磁控溅射技术优缺点
磁控溅射镀膜
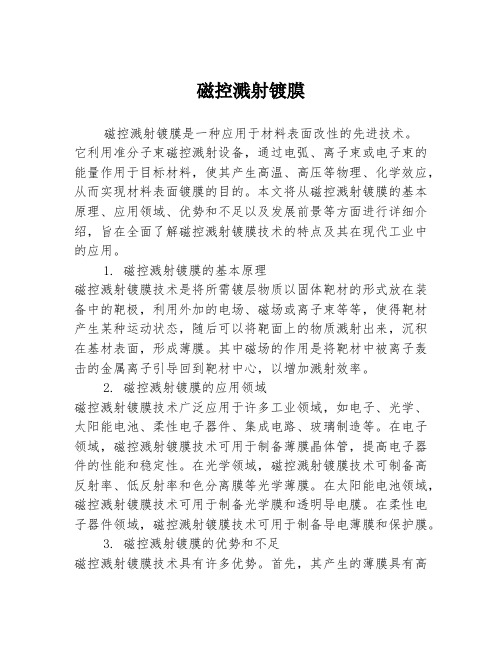
磁控溅射镀膜磁控溅射镀膜是一种应用于材料表面改性的先进技术。
它利用准分子束磁控溅射设备,通过电弧、离子束或电子束的能量作用于目标材料,使其产生高温、高压等物理、化学效应,从而实现材料表面镀膜的目的。
本文将从磁控溅射镀膜的基本原理、应用领域、优势和不足以及发展前景等方面进行详细介绍,旨在全面了解磁控溅射镀膜技术的特点及其在现代工业中的应用。
1. 磁控溅射镀膜的基本原理磁控溅射镀膜技术是将所需镀层物质以固体靶材的形式放在装备中的靶极,利用外加的电场、磁场或离子束等等,使得靶材产生某种运动状态,随后可以将靶面上的物质溅射出来,沉积在基材表面,形成薄膜。
其中磁场的作用是将靶材中被离子轰击的金属离子引导回到靶材中心,以增加溅射效率。
2. 磁控溅射镀膜的应用领域磁控溅射镀膜技术广泛应用于许多工业领域,如电子、光学、太阳能电池、柔性电子器件、集成电路、玻璃制造等。
在电子领域,磁控溅射镀膜技术可用于制备薄膜晶体管,提高电子器件的性能和稳定性。
在光学领域,磁控溅射镀膜技术可制备高反射率、低反射率和色分离膜等光学薄膜。
在太阳能电池领域,磁控溅射镀膜技术可用于制备光学膜和透明导电膜。
在柔性电子器件领域,磁控溅射镀膜技术可用于制备导电薄膜和保护膜。
3. 磁控溅射镀膜的优势和不足磁控溅射镀膜技术具有许多优势。
首先,其产生的薄膜具有高质量、高致密性和良好的附着力。
其次,磁控溅射镀膜过程中无需加热基材,可避免基材变形和热损伤。
此外,磁控溅射镀膜技术具有膜层成分可调、薄膜复杂结构可控等特点。
然而,磁控溅射镀膜技术也存在不足之处。
一方面,磁控溅射镀膜设备体积较大、成本较高,且对真空度要求较高。
另一方面,由于目前磁控溅射镀膜技术仍处于发展阶段,其在大尺寸薄膜制备和高速镀膜方面还存在一定限制。
4. 磁控溅射镀膜的未来发展随着科学技术的不断进步,磁控溅射镀膜技术将进一步得到发展和完善。
一方面,磁控溅射镀膜技术将在薄膜成分调控和复杂结构薄膜制备方面取得更大突破,以满足不同行业对薄膜材料的需求。
磁控溅射镀膜技术综合介绍
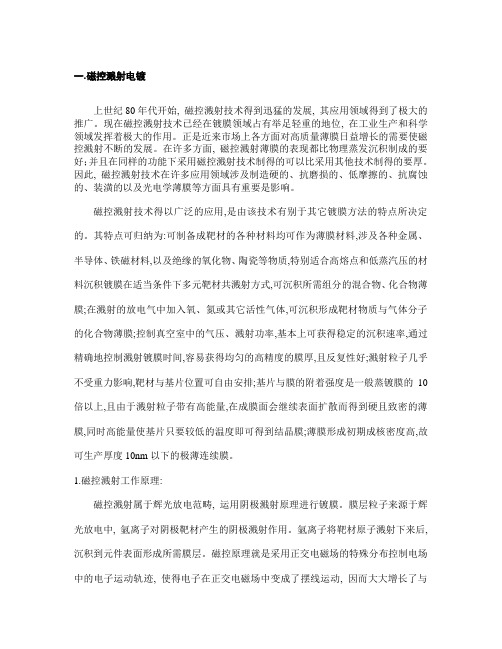
一.磁控溅射电镀上世纪80年代开始, 磁控溅射技术得到迅猛的发展, 其应用领域得到了极大的推广。
现在磁控溅射技术已经在镀膜领域占有举足轻重的地位, 在工业生产和科学领域发挥着极大的作用。
正是近来市场上各方面对高质量薄膜日益增长的需要使磁控溅射不断的发展。
在许多方面, 磁控溅射薄膜的表现都比物理蒸发沉积制成的要好;并且在同样的功能下采用磁控溅射技术制得的可以比采用其他技术制得的要厚。
因此, 磁控溅射技术在许多应用领域涉及制造硬的、抗磨损的、低摩擦的、抗腐蚀的、装潢的以及光电学薄膜等方面具有重要是影响。
磁控溅射技术得以广泛的应用,是由该技术有别于其它镀膜方法的特点所决定的。
其特点可归纳为:可制备成靶材的各种材料均可作为薄膜材料,涉及各种金属、半导体、铁磁材料,以及绝缘的氧化物、陶瓷等物质,特别适合高熔点和低蒸汽压的材料沉积镀膜在适当条件下多元靶材共溅射方式,可沉积所需组分的混合物、化合物薄膜;在溅射的放电气中加入氧、氮或其它活性气体,可沉积形成靶材物质与气体分子的化合物薄膜;控制真空室中的气压、溅射功率,基本上可获得稳定的沉积速率,通过精确地控制溅射镀膜时间,容易获得均匀的高精度的膜厚,且反复性好;溅射粒子几乎不受重力影响,靶材与基片位置可自由安排;基片与膜的附着强度是一般蒸镀膜的10倍以上,且由于溅射粒子带有高能量,在成膜面会继续表面扩散而得到硬且致密的薄膜,同时高能量使基片只要较低的温度即可得到结晶膜;薄膜形成初期成核密度高,故可生产厚度10nm以下的极薄连续膜。
1.磁控溅射工作原理:磁控溅射属于辉光放电范畴, 运用阴极溅射原理进行镀膜。
膜层粒子来源于辉光放电中, 氩离子对阴极靶材产生的阴极溅射作用。
氩离子将靶材原子溅射下来后,沉积到元件表面形成所需膜层。
磁控原理就是采用正交电磁场的特殊分布控制电场中的电子运动轨迹, 使得电子在正交电磁场中变成了摆线运动, 因而大大增长了与气体分子碰撞的几率。
用高能粒子(大多数是由电场加速的气体正离子)撞击固体表面(靶), 使固体原子(分子)从表面射出的现象称为溅射。
热处理中的磁控溅射热处理技术
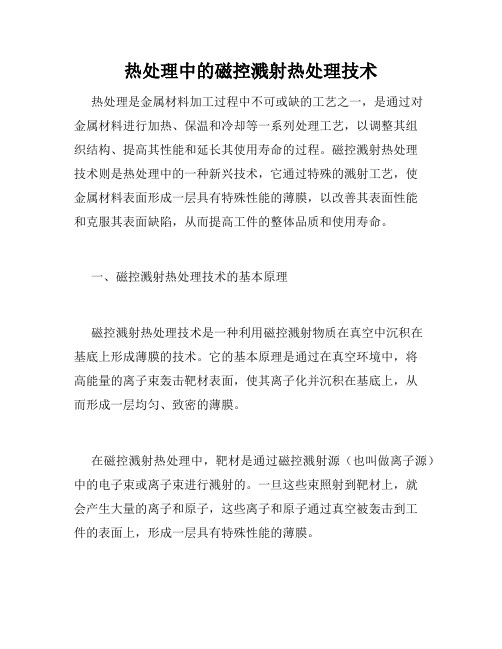
热处理中的磁控溅射热处理技术热处理是金属材料加工过程中不可或缺的工艺之一,是通过对金属材料进行加热、保温和冷却等一系列处理工艺,以调整其组织结构、提高其性能和延长其使用寿命的过程。
磁控溅射热处理技术则是热处理中的一种新兴技术,它通过特殊的溅射工艺,使金属材料表面形成一层具有特殊性能的薄膜,以改善其表面性能和克服其表面缺陷,从而提高工件的整体品质和使用寿命。
一、磁控溅射热处理技术的基本原理磁控溅射热处理技术是一种利用磁控溅射物质在真空中沉积在基底上形成薄膜的技术。
它的基本原理是通过在真空环境中,将高能量的离子束轰击靶材表面,使其离子化并沉积在基底上,从而形成一层均匀、致密的薄膜。
在磁控溅射热处理中,靶材是通过磁控溅射源(也叫做离子源)中的电子束或离子束进行溅射的。
一旦这些束照射到靶材上,就会产生大量的离子和原子,这些离子和原子通过真空被轰击到工件的表面上,形成一层具有特殊性能的薄膜。
二、磁控溅射热处理技术在金属材料中的应用磁控溅射热处理技术在金属材料中的应用非常广泛,主要体现在以下几个方面:1、表面强化处理:由于磁控溅射薄膜具有非常高的耐腐蚀性、耐磨性和耐热性等特点,在金属材料表面形成一层磁控溅射薄膜能够有效的提高其表面硬度和耐腐蚀性,从而延长金属材料的使用寿命。
2、强化焊接接头:磁控溅射技术还可以用于强化焊接接头,主要是通过在接头表面形成一层磁控溅射薄膜,从而改善焊接接头的力学性能和耐久性能。
在新能源汽车、航空航天、冶金等领域中的部分关键零部件都采用磁控溅射技术进行强化处理。
3、周期性复合薄膜:磁控溅射薄膜具有非常高的复合性能,能够形成优异的界面结构和相互补偿的性能,因此,在制备具有周期性复合结构薄膜方面有着卓越的应用前途。
例如,刀具表面复合结构膜制备、切削刃合金粉末材料复合表面膜制备等都运用到了磁控溅射技术。
三、磁控溅射热处理技术的优势与展望作为金属材料加工中的一种新兴技术,磁控溅射热处理技术拥有诸多优势,如下:1、非常适合高温材料的制备,例如Co-Ni-Cr-W-Al-Y的高温合金材料。
pvd磁控溅射原理

pvd磁控溅射原理PVD磁控溅射简介PVD磁控溅射(Physical Vapor Deposition Magnetron Sputtering)是一种常用的薄膜制备技术。
它能够在材料表面沉积一层精密、均匀的薄膜,具有广泛的应用领域。
原理PVD磁控溅射利用高能粒子撞击物质表面,使得物质从源材料蒸发、溅射并沉积在基底上。
以下是PVD磁控溅射的主要原理:1. 原始材料选择合适的源材料作为溅射靶材。
这些靶材通常是纯净且具有较高的密度,以保证沉积薄膜的质量。
2. 气氛控制通过调节气氛组成和压力来控制溅射过程中的气氛。
常用的气体有氩、氮等,其主要作用是保持反应室内的稳定环境。
3. 溅射过程在反应室内,将源材料靶材放置于阴极位置,并加上高压电源,形成磁场。
这个磁场激活了准直磁控电子束,使其环绕靶材运动。
电子束激发了靶材原子,使其脱离靶材并向基底表面运动。
4. 沉积薄膜溅射的源材料原子在运动过程中与基底表面相互冲击结合,形成薄膜沉积。
这些原子在基底表面形成结晶或非晶的薄膜结构。
应用PVD磁控溅射技术广泛应用于以下领域:•光电子学:制备光学薄膜,如反射层、透镜等。
•显示技术:用于制造液晶显示器、有机发光二极管(OLED)等。
•硬盘制造:用于制备磁性材料薄膜,如磁头、磁盘等。
•太阳能电池:制造多层薄膜太阳能电池。
•汽车工业:用于制备汽车玻璃涂层、汽车内部装饰等。
优缺点PVD磁控溅射技术具有以下优点和缺点:优点•薄膜均匀性好,可控性强。
•溅射速率可调节,适合制备不同厚度的薄膜。
•可制备多种材料薄膜,针对不同应用需求。
•薄膜在界面附着力强,具有较好的耐久性。
缺点•靶材利用率低,需定期更换。
•受制于靶材材料的限制,无法制备非金属或高熔点材料薄膜。
•沉积速率较慢,需要较长的时间。
综上所述,PVD磁控溅射技术是一种重要的薄膜制备方法。
它在各个领域都有广泛的应用,并呈现出许多独特的优点。
随着科学技术的不断发展,PVD磁控溅射技术将在未来发挥更大的作用。
磁控溅射技术

磁控溅射技术磁控溅射技术(MagnetronSputtering)是一种工艺技术,它可以将物质的激素部分转化成独立的离子,并将其射射到待涂层物体表面上,从而使得涂层物体表面形成一层薄膜。
磁控溅射技术被广泛应用于光学、电子、机械设备、制药设备、光通信等行业,是当今高科技领域研发设计的重要手段之一。
磁控溅射技术原理磁控溅射技术是一种将原子或分子能量值降低,使其出现球形高电荷状态,再以特殊的磁场配合电磁场,使之发出离子流,再将其射向待涂层物体表面,从而形成薄膜的一种物理沉积技术。
磁控溅射通常使用氩气或其它气体作为原料,采用高频电源充电,直流源来作用在特殊的磁场之中,形成电磁场作用于放电管内,使空气中的氩气分子离子化,形成加速离子,经过磁场的钙卡位作用,在被涂层表面上沉积成为薄膜。
磁控溅射技术优势磁控溅射技术具有诸多优势,其中最重要的优势是它可以生产出高精度涂层,涂层形貌相对较好,表面粗糙度低,具有良好的界面结构,在结构上可以产生变形和裂缝,从而改善其性能。
另外,由于磁控溅射技术本身的特性,它可以有效的改善层间的粗糙度、表面粗糙度等,使其表面进一步得到改善,从而提高涂层膜的性能。
此外,磁控溅射技术具有操作简单、速度快、改善特性及低成本等优势。
磁控溅射技术的应用磁控溅射技术在当今社会的应用十分广泛,它可以用于制造射频集成电路、宽带光缆、光学组件等电子元件,以及滤光片、反光镜、薄膜开关等光电子器件等。
此外,磁控溅射技术还可用于制造高性能的压电器件、高性能的催化剂和特殊材料等。
磁控溅射技术还可以用于核壳结构和整体结构的复合材料涂层,以及空间舱体、大型塔台等涂装,使其具备良好的抗腐蚀性、绝缘性以及机械特性等特性。
结论磁控溅射技术是一种物理沉积技术,其原理是形成一种电磁场作用于放电管,使其出现高电荷状态,然后形成加速离子,最后将其射向待涂层物体表面,从而形成薄膜。
磁控溅射技术具有生产高精度涂层、良好的表面粗糙度,改善特性及低成本等优势,在光学、电子、机械设备、制药设备以及光通信领域有着广泛的应用,是一项重要的技术。
磁控溅射仪的缺点调研2
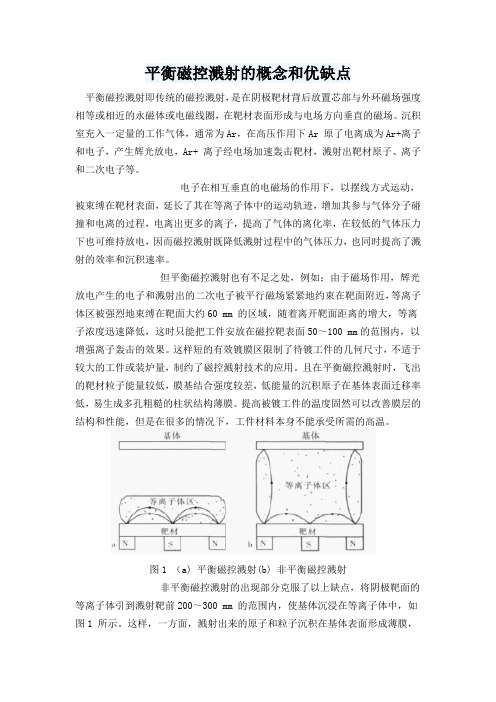
平衡磁控溅射的概念和优缺点平衡磁控溅射即传统的磁控溅射,是在阴极靶材背后放置芯部与外环磁场强度相等或相近的永磁体或电磁线圈,在靶材表面形成与电场方向垂直的磁场。
沉积室充入一定量的工作气体,通常为Ar,在高压作用下Ar 原了电离成为Ar+离子和电子,产生辉光放电,Ar+ 离子经电场加速轰击靶材,溅射出靶材原子、离子和二次电子等。
电子在相互垂直的电磁场的作用下,以摆线方式运动,被束缚在靶材表面,延长了其在等离子体中的运动轨迹,增加其参与气体分子碰撞和电离的过程,电离出更多的离子,提高了气体的离化率,在较低的气体压力下也可维持放电,因而磁控溅射既降低溅射过程中的气体压力,也同时提高了溅射的效率和沉积速率。
但平衡磁控溅射也有不足之处,例如:由于磁场作用,辉光放电产生的电子和溅射出的二次电子被平行磁场紧紧地约束在靶面附近,等离子体区被强烈地束缚在靶面大约60 mm 的区域,随着离开靶面距离的增大,等离子浓度迅速降低,这时只能把工件安放在磁控靶表面50~100 mm的范围内,以增强离子轰击的效果。
这样短的有效镀膜区限制了待镀工件的几何尺寸,不适于较大的工件或装炉量,制约了磁控溅射技术的应用。
且在平衡磁控溅射时,飞出的靶材粒子能量较低,膜基结合强度较差,低能量的沉积原子在基体表面迁移率低,易生成多孔粗糙的柱状结构薄膜。
提高被镀工件的温度固然可以改善膜层的结构和性能,但是在很多的情况下,工件材料本身不能承受所需的高温。
图1 (a) 平衡磁控溅射(b) 非平衡磁控溅射非平衡磁控溅射的出现部分克服了以上缺点,将阴极靶面的等离子体引到溅射靶前200~300 mm 的范围内,使基体沉浸在等离子体中,如图1 所示。
这样,一方面,溅射出来的原子和粒子沉积在基体表面形成薄膜,另一方面,等离子体以一定的能量轰击基体,起到离子束辅助沉积的作用,大大的改善了膜层的质量。
磁控溅射技术及其应用

•
•
•
三、磁控溅射镀膜技术发展
3、反应磁控溅射技术
• 靶中毒:迟滞现象使反应气体与靶材作用生成的化合物覆盖在靶材表面,积 累大量的正电荷无法中和,在靶材表面建立越来越高的正电位,阴极位降区 的电位随之降低,最终阴极位降区电位降减小到零,放电熄灭,溅射停止, 这种现象称为靶中毒。 • 打弧:当靶材表面化合物层电位足够高时,进而发生击穿,巨大的电流流过 击穿点,形成弧光放电,导致局部靶面瞬间被加热到很高的温度,发生喷射
可以制备成靶材。磁控溅射镀膜在相互垂直的磁场和电场的双重作用
下,沉积速度快,膜层致密且与基片附着性好,非常适合于大批量且高 效率的工业化生产。
二、磁控溅射镀膜技术原理
2、磁控溅射技术
• 磁控溅射的工作原理是在辉光放电 的两极之间引入磁场,电子受电场 加速作用的同时受到磁场的束缚作 用,运动轨迹成摆线,增加了电子
三、磁控溅射镀膜技术发展
5、脉冲磁控溅射技术
• 脉冲磁控溅射是采用矩形波电压的脉冲电源
代替传统直流电源进行磁控溅射沉积。脉冲
磁控溅射技术可以有效的抑制电弧产生进而 消除由此产生的薄膜缺陷,同时可以提高溅 射沉积速率,降低沉积温度等一系列显著优
点。
• 脉冲可分为双向脉冲和单向脉冲。双向脉冲 在一个周期内存在正电压和负电压两个阶段 ,在负电压段,电源工作于靶材的溅射,正
射的同时,阳极靶完成表面清洁,
如此周期性地变换磁控靶极性,就 产生了“自清洁”效应。
四、磁控溅射镀膜技术的发展
6、磁控溅射新发展
•
高速溅射:高速溅射能够实现高速率沉积,可以缩短溅射镀膜的时间,提高 工业生产的效率;有可能替代目前对环境有污染的电镀工艺。
•
自溅射:当溅射率非常高,以至于在完全没有惰性气体的情况下也能维持放 电,即是仅用离化的被溅射材料的蒸汽来维持放电,这种磁控溅射被称为自 溅射。被溅射材料的离子化以及减少甚至取消惰性气体,会明显地影响薄膜 形成的机制,加强沉积薄膜过程中合金化和化合物形成中的化学反应。由此 可能制备出新的薄膜材料,发展新的溅射技术,例如在深孔底部自溅射沉积 薄膜。
磁控溅射技术

磁控溅射技术
磁控溅射技术(MagnetronSputtering)是一种应用广泛的凝膜
技术,它利用磁控来控制溅射过程以形成薄膜。
它主要用于无机和有机薄膜制备,这是由冷却通道技术和室温技术支持的。
磁控溅射技术可用于制备压电,磁性,光学,光电,绝缘,热电和磁性薄膜等功能的材料。
磁控溅射技术的基本原理是利用一个电磁场来极化溅射流体中
的粒子,这样就可以保证溅射流体中的粒子被准确地导向衬底表面,有效控制薄膜的厚度,表面形貌和发射谱。
它主要应用于溅射池,用作源材料,溅射膜或衬底表面,也可以利用它来制备特殊效应膜,如调制器晶元,表面定向膜,孔道膜等。
由于磁控技术能够准确控制粒子的导向,因此可以用来制备金属,金属氧化物,复合膜,碳化物膜等多种膜材料。
磁控溅射技术与传统的非磁控技术相比,具有许多优势。
首先,磁控技术可以更好地控制溅射过程,从而减少溅射过程中的凝聚态粒子。
此外,振荡电场和磁场可以减少衬底表面上的热效应,使衬底表面更加平滑,从而改善薄膜的物理性能。
此外,磁控技术不仅可以为膜材料制备提供精确的控制,而且可以用来控制不同衬底表面的溅射,不仅可以形成多层膜,还可以形成立体结构的膜。
除了上述优点之外,磁控技术还具有一些有点。
因为薄膜溅射一般会受到溅射池内粒子数量的限制,因此当溅射一个特定厚度的膜时,
磁控技术会受到溅射池内粒子数量的限制,从而会影响薄膜的质量。
此外,磁控技术的设备成本也较高,而且有时会受到磁场的影响而产生失效。
总之,磁控溅射技术是一种能够有效控制溅射过程,准确制备功能材料的一种技术,它的应用范围一直在扩大,已经广泛应用于无机和有机膜材料的制备。
直流磁控溅射和射频磁控溅射的异同点

直流磁控溅射和射频磁控溅射的异同点示例文章篇一:哎呀,亲爱的朋友们,你们知道什么是直流磁控溅射和射频磁控溅射吗?哈哈,一开始我也不太懂呢!不过经过一番学习和研究,我现在可算是有点明白啦!咱们先来说说直流磁控溅射吧。
直流磁控溅射就像是一个超级大力士,能把材料强有力地溅射到目标表面。
它工作的时候呀,就好像是一个勇敢的战士,勇往直前,毫不退缩。
比如说,在制造金属薄膜的时候,直流磁控溅射那可是大显身手。
它能够让金属原子快速地、大量地跑到要镀膜的地方去。
“那射频磁控溅射又是什么样的呢?”你们可能会这样问。
嘿嘿,射频磁控溅射就像是一个灵活的小精灵。
它可不像直流磁控溅射那样只能处理导电的材料,它连那些不导电的材料也能搞定!这是不是很神奇?就好比咱们做手工,直流磁控溅射可能只能用特定的工具,而射频磁控溅射就像是拥有一个装满各种工具的百宝箱,不管什么材料都能应对自如。
那它们到底有啥不一样呢?直流磁控溅射处理导电材料很厉害,但是一碰到不导电的,它就没辙啦。
射频磁控溅射呢,不管导电不导电,它都能轻松应对。
还有啊,它们在能量利用上也有差别。
直流磁控溅射就像是个直性子,能量用起来比较直接,射频磁控溅射则更像是个心思细腻的小伙伴,能量运用得更加巧妙。
“那到底哪个更好呢?”其实呀,这可没有绝对的答案。
得看具体的情况。
如果只是处理导电材料,那直流磁控溅射可能就够了,又快又有效。
但要是遇到不导电的材料,那还得靠射频磁控溅射出马。
所以说,直流磁控溅射和射频磁控溅射都有自己的本领,就看我们在什么情况下需要它们来大显身手啦!总之,这两种溅射方法各有各的特点和优势,我们要根据实际需求来选择,才能达到最好的效果哟!示例文章篇二:哇塞!同学们,你们知道吗?今天老师给我们讲了直流磁控溅射和射频磁控溅射,这可太有意思啦!咱们先来说说直流磁控溅射吧。
就好像我们跑步,一直朝着一个方向使劲跑,直流磁控溅射里的电流啊,就像这样一直朝着一个方向流动。
你说神奇不神奇?那射频磁控溅射又是咋回事呢?这就好比我们跳绳,绳子一会儿上一会儿下,电流也是这样来回变化的哟!直流磁控溅射的优点可不少呢!它就像个大力士,干活儿特别有力气,效率高,能快速地把材料溅射到我们想要的地方。
磁控溅射技术

磁控溅射技术
磁控溅射技术是一种用于微纳米特征工艺分析的技术,在近年来得到了广泛应用。
该
技术是基于半导体表面放电原理,通过磁场控制机构,利用低功耗高频电流从模拟电源,
从而产生来自放电点的溅射。
磁控溅射技术的溅射比传统的激光刻蚀技术具有更多的优势,如灵活性高、机械结构
简单、成本低廉、运行灵敏度高、确保模板准确性能高等优点。
磁控溅射技术的控制简单,开关电源可以在不同的工艺步骤精确控制可变的放电电压和时延,这有利于微纳米特征的
精准制作。
磁控溅射技术可以用于波导、光改良器、外观设计、芯片铁电存储器等半导体设计工
艺及相关材料技术研究领域,可实现大型化、灵敏度提升、电器结构设计及集成结构改变
现有应用。
磁控溅射技术可以实现层之间的特定位置的放电,这是激光刻蚀技术无法实现的,磁
控溅射技术具有更小的辐射范围,更平均的放电量、更少的热变形和功率损耗,从而更有
效地改进半导体表面上的尺寸和形貌。
磁控溅射技术有助于维持深沟微型元件、半导体晶体管、电阻器、开关或TFT晶体管
上的3D结构特征,而芯片的可靠性也因此受益,其它一些元件的三维特征也可以通过磁
控溅射技术实现,如细节的表面缺陷、沉积等表面成形技术。
由于磁控溅射技术具有灵活性高,机械结构简单,成本低,运行灵敏度高,确保模板
准确性高等优点,因此在半导体特征分析、特征形貌改变、细节处理和尺寸控制等应用方
面受到广泛关注和使用。
磁控溅射技术可以实现精确和快速的特征制作,从而可以大大提
升工作效率和产品质量。
磁控溅射工艺技术

磁控溅射工艺技术磁控溅射工艺技术是一种常用的薄膜制备技术。
它通过使用磁场来控制离子轰击靶材,使其产生高速的离子撞击薄膜材料表面,将薄膜材料从靶材上溅射下来,形成均匀且致密的薄膜。
磁控溅射工艺技术具有许多优点。
首先,由于离子束的高速撞击,磁控溅射能产生高质量的薄膜,具有较好的致密性和纯度,适用于多种薄膜应用,如光学薄膜、电子器件薄膜、装饰薄膜等。
其次,磁控溅射可以制备较厚的薄膜,较常用的物理气相沉积技术能制备更厚的薄膜,使其应用范围更广泛。
此外,磁控溅射具有较高的反应速率和较短的加工时间,提高了工艺的效率。
同时,磁控溅射工艺技术可以在大范围内调节薄膜成分,可以制备多层膜以及合金薄膜,满足不同应用的需求。
关于磁控溅射工艺技术的具体流程,首先需要准备靶材和基底材料。
靶材是要溅射的原材料,可以是金属、合金、氧化物等,而基底材料是要涂覆薄膜的表面。
然后,将靶材和基底装入溅射腔室,创建真空环境,并加入惰性气体,如氩气作为溅射介质。
接下来,加入高频电源和磁控源,产生磁场,通过调节参数和气压,控制离子的能量和方向。
当离子撞击靶材时,靶材表面的原子会被撞击下来,形成蒸汽和离子。
蒸汽和离子会沉积在基底上,形成均匀且致密的薄膜。
溅射过程中,还可以通过旋转靶材和基底来实现均匀溅射。
最后,经过一段时间的溅射,薄膜达到一定厚度后,工艺结束,可取下基底材料,制备成薄膜器件。
然而,磁控溅射工艺技术也存在一些问题。
首先,溅射过程中会产生较高的温度,可能导致靶材损伤或薄膜质量变差。
此外,溅射靶材的选取和制备对薄膜质量至关重要,需要进行一定的实验和优化。
总之,磁控溅射工艺技术是一种重要的薄膜制备技术,具有广泛的应用前景。
随着科技的不断发展,磁控溅射工艺技术也在不断进步和完善,为各行业的研究和生产提供了强大的支持。
磁控溅射的基本原理
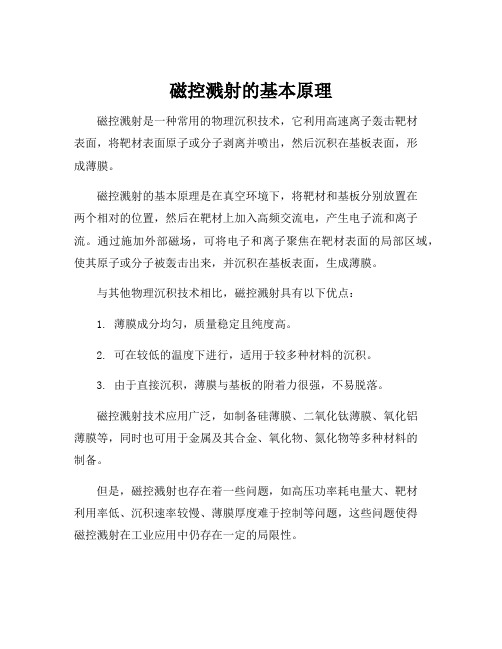
磁控溅射的基本原理
磁控溅射是一种常用的物理沉积技术,它利用高速离子轰击靶材
表面,将靶材表面原子或分子剥离并喷出,然后沉积在基板表面,形
成薄膜。
磁控溅射的基本原理是在真空环境下,将靶材和基板分别放置在
两个相对的位置,然后在靶材上加入高频交流电,产生电子流和离子流。
通过施加外部磁场,可将电子和离子聚焦在靶材表面的局部区域,使其原子或分子被轰击出来,并沉积在基板表面,生成薄膜。
与其他物理沉积技术相比,磁控溅射具有以下优点:
1. 薄膜成分均匀,质量稳定且纯度高。
2. 可在较低的温度下进行,适用于较多种材料的沉积。
3. 由于直接沉积,薄膜与基板的附着力很强,不易脱落。
磁控溅射技术应用广泛,如制备硅薄膜、二氧化钛薄膜、氧化铝
薄膜等,同时也可用于金属及其合金、氧化物、氮化物等多种材料的
制备。
但是,磁控溅射也存在着一些问题,如高压功率耗电量大、靶材
利用率低、沉积速率较慢、薄膜厚度难于控制等问题,这些问题使得
磁控溅射在工业应用中仍存在一定的局限性。
因此,在实际应用中,需要根据不同需求选择合适的沉积技术,以达到最好的效果。
同时,磁控溅射技术的不断改进也将为其更广泛的应用提供更多可能性。
磁控溅射 成本
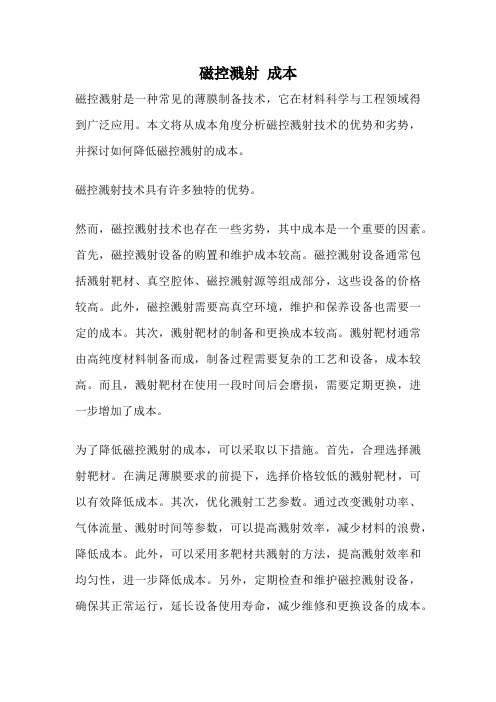
磁控溅射成本
磁控溅射是一种常见的薄膜制备技术,它在材料科学与工程领域得到广泛应用。
本文将从成本角度分析磁控溅射技术的优势和劣势,并探讨如何降低磁控溅射的成本。
磁控溅射技术具有许多独特的优势。
然而,磁控溅射技术也存在一些劣势,其中成本是一个重要的因素。
首先,磁控溅射设备的购置和维护成本较高。
磁控溅射设备通常包括溅射靶材、真空腔体、磁控溅射源等组成部分,这些设备的价格较高。
此外,磁控溅射需要高真空环境,维护和保养设备也需要一定的成本。
其次,溅射靶材的制备和更换成本较高。
溅射靶材通常由高纯度材料制备而成,制备过程需要复杂的工艺和设备,成本较高。
而且,溅射靶材在使用一段时间后会磨损,需要定期更换,进一步增加了成本。
为了降低磁控溅射的成本,可以采取以下措施。
首先,合理选择溅射靶材。
在满足薄膜要求的前提下,选择价格较低的溅射靶材,可以有效降低成本。
其次,优化溅射工艺参数。
通过改变溅射功率、气体流量、溅射时间等参数,可以提高溅射效率,减少材料的浪费,降低成本。
此外,可以采用多靶材共溅射的方法,提高溅射效率和均匀性,进一步降低成本。
另外,定期检查和维护磁控溅射设备,确保其正常运行,延长设备使用寿命,减少维修和更换设备的成本。
磁控溅射是一种常见的薄膜制备技术,具有许多优势和劣势。
成本是影响磁控溅射技术应用的重要因素之一。
为了降低磁控溅射的成本,可以选择合适的溅射靶材、优化溅射工艺参数,以及定期检查和维护设备。
通过这些措施,可以在保证薄膜质量的前提下,有效降低磁控溅射的成本,促进该技术的应用和推广。
磁控溅射制备氧化铝薄膜及其设备开发

磁控溅射制备氧化铝薄膜及其设备开发磁控溅射是一种目前广泛应用于制备氧化铝薄膜的技术。
该技术不仅能够制备均匀、高质量的氧化铝薄膜,而且还可以对薄膜的物理性质进行调节,满足不同应用的需求。
本文将介绍磁控溅射制备氧化铝薄膜的原理、优势以及设备开发的关键技术。
一、磁控溅射制备氧化铝薄膜的原理磁控溅射是一种利用高能离子轰击固体材料表面来制备薄膜的技术。
其基本原理是,在低压气体环境中,利用磁控电弧等方式将金属或合金材料的表面离子化,然后让这些离子在外场的作用下沿着一定方向均匀地射向衬底,在衬底上形成薄膜。
以氧化铝薄膜为例,磁控溅射制备过程中,首先要准备具有良好导电性能的氧化铝靶材。
然后,在氩气等的惰性气体环境下,通过磁控电弧等方式将靶材表面的原子离子化,形成铝离子和氧离子。
这些离子在外场的作用下均匀地沉积在附近的衬底上,形成一层均匀的氧化铝薄膜。
整个制备过程可以通过改变各种参数来控制薄膜的厚度、结构和物理性质。
二、磁控溅射制备氧化铝薄膜的优势相比于其他薄膜制备技术,磁控溅射制备氧化铝薄膜具有以下优势:1. 薄膜均匀性好。
磁控溅射制备过程中,离子在外场的作用下沿着一定方向均匀地射向衬底,因此制备的氧化铝薄膜具有良好的均匀性。
2. 薄膜的物理性质可调节。
制备氧化铝薄膜时,可以通过改变各种参数,如离子能量、衬底温度等,来调节薄膜的物理性质。
因此可以得到不同性质的氧化铝薄膜,满足不同应用的需求。
3. 制备过程简单、易于自动化。
磁控溅射制备氧化铝薄膜的制备过程较为简单,且不需要高温高压,对于薄膜材料及衬底材料也有较广的适应性。
同时,由于其制备过程较为稳定,可以进行自动化控制。
三、磁控溅射制备氧化铝薄膜设备的关键技术磁控溅射制备氧化铝薄膜的设备主要由靶材、离子源、外场源(磁场等)和衬底等构成。
因此,设备的关键技术主要包括:1. 靶材的选择。
靶材的选择对于制备氧化铝薄膜至关重要。
一方面,靶材的纯度和制备过程中的气氛会影响薄膜的质量;另一方面,靶材的导电性能也会影响离子化的效率。
金属磁控溅射技术研究报告
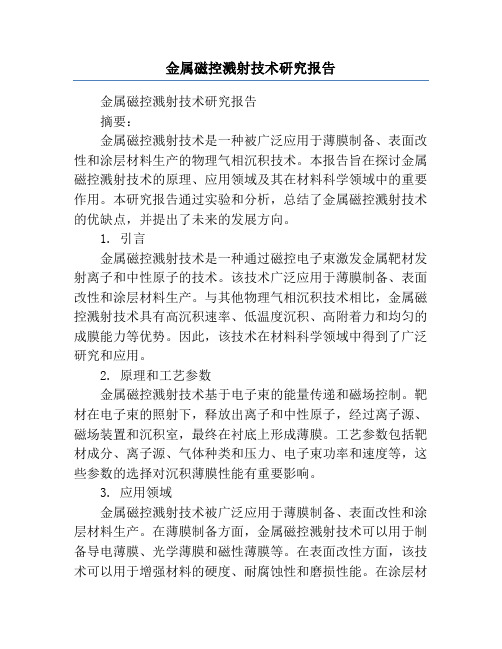
金属磁控溅射技术研究报告金属磁控溅射技术研究报告摘要:金属磁控溅射技术是一种被广泛应用于薄膜制备、表面改性和涂层材料生产的物理气相沉积技术。
本报告旨在探讨金属磁控溅射技术的原理、应用领域及其在材料科学领域中的重要作用。
本研究报告通过实验和分析,总结了金属磁控溅射技术的优缺点,并提出了未来的发展方向。
1. 引言金属磁控溅射技术是一种通过磁控电子束激发金属靶材发射离子和中性原子的技术。
该技术广泛应用于薄膜制备、表面改性和涂层材料生产。
与其他物理气相沉积技术相比,金属磁控溅射技术具有高沉积速率、低温度沉积、高附着力和均匀的成膜能力等优势。
因此,该技术在材料科学领域中得到了广泛研究和应用。
2. 原理和工艺参数金属磁控溅射技术基于电子束的能量传递和磁场控制。
靶材在电子束的照射下,释放出离子和中性原子,经过离子源、磁场装置和沉积室,最终在衬底上形成薄膜。
工艺参数包括靶材成分、离子源、气体种类和压力、电子束功率和速度等,这些参数的选择对沉积薄膜性能有重要影响。
3. 应用领域金属磁控溅射技术被广泛应用于薄膜制备、表面改性和涂层材料生产。
在薄膜制备方面,金属磁控溅射技术可以用于制备导电薄膜、光学薄膜和磁性薄膜等。
在表面改性方面,该技术可以用于增强材料的硬度、耐腐蚀性和磨损性能。
在涂层材料生产方面,金属磁控溅射技术可以用于生产防腐涂层、摩擦材料和生物医学用材料等。
4. 优缺点分析金属磁控溅射技术具有高沉积速率、低温度沉积、高附着力和均匀的成膜能力等优点。
然而,该技术也存在一些缺点,例如对靶材的资源消耗较大、沉积过程中的离子束散射和沉积杂质的增加等。
对于这些问题,我们可以通过改进设备和工艺来降低其影响。
5. 未来发展方向为了进一步应对金属磁控溅射技术的挑战,未来的研究可以从以下几个方面展开。
首先,可以改进靶材的设计和制备,以提高资源利用率。
其次,可以优化工艺参数的选择,以减少离子束的散射和沉积杂质的增加。
最后,可以结合其他物理气相沉积技术,探索新的复合材料和结构材料的制备方法。
二氧化硅磁控溅射镀膜

二氧化硅磁控溅射镀膜
首先,让我们从工艺原理方面来看。
磁控溅射是一种利用磁场
控制等离子体的溅射技术,通过在真空室中加入惰性气体(如氩气)并施加高频电场,使得靶材表面的原子被激发并溅射到基板表面上,形成薄膜。
而二氧化硅作为靶材,则会在这个过程中被溅射到基板
表面上,形成二氧化硅薄膜。
其次,我们可以从应用领域来看。
二氧化硅薄膜具有良好的光
学性能和化学稳定性,因此在光学薄膜领域应用广泛,比如制备反
射膜、抗反射膜等。
同时,在电子器件领域,二氧化硅薄膜也常用
于制备绝缘层或介质层。
此外,二氧化硅薄膜还可以用于生物医学
领域,比如制备生物传感器等。
然后,让我们从优点和局限性来看。
磁控溅射镀膜技术具有沉
积速度快、薄膜致密性好、成膜均匀等优点,能够制备高质量的薄膜。
然而,这种技术也存在着设备复杂、成本较高、靶材利用率低
等局限性。
最后,让我们从发展趋势来看。
随着材料科学和工艺技术的不
断发展,磁控溅射镀膜技术也在不断改进和完善,比如引入多靶材
联合溅射、优化工艺参数等,以提高薄膜的性能和降低成本。
同时,磁控溅射镀膜技术也在向微纳米尺度发展,以满足微纳电子器件和
光学器件对薄膜质量和加工精度的要求。
综上所述,二氧化硅磁控溅射镀膜技术具有广泛的应用前景和
发展空间,但同时也需要不断改进和创新,以适应不同领域对薄膜
性能和加工工艺的需求。
磁控溅射工艺用处

磁控溅射工艺用处
磁控溅射是一种物理气相沉积技术,它利用磁场控制等离子体中的电子运动,使其在靶材表面产生溅射效应,从而将靶材原子或分子沉积到基材表面形成薄膜。
这种工艺具有许多优点,例如:
1. 制备的薄膜具有高纯度、高密度、高附着力和良好的结晶性能。
2. 可以在低温下进行,避免了高温对基材的损伤。
3. 可以控制薄膜的厚度、组成和结构,实现对薄膜性能的精确调控。
4. 适用于制备各种材料的薄膜,如金属、合金、半导体、氧化物等。
因此,磁控溅射工艺被广泛应用于许多领域,例如:
1. 电子学:用于制备集成电路、半导体器件、太阳能电池等。
2. 光学:用于制备光学薄膜、反射镜、滤光片等。
3. 机械工程:用于制备耐磨涂层、防腐涂层、超导材料等。
4. 生物医学:用于制备生物传感器、药物释放系统等。
总的来说,磁控溅射工艺是一种非常重要的薄膜制备技术,它的应用领域非常广泛,对于现代科技的发展起到了重要的推动作用。
浅析磁控溅射镀膜中旋转阴极的优缺点

浅析磁控溅射镀膜中旋转阴极的优缺点黄新盈深圳市微普诺薄膜技术有限公司(0755‐26451949)磁控溅射旋转阴极在现今大面积玻璃镀膜中广泛采用,与平面阴极相比,各有其优缺点。
本文尝试对旋转阴极的优缺点进行以下分析。
旋转阴极的优点主要有以下几点:1 靶材利用率高,可达90%。
同时也意味着更长的运行时间。
2 溅射速率高(通常是平面阴极的2‐3倍,具体视靶材种类而定)。
3 有效减少打弧和靶面掉渣,工艺稳定性好。
可以消除平面靶较易形成的再沉积区,这些被污染的靶面,极易产生掉渣然后落到玻璃基板上。
同样这些地方很容易产生打弧,打弧又造成了更多掉渣和大颗粒的形成。
所以旋转阴极消除了再沉积区,从而保证了镀膜工艺的长期稳定性。
4 无需“烧靶”,可以节省靶材消耗和烧靶时间。
5 快速便捷的换靶操作,在某些设计简捷的旋转阴极上可以实现,如美国SCI公司等。
这对配备多个旋转阴极的镀膜生产线特别有意义,节省时间意味着产能的提升。
6 低熔点靶材亦能使用高功率溅射(包括所以材料)。
因为靶材旋转,所以靶面没有一直处于等离子体区内,使溅射速率得以提高。
7 旋转靶材比平面靶材更加昂贵,但其极高的靶材利用率使得旋转靶的性价比更好。
而旋转阴极的缺点主要是:1 旋转阴极更加复杂,需要更多部件,需要驱动系统配合。
所以最初的设备投资要高于平面阴极。
2 旋转阴极有移动部件,生产中真空密封不时会有泄漏,即便是成熟的旋转阴极,能够可以做到简单,最小程度的更换密封,但相比平面阴极而言,仍需要更高的维护成本。
3 旋转阴极增加了系统中的不稳定因素,因为在生产中需要不停的旋转。
结论旋转阴极在大面积玻璃镀膜工业中,特别是Low‐e镀膜中扮演了重要的脚色。
因为旋转阴极解决了平面阴极掉渣和靶材利用率的问题,并且提高了溅射速率。
但虽之而来的是增加了阴极机构的复杂性和初期投资。
旋转阴极所带来的好处将在后续的长期生产得到充分体现。
至于靶材成本,需要分别比较分析每种靶材的制造成本,利用率,回收价值…等因素来综合考虑。
磁控溅射技术的原理及应用

磁控溅射技术的原理及应用磁控溅射技术是一种非常重要的材料加工技术,它在现代工业制造领域中被广泛应用。
磁控溅射技术的原理比较复杂,需要结合物理学知识和材料科学知识才能够深入理解。
下面,我们将从原理、应用和优缺点等方面来分析磁控溅射技术。
一、磁控溅射技术的原理磁控溅射技术的核心原理是,在高真空下,利用离子轰击的原理使靶材表面的原子或分子离开,形成高速运动的原子团,然后以高速度击打到所需要涂覆的材料表面,与另一组原子或分子相碰撞,并沉积成薄膜层。
磁控溅射技术的溅射源主要由靶材、基底和磁场组成。
当高纯度的气体在真空室内电离后,离子会在靶材表面束缚,形成一个带正电荷的等离子体潮流,进入强磁场的作用下,靶材上的非离子原子或分子就会沿用聚变的道理抛射出去,进而形成一个离子束,成为靶材的溅射。
当基底和溅射源靶材相对静止时,基底上的沉积物层就会开始形成。
因此,在磁控溅射技术中,溅射过程控制好磁场强度和靶材等离子体激发能量是非常重要的。
二、磁控溅射技术的应用磁控溅射技术的应用范围非常广泛,主要应用在金属、合金、半导体材料的表面修饰和通过涂层改善材料表面性能来达到特殊的功能和应用。
涂层厚度可从几纳米到数百纳米改变。
(1) 太阳能光伏在太阳能光伏中,磁控溅射技术被广泛应用。
可以通过沉积一层光谱选择层来增加光吸收,在应用中产生光电性能提高,并延长光电池的寿命。
此外,磁控溅射技术制备的透明导电电极,可以大幅提高太阳能电池的效率和环保性能。
(2) 光学加工磁控溅射技术用于光学加工领域。
可以制备一种极细的金属纤维单丝,这种金属纤维单丝可以做为微型光学的部件,如光纤中介面。
纤维自身具有一定的弯曲、拉伸和扭曲能力,便于融合和加工成三维微机械结构,做成微型光学元件、微型透镜和扫描电子显微镜等。
(3) 电子和半导体技术磁控溅射技术可以制备各种电子和半导体材料,例如氧化物、铜铝金属等等。
在半导体器件和电子元件中使用磁控溅射技术,可以获得高精度和超薄膜的电池、LED、CRT以及开关电源等电子元件。
- 1、下载文档前请自行甄别文档内容的完整性,平台不提供额外的编辑、内容补充、找答案等附加服务。
- 2、"仅部分预览"的文档,不可在线预览部分如存在完整性等问题,可反馈申请退款(可完整预览的文档不适用该条件!)。
- 3、如文档侵犯您的权益,请联系客服反馈,我们会尽快为您处理(人工客服工作时间:9:00-18:30)。
磁控溅射技术优缺点
磁控溅射自问世后就获得了迅速的发展和广泛的应用,有力地冲击了其它镀膜方法的地位,主要是由它以下的优点决定的:
1、沉积速度快、基材温升低、对膜层的损伤小;
2、对于大部分材料,只要能制成耙材,就可以实现溅射;
3、溅射所获得的薄膜与基片结合较好;
4、溅射所获得的薄膜纯度高、致密性好、成膜均匀性好;
5、溅射工艺可重复性好,可以在大面积基片上获得厚度均匀的薄膜;
6、能够精确控制镀层的厚度,同时可通过改变参数条件控制组成薄膜的颗粒大小;
7、不同的金属、合金、氧化物能够进行混合,同时溅射于基材上;
8、易于实现工业化。
但磁控溅射也存在着一些问题,主要有:
1、磁控溅射所利用的环状磁场迫使二次电子跳栏式地沿着环状磁场转圈。
相应地,环状磁场控制的区域是等离子体密度最高的部位。
在磁控溅射时,可以看见溅射气体——氩气在这部位发出强烈的淡蓝色辉光,形成一个光环。
处于光环下的靶材是被离子轰击最严重的部位,会溅射出一条环状的沟槽。
环状磁场是电子运动的轨道,环状的辉光和沟槽将其形象地表现了出来。
磁控溅射靶的溅射沟槽一旦穿透靶材,就会导致整块靶材报废,所以靶材的利用率不高,一般低于40%;
2、等离子体不稳定;
3、不能实现强磁性材料的低温高速溅射,因为几乎所有的磁通都通不过磁性靶子,所以在靶面附近不能加外加强磁场。