YPD400镦锻机液压系统的设计
机械毕业设计313YZY400静压桩机压桩机构设计
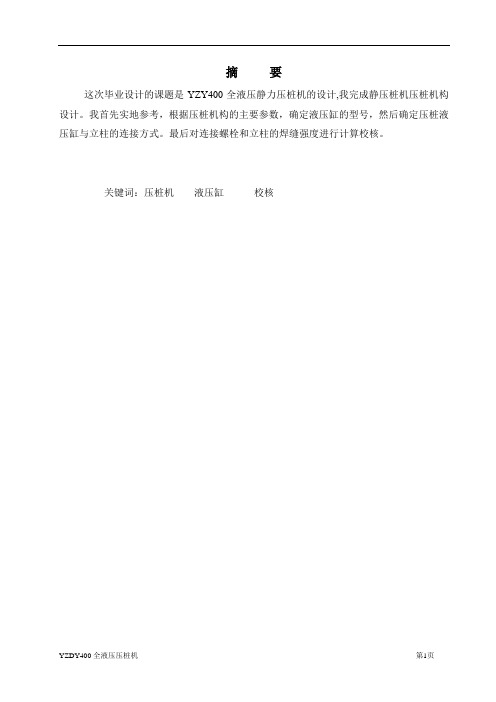
摘要这次毕业设计的课题是YZY400全液压静力压桩机的设计,我完成静压桩机压桩机构设计。
我首先实地参考,根据压桩机构的主要参数,确定液压缸的型号,然后确定压桩液压缸与立柱的连接方式。
最后对连接螺栓和立柱的焊缝强度进行计算校核。
关键词:压桩机液压缸校核AbstractThe task of graduate design will design a pile driver of statics YZY400 include hydraulic pressure. I will finish landscape orientation and circumgyrate framework of this pile driver . First of all , I reference tower crane and base tread framework’s parameter , then make sure model number of fluid cylinder , secondly , I make sure all dimension of tread part and chose parts , lastly , I finish to cheak all dimension and intensity.Keywords : pile driver fluid cylinder check1.绪论压桩机移动平稳、转场方便、施工效率高,因此,压桩机已经占绝对主导地位。
本文所述液压静力压桩机主要是指抱压式液压静力压桩机。
20世纪90年代末期以来,旧城改造在土木工程施工过程中,首先要进行的是基础施工。
桩基础是建筑施工特别是高层建筑施工中最为常见的基础形式。
桩的种类及其施工方法因上部建筑物或载荷情况不同而多种多样。
其中,将预制桩完全依靠静载平稳、安静地压入软弱地基,是一种新型的桩基础施工方法--静压桩工法。
钻镗专用机床液压系统设计

钻镗专用机床液压系统设计本文主要介绍了钻镗专用机床液压系统的设计。
液压系统作为一种重要的传动系统,具有传递动力大、易实现无级调速、运行平稳等特点,在机床制造业中得到了广泛应用。
本文设计了一种钻镗专用机床液压系统,旨在提高钻镗加工的效率和精度,并降低操作难度和能耗。
一、设计需求在进行液压系统设计之前,首先需要明确钻镗专用机床的主要工艺流程和性能参数。
钻镗专用机床主要用于对工件进行高精度孔的加工,主要包括钻孔、扩孔、铰孔和镗孔等工艺。
考虑到这些工艺对液压系统的要求,本次设计主要需要满足以下需求:1.提供稳定的主轴运动,以确保钻孔、铰孔和镗孔的精度;2.能够实现快速进给和精确微调,以提高加工效率;3.具备有效的冷却和润滑系统,以降低刀具磨损和设备故障率;4.操作简单,安全可靠,降低操作难度;5.节能环保,减少能耗。
二、设计方案根据上述需求,我们设计了一种钻镗专用机床液压系统,主要包括以下组成部分:1.液压泵:提供液压油的动力来源,可根据实际需求选择定量液压泵或变量液压泵。
2.液压缸:执行元件,用于推动主轴箱进行孔加工。
根据加工需求,可选择单活塞杆液压缸或双活塞杆液压缸。
3.控制阀:控制液压油的流向和流速,从而实现不同的动作和调节精度。
本次设计选用方向阀和压力阀。
4.冷却润滑系统:通过将液压油与冷却润滑剂混合,有效降低油温和提高润滑效果,包括冷却器和润滑剂搅拌器等。
5.液压油箱:储存液压油,并去除其中的杂质和气体。
同时,液压油箱还具有调节油温和油位等功能。
6.液压管路和连接件:用于连接液压系统中各个元件,保证液压油的传输和密封效果。
三、具体设计1.动力源选择:考虑到钻镗专用机床的性能参数和实际需求,我们选用变量式液压泵作为动力源。
这种泵具有良好的节能性和负载适应性能。
2.执行元件设计:液压缸作为执行元件,需要具备一定的推力和速度调节能力。
我们选用双活塞杆液压缸,以实现更稳定的动力输出。
3.控制阀选用:在本次设计中,我们选用方向阀和压力阀进行控制。
400kN单柱液压锻压机总体设计开题报告

随着现代化工业的发展,人们对锻件的尺寸精度和生产效率提出了越来越高的要 求,因而对锻造液压机的锻造速度和压下精度的要求也随之提高。为了适应这种需求, 锻造液压机得到了较大的发展和进步。目前国内外新发展的锻造液压机多数以液压油为 介质,采用泵直接驱动,计算机控制,同时与操作机进行联动控制。
2
锻压机床是工业基础装备的重要组成部分之一,在航空航天、汽车制造、交通运输、 冶金化工等等重要工业部门得到广泛应用。
迄今为止,我国锻压机床经半个多世纪的发展,通过国家经济建设“七五”、“八 五”、“九五”、“十五”规划的实施,已经从只能生产单机发展到能够生产装备机械 化、半自动化和自动化锻压生产线,大重型锻压机和具有各种特殊功能的先进特种锻压 机床。
5 进度计划
2011 年 12 月---- 2012 年 1 月:收集资料,确定设计系及阅读技术文献,书写开题报告。 2012 年 1 月---- 2012 年 2 月:开始总体设计,完成机械部分,传动部分设计。
完成总装配图,A0 图纸 1 张,完成部分零件图 A1 图纸 3 张等。 2012 年 2 月---- 2012 年 3 月:完成电气控制部分设计,完成电气控制系统图, A1 图纸 1 张,撰写说明书。 2012 年 3 月---- 2012 年 4 月:中期答辩 2012 年 4 月---- 2012 年 5 月:编写毕业论文。 2012 年 5 月---- 2012 年 6 月:毕业答辩准备和答辩。
20 世纪 60 年代以后,锻压机械改变了从 19 世纪开始的向重型和大型方向发展的 趋势,转而向高速、高效、自动、精密、专用、多品种生产等方向发展。于是出现了每 分种行程 2000 次的高速压力机、60000 千牛的三坐标多工位压力机,25000 千牛的精 密冲裁压力机,能冷镦直径为 48 毫米钢材的多工位自动冷镦机和多种自动机、自动生 产线等。各种机械控制的、数字控制的和计算机控制的自动锻压机械以及与之配套的操 作机、机械手和工业机器人也相继研制成功。现代化的锻压机械可生产精确制品,有良 好的劳动条件,环境污染很小。
400液压系统的工作流程
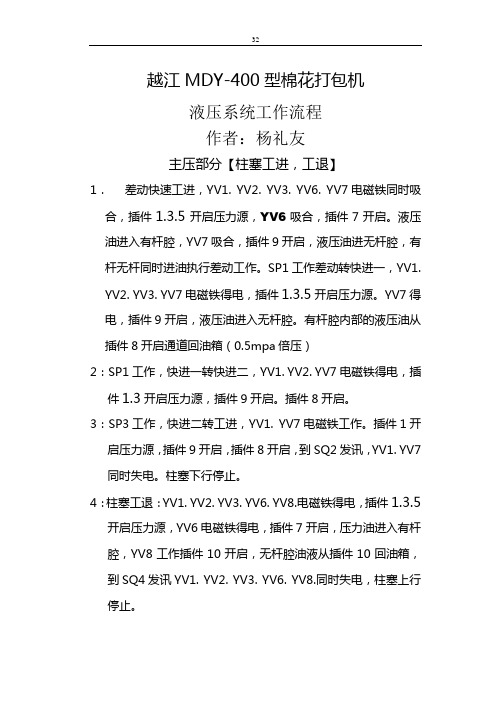
越江MDY-400型棉花打包机液压系统工作流程作者:杨礼友主压部分【柱塞工进,工退】1.差动快速工进,YV1. YV2. YV3. YV6. YV7电磁铁同时吸合,插件1.3.5开启压力源,YV6吸合,插件7开启。
液压油进入有杆腔,YV7吸合,插件9开启,液压油进无杆腔,有杆无杆同时进油执行差动工作。
SP1工作差动转快进一,YV1.YV2. YV3. YV7电磁铁得电,插件1.3.5开启压力源。
YV7得电,插件9开启,液压油进入无杆腔。
有杆腔内部的液压油从插件8开启通道回油箱(0.5mpa倍压)2:SP1工作,快进一转快进二,YV1. YV2. YV7电磁铁得电,插件1.3开启压力源,插件9开启。
插件8开启。
3:SP3工作,快进二转工进,YV1. YV7电磁铁工作。
插件1开启压力源,插件9开启,插件8开启,到SQ2发讯,YV1. YV7同时失电。
柱塞下行停止。
4:柱塞工退:YV1. YV2. YV3. YV6. YV8.电磁铁得电,插件1.3.5开启压力源,YV6电磁铁得电,插件7开启,压力油进入有杆腔,YV8工作插件10开启,无杆腔油液从插件10回油箱,到SQ4发讯YV1. YV2. YV3. YV6. YV8.同时失电,柱塞上行停止。
5:脱箱上行:YV1. YV2. YV4电磁铁得电,插件1.3开启压力源,YV4得电,插件11开启,压力油进入脱箱无杆腔,到SQ5发讯时YV1. YV2. YV4失电。
脱箱上行到位停止。
6:脱箱下行:YV5得电插件12开启,脱箱油缸无杆腔液压油从插件12通道回油箱。
预压部分1.预压差动快进。
YV9. YV11. YV12. YV13电磁铁得电,插件13,14开启压力源,YV10得电,插件16关闭,YV16得电压力油进入有杆腔。
YV13电磁铁得电, 插件19开启,压力油进入无杆腔,无杆有杆同时进油协调执行差动。
2.SQ9发讯后. YV9. YV11. YV13. YV15 (YV12失电YV15得电)YV9. YV11得电,插件13.14开启压力源,YV13得电,插件19开启,压力油进入无杆腔。
锻造操作机液压系统设计与仿真分析

锻造操作机液压系统设计与仿真分析摘要:锻造操作机是核电、火电、轨道交通等重大装备制造的关键设备。
锻造操作机液压控制系统包括夹持系统、提升俯仰系统、水平移动系统、缓冲系统、大车行走系统和夹钳旋转系统。
采用平均流量法对液压泵站进行节能设计。
在数学模型的基础上对液压系统的关键控制性能(快速性、准确性、起动性)和可靠性进行仿真分析研究。
结果表明,通过对液压系统回路的合理设计,改善了液压系统的控制性能,提高了液压系统的可靠性,可为大流量液压系统的设计提供理论指导,实现锻造操作机的快速、精确、稳定、智能控制。
关键词:锻造操作机;液压系统;设计;仿真0引言目前,我国的大型操作机主要依赖进口,不仅价格昂贵、供货周期长,而且也使我国大型锻件的制造加工技术受制于人。
因此,自主研发大型锻造操作机对我国重大装备制造业的发展有重要意义。
锻造操作机的灵巧性和快速性是保证锻件质量的重要指标,而大型操作机的大负载、大惯量和冲击载荷对传动系统的设计带来了很大的困难,通常需要采用机电液混合驱动的方式来实现快速和准确控制,因此,液压系统是大型操作机设计的关键之一。
1操作机液压系统设计1.1操作机液压系统功能分析锻造操作机主要由大车、夹钳和台架三部分组成,为满足开坯、拔长、镦粗和整圆等锻造工艺要求,操作机需要具备行走、夹钳开闭、旋转、提升、平移和缓冲等多种功能。
对于大型操作机,上述功能主要由液压驱动方式来实现。
行走功能:由液压系统驱动大车前进和后退,实现锻件的水平移动。
通过液压马达来实现大车的运动和定位,同时控制大车起停带来的冲击。
夹持功能:由液压系统驱动夹钳实现锻件的夹持和旋转。
通过夹钳液压缸实现锻件的夹持,通过液压马达驱动夹钳旋转,并实现准确定位。
悬架功能:由液压系统驱动悬架液压缸实现夹钳和锻件的垂直移动和俯仰。
同时设置液压缓冲机构,以缓解锻压对夹钳的冲击。
1.2操作机液压控制系统的设计操作机在机构构型上通常采用解耦设计,将操作机主要功能分解成夹持、提升俯仰、水平移动、锻造缓冲、大车行走、夹钳旋转等6个相对独立的运动,这使得液压系统的设计也具有独立性。
YPD400镦锻机液压系统的设计
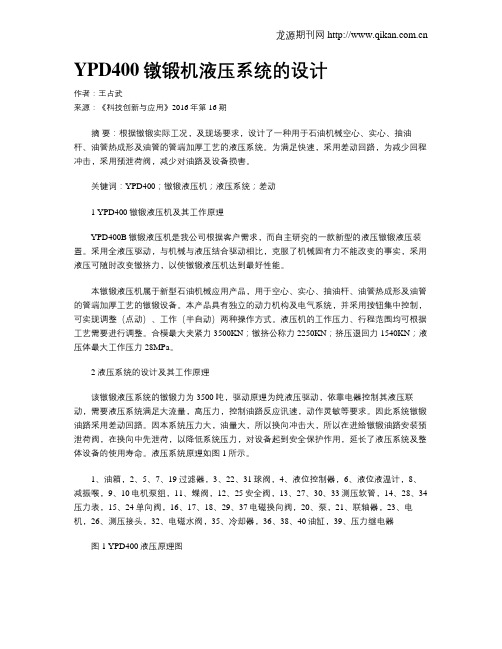
YPD400镦锻机液压系统的设计作者:王占武来源:《科技创新与应用》2016年第16期摘要:根据镦锻实际工况,及现场要求,设计了一种用于石油机械空心、实心、抽油杆、油管热成形及油管的管端加厚工艺的液压系统。
为满足快速,采用差动回路,为减少回程冲击,采用预泄荷阀,减少对油路及设备损害。
关键词:YPD400;镦锻液压机;液压系统;差动1 YPD400镦锻液压机及其工作原理YPD400B镦锻液压机是我公司根据客户需求,而自主研究的一款新型的液压镦锻液压装置。
采用全液压驱动,与机械与液压结合驱动相比,克服了机械固有力不能改变的事实,采用液压可随时改变镦挤力,以使镦锻液压机达到最好性能。
本镦锻液压机属于新型石油机械应用产品,用于空心、实心、抽油杆、油管热成形及油管的管端加厚工艺的镦锻设备。
本产品具有独立的动力机构及电气系统,并采用按钮集中控制,可实现调整(点动)、工作(半自动)两种操作方式。
液压机的工作压力、行程范围均可根据工艺需要进行调整。
合模最大夹紧力3500KN;镦挤公称力2250KN;挤压退回力1540KN;液压体最大工作压力28MPa。
2 液压系统的设计及其工作原理该镦锻液压系统的镦锻力为3500吨,驱动原理为纯液压驱动,依靠电器控制其液压联动,需要液压系统满足大流量,高压力,控制油路反应讯速,动作灵敏等要求。
因此系统镦锻油路采用差动回路。
因本系统压力大,油量大,所以换向冲击大,所以在进给镦锻油路安装预泄荷阀,在换向中先泄荷,以降低系统压力,对设备起到安全保护作用,延长了液压系统及整体设备的使用寿命。
液压系统原理如图1所示。
1、油箱,2、5、7、19过滤器,3、22、31球阀,4、液位控制器,6、液位液温计,8、减振喉,9、10电机泵组,11、蝶阀,12、25安全阀,13、27、30、33测压软管,14、28、34压力表,15、24单向阀,16、17、18、29、37电磁换向阀,20、泵,21、联轴器,23、电机,26、测压接头,32、电磁水阀,35、冷却器,36、38、40油缸,39、压力继电器图1 YPD400液压原理图本液压系统一拖二配控制,可同时满足两套镦锻机液压要求,整个液压系统由辅助油路,夹紧油路,镦锻油路,泵站高压供油油路,泵站低压辅助供油油路,冷却油路组成。
YZY400全液压静力压桩机的液压系统设计

毕业设计论文题目YZY400全液压静力压桩机的液压系统设计目录:摘要. . . . . . . . . . . . . . . . . . . . . . . . . . . . . . . . . . . . . . . . . . . . . . . . . . . . . . . . . . . . . . . . .5 总论. . . . . . . . . . . .. . . . . . . . . . . . . . . . . . . . . . . . . . . . . . . . . . . . . . . . . . . . . . . . . . . . .71 液压缸的参数值. . . . . . . . . . . . . . . . . . . . . . . . . . . . . . . . . . . . . . . . . .. . .92 液压泵的选用.. . . . . . . . . . . . . . . . . . . . . . . . . . . . . . . . . . . . . . . . . . . . . .93 电动机的选用. . . . . . . . . . . . . . . . . . . . . . . . . . . . . . . . . . . . . . . . . . . . . . .103.1 电动机Ⅰ的选用. . . . . . . . . . . . . . . . . . . . . . . . . . . . . . . . . . . . . . .103.2 电动机П的选用. . . . . . . . . . . . . . . . . . . . . . . . . . . . . . . . . . . . . . . 104 液压阀的选择. . . . . . . . . . . . . . . . . . . . . . . . . . . . . . . . . . . . . . . . . . . .104.1方向控制阀的选择. . . . . . . . . . . . . . . . . . . . . . . . . . . . . . . . . . . . . 114.1.1单向控制阀的选择. . . . . . . . . . . . . . . . . . . . . . . . . . . . . . . . 114.1.2 换向阀的选择. . . . . . . . . . . . . . . . . . . . . . . . . . . . . . . . . . . .124.2压力阀的选择. . . . . . . . . . . . . . . . . . . . . . . . . . . . . . . . . . . . . . . . 134.3流量控制阀的选择. . . . . . . . . . . . . . . . . . . . . . . . . . . . . . . . . . . .. .144.4压力表开关的选择. . . . . . . . . . . . . . . . . . . . . . . . . . . . . . . . . . . . . 154.5压力表的选择. . . . . . . . . . . . . . . . . . . . . . . . . . . . . . . . . . . . . . . . . 155 液压油的选择. . . . . . . . . . . . . . . . . . . . . . . . . . . . . . . . . . . . . . . . . . . . . . .156 联轴器的选择. . . . . . . . . . . . . . . . . . . . . . . . . . . . . . . . . . . . . . . . . . . . . . .167 油箱的设计. . . . . . . . . . . . . . . . . . . . . . . . . . . . . . . . . . . . . . . . . . . . . . . . .177.1确定油箱的有效容积大致外形尺寸. . . . . . . . . . . . . . . . . . . . . . . . 177.2滤油器的选择. . . . . . . . . . . . . . . . . . . . . . . . . . . . . . . . . . . . . . . . . 187.2.1 吸油滤油器(粗滤器)的选择. . . . . . . . . . . . . . . . . . . . . . . . 187.2.2 回油滤油器(精滤器)的选择. . . . . . . . . . . . . . . . . . . . . .197.3空气滤清器的选择. . . . . . . . . . . . . . . . . . . . . . . . . . . . . . . . . . . . . 197.4液位计的选择. . . . . . . . . . . . . . . . . . . . . . . . . . . . . . . . . . . . . . . . . 207.5油箱各板尺寸及附件安装位置的确定. . . . . . . . . . . . . . . . . . . . . 207.5.1油箱的总体设计. . . . . . . . . . . . . . . . . . . . . . . . . . . . . . . . . . 207.5.2初定各板面的厚度. . . . . . . . . . . . . . . . . . . . . . . . . . . . . . . 207.5.3隔板的设计. . . . . . . . . . . . . . . . . . . . . . . . . . . . . . . . . . . . . . 207.5.4各面板的安装尺寸. . . . . . . . . . . . . . . . . . . . . . . . . . . . . . . . . 217.5.4.1上面板中各安装尺寸的确定. . . . . . . . . . . . . . . . . . . . 217.5.4.2起吊螺钉的选用及校核. . . . . . . . . . . . . . . . . . . . . . . . 217.5.4.3盖板上各器件的定位. . . . . . . . . . . . . . . . . . . . . . . . . 21.1螺栓的布置. . . . . . . . . . . . . . . . . . . . . . . . . . . . . . . . . . .21.2起吊螺钉布置. . . . . . . . . . . . . . . . . . . . . . . . . . . . . . . . .22.3空气滤清器的定位. . . . . . . . . . . . . . . . . . . . . . . . . . . . .22.4回油滤油器的定位. . . . . . . . . . . . . . . . . . . . . . . . . . . . .22.5吊环的选择及安装. . . . . . . . . . . . . . . . . . . . . . . . . . . . .227.5.4.4左面板上液位计的定位. . . . . . . . . . . . . . . . . . . . . . . . . 247.5.4.5右面板上放油口的定位. . . . . . . . . . . . . . . . . . . . . . . . 247.5.4.6隔板上吸油滤油器的定位. . . . . . . . . . . . . . . . . . . . . . . 247.5.4.7底脚的设计. . . . . . . . . . . . . . . . . . . . . . . . . . . . . . . . . . 257.5.4.8油箱厚及焊接宽度的校核. . . . . . . . . . . . . . . . . . . . . . . 268 油管的设计计算. . . . . . . . . . . . . . . . . . . . . . . . . . . . . . . . . . . . . . . . . 288.1钢管管径的选择与设计. . . . . . . . . . . . . . . . . . . . . . . . .. . . . . . 288.1.1液压泵的吸油管. . . . . . . . . . . . . . . . . . . . . . . . .. . . . . . . 28.1泵Ⅰ的吸油管. . . . . . . . . . . . . . . . . . . . . . . .. . . . . . .28.2 泵Ⅱ的吸油管. . . . . . . . . . . . . . . . . . . . . . . . .. . . . 298.1.2 液压泵的排油管. . . . . . . . . . . . . . . . . . . . . . . . .. . . . . . .29.1 泵Ⅰ的排油管. . . . . . . . . . . . . . . . . . . . . . . .. . . . . . . 29.2 泵Ⅱ的排油管. . . . . . . . . . . . . . . . . . . . . . . . .. . . . . . . 298.1.3 液压系统油路. . . . . . . . . . . . . . . . . . . . . . . . .. . . . . . .30.1单只压桩油缸进油油路. . . . . . . . . . . . . . . . . . . . . . . . .. . .30.2 压桩系统总油路. . . . . . . . . . . . . . . . . . . . . . . . .. . . . . . . 30.3 泵Ⅰ对压桩油缸进油油路. . . . . . . . . . . . . . . . . . . . . . . . .30.4 泵Ⅱ对压桩油缸进油油路. . . . . . . . . . . . . . . . . . . . . .308.1.4 夹桩系统油路. . . . . . . . . . . . . . . . . . . . . . . . . .. . . . . . . . . .31.1 单只夹桩油缸进油油路. . . . . . . . . . . . . . . . . . . . . .. . . . . 31 .2夹桩系统进油油路. . . . . . . . . . . . . . . . . . . . . . . . . . . . . . . . . . . .318.1.5 行走系统(纵移和横移). . . . . . . . . . . . . . .. . . . . . . . . . . . . . . .318.1.6 顶升系统油路. . . . . . . . . . . . . . . . . . . . . . . . . . . . . . . . . . . . . . . . 328.1.7 回油系统油路. . . . . . . . . . . . . . . . . . . . . . . . . . . . . . . . . . . . . . . . 32.1 泵Ⅰ的回油油路. . . . . . . . . . . . . . . . . . . . . . . . . . . . . . . . . . . . . .32.2 泵Ⅱ的回油油路. . . . . . . . . . . . . . . . . . . . . . . . . . . . . . . . . . . . . .32.3 系统的总回油油路. . . . . . . . . . . . . . . . . . . . . . . . . . . . . . . . . . . . 338.2胶管的选择. . . . . . . . . . . . . . . . . . . . . . . . . . . . . . . . . . . . . . . . . . . . . . . . .348.3接头体的设计. . . . . . . . . . . . . . . . . . . . . . . . . . . . . . . . . . . . . . . . . . . . . . .349.总结与展望. . . . . . . . . . . . . . . . . . . . . . . . . . . . . . . . . . . . . . . . . . . . . . . . . . . .36 致谢. . . . . . . . . . . . . . . . . . . . . . . . . . . . . . . . . . . . . . . . . . . . . . . . . . . . . . . 37 参考书目. . . . . . . . . . . . . . . . . . . . . . . . . . . . . . . . . . . . . . . . . . . . . . . . . . . 38摘要这次毕业设计的课题是YZY400全液压静力压桩机的设计,我们是团队毕业设计,我完成静压桩机的液压系统。
400kJ全液压模锻锤的液压系统设计

De s i g n o f Hy d r a u hc S y s t e m f o r t he W h o l e Hy d r a u l i c Di e F o r g i ng Ma c h i n e
C A O Q i n g 1 , L E I B u - f a n g ' , L I Y o n g - t a n g a , H E Z h o n g - k u i
m o l d ,s e c u i r t y p r o t e c t i o n a n d C o o l i n g nd a i f l t e i r n l f o w or f h i t t i n g ,1 4 A x i l a P i s t o n P u m p s a r e j o i n t e d or f o i l i n g .
( 1 . T a i y u a n Un i v e r s i t y o f S c i e n c e a n d T e c h n o l o g y, T a i y u a n 0 3 0 0 2 4, Ch i n a ;
2 . Y u t o n g B u s C o . , L t d . , Z h e n g z h o u 4 5 0 0 6 1 , C h i n a )
4 0 0 k J全液压模锻锤 的液压 系统设计
曹 清 , 雷 步 芳 , 李 永 堂 , 何 忠奎
( 1 . 太原 科技 大 学 , 山西 太原
摘
0 3 0 0 2 4; 2宇 通客 车 , 河南 郑州
4 5 0 0 6 1 )
要: 根 据 全 液 压 模 锻 锤 结 构 形 式 及 其 工 况 的 要求 , 设 计 了一 种 用 于 4 0 0 k J全 液 压 模 锻 锤 的 液 压 系 统 。 其 主 功 能 主 要 包 括 泵 站 供 油
液压传动课程设计--设计一台立式镗孔组合机床液压系统

液压传动课程设计--设计一台立式镗孔组合机床液压系统液压系统设计思路:1. 确定液压系统的工作压力和流量要求。
根据立式镗孔组合机床的加工特点和工作要求,确定系统的最大工作压力和流量。
2. 选取液压元件。
根据系统的工作压力和流量要求,选取液压泵、液压马达、液压阀等液压元件。
液压泵的类型可以选择齿轮泵、叶片泵或活塞泵等。
液压马达的类型可以选择齿轮马达或液压马达等。
液压阀的选择要根据系统的控制要求,如选择压力阀、流量阀、方向阀等。
3. 确定液压系统的布局。
根据立式镗孔组合机床的结构和工作要求,确定液压泵、液压马达、液压阀等液压元件的布置位置和互连关系。
4. 设计液压系统的工作流程。
根据立式镗孔组合机床的工作流程和工艺要求,确定液压系统的工作流程。
包括液压元件的工作顺序、开关时间及液压系统的控制方式等。
5. 进行液压系统的参数计算和选型。
根据液压系统的工作压力和流量要求,以及液压元件的选型,进行各液压元件的参数计算和选型。
6. 进行液压系统的零件选配和设计。
根据液压系统的工作压力和流量要求,选配和设计液压系统所需的零件,如管路、接头、密封件等。
7. 进行液压系统的动态分析和优化设计。
通过使用液压系统的动态模拟软件,对液压系统进行动态分析和优化设计,以提高系统的稳定性和性能。
8. 进行液压系统的总体集成和装配调试。
根据液压系统的设计要求,进行液压系统的总体集成和装配调试,以确保液压系统的正常运行。
9. 进行液压系统的系统调试和性能测试。
对液压系统进行系统调试和性能测试,以检查液压系统的正常运行和满足工艺要求。
10. 进行液压系统的运行监测和维护保养。
对液压系统进行运行监测和维护保养,定期检查液压系统的工作状态和性能,及时处理可能出现的故障和异常情况。
400kN单柱液压锻压机总体设计
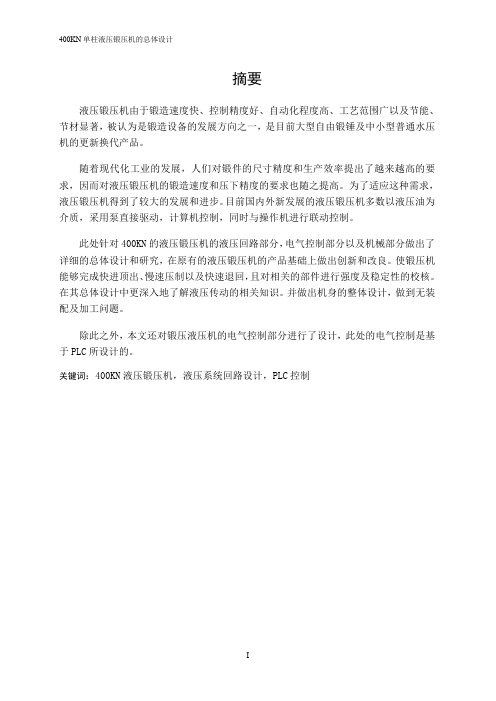
4 液压机电气控制系统设计 ....................................... 30 4.1 基于 PLC 的电气控制 .............................................................................................................30 4.2 三相异步电动机 ......................................................................................................................33 4.3 配电箱 ........................................................................................................................................33
400KN 单柱液压锻压机的总体设计
液压机的液压系统设计

液压机的液压系统设计
液压机的液压系统最基本的组成部分就是液压源,加工设备和液压执行元件。
一般常见的液压系统主要包括油泵、控制阀、液压缸、油箱和管路等各个部分。
常规液压系统的设计流程一般分为如下几个步骤:
1. 确定加工设备的工作需求:设计师需要了解液压机工作载荷、速度、精度以及循环时间等各方面的工作要求。
2. 根据工作要求配置液压源:一般情况下,液压源包括液压泵、油箱、冷却器和滤芯等部件,根据用户需要,液压机可以使用不同的液压泵,如齿轮泵、柱塞泵和推进式泵等。
3. 选定控制阀:液压控制阀是确定液压动作的关键部件。
设计师需要选择合适的控制阀类型和规格以及确定液压回路的组合。
4. 设计液压缸:设计师应该根据工作载荷和速度的要求,选定合适的液压缸型号和规格。
5. 设计管路系统:液压管路的设计包括液压管材料、管路尺寸选择、并联和分流等元素的确定。
6. 确定液压系统的相关参数:设计师需要根据实际情况,确定油液压力、设备的各个动作速度以及循环时间等参数。
液压机的液压系统设计需要根据工作场景和工作要求进行综合
考虑,充分了解设备的性能参数和工作条件,才能发挥设备的最佳工作状态。
锻造操作机液压系统设计与仿真

锻造操作机液压系统设计与仿真锻造操作机是锻造行业中的重要设备,其液压系统是实现设备动作和控制的关键部分。
本文将介绍锻造操作机液压系统的设计及其仿真分析,以期提高设备的性能和可靠性。
锻造操作机主要用于金属材料的锻造加工,其液压系统具有以下特点:动作精度高,能够实现精确的位移、速度和力控制。
需要承受高温、高压和高冲击负荷,因此要求液压元件具有高性能和长寿命。
系统中涉及多种液压元件和辅助元件的协调工作,因此需要精心设计液压回路和控制策略。
系统原理锻造操作机液压系统主要由液压泵、液压缸、液压阀、管道和辅助元件等组成。
根据设备工艺需求,设计液压系统原理图,确定液压缸数量、连接方式以及液压回路。
元件选型选择高品质的液压元件,如液压泵、液压缸、液压阀等,是保证液压系统性能的关键。
元件的选型还应考虑如下因素:布置方案根据设备结构和空间布局,设计液压系统的布置方案。
在保证系统性能的同时,应考虑如下因素:利用仿真软件对设计的液压系统进行仿真分析,可以评估系统的性能和可靠性。
通过仿真,可以得出如下在不同工况下,液压系统中的压力、流量和功耗等参数变化较小,系统性能稳定。
液压元件的选择和设计能够满足锻造操作机的工艺要求。
在一定范围内,液压系统的响应速度较快,能够适应快速动作的需求。
根据仿真结果,可以进一步优化液压系统设计,如调整液压回路参数、优化元件布置等。
仿真还可以指导设备的调试和优化,提高设备的可靠性和稳定性。
本文介绍了锻造操作机液压系统的设计与仿真分析。
通过合理设计液压系统原理、选择高品质的液压元件以及制定有效的布置方案,能够提高锻造操作机的性能和可靠性。
利用仿真软件对设计的液压系统进行仿真分析,可以评估系统的性能和可靠性,为系统的优化提供指导。
本文的研究成果对锻造操作机液压系统的设计和应用具有一定的参考价值。
随着科技的不断发展,锻造操作机液压系统的设计将面临更多新的挑战。
未来研究方向可以包括:研究新型的液压元件和控制系统,以满足锻造操作机不断提高的性能需求。
毕业设计---镗床液压系统设计

摘要面对我国经济近年来的快速发展,机械制造工业的壮大,在国民经济中占重要地位的制重造业领域得以健康快速的发展。
制造装备的改进,使得作为制造工业重要设备的各类机加工艺装备也有了许多新的变化,尤其是孔加工,其在今天的液压系统的地位越来越重要。
镗床液压系统的设计,除了满足主机在动作和性能方面规定的要求外,还必须符合体积小、量轻、成本低、效率高、结构简单、工作可靠、使用和维修方便等一些公认的普遍设计原则。
液压系统的设计主要是根据已知的条件,来确定液压工作方案、液压流量、压力和液压泵及其它元件的设计。
综上所述,完成整个设计过程需要进行一系列艰巨的工作。
设计者首先应树立正确的设计思想,努力掌握先进的科学技术知识和科学的辩证的思想方法。
同时,还要坚持理论联系实际,并在实践中不断总结和积累设计经验,向有关领域的科技工作者和从事生产实践的工作者学习,不断发展和创新,才能较好地完成机械设计任务。
关键词:液压缸;液压泵;换向阀AbstractFaced with China's rapid economic development in recent years, mechanical manufacturing industry growth, play a significant role in the national economy was healthy and rapid development of the field of heavy industry. Improvement of the manufacturing equipment, making various types of machining process as an important equipment manufacturing industry equipment has many new changes, especially the hole, it is becoming more and more important in today's hydraulic system.Hydraulic system design of boring machine, in addition to meeting the host provided for in action and performance requirements, must also comply with the small volume, light weight, low cost, high efficiency, simple structure, reliable working, convenient operation and maintenance, and other generally recognized principles of universal design. Design of the hydraulic system is based mainly on a known condition, programme of work to determine the hydraulic, hydraulic pumps and hydraulic flow, pressure, and other elements of design.To sum up, a series of hard work through the design process needed. Designers should first establish a correct design, efforts to acquire advanced knowledge of science and technology and science of dialectical thinking method. At the same time, we must persist in integrating theory with practice, and constantly sum up and design experience accumulated in the practice, to the fields of science and technology workers and workers engaged in the production, continuous development and innovation in order to better complete mechanical design tasks. Keywords: hydraulic cylinder, and hydraulic pump valve目录摘要 (6)Abstract ............................................................................................ 错误!未定义书签。
锻造操作机液压控制系统设计

锻造操作机液压控制系统设计1. 绪论a. 选题背景和意义b. 国内外研究现状c. 研究内容和研究方法2. 锻造操作机液压控制系统设计的原理和技术分析a. 锻造操作机的工艺流程b. 液压系统的原理和组成c. 液压控制系统设计的技术分析3. 液压控制系统的设计过程a. 液压控制系统的总体设计b. 液压系统液压源和传动元件的设计c. 液压系统控制阀的选型与组合d. 电气控制系统的设计4. 液压控制系统的测试与验证a. 液压系统的主要性能指标测试b. 液压控制系统的性能测试c. 液压控制系统的故障诊断与排除5. 结论与展望a. 取得的成果和创新点b. 工作的不足和改进方向c. 未来的研究方向和展望第1章:绪论1.1 选题背景和意义随着现代工业生产的不断发展,液压控制技术已成为工业自动化和机械传动领域中不可或缺的重要技术。
锻造操作机作为机械加工领域中的重要设备之一,它的使用范围日益广泛。
由于锻造作业需要快速、高效、准确地完成,因此对于液压控制系统的要求也越来越高。
针对这种需求,本文设计一套自动化液压控制系统,以提高锻造机械加工的效率和质量。
1.2 国内外研究现状目前,国内外研究和应用液压控制技术的范围已非常广泛。
针对液压控制技术在机械加工领域的应用研究,国内外专家学者进行了大量研究,提出了一系列液压控制系统的理论和技术,应用于实际生产中。
如国外学者 Johanan Kurtzberg 和 Nir Arazi,提出了一种新型的液压系统,可以用于锻造操作机中。
该系统采用了高压电缆代替传统的皮带或链条传动,具有可靠性高、噪音小、维护方便等优点。
国内用于锻压设备控制的液压系统,主要采用伺服液压控制技术。
伺服液压控制技术是传统液压控制技术的一个重要分支,其主要特点是能实现高精度控制和动态响应。
1.3 研究内容和研究方法本文旨在研究一套适用于锻造操作机的液压控制系统,主要包括以下内容:(1)对锻造操作机的工艺流程进行研究,为液压控制系统的设计提供理论基础。
液压系统的设计步骤和内容

液压系统的设计步骤和内容(总1页) -本页仅作为预览文档封面,使用时请删除本页-液压系统的设计步骤和内容液压系统的设计是整个机器设计的一部分,它的任务是根据机器的用途、特点和要求,利用液压传动的基本原理,拟定出合理的液压系统图,再经过必要的计算来确定液压系统的参数,然后按照这些参数来选用液压元件的规格和进行系统的结构设计。
液压系统的设计步骤大体如下:1、液压系统的工况分析在开始设计液压系统时,首先要对机器的工作情况进行详细的分析,一般要考虑下面几个问题。
1)确定该机器由哪些运动需要液压传动来完成。
2)确定各运动的工作顺序和各执行元件的工作循环。
3)确定液压系统的主要工作性能。
例如:执行元件的运动速度、调速范围、最大行程以及对运动平稳性要求等。
4)确定各执行元件所承受的负载及其变化范围。
2、拟定液压系统原理图拟定液压系统原理图一般要考虑以下几个问题。
1) 采用何种型式的执行机构。
2)确定调速方案和速度换接方法。
3)如何完成执行机构的自动循环和顺序动作。
4) 系统的调压、卸荷及执行机构的换向和安全互锁等要求。
5) 压力测量点的合理选择。
根据上述要求选择基本回路,然后将各基本回路组合成液压系统。
当液压系统中有多个执行部件时,要注意到它们相互间的联系和影响,有时要采用防干扰回路。
在液压系统原理图中,应该附有运动部件的动作循环图和电磁铁动作顺序表。
3、液压系统的计算和选择液压元件液压系统计算的目的是确定液压系统的主要参数,以便按照这些参数合理选择液压元件和设计非标准元件。
具体计算步骤如下:1)计算液压缸的主要尺寸以及所需的压力和流量。
2计算液压泵的工作压力、流量和传动功率。
3)选择液压泵和电动机的类型和规格。
4)选择阀类元件和辅助元件的类型和规格。
4、对液压系统进行验算必要时,对液压系统的压力损失和发热温升要进行验算,但是经过生产实践考验过的同类型设备可供类比参考,或有可靠的试验结果,那末也可以不再进行验算。
液压课程设计---钻镗专用机床液压系统

图2.1液压缸的负载图和速度图
2.4初定液压缸的参数
主缸:
1.初选液压缸的工作压力p1
2.机床的最大负载F=4316N,根据下表2.2可得:
表2.2按负载选择液压执行元件的工作压力
载荷/kN
<5
5~10
10~20
20~30
30~50
>50
工作压力(MPa)
0.8~1
1.5~2
2.5~3
2.3工况分析
(1)负载分析
主缸:
钻镗阻力
=4000N
工作台重量
=1000N
摩擦阻力
=G×fs=1000×0.2=200N
=G×fd=1000×0.1=100N
惯性阻力
F惯=ma= × =1000/10×7/0.2×60=58N
重力阻力
因工作部件是卧式安装,故重力阻力为零。
密封阻力
将密封阻力考虑在液压缸的机械效率中去,取液压缸机械效率
由此求得液压缸无杆腔有效工作面积A1= = =63.6cm2
液压缸有杆腔面积A1= = =32.4cm2
工进时采用调速阀调速,查设计手册,调速阀最小稳定流量为qmin=0.05L/min,工进速度V=0.5m/min,则 = =10cm2
10cm2<A2< A1,故满足速度稳定性要求。
副缸:
取副缸压强为p=0.63MPa
动摩擦系数fd
快进
工进
快进
工进
快退
进给缸
4000
1000
500
200
55
7
0.5
5
0.2
0.2
0.1
夹紧缸
1000
- 1、下载文档前请自行甄别文档内容的完整性,平台不提供额外的编辑、内容补充、找答案等附加服务。
- 2、"仅部分预览"的文档,不可在线预览部分如存在完整性等问题,可反馈申请退款(可完整预览的文档不适用该条件!)。
- 3、如文档侵犯您的权益,请联系客服反馈,我们会尽快为您处理(人工客服工作时间:9:00-18:30)。
YPD400镦锻机液压系统的设计
根据镦锻实际工况,及现场要求,设计了一种用于石油机械空心、实心、抽油杆、油管热成形及油管的管端加厚工艺的液压系统。
为满足快速,采用差动回路,为减少回程冲击,采用预泄荷阀,减少对油路及设备损害。
标签:YPD400;镦锻液压机;液压系统;差动
1 YPD400镦锻液压机及其工作原理
YPD400B镦锻液压机是我公司根据客户需求,而自主研究的一款新型的液压镦锻液压装置。
采用全液压驱动,与机械与液压结合驱动相比,克服了机械固有力不能改变的事实,采用液压可随时改变镦挤力,以使镦锻液压机达到最好性能。
本镦锻液压机属于新型石油机械应用产品,用于空心、实心、抽油杆、油管热成形及油管的管端加厚工艺的镦锻设备。
本产品具有独立的动力机构及电气系统,并采用按钮集中控制,可实现调整(点动)、工作(半自动)两种操作方式。
液压机的工作压力、行程范围均可根据工艺需要进行调整。
合模最大夹紧力3500KN;镦挤公称力2250KN;挤压退回力1540KN;液压体最大工作压力28MPa。
2 液压系统的设计及其工作原理
该镦锻液压系统的镦锻力为3500吨,驱动原理为纯液压驱动,依靠电器控制其液压联动,需要液压系统满足大流量,高压力,控制油路反应讯速,动作灵敏等要求。
因此系统镦锻油路采用差动回路。
因本系统压力大,油量大,所以换向冲击大,所以在进给镦锻油路安装预泄荷阀,在换向中先泄荷,以降低系统压力,对设备起到安全保护作用,延长了液压系统及整体设备的使用寿命。
液压系统原理如图1所示。
1、油箱,
2、5、7、19过滤器,
3、22、31球阀,
4、液位控制器,6、液位液温计,8、减振喉,9、10电机泵组,11、蝶阀,12、25安全阀,13、27、30、33测压软管,14、28、34压力表,1
5、24单向阀,1
6、1
7、1
8、2
9、37电磁换向阀,20、泵,21、联轴器,23、电机,26、测压接头,32、电磁水阀,35、冷却器,36、38、40油缸,39、压力继电器
图1 YPD400液压原理图
本液压系统一拖二配控制,可同时满足两套镦锻机液压要求,整个液压系统由辅助油路,夹紧油路,镦锻油路,泵站高压供油油路,泵站低压辅助供油油路,冷却油路组成。
主油路采用大流量阀、结合油缸差动控制技术,具有控制压力稳定,大流量,
结构紧凑,反应灵敏等特点。
镦锻油路采用泄压控制,可有效减小工作过程中换向冲击,防止系统过振。
镦锻时,采动差动回路,可使镦锻缸迅速达到工作位置,缩短进给时间,有效地防止时间过长工作冷却问题,可使工作快速成形。
同时设置安全保护系统,在系统超压时,能有效报警或控制系统停机,以防发生事故。
整个系统辅助油路采用低压、流量小、控制稳定、结构紧凑反应灵敏特点。
冷却回路是对液压油油温控制和杂质过滤,确保系统正常工作。
2.1 液压系统的要求
系统只允许单阀切换,单缸动作。
2.2 液压系统的启动
分启动电机泵组20、21、23。
启动高压电机泵组电机泵组,电机10通电后,液压油从油箱1,吸油滤油器5,通过蝶阀11,减震喉8,进而从电机泵组的高压柱塞泵输出高压油,进入集成块,电磁溢流阀不得电,卸荷,泵出来的油液经电磁溢流阀直接回油箱。
控制油路均接压力口,但均未接通。
2.3 上下胎板提起分模
3T得电,电液换向阀换至右位,辅助油缸2有杆腔进油,无杆腔油液流回油箱,上胎板提起与下胎板分模。
2.4 上下胎板合模
将加热好的工件置入下模腔内,这时2T得电,换阀至左位,辅助油缸无杆腔进油,活塞杆伸出,有杆腔油液流回油箱,上胎板落下,上下模合拢。
2.5 夹紧缸锁紧
主油路高压油经单向阀15、至电液阀的7T得电,液压油进入夹紧缸1无杆腔,推动叉座上斜块插入加压并锁紧。
有杆腔油液经冷却器32、回油滤油器12流回油箱。
2.6 镦锻油缸快进
主油路高压油至换向阀17,此时电磁阀14T得电,油液到换向阀18,这时镦挤缸1为差动连接,有杆腔流出的油液同时进入无杆腔,镦锻油缸活塞杆快速伸出,冲杆快速接近工件,实现快进。
2.7 镦锻油缸加压
当冲杆接触工件后,油缸压力开始升高,升至设定值时,电液换向阀18的10T得电,电磁换向阀切换至左位,油缸小腔通油箱,油缸大腔推力增大,镦挤工件完毕(工进)。
2.8 镦锻油缸回程
当油压升压力继电器设定的最大值28MPa时,电磁换向阀18T得电0.3S,实现压力预泄,减少油路换向冲击,以减小噪声和振动,吸收脉动。
然后电磁换向阀18的11T得电,切换至右位,油缸小腔进油,大腔油液经电磁换向阀18、17和球阀,冷却器,回油滤油器流回油箱。
冲杆退至起始位置,电磁换向阀17和18同时断电回到中位。
2.9 夹紧缸抽回斜块
电液换向阀8T得电,换至右位,活塞杆有杆腔进油,叉座退回至起始位置,抽回斜块。
2.10 分模,取出工件
电液换向阀3T得电,切换至右位,上胎板提起,上下模块分离,取出工件。
完成一个工作循环。
3 液压系统的性能分析
最大工作压力28MPa,工作压力可根据需要调整,并设有安全阀,避免压力过高,确保设备的正常使用。
本设备利用电机泵组做动力源,通过换向阀的结合运用,带动油缸前进、后退,达到工作要求。
采用差动回路,满足能趁热镦锻。
本液压控制系统具有油阻小,结构简单、紧凑,通流量大,响应快,安全可靠性等特点。
参考文献
[1]刘新德,赵曼琳,吴志明.GB/T3766-2001.液压系统通用技术条件[S].1983.
[2]贾培起.液压缸[M].北京:科学技术出版社,1987.
[3]刘辉,林玲.基于PLC控制的液压控制系统[J].科技动态.
[4]张书奇.液压自动往复液压缸的设计[J].液压气动与密封,2003.
[5]程大先.机械设计手册单行本液压传动[M].北京:化学工业出版社,2004.
[6]赵兵,张启明.重型机械标准[Z].1998.
作者简介:王占武(1973-),男,辽宁省阜新市人,工作单位:辽宁北辰液压气动有限公司,职务:技术部长,研究方向:液压。