机械制造基础 第2章 金属塑性成形技术
工程材料与机械制造基础课件:塑性成形-

2)雙晶: 雙晶亦叫孿晶。雙晶是晶體在外力作用下晶格的一部
分相對另一部分發生轉動。 未變形部分和變形部分的交界面稱為雙晶面。在雙晶
面兩側形成鏡面對稱,如圖3-3所示。
3.1.1 塑性成形的實質
雙晶面
在鍛壓生產中,還應注意使鍛造流線盡可能沿著零件的外形 輪廓分佈,並在切削加工過程中保持鍛造流線不被切斷,使材料 的力學性能得到最充分的發揮。
如圖3-8a)為模鍛鉤,流線分佈合理,使用壽命長,且材料 消耗少,而圖3-8b)是用板材直接切削加工出的拖鉤,拖鉤內側流 線組織被切斷,使用時容易沿切斷處斷裂。
塑性成形 概述
常見的塑性加工方法:
P
P
1 1
2
2
3
3
P 1
2
3
4
a) 自由鍛
b) 模鍛
c) 擠壓
1. 錘頭 2. 坯料 3. 下抵鐵 1. 上模 2. 坯料 3. 下模 1. 擠壓筒 2. 沖頭3. 坯料 4. 擠壓凹模
塑性成形 概述
1
1
1
2
2
2
3
4
d) 拉拔
1. 拉拔模 2. 坯料
e) 軋製
1. 軋輥 2. 坯料
一般金屬的某一質點移動時阻力最小的方向是通 過該質點向金屬變形部分的周邊所作的法線方向,因 為質點沿此方向移動的距離最短,所需的變形功最小。
3.1.4 塑性成形基本規律
2. 最小阻力定律
塑性變形時金屬各質點首先向阻力最小方向移動, 稱為最小阻力定律。
一般金屬的某一質點移動時阻力最小的方向是通 過該質點向金屬變形部分的周邊所作的法線方向,因 為質點沿此方向移動的距離最短,所需的變形功最小。
金属塑性成形课件

2023-11-06•金属塑性成形概述•金属塑性成形工艺•金属塑性成形设备•金属塑性成形技术的发展趋势•金属塑性成形过程中的缺陷与质量控制目•金属塑性成形实例分析录01金属塑性成形概述金属塑性成形是一种使金属材料发生塑性变形,以获得所需形状、尺寸和性能的加工方法。
金属塑性成形广泛应用于机械制造、航空航天、汽车、电子等领域,是一种重要的材料加工技术。
金属塑性成形的定义金属塑性成形可以制造出复杂形状的零件,并且能够获得较高的精度和表面质量。
与切削加工相比,金属塑性成形具有更高的材料利用率和更低的能耗。
金属塑性成形过程中材料的变形是均匀的,因此可以避免应力集中和裂纹等缺陷。
金属塑性成形的特点03金属塑性成形的基本原理包括应力状态、屈服准则、塑性流动规律等。
金属塑性成形的基本原理01金属塑性成形的原理是基于金属的塑性变形规律,即在外力作用下,金属材料会发生形状和尺寸的变化。
02在金属塑性成形过程中,材料的变形受到应力状态、变形温度、变形速度等因素的影响。
02金属塑性成形工艺自由锻工艺自由锻是利用冲击力或静压力使金属坯料变形,并施加外力将其锻造成所需形状和尺寸的锻造方法。
定义特点流程应用自由锻具有较大的灵活性,可以生产形状各异的锻件,但生产效率较低,适用于单件或小批量生产。
自由锻的流程包括坯料准备、加热、变形和锻后冷却。
自由锻主要用于大型锻件和难变形材料的加工,如轴、轮毂、法兰等。
模锻工艺模锻是利用模具使金属坯料变形,并施加外力将其锻造成所需形状和尺寸的锻造方法。
定义模锻具有较高的生产效率,且能获得较为精确的形状和尺寸,但模具制造成本较高。
特点模锻的流程包括坯料准备、加热、放入模具、变形、锻后冷却和修整。
流程模锻广泛应用于中小型锻件的生产,如齿轮、轴套、法兰等。
应用板料冲压工艺板料冲压是利用冲压机将金属板料变形,并施加外力将其冲制成所需形状和尺寸的加工方法。
定义板料冲压具有较高的生产效率,且能获得较为精确的形状和尺寸,但模具对材料的厚度和硬度有一定要求。
《金属塑性成形方法》课件
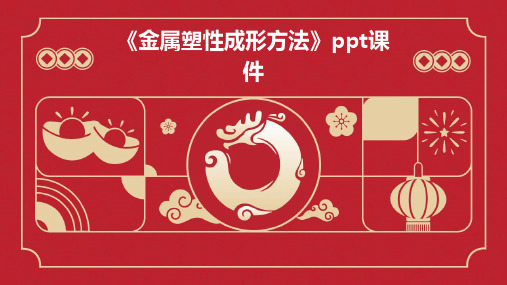
目录
CONTENTS
• 金属塑性成形方法简介 • 金属塑性成形的基本原理 • 金属塑性成形的主要方法 • 金属塑性成形的质量控制 • 金属塑性成形技术的发展趋势
01 金属塑性成形方法简介
CHAPTER
金属塑性成形的基本概念
金属塑性成形是一种通过施加外 力使金属材料发生塑性变形,从 而获得所需形状和性能的加工方
大型金属件和复杂形状的金属件制造,如轴、齿轮、连杆等。
模型锻造
要点一
总结词
通过将金属坯料放置在模具中,在高温和高压下使其发生 塑性变形,从而获得所需形状和尺寸的金属件。
要点二
详细描述
模型锻造是一种常见的金属塑性成形方法,通过将金属坯 料放置在模具中,在高温和高压下使其发生塑性变形,从 而获得所需形状和尺寸的金属件。模型锻造过程中,金属 坯料在高温和高压下发生变形,内部晶粒结构发生变化, 从而提高了金属的力学性能。模型锻造适用于中小型金属 件制造,如齿轮、轴承、气瓶等。
过程稳定可控。
在线检测
采用先进的在线检测技术,对成形 过程中的产品进行实时检测,及时 发现并处理问题。
成品检测
对成形后的产品进行全面的检测, 包括尺寸、外观、性能等,确保产 品质量符合要求。
05 金属塑性成形技术的发展趋势
CHAPTER
高性能金属材料的开发与应用
高强度钢
通过合金化、热处理等手段提高 钢材的强度和韧性,用于制造轻
流动法则与加工硬化
流动法则是描述金属在塑性成形过程中应力的分布规律。加工硬化是指 在塑性成形过程中,随着变形的进行,材料的强度和硬度逐渐提高的现 象。
金属塑性变形的工艺基础
塑性成形的基本方法
材料成型工艺基础-金属塑性成形课件
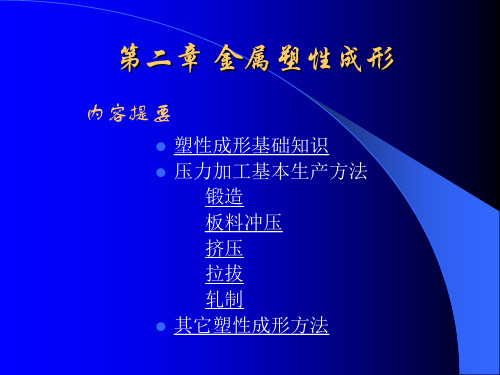
扩展市场,开发未来,实现现在。202 0年12 月8日星 期二上 午12时 44分36 秒00:4 4:3620. 12.8
做专业的企业,做专业的事情,让自 己专业 起来。2 020年1 2月上 午12时4 4分20. 12.800:44December 8, 2020
人生不是自发的自我发展,而是一长 串机缘 。事件 和决定 ,这些 机缘、 事件和 决定在 它们实 现的当 时是取 决于我 们的意 志的。2 020年1 2月8日 星期二 12时44 分36秒 Tuesday , December 08, 2020
感情上的亲密,发展友谊;钱财上的 亲密, 破坏友 谊。20. 12.8202 0年12 月8日星 期二12 时44分 36秒20 .12.8
4.冷镦
2.5其他成形
冷镦机
2.5其他成形
每一次的加油,每一次的努力都是为 了下一 次更好 的自己 。20.12. 820.12. 8Tuesd ay , December 08, 2020
天生我材必有用,千金散尽还复来。0 0:44:36 00:44:3 600:44 12/8/20 20 12:44:36 AM
五、锻件的结构工艺性
轴类零件 杆类零件 盘类零件
2.2自由锻
§3 模锻
一、模锻方式
锤上模锻 压力机上模锻 胎模锻
蒸汽 - 空气锤
锤上模锻
2.3模 锻
锻模结构
2.3模 锻
思考题
2.3模 锻
模锻能否直接锻出通孔?
二、模锻工序
2.3模 锻
形状简单的零件: 预锻→终锻→清理
形状较复杂或锻造比大的零件: 制坯→预锻→终锻→清理 连杆锻模 曲轴模锻
机械制造基础 第2章-锻压1可锻性
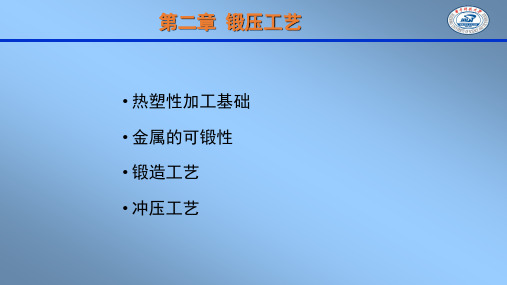
2.1 热塑性加工基础
2.1.3 纤维组织、流线与锻造比
➢ 钢锭开坯 热加工生产采用的原始坯料是铸锭。其内部组织很不均匀,晶粒较粗大,并存
在气孔、缩松、非金属夹杂物等缺陷。铸锭加热后经过热加工,由于塑性变形及再 结晶,从而改变了粗大、不均匀的铸态结构,获得细化了的再结晶组织。同时还可 以将铸锭中的气孔、缩松等压合在一起,使金属更加致密,力学性能得到很大提高 。
第二章 锻压工艺
• 热塑性加工基础 • 金属的可锻性 • 锻造工艺 • 冲压工艺
概述
1. 你知道枪管、炮管是如何制造的吗?什么是来复线?它是如何制造的? 来复线是径向锻造的。
概述
利用金属在外力作用下所产生的塑性变形,来获得具有一定形状、尺 寸和机械性能的原材料、毛坯或零件的生产方法,称为金属塑性成型(也 称为压力加工)。
压力加工中作用在金属坯料上的外力主要有两种:冲击力和静压力。 锤类设备产生冲击力,轧机与压力机设备产生静压力。 金属塑性成型的基本生产方法有以下几种:
压力加工工艺
各种块体压力加工工艺
各种板料冲压工艺
各种加工方法的应用范围
• 轧制、挤压、拉拔
主要用于金属型材、板材、
钢材和线材等原材料。
• 锻造 用于承受重载荷的机器零件,如机器的 主轴、重.1.2 冷变形与热变形
2.热变形: 在再结晶温度以上的变形。变形后,金属具有再结晶组织、而无加工硬化痕迹。
也称热加工。 ➢ 优点:金属能以较小的功达到较大的变形,加工尺寸较大和形状比较复杂的工件, 同时获得具有高机械性能的再结晶组织。 ➢ 缺点:金属表面容易形成氧化皮,而且产品尺寸精度和表面质量较低,劳动条件 和生产率也较差。
• 板料冲压 广泛用于汽车制造、电器、仪表及日 用品工业等方面。
机械制造基础第三版课后答案
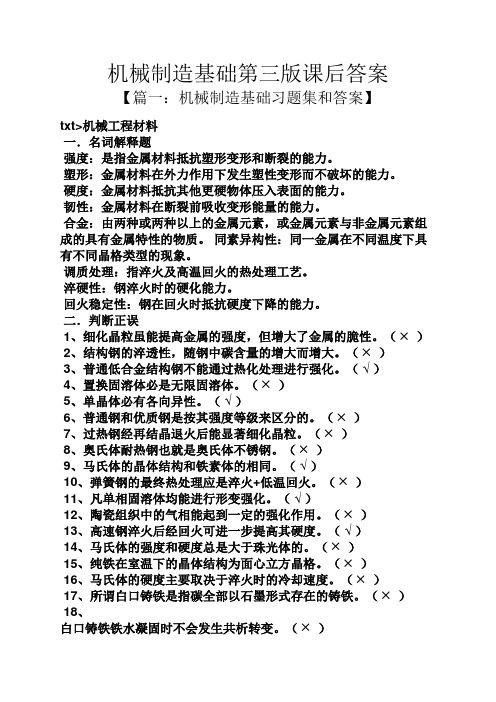
机械制造基础第三版课后答案【篇一:机械制造基础习题集和答案】txt>机械工程材料一.名词解释题强度:是指金属材料抵抗塑形变形和断裂的能力。
塑形:金属材料在外力作用下发生塑性变形而不破坏的能力。
硬度:金属材料抵抗其他更硬物体压入表面的能力。
韧性:金属材料在断裂前吸收变形能量的能力。
合金:由两种或两种以上的金属元素,或金属元素与非金属元素组成的具有金属特性的物质。
同素异构性:同一金属在不同温度下具有不同晶格类型的现象。
调质处理:指淬火及高温回火的热处理工艺。
淬硬性:钢淬火时的硬化能力。
回火稳定性:钢在回火时抵抗硬度下降的能力。
二.判断正误1、细化晶粒虽能提高金属的强度,但增大了金属的脆性。
(╳)2、结构钢的淬透性,随钢中碳含量的增大而增大。
(╳)3、普通低合金结构钢不能通过热化处理进行强化。
(√ )4、置换固溶体必是无限固溶体。
(╳)5、单晶体必有各向异性。
(√ )6、普通钢和优质钢是按其强度等级来区分的。
(╳)7、过热钢经再结晶退火后能显著细化晶粒。
(╳)8、奥氏体耐热钢也就是奥氏体不锈钢。
(╳)9、马氏体的晶体结构和铁素体的相同。
(√ )10、弹簧钢的最终热处理应是淬火+低温回火。
(╳)11、凡单相固溶体均能进行形变强化。
(√ )12、陶瓷组织中的气相能起到一定的强化作用。
(╳)13、高速钢淬火后经回火可进一步提高其硬度。
(√ )14、马氏体的强度和硬度总是大于珠光体的。
(╳)15、纯铁在室温下的晶体结构为面心立方晶格。
(╳)16、马氏体的硬度主要取决于淬火时的冷却速度。
(╳)17、所谓白口铸铁是指碳全部以石墨形式存在的铸铁。
(╳)18、白口铸铁铁水凝固时不会发生共析转变。
(╳)19、铸件可用再结晶退火细化晶粒。
(√ )20、冷热加工所形成的纤维组织都能使金属出现各向异性。
(√ )21、奥氏体的塑性比铁素体的高。
(√ )22、白口铸铁在室温下的相组成都为铁素体和渗碳体。
(√ )23、过共析钢的平衡组织中没有铁素体相。
金属塑性成形课件

要点二
高强度材料加工
挤压和拉拔适用于高强度材料的加工,如高强度钢、钛合金等,可以获得高精度、高质量的制品。
模具成本高
挤压和拉拔使用的模具制造较为复杂,成本较高,同时生产效率较低。
要点三
连续变形加工
锻造和轧制是两种连续变形加工的方法,锻造是通过冲击、静压等手段将金属坯料变形,而轧制则是将金属坯料放入轧辊中,通过旋转轧辊使金属变形并获得所需形状和尺寸的制品。
确定合理的变形程度,以充分利用材料的塑性潜力,同时避免材料开裂和变形过大。
合理控制应变速率,以实现材料的均匀变形和避免局部过快变形。
03
工艺参数的选择和控制
02
01
成形过程的模拟和仿真
模拟软件选用
选择适合的数值模拟软件,如有限元法或有限差分法等,对成形过程进行仿真和分析。
模拟精度控制
根据实际需要,提高模拟精度,以更准确地预测成形过程中的各种问题和缺陷。
成形方案优化
通过模拟和仿真,优化成形方案,提高生产效率和产品质量。
01
03
02
根据产品的特点和成形工艺的要求,选择适合的检测方法,如力学性能测试、金相分析、X射线检测等。
产品质量的检测和分析
检测方法选择
对检测结果进行误差分析,找出影响检测结果的主要因素,提出相应的控制措施。
误差分析和控制
根据产品质量检测结果,对产品结构进行优化,提高产品质量和使用性能。
产品结构优化
设备升级改造
针对成形过程中的设备和工艺装备进行升级改造,提高设备的自动化程度和生产效率。
工艺流程优化
通过对成形过程的各阶段进行全面分析,找出瓶颈和不足之处,提出相应的优化措施。
节能减排措施
采取节能减排措施,降低成形过程中的能源消耗和环境污染,实现绿色生产。
机械制造基础-塑性成形
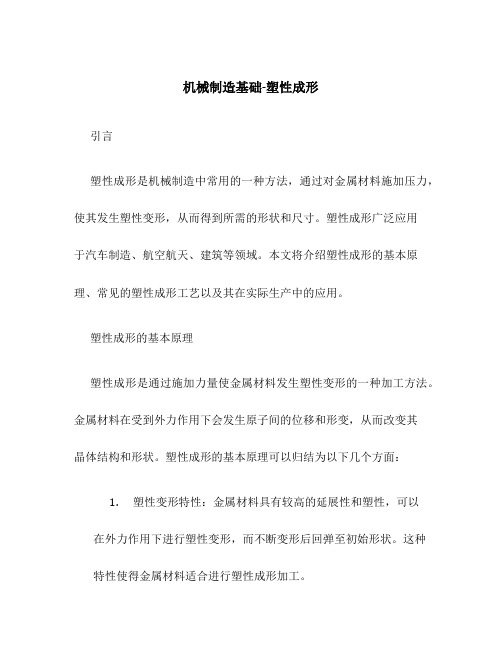
机械制造基础-塑性成形引言塑性成形是机械制造中常用的一种方法,通过对金属材料施加压力,使其发生塑性变形,从而得到所需的形状和尺寸。
塑性成形广泛应用于汽车制造、航空航天、建筑等领域。
本文将介绍塑性成形的基本原理、常见的塑性成形工艺以及其在实际生产中的应用。
塑性成形的基本原理塑性成形是通过施加力量使金属材料发生塑性变形的一种加工方法。
金属材料在受到外力作用下会发生原子间的位移和形变,从而改变其晶体结构和形状。
塑性成形的基本原理可以归结为以下几个方面:1.塑性变形特性:金属材料具有较高的延展性和塑性,可以在外力作用下进行塑性变形,而不断变形后回弹至初始形状。
这种特性使得金属材料适合进行塑性成形加工。
2.金属的流动性:金属材料具有较好的流动性,即在塑性变形过程中,金属材料可以顺应应力分布的变化,在不同部位形成不同的变形形状。
这种流动性使得金属材料能够通过塑性成形加工来实现复杂的形状和结构。
3.应力与应变的关系:金属材料在受到外力作用下,会引起其内部产生应力,从而引起形变。
应力与应变之间的关系可以通过应力-应变曲线来表示,该曲线可以描述金属材料在不同应力下的塑性变形特性。
常见的塑性成形工艺塑性成形工艺根据其加工原理和特点的不同,可以分为压力成形和非压力成形两大类。
压力成形是通过施加压力使金属材料发生塑性变形的一种成形方式。
常见的压力成形工艺包括冲压、压铸、锻造等。
1.冲压:冲压是通过将金属材料放置在冲压模具中,并施加较大的冲击力使金属材料在模具中发生塑性变形。
冲压工艺可以实现高质量的金属零件加工,并能够高效率地进行批量生产。
2.压铸:压铸是通过将熔化的金属材料注入到压铸模具中,并施加高压将金属材料填充至模具中的空腔中,然后冷却固化,最终得到所需的零件形状。
压铸工艺适用于制造复杂形状的零件,可以获得高度精密的产品。
3.锻造:锻造是通过施加压力使金属材料发生塑性变形的一种成形方式。
锻造工艺分为冷锻和热锻两种。
- 1、下载文档前请自行甄别文档内容的完整性,平台不提供额外的编辑、内容补充、找答案等附加服务。
- 2、"仅部分预览"的文档,不可在线预览部分如存在完整性等问题,可反馈申请退款(可完整预览的文档不适用该条件!)。
- 3、如文档侵犯您的权益,请联系客服反馈,我们会尽快为您处理(人工客服工作时间:9:00-18:30)。
组织:与冷变形后基本形同;性能:保留高的强度和塑性
2)再结晶
T再 =( 0.35~0.4)T熔 (K) 纯金属
再结晶:加热到较高温度时,原子扩散能力增强,在金属 内部重新排列,形成新的晶粒取代冷变形中已变形的晶粒。
组织:恢复到冷变形前的状态;性能:加工硬化消除
2.辅助工序 为方便基本工序的操作,先对坯料进行少量的变形,如
压肩、压钳口、倒棱等; 3.精整工序
为使锻件尺寸、表面合格,基本工序后应用的工序,如 校正、滚圆、表面平整等。
二、自由锻基本工序
圆饼类基零件本工序 — 完成锻件基本变形和成形的工序。
1. 礅粗: H ,S
轴杆类零件
2. 拔长: L ,S
形变亚晶粒示意图
5%冷变形纯铝中的位错网
(3)产生变形织构 当塑性变形很大时,多数晶粒的晶格位向会趋于一
致,这种现象称为择优取向或称变形织构。
● 产生织构后:性能有方向性,纵优于横,一般不利(如冲 压时的制耳现象)
无
有
各向异性导致的铜板 “制耳”
2 力学性能影响
(1)加工硬化
金属随着变形量增多,表现出强度、硬度显著升高,塑性、 韧性下降,这种现象称为加工硬化,亦称形变强化。
3.不利于继续变形—须用再结晶退火消除之。
(2)残余内应力
由于变形不均匀而残留在金属内部的应力。 残余应力的存在会对构件的强度、刚度、稳定性及抗疲劳 等性能产生影响。
二、 温度对冷变形后金属组织和性能的影响
1) 回复 T回 =(0.25~ 0.3)T熔 (K) 加热温度不高时,冷变形金属原子扩散能力不强,只能
1) 定在最大截面处; (如图a则无法出模) 2) 深度最浅易充型; (图中b充型难) 3) 错模现象易检查; (图中c不易查错模) 4) 平面分型易制造。 (图中的d面较合理)
分模面选择的特殊要求 1)对于头部尺寸显著偏大的锻件,选用曲面分模而
不用平面分模,保证上下模膛深度大致相同,利于充型。
(a)不合理
三、热变形组织
组织致密------缩孔缩松被压合 出现锻造流线------纤维组织(热变形使晶粒和分
布在晶界上的非金属夹杂物被拉长,拉上的晶粒经再结 晶变成等轴晶,而夹杂物形状保留下来)
合理利用锻造流线的分布
(零件工作时承受的最大拉应力 的方向与纤维方向平行;切应 力方向与纤维方向垂直;并且 纤维方向尽量与零件的外形轮 廓相符而不被切断)
a)
b)
c)
合理的锻造流线分布
a)模锻制造曲轴 b)局部镦粗法制造螺栓 c)轧制齿形制造齿轮
冷变形、热变形与温变形
热变形 以上 T再 以下 冷变形
冷变形 低于该金属再结晶温度的变形,变形将伴
随出现加工硬化
热变形 高于该金属的再结晶温度的变形,亦称热
变形。热变形过程产生的加工硬化被随后的回复与 再结晶的软化消除,使金属保持高塑性状态。
铸件有铸造缺陷,易产生应力集中; c. 压力加工可产生形变强化和纤维组织。
2、塑性成形的成形性差于铸造 铸造 : 液态成型,易生产形状复杂零件;
专用设备,设备吨位大; 锻压 : 固态成型 塑性变形难
生产零件形状简单
3、塑性成形的适用材料少于铸造件 高塑性合金:纯金属,单相固溶体合金,化合物极
少的合金
延 伸率 % 冲击韧度/J cm -2
HB 强 度极 限/MPa
加工硬化是强化金属的重要途径,加工硬化的本质是位错在
晶界处的塞积。
产生原因: 位错运动、互相交割→塞积、割阶、 固定、缠结等 → 阻碍位错进一步 运动→变形抗力↑
360 320 280 240 200 160 120 80 40
0
700
零件轮廓
锻件尺寸、公差
以粗实线表示锻件形状,双点划线表示零件形状 并将零件尺寸注在锻件相应尺寸线下面的括号内
2. 计算坯料的质量和尺寸 ① 根据锻件图计算体积:
V锻件= V1 + V2 + ……
② 根据V件计算锻件质量和坯料质量(M坯)
M锻件 = V锻件× ρ (Kg)
( ρ— 密度 碳钢 ρ = 7.85g/cm3)
2.1.2 金属变形过程的组织和性能 一、冷变形后金属的组织与性能 1、组织变化
(1)晶粒拉长 当变形量很大,晶粒沿变形方向
拉长呈纤维状,这种组织称为纤维组织。
冷变形前后的晶粒形状示意图
(2) 晶粒细化、位错密度增加
滑移面附近晶格严重扭曲,存在大量残余应力,并出现大量 的碎晶,增大位错的数目和滑移阻力—强度、硬度↑塑形、韧性↓
更接近锻
件形状
锻件形状
例:连杆模锻
弯曲连杆
2.2.3 胎模锻
定义:胎模锻是在自由锻设备上使用活动单膛模具生产
模锻件的工艺方法。 工艺:自由锻预锻→胎膜锻成形
与自由锻比较具有的特点:
(1)操作简便,生产率高,对工人技术要求不高。 (2)锻件形状、尺寸精度高,敷料少、加工余量小。 (3)内部组织致密,纤维组织分布更符合性能要求。
强度极 限 600
220
布氏硬度
500
180 400 160 300
延 伸率 % 冲击韧度
140 200 120 100
0
20 40 60
80
%
变形程度
冷塑性变形对低碳钢力学性能的影响
加工硬化的意义: 1.使压力加工制品截面均匀;
2.提高金属强度、硬度和耐磨性。 ——不能热处理强化的纯金属和某些合金
蒸汽料—变空形气锤 630Kg~5T
水压机(吨位最大,300T)
压力机
油压机
巨型锻件的唯
一成形设备
锻锤吨位 = 落下部分总重量 = 活塞+锤头+锤杆 压力机吨位 = 滑块运动到下始点时所产生的最大压力
自由锻工序
1.基本工序 使坯料完成主要变形的工序称为基本工序,常用的有镦粗、
拔长、冲孔、扩孔、弯曲、切割、扭转、错移和锻接等;
(b)合理
2)有流线方向要求的锻件,流线方向应与切应力垂
直,避免切断流线组织。
(a)不合理
(b)合理
② 确定加工余量、公差及工艺余块 通常按照锻锤吨位确定,可查手册(同自由锻件)
加工余量: 1公~差4m:m0.3~3mm
比自由锻小得多
工艺余块:成批生产,少加或不加
③ 模锻斜度 一般为 5-15°,
1、绘制锻件图
绘制锻件图时应考虑: 1.敷料,又称:余块,
目的:填平补齐简化工艺 2.加工余量
便于切削留余地 3.锻件公差
留给锻工操作余地 4.设计模锻斜度和圆角 绘图注意事项
①粗实线表示锻件轮廓; ②双点线表示零件; ③尺寸线上下数字表示尺寸:
线上:锻件尺寸和公差 线下:零件尺寸加括号
锻件轮廓
与模锻比较具有的特点:
(1)设备简单。 (2)工艺灵活,可以局部成形。 (3)胎具简单,制造容易。
胎模的种类
常用来非回转体锻 件的成形或制坯
端面凸台或凹坑的回转 体制坯
2.2.4 锻造工艺及结构设计
2.2.4.1 自由锻的锻造工艺
自由锻工艺规程的制定 1. 绘制锻件图 2. 计算坯料的质量和尺寸 3. 确定变形工序 4. 选择设备吨位 5. 确定锻造加热温度、火次和冷却方式 6. 制定(填写)工艺卡
M M M M 坯料 = 锻件+ 氧化 + 切除
M氧化取锻件质量的2%~3%(首次加热),以后每 次加热1.5%~2% ;
M切除取锻件质量的2%~4%
③ 选择坯料体积(V坯 )和长度(Ho)
V坯 = M坯 /ρ
Ho = V坯/S坯
S坯 —— 选用的坯料截面积 (cm2)
镦粗件坯料长度 1.25 Do ≤ Ho ≤ 2.5 Do
第二章 金属的塑性成形
教学要求:
本章是材料成型的重要工艺,要求掌握: 1. 各种锻压方法的原理、特点及适用范围; 2. 常用锻压方法的选择原则及应用; 3. 常用锻压方法的工艺规程及结构工艺设计 。
2.1 金属塑性成形的工艺基础 2.1.1 金属塑性成形工艺的种类 一、塑性成形的定义:
在外力作用下通过塑性变形生产所需形状和尺寸的 零件或毛坯的工艺方法。
模膛深度与宽度之比(h/b)越大,斜度取越大
④ 模锻圆角半径:
作用:易于充满模腔,便于取模;避免应力集中,提高模 具寿命。
外圆角半径γ取1.5~12mm 内圆角半径 R比γ大2-3倍 模膛深度 h 越大,圆角半径取值越大
⑤ 冲孔连皮厚度 (δ)(详见专业手册)
太厚: 浪费金属、冲孔时锻件易变形。 太薄: 锤击力太大,模具易压塌或加速磨损。
钢中含碳量和Me含量越高,锻件形状越复杂,尺寸越大, 冷却速度要越慢。有空冷、坑冷、炉冷。 ③ 锻后热处理:
6. 制定(填写)工艺卡
2.2.4.2 锤上模锻工艺设计
一、绘制锻件图
① 选择分模面 分模面即上下模锻件上的分界面。
锤头
模膛
上模
飞边槽
分模面parting plane 下模
模垫
分模面选择的基本原则:
2.2 金属塑性变形工艺
2.2.1 自由锻造(Open Die forging)
简称自由锻,是金属沿变形方向可以自由流动的锻造方法
上砥铁
坯料 下砥铁
自由锻特点
1. 工具简单,通用性好 2. 操作灵活适应广泛; 3. 大型锻件唯一方法。
自由利用锻冲击设力备使 与吨位
坯料变形
空气锤 65~750Kg 锻锤 利用压力使坯
二、塑性成形的主要生产方式及应用
应用 (1)力学性能要求较高的零件(重载荷、变载荷、受冲击的零
件),如传动零件------锻造; (2)薄壁零件,如汽车外壳、车门、飞机结构件-----冲压; (3)型材、棒材、板材、线材及各种管材-----轧制、挤压、拉