材料成形工艺基础最新精品课件第三章金属的铸造成形工艺方法
材料成型第3章金属的铸造形成工艺2

61
3. 离心铸造应用范围
用离心铸造法生产产量很大的铸件有以下几种: (1) 铁管,世界上每年球墨铸铁管件总产量的近一半是用离心铸造法生产的; (2) 柴油发动机和汽油发动机的气缸套。 (3) 各种类型的铜套。 (4) 双金属钢背铜套、各种合金的轴瓦。 (5) 造纸机滚筒。
材料成型第3章金属的铸造形成工艺2
冷压室卧式压铸(目前应用最多)
(3)取出铸件:铸件凝固之后,抽芯机构将型腔两侧型芯同时抽 出,动型左移开型,铸件则借冲头的前伸动作离开压室。此后, 在动型继续打开过程中,由于顶杆停止了左移、铸件在顶杆的作 用下被顶出动型(图d)。
材料成型第3章金属的铸造形成工艺2
冷室压铸机的压室 和熔炉是分开的, 压铸时要从保温炉 中舀取金属液倒入 压室内,再进行压 铸。
材料成型第3章金属的铸造形成工艺2
冷压室卧式压铸(目前应用最多)
(1)注入金属 先闭合压型,将勺内金属液通过压室上的注 液孔向压室内注入(图a)。 (2)压铸压射冲头向前推进,金属液被压人压型中(图b)。
材料成型第3章金属的铸造形成工艺2
1、压力机工作原理及应用 (1)热压室压铸机
热室压铸机的压室 与合金熔化炉联成一体, 压室浸在保温坩埚的液 体金属中,压射机构装 在坩埚上面,用机械机 构或压缩空气所产生的 压力进行压铸。
图3-23为热室压铸机工作原理示意图。
材料成型第3章金属的铸造形成工艺2
(2)冷压室压铸机
材料成型第3章金属的铸造形成工艺2
二、 压力铸造
定义:在高压(30~70MPa) 下将液态或半液态合金 快速( 5~100mm/s,t=0.05~0.2s))地压入金属铸型中, 并在压力下凝固,以获得铸件的方法。
材料成型技术

第一章金属的液态成形将熔融的金属液浇注入铸型内,待冷却凝固后获得所需形状和性能的毛坯或零件的工艺过程称为铸造。
用铸造方法制成的毛坯或零件称为铸件。
与其它金属加工方法相比,铸造具有如下优点:(1)原材料来源广(2)生产成本低(3)铸件形状与零件接近,尺寸不受限制第一节液态成形铸造理论基础铸造性能是合金在铸造生产中所表现出来的性能,包括合金的流动性、收缩性等。
一、合金的凝固与收缩液体金属在凝固和冷却过程中,体积和尺寸减少的现象,称为合金的收缩。
1、铸件的凝固方式(1)逐层凝固方式(2)糊状凝固方式(3)中间凝固方式2、合金的收缩方式(1)液态收缩:从浇注—液相线(2)凝固收缩:液相线—固相线(3)固态收缩;固相线—室温,是产生内应力、裂纹和变形的主要原因3、影响收缩的因素(1)化学成分碳、硅量高,收缩减少;锰、硫量高,收缩增大。
(2)浇注温度浇注温度越高,收缩越大。
(3)铸件结构和铸型条件二、合金的流动性和充型能力1、流动性流动性是指熔融金属本身的流动能力。
合金流动性好的优点:(1)易获得形状复杂、轮廓清晰的薄壁件;(2)有利于气体和夹杂物的上浮和排除;(3)有利于补缩;因此,能有效防止铸件出现冷隔、浇不足、气孔、夹渣、缩孔等缺陷。
合金流动性的大小通常用浇注流动性试样的方法来测定。
2、影响合金流动性的因素(1)合金种类(2)化学成分一般规律:合金的凝固范围宽,流动性差。
硅提高流动性;锰的影响不大;硫易形成硫化锰,降低流动性;磷提高流动性。
3、合金的充型能力在实际生产条件下,熔融金属充满型腔,获得形状完整、轮廓清晰铸件的能力,叫合金的充型能力。
影响充型能力的因素有:(1)铸型填充条件:包括铸型的蓄热能力、温度及铸型中的气体等。
(2)浇注条件:包括浇注温度、充型压力等。
(3)铸件结构三、铸造性能对铸件质量的影响1、铸件中的缩孔和缩松缩孔是容积较大而集中的孔洞。
缩松是细小而分散的孔洞。
(1)缩孔缩孔通常隐藏在铸件上部或最后凝固的部位。
金属的铸造成型工艺.ppt
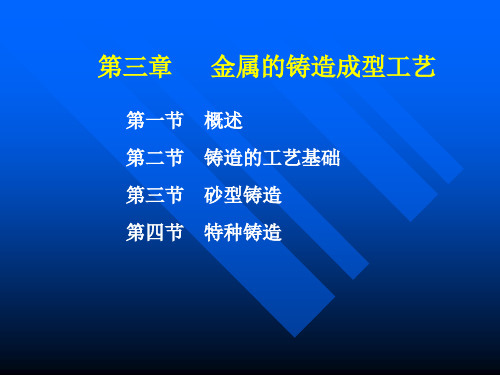
低压铸造:
➢ 定义:是指液态金属在低的气体压力作用下从坩埚中
自下而上地充填型腔并凝固而获得铸件的一种铸造方法。
➢ 工艺过程:
低压铸造火车车轮示意图
➢ 特点和应用:
1、充型压力和充型速度易于控制,气孔、夹渣较少; 2、铸型散热快,组织致密,机械性能好; 3、无需冒口设置,金属利用率高; 4、铸件尺寸精度高,表面光洁; 5、适于生产质量要求高的铝镁等有色金属铸件。
第三章 金属的铸造成型工艺
第一节 概述 第二节 铸造的工艺基础 第三节 砂型铸造 第四节 特种铸造
第一节 概 述
金属的成形方法可分为铸造、塑性成形(或称压力加 工)、切削加工、焊接和粉末冶金五大类。
铸造是生产金属零件毛坯的主要工艺方法之一,与其 它工艺方法相比,它具有成本低,工艺灵活性大,适合生 产不同材料、形状和重量的铸件,并适合于批量生产。
作用下将熔融金属浇注到铸型中制造铸件的一种铸造方法, 也称永久型铸造。
➢ 工艺过程:
➢ 特点和应用:
1、可重复使用,生产效率高,劳动条件好,但成本高; 2、铸件精度高,表面粗糙度较低; 3、金属散热性能好,晶粒细化,机械性能好; 4、不透气且无退让性,易造成铸件浇不足或开裂。 5、适于生产大批量有色金属铸件。
使之在高压和高速下充填型腔,并在高压下成形结晶而获 得铸件的一种铸造方法。
➢ 工艺过程:
大型压铸机及压铸模
➢ 特点和应用:
1、浇注时间短,易于机械化、自动化作业; 2、铸型散热快,晶粒细化,耐磨、耐蚀性好; 3、铸件尺寸精度高,表面光洁; 4、凝固速度快,排气困难,易形成疏松和缩孔; 5、模具成本高,铸件尺寸受限; 6、适于有色金属薄壁复杂铸件的大批量生产。
连续铸造:
工程材料及成形工艺基础 ppt课件

ppt课件
概述—特点、分类
特点:
优点:零件的形状复杂; 工艺灵活; 成本较低。
缺点:机械性能较低; 精度低; 效率低、劳动条件差
铸造方法
砂型铸造——90%以上;
特种铸造——铸件性能较好,精度低,效率高 金属型铸造、压力铸造、熔模铸造、离心铸造……
7
ppt课件
概述—本章要点
本章要点 金属铸造性能 砂型铸造 铸造工艺设计要点 特种铸造
ppt课件
铸件的结构工艺性
进行铸件结构设计,不仅要保证其力学性能 要求,还必需考虑铸造工艺和合金铸造性能对铸件 结构的要求,使铸件的结构与这些要求相适应。使 这些铸件具有良好的工艺性,以便保证铸件质量, 降低生产成本,提高生产率。
一、铸件结构应利于避免或减少铸件缺陷
铸件的结构,如果不能满足合金铸造性能的要 求,将可能产生浇不足、冷隔、缩松、气孔、裂 纹和变形等缺陷。
不用或少用型芯
46
ppt课件
型芯稳固、排气清理方便
47
ppt课件
48
ppt课件
3. 铸件的结构斜度
垂直于分型面的非加工面上设计出结构斜度, 斜度较大。与拔模斜度不同,结构斜度是在设计时 设计上去的,不再被加工掉。
49
ppt课件
4. 组合铸件的应用
大型复杂铸件.
三、 铸件结构要便于后续加工 减少加工量,便于加工
1. 铸件外形尽量简单
(1)避免外部的侧凹,减少分型面或外部型芯: (2)分型面应平直: (3)凸台和筋的设计应便于造型和起模: (4)铸件的垂直壁上应考虑给出结构斜度:
41
ppt课件
减少分型面数目
42
ppt课件
43
材料成形工艺基础最新精品课件第三章金属的铸造成形工艺方法

3)铸件尺寸精度可达 CT4~8级,表面粗糙度Ra1.6~ 12.5μm。其精度和表面质量比 其他铸造方法都高,可实现少、 无切削加工,省工、省料、成本 低。
1. 实型铸造工艺过程
图3-17 实型铸造 (a)泡沫塑料模;(b)铸型;(c)浇注;(d)铸件
2. 实型铸造的特点及应用
(1)精度高 无需起模,因而无飞边毛 刺,
(2)设计灵活 各种形状复杂铸件的模 样均可采用泡沫塑料模粘合,成形为整 体,
(3)降低成本
实型铸造具有无与伦比的优势,被国内外铸造界称为“21世纪的铸造技术”。 经过十多年的生产实践,我国的实型铸造技术取得了飞跃的发展,但要保证技术 、生产与质量同步发展还需要不懈的努力。实型铸造主要用于不易起模等复杂铸 件的批量及单件生产,如各种电机壳、变速箱壳体、叉车箱体等。
图3-13 低压铸造示意图
(a)合型;(b) 压铸;(c) 取出铸件
低压铸造
2. 低压铸造的特点及应用
1)充型压力和速度便于 控制,故可适应各种铸型,如 金属型、砂型、熔模型壳、树 脂壳型等。由于充型平稳,冲 刷力小,且液流和气流的方向 一致,故气孔、夹渣等缺陷较 小。
2)铸件的组织致密,力学 性能较高。对于铝合金针孔缺 陷的防止和提高铸件的气密性, 效果尤为显著。
3.2.1 金属型铸造
金属型铸造
1. 金属铸型的结构
金属铸型的结构有整体式、水平分型式、垂直分型式和复合分型式几种
2.金属型的铸造工艺
(1)预热金属型 (2)喷刷 (3)控制开型 (4)加强金属型的排气
金属材料的成型工艺解析PPT课件

组合式金属型
第17页/共110页
• 金属型优点:
金属型缺点:
• 一型多铸,生产效率高
• 铸件尺寸精度高,表面质 量好 (IT12~14, Ra6.3~12.5)
• 铸件冷却快,组织致密,
金属型成本高
没有退让性,不宜生 产形状复杂的铸件
铸件冷却快,组织致 密,机械性能好
机械性能好
金属型铸造主要用于铜、铝、镁等有色金属铸件的大
热轧是将材料加热到再结晶温度以上进行轧制,热 轧变形抗力小,塑性较差或变形量大,生产效率高,适 合轧制较大断面尺寸,塑性较差或变形量较大的材料。
冷轧是在室温下对材料进行轧制。与热轧相比,冷 轧产品尺寸精度高,表面光洁,机械强度高。冷轧变形 抗力大,适于轧制塑性好,尺寸小的线材、薄板材等。
根据轧辊轴线与坯料轴线方向的不同
挤压主要的影响因素:
在挤压的主要影响因素中,挤压模的角度α和坯料 挤出前后的横截面积之比A0/Af(称为挤压比)属于几 何变量;此外,坯料的温度、挤出的速度以及润滑剂 的种类对挤压工艺来说也相当重要。
第48页/共110页
挤压成形的特点:
1、挤压时金属坯料在三向受压状态变形, 因此可提高金属坯料的塑性;
2、回复和再结晶
保持加工硬化,消除 内应力。如冷卷弹簧 进行去应力退火。
消除加工硬化, 提高塑性。
再结晶速度取 决于加热温度和变 形程度。
再结晶也是一 个形核、晶核长大 的过程。
第35页/共110页
3、冷变形和热变形
冷变形 —— 再结晶温度以下的塑性变形。
热变形 —— 再结晶温度以上的塑性变形
冷变形
第44页/共110页
➢ 楔横轧:利用两个外表镶有凸块并作同向旋转的平行
金属材料成型基础ppt课件.ppt

在整堂课的教学中,刘教师总是让学 生带着 问题来 学习, 而问题 的设置 具有一 定的梯 度,由 浅入深 ,所提 出的问 题也很 明确
在整堂课的教学中,刘教师总是让学 生带着 问题来 学习, 而问题 的设置 具有一 定的梯 度,由 浅入深 ,所提 出的问 题也很 明确
流动性(cm)
温度(℃)
影响液态合金流动性的因素: 1.合金的化学成分
b a
300
200
100 0
80 60 40
20 0
Pb 20 40 60 80 Sb
a)在恒温下凝固 b)在一定温度范围内凝固
充型能力越强。 (3)浇注系统的的结构 浇注系统的结构越复杂,流动阻力
越大,充型能力越差。
在整堂课的教学中,刘教师总是让学 生带着 问题来 学习, 而问题 的设置 具有一 定的梯 度,由 浅入深 ,所提 出的问 题也很 明确
三、铸型充填条件
(1)铸型的蓄热系数 铸型的蓄热系数表示铸型从其中的 金属吸取热量并储存在本身的能力。
铸件输送机
1)振击压实
型砂
落砂
捅箱机
压铁传送机
2)汽动微振压实
3)高压造型
加砂机
压铁
4)抛砂加紧砂机实
上箱造型机
合箱 合箱机
下箱造型机
下芯
下箱翻箱、落箱机 铸型输送机
冷却箱
浇注
冷却
在整堂课的教学中,刘教师总是让学 生带着 问题来 学习, 而问题 的设置 具有一 定的梯 度,由 浅入深 ,所提 出的问 题也很 明确
二、机器造型
1)生产效率高; 2)铸型质量好(紧实度高而均匀、型腔轮廓清晰); 3)设备和工艺装备费用高,生产准备时间较长。
适用于中、小型铸件的成批、大批量生产。
- 1、下载文档前请自行甄别文档内容的完整性,平台不提供额外的编辑、内容补充、找答案等附加服务。
- 2、"仅部分预览"的文档,不可在线预览部分如存在完整性等问题,可反馈申请退款(可完整预览的文档不适用该条件!)。
- 3、如文档侵犯您的权益,请联系客服反馈,我们会尽快为您处理(人工客服工作时间:9:00-18:30)。
操作简单,应用广泛
体等形状较复杂的铸件
三箱造型
铸件有两个最大截面,分模、两个分型面且为平面、三个砂箱造 型,中箱高度与中箱模样高度相同,所以无法机器造型。操作繁 琐,容易错箱
主要用于手工造型,单件、小批量生产具 有两个分型面的中、小型铸件
挖砂造型
最大截面不在一端,而且不是平面。为了取出模样,造型时要人 工挖去阻碍起模的型砂。造型费时,生产率低,容易掉砂
(1)因为在陶瓷层处于弹性状态下
起模,同时陶瓷型高温时变形小,故铸 件的尺寸精度可达CT5~8级,表面粗糙度 Ra3.2~12.5μm。此外,陶瓷材料耐高温, 故也可浇注高熔点合金。
(2)陶瓷型铸件大小不受限制,从几 公斤到数吨。
(3)在单件、小批生产条件下,投资
少、生产周期短,在一般铸造车间较易 实现。
4)金属在压力下凝固,冷 却速度又快,铸件组织细密,表 层紧实,强度、硬度高,抗拉强 度比砂型铸造提高20%~40%。
3.2.4. 低压铸造
低压铸造是液态金属在压力作 用下由下而上充填型腔,以形成 铸件的一种方法(0.02—0.06MPa)。 1. 低压铸造的工艺过程
低压铸造的原理如图3-13(a) 所示。其下部是一个密闭的保温 坩埚炉,用于储存熔炼好的金属 液。坩埚炉的顶部紧固着铸型 (通常为金属型或砂型),垂直 升液管使金属液与朝下的浇注系 统相通。
3)由于省去了补缩冒口, 使金属的利用率提高到90~98%。
4)由于提高了充型能力, 有利于形成轮廓清晰、表面光 洁的铸件,这对于大型薄壁件 的铸造尤为有利。
3.2.5 离心铸造
离心铸造
将液态金属浇入高速回转(通常为250~1500r/min)的铸型中,使其在离心力作 用下充填铸型并凝固而获得铸件的方法称为离心铸造。
1. 手工造型方法
根据铸件的形状不同可采取不同的造型方法,而造型方法不同其结构 的设计也不同。
造型方法名称
主要特点
适用范围
整模造型
模样为整体模,分型面是平面,型腔全部在半个铸型内,造型简 单,不会错箱
最大截面位于一端且为平面的简单铸件、 适用于各种生产批量
分模造型
模样沿最大截面分两半,分型面是平面,型腔位于上、下两砂箱, 适用于最大截面在中部的套类、管类和阀
(a)浇入定量液体金属
(b)上型向下挤压
图3-19 挤压铸造示意图
1-上型;2-金属液;3-铸件;4-下型
2. 挤铸的特点及应用 挤铸与压力铸造及低压铸造的共同点是,压力的作用是使铸
件成形并产生“压实”,使铸件致密。其不同点是挤铸时没有浇 口,且铸件的尺寸较大,较厚时,液流所受阻力较小,所需的压 力远比压力铸造小,挤铸的压力主要用于使铸件压实而致密。
陶瓷型铸造的不足是不适于批量大、
重量轻或形状复杂铸件,且生产过程难 以实现机械化和自动化。
图3-16 陶瓷型铸造工艺过程
目前陶瓷型铸造主要用于生产厚大的
精密铸件,广泛用于铸造冲模、锻模、
玻璃器皿模、压铸模、模板等,也可用 于生产中型铸钢件。
3.2.7 实型铸造
实型铸造是采用聚苯乙烯泡沫塑料模样代替普通模样,采用微震加负压紧实造 好型后不取出模样就浇入金属液,在金属液的作用下,塑料模样燃烧、气化、消失, 金属液取代原来塑料模所占据的空间位置,冷却凝固后获得所需铸件的铸造方法。
图3-8机器造型用模板
3.2 特种铸造
随着科学技术的发展、铸造生产工艺的改进,为适应社会的需 求,不断地出现了一些与砂型铸造的造型材料和工艺不同的其它铸 造方法,统称为特种铸造,如熔模铸造、金属型铸造、压力铸造、 离心铸造、壳型铸造、陶瓷型铸造、磁型铸造等。与砂型铸造相比 ,特种铸造具有铸造精度和表面质量高、内在性能好、原材料消耗 低、工作环境好等优点。特种铸造的每个铸造方法均有其优越之处 和适用的场合,但不同的铸造方法其铸件的结构、形状、尺寸、质 量、材料种类往往受到某些限制,成本也各不相同。
第3章 金属的铸造成形工艺方法
3.1 砂型铸造(重点内容)
3.1.1 砂型铸造过程 3.1.2 手工造型 3.1.3 机器造型
3.2 特种铸造
3.2.1 金属型铸造 3.2.2 熔模铸造
3.2.3 压力铸造
3.2.4 低压铸造
3.2.5 离心铸造
3.2.6 陶瓷型铸造
3.2.7 实型铸造
3.2.8 壳型铸造
图3-13 低压铸造示意图
(a)合型;(b) 压铸;(c) 取出铸件
低压铸造
2. 低压铸造的特点及应用
1)充型压力和速度便于 控制,故可适应各种铸型,如 金属型、砂型、熔模型壳、树 脂壳型等。由于充型平稳,冲 刷力小,且液流和气流的方向 一致,故气孔、夹渣等缺陷较 小。
2)铸件的组织致密,力学 性能较高。对于铝合金针孔缺 陷的防止和提高铸件的气密性, 效果尤为显著。
3.2.9 挤压铸造
1. 挤铸原理
最简单的挤压铸造法如图3-10所示。其主要特征是挤压铸造的 压力较小(2~10MPa),其工艺过程是在铸型中浇入一定量液态 金属,上型随即向下运动,使液态金属自下而上充型,且挤压铸 造的压力和速度(0.1~0.4m/s)较低。无涡流飞溅现象,因此铸件 致密而无气孔。
(4)生产批量不受限制,单件小批、 成批、大量生产均可适用。
3.2.3 压力铸造
压力铸造是将溶融金属在高压下快 速压入金属铸型中,并在压力下凝固, 以获得铸件的方法。 1. 压力铸造的工艺过程 压力铸造是在 压铸机上完成的。
(a)浇注;(b)压射;(c)开型
压力铸造
2. 压力铸造的特点及应用
1)压力铸造的生产率比其 他铸造方法都高,每小时可压铸 50~500件,操作简便,易实现 自动化或半自动化生产。
3.2.8 壳型铸造
壳型铸造
壳型铸造是用酚醛树脂砂制造薄壳砂型或型芯的铸造方法。 1. 覆膜砂的制备 2. 壳型(芯)的制造过程
3. 壳型铸造的特点及应用 (1)覆膜砂可以较长期贮存(三个月以上),且砂的消耗量少; (2)无需捣砂,能获得尺寸精确的壳型及芯; (3)壳型(芯)强度高,重量轻,易搬运; (4)壳型(芯)透气性好,可用细原砂得到光洁的铸件表面; (5)无需砂箱,壳型及壳芯可长期存放。
3.2.1
金属铸型的结构有整体式、水平分型式、垂直分型式和复合分型式几种
2.金属型的铸造工艺
(1)预热金属型 (2)喷刷 (3)控制开型 (4)加强金属型的排气
3. 金属型铸造的特点及应用
(1)实现了一型多铸,省去了配砂、造型、落砂等工序,节约了大量的 造型材料、造型工时、场地,改善了劳动条件,提高了生产率。而且便于实 现机械化、自动化生产。
用于整体模样且分型面为曲面的铸件,只 适用于单件、小批量生产
假箱造型
为了克服挖砂造型的缺点,在造型前特制一个底胎,然后在底胎 上造下箱。由于底胎不参加浇注,故称做假箱。此法比挖砂造型 简单,且分型面整齐
适用于成批生产,需挖砂的铸件
活块造型
将妨碍起模的小凸台、肋板等做成活动镶嵌结构,待起模时先起 出主体模样,然后再从侧面取出活动的镶嵌活块。造型生产率低, 要求工人技术水平高
主要用于带有突出部分难以起模的铸件, 单件、小批量生产
刮板造型
用刮板代替模样造型,可节约木材,缩短生产周期。但造型生产 率低,要求工人技术水平高,铸件尺寸精度差
主要用于等截面或回转体大、中型铸件, 单件小批量生产。如大皮带轮、铸管等
采用活动砂箱造型,在铸型合箱后,将砂箱脱出,重新用于造型。 脱箱造型(无箱造) 浇注时为了防止错箱,需用型砂将铸型周围填紧,也可在铸型上
3.1.3 机器造型
1. 机器造型工艺过程
机械造型
机器造型
2. 机器造型工艺特点 机器造型采用模板造型,模板是由模样、浇注系统与底板连接
成一体的专用模具。底板形成分型面,模板形成砂型型腔。小铸 件通常采用底板两侧都有模样的双面模板及其配套的砂箱(a), 其他大多数情况下则采用上、下模分开装配的单面模板造型,用 上模板造上砂箱,用下模板造下砂箱(b)。
2)压力铸造由于熔融金属 是在高压下高速充型,合金充型 能力强,能铸出结构复杂、轮廓 清晰的薄壁、精密的铸件;可直 接铸出各种孔眼、螺纹、花纹和 图案等;也可压铸镶嵌件。
3)铸件尺寸精度可达 CT4~8级,表面粗糙度Ra1.6~ 12.5μm。其精度和表面质量比 其他铸造方法都高,可实现少、 无切削加工,省工、省料、成本 低。
(2)金属型铸件的尺寸精度高,表面质量好,铸件的切削余量小,节约 了机械加工的工时,节省了金属。
(3)金属型冷却速度快,铸件组织细密,力学性能好。
(4)铸件质量较稳定,废品率低。
金属型铸造的主要缺点是:金属型制造成本高、周期长,铸造工艺要求严格, 不适于单件、小批量生产。由于金属型冷却速度快,不宜铸造形状复杂和大型薄壁 件。
机器造型,所以选用三箱造型不合适。通过加环形型芯可以将三 箱造型改为两箱造型。
图3-5在图3-3中选用的是活块造型,如果大批量生产机器造型 很难去除活块,所以通过在侧壁加一个型芯取代活块造型,因为 是大批量生产,所以增加一个型芯也是有必要的。
图3-4环形型芯将三箱改为两箱造型
图3-5测壁外型芯代替活块
3.2.2 熔模铸造
熔模铸造
熔模铸造是用易熔材料制成模样,在模样上涂挂若干层耐火材料,
硬化后加热融化模样制成型壳,再经焙烧、然后在型壳温度很高情况下 进行浇注,从而获得铸件的一种方法,也称失蜡铸造。
1. 熔模铸造的工艺过程
熔模铸造的工艺过程包括:制造蜡模、制壳、脱蜡、熔烧、浇注等, 其基本工艺过程如图3-11所示。
2. 熔模铸造的特点及应用
(1)铸件精度高,表面光洁,一般 尺寸公差可达CT4~7,表面粗糙度 Ra1.6~12.5μm。
(2)可铸出形状复杂的薄壁铸件,
如铸件上的凹槽(>3mm宽)、小孔 (φ≥2.5mm)均可直接铸出。