采用半干法脱硫工艺锅炉的烟囱选型
锅炉烟气脱硫脱硝工艺比选

锅炉烟气脱硫脱硝工艺比选一、烟气脱硫:根据吸收剂及脱硫产物在脱硫过程中的干湿状态,火力发电行业一般将脱硫技术分为湿法、干法和半干(半湿)法。
(1)湿法烟气脱硫技术是用含有吸收剂的浆液在湿态下脱硫和处理脱硫产物,该方法具有脱硫反应速度快、脱硫效率高、吸收剂利用率高、技术成熟可靠等优点,但也存在初投资大、运行维护费用高、需要处理二次污染等问题。
应用最多的湿法烟气脱硫技术为石灰石湿法,如果将脱硫产物处理为石膏并加以回收利用,则为石灰石-石膏湿法,否则为抛弃法。
其他湿法烟气脱硫技术还有氨洗涤脱硫和海水脱硫等。
(2)干法烟气脱硫工艺均在干态下完成,无污水排放,烟气无明显温降,设备腐蚀较轻,但存在脱硫效率低、反应速度慢、石灰石利用率较低等问题,有些方法在设备大型化的进程中困难很大,技术尚不成熟(主要有炉内喷钙等技术)。
半干法通常具有在湿态下进行脱硫反应,在干态下处理脱硫产物的特点,可以兼备干法和湿法的优点。
主要包括喷雾干燥法、炉内喷钙尾部增湿活化法、烟气循环流化床脱硫法、电子束辐照烟气脱硫脱氮法等。
下表为几种主要脱硫工艺的比较。
目前,在众多的脱硫工艺中,石灰石—石膏湿法烟气脱硫工艺(简称FGD)应用最广。
据统计,80%的脱硫装置采用石灰石(石灰)—石膏湿法,10%采用喷雾干燥法(半干法),10%采用其它方法。
湿法脱硫工艺是目前世界上应用最多、最为成熟的技术,吸收剂价廉易得、副产物便于利用、煤种适应范围宽,并有较大幅度降低工程造价的可能性。
安徽电力设计院建议采用炉内与炉外湿法脱硫相结合的方法进行脱硫,脱硫效率可达98%。
二、脱硝:烟气脱硝工艺可以分为湿法和干法两大类。
(1)湿法,是指反应剂为液态的工艺技术。
通过氧化剂O2、ClO2、KMnO2把NO x氧化成NO2,然后用水或碱性溶液吸收脱硝。
包括臭氧氧化吸收法和ClO2气相氧化吸收法。
(2)干法,是指反应剂为气态的工艺技术。
包括氨催化还原法和非催化还原法。
无论是干法还是湿法,依据脱硝反应的化学机理,又可以分为还原法、分解法、吸附法、等离子体活化法和生化法等。
循环半干法在锅炉烟气二次脱硫示范项目中的应用

收稿 日期 :0 1 82 2 1- —4 0
・
运 行 与管 理 ・
循环 半 干法 在锅 炉烟 气二 次脱 硫示 范项 目中的应用
表 2 脱硫 系统主要设计参数
5 5
结果 如 表 1 示 。 所
表 1 煤质化验数据
名 称
烟气量 ( 标态 , 湿基 , 实际 O ) : 烟气量 ( 标态 , 干基 , 实际 O ) :
气流 冲刷 , 烟气 、 吸收剂 和循 环灰充 分混 合后进 人反 应器 的直筒 段 。在反应 器 内文丘 里管 的 出口扩 管段
设有 喷水装 置 , 喷人 雾 化水 以降 低 反应 器 内的 烟 温
至高 于烟气 水露 点 1 【左 右 。在 降温 和 增 湿 条件 5o =
下, 烟气 中的 S : C ( H) 0 与 a O 反应 生成 亚硫 酸钙 和
经 济 的是杭 州 、 阳产 的氢氧 化钙 粉 , 品质化 验结 富 其 果 ( 度、 度、 纯 粒 活性 等 ) 如下 :
氢 氧 化钙 纯度 : 8 % > I 5
F D装 置可用率 G
等工 作 , 安装 反应 塔 、 在 粉仓 、 水泵 、 仓泵 和风机 等新
设备 后进 行新 设备 的调 试及 整体试 运 。 在 此次 脱 硫 改造 过 程 中 , 针对 考 察 过程 中发 现
摘
关注。
运 行 管 理 和 技 术 改 要: 介绍了循 环半 干法 在绍兴市 锅炉烟气 二次脱硫 改造示 范项 目中的应用情 况。经 造 工 作 。
过半年 的运行 , 此次二次脱硫改造虽然成功 , 增加 了企业 负担 ; 但 另外脱硫灰 如何妥善处理值得 关键 词 : 循环半干法 ; 应用 ; 社会效 益; 脱硫
2X75t锅炉半干法脱硫工艺图

半干法脱硫技术方案2×75t/h循环流化床锅炉烟气脱硫除尘技术方案第一章技术规范1.1总则本技术方案适用于2×75t/h循环流化床锅炉烟气脱硫除尘工程系统的功能设计。
1.2.工程概况项目名称: 2×75t/h循环流化床锅炉烟气脱硫除尘工程建设地点:现有2台75t/h锅炉,根据该公司的环保目标,SO2达标排放浓度减排90%以上,粉尘达标排放浓度为30mg/Nm3。
所以现对二台锅炉做出以下半干法脱硫配有单元布袋除尘器。
本技术方案所涉及范围为1台75吨锅炉炉后全套除尘、脱硫系统等。
1.3设计和运行条件1.3.1锅炉1.3.2 烟气参数表根据贵公司的所提供的参数1.3.3吸收剂本技术方案的脱硫剂采用消石灰。
根据《建筑石灰试验方法化学分析方法》(JC/T478.1一92)和《建筑石灰试验方法物理试验方法》(JC/T478.1一92),检验结果如下:氢氧化钙(Ca(0H)2)>含量:90 % 粒度:100% < 1mm 90% < 0.8mm消化速度:T60<4min1.3.4设计要求脱硫率>90% ,SO2排放浓度≤100mg/Nm³,除尘器排放浓度≤30mg/Nm³1.4规范与标准脱硫除尘系统及其配套辅机设计、制造、检验原则上采用中国现行规范和标准,但凡按引进技术设计制造的设备,均按引进技术相应的标准,若本公司使用的规范及标准与本技术规范所用标准发生矛盾时,按较高标准执行。
本技术规范书要求符合(但不限于)下列规范及标准:设计标准1) 技术方案的设计符合《火力发电厂设计技术规程》(DL5000-2000)规定。
2) DL/T5054-1996 《火力发电厂汽水管道设计技术规定》3) DL/T5072-1997 《火力发电厂保温油漆技术规范》4) DL468-92 《电站锅炉风机选型和使用导则》第二章技术方案2.1对脱硫除尘装置总的技术要求1) 锅炉脱硫系统在正常工况下运行时,保证系统的脱硫效率大于90%,除尘效率高于99.8%,脱硫后除尘器出口烟温不低于97℃。
电厂锅炉脱硫脱硝及烟气除尘技术

电厂锅炉脱硫脱硝及烟气除尘技术摘要:随着国内工业的快速发展,工业生产的污染问题越来越严重。
在火电企业的发展中,大量的电力是以破坏周围环境为代价的。
因此,电力企业需要严格控制发电过程中产生的各种污染物的排放,以保持火电企业的可持续发展,增强其市场竞争力。
关键词:电厂锅炉;脱硫脱硝;烟气除尘技术引言火电厂燃煤过程中产生的氮氧化物和硫氧化物对环境构成了极大的威胁,这些有害物质容易形成酸雨等灾害。
因此,有必要对火电厂的燃烧过程进行有效的改造。
在生产过程中,锅炉的脱硫脱硝处理主要依靠反应塔内的对流交换和物理化学吸附,但不同的生产结构在处理方式的选择上会有一定的差异。
因此,需要相关技术人员根据实际需要进行优化调整,使锅炉整体吸附率达到合格排放的标准。
1电厂锅炉脱硫脱硝技术分析就锅炉脱硫脱硝技术的实际应用而言,目前很多企业相关技术试验方案落实不到位,达不到脱硫脱硝的基本要求。
有些技术应用甚至处于迷茫甚至混乱的阶段。
其中一些企业还借鉴国外先进的脱硫脱硝经验和技术,与中国传统技术相结合,希望达到技术创新的目的。
1.1湿法脱硫脱硝技术第一种是利用吸收剂吸收火力发电过程中的气体污染物,从而达到脱硫脱硝的效果。
由硫和氮与氧反应形成的氧化物通常能够与碱性物质发生化学反应。
因此,为了增加脱硫脱硝的效果,往往选择碱性物质作为吸收剂;第二种采用的是传统的石灰石—石膏湿法技术,由于其应用时间长,应用效果也比较理想,基本能够达到百分之九十以上的脱除率。
与此同时,石灰石—石膏湿法技术应用中得到产物还能进行回收并进行二次利用,从而有效避免由于脱硫脱硝后所产生的物质对于环境产生的二次污染以及产物难以处理的难题。
1.2炉后半干法脱硫技术炉后半干法脱硫最常用的工艺是旋转喷雾半干法工艺,旋转喷雾反应系统由喷雾反应塔和石灰浆制备系统组成。
石灰制备系统将生石灰(CaO)制备成一定浓浆液,通过旋转雾化器喷入半干式反应塔内形成微小液滴。
与石灰度的Ca(OH)2浆液滴充分接触和反应,去除SO2气体。
烟气脱硫后烟囱结构的选型设计

双管集束钢筋混 凝土 烟 囱是 将 承重结 构 ( 钢筋 混凝 土 外简 ) ( G Sfegs eurao yt 。根据 加装 脱硫 系统 后 烟气 的 和 排 烟 管 完 全 分 开 , 外 简 壁 免 受 烟 气 的 直 接 影 响 , 一 台 炉 设 F D u a sli tnss m) l d fz i e 使 且 流速 、 度 、 度的变化 和工艺所 提燃煤 成分等 资料 , 过 对采用 温 湿 通 个排 烟管 , 排烟管简 体可按工艺设 计 的要求 尽可能 做成等 直径
经济上合理 的方案 国 产 凝 汽 式 燃 煤 发 电 机 组 。燃 料 采 用 阳 泉 矿 区 生 产 的 优 质 无 烟 中择优 选定技术 上可行 、
1 煤, 原推荐 两台炉合用 一座双 管 集束 烟 囱 , 高 度为 20m, 口 其 4 出 2. 双管 集束 式钢 筋混 凝 土烟 囱
一
双管集束式钢筋 混凝土烟 囱和 单 简式 2 /0 m钢 筋混 凝 土烟 囱 0 4 1 或 变 直 径 小 坡 度 段 , 管 内 烟 气 在 运 行 过 程 中 始 终 处 于 负 压 运 行 使 这 两种结构型式 的技 术经济分析 比较 , 出 了两 炉合用 一座 防腐 工况 , 提 对于脱 硫后烟 气温度 低 、 烟气抬 升高度低 的特性 , 以达到 可 改进型单简式烟 囱结 构的可行性 。 降低腐蚀 等级和减 弱腐 蚀 强 度的 目的。对 承重 的钢 筋混 凝土 外 该电厂烟气 的排 放方 式 与传 统 的不 同之 处在 于加 装 了湿 法 简而言 , 混凝土 简体基 本上 处 于常 温 条件 下 ] 作 , 构 的温度 应 : 结 烟 气 脱 硫 系统 , 先 介 绍 该 系统 的 工 艺 流 程 。湿 法 烟 气 脱 硫 系 统 力 明 显 减 小 , 而 避 免 筒 体 由 于 温 差 过 大 而 产 生 裂 缝 和 腐 蚀 , 首 从 有
火力发电厂烟气循环流化床半干法脱硫系统设计规程

火力发电厂烟气循环流化床半干法脱硫系统设计规程一、前言火力发电厂作为能源的重要供应者,在发展过程中也面临着环保要求的不断提高。
烟气脱硫是保护大气环境、减少硫氧化物对人体健康的影响的重要手段。
烟气循环流化床半干法脱硫技术因其具有高脱硫效率、低能耗、操作稳定等优点,逐渐受到火力发电厂的青睐。
二、烟气循环流化床半干法脱硫系统工艺概述烟气循环流化床半干法脱硫系统是采用石灰石浆液作为脱硫剂,通过在反应塔内与烟气进行接触反应,将烟气中的二氧化硫进行吸收,形成石膏。
脱硫反应后的烟气通过旋风除尘器,净化后排放到大气中。
而石膏通过脱硫废水处理系统进行处理,使其达到国家排放标准。
系统操作中,石灰石浆液通过气力输送管道输送到反应器塔中,通过旋风分离器将石膏和石灰石分离,石膏送到石膏浆液处理系统,石灰石返回到循环槽进行循环利用。
三、烟气循环流化床半干法脱硫系统主要设备及其特点1.反应器塔反应器塔是烟气循环流化床半干法脱硫系统的核心设备,主要由进气口、出口、填料层、雾化喷淋层等组成。
其主要特点包括:填料层的选择要注意填料的比表面积,容积比和对流湿度等参数;雾化喷淋层的设计要根据烟气流速、反应器的容积和石灰石浆液的流量进行合理设计。
2.旋风除尘器旋风除尘器是用于对脱硫反应后烟气中的粉尘进行除尘,其主要特点包括:结构紧凑、除尘效率高、易于维护、运行稳定等。
3.气力输送系统气力输送系统是用于输送石灰石浆液到反应器塔中,其主要特点包括:输送过程中石灰石浆液无泄漏、设备运行稳定、输送距离远等。
4.脱硫废水处理系统脱硫废水处理系统是用于对反应后产生的废水进行处理,使其达到国家排放标准,其主要特点包括:处理效率高、占地面积小、废水排放达标、运行成本低等。
四、设计规程1.设计依据根据国家《烟气污染物排放标准》等相关标准,结合火力发电厂的实际情况,确定系统的设计参数和工艺流程。
2.脱硫效率系统设计应保证脱硫效率达到国家标准要求,并对脱硫效率进行动态监测,确保系统运行稳定、可靠。
循环流化床半干法脱硫技术的应用

循环流化床半干法脱硫技术的应用摘要:本文结合承钢180m2烧结机烟气脱硫工程的应用实例,介绍了循环流化床半干法脱硫系统的工艺、设备选型、运行情况及技术经济指标。
关键词:循环流化床;半干法;脱硫;工艺;循环流化床半干法脱硫技术在我国许多大型钢铁企业得到了广泛应用,接下来,笔者将以大连绿诺集团有限公司总承包的承钢180m2烧结机烟气脱硫工程为例,介绍循环流化床半干法脱硫技术的具体应用。
1 工艺介绍烧结机主抽风机出来的烟气经入口挡板门进入脱硫塔的底部,烟气流经脱硫塔底部文丘里装置时被加速,并与喷入的水和浆液接触,烟气降至70~90℃左右。
烟气中的SO2与脱硫剂反应,生成亚硫酸钙、硫酸钙等。
烟气带走大量的固体颗粒,进入布袋除尘器除尘,除尘后的净烟气经增压风机排入新建烟囱。
布袋除尘器收集到的脱硫灰一部分经过返料装置进入脱硫塔,另一部分至灰库外排。
循环流化床半干法脱硫工艺流程框图如图1所示。
2设备选型及技术参数承钢180m2烧结机烟气参数:入口烟气量105万m3/h(工况),入口烟气温度150℃,入口SO2浓度≤1500mg/Nm3,入口粉尘浓度≤200mg/Nm3;要求出口粉尘浓度≤30 mg/Nm3,出口SO2浓度≤100mg/Nm3。
根据上述参数,对主要设备选型:1)脱硫塔根据烟气量,选择脱硫塔直径8.2m,高度42m。
2)布袋除尘器选择长袋低压脉冲布袋除尘器,过滤面积20588m2,压力损失<1.5kPa,耐负压5kPa。
3)脱硫风机脱硫系统配置一台可以满足烧结机满负荷生产的离心式风机,采用变频器控制,用于克服FGD装置造成的烟气压降。
脱硫风机的处理烟气量为105万m3/h,全压4kPa。
3 运行情况承钢180m2烧结机烟气脱硫项目(如图2所示)已通过河北省环境保护厅工程治理验收。
整体设备运行稳定,出口烟气SO2浓度≤100mg/Nm3,符合《大气污染物综合排放标准》GB16297-1996 的要求。
电厂烟囱地基处理设计方案比较

电厂烟囱地基处理设计方案比较1 工程概况新疆西部合盛热电有限公司2×330mw机组新建工程,系火力热电项目,采用抽汽供热凝气式汽轮发电机组,配2台1025t/h煤粉锅炉,脱硫采用半干法工艺,配套烟囱高度为210米,出口直径7.5米单筒烟囱(烟囱为乙类建筑),为合盛硅业的自备电厂,工程建设地点位于新疆石河子市化工新材料产业园,距石河子市以北27km。
2 工程地质条件概况及处理设想烟囱基础区域土层:根据地勘资料可知:①由于勘测厂址区域地貌为玛纳斯河下游的冲洪积平原,地下水埋深较浅,水位基本稳定为-2.95~-4.85m 左右,地下水主要由玛河侧向补给及农田灌溉入渗补给。
②抗震基本设防烈度为7度,设计基本地震加速度为0.188g,ⅲ类场地土,特征周期0.55s。
烟囱区域勘测点判定为中等液化,液化深度为4.8-6.5m。
③地下水对混凝土结构具有腐蚀性;对钢筋混凝土结构中的钢筋具有微腐蚀性。
场地土对混凝土结构具有弱腐蚀性,对钢筋混凝土中的钢筋具有微腐蚀性。
④按实际情况进行估算,最下层的粉土为实际基础持力层,虽然粉土以上的圆砾土性状优良,但土层薄导致在开挖时按估算埋深大部分将去除,剩余部分无法发挥作用从而全部去除。
因此,由于存在上述特点,本工程地基不满足330mw等级电厂的设计要求,需进行地基处理。
在考虑到电厂建筑的埋深,烟囱基础埋深在6米的情况,烟囱基础以下应适当的做一定厚度的换填土层,地基处理方案也就明确在解决软弱下卧层的问题。
依据地基强度及变形要求、场地地层分布情况、建筑材料的分布情况等因素综合分析,初步设想烟囱地基处理由3种备选方案:(1)换填砂砾石垫层方案;(2)钻孔灌注桩方案;(3)换填砂砾石垫层+钻孔灌注桩方案。
3 地基处理方案比较3.1 砂砾石碾压换填方案单纯采用粉土层作为持力层将导致计算的烟囱基础外形巨大且变形无法满足。
为此需要将圆砾以上的土层全部清除,然后用工程性质较好的天然级配的砂砾石,分层铺垫、逐层碾压,这样换填3.0m 即可达到设计标高要求。
锅炉烟气半干法脱硫技术

锅炉烟气半干法脱硫技术摘要:锅炉烟气脱硫工艺分为湿法、半干法和干法三种,半干法脱硫技术以投资省、占地小、运行费用低、能节省大量的水、能有效脱除烟气中的SO3等优势,具有更大的发展前景。
关键字:半干法脱硫;循环流化床;预除尘器;脱除SO31 引言近年来,随着社会工业生产的快速发展,环境问题日渐突出,雾霾天气愈发严重,各国的环境保护意识日益加强,大气污染物排放的控制越来越严格。
虽然风电、太阳能发电、核电等新型能源产业发展迅速,但在相当长的一段时间内火电厂在能源结构中仍将占据较大比重,煤炭仍是火电厂的重要燃料,煤炭燃烧过程中产生大量的二氧化硫气体,成为空气的重要污染源,也是形成酸雨的重要原因。
世界上大多数国家都强制要求火电厂必须安装烟气脱硫装置,以除去烟气中所含的硫化物,达到环保排放标准。
我国最新颁布的《火电厂大气污染物排放标准》( GB13223 -2011) 对火电厂 SO2的排放提出了严格的限制要求。
2 半干法脱硫技术介绍燃煤锅炉脱硫方式通常分为燃烧前脱硫、燃烧中脱硫和燃烧后脱硫三种,其中燃烧后脱硫即烟气脱硫(FGD)是当今世界上普遍采用的方法。
烟气脱硫按反应产物的物质形态(液态、固态)可分为湿式、半干式和干式三种。
目前世界上大型机组采用的脱硫方法主要为湿法脱硫,如石灰石-石膏法、海水法等。
干法脱硫工艺主要利用粉末状的吸收剂对烟气中的二氧化硫进行吸收,整个生产流程在干燥状态下完成,其产生的衍生物也为干燥的粉末。
目前常有的干法脱硫工艺主要有炉内喷钙法和炉内喷钙尾部增湿脱硫技术,此种烟气脱硫技术已经在欧洲、北美等地区得到了大量应用。
半干法脱硫是利用物理方法将吸收浆液进行雾化处理,利用雾化的吸收液完成对烟气中二氧化硫的吸收。
雾化的浆液增加了吸收剂和烟气的接触面积,从而提高了吸收剂与烟气的反应速度和吸收率。
同时,吸收剂吸收了烟气的热量,脱硫产物的水分减少,以固态的形式排出。
半干法脱硫兼具湿法脱硫及干法脱硫的特点,主要是在湿状态下脱硫,干状态下处理脱硫产物。
火电厂脱硫烟囱的结构选型

Q : ( 王)
工 业 技 术
Ch i n a Ne W Te c h n o l o e s a nd Pr o d uc t s
火 电厂脱硫 烟 囱的结构选 型
魏 青 张代刚 ( 中机 国能 电力工程有限公 司, 上海 2 0 0 0 6 1 )
资料相 对很 少 , 经 验也 不多 , 只是从 烟气 的 条 的规 定 : 当 排 放 强 腐蚀 性 烟气 时 , 宜 采 腐 蚀等 级对 烟 囱的腐蚀 设计 进行要 求 。从 用多 管式 或 套筒 式 烟 囱结 构 型式 , 其排 烟 9 9 1 年至 1 9 9 8年 ,有关 单位 曾对 国 内部 内筒 应 采用 耐 酸材 料构 成 ; 当排 放 中 等腐 国际工 业 烟 囱协 会 在 《 钢 烟 囱标 准 规 1 程》 中针对脱硫后 的烟气腐蚀性能( 烟气 分 电厂 的烟 囱进 行过 调查 , 得 出如 下结 论 : 蚀性 烟 气时 , 既 可采 用 多 管式 或 套 筒式 烟 腐蚀 性 能对 其 它 类 型烟 囱同样 适 用 ) 作 出 ( 1 ) 烟气 处 于 正 压 运 行 的 烟 囱 , 烟 囱 囱 ,也 可 采 用 改 进 型 钢 筋 混 凝 土 单 筒 烟 以下 说 明 : 内部腐 蚀 较 重 , 烟 囱 内衬及 保 温层 密闭 性 囱 ; 当排 放 弱 腐 蚀性 烟气 时 , 可 采 用 改 进 ( 1 ) 烟气 冷 凝 物 中氯 化 物 或氟 化 物 的 效 果差 的烟 囱 , 钢筋 混 凝 土外 壁有 不 同程 型钢筋 混 凝土 单筒 烟 囱 。 存 在 将使 其腐 蚀 性大 大提 高 。 度 的腐 蚀现 象 。 《 工 业建 筑 防腐 蚀 设计 规 范 》 6 . 3 . 1 条 排放 的气体 中含有 酸性 冷凝 液时 , 宜 ( 2 ) 处于 烟 气 脱硫 系统 下 游 的浓 缩 或 ( 2 ) 一般 烟 囱筒壁 内表 面都结 露 , 保 温 规 定 : 饱 和 烟气 条 件 通 常被 视 为 高腐 蚀 等级 ( 化 层 很潮 湿 。不 安 装 G G H的 F G D系 统 的烟 采 用套 筒式 排气筒 或塔 架式 排气 筒 。并 给 囱中凝 结水 量会 比较大 , 应按 湿烟 囱设计 。 出了以下比较成熟 的判定标准 :排放气体 学荷载) 。 ( 3 ) 确 定 含有 硫 磺 氧 化 物 的烟 气腐 蚀 ( 3 ) 采用湿法脱硫装置的烟 囱, 烟 气 中含有 酸性冷 凝液 ( 即温 度低 、 湿度 大 的条 等级 ( 化学荷载 ) 是按 S 0 的 含 量 值 为 依 含 水量 大 。 应 重视 冷凝 稀 酸液 的渗 透和 隔 件 下 ) , 冷 凝 液会顺 内衬 或 内筒 向下流 淌 , 离, 对冷 凝 稀酸 液采 取 聚集 和排 除措施 。 并 可能 通过块 体砌 体 内衬 的灰缝 渗入 外筒 3 烟 囱 的设 计 标准 内表面 时 , 推 荐采 用套筒 式或 塔架 式 。 3 . 1国 际 工业 烟 囱协会 ( C I C I N D ) 的 2 0 0 5 年9 月, 中国 电力 工程 顾 问集 团 酸, 它 的 化合 物温 度 约 为 6 0  ̄ C, 低 于氯 酸 公 司 已就 脱硫 烟 囱设计 问题在 上 海主持 召 表 I脱 硫后 烟 气对 烟 囱影 响 开了 “ 火 力发 电厂 烟 囱设 计技 术交 流会 ” 。 亭 号 脱硫后烟 气对烟 囱环境 描述 脱硫后烟气 对烟 囱的影 响 备 注 会 议纪 要指 出 :湿法 脱硫 烟 囱的烟气 可 按
半干法烟气脱硫技术工艺及技术参数
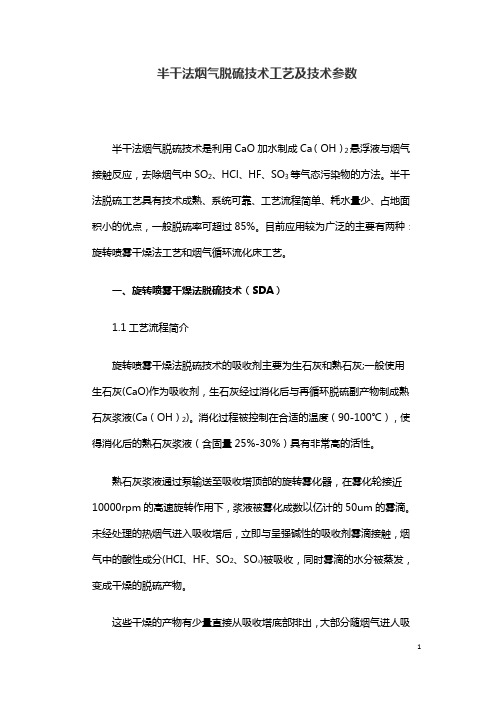
半干法烟气脱硫技术工艺及技术参数半干法烟气脱硫技术是利用CaO加水制成Ca(OH)2悬浮液与烟气接触反应,去除烟气中SO2、HCl、HF、SO3等气态污染物的方法。
半干法脱硫工艺具有技术成熟、系统可靠、工艺流程简单、耗水量少、占地面积小的优点,一般脱硫率可超过85%。
目前应用较为广泛的主要有两种:旋转喷雾干燥法工艺和烟气循环流化床工艺。
一、旋转喷雾干燥法脱硫技术(SDA)1.1工艺流程简介旋转喷雾干燥法脱硫技术的吸收剂主要为生石灰和熟石灰;一般使用生石灰(CaO)作为吸收剂,生石灰经过消化后与再循环脱硫副产物制成熟石灰浆液(Ca(OH)2)。
消化过程被控制在合适的温度(90-100℃),使得消化后的熟石灰浆液(含固量25%-30%)具有非常高的活性。
熟石灰浆液通过泵输送至吸收塔顶部的旋转雾化器,在雾化轮接近10000rpm的高速旋转作用下,浆液被雾化成数以亿计的50um的雾滴。
未经处理的热烟气进入吸收塔后,立即与呈强碱性的吸收剂雾滴接触,烟气中的酸性成分(HCI、HF、SO2、SO3)被吸收,同时雾滴的水分被蒸发,变成干燥的脱硫产物。
这些干燥的产物有少量直接从吸收塔底部排出,大部分随烟气进人吸收塔后的除尘器内被收集,再通过机械或气力方式输送,处理后的洁净烟气通过烟囱排放。
根据实际情况,SDA系统还可以采用部分脱硫产物再循环制浆以提高吸收剂的利用率。
烟气在喷雾干燥吸收塔中的停留时间一般为10-12S,吸收塔内飞灰和脱硫灰大部分通过除尘器收集,只有5%-10%的干燥固体物从吸收塔底部排出。
1.2影响脱硫效率的主要因素1.2.1雾滴粒径雾滴粒径越小,传质面积也越大,但粒径过细,干燥速度也越快,气液反应就变成了气固反应,脱硫效率反而会降低。
有关研究表明,雾化粒径在50um时脱硫率较高。
1.2.2接触时间在旋转喷雾干燥法脱硫技术中,以烟气在脱硫塔中的停留时间来衡量烟气与脱硫剂的接触时间,停留时间主要取决于液滴的蒸发干燥时间,一般为10-12S,降低脱硫塔的空塔流速,延长停留时间,有利于提供脱硫率。
陶瓷工业窑炉废气使用半干法烟气脱硫除尘技术探讨

陶瓷工业窑炉废气使用半干法烟气脱硫除尘技术探讨关键词:半干法窑炉脱硫烟气陶瓷摘要:简述建筑陶瓷工业窑炉烟气特性,介绍目前该行业主要使用的工艺,并提出采用半干法脱硫除尘工艺。
对该工艺进行分析,提出难点及解决办法,降低陶瓷行业工业窑炉排放废气浓度,提高行业的清洁生产水平。
abstract: sketch about building ceramic industry’s furnace exhaust gas’s characteristic , and introduce some major technics deal with the exaust gas , suggest use in wet and dry fgd . in the words , talking about the technology using in this industry will bring some difficults , and try to solve the difficults , to reduce the ceramic industry’s furnace exhaust gas’s effluent concentration,and raise the industry’s cleaner production.中图分类号: tu834.6 文献标识码: a 文章编号:一、项目介绍陶瓷工业窑炉主要采用辊道窑进行生产,排出的废气在目前的行业中大部分均采用湿式脱硫除尘塔系统,这样的结果是so2的排放浓度虽然达标,但粉尘排放浓度很难到新的陶瓷工业排放标准(《陶瓷工业污染物排放标准》(gb25464-2010)),而且采用湿法烟气脱硫,将产生大量的脱硫废水,而且污水处理系统所需的占地面积进一步扩大;废水量的增加,占地面积的进一步需求,使得产品生产过程中需要的能耗也进一步提供,为了进一步提高企业竞争力,根据陶瓷工业行业新的排放要求及进一步提高清洁生产,节能降耗,我公司在原有半干法脱硫系统的基础上开发了半干法窑炉脱硫除尘系统。
湿法与半干法烟气脱硫工艺技术比较
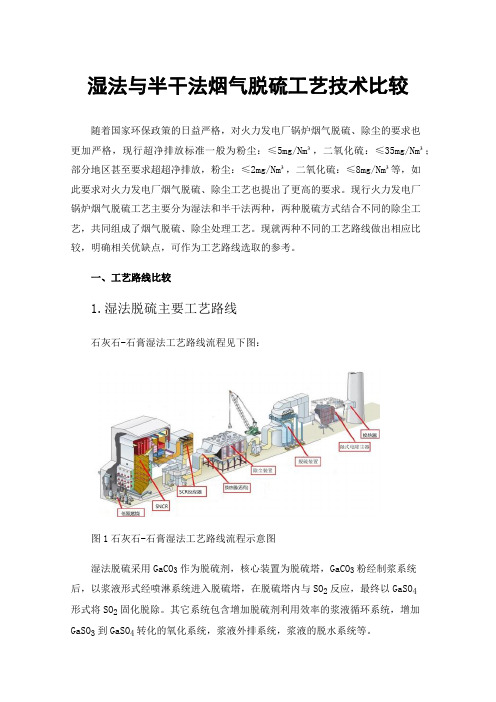
湿法与半干法烟气脱硫工艺技术比较随着国家环保政策的日益严格,对火力发电厂锅炉烟气脱硫、除尘的要求也更加严格,现行超净排放标准一般为粉尘:≤5mg/Nm³,二氧化硫:≤35mg/Nm³;部分地区甚至要求超超净排放,粉尘:≤2mg/Nm³,二氧化硫:≤8mg/Nm³等,如此要求对火力发电厂烟气脱硫、除尘工艺也提出了更高的要求。
现行火力发电厂锅炉烟气脱硫工艺主要分为湿法和半干法两种,两种脱硫方式结合不同的除尘工艺,共同组成了烟气脱硫、除尘处理工艺。
现就两种不同的工艺路线做出相应比较,明确相关优缺点,可作为工艺路线选取的参考。
一、工艺路线比较1.湿法脱硫主要工艺路线石灰石-石膏湿法工艺路线流程见下图:图1石灰石-石膏湿法工艺路线流程示意图湿法脱硫采用GaCO3作为脱硫剂,核心装置为脱硫塔,GaCO3粉经制浆系统后,以浆液形式经喷淋系统进入脱硫塔,在脱硫塔内与SO2反应,最终以GaSO4形式将SO2固化脱除。
其它系统包含增加脱硫剂利用效率的浆液循环系统,增加GaSO3到GaSO4转化的氧化系统,浆液外排系统,浆液的脱水系统等。
为降低大量粉尘进入脱硫塔,对脱硫循环浆液造成不利影响,一般在烟气进入脱硫塔前,须进行脱尘处理。
而又由于湿法脱硫塔顶部仅设有除雾器,对液滴脱除效率不高,要达到粉尘超净排放,一般需在脱硫塔后配套湿式电除尘器来实现。
故整体处理工艺一般如下:锅炉烟气经SCR脱硝处理后,一级配套高效除尘器(电袋、布袋除尘器、电除尘器)进行脱硫前除尘,保证脱硫入口烟气粉尘浓度满足要求。
经一级除尘后烟气进入湿法喷淋塔进行脱除SO2反应。
由于湿法脱硫反应环境无法脱除烟气中以细微硫酸雾滴存在的SO3,在湿法喷淋塔之后必须进一步配套湿式电除尘器来实现脱除。
配套的二级湿式电除尘器同时肩负粉尘减排提效作用。
由于湿法路线后级脱硫及除尘均在湿式环境下进行,为了提高排烟温度,系统通常还同时配套换热器。
锅炉烟气除尘脱硫工程工艺设计
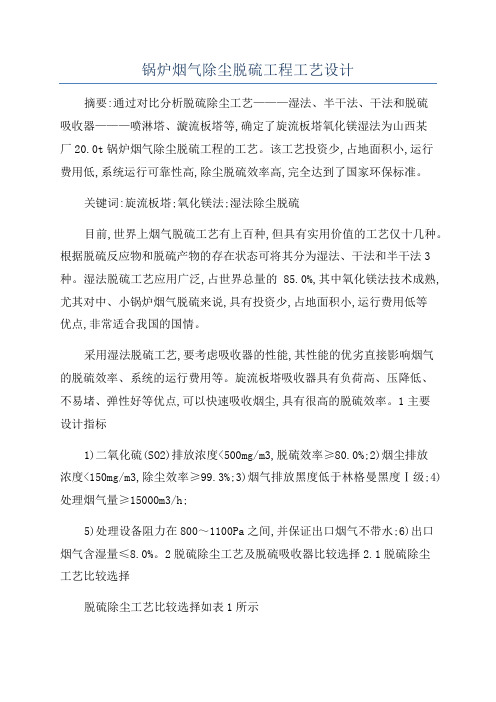
锅炉烟气除尘脱硫工程工艺设计摘要:通过对比分析脱硫除尘工艺———湿法、半干法、干法和脱硫吸收器———喷淋塔、漩流板塔等,确定了旋流板塔氧化镁湿法为山西某厂20.0t锅炉烟气除尘脱硫工程的工艺。
该工艺投资少,占地面积小,运行费用低,系统运行可靠性高,除尘脱硫效率高,完全达到了国家环保标准。
关键词:旋流板塔;氧化镁法;湿法除尘脱硫目前,世界上烟气脱硫工艺有上百种,但具有实用价值的工艺仅十几种。
根据脱硫反应物和脱硫产物的存在状态可将其分为湿法、干法和半干法3种。
湿法脱硫工艺应用广泛,占世界总量的85.0%,其中氧化镁法技术成熟,尤其对中、小锅炉烟气脱硫来说,具有投资少,占地面积小,运行费用低等优点,非常适合我国的国情。
采用湿法脱硫工艺,要考虑吸收器的性能,其性能的优劣直接影响烟气的脱硫效率、系统的运行费用等。
旋流板塔吸收器具有负荷高、压降低、不易堵、弹性好等优点,可以快速吸收烟尘,具有很高的脱硫效率。
1主要设计指标1)二氧化硫(SO2)排放浓度<500mg/m3,脱硫效率≥80.0%;2)烟尘排放浓度<150mg/m3,除尘效率≥99.3%;3)烟气排放黑度低于林格曼黑度Ⅰ级;4)处理烟气量≥15000m3/h;5)处理设备阻力在800~1100Pa之间,并保证出口烟气不带水;6)出口烟气含湿量≤8.0%。
2脱硫除尘工艺及脱硫吸收器比较选择2.1脱硫除尘工艺比较选择脱硫除尘工艺比较选择如表1所示湿法脱硫石灰膏法双碱法90989098氧化镁法9098一般氨法海水法7090高一般一般易高高708560~7560~90≥90半干法喷雾干燥炉内喷钙循环流化床等离子体干法钠法9脱硫效率/%可靠性结垢90~98098高易结垢~~~~~~高高高不不不结结结不不堵堵不不易结结结不不堵堵易不结垢垢垢垢垢垢垢堵塞堵塞堵塞中堵塞中不堵塞中堵塞堵塞占地大小中小大中中面积运行费用投资通过对脱硫除尘工艺———湿法、半干法、干法的对比分析:石灰石-石膏法虽然工艺非常成熟,但投资大,占地面积大,不适合中、小锅炉。
火电厂脱硫烟囱的结构选型

火电厂脱硫烟囱的结构选型作者:魏青张代刚来源:《中国新技术新产品》2013年第16期摘要:随着生态环境日益严峻以及我国环保标准的逐步提高,火力发电厂对烟气在排放到大气之前都要采取一定的脱硫及脱氮措施。
石灰石石膏湿法脱硫工艺以其适用煤种广、脱硫效率高等特点,目前已成为国内技术成熟、应用广泛、运行可靠的脱硫方法之一。
根据工艺专业要求,不设GGH装置(烟气加热系统),相比设GGH装置来讲对烟囱防腐提出了更高的要求。
关键词:火电厂;脱硫;烟囱中图分类号:F40 文献标识码:A1 脱硫后的烟气特点湿法脱硫工艺对烟气中的SO2脱除效率很高,但对烟气中造成腐蚀的主要成分SO3脱除效率并不高,只有约20%左右。
脱硫处理后的烟气一般还含有氟化氢和氯化物等,它们是腐蚀强度高、渗透性强、且较难防范的低温高湿稀酸型物质。
脱硫后烟气对烟囱影响见表1。
烟气脱硫后,虽然能使大气环境得到改善,但对烟囱的腐蚀隐患并未消除,相反,脱硫后的烟气环境(低温、高湿等)使腐蚀状况进一步加剧,因此烟囱的抗腐蚀性能需要提高,尤其脱硫系统不设置GGH时烟囱的抗腐蚀性能要求更高。
2有关烟气对烟囱腐蚀的现状2.1 国际上有关标准国际工业烟囱协会在《钢烟囱标准规程》中针对脱硫后的烟气腐蚀性能(烟气腐蚀性能对其它类型烟囱同样适用)作出以下说明:(1)烟气冷凝物中氯化物或氟化物的存在将使其腐蚀性大大提高。
(2)处于烟气脱硫系统下游的浓缩或饱和烟气条件通常被视为高腐蚀等级(化学荷载)。
(3)确定含有硫磺氧化物的烟气腐蚀等级(化学荷载)是按SO3的含量值为依据。
(4)烟气中的氯离子遇水蒸气形成氯酸,它的化合物温度约为60℃,低于氯酸露点温度时,就会产生严重的腐蚀,即使是化合物中很少量的氯化物也会造成严重腐蚀。
(5)烟气脱硫过程能够对氧化硫起到良好的去除作用,然而在净化装置的下游,氧化硫浓度的降低使得烟气的浓度变高,致使底部潮湿,这样烟气的温度就会降低。
当温度低于80℃时,烟气中的酸性气体凝结成酸液。
脱硫电厂烟囱选型分析
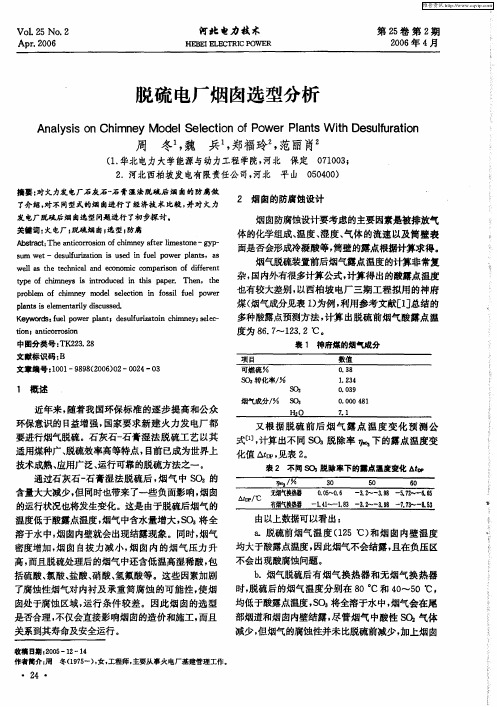
Ss O , 随着我国环保标准的逐步提高和公众 环保意识的日益增强 , 国家要求新建火力发 电厂都
要进行烟气脱硫。石灰石一 石膏湿法脱硫工艺 以其
烟气成分/
S
H O 2
71 .
又 根据脱 硫 前后 烟 气 露点 温度 变 化 预测 公
囱处于腐蚀区域 , 运行条件较差 。因此烟 囱的选型
由以上数据可以看出 : a .脱硫前烟气温 度 (2 15℃) 和烟 囱内壁 温度 均大于酸露点温度 , 因此烟气不会结露 , 且在负压区 不会出现酸腐蚀问题 。
b .烟气脱硫后 有烟气换 热器和无烟气换热器
时, 脱硫后 的烟气温度分别在 8 C和 4 - 5 O。 0 ̄ 0℃, 均低于酸露点温度 ,( 将全溶于水中, S) 3 烟气会在尾
维普资讯
Vo 5 No 2 L2 .
Ap . 0 6 r2 0
河北 电力 技 术
HE EI F ' RI OW E B . T CP EL L R
第 2卷 第 2 5 期
20 年 4 06 月
脱 硫 电厂 烟 囱选 型分析
An lss o i e d l e e t n o o rPlns W i s l r t n a y i n Chmn y Mo e lc i fP we a t t De uf a i S o h u o
周 冬 魏 兵 郑福玲 范丽肖 , , ,
(. 1 华北电力大学能源与动力工程学院, 河北 保定 0 10  ̄ 70 3 2 河北西柏坡发 电有限责任公 司, . 河北 平 山 0 0 0 ) 5 40
摘 要 : 火力发 电厂石灰石‘ 膏湿法 脱硫 后烟 囱的防腐做 对 石
了介绍, 对不同型式的烟囱进行 了经济技术比较, 并对火力
半干法烟气脱硫工艺在球团竖炉的应用

半干法烟气脱硫工艺在球团竖炉的应用本文结合工程实践,详细介绍了半干法烟气脱硫在镔鑫特钢材料公司球团竖炉中的应用,半干法脱硫工艺脱硫效率高、系统简单、运行阻力低,操作维护方便等优点。
半干法脱硫系统运行后,大大降低了SO2的排放浓度,减少了环境污染,到达节能减排,改善厂区环境的目的,具有良好的社会效益和经济效益。
近年来,钢铁企业污染排放一直较为严重,球团竖炉生产过程中,产生大量的粉尘及SO2等有害物质,对环境造成污染,其污染治理一直是钢铁企业污染治理的重点。
为减少球团竖炉生产过程中粉尘及SO2的排放,满足环保要求,镔鑫特钢材料公司对现有竖炉增设一套烟气脱硫设施。
根据竖炉烟气的特点,在球团竖炉主抽风机烟道出口,设置一套半干法脱硫系统。
笔者作为该工程的主要设计人,对脱硫系统做出了详图设计。
1 半干法脱硫工艺原理1.1 工艺原理石灰石-石膏法烟气脱硫技术以生石灰(CaO)作为吸收剂,生石灰经过消化后制成熟石灰浆液(Ca(OH)2)。
作为脱硫剂,熟石灰浆液经过泵输送的吸收塔顶部的喷淋层,在吸收塔喷淋层内对烟气开展喷淋洗涤,使烟气中的SO2反应生成CaSO3,同时向吸收塔内的浆液鼓入空气,使CaSO3转化为CaSO4,脱硫剂的最终产物为石膏(CaSO4˙2H2O)。
脱硫后的烟气经高效除雾器除去雾滴后,由塔顶烟囱排放,SO2的脱硫率可高达97%以上。
该工艺的反应机理为:SO2被雾滴吸收:SO2(g)→SO2(l)+H2O→H++HSO3-→H++SO32-SO2+Ca(OH)2→CaSO3+H2O部分SO2完成如下反应:SO2+1/2O2+ Ca(OH)2→CaSO4+H2O氧化:HSO3-+1/2O2→SO32-+H+SO32-+1/2O2→SO42-结晶:Ca2++SO32-+1/2H2O→CaSO3˙1/2H2O(s)Ca2++SO42-+2H2O→CaSO4˙2H2O(s)1.2 工艺流程烟气由抽引风机引入吸收塔,在吸收塔内,烟气从吸收塔下部进入塔体,吸收剂从上向下分几层喷淋,烟气与石灰浆液快速接触后被迅速吸收,发生化学反应,除去烟气中的SO2、SO3及HCl等酸性气体。
半干法脱硫存在的问题

烟气循环流化床石灰半干法脱硫存在的问题与改造方案烟气循环流化床石灰半干法脱硫存在的问题与改造方案摘要:烟气循环流化床石灰半干法脱硫在我国属于新兴的环保项目,本文主要针对某厂#6炉烟气循环流化床石灰半干法脱硫自投运以来存在的问题进行了分析,并针对每个问题提出了可行性解决方案,其中部分方案已经得以实施,并取得一定成效。
关键词:半干法脱硫存在问题解决方案1、脱硫系统概述某厂#6 炉150MW机组是上海锅炉厂生产的循环流化床锅炉,烟气脱硫除尘系统,采用循环流化床半干法脱硫装置,脱硫除尘岛布置在锅炉尾部的空气预热器出口至烟囱的区域范围,每台锅炉的烟气从空气预热器出来后,进入预除尘器(ESP1)预除尘,除去85%的飞灰,然后进入脱硫塔,在塔内进行脱硫反应,再进入脱硫除尘器(ESP2),除尘后由吸风机排入烟道通过烟囱排放到大气。
脱硫工程除消石灰制备系统和压缩空气系统采用三台机组共用外,其它系统为一台机组一套配置,主要包括:烟气系统、预除尘系统、脱硫塔系统、脱硫电除尘器系统、脱硫工艺水系统、物料再循环系统等。
脱硫塔是烟气脱硫系统的核心设备,其包括烟气进入口、雾化喷嘴安装口、回料口和仓顶排气接入口、顶部封盖、烟气径向出口、底部排灰斗等,从预除尘器出来的烟气经过脱硫塔排出,在脱硫塔中,增湿雾化水、吸收剂分别从文丘里装置扩散管上端喷入,从脱硫电除尘器返回的脱硫灰返回到中间文丘里管的收缩段出口部分。
烟气与脱硫剂进行混合、反应,这种强烈的多相流保证烟气中的SO2与脱硫剂具有较好的反应、换热及传质性能。
从而达到脱硫的目的。
从预除尘器出来的烟气中未被捕集的烟尘、脱硫塔产生的脱硫副产物(脱硫灰)、未完全反应的吸收剂等被气流夹带从脱硫塔顶部排出,进入脱硫电除尘器,这些粉尘绝大部分被捕集落入到电除尘器的灰斗中。
根据脱硫塔内压差的控制信号,一、二电场灰斗下的大部分脱硫灰通过空气斜槽返回脱硫塔参与进一步的化学反应,形成了物料的再循环,只有一小部分物料排出脱硫系统。
- 1、下载文档前请自行甄别文档内容的完整性,平台不提供额外的编辑、内容补充、找答案等附加服务。
- 2、"仅部分预览"的文档,不可在线预览部分如存在完整性等问题,可反馈申请退款(可完整预览的文档不适用该条件!)。
- 3、如文档侵犯您的权益,请联系客服反馈,我们会尽快为您处理(人工客服工作时间:9:00-18:30)。
采用半干法脱硫工艺锅炉的烟囱选型
摘要:燃煤电厂烟气脱硫技术是控制SO2危害有效的手段之一,由于烟囱的材
料和施工质量,对我国脱硫烟囱有不同程度的破坏。
通过分析半干法脱硫后烟囱
烟气的操作条件和特点,对半干法脱硫烟囱的结构形式及防腐方案选择分析,确
保烟囱的设计合理使用年限正常发挥其功能,以确保装置的正常运行。
关键词:锅炉;半干法脱硫;烟气特点;烟囱选型
1半干法脱硫形式工艺
采用气力输送或原煤混掺的方式向炉内喷入CaCO3粉末,在循环流化床锅炉
炉内800℃以上环境下,CaCO3受热分解成CaO、CO2。
CaO与锅炉烟气中的SO2、SO3反应生成CaSO4,未反应完的CaO和未脱除的SO2随烟气进入下游。
CaO+SO2+O2→CaSO4
CaO+SO3→CaSO4
在锅炉尾部增加活化脱硫塔,离开的锅炉的未反应完的CaO因为脱离了高温区,活性降低,不在与SO2进行反应,故在炉后增加活化脱硫塔,利用少量的水
使CaO生成 Ca(OH)2在低温状态下也具有较高的反应活性,这些将于烟气中
剩余的SO2反应生成CaSO3,部分被氧化成CaSO4。
CaO+H2O→Ca(OH)2
Ca(OH)2+SO2→CaSO3+H2O
CaSO3+1/2O2→CaSO4
半干法设备大多为固定设备,动设备很少,系统都在干态下进行,系统无需
考虑防腐问题。
就设备复杂程度比较,半干法脱硫设备构造简单,主体塔内部为
空塔,基本没有内部安装的设备,外围配合设备也很少。
2半干法脱硫技术
2.1喷雾干燥脱硫技术
喷雾干燥脱硫技术使用生石灰(CaO)作为吸收剂,生石灰经过消化后制成
熟石灰浆液(Ca(OH)2),熟石灰浆液通过泵输送至吸收塔顶部的旋转雾化器,在雾化轮高速旋转作用下,浆液被雾化成雾滴,含硫烟气进入吸收塔后,与呈强
碱性的吸收剂雾滴相接触,烟气中的其他酸性成份(如HCl、HF、SO3)被吸收,同时雾滴的水分被蒸发,变成干燥的脱硫产物。
喷雾干燥半干法脱硫技术的反应过程:
CaO+H2O→Ca(OH)2
Ca(OH)2+SO2→CaSO3+H2O
Ca(OH)2+SO3→CaSO4+H2O
Ca(OH)2+2HCl→CaCl2+2H2O
Ca(OH)2+2HF→CaF2+2H2O
2CaSO3+O2→CaSO4
喷雾干燥脱硫技术工艺流程较简单,投资也较小,适用于小机组、中低硫煤,在钙硫比为 1.5时,脱硫效率可达70%~80%,副产物没有成熟的商用利用途径。
2.2烟气循环流化床技术
从锅炉出来的含有粉尘和SO2的烟气,从脱硫塔的底部经文丘里管进入吸收塔,与吸收剂发生反应后,烟气温度高于烟气露点温度15℃以上进入除尘器。
生
石灰在消化器内加水消化后,在消石灰仓储存。
将一定量的消石灰粉和水在文丘
里喉口上端加入,在脱硫塔内与烟气混合流动,并与烟气中的SO2反应,生成亚
硫酸钙和硫酸钙,进入后面的除尘器。
反应产物通过空气斜槽返回塔内,再次循
环参与脱硫反应。
烟气循环流化床技术的反应过程:
SO2+H2O→H2SO3
Ca(OH)2+H2SO3→CaSO3+2H2O
CaSO3(L)→CaSO3(S)
CaSO3+1/2O2→CaSO4
CaSO4(L)→CaSO4(S)
烟气循环流化床法脱硫效率较高,在Ca/S大于1.3、烟气温度高于绝热饱和温度15℃以上,脱硫效率达到90%以上,是目前半干法同类脱硫技术中单塔处理能力最大、脱硫效率较高的一种脱硫方法的,但副产物缺少有效的商业化利用途径。
2.3 循环悬浮式半干法脱硫技术
循环悬浮式半干法烟气净化+布袋除尘器工艺,主要根据循环流化床理论,采用悬浮方式,使吸收剂在反应塔内悬浮、反复循环,与烟气中的酸性物质充分接触反应来实现脱硫的一种方法。
其既有干法无污水排放、脱硫后产物易处理的好处,又有湿法脱硫反应速度快、脱硫效率高的优点。
SO2(气)+H2O→H2SO3(液)
Ca(OH)2(液)+H2SO3(液)→CaSO3(液)+2H2O
Ca(OH)2(固)+H2SO3(液)→CaSO3(液)+2H2O
CaSO3(液)→CaSO3(固)
CaSO3(液)+1/2O2(液)→CaSO4(液)
CaSO4(液)→CaSO4(固)
3半干法脱硫工艺主要影响因素
3.1近绝热饱和温度差
半干法烟气脱硫反应中出口烟的温度和烟气的绝热饱和温度之间的差额即近绝热饱和温度差,在其数值较小的情况下,水的消耗大、需要补充大量的水,使液相在吸收塔内的存在时间加长,有利于SO2的吸收,但在系统内易出现阻塞、结露等现象;如绝热饱和温度差进一步提高,脱硫效率会有所降低。
通常出口烟温高于绝热饱和温度15℃以上,既能保证脱硫效率,又能避免出现阻塞、结露现象。
3.2烟气停留时间
随着吸收塔内烟气和吸收剂接触停留时间增加,脱硫效率会有所提升,在烟气循环流化床脱硫工艺中,其烟气停留时间控制在6~8s以内为宜;旋转喷雾反应器内烟气流速约1.2~1.6m/s,石灰系统的烟气停留时间为8~12s。
3.3 Ca/S(钙硫比)
通常随着钙硫比的增大脱硫效率增加,钙硫比的大小与烟气的停留时间也密切相关,对于较长的停留时间,即使是在较低的、合适的钙硫比的情况,也可以获得较高的脱硫效率。
3.4吸收剂再循环倍率
对循环流化床半干法脱硫工艺来说,吸收剂再循环倍率直接影响脱硫效率和钙的利用率。
再循环倍率越高,脱硫效率越高,钙的利用率也越高,但是太高的再循环倍率会使吸收系统压降增加,增加系统的能耗。
3.5雾滴粒径
对旋转喷雾脱硫工艺来说,浆液雾化粒径与雾化空气压力大小以及雾化旋转喷嘴的转速有关。
雾化压力和转速越大,浆滴粒径越小,有利于SO2的吸收、钙
的利用和产物干燥,但是雾滴过小,在与烟气接触的过程中容易干燥而使反应速
度下降,影响了钙的利用。
3.6液气比
对旋转喷雾脱硫工艺来说,脱硫效率与液气比有关。
在一定吸收剂浓度的情
况下,液气比越大,越有利于SO2的吸收,但是过高的液气比,存在产物不易完
全干燥,增加塔壁积垢的风险。
4半干法脱硫烟囱常用形式
4.1防腐型单筒式烟囱
在外筒内壁采用“2布5涂”法涂上OM涂料;将现浇发泡聚氨酯保温隔热层。
该方案已使用多年,隔热层外内衬采用带企口烧结釉面耐酸耐火砌块,用耐酸胶
泥砌筑,该技术成熟且较为普遍,但施工过程工序较多,衬砌和保温层密度较低,施工难度较大,施工质量难以控制。
4.2防腐型单筒式烟囱
用防水耐酸胶泥在混凝土墙表面批刮,平均厚度2 ~ 33mm,,使整个封闭的
空间,耐酸涂抹均匀,然后吹防水抗渗的三面光腐蚀陶瓷砖,并粘贴到位置,内
壁和挤压密实,保证平躺,垂直的,水泥砂浆关节和结合层,和纵向接缝错开。
该防腐内衬系统由胶粘剂层和轻质防腐陶瓷砖层双层结构组成,其中胶黏剂
层是防腐蚀的关键,轻质防腐陶瓷砖主要起到保护和保温隔热效果。
4.3钢套筒式烟囱
钢内筒采用不锈钢316L,中间60mm厚硅酸铝保温棉及空气层作为隔热层,
外筒材质Q235B,作为整个烟囱的主要支撑。
套筒式烟囱从结构体系上避免了烟
气腐蚀对烟囱结构主体的安全危害,对烟气负压运行和烟气抬升相对较好。
钢套
筒烟囱从出厂时分段预制成成品,现场仅需拼接螺栓把住即可,施工简单,周期短,特别适合小型燃煤锅炉烟气排放及对工期要求严格的项目使用。
5结束语
采用半干法脱硫工艺的锅炉,烟气与湿法脱硫(不设置GGH)相比,温度较
高(相当于设置GGH),湿度较低,因此腐蚀性减弱(中等腐蚀性等级),采用
套筒式钢烟囱完全能满足安全运行要求。
参考文献:
[1] 杨晓飞.半干法烟囱设计标准的完善建议[J].中国标准化,2017(09)。