尘手套检查,来回摸边缘不刮手套,不起毛屑。
3.1.1.6数冲开料需要去毛屑,戴无尘手套检查,来回摸边缘不刮手套,不起毛屑。
3.1.1.7机加工的工件需要去毛屑,戴无尘手套检查,来回摸边缘不刮手套,不起毛屑。
3.1.1.8外发加工回来工件或部品需要去毛屑,IQC 戴无尘手套检查,来回摸边缘不刮手套,不起毛屑。
3.1.2尺寸控制3.1.2.1为保证钣金成形尺寸,减少过程累积误差对工件尺寸的影响,剪床开料尺寸允差按下表检验:3.1.2.2对一开几过多的开料件,如单一方向开料数量超过六件(一般应为偶数),应先将料对开,然尺寸范围 0-200 200-500 500-1000 >1000 允许偏差±0.15±0.3±0.5±0.8有毛刺,刮手NG有毛刺,刮手NG有倒角及不刮手---OK3.6.1.5布于主要外观表面及拼角位的焊缝应满焊,并能方便地打磨处理,不能作打磨处理的次要外观表面及拼角位的焊缝及焊点一定要平顺均匀,大小适中。
3.6.1.6对外表面为胶沙不锈钢的钣金箱体之焊接,应尽量避免于产品外观之正反面烧焊,而将焊点布于内折边及拼角位,对不作喷涂处理之不锈钢其上所焊接之螺丝或丝母,也应为不锈钢、避免生锈及腐蚀影响外观及使用。
钣金折弯系数

折 弯 系 数 一 览 表
A5052P/5052P铝板(90° )
板材厚度 V型槽 折弯最小尺寸 实际厚度 0.3
ξ ξ
6 4
7 5
8 5.5
10 7
12 8.5
16 11
25 17.5
40 28
备注
0.5 0.8 1 1.2 1.5 2 2.5 3 4
实际厚度 实际厚度
ξ
实际厚度
ξ
0.87 1.6
ξ 0.7 实际厚度 0.46 ξ 1.1 实际厚度 ξ
1.35-1.40
0.46 1.16
0.46 1.22
压平系数 为0.5
实际厚度 0.95 ξ 1.62 实际厚度 1.17 ξ 1.86 实际厚度
ξ
0.95 1.72 1.17 2 1.41 2.32
0.95 1.84 1.17 2.06 1.41 2.4 2.98
实际厚度
ξ
实际厚度
ξ
1.34 2.16
1.34 2.24 2.75
1.34 2.34
实际厚度
ξ
实际厚度
ξ
2.3 3.5
1.34 2.48 1.85 3.04 2.3 3.72
实际厚度
ξ
1.88 3.46 2.3 3.9 2.85 4.64
2.85 5.16
实际厚度
ξ
SUS304不锈钢板(90° )
板材厚度 V型槽 折弯最小尺寸 实际厚度 0.3 0.5 0.8 1 1.2 1.5 2 2.5 3 4 6 4 7 5 8 5.5 10 7 12 8.5 16 11 25 17.5 40 28 备注
V16为不垫膜
实际厚度
ξ
钣金件通用公差精度的标准
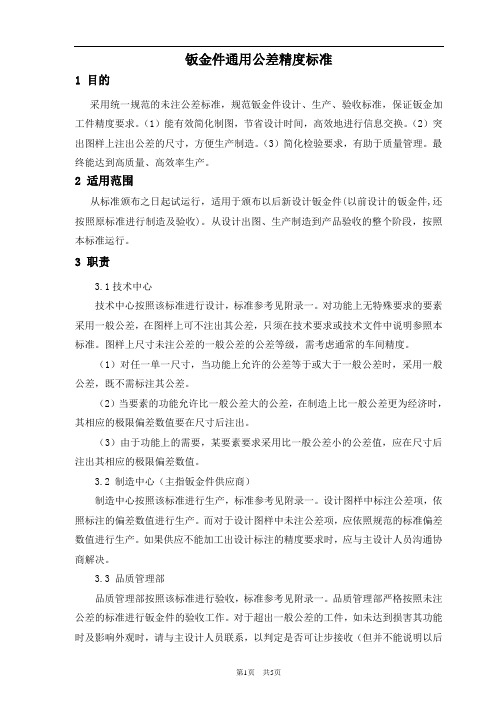
钣金件通用公差精度标准1 目的采用统一规范的未注公差标准,规范钣金件设计、生产、验收标准,保证钣金加工件精度要求。
(1)能有效简化制图,节省设计时间,高效地进行信息交换。
(2)突出图样上注出公差的尺寸,方便生产制造。
(3)简化检验要求,有助于质量管理。
最终能达到高质量、高效率生产。
2 适用范围从标准颁布之日起试运行,适用于颁布以后新设计钣金件(以前设计的钣金件,还按照原标准进行制造及验收)。
从设计出图、生产制造到产品验收的整个阶段,按照本标准运行。
3 职责3.1技术中心技术中心按照该标准进行设计,标准参考见附录一。
对功能上无特殊要求的要素采用一般公差,在图样上可不注出其公差,只须在技术要求或技术文件中说明参照本标准。
图样上尺寸未注公差的一般公差的公差等级,需考虑通常的车间精度。
(1)对任一单一尺寸,当功能上允许的公差等于或大于一般公差时,采用一般公差,既不需标注其公差。
(2)当要素的功能允许比一般公差大的公差,在制造上比一般公差更为经济时,其相应的极限偏差数值要在尺寸后注出。
(3)由于功能上的需要,某要素要求采用比一般公差小的公差值,应在尺寸后注出其相应的极限偏差数值。
3.2 制造中心(主指钣金件供应商)制造中心按照该标准进行生产,标准参考见附录一。
设计图样中标注公差项,依照标注的偏差数值进行生产。
而对于设计图样中未注公差项,应依照规范的标准偏差数值进行生产。
如果供应不能加工出设计标注的精度要求时,应与主设计人员沟通协商解决。
3.3 品质管理部品质管理部按照该标准进行验收,标准参考见附录一。
品质管理部严格按照未注公差的标准进行钣金件的验收工作。
对于超出一般公差的工件,如未达到损害其功能时及影响外观时,请与主设计人员联系,以判定是否可让步接收(但并不能说明以后都可降低标准)。
若工件的功能受到损害时请供应商返工或报废。
4 制定本标准依据参考国际标准:ISO 2768, 国家标准:GB/T 1184-1996、GB/T 1804-2000。