锅炉供热控制系统设计
锅炉温度PID控制系统设计
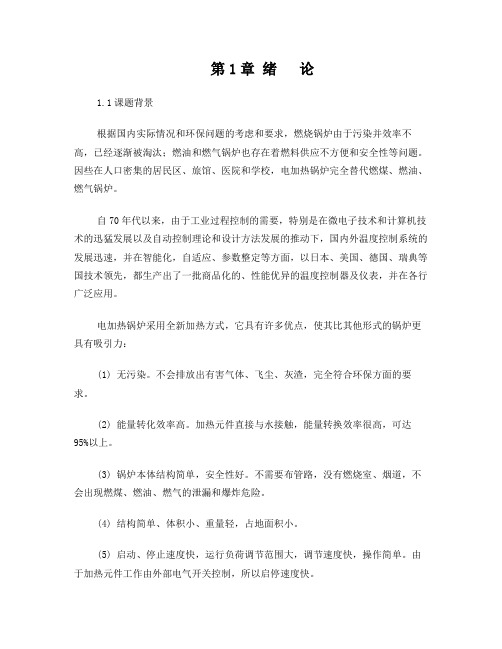
第1章绪论1.1课题背景根据国内实际情况和环保问题的考虑和要求,燃烧锅炉由于污染并效率不高,已经逐渐被淘汰;燃油和燃气锅炉也存在着燃料供应不方便和安全性等问题。
因些在人口密集的居民区、旅馆、医院和学校,电加热锅炉完全替代燃煤、燃油、燃气锅炉。
自70年代以来,由于工业过程控制的需要,特别是在微电子技术和计算机技术的迅猛发展以及自动控制理论和设计方法发展的推动下,国内外温度控制系统的发展迅速,并在智能化,自适应、参数整定等方面,以日本、美国、德国、瑞典等国技术领先,都生产出了一批商品化的、性能优异的温度控制器及仪表,并在各行广泛应用。
电加热锅炉采用全新加热方式,它具有许多优点,使其比其他形式的锅炉更具有吸引力:(1) 无污染。
不会排放出有害气体、飞尘、灰渣,完全符合环保方面的要求。
(2) 能量转化效率高。
加热元件直接与水接触,能量转换效率很高,可达95%以上。
(3) 锅炉本体结构简单,安全性好。
不需要布管路,没有燃烧室、烟道,不会出现燃煤、燃油、燃气的泄漏和爆炸危险。
(4) 结构简单、体积小、重量轻,占地面积小。
(5) 启动、停止速度快,运行负荷调节范围大,调节速度快,操作简单。
由于加热元件工作由外部电气开关控制,所以启停速度快。
(6) 可采用计算机监控,完全实现自动化。
其温度的控制都能通过微控制芯片完成,使锅炉的运行完全实现自动化,最大程度地将控制器应用于传统的锅炉行业。
本课题主要研究锅炉温度的过程控制。
新型锅炉是机电一体化的产品,可将电能直接转化成热能,具有效率高,体积小,无污染,运行安全可靠,供热稳定,自动化程度高的优点,是理想的节能环保的供暖设备。
加上目前人们的环保意识的提高,电热锅炉越来越受人们的重视,在工业生产和民用生活用水中应用越来越普及。
电热锅炉目前主要用于供暖和提供生活用水。
主要是控制水的温度,保证恒温供水。
随着计算机和信息技术的高速发展,单片机广泛的应用于工业控制中。
工业控制也越来越多的采用计算机控制,在这里我们采用51系列单片机来做控制器。
锅炉供暖控制系统设计
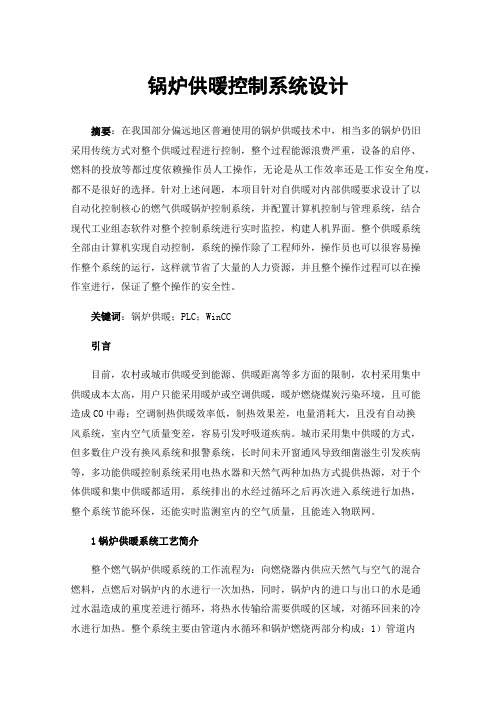
锅炉供暖控制系统设计摘要:在我国部分偏远地区普遍使用的锅炉供暖技术中,相当多的锅炉仍旧采用传统方式对整个供暖过程进行控制,整个过程能源浪费严重,设备的启停、燃料的投放等都过度依赖操作员人工操作,无论是从工作效率还是工作安全角度,都不是很好的选择。
针对上述问题,本项目针对自供暖对内部供暖要求设计了以自动化控制核心的燃气供暖锅炉控制系统,并配置计算机控制与管理系统,结合现代工业组态软件对整个控制系统进行实时监控,构建人机界面。
整个供暖系统全部由计算机实现自动控制,系统的操作除了工程师外,操作员也可以很容易操作整个系统的运行,这样就节省了大量的人力资源,并且整个操作过程可以在操作室进行,保证了整个操作的安全性。
关键词:锅炉供暖;PLC;WinCC引言目前,农村或城市供暖受到能源、供暖距离等多方面的限制,农村采用集中供暖成本太高,用户只能采用暖炉或空调供暖,暖炉燃烧煤炭污染环境,且可能造成CO中毒;空调制热供暖效率低,制热效果差,电量消耗大,且没有自动换风系统,室内空气质量变差,容易引发呼吸道疾病。
城市采用集中供暖的方式,但多数住户没有换风系统和报警系统,长时间未开窗通风导致细菌滋生引发疾病等,多功能供暖控制系统采用电热水器和天然气两种加热方式提供热源,对于个体供暖和集中供暖都适用,系统排出的水经过循环之后再次进入系统进行加热,整个系统节能环保,还能实时监测室内的空气质量,且能连入物联网。
1锅炉供暖系统工艺简介整个燃气锅炉供暖系统的工作流程为:向燃烧器内供应天然气与空气的混合燃料,点燃后对锅炉内的水进行一次加热,同时,锅炉内的进口与出口的水是通过水温造成的重度差进行循环,将热水传输给需要供暖的区域,对循环回来的冷水进行加热。
整个系统主要由管道内水循环和锅炉燃烧两部分构成:1)管道内水循环:自来水经过过滤软化处理以后,经由分水器进入供暖管道内部,送入锅炉中,进行加热后,经由换热泵管网送至用户处用于取暖。
经由用户出散热后,经过换热站,再次经由循环泵管网送至锅炉内加热。
基于PLC和FCS集中供热锅炉控制系统设计
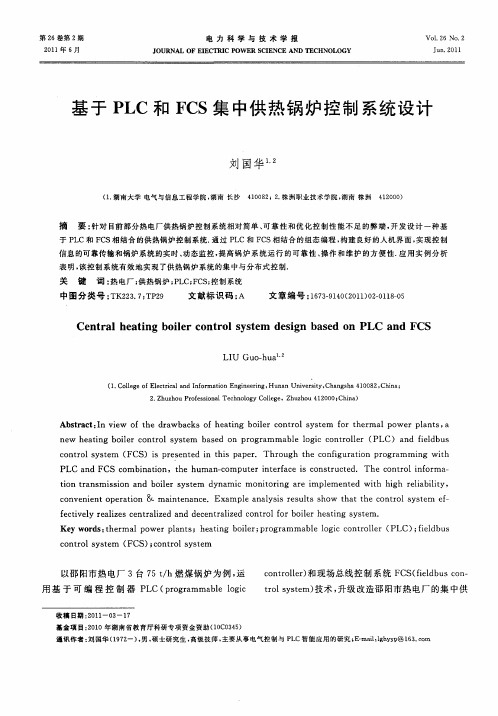
Ab ta t I iw f t e d a a k f h a i g b i r c n r l s s e f r t e ma o r p a t , sr c :n v e o h r wb c s o e tn o l o t o y t m o h r lp we ln s a e
P n LC a d FCS c mb n t n h u n c mp t r i t r a e i c n t u t d Th o t o n o ma o i a i 。t e h ma — o u e n e f c S o s r c e . o e c n r li f r — to r n mi so n o l r s se d n m i m o i rn r mp e n e t i h r l b l y i n t a s s i n a d b i y t m y a c e n t i g a e i l me t d wi h g e i i t , o h a i
LI GU — u U O h a ・
( . l g fElcre 1a d I fr ainEn ie rn H u a iest , a g h 1 0 2, ia; 1 Col e0 e tia n non s a4 0 8 Chn e
第 2 6卷 第 2期 2 1 年 6月 01
电 力 科 学 与 技 术 学 报
J oURNAL OF ECTRI P EL C OW E S ENCE AND R CI TEeHNOL OGY
常压热水锅炉房供热系统设计

常压热水锅炉房供热系统设计常压热水锅炉有其一定的优点,同时也给系统设计、运行带来了一系列的问题,其不可承压的特殊性要求,使常压热水锅炉房的设计与承压锅炉房有较大的不同,但这些问题在得到充分重视的前提下,扬长避短,就能保证供热系统安全可靠的运行。
常压热水锅炉供热系统受到了越来越多的关注和应用,尤其在局部供暖中的应用显得更加突出。
标签:常压热水锅炉房;供热系统设计前言常压热水锅炉无需专门的安全检验、性价比较高、运行安全可靠,近年来在港口工程的供热系统设计中越来越多的用户要求采用常压热水锅炉。
近20 年来,为节约投资、修旧利废,常压热水锅炉应用于采暖及生活热水系统迅速发展,常压热水锅炉也成为一种新型热源,并且用量也越来越大。
常压热水锅炉又称为无压热水锅炉,该锅炉运行时锅筒内保持大气压力,供应不大于95℃的热水,一、常压热水锅炉的特点常压热水锅炉是指锅炉本体开孔或者用连通管与大气相通,在任何情况下,锅炉本体顶部表压为零的锅炉,可用于供水温度≤95℃的热水供热系统,单台功率≤2.8MW。
他具有以下特点:⑴采用开式锅筒,系统处于常压状态,本身无爆炸危险性、安全性高;⑵循环泵安装于锅炉的出水侧,降低了锅筒承受的压力;⑶循环泵兼有补水泵的功能,循环泵扬程计算方法与承压锅炉循环泵的计算方法有明显不同;⑷安装地点灵活,不受承压锅炉安装位置规定若干限制的约束;⑸锅炉的供水温度与循环泵入口处的水压有关。
二、常压热水锅炉房供热系统设计1.循环水泵的选型与配置。
常压热水鍋炉系统的循环水泵安装在锅炉的出水管段上,循环水泵出水先进入热水管网,当系统停止运行时,回水管路上的自动启闭阀关闭,管路系统与锅炉断开。
一般清水泵的最高设计水温为80℃,热水管路上循环水泵的工作温度为95℃,宜配置型热水泵。
在承压热水锅炉的闭式循环中,水泵入口和出口承受着相等的静水压力,水泵扬程主要克服循环管路上的沿程和局部损失。
在常压热水锅炉系统的开式循环中,水泵扬程与流动阻力和系统高度有关,循环水泵实际起加压泵的作用。
基于PLC的锅炉供热控制系统的设计的开题报告
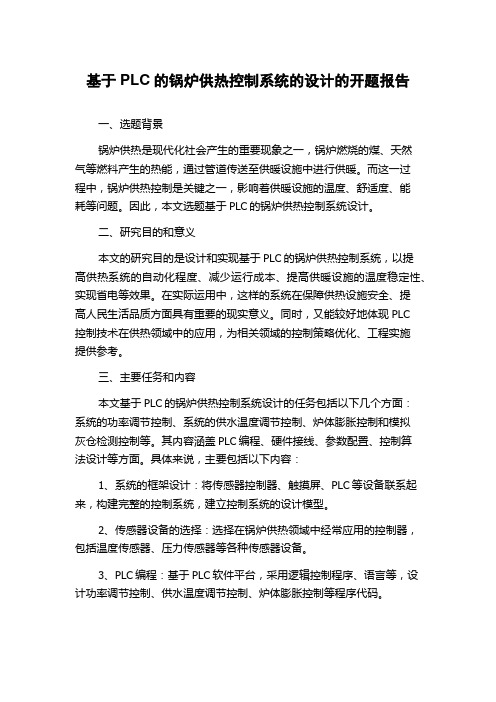
基于PLC的锅炉供热控制系统的设计的开题报告一、选题背景锅炉供热是现代化社会产生的重要现象之一,锅炉燃烧的煤、天然气等燃料产生的热能,通过管道传送至供暖设施中进行供暖。
而这一过程中,锅炉供热控制是关键之一,影响着供暖设施的温度、舒适度、能耗等问题。
因此,本文选题基于PLC的锅炉供热控制系统设计。
二、研究目的和意义本文的研究目的是设计和实现基于PLC的锅炉供热控制系统,以提高供热系统的自动化程度、减少运行成本、提高供暖设施的温度稳定性、实现省电等效果。
在实际运用中,这样的系统在保障供热设施安全、提高人民生活品质方面具有重要的现实意义。
同时,又能较好地体现PLC控制技术在供热领域中的应用,为相关领域的控制策略优化、工程实施提供参考。
三、主要任务和内容本文基于PLC的锅炉供热控制系统设计的任务包括以下几个方面:系统的功率调节控制、系统的供水温度调节控制、炉体膨胀控制和模拟灰仓检测控制等。
其内容涵盖PLC编程、硬件接线、参数配置、控制算法设计等方面。
具体来说,主要包括以下内容:1、系统的框架设计:将传感器控制器、触摸屏、PLC等设备联系起来,构建完整的控制系统,建立控制系统的设计模型。
2、传感器设备的选择:选择在锅炉供热领域中经常应用的控制器,包括温度传感器、压力传感器等各种传感器设备。
3、PLC编程:基于PLC软件平台,采用逻辑控制程序、语言等,设计功率调节控制、供水温度调节控制、炉体膨胀控制等程序代码。
4、参数配置:为PLC编程设定控制参数,包括控制时序和控制范围等关键参数;同时设计参数调节程序,通过丰富参数调节方式,实现定制化控制方案。
5、控制算法设计:从系统的高级控制角度出发,采用现代化控制算法,设计稳态控制、过程控制、最优控制等各种算法,优化系统的整体控制效果。
四、研究成果预期设计出基于PLC的锅炉供热控制系统,掌握了供热领域常用的传感器设备和控制器,建立了一个完整的控制系统。
实验结果也体现出该系统的优异性能,具体体现在系统的控制精度、控制响应速度、稳定性等方面。
基于PLC的锅炉供热控制系统的设计

基于PLC的锅炉供热控制系统的设计一、本文概述随着科技的不断发展,可编程逻辑控制器(PLC)在工业自动化领域的应用日益广泛。
作为一种高效、可靠的工业控制设备,PLC以其强大的编程能力和灵活的扩展性,成为现代工业控制系统的重要组成部分。
本文旨在探讨基于PLC的锅炉供热控制系统的设计,通过对锅炉供热系统的分析,结合PLC控制技术,实现对供热系统的智能化、自动化控制,提高供热效率,降低能耗,为工业生产和居民生活提供稳定、可靠的热源。
文章首先介绍了锅炉供热系统的基本构成和工作原理,分析了传统供热系统存在的问题和不足。
然后,详细阐述了PLC控制系统的基本原理和核心功能,包括输入/输出模块、中央处理单元、编程软件等。
在此基础上,文章提出了基于PLC的锅炉供热控制系统的总体设计方案,包括系统硬件选型、软件编程、系统调试等方面。
通过本文的研究,期望能够实现对锅炉供热控制系统的优化设计,提高供热系统的控制精度和稳定性,降低运行成本,促进节能减排,为工业生产和居民生活提供更加安全、高效的供热服务。
也为相关领域的研究人员和技术人员提供有价值的参考和借鉴。
二、锅炉供热系统基础知识锅炉供热系统是一种广泛应用的热能供应系统,其主要任务是将水或其他介质加热到一定的温度,然后通过管道系统输送到各个用户端,满足各种热需求,如工业生产、居民供暖等。
该系统主要由锅炉本体、燃烧器、热交换器、控制系统和辅助设备等几部分构成。
锅炉本体是供热系统的核心设备,负责将水或其他介质加热到预定温度。
其根据燃料类型可分为燃煤锅炉、燃油锅炉、燃气锅炉、电锅炉等。
锅炉的性能参数主要包括蒸发量、蒸汽压力、蒸汽温度等。
燃烧器是锅炉的重要组成部分,负责燃料的燃烧过程。
燃烧器的性能直接影响到锅炉的热效率和污染物排放。
燃烧器需要稳定、高效、低污染,同时要适应不同的燃料类型和负荷变化。
热交换器是锅炉供热系统中的关键设备,负责将锅炉产生的热能传递给水或其他介质。
热交换器的设计应保证高效、稳定、安全,同时要考虑到热能的充分利用和防止结垢、腐蚀等问题。
电热锅炉供热供热控制系统开题报告
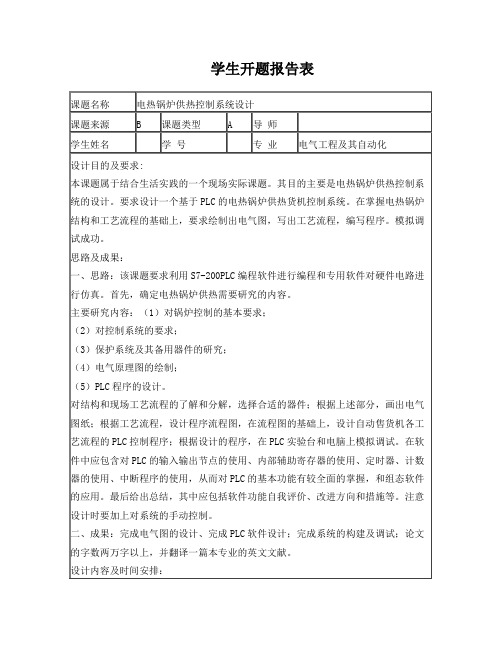
一、思路:该课题要求利用S7-200PLC编程软件进行编程和专用软件对硬件电路进行仿真。首先,确定电热锅炉供热需要研究的内容。
主要研究内容:(1)对锅炉控制的基本要求;
(2)对控制系统的要求;
(3)保护系统及其备用器件的研究;
(4)电气原理图的绘制;
(5)PLC程序的设计。
对结构和现场工艺流程的了解和分解,选择合适的器件;根据上述部分,画出电气图纸;根据工艺流程,设计程序流程图,在流程图的基础上,设计自动售货机各工艺流程的PLC控制程序;根据设计的程序,在PLC实验台和电脑上模拟调试。在软件中应包含对PLC的输入输出节点的使用、内部辅助寄存器的使用、定时器、计数器的使用、中断程序的使用,从而对PLC的基本功能有较全面的掌握,和组态软件的应用。最后给出总结,其中应包括软件功能自我评价、改进方向和措施等。注意设计时要加上对系统的手动控制。
5 . 实验室具有先进仪器可以进行模拟调试;
指导教师签名: 日期:
课题类型:A、工程设计,B、工程技术研究,C、软件开发,D、机械设计,E、实验研究,
F、理论研究,G、其它
学生开题报告表
课题名称
电热锅炉供热控制系统设计
课题来源
B
课题类型
A
导 师
学生姓名
学 号
专 业
电气工程及其自动化
设计目的及要求:
本课题属于结合生活实践的一个现场实际课题。其目的主要是电热锅炉供热控制系统的设计。要求设计一个基于PLC的电热锅炉供热货机控制系统。在掌握电热锅炉结构和工艺流程的基础上,要求绘制出电气图,写出工艺流程,编写程序。模拟调试成功。
二、成果:完成电气图的设计、完成PLC软件设计;完成系统的构建及调试;论文的字数两万字以上,并翻译一篇本专业的英文文献。
电锅炉蓄能式供暖系统设计规范

电锅炉蓄能式供暖系统设计规范0、总则0.1为了进一步规范设计及指导电锅炉蓄能式供暖工程施工,扭转设计与工程存在的不合理与不统一的状况,制定本规范;0.2本设计规范适用于电锅炉蓄能式供暖系统的设计及工程施工与验收等;0.3按本规范进行系统设计时,尚应符合国家现行的有关标准、规范的规定。
当有所冲突时,应以国家规范、标准为准。
1、系统综合设计1.1系统简介1.1.1电锅炉蓄能式供暖系统工作原理电锅炉蓄能式供暖是采用电锅炉为制热设备,利用供电电费峰谷差值,在供电谷值时段,开启电锅炉,加热热媒并储存在蓄能水箱中。
在供电高峰时段关闭电锅炉,由储存在蓄能水箱中的热水向采暖系统供热。
这样,它既能使供电电网运行“削峰填谷”,又可充分利用廉价的低谷电价,达到经济运行的目的,使用户和供电部门都能从中受益。
因此,电锅炉蓄能式供暖系统是取代燃煤锅炉、值得推广的最佳供暖方式之一。
1.1.2电锅炉供暖的优越性1.1.2.1电锅炉是真正的环保型绿色产品,具有无污染、无噪音等优点,这是燃煤、燃油及燃气锅炉无法比拟的。
1.1.2.2电锅炉蓄能式供暖系统既能合理分配用电负荷、提高配电设备利用率,同时又充分利用低谷电价,节约运行费用,降低运行成本。
1.1.2.3电锅炉蓄能式供暖系统中,锅炉本体体积小,结构简单、紧凑,占地面积小,不需要烟囱和燃料堆放场地,极大的节约锅炉房用地。
1.1.2.4电锅炉蓄能式供暖系统自动化控制程度高,具有超温、过载、短路、漏电、缺水,缺相等六重自动保护功能,运行安全可靠,实现了机电一体化。
1.1.2.5电锅炉具有高效、节能等优点。
其运行热效率达98%以上。
1.1.2.6电锅炉可逐级加减负荷,调节过程平稳,控制精度高。
1.1.2.7电锅炉蓄能式供暖系统适用范围广,可以满足各种环境及条件的需要,适用于宾馆、饭店、机关、学校、住宅等的取暖和洗浴。
1.1.3电锅炉蓄能式供暖系统1.1.3.1常压电锅炉原则上一般不作为蓄能式供暖系统的热力设备。
锅炉燃烧系统的控制系统设计毕业论文

锅炉燃烧系统的控制系统设计摘要:锅炉是热电厂重要且基本的设备,其最主要的输出变量之一就是主蒸汽压力。
主蒸汽压力的自动调节的任务是维持过热器出口气温在允许范围内,以确保机组运行的安全性和气温在允许范围内,以确保机组运行的安全性和[1]经济性。
锅炉所产生的高压蒸汽既可作为驱动透平的动力源,又可以作为精馏、干燥、反可以作为精馏、干燥、反应、加热等过程的热源。
随着工业生产的规模不断扩大,作为动力和热源的过滤,也向着大容量、高参数、高效率的方向发展。
在控制算法上、综合运用了单回路控制、串级控制、比值控制等控制方法实现了燃料量控制调节蒸汽压力、送风量控制调节烟气含氧量、引风量控制炉膛负压,并有效克服了彼此的扰动,使整个系统稳定运行。
运行。
关键词:锅炉;蒸汽压力;单回路控制;关键词:锅炉;蒸汽压力;单回路控制;ControlsystemdesignoftheboilercombustionsystemAbstract:Theboilerisimportantandbasicequipmentofthethermalpowerplan t,oneofthemainoutputvariableisthemainsteampressure.Thetaskoftheauto maticadjustmentofthemainsteampressureistomaintainthesuperheateroutle ttemperaturewithintheallowablerange,toensurethesafetyandeconomyofth eunitoperation.Theboilersproducehighpressuresteamcanbeusedasasource ofpower-driventurbine,butalsoasadistillation,drying,reaction,heatingandprocesshe atsource.Withindustrialproductionexpanding,asafilterforpowerandheat,b utalsotowardthehigh-capacity,high-parameter,high-efficiencydirection.Inthecontrolalgorithm,theintegrateduseofsingle-loopcontrol,cascadecontrol,ratiocontrol,thecontrolmethodoffuelcontroltoadjustthevaporpressure,airvolumecontroltoadjustthefluegasoxygenconten t,thewindcontrolthefurnacenegativepressure,andeffectivelyovercomeeac hotherdisturbancessothatthewholestabilityofthesystem.Keywords:Boiler;Vaporpressure;Single-loopcontrol引言引言随着城市的快速发展,我们对用电的需求也越来越大,如何利用好有限的能源来保证供电是一个重要的话题,在能源的利用过程中如何更加提高能源的利用率是一个可研究性的话题,本文基于上述话题对电厂的燃烧锅炉控制进行了研究。
PLC电热锅炉供热控制系统设计

PLC电热锅炉供热控制系统设计一、引言随着社会的不断发展,人们对于供热系统的要求也越来越高。
为了提高供热系统的自动化程度和安全性,PLC(可编程逻辑控制器)技术得到了广泛应用。
本文将针对PLC电热锅炉供热控制系统的设计进行详细讨论,以确保系统运行稳定、安全。
二、PLC电热锅炉供热控制系统设计方案1. 系统架构设计PLC电热锅炉供热控制系统主要由PLC控制器、传感器、执行器等组成。
其中,PLC控制器作为系统的大脑,负责对各个执行器的控制和监测工作。
传感器用于采集环境温度、水箱水位等信息,反馈给PLC控制器,从而实现对系统的自动控制。
2. 系统功能设计(1)温度控制功能:通过传感器实时监测环境温度,当环境温度低于设定值时,PLC控制器将启动电热锅炉,加热水箱中的水,直到温度达到设定值为止。
(2)水位控制功能:传感器监测水箱水位,当水位低于设定值时,PLC将启动给水泵进行给水,保证水箱水位在合适范围内。
(3)故障诊断功能:系统内置故障诊断模块,通过监测系统各部件的运行状态,及时发现故障并进行报警提示,保证系统安全稳定运行。
3. 系统性能设计(1)稳定性:系统采用双PLC热备份设计,确保系统在一台PLC故障时可以自动切换到备用PLC,保证系统的连续运行。
(2)可靠性:系统采用高品质的传感器和执行器,具有较高的抗干扰能力和稳定性,从而确保系统的可靠性。
4. 系统通信设计系统采用以太网通信方式,PLC控制器通过以太网与上位机连接,实现对系统的远程监控和控制。
上位机可以实时监测系统运行状态、温度水位等信息,方便操作人员进行远程管理。
三、系统实施与调试1. 硬件安装:安装PLC控制器、传感器、执行器等硬件设备,确保设备安装位置合理,连接正确。
2. 软件编程:编写PLC控制程序,包括温度控制、水位控制、故障诊断等功能模块。
3. 系统调试:进行系统联调和调试,检验系统各部件是否正常工作,确保系统实现预期功能。
四、系统运行维护1. 定期检查:定期检查系统各部件的运行状态,及时更换老化部件,保持系统的正常运行。
基于PID算法的锅炉恒温控制系统毕业设计

基于PID算法的锅炉恒温控制系统毕业设计锅炉恒温控制系统是现代工业控制系统中的一种重要应用,其主要目标是通过控制锅炉的供热温度来保持恒定的室内温度。
而PID算法是一种经典的反馈控制算法,被广泛应用于工业自动化控制过程中。
本篇文章将介绍基于PID算法的锅炉恒温控制系统的设计。
首先,我们需要明确锅炉恒温控制系统的基本原理。
锅炉恒温控制系统由温度传感器、控制器和执行器(例如阀门)组成。
温度传感器用于检测当前室内温度,将检测到的温度信号传递给控制器。
控制器根据设定的目标温度和当前温度之间的差异,计算出控制信号,并将该信号传递给执行器,以调节锅炉的供热。
PID算法的设计基于对系统的模型和特性的理解。
PID控制器包括比例、积分和微分三个部分。
比例控制部分根据当前误差信号的大小,按照一定的比例系数来生成控制信号。
积分控制部分用于累积误差信号,并按照一定的积分系数来生成控制信号,以消除系统的积分误差。
微分控制部分用于检测误差变化率,并按照一定的微分系数来生成控制信号,以消除系统的超调和震荡。
设计基于PID算法的锅炉恒温控制系统的步骤如下:1.确定系统的数学模型:锅炉恒温控制系统可以近似视为一阶惯性环节。
根据温度传感器的输出和锅炉供热温度之间的关系,可以得到系统的传递函数。
根据传递函数,可以确定比例、积分和微分系数。
2.系统参数调整:为了使系统响应更加稳定和快速,需要对比例、积分和微分系数进行调整。
调整的方法可以是试错法或者自动调参法,以使系统的动态响应达到设计要求。
3.控制策略选择:PID算法有多种控制策略可选择,如串级控制、级联控制、迭代控制等。
根据实际情况和系统需求,选择适合的控制策略。
4.实现与调试:将PID算法实现到控制器硬件中,并进行系统的调试和稳定性测试。
检查控制器的输出和系统的响应是否满足设计要求,如稳定性、超调量、响应时间等。
最后,本篇文章还需要考虑锅炉恒温控制系统的优化。
可以采用先进的控制算法,如模糊控制、自适应控制等,以提高系统的稳定性和性能。
毕业设计(论文)_基于PLC的锅炉出水温度控制系统的研究与设计
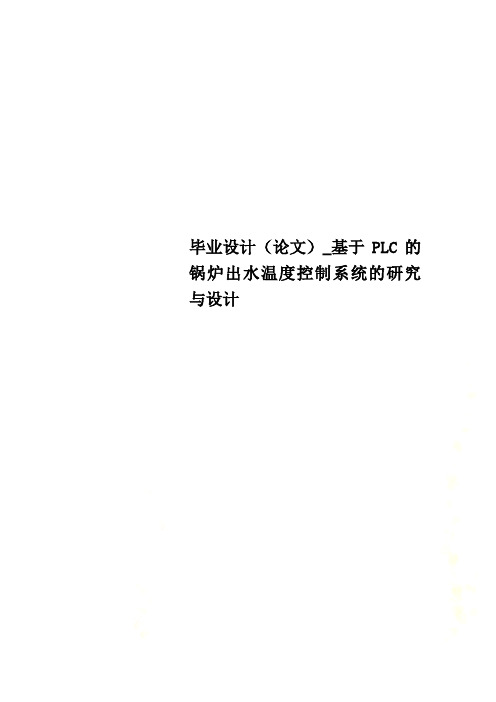
毕业设计(论文)_基于PLC的锅炉出水温度控制系统的研究与设计毕业设计锅炉出水温度控制系统的研究与设计总计毕业设计(论文)61页表格2表插图16幅I摘 要随着我国经济的发展,资源和环境矛盾同趋尖锐,使我国的现代化建设面临严峻挑战。
作为温度控制系统重要能源转换设备的锅炉能耗巨大,占我国原煤产量的三分之一左右。
然而,我国目前运行的很多锅炉控制系统自动化水平不高、安全性低,工作效率和环境污染普遍低于国家标准,因此实现锅炉的计算机自动控制具有重要的意义。
随着科学技术的不断发展人们开始利用各种先进的仪器和技术组成计算机控制系统来代替人工复杂的控制操作,直接数字控制DDC 系统(Direct Control ),便是其中之一。
直接数字控制DDC 系统,它是工业生产计算机控制系统中用的最广泛的一种系统应用形式,在这类系统中的计算机,除了经过输入通道对多个工业过程参数进行巡回检测采集外,它还代替了模拟调节系统中的模拟调节气,按预定的调节规则进行调解运算,然后将运算结果通过过程输出通道输出并作用于执行机构,以实现多回路调节的目的。
本设计设计了基于PLC 的锅炉温度控制系统,该系统包括下位机控制和上位机控制两部分。
文中给出了通过时间和室外温度相结合的控制策略对系统温度进行调节控制。
关键字:锅炉;计算机控制; PLCAbstractWith China’s economic development,resources and the environment has become increasingly acute contradictions,so that the modernization of our country is facing a formidable challenge.As an important energy source conversion equipment,heating system of the industrial boiler consumes about one-third of China’s coal.However,the majori ty of China’s current operating boiler system’s security and efficiency is generally lower than the national standard.So it's great significance to achieve automatic control for boiler with computer.Along with science technical develop continuously people start making use of every kind of advanced instrument constituting the calculator control system with the technique to the control operation that replace the artificial complicacy, direct arithmetic figure control DDC system( Direct Control), just one of them Direct arithmetic figure control DDC system, it is an industry to produce convenient and the most extensive a kind of system in system of control of calculator application form, in addition to through importation passage to several industries process parameter proceeding cruising to return to examination to collect, it returned to replace the emulation regulates the emulation in the system regulates the spirit, at the set regulate rule proceed the intermediation carries to calculate, then will carry to calculate result pass process output passage output combine function in carry out the organization, to realize many the purpose that back track regulate.the paper presents a overall control thinking,the system designed to heating in winter includes superordinate computer control system and the subordinate system.To meet all the campus’s winter heating,it gives a complete control strategy which combined with time and outdoor’s temperature.IIKey Words:Boiler;Computer Control; PLCIII目录摘要 (I)ABSTRACT (II)第1章绪论 (6)1.1锅炉温度控制系统现状 (6)1.2锅炉自动控制的发展历史 (7)1.4课题意义 (9)第2章锅炉温度控制系统的总体介绍 (11)2.1锅炉温度控制系统的组成 (11)2.2交流电机的变频调速系统介绍 (13)2.2.1变频器驱动的特点 (13)2.2.2变频调速的基本原理 (14)2.2.3变频器基本结构 (15)2.3燃煤锅炉的工作过程 (17)2.3.1 燃煤锅炉的组成 (17)2.3.2燃煤锅炉的工作过程 (18)2.4燃煤锅炉的自动调节任务 (19)第3章控制系统下位机的设计 (22)3.1PLC软件介绍 (22)3.1.1 模块式PLC的基本结构 (23)3.1.2 PLC的特点 (24)3.2STEP7软件简介 (25)3.3控制系统所用功能块 (27)3.4锅炉控制系统的硬件组态 (29)3.5锅炉系统下位机程序设计 (31)3.5.1 系统下位机控制程序实现 (31)3.6本章小结 (41)第4章控制系统上位机设计 (42)IV4.1WINCC软件介绍 (42)4.2WINCC的特点 (43)4.3WINCC主要控制模块 (43)4.4项目组态 (45)4.5系统监控界面设计 (46)4.6I NTERNET远程监控 (52)4.6.1 WEB Navigator简介 (52)4.6.2 WEB Navigator的优点 (53)4.6.3 远程WEB发布与浏览 (55)4.6.4 使用WEB Navigator 过程中遇到的问题及解决办法 (55)4.7本章小结 (57)第5章系统的抗干扰设计 (58)5.1PLC系统的抗干扰性 (58)5.1.1 电磁干扰源及对系统的影响 (59)5.1.2 系统外引线的干扰 (59)5.1.3 PLC系统内部的干扰 (60)5.1.4 PLC控制系统工程应用的抗干扰设计 (61)5.2控制系统主要抗干扰措施 (61)第6章结论与展望 (63)6.1总结 (63)6.2展望 (64)致谢 (65)参考文献 (66)V第1章绪论1.1锅炉温度控制系统现状锅炉是化工、炼油、发电等工业生产过程中必不可少的重要的动力设备。
电锅炉蓄能式供暖系统设计规范

电锅炉蓄能式供暖系统设计规范设计规范:电锅炉蓄能式供暖系统总则:为了规范电锅炉蓄能式供暖工程的设计和施工,本规范制定。
适用于电锅炉蓄能式供暖系统的设计、施工和验收。
在按本规范进行系统设计时,应符合国家现行的有关标准和规范的规定。
当有冲突时,以国家规范和标准为准。
系统综合设计:1.1 系统简介1.1.1 电锅炉蓄能式供暖系统工作原理电锅炉蓄能式供暖系统采用电锅炉为制热设备,利用供电电费峰谷差值,在供电谷值时段,开启电锅炉,加热热媒并储存在蓄能水箱中。
在供电高峰时段关闭电锅炉,由储存在蓄能水箱中的热水向采暖系统供热。
这种供暖方式可以使供电电网运行“削峰填谷”,充分利用廉价的低谷电价,达到经济运行的目的,同时取代燃煤锅炉,是最佳供暖方式之一。
1.1.2 电锅炉供暖的优越性1.1.2.1 电锅炉是真正的环保型绿色产品,具有无污染、无噪音等优点,这是燃煤、燃油及燃气锅炉无法比拟的。
1.1.2.2 电锅炉蓄能式供暖系统既能合理分配用电负荷、提高配电设备利用率,同时又充分利用低谷电价,节约运行费用,降低运行成本。
1.1.2.3 电锅炉蓄能式供暖系统中,锅炉本体体积小,结构简单、紧凑,占地面积小,不需要烟囱和燃料堆放场地,极大的节约锅炉房用地。
1.1.2.4 电锅炉蓄能式供暖系统自动化控制程度高,具有超温、过载、短路、漏电、缺水,缺相等六重自动保护功能,运行安全可靠,实现了机电一体化。
1.1.2.5 电锅炉具有高效、节能等优点。
其运行热效率达98%以上。
1.1.2.6 电锅炉可逐级加减负荷,调节过程平稳,控制精度高。
1.1.2.7 电锅炉蓄能式供暖系统适用范围广,可以满足各种环境及条件的需要,适用于宾馆、饭店、机关、学校、住宅等的取暖和洗浴。
1.1.3 电锅炉蓄能式供暖系统1.1.3.1 常压电锅炉原则上一般不作为蓄能式供暖系统的热力设备。
1.1.3.2 承压蓄能供暖系统示意图见图一。
本文介绍了电锅炉蓄能式供暖系统的设计规范和运行方式。
电热锅炉供热系统的PLC控制程序设计

xxxxxxx机电工程系毕业设计论文电热锅炉供热系统的PLC控制程序设计题目专业名称学生姓名指导教师毕业时间绪论现在生产线控制的主流品种是以继电器、接触器为主的控制装置。
继电器、接触器是一些电磁开关。
由励磁线圈、铁心磁路、触点等部件组成。
通过继电器接触器等其它控制元件的线路连接,可以实现一定的控制逻辑,从而实现设备的各种操作控制。
人们将由导线连接决定器件间的逻辑关系的控制方式称为接线逻辑。
随着工业自动化的程度的不断提高,使用继电器电路构成工业控制系统的缺陷不断暴露出来。
首先是复杂的系统使用成百上千个各种各样的继电器,成千上万根导线连接的密如蛛网。
只要有一个电器,一根导线出现故障,系统就不能工作,这就大大降低了这种接线逻辑的可靠性。
其次是这样的系统维修机改造很不容易,特别是技术改造,当试图改造工作设备的工作过程以改善设备各功能时,人们宁愿重新生产一套控制设备都不愿将继电器控制柜中的线路重接。
而PLC由于采用现代大规模集成电路技术,采用严格的生产工艺制造,内部电路采用了先进的抗干扰技术,具有很高的可靠性。
同时PLC用存储逻辑代替接线逻辑,大大减小了控制设备的外部接线,是控制系统设计及建造的周期大大缩短了。
同时维护也变得容易起来。
更重要的是同一设备经过改变程序改变生产过程成为可能。
本文以PLC技术在锅炉多功能供热系统为例,来阐明PLC在工业控制中发挥的巨大作用关键词:锅炉多功能供热;PLC;目录1 绪论 (2)1.1 PLC的基本概念 (5)1.2 PLC的诞生 (5)1.3 PLC的特点 (6)2 PLC的介绍 (7)2.1 PLC的流派 (7)2.2 PLC的结构和工作原理 (8)3 PLC的应用领域 (11)3.1开关量的逻辑控制 (11)3.2模拟量控制 (11).3.3运动控制 (12)3.4过程控制 (12)3.5数据控制 (12)4 PLC的基本结构 (12)4.1中央处理单元 (13)4.2 存储器 (13)4.3I/O模块 (14)4.4 电源 (15)4.5 底板或机架 (16)4.6 PLC系统的基本设备 (16)5 PLC的基本工作原理 (16)5.1 扫描技术 (16)5.2 PLC与继电器控制与系统微机区别 (18)5.3 基本指令系统特点 (18)5.4编程语言的形式 (19)5.5 PLC控制系统的设计基本原则 (20)5.6 PLC程序的内容和质量评价指标 (21)5.7 PLC程序的调试方法及步骤 (22)5.8 PLC的造型方法 (23)5.9经济性考虑 (27)6 基于PLC的电热锅炉供热控制系统设计 (28)6.1电热锅炉供热控制系统设计要求 (29)6.2电热锅炉供热控制系统设计方案 (30)6.3电热锅炉供热控制系统设计的程序部分的介绍 (34)致谢 (37)参考文献 (38)1.1 PLC的基本概念PLC即可编程控制器(Programmable logic Controller),是指以计算机技术为基础的新型工业控制装置。
基于PLC的锅炉燃烧控制系统的设计-毕业论文

摘要随着社会经济的飞速发展,城市建设规模的不断扩大,以及人们生活水平的不断提高,对城市生活供暖的用户数量和供暖质量提出了原来越高的要求。
结合现状,本论文供暖锅炉监控系统,设计了一套基于PLC和变频调速技术的供暖锅炉控制系统。
该控制系统以一台工业控制机作为上位机,以西门子S7-300可编程控制机为下位机,系统通过变频器控制电机的启动,运行和调速。
上位机监控采用WinCC设计,主要完成系统操作界面设计,实现系统启停控制,参数设定,报警联动,历史数据查询等功能。
下位机控制程序采用西门子公司的STEP7编程软件设计,主要完成模拟量信号的处理,温度和压力信号的PID控制等功能,并接受上位机的控制指令以完成风机启停控制,参数设定,循环泵的控制和其余电动机的控制。
本文设计的变频控制系统实现了锅炉燃烧过程的自动控制,系统运行稳定可靠。
采用锅炉的计算机控制和变频控制不仅可大大节约能源,促进环保,而且可以提高生产自动化水平,具有显著的经济效益和社会效益。
关键字:锅炉控制;变频调速;组态软件;PLCAbstractAlong with social economy’s swift development, the urban construction scale’s unceasing expansion , as well as the peple living standard’s unceasing enhancement , set more and more high request to the city life heating’s user quantity and the heating quality. The union present situation, the present paper heating boiler supervisory sysem, has designed a set based on PLC and the frequency conversion velocity modulation technology heating boiler control system.This control system takes the superior machine by one Industry cybertrons , west of family household S7-300 programmable controller for lower position machine ,system through frequency changer control motor’s start , movement and vclocity modulation .the superior machine monitoring software uses the three dimensional strength to control the WinCC design , mainly completes the system operation contract surface design ,realizes the system to open/stops functions and so on control ,parameter hypothesis ,warning linkage,historical data inquiry. The lower position machine control procedure uses Siemen’s STEP7 programming software design , mainly completes the simulation quantity signal processing , temperature and pressure signal functions and so on PID control , and receives the superior machine control command to complete the air blower to open/stops the control , the parameter hypothesis, the circulating pump control and other electric motor’s control.This article designs the frequency conversion processs automatic control, the systems operation is stable, is reliable. Uses boiler’s computer control and the frequency converseon control noe only may save the energy greatly, the promotion environmental protection moreover may raise the production automation level, has the remarkable economic efficiency and the social efficiency.Key Words:Boiler control;Frequency conversion velocity modulation ;Configuration Software;PLC目录摘要 0Abstract (1)第1章概述 (4)1.1 项目背景及课题的研究意义 (4)1.2 供暖锅炉控制的国内外研究现状 (5)1.3锅炉控制系统的发展趋势 (6)1.4本文所做工作 (7)第2章系统方案设计 (9)2.1锅炉控制研究简介 (9)2.2 总体设计思路 (9)2.3方案比较 (10)2.3.1方案1 (10)2.3.2 方案2 (10)2.4方案论证与方案确定 (11)第3章硬件设计 (12)3.1 用户系统框图 (12)3.2 锅炉系统的理论分析 (13)3.2.1变频调速基本原理 (13)3.2.2变频调速在供暖锅炉中的应用 (13)3.2.3变频调速节能分析 (14)3.3燃烧过程控制 (19)3.4锅炉控制系统设计 (20)3.5控制系统构成介绍 (21)第4章软件设计 (25)4.1 S7-300系列PLC简介 (26)4.2 PLC编程语言简介 (28)4.2.1 PLC编程语言的国际标准 (28)4.2.2复合数据类型与参数类型 (29)4.2.3系统存储器 (29)4.2.4 S7-300 CPU中的寄存器 (30)4.3 STEP7 的原理 (31)4.3.1 STEP7概述 (31)4.3.2 硬件组态与参数设置 (32)4.3.3 符号表 (36)4.3.4 逻辑块 (37)4.3程序设计 (38)4.4通信系统 (41)4.5人机界面 (43)4.5.1监控软件WinCC介绍 (43)4.5.2监控系统设计 (45)4.5.3锅炉监控界面设计 (49)第5章结论 (53)5.1 成果的创造性和先进性 (53)5.2作用意义(经济效益和社会意义) (53)5.3 推广应用范围和前景 (53)5.4 需要进一步改进之处 (54)参考文献 (55)外文资料翻译 (56)外文翻译原文 (56)外文翻译译文 (68)致谢 (75)附录 (76)附录1 程序清单 (76)附录2 I/O点数分配表 (96)附录3 物理参数比较表 (97)第1章概述1.1 项目背景及课题的研究意义工业锅炉是工业生产和集中供热过程中重要的动力设备。
供热电锅炉的PLC控制系统优化设计

O p i a e i n f r PLC o t o y t m fhe tng ee t i ie tm l d sg o c n r l s se o a i l c r c bo l r
G UO a s a H ih n
( rh atDini ies y in 1 2 1 Note s a l Unv ri ,Jl 3 0 2,C ia t i hn )
核 心 。采 用 4组 电 加 热 管 自动 投 切 的控 制 方 式 , 证 了 系 统 的 可 靠 性 与 经 济 性 , 给 出 了 基 本 的 硬 件 配 置 和 编 程 保 并
原理 。
关 键 词 : 加热 锅 炉 ; 编程 序控 制 器 ( L ) 控 制 方 式 ; 靠 性 电 可 PC ; 可 中 图 分 类 号 :T 2 3 P 7 文 献 标 识 码 :A 文 章 编 号 :0 2—16 ( 0 1 0 0 7 0 10 6 3 2 1 ) 3— 18— 2
1 基 于 P C的具 有较 高 自动化 程度 的电热锅 炉 控 套 L 制 系统 。
组数 , 反之 , 少 电加 热 管组 数 , 减 以达 到 节 约用 电量
的 目的 ; 锅炉 中通 过 电加 热 管 加 热 的水 通 过 循 环 泵
直 接 向供 暖 系统供 热 , 环 泵 有 主泵 和 备 用 泵 可 供 循
Absr c : s p p rpu sfr r st e o tma e in fra o tc c n r ls se o lc rc b i rwh c s sS c t a t Thi a e t o wa d h p i ld sg o utma i o to y t m fe e ti ol ih u e i - e me s S —2 0 PL a o e a c r i g t r o .p o o e o a o u o t wic ngwh c u r n e st e r l・ n 7 0 C sc r c o d n owo k f w l r p s st d pta t ma i s thi ih g a a te h e i c a i t n c n my o h y t m n r vd s b sc h r wa e p o l sa d p o r mm ig p i c p e . b l y a d e o o ft e s se a d p o i e a i a d r r f e n r g a i i n rn i ls
(完整版)锅炉燃烧系统的控制系统设计

(完整版)锅炉燃烧系统的控制系统设计⽬录1锅炉⼯艺简介 (1)1.1锅炉的基本结构 (1)1.2⼯艺流程 (2)1.2煤粉制备常⽤系统 (3)2 锅炉燃烧控制 (4)2.1燃烧控制系统简介 (4)2.2燃料控制 (4)2.2.1燃料燃烧的调整 (4)2.2.2燃烧调节的⽬的 (5)2.2.3直吹式制粉系统锅炉的燃料量的调节 (5)2.2.4影响炉内燃烧的因素 (6)2.3锅炉燃烧的控制要求 (11)2.3.1 锅炉汽压的调整 (11)3锅炉燃烧控制系统设计 (14)3.1锅炉燃烧系统蒸汽压⼒控制 (14)3.1.1该⽅案采⽤串级控制来完成对锅炉蒸汽压⼒的控制 (14)3.2燃烧过程中烟⽓氧含量闭环控制 (17)3.2.1 锅炉的热效率 (18)3.2.2反作⽤及控制阀的开闭形式选择 (20)3.2.3 控制系统参数整定 (20)3.3炉膛的负压控制与有关安全保护保护系统 (21)3.3.1炉膛负压控制系统 (22)3.3.2防⽌回⽕的连锁控制系统 (23)3.3.3防⽌脱⽕的选择控制系统 (24)3.4控制系统单元元件的选择(选型) (24)3.4.1蒸汽压⼒变送器选择 (24)3.4.2 燃料流量变送器的选⽤ (24)4 DCS控制系统控制锅炉燃烧 (26)4.1DCS集散控制系统 (26)4.2基本构成 (27)锅炉燃烧系统的控制4.3锅炉⾃动燃烧控制系统 (31)总结 (33)致谢 (34)参考⽂献 (35)1锅炉⼯艺简介1.1锅炉的基本结构锅炉整体的结构包括锅炉本体和辅助设备两⼤部分。
1、锅炉本体锅炉中的炉膛、锅筒、燃烧器、⽔冷壁、过热器、省煤器、空⽓预热器、构架和炉墙等主要部件构成⽣产蒸汽的核⼼部分,称为锅炉本体。
锅炉本体中两个最主要的部件是炉膛和锅筒。
炉膛⼜称燃烧室,是供燃料燃烧的空间。
将固体燃料放在炉排上进⾏⽕床燃烧的炉膛称为层燃炉,⼜称⽕床炉;将液体、⽓体或磨成粉状的固体燃料喷⼊⽕室燃烧的炉膛称为室燃炉,⼜称⽕室炉;空⽓将煤粒托起使其呈沸腾状态燃烧、适于燃烧劣质燃料的炉膛称为沸腾炉,⼜称流化床炉;利⽤空⽓流使煤粒⾼速旋转并强烈⽕烧的圆筒形炉膛称为旋风炉。
电锅炉温度控制系统的设计

电锅炉温度控制系统的设计一、系统组成1.传感器:用于实时采集电锅炉的温度信号;2.控制器:根据传感器采集到的温度信号进行处理,并输出控制信号;3.执行器:接收控制信号,控制电锅炉的加热功率;4.用户界面:用于操作和监视系统的运行情况。
二、控制原理电锅炉温度控制系统的基本原理是通过调整电锅炉的加热功率以控制水温。
根据电锅炉的加热功率与水温的关系,可以得到一个传输函数,用于描述系统的动态特性。
通过对传输函数进行数学建模,可以采用各种控制方法进行控制。
三、控制策略1.比例控制:根据电锅炉的温度偏差与设定值之间的差距,输出一个与偏差成比例关系的控制信号,用以控制加热功率;2.比例-积分控制:在比例控制的基础上增加积分作用,用于消除稳态误差,提高系统的稳定性和静态精度;3.比例-微分控制:在比例控制的基础上增加微分作用,用于预测系统的未来状态,并提前做出调整,以减小温度超调和响应时间;4.比例-积分-微分控制:综合利用比例、积分和微分控制的优点,以达到更好的控制效果。
四、系统优化为了进一步提高电锅炉温度控制系统的性能,可以通过以下方式进行系统优化:1.根据实际情况选择合适的控制策略,并进行参数调整,以获得最佳的系统响应;2.在传感器和控制器之间增加信号滤波模块,以消除传感器信号中的噪声和干扰;3.引入自适应控制算法,以根据系统当前的工作状态和性能要求,动态调整控制参数;4.在控制器中增加故障诊断和报警功能,以监测和预测系统的故障状态,并及时采取措施排除故障。
综上所述,电锅炉温度控制系统的设计应综合考虑系统组成、控制原理、控制策略和系统优化等因素,以实现稳定、高效的供热或蒸汽输出。
在实际工程中,还需要结合具体情况进行系统参数调整和优化,以满足用户的需求。
- 1、下载文档前请自行甄别文档内容的完整性,平台不提供额外的编辑、内容补充、找答案等附加服务。
- 2、"仅部分预览"的文档,不可在线预览部分如存在完整性等问题,可反馈申请退款(可完整预览的文档不适用该条件!)。
- 3、如文档侵犯您的权益,请联系客服反馈,我们会尽快为您处理(人工客服工作时间:9:00-18:30)。
1 引言1.1 系统设计背景近年来,加热炉温度控制系统是比较常见和典型的过程控制系统,温度是工业生产过程中重要的被控参数之一,冶金﹑机械﹑食品﹑化工等各类工业生产过程中广泛使用的各种加热炉﹑热处理炉﹑反应炉,对工件的处理均需要对温度进行控制。
因此,在工业生产和家居生活过程中常需对温度进行检测和监控。
由于许多实践现场对温度的影响是多方面的,使得温度的控制比较复杂,传统的加热炉电气控制系统普遍采用继电器控制技术,由于采用固定接线的硬件实现逻辑控制,使控制系统的体积增大,耗电多,效率不高且易出故障,不能保证正常的工业生产。
随着计算机控制技术的发展,传统继电器控制技术必然被基于计算机技术而产生PLC控制技术所取代。
而PLC 本身优异的性能使基于PLC控制的温度控制系统变的经济高效稳定且维护方便。
这种温度控制系统对改造传统的继电器控制系统有普遍性意义。
通过本设计可以熟悉并掌握西门子S7-300PLC的原理与功能以及它的编程语言,以自动控制理论为指导思想,解决工业生产及生活中温度控制的问题。
1.2 系统工作原理加热炉温度控制系统基本构成如图1-1所示,它由PLC主控系统、固态继电器、加热炉、温度传感器等4个部分组成。
PLC主控系统图1-1 加热炉温度控制系统基本组成加热炉温度控制实现过程是:首先温度传感器将加热炉的温度转化为电压信号,PLC主控系统内部的A/D将送进来的电压信号转化为西门子S7-300PLC可识别的数字量,然后PLC将系统给定的温度值与反馈回来的温度值进行比较并经过PID运算处理后,给固态继电器输入端一个控制信号控制固态继电器的输出端导通与否从而使加热炉开始加热或停止加热。
既加热炉温度控制得到实现。
其中PLC主控系统为加热炉温度控制系统的核心部分起着重要作用。
1.3 系统组成本系统的结构框图如图2-3所示。
由图1-2可知,温度传感器采集到数据后送给S7-300PLC,S7-300PLC通过运算后给固态继电器一个控制信号从而控制加热炉的导通与否。
上位机是编写PLC程序以及监控温度的变化。
1.4 系统设计目标及技术要求本系统应能够控制在设定值的±5℃的误差范围内并且具有温度上下限报警功能和故障报警功能。
由学校提供,模拟真实锅炉的温度检测和控制模块,可自行将0~10V模拟信号转化为占空比对锅炉进行加热。
输出的模拟信号也是0~10V,锅炉外接24V直流电源。
1.5 技术综述自70年代以来,由于工业过程控制的需要,特别是在电子技术的迅猛发展,以及自动控制理论和设计方法发展的推动下,国外温度控制系统发展迅速,并在智能化自适应参数自整定等方面取得成果。
在这方面以日本、美国、德国、瑞典等国技术领先,并且都生产出了一批商品化的性能优异的温度控制器及仪器仪表,在各行业广泛应用。
目前,国外温度控制系统及仪表正朝着高精度智能化、小型化等方面快速发展。
温度控制系统在国内各行各业的应用虽然已经十分广泛,但从国内生产的温度控制器来讲,总体发展水平仍然不高,同国外的日本、美国、德国等先进国家相比,仍然有着较大的差距。
目前,我国在这方面总体技术水平处于20世纪80年代中后期水平。
成熟产品主要以“点位”控制及常规的PID控制器为主,它只能适应一般温度系统控制,难于控制滞后复杂时变温度系统控制,而且适应于较高控制场合的智能化、自适应控制仪表国内技术还不十分成熟,形成商品化并广泛应用的控制仪表较少。
现在,我国在温度等控制仪表业与国外还有着一定的差距。
温度控制系统大致可分别用3种方式实现,一种是用仪器仪表来控制温度,这种方法控制的精度不高。
另一种是基于单片机进行PID控制,然而单片机控制的DDC 系统软硬件设计较为复杂, 特别是涉及到逻辑控制方面更不是其长处, 而PLC 在这方面却是公认的最佳选择。
随着PLC功能的扩充在许多PLC控制器中都扩充了PID 控制功能。
因此本设计选用西门子S7-300PLC来控制加热炉的温度。
2 下位机硬件系统设计随着微处理器、计算机和数字通信技术的飞速发展,计算机控制已经广泛地应用在所有的工业领域。
现代社会要求制造业对市场需求作出迅速反应,生产出小批量、多品种、多规格、高质量的产品。
为了满足这一要求,生产设备和自动化生产线的控制系统必须具有极高的可靠性和灵活性。
可编程序控制器(Programmable Logic Controller)正是顺应这一要求出现的,它是以微处理器为基础的通用控制装置。
本系统控制软件设计分为PLC的软件和工控机的软件设计两部分,其中下位机使用的软件为siemens公司的step7。
本章主要介绍西门子S7-300系列PLC以及其它硬件的组成与选型。
2.1 硬件系统框图2.2 传感器温度是一个基本的物理量,自然界中的一切过程无不与温度密切相关。
温度传感器是最早开发,应用最广的一类传感器。
根据美国仪器学会的调查,1990年,温度传感器的市场份额大大超过了其他的传感器。
从17世纪初伽利略发明温度计开始,人们开始利用温度进行测量。
真正把温度变成电信号的传感器是1821年由德国物理学家赛贝发明的,这就是后来的热电偶传感器。
50年以后,另一位德国人西门子发明了铂电阻温度计。
在半导体技术的支持下,本世纪相继开发了半导体热电偶传感器、PN 结温度传感器和集成温度传感器。
与之相应,根据波与物质的相互作用规律,相继开发了声学温度传感器、红外传感器和微波传感器。
这里我们主要介绍热电阻和热电偶。
2.2.1 热电阻热电阻是中低温区最常用的一种温度测量元件。
热电阻是基于金属导体的电阻值随温度的增加而增加这一特性来进行温度测量的。
当电阻值变化时,二次仪表便显示出电阻值所对应的温度值。
它的主要特点是测量精度高,性能稳定。
其中铂热电阻的测量精度是最高的。
铂热电阻根据使用场合的不同与使用温度的不同,有云母、陶瓷、簿膜等元件。
作为测温元件,它具有良好的传感输出特性,通常和显示仪、记录仪、调节仪以及其它智能模块或仪表配套使用,为它们提供精确的输入值。
若做成一体化温度变送器,可输出4-20mA标准电流信号或0-10V标准电压信号,使用起来更为方便。
热电阻大都由纯金属材料制成,目前应用最多的是铂和铜。
此外,现在已开始采用铬、镍、锰和铑等材料制造热电阻。
根据使用场合的不同,热电阻也有铠装式热电阻、装配式热电阻、隔爆式热电阻等种类,与热电偶类似。
铂电阻的工作原理是,在温度作用下,铂热电阻丝的电阻值随温度变化而变化,且电阻与温度的关系即分度特性符合IEC标准。
分度号Pt100的含义为在0℃时的名义电阻值为100Ω,目前使用的一般都是这种铂热电阻。
此外还有Pt10、Pt200、Pt500和Pt1000等铂热电阻,Cu50、Cu100的铜热电阻等。
2.2.2 热电偶工业热电偶作为测量温度的传感器,通常和显示仪表、记录仪表和电子调节器配套使用,它可以直接测量各种生产过程中不同范围的温度。
若配接输出4-20mA、0-10V 等标准电流、电压信号的温度变送器,使用更加方便、可靠。
对于实验室等短距离的应用场合,可以直接把热电偶信号引入PLC进行测量。
热电偶的工作原理是,两种不同成份的导体,两端经焊接,形成回路,直接测量端叫工作端(热端),接线端子端叫冷端,当热端和冷端存在温差时,就会在回路里产生热电流,这种现象称为热电效应;接上显示仪表,仪表上就会指示所产生的热电动势的对应温度值,电动势随温度升高而增长。
热电动势的大小只和热电偶的材质以及两端的温度有关,而和热电偶的长短粗细无关。
根据使用场合的不同,热电偶有铠装式热电偶、装配式热电偶、隔爆式热电偶等种类。
装配式热电偶由感温元件(热电偶芯)、不锈钢保护管、接线盒以及各种用途的固定装置组成。
铠装式热电偶比装配式热电偶具有外径小、可任意弯曲、抗震性强等特点,适宜安装在装配式热电偶无法安装的场合,它的外保护管采用不同材料的不锈钢管,可适合不同使用温度的需要,内部充满高密度氧化绝缘体物质,非常适合于环境恶劣的场合。
隔爆式热电偶通常应用于生产现场伴有各种易燃、易爆等化学气体的场合,如果使用普通热电偶极易引起气体爆炸,则在这种场合必须使用隔爆热电偶。
热电偶传感器有自己的优点和缺陷,它灵敏度比较低,容易受到环境干扰信号的影响,也容易受到前置放大器温度漂移的影响,因此不适合测量微小的温度变化。
由于热电偶温度传感器的灵敏度与材料的粗细无关,用非常细的材料也能够做成温度传感器。
也由于制作热电偶的金属材料具有很好的延展性,这种细微的测温元件有极高的响应速度,可以测量快速变化的过程,如燃烧和爆炸过程等。
对一般的工业应用来说,为了保护感温元件避免受到腐蚀和磨损,总是装在厚厚的护套里面,外观就显得笨大,对于温度场的反应也就迟缓得多。
使用热电偶的时候,必须消除环境温度的波动对测量带来的影响。
有的把它的自由端放在不变的温度场中,有的使用冷端补偿器抵消这种影响。
当测量点远离仪表时,还需要使用热电势率和热电偶相近的导线来传输信号,这种导线称为补偿导线。
本设计选用镍铬-镍硅N型热电偶。
2.3 PLC的基本概念可编程序控制器简称为PLC,它的应用面广、功能强大、使用方便,已经成为当代工业自动化的主要支柱之一。
PLC已经广泛地应用在各种机械设备和生产过程的自动控制系统中,PLC在其它领域,例如在民用和家庭自动化设备中的应用也得到了迅速的发展。
2.3.1 S7-300简介S7-300是模块化的中小型PLC,适用于中等性能的控制要求。
品种繁多的CPU 模块、信号模块和功能模块能满足各种领域的自动控制任务,用户可以根据系统的具体情况选择合适的模块,维修时更换模块也很方便。
S7-300有很高的电磁兼容性和抗振动抗冲击能力,有350多条指令,其编程软件STEP7功能强大,可以使用多种编程语言。
S7-300采用紧凑的、无槽位限制的模块结构,各个模块都安装在导轨上,用螺栓锁紧即可。
模块如下:(1) 数字量输入模块数字量输入模块用于连接外部的机械触点和电子数字式传感器,例如二线式光电开关和接近开关等。
数字量输入模块将从现场传来的外部数字信号的电平转换为PLC 内部的信号电平。
输入电路中一般设有RC滤波电路,以防止由于输入触点抖动或外部干扰脉冲引起的错误输入信号,输入电流一般为数毫安。
(2)数字量输出模块SM 322数字量输出模块将S7-300的内部电平信号转化为控制过程所需的外部信号电平,同时具有隔离和功率放大的作用。
输出模块的功率放大元件有驱动直流负载的大功率晶体管和场效应晶体管、驱动交流负载的双向晶闸管或固态继电器,以及既可以驱动交流负载又可以驱动直流负载的小型继电器。
输出电流典型值为0.5~2A,负载电源由外部现场提供。
(3)数字量输入/输出模块SM323是S7-300的数字量输入/输出模块,它由两种型号可供选择。