塑料挤出技术
塑料挤出成型技术
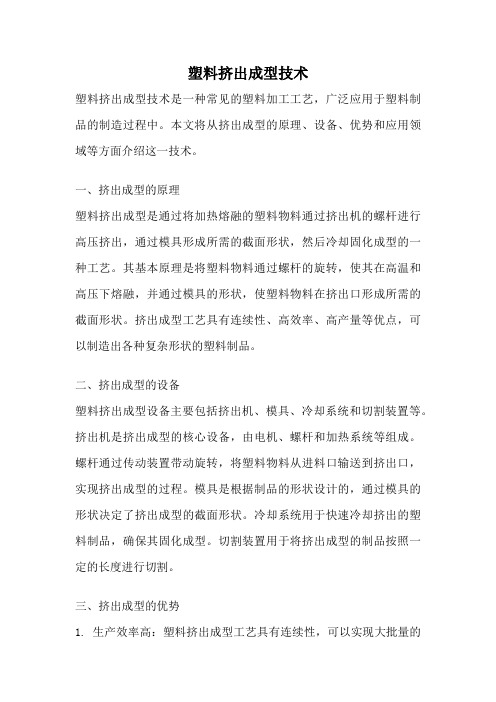
塑料挤出成型技术塑料挤出成型技术是一种常见的塑料加工工艺,广泛应用于塑料制品的制造过程中。
本文将从挤出成型的原理、设备、优势和应用领域等方面介绍这一技术。
一、挤出成型的原理塑料挤出成型是通过将加热熔融的塑料物料通过挤出机的螺杆进行高压挤出,通过模具形成所需的截面形状,然后冷却固化成型的一种工艺。
其基本原理是将塑料物料通过螺杆的旋转,使其在高温和高压下熔融,并通过模具的形状,使塑料物料在挤出口形成所需的截面形状。
挤出成型工艺具有连续性、高效率、高产量等优点,可以制造出各种复杂形状的塑料制品。
二、挤出成型的设备塑料挤出成型设备主要包括挤出机、模具、冷却系统和切割装置等。
挤出机是挤出成型的核心设备,由电机、螺杆和加热系统等组成。
螺杆通过传动装置带动旋转,将塑料物料从进料口输送到挤出口,实现挤出成型的过程。
模具是根据制品的形状设计的,通过模具的形状决定了挤出成型的截面形状。
冷却系统用于快速冷却挤出的塑料制品,确保其固化成型。
切割装置用于将挤出成型的制品按照一定的长度进行切割。
三、挤出成型的优势1. 生产效率高:塑料挤出成型工艺具有连续性,可以实现大批量的生产,提高生产效率。
2. 制品质量稳定:挤出成型的制品形状稳定,尺寸精确,质量可靠。
3. 适用范围广:挤出成型工艺适用于各种塑料,可以制造出各种形状的制品,如管材、板材、型材等。
4. 设备投资少:相对于其他塑料加工工艺,挤出成型设备投资较少,生产成本较低。
5. 可塑性强:挤出成型的塑料物料可根据需要选择,可以加入各种填充剂、增强剂等,增加塑料的性能。
四、挤出成型的应用领域塑料挤出成型技术广泛应用于建筑、包装、汽车、电子、家电等行业。
在建筑行业中,挤出成型制造的塑料管材、型材、板材等被广泛应用于室内装饰、给排水系统、电线电缆等方面。
在包装行业中,挤出成型用于制造各种塑料包装盒、瓶子、袋子等。
在汽车行业中,挤出成型的塑料制品用于汽车内饰、外饰等部件。
在电子和家电行业中,挤出成型的塑料制品用于电线电缆的保护管、电器外壳等。
塑料挤出技术

第五章挤出成型5.0 本章介绍1、主要内容:概论、单螺杆挤出机的基本结构、挤出理论和几种制品的挤出工艺。
2、重点:挤出理论、粒料的制备3、难点:挤出理论。
4、教学要求:(1)掌握挤出理论,单螺杆挤出机的结构。
(2)掌握几种制品的挤出工艺。
挤出成型又称挤出模塑,是塑料重要的成型方法之一,绝大多数热塑性塑料均可用此法成型。
这种成型方法的特点是具有很高的生产率且能生产连续的型材,如管、棒、板、薄膜、丝、电线、电缆以及各种型材,还可用来混合、塑化、造粒和着色等。
挤出成型过程分两个阶段进行。
第一阶段将物料加热塑化,使呈粘流状态并在加压下通过一定形状的口模而成为截面与口模形状相仿的连续体;第二阶段将这种连续体用适当的方法冷却、定型为所需产品。
物料的塑化和加压过程一般都是在挤出机内进行。
挤出机按其加压方式可分为螺杆式和柱塞式两种。
前者的特点是,借助螺杆旋转时螺纹所产生的推动力将物料推向口模。
这种挤出机中通过螺杆强烈的剪切作用,促进物料的塑化和均匀分散,同时使挤出过程连续进行,因此可以提高挤出制品的质量和产量,它适用于绝大多数热塑性塑料的挤出。
柱塞式挤出机中,通过粒筒加热塑化的物料,由柱塞推向口模。
这种挤出机能够产生较大的压力,一般来说,其操作是间歇进行,物料的塑化程度和均匀性不如螺杆式挤出机,因此应用范围受限制。
它适用于聚四氟乙烯,超高相对分子质量聚乙烯等塑料的挤出。
本章以螺杆式挤出机的挤出工艺及有关辅助设备为重点加以介绍。
5.1 单螺杆挤出机的基本结构和辅机一、单螺杆挤出机基本结构单螺杆挤出机基本结构,主要由传动系统、加料系统、挤压系统、加热系统、冷却系统以及机头和口模等部分组成1、传动系统传动系统是挤出机的重要组成部分之一。
它的作用是在给定的工艺条件(如机头压力、螺杆转数、挤出量、温度等)下使螺杆具有必要的扭矩和转数均匀地回转而完成挤出过程。
传动系统由电动机、减速装置、变速器及轴承系统组成。
常用的挤出机电动机有交流整流子电动机和直流电动机。
塑料挤出工艺流程
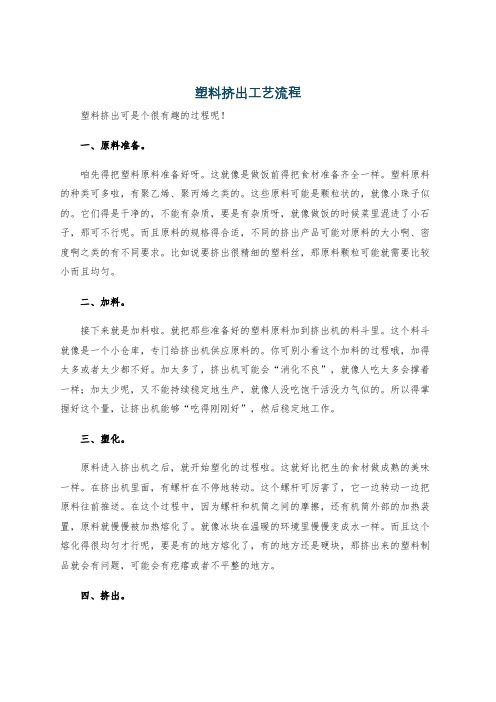
塑料挤出工艺流程塑料挤出可是个很有趣的过程呢!一、原料准备。
咱先得把塑料原料准备好呀。
这就像是做饭前得把食材准备齐全一样。
塑料原料的种类可多啦,有聚乙烯、聚丙烯之类的。
这些原料可能是颗粒状的,就像小珠子似的。
它们得是干净的,不能有杂质,要是有杂质呀,就像做饭的时候菜里混进了小石子,那可不行呢。
而且原料的规格得合适,不同的挤出产品可能对原料的大小啊、密度啊之类的有不同要求。
比如说要挤出很精细的塑料丝,那原料颗粒可能就需要比较小而且均匀。
二、加料。
接下来就是加料啦。
就把那些准备好的塑料原料加到挤出机的料斗里。
这个料斗就像是一个小仓库,专门给挤出机供应原料的。
你可别小看这个加料的过程哦,加得太多或者太少都不好。
加太多了,挤出机可能会“消化不良”,就像人吃太多会撑着一样;加太少呢,又不能持续稳定地生产,就像人没吃饱干活没力气似的。
所以得掌握好这个量,让挤出机能够“吃得刚刚好”,然后稳定地工作。
三、塑化。
原料进入挤出机之后,就开始塑化的过程啦。
这就好比把生的食材做成熟的美味一样。
在挤出机里面,有螺杆在不停地转动。
这个螺杆可厉害了,它一边转动一边把原料往前推送。
在这个过程中,因为螺杆和机筒之间的摩擦,还有机筒外部的加热装置,原料就慢慢被加热熔化了。
就像冰块在温暖的环境里慢慢变成水一样。
而且这个熔化得很均匀才行呢,要是有的地方熔化了,有的地方还是硬块,那挤出来的塑料制品就会有问题,可能会有疙瘩或者不平整的地方。
四、挤出。
塑化好的塑料就该挤出啦。
这个时候,塑料就像听话的小宠物一样,被螺杆沿着机筒的通道挤到模具那里。
模具就像是一个神奇的造型师,可以把塑料变成各种各样的形状。
如果是圆形的模具,那挤出来的就是圆形的塑料制品,像塑料管材之类的;如果是扁平的模具,那就可以挤出塑料片材。
这个过程就像是把软软的面团通过不同形状的模具做成各种点心一样,超级神奇的。
五、冷却定型。
刚挤出来的塑料制品还是热乎乎、软软的呢,就像刚出炉的面包。
塑料挤塑工艺的原理和特点
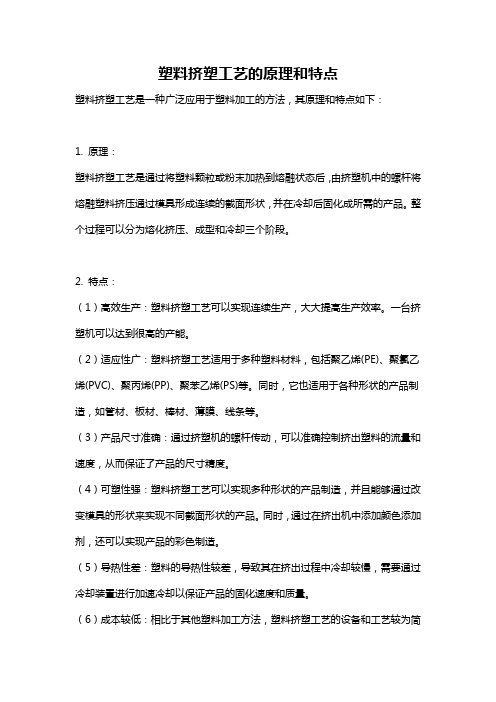
塑料挤塑工艺的原理和特点
塑料挤塑工艺是一种广泛应用于塑料加工的方法,其原理和特点如下:
1. 原理:
塑料挤塑工艺是通过将塑料颗粒或粉末加热到熔融状态后,由挤塑机中的螺杆将熔融塑料挤压通过模具形成连续的截面形状,并在冷却后固化成所需的产品。
整个过程可以分为熔化挤压、成型和冷却三个阶段。
2. 特点:
(1)高效生产:塑料挤塑工艺可以实现连续生产,大大提高生产效率。
一台挤塑机可以达到很高的产能。
(2)适应性广:塑料挤塑工艺适用于多种塑料材料,包括聚乙烯(PE)、聚氯乙烯(PVC)、聚丙烯(PP)、聚苯乙烯(PS)等。
同时,它也适用于各种形状的产品制造,如管材、板材、棒材、薄膜、线条等。
(3)产品尺寸准确:通过挤塑机的螺杆传动,可以准确控制挤出塑料的流量和速度,从而保证了产品的尺寸精度。
(4)可塑性强:塑料挤塑工艺可以实现多种形状的产品制造,并且能够通过改变模具的形状来实现不同截面形状的产品。
同时,通过在挤出机中添加颜色添加剂,还可以实现产品的彩色制造。
(5)导热性差:塑料的导热性较差,导致其在挤出过程中冷却较慢,需要通过冷却装置进行加速冷却以保证产品的固化速度和质量。
(6)成本较低:相比于其他塑料加工方法,塑料挤塑工艺的设备和工艺较为简
单,投资成本较低,操作相对简单,维护成本也较低。
总的来说,塑料挤塑工艺是一种高效、适应性广、产品尺寸准确、可塑性强、成本较低的塑料加工方法。
它在包装、建筑、汽车、电子、家电等行业中得到广泛应用,并且随着科技的不断进步和工艺的改进,塑料挤塑工艺将会更加多样化和灵活化。
挤出成型的原理和工艺流程
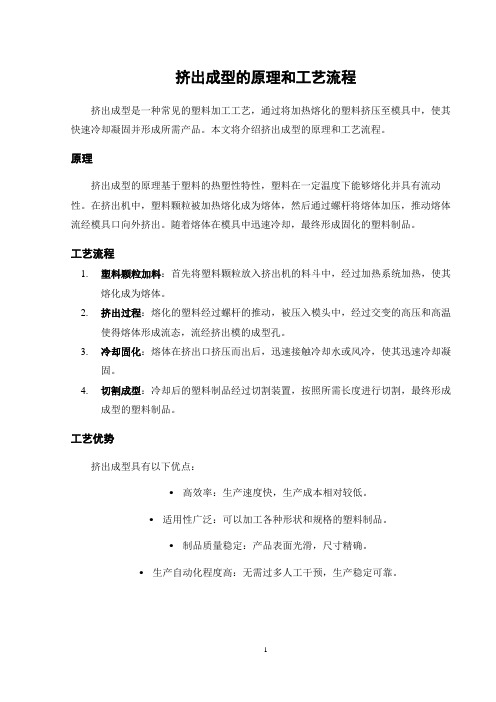
挤出成型的原理和工艺流程
挤出成型是一种常见的塑料加工工艺,通过将加热熔化的塑料挤压至模具中,使其快速冷却凝固并形成所需产品。
本文将介绍挤出成型的原理和工艺流程。
原理
挤出成型的原理基于塑料的热塑性特性,塑料在一定温度下能够熔化并具有流动性。
在挤出机中,塑料颗粒被加热熔化成为熔体,然后通过螺杆将熔体加压,推动熔体流经模具口向外挤出。
随着熔体在模具中迅速冷却,最终形成固化的塑料制品。
工艺流程
1.塑料颗粒加料:首先将塑料颗粒放入挤出机的料斗中,经过加热系统加热,使其
熔化成为熔体。
2.挤出过程:熔化的塑料经过螺杆的推动,被压入模头中,经过交变的高压和高温
使得熔体形成流态,流经挤出模的成型孔。
3.冷却固化:熔体在挤出口挤压而出后,迅速接触冷却水或风冷,使其迅速冷却凝
固。
4.切割成型:冷却后的塑料制品经过切割装置,按照所需长度进行切割,最终形成
成型的塑料制品。
工艺优势
挤出成型具有以下优点:
•高效率:生产速度快,生产成本相对较低。
•适用性广泛:可以加工各种形状和规格的塑料制品。
•制品质量稳定:产品表面光滑,尺寸精确。
•生产自动化程度高:无需过多人工干预,生产稳定可靠。
应用领域
挤出成型广泛应用于塑料制品生产行业,如管道、板材、型材、薄膜、包装材料等领域。
其高效率、高质量的特点使其成为塑料制品生产中不可或缺的一环。
总的来说,挤出成型作为一种常见的塑料加工工艺,通过简单高效的操作流程,可以生产出质量稳定的塑料制品,在工业生产中发挥着重要作用。
塑料挤出成型技术
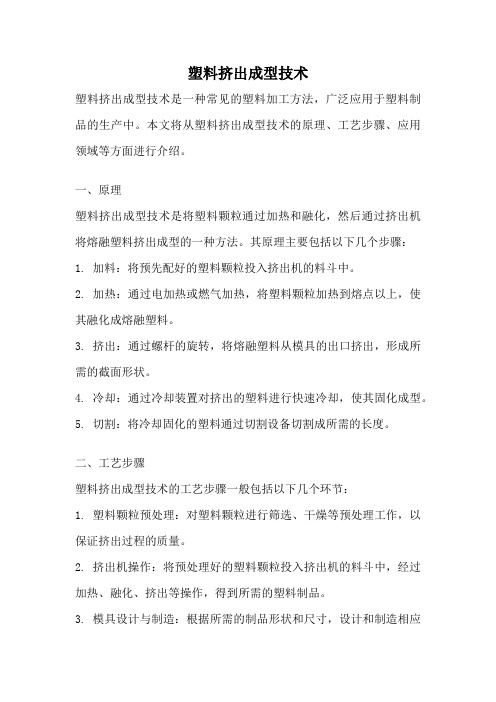
塑料挤出成型技术塑料挤出成型技术是一种常见的塑料加工方法,广泛应用于塑料制品的生产中。
本文将从塑料挤出成型技术的原理、工艺步骤、应用领域等方面进行介绍。
一、原理塑料挤出成型技术是将塑料颗粒通过加热和融化,然后通过挤出机将熔融塑料挤出成型的一种方法。
其原理主要包括以下几个步骤:1. 加料:将预先配好的塑料颗粒投入挤出机的料斗中。
2. 加热:通过电加热或燃气加热,将塑料颗粒加热到熔点以上,使其融化成熔融塑料。
3. 挤出:通过螺杆的旋转,将熔融塑料从模具的出口挤出,形成所需的截面形状。
4. 冷却:通过冷却装置对挤出的塑料进行快速冷却,使其固化成型。
5. 切割:将冷却固化的塑料通过切割设备切割成所需的长度。
二、工艺步骤塑料挤出成型技术的工艺步骤一般包括以下几个环节:1. 塑料颗粒预处理:对塑料颗粒进行筛选、干燥等预处理工作,以保证挤出过程的质量。
2. 挤出机操作:将预处理好的塑料颗粒投入挤出机的料斗中,经过加热、融化、挤出等操作,得到所需的塑料制品。
3. 模具设计与制造:根据所需的制品形状和尺寸,设计和制造相应的模具。
4. 挤出成型:将熔融塑料从模具的出口挤出,形成所需的截面形状。
5. 冷却与固化:通过冷却装置对挤出的塑料进行快速冷却,使其固化成型。
6. 切割与包装:将冷却固化的塑料通过切割设备切割成所需的长度,并进行包装。
三、应用领域塑料挤出成型技术广泛应用于各个领域的塑料制品生产中,例如:1. 建筑行业:生产塑料管道、塑料板材、塑料薄膜等建筑材料。
2. 包装行业:生产塑料袋、塑料瓶、塑料容器等包装制品。
3. 汽车行业:生产汽车零部件,如塑料车门、塑料仪表盘等。
4. 家电行业:生产电视机外壳、冰箱内胆等家电配件。
5. 日用品行业:生产塑料梳子、塑料杯子、塑料衣架等日用品。
总结:塑料挤出成型技术是一种常见的塑料加工方法,通过加热和融化塑料颗粒,然后通过挤出机将熔融塑料挤出成型。
该技术具有工艺简单、生产效率高、适用范围广等优点,被广泛应用于各个领域的塑料制品生产中。
塑料挤出成型技术

塑料挤出成型技术塑料挤出成型技术是一种常见的塑料加工方法,也是工业生产中常用的一种成型工艺。
它通过塑料熔化、挤出和冷却过程,将原料塑料加工成希望的形状,广泛应用于包装、建筑、电子、汽车等行业。
塑料挤出成型技术的主要步骤包括原料准备、料斗进料、塑化、挤出、冷却、切割和收集。
首先需要选择合适的塑料原料,常见的有聚乙烯(PE)、聚丙烯(PP)、聚氯乙烯(PVC)等多种塑料。
然后将原料倒入料斗,通过螺杆与筒筒的高速旋转和加热,将塑料逐渐熔化和塑化,形成熔融状态的塑料。
接下来,熔融塑料被螺杆推进到挤出机头处。
挤出机头上设有一个模具,通过机头的压力和模具的形状来决定最终挤出产物的形状。
同时,通过调整机头和模具的温度和压力,可以控制挤出产物的尺寸和外观。
在挤出机头之后,熔融塑料经过冷却系统的冷却,使其迅速固化。
冷却系统通常由水或气流组成,可以根据具体需求进行调整。
冷却后的塑料产品被切割成所需的长度,然后便可由收集系统进行收集和包装。
塑料挤出成型技术具有许多优点。
首先,它可以高效地生产出大量形状复杂、尺寸精确的塑料制品。
其次,挤出成型的产品表面光滑,质量稳定可靠。
此外,该技术可以应用于各种塑料品种,满足不同行业的需求。
与注塑成型相比,塑料挤出成型的设备和工艺简单,易于操作和维护。
然而,塑料挤出成型技术也存在一些问题需要注意。
首先,塑料挤出过程中的原材料选择和控制非常重要,不同的塑料材料具有不同的特性,选择合适的塑料对产品质量至关重要。
其次,在挤出机的运行过程中,需要严格控制温度、压力等参数,确保挤出产物的质量和外观。
综上所述,塑料挤出成型技术是一种重要的塑料加工方法,广泛应用于各个行业。
正确掌握和应用塑料挤出成型技术,可以提高产品质量、降低生产成本,并为工业发展提供有力支持。
因此,我们在实际生产中要充分了解该技术的原理和操作要点,注重原料的选择和质量控制,以确保塑料挤出成型的效果和成品质量。
这样才能更好地推动我国塑料行业的快速发展,迎接技术创新和市场竞争的挑战。
塑料挤出成型技术论文

塑料挤出成型技术论文塑料挤出成型技术是一种常见的塑料加工方法,广泛应用于工业生产中。
本文将对塑料挤出成型技术进行详细介绍,包括其原理、工艺特点以及应用领域。
一、原理塑料挤出成型是指将塑料颗粒通过加热软化后,通过挤出机的螺杆将软化塑料挤出成型具有一定截面形状的产品的一种加工方法。
挤出机将熔融塑料物料压入模具中成形,然后冷却固化,最终得到所需的塑料制品。
二、工艺特点1.高效率:塑料挤出成型技术生产效率高,一台挤出机可以连续24小时工作,生产效率高,适合大批量生产。
2.成型精度高:通过挤出机的螺杆和模具的设计,可以实现复杂形状的产品挤出成型,保证产品的尺寸精准。
3.节能环保:相比其他塑料加工方法,挤出成型过程中能耗较低,且废料少,符合环保要求。
4.适用范围广:塑料挤出成型技术适用于各种类型的塑料,包括聚乙烯、聚丙烯、聚氯乙烯等,应用领域广泛。
三、应用领域1.建筑行业:塑料挤出成型技术在建筑行业中得到广泛应用,如生产塑料管道、门窗框等建筑材料。
2.包装行业:塑料挤出成型技术可生产各种塑料包装制品,如塑料瓶、塑料薄膜等,应用于食品、日用品等包装行业。
3.交通运输:塑料挤出成型技术也用于生产汽车配件、船舶构件等交通运输领域的制品。
4.家居用品:塑料挤出成型技术可制造家具、厨房用具等家居用品,广泛应用于家居生活领域。
综上所述,塑料挤出成型技术作为一种常见的塑料加工方法,具有高效率、成型精度高、节能环保等特点,被广泛应用于建筑、包装、交通运输、家居用品等领域,为各行业提供了高质量的塑料制品。
随着科技的不断进步,塑料挤出成型技术将在未来有更广阔的发展空间,为塑料制品的生产带来更多创新和可能性。
塑料挤出成型技术有哪些

塑料挤出成型技术有哪些在塑料加工领域中,塑料挤出成型技术是一种常见且广泛应用的制造方法。
通过塑料挤出成型技术,可以生产出各种形状和尺寸的塑料制品,应用于日常生活、工业生产等诸多领域。
塑料挤出成型技术主要包括以下几种形式。
1. 单螺杆挤出技术单螺杆挤出技术是一种较为基础的挤出成型技术,通过单螺杆挤出机将加热熔化的塑料原料压入模具中,形成所需形状的制品。
单螺杆挤出机具有结构简单、操作方便等优点,广泛应用于塑料管材、板材等制品的生产。
2. 双螺杆挤出技术双螺杆挤出技术相较于单螺杆挤出技术,在挤出效果和生产效率上有所提升。
双螺杆挤出机通过两根螺杆共同作用,使塑料原料更均匀地被挤出,适用于生产复杂结构或要求更高精度的塑料制品。
3. 鼓风机挤出技术鼓风机挤出技术是一种应用较为广泛的塑料挤出工艺,主要适用于生产塑料薄膜、袋类制品等。
通过鼓风机挤出机将高压气流吹入熔化的塑料原料中,使其在模具中薄而均匀地被挤压形成薄膜状制品。
4. 吹塑挤出技术吹塑挤出技术是一种常用于生产塑料容器、瓶子等中空制品的挤出工艺。
通过吹塑挤出机将熔化的塑料颗粒挤出并在模具中吹气,使其膨胀成型而成中空制品。
吹塑挤出技术能够生产出形状复杂、壁薄的塑料制品,广泛应用于包装行业。
5. 挤出涂层技术挤出涂层技术是将熔化的塑料原料挤出并涂覆在基材表面,形成带有塑料涂层的制品的工艺。
挤出涂层技术可以提高制品的耐磨性、防水性等性能,广泛应用于制造建筑材料、电缆等领域。
综上所述,塑料挤出成型技术涵盖了单螺杆挤出、双螺杆挤出、鼓风机挤出、吹塑挤出和挤出涂层等多种形式。
这些技术各具特点,适用于不同类型的塑料制品生产,为塑料加工领域的发展提供了多种解决方案。
随着技术的不断发展和创新,塑料挤出成型技术将会进一步完善和拓展,推动塑料制品的生产和应用领域不断扩大。
塑料挤出的基本原理

塑料挤出的基本原理塑料挤出是一种常用的工艺方法,用于制造各种塑料制品,如管道、板材、薄膜、线缆保护套等。
这种工艺方法的基本原理是通过加热、熔融和挤出,将塑料料料从挤出机的筒体中挤出,经过模头形成所需的截面和尺寸,并通过冷却和定型工艺使其固化。
塑料挤出工艺的主要组成部分包括挤出机、模头、冷却装置和牵引设备等。
下面将从这些方面详细介绍塑料挤出的基本原理。
1.挤出机:挤出机是塑料挤出工艺的核心装备,由进料系统、螺杆和筒体组成。
首先,塑料原料通过进料系统被送入挤出机的筒体中。
然后,在机筒的加热和螺杆的运转下,塑料原料逐渐熔化并混合均匀。
最后,高温高压下的熔融塑料由螺杆推送向模头。
2.模头:模头是挤出机的核心部件之一,其主要作用是将熔融塑料按照所需的截面和尺寸形成,然后经过冷却和定型设备进行固化。
模具的设计和制造对最终制品的质量和性能有着重要影响。
常见的模头类型包括单螺杆模头、双螺杆模头、多螺杆模头和陶瓷膜模头等。
3.冷却装置:冷却装置用于使熔融塑料快速冷却和固化,从而形成所需的截面和尺寸。
冷却装置通常由水冷却系统组成,水通过内部的管道流过模具周围,对熔融塑料进行冷却。
不同的挤出工艺,例如真空冷却、喷淋冷却、气体冷却等,可以根据具体的要求来选择。
4.牵引设备:牵引设备用于将挤出的塑料制品从模具上牵引出来,并提供适当的张力,以保持制品的尺寸和形状。
牵引设备通常由牵引辊或牵引链组成,具有不同速度调节,以适应不同的生产需求。
总的来说,塑料挤出的基本原理可以归纳为四个步骤:加热、熔融、挤出和冷却。
通过挤出机,将塑料原料加热熔融,然后通过模头形成所需的截面和尺寸,并通过冷却装置使其固化。
牵引设备用于将制品从模具上牵引出来,并保持其尺寸和形状。
这种工艺方法广泛应用于塑料制品的生产中,具有高效、经济和可塑性好的特点。
塑料挤出成型工艺与实例
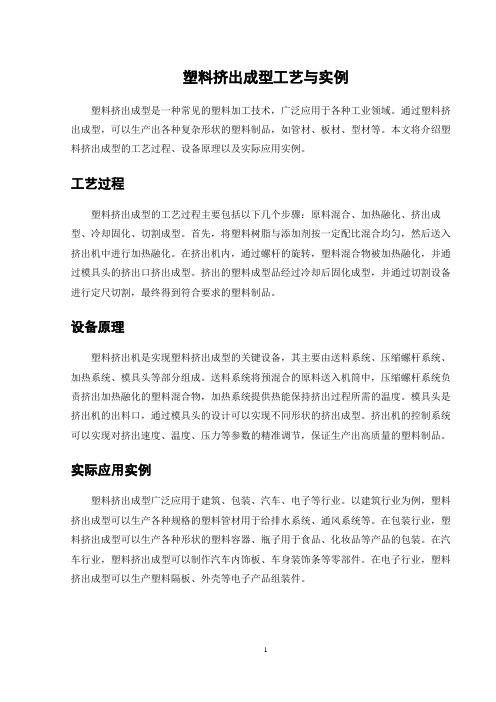
塑料挤出成型工艺与实例塑料挤出成型是一种常见的塑料加工技术,广泛应用于各种工业领域。
通过塑料挤出成型,可以生产出各种复杂形状的塑料制品,如管材、板材、型材等。
本文将介绍塑料挤出成型的工艺过程、设备原理以及实际应用实例。
工艺过程塑料挤出成型的工艺过程主要包括以下几个步骤:原料混合、加热融化、挤出成型、冷却固化、切割成型。
首先,将塑料树脂与添加剂按一定配比混合均匀,然后送入挤出机中进行加热融化。
在挤出机内,通过螺杆的旋转,塑料混合物被加热融化,并通过模具头的挤出口挤出成型。
挤出的塑料成型品经过冷却后固化成型,并通过切割设备进行定尺切割,最终得到符合要求的塑料制品。
设备原理塑料挤出机是实现塑料挤出成型的关键设备,其主要由送料系统、压缩螺杆系统、加热系统、模具头等部分组成。
送料系统将预混合的原料送入机筒中,压缩螺杆系统负责挤出加热融化的塑料混合物,加热系统提供热能保持挤出过程所需的温度。
模具头是挤出机的出料口,通过模具头的设计可以实现不同形状的挤出成型。
挤出机的控制系统可以实现对挤出速度、温度、压力等参数的精准调节,保证生产出高质量的塑料制品。
实际应用实例塑料挤出成型广泛应用于建筑、包装、汽车、电子等行业。
以建筑行业为例,塑料挤出成型可以生产各种规格的塑料管材用于给排水系统、通风系统等。
在包装行业,塑料挤出成型可以生产各种形状的塑料容器、瓶子用于食品、化妆品等产品的包装。
在汽车行业,塑料挤出成型可以制作汽车内饰板、车身装饰条等零部件。
在电子行业,塑料挤出成型可以生产塑料隔板、外壳等电子产品组装件。
通过塑料挤出成型技术,可以实现对塑料原料的高效加工,生产出多样化的塑料制品,满足不同行业的需求。
挤出成型工艺简单易操作,具有较高的生产效率和一定的经济性,因此得到了广泛的应用和推广。
总而言之,塑料挤出成型是一种重要的塑料加工技术,在工业生产中有着广泛的应用前景,通过不断改进技术和设备,可以进一步提升挤出成型的生产效率和产品质量,推动塑料制品产业的发展。
塑料挤出成型工艺与实例分析
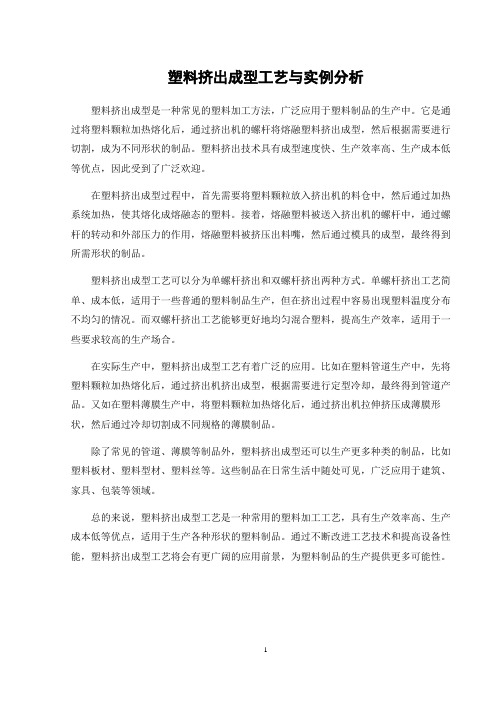
塑料挤出成型工艺与实例分析塑料挤出成型是一种常见的塑料加工方法,广泛应用于塑料制品的生产中。
它是通过将塑料颗粒加热熔化后,通过挤出机的螺杆将熔融塑料挤出成型,然后根据需要进行切割,成为不同形状的制品。
塑料挤出技术具有成型速度快、生产效率高、生产成本低等优点,因此受到了广泛欢迎。
在塑料挤出成型过程中,首先需要将塑料颗粒放入挤出机的料仓中,然后通过加热系统加热,使其熔化成熔融态的塑料。
接着,熔融塑料被送入挤出机的螺杆中,通过螺杆的转动和外部压力的作用,熔融塑料被挤压出料嘴,然后通过模具的成型,最终得到所需形状的制品。
塑料挤出成型工艺可以分为单螺杆挤出和双螺杆挤出两种方式。
单螺杆挤出工艺简单、成本低,适用于一些普通的塑料制品生产,但在挤出过程中容易出现塑料温度分布不均匀的情况。
而双螺杆挤出工艺能够更好地均匀混合塑料,提高生产效率,适用于一些要求较高的生产场合。
在实际生产中,塑料挤出成型工艺有着广泛的应用。
比如在塑料管道生产中,先将塑料颗粒加热熔化后,通过挤出机挤出成型,根据需要进行定型冷却,最终得到管道产品。
又如在塑料薄膜生产中,将塑料颗粒加热熔化后,通过挤出机拉伸挤压成薄膜形状,然后通过冷却切割成不同规格的薄膜制品。
除了常见的管道、薄膜等制品外,塑料挤出成型还可以生产更多种类的制品,比如塑料板材、塑料型材、塑料丝等。
这些制品在日常生活中随处可见,广泛应用于建筑、家具、包装等领域。
总的来说,塑料挤出成型工艺是一种常用的塑料加工工艺,具有生产效率高、生产成本低等优点,适用于生产各种形状的塑料制品。
通过不断改进工艺技术和提高设备性能,塑料挤出成型工艺将会有更广阔的应用前景,为塑料制品的生产提供更多可能性。
1。
塑料挤出工艺流程

塑料挤出工艺流程塑料挤出工艺是一种常见且广泛应用于塑料制品生产的工艺,通过将塑料加热至熔融状态,然后通过挤出机将熔融塑料挤出成型。
下面将对塑料挤出工艺的流程进行详细介绍。
首先,在挤出工艺的准备阶段,需要准备好所需的原料,包括塑料颗粒、添加剂(如增塑剂、着色剂等)以及辅助材料,如脱模剂。
其中,塑料颗粒的选择需要根据产品的要求来确定,不同的塑料有着不同的特性和用途。
在选择和配比原料时,需要进行试验和调整,以确保产品的质量和性能。
接下来,将准备好的原料放入挤出机的料斗中,并通过输送装置将原料送入挤出机的螺杆进料段。
在螺杆的作用下,原料开始融化,并随着螺杆的转动被推进到挤出机的螺杆运动段。
在螺杆运动段,原料受到高温和高压的作用,进一步熔化和均匀混合,形成一个均一的塑料熔体。
螺杆运动的速度和压力的控制对于塑料熔体的质量和性能至关重要,需要根据产品的要求进行调整。
当塑料熔体达到所需的熔融状态后,会进入到挤出机的模头。
模头是一个具有特定形状的金属模具,在挤出机的压力下,将塑料熔体挤出成型。
模头的形状和尺寸决定了最终产品的外观和尺寸。
在挤出过程中,除了通过模头挤出塑料熔体外,还需要对其进行冷却和固化。
冷却和固化的方式可以有多种,例如通过水或气体进行冷却。
冷却和固化的时间和方式需要根据塑料的种类和产品的要求进行调整。
最后,产品经过切割和整形处理,去除多余的部分,使其成为一个完整的塑料制品。
切割和整形的方式可以通过刀具、切割机或热切割来实现。
综上所述,塑料挤出工艺是一个通过将塑料加热至熔融状态,然后通过挤出机将塑料熔体挤出成型的工艺。
该工艺流程包括原料准备、塑料熔化、挤出成型、冷却固化和切割整形等步骤,每个步骤都需要合理的控制和调整,以确保最终产品的质量和性能。
塑料挤出工艺在塑料制品生产中具有广泛的应用,并在日常生活中扮演着重要的角色。
挤出成型工艺技术
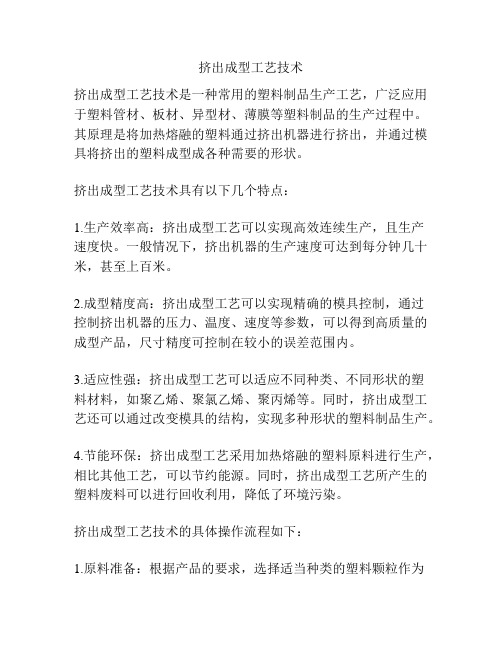
挤出成型工艺技术挤出成型工艺技术是一种常用的塑料制品生产工艺,广泛应用于塑料管材、板材、异型材、薄膜等塑料制品的生产过程中。
其原理是将加热熔融的塑料通过挤出机器进行挤出,并通过模具将挤出的塑料成型成各种需要的形状。
挤出成型工艺技术具有以下几个特点:1.生产效率高:挤出成型工艺可以实现高效连续生产,且生产速度快。
一般情况下,挤出机器的生产速度可达到每分钟几十米,甚至上百米。
2.成型精度高:挤出成型工艺可以实现精确的模具控制,通过控制挤出机器的压力、温度、速度等参数,可以得到高质量的成型产品,尺寸精度可控制在较小的误差范围内。
3.适应性强:挤出成型工艺可以适应不同种类、不同形状的塑料材料,如聚乙烯、聚氯乙烯、聚丙烯等。
同时,挤出成型工艺还可以通过改变模具的结构,实现多种形状的塑料制品生产。
4.节能环保:挤出成型工艺采用加热熔融的塑料原料进行生产,相比其他工艺,可以节约能源。
同时,挤出成型工艺所产生的塑料废料可以进行回收利用,降低了环境污染。
挤出成型工艺技术的具体操作流程如下:1.原料准备:根据产品的要求,选择适当种类的塑料颗粒作为原料。
根据挤出机器的要求,将塑料颗粒加入到机器的料斗中。
2.熔化塑料:通过挤出机器的加热系统和螺旋挤杆的旋转运动,将塑料颗粒加热熔化,形成熔融状态的塑料。
3.挤出成型:将熔融状态的塑料通过挤出机器的头部挤出口,经过模具的成型空腔,挤出成型。
模具的形状和结构决定了最终成型产品的形状和尺寸。
4.冷却固化:挤出成型后的塑料制品需要进行冷却固化,使其在形状稳定的同时,保持一定的强度和硬度。
通常可以通过水冷、风冷等方式进行冷却。
5.切割修整:冷却固化后的塑料制品还需要进行切割和修整。
可以采用自动切割机器或手动切割工具进行处理,将制品切割成所需的长度或形状。
6.质量检验:对切割修整后的产品进行质量检验,检查产品的尺寸精度、外观质量等。
如发现问题,需要进行修复或淘汰。
挤出成型工艺技术的应用范围非常广泛,几乎涵盖了塑料制品的各个领域。
塑料挤出成型
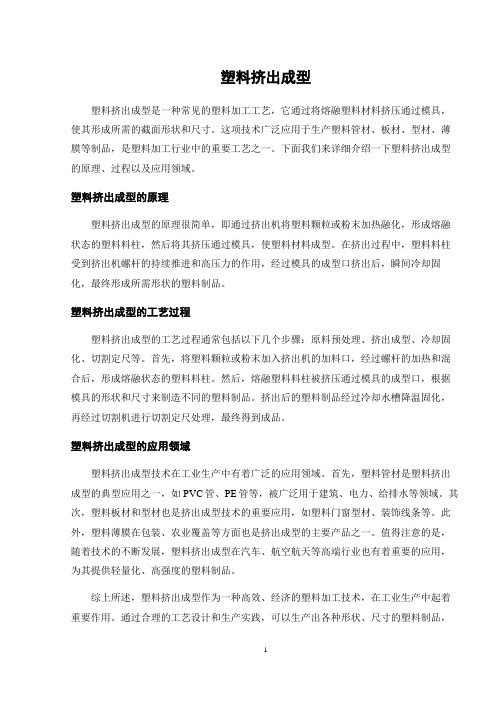
塑料挤出成型塑料挤出成型是一种常见的塑料加工工艺,它通过将熔融塑料材料挤压通过模具,使其形成所需的截面形状和尺寸。
这项技术广泛应用于生产塑料管材、板材、型材、薄膜等制品,是塑料加工行业中的重要工艺之一。
下面我们来详细介绍一下塑料挤出成型的原理、过程以及应用领域。
塑料挤出成型的原理塑料挤出成型的原理很简单,即通过挤出机将塑料颗粒或粉末加热融化,形成熔融状态的塑料料柱,然后将其挤压通过模具,使塑料材料成型。
在挤出过程中,塑料料柱受到挤出机螺杆的持续推进和高压力的作用,经过模具的成型口挤出后,瞬间冷却固化,最终形成所需形状的塑料制品。
塑料挤出成型的工艺过程塑料挤出成型的工艺过程通常包括以下几个步骤:原料预处理、挤出成型、冷却固化、切割定尺等。
首先,将塑料颗粒或粉末加入挤出机的加料口,经过螺杆的加热和混合后,形成熔融状态的塑料料柱。
然后,熔融塑料料柱被挤压通过模具的成型口,根据模具的形状和尺寸来制造不同的塑料制品。
挤出后的塑料制品经过冷却水槽降温固化,再经过切割机进行切割定尺处理,最终得到成品。
塑料挤出成型的应用领域塑料挤出成型技术在工业生产中有着广泛的应用领域。
首先,塑料管材是塑料挤出成型的典型应用之一,如PVC管、PE管等,被广泛用于建筑、电力、给排水等领域。
其次,塑料板材和型材也是挤出成型技术的重要应用,如塑料门窗型材、装饰线条等。
此外,塑料薄膜在包装、农业覆盖等方面也是挤出成型的主要产品之一。
值得注意的是,随着技术的不断发展,塑料挤出成型在汽车、航空航天等高端行业也有着重要的应用,为其提供轻量化、高强度的塑料制品。
综上所述,塑料挤出成型作为一种高效、经济的塑料加工技术,在工业生产中起着重要作用。
通过合理的工艺设计和生产实践,可以生产出各种形状、尺寸的塑料制品,满足不同行业的需求。
相信随着技术的不断进步,塑料挤出成型技术将会在未来发展中发挥更加重要的作用,为塑料制品的生产提供更好的解决方案。
塑料的挤出成型工艺
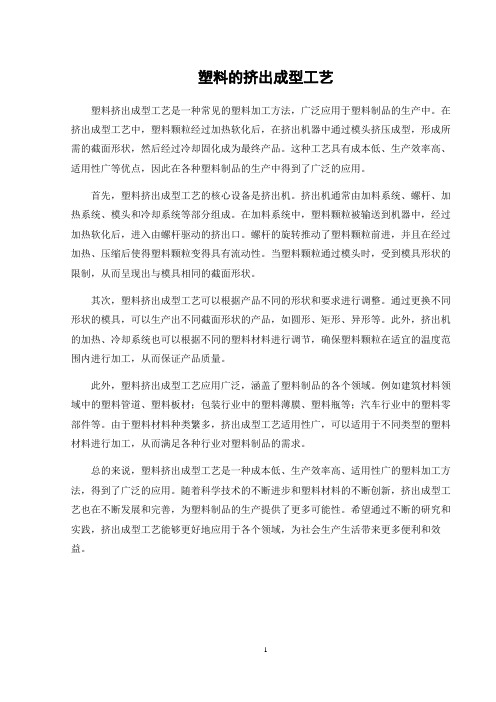
塑料的挤出成型工艺塑料挤出成型工艺是一种常见的塑料加工方法,广泛应用于塑料制品的生产中。
在挤出成型工艺中,塑料颗粒经过加热软化后,在挤出机器中通过模头挤压成型,形成所需的截面形状,然后经过冷却固化成为最终产品。
这种工艺具有成本低、生产效率高、适用性广等优点,因此在各种塑料制品的生产中得到了广泛的应用。
首先,塑料挤出成型工艺的核心设备是挤出机。
挤出机通常由加料系统、螺杆、加热系统、模头和冷却系统等部分组成。
在加料系统中,塑料颗粒被输送到机器中,经过加热软化后,进入由螺杆驱动的挤出口。
螺杆的旋转推动了塑料颗粒前进,并且在经过加热、压缩后使得塑料颗粒变得具有流动性。
当塑料颗粒通过模头时,受到模具形状的限制,从而呈现出与模具相同的截面形状。
其次,塑料挤出成型工艺可以根据产品不同的形状和要求进行调整。
通过更换不同形状的模具,可以生产出不同截面形状的产品,如圆形、矩形、异形等。
此外,挤出机的加热、冷却系统也可以根据不同的塑料材料进行调节,确保塑料颗粒在适宜的温度范围内进行加工,从而保证产品质量。
此外,塑料挤出成型工艺应用广泛,涵盖了塑料制品的各个领域。
例如建筑材料领域中的塑料管道、塑料板材;包装行业中的塑料薄膜、塑料瓶等;汽车行业中的塑料零部件等。
由于塑料材料种类繁多,挤出成型工艺适用性广,可以适用于不同类型的塑料材料进行加工,从而满足各种行业对塑料制品的需求。
总的来说,塑料挤出成型工艺是一种成本低、生产效率高、适用性广的塑料加工方法,得到了广泛的应用。
随着科学技术的不断进步和塑料材料的不断创新,挤出成型工艺也在不断发展和完善,为塑料制品的生产提供了更多可能性。
希望通过不断的研究和实践,挤出成型工艺能够更好地应用于各个领域,为社会生产生活带来更多便利和效益。
1。
塑料制品的挤出和注塑加工技术
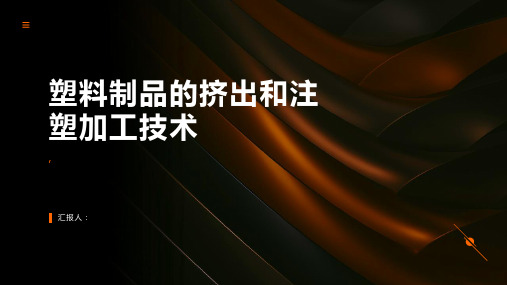
4
挤出与注塑加工技术的 应用范围和比较
挤出加工技术的应用范围
塑料管材、板材、 薄膜、型材等制 品的生产
塑料包装材料、 容器、日用品等 制品的生产
塑料建筑材料、 装饰材料、家具 等制品的生产
塑料电子电器、 汽车、医疗器械 等制品的生产
注塑加工技术的应用范围
汽车行业:制造汽车 零部件、内饰件等
电子行业:制造电子 产品外壳、按键等
塑料制品的挤出和注 塑加工技术
,
汇报人:
目录 /目录
01
点击此处添加 目录标题
02
挤出加工技术
03
注塑加工技术
04
挤出与注塑加 工技术的应用 范围和比较
05
挤出和注塑加 工技术的发展 趋势和挑战
1 添加章节标题
2 挤出加工技术
挤出成型原理
挤出机:将塑料原料熔化、塑化、挤出 模具:成型塑料制品的形状和尺寸 冷却系统:冷却挤出的塑料制品,使其固化 牵引装置:控制塑料制品的挤出速度和质量
家居行业:制造家具、 厨具等
医疗行业:制造医疗 器械、耗材等
其他行业:制造玩具、 文具等
挤出与注塑加工技术的比较
挤出成型:适 注塑成型:适 用于生产连续、 用于生产形状 长条状的塑料 复杂、尺寸精 制品,如管材、 确的塑料制品, 板材、薄膜等。 如汽车零部件、
家电外壳等。
挤出成型的优 点:生产效率 高,成本低, 适用于大批量
挤出和注塑加工技术的挑战:环保、节能、降耗
技术创新与进步的具体表现:新型材料的研发和应用、新型加工工艺的研发和应用、 新型设备的研发和应用
技术创新与进步的意义:提高生产效率、降低生产成本、提高产品质量、减少环境污染
环保与可持续发展要求
塑料挤出成型加工方法有哪些

塑料挤出成型加工方法有哪些塑料挤出成型是一种常见的塑料加工方法,通过在高温下使塑料熔化后,在模具中挤出所需形状的工艺过程。
塑料挤出成型具有生产效率高、产品质量稳定等优点,被广泛应用于塑料制品的生产制造中。
在塑料挤出成型加工过程中,可以采用多种不同的方法和技术,以下将介绍几种常见的塑料挤出成型加工方法:单螺杆挤出法单螺杆挤出机是一种常用的挤出设备,通过单螺杆旋转带动塑料料料向前进行挤出成型。
在单螺杆挤出过程中,常用于生产直径较小、长度较长的塑料制品,如管材、棒材等。
通过调节单螺杆的转速和温度,可以控制挤出速度和成型温度,以满足不同塑料制品的要求。
双螺杆挤出法双螺杆挤出机采用两个螺杆同步旋转的方式,能够更均匀地将塑料熔体挤出,实现对挤出产品的更精确控制。
双螺杆挤出法常用于生产较复杂、精密度要求较高的塑料制品,如异型材、薄膜等。
双螺杆挤出机具有挤出均匀、生产效率高等优点,适用于需求量大、产品质量要求高的生产场景。
水冷式挤出法水冷式挤出是一种在挤出机挤出后采用水冷形式进行冷却成型的加工方法。
水冷式挤出法可以快速降低塑料制品的温度,避免因热度过高而导致变形或质量不稳定的问题。
水冷式挤出法常用于生产对产品温度要求严格、表面光滑度高的塑料制品,如透明板材、塑料薄膜等。
吹塑挤出法吹塑挤出是一种将挤出的熔融塑料经过模具吹气成型的加工方法。
吹塑挤出法通常用于生产中空或中空轮廓的塑料制品,如瓶子、容器等。
通过控制挤出速度和模具设计,可以实现不同形状和大小的塑料制品生产,具有生产效率高、成本较低等优点。
挤出压花法挤出压花法是一种通过在挤出机出口处设置压花轮对挤出的塑料进行压花成型的加工方法。
挤出压花法常用于生产表面花纹、图案丰富的塑料制品,如地板、墙板等。
通过更换不同的压花轮,可以实现多样化的产品设计。
挤出压花法具有生产效率高、生产速度快的优点,适用于大批量生产的工艺要求。
以上介绍了几种常见的塑料挤出成型加工方法,每种方法都有其独特的特点和适用范围。
塑料加工中的挤出工艺和控制

塑料加工中的挤出工艺和控制在现代工业生产中,塑料是一种非常重要的材料,广泛应用于各个领域。
而塑料制品的生产过程中,挤出工艺是一种非常重要的加工方式。
本文将对塑料挤出工艺进行详细讲解,并对控制方法进行探讨。
一、挤出工艺挤出工艺是一种通过挤出机将塑料熔化后挤出成型的方法,广泛应用于各种塑料制品的生产。
挤出机一般由进料系统、熔化系统、挤出系统、定型系统和切断系统等组成。
进料系统是将原料塑料送入挤出机的部分,其主要组成部分有料斗、送料器、螺杆等。
在进料系统中,挤出机需要根据不同原料塑料的种类和特性确定不同的送料方式和送料速度,以保证塑料能够均匀地进入挤出机。
熔化系统则是将进入挤出机的塑料经过加热熔化,由螺杆推动熔融塑料向前运动。
在熔化系统中,一般根据不同的塑料种类和需要调节塑料的熔化温度和流动性来进行不同的调节,以保证挤出后制品的质量。
挤出系统是将熔融的塑料挤出成型的部分,其主要由螺杆、机头等组成。
在挤出系统中,通过螺杆的旋转和机头的成型模具,将熔融的塑料挤压出去,并根据需要进行定型和冷却处理。
定型系统是将挤出的塑料制品进行固化和定形的部分,其一般由冷却水池、冷却辊、收卷机等组成。
在定型系统中,根据不同的塑料制品和需要定型的形状、尺寸等进行不同的调节,以保证制品的准确和美观。
切断系统则是将已经固化的塑料制品进行切断、检验的部分,其主要包括切断机、检验机等。
在切断系统中,需要注意切断的位置和方法,以避免制品出现裂痕等质量问题。
二、挤出工艺控制挤出工艺的控制是保障塑料制品质量的关键。
在进行塑料挤出加工时,需要注意以下几点:1、温度控制塑料的加工温度直接影响制品的质量。
如果温度过低,则会造成塑料流动不畅、成型不完整等问题;而温度过高则会造成制品变形、气泡等问题。
因此在进行挤出加工时,需要根据不同的塑料种类和制品要求来确定不同的加工温度。
2、压力控制挤出加工时,熔融塑料需要受到螺杆的压力推动,以确保塑料能够均匀流动和挤出成型。
- 1、下载文档前请自行甄别文档内容的完整性,平台不提供额外的编辑、内容补充、找答案等附加服务。
- 2、"仅部分预览"的文档,不可在线预览部分如存在完整性等问题,可反馈申请退款(可完整预览的文档不适用该条件!)。
- 3、如文档侵犯您的权益,请联系客服反馈,我们会尽快为您处理(人工客服工作时间:9:00-18:30)。
第五章挤出成型5.0 本章介绍1、主要内容:概论、单螺杆挤出机的基本结构、挤出理论和几种制品的挤出工艺。
2、重点:挤出理论、粒料的制备3、难点:挤出理论。
4、教学要求:(1)掌握挤出理论,单螺杆挤出机的结构。
(2)掌握几种制品的挤出工艺。
挤出成型又称挤出模塑,是塑料重要的成型方法之一,绝大多数热塑性塑料均可用此法成型。
这种成型方法的特点是具有很高的生产率且能生产连续的型材,如管、棒、板、薄膜、丝、电线、电缆以及各种型材,还可用来混合、塑化、造粒和着色等。
挤出成型过程分两个阶段进行。
第一阶段将物料加热塑化,使呈粘流状态并在加压下通过一定形状的口模而成为截面与口模形状相仿的连续体;第二阶段将这种连续体用适当的方法冷却、定型为所需产品。
物料的塑化和加压过程一般都是在挤出机内进行。
挤出机按其加压方式可分为螺杆式和柱塞式两种。
前者的特点是,借助螺杆旋转时螺纹所产生的推动力将物料推向口模。
这种挤出机中通过螺杆强烈的剪切作用,促进物料的塑化和均匀分散,同时使挤出过程连续进行,因此可以提高挤出制品的质量和产量,它适用于绝大多数热塑性塑料的挤出。
柱塞式挤出机中,通过粒筒加热塑化的物料,由柱塞推向口模。
这种挤出机能够产生较大的压力,一般来说,其操作是间歇进行,物料的塑化程度和均匀性不如螺杆式挤出机,因此应用范围受限制。
它适用于聚四氟乙烯,超高相对分子质量聚乙烯等塑料的挤出。
本章以螺杆式挤出机的挤出工艺及有关辅助设备为重点加以介绍。
5.1 单螺杆挤出机的基本结构和辅机一、单螺杆挤出机基本结构单螺杆挤出机基本结构,主要由传动系统、加料系统、挤压系统、加热系统、冷却系统以及机头和口模等部分组成1、传动系统传动系统是挤出机的重要组成部分之一。
它的作用是在给定的工艺条件(如机头压力、螺杆转数、挤出量、温度等)下使螺杆具有必要的扭矩和转数均匀地回转而完成挤出过程。
传动系统由电动机、减速装置、变速器及轴承系统组成。
常用的挤出机电动机有交流整流子电动机和直流电动机。
减速器一般为定轴轮系减速器、齿轮减速器和涡轮减速器。
国产挤出机有采用摆线针轮减速器的。
三相整流子电动机和普通齿轮减速器和涡轮减速箱组成的传动系统,运转可靠、性能稳定,控制、维修方便。
电动机得到合理的利用,启动性能也很好,其调速范围有1:3, 1:6;1:160但由于调速范围大于1:3后电动机体积显著增大,成本也相应提高,故国内大都采用1:3的整流子电动机。
直流电动机和一般齿轮减速箱组成的传动系统的调速范围较宽。
改变电枢电压时得到的是恒扭矩调速;改变激磁电压得到的是恒功率调速,此时随着转数的增加功率保持不变,而扭矩相应减少。
为充分利用直流电动机这一特性,可用其恒扭矩调速段来加上硬Pvc等硬料,用恒功率调速段来加工较软的物料,这样可以合理利用电动机。
但当直流电动机的转速低于100 - 200r /min时,其工作性能是不稳定的,而且在低速时电动机冷却能力也相应下降。
为此,可以另加鼓风机进行强力冷却。
用直流电动机和摆线针轮减速器或行星齿轮减速器组成的传动系统具有紧凑、轻便、效率高、声响小的特点。
2、加料系统加料系统是由加料斗和上料装置所组成的。
加料斗的形式有圆锥形、圆柱形-圆锥形、矩形等。
料斗侧面开有视镜孔以观察料位,料斗的底部有开合门以停止和调节加料量。
料斗的上方可以加盖以防止灰尘、湿气及其他杂物进入。
料斗的材料一般采用铝板和不锈钢板。
料斗的容量至少应容纳1-1. 5h的挤出量。
加料口的形状有矩形与圆形两种,一般多采用矩形。
上料有人工上料和自动上料两种。
自动上料装置主要有鼓风上料、弹簧上料、真空吸料等。
(1)鼓风上料器鼓风上料器是利用风力将料吹人输料管,再经过旋风分离器进人料斗。
这种上料方法适于输送粒料而不适于粉料。
(2)弹簧上料器弹簧上料器由电动机、弹簧夹头、进料口及软管组成。
电动机带动弹簧高速旋转,这时在弹簧的任何一点都产生轴向力和离心力,在这些力的作用下,物料被提升,到达进料口时,由于离心力的作用而进入料斗。
它适于输送粉料、粒料以及块状料。
这种送料器结构简单、轻巧、效率高,可靠,故应用范围广。
但其输送距离小,在送料时可能出现"打管"现象而产生较大的噪音,软管易磨损,弹簧选用不当易损坏等。
(3)真空吸料装置真空吸料装置有利于排除物料中的水分和气体。
由于它是靠物料自重进料,不能避免进料不均匀现象,除非设置强制加料螺旋。
3、挤压系统(1)螺杆挤出机的挤压系统由螺杆和粒筒所组成。
螺杆是关键性部件,通过它的转动,料筒内的物料才能发生移动,得到增压和部分的摩擦热量,混匀后定量定压地输送到机头而成型。
根据塑料在挤出机中物料的三种状态变化过程及螺杆各部位的工作要求,通常将挤出机的螺杆分为加料段L1 (又称固体输送段)、熔融段L2(又称压缩段)和均化段L3(又称计量段)三段。
这种螺杆称为常规全螺纹螺杆或三段式螺杆(见图5-2)。
虽然目前已出现许多新型螺杆,其中有四段、五段等,根据挤出原理给予各段以新的职能。
但是三段式螺杆则是最基本的。
(2)料筒料筒作为挤压系统的组成部分,和螺杆共同完成对塑料的固体输送、熔融和定量定压输送作用。
料筒的结构形式关系到热量传递的稳定性和均匀性,并影响固体输送率。
料筒结构分为整体式和组合式(又称分段式)。
整体式料筒结构,易保证较高的制造和装配精度,简化装配工作,便于加热冷却系统的设置和拆装,而且热量沿轴向分布比较均匀,但是这种料筒的加工设备要求较高,当内表面磨损后难以复修。
组合式料筒是由几段料筒组合而成,便于改变料筒长度,适应不同长径的螺杆。
排气式挤出机多用这种料筒,便于设置排气段。
组合式料筒的加工要求很高,料筒各段多采用法兰螺栓联接,难以保持加热均匀性,增加热损失,对加热冷却系统的设置和维修不便。
由于塑料在塑化和挤压过程中温度可达250度,压力达到55MPa,料筒的材质必须具有较高的强度、坚韧和耐腐蚀。
料筒通常是由钢制外壳和合金钢内衬共同组成。
衬套磨损后可以拆除和更换。
衬套和料筒要配合好,以保证整个料筒壁上热传导不受影响,料筒和衬套间不能相对运动,又要保证能方便地拆出。
根据挤出过程的理论和实践证明,增加料筒内表面的摩擦系数可提高塑料的输送能力,因此,挤出机料筒的加料段内开设有纵向沟槽和靠近加料口的一段料筒内壁做成锥形。
轴向沟槽的数量与料筒直径的大小有关。
槽数太多,会导致物料回流使输送量下减。
槽的形状有长方形的、三角形的或其他形状的。
这种开槽料筒与未开槽的料筒相比,具有输送率高、挤出量对机头压力变化的敏感性小等特点。
但由于需要采用强力冷却而消耗很大能量,在料筒加料段末端可能产生极高的压力,有损坏带有沟槽的薄壁料筒的危险;螺杆磨损较大;挤出性能对原料的依赖性较大。
因此在小型挤出机上采用此结构受到限制。
料筒加料口的形状及开设位置对加料性能有很大影响。
加料口应保持物料自由、高效地加人料筒不易产生架桥,便于设置冷却系统和利于清理。
4、加热冷却系统为使塑料在加工工艺所要求的温度内挤出,一般挤出机上都设有加热冷却系统装置及测量、控制温度的仪器仪表。
(1)挤出机的加热目前挤出机的加热方法有载热体加热、电阻加热和电感应加热等。
由于挤出机的料筒较长,挤出工艺对料筒在轴线方向的温度有一定要求,根据螺杆直径和长径比的大小,将料筒分为若干区段进行加热。
机头可视其类型和大小设定加热段。
(2)挤出机的冷却冷却装置是保证塑料在工艺要求的范围内稳定挤出的一个重要部分,它与加热系统又是密切联系而不可分割的。
随着挤出机向高速高效发展,螺杆转速不断提高,物料在料筒内所受的剪切和摩擦会加剧,因此对料筒和螺杆必须进行冷却。
在料筒的加料段和料斗座部位设冷却装置是为加强这段固体物料的输送。
l)料筒的冷却料筒冷却方法有风冷和水冷两种。
风冷的特点是冷却比较柔和、均匀、干净,但风机占有空间体积大,其冷却效果易受外界气温的影响。
一般用十中小型挤出机较为合适。
与风冷相比,水冷的冷却速度快、体积小、成本低。
但易造成急冷,水一般都未经过软化处理,水管易出现结垢和锈蚀现象而降低冷却效果或被堵塞、损坏等。
2)螺杆冷却螺杆冷却的目的是利于物料的输送,同时防止塑料因过热而分解。
通入螺杆中的冷却介质为水或空气。
在最新型挤出机上,螺杆的冷却长度是可以调整的。
根据各种塑料的不同加工要求,依靠调整伸进螺杆的冷却水管的插人长度来提高机器的适应性。
3)料斗座的冷却挤出机工作时,进料口温度过高,易形成"架桥",进料不畅,严重时不能进料,因此,加料斗座应设置冷却装置并防止挤压部分的热量传到止推轴承和减速箱,保证挤出机的正常工作。
冷却介质多采用水。
5、分流板、过滤网在料筒和口模连接处设置分流板(又称多孔板)和过滤网,其作用是使物料流由旋转运动变为直线运动,阻止杂质和未塑化物料通过并增加料流背压,使制品更加密实。
其中分流板还起支撑过滤网的作用,但在挤出硬聚氯乙烯等粘度大而稳定性差时,一般不用过滤网。
二、辅助设备挤出机辅助设备大致可分为以下三类:1、挤压前物料处理的设备(如预热、干燥等)一般用于吸湿性塑料。
干燥设备有烘箱或沸腾干燥器等。
有的干燥设备直接设置在加料斗上。
2、挤出物的处理设备如用作冷却、牵引、卷取、切断和检验设备。
3、控制生产条件的设备指各种控制仪表,如温度控制器、电动机启动装置、电流表、螺杆转数表和测定机头压力的装置等。
以上三类设备不仅随制品的种类。
对制品质量的要求及自动化程度不同而异,而且每一类设备又有许多的形式。
5.3 塑料制品的挤出工艺一、管材的挤出管材是挤出成型的主要产品之一。
挤出管材的塑料有聚氧乙烯、聚乙烯、聚丙烯、ABS,聚酞胺及聚四氟乙烯等。
目前以聚氯乙烯和聚乙烯为主二挤出管材的生产工艺流程由挤出机、机头、定径套、冷却槽、牵引和切割装置所组成。
1、硬质聚氯乙烯的管材挤出硬质PVC的生产可采用两种工艺。
(1)采用双螺杆挤出机,将PVC粉料(包括稳定剂、润滑剂、填充剂等)经高速搅拌机混合后直接挤出管材。
这种方法生产率高,管材质量好,在有些国家生产硬质PVC管材均采用此法。
(2)采用挤出机生产时,由于其混合、塑化性能较差,先将PVC粉料制成粒料,然后挤出管材。
(1)原料的选择原料直接关系到管材的质量,选择原料时要考虑其来源和成本,管材的使用场合和环境条件。
因为使用条件不同对管材有不同的要求,所用成型设备及成型工艺条件也不尽相同。
用于输送腐蚀性液体和气体的硬质PVC管要求有一定的强度、能承受内外压力,耐热耐腐蚀。
宜选用国产PVC树脂型号为Xj一4或Xj-5,前者的平均聚合度为850-980,后者为720-850。
耐压管材则应选用平均聚合度为1160的树脂。
大口径管材,其壁较厚,为了保持良窄的性能又便于加工,可选用高、低聚合度的树脂按一定比例(前者的比例较大)共混后进行挤出成型。