车削刀具选择
车刀种类和角度选择原则详解
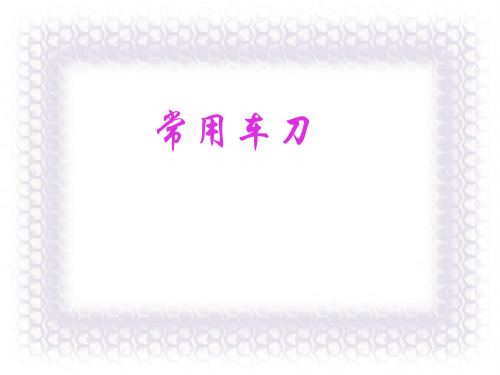
车刀不对准工件中心对角度的影响
五、车刀刃磨
无论硬质合金车刀(焊接)或高速钢 车刀,在使用之前都要根据切削条 件所选择的合理切削角度进行刃磨 ,一把用钝了的车刀,为恢复原有 的几何形状和角度,也必须重新刃 磨。
重 要 性
三分手艺、七分刀 徒弟的手、师傅的刀
1.磨刀步骤(图a~d)
⑴磨前刀面 把前角和刃倾角磨正确。 ⑵磨主后刀面 把主偏角和主后角磨正确。 ⑶磨副后刀面 把副偏角和副后角磨正确。 ⑷磨刀尖圆弧 圆弧半径约0.5~2mm左右。 ⑸研磨刀刃 车刀在砂轮上磨好以后,再用油石加些机油研磨车 刀的前面及后面,使刀刃锐利和光洁。这样可延长车刀的使用寿命。 车刀用钝程度不大时,也可用油石在刀架上修磨。硬质合金车刀可 用碳化硅油石修磨。
前角γo
——在主切削刃选定点的正交平面po内, 前刀面与基面之间的夹角
。
后角αo
——在正交平面po内,主后刀面与切削 平面之间的夹角。
主偏角κr
——主切削刃在基面上的投影与进给方 向的夹角。
刃倾角λs ——在切削平面ps内,主切削刃与 基面pr的夹角。
其他角度:
副前角γoˊ、 副后角αoˊ、 副偏角κrˊ、 刃倾角λsˊ
3.主偏角、副偏角的选择 (1)主偏角的选择 A、主偏角κr的增大或减小对切削加工有利的一 面 在背吃刀量ap与进给量f 不变时,主偏角κr减小 将使切削厚度hD减小,切削宽度bD增加,参加 切削的切削刃长度也相应增加,切削刃单位长度 上的受力减小,散热条件也得到改善。 主偏角κr减小时,刀尖角增大,刀尖强度提高, 刀尖散热体积增大。 所以,主偏角κr减小,能提高刀具耐用度。
(4)良好的工艺性和经济性
刀具的选择

刀具的选择,如何选择刀具1.豆丁网址:刀具的选择原则2.(1)尽可能选择大的刀杆横截面尺寸,较短的长度尺寸进步刀具的强度和刚度,减小刀具振动;3.(2)选择较大主偏角(大于75°,接近90°);粗加工时选用负刃倾角刀具,精加工时选用正刃倾角刀具;4.(3)精加工时选用无涂层刀片及小的刀尖圆弧半径;5.(4)尽可能选择标准化、系统化刀具;6.(5)选择正确的、快速装夹的刀杆刀柄。
7. 2.选择车削刀具的考虑要点8.数控车床一般使用标准的机夹可转位刀具。
机夹可转位刀具的刀片和刀体都有标准,刀片材料采用硬质合金、涂层硬质合金等。
9.数控车床机夹可转位刀具类型有外圆刀、端面车刀、外螺纹刀、切断刀具、内圆刀具、内螺纹刀具、孔加工刀具(包括中心孔钻头、镗刀、丝锥等)。
10.11.首先根据加工内容确定刀具类型,根据工件轮廓外形和走刀方向来选择刀片外形(如图所示)。
主要考虑主偏角,副偏角(刀尖角)和刀尖半径值。
12.13.14.可转位刀片的选择:15.(1)刀片材料选择:高速钢、硬质合金、涂层硬质合金、陶瓷、立方碳化硼或金刚石。
16.(2)刀片尺寸选择:有效切削刃长度、主偏角等。
17.(3)刀片外形选择:依据表面外形、切削方式、刀具寿命等。
18.(4)刀片的刀尖半径选择19.1)粗加工、工件直径大、要求刀刃强度高、机床刚度大时选大刀尖半径值。
20.2)精加工、切深小、细长轴加工、机床刚度小选小刀尖半径值。
21.3.选择铣削刀具的考虑要点22.在数控铣床上使用的刀具主要立铣刀、面铣刀、球头刀、环形刀、鼓形刀和锥形刀等。
如图所示。
常用到面铣刀、立铣刀、球头铣刀和环形铣刀。
除此以外还有各种孔加工刀具,如钻头(锪钻、铰刀、丝锥等)镗刀等。
23.面铣刀(也叫端铣刀)如图所示,面铣刀的圆周表面和端面上都有切削刃。
面铣刀多制成套式镶齿结构和刀片机夹可转位结构,刀齿材料为高速钢或硬质合金,刀体为40Cr。
24.立铣刀如图所示,立铣刀是数控机床上用得最多的一种铣刀。
不锈钢的车削技巧

不锈钢的车削技巧主要包括以下几个方面:1.刀具选择:选择适合不锈钢车削的刀具非常重要。
通常,选择具有较高耐热性、耐磨性和与不锈钢亲和作用小的刀具材料,如高碳、高钒或钼系的高速钢。
此外,刀具的几何形状和角度也需要根据具体加工要求进行选择。
2.切削用量选择:切削用量包括切削速度、进给量和切削深度。
对于不锈钢的车削,切削速度通常较低,一般为普通碳钢切削速度的40%~60%。
进给量和切削深度也需要根据具体情况进行选择,以避免刀具过度磨损和工件表面质量下降。
3.冷却液选择:使用合适的冷却液可以有效降低切削温度,减少刀具磨损和提高工件表面质量。
对于不锈钢的车削,通常选择具有较好冷却和润滑性能的冷却液。
4.操作技巧:在车削不锈钢时,需要注意以下几点操作技巧:首先,保持刀具的锋利,及时更换磨损的刀具;其次,避免使用过大的切削用量,以减少刀具的受力;最后,注意工件的装夹方式和切削力的方向,以避免工件变形或振动。
此外,还需要注意以下几点:1.由于不锈钢的塑性大、韧性高,车削时容易产生积屑瘤和鳞刺,这不仅影响工件的表面粗糙度,还会使刀具的磨损加快。
因此,需要选择合适的刀具材料和几何角度,以及合理的切削用量来避免这些问题的产生。
2.不锈钢的导热性差,导致切削热无法及时散出,使刀具的刃口温度升高,加剧刀具磨损。
为了降低切削温度,可以采用浇注冷却液的方法。
3.在车削过程中,应随时注意观察切削情况,如发现异常现象(如振动、噪声、温度升高等),应及时采取措施进行调整。
4.对于不同种类和规格的不锈钢材料,其车削性能也会有所不同。
因此,在实际加工前,最好先进行一些试验性切削,以确定最佳的切削参数和工艺方案。
总之,掌握不锈钢的车削技巧需要综合考虑多个因素,包括刀具选择、切削用量、冷却液和操作技巧等。
通过合理的选择和调整这些参数,可以提高加工效率、降低生产成本并获得高质量的工件。
车削刀具的选择

车削刀具的选择PVLN用于外圆和仿型加工(背面可逃避50°)PDJN和PVJN 这两种主要用在仿型加工中的,也可加工外圆和端面的,只是其刀尖强度有限,不适合于重切削的粗车.(背面可逃避32°)PSSN 可加工外圆和倒角(背面可逃避45°)PSBN和PTGN 一般加工外圆PSKN和PTFN加工端面PDHN 除加工外圆\端面外,还可以加工大圆弧的曲线加工(背面可逃避17.5°)PRGN和PRGC 是用于加工车削外圆/端面/仿型加工(背面可逃避45°和60°)PRXC 除上述的加工外还可以短距离纵向切削(背面可逃避45°)PVVN适用于横向大曲面(如大球体等)楔型紧固和双重压紧:W和M型夹紧可靠,适用于切削力较大的场合,如加工条件恶劣、钢的粗加工、铸铁等短屑的加工等WWLN和WTKN用于加工外圆和端面(背面可逃避5°和15°)WTJN用于加工外圆和仿型(背面可逃避27°)WTEN用于外圆加工(背面可逃避27°)MVVN用于大曲面和外圆加工的(72.5°)MVLN用于外圆和仿型加工(背面可逃避45°)选外圆刀的关键:一定要知道刀具的工艺路线,也就是了解清楚工件图的曲线是如何,先外圆的时候要避免刀角的各个角与工件的接触,能避开就能完成其加工的要求了。
Ⅰ车孔刀与外圆车刀相比有如下特点:1.由于尺寸受到孔径的限制,装夹部分结构要求简单、紧凑,夹紧件最好不外露,夹紧可靠。
2.刀杆悬臂使用,刚性差,为增强刀具刚性尽量选用大断面尺寸刀杆,减少刀杆长度。
3.内孔加工的断屑、排屑可靠性比外圆车刀更为重要,因而刀具头部要留有足够的排屑空间。
Ⅱ。
常用的车刀有三种不同截面形状的刀柄,即圆柄、矩形柄和正方形柄。
普通型和模块式的圆柄车刀多用于车削加工中心和数控车床上。
矩形和方形柄多用于普通车床。
还有一些特殊用途的车孔刀,如柄部有切削液输送孔的,柄部装有减振机构的和用于重金属做刀柄的等,但是不常用。
精密车削所用的刀具及其切削用量的选择

图示为ห้องสมุดไป่ตู้精密车床上加工黄铜H62所用的金刚石精密车刀,工件要求表面粗糙度值为Ra0.03μm。为加强刀尖和刃口部位强度,采用前角γo=-5°~-10°,αo=2°~3°,过渡刃为0.05mm
车刀前面、后面的表面粗糙度值Ra应不大于0.02μm;刃倾角为10°,以利于排屑;车刀采用6°后角和3°副后角,可以减小振动,并使刀具后面对工件有轻微的挤压作用
切削速度越高,获得的表面粗度值越小,但刀具磨损及振动也随之加剧,所以应根据实际情况合理选择
进给量
f
一般选f=0.01~0.04mm/r
一般取f=0.02~0.04mm/r
背吃刀量ap
双面加工余量为0.3~0.5mm
半精加工ap=0.05~0.1mm,精加工时ap=0.02~0.05mm,超精密加工时ap=0.003~0.006mm
精密车削所用的刀具及其切削用量的选择
车刀
金刚石车刀
硬质合金精密车刀
刀具材料种类
有天然单晶金刚石和人造聚晶金刚石两种
有细颗粒的硬质合金和超细颗粒的硬质合金两种
刀具材料特点和应用
金刚石具有硬度高、耐磨性好、刃口锋利和摩擦因数小等优点,但韧性很差,刃磨困难
金刚石刀具适用于有色金属及其合金(如铝、紫铜、黄铜、巴氏合金、铍铜、锌等)及非金属材料(如酚醛塑料、陶瓷等)的精密车削
用于精密车削铜料,能获得镜面
切削用量
的选择
切削速度vc
可采用很高的切削速度,也可以低速进行切削,例如在CGM6125车床上加工黄铜H62材料时,可选切削速度vc≥68m/min或vc≤17m/min
一般采用高的切削速度。车铝合金材料vcmax=350m/min,车铜合金材料vcmax=400m/min;车镁合金材料vcmax=100m/min
刀具及切削参数选择
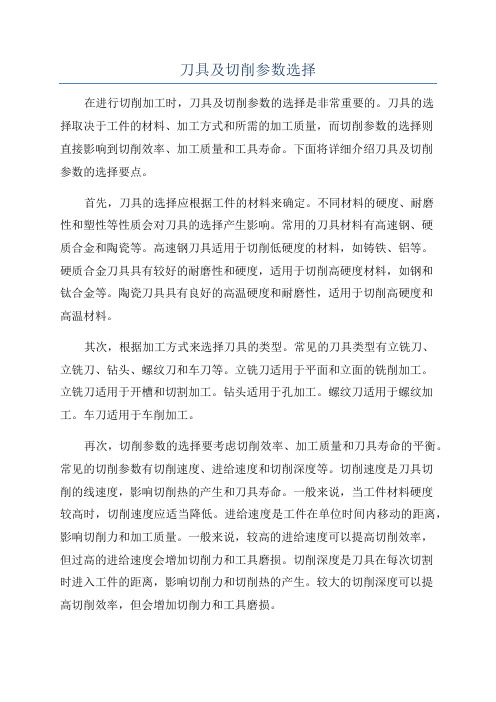
刀具及切削参数选择在进行切削加工时,刀具及切削参数的选择是非常重要的。
刀具的选择取决于工件的材料、加工方式和所需的加工质量,而切削参数的选择则直接影响到切削效率、加工质量和工具寿命。
下面将详细介绍刀具及切削参数的选择要点。
首先,刀具的选择应根据工件的材料来确定。
不同材料的硬度、耐磨性和塑性等性质会对刀具的选择产生影响。
常用的刀具材料有高速钢、硬质合金和陶瓷等。
高速钢刀具适用于切削低硬度的材料,如铸铁、铝等。
硬质合金刀具具有较好的耐磨性和硬度,适用于切削高硬度材料,如钢和钛合金等。
陶瓷刀具具有良好的高温硬度和耐磨性,适用于切削高硬度和高温材料。
其次,根据加工方式来选择刀具的类型。
常见的刀具类型有立铣刀、立铣刀、钻头、螺纹刀和车刀等。
立铣刀适用于平面和立面的铣削加工。
立铣刀适用于开槽和切割加工。
钻头适用于孔加工。
螺纹刀适用于螺纹加工。
车刀适用于车削加工。
再次,切削参数的选择要考虑切削效率、加工质量和刀具寿命的平衡。
常见的切削参数有切削速度、进给速度和切削深度等。
切削速度是刀具切削的线速度,影响切削热的产生和刀具寿命。
一般来说,当工件材料硬度较高时,切削速度应适当降低。
进给速度是工件在单位时间内移动的距离,影响切削力和加工质量。
一般来说,较高的进给速度可以提高切削效率,但过高的进给速度会增加切削力和工具磨损。
切削深度是刀具在每次切割时进入工件的距离,影响切削力和切削热的产生。
较大的切削深度可以提高切削效率,但会增加切削力和工具磨损。
此外,还应考虑冷却润滑剂的选择和使用。
合适的冷却润滑剂可以降低切削热的产生,减小工具磨损,提高加工质量。
综上所述,刀具及切削参数的选择需要考虑工件材料、加工方式和所需加工质量。
合理选择刀具类型和切削参数可以提高切削效率、加工质量和工具寿命。
在实际应用中,还需要根据具体情况进行调整和优化。
1.6 数控车刀的选择与使用解析

2018/10/6
15
“确定刀片的断屑槽型代码或ISO断 屑范围代码”图标如前图所示。ISO标准 按切削深度aP和进给量的大小将断屑范 围分为A、B、C、D、E、F六个区,其中A、 B、C、D为常用区域,WALTER标准将断屑 范围分为图中各色块表示的区域,ISO标 准和WALTER标准可结合使用,如前图所 示。根据选用标准,按加工的切削深度 和合适的进给量来确定刀片的WALTER断 屑槽型代码或ISO分类范围。
2018/10/6 4
2018/10/6
5
1、机床影响因素
“机床影响因素”图标如图所示。为保 证加工方案的可行性、经济性,获得最佳加 工方案,在刀具选择前必须确定与机床有关 的如下因素: (1)机床类型:数控车床、车削中心; (2)刀具附件:刀柄的形状和直径,左切和右 切刀柄; (3)主轴功率; (4)工件夹持方式。
2018/10/6
6
2、选择刀杆
“选择刀杆”图标如图所示。其中,刀杆类 型尺寸见下表。
选用刀杆时,首先应选用尺寸尽可能大的刀杆,同时 要考虑以下几个因素: (1)夹持方式; (2)切削层截面形状,即切削深度和进给量; (3)刀柄的悬伸。
2018/10/6
7
3、刀片夹紧系统
刀片夹紧系统常用杠杆式夹紧系统,“杠杆式夹紧系 统”图标如图所示。 (1) 杠杆式夹紧系统 杠杆式夹紧系统是最常用的刀片夹紧方式。其特点为: 定位精度高,切屑流畅,操作简便,可与其它系列刀具产品 通用。 (2)螺钉夹紧系统 特点:适用于小孔径内孔以及长悬伸加工
1.9 数控车刀的选择与使用
由于数控车床的加工对象多为回转体, 一般使用通用三爪卡盘夹具,因而在工艺装 备中,我们将以WALTER系列车削刀具为例, 重点讨论车削刀具的选用及使用问题。
车刀的分类和选择

车刀的分类和选择车刀是机械车床上常用的切削工具之一,它对加工效率和加工质量都有重要影响。
选择适合的车刀分类和类型对于提高加工效率、降低切削成本至关重要。
本文将介绍车刀的分类和选择方法,帮助读者更好地理解和应用车刀。
一、车刀的分类根据车刀的结构和用途,可以将车刀分为以下几类:1. 工具刀片:广义上的车刀,通常由刀柄和刀片组成。
刀柄负责固定刀片,刀片进行切削工作。
工具刀片多用于外圆和内圆粗加工,适用于不同材料的车削操作。
2. 特殊刀片:用于特殊形状的车削。
如内外圆刀片、角刀片等。
特殊刀片适用于需要切削复杂外形的工件,提供更好的切削质量和加工精度。
3. 超硬刀片:采用高硬度材料制成的刀片,如金刚石、立方氮化硼等。
超硬刀片具有较高的硬度和耐磨性,适用于加工硬质材料如铸铁、合金钢等。
4. 镗刀:用于车削大孔径和参考表面。
镗刀采用特殊设计,能够提供更高的刚性和稳定性,适用于大直径工件和高精度加工。
5. 切断刀片:用于切断工件的刀片,有直刃和曲刃两种形式。
切断刀片适用于金属材料的切割,如车削工件的分离和切除。
二、车刀的选择选择适合的车刀是提高车削加工效率的关键。
以下是选择车刀时应考虑的因素:1. 加工材料:根据工件材料的不同,选择不同材质和刀片类型的车刀。
对于铸铁、不锈钢等材料,可选择高速钢刀片;对于合金钢、钛合金等硬材料,应选择超硬刀片。
2. 加工工艺:根据不同的车削工艺,选择合适的车刀类型。
对于粗车、精车和薄层车削等工艺,可以选择不同切削参数和刀片结构的车刀。
3. 切削条件:根据切削深度、进给速度和切削速度等切削条件,选择适合的刀片形状和材料。
对于大切削深度和高切削速度的加工,应选择具有高硬度和耐磨性的刀片。
4. 加工精度:根据对加工精度的要求,选择合适的刀片精度和结构。
如果需要高精度的加工,应选择刀片精度高、几何形状复杂的刀片。
5. 经济性:根据加工成本和刀具寿命,选择经济合理的车刀。
应选用具有长寿命和更换成本低的刀具,以优化切削成本。
车削切削用量选取参考表讲解学习
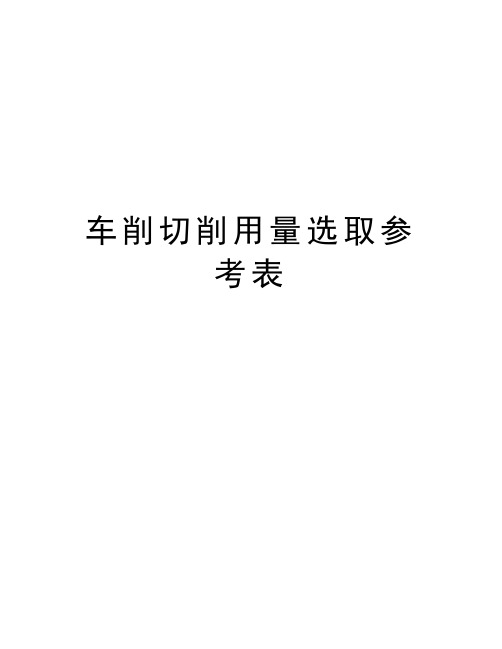
2.1
0.9
>360~500
1.4
0.7
1.5
0.7
1.5
0.8
1.7
0.8
1.9
0.9
2.2
1
1、粗加工,表面粗糙度为Ra50~12.5时,一次走刀应尽可能切除全部余量。
2、粗车背吃刀量的最大值是受车床功率的大小决定的。中等功率机床可以达到8~10mm。
二、高速钢及硬质合金车刀车削外圆及端面的粗车进给量
工件材料
车刀刀杆尺寸(mm)
工件 直径(mm)
切深
≤3
3~5
5~8
8~12
>12
进给量fmm/r
碳素结构钢、合金结构钢、耐热钢
16×25
20
0.3~0.4
—
—
—
—
40
0.4~0.5
0.3~0.4
—
—
—
60
0.5~0.7
0.4~0.6
0.3~0.5
—
—
100
0.6~0.9
0.5~0.7
0.5~0.6
0.4~0.5
275-335
0.25
8
17-21
0.5
66-72
82-90
0.75
YT5
105-120
0.5
215-245
0.4
高强度钢
225~350
1
20-26
0.18
90-105
115-135
0.18
YT15
150-185
0.18
380-440
0.13
>300HBS时宜用W12Cr4V5Co5及W2Mo9Cr4VCo8
浅述数控车削加工中刀具和切削液的选择

3
洲
岫或动 物 形成跆
车削精密螺皱
1切 断 刀; 9 " 刀 ;_ 0右偏 刀 ; 弯头 车 一 2 0左偏 - 39。 4 - 刀 ; 直头车 刀 ; 成 形车 刀;一 5 一 6 一 7 宽刃精车 刀;一 8 外螺纹 车刀 ; 端 面车刀 ; 一 9 一 1 内螺纹 车刀 ;1 0 1一 内槽车刀 ;2 通孔车刀 ;3 盲孔车刀 1_ 1一 图 3常用车刀类型 袁 1常用车刀的基本 用途
示
乳化油 ,用 4  ̄S 0 O倍的水稀释而成, 车削、钻孔 冷却和清洗性能好 轧{ 也液 2 )以矿物油为主,少量 表面话性剂的 车削 、攻螺纹 乳化油,用 1 ~2 O 0倍的水稀释而成 , 冷却和润滑性能好 3 、在乳化液中加^极压添加剂 高速车削
、
钻孔
1 )矿 2 . 1切削液 的作用 2 .冷却作 用 .I 1 切 削液 可以将 切削过程 中所产生 的热量迅 速地 从切 削区带走 , 切削温度降低 。 使 切削液 的 流动 性越好 , 、 系数 和汽化热等 参数越 比热 导热 高, 则冷却性能越好 。 2 . 滑作用 .2润 1 切 削液能在刀具的前后刀面 与工 件之间形 成一 层润滑薄膜 , 以避 免刀具与工件 或切屑 可 间的直接接触 , 减轻摩擦 和黏结程度 , 因而可减 轻刀具 的磨 损 , 高工件 表面的加工质量。 提 其润 滑性 能取决于切削液 的渗透能力 、 形成 润滑膜 的能力 和强度 。 2- 1 3清洗作用 切 削液 可以冲走切 削 区域和 机床上的细碎 切屑 和脱落的磨粒 , 而避免切屑时黏 附刀具 、 从 堵塞排 屑和划 伤已加 工表面 。 因此 , 要求切削液 有 良好 的流动性 ,并且在 使用时有足够 大的压 力和流 量。 2. .4防锈作用 1 为减轻 工件 、 刀具和机床受周 围介质 ( 如空 气、 水分等 ) 的腐蚀 , 要求切 削液 具有 一定 的防 锈作用 。 防锈作 用的好坏 , 取决于切削液本身 的
车削刀具简介

车削刀具简介一、车刀的种类直头车刀 45°弯头车刀 75°偏刀90度偏刀切断刀扩孔车刀(通孔)扩孔车刀(盲孔)螺纹车刀车刀的种类1.按用途可分为:①外圆车刀主偏角一般取45°、75°和90°,用于车削外圆表面和台阶;②端面车刀主偏角一般取45°,用于车削端面和倒角,也可用来车外圆;③切断、切槽刀用于切断工件或车沟槽。
④镗孔刀用于车削工件的内圆表面,如圆柱孔、圆锥孔等;⑤成形刀有凹、凸之分。
用于车削圆角和圆槽或者各种特形面;⑥内、外螺纹车刀用于车削外圆表面的螺纹和内圆表面的螺纹。
2.按结构可分为:①整体式车刀刀头部分和刀杆部分均为同一种材料。
用作整体式车刀的刀具材料一般是整体高速钢,②焊接式车刀刀头部分和刀杆部分分属两种材料。
即刀杆上镶焊硬质合金刀片,而后经刃磨所形成的车刀。
③机械夹固式车刀刀头部分和刀杆部分分属两种材料。
它是将硬质合金刀片用机械夹固的方法固定在刀杆上的。
它又分为机夹重磨式和机夹不重磨式两种车刀。
图2所示即是机夹重磨式车刀。
图3即是机夹不重磨车刀。
两者区别在于:后者刀片形状为多边形,即多条切削刃,多个刀尖,用钝后只需将刀片转位即可使新的刀尖和刀刃进行切削而不须重新刃磨;前者刀片则只有一个刀尖和一个刀刃,用钝后就必须的刃磨。
图2 机夹重磨式车刀图3 机夹不重磨式车刀目前,机械夹固式车刀应用比较广泛。
尤其以数控车床应用更为广泛。
用于车削外圆、端面、切断、镗孔、内、外螺纹等。
3、常用车刀的用途如图4所示:外圆车刀(90°偏刀、75°偏刀、 60°偏刀)车外圆和台阶;端面车刀(45°弯头刀)车端面;切刀切槽和切断;螺纹车刀车内外螺纹;镗孔刀车内孔;滚花刀滚网纹和直纹;圆头刀车特形面。
图4 车刀用途示意图三、车刀的组成图5所示为车刀组成示意图。
它是由刀头和刀杆两部分组成。
刀头用于切削,又称切削部分;刀杆用于把车刀装夹在刀架上,又称夹持部分。
机床刀具的正确选择与使用方法
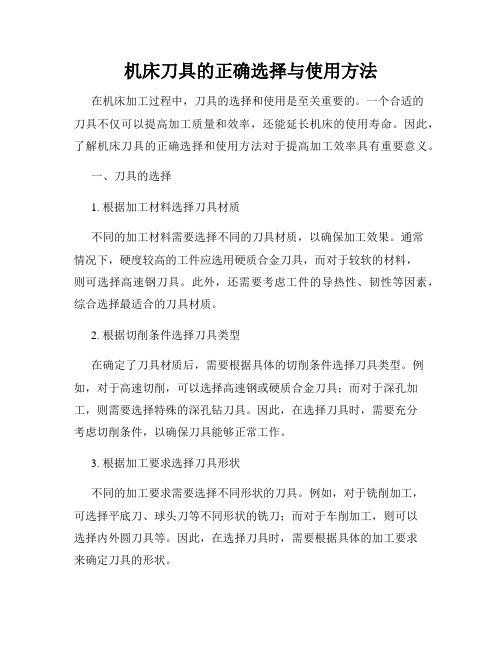
机床刀具的正确选择与使用方法在机床加工过程中,刀具的选择和使用是至关重要的。
一个合适的刀具不仅可以提高加工质量和效率,还能延长机床的使用寿命。
因此,了解机床刀具的正确选择和使用方法对于提高加工效率具有重要意义。
一、刀具的选择1. 根据加工材料选择刀具材质不同的加工材料需要选择不同的刀具材质,以确保加工效果。
通常情况下,硬度较高的工件应选用硬质合金刀具,而对于较软的材料,则可选择高速钢刀具。
此外,还需要考虑工件的导热性、韧性等因素,综合选择最适合的刀具材质。
2. 根据切削条件选择刀具类型在确定了刀具材质后,需要根据具体的切削条件选择刀具类型。
例如,对于高速切削,可以选择高速钢或硬质合金刀具;而对于深孔加工,则需要选择特殊的深孔钻刀具。
因此,在选择刀具时,需要充分考虑切削条件,以确保刀具能够正常工作。
3. 根据加工要求选择刀具形状不同的加工要求需要选择不同形状的刀具。
例如,对于铣削加工,可选择平底刀、球头刀等不同形状的铣刀;而对于车削加工,则可以选择内外圆刀具等。
因此,在选择刀具时,需要根据具体的加工要求来确定刀具的形状。
二、刀具的使用方法1. 切勿超负荷使用刀具刀具在工作时会受到一定的负荷,如果超负荷使用,容易导致刀具磨损过快甚至断裂。
因此,在使用刀具时,需要根据切削条件合理设置切削参数,避免超负荷使用刀具。
2. 定期检查刀具状态刀具在使用过程中会出现磨损,因此需要定期检查刀具状态。
一旦发现刀具磨损严重或者出现其他异常情况,应及时更换或修磨刀具,以确保刀具的正常使用。
3. 注意刀具的保养刀具在使用过程中需要定期进行清洁和保养,以延长刀具的使用寿命。
在清洁时,应使用专用清洁剂擦拭刀具表面,防止刀具受到腐蚀。
同时,在使用完毕后,应将刀具储存在干燥通风的环境中,避免受潮生锈。
总结:正确选择和使用机床刀具对于提高加工效率和质量具有重要意义。
通过根据加工材料选择刀具材质、根据切削条件选择刀具类型、根据加工要求选择刀具形状等方法,能够有效提高刀具的使用效率和寿命。
山特维克车削理论及车刀选择
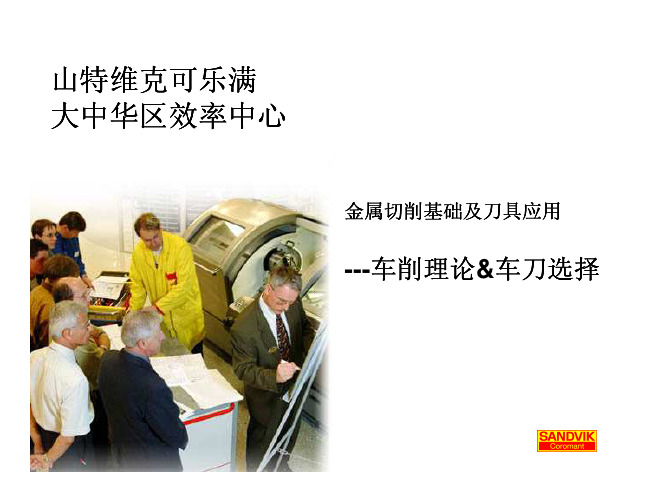
/April 20, 2006
3
车削中的常用公式
πx D x n Vc = 1000 Q = Vc x ap x fr
VC(线速度)
Vc和n的关系
/April 20, 2006
4
车削三要素与刀具寿命
1. 切深增加 切深增加50%刀片磨损增加 刀片磨损增加 20%。 。 2. 走刀量增加 走刀量增加20%刀片磨损增加 刀片磨损增加 20%; ; 3. 切削速度增加 切削速度增加20%刀片磨损增 刀片磨损增 加50%; ;
16
切削刃的强化
负刃带提高了切削刃的强度
负刃带提高了切削刃的强度,但会产生更高的切削力
/April 20, 2006
17
刀片前角
正前角和负前角切削作用
刀片前刃面与通过工件轴线的水平面之间的夹角
/April 20, 2006
18
CVD 涂层的热裂纹
涂层 基体
涂层过程中 CVD coating
冷却中
6.0
3.0
1.5
1.0
0.5
进给量 fn (mm/rev)
0.1
/April 20, 2006
0.2
0.3
15
0.4
0.5
0.6
切削刃的强化
通过圆角处理获得最终的微观槽形
在涂层之前进行ER处理(切削刃倒圆),并获得切削刃的最终形 状(微观槽形) W / H之间的关系取决于具体应用
/April 20, 2006
1. Vc: m/min 米/分钟 分钟 2. ap: mm 毫米 3. fr(fn): mm/r 毫米 转 毫米/转
/April 20, 2006 2
切屑形状与切削参数的对应关系
车削刀具选择

卧式数控车床选刀目录一机卡车刀的选用 (1)二孔加工刀具的选用 (9)三切断和切槽刀 (12)四螺纹车刀 (13)五刀具材料 (16)六刀具厂商 (17)七刀具干预图 (18)八刀具允许的最大转动惯量 (19) (21)数控车床刀具系统比卧车复杂。
要求安装数量多,安装可靠,自动换刀,装卸方便迅速还要求切削时间短以提高生产率。
因此普遍采用机卡车刀。
机卡车刀是把压制有合理的几何参数,在一定的切削用量范畴内保证卷屑,断屑并有几个刀刃的刀片,用机械卡固方式装卡在标准刀体上的一种新型刀具。
它防止了硬质合金刀片在焊接中产生的种种不良后果,因此能充分发挥刀片材料原有的切削性能,提高了车刀的耐用度和切削加工的生产率.另外刀体可重复使用,能节约大量制造刀体的钢材.还便于使刀具标准化和集中生产,同一型号刀片的几何形状较一致切削效果稳定.有利于提高零件加工质量,简化了刀具的管理工作.使用时,当刀刃磨损后,只需松开卡紧机构将刀片转一个角度,不必重磨,大大缩短了换刀.磨刀.装刀的辅助时间,而且可以防止刀片由于重磨而造成的缺陷.因此机卡车刀也叫不重磨车刀或可转位车刀。
除不可防止的情况外,为用户选用的都应该是机卡车刀。
一机卡车刀的选用侧重外外表车刀的选用。
内孔车刀大体相同,其特殊性问题另做表达。
ISO对外外表车刀型号是如下表示的,它是国内外刀具厂商的统一标准。
选刀工作也就是确定型号中的各项内容,按选刀时考虑问题的大体顺序分叙如下:(一)刀片形状的选择:外内外表车刀刀片形状关系车刀类型,它取决于加工部位的形状,是选刀的最重要内容。
它主要涉及刀具的主偏角,刀尖角和有效刃数等。
一般来讲刀尖角愈大刀尖强度愈高,应尽量采用。
但刀尖角小干预现象少,适用于复杂型面,开挖沟槽及下坡的型面。
刀片形状甚多,某些厂家列出十几种,本厂实际只用过图1所示七种,也正是ISO规定的七种基本类型。
图1 图280°菱型刀片C,目前是我厂选用最多的。
硬车削轴承的刀具材质选择及案例

主要加工难点在于滚道弧度于滚道内粗糙度为 Ra0.4。
郑州华菱超硬材料有限公司
硬车削轴承的刀具材质选择及案例
硬车削风电轴承的刀具方案
风电轴承外环加工工况介绍:
月形槽内均匀分布若干个油孔,为强断续切削。 另月形槽滚道衔接处加工余量大,刀片承受切削力大。
• 热处理后的轴承,如风电轴承,冶金轴承,轮毂轴承单元,硬度一般在HRC50以上,对刀具的耐磨性和 寿命提出很高的要求。
• 大型轴承,如风电轴承直径大,热处理后加工余量2-6mm,加工余量不均,而且加工部位外环滚道月型 槽部位存在油孔,刀具需要很好的抗冲击韧性,反之就会很容易崩碎。
• 同时轴承对精度和表面粗糙度要求较高,如风电轴承的滚道弧度精度公差要求为0.08,滚道的表面粗糙 度为Ra0.4,很多刀具都满足不了要求,或者就是加工不了一个工件就不能使用了,影响工件质量。
硬车削轴承的刀具材质选择及案例
立方氮化硼刀具硬车削轴承时可承受的吃刀深度
ቤተ መጻሕፍቲ ባይዱ特性方向
韧性(粗加工)
硬度(精加工)
热后硬车齿轮 的精加工
刀具材质
BN-S20 BN-H20 BN-S200 BN-H11 BN-H05 BN-H10 BN-H21 BN-H05 C25(涂层CBN刀片) BN-H10 C25(涂层CBN刀片) BN-H21 C25(涂层CBN刀片)
硬车削轴承的刀具材质选择及案例
硬车削风电轴承的刀具方案
硬车削风电轴承外环挡边的案例:
加工部位:风电轴承外环挡边
加工尺寸:2750mm
工件材质:42CrMo4
数控车削刀具选用

任务4.1 数控车削刀具及选用
4.1.3熟悉刀具基本几何参数及选用
1.车刀的几何形状 金属切削加工所用的刀具种类繁多、形状各异,但是它们参
加切削的部分在几何特征上都有相同之处。外圆车刀的切削 部分可作为其他各类刀具切削部分的基本形态,其他各类刀 具就其切削部分而言,都可以看成是外圆车刀切削部分的演 变。因此,通常以外圆车刀切削部分为例来确定刀具几何参 数的有关定义。
上一页 下一页 返回
任务4.1 数控车削刀具及选用
③耐热性。刀具材料的耐热性要好,能承受高的切削温度, 具备良好的抗氧化能力。
④工艺性能和经济性。刀具材料应具备好的锻造性能、热处 理性能、焊接性能、磨削加工性能等,而且要追求高的性能 价格比。
2.各种刀具材料性能特点及应用 (1)金刚石刀具材料性能特点及应用 金刚石是碳的同素异构体,它是自然界已经发现的最硬的一
上一页 下一页 返回
任务4.1 数控车削刀具及选用
6.刃倾角选用 刃倾角表示刀刃相对基面的倾斜程度,刃倾角主要影响切屑
流向和刀尖强度。切削刃刀尖端倾斜向上,刃倾角为正值, 切削开始时刀尖与工件先接触,切屑流向待加工表面,可避 免缠绕和划伤已加工表面,对精加工和半精加工有利。切削 刃刀尖端倾斜向下,刃倾角为负值,切削开始时刀尖后接触 工件,切屑流向已加工表面;在粗加工开始,尤其是断续切削 时,可避免刀尖受冲击,起保护刀尖的作用,并可改善刀具 散热条件。
上一页 下一页 返回
任务4.1 数控车削刀具及选用
4.数控刀具应系列化、标准化和通用化 数控刀具实现系列化、标准化和通用化,可尽量减少刀具规
格,便于刀具管理,降低加工成本,提高生产效率。 5.为了保证生产稳定进行,数控刀具应能可靠地断屑或卷屑
车削切削用量选取参考表

0.75
YT5
170-220
0.5
335-490
0.4
中碳
175~225
1
52
0.2
165
200
0.18
YT15
305
0.18
520
0.13
4
40
0.4
125
150
0.5
YT14
200
0.4
395
0.25
8
30
0.5
100
120
0.75
YT5
160
0.5
305
0.4
碳 钢
低碳
100~200
4、加工淬硬钢时,进给量应减小。硬度为HRC45-56时,乘以修正系数:0.8, 硬度为HRC57-62,乘以修正系数:k=0.5。
三、按表面粗糙度选择进给量的参考值
工件材料
粗糙度等级(Ra)
切削速度(m/min)
刀尖圆弧半径
0.5
1
2
进给量fmm/r
碳钢及合金碳钢
10~5
≤50
0.3~0.5
0.45~0.6
1
0.3
1.1
0.3
—
—
—
—
>18~30
1
0.3
1
0.3
1.1
0.3
1.3
0.4
1.4
0.4
—
—
>30~50
1.1
0.3
1
0.3
1.1
0.4
1.3
0.5
1.5
0.6
1.7
0.6
>50~80
1.1
车削碳钢类零件的刀具选择

车削加工碳钢类零件目录第1章绪论 (2)1.1课题研究的背景及意义 (2)1.2本课题研究的目的及主要内容................................... 错误!未定义书签。
第2章刀具研究的基本要素. (4)2.1车削加工的概念与特点 (4)2.2碳钢的类别与特点 (4)2.3切削刀具的类别与特点 (4)第3章刀具选择的条件 (6)3.1切削刀具的材料 (6)3.2刀具的几何角度与刀具的选择 (7)第4章车削碳钢轴类零件的刀具选择 (10)4.1车削碳钢轴类零件的工艺 (10)4.2车削碳钢轴类零件的刀具选择 (10)第5章总结 (13)5.1总结 (13)5.2展望............................................................................... 错误!未定义书签。
参考文献. (14)致谢 (15)车削加工碳钢类零件的切削刀具选择研究摘要现代制造技术的发展,极大地推动了切削技术的进步。
随着生产加工过程快速化和精确化的需要,对金属切削刀具提出了高可靠度、高精度、长寿命、快速转位更换、断屑良好等更高要求。
现代加工刀具费用一般只占制造成本3~4%,但它对总制造成本影响却要大得多。
计划经济时代机械加工企业从控制加工成本出发制订刀具消耗定额进行成本控制,有些企业高效率进口设备上使用低性能焊接刀具,不能发挥设备性能反而造成更大浪费事实。
因此在切削加工中,根据不同加工特征,正确地选择所需刀具有十分重要的意义。
1.分析碳钢类零件特点的基础上,选择常用的碳钢为研究对象。
2.以普通的CA6140车床为车削载体,来研究车削刀具。
3.用车削加工轴类碳钢零件为例,做出刀具选择研究。
关键词:制造技术、车削加工、刀具第1章绪论1.1课题研究的背景及意义制造业是国民经济支柱产业。
我国已经成为世界加工厂,可我国制造业人均劳动生产率与美、欧、日等工业发达国家地区相比还有很大差距,只为欧、美、日等发达地区国家二十分之一左右。
数控车床常用数控刀具概述

数控加工刀具的选择
数控机床刀具的选用原则 刀具的选用应根据机床的加工能力、工
件材料的性能、加工工序、切削用量、以及 其他相关因素正确选用刀具和刀柄。
刀具选择的基本原则是:所选刀具应与 被加工材料相适应、安装调整方便、刚性好、 耐用度和精度高
数控刀具的种类
数控刀具的种类(按切削工艺分类)
1.车削刀具 (1)外圆车刀
三爪卡盘特点: 三个卡爪是同步运动的,能自动定心,一般不需
要找正。 卡爪:正爪
反爪——装夹直径较大的零件。 装夹特点:方便、省时、自动定心好,但夹紧力
小 适用范围:装夹外型规则的中、小型工件。
三爪卡盘装夹工件的找正
找正原因: (1)工件较长,旋转中心与主轴中心不重合 (2)卡盘使用时间过长,已失去应用的精度
固定顶尖刚性好,定心准确,但中心孔与顶尖之 间是滑动摩擦,易磨损和烧坏顶尖。因此只适用 于低速加工精度要求较高的工件。支承细小工件 时可用反顶尖,这时工件端部作成顶尖形。
活顶尖内部装有滚动轴承,顶尖和工件一起转动 ,能在高转速下正常工件。但活顶尖的刚性较差 ,有时还会产生跳动而降低加工精度。所以,活 顶尖只适用于精度要求不太高的工件。
为了防止工件由于切削力作用而产生]轴向 位移,可在卡盘内装一限位支承,或利用工件 的阶台作限位。
谢 谢!
顶尖
顶尖有前顶尖和后顶尖两种,用于定心并承受工 件的重力和切削力
前顶尖:
可直接安装在车床主轴锥孔中,也可用 三爪自定心卡盘夹住一自制有60°锥角 的钢制前顶尖。这种顶尖卸下后再次使 用时必须将锥面再车一刀,以保证顶尖 锥在的轴线与车床主轴旋转中心同轴。
后顶尖:
有固定顶尖和活顶尖两种。使用时可将后顶尖插 入车床尾座套筒的锥孔内。
数控加工工艺——第五章 数控加工刀具的选择
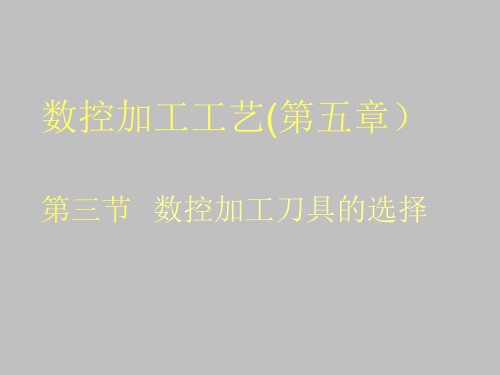
第三节 数控加工刀具的选择
第三节 数控加工刀具的选择
一、选择数控加工刀具应考虑的因素
选择数控加工刀片或刀具应考虑的因素是多方面的, 如机床的种类、型号、被加工的材料等,大致可归纳为以 下几点。
(1)被加工材料及性能。
(2)切削工艺的类别。
(3)被加工工件的几何形状、零件精度和加工余量等因 素。
扩孔直径较小或中等时,选用高速钢整体式扩孔;扩 20
第三节 数控加工刀具的选择
三、数控铣削刀具的选择
1.铣刀的类型 (1) 面铣刀。 如图5-6所示
图5-6 面铣刀
第三节 数控加工刀具的选择
硬质合金面铣刀按刀片和刀齿的安装方式不同,可分 为整体式、机夹-焊接式和可转位式3种(图5-7)。
图5-7硬质合金面铣刀
第三节 数控加工刀具的选择
(2) 立铣刀。立铣刀是数控机床上用得最多的一种 铣刀,其结构如图5-8所示。
第三节 数控加工刀具的选择
图5-15 直柄浅孔钻
第三节 数控加工刀具的选择
1-工件;2-钻套;3-外钻管;4-喷嘴;5-内钻管;6-钻头 图5-15 直柄浅孔钻
第三节 数控加工刀具的选择
2.扩孔刀具的选择
扩孔钻是主要的扩孔刀具,用于扩大孔径并提高孔的 加工精度。
扩孔钻的结构形式有高速钢整体式(图5-17(a))、镶 齿套式(图5-17(b))及硬质合金可转位式(图5-17(c)) 等。
可转位面铣刀分粗齿、细齿和密齿3种。粗车铣 刀一般用于粗铣钢件;粗铣带断续表面的铸件或平 稳条件下铣削钢件时,可选用细齿铣刀;而密齿铣 刀一般用于薄壁铸件的加工。
第三节 数控加工刀具的选择
由于铣削时有冲击,面铣刀的前角一般比车刀略小。 前角的数值主要根据刀具材料与工件材料来选择,其具 体数值可参见表5-2。
- 1、下载文档前请自行甄别文档内容的完整性,平台不提供额外的编辑、内容补充、找答案等附加服务。
- 2、"仅部分预览"的文档,不可在线预览部分如存在完整性等问题,可反馈申请退款(可完整预览的文档不适用该条件!)。
- 3、如文档侵犯您的权益,请联系客服反馈,我们会尽快为您处理(人工客服工作时间:9:00-18:30)。
卧式数控车床选刀目录一机卡车刀的选用 (1)二孔加工刀具的选用 (9)三切断与切槽刀 (12)四螺纹车刀 (13)五刀具材料 (16)六刀具厂商 (17)七刀具干涉图 (18)八刀具允许的最大转动惯量 (19)附录1、本厂卧式数控车床刀具安装尺寸 (21)数控车床刀具系统比卧车复杂。
要求安装数量多,安装可靠,自动换刀,装卸方便迅速还要求切削时间短以提高生产率。
因此普遍采用机卡车刀。
机卡车刀就是把压制有合理的几何参数,在一定的切削用量范畴内保证卷屑,断屑并有几个刀刃的刀片,用机械卡固方式装卡在标准刀体上的一种新型刀具。
它避免了硬质合金刀片在焊接中产生的种种不良后果,因此能充分发挥刀片材料原有的切削性能,提高了车刀的耐用度与切削加工的生产率.另外刀体可重复使用,能节约大量制造刀体的钢材.还便于使刀具标准化与集中生产,同一型号刀片的几何形状较一致切削效果稳定.有利于提高零件加工质量,简化了刀具的管理工作.使用时,当刀刃磨损后,只需松开卡紧机构将刀片转一个角度,不必重磨,大大缩短了换刀、磨刀、装刀的辅助时间,而且可以避免刀片由于重磨而造成的缺陷.因此机卡车刀也叫不重磨车刀或可转位车刀。
除不可避免的情况外,为用户选用的都应该就是机卡车刀。
一机卡车刀的选用侧重外表面车刀的选用。
内孔车刀大体相同,其特殊性问题另做叙述。
ISO对外表面车刀型号就是如下表示的,它就是国内外刀具厂商的统一标准。
选刀工作也就就是确定型号中的各项内容,按选刀时考虑问题的大体顺序分叙如下:(一)刀片形状的选择:外内表面车刀刀片形状关系车刀类型,它取决于加工部位的形状,就是选刀的最重要内容。
它主要涉及刀具的主偏角,刀尖角与有效刃数等。
一般来讲刀尖角愈大刀尖强度愈高,应尽量采用。
但刀尖角小干涉现象少,适用于复杂型面,开挖沟槽及下坡的型面。
刀片形状甚多,某些厂家列出十几种,本厂实际只用过图1所示七种,也正就是ISO规定的七种基本类型。
图1 图2 80°菱型刀片C,目前就是我厂选用最多的。
该种刀片刀尖角大小适中,刀片有较好的强度,散热性与耐用度。
装在刀杆上形成95°主偏角,它可用于端面、外圆、内孔台阶的加工。
因可沿图2示的三个方向进刀,台阶轴间的圆角、倒角亦可通过插补完成。
这种刀片的可卡固性好,可以用刀片的底面与非切削位置上的 80°刀尖角的相临两侧面定位,定位方式可靠。
且刀尖位置精度仅与刀片的外形精度有关,刀片换位精度较高。
该刀片的缺点就是有两个100°的刀尖往往不能很好利用。
或许有其它场合需要100°刀尖角做外圆、端面的耐冲击切削,但机会不多。
所以实际有效刃数只有两个,比正方形刀片S 有效刃数少一半。
55°菱型刀片D与35°菱型刀片V,因其刀尖角小所以干涉现象少,多用于复杂型面与沟槽加工如图3示,特别就是内外表面遇有下坡形状,一般都用这种刀形。
由于刀尖角小刀片强度低,特别就是35°V型刀片几乎都就是正前角刀片,强度尤低。
所以D、V形刀片更适合于切削用量小的零件、细长轴。
调整刀片方向可达轴向力较小,也常用于小孔径悬伸长的内孔加工与其它型面的精加工,半精加工。
因为刀尖角大的C型刀片,容易造成对工件的挤压使尺寸不稳定,对Cp值要求较高的加工表面,往往用D、V形刀片做精加工。
图3正三角形刀片T,正方形刀片S。
刀片强度高,价格最便宜,各刀刃都能得到利用。
由于这种刀片许多情况下只能往一个方向进给如图4示,所以往往用于单纯车外圆,端面。
也适于小孔径的孔加工。
S型刀片另一个优点就是有效切削刃长,达整个切削刃的2/3,更适于吃刀深大的切削。
图4圆形刀片R使用场合不就是很多,但有特殊用途。
像仿形切削一些曲面,加工越程槽,加工冲击力大的断续表面等。
R型刀片呈碟形,周边最高,沿周边就是封闭的卷屑槽,向任意方向走刀都有一定的前角,刀片磨损后可以转过一定的角度再次使用。
这种刀片的缺点就是切削力大,易产生振动。
凸三角形刀片W与C型刀片刀尖角相同,刀片能调换三个位置,比C型多一个位置而价格与C型差不多,故有代替C型刀片的趋势。
它的缺点与C型刀片比一就是刀片卡固不甚牢固,ISCAR在刀垫上采取了措施改善了,二就是刀刃长度小、有效切削刃也只能占切削刃的1/4,故不能做吃刀深很大的加工,而当前加工余量随毛坯的改善而减小,单边余量很少超过3mm,所以W型刀片在一些刀具厂已取代了C型刀片的领先地位。
近年又出现了一种80°的四边形-Q型刀片,如图5,它比C型刀片有效刃增加了一倍,但它在切削有直角的内孔、外圆时要受到刀刃长度的限制,通用性差。
本厂尚未选用过。
图5(二)车刀类型的选择:就就是刀杆头部的选择。
刀具要有较高的强度,又不能与工件产生干涉。
所以刀杆头部形式按主偏角与直头,偏头分有十几种形式,各形式规定了相应的代码。
应用时必须结合工件形状与刀片类型相协调。
80°菱型刀片C 及凸三角形刀片W 安装往往呈95°主偏角如图6。
圆形刀片R 主要安装形式如图7。
加工外圆端面 外圆 、仿形 外圆、 端面仿形图6 图7、正三角形刀片T,正方形刀片S 的主要安装形式如图8。
外圆 端面 外圆、倒角 外圆、端面图8外圆 、仿形55°菱型刀片D 与35°菱型刀片V 安装形式变化较多,主要安装形式如图9。
外圆 、仿形 外圆 、仿形 端面、外圆 、仿形图9外圆、倒角 外圆端面、倒角 端面 外圆外圆、仿形外圆、仿形 端面、外圆、仿形车刀类型的选择着眼于刀具的主偏角。
一般情况有直角台阶的工件可选择大于或等于90°主偏角的刀杆。
一般粗车可选主偏角45°~90°,精车可选45°~75°的中间切入、仿形`可选62°30'~117°30'的。
工艺系统刚度好时主偏角可选较小值,反之选较大值。
(三)刀片卡紧方式的选择:刀片形状与车刀类型选定后,样本上有时会出现几种刀片卡紧方式。
主要有C,D,M,P,S五种,简述其特点供选择参考。
图101 上压式卡紧C:卡紧压力大,通过两定位侧面获得稳定的定位与卡紧。
且卡紧元件少,装卸使用方便,但刀片上的压板对排屑有防碍,易被切屑擦伤。
它广泛应用于无孔刀片,陶瓷与立方氮化硼刀片。
2上压与销孔卡紧D:又称RC卡紧。
卡紧可靠、用于切削力较大的外圆重切,称之为牢固卡紧。
但内孔刀难以采用。
3上压与销孔双重卡紧M:卡紧可靠但结构不太紧凑。
切削力大的场合:如加工条件恶劣的钢的粗加工,铸铁短屑加工较适用。
4销孔卡紧P:就是杠杆式卡紧,用于刀片中心圆柱销孔卡紧。
定位与卡紧比较可靠,前面开放有利于排屑。
一般中、轻切削选用。
5螺钉卡紧S:又称螺纹偏心卡紧。
卡紧元件少,结构简单,装卸刀片与转位方便迅速,制造方便排屑无阻。
但松开或紧固螺纹偏心销不太方便。
断续切削时容易使偏心销受冲击与振动而失去自锁能力。
轻切削小孔切削的菱型刀片,三角形刀片与镗刀头应用较多。
(四)刀片法后角的选择:常用的有N(O°),C(7°),P(11°),E(20°),B(5°)等。
一般粗加工,半精加工多用N型,因系O°后角,刀片的正反面都可用,负前角的刀片几乎都采用N型。
刀片后角虽为O°但刀体本身安装刀片的平面有倾斜(通常就是7°),保证了刀具切削中的后角,半精加工可用C型,P型,也可用带断屑槽的N型刀片。
加工铸铁与硬钢用N型,加工不锈钢可用C型P型,仿形刀片也多用C型P型,加工铝合金则应用后角大的P型E型刀片。
加工弹性恢复性好的材料可选择大一些的后角。
一般镗刀片选用C型P型避免后面刮擦。
但大孔也可选用N型刀片。
(五)切削方向选择:即刀柄的左,右手方向。
有三种情况:R(右手),L(左手)与N(左右手)。
辩别方法:伸展手掌手背向上,姆指指示刀片方位,余四指指示刀头方向,符合左手即左手刀,符合右手即右手刀,如图11示。
选刀时要考虑前后刀架的区别;刀面朝上朝下的区别;主轴的旋转方向,以及刀架的进给方向。
一般情况下车床自右向左进刀,刀面朝上朝前。
所以经济型数控车床采用前刀架基本上用右手刀,而普及型用后刀架则为左手刀。
刀片方位 右手刀 左手刀 左右手刀右手刀图11(六)刀杆尺寸的选择:刀杆的基本尺寸有刀尖高度,刀杆宽度及长度。
在标准尺寸系列中,刀的高度宽度及长度都就是对应的。
选择时应按机床匹配。
其中最重要的就是刀尖高度,因为车刀刀尖必须处于车床主轴中心线的等高位置,因故不能匹配则由刀垫,刀夹予以解决。
刀杆长度由二十几种代码表示32~500的各种长度。
刀杆长度由夹持长度及悬伸量确定的,外圆刀杆悬伸量一般为刀尖高度的1、5倍,内孔刀的悬伸量则决定于孔深或加工部位的位置。
刀杆太长宁肯锯短也不要悬选择伸过长,因过长易导制振颤与干涉。
(七) 切削刃尺寸的选择:切削刃长度应根据加工余量来定。
刀片形状刀具主偏角对有效切削刃长度影响很大。
C,S 型刀片有效切削刃可占切削刃长度的2/3,D 型则占1/2,V ,W 型刀片 有效切削刃只能占切削刃长度的1/4,T 型刀片能占切削刃长度的1/2。
圆形刀片R 有效切削刃的弧度占其直径的0、4倍。
有效切削刃长度必须大于切削深度,否则要换大尺寸刀片或减少切深。
(八) 刀片其它参数:刀片型号表示如下:与车刀型号对照瞧出:刀片形状,刀片法后角,切削刃尺寸等参数在选择车刀时即已确定。
而刀片厚度随切削刃尺寸确定。
只需选择其余参数。
1、刀片精度:其等级即尺寸公差等级,国标有A—U,12个等级,车削常用为G,M,U三级。
一般精密加工选用高精度的G级,非金属材料的精加工,半精加工也宜选G级刀片。
淬硬钢(HRC ≥45)的精加工也可选G级。
而一般金属精加工,半精加工皆用M级,粗加工甚至可选U级刀片。
车刀样本中一般加工几乎都就是M级,陶瓷立方氮化硼刀片则多用G级。
大多数情况下刀片精度等级随着刀片形状,尺寸,材料,用途的选定也就确定了。
2、刀片类型:指的就是有无断屑槽及中心孔。
在刀体选定后,可适用的刀片就已确定为一种或几种类型。
通常更倾向选择A,G,N等正反面都有刀刃的类型以利提高刀片的利用率。
3、刀尖半径:刀尖圆弧半径不仅影响切削效率,而且关系到被加工件表面粗糙度及精度。
从刀尖圆弧半径与最大进给量关系来瞧,最大进给量不应超过刀尖圆弧半径的80%,否则将恶化切削条件,甚至出现螺纹状与打刀问题。
因此选择刀尖圆弧半径至少要等于最大进给量的1、25倍,一般应为2倍。
刀尖角小时允许进给量还应下降。
刀尖圆弧半径增加,固然使工件表面光洁、刀刃强度提高、刀具磨损减小。
但使切削力增加、易于振动、切屑处理情况恶化。
为保证断屑、切削余量与进给量有一个最小值,当刀尖圆弧半径减小,所得到的这两个最小值也相应减小。