曲轴油孔加工过程中的问题及解决措施
4E系列柴油机曲轴和轴瓦早期故障控制

对导致 曲轴轴瓦早期 出现的故障进行 了分
析 :曲轴油孔倒角 、机体披锋 、机体 、机油冷
以此为标记把关 ,同时规定 :每一工序没有装完一台机时不
能离 开现 场 。
层 灰尘 ,抽 检装 机前 的机体 时会 发现 以上 部位有 不 干净现 象 ;机 油冷 却器是 机油 进入 主油 道前 的零件 ,没 有经 过机 滤 ,所 以机 油冷却器 一有杂物会 直接流 到曲轴与轴 瓦之 间 , 导致故障 。 轴瓦表 面有 异物。装配时 ,由于一些原 因,轴 瓦表面有
轴颈和连 杆颈 油孔倒角质量相差很大 ,我们 的
瓦 的早期故 障中,检查机体主油道披锋时就发 现在故 障机 中有去不干净 的,对这一问题 ,我 们通过控制好机体披锋 即控制好去披锋过程 的
参数一去披锋的 电流 、通 电时间和工装 的定期 检查和更换来控制 ,同时在机加工入库处和装
供应 商中 ,北方某供应 厂商提供 的曲轴倒 角质
且 质 量 人 员 要 作 好 规 定 内容 的 培 训 和 在 顶 岗 时 候 的重 点 监 控 。 其 次 每 年 都 有 一 些 新 的员 工 进 来 ,分 配 到 各 工 序 中 ,监
时有杂物 ,有的操作工用手去擦 ,手本身就 比较脏 ,越擦 越
脏 ,导致异 物直 接在曲轴轴瓦之间 ,造成故 障隐患 。出现故 障后 ,我们对这 几个 零件过程都进行 了严控 :对机体 除了对 以上部分重点控制外 ,还规定清洗后超一天不装机 的必须 重 新清洗 ,对其他 内部零件 洗好 后要马上拉到总成 区防尘较好
柴油机曲轴磨损原因分析与检查修理方法
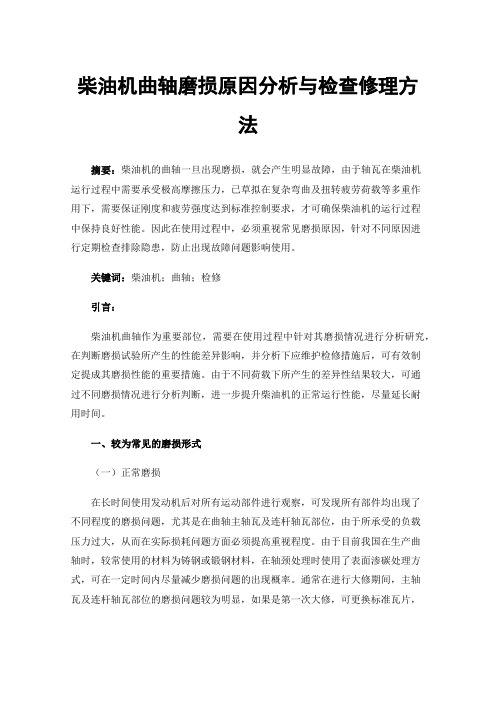
柴油机曲轴磨损原因分析与检查修理方法摘要:柴油机的曲轴一旦出现磨损,就会产生明显故障,由于轴瓦在柴油机运行过程中需要承受极高摩擦压力,已草拟在复杂弯曲及扭转疲劳荷载等多重作用下,需要保证刚度和疲劳强度达到标准控制要求,才可确保柴油机的运行过程中保持良好性能。
因此在使用过程中,必须重视常见磨损原因,针对不同原因进行定期检查排除隐患,防止出现故障问题影响使用。
关键词:柴油机;曲轴;检修引言:柴油机曲轴作为重要部位,需要在使用过程中针对其磨损情况进行分析研究,在判断磨损试验所产生的性能差异影响,并分析下应维护检修措施后,可有效制定提成其磨损性能的重要措施。
由于不同荷载下所产生的差异性结果较大,可通过不同磨损情况进行分析判断,进一步提升柴油机的正常运行性能,尽量延长耐用时间。
一、较为常见的磨损形式(一)正常磨损在长时间使用发动机后对所有运动部件进行观察,可发现所有部件均出现了不同程度的磨损问题,尤其是在曲轴主轴瓦及连杆轴瓦部位,由于所承受的负载压力过大,从而在实际损耗问题方面必须提高重视程度。
由于目前我国在生产曲轴时,较常使用的材料为铸钢或锻钢材料,在轴颈处理时使用了表面渗碳处理方式,可在一定时间内尽量减少磨损问题的出现概率。
通常在进行大修期间,主轴瓦及连杆轴瓦部位的磨损问题较为明显,如果是第一次大修,可更换标准瓦片,而第二次及第三次大修时,可磨削曲轴变更换加大轴瓦等方式进行处理,都可起到配合间隙的作用。
(二)异常磨损这种情况的出现表现为柴油机运转过程中突然发生故障,而实际运行时间并未达到大修期限。
在对此情况进行检查时可发现,较为常见的形成原因中,主要是由于污物影响润滑油或瓦片合金层脱落等情况,导致出现曲轴个别轴径拉伤及烧瓦等现象[1]。
二、磨损原因分析(一)磨损沿径向分布问题由于磨损沿方向均匀程度有限,从而所形成的磨损情况也存在明显差别,轴径磨损后通常为椭圆形,而轴向体现为锥形,通常这种磨损的情况是由于作用力所形成的不均匀现象所导致。
曲轴油孔口倒角加工工艺讨论
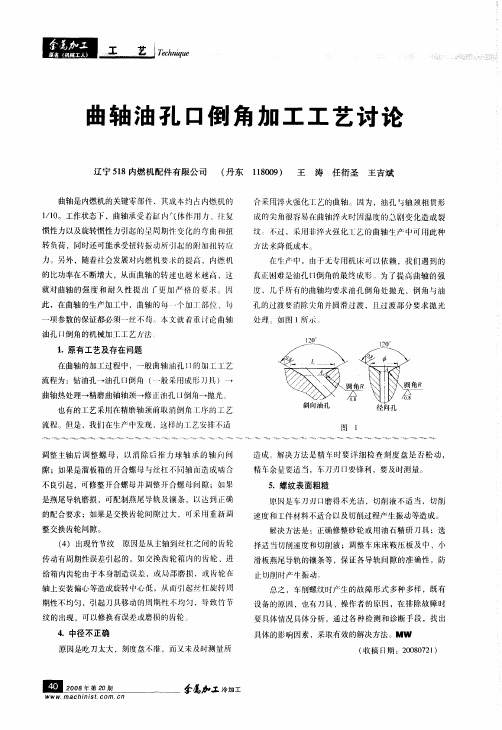
倒 角所用的高速钢或硬 质合 金刀具来修正倒角 都较为 困 难甚 无法实现 所以,我们采取磨削的方式 。
2 .初步解决问题的两种方式
起初 ,我们 用 2所示 磨头 先修 正 倒 角 的外 形 尺 寸 ,再进行油孔抛光。但在修正倒角时经常 会破坏在 淬 火前的倒角工序 所形成的倒角 与f - 之 问的过渡 圆弧 E/ hL
曲轴热处理一 精磨 曲轴轴颈一修 正f- 倒角一抛光 t LJ  ̄ L f .
也有的工 艺采用在精磨轴领 前取消倒角 工序的工 艺 流程 。但是 ,我们在生产 中发现 ,这样 工 安排不适 0
¨ I 。¨ ¨ . ’ _ ’_ 1 。 。 } ‘_¨I ’ ’ ’ 。l l¨ 。l ‘h・ ’ ・ ‘} ’’¨ ’l ’’ 。} I_ ¨h 。 ¨l I. … 。l・ ’- ’¨ l 。 ‘。I 。 L 。 - ’j I・ 。lI 。 。
4 m深度范围内是淬火形成的硬化层 ,若 采用如淬 火前 m
形 ,保证 各项参数 的要求 。
( )去尖角 用另一个修成倒圆锥形的磨头去除油孑 2 L
倒角 与油孔相交处的锐边尖角。使用中,用手把握风动砂 轮机 ,以不同的 a角使磨 头绕 油孔 的中心线转动 ,如 图4
所示 ,注意在改变 角大小时不要抬起气动砂轮机 以使磨 头连续的磨削,这样 ,磨出来 的倒角与油孔问的过渡就能
合采用淬 火强化 艺的曲轴。因 为,油孔 轴预相 贯形 成的尖 角很容易在曲轴淬 火时因温度的 剧变化造 成裂 纹 不过 ,采』 非淬火强 化工 艺的曲轴 生产 中可用此 种 { 】
方法 米降 低成本。
在' f‘ t' - 中,由于尢专用机床 叮以依赖 ,我 们遇 到的 真1 困难是油孔 [倒 角的最终 成形。为了提高 曲轴 的强 I 二 _ _ l 度 ,几 乎所有的曲轴均要求油孔 倒角处抛光 ,倒角 与油 孑 的过渡 要消除火角并圆滑过 渡,且过 渡部分 要求抛 光 L
曲轴后端漏油的原因分析及维修措施
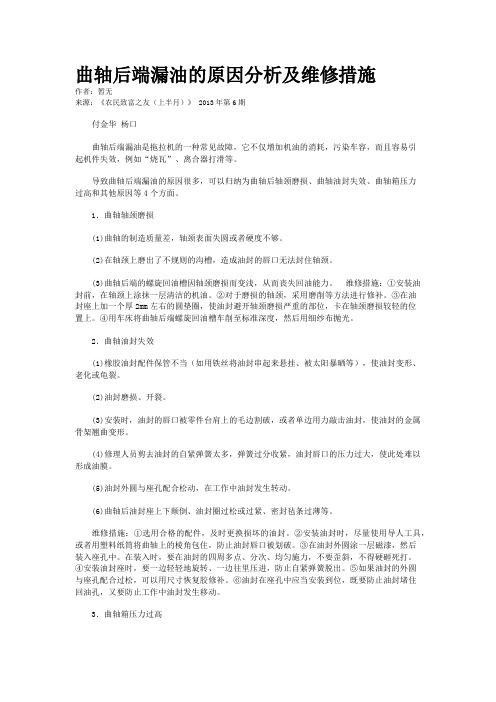
曲轴后端漏油的原因分析及维修措施作者:暂无来源:《农民致富之友(上半月)》 2013年第6期付金华杨口曲轴后端漏油是拖拉机的一种常见故障,它不仅增加机油的消耗,污染车容,而且容易引起机件失效,例如“烧瓦”、离合器打滑等。
导致曲轴后端漏油的原因很多,可以归纳为曲轴后轴颈磨损、曲轴油封失效、曲轴箱压力过高和其他原因等4个方面。
1.曲轴轴颈磨损(1)曲轴的制造质量差,轴颈表面失圆或者硬度不够。
(2)在轴颈上磨出了不规则的沟槽,造成油封的唇口无法封住轴颈。
(3)曲轴后端的螺旋回油槽因轴颈磨损而变浅,从而丧失回油能力。
维修措施:①安装油封前,在轴颈上涂抹一层清洁的机油。
②对于磨损的轴颈,采用磨削等方法进行修补。
③在油封座上加一个厚2mm左右的圆垫圈,使油封避开轴颈磨损严重的部位,卡在轴颈磨损较轻的位置上。
④用车床将曲轴后端螺旋回油槽车削至标准深度,然后用细纱布抛光。
2.曲轴油封失效(1)橡胶油封配件保管不当(如用铁丝将油封串起来悬挂、被太阳暴晒等),使油封变形、老化或龟裂。
(2)油封磨损、开裂。
(3)安装时,油封的唇口被零件台肩上的毛边割破,或者单边用力敲击油封,使油封的金属骨架翘曲变形。
(4)修理人员剪去油封的自紧弹簧太多,弹簧过分收紧,油封唇口的压力过大,使此处难以形成油膜。
(5)油封外圆与座孔配合松动,在工作中油封发生转动。
(6)曲轴后油封座上下颠倒、油封圈过松或过紧、密封毡条过薄等。
维修措施:①选用合格的配件,及时更换损坏的油封。
②安装油封时,尽量使用导人工具,或者用塑料纸筒将曲轴上的棱角包住,防止油封唇口被划破。
③在油封外圆涂一层磁漆,然后装入座孔中。
在装入时,要在油封的四周多点、分次、均匀施力,不要歪斜,不得硬砸死打。
④安装油封座时,要一边轻轻地旋转、一边往里压进,防止自紧弹簧脱出。
⑤如果油封的外圆与座孔配合过松,可以用尺寸恢复胶修补。
⑥油封在座孔中应当安装到位,既要防止油封堵住回油孔,又要防止工作中油封发生移动。
高效加工B12D曲轴斜油孔工艺

图1 目前生产的B12D四缸发动机曲轴结构
度,控制总长度;最后车削外圆,控制 58mm的外 圆再用中心钻钻中心孔。 第二,根据图样,工作台向左转换 62 ° 48 ′ 。 由于车床构造,不能一次性准确转换到位,需要经 过多次的试车与测量来转换刀架位置以达到精度要 求。 首先车去部分多余材料,然后转动小滑板,进 行车削,车削一次,用万能角度尺测量一次,根据 图样测量角度为207° 8′ ~207° 12′ ,测量时以端面 为基准,要借助灯光观察。同时要用游标卡尺测量 长度为 17mm 斜面,以防车削过多。最后,工作台 调整归位。 第三,根据图样角度要求,工作台向右旋转 30 ° ,然后转动刀架利用特制的切槽刀,转动小滑 板,进行车削,车削一次用万能角度尺以斜面为基 准测量一次,根据图样测量角度为 87° 8′ ~87° 16′ ,
T工 艺
echnique
高效加工B12D曲轴斜油孔工艺
柳州欧维姆机械股份有限公司设备厂 (广西 545006) 黄艺年
曲轴斜油孔加工是曲轴加工中的难点之一,除 了具有深孔加工的特点外,还因为孔与孔之间是三 维分布,各断面尺寸、形状和刚度均不同,因此给 定位、夹紧、钻孔及冷却等都带来很大难度。目 前,比较传统的加工方法是:工序分散的并行加工 工艺,而且大多采用复合刀具。采用这样的加工工 艺干扰因素和不确定因素多,刀具复杂,管理成本 较高,且加工设备占地面积大。由于公司机加工车 间厂房比较狭小,如果采取传统工艺很难适应生产 需要。这就要求工序集中在单台设备上完成曲轴斜 油孔的全部加工,且仅需在单台设备上进行曲轴的 一次装夹,是提高生产效率的高效加工工艺方法。 下面介绍一下我公司现在使用的加工工艺。
32
3EA113发动机曲轴加工质量问题的探讨
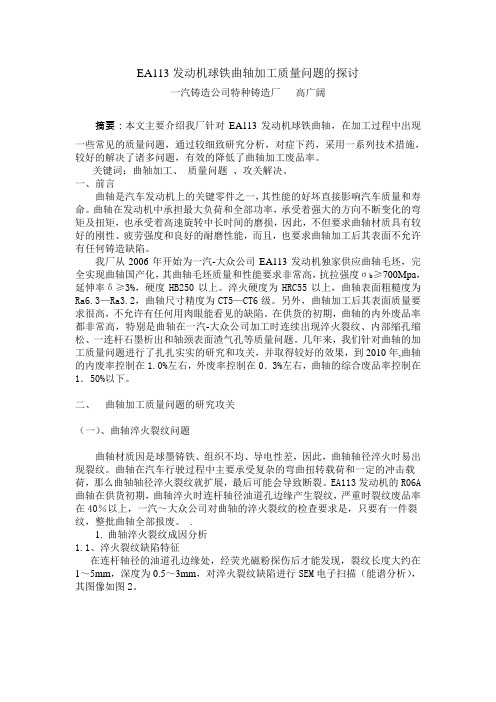
EA113发动机球铁曲轴加工质量问题的探讨一汽铸造公司特种铸造厂高广阔摘要:本文主要介绍我厂针对EA113发动机球铁曲轴,在加工过程中出现一些常见的质量问题,通过较细致研究分析,对症下药,采用一系列技术措施,较好的解决了诸多问题,有效的降低了曲轴加工废品率。
关键词:曲轴加工、质量问题、攻关解决。
一、前言曲轴是汽车发动机上的关键零件之一,其性能的好坏直接影响汽车质量和寿命。
曲轴在发动机中承担最大负荷和全部功率,承受着强大的方向不断变化的弯矩及扭矩,也承受着高速旋转中长时间的磨损,因此,不但要求曲轴材质具有较好的刚性、疲劳强度和良好的耐磨性能,而且,也要求曲轴加工后其表面不允许有任何铸造缺陷。
我厂从2006年开始为一汽-大众公司EA113发动机独家供应曲轴毛坯,完全实现曲轴国产化,其曲轴毛坯质量和性能要求非常高,抗拉强度σb≥700Mpa,延伸率δ≥3%,硬度HB250以上。
淬火硬度为HRC55以上,曲轴表面粗糙度为Ra6.3—Ra3.2,曲轴尺寸精度为CT5—CT6级。
另外,曲轴加工后其表面质量要求很高,不允许有任何用肉眼能看见的缺陷。
在供货的初期,曲轴的内外废品率都非常高,特别是曲轴在一汽-大众公司加工时连续出现淬火裂纹、内部缩孔缩松、一连杆石墨析出和轴颈表面渣气孔等质量问题。
几年来,我们针对曲轴的加工质量问题进行了扎扎实实的研究和攻关,并取得较好的效果,到2010年,曲轴的内废率控制在1.0%左右,外废率控制在0.3%左右,曲轴的综合废品率控制在1.50%以下。
二、曲轴加工质量问题的研究攻关(一)、曲轴淬火裂纹问题曲轴材质因是球墨铸铁、组织不均、导电性差,因此,曲轴轴径淬火时易出现裂纹。
曲轴在汽车行驶过程中主要承受复杂的弯曲扭转载荷和一定的冲击载荷,那么曲轴轴径淬火裂纹就扩展,最后可能会导致断裂。
EA113发动机的R06A 曲轴在供货初期,曲轴淬火时连杆轴径油道孔边缘产生裂纹,严重时裂纹废品率在40%以上,一汽~大众公司对曲轴的淬火裂纹的检查要求是,只要有一件裂纹,整批曲轴全部报废。
缸体不同角度曲轴瓦面斜油孔加工方式创新
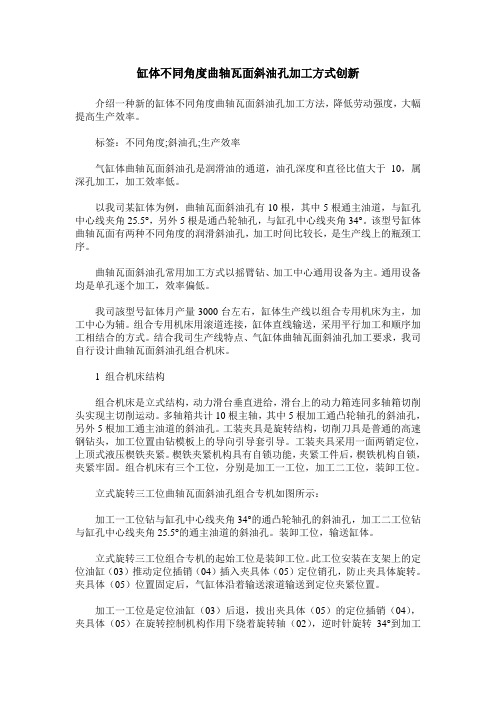
缸体不同角度曲轴瓦面斜油孔加工方式创新介绍一种新的缸体不同角度曲轴瓦面斜油孔加工方法,降低劳动强度,大幅提高生产效率。
标签:不同角度;斜油孔;生产效率气缸体曲轴瓦面斜油孔是润滑油的通道,油孔深度和直径比值大于10,属深孔加工,加工效率低。
以我司某缸体为例,曲轴瓦面斜油孔有10根,其中5根通主油道,与缸孔中心线夹角25.5°,另外5根是通凸轮轴孔,与缸孔中心线夹角34°。
该型号缸体曲轴瓦面有两种不同角度的润滑斜油孔,加工时间比较长,是生产线上的瓶颈工序。
曲轴瓦面斜油孔常用加工方式以摇臂钻、加工中心通用设备为主。
通用设备均是单孔逐个加工,效率偏低。
我司該型号缸体月产量3000台左右,缸体生产线以组合专用机床为主,加工中心为辅。
组合专用机床用滚道连接,缸体直线输送,采用平行加工和顺序加工相结合的方式。
结合我司生产线特点、气缸体曲轴瓦面斜油孔加工要求,我司自行设计曲轴瓦面斜油孔组合机床。
1 组合机床结构组合机床是立式结构,动力滑台垂直进给,滑台上的动力箱连同多轴箱切削头实现主切削运动。
多轴箱共计10根主轴,其中5根加工通凸轮轴孔的斜油孔,另外5根加工通主油道的斜油孔。
工装夹具是旋转结构,切削刀具是普通的高速钢钻头,加工位置由钻模板上的导向引导套引导。
工装夹具采用一面两销定位,上顶式液压楔铁夹紧。
楔铁夹紧机构具有自锁功能,夹紧工件后,楔铁机构自锁,夹紧牢固。
组合机床有三个工位,分别是加工一工位,加工二工位,装卸工位。
立式旋转三工位曲轴瓦面斜油孔组合专机如图所示:加工一工位钻与缸孔中心线夹角34°的通凸轮轴孔的斜油孔,加工二工位钻与缸孔中心线夹角25.5°的通主油道的斜油孔。
装卸工位,输送缸体。
立式旋转三工位组合专机的起始工位是装卸工位。
此工位安装在支架上的定位油缸(03)推动定位插销(04)插入夹具体(05)定位销孔,防止夹具体旋转。
夹具体(05)位置固定后,气缸体沿着输送滚道输送到定位夹紧位置。
大功率曲轴跳动超差的原因剖析及其解决措施
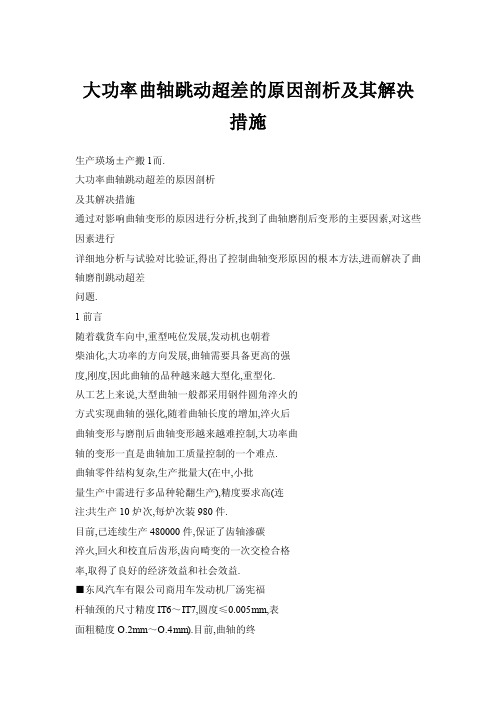
大功率曲轴跳动超差的原因剖析及其解决措施生产瑛场±产搬l而.大功率曲轴跳动超差的原因剖析及其解决措施通过对影响曲轴变形的原因进行分析,找到了曲轴磨削后变形的主要因素,对这些因素进行详细地分析与试验对比验证,得出了控制曲轴变形原因的根本方法,进而解决了曲轴磨削跳动超差问题.1前言随着载货车向中,重型吨位发展,发动机也朝着柴油化,大功率的方向发展,曲轴需要具备更高的强度,刚度,因此曲轴的品种越来越大型化,重型化.从工艺上来说,大型曲轴一般都采用钢件圆角淬火的方式实现曲轴的强化,随着曲轴长度的增加,淬火后曲轴变形与磨削后曲轴变形越来越难控制,大功率曲轴的变形一直是曲轴加工质量控制的一个难点.曲轴零件结构复杂,生产批量大(在中,小批量生产中需进行多品种轮翻生产),精度要求高(连注:共生产10炉次,每炉次装980件.目前,已连续生产480000件,保证了齿轴渗碳淬火,回火和校直后齿形,齿向畸变的一次交检合格率,取得了良好的经济效益和社会效益.■东风汽车有限公司商用车发动机厂汤宪福杆轴颈的尺寸精度IT6~IT7,圆度≤0.005mm,表面粗糙度O.2mm~O.4mm).目前,曲轴的终/]nz仍普遍采用磨削工艺,为满足曲轴日益提高的加工要求,对曲轴磨床提出了很高的要求,现代曲轴磨床除了要有很高的静态,动态刚度和很高的N-r-精度外,还要求有很高的磨削效率和更多的柔性.基于此,目前连杆轴颈磨床的磨削工艺已越来越多地使用跟踪磨削工艺,决定了目前的磨削工艺只能是先磨全部的主轴轴颈再磨全部的连杆轴颈,这也在无形中增加曲轴变形的控制难度.由于曲轴在装配过程中,与轴瓦间的配合有较高要齿项不接触工装装炉圈5改进后装炉方式圈2010年第7期汽车工艺与材料AT&M129.生导琐场求,故对主轴轴颈跳动要求较高,对六缸大功率发动机而言,特别要控制3,4,5主轴轴颈跳动,以免在发动机运行时发生曲轴的"抱瓦"或"拉瓦"等质量事故.我厂采用的加工工艺为主轴轴颈及连杆轴颈圆角淬火一低温回火一修整中心孔一磨全部的主轴轴颈一磨全部的连杆轴颈,且在加工过程中不允许对曲轴进行校直.在我厂某一大功率曲轴的生产调试过程中,磨削后出现第3,4,5主轴轴颈跳动超差,实际情况第3,5t轴轴颈跳动平均值为0.082mm,最大为0.13mm,偏于公差上限,第4主轴轴颈跳动平均值为0.1mm,最大为0.14mm,通过统计废品率达到了10%~35%,跳动超差直接导致曲轴报废,因此解决曲轴磨削工序变形超差的质量问题势在必行.2大功率曲轴磨削跳动超差的原因分析2.1当瞬时应力大于材料的弹性极限时,产生了曲轴的不均匀塑性变形曲轴在磨削时除了所受的磨削力外,还存在淬火时工件内部产生的残余应力,虽然经过回火工序,该残余应力得到释放,但不可能完全释放.还有在磨削时因偏磨产生的组织应力.当存在磨削烧伤时,因组织转变而形成组织应力.在磨削主轴轴颈和连杆轴颈时,因有中心架抵消磨削力,因此曲轴所受的瞬时力大于材料弹性极限的可能性很小,曲轴在磨NH,1-所受的磨削力是不可能消除的,所以这种情况并不是产生曲轴变形的主要原因.通过多次调整磨削参数,磨削方式及磨削顺序,都无法从根本上解决磨削后曲轴的变形超差问题,这样间接证明了磨削工序并不是曲轴变形的主要原因. 2_2磨削过程中释放的残余应力导致曲轴变形曲轴内部的残余应力,主要是在淬火过程中因热胀冷缩的体积变化,以及因相变时新旧两相比容差异而发生的体积变化形成的.该残余应力的大小决定了曲轴淬火变形的大小:该残余应力经过回火后部分得到释放,但不可能完全释放.因此,在磨削时剩余残余应力释放导致曲轴变形.2.3轴颈内外两侧受力不均.导致曲轴变形淬火后曲轴表面存在很大的压应力,该压应力从表面向内部递减,磨削时如果偏磨,将造成曲轴表面压应力的变化,在相对方向不均衡的情况下,导致曲轴变形.为了验证残余应力及偏磨对曲轴变形的影响,做了如下试验.(1)在前期加工的曲轴中挑取淬火后第4主轴轴颈跳动在O9~10mm之间的曲轴3根,这3根曲轴淬火前全部是合格曲轴,对这3根曲轴的相位进行测量,测量结果见表1.相位全部因淬火变形而发生变化,该3根曲轴中心孔修正后,第4主轴轴颈跳动在0.6~0.8mm之间;磨削后第3,4,55轴轴颈跳动全部超差,第4主轴轴颈跳动全部为0.16mm,第3,5主轴轴颈跳动为O.13~0.15mm.由此可见,淬火变形导致连杆轴颈相位变化,后续磨削时产生偏磨, 曲轴跳动超差:淬火后内应力过大,导致后续磨削时内应力释放,曲轴跳动超差.(2)加工3根内铣相位为15'的曲轴,相位超差3.~5..淬火后曲轴变形控制在O.6mm以内:中,CqL 修正后,第4主轴轴颈跳动控制在O.35mm以内:磨削后第4主轴轴颈跳动为0.15~0.18mm,3根曲轴跳动全部超差.30f汽车T艺与材料AT&M2010年第7期.生亭礤锚经过以上分析发现,曲轴磨削后变形超差的主要原因如下.(7)淬火后曲轴内应力过大,导致曲轴变形超差.虽经回火后应力得到一定的释放,但仍有较大的残余应力带到了磨削工序中.在曲轴磨削过程中,残余应力持续释放而导致跳动超差.(2)因淬火变形导致曲轴相位发生变化,致使磨削时连杆轴颈发生偏磨,导致曲轴因受力不均产生变形.通过以下方法可解决磨削后的曲轴变形.(1)控制淬火后的曲轴变形.(2)控制曲轴的内应力.(3)降低曲轴的变形量,减少曲轴偏磨.(4)通过更改磨削工艺,控制曲轴内应力的释放,避免曲轴变形超差.3曲轴淬火变形,内应力过大的原因分析及其解决措施3.1影响曲轴变形的原因分析(1)由于热胀冷缩和组织转变,发生了体积的变化,导致材料内部产生应力.当瞬时应力大于材料的弹性极限时,产生了曲轴的不均匀塑性变形;当轴颈淬火层深不均匀和轴颈侧面的淬火高度过高时,特别是连杆轴颈与第4主轴轴颈层深不均匀和轴颈侧面的淬火高度过高(连杆轴颈内外结构不一样,直接导致淬火层深不均匀和侧面淬火高度过高对整个曲轴的变形影响最大),轴颈的塑性变形不一样,引起曲轴变形.(2)曲轴在加热和冷却过程中,因为热胀冷缩和组织转变而引起曲轴整体长度变化,此时要求曲轴可以自由伸缩,尾架顶紧力不能太大,如果太大则曲轴将会发生塑性变形.(3)毛坯内应力和机械加工应力的存在,对淬火过程中的瞬时应力有叠加作用,导致曲轴产生不均匀的塑性变形.(4)盐轴在淬火过程中,感应器对曲轴的压力不能太大,力度调整到感应器在淬火过程中正好不脱离曲轴,特别是在曲柄的上,下支点,感应器对曲轴的压力不能差别太大,否则直接引起曲轴的变形.3.2表面感应淬火内应力形成的一般规律零件在加热和冷却过程中,将发生热胀冷缩的体积变化,以及因相变时新旧两相比容差异而发生体积变化.热传导过程中由于零件的表面比心部先加热或冷却,在截面上各部分之间存在温差,致使零件表面和心部不能在同--8,1-期发生上述的体积变化,各部分体积变化相互牵制而产生内应力.加热或冷却速度越大,在零件截面上的温差增大,形成的内应力便越大.热处理过程中所形成的内应力可称为瞬时应力;热处理后在零件内存在的应力则称为残余应力.瞬时应力随着温度的变化而改变其应力大小和方向.如果瞬时应力始终小于材料的弹性极限时,则引起瞬时应力的原因消失后,瞬时应力随即消失;但若瞬时应力大于材料的弹性极限而弓1起不均匀塑性变形,那么当造成应力的原因消失后而保留在零件之中的内应力即为残余应力.根据内应力形成的原因不同,又可分为由温差引起的胀缩不均匀而产生的热应力和由相变不同期及组织不均匀产生的组织应力.3.3解决层深均匀性和侧面淬火高度的措施分析该大功率曲轴生产线所用淬火机是进口法国的EFD淬火机,进口感应器不但价格昂贵,而且热效率极低,因此有必要对进口感应器国产化.在使用进口感应器调试过程中,层深均匀性和淬火后曲轴变形均未得到解决.根据切片结果,对感应器有效圈进行了改进,层深均匀性得到了一定程度的提高,但是侧面淬火深度和高度,仍有一定的缺陷,因此淬火后曲轴变形超差的质量问题,仍未得到彻底解决.通过两轮国产化感应器中间试验,根据前期切片结果,又对感应器有效圈进行了优化试验,层深均匀性和侧面淬火高度均得到彻底解决.为了获得均匀的有效硬化层深度,在感应加热周期内,圆角区要比圆柱区提供更多的能量,以弥补热传导损失的热量.2o10年第7期汽车工艺与材料AT&Ml31.生产碗场由传热学可知,沿某方向通过微区面积ds=dyXdz的热流量是:dqx=/1X(dT/dX)XdsXdt(1)式中,为材料的导热系数;d7-/dX为沿方向该点的温度梯度:df为微量时间.由上式可知,热传导损失的热量与导热系数,温度梯度,导热面积和加热时间成正比.同一轴颈加热时,圆角区和圆柱区的导热系数和加热时间是相同的.导热面积可以分别计算出来,但是两处的温度梯度不同,而且随加热时间而变,要精确计算温度梯度对热流量的影响是十分困难的.定性分析和实践表明,感应加热时,圆角区的升温快,因为沿加热层深度方向和加热区的边缘温度梯度大,热流量损失大,相反则圆柱区的热量损失小.切片试样及切片结果,正好与分析的状况相同.由于有效圈几何形状设计不合理且焊点较多,导致感应器效率低,为了满足层深的工艺要求,必须增加加热时间,加热时间过长导致淬火后变形量过大而造成曲轴报废,此期间曲轴淬火后跳动超差的废品率达到了60%~70%.具体淬火参数见表2.进口感应器有效圈结构见图1.轴颈功率/kw加热时I'~/s冷却时l'~/s备注王袖轴颈2—6180/160/14016/22/2216/16/163组参连许轴颈1~6120~180璃零龠蘑I王轴轴颈318022||蔼∞王轴轴颈1||.180一16薯l虽然影响圆角区温度和圆柱区温度的因素除了热传导之外,还有表面热辐射损失,但是由于加热时间短(12~14s左右),热损失之差不大于3%,可以忽略不计.因此,感应器的设计就是要使圆角处得到足够的热量.(1)进口感应器优,缺点分析进口感应器采用的是有效圈圆弧段与曲轴轴颈表面成45.的结构形式,形状采用的是异型结构(见图1).该感应器有效圈圆弧段设计完全基于使圆角处得到足够的热量,有效圈圆弧段磁场直接作用在圆角和侧面直接加热,而轴颈处硅钢片数量太少,因圆角处的热量损失最大,如果轴颈处热量仅靠圆角处的热量传递,在短时间内不能满足轴颈层深的需要,这是造成感应器效率低的主要原因.该感应器有效圈不是一个整体,由很多部分焊接而成,焊点很多,功率损失大,这是造成感应器效率低的次要原因.此种感应器有效圈圆弧段设计极易出现马鞍形淬火层深,圆角处与轴颈处层深差别太大.如果欲满足轴颈层深的工艺要求,必须增加加热时间,当时的加热时间为22~24S,加热时间越长,曲轴变形越大.采用这种结构形式,能很好地保证侧面淬火高度.查阅前期曲轴的图1进口感应器有效圈结构(2)第一轮感应器优,缺点分析第一轮感应器采用的是有效圈圆弧段与曲轴轴颈表面成0.的结构形式,有效圈是由1OmmX1Omm的标;隹矩形铜管制作而成(见图2).该感应器有效圈圆弧段磁场直接作用在侧面和轴颈上,直接对侧面和轴颈加热,而圆角处大部分热量是由轴颈和侧面传32J汽车T艺与材料AT&M2010年第7期生产碗场.±搬汤导而来,再加上轴颈处还有部分硅钢片,且该感应器有效圈圆弧段是一整根铜管弯制而成,没有焊点,从而使感应器效率得到极大提高.因此种有效圈圆弧段设计极易出现侧面深度太深,圆角处深度太浅,层深不均匀,故引起曲轴变形.由于感应器热效率的提高,淬火功率和淬火时间都有了适当的缩短,曲轴变形与进口感应器相比,下降了很多,但是仍旧存在40%的废品,因此进~步对感应器有效圈结构进行改进势在必行,具体淬火参数见表3.第一轮感应器有效圈结构见图2.轴颈功率/kW加热时1~1/s冷却时I'~1/s备注图2第一轮感应器有效圈结构(3)第二轮改进感应器优,缺点分析第二轮改进感应器采用的是前有效圈左侧圆弧段与曲轴轴颈表面成0.,前有效圈右侧圆弧段与曲轴轴颈表面成45.,后有效圈左侧圆弧段与曲轴轴颈表面成45.,后有效圈右侧圆弧段与曲轴轴颈表面成0.的结构形式,有效圈是由6mm×12mm的异形铜管制作而成,见图3.该感应器有效圈圆弧段磁场--N直接作用在圆角和侧面上,直接对侧面和圆角加热i而另一侧有效圈圆弧段磁场直接作用在侧面和轴颈上,对轴颈与侧面加热i再加上轴颈处还有部分硅钢片,且该感应器有效圈圆弧段是一整根异形铜管弯制而成,没有焊点.f!t~IL,该感应器效率很高.该感应器很好地保证了侧面淬火高度(侧面淬火高度工艺要求为6min).前有效圈剖面图后有效圈剖面图图3第二轮改进感应器有效圈结构2o1o年第7期汽车I艺与材料AT&Mf33生产硬场该感应器综合了进口感应器和第一轮感应器所有优点,同时避免了以上两种感应器的缺点,感应器的效率和稳定性都有了很大的提高,加热功率和加热时间又在第一轮感应器的基础上进行了缩短,切片结果显示,层深均匀性及侧面淬火高度全部优于前两轮感应器切片结果,具体淬火参数见表4,淬火层深切片数据见表5.轴颈功率/kW加热时间/s冷却时I'~1/s备注轴颈左罢淬右星淬轴曩火3.4毛坯内应力的控制方法(1)在前期生产过程中,毛坯厂为了节省节拍时间,缩短了曲轴的正火时间,因此为了降低曲轴毛坯的内部应力,必须保证正火炉温的均匀性和正火的时间,以保证内部组织的均匀性,避免产生内应力. (2)在目前国内的锻造水平下,如dC11曲轴毛坯.国内很难保证一次锻造成形,锻造后很多地方不能满足毛坯图纸的工艺要求.为了降低废品率,毛坯厂对不能满足工艺要求的部位(如充不满,有凹陷等)进行堆焊,而堆焊后又没有按照正规的热处理工艺进行去应力退火,因此为了消除堆焊产生的内部应力,对毛坯厂提出了以下2点要求.a.尽量避免对毛坯进行堆焊.b.对部分必须堆焊的毛坯,按正规热处理工艺进行去应力退火.3.5尾架顶紧力与感应器配重的调整(1)为了保证曲轴在淬火过程中的自由伸缩,尾架项紧力应尽可能小,经过2轮工艺试验,尾架项紧力由2X10Pa降低为O5X1OPa,益轴淬火后第4主轴轴颈跳动量平均降低O.18mm.(2)为了防止曲轴在淬火过程中产生塑性变形,必须尽量降低感应器对曲轴的压力,特别是在曲柄上,下支点的压力,如果曲柄上,下支点的压力差太大,则外力叠加后导致曲轴产生塑性变形.3.6淬火工序改进前,后数据对比分析在该曲轴前期投产过程中,淬火后曲轴变形过大一直是曲轴生产线质量控制的一个难点,整条曲轴生产线因为淬火后曲轴变形过大而无法顺利生产.曲轴生产线的淬火工序废品率一直居高不下,废品率达到了40%之多(回火后第4主轴轴颈跳动工艺要求为0.8 mm),回火后国产毛坯的第4主轴轴颈跳动平均在O.79mm.为了挽救曲轴,部分跳动超差的曲轴不得不继续下流,靠磨床来挽救,这不但造成了对磨床的损害,而且造成人力,物力的极大浪费.改进前,国34I汽车工艺与材料AT&M2010年第7期.生产琐扬产毛坯回火后曲轴第4主轴轴颈跳动数据见表6.两轮的国产化感应器中间试验,对感应器有效圈结构进行了改进,调整了尾架项紧压力和感应器压力,有效地控制了毛坯内应力的产生.目前,淬火后曲轴变形已基本得到很好地控制,淬火后国产毛坯的第4主轴轴颈跳动平均在0.28mm左右,回火后基本能控制在0.22mm左右,废品率控制在1%以内(淬火后第4主轴轴颈跳动工艺要求为08mm,回火后第4主轴轴颈跳动工艺要求为O.6mm),很好地满足了后续加工工艺的要求.改进后国产毛坯淬火,回火后曲轴第4主轴颈跳动数据见表7.4减少偏磨,避免曲轴因表面应力分布不均而产生变形在磨削主轴轴颈时,以顶尖孑L为基;隹,要想避免曲轴产生偏磨,必须控制曲轴淬火的变形.根据前面零件号淬火回火的分析可知,曲轴在淬火时因应力的作用,变形不可避免.特别对大功率曲轴而言,目前需要解决的是尽量降低曲轴的变形量,通过修正中心孔来降低轴颈对顶尖的跳动,尽而减少曲轴的偏磨,避免曲轴因表面应力分布不均而产生变形.目前,我厂曲轴中心孔修正采用的方法是以第2,6主轴轴颈中心轴线为基准,设备修正后的中心孔中心连线与第2,6主轴轴颈中心轴线理论上应重合, 也就是说,修正后的中心孔反映第2,6主轴轴颈中心轴线.从目前现场加工的曲轴来看,对后续减少偏磨量的效果明显,修正效果很好.该修正方法仅适合于淬火后变形规则的曲轴,如果淬火后出现"S"曲轴,该修正方法对磨削将产生不利影响.5更改磨削工艺,控制曲轴内应力的释放,避免曲轴变形超差为了将曲轴内部应力进行释放,可以先对曲轴主轴轴颈进行预磨(必须保证轴颈圆度),然后再磨削全部连杆轴颈,这样可以提前将曲轴内部应力进行释2010年第7期汽车T艺与材料A T&M『35生产碗琶放,最后再精磨全部主轴轴颈,这种磨削方式可以在保证曲轴质量的同时,避免曲轴变形超差.采用这种方法的前提是必须新增磨床或改为双砂轮磨床,我厂该曲轴线已不可能采用该方式.后期再建新的生产线时,可以提前考虑采用这种磨削方式或采用双砂轮磨床,以避免曲轴因前序内应力过大而产生曲轴变形超差.6磨削工序改进前后效果对比验证改进前,因淬火后曲轴内应力较大,曲轴变形过大,磨削后因内应力释放,一直存在着磨削工序跳动超差的质量问题(工艺要求第2,3,5,6主轴轴颈跳动为0.1mm,第4主轴轴颈跳动为0.13mm).实际情况第3,5主轴轴颈跳动平均值为0082mm,最大为0.013mm,第4主轴轴颈跳动平均值为01mm,最大为O.14mm.通过对多批曲轴分批进行统计,磨削工序废品率达到了10%~35%之多,改进前磨削工序后曲轴第3,4,5主轴轴颈跳动数据见表8.零件号第3主轴颈第4主轴颈第5A.轴颈通过对感应器有效圈的改进设计及毛坯应力的控制,对尾架项紧力和感应器配重调整,解决了曲轴淬火变形,降低了曲轴的内应力,进而彻底解决了磨削后曲轴变形超差.通过对该工序160件曲轴进行跟踪检测,结果没有一根曲轴磨削后跳动出现超差,该工序因跳动超差的废品率降为零,第3主轴轴颈跳动平均值为0044mm,第5主轴轴颈跳动平均值为0.045mm,第4主轴轴颈跳动平均值为0.047mm,改进后磨削工序后曲轴第3,4,5i轴轴颈跳动数据详见表9.零件号第3主轴颈第4主轴颈第5主轴颈7G00087GOOlO7G00057Go0237C-00227G0127G0o067G00147G00177G0O16002…q∞|薯0:03&077结束语欢迎订购EEC指令(中英文对照版)0为了满足目前我国汽车行业对国外汽车法规了解和掌握的迫切需要,国家汽车质量监督检验中心(长春)与莱茵技术(上海)有限公司北京办事处合作组织汽车行业专业人士翻译了最新EEC指令,并委托《汽车文摘))杂志编辑出版.全套,丑EC指令共计58本,并附光盘一张,为中英文逐页对照形式,便于使用.黪.该EEC指令由《汽车文摘》杂志编辑部负责向汽车行业各企业推广销售,价格为7500~L/套,欢迎各企业来电咨询嗡受一联系人:杜女士电话:0431:85789859传真:0431:85789810E—mail:**************** I36f汽车212艺与材料AT&M2010年第7期∞∞∞O.OOOOO^U^OO^嘶∞∞叭∞O0OOOOOO0。
曲轴线磨床磨削加工质量问题解析

曲轴线磨床磨削加工质量问题解析1.概述发动机曲轴连杆颈和主轴颈需要磨削加工,精度要求高,尺寸要求都在微米级,加工过程中经常会出现尺寸及形位公差超差的问题。
主要有主轴颈跳动超差,主轴颈/连杆颈外圆尺寸超差、连杆颈相位角度超差等问题,下面针对这三个问题,做一下详细的解析。
2跳动问题排查1..出现跳动问题,分两种情况;第一,如果是偶尔出现,则需要检查工件顶尖孔是否有铁屑,机床装夹是否异常,是否需要调整冷却水冲洗的角度及方向。
第二,如果大量出现时,当然也要排除来料的问题,再检查机床本身的问题。
头尾架顶尖跳动是否正常,顶尖是否松动;尾架顶尖中存在一个弹簧,如果有必要可以更换一个新的弹簧;中心架的推出和抬起度检查,因为M2的跳动过大也会导致其他轴径跳动偏大;V型架支撑是否调整不好与工件有干涉;尾架顶尖气压不合适;图中尾架套筒夹紧压力当前6bar,可以适当减小,最大6bar。
根据工件跳动波动规律适当修正;例如M1,连续测几根工件,用表打出工件跳动的大小及高低点,然后在机床的Juwop/u中进行修正,如果Main 1跳动在P1角度为最高点,则在M1的X中做个正值修正,如果其他角度,可以在Y轴也适当修正,这样就可以把M1的高点适当修正回来。
3尺寸波动问题尺寸波动问题则分为某个测头加工的所有尺寸均有问题,还是仅这个测头加工的其中个别轴径有问题。
如果是这个测头加工的所有轴径都有问题,则需要怀疑这个测头本身是否有问题;如果工件圆度不好,则肯定都会影响直径;砂轮太钝或者到寿命,一样影响直径,则需要修砂轮及更换砂轮;首先验证侧头的重复性,检查测头机械上是否松动,测头线缆是否进水,检查测头的温度补偿系数是否输入正确,还有就是Marposs信号转接头及P7出现问题。
如果仅是某个轴径出问题,则需要把测头落在相应轴径上,看看是否与工件有干涉或者碰到工件油孔。
除掉上面这些原因,如果加工中出现尺寸过大或者过小的报警时候,则进入到相应的Marposs界面,查看是加工到那个轴径时候报警。
曲轴加工维修方案
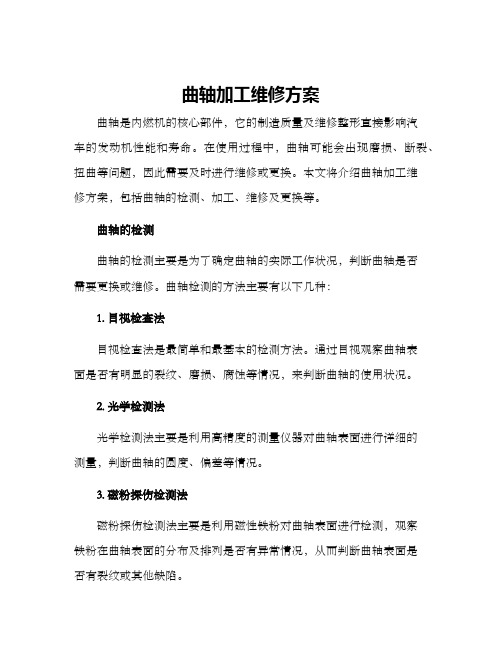
曲轴加工维修方案曲轴是内燃机的核心部件,它的制造质量及维修整形直接影响汽车的发动机性能和寿命。
在使用过程中,曲轴可能会出现磨损、断裂、扭曲等问题,因此需要及时进行维修或更换。
本文将介绍曲轴加工维修方案,包括曲轴的检测、加工、维修及更换等。
曲轴的检测曲轴的检测主要是为了确定曲轴的实际工作状况,判断曲轴是否需要更换或维修。
曲轴检测的方法主要有以下几种:1. 目视检查法目视检查法是最简单和最基本的检测方法。
通过目视观察曲轴表面是否有明显的裂纹、磨损、腐蚀等情况,来判断曲轴的使用状况。
2. 光学检测法光学检测法主要是利用高精度的测量仪器对曲轴表面进行详细的测量,判断曲轴的圆度、偏差等情况。
3. 磁粉探伤检测法磁粉探伤检测法主要是利用磁性铁粉对曲轴表面进行检测,观察铁粉在曲轴表面的分布及排列是否有异常情况,从而判断曲轴表面是否有裂纹或其他缺陷。
曲轴制造加工需要使用高精度的数控机床进行加工,以保证曲轴的几何形状与尺寸精度。
曲轴加工的主要工艺包括以下几个步骤:1. 粗加工粗加工主要是将原材料加工成粗曲轴。
这个过程需要使用数控机床进行车、铣、钻等加工工艺。
2. 圆轴磨削圆轴磨削是将粗曲轴经过磨削工艺,使得曲轴的圆度误差和偏差达到正负2微米。
圆轴磨削工艺需要使用高精度的数控磨床进行加工。
3. 轴颈磨削轴颈磨削是对曲轴轴颈进行磨削加工,使得轴颈的精度达到正负1微米。
轴颈磨削工艺需要使用高精度的数控磨床进行加工。
4. 孔加工孔加工是将曲轴上的油道、针轴等部位进行加工处理,以保证各部位间的流体通畅。
孔加工需要使用高精度的数控钻床、车床进行加工。
曲轴的维修主要是对曲轴进行磨削、修补等处理,使得曲轴能够继续使用。
曲轴维修的具体工艺取决于曲轴的损坏状况,维修工艺包括以下几个步骤:1. 清洗曲轴在使用过程中会有一些脏污的物质沉积在曲轴表面,因此需要对曲轴进行清洗处理。
清洗工艺需要使用专门的清洗设备和洗涤液。
2. 磨削曲轴的磨削是曲轴维修的核心步骤,主要是对曲轴表面进行磨削处理,以去除曲轴表面的缺陷。
钻曲轴斜油孔工艺参数的两种快速求解方法
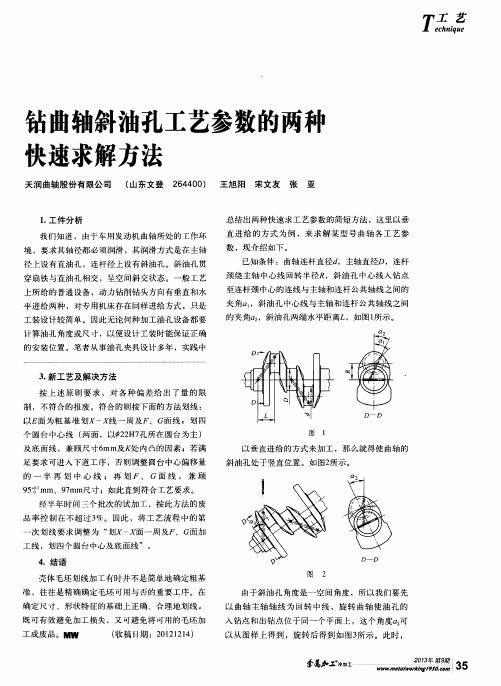
拦旦 圭 . . . 搀查 .
滚柱直线导轨副的结构设计及 寿命验证
广 东高新凯特精 密机械股 份有 限公 司 ( 江 门 5 2 9 1 o o ) 冯健文 赵 美玲 曹鹏 杰 陈伟就
近几年高刚性 、重负载机床越来越 多采用滚柱 直线导轨副代替原来 的滚珠直线导轨及滑动导轨 ,
精密磨削,导轨的直线度决定导轨副的运动精度 。
②滑 块 是导 轨 副 与 安装 滑 台 相 联 的部 件 ,由滑 块 主
体 、返向器、半圆柱、回柱管道、保持架和密封件 等组成。滑块主体同样经淬火和精密磨削而 成 ;返
向器 、
柱 循
1 . 结构设 计
( 1 )整体 结构 滚柱直线导轨 副 由导轨 、滑
块 和滚柱 组成 ,如图1 所示 ,其 中:①导轨是导轨 副 与安装 底座相联 接的部 件 ,材料 采用优 质合金
钢 ,滚 道 经表 面 淬 火 处理 ,导 轨 的 定位 侧 面 和 沟槽
图 1 滚柱直线导轨 副结构 图
作为直角三角形的一个直 角边 ,以 图4 中 、 两
点 的距 离 作 为 另一 个 直 角边 ,这 样就 可以 得 到 如 图
颈绕主轴 中心线 回转半径R,斜 油孔中心 线入钻 点
至 连 杆颈 中心 的 连 线 与 主轴 和 连 杆 公共 轴 线 之 间 的 夹 角a ,斜 油 孔 中心 线 与主 轴 和 连 杆 公 共 轴 线之 间 的夹 角a ,斜 油孔 两 端 水平 距离 ,如 图1 所示 。
工装设计较 简单 。因此无论何种加 工油孔设备都要
准 ,往 往是 精 确 确 定毛 坯 可 用 与 否 的 重要 工 序 。 在 确 定 尺 寸 、形 状 特 征 的 基础 上 正 确 、 合理 地 划 线 , 既 可 有效 避 免 加 工 损失 ,又 可 避 免将 可 用 的 毛坯 加
滚轧工艺在曲轴斜油孔加工中的应用

孔 , 以 保 证 斜 油 孔 的 质 量 , 止 曲轴 油 腔 泄 漏 。 可 防
保 证 了 机 车 的 正 常 操 纵 , 保 铁 路 运 输 安 全 畅 通 。口 确
收 稿 日期 :O 2—0 2O 5—2 3
—
5
一
维普资讯
现 场 经 验
铁 道 机 车 车辆 工人 第 7期 2 O O2年 7月
积 屑瘤 , 导致 已加 工 面拉 毛 , 曲轴斜 油孔 的加工 难 以达 到设 计要 求 。内孔 使
HB, 硬 度 不 均 匀 , 一 表 面 的 硬 度 值 甚 至 相 差 5 I 且 同 0F B,加 工 时 刀 具 易 产 生
一
o
① 放 大
图 1 1V 8 6 2 0曲 轴 斜 油 孔 示 意 图
() 车 在运用 中 , 操 纵端 总控 制 开 关 I 4机 非 K不 可 在 闭 合 状 态 。在 巡 检
其 加 工 工 艺 为 : 化 前 的 钻 孔 尺 寸 改 为 0 1l n 原 加 工 工 艺 是 氮 化 前 氮 4 n ( l 粗 钻 成 mm) 氮 化 后 扩 孔 分 为 2次 , 先 扩 成 06 t n孔 , 扩 成 0 7. ; 即 4 u t 再 4 5
ll , 证 第 2次 扩 孔 余 量 均 匀 , 孔 后 的 孔 内硬 度 均 匀 。 精 铰 孔 后 , 据 nn孔 保 扩 根 孔 的实测 尺 寸调整 滚轧 头 , 图 2 见 。根 据 外 套 刻 度 , 以 按 0 2 . 可 .5/n的 增 表 显 示后 , 立 即断 开非 操 纵 端 的开 K、2 , 应
柴油机曲轴工艺设计方案[]
![柴油机曲轴工艺设计方案[]](https://img.taocdn.com/s3/m/25f30449caaedd3383c4d3a4.png)
0 引言本次毕业设计是关于R180柴油机曲轴的工艺设计及其中两道工序的夹具设计。
曲轴是柴油机中的关键零件之一,其材质大体分为两类:一是钢锻曲轴,二是球墨铸铁曲轴。
由于采用铸造方法可获得较为理想的结构形状,从而减轻质量,且机加工余量随铸造工艺水平的提高而减小。
球铁的切削性能良好,并和钢制曲轴一样可以进行各种热处理和表面强化处理,来提高曲轴的抗疲劳强度和耐磨性。
而且球铁中的内摩擦所耗功比钢大,减小了工作时的扭转振动的振幅和应力,应力集中也没有钢制曲轴来的敏感。
所以球墨铸铁曲轴在国内外得到广泛采用。
本次设计中曲轴的材质为球铁。
从目前整体水平来看, 毛坯的铸造工艺存在生产效率低,工艺装备落后,毛坯机械性能不稳定、精度低、废品率高等问题。
从以下几个工艺环节采取措施对提高曲轴质量具有普遍意义。
①熔炼国内外一致认为,高温低硫纯净铁水的获得是生产高质量球铁的关键所在。
为获得高温低硫磷的纯净铁水,可用冲天炉熔化铁水,经炉外脱硫,然后在感应电炉中升温并调整成分。
②球化处理③孕育处理冲天炉熔化球铁原铁水,对铜钼合金球铁采用二次孕育。
这对于防止孕育衰退,改善石墨形态,细化石墨及保证高强度球铁机械性能具有重要作用。
④合金化配合好铜和钼的比例对形成珠光体组织十分有利,可提高球铁的强度,而且铜和钼还可大大降低球铁件对壁厚的敏感性。
⑤造型工艺气流冲击造型工艺优于粘土砂造型工艺,可获得高精度的曲轴铸件,该工艺制作的砂型具有无反弹变形量的特点,这对于多拐曲轴尤为重要。
⑥浇注冷却工艺采用立浇—立冷,斜浇—斜冷、斜浇—反斜冷三种浇注方式较为理想,其中后一种最好。
斜浇—反斜冷的优点是:型腔排气充分,铁水充型平稳,浇注系统撇渣效果好,冒口对铸件的补缩效果好,适应大批量流水线生产。
目前,国内大部分专业厂家普遍采用普通机床和专用组合机床组成的流水线生产,生产效率、自动化程度较低。
曲轴的关键技术工程仍与国外相差1~2个数量级。
国外的机加工工艺大致可归纳为如下几个特点。
曲轴斜油孔加工夹具设计中空间角度的计算问题
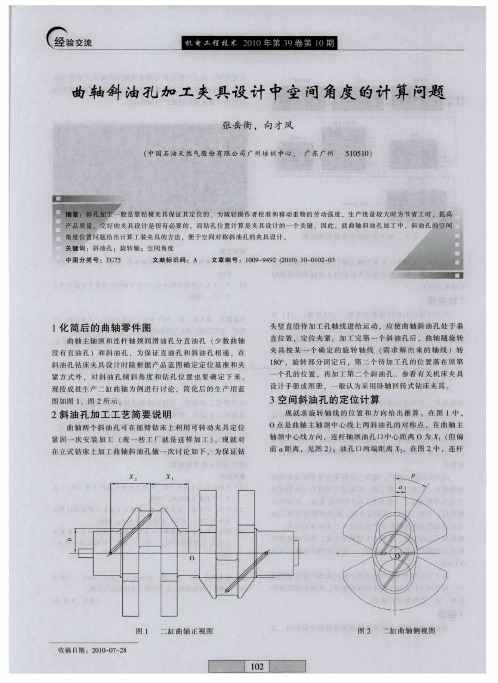
曲轴斜 油孔 加工夹 具设 计 中空 间角度 的计 算 问题
张岳 衡 . 向 才风
( 国石 油 天 然 气 股份 有 限 公 司 广 卅培 训 中心 , 广 东广 州 中 I 50 1) 15 0
翳勇 舅 舅
中图 分 类 号 :T 5 G7
是钻夹保其位。减操者准移重的动度生批较时节工, 靠模具证定的为轻作校和动物劳强,产量大为 时提 省 高
2斜 油 孔 加 工 工 艺 简 要说 明
曲 轴 两 个 斜油 孔 可 在摇 臂钻 床 上 利 用 可 转 动 夹 具 定 位 紧 同一 次安 装 加 1 现 一 些 工 厂 就 是 这 样 加 _ ) 现 就 对 :( 丁 。
在 立 式 钻 床 上 加丁 曲轴 斜 油 孔做 一 次 讨 论 如 下 ,为 保 证 钻
X2
X
l
a
√
/ 一
]
0
1
\
『 I 二缸曲轴正视图 皋 l
收稿 日期 :2 1 — 7 2 000—8
/
\ ~
~ 一 一
/
图 2 二缸曲轴侧视罔
r—— —— ——— —— ——T ——— —— ———r —— ——— ——— ——_ 1
文 献 标 识 码 :A 文章 编 号 : 10 — 4 2(01) 1 - 1 2 0 09 99 2 0 000—3
一
甓 一
i _
1 简 后 的 曲轴 零 件 图 化
曲 轴 主 轴 颈 和 连 杆 轴 颈 润 滑 油 孔 分 直 油 孔 ( 数 曲轴 少 没 有 直 油 孔 )和 斜 油 孔 ,为 保 证 卣油 孑 和 斜 油 孑 相 通 ,在 L L 斜 油 孔 钻 床 央 具 设 计 时 除 根 据 产 品 蓝 图 确 定 定 位 基 准 和夹
柴油机曲轴实用检修技术

柴油机曲轴的实用检修技术摘要:曲轴是柴油机的重要部件,由于种种原因,柴油机曲轴故障繁生,而曲轴的修理长期缺乏特定的目标,各施其法,修复效果和经济效益也不尽相同。
曲轴或轴类损坏的特征,集中表现在扭曲、弯曲变形以及轴颈表面烧伤、拉痕或过度磨损等,针对上述现象,只有采取合理的检修工艺,才能保证修复后的轴件正常运转。
关键词:柴油机曲轴;故障曲轴;修理方法与步骤中图分类号:tk428 文献标识码:a 文章编号:1673-8500(2013)03-0059-01柴油机曲轴在工作过程中由于受到活塞力、往复惯性力、曲轴旋转惯性力等的作用,使之发生横向、轴向、切向的变形,所受力通过轴承传到机体上。
曲轴在运转中引发的故障,只有极少数是因制造质量问题引起的,而大多则是由于安装、检修不佳所致。
一、对于故障曲轴的清理及检查方法与步骤1.测量曲轴的摆动差。
主轴的摆动差是曲轴在瓦内旋转时的摆动数值之差。
把磁性千分表架放在曲轴主轴承座的平面上,触针顶在主轴颈上方位置,盘车使曲柄销停在某一位置时,调节千分表,使指针指在零。
然后盘车,每转记下千分表读数,要求主轴摆动差在0.05mm以内。
2.测量曲轴的主轴颈水平。
用高精密度水平仪测量。
曲轴旋转,每转测量一次,每次测轴颈两端的两个点。
为防止水平仪有误差,测量时必须把水平仪转,反复测两次,取它的平均值。
至于飞轮重量的影响,它会使曲轴产生微小的弯曲,而且主轴颈的锥度也会产生影响,在测量时要予以考虑。
3.测量曲轴在轴承座孔内的位置。
用内径千分尺在主轴中心的水平位置测量主轴与两侧轴承座孔的三条筋的距离。
每一对数值应该相等。
测量的目的,一方面是在修换底瓦时做参考,另一方面是检查曲轴有无歪斜情况。
4.检查测量主轴颈和曲柄销表面粗糙度、圆度和圆柱度。
圆度和圆柱度公差都要求小于0.05mm,表面粗糙度不能满足要求的,应该用油石磨光。
主轴颈与曲柄销必须进行超声波探伤,检查有无缺陷,以及缺陷发展情况,尤其是在主轴颈与拐臂连接的根部。
曲轴机加工动平衡问题系统研究及解决
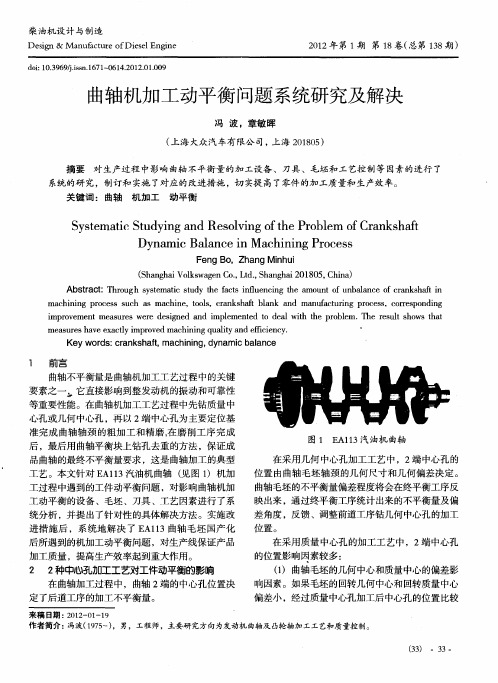
几何 中心的重复度要求较高 ,并且要求不同批此 的 毛坯质量中心一致性要好 ,几何中心孔的优势是加 工节 拍较 快 。质量 中心孔 工 艺能弥 补毛 坯质 量 中心 与几何中心不重合的偏差 , 但加工节拍较长且会造 成粗加工工序 中的不均匀切削。 3 曲轴机加工动平衡问题的解决方法 E 13 A 曲轴在毛坯加工和刀具 国产化过程中都 1 碰到了不 同程度的曲轴机加工中的动平衡问题 ,其 现象 为终 平衡 工序 的工 件 2次平衡 率 高 ,终平 衡工 序加工节拍长,严重时甚至会造成大量 的工件无法 自动终平衡 。通过对影响工件不平衡量的各种 因素 进行系统分析 ,量化评价并采取相应的解决措施 ,
Ke ywor s ca k h f ma hnn , y a cb ln e d : rn s at , c iig d n mi aa c
1
前 言
曲轴不平衡量是 曲轴机加工工艺过程 中的关键
要素之一 它直接影响到整发动机的振动和可靠性 等重要性能。在曲轴机加工工艺过程中先钻质量中
成 刀具 异常 损耗 。
制造的质量 中心孔加工专机,见 图 2 。
()质量中心孔专机的平衡框架不平衡量的偏 2 差影响因素 。每次在执行专机标定程序前应该先校 准平衡框架的不平衡量,否则框架的不平衡量将传 递到加工工件上 ,造成工件 的终平衡工序不平衡量
增大 。 ()质 量 中心孔 专机 的标定 情况 。质 量 中心 孔 3
在 动平 衡 专机上 测量 出刀柄 的不平衡 量 和不 平衡 角 度后 , 直接 在刀 柄旋 转外 套上 钻孑 去重 , L 参见 图 3 。
操作 ,每天做 1 次标定 2以保证设备 的良好加工状
态。
质量中心孔专机的动平衡测量校准和标定 ,主 要是评价设备对不平衡量测量 的准确性和稳定性 , 校准和标定前对平衡测量框架的清洁非常重要 。正 常生产时 ,也必须定期清洁框架 , 保证框架上面不
枪钻加工曲轴油孔方法探讨
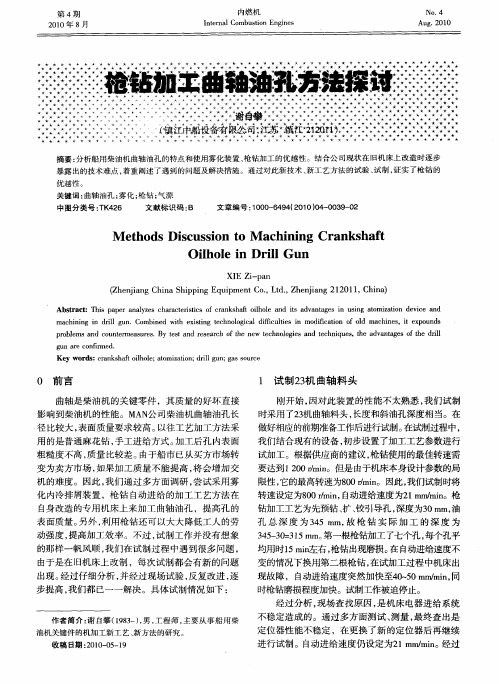
21年 8 00 月
内燃 机
I t r a o u t n E gn s n e n lC mb si n i e o
No .4
Au .201 g 0
摘要 : 分析船用柴油机 曲轴油孑 的特点和使用雾化装置 、 L 枪钻加 工的优越性 。结合公 司现状在旧机床上改造时逐步 暴露 出的技术难点 , 着重 阐述了遇到的问题及解决措施 。通过对此新技术 、 新工艺方法 的试 验 、 试制 , 证实 了枪钻的
★ ★ ★ ★ ★ ★ ★ ★ ★ ★
★
★
★ ★
^ ★ ★ ★ ★★ Nhomakorabea做好相应 的前期准备工作后进行试制 。 在试制 过程中 ,
★
我们结合现有的设备 , 初步设置了加工工艺参数进行 试加工。根据供应商的建议 , 枪钻使用的最佳转速需 要 达到 1 0 ri。但是 由于机床本 身设计 参数 的局 0r n 2 / a
★ ★ ★ ★ ★ ★ ★ ★ ★ ★ * ★ t ★ ★
★
★
★
★
★
★
★
★ ★ ★
变 为卖方 市场 , 如果 加 工质 量不 能提 高 , 将会 增加 交
机 的难度 。因此 , 们 通过 多方 面调 研 , 我 尝试 采用 雾
化 内冷排 屑装 置 ,枪 钻 自动进 给 的加工 工 艺方 法 在
自身改造 的专 用机 床上 来加 工 曲轴 油孔 ,提高孔 的 表 面质量 。 外 , 用枪 钻还 可 以大大 降低 工人 的劳 另 利 动强 度 , 高加 工效 率 。不过 , 制工 作 并没 有想 象 提 试 的那 样一 帆风顺 , 们在 试制 过 程 中遇 到很 多问题 , 我
曲轴油孔工作原理

曲轴油孔工作原理一、曲轴油孔的润滑作用曲轴油孔是曲轴内部油路的组成部分,它为曲轴提供润滑油,以减少摩擦和磨损。
通过曲轴油孔,润滑油可以顺畅地流到曲轴的各个部分,如轴承、轴颈等,形成一层油膜,起到润滑作用。
这可以大大降低曲轴在工作过程中的摩擦阻力,减少磨损,提高曲轴的使用寿命。
二、曲轴油孔的冷却作用除了润滑作用,曲轴油孔还具有冷却作用。
在曲轴的高速旋转过程中,摩擦会产生大量的热量,这些热量如果不能及时散出,将会对曲轴造成热损伤。
通过曲轴油孔,润滑油可以将摩擦产生的热量带走,并通过油底壳将热量散发到空气中,从而起到冷却作用。
三、曲轴油孔的清洁作用曲轴油孔还有清洁作用。
在润滑油流经曲轴的过程中,可以带走曲轴内部的杂质和污物,如金属屑、碳颗粒等。
这些杂质和污物如果留在曲轴内部,将会加速曲轴的磨损和损坏。
因此,通过曲轴油孔的润滑油清洁作用,可以保持曲轴内部的清洁,延长曲轴的使用寿命。
四、曲轴油孔的压力供油曲轴油孔通过一定的结构设计和压力调节,可以实现压力供油。
在发动机工作时,润滑系统会产生一定的压力,这个压力可以通过曲轴油孔传递到曲轴内部。
压力供油可以确保润滑油在曲轴内部的顺畅流动,并且能够根据曲轴的工作需要自动调节供油量,实现润滑油的合理分配。
五、曲轴油孔的油膜保护通过曲轴油孔流到曲轴各个部分的润滑油,会在相应的摩擦表面上形成一层油膜。
这层油膜可以起到保护作用,将金属表面与空气、水分等介质隔离,防止金属表面的氧化和腐蚀。
同时,油膜还可以减少金属间的直接接触,降低摩擦系数,减少因摩擦产生的热量,从而起到保护曲轴的作用。
综上所述,曲轴油孔的工作原理主要体现在润滑、冷却、清洁、压力供油和油膜保护等方面。
这些功能的正常发挥对于确保曲轴的正常运转和延长其使用寿命具有重要意义。
因此,在日常维护和保养过程中,需要关注曲轴油孔的状态,保证其畅通无阻,以保证发动机的正常运行。
- 1、下载文档前请自行甄别文档内容的完整性,平台不提供额外的编辑、内容补充、找答案等附加服务。
- 2、"仅部分预览"的文档,不可在线预览部分如存在完整性等问题,可反馈申请退款(可完整预览的文档不适用该条件!)。
- 3、如文档侵犯您的权益,请联系客服反馈,我们会尽快为您处理(人工客服工作时间:9:00-18:30)。
曲轴油孔加工过程中的问题及解决措施
一、深孔钻概念
在机械制造业中,一般将孔深超过孔径10倍的圆柱孔称为深孔。
深孔按扎深与孔径之比(L/D)的大小通常可分为一般深孔、中等深孔及特殊深孔3种。
1 L/D=10~20,属于一般深孔。
常在钻床或车床上用接长麻花钻孔加工。
2 L/D=20~30,属于中等深孔。
常在车床上加工。
3 L/D=30~100,属于特殊孔深。
必须使用深孔钻在深孔钻床或专用设备上加工。
二、深孔加工难点
1.不能直接观察到切削情况。
仅凭声音、看切削、观察机床负荷、油压等参数来判断排屑与钻头磨损情况。
2. 切削热不易传出。
3.排屑较困难,如遇切削阻塞则会引起钻头损坏。
4.因钻杆长、刚性差、易振动,会导致孔轴线偏斜,影响到加工精度及生产效率。
三、深孔加工类型(曲轴油孔工艺案例)
深孔钻的类型、使用范围及工作原理,深孔钻按排屑方式分为外派屑和内排屑2种,外排屑有枪钻、整体合金孔钻(可分为有冷却和无冷却孔2种):内排屑又分为BTA深孔钻、喷吸钻和DF系统深孔钻3种。
(下面我们来介绍下曲轴油孔工艺)
01、曲轴油孔工艺图纸
第一步:选择平底钻在曲轴的连杆或主轴曲面上铣出小平面(为后序引导钻提供基础平面)。
第二步:选择引导钻在连杆或主轴上钻入1.5D-2D的孔深(为后序深孔钻提供良好的导向和预钻准备)。
第三步:选择深孔钻头在已有的孔径上钻通该孔径。
第四步:(主轴/连杆颈)孔口倒角,去除孔口毛刺。
PS:曲轴油孔工艺一般分为两种类型,
1、交叉孔:连杆油孔和主轴油孔相互交叉。
(加工有难度)
2、直通孔:连杆有油孔,主轴无油孔。
上面描述的油孔工艺是很多工厂采用的普遍方式,也有的工厂把第一步和第二步合并了,用平底钻当做引导钻的方式进行预定心(这里不建议工厂采用这种形式),貌似加工的效率提高了,其实后面的刀具维护成本会增加,请注意。
(有需要油孔加工程序的可以联系小编我,提供程序供您研究)
02、曲轴油孔加工注意问题
一般平底钻和引导孔的长短很接近,在更换刀具的时候请操作者要看清楚,否则容易发生撞刀事件。
1.倒角钻在加工孔口倒角的时候,孔口倒角的大小会有差别,一般是新刀换刀后,一
般是刀具磨损剧烈情况,(换刀/程序中修改参数可以改正过来)。
2.MQL流量变小,这个会导致深孔钻断裂,产品报废,(点检可以发现这类问题,油
品日常的消耗也可以发现)。
3.修磨回来的深孔钻在装刀前,要看内冷孔是否有阻塞现象。
四、影响深孔加工的因素
1.深孔加工操作要点
主轴和刀具导向套、刀杆支撑套、工件支撑套等中心线的同轴度应符合要求;切削液系统应畅通正常;工件的加工端面上不应有中心孔,并避免在斜面上钻孔;切削形状应保持正常,避免生成直带状切削;采用较高速度加工通孔,当钻头即将钻透时,应降速或停机以防损坏钻头。
2.深孔加工切削液
深孔加工过程中会产生大量的切削热,并不易扩散,需要供给充足的切削液润滑冷却刀具。
一般选用1:100的乳化液或极压乳化液,需要较高加工精度和表面质量或加工韧性材料时,选用极压乳化液或高浓度极压乳化液,切削油的运动粘度通常选用(40)10~20 cm2/s,切削液流速为15~18 m/s ;加工直径较小时选用粘度低的切削油;要求精度高的深孔加工,可选用切削油配比为40%煤油+20%氯化石蜡。
切削液的压力和流量与孔径及加工方式有着密切的关系。
外排屑深孔钻切削液的压力与流量
孔径/mm
压力/Mpa
流量/(L/min)
4-10
2.5-6
8-20
10-15
2-5
20-30
15-20
1.5-4.5
30-40
25-20
1.5-4
40-50
25-30
1.5-3
50-60
内排屑深孔钻切削液的压力与流量
孔径/mm
压力/Mpa
流量/(L/min)
8-15
5-6.5
20-50
15-25
4-5.5
50-70
25-35
3-4.5
70-100
35-45
2.5-4.5
100-125
45-80
2-3
125-200
3.使用深孔钻注意事项
3.1加工端面与工件轴心线垂直,以保证端面密封可靠。
3.2正式加工前在工件孔位上预钻1个浅孔,引钻时可起导向定心作用。
3.3为保证刀具使用寿命,最好采用自动走到。
3.4 进液器、活动中心支承中的各导向元件如有磨损,应及时更换,以免影响钻孔精度。